Формообразование поверхностей деталей «Проходник»
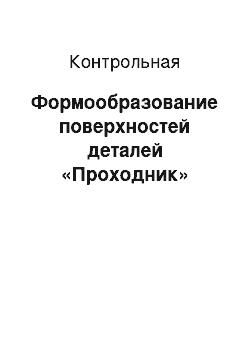
Задача нормирования времени возникает на различных этапах проектирования технологического процесса сборки. В начале ее приходится решать для установления типа производства. На основе разработанных технологических схем общей и узловой сборки выявляют несколько характерных операций и для них определяют нормы времени по укрупненным нормативам или другими приближенными методами нормирования… Читать ещё >
Формообразование поверхностей деталей «Проходник» (реферат, курсовая, диплом, контрольная)
Задача нормирования времени возникает на различных этапах проектирования технологического процесса сборки. В начале ее приходится решать для установления типа производства. На основе разработанных технологических схем общей и узловой сборки выявляют несколько характерных операций и для них определяют нормы времени по укрупненным нормативам или другими приближенными методами нормирования. Сопоставляя среднеарифметическое из этих норм с темпом работы, устанавливают тип производства.
На этапе разработки маршрутной технологии нормы времени устанавливают на все операции технологического процесса после выявления их структуры и содержания. Для серийного производства при нормировании используют укрупненные нормативы, для массового применяют расчетно-аналитический метод нормирования.
На этапе разработки операционной технологии в массовом производстве установленные ранее нормы времени корректируют после внесения в содержание операций отдельных изменений (уменьшение и перекрытие элементов штучного времени, изменение структуры операций). Откорректированные нормы времени увязывают с темпом работы. Содержание операций и нормы времени подробно прорабатывают при автоматизации сборочных процессов, при многомашинном обслуживании, а также при использовании роботов на основных и вспомогательных операциях.
1. Отделочный этап
1.1 Круглошлифовальная операция
1.Шлифовать поверхность Ш 38,3 предварительно (по вариантуврезной схемой).
Выбор режущего инструмента
Выбираем шлифовальный круг прямого профиля ПП по ГОСТ 2424–83.
Геометрические параметры круга: Dк=600 мм; Н=250 мм; В=60 мм.
Параметры материала:15А50С1К
15А-электрокорунд нормальный для предварительной обр-ки легированных сталей [1,стр.242]
50-зернистость для предварительного шлифования [1,стр.247,табл.166]
П-индекс зернистости (содержание осн. фракции-55%) [1,стр.245]
С1-степень твердости для круглого врезного шлифования [1,стр.249]
К1-керамическая связка для всех видов шлифования, для инструмента из электрокорунда [1,стр.247]
А-класс точности [1,стр.250]
Максимальная скорость вращения круга-35 м/с.
Полное обозначение инструмента: ПП 600×250х40 15А50С1К 35 м/с.
Рис.1-Шлифкруг прямого профиля ПП. ГОСТ 2424–83
Выбор цикла шлифования
Обработка проводится с циклом без окончательного шлифования.
Рис.2-Схема цикла без окончательного шлифования
Расчет технологических режимов резания
1.Окружная скорость заготовки:
2.Частота вращения заготовки и действительная скорость вращения:
Используем круглошлифовальный станок модели 3151:
Технические данные:
Наибольший диаметр шлифкруга Dк, мм…600
Наибольшая высота шлифкруга В, мм…100
Внутренний диаметр круга, мм…305
Максимальный диаметр шлифования, мм…150
Частота вращения шпинделя шлифовальной бабки, об/мин…1100
Мощность двигателя шлифовальной бабки, кВт…7
Частота вращения планшайбы бабки, об/мин…75,150,300
Принимаем ;
Действительная скорость вращения заготовки:
3.Окружная скорость абразивного круга:
4.Расчет минутной радиальной подачи (средней) в мм/мин:
Максимальное значение подачи:
Минимальное значение подачи :
Среднее значение:
5.Расчет основного времени обработки:
Где припуск обработки на сторону, коэффициент выхаживания.
6.Расчет эффективной мощности шлифования:
полезная мощность станка;
шлифование возможно
7.Проверка на условие бесприжоговости:
Удельная мощность:
Допустимая удельная мощность:
гдекоэффициент для твердости материала круга С1,
условие выполняется.
1.2 Круглошлифовальная операция
1.Шлифовать поверхность Ш 38,02 окончательно (по вариантуврезной схемой).
