Технологический процесс изготовления вала насоса
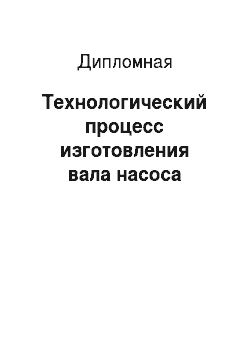
При разработке схем базирования учитываем принцип и единства баз: на всех операциях обработки по возможности использовать одну и ту же базу, как установочную, так и измерительную и принцип постоянства баз: на всех операциях обработки необходимо применять по возможности одни и те же базы. Также важно учитывать правило шести точек, при котором деталь базируется на шести неподвижных точках, которые… Читать ещё >
Технологический процесс изготовления вала насоса (реферат, курсовая, диплом, контрольная)
1. Анализ исходных данных Задача данного раздела — на базе анализа технических требований предъявляемых к детали и годового объема выпуска сформулировать задачи, которые необходимо решить в дипломном проекте для достижения цели, сформулированной во введении.
1.1 Анализ служебного назначения и условий работы детали Деталь «Вал насос-мотора», чертеж 01. М15.017.011.000, является вращающейся деталью и предназначена для обеспечения передачи крутящего момента с шатунов на блок цилиндров насос-мотора, который работает как в режиме насоса, так и в режиме мотора. Вал в сборе с подшипниками устанавливается в корпус насос-мотора.
1.2 Систематизация и классификация поверхностей Цель систематизации поверхностей — выявление поверхностей, имеющих определяющее значение для выполнения детали своих функций. При систематизации поверхностей будем опираться на данные (рис. 1.1.).
Цель классификации поверхностей по служебному назначению — выявление поверхностей являющихся: основными и вспомогательными конструкторскими базами, поверхностей выполняющих исполнительные функции детали, а также свободных поверхностей не входящих во взаимодействие с другими сопряженными поверхностями. Классификацию поверхностей детали по служебному назначению сводим в таблицу 1.1.
Таблица 1.1.
Вид поверхности | № поверхности | |
ИП | 6,8,10,11,14,15,16,24,25,26,27,28,29,30,31,32,39,40,41, а также 47 и 48 (не показаны) | |
ОКБ | 6,8,13,29 | |
ВКБ | 1,5,17 | |
СП | остальные | |
Рис. 1.1. Схема кодирования поверхностей и размеров детали
1.3 Анализ технологичности конструкции детали Анализ технологичности конструкции детали будем проводить по следующим группам критериев:
— технологичность заготовки;
— технологичность установки;
— технологичность обрабатываемых поверхностей;
— технологичность общей конфигурации детали.
1.3.1 Технологичность заготовки Вал изготавливается из стали 30 ХМ. Материал не является дефицитным, при относительно невысокой стоимости он обладает хорошими качествами: предел прочности при растяжении 610 МПа, предел прочности при сжатии 780 МПа, твердость 22…29 HRC.
В таблице 1.2 представлен химический состав данной стали, а в таблице 1.3 ее механические свойства.
Таблица 1.2 Химический состав стали 30ХМ, %
С | Si | Mn | Cr | Mo | Ni | P | S | Cu | |
не более | |||||||||
0.26−0.33 | 0.17−0.37 | 0.40−0.70 | 0.80−1.10 | 0.15−0.25 | 0.30 | 0.025−0.035 | 0.035−0.025 | 0.30 | |
Таблица 1.3 Механические свойства стали 30ХМ в состоянии поставки
0,2 | в | KCU, Дж/см2 | HRC | |||
МПа | % | |||||
Технологические свойства:
— температура ковки, С: начала 1260, конца 760−800;
— свариваемость — ограниченно свариваемые;
— обрабатываемость резаниемпри HB 229−269, в = 610 МПа, KV тв.спл. = 0,70, KV б.ст. = 0,3
— склонность к отпускной хрупкости — не склонна.
Заготовку вала возможно получить отрезкой проката круглого профиля, так и штамповкой на горизонтально-ковочной машине (ГКМ). Наиболее предпочтительный вариант получения заготовки определим экономическим расчетом.
За критерий обрабатываемости принят коэффициент [бар]:
(1.1)
где КГ — коэффициент, учитывающий группу стали по обрабатываемости;
В — предел прочности обрабатываемого материала;
nV — показатель степени при обработке;
.
Значение данного коэффициента будем учитывать при выборе материала режущих инструментов.
