Булат.
Давно ли люди гибнут за металл и как именно закалялась сталь
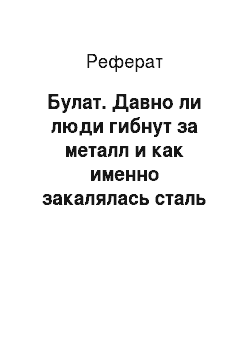
Существует четыре основных типа клинков или сталей которые называются «дамасскими» — сварные, инкрустированные, травленые и, наконец, тигельная. Это разнообразие под одним именем приводило к путанице в литературе. Сварной дамаск еще называемый механическим дамаском, поскольку делался путем кузнечной сварки нескольких составляющих железа или стали вместе для получения декоративного… Читать ещё >
Булат. Давно ли люди гибнут за металл и как именно закалялась сталь (реферат, курсовая, диплом, контрольная)
Булат — одна из самых интересных и загадочных страниц в истории металлургии. Сейчас хорошо известно, как в древние времена делали каменные топоры, бронзовую утварь, варили железо и плавили чугун, но до нашего времени остаются нераскрытыми многие секреты производства булатного оружия.
Впервые Европа познакомилась с булатом при столкновении армии Александра Македонского с войсками индийского царя Пора. Особенно поразил македонцев панцирь захваченного в плен царя. Он был сделан из необыкновенно прочного белого металла, на котором македонское оружие не смогло сделать ни вмятины, ни царапины. Из булата были изготовлены и широкие индийские мечи, которые легко рассекали пополам македонское железо. По свидетельству историков, древнее европейское железное оружие было настолько мягкое, что после двух-трех ударов уже гнулось, и воины вынуждены были отходить, чтобы выпрямить клинок. Естественно, что индийские мечи для македонцев казались чудом.
Задолго до этого с Гималайских гор в Пенджаб (древнейшее княжество в Индии) спустилась каста кузнецов, хорошо знающих железное дело и умеющих изготовлять железное оружие с необычайными свойствами. Из Пенджаба индийское железо и способы его обработки распространились в Сиам и Японию.
Вальтер Скотт в своем романе «Талисман» рассказывает о состязании в ловкости между султаном Саладином и английским королем Ричардом Львиное Сердце. Во время состязания Ричард своим мечом разрубил на две части копье одного из рыцарей — все видели высокую прочность стали и страшную силу удара короля. В ответ Саладин подбросил в воздух тонкое покрывало и рассек его своей саблей — прекрасное доказательство остроты клинка и ловкости воина. Клинок султана был булатный. Это одна из многих легенд, рассказывающая о чудесных свойствах булата.
Булат — знаменитая сталь, о которой слышали многие, даже не металлурги. Первые сведения о булате до нас дошли от участников походов Александра Македонского в Индию — 2300 лет назад. А свойствами клинки обладали действительно удивительными. Будучи твердыми и прочными, они одновременно обладали большой упругостью и вязкостью. Клинки перерубали железные гвозди и в то же время свободно сгибались в дугу. Нет ничего удивительного в том, что индийские мечи крошили европейские, которые в древности часто делались из недостаточно упругих и мягких низкоуглеродистых сортов стали.
Лезвие индийского клинка после заточки приобретало необыкновенно высокие режущие способности. Хороший клинок легко перерезал в воздухе газовый платок, в то время как даже современные клинки из самой лучшей стали могут перерезать только плотные виды шелковых тканей. Правда, и обычный стальной клинок можно закалить до твердости булата, но он будет хрупким, как стекло, и разлетится на куски при первом же ударе. Поэтому позднее, когда европейские сабли начали изготовлять из прочных и твердых сортов углеродистых сталей, они ломались при ударе индийского оружия.