Выбор режущего инструмента
Выбираем шлифовальный круг прямого профиля ПП по ГОСТ 2424–83.
Геометрические параметры круга (аналогичные) :Dк=600 мм; Н=250 мм; В=60 мм.
Параметры материала:24А20С2К;
24А-электрокорунд нормальный для окончательной обр-ки легированных сталей [1,стр.242]
20-зернистость для окончательного шлифования [1,стр.247,табл.166]
С2-степень твердости для круглого врезного шлифования [1,стр.249]
К-керамическая связка для всех видов шлифования, для инструмента из электрокорунда [1,стр.247]
2-класс неуравновешенности [1,стр.250]
Максимальная скорость вращения круга-35 м/с.
Полное обозначение инструмента: ПП 600х250х40 24А20С2К 35 м/с.
Выбор цикла шлифования
Поскольку проводиться окончательное шлифование на 5 квалитет после термообработки легированной стали, обработка производиться полным циклом шлифования.
Рис.3-Схема полного цикла шлифования
Расчет технологических режимов резания
1.Окружная скорость заготовки для закаленной стали:
2.Частота вращения заготовки и действительная скорость вращения:
Используем аналогичный круглошлифовальный станок модели 3151.
Принимаем ;
Действительная скорость вращения заготовки:
3.Окружная скорость абразивного круга:
4.Расчет минутной радиальной подачи на каждом этапе, в мм/мин:
Подача на участке 0−1:
Подача на участке 1−2:
5.Расчет основного времени обработки:
Где припуск обработки на сторону, припуск обработки на этапе 0−1,
припуск обработки на этапе 1−2,
коэффициент выхаживания.
6.Расчет эффективной мощности шлифования на каждом этапе:
полезная мощность станка;
шлифование возможно
7.Проверка на условие бесприжоговости:
Удельная мощность:
Допустимая удельная мощность:
гдекоэффициент для твердости материала круга С2,
условие выполняется.
1.3 Внутришлифовальная операция
1.Шлифовать поверхность Ш 32,95 окончательно (по вариантупродольное схемой).
Выбор режущего инструмента
Выбираем шлифовальный круг прямого профиля ПП по ГОСТ 2424–83.
Геометрические параметры круга: Dк=10мм; Н=5 мм; В=11 мм.
Параметры материала:24А50ПС18К0А2;
24А-электрокорунд нормальный для окончательной обр-ки легированных сталей [1,стр.242]
50-зернистость для окончательного внутреннего шлифования [1,стр.247,табл.166]
П-индекс зернистости (содержание осн. фракции-55%) [1,стр.245]
С1-степень твердости для внутреннего окончательного шлифования [1,стр.249]
8-номер структуры абразива для внутреннего шлифования [1,стр.249]
К0-керамическая связка для малогабаритных кругов для внутреннего шлифования, для инструмента из электрокорунда [1,стр.247]
А-класс точности [1,стр.250]
2-класс неуравновешенности [1,стр.250]
Максимальная скорость вращения круга-35 м/с.
Полное обозначение инструмента: ПП 10х5х11 24А50ПС18К0А2 35 м/с.
Выбор цикла шлифования
Поскольку проводиться окончательное шлифование на 7 квалитет после термообработки, обработка производиться полным циклом шлифования.
Расчет технологических режимов резания
1.Окружная скорость заготовки для закаленной стали:
2.Частота вращения заготовки и действительная скорость вращения:
Используем внутришлифовальный станок модели 3К228В:
Технические данные:
Наибольший диаметр шлифкруга Dк, мм…25
Наибольшая высота шлифкруга В, мм…25
Максимальный диаметр шлифования, мм…200
Частота вращения шпинделя шлифовальной бабки, об/мин…20 000−100 000
Мощность двигателя шлифовальной бабки, кВт…5,5
Частота вращения бабки заготовки, об/мин…280−2000
;
3.Окружная скорость абразивного круга (при этом выбираем частоту вращения круга) :
4.Расяитуем величину подач при обработке.:
Продольная подача:
Минутная подача:
5.Расчет величины рабочего хода стола:
.
6. Определить число одинарных и двойных ходов:
.
.
7.Расчитать поперечную подачу на один ход
.
8.Расчет основного времени обработки:
Где припуск обработки на сторону, припуск обработки на этапе 0−1,
припуск обработки на этапе 1−2,
6.Расчет эффективной мощности шлифования на каждом этапе:
.
полезная мощность станка;
шлифование возможно
7.Проверка на условие бесприжоговости:
Удельная мощность:
Допустимая удельная мощность:
гдекоэффициент для твердости материала круга С1,
условие выполняется.