1.3.2 Технологичность установки
Черновыми базами для установки заготовки на первой операции могут быть цилиндрические и торцевые поверхности заготовки. В дальнейшем за базы приняты цилиндрическая пов. 2 и торцевая пов.1 и центровые отверстия ли цилиндрическая пов.13 и торцевая пов.15, в зависимости от установа. Данные технологические базы обеспечивают надежную ориентацию и закрепление заготовки, возможность свободного подвода инструмента при обработке.
Измерительные базы детали можно использовать в качестве технологических баз, т.к. точность и шероховатость этих баз обеспечивает требуемую точность обработки.
Таким образом, с точки зрения установки при обработке, деталь можно считать технологичной.
1.3.3 Технологичность обрабатываемых поверхностей
Предполагается обрабатывать все поверхности детали. Число обрабатываемых поверхностей 41: 16 цилиндрических: 2, 4, 6, 7, 8, 10, 11, 13, 18, 22, 24, 28, 29, 35, 38, 40; 15 торцевых: 1, 3, 5, 9, 21, 23, 25, 27, 30, 33, 34, 36, 37, 39; резьбовые поверхности: пов. 20, 32; сферические: 26, 31, 41; технологические канавки и уклоны: пов.9, 12; шпоночный паз 14, 15, 16; фаски, галтели.
Протяженность обрабатываемых поверхностей невелика и определяется условиями компоновки насоса-мотора.
Для обеспечения нормальной работоспособности всех узлов насоса-мотора назначены следующие требования к геометрии вала: допуск К5 на шейку вала, сопрягаемую с шестерней гидромашины, допуск ! на шейки под подшипники; допуски на шероховатость назначаем по [1], точность резьбовых соединений по [1], допуски торцевого и радиального биения назначаем по. Точность и шероховатость поверхностей 6, 8, 13, 25 (ОКБ) определяется условиями эксплуатации вала. Уменьшение точности приведет к снижению точности установки вала в насосе-моторе. Все отверстия вала доступны для обработки. Поверхности различного назначения разделены, что облегчает обработку. Форма детали позволяет обрабатывать поверхность напроход. Обработка поверхностей в упор затруднений не вызывает.
Таким образом, с точки зрения обрабатываемых поверхностей, деталь можно считать технологичной.
1.3.4 Технологичность общей конфигурации детали
Деталь имеет достаточную жесткость и прочность. Радиусы закруглений и фаски выполняются по ГОСТ 10 948–64, форма и размеры канавок по ГОСТ 8820–69. Такая унификация упростит обработку и контроль этих элементов вала.
Вал можно отнести к типу деталей «валы», для которых разработан типовой ТП.
Форма детали позволяет вести одновременную обработку нескольких поверхностей: цилиндрических- 6, 8, 10,11, торцовых 1,2,4. При обработке на станке с ЧПУ сферических пов. 26 и 31 и нарезание резьбы в отверстиях можно осуществить на одной операции. Оборудование может быть простым, универсальным, оснастку также можно применять универсальную. Все поверхности вала доступны для контроля.
Таким образом, с точки зрения общей компоновки детали ее можно считать технологичной.
Поскольку деталь отвечает требованиям технологичности по всем 4 группам критериев, можно сделать вывод о ее достаточно высокой технологичности.
1.4 Формулировка задач дипломного проекта
На базе анализа технических требований к детали сформулируем задачи дипломного проекта:
1. Определить тип производства и выбрать стратегию разработки технологического процесса;
2. Выбрать оптимальный метод получения заготовки и маршрут обработки поверхностей;
3. Разработать технологический маршрут и схемы базирования заготовки;
4. Выбрать оборудование, приспособления, режущий инструмент, средства контроля;
5. Рассчитать припуски на обработку на спроектированные технологические операции
6. Рассчитать и спроектировать станочное приспособление для токарной операции и приспособление контроля биения отверстия
7. Рассчитать и спроектировать режущий инструмент для токарной операции
8. Провести линейную оптимизацию режимов резания на токарной операции
9. Спроектировать участок механического цеха
10. Провести научные исследования по повышению стойкости режущего инструмента и повышению производительности обработки
11. Рассмотреть мероприятия по обеспечению безопасности и экологичности проекта
12. Определить экономическую эффективность проекта.
2. Определение типа производства
2.1 Выбор и проектирование заготовки Задача данного раздела — в зависимости от детали и годового объема выпуска определить тип производства и на его базе выбрать оптимальную стратегию разработки технологического процесса
2.1.1 Определение типа производства Тип производства определяем с учетом годовой программы, массы детали и качественной оценки трудоемкости ее изготовления. По трудоемкости данную деталь можно отнести к деталям средней трудоемкости.