Основное назначение булата — изготовление клинков. Главное достоинство клинка — острота его лезвия. Лезвие булатного клинка можно было заточить до почти неправдоподобной остроты и сохранить эту остроту надолго. У клинков из обычной углеродистой стали заостренное лезвие выкрашивается уже при заточке — как бритву, его заточить нельзя, а булат затачивали до остроты бритвы, и он сохранял свои режущие свойства после того, как побывал в деле. Такое возможно лишь тогда, когда сталь обладает одновременно высокой твердостью, вязкостью и упругостью — и в этом случае лезвие клинка способно самозатачиваться. Булатная сабля легко сгибалась на 90−120 градусов, не ломаясь. Есть сведения, будто настоящий булатный клинок носили вместо пояса, обматывая им талию. Слитки литого булата в виде разрубленных лепешек «вутцев» привозились из Индии в Сирию, где в городе Дамаске из них выковывали эти сказочные клинки. Но индийская булатная сталь стоила очень дорого, и сирийские кузнецы изобрели сварной булат, правильно определив, что булат — первый созданный человеком композит, состоит из частиц твердой углеродистой стали в матрице из мягкой и упругой низкоуглеродистой стали.
Индия была родиной булата. Отсюда в восточные страны ввозили вутцы — «хлебцы» из стали. Они имели вид плоской лепешки диаметром около 12,5 см, толщиной 0,25 см и весом около 900 гр. Каждый такой хлебец разрубался пополам на равные части, чтобы покупатель мог рассмотреть строение металла.
Индийские мастера много веков владели искусством обработки стали. Знаменитый арабский путешественник и географ Эдризи в 1154 году писал, что индусы в его время славились производством стали и ковкой мечей. За сотню лет до этого Бируни, описывая производство стали и мечей, восклицал: «Никогда не будет народа, который лучше разбирался бы в отдельных видах мечей и в их названиях, чем жители Индии!» .
И он далее рассказывает, что мечи в Индии делали разных цветов: зеленые (отполированное железо натирали раскаленным порошком медного купороса), синие, белые, цвета фиринд или фаранд («шелковая узорчатая ткань»), т. е. с узорчатым рисунком на стали, с красным полем и белыми узорами на нем.
Узоры, рисунки на металле были самой главной внешней отличительной особенностью булатных мечей. На некоторых булатах узоры были видимы невооруженным глазом сразу после полировки. На других узоры появлялись только после травления соком растений. Узор мог быть крупным или мелким.
Мастера Востока тщательно хранили секрет производства булата, передавая его из рода в род. Было несколько известных центров по изготовлению булата. Особенно славился этим сирийский город Дамаск. Там уже 1800 лет назад существовала первая крупная мастерская по изготовлению стали и производству оружия из индийского вутца. Мечи из Дамаска в средние века попадали даже в африканские племена. Название — дамасская сталь позже стала собирательным понятием булатной стали, изготовлявшейся в разных странах.
Булатные клинки ценились очень высоко во все времена. Бируни, сообщая о различных видах индийских мечей, упоминая один из них — маджли, на котором изображены животные, деревья, пишет: «Стоимость такого меча равна цене лучшего слона; если же рисунок будет изображать человека, то ценность и стоимость меча еще выше». Да и в более поздние времена, например в начале XIX в., у синдского эмира была булатная сабля, за которую он не согласился взять 900 фунтов стерлингов, что составляет, примерно, — 9000 руб. золотом!
Дамасская сталь получалась путем многократных проковок в разных направлениях пучка из стальных прутков разной твердости. Качество клинков из сварной дамасской стали было по тем временам очень высокое, но такого сочетания прочности и упругости как в оружии из литого индийского булата сирийским кузнецам добиться не удалось.
Существует четыре основных типа клинков или сталей которые называются «дамасскими» — сварные, инкрустированные, травленые и, наконец, тигельная. Это разнообразие под одним именем приводило к путанице в литературе. Сварной дамаск еще называемый механическим дамаском, поскольку делался путем кузнечной сварки нескольких составляющих железа или стали вместе для получения декоративного и функционального узора. Эта методика широко использовалась в Европе веками. Узор и декорирование с помощью инкрустации или травления часто называется искусственным дамаском. Узоры и рисунки, сделанные инкрустацией разных металлов и драгоценных камней в стальное лезвие широко распространены в оружии из России и других мест. В основном травленый рисунок на клинках использовался в Индии в IXX веке, видимо для того, что бы подделать тигельную дамасскую сталь.
И четвертая разновидность сделана из тигельной стали, иногда ее называют восточным (азиатским) Дамаском или кристаллическим Дамаском. Именно этот Дамаск и вызывал такой интерес и столько споров на протяжении столетий.
