Технология сварки углеродистых и низкоуглеродистых низколегированных конструкционных сталей
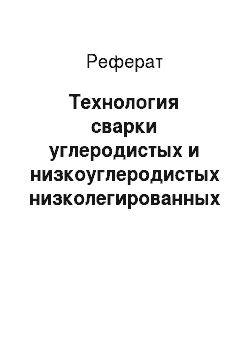
Стали обыкновенного качества поставляют без термообработки в горячекатаном состоянии. По степени раскисления различают три группы сталей обыкновенного качества: кипящие (кп), полуспокойныс (пс) и спокойные (сп). Кипящую сталь, содержащую не более 0,07% Si, получают при неполном раскислении металла. Сталь характеризуется резко выраженной неравномерностью распределения серы и фосфора по толщине… Читать ещё >
Технология сварки углеродистых и низкоуглеродистых низколегированных конструкционных сталей (реферат, курсовая, диплом, контрольная)
Состав и свойства сталей, основные сведения о свариваемости
Углеродистыми конструкционными (машиноподелочными, или строительными) называют стали, в которых содержание углерода находится в пределах 0,08…0,7%, а количество постоянных примесей не превышает (по верхнему пределу) 0,8% Мп; 0,35% Si; 0,04% Р; 0,05% S; 0,05% СЬ. Помимо постоянных примесей в металле могут находиться в небольшом количестве случайные примеси, попадающие в сталь из шихтовых материалов или из скрапа.
Углерод является основным легирующим элементом в углеродистых конструкционных сталях и определяет их механические свойства. Повышение его содержания усложняет технологию сварки и затрудняет получение равнопрочного сварного соединения без дефектов.
Углеродистые конструкционные стали классифицируют по способу изготовления, по качеству и степени раскисления стали. По качественному признаку их разделяют на две группы: обыкновенного качества и качественные.
Стали обыкновенного качества поставляют без термообработки в горячекатаном состоянии. По степени раскисления различают три группы сталей обыкновенного качества: кипящие (кп), полуспокойныс (пс) и спокойные (сп). Кипящую сталь, содержащую не более 0,07% Si, получают при неполном раскислении металла. Сталь характеризуется резко выраженной неравномерностью распределения серы и фосфора по толщине проката. Местная повышенная концентрация серы может привести к образованию кристаллизационных трещин в шве и околошовной зоне. Кипящая сталь склонна к старению в околошовной зоне и переходу в хрупкое состояние при отрицательных температурах. В спокойной стали, содержащей нс менее 0,12% Si, распределение серы и фосфора более равномерно. Эти стали менее склонны к старению. Полуспокойная сталь занимает промежуточное положение между кипящей и спокойной сталью.
В сварочной технике в зависимости от содержания углерода конструкционные углеродистые стали условно разделяют на низко-, среднеи высокоуглсродистыс. К низкоуглеродистым относят стали, содержащие до 0,25% С, к среднеуглеродистым — 0,26…0,45% С, к.
высокоуглеродистым — 0,46…0,75% С. Последние отличаются плохой свариваемостью и их практически не применяют для изготовления сварных конструкций. Температурная область применения углеродистых сталей от -40 до +425 °С, низколегированных от -70 до +475 °С.
В зависимости от назначения в соответствии с ГОСТ 380–94 стали обыкновенного качества поставляют по трем группам: А — по механическим свойствам; Бхимическому составу; Вмеханическим свойствам и химическому составу. Сталь группы, А для производства сварных конструкций не используют, а сталь группы Б находит ограниченное применение. Как правило, для сварных конструкций применяют сталь группы В всех степеней раскисления. Перед обозначением марок сталей группы Б и В указывают их группу, например БСтЗпс, ВСтЗсп.
Углеродистую качественную сталь (марки 10, 15, 20 и др.) поставляют в соответствии с ГОСТ 1050–88 и 4543−71. Она содержит пониженное количество серы. Стали этой группы применяют для изготовления консгрукций в горячекатаном состоянии и в меньшем объеме после нормализации или закалки с отпуском.