Определим массу детали по формуле:
кг (2.1)
где с — плотность материала, для стали 30ХМ, принимаем с = 0,0785 кг/см3;
V — объем детали, см3
Объем детали определяем как алгебраическую сумму объемов тел за вычетом полых цилиндрических составляющих и сегментов, входящих в конфигурацию детали:
Зная объем детали и плотность материала, из которого сделана деталь, определяем массу детали:
Тип производства зависит от годового объема выпуска деталей, ее массы и трудоемкости. По трудоемкости данную деталь можно отнести к деталям средней трудоемкости, поэтому при годовом объеме выпуска N = 15 000 шт /год и массе детали m =2,56 кг по] принимаем тип производства — среднесерийное.
Рассчитаем объем партии запуска изделий, шт:
(2.2)
где Nг — годовой объем выпуска деталей;
F — число рабочих дней в году.
2.1.2 Выбор стратегии разработки технологического процесса Задача данного подраздела — в зависимости от типа производства выбрать оптимальную стратегию разработки технологического процесса — принципиальный подход к определению его составляющих (показателей ТП), способствующей обеспечению заданного выпуска деталей заданного качества с наименьшими затратами.
1. В области организации технологического процесса:
Вид стратегии — последовательная, в отдельных случаях циклическая; линейная, в отдельных случаях разветвленная; жесткая, в отдельных случаях адаптивная;
· Форма организации технологического процесса — переменно-поточная форма организации технологического процесса
· Повторяемость изделий — периодически повторяющиеся партии
2. Метод получения заготовки:
· Оптимальный вариант получения заготовки — прокат или штамповка на ГКМ;
· Выбор последовательности обработки — по таблицам с учетом коэффициентов удельных затрат;
· Припуск на обработку — незначительный;
· Метод определения припусков — табличный.
3. В области разработки технологического процесса:
· Степень унификации ТП — разработка технологического процесса на базе типового ТП;
· Степень детализации разработки ТП — маршрутный или маршрутно-операционный технологический процесс;
· Принцип формирования маршрута — концентрация операций и совмещение по возможности переходов;
· Обеспечение точности — работа на настроенном оборудовании, с частичным применением активного контроля;
· Базирование — с соблюдением принципа постоянства баз и по возможности принципа единства баз на последующих операциях технологического процесса;
4. В области выбора средств технологического оснащения (СТО):
· Оборудование — универсальное, в том числе с ЧПУ, специализированные;
· Приспособления — универсальные, стандартные, нормализованные, специализированные;
· Режущие инструменты — стандартные, нормализованные, специальные;
· Средства контроля — универсальные, специальные
5. В области проектирования технологических операций:
· Содержание операций — одновременная обработка нескольких поверхностей, исходя из возможностей оборудования;
· Загрузка оборудования — периодическая смена детали на станках, коэффициент закрепления операций от 10 до 20;
· Расстановка оборудования — по группам станков, предметно замкнутые участки;
· Настройка станков — по измерительным инструментам и приборам или работа без предварительной настройки по промерам.
6. В области нормирования технологического процесса:
· Определение режимов резания — по общемашиностроительным нормативам и эмпирическим формулам;
· Нормирование — детальное пооперационное;
· Квалификация рабочих — средняя;
· Технологическая документация — маршрутные и операционные карты.
Принятой стратегией будем руководствоваться при разработке технологического процесса изготовления вала.
2.2 Выбор и проектирование заготовки Задача данного подраздела — выбрать методы получения заготовки и обработки поверхностей, обеспечивающих минимум суммарных затрат на получение заготовки и ее обработку.
2.2.1 Выбор метода получения заготовки Учитывая конструкцию изготавливаемого вала и материал заготовки — сталь 30ХМ, можно предложить два основных альтернативных метода получения заготовки:
1. Прокат;
2. Штамповка на ГКМ.
1. Прокат По ГОСТ 2590–71 определим диаметр прутка для данной заготовки:
1) определим припуск на механическую обработку шейки вала наибольшего диаметра:
(2.3.)
где Dдmin — наименьший предельный размер расчетной ступени по чертежу, мм;
2 Zomin — расчетный минимальный общий припуск на обработку по диаметру, мм;
Определим значение минимального припуска после каждой операции по формуле:
(3.3)
где Rz, h, мм — высота неровностей и дефектный слой, образовавшиеся на обрабатываемой поверхности при предыдущей обработке;
i, ммсуммарное значение пространственных отклонений;
уi, мм — погрешность установки.