Дамасская сталь делается из тигельной стали, которую куют особым образом, в результате чего образуется рисунок. Тигельная сталь, как видно из названия, производиться в тигле — керамической форме — горшке. Сталь это железо с содержанием углерода в размере около 0.8%. В античные времена сталь производилась самыми разными способами, но тигельная выгодно отличалась тем что была жидкой в процессе производства и потому клинок получался гомогенным стальным и без остатков шлака — два свойства, которых остальные технологии были лишены.
Арабский ученый XII века Едриза сообщает, что в его время индийцы еще славились производством железа, индийской сталью и выковкой знаменитых мечей. В дамаске из этой стали изготовляли клинки, славу о которых крестоносцы разнесли по всей Европе. К сожалению, в Древней Индии так тщательно прятали секреты выплавки вутца, что, в конце концов, потеряли их совсем. Уже в конце XII века клинки из литого булата высшего качества «табан» не могли делать ни в Индии, ни в Сирии, ни в Персии.
После того как Тимур покорил Сирию и вывез оттуда всех мастеров, искусство изготовления оружия из литого булата переместилось в Самарканд; однако вскоре оно везде пришло в упадок. Потомки вывезенных мастеров, рассеявшись по всему Востоку, окончательно потеряли способы изготовления булатного оружия. В XIV — XV веках секрет производства литого булата и изготовления из него холодного оружия был окончательно потерян.
Европейские кузнецы не смогли до конца разгадать секрет производства даже дамасской сварной стали и больше преуспели в производстве клинков из однородной (гомогенной) стали с имитацией рисунка булата на поверхности клинка. Особенно широко развернулось производство подделок под булат в XVIII—XIX вв.еках. В это время в Европе научились производить высокоуглеродистую литую сталь, и западноевропейские мастера, оставив попытки раскрыть секреты производства сварочного булата, начали изготовлять из нее довольно хорошее холодное оружие. В Италии (Милан), в Испании (Толедо), в Германии (Золинген), во Франции (Льеж) и даже в Англии стали широко производить «ложный булат» .
" Ложные булаты", особенно золингеновские и толедские, приобрели известность благодаря высокой степени полировки и красивыми узорами, которые наносились на клинки различными методами. Ремесленники, рисующие декоративные узоры на металле, назывались «дамаскировщиками», а клинки «ложного булата» — «дамаскированными». Многие «дамаскированные» клинки были не очень высокого качества, поскольку они изготовлялись из обычной шведской или английской углеродистой стали.
На протяжении последних 200 лет бытовало мнение, что Дамасскую сталь делали из тигельной стали производимой в Индии, и известной как вутц. Британские торговцы и офицеры были свидетелями производства и использования этой удивительной стали в Индии. Восторженные свидетели привозили образцы ее в Британию, что бы исследовать и понять причину, почему же эта сталь так хороша. Потому устоялось мнение, что Дамаскую сталь производила Индия и Шри-Ланка (которые были частями Британской Империи) по так называемой «вутц технологии». Это смешивание железа и растительного материала — листьев, в тигле и нагревание его. Листья сгорали, производя насыщенную углеродом атмосферу, которая насыщала углеродом железо, для образования стали. Тигли обычно имели конусообразную форму и делались из обычной глины с добавкой шелухи риса. Не существует энтографических свидетельств из Южной Индии и Шри-Ланки, подтверждающих, что из вутца делались клинки с дамасским рисунком. Похоже, что вутц и дамасский узор оказались, ассоциированы друг с другом до 1820 годов и остаются ассоциированными до сих пор.
До недавнего времени многие исследователи заявляли, что знания об изготовлении дамасской стали, были «утеряны». Действительно, почему клинки вели себя таким уникальным образом, не было понятно, пока не закончилось предыдущее тысячелетие.
Не все тигельные стали способны произвести дамасский узор. Это то, что озадачивало столько много кузнецов и исследователей такое длительное время. Столетиями существовала вера в то, что качество стали, каким то образом, связано с рисунком.
Не одно столетие металлурги всех стран и народов пытались выплавить булатную сталь, но злополучная тайна никому не давалась. В XIX веке учеными-металлургами предпринималось множество попыток раскрыть секрет литого булата, даже великий английский ученый Майкл Фарадей, пытавшийся получить булат путем добавки к стали алюминия и платины, безуспешно бился над решением этой задачи.