2. Хонингование
1.Параметры обрабатываемой поверхности для предшествующей и текущей ступеней обработки:
Поверхностьотверстие Ш 32 Н6; Ra 0,32, L=46.
Предшествующая операцияшлифование: Ш31,95 Н6, Rа 0,63.
2. Определение припуска на хонингование:
2z=0,04 (мм) — припуск на диаметр [2,стр.114,табл.П.5.3];
z=0,02 (мм) — припуск на сторону [3,стр. 431, табл.71];
припуск на черновой обработке [3,стр.431,табл.70],
припуск на чистовой обработке [3,стр.431,табл.70].
3. Выбор оборудования для операции хонингования:
Выбираем вертикальный хонинговальный станок ОФ-50 [4,стр.255,табл.1,36]:
Технические данные:
Наибольший диаметр хонингования, мм…50
Наибольшая длина хода, мм…200
Скорость хонинговальной головки, об/мин…200−800
Мощность приводного электродвигателя, кВт…1
Вес станка, кН…10
4. Назначение инструмента:
Поскольку припуск z=0,025<0,05 мм, применяем абразивный инструмент.
Применяем абразивные бруски на основе бруска прямоугольного БП по ГОСТ 2456–82.
Рис.4- Брусок прямоугольный БП. ГОСТ 2456–82
обработка поверхность деталь хонингование Состав, размеры и число брусков в хонинговальной головке:
Состав материала абразива для закаленной стали- 63С М40 СМ1 7 Б А [3,стр.433,табл.73], где;
63Сзеленый карбид кремния для абразивной обработки [1,стр.243],
М40- зернистость для хонингования [1,стр.247],
СМ1- степень твердости для хонингования [1,стр.249],
7- номер структуры зерна [1,стр.249],
Ббакелитовая связка для абразивного инструмента [1,стр.243];
Акласс точности [1,стр.250]
Рис. 5- Геометрические параметры обработки Геометрические размеры брусков [3,стр.433,436]:
l=(0,5…0,75)*L=0,5*33=16,5 (мм) — длина брусков. Примем l=17 (мм).
lвых=1/3*l=1/3*17=5,66 (мм) — длина выходов брусков. Примем lвых=6 (мм).
Lрх=L+2*lвых-l=46+2*6−17=41 (мм) — длина рабочего хода.
Режущий периметр [3,стр.434]:
режущая поверхность брусков,
где периметр обр. поверхности.
Примем количество брусков в головке-3 [3,cтр.431,433];
Ширина брусков: .
Высота с=4,5 (мм).
Полное обозначение инструмента: БП 8х4,5х22 63С М40 СМ1 7 Б, А ГОСТ 2456–82.
5. Назначение продольной подачи:
Поскольку Lрх=35,5<50, то примем Vпр=5 (м/мин) [3,стр.435].
6. Назначение окружной скорости вращения головки:
Примем Vвр. черн=Кчерн*Vпр=3*5=15 (м/мин) — на черновом этапе,
Vвр.чист=Кчист*Vпр=7*5=35 (м/мин) — на чистовом этапе, Где К=Vвр/Vпрсоотношение между скоростью вращения и скоростью возвратно-поступательного движения хонинговальной головки.
Кчерн=3; Кчист=7 [3,стр.436,табл.74].
7. Назначение поперечной подачи:
Sпоп.черн=0,003 (мм/дв.х) — на черновом этапе,
Sпоп.чист=0,0004 (мм/дв.х) — на чистовом этапе.
8. Число двойных ходов:
.
9. Расчет времени обработки:
3. Суперфиниширование
1.Параметры обрабатываемой поверхности для предшествующей и текущей ступеней обработки:
Поверхностьхвостовик Ш 46 h7; Ra 0,32, L=46
Предшествующая операцияшлифование: h7, Rа 0,63.
2. Определение припуска на суперфиниширование:
2z=0,05 (мм) — припуск на диаметр [2,стр.114,табл.П.5.3];
z=0,0025 (мм) — припуск на сторону [3,стр. 438, табл.75];
Припуск на операции должен превышать высоту неровностей поверхности полученной на предыдущей обработке — чистовом шлифовании (Rz 1,25).
3. Выбор оборудования для операции суперфиниширования:
Выбираем суперфинишный круглошлифовальный станок 3870Б :
Технические данные:
Наибольший диаметр обрабатываемой модели, мм…140
Наибольшая длина обрабатываемой детали, мм…360
Мощность приводного электродвигателя, кВт…3
Масса станка, т…3,61
4. Назначение инструмента:
Применяем абразивные бруски на основе бруска прямоугольного БП по ГОСТ 2456–82.