Суммарное значение пространственных отклонений определим по формуле:
(3.4)
где к.о. -общая кривизна заготовки (учитывается на первой операции механической обработки);
см — величина смещения заготовки, т.к. обработка ведется в патроне за величину смещения принимаем отклонение от соосности.
Общая кривизна заготовки:
(3.5)
где к — удельная изогнутость и коробление заготовки, мкм/мм;
l — длина заготовки, мм. Так как допустимая кривизна реза прутка не должна превышать 5 мм, длина заготовки составляет 209,5 мм.
Погрешность установки для однопозиционной обработки:
(3.6)
где б — погрешность базирования;
з — погрешность закрепления.
Так как при обработке диаметра измерительные и технологические базы совпадают, погрешность базирования б = 0 при всех установках заготовки.
2) по рассчитанному диаметру определяем ближайший диаметр заготовки из сортового проката: Dз = 95 мм.
Для проведения в дальнейшем технико-экономического обоснования выбора заготовки необходимо определить коэффициент использования материала для данного метода.
Коэффициент использования материала определим по формуле:
Ки1=q/Q, (2.2.)
где q — масса детали, q = 2,56 кг (см. п. 2.1.1.);
Qмасса заготовки Объем заготовки:
Зная объем детали и плотность материала, определяем массу заготовки:
Подставив полученные значения масс детали и заготовки в формулу 2.2., получим коэффициент использования материала для отрезки из проката: Ки1=2,56/11,653=0,22.
2. Штамповка на ГКМ Ведем расчет поковки по ГОСТ 7505–89.
Исходные данные для расчета.
Ориентировочная величина расчетной массы поковки, кг:
(2.2.)
где МД -масса детали, кг;
Кр — расчетный коэффициент, устанавливаемый в соответствии с приложением 3 (табл.20).
Класс точности — Т5 (приложение 1).
Группа стали — М1 (табл.1).
Степень сложности — С3 (приложение 2).
Конфигурация поверхности разъема штампа — П (плоская) (табл.1)
Исходный индекс — 9 (табл.2).
По табл. 3 ГОСТ 7505–89 определяем припуски на механическую обработку, рассчитываем размеры поковки и их допустимые отклонения, учитывая дополнительные припуски, по табл. 8 ГОСТ 7505–89 назначаем допуски поковки. Все значения вносим в таблицу 2.1.
Таблица 2.1 Допуски и припуски на размеры поковки
Размер детали, мм | Поверхн-ти, на которые назначается припуск | Допуск на размер поковки, мм | Припуск, мм | Расчет размера поковки | Окончатль-ный размер (учитывая округления до 0,5 мм) | |
1,4 | 1,4 | 87+2(1,4+0,3+0,4) | ||||
1,4 | 1,4 | 63+2(1,4+0,3+0,4) | ||||
1,4 | 1,5 | 45+2(1,5+0,3+0,4) | ||||
19,5 | 1,2 | 1,3 | 19,5+(1,3+0,3+0,4) | 21,5 | ||
1,2 | 1,4 | 21+(1,4+0,3+0,4) | ||||
Остальные требования по ГОСТ 7505–89 | ||||||
Дополнительные припуски, учитывающие:
смещение по поверхности разъема штампа — 0,3 мм (табл.4);
изогнутость и отклонения от плоскости и от прямолинейности — 0,4 мм (табл.5);
Радиус закругления наружных углов — 4,0 мм (табл.7).
Штамповочный уклон — 7 (табл.18).
Для проведения в дальнейшем технико-экономического обоснования выбора заготовки необходимо определить коэффициент использования материала для данного метода. Коэффициент использования материала определим по формуле 2.2.
Объем заготовки определяем как алгебраическую сумму объемов тел за вычетом полых цилиндрических составляющих и сегментов, входящих в конфигурацию заготовки:
Зная объем детали и плотность материала, определяем массу заготовки:
Подставив полученные значения масс детали и заготовки в формулу (2.2.), получим коэффициент использования материала для ковки на горизонтально-ковочных машинах: Ки2=2,56/4,86=0,53.
Для окончательного решения по выбору метода получения заготовки, следует провести сравнительный экономический анализ по технологической себестоимости.
2.2.2 Экономическое обоснование выбора метода получения заготовки Оценку эффективности различных вариантов получения заготовок чаще всего проводят по двум показателям:
а) коэффициенту использования материала заготовки (см. формулу 2.2.)
б) технологической себестоимости изготовления детали. Сюда включаются только те статьи затрат, величины которых изменяются при переходе одного варианта к другому.