Он и производитель мечей Вилкинсон исследовали дамасскую сталь, что бы разобраться: что делает ее острее и крепче ее ординарных европейских конкурентов. Исследования дамасской стали привели к экспериментам с добавлением разных металлов в сталь, в надежде повторить узор. Дамасского узора не получилось, но исследователи обратили внимание на то, как разные добавки в сталь меняют ее свойства — упрочняют, делают ее нержавеющей.
В результате исследования продолжались, но уже не с целью повторить дамасский узор, но изучить свойства сплавов со сталью. Таким образом, исследования дамасской стали, прямо привели к открытию и развитию легированных сталей — материалу без которого немыслима современная цивилизация, из которой делают все от миниатюрного винтика до океанского корабля. Однако как воспроизвести узор, так и осталось, не выяснено.
Но получить литой булат, не уступающий по свойствам индийскому вутцу, удалось только русскому ученому, горному начальнику златоустовских заводов П. П. Аносову в 40-ых годах XIX века. Сохранившийся до наших дней аносовский булатный клинок, перерубает гвозди, гнется в дугу и на лету перерубает газовый платок.
Секрет древних индийских мастеров открыт? И да и нет. После смерти П. П. Аносова, не смотря на оставленный им подробный рецепт, воспроизвести литой булат не удается никому!
Однако детали его исследований остаются практически неизвестными за пределами России. Аносов был в курсе исследований Фарадея и послал ему клинок собственного изготовления. Этот клинок теперь храниться в Музее Фарадея в Лондоне. Узор уже не так хорошо виден из-за возраста клинка и чистки, но все равно по тому, что видно можно заключить, что Аносов действительно изготовил клинок дамасской стали. Но, не смотря на то, что он умел повторять узор, научное объяснение этому оставалось загадкой.
Так продолжалось до начала XXI века, когда металлургическая наука, наконец, смогла найти объяснение самых известных Дамасских рисунков.
Существует две основные группы узоров дамасской стали и каждый имеет огромное количество вариаций, один с содержанием углерода менее 0.8% углерода и другой с содержанием более 0.8%. Разное содержание углерода производит различную микроструктуру, когда сталь откована и протравлена. Недавние исследования показали, что образование узора в стали, с содержанием углерода более 0.8% вызвано микроскопическим наличием некоторых модифицирующих элементов.
В процессе продолжительной холодной ковки, фазы этих микроструктур упорядочивались в стали. После протравки эти фазы проявлялись как темные линии или нити видимые невооруженным глазом, образуя Дамасский узор. Пока современное лабораторное оборудование не смогло обнаружить эти модифицирующие элементы в микроскопических количествах, никто не мог предположить, что это ключевой момент в создании дамасского узора.
Но не будем забывать о том, что индийские металлурги умели производить такую сталь уже, по меньшей мере, в I (а, по некоторым данным даже в III) тысячелетии до н.э. И мы говорим о секрете стали, который, даже в наш индустриальный век и при таком огромном интересе к проблеме выдающихся ученых современности, смогли разгадать лишь сравнительно недавно! Как же тогда и главное: откуда древнеиндийские мастера могли получить такие высокотехнологичные знания?
В древнеиндийских литейных мастерских процесс изготовления вутца — слитка высокоуглеродистой стали происходил примерно таким образом.
Железная руда и древесный уголь смешивались и нагревались примерно до 1200 °C в каменном горне. При этом железо восстанавливалось (освобождалось от кислорода) вследствие реакций с углеродом древесного угля и образовывало губчатую массу.
Примеси «выжимались» из губчатого железа ковкой. В результате получался кусок сварочного железа с низким содержанием углерода. Эти куски железа науглероживали, нагревая их вместе с древесным углем в закрытом глиняном тигле, предотвращавшем вторичное окисление железа. При появлении хлюпающего звука в тигле, свидетельствовавшего об образовании некоторого количества расплава, тигель подвергали медленному охлаждению, оставляя его в остывающей печи.
Индия вела широкую торговлю вуцем в виде слитков диаметром около 8 см. Кузнецы Среднего Востока ковали из этих слитков дамасские клинки после их нагрева до 650 — 850 °C. В этом интервале температур сверхвысокоуглеродистые стали становятся пластичными. Готовые клинки закаливали путем нагрева и быстрого охлаждения в воде, рассоле или другой жидкости.
