Исследование и разработка математического и программного обеспечений подсистемы САПР лазерной резки листового материала
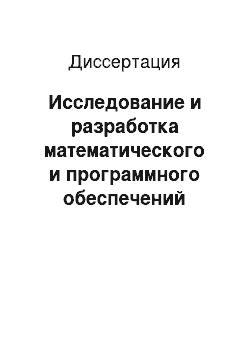
Математическое обеспечение — совокупность математических моделей, методов и алгоритмов, необходимых для построений инструментов проектировщика — подсистем САПР. Программное обеспечение — совокупность программных средств и соответствующих программных документов, представленных в заданной форме и позволяющих строить подсистемы САПР для решения различных задач проектирования. Общие принципы… Читать ещё >
Содержание
- Глава 1. СОСТОЯНИЕ ВОПРОСА, ЦЕЛИ И ЗАДАЧИ ИССЛЕДОВАНИЯ
- 1. 1. Обзор существующих пакетов программ и основные принципы оптимизации, заложенные в них
- 1. 1. 1. САПР «Техтран»
- 1. 1. 2. Интегрированная САПР «СИРИУС»
- 1. 1. 3. ПО фирмы «Bystronic»
- 1. 2. 0 преимуществах оптимизации холостого прохода деталей по сравнению с циклической резкой
- 1. 3. Основные результаты анализа
- 1. 1. Обзор существующих пакетов программ и основные принципы оптимизации, заложенные в них
- Выводы по главе 1
- Глава 2. МАТЕМАТИЧЕСКАЯ МОДЕЛЬ НАХОЖДЕНИЯ ОПТИМАЛЬНОГО ОБХОДА ДЕТАЛЕЙ ПРИ ЛАЗЕРНОЙ РЕЗКЕ
- 2. 1. Постановка задачи
- 2. 2. Разбиение деталей на листе материала на группы
- 2. 3. Нахождение минимального холостого прохода в группе деталей
- 2. 4. Нахождение минимального холостого прохода при вырезке внутренних отверстий деталей
- 2. 5. Нахождение минимального холостого прохода при вырезке деталей внутри отверстий и правила построения оптимального маршрута
- 2. 6. Нахождение минимального холостого прохода среди групп деталей
- 2. 7. Методика объединения контуров нескольких деталей в один контур непрерывного реза и необходимые условия для этого
- Выводы по главе 2
- Глава 3. АЛГОРИТМИЧЕСКОЕ И ПРОГРАММНОЕ ОБЕСПЕЧЕНИЕ ПОИСКА ОПТИМАЛЬНОЙ ДЛИНЫ РЕЗА И ХОЛОСТЫХ ПРОХОДОВ
- 3. 1 Разработка пакета раскроя материала, его структура и возможности
- 3. 2. Подсистема САПР оптимизации длины холостого прохода и минимизации реза «Обход»
- 3. 3 Блок-схема алгоритма нахождения минимального холостого прохода в группе деталей
- 3. 4. Алгоритм нахождения минимального холостого прохода при вырезке внутренних отверстий деталей
- 3. 5. Алгоритм нахождения минимального холостого прохода среди групп деталей
- 3. 6 Блок-схема алгоритма объединения контуров нескольких деталей в один контур непрерывного реза
- 3. 7. Нахождение оптимального холостого прохода и минимального реза среди деталей на листе материала
- 3. 1 Разработка пакета раскроя материала, его структура и возможности
- 4. 1. Показатель эффективности оптимального холостого прохода и минимального реза деталей при лазерной резке
- 4. 2. Сравнительный анализ разработанной подсистемы САПР Обход" поиска оптимального холостого прохода и реза деталей с существующими пакетами программ,
- 4. 3. Реализация алгоритма нахождения минимальной длины реза деталей в случае совмещенного реза
Исследование и разработка математического и программного обеспечений подсистемы САПР лазерной резки листового материала (реферат, курсовая, диплом, контрольная)
Наиболее распространенным технологическим процессом в машиностроении и других отраслях является резка — основная операция заготовительного производства [73,81].
