Функциональная схема АСК давления газообразного аммиака и азота, АСР температуры газа в зонах диссоциатора, расхода и соотношения "азот – диссоциированный
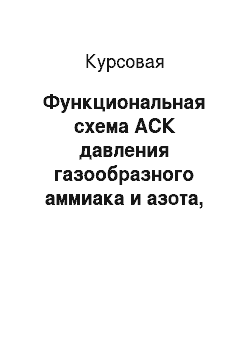
Рисунок 6 — Схема общего вида термоэлектрического преобразователя Измерение температуры в ячейке осуществляется с помощью платинородий-платиновой термопары в защитном чехле. Для обеспечения длительной стабильности термоэлектрических свойств термопары ее защищают двумя чехлами: фарфоровым и карбофраксовым. Это значительно увеличивает инерционность датчика температуры. Платинородий-платиновые… Читать ещё >
Функциональная схема АСК давления газообразного аммиака и азота, АСР температуры газа в зонах диссоциатора, расхода и соотношения "азот – диссоциированный (реферат, курсовая, диплом, контрольная)
Курсовая работа Функциональная схема АСК давления газообразного аммиака и азота, АСР температуры газа в зонах диссоциатора, расхода и соотношения «азот — диссоциированный аммиак» станции приготовления контролируемой атмосферы.
1. Назначение, функции и параметры агрегата.
В печах термической и термохимической обработки применяют различные контролируемые атмосферы, в том числе получаемые при сжигании природного газа с коэффициентом расхода воздуха 0,25−0,3 (эндогаз) и коэффициентом расхода воздуха 0,5−0,95 (экзогаз), при диссоциации аммиака, из технического азота и др. В табл. 1 приведены характеристики некоторых контролируемых атмосфер, применяемых в термических отделениях прокатных цехов металлургических заводов.
Таблица 1. Состав защитных атмосфер (температура точки росы (-40) — (-50)).
Тип атмосферы. | Состав, % (объемн.). | Метод производства. | |||
СО. | Сжигание природного газа при б=0.95; очистка С и. Очистка технического азота от с добавкой диссоциированного аммиака Диссоциация аммиака. | ||||
Азотная (экзогаз). | 1−2. | 1−2. | 96−96.5. | ||
Азотная. | 4−5. | ; | 95−96. | ||
Водородная. | ; | ||||
Упрощенная технологическая схема получения контролируемой атмосферы из диссоциированного аммиака показана на рисунке 1. Жидкий аммиак из баллонов испаряется в испарителе 1 при 20−30° С. Газообразный аммиак проходит через диссоциатор и разлагается при 1000° С. Применение катализатора, часто окиси железа, понижает температуру диссоциации на 100° С и более.
Й — жидкий аммиак из баллонов; II — вода; III — воздух; IV — готовая контролируемая атмосфера; 1 — испаритель; 2 — регулятор давления; 3 — диссоциатор; 4 — скруббер; 5 — комплект приборов для измерения температуры; 6 — водяной холодильник; 7 — газоанализатор на водород; 8 — фреоновый холодильник; 9 — блок осушки; 10 — влагомер; 11 — расходомер готовой атмосферы; 12 — манометр; 13 — камера сжигания; 14 — расходомер воздуха; 15 — регулятор соотношения диссоциированный аммиак — воздух; 16 — регулятор температуры в диссоциаторе; 17 — расходомер диссоциироваииого аммиака; 18 — регулятор уровня в испарителе; 19 — клапаны Рисунок 1 — Технологическая схема получения диссоциированного аммиака и система контроля и автоматики Из диссоциатора смесь водорода и азота (75% И2 и 25% N2) проходит через змеевик испарителя, отдавая тепло жидкому аммиаку, и идет в скруббер где освобождается от следов аммиака, растворяющегося в воде. После скруббера смесь газов поступает в водяной и фреоновый холодильники 6 и 8, а затем в блок осушки, где осушается силикагелем или алюмогелем до точки росы (-40) — (-50)° С.
Для уменьшения взрывоопасности смеси газов и в случае, когда нужна защитная атмосфера с более низким содержанием водорода, часть водорода сжигается в камере 13, а полученные пары воды конденсируются в холодильниках 6 и 8.
2. Вид агрегата.
