ВЗУ для очистки газов от газового конденсата
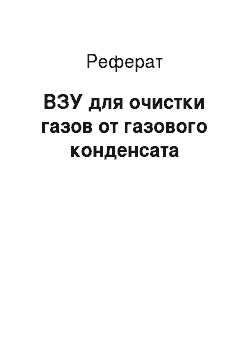
Предварительные расчеты аппаратов основывались на расчетах вихревых труб для газов и труб, работающих на двухфазных потоках, в которых при увеличении концентрации жидкости от 0,1 до 1,5% резко снижалась разность температур охлаждения tx и температур нагревания Тг, поскольку для В3У, работающих на двухфазных потоках с более высоким содержанием жидкости, данные отсутствуют. Расчет вихревого… Читать ещё >
ВЗУ для очистки газов от газового конденсата (реферат, курсовая, диплом, контрольная)
Основными геометрическими параметрами ВЗУ, влияющими на процесс дегазации, являются: угол ввода и вывода жидкостного потока, величина относительной площади винтовых нарезок, их конфигурация и количество каналов на единицу длины. На рис. 2 приведена схема предварительного закручивающего устройства.
Экспериментально были определены размеры предварительного винтового закручивающего устройства, которые приведены в таблице3. 1.
Видно, что с увеличением диаметра ВЗУ уменьшается отношение оптимальных значений хода винтового канала к его глубине.

Рис. 3.2. Схема камеры предварительной закрутки
Таблица 3.1 Геометрические размеры ВЗУ
Э, мм. | ||||
S, мм. | ||||
А, мм. | ||||
S/А. | 0,4. | 1,42. | 1,6. | 2,0. |
Было установлено, что угол раскрытия диффузора варьируется в пределах от 22 до 56 угловых градусов.
На рис. 3.3 приведены графики расхода газожидкостного потока в зависимости от входного давления при различных значениях углов расположения предварительно завихряюших каналов.
В настоящее время добываемый газ в своем составе содержит от 1,6 до 5 г/м3 стабильного конденсата, от 100 до 500 г парообразной влаги на 1000 м газа и до 1.65 г на 100 м сероводорода. Эти показатели не соответствуют требованиям ОСТ 51 40−74 «Газы горючие природные, подаваемые в магистральный газопровод»:
- — температура точки россы -10°Сs- -20°С;
- — механические примеси не более 3 г на 100 м³ газа;
- — содержание сероводорода не более 2 г на 100 м³ газа.
Следовательно, для приведения качественных показателей добываемого газа в соответствие с требовании НТД необходимо произвести осушку его от влаги, извлечь конденсат и понизить температуру точки росы до требуемого уровня.
Внедрение технологий низкотемпературной подготовки газа в системе сбора газовых месторождений обеспечило рациональное использование энергии газового пласта. Позволило снизить опасность разгерметизации промысловых газопроводов и достичь более глубокого извлечения жидкого конденсата без использования специальных технологий и реагентов. Однако предложенный способ подготовки газа требует больших капитальных затрат и высокие энергетические затраты при эксплуатации. Для повышения эффективности разделения конденсата от газа нами предлагается использовать вихревое устройство, приведенное на рис3.4.
ВЗУ для очистки газов от газового конденсата содержит кожух 1, в котором концентрично с образованием межтрубного кольцевого пространства 2 установлена вихревая труба 3 с камерой горячего потока 4 и энергоразделителем, выполненным в виде входных тангенциальных сопел 5 в стенке вихревой трубы 3, со стороны входного торца трубы 3, и диафрагменного диска 6, перекрывающего выходной торец кожуха 1 и входной торец вихревой трубы 3. Диск 6 энергоразделителя выполнен со сквозным осевым каналом 7, связывающим камеру 4 горячего потока с камерой 8 холодного потока.
Для отвода конденсата в диске 6 выполнены профилированные радиальные каналы 9, связывающие межтрубное пространство 2 с емкостью 10 для сбора конденсата.
На другом конце вихревой трубы 3 в ее стенке проведены выходные тангенциальные сопла 11, связывающие камеру 4 горячего потока с межтрубным кольцевым пространством 2, а выходной торец вихревой трубы 3 перекрыт эжектором 12; по наружной поверхности вихревой трубы 3 выполнено оребрение 13. Очищаемый газ поступает в устройство через патрубок 14 ввода, а через патрубок 15 отводится очищенный газ.
Эффективность в предлагаемом вихревом аппарате достигается тем, что в качестве абсорбента используется собственный газовый конденсат. Перед разделением абсорбента на два потока его предварительно завихряют, а последующее завихрение одного из потоков абсорбента производят в вихревой трубе с одновременной конденсацией абсорбента в ней, при этом в вихревой трубе поддерживают пресыщение, степень которого М определяется из выражения.