К легированным сталям относится широкая номенклатура конструкционных сталей, в состав которых входят легирующие элементы, отсутствующие в углеродистых сталях, или те же марганец и кремний, но в повышенном количестве. Легирующие элементы, вводимые в сталь, вступая во взаимодействие с железом и углеродом, изменяют ее свойства. Это повышает механические свойства стали и, в частности, снижает порог хладноломкости. В результате появляется возможность снизить массу конструкции.
Легированные стали классифицируются по следующим основным признакам: химическому составу, структуре, свойствам и назначению. По химическому составу их разделяют на гри группы: низко-, среднеи высоколегированные. По структуре, полученной при охлаждении на воздухе после нагрева до 920 °C, легированные стали бывают ферритноперлитными, перлитными, бейнитными, мартенситными, ферритными и аустенитными. По свойствам они подразделяются: на стали нормальной и повышенной прочности, хладостойкие, теплоустойчивые, коррозионно-стойкие и другие. По назначению легированные стали классифицируются на две основные группы: строительные, применяемые для изготовления сварных конструкций, и машиностроительные, предназначенные, главным образом, для производства деталей машин и механизмов, корпусных и других конструкций.
Свариваемость низкоуглеродистых сталей. Низкоуглеродистые нелегированные стали имеют достаточно хороший комплекс свойств, позволяющий при сварке получать равнопрочные основному металлу сварные соединения. Их применяют при изготовлении металлических строительных конструкций, корпусов судов, конструкций нефтяной и газовой промышленности и т. д. Эти стали малочувствительны к скорости охлаждения и практически не закаливаются с получением мартенситной структуры. Поэтому в условиях сварочных скоростей охлаждения их свойства по сравнению с горячекатаным состоянием изменяются незначительно. В зонах теплового влияния сварных соединений ощутимого повышения твердости не наблюдается. Как правило, твердость зоны термического влияния у низкоуглеродистых нелегированных сталей не превышает 180 НВ.
Склонность к образованию горячих и холодных трещин у этих сталей практически отсутствует. Поэтому изделия из указанных сталей свариваются без осложнений различными методами сварки как при малых, так и при больших значениях погонной энергии. Лишь при сварке изделий больших толщин (35…40 мм и больше), особенно в условиях низких температур (ниже -10 °С), в связи с увеличением уровня сварочных напряжений прилегающие к свариваемым кромкам участки рекомендуется подогреть до температуры 100 °C.
Свойства сварных соединений низкоуглсродистых нелегированных сталей в основном определяются степенью огрубления сгруктуры металла околошовной зоны и шва. Металл шва при обычных для сварки скоростях охлаждения, как правило, имеет крупнозернистую ферритноперлитную или сорбитообразную структуру. В наибольшей степени круинозернистость структуры металла шва проявляется при электрошлакой сварке, меньше при газовой сварке и еще меньше при дуговых способах сварки.
Зона термического влияния при сварке низкоуглсродистых сталей может быть охарактеризована в связи с диаграммой состояния Fe-C и кинетическими зависимостями распада аустенита при охлаждении. Схема сгроения зоны термического влияния сварного соединения и ее структурные участки на низкоуглсродистых сталях при дуговой однослойной сварке приведены на рис. 1.
На участке неполного расплавления (зона сплавления) металл надевается в интервале температур между линиями солидуса и ликвидуса, что приводит к частичному оплавлению зерен металла, облегчающему развитие крупного зерна. Этот интервал температур у низкоуглеродистых сталей невелик (около 30…40°С). Поэтому зона сплавления представляет собой узкую полоску металла, шириной 0,08…0,10 мм при дуговой сварке и около 0,15…0,20 мм при электрошлаковой и газовой методах сварки. В процессе взаимодействия оплавленных зерен основного металла с расплавленным металлом сварочной ванны развивается ликвационный процесс диффузионного перераспределения примесей и происходит непосредственное сращивание кристаллов шва с зерном основного металла. Свойства этого участка зачастую определяют качество сварного соединения. Структура ферритно-перлитная с окантовкой перлитных выделений ферритными прослойками.