На стадии проектирования технологических процессов оптимальный вариант заготовки, если известны массы заготовки и детали, можно определить путем сравнения технологической себестоимости изготовления детали, рассчитанной по формуле:
Sтд = Sзаг?Q + Sмех(Q-q) — Sотх(Q-q), (2.3.)
где Sзаг -стоимость одного кг заготовки, руб/кг;
Sмех — стоимость механической обработки, отнесенная к одному кг срезаемой стружки, руб/кг;
Sотх — цена 1 кг. отходов, руб/кг, Sотх = 0,0144 руб/кг;
Sмех = Sс + Ен?Sк, (2.4.)
где Sс — текущие затраты на 1 кг стружки, руб/кг;
Sк — капитальные затраты на 1 кг стружки, руб/кг;
По табл. 3.2 [Технология отрасли] для автомобильного и сельскохозяйственного машиностроения Sс = 0,188 руб/кг, Sк = 0,566 руб/кг.
Ен — нормативный коэффициент эффективности капитальных вложений, Ен = 0,15.
Смех = 0,188 + 0,15?0,566 = 0,273 руб/кг.
Это значение принимаем для обоих методов получения заготовки.
Стоимость заготовки, полученной методом проката:
(2.5.)
где М — затраты на материал заготовки, руб
(2.6.)
где Qмасса заготовки, кг;
Sцена 1 кг материала заготовки, руб;
q — масса готовой детали, кг;
где Со.з. — технологическая себестоимость операций правки, калибрования прутков, разрезки их на штучные заготовки:
(2.6.)
где Сп.з. — приведенные затраты на рабочем месте, руб/ч;
Тшт (ш-к) — штучное или штучно-калькуляционное время выполнения заготовительной операции (правки, калибрования, резки и др.).
Подставим рассчитанные значения в формулу (2.)
Стоимость заготовки, полученной методом ковки на ГКМ с достаточной для стадии проектирования точностью можно определить по формуле:
Сзаг = Сi/1000 kт kc kв kм kп, (2.5.)
где Сi — базовая стоимость одного 1 т поковки, полученной на ГКМ, руб.:
Сi = 0,725 руб;
kт — коэффициент, зависящий от класса точности, для поковок нормального класса точности:
kт = 1;
kc — коэффициент, зависящий от группы сложности поковки, для третьей группы сложности:
kc =1,0;
kв — коэффициент, зависящий от марки материала и массы поковки, для стали 40Х при массе поковки менее 10 кг:
kв =0,8;
kм — коэффициент, зависящий от марки материала поковки, для стали 30ХМ:
kм = 1;
kп — коэффициент, зависящий от объема производства поковок и группы серийности:
kп = 1;
Подставим определенные значения в формулу (2.5.):
Сзаг = Сi/1000 kт kc kв kм kп
Подставим полученные данные в формулу (2.3) и рассчитаем технологическую себестоимость изготовления детали, для двух методов получения заготовки:
— для проката:
Стд1 = 0,293,12+ 0,273 (3,12−2,2) — 0,0144(3,12−2,2)= 1,143 руб.;
— для штамповки на ГКМ:
Стд2 = 0,8212,64+ 0,273 (2,64−2,2) — 0,0144(2,64−2,2) = 2,281 руб.
Расчеты проведены в ценах 1985 года. Для учета ценовой инфляции введем коэффициент К = 10 000. Тогда стоимость заготовки:
— для литья в земляные формы Сзаг1=0,29 810 000=2980 руб;
— для литья в оболочковые формы Сзаг2=0,82 110 000=8210 руб.
Полная себестоимость с учетом коэффициента инфляции составит:
— для литья в земляные формы Стд1=11 430 руб;
— для литья в оболочковые формы Стд2=22 810 руб.
Вывод: по результатам проведения сравнительного анализа технологической себестоимости двух методов получения отливки можно заключить, что экономически целесообразнее использовать при получении заготовки детали метод ковки на горизонтально-ковочной машине, т.к. полная себестоимость получения заготовки этим методом существенно ниже чем методом отрезки сортового проката.
Экономический эффект при изготовлении детали из заготовки полученной ковкой на ГКМ, по сравнению с изготовлением детали резкой сортового проката для годовой программы выпуска-15 000 шт. составит:
Э=(Стд2 — Стд1)· N= (22 810−11 430)· 15 000=170700000 руб.
3. Технологический маршрут и план изготовления детали
3.1 Обоснование технологического маршрута изготовления детали. План изготовления детали Задача раздела — разработать оптимальный технологический маршрут, т. е. такую последовательность операций, которая обеспечит получение из заготовки готовой детали с наименьшими затратами, при этом необходимо разработать такую схему базирования заготовки на каждой операции, которая обеспечила бы минимальную погрешность обработки.