Рис.5- Брусок прямоугольный БП. ГОСТ 2456–82
Применяем число брусков-2;
Состав материала брусков:
Состав материала абразива для закаленной стали- 23А М14 СМ1 7 Б А [3,стр.433,табл.73], где;
23Абелый электрокорунд для абразивной обработки [1,стр.243],
М14- зернистость для суперфиниширования [1,стр.247],
СМ1- степень твердости для суперфиниширования [1,стр.249],
7- номер структуры зерна [1,стр.249],
Ббакелитовая связка для абразивного инструмента [1,стр.243];
Акласс точности [1,стр.250].
Геометрические размеры брусков:
Поскольку имеем на данной поверхности лыски шириной b=20 мм, ширина бруска должна быть равна В=1,6*b=1,6*20=32 (мм) [3,стр.438].
Рис. 6 Схема расположения абразивных брусков.
Длина бруска для врезного суперфиниширования без продольной подачи равна l=L=30(мм);
Высота бруска с=8 (мм).
Полное обозначение инструмента: БП 22х8х30 23А М14 СМ1 7 Б, А ГОСТ 2456–82;
Стандартные бруски подвергаються пропитке твердым смазочным материалом в виде раствора или расплава [3,стр.438].
Угол установки между брусками-60 градусов [3,стр.439].
Рис.7- Схема закрепления абразивных брусков.
5. Расчет режимов резания Амплитуда колебаний осциллирующего движения брусков А=(2…6)=4 (мм) [3,стр.439].
Скорость колебаний Vкол=(5…7)=5 (м/мин) [3,стр.439].
Вращательная скорость детали [3,стр.439]:
на черновом этапе Vвр. черн=Кчерн*Vкол=3*Vкол=3*5=15 (м/мин),
на чистовом этапе Vвр. чист=Кчист*Vкол=10*Vкол=10*5=50 (м/мин),
где К=Vвр/Vкол.
Давление брусков для деталей из стали, 0,1−0,3 МПа [3,стр.439]. Примем 0,2 МПа.
6. Расчет основного машинного времени:
где Ст=0,067, k1=0,62- коэффициенты.
4. Технологическое нормирование операций ТП
1.Определение программы запуска:
где Nвыпзаданная годовая программа выпуска (4200шт.),
a=2,5%- общая доля вероятного брака,
b=3,5%- общая доля деталей идущих на запчасти, с=3%- общая доля деталей незавершенного производства.
2.Определение размера партии деталей:
где a=6- периодичность запуска (3,6,12,24),
254- число рабочих дней в году.
Нормирование операций ТП:
Табл. 1. Нормирование операций
Наименование Операций | Основное время, To | Вспомогательное время, Tв | Опер. время, Топ | Время обслуживания, Тоб | Время нормированных перерывов, Тнп | Штучное время, Тшт | Подготовит-заключит. время, Тп-з | Тп-з./n | Штучно калькуляционное время, Тшт-к | |||||||
Установка и снятие детали | Управление станком | Измерение деталей | Серийное | |||||||||||||
1. | Токарная | 1.12 | 0.15 | 0.205 | 0.29 | 1.2 | 2.32 | 0.33 | 0.0394 | 0.37 | 0,1392 | 2.8236 | 0.28 | 3,1036 | ||
Сверлильная | 2.11 | 0.07 | 0.15 | 0.04 | 0.48 | 2,59 | 0.05 | 0.044 | 0.1 | 0.038 | 2,678 | 0.35 | 3,028 | |||
Зубофрезерная | 3.6 | 0.06 | 0.11 | 0.15 | 0.59 | 4.19 | 0.2 | 0.071 | 0.27 | 0.336 | 4.726 | 0.45 | 5.176 | |||
4. | Круглошлифовальная предварительная | 0.15 | 0.07 | 0.03 | 0.09 | 0.35 | 0.49 | 0.14 | 0.0083 | 0.15 | 0.0136 | 0.6436 | 0.2 | 0.844 | ||
5. | Круглошлифовальная окончательная | 0.28 | 0.07 | 0.03 | 0.09 | 0.35 | 0.633 | 0.14 | 0.0083 | 0.15 | 0.0136 | 0.786 | 0.2 | 0.986 | ||
Внутришлифовальная | 0.71 | 0.07 | 0.06 | 0.04 | 0.31 | 1.02 | 0.14 | 0.017 | 0.16 | 0.043 | 1.203 | 0.4 | 1.63 | |||
Хонинговальная | 0.38 | 0.06 | 0.05 | 0.085 | 0.36 | 0.74 | 0.03 | 0.013 | 0.04 | 0.079 | 0.849 | 0.13 | 0.979 | |||
Суперфинишная | 0.6 | 0.08 | 0.07 | 0.08 | 0.43 | 0.78 | 0.03 | 0.014 | 0.04 | 0.083 | 0.893 | 0.25 | 1.143 | |||
Пример нормирования для заданной круглошлифовальной предварительной операции:
Топ.=То+Тв'=0,15+(0,07+0,03+0,09)х1,85=0,49 (мин.);
Тшт.=Топ.+Тоб.+Тн.п.=0,49 +0,14+0,0136=0,6436 (мин.);
Тшт-к.=Тшт+Тп-з./n=0,6436+8/40=0,844 (мин.).