M = (P1 — P2)KC (t / 2nRT)),.
где Р1 и Р2 — давление входящего потока и отводящего потока газа;
К — экспериментальный коэффициент;
С — площадь отверстий выхода абсорбента;
т — молярный объем абсорбента в поле контакта с газом;
R — универсальная газовая постоянная;
Т — абсолютная температура газа на периферии в вихревой трубе;
После дросселирования газожидкостной смеси абсорбент подают на абсорбцию.
Благодаря тому, что в качестве абсорбента используется собственный газовый конденсат, появляется возможность обеспечения очистки газа без введения дополнительного химического абсорбента и процесса его регенерации, что существенно снижает затраты на осуществление процесса очистки.
Получение собственного газового конденсата осуществляется тем, что поток газа завихряется в вихревой трубе, где поддерживается пресыщение М, величина которого определяется по формуле, приведенной выше. В результате вихревого эффекта периферийный теплый поток передает свое тепло холодному входящему очищаемому газу, конденсируется и непрерывно выводится на абсорбцию в парообразном состоянии. Такое формирование абсорбента в виде собственного газового конденсата значительно упрощает технологический процесс очистки и уменьшает цикл подготовки газа.
Выполнение на наружной поверхности вихревой трубы оребрения позволяет осуществить предварительное завихрение газового потока и абсорбента и обеспечить разделение абсорбента на два потока, один из которых отводится в виде конденсата, а другой подается через входные тангенциальные сопла в вихревую трубу, где его вновь завихряют для интенсификации процесса осушки.
Процесс образования абсорбента в виде собственного газового конденсата и абсорбционная очистка газа идут непрерывно замкнутым циклом по мере поступления в устройство газа для очистки с постоянным отводом очищенного газа и конденсата.
Разработанный аппарат успешно испытан и внедрен на Кокуйском месторождении на площадке подготовки газа. Результаты испытаний показали, что очищаемый газ с газожидкостным конденсатом и влагой имеет следующий состав, об. %:
метан — 63,4;
этан — 9,4;
пропан — 3,1;
изобутан — 0,6;
н-бутан — 0,5;
изопентан — 0,2;
н-пентан — 0,1;
кислород — 2,6;
азот — 20,1;
содержание сероводорода, вес. 6%,;
газа в количестве 27 500 нм /ч при Т = 0 °C под давлением 1,95 МПа поступает на эжектор 12. При сбросе давления вследствие дросселирования на 0,35 МПа поток газа завихряется и делится на два потока. Отсепарированный газовый конденсат, как более тяжелый, выводится с периферийной зоны потребителю. А второй поток газа вновь завихряют в вихревой трубе 3, в которой поддерживают пересыщение, степень которого М = 1,72.
Один из потоков газа, возникших вследствие вихревого эффекта в вихревой трубе 3 (рис. 3.4), делится на две зоны: теплую — периферийную и холодную — осевую. Холодный осушенный поток до Т росы = -20°С имеет следующий состав, об. %: метан -64,6; этан — 9,5; пропан — 3,1; изобутан — 0,5; н-бутан — 0,1; кислород — 2,2; азот — 20; содержание влаги по Фишеру (2) -0,061 г/м, содержание сероводорода, вес. %, отсутствует. Его в количестве 26 675 нм3 /ч при температуре 0 °C и под давлением 1,6 МПа вывели потребителю.
Газовый конденсат практически состоял только из светлых нефтяных фракций и в стабильном состоянии отвечал требованиям отраслевого стандарта ОСТ 51.65−80. Его фракционный состав по Энглеру, °С: НК-28; 5% 55; 10% 60; 20% 70; 30% 79; 40% 87; 50% 95; 60% 102; 70% 112; 80% 124; 90% 150; 95% 180; К.К. 190.43.
Газовый конденсат с отношением выход/остаток 96/2,5 в количестве 3,3 т/сутки с давлением 1,6 МПа при температуре 0 °C направляется потребителю как сырье для производства моторных топлив.
Из результатов промышленных исследований следует:
- — использование в качестве абсорбента собственного конденсата позволяет исключить использование большого количества химического реагента;
- — предельные и запредельные перепады давлений показывают высокую эффективность контакта очищаемого газа с абсорбентом в виде собственного газового конденсата, полученную благодаря предложенной степени пресыщения;
- — обеспечивается высокая степень очистки газа от газового конденсата;
- — допустимые расходы потоков газа позволяют получить дополнительное количество конденсата и вывести его потребителю;
- — появляется возможность очистить газ ниже температуры росы при исключении процесса замерзания конденсата, при этом дросселирование не приводит к выходу из строя оборудования.