1- испаритель; 2 — диссоциатор; 3 — камера сжигания; 4 — трубчатый холодильник; 5 — камера охлаждения; 6 — блок сушки; 7 — система регулирования состава газа Рисунок - 2 Установка ДА-ЗОС (ОКБ-674) для приготовления атмосферы из аммиака.
На рисунке 2 показана конструкция установки для изготовления атмосферы из аммиака ДА-ЗОС (ОК.Б-674). Вся установка состоит из блоков: испарителя аммиака с диссоциатором, сжигания, охлаждения газа и осушки. В блок испаритель-диссоциатор входят испаритель аммиака, диссоциатор и трубчатый холодильник. Испаритель представляет собой металлический сосуд высокого давления со сферическими днищами и предохранительным клапаном. Испаритель имеет змеевиковый и электрический подогреватели жидкого аммиака. Диссоциатор изготовляют в виде шахтной электропечи, футерованной огнеупорным кирпичом с жароупорной ретортой, заполненной катализатором. Температура контролируется и регулируется автоматически.
Блок Сжигания состоит из камеры сжигания, системы контроля и автоматического регулирования состава газа. В камере находится катализатор горения. Водяная рубашка служит, для отвода избытка тепла от камеры.
Блок охлаждения газа состоит из трубчатого холодильника с гидравлическим затвором, камеры охлаждения с ребристыми охладителями и холодильных установок. Блок сушки состоит из двух силикагелевых осушителей и электрокалорифера для подогрева воздуха. Наружные стенки осушителя охлаждаются водой. В электрокалорифере находится теплоизоляция и съемный электронагреватель. Ниже приведена техническая характеристика установки ДА-ЗОС Производительность в м2/ч… 30.
Установленная мощность кВт… 29.
Рабочая температура диссоциатора в°С 650−700.
Напряжение сети в B… 220/380.
Состав атмосферы:
без дожигания водорода… 75% Н2, 25% N2.
с дожиганием водорода… 4−20% Н2, 80−96% N2.
Точка росы в°С,… -40 -50.
Габаритные размеры в мм… 3400Х 3300Х 2325.
Из отдельных блоков можно составлять установки; например, могут быть смонтированы следующие установки: с диссоциацией аммиака без последующего сжигания, с диссоциацией аммиака с частичным сжиганием, с сушкой или без нее, для очистки технического азота, для частичного сжигания водорода с сушкой или без нее. Кроме того, эти блоки могут быть использованы и для монтажа установок других типов атмосфер.
Существует адсорбент — «молекулярные сита». Такое название адсорбент имеет потому, что размер его пор приближается к размеру молекул. Если размер молекул поглощаемого вещества превышает размер пор адсорбента, то они не проходят и не поглощаются, если же меньше, то они проникают в адсорбент и поглощаются им.
Этот адсорбент представляет собой кристаллическое вещество, сходное с искусственно приготовленными алюмосиликатами — цеолитами. Сушка газа с помощью «молекулярных сит» может быть доведена до точки росы (-70) — (-80)°С. Когда молекулярные сита насыщаются поглощенными веществами, их очищают путем регенерации при температуре 300−350° С.
При использовании молекулярных сит для сушки и разделения веществ конструкции существующих установок с силикагелем или этаноламинами должны быть изменены, так как десорбция поглощенных молекулярными ситами веществ происходит при более высоких температурах, а также изменяются и другие условия — нагрузка, давление, влажность и т. д.
Для приготовления контролируемой атмосферы аммиачной группы можно использовать другую схему. Обезвоженный аммиак испаряется и смешивается с воздухом (1 часть аммиака и 3,6 части воздуха). Смесь пропускается над катализатором, и происходит следующая реакция: 4NН3 + 302 -" 2N2 + + 6Н2О + Q (тепло). После этого газ охлаждается и осушивается до точки росы -40° С и ниже. Атмосфера состоит из 99,5−60% N2 и 0,5−40% Н2. Эта атмосфера находит применение для нагрева высокоуглеродистой лезвийной стали, нержавеющей стали и цветных металлов.
Для получения аналогичных контролируемых атмосфер может быть использован также азот, находящийся в баллонах. Такой азот обычно содержит 3−5% кислорода. Азот смешивается с диссоциированным и охлажденным аммиаком, после чего смесь пропускается над катализатором, способствующим реакции кислорода с водородом при комнатной температуре или продувается через медную стружку и затем осушивается до требуемой точки росы. Можно также пропускать газ через реторту с раскаленным древесным углем. В этом случае в составе атмосферы будет приблизительно 5% СО и остальное N2.
