Технология и оборудование сварки
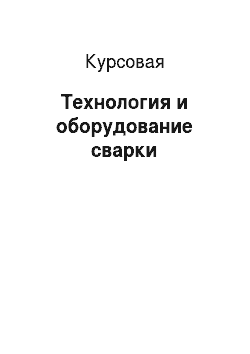
Данный способ широко используют в промышленности для соединения металлов повышенной толщины: стали и чугуна различного состава, меди, алюминия, титана и их сплавов. К преимуществам способа относится возможность сварки за один проход металла практически любой толщины, что не требует удаления шлака и соответствующей настройки сварочной установки перед сваркой последующего прохода, как при других… Читать ещё >
Технология и оборудование сварки (реферат, курсовая, диплом, контрольная)
МИНИСТЕРСТВО ОБРАЗОВАНИЯ И НАУКИ.
РОССИЙСКОЙ ФЕДЕРАЦИИ ГОСУДАРСТВЕННОЕ ОБРАЗОВАТЕЛЬНОЕ УЧРЕЖДЕНИЕ ВЫСШЕГО ПРОФЕССИОНАЛЬНОГО ОБРАЗОВАНИЯ.
«УФИМСКИЙ ГОСУДАРСТВЕННЫЙ НЕФТЯНОЙ ТЕХНИЧЕСКИЙ УНИВЕРСИТЕТ».
Кафедра «Технология нефтяного аппаратостроения».
Курсовая работа.
Технология и оборудование сварки Выполнил студ. гр..
Проверил преподаватель.
УФА 2010.
Содержание Введение.
1. Определение свариваемости применяемых материалов Сталь 17ГС по ГОСТ 5520–79.
2. Узел приварки нижней обечайки, нижнего эллиптического днища и опорной обечайки (Узел Г).
3. Расчет режимов электрошлаковой сварки Приложение Список использованной литературы.
Введение
электрошлаковая сварка сталь Сварка — один из наиболее распространенных технологических процессов всех отраслей машиностроения. В частности, это основной метод изготовления колонного и емкостного оборудования нефтепереработки, а также труб магистральных и технологических трубопроводов..
Современное оборудование нефтепереработки характеризуется высокой сложностью и ответственностью. Поэтому при его изготовлении используются самые разные способы и методы сварки.
В данной работе рассмотрены несколько типичных задач, стоящих при проектировании оборудования. В частности, это сварка разнородных материалов, сварка обечаек с разными толщинами, приварка штуцеров и опор и т. д. Для каждого из этих случаев были подобраны присадочные материалы и рассчитаны основные параметры сварочного процесса — сила и напряжение сварочного тока, скорость подачи электрода и прочие.
1. Определение свариваемости применяемых материалов Сталь 17ГС по ГОСТ 5520−79.
По качественному признаку данная сталь относится к классу конструкционная низколегированная феррито-перлитного класса повышенной прочности. Сталь 17ГС применяется: для изготовления корпусов аппаратов, днищ, емкостного оборудования, фланцев и других сварных деталей, работающих под давлением при температурах от -40 °С до +475 °С; для изготовления деталей и элементов трубопроводов пара и горячей воды атомных станций (АС), с расчётной температурой среды не выше 350 °C при рабочем давлении менее 2,2 МПа (22 кгс/см2); для изготовления электросварных прямошовных газопроводных труб диаметром 530, 720 и 820 мм.
Химический состав стали 17ГС по ГОСТ 5520–79.
С (0,14−0,20%); Si (0,4−0,6%); Mn (1,0−1,4%); S (? 0,004%);
P (?0,035%); Cr (?0,3%); Cu (?0,3%); As (?0,08%); Ni (?0,3%); N (? 0,008%);
Углерод является основным легирующим элементом, который определяет механические свойства этой группы сталей. Повышение его содержания в стали усложняет технологию сварки и затрудняет возможности получения равно прочного сварного соединения без дефектов. Поэтому свариваемость углеродистых сталей можно условно оценить по эквивалентному содержанию углерода, которое определяется по формуле.