Тип производства — среднесерийное;
Способ получения исходной заготовки — штамповка на ГКМ;
Метод достижения точности — по настроенному оборудованию.
На рисунке 1.1. представлена схема кодирования детали, т. е. изображен эскиз детали с пронумерованными поверхностями и буквенными обозначениями чертежных размеров.
Технологический маршрут, выбранный в соответствии рекомендациям [Выбор маршрутов обработки поверхностей деталей машин. Сост. Михайлов А. В., Пашко Н. М.] представлен в таблице 3.1:
Таблица 3.1 Технологический маршрут изготовления детали
№ операции | Наименование операции | Оборудование (тип, модель) | Содержание операции | Точ-ность (IT) | Ra, мкм | |
Заготовительная | Горизонтально-ковочная машина | |||||
Фрезерно-центровальная | Фрезерно-центровальный п/а МР-71М | переход1: фрезеровать торцы 1,17 | ||||
переход 2: сверлить центровые отверстия 47 и 48 | ||||||
Токарная | Токарно-винторезный станок 16Б16П | Установ, А точить пов. 13,46,11,8. | 12,5 | |||
Установ Б точить пов. 2, 3,4,6 | 12,5 | |||||
Токарная | Токарно-винторезный станок 16Б16П | Установ, А точить точить пов. 13,46,11,8. | 6,3 | |||
Установ Б точить пов. 2, 3,4,6 | 6,3 | |||||
Токарная с ЧПУ | Токарно-винторезный станок 16К20Ф3 | Установ, А точить пов. 17,13,12,11,10,9,8,7, 3…6, фаски, уклоны и канавки | 2,5 | |||
Токарная | Токарно-винторезный станок 1А616П | Установ А: переход1: сверлить отв. 38, | 6,3 | |||
переход 2: зенкеровать пов. 38,40,41, | 2,5 | |||||
переход 3: нарезать резьбу пов.39 | 7 ст. | 2,5 | ||||
Установ Б: сверлить отв. 28 | ||||||
Сверлильно-фрезерная | Сверлильно-фрезерно-расточной станок 2254ВМФ4 | Установ, А переход 1: сверлить 14 отв. пов.22 | ||||
переход 2: зенкеровать 14 отв.22 | ||||||
переход 3: нарезать резьбу в отв.22 | 7 ст. | 2,5 | ||||
переход 4: сверлить 7 отв. 33 и отв 26 | ||||||
переход 5: фрезеровать 7 отв. 33 и отв 26 | ||||||
Фрезерная | Специальный консольно-фрезерный станок ГФ-792 | переход 1: фрезеровать шпон. паз (пов. 14,15,16) | ||||
переход 2: фрезеровать шпон. паз (пов. 14,15,16) | ||||||
переход 3: сверлить отв.35 | ||||||
переход 4: сверлить отв.47 | ||||||
Термическая | Печь индукционная | Закалить, отпустить, пов. 24,40,41 защитить от окалины | +1 на все поверхности кроме 24,40, 41 | |||
Очистная | Очистить от окалины | |||||
Плоскошлифовальная | Плоскошлифовальный станок 3П756Л | Шлифовать торец 1 | 2,5 | |||
Круглошлифовальная | Круглошлифовальный станок 3М150 | Шлифовать пов. 13 8 и 6, торец 5 | 1,25 | |||
Круглошлифовальная | Круглошлифовальный станок 3М150 | Шлифовать пов. 13 8 и 6 | 0,63 | |||
Токарная | Токарно-винторезный станок 1А616П | Установ, А Полировать пов. 11 | ; | 0,32 | ||
Установ Б Притереть пов. 33 и 26 | ; | 0,16 | ||||
Слесарная | Верстак слесарный | Притупить острые кромки, маркировать электрографом согл. ТТ | ; | ; | ||
Моечная | Моечная машина | ; | ; | |||
Азотирование | Печь для азотирования | согл. ТТ | ; | ; | ||
Контрольная | ; | ; | ; | ; | ||
План изготовления детали
План изготовления — графическое изображение технологического маршрута с указанием теоретических схем базирования и технических требований на операции.
План изготовления состоит из четырех граф:
Графа «Операция», которая включает в себя название и номер операции.
Графа «Оборудование», которая включает в себя оборудование, при помощи которого производится обработка поверхностей на данной операции.