Рис. 1. Схема строения зоны термического влияния сварного соединения при дуговой сварке низкоуглеродистых сталей
На участке перегрева металл нагревается в интервале максимальных температур от 1100… 1150 °C до температур линии солидуса. В этих условиях зерно аустенита успевает сильно вырасти, а последующая перекристаллизация при охлаждении нс даст его заметного измельчения. Феррит окружает укрупненные перлитные зерна своеобразной каймой, причем иногда здесь вследствие перегрева после охлаждения образуется неблагоприятная видманштеттовая структура, способствующая охрупчиванию металла. Металл участка перегрева вследствие крупнозернистого сгроения характеризуется ухудшенными механическими свойствами (прочностью, пластичностью). Поэтому чем меньше этот участок, тем выше качество сварного соединения.
На участке нормализации металл нагревается от температуры точки Асз до температуры 1150 °C. В этом интервале максимальных температур зерно аустенита вырасти не успевает. Поэтому последующая перекристаллизация металла при охлаждении приводит к образованию мелкозернистой ферритно-перлитной структуры с высокими механическими свойствами.
На участке неполной перекристаллизации металл нагревается до максимальных температур между точками Ас и Лс3, поэтому данный участок характеризуется почти неизменившимися исходными зернами феррита, не прошедшими перекристаллизацию, и расположенными вокруг них колониями мелких зерен феррита и перлита, образовавшихся в результате перекристаллизации. Механические свойства этого участка хуже, чем свойства участка нормализации.
Участок рекристаллизации наблюдается при сварке металла, подвергшегося до сварки холодной обработке давлением (холодной прокатке, гибке, штамповке и т. д.). При нагреве такого металла в интервале максимальных температур от 500…550 °С до температуры точки Ас в нем происходят процессы рекристаллизации, которые могут несколько снизить механические свойства металла этого участка вследствие разупрочнения из-за снятия наклепа. Если свариваемая сталь до сварки не подвергалась пластической деформации (горячекатаная или отожженная сталь), то на этом участке никаких структурных изменений не происходит.
При нагреве металла от 100 до 500 °С (участок возврата и старения) его структура в процессе сварки не претерпевает видимых изменений. Однако на этом участке может иметь место снижение пластичности, главным образом ударной вязкости, вызванное процессами старения металла. У некоторых сталей, содержащих повышенное количество кислорода и азота (обычно кипящих), на1рев до температуры 150…350 °С сопровождается резким снижением ударной вязкости и сопротивляемости разрушению.
Ширина различных участков зоны термического влияния определяется способом и режимом сварки и в некоторой степени зависит от толщины свариваемого металла.
Свариваемость низкоуглеродистых низколегированных сталей. Эти стали применяются в различных конструкциях взамен углеродистых, обеспечивая снижение металлоемкости на 20…50%. Они широко используются в строительстве трубопроводов, конструкций газонефтсхимических производств, судов, мостов и других сооружений. Поставляют их преимущественно в горячекатаном виде.
Содержание углерода в низколегированных сталях не превышает 0,23%. В зависимости от легирующих элементов, суммарное содержание которых в составе стали не превышает 4,0%, различают марганцовистые, кремнемарганцовистые, хромокремнемарганцовистые и другие стали. Легирующие элементы растворяются в феррите, упрочняют его и измельчают перлит. Благодаря этому прочностные характеристики повышаются и предел прочности достигает величины 550 МПа. Наличие повышенного содержания марганца в этих сталях повышает ударную вязкость и хладноломкость, обеспечивая удовлетворительную свариваемость.
Введение
в низколегированные стали небольшого количества меди (0,3…0,4%) повышает стойкость стали против атмосферной коррозии и коррозии в морской воде.
По своей свариваемости стали этой группы мало отличаются от нелегированных низкоуглеродистых сталей. Аналогичны им по свариваемости стали низколегированные марок 09Г2 и 09Г2С. Повышенное содержание марганца в этих сталях снижает критическую скорость охлаждения, однако пониженное содержание углерода в них предопределяет практически отсутствие появления закалочных структур при сварке.