Широкое применение находят различные механические ^ методы разделения металлов [1], в первую очередь резка ножовочными полотнами, ленточными пилами, фрезами и др. [67]. В производстве используются разнообразные станки общего и специального назначения для раскроя листовых, профильных, и других заготовок и деталей из различных металлов и сплавов. Однако при многих достоинствах этого процесса следует отметить недостатки, связанные с низкой производительностью, малой стойкостью отрезного инструмента, трудностью или невозможностью раскроя материалов по сложному криволинейному контуру. ^ В промышленности получил распространение ряд процессов разделения материалов, основанных на электрофизическом, электрохимическом и физико-химическом воздействиях. Ацетиленокислородная резка, плазменная резка проникающей дугой и другие физико-химические методы разделения обеспечивают повышение производительности по сравнению с механическими методами, но не обеспечивают высокой точности и чистоты поверхностей реза и требуют в большинстве случаев последующей механической обработки. Электроэрозионная резка позволяет осуществлять процесс разделения материалов с малой шириной и высоким качеством реза, но и одновременно с этим характеризуется низкой производительностью.
Поэтому и возникла настоятельная производственная необходимость в разработке и промышленном освоении методов резки современных конструкционных материалов, сочетающих высокие показатели как по производительности процесса, так и по точности и качеству поверхностей реза. К числу таких перспективных процессов разделения материалов следует отнести лазерную резку металлов.
Сфокусированное лазерное излучение, обеспечивая высокую концентрацию энергии, позволяет разделять практически любые металлы и сплавы независимо от их теплофизических свойств. При этом можно получать узкие разрезы с минимальной зоной термического влияния. При лазерной резке отсутствует механическое воздействие на обрабатываемый материал, и возникают минимальные деформации, как временные в процессе резки, так и остаточные после полного остывания. Вследствие этого можно осуществлять лазерную резку с высокой степенью точности, в том числе и легкодеформируемых и нежестких заготовок или деталей. Благодаря большой плотности мощности лазерного излучения обеспечивается высокая производительность процесса в сочетании с высоким качеством поверхностей реза. Кратко рассмотренные особенности лазерной резки наглядно демонстрируют несомненные преимущества процесса в сравнении с традиционными методами обработки.
На сегодняшний день применение лазеров [10,27] при раскрое и резке очень распространено, так как одновременно с высокой точностью и производительностью обработки в этом случае обеспечивается значительная экономия материала за счет очень малой ширины реза и рациональной системы раскроя в сравнении с традиционными технологиями. При этом эффективность вырезания изделий сложного профиля значительно выше, чем при обычной вырубной штамповке листовых изделий. Лазерный раскрой материалов широко используется в современной автомобильной, аэрокосмической, судостроительной, электротехнической, легкой промышленности, сельскохозяйственном машиностроении.
Экономия материальных ресурсов — один из важнейших факторов повышения эффективности любого производства. Главный путь решения данной проблемы — снижение материалоемкости промышленной продукции. Для этого используют рациональный раскрой материала, который сводится к оптимальной раскладке деталей на листе материала [71]. Основной характеристикой экономичности раскроя служит так называемый коэффициент раскроя, представляющий собой отношение полезной площади всех заготовок к площади, используемой для их получения.
Проектирование процессов [74,75] лазерной резки, в том числе не только составление карт раскроя, но и нахождение оптимального маршрута режущего инструмента и их автоматизация, является актуальной задачей, поскольку:
1. Существующие методы и средства проектирования процессов лазерной резки не удовлетворяют выросшим требованиям качества резки.
2. Современные средства автоматизации проектирования также не удовлетворяют поставленным задачам, т.к. не решают ряда насущных проблем, возникающих при подготовке карт раскроев.
3. В настоящее время проектирование, технологическая подготовка производства и их автоматизация тесно связаны, что особенно отличает рассматриваемую область от других направлений [88,89].