Аммиачная группа атмосфер имеет следующие преимущества: с жидким аммиаком легче обращаться, чем с баллонами газа, эта группа атмосфер почти не имеет посторонних примесей; нетрудно получить диссоциацию аммиака, и газ не требует дальнейшей очистки.
К недостаткам аммиачной группы можно отнести следующее: большие затраты по сравнению с затратами, произведенными для получения других атмосфер; эти атмосферы взрывоопасны в более широком интервале температур, чем другие атмосферы, за исключением атмосфер с невысоким содержанием водорода (до 15%); при содержании в атмосфере незначительного количества недиссоциированного аммиака происходит нежелательное азотирование стали.
3. Статические и динамические характеристики агрегата.
спецификация агрегат регулирование динамический В установках диссоциированного аммиака автоматически контролируются:
1) расходы; диссоциированного аммиака, воздуха на сжигание части водорода, готовой контролируемой атмосферы;
2) давление: жидкого аммиака, газообразного аммиака после испарителя, готовой атмосферы;
3) температура: в зонах диссоциатора, в камере сжигания, в блоке осушки;
4) состав газа: на содержание водорода после частичного сжигания, на содержание влаги в готовой атмосфере.
Автоматизация установки сводится к стабилизации ряда основных параметров. Автоматически регулируется уровень жидкого аммиака в испарителе регулятором 18, давление аммиака перед диссоциатором регулятором 2 (рисунок 1).
Диссоциатор обогревается электронагревателями, разделенными иногда на несколько зон. В каждой зоне позиционным регулятором 16 поддерживаете заданная температура.
В случае сжигания части водорода может поддерживаться соотношение газ — воздух. Регулятор 15 отрабатывает определенное соотношение давлений, чн при данном открытии клапанов 19 означает поддержание необходимого соотни шения расходов. Изменение содержания водорода в контролируемой атмосфер осуществляется изменением задания регулятору соотношения 15.
На установках получения диссоциированного аммиака также применяют во взрывоопасных местах пневматическую аппаратуру и регуляторы прямою действия.
К статическим характеристикам относятся нагрузка, давление, влажность.
4. Контроль давления.
Мановакууметр.
Принцип действия манометра основан на уравновешивании измеряемого давления силой упругой деформации трубчатой пружины или более чувствительной двухпластинчатой мембраны, один конец которой запаян в держатель, а другой через тягу связан с трибко-секторным механизмом, преобразующим линейное перемещение упругого чувствительного элемента в круговое движение показывающей стрелки.
Диаметр корпуса -160 мм Класс точности приборов — 1,5 (по заказу — 1,0).
Степень защиты — IP40 (по заказу — IP53).
Масса приборов — не более 1,2 кг Средний срок службы — 10 лет Материалы деталей:
корпус — сталь, алюминиевый сплав, ударопрочный полистирол стекло — оконное трубчатая пружина — медный сплав, железо-никелевый сплав держатель — медный сплав, сталь механизм — бронза, нержавеющая сталь, сталь 0,8 кп Приборы МП4-У, ВП4-У и МВП4-У выдерживают воздействие вибрации в диапазоне частот от 5 до 25 Гц с амплитудой до 0,1 мм (группа L3 по ГОСТ 12 997–84).
Класс точности приборов МП4-У, ВП4-У и МВП4-У 1 и 1,5.
Диапазон измерений избыточного давления от 0 до 75% диапазона показаний; вакуумметрического давления равен диапазону показаний.
Приборы МП4-У, ВП4-У и МВП4-У устойчивы к воздействию температуры окружающего воздуха от минус 50 до плюс 60 °C, в корпусе из полистирола — от минус 30 до плюс 60 °C.
Степень защиты приборов МП4-У, ВП4-У и МВП4-У от проникновения внешних твердых предметов, пыли и воды — IP40 и IP53.
Рисунок 4 — Мановакууметр
Милливольтметр.
а — измерительный механизм с внешним постоянным магнитом; б — электрическая схема с термоэлектрическим термометром Рисунок 5 — Магнитоэлектрический милливольтметр Принцип работы милливольтметра заключается в использовании взаимодействия магнитного поля неподвижного магнита и постоянного тока, протекающего через обмотку подвижной рамки.