Несколько иначе ведут себя при сварке стали 10Г2С1, 10ХСНД, 15ХСНД, 17ГС и им аналогичные. У этих сталей при высоких скоростях охлаждения в околошовной зоне могут появиться неравновесные структуры закалочного характера. Поэтому рассматриваемая группа низколегированных сталей требует ограничений условий ведения сварочного процесса. Сварку таких сталей лучше выполнять либо при повышенных значениях погонной энергии без подогрева, либо с небольшим подогревом при умеренных значениях погонной энергии. Указанные ограничения по условиям сварки касаются в основном металла, толщиной более 25…30 мм. При малых толщинах, даже если в околошовной зоне образуется мартенсит, то его количество настолько мало, что влияния на свойства металла практически не оказывает. Твердость участков зоны термического влияния сварных соединений этих сталей нс превышает 220 НВ.
Большего внимания требует сварка низколегированных сталей с карбонигридным упрочнением (например, марок 14Г2АФ, 16Г2АФ, 18Г2АФ и др.). Принцип легирования этих сталей и создания в них повышенной прочности и вязкости основан на образовании дисперсной упрочняющей фазы на базе имеющихся в стали микролегирующих элементов (V, Nb, N, Ti и др.) и получении очень мелкого зерна за счет ограничивающих его рост нс растворяющихся при нагреве нитридов и карбонитридов. Последние служат также центрами превращения во время перекристаллизации при охлаждении. Упрочняющая дисперсная карбонитридная или нитридная фаза выделяется и упрочняет феррит в процессе охлаждения, повышая прочность металла, а получение мелкого зерна (балл 10… 12) способствует повышению его вязкости и хладостойкости.
Условия обеспечения высокой прочности и вязкости гребуют сохранения упрочняющей фазы в дисперсном состоянии и сохранения мелкого зерна. Повышение погонной энергии при сварке и соогветственно увеличение времени пребывания металла околошовной зоны при высоких температурах в принципе может привести к коагуляции и растворению дисперсной фазы, а также к росту зерна. Вследствие этого свойства стали в этой зоне будут ухудшаться. Поэтому сварку сталей с карбонитридным упрочнением и мелким зерном целесообразно проводить при умеренных погонных энергиях. При этом наиболее приемлемыми способами сварки этих сталей являются дуговая сварка в защитных газах и ручная дуговая сварка покрытыми электродами, позволяющими обеспечивать малое тепловое воздействие на зону термического влияния.
Стремление к снижению металлоемкости конструкций и изделий привело к использованию низколегированных сталей в термически улучшенном состоянии — после закалки и высокого отпуска при температурах 550…670 °С. В таком состоянии применяют, например, стали 10ХСНД, 17ГС, 16Г2АФ и др., для которых наряду с высокой прочностью характерны достаточная пластичность, вязкость, повышенное сопротивление хрупким разрушениям и др. Сварка таких сталей осложняется тем, что на тех участках зоны термического влияния, где максимальная температура нагрева лежит в пределах 500 °С…Лс3, происходит некоторое разупрочнение металла, сопровождаемое провалом твердости. Степень этого разупрочнения тем больше, чем выше прочность закаленной и отпущенной стали и чем больше погонная энергия при сварке. Поэтому сварку термически улучшенных низколегированных сталей предпочтительно выполнять с малым временем пребывания металла при высоких температурах. Это легко обеспечивается применением умеренных погонных энергий при дуговой сварке в защитных газах, а также ручной дуговой сварке покрытыми электродами.
В некоторых случаях рациональным способом обеспечения однородных свойств сварных соединений термически улучшенных низколегированных сталей может быть их термообработка после сварки, причем такая же, какой подвергалась сталь перед сваркой. Такой термообработке могут подвергаться сварные изделия целиком, если размеры их невелики и нет опасений больших короблений. В этом случае термообработка устраняет нс только разупрочнение металла, но и повышенную твердость и хрупкость упрочненных зон, нагревавшихся при сварке выше температуры точки Лс3, а также существенно снижает уровень остаточных сварочных напряжений.