В соответствии с предложенной Р. И. Сольницевым концепцией, САПР рассматривается как инструментарий проектировщика, где каждый инструмент включает основные компоненты технического, лингвистического, программного, информационного, методического и организационного обеспечения. Автоматизация практической деятельности человека позволяет повысить производительность труда [77]. Наиболее важными компонентами САПР в рассматриваемой области являются математическое и программное обеспечения, поскольку использование этих компонент позволит автоматизировать процесс подготовки карт раскроя для лазерной резки.
Математическое обеспечение — совокупность математических моделей, методов и алгоритмов, необходимых для построений инструментов проектировщика — подсистем САПР. Программное обеспечение — совокупность программных средств и соответствующих программных документов, представленных в заданной форме и позволяющих строить подсистемы САПР для решения различных задач проектирования [36,60,61]. Общие принципы и направления САПР разработаны в трудах И. П. Норенкова [55,56,57], Р. И. Сольницева [78,79,80], В Н. Нуждина [58], В. И. Анисимова [7], Г. Д. Дмитревича [30], Д. И. Батищева [11,12] и др. Направление, связанное с раскроем, отражено в работах Э. А. Мухачевой [52], Ф. В. Бабаева [8], В. В. Мартынова [48,49,50,51,92,93], Л. В. Канторовича, В. А. Залгаллера [31] и др.
Другими, не менее важными факторами повышения эффективности производства являются: экономия общего технологического времени, экономия энергозатрат, продление срока службы лазерного оборудования.
Под общим технологическим временем [2,3,26,34] понимается время, затраченное на подготовку к вырезке и время, затрачиваемое непосредственно на саму вырезку. Подготовку к вырезке можно разделить на две части: нахождение оптимального расклада деталей на листе заготовки и нахождение оптимальной длины раскроя этих деталей. В дальнейшем рассматриваются время на поиск оптимальной длины раскроя и время вырезки деталей. Сумму этих времен и будем называть общим технологическим временем.
Однако лазерное оборудование является дорогим и энергоемким оборудованием [70,83]. Поэтому снижение времени и расхода рабочего тела на выполнение операций лазерной резки является существенной экономией не только электроэнергии, но и продлит срок службы самого to оборудования.
В частности, весьма актуальной является задача нахождения минимальной длины прохода лазерного луча при резке листового материала. Решение этой задачи, также как и полной задачи проектирования лазерной резки невозможно без применения средств автоматизации проектирования как самого процесса лазерной резки, так и управляющих программ для лазерных установок резания [4,5,9,21,25,47].
Целью настоящей работы является разработка математических методов и моделей, алгоритмов и программного обеспечения нахождения оптимальной длины холостых проходов и минимальной длины реза при лазерной резке листового материала.
Методы исследования базируются на методах комбинаторной геометрии и методах оптимизации технических решений [6,23,33,62]. Поиск оптимальной ** длины холостых проходов при вырезке деталей на листе материала основан на поиске оптимального расположения точек врезания на контурах деталей, внутренних отверстиях и объединения деталей в один контур реза. Это осуществляется с помощью метода сопряженного градиента и алгоритмов, предложенных автором. Расчеты проводились при помощи ПК на базе процессора Intel г.
Pentium-II с использованием математических систем Matlab [83], MathCAD [29], и программ, реализованных в среде Visual С++ [86].
Научную новизну и ценность составляет:
1. Предложена методика объединения контуров деталей в линию непрерывного реза при наличии точек касания или общих сторон. Также предложена методика разбиения деталей на листе материала на группы с целью нахождения кратчайших холостых проходов в группах.
2. Разработана математическая модель, основанная на минимизации глобальной целевой функции, в результате которой находятся оптимальные положения точек врезания в контуры деталей. В качестве целевой функции предложена функция суммы расстояний между точками врезания всех деталей в группе.
3. Предложен единый алгоритм для нахождения оптимальных точек врезания, как внешних контуров деталей, так и внутренних отверстий, а также для деталей, расположенных внутри этих отверстий.