Булат (дамасская сталь) являлся продуктом естественной кристаллизации стали, получаемой при соединении железа с углеродом. Сущность образования булата заключалась в насыщении сплава большим количеством углерода (около 1,3 — 1,5%). В условиях медленного охлаждения образовывалось и находилось в некотором излишке соединение железа с углеродом — так называемый цементит, который не растворялся, как это бывает в обычной стали, а оставался в железе как бы во взвешенном состоянии.
Прослойки цементита как бы обволакивались медленно стынущим мягким железом. Поэтому при высоком содержании углерода, что придает металлу твердость, булат сохраняет высокую вязкость, упругость, которой лишена обыкновенная сталь. Из-за наличия прослоек хрупкого цементита отковка булата должна производиться крайне осторожно, ударами легкого молота, с многократным нагреванием до критической температуры — до температуры красного каления, переход за которую ведет к потере булатом своих основных свойств и характерного рисунка. Процесс изготовления булата был очень трудоемким, длительным и требовал высокого искусства.
Уже в наше время, златоустовские металлурги вновь попытались воскресить технологию производства булата. Сложны и длительны были эти поиски, но узорчатая сталь вновь была получена, хотя полностью повторить аносовский булат не удалось. Легендарная упругость клинков достигнута не была.
Современные качественные легированные стали превосходят дамасскую сталь по всем показателям: прочности, упругости, режущим свойствам, но добиться таких выдающихся свойств в одном образце не удается и сейчас. Конечно, много вопросов еще остается и тайна ждет своей разгадки!
Знакомство европейцев с булатом началось еще в эпоху римского владычества — около 2000 лет назад. Позднее славу булатного оружия разнесли купцы, приобретавшие его в Дамаске и развозившие по многим странам. С начала III в. способ ковки дамасских мечей распространился в Западной Европе. Однако спустя 700 лет секрет производства мечей был снова утерян.
В средние века производство булатов было и на Руси. Имеются документы, подтверждающие, что в Москве существовало производство булатов. Так, в 1616 г. оружейный мастер Дмитрий Коновалов выковал зерцало из булата. В ряде документов встречаются записи: «…сабельные полосы, булат синей, московский выков», «сабля полоса русская с долами на булатное дело». Однако к концу XVII в. это искусство, видимо, пришло в упадок, а потом и вовсе забылось.
Здесь уместно будет затронуть вопрос — почему же так легко были утрачены многие секреты древних мастеров?
Академик Л. Ф. Верещагин, отвечая на этот вопрос, приводит пример с загадкой дамасской стали: «Как удавалось людям средневековья без нынешней техники и без легирующих добавок получать эту изумительную нержавеющую и необыкновенно прочную сталь? Если производство дамасских клинков было уже когда-то освоено, то почему же люди забыли его?» .
Сам он так ответил на этот вопрос: «То, что случайно найдено путем экспериментов и еще не осмыслено, не понято людьми, принадлежит им только наполовину. Человеку выпала большая удача — он нашел самородок золота. Нашел случайно. Он порадовался увесистой находке, подержал ее в руках, спрятал под куст в надежде вернуться сюда, а потом сколько не искал, уже не мог ее найти. Примерно то же случилось и с дамасской сталью. Случай дал ее в руки человеку, случай и отнял» .
Но так ли он прав? Элементарная логика нам подсказывает, что подобное утверждение справедливо лишь для тех случаев, когда речь, действительно, идет о некоем случае, произошедшим с одним-единственным человеком, но в здесь мы видим совсем иную ситуацию.
Во-первых, производство булата или дамасской стали — очень сложный, длительный и высокотехнологичный процесс, где необходимо точное соблюдение всех необходимых для этого условий. И такой сложный процесс вряд ли не мог стать результатом случайного открытия одного человека.
Во-вторых, производством булата в Индии занимался не один человек, а целая армия ремесленников, на протяжении тысячелетий!
И, в-третьих, не стоит забывать, что мы, в данном случае, говорим именно об Индии — одной из древнейших цивилизаций на Земле, где существует немало загадок, касающихся того, откуда древние индийцы могли получить свои знания о таких сверхтехнологичных вещах, которые, зачастую, наши современная науки и производство не в состоянии ни объяснить, ни повторить! Сами же индийцы отвечают на этот вопрос очень просто: «Эти знания нашим предкам дали боги!» .