Измерительный механизм милливольтметра с внешним магнитом приведен на рисунке 5а. Он состоит из постоянного магнита 2, полюсного наконечника 1, подвижной рамки 8, неподвижного сердечника 9, стрелки 3. Полюсные наконечники и неподвижный сердечник выполнены из магнитномягкой стали, обмотка рамки — из медной изолированной проволоки. Ось рамки образована двумя кернами 6, установленными в агатовых или корундовых подпятниках, которые расположены в опорных винтах 5.
Рамка двигается вместе с легкой стрелкой, один конец которой перемещается относительно шкалы, а на другом расположены два усика с грузами 10. Перемещением грузов по винтовой нарезке усиков добиваются уравновешивания подвижной части. Центр тяжести проходит через ось вращения.
Спиральные пружинки 7, изготавливаемые из бронзовых сплавов, обеспечивают электрический контакт с перемещающейся рамкой и создают противодействующий уравновешивающий момент. У верхней пружины конец наружного витка закреплен в вилке, связанной с поводком корректора нуля 4.
Спиральная пластинка 11 является магнитным шунтом, перемещая который можно в определенных пределах изменять величины магнитной индукции в воздушном зазоре, в котором обеспечивается равномерное радиальное магнитное поле в необходимом интервале углов поворота рамки.
Сердечник, подвижная часть, винты с подпятниками закреплены в обойме с мостиком 12. Последние изготовлены из немагнитных материалов.
Рамка Rp включается в цепь ТЭП (рисунок 5б) с помощью компенсационных А1 и В1, и медных С проводов. Сила тока, протекающего в цепи, зависит от величины ТЭДС ЕАВ (t2, t0) и сопротивления измерительной цепи.
I = ЕАВ (t2, t0)/(RГ+RВН),.
где RГ — сопротивление милливольтметра, складывающееся из сопротивления рамки Rp и добавочного сопротивления Rдоб, Ом; RBH — сопротивление внешней цепи, складывающееся из сопротивлений термопары RТ, компенсационных RКП, соединительных проводов Rc, а также подгоночной катушки, RПК, Ом.
При протекании тока через рамку, окруженную полем постоянного магнита, возникает магнитоэлектрический момент М (Нм), поворачивающий рамку и равный:
M-2r*I*n*B*I,.
где 2 г — ширина рамки, м; l — длина рамки, м; n — число витков обмотки рамки; В-магнитная индукция в воздушном зазоре, Тл; I — ток, протекающий в рамке, А.
При перемещении рамка одновременно закручивает спиральные пружины, которые создают противодействующий упругий момент (Н*м):
Мп = W*ц, где W — удельный противодействующий момент (момент пружин, отнесенный к единице угла поворота рамки), Н*м/рад; ц — угол поворота рамки, рад.
Удельный противодействующий момент зависит от материала и размеров пружинок или других видов подвески, например, растяжек. Вращение рамки будет продолжаться до тех пор, пока магнитоэлектрический момент не уравновесится противодействующим упругим моментом М = Мn.
ц = 2r*l*n*B*I/W;
Принимая, что 2r, l, n, В, W для данной конструкции прибора при нормальных условиях эксплуатации являются постоянными величинами, получим ц = CoI.
где Co = 2г*l*n*В/W — чувствительность измерительного механизма к току, рад/А.
Следовательно, чем больше ток, тем больше угол поворота рамки. Получим:
ц = Co — ЕАВ (t2, t0)/(RГ+RВН).
В общем виде угол поворота <�р зависит от ряда параметров (для данного типа ТП):
ц =f (t, t0, RГ, RВН).
Для получения однозначной зависимости угла поворота рамки, а следовательно, и положения стрелки относительно оцифрованной шкалы прибора необходимо градуировать милливольтметр при заданных величинах t0 = 0 °C и RВН = 5; 15; 25 Ом. Подгоночная катушка RПК предназначена для того, чтобы в реальных условиях эксплуатации (изменяющиеся и заранее неизвестные значения сопротивлений RT, RПК, Rс) довести общую величину RВН до значения, при котором был проградуирован прибор.
5. Контроль и регулирование температуры.
Термопара — ТХА-151.