Известно, что гидраты газов представляют собой твердые соединения (клатраты), в которых молекулы газа при определенных давлениях и температурах заполняют структурные пустоты кристаллической решетки, образованной молекулами воды с помощью прочной водородной связи.
Молекулы воды при образовании гидрата и сооружении полостей как бы раздвигаются молекулами газа, заключенными в эти полости. Удельный объем воды в гидратном состоянии возрастает до 1,26 — 1,32 см3/г (удельный объем воды в состоянии льда — 1,09 см3/г). Соотношение воды и газа зависит от размера молекул газа — гидратообразователя. Один объем воды в гидратном состоянии связывает в зависимости от характеристики исходного газа от 70 до 300 объемов газа.
Чем выше молекулярная масса индивидуального газа или смеси газов, тем ниже требуется давление для образования гидратов при одной и той же температуре. Экспериментально доказано, что в объеме воды при наличии центров кристаллизации активно образуются гидраты. Скорость накопления гидрата при этом определяется разницей содержания равновесного газа в воде до и после образования гидрата.
Поэтому, для прогнозирования места образования и интенсивности накопления гидратов в различных частях технологической системы транспорта газа необходимо знать влагосодержание газа и изменение его в различных термодинамических условиях.
График равновесных параметров гидратообразования построен на рис. 5.
Для предупреждения образования гидратов в потоке газов необходимо устранить хотя бы одно из основных условий существования гидратов: высокое давление, низкую температуру или влагу. В связи с этим основными методами борьбы с гидратами являются понижение давления, повышение температуры, осушка газов или ввод антигидратных ингибиторов.
Нами предлагается для предотвращения гидратообразования проводить удаление влаги (осушку) используя ВЗУ.
Для осушки газа с малым конденсатным фактором требуется удалить только часть влаги и снизить относительную влажность газа примерно на 6070%. Иными словами, нужно понизить точку росы газа до такой величины, чтобы она была на 5−7 °С ниже рабочей температуры в газопроводе, что мы и имеем после дросселирования газа на скважинах и в газопроводе внешнего транспорта газа.
Предварительные расчеты аппаратов основывались на расчетах вихревых труб для газов и труб, работающих на двухфазных потоках, в которых при увеличении концентрации жидкости от 0,1 до 1,5% резко снижалась разность температур охлаждения tx и температур нагревания Тг, поскольку для В3У, работающих на двухфазных потоках с более высоким содержанием жидкости, данные отсутствуют. Расчет вихревого аппарата проводился по методике, представленной в третьей главе.
Аппарат был смонтирован в технологическую схему по осушке газа, которая показана на рис3.6.

Рис. 3. 5. График равновесных параметров гидратообразования
На рис. 3.6 приведена технологическая схема по осушки газа с использованием ВЗУ.
Полученные результаты в ходе промышленного пробега представлены ниже. Если перед вихревым аппаратом содержание влаги в газе по Фишеру составляло 5,05% масс., то после осушки снизилось до 0,061% масс., температура росы газа достигла -20 С.
Нами рассматривается вопрос десорбции в вихревых аппаратах при регенерации моноэтаноламина (МЭА) от сероводорода для установок абсорбционной очистки газа. Приводятся результаты исследования вихревых эффектов и методика расчета вихревых аппаратов.
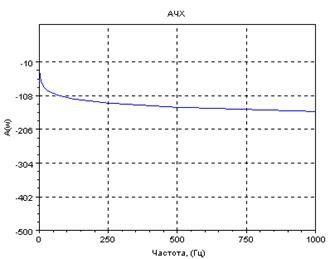
Рис. 3.6. Технологическая схема сбора и осушки газа
По характеру трансформации тепла установку абсорбционной очистки газа от сероводорода можно отнести к группе расщепительной трансформации, где абсорбция и десорбция газа абсорбентом производятся при нагреве и охлаждении, сжатии и сбросе давления.
При расщепительной трансформации к установке подводится поток тепла Qc среднего потенциала с температурой Тс, который в установке делится (расщепляется) на два потока — низкого ТН и повышенного ТВ потенциала.
Здесь в отличие от системы прямого потребления тепла необходимо осуществление двух циклов. Первый является прямым и служит для получения работы L при использовании тепла среднего потенциала Qc, подводимого на уровне ТС > ТОС .
Работа L в данном случае используется для осуществления обратного цикла, служащего для отвода тепла со среднего уровня ТС на верхний ТВ. Аналогичный результат может быть получен не только с помощью осуществления циклов, но и посредством использования разомкнутого процесса (и даже вообще без изменения состояния рабочего теплапри использовании электромагнитных явлений в развитой гидродинамической кавитации на струйных установках вихревого типа).