Кстати, в этом с ними солидарны практически все народы мира. В любой культуре металлообработке, согласно мифологии, людей обучили боги, а «секрет стали», так же, как знаменитый «секрет бессмертия», был одной из самых заповедных тайн богов и тот счастливец, которому боги, по каким-то, только им известным причинам, этот секрет открывали, считался «благословенным любимцем богов» .
Некоторые полагают, что сейчас можно произвести слиток булатной стали, а потом из него получать, например путем проката, ленту для лезвий. При этом упускают из виду, что булатная сталь получается лишь после особой технологии изготовления изделий. Отковку булатного изделия надо вести очень осторожно, так искусно, чтобы при этом структура металла не разрушалась, а лишь сминалась, и волокна «твердой» и «мягкой» составляющих переплетались между собой.
Только в таком случае получался материал, обладающий одновременно и большой твердостью, и большой вязкостью. И такое строгое соблюдение определенной температуры и режима ковки необходимо для каждого отдельного изделия. Это требовало долгого и кропотливого труда искусного ремесленника. Поэтому, пожалуй, только холодное оружие по своей цене и могло найти себе покупателя.
Еще один центр производства качественных клинков образовался в средние века в Японии. Японский булат обладал каким-то необыкновенным качеством железа, которое после целого ряда проковок приобретало даже более высокую твердость и прочность, чем дамасская сталь. Мечи и сабли, приготовленные из этого железа, отличались удивительной вязкостью и необыкновенной остротой.
Уже в наше время был сделан химический анализ стали, из которой изготовлено японское оружие XI—XIII вв.еков. И древнее оружие раскрыло свою тайну: в стали был найден молибден!
Сегодня хорошо известно, что сталь, легированная молибденом, обладает высокой твердостью, прочностью и вязкостью. Молибден — один из немногих легирующих элементов, добавка которого в сталь вызывает повышение ее вязкости и твердости одновременно. Но, при этом, не стоит, так же забывать, что молибден, не только «редкоземельный», но и очень тугоплавкий металл и плавится при 2400 °C!
Все другие элементы, увеличивающие твердость и прочность стали, способствуют повышению ее хрупкости. Естественно, что в сравнении с дамасскими клинками, сделанными из железа и стали, японские легированные мечи и сабли казались чудом. Но значит ли это, что японцы умели в то далекое время делать легированную сталь?
Конечно, нет. Что такое легированная сталь, они даже не знали, по той простой причине, что само это понятие появилось лишь в наше время, так же как и не знали, что такое молибден, хотя прекрасно понимали, что, для изготовления подобных клинков требуется очень высокий температурный режим.
Руда, из которой древние японские мастера выплавляли железо, содержала значительную примесь окиси молибдена. Выплавленное из обогащенных молибденом «песков» кричное железо проковывалось в прутья и закапывалось в болотистую землю. Время от времени прутья вынимали и снова зарывали, и так на протяжении 8 — 10 лет.
Насыщенная солями и кислотами болотная вода разъедала пруток и делала его похожим на кусок сыра. Тем самым из заготовки удалялись вредные примеси, быстрее разъедаемые болотной водой. Затем разогретую заготовку японский кузнец проковывал в тонкую полосу, сгибал, опять проковывал и так несколько тысяч раз! Но и японские клинки, при всей их выдающейся остроте и прочности, не обладали качествами индийского булата, особенно упругостью.
В японской литературе нередко можно встретить описание того, как разгневанный или разгоряченный боем самурай, неверно рассчитав силу своего удара, ломал свой меч, да еще в самый неподходящий для этого момент. Зачастую подобный случай мог стоить самому самураю жизни и не только потому, что он, во время битвы, оказывался практически невооруженным (ведь у него оставался еще и короткий меч), но и потому, что, обезоружив себя, он, таким образом, обесчещивал себя и предавал своего сегуна, а за это полагалось делать харакири.
Отметим сразу, что, когда мы говорим о древней металлургии, мы опираемся не только на письменные источники, свидетельствующие о наличии таковой у наших далеких предков, но и на вполне реальные артефакты, являющиеся продуктами ее производства и дошедшие до наших дней, наличие которых полностью снимает вопрос о том, соответствовали эти свидетельства реальному положению вещей.