Рисунок 6 — Схема общего вида термоэлектрического преобразователя Измерение температуры в ячейке осуществляется с помощью платинородий-платиновой термопары в защитном чехле. Для обеспечения длительной стабильности термоэлектрических свойств термопары ее защищают двумя чехлами: фарфоровым и карбофраксовым. Это значительно увеличивает инерционность датчика температуры. Платинородий-платиновые термопары могут длительно работать в интервале температур от 0 до 1300 °C, а кратковременно — до 1600 °C. Эти термопары сохраняют стабильность градуировочной характеристики в окислительной и нейтральных средах. В восстановительной атмосфере работать не могут, так как происходит существенное изменение ТЭДС. Так же отрицательно воздействует на ТП контакт с углеродом (науглероживание проволоки искажает термоэлектрическую характеристику платины и приводит к погрешностям в измерении), парами металлов, соединениями углерода и кремния, а также рядом других материалов, загрязняющих термоэлектроды. Эта термопара является наиболее точным и используется также в качестве образцовых рабочих эталонов и термометров 1-го, 2-го и 3-го разрядов.
На рисунке 4 показана конструкция технического ТП. Термопара расположена в специальной защитной арматуре, обеспечивающей защиту термоэлектродов от механических повреждений и воздействия измеряемой среды. Арматура включает защитный чехол 1, гладкий или с неподвижным штуцером 2, и головку 3, внутри которой расположено контактное устройство 4 с зажимами для соединения термоэлектродов 5 с проводами, идущими от измерительного прибора к термометру. Термоэлектроды по всей длине изолированы друг от друга и от защитной арматуры керамическими трубками (бусами) 6.
Тип ТХА. Материал термоэлектродов: хромель и алюмель Хромель-алюмелевые термопары считаются термопарами общего назначения. Отличаются невысокой стоимостью. Используются в самых различных щупах. Этими термопарами можно измерять температуры в диапазоне от -270°C до +1372°C. Чувствительность составляет примерно 41 мкВ/°C.
Автоматические потенциометры.
Автоматические потенциометры служат для компенсационных измерений термоЭДС без ручных манипуляций, свойственных неавтоматическим потенциометрам. У последних ручные манипуляции после стандартизации тока сводятся к следующей необходимости перемещать движок реохорда до тех пор, пока стрелка гальванометра не встанет на ноль. При этом перемещение движка производится во вполне определенном направлении.
Измерительная схема автоматического потенциометра в принципе не отличается от схемы не автоматического потенциометра (рис. 7).
Схема имеет три источника напряжения (батарея Б, нормальный элемент НЭ и термопару Т) и три цепи. Цепь батареи выполнена в виде моста: в диагональ BD включается питание, а в диагональ CA — цепь термопары. Цепь нормального элемента подключается к плечу CD компенсационной цепи. С помощью переключателя П в цепь термопары или в цепь нормального элемента включается электронный усилитель ЭУ (в том числе и вибрационный преобразователь). При включении цепи нормального элемента вводится шунтирующее сопротивление R1, параллельное электронному усилителю, так как в этом случае величина напряжения небаланса бывает много больше, чем при включении цепи термопары.
Электронные автоматические потенциометры называют иногда приборами с непрерывной балансировкой, так как измерение небаланса производится здесь с частотой переменного тока 50 Гц.
Широкое применение имеют многоточечные автоматические потенциометры с самопишущим устройством, предназначенным для записи показаний нескольких термопар. Такие потенциометры имеют автоматически действующие переключатели для поочередного включения в измерительную цепь цепей отдельных термопар. Запись производится либо различным цветом, либо определенными знаками для каждой термопары.
Поверка потенциометров производится путем сравнения их показаний с показаниями образцовых потенциометров более высокого класса точности. Погрешность образцового потенциометра не должна превышать 1/3 К, где К — численное выражение класса точности поверяемого прибора.
Исполнительный механизм МЭО.
Регулирование расхода происходит при помощи исполнительных механизмов МЭО-10/25 — электромеханическая система, предназначенная для приведения в действие запорно-регулирующей трубопроводной арматуры в системах автоматического регулирования технологическими процессами, в соответствии с командными сигналами регулирующих и управляющих устройств.
1-редуктор; 2-электродвигатель; 3-блок сигнализации положения; 4-ввод штуцерный; 5-розетка; 6-заземляющий болт; 7-ручной дублер; 8-рычаг; 9-крышка; 10-упор Рисунок 8 — Исполнительный механизм МЭО Фактически МЭО представляет собой исполнительный механизм, перемещающий различные регулирующие органы по сигналам специальных команд, которые направляются из автоматических и регулирующих устройств. Эти команды подаются в виде аналоговых или дискретных электрических сигналов, на основании которых МЭО преобразует его во вращательное движение выходного вала на определенный угол. Исполнительный механизм МЭО оборудован датчиками обратной связи.