4. Разработана подсистема САПР «Обход», автоматизирующая процесс нахождения наикратчайшего маршрута лазерной режущей головки при раскрое листового материала.
Практическая ценность работы заключается в сокращении холостых проходов на 30−60% по сравнению с существующими пакетами раскроя листового материала («Техтран», САПР «СИРИУС», программное обеспечение фирмы «Bystronic»). Общее технологическое время обработки листа сокращается на 10−15%, длина реза деталей, расположенных без полей допуска, сокращается на 10−30%. Созданные методики и алгоритмы использованы в разработке системы САПР раскроя материала «Раскрой» — в созданной диссертантом подсистеме САПР «Обход» .
Реализация результатов работы. Результаты работы и соответствующее программное обеспечение внедрено на ФГУП ЦНИИ КМ «Прометей», что подтверждено соответствующим актом о внедрении.
Апробация работы. Основные результаты работы докладывались на научных конференциях «Гагаринские научные чтения» (г. Москва, 2000г), «Техническая кибернетика, радиоэлектроника и системы управления» (г. Екатеринбург, 2000г), научной сессии аспирантов (СПГУАП, 2000, 2002, 2003гг), международной конференции «Instrumentation in Ecology and Human Safety 2002» («IEHS'02», St. Petersburg) [40,41,42,43,44,46].
Публикации. Опубликовано 12 научных работ, 7 работ по теме диссертации, из них 1 статья [45] и тезисы к 6 докладам на международных и всероссийских научно-технических конференциях.
Структура и объем диссертации
Диссертация состоит из введения, четырех глав, заключения и библиографии.
Выводы по главе 4.
1. Предложен коэффициент эффективности холостых проходов, отражающий оценку найденного решения обхода деталей при резке. Чем меньше данный коэффициент, тем оптимальней найденное решение.
2. Показано, что разработанные математическая модель, методики, алгоритмы и подсистема САПР «Обход» дают более эффективное решение нахождения кратчайшего маршрута обхода деталей при их вырезке по сравнению с рассмотренными пакетами САПР «Техтран», интегрированной САПР «СИРИУС», ПО фирмы «Bystronic» на 30−60%.
3. Показано, что, применяя разработанную подсистему САПР «Обход», длина реза уменьшается на 10−30%.
ЗАКЛЮЧЕНИЕ
.
В ходе проведенных работ по диссертации получены следующие результаты.
1. Разработана математическая модель и методика, основанная на минимизации глобальной целевой функции, в результате применения которых находятся оптимальные положения точек врезания в контуры деталей. В качестве целевой функции предложена функция суммы расстояний между точками врезания всех деталей в группе.
2. Предложен единый алгоритм для нахождения оптимальных точек врезания, как внешних контуров деталей, так и внутренних отверстий, а также для деталей, расположенных внутри этих отверстий.
3. Предложена методика объединения контуров деталей в линию непрерывного реза при наличии точек касания или общих сторон.
4. На основании предложенной математической модели разработаны алгоритмы поиска наикратчайшего холостого прохода в группе деталей, нахождения минимального холостого прохода среди групп деталей, нахождения минимального холостого прохода при вырезке внутренних отверстий деталей и деталей, находящихся в отверстиях, объединения контуров нескольких деталей в один контур непрерывного реза.
5. На основе разработанных методик и алгоритмов, разработана и реализована подсистема САПР «Обход», позволяющая найти наикратчайший маршрут обхода деталей при лазерной резке.
6. Тестирование созданной подсистемы на основе разработанных алгоритмов показало его математическую состоятельность. Разработанная математическая модель и алгоритмы позволили сократить длину холостых проходов на 30−60% по сравнению с существующими моделями, а общее технологическое время обработки листа материала на 10−15%. Длина реза деталей при совмещенных сторонах сокращается на 10−30%.