И, сколько бы ни было легенд о существовании в древности некой загадочной технологии выплавки чрезвычайно упругой и крепкой стали, совершенно не подверженной коррозии, только наличие предметов, изготовленных из такой стали, может пролить нам свет на истину.
Но такие предметы есть! Дамасские и булатные (что, по сути, — одно и то же) клинки сохранились до наших дней! Они хорошо известны и историкам, и коллекционерам, и специалистам, в области металловедения. И это — факт. Так же как и то, что настоящий секрет этой стали, не разгадан до сих пор!
Как уже писалось выше, еще в середине XIX века в России были изготовлены образцы сплавов, подобные булату, а современные златоустовские мастера повторяют этот опыт. Но! Эти сплавы лишь по некоторым характеристикам аналогичны дамаску, в частности, по знаменитому рисунку металла, но не обладают его прочностью и невероятной пластичностью. Так что, пока мы можем говорить лишь о некоторых успехах, которые приближают нас к разгадке этой величайшей тайны, но не о том, что она, наконец, разгадана.
И здесь невольно задаешься вопросом: «Как же такое может быть, чтобы наши современные ученые, вооруженные такими знаниями, многовековым опытом металлообработки и самыми современными технологиями и оборудованием, не могли повторить того, что в, поистине, промышленных масштабах изготовляли древнеиндийские металлурги?». И такие вопросы возникают не только у автора и не только здесь; их довольно часто задают специалистам металлургии. Но ответы, которые обычно можно услышать на них звучат, по меньшей мере, крайне неубедительно.
Один из подобных ответов, по сути, сводящийся к идее «да они сами не поняли, что случайно сотворили», уже приводился выше, но есть и другие варианты, например: «А нам сейчас и не надо это понимать, так как у нас другие задачи и нам нужно не мечи делать, а другие вещи, более необходимые в народном хозяйстве» .
Что тоже вызывает сильно недоумение. Так и хочется в ответ спросить: «А у нас, что нет армии, где до сих пор используется холодное оружие? И разве наши бойцы отказались бы от возможности пользоваться ножами, кортиками и штык-ножами не из легированной стали, а из настоящего булата? И неужели Министерство обороны не захотело бы ввести в состав предметов личного вооружения спецназа меч, способный опоясывать бойца? Или у наших военных нет на это ни денег, ни заинтересованности?». Подобные объяснения кажутся, как минимум, надуманными и являются обыкновенной попыткой скрыть собственную некомпетентность под маской незаинтересованности.
Нередко из уст специалистов можно услышать и другое объяснение: «Булат являлся штучным продуктом некоторых мастеров и производился исключительно кустарным способом, поэтому, в современном производстве он просто нерентабелен». Но, во-первых, как можно говорить о рентабельности производства булата, когда неизвестен весь технологический процесс его изготовления? А, во-вторых, это утверждение тоже не соответствует действительности, так как доподлинно известно, что древнеиндийские металлурги обеспечивали булатной сталью весь древний мир, на протяжении нескольких столетий и в промышленных масштабах!
Кроме того, сегодня мы живем в век композитных материалов, производство и применение которых играет в научно-производственном процессе, чуть ли, не первостепенную роль. И далеко не всегда новые материалы появляются в ответ на нужды производства; довольно часто можно наблюдать и обратный процесс — сначала новый материал рождается где-нибудь в недрах научно-исследовательской лаборатории, а уж потом, иной раз, спустя несколько десятилетий, он находит свое применение. Когда же мы говорим о булате, то имеем в виду первый в истории человечества композитный материал! Разве это не важно?
Получается такой парадокс.
Общество и производство остро нуждается в новых композитных материалах.
Есть образцы древнейшего композитного материала, веками подтверждавшего свои уникальные и неоценимые качества.
Есть заинтересованность армии в этом материале.
Характеристики материала делают его применимым не только для производства холодного оружия, но и в других областях человеческой деятельности.
Веками отработанная технология изготовления его в промышленных масштабах доказывает, что он вполне подходит, в качестве продукта современного производства.
Но, при всем этом, никто, сколь-нибудь серьезно этим вопросом не занимается.