6. Контроль и регулирование расхода и соотношения.
Диафрагма.
Для измерения расходов газа и воздуха на нагревательных печах наибольшее распространение получили расходомеры, действие которых основано на дросселировании потока при помощи дроссельного (сужающего) устройства постоянного сечения. Местное сужение потока в круглом трубопроводе создается при помощи установки дроссельного устройства, в качестве которого, как правило, используют диафрагму (рис 9). Диафрагма представляет собой тонкий диск с концентрическим цилиндрическим отверстием с острой входной кромкой. Сталь, «-из которой изготовляют диафрагму, различна в зависимости от того, в какой среде она работает.
Рисунок 9 — Течение вещества через диафрагму (а), эпюры давления (б) и скорости (в).
Если через сужающее устройство протекает сжимаемая среда (газ или пар), то вследствие понижения давления увеличивается ее объем. Это приводит к тому, что скорость потока возрастает и становится больше скорости несжимаемой среды. В результате на сужающем устройстве увеличивается перепад давления.
Дифманометр.
Рисунок 10 — Дифманометр Дифманометр не имеет отсчетных устройств и снабжен преобразователем с магнитной компенсацией. Может использоваться с вторичным прибором. Чувствительный элемент мембранный блок-две мембранные коробки. Внутри мембранной коробки дистиллированная вода. Подвод давления через две трубки по действием разности давлений. В плюсовой камере мембранной коробки происходит сжатие. Жидкость из неё перетекает в верхнюю коробку — отрицательная камера. В результате происходит перемещение верхней мембраны, что приводит к перемещению магнитного флунжера, который установлен внутри передающего преобразователя с магнитной компнсацией и усиливается усилителем. В магнитном преобразователе магнитных потоков сигнал преобразуется в электрический. Выходной сигнал постоянного тока — 0,5 мА Таблица 2 — Сводная таблица функциональной схемы.
Обозначение позиции. | Наименование прибора, устройства. | Тип. | Технические данные. | Количество. | Примечание. | |
1а, 2а, 3а. | Манометр | МВП4-У1. | Измерение давления 100ч2400 кПа. | |||
4б, 7 В, 8 В. | Милливольтметр | Ш4 501. | Погрешность измерения прибора ±1,6%. | |||
4а, 5а. | Термопара. | ТХА-151. | Температура измерения от -50 єС до 1000єС. | |||
7а, 8а, 9а, 11а. | Диафрагма. | Ду= 125 мм. | ||||
7б, 8б, 9б, 11б. | Дифманометр мембранный с индукционным датчиком. | ДМ — 23 373. | Измерение давления 1,6ч2500 кПа. | |||
5б, 9 В, 11 В. | Миллиамперметр или Автоматический Патенциометр? | КСУ-1. | Погрешность ± 0,5%. Температура окружающей среды: 0 °C -50°С. | |||
5 В, 9 г. | Задатчик. | ЗРУ-24. | ||||
5 г, 9д. | Регулятор | РП4-Т. | ~220 В. | |||
5д, 10б. | Переключатель кулачковый, универсальный. | ПКУ 3−14С-2004. | 500 В, 4 секции. | |||
5е, 10а. | Исполнительный механизм. | МЭО-10/25. | Номинальный момент вращения 100 Н· м. Время 1-го оборота 25 секунд. | |||
Список используемой литературы.
1. О. М. Блинов «Автоматизация металлургических печей», Москва «Металлургия» 1975, 375с.
2. Каганов В. Ю, Блинов О. Н, Беленький А. М. Автоматизация управления металлургическими процессами — М: Металлургия. 1974. — 416 с.
3. Глинков Г. М. АСУ ТП в черной металлургии — М: 1999. — 3 Юс.
4. Зайцев Г. Ф. Теория автоматического управления и регулирования — К.: 1988.-432 с.
5. А. И. Емельянов, О. В. Капник Проектирование систем автоматизации технологических процессов — М.: Энергоатомиздат 1983. — 399 с.
6. Кликовский K. JL, Купер В. Я. Методы и средства измерений. М.: Энергоиздат, 1986, — 448 с.