Коэффициент загрузки:
— расчетное число станков,
принятое число станков,
— такт выпуска продукции,
(ч.) — действительный годовой фонд времени, где
(ч.) — календарный годовой фонд времени, при двухсменной работе,
— коэффициент, учитывающий ремонт оборудования (0,95…0,97).
Расчет и оптимизация загрузки оборудования
Табл. 2. Загрузка оборудования до оптимизации
№ | Наименов. операции | Модель оборудования | Т шт-к | Расчетное число станков, mр | Коэфф. загрузки, з | Средний коэфф. загрузки, з ср | |
Токарная | 16Б16А | 3.104 | 0.0227 | 0.0227 | 0.015 | ||
Сверлильная | 5К310 | 3.028 | 0.0221 | 0.0221 | |||
Зубофрезерная | 5В832 | 5.176 | 0.0378 | 0.0378 | |||
Круглошлифовальная предварительная | 0.844 | 0.0062 | 0.0062 | ||||
Круглошлифовальная окончательная | 0.986 | 0.0072 | 0.0072 | ||||
Внутришлифовальная | 3К228В | 1.63 | 0.012 | 0.012 | |||
Хонинговальная | ОФ-50 | 0.979 | 0.0072 | 0.0072 | |||
Суперфинишная | 3870Б | 1.143 | 0.835 | 0.835 | |||
Табл. 3. Загрузка оборудования после оптимизации
№ | Наименов. операции | Модель оборудования | Т шт-к | Расчетное число станков, mр | Принятое число станков, mпр | Коэфф. загрузки, з | Средний коэфф. загрузки, з ср | |
Токарная | 16Б16А | 3.104 | 0.0227 | 0.011 | 0.0082 | |||
Сверлильная | 5К310 | 3.028 | 0.0221 | 0.011 | ||||
Зубофрезерная | 5В832 | 5.176 | 0.0378 | 0.0095 | ||||
Круглошлифовальная предварительная | 0.844 | 0.0062 | 0.006 | |||||
Круглошлифовальная окончательная | 0.986 | 0.0072 | 0.007 | |||||
Внутришлифовальная | 3К228В | 1.63 | 0.012 | 0.006 | ||||
Хонинговальная | ОФ-50 | 0.979 | 0.0072 | 0.007 | ||||
Суперфинишная | 3870Б | 1.143 | 0.835 | 0.008 | ||||
График загрузки до оптимизации График загрузки после оптимизации
1. Справочник технолога-машиностроителя. Под ред. Косиловой А. Г. и Мещерякова Р. К. т.2., М., 1985, 656 с.
2. Определение припусков на механическую обработку и технологические размерные расчеты. Гранин В. Ю., Долматов А. И., Лимберг Э. А., Харьков, ХАИ, 1993, 119 стр.
3. Справочник технолога-машиностроителя. Под ред. Косиловой А. Г. и Мещерякова Р. К. т.1., М., 1985, 656 с.
4. Металлорежущие станки. Под ред. Ачеркана Н. С., т.1, М., Машиностроение, 1965, 765 с.
5. Выбор оборудования и метода механической обработки детали по минимуму приведенных затрат. Мунгиев А. М., Горбачев А. Ф., Жданов А. А., Харьков, ХАИ, 2006, 60 стр.
6. Оформление технологической документации в курсовых и дипломных проектах. Барсуков А. П., Горбачев А. Ф., Гранин В. Ю., Харьков, ХАИ, 1990, 45 стр.