Графа «Операционный эскиз», которая включает в себя изображение детали, схему базирования (точки закрепления), простановку операционных размеров, обозначение обрабатываемых поверхностей и указание шероховатости получаемой на данной операции.
Графа «Технические требования», которая включает в себя допуски на операционные размеры и отклонения формы.
План изготовления корпуса внутреннего шарнира представлен на листе 05. М15.269.08. графической части.
3.2 Выбор технологических баз Теоретическая схема базирования представлена на плане изготовления детали и представляет собой схему расположения на технологических базах заготовки «идеальных» точек, символизирующих позиционные связи заготовки с принятой схемой координат станочного приспособления.
При разработке схем базирования учитываем принцип и единства баз: на всех операциях обработки по возможности использовать одну и ту же базу, как установочную, так и измерительную и принцип постоянства баз: на всех операциях обработки необходимо применять по возможности одни и те же базы. Также важно учитывать правило шести точек, при котором деталь базируется на шести неподвижных точках, которые лишают её шести степеней свободы. Обработку детали начинаем с поверхности, которая служит опорной базой для дальнейших операций. Для обработки этой поверхности в качестве опорной базы приходится принимать необработанную поверхность. После этого, когда она обработана, обрабатываем остальные поверхности, соблюдая при этом определённую последовательность, сначала обрабатываем поверхность, к точности которой предъявляются меньшие требования, а потом поверхности, которые должны быть более точными.
Операции согласно типовому технологическому процессу изготовления разбиваем на установы. Индекс около номера поверхности обозначает номер операции, на которой она получена. Индекс 00 — относится к заготовительной операции, буквы А, Б — указывают, что поверхность обработана на данной операции с установа, А или Б. Арабские цифры 1,2,3 и т. д. обозначают переход на котором был получен данный размер.
В связи с тем, что вал представляет собой тело вращения, первоначально заготовка обрабатывается на станках токарной группы.
На 005 фрезерно-центровальной операции в качестве черновых технологических баз используем технологические базы, указанные на чертеже заготовки (см. чертеж 05. М15.269.15) ими являются цилиндрическая поверхность 6 и торцовая поверхность 5. Ось материализуем наружными цилиндрическими поверхностями.
На 010 и 015 токарных операциях и на 020 токарной операции с ЧПУ на установе, А в качестве двойной направляющей базы используем ось поверхности 2, в качестве опорной базы торец 1; на установе Б — в качестве двойной опорной базы используем ось поверхности 13, в качестве опорной базы торец 17. В качестве опорной базы принимаем, в зависимости от установа, пов.2 и 13 соответственно.
На 025 сверлильной на установе, А в качестве двойной направляющей базы используем ось поверхности 2, в качестве опорной базы торец 1; на установе Б — в качестве двойной направляющей базы используем ось поверхности 13, в качестве опорной базы торец 5. В качестве опорной базы принимаем, в зависимости от установа, пов.2 и 13 соответственно.
На 030 сверлильно-фрезерной, 050 плоскошлифовальной, 065 полировальной операциях в качестве направляющей базы используем ось поверхности 8, в качестве установочной базы торец 17, в качестве опорной базы принимаем пов.8.
На 035 фрезерной операции на в качестве двойной направляющей базы используем ось поверхности 6, в качестве опорных баз торец 1 и цилиндрическую поверхность На 055 и 060 круглошлифовальных операциях двойной направляющей базой является ось. Поверхности 17 и 27, использующиеся для простановки в них специальных центров используются в качестве опорных баз.
Сведем все данные по технологическим базам и размерам получаемым на операциях ТП в таблицу 3.2.