Примером использования системы второго вида может служить установка, принципиальная схема которой показана на рис. 3.8. К установке подводится поток газа GC при давлении РС и температуре Т<�с который орошается абсорбентом и разделяется на две части. Одна часть потока газа растворяется в абсорбенте, другая, очищенная, выводится с установки. Насыщенный абсорбент со значением расхода Gx поступает в промежуточный теплообменник, нагревается и разделяется на два газожидкостных потока. Один из потоков с расходом Gx1+H2S поступает в струйную вихревую установку и расширяется в ней при изменении давления с РС до РН. При этом в процессе расширения газожидкостного потока идет дегазация газа, вследствии, чего и температура газа понижается с ТС до ТН<�ТОС. Затем очищенный газ выводится к потребителю, а регенерированный абсорбент возвращается на аб-сорбцию с расходом СХ1 — Другая часть абсорбента с расходом GX2 +H2S поступает в десорбер и расширяется в нем при изменении давления с РС до РН. В процессе расширения и нагрева идет полная дегазация абсорбента, при этом температура абсорбента повышается с ТС до ТВ, и регенерированный абсорбент возвращается на абсорбцию через теплообменник с расходом Gx2-H2S, где отдает свое тепло насыщенному раствору и охлаждается от температуры ТВ до ТН.
Таким образом, в рассматриваемой установке в результате использования энергии давления подведенного потока газа при ТС>ТО.С. происходит разделение потока абсорбента на две части: GX1 +H2S с низкой температурой регенерации ТН и поток GX2 +H2S с повышенной температурой регенерации ТВ. Первый из них может быть использован для абсорбции как грубо регенерированный абсорбент, второй — как тонко регенерированный.

Рис. 3.8. Схема абсорбционной очистки газа

Рис. 3.7.Вихревой аппарат для регенерации МЭА
По характеру протекания процесса во времени установка относится к группе непрерывного действия, и характеристика работы меняется только в пределах, определяемых регулированием, что экономически часто может быть более выгодным из-за меньших габаритов и меньшего числа элементов оборудования благодаря возможности совмещения разных функций в одном аппарате.
Постепенное расширение области использования струйных установок вихревого типа (вихревая труба на втором потоке абсорбента с расходом GX2 +H2S), отличающихся исключительной простотой конструкции, обусловлено их преимуществом, проявляющимся там, где имеется источник сжатого газа, что исключает необходимость использования специального компрессора.
На основании вышеприведенных результатов исследований был разработан и сконструирован кавитационно-вихревой аппарат (рис. 3.7) для процесса десорбции сероводорода из раствора МЭА, который внедрен на установке по очистке газа от сероводорода. Результаты, полученные в ходе промышленных испытании, приведены в табл.3. 2.
Вихревой аппарат для регенерации раствора МЭА показал хорошую степень дегазации кислых газов (до 45%). Экономия тепловой энергии, при этом затрачиваемая на регенерацию МЭА при эксплуатации ВЗУ, снизилась на 30%. При внедрении трех и более ступеней регенерации МЭА предложенными вихревыми аппаратами возможно исключение из технологической схемы колонны — десорбера.
Таблица 3.2 Результаты промышленных испытаний
Номер образца. | Содержание сероводорода в растворе МЭА, г/л. | Температура раствора МЭА перед ВЗУ, °С. | Расход раствора МЭА, м /ч. | ||
на входе в ВЗУ (после К-1). | на выходе ВЗУ. | на выходе из К-2. | |||
22,5. | 15,3. | 12,7. | |||
32,1. | 18,7. | 16,2. | |||
28,1. | 16,0. | 14,3. | |||
25,9. | 14,2. | 12,1. | |||
26,3. | 15,0. | 11,5. | |||
28,5. | 17,0. | 12,0. | |||
27,7. | 15,5. | 10,0. | |||
27,5. | 15,4. | 10,5. |
Анализ литературы и патентных материалов указывает, что наметилась тенденция предпочтительного использования энергии потока в кавитационных вихревых аппаратах. Проведенное экспериментальное и визуальное изучение работы вихревого аппарата позволило установить следующие основные физические принципы действия аппарата:
во — первых, дегазирующие действия резкого падения давления жид;
кости в закручивающем устройстве;
во-вторых, сепарирующие действия центробежных сил при разделении газа и жидкости;
в-третьих, влияние на устойчивость работы аппарата характера течения жидкости, определяемого, в свою очередь, формой и размерами аппарата.
Разработанный кавитационно-вихревой аппарат для выделения газового конденсата и влаги из газа позволяет достичь содержания влаги по Фишеру 0,061 г/м3, что предотвращает образование гидратов.
Внедрение вихревого аппарата в процесс десорбции позволяет проводить процесс регенерации МЭА без использования аппаратов колонного типа.