7. Разработанная подсистема САПР «Обход» внедрена на ФГУП ЦНИИ КМ «Прометей.
Список литературы
- Автоматизация группирования деталей механообрабатывающего производства / Бордня Ю. С., Рыбак Н. Т., Огнев Ю. Ф., Муравьев М. В., Чикризов С. В. и др. // Авиац. пром-ть — 1992. — № 1. — С.24−26.
- Автоматизированная подготовка программ для станков с ЧПУ: Справочник / Р. А. Сафраган, Г. В. Евгеньев, А. Л. Дерябин и др.- Под общ. ред. Р. Э. Сафрагана. Киев: Техника, 1986 — 191 с.
- Автоматизированная система проектирования маршрута обработки отверстий на станках с ЧПУ / Юнаш Э. Л. // Прогрес. технол. чистов. и отдел, обрзб. // Челяб. гос. техн: ун-т. Челябинск, -1991. — С.101−103. ,
- Автоматизированный расчет эффективных: режимов резания на ПЭВМ / Белоусов А. И. // Пути повыш. эффект, использ. реж. инстр.: Тез. докл. 3 Всес. научн.-техн. совещ. Москва, 15−17 окт., 1991. — М.: 1991. — С.18−19.
- Алгоритмы оптимизации проектных решений. /Под ред. Половинкина А.И./. М.: Энергия. 1976. 184с.
- Анисимов В.И. и др. Учебно-исследовательская система автоматизированного проектирования радиоэлектронных схем. Л., 1989. 256с.
- Бабаев Ф.В. Оптимальный раскрой материалов с помощью ЭВМ. М.: Машиностроение, 1982. 167с.
- Байков В.Д., Ваткевич С. Н. Решение траекторных задач в микропроцессорных системах ЧПУ / Под. ред.
- B.Б.Смолова Л. Машиностроение, Ленингр. отд-ние, 1986. — 106 с.
- Ю.Балоптин Ю. А., Крылов К. И., Шарлай С. Ф. Применение ЭВМ при разработке лазеров. Л.: Машиностроение, Ленингр. отд-ние. 1989.235с.
- Батищев Д.И. Поисковые методы оптимального проектирования. М.: Советское радио. 1975. 216с.
- Батищев Д.И. Методы оптимального проектирования. М. Радио и связь, 1984. 248с.
- Болтов В.П. Геометрический и программный комплекс интерактивно-графического программирования в САПР. Докторская диссертация, ДВГМА, Владивосток. 1999.
- Борушек С.С., Волков А. А., Ефимова М. М. и др. Единая система конструкторской документации: справочное пособие. М.: Издательство стандартов, 1989, 352с.
- Бронштейн И.Н., Семендяев К. А. Справочник по математике. М.: Наука, 1965. — 608с.
- Вахвалов В.А. САПР программ для станков с ЧПУ // Механизация и автоматизация производства. 1984. — № 5.1. C.10−12.
- Веденов А.А., Гладуш Г. Г. Физические процессы при лазерной обработке материалов. М.: Энергоатомиздат. 1985. 205с.
- Вермишев Ю.Х. Методы автоматизированного поиска решений при проектировании сложных технических систем. М.: Радио и связь. 1982. 152с.
- Ветко А.Н., Калинин В. В., Хрусталева Л. В., Корьячев А. Н., Прохоров А. Ф. Кодирование конструктивно-технологических параметров корпусных деталей в САПР технологических систем / Вестник машиностроения. 1984. — № 10. — С.51−54.
- Выгодский М.Я. Справочник по высшей математике. М.: Наука, 1964. — 872 с.
- Геминтерн В.И., Каган Б. М. Методы оптимального проектирования. М.: Энергия, 1980. 213с.
- Гжиров Р.Н. Краткий справочник конструктора. Л.: Машиностроение. Ленинградское отд-е, 1983, 464с.
- Гильман A.M., Егоров Ю. Б. Разработка управляющих программ для станков с ЧПУ в системе автоматизациипроектирования технологических процессов // Станки и инструмент. 1990. — № 12. — С.14−16.