Таблица 3.2 Технологические базы
№ операции | Название | № опорных точек | Характер появления | Реализация | Операционные размеры | Единство баз | |||
Явная | Скрытая | Естественная | Искусственная | ||||||
ДН О О | 1,2,3,4 | ; | ; | 2Б10-А, 2Ж10-Б Z10-A, Э10-А, Э10-Б | |||||
У ДО О | 1,2,3 4,5 | ; | ; | 2Б20-Б, 2Ж20-А, ДЮ20-А, 2J20-Б Z20-Б, Э20-Б F20-Б, G20-A | ; | ||||
У ДО О | 1,2,3 4,5 | ; | ; | 2Ж30-А, 2Б30-Б Z30-Б | ; | ||||
У ДО О | 1,2,3 4,5 | ; | ; | 2 М40−1, 2И40−4, 2Т40−3, 2Т40−2, 2ХХ40 СК20-А, Z20-Б, | ; | ||||
У ДО О | 1,2,3 4,5 | ; | ; | V50-Б, 2Д50-Б, Е50-А, 2Ф50-А, 2Щ50-А, 2Г50-А, 2Н50, 2П50 ИЬ50-А, МИ50, КК50, МХ50 | ; | ||||
У ДО О | 1,2,3 4,5 | ; | ; | 2Х60, 2Ш60, Ъ60 БЛ60, СЕ60 | ; | ||||
3.3 Обоснование простановки операционных размеров
Способ простановки операционных размеров выбираем в зависимости от метода достижения точности. Для выполнения выше рассмотренных операций применяем метод достижения точности размеров с помощью настроенного оборудования. В этом случае имеет место несколько вариантов простановки операционных размеров, получение которых зависит от технологических возможностей применяемого оборудования. Так как при разработке технологического процесса изготовления детали использовалось стандартное и универсальное оборудование, то было бы целесообразно применить координатный способ простановки операционных размеров. Токарные станки с ЧПУ применяемые при обработке могут реализовывать выше описанную схему простановки операционных размеров, или схему простановки операционных размеров, когда нуль детали перемещен на правый крайний торец.
В нашем случае при чистовой обработке используем первую схему простановки операционных размеров.
3.4 Назначение операционных технических требований
1. Заготовительная операция: все требования предъявляемые к поковке по качеству и точности назначаем согласно рекомендациям ГОСТ 7505–89 (см. п. 2.2.).
2. Допуски на операционные размеры в осевом направлении рассчитываем по следующим формулам:
— для операции 005 — фрезерно-центровальной:
TAi = icт+ с.ш., (3.1)
где TAi — допуск на размер, А на i-той операции;
icт — статистическая погрешность на i-той операции;
с.ш. — смещение штампа, возникающее на заготовительной операции;
(смещение штампа не учитывается при определении допусков на центровые отверстия и на габаритный размер);
— для остальных операций:
TAi = icт + i, (3.2)
где TAi — допуск на размер, А на i-ой операции;
icт — статистическая погрешность на i-той операции;
i— величина торцового биения, определяемая по прил.2 [РАЗМЕРН].
На операциях, в которых единство баз не соблюдается:
TAi = icт + I + б, (3.3)
где б — погрешность базирования
2. Допуски на диаметральные размеры назначаются, исходя из квалитета точности, который обеспечивает оборудование в радиальном направлении. Его выбираем по прил.1 [РАЗМЕРН], значения допусков берутся из [поля допусков].
3. Значения погрешностей формы на диаметральные размеры назначаем, руководствуясь прил.2 [РАЗМЕРН]. Величина отклонения от соосности определяется как половина погрешности радиального биения.
4.Шероховатость, получаемую при обработке поверхностей, назначаем с учетом рекомендаций (прил. 1[РАЗМЕРН]).
5. Для операции 040 термической:
Определяем приведенный средний диаметр вала:
dср = (d1l1 + d2l2+…+ dnln)/l (3.3)
где d1, d2, dn— диаметры ступеней;
l1, l2, ln — длины ступеней;
l — общая длина вала.
dср = (8719,5 + 631,5+45 103,5+4020+3060)/204,5= 48,87 мм;
В табл.4.8 [горбац] находим к — величину удельной изогнутости оси вала:
к = 0,8 мкм/мм = 0,008, затем вычисляем значения отклонений от соосности при термообработке по формуле:
i = кli, (3.4)
где к — величина удельной изогнутости оси вала,;
li — длина i — той ступени вала.
1 = 0,819,5=0,156 мм;
2 = 0,0081,5=0,012 мм;
3 = 0,8 103,5 = 0,828 мм;
4 = 0,820=0,16 мм;
5 = 0,860=0,048 мм.
4. Выбор средств технологического оснащения (СТО) Задача раздела — выбрать для каждой операции ТП такие оборудование, приспособление, режущий инструмент (РИ) и средства контроля, которые бы обеспечили заданный выпуск деталей заданного качества с минимальными затратами.
4.1 Выбор оборудования При выборе типа и модели металлорежущих станков будем руководствоваться следующими правилами:
1. Производительность, точность, габариты, мощность станка должны быть минимальными, но достаточными для того, чтобы обеспечить выполнение требований предъявляемых к операции.
2. Станок должен обеспечить максимальную концентрацию переходов на операции в целях уменьшения числа операций, количества оборудования, повышения производительности и точности за счет уменьшения числа перестановок заготовки.
3. В случае недостаточной загрузки станка его технические характеристики, должны позволять обрабатывать другие детали, выпускаемые данным цехом или участком.
4. Оборудование не должно быть