(1.1).
где С, Mn, Cr, Mo, Ni, Cu, P — процентное содержание химических элементов в стали;
Так как Сэ > 0,45%, в зависимости от толщины металла применяем предварительный подогрев.
Температуру предварительного подогрева для повышения сопротивляемости металла шва к холодным трещинам определяют в зависимости от эквивалента углерода Cэ и толщины свариваемой заготовки (рисунок 1.1).
Рисунок 1.1 — График подбора температуры предварительного подогрева Сначала рассчитывается значение эквивалента углерода без учета толщины металла по формуле:.
(1.2).
Влияние толщины свариваемого металла учитывается поправкой.
Полный эквивалент углерода определяется выражением.
Температура предварительного подогрева определяется по формуле.
Таким образом, требуется предварительный подогрев деталей до температуры 123,7оС.
Склонность к образованию горячих трещин определяется отношением
(1.3).
Так как HCS<4, то данный материал не склонен к образованию горячих трещин[1].
2. Узел приварки нижней обечайки и нижнего эллиптического днища (узел Г).
Узел приварки нижней обечайки и нижнего эллиптического днища электрошлаковой сваркой по ГОСТ 15 164–78. Исходя из толщины свариваемых деталей (S1=S2 = 50 мм) по ГОСТу выбираем вид сварного соединения С1, способ сварки — ШЭ (сварка проволочным электродом).
s, s1 — толщины свариваемых деталей, bр — зазор в стыке,.
q — усиление шва.
Рисунок 2.1 — Сварка нижней обечайки и нижнего эллиптического днища.
S1 = S2 = 50 мм; q = 3 мм; bp = 25 мм.
Данный способ широко используют в промышленности для соединения металлов повышенной толщины: стали и чугуна различного состава, меди, алюминия, титана и их сплавов. К преимуществам способа относится возможность сварки за один проход металла практически любой толщины, что не требует удаления шлака и соответствующей настройки сварочной установки перед сваркой последующего прохода, как при других способах сварки. Для сварки используют один или несколько проволочных электродов или электродов другого увеличенного сечения и флюс.
Сваривается сталь 17ГС следовательно выбираем [1,2]:
- сварочную проволоку: Св-08ГС ГОСТ 2246;
- флюс: АН-8 ГОСТ 9087.
3. Расчет режимов электрошлаковой сварки.
Электрошлаковая сварка характерна тем, что основная часть тепла, необходимая для нагрева и плавления основного и электродного металлов, образуется за счет прохождения электрического тока через расплавленный флюс — шлак. Такая сварка чаще всего ведется с принудительным формированием шва и обычно выполняется при вертикальном положении свариваемых деталей. Образование шлаковой ванны производится дуговым процессом, но может быть также осуществлено с помощью электропроводного флюса. Электрошлаковый процесс протекает устойчиво как на постоянном, так и на переменном токе, но чаще электрошлаковую сварку ведут на переменном токе от трансформатора с жесткой характеристикой. Установлено, что устойчивость электрошлакового процесса возрастает с повышением электропроводности флюса.
Скорость сварки, напряжение сварочного тока на электродных проволоках, количество электродных проволок выбираем по таблице в зависимости от толщины свариваемых кромок заготовок (S=50 мм)[1]:
n=1.
n — количество электродных проволок.
dпроволоки=3 мм Скорость подачи электродной проволоки определяют по формуле:
(2.2).
где — площадь завариваемого зазора, (=1250 мм2).
— суммарная площадь поперечного сечения электродных проволок:
(мм2).
Скорость подачи электродной проволоки равна:
Сила сварочного тока рассчитывается по формуле:
(2.3).
Требуемый объем флюса находится:.
где h — глубина шлаковой ванны, мм, h = 40 мм[1].
B — ширина завариваемого зазора между заготовками, мм, В = 25 мм[1].