- Горанский Г. К., Бендерова Э. И. Технологическое проектирование в комплексных автоматизированных системах подготовки производства. М.: Машиностроение. 1981. 455с.
- Григорьянц А.Г., Соколов А. А. Лазерная резка металлов. М.: Высшая школа. 1988. 126с.
- Дьяконов В.П. Математическая система Maple V R3/R4/R5. М.: Солон. 1998. 398с.
- Дьяконов В.П., Абраменкова И.В. Mathcad 8 PRO в математике, физике и Internet. М.: «Нолидж». 2000. 491с.
- Дмитревич Г. Д., Анисимов В. И. Виртуальная вычислительная машина для автоматизированного проектирования: (опыт разработки и развитие). JL: ЛДНТП. 1990. 23с.
- Канторович Л.В., Залгаллер В. А. Рациональный раскрой промышленных материалов. Изд. 2-е, испр. и доп., Новосибирск: Наука, 1971. 299с.
- Капустин Н.М., Гайгал И. В. Проектирование оптимального технологического процесса обработки основных отверстий на обрабатывающем центре // Изв. вузов. Машиностроение. 1975. — № 4. — С.169−173.
- Кеннон С. Р. Дуликарвич Дж.С. Построение сеток с помощью оптимизационного метода. М.: Мир. Аэро/космическая техника. № 1, 1987. с 107−112.
- Корсаков B.C., Капустин Н. М., Темпельгоф К.-Х., Лихтенберг X. Автоматизация проектированиятехнологических процессов в машиностроении. М.: Машиностроение. 1985. 303с.
- Корчак С.А., Кошин А. А., Ракович А. Г., Синицын Б. И. САПР технологических процессов, приспособлений и режущих инструментов. М.:Машиностроение, 1988, 399с.
- Корячко В.П., Курейчик В. М., Норенков И. П. Теоретические основы САПР. М.: Энергоиздат .1987. 397с.
- Кривомазов Д.В., Шалаев П. А. Стандартизация в области систем автоматизированного проектирования изделий и технологических процессов в машиностроении.-М.: Изд-во стандартов, 1987, 324с.
- Кузнецов Ю.Н., Кузубов В. И., Волощенко А. Б. Математическое программирование. М.: Высшая школа. 1976. 351с.
- Лакирев С.Г. Обработка отверстий. Справочник. -М.: Машиностроение, 1984. 208 с.
- Макарчук Н.В. Алгоритм поиска минимальной длины прохода лазерного луча при резке листового материала. /Сборник тезисов докладов научной сессии аспирантов. СПб: СПГУАП, 2002, с.41−44.
- Макарчук Н.В. Оптимизация холостых проходов при лазерной резке листового материала. /Сборник тезисов докладов научной сессии аспирантов. СПб: СПГУАП, 2003, с.48−51.
- Макарчук Н.В. Постановка и анализ задачи оптимального обхода деталей при лазерной резке. /Сборник тезисов докладов научной сессии аспирантов. СПб: СПГУАП, 2000, с. 29−31.
- Макарчук Н.В., Макарчук А. В. Разработка оптимальных методов раскроя листового материала при лазерной резке. /Сборник тезисов докладов конференции «Гагаринские научные чтения». М., 2000, с. 25−26.
- Макарчук Н.В., Макарчук А. В. Разработка оптимальных методов раскроя листового материала при лазерной резке. /Сборник тезисов докладов конференции «Техническая кибернетика, радиоэлектроника и системы управления».г. Екатеринбург, 2000, с. 32−34.
- Макарчук Н.В., Макарчук А. В., Пиль Э. А. «Компьютерная программа оптимизации холостых проходов и раскроя при лазерной резке листового материала», Приборы и системы. Управление, контроль, диагностика, 2003, № 10, с. 25−26.
- Makarch.uk N.V. Algorithm of optimal cut for laser cutting. /"IEHS'02″, Instrumentation in ecology and human safety. St. Peterburg 2002, p.183−185.
- Михайлов-Тепляков В.А., Богданов М. П. Автоматизированная лазерная резка материалов. Л.: Машиностроение. 1976. 208с.
- Мартынов В.В., Валиуллин A.M. Алгоритм нахождения областей допустимых размещений плоских геометрических объектов в произвольных областях. /Принятие решений в условиях неопределенности. Межвуз. научн. сб. Уфа. УГАТУ, 2000. С.126−135.
- Мартынов В.В., Валиуллин A.M. Реализация алгоритма нахождения области допустимых геометрических объектов на базе суммы Минковского. /Принятие решений вусловиях неопределенности. Межвуз. научн. сб. Уфа: УГАТУ, 1999. С.183−192.
- Мартынов В.В. Использование операций Минковского при анализе взаимного расположения геометрических объектов. /Принятие решений в условиях неопределенности. Межвуз. научн. сб. Уфа. УГАТУ, 1999. С.167−174.
- Мартынов В.В., Валиуллин A.M. Регулярное размещение двумерных геометрических объектов сложной формы. / Электронный журнал «Прикладная геометрия», вып. 3, № 4, 2001, с.9−20.
- Мухачева Э.А. Рациональный раскрой промышленных материалов. М.: Машиностроение, 1984. 175с.
- Машиностроение: справочное пособие. М.: издательство стандартов, 1989. 429с.
- Никитенко В.Д. Подготовка программ для станков с числовым программным управлением. М.: Машиностроение, 1973, — 240 с.
- Норенков И.П. Введение в автоматизированное проектирование технических устройств и систем. М.: Высшая школа, 1986. — 308с.
- Норенков И.П. и др. Системы автоматизированного проектирования. -М.:Мир, 1985. 368с.
- Норенков И.П., Маничев В. Б. Основы теории и проектирования САПР. М.: Высшая школа. 1990. 335с.
- Нуждин В.Н. Системы автоматизированного обучения и проектирования./Межвузовский сборник научных трудов, Иваново: ИВГУ. 1989. 159с.
- Оптимизация холостых ходов при обработке деталей на станках с ЧПУ / Антонов М. Н. // Радиопромышленность 1991. -№ 9. — С.3−4.
- Павлов В.В. Математическое обеспечение САПР. М. МФТИ, 1978. 66с.
- Петренко А.И. Основы автоматизации проектирования. Киев: Техшка. 1982. 293с.
- Петренко А. И. Семенков О.И. Основы построения систем автоматизированного проектирования. Изд. второе, стереотипное. Киев: «Вища школа». 1985. 293с.
- Пиль Э.А. Автоматизированная система выбора последовательности обработки отверстий на станках с ЧПУ // Автоматизация и современная технология. 1992. № 7, -С.19.
- Пиль Э.А. Выбор порядка обработки отверстий на станках с ЧПУ с помощью персональной ЭВМ // Станки и инструмент. 1991. — № 11. — С.35−36.
- Пиль Э.А. Методика кодирования плоских корпусных деталей // Автоматизированное проектирование в машиностроении: Мат-лы научн.-техн. конф. Устинов, Межвуз. типогр., 29−31 окт., 1985, — С. 33.
- Пиль Э.А. Обработка групп отверстий в плоских корпусных деталях на обрабатывающих центрах // Изв. ВУЗов. Приборостроение. 1990. — № 7, — С.94−96.
- Плотко В.Н., Цымбал Г. Я. Проектирование траектории движения инструмента для обрабатывающих центров сверлильно-фрезерно-расточного типа // Автоматизация процессов проектирования. Минск: Мат-лы техн. кибернетики АН БССР. — 1983, вып. 2 — С. 46−58:
- Прасов Г. JI., Цукерман Б. К., Чудаков А. Д. Система автоматизированной подготовки управляющих программ для станков с ЧПУ ТЕХТРАН СМ-1 // Технология автомобилестроения. 1983.- № 5. С.6−11.