Определяем требуемый объем флюса:
Выбор сварочного оборудования..
Выбираем сварку проволочным электродом источником У875. Характеристики источника:
— сила тока — 1500 А;
— ПВ — 100%;
— размер электрода — 3 мм;
— количество электродов — 1;
— скорость подачи электродов — 14…500 м/ч;
— максимально свариваемая толщина — 50…100 мм.
Приложение 1.
Карта технологического процесса сварки.
1. Наименование изделия Сосуды, работающие под давлением.
2. Способ сварки Электрошлаковая сварка.
3. НТД по сварка Сосуды и аппараты стальные сварные ОСТ-26−291−94.
4. Основной материал Сталь 17ГС по ГОСТ 5520–79.
Диаметр 2000 мм, толщина 50 мм.
5. Соединение: вид соединения стыковое вид разделки без скоса кромки.
тип соединенияC1 по ГОСТ 15 164–78.
Конструкция соединения. | Конструктивные элементы шва. | |
Толщина свариваемых кромок. S, мм. | Ширина шва. e, мм. | Усиление шва. g, мм. | Зазор между кромками. b, мм. | |
25. | ||||
6. Способ подготовки кромок: Обработать края свариваемых деталей режущим инструментом для получения нужного размера, свариваемые кромки и прилегающие к ним поверхности зачистить механическим способом до металлического блеска на ширину не менее 12 мм с наружной и внутренней стороны детали. Удалить следы масел, грязи и других загрязнений.
7. Способ сборки: на прихватках с обеспечением равномерного зазора.
8. Требования к прихваткам: Длина прихваток должна составлять 60…80 мм и располагаться они должны равномерно по окружности трубы в количестве 8−10 штук. Прихватки должны быть проверены на отсутствие дефектов внешним осмотром, участки, имеющие дефекты, перед сваркой необходимо удалить механическим способом.
9. Сварочный материал по ГОСТ 2246, ГОСТ 9087:.
Марки сталей. | Сварочная проволока. | Флюс. | |
17ГС. | Св-08ГС. | АН-8. | |
10. Положения шва при сварке: все пространственные положения.
11. Подогрев: Сварка производится дополнительным нагревом до температуры 130 °C.
12. Сварочное оборудование: сварочный автомат У875.
13. Режим сварки:.
Диаметр электрода. dэл, мм. | Сварочный ток. I, А. | Скорость сварки, м/ч. | Скорость подачи проволоки. м/ч. | Число проходов. n. | |
1,5. | |||||
14. Термическая обработка сварного соединения: предназначенные для работы в средах, вызывающих коррозию, должны подвергаться термической обработке по требованию, оговоренному в проекте. Режим термической обработки должен быть согласован со специализированной научно-исследовательской организацией.
15. Требования по контролю качества сварного соединения:
Визуальный и измерительный контроль — 100% стыков.
Рентгенконтроль, УЗК: Объем контроля в соответствии с требованиями НТД, либо проекта.
Нормы оценки качества в соответствии с ОСТ 26−291−94..
Другие методы контроля согласно требованию проекта.
Список использованных источников.
1 Учебно-методическое пособие для выполнения практических работ курсового проекта. /Файрушин А.М., Ризванов Р. Г., Карпов А.Л.-Уфа, 2004,-60с.
2 ОСТ 26−291−94 Сосуды и аппараты стальные сварные. Общие технические условия.- М.: Издательство стандартов, 1994.
3 ГОСТ 15 164–78 Электрошлаковая сварка. Соединения сварные. Основные типы, конструктивные элементы и размеры.-М.Издательство стандартов, 1987.-17с.
4 ГОСТ 2246–70 Проволока стальная сварочная. Технические условия (2002, с попр. 2003).
5 ГОСТ 30 482–97 Электрошлаковая сварка сталей. Требования к технологическому процессу.
6 ТУ14−1-4853−90 Прокат толстолистовой стойкий к коррозионному растрескиванию.