- Принс М.Д. Машинная графика и автоматизация проектирования. М.: Советское радио, 1975. 232с.
- Пронин М.М., Старцев В. Н., Попов В. О. и др. Лазерная обработка материалов, перспективные технологии и оборудование. /Вопросы материаловедения, СПб. № 3(20)г 1999. с.375−393.
- Рациональный раскрой материалов с использованием ЭВМ и математических методов. Всесоюзный семинар. Тезисы докладов. М.: ГВЦ Госснаб СССР. 1976, 100с.
- Рыкалин Н.Н., Углов А. А., Кокора А. Н. Лазерная обработка материалов. М.: Машиностороение, 1975. 296с.
- Сикора Е. Оптимизация процессов обработки резанием с применением вычислительных машин. М.: Машиностроение, 1983. — 232 с.
- Системы автоматизированного проектирования: в в 9 книгах /под ред. Норенкова И. П. М.1986.
- Системы автоматизированного проектирования/ пер. с англ. Под ред. Попкова Ю. С. М.:Наука, 1985, 376с.
- Система автоматизированного проектирования управляющих программ для станков с ЧПУ. Техтран. Версия 4.4. Раскрой листового материала. НИП-Информатика. 1993−2002. 180с.
- Соломенцев Ю.М., Митрофанов В. Г., Прохоров А. Ф. и др. Автоматизированное проектирование и производство в машиностроении. М. Машиностроение, 1986. 256е.
- Сольницев Р.И., Кане М. А. Основы САПР. -Л.: ЛИАП 1987, — 52с.
- Сольнндев Р.И. Автоматизация проектирования систем автоматического управления. М.: Высшая школа. 1991. 335с.
- Сольницев Р.И., Андронов В. Н. Основы математического обеспечения САПР. Л.:ЛИАЛ, 1988. -101с.
- Старостин В.Г.^ Лелгохин В. Е. Формализация проектирования процессов обработки резанием. М.: Машиностроение, 1986. — 136 с.
- Тихомиров А.В. Технология и машины для газолазерной резки металлов и неметаллических материалов. ЦИНТИхимнефтемаш. М.1982, 40с.
- Потемкин В.Г. Система инженерных и научных расчетов MATLAB 5.x в 2 томах.М.: Диалог-МИФИ. 1999.
- Техтран система программирования оборудованием с ЧПУ/ А. А. Лиферов, О. Ю. Батунер, М. Ю. Блюдзе и др. -Л.: Машиностроение, Ленингр. отд-ние, 1987. — 109 с.
- Химмельблау Д. Прикладное математическое программирование. М.: Мир. 1975. 510с.
- Холзнер С. Visual С++6. СПб.: Питер. 2000. 570с.
- Холмогорцев Ю.П. Оптимизация процессов обработки отверстий. М.: Машиностроение, 1984. — 184 с.
- Цветков В.Д. Система автоматизированного проектирования технических процессов. М.: Машиностроение. 1972. 240с.
- ЭВМ в проектировании и производстве: сб. статей,-вып.2 / под общ. Ред. Орловского Г. В. М.: Машиностроение, 1985, 295с.
- Heckmann R., Lengauer Т. Computing closely matching upper and lower bounds on textile nesting problems./ European Journal of Operational Research. 1998. № 108. F 473−489.
- Li Z., Milenkovic V.J. Compaction and Separation Algorithms for Non-convex Polygons and Their Applications./ European Journal of Operational Research. 1995. № 84. P 539 561.
- Martynov V. Geometrical objects regular placement onto a stock sheet or strip./ Pesquisa Operacional, Vol. 19, № 2.-SP-BRASIL., Instituto Nacionale de Pesquisas Espacials, dezembro de 1999. 12 (211−222).
- Stoyan Yu., Pankratov A.V. Regular packing of congruent polygons on the restangular sheet. / European Journal of Operational Research. 1999. № 113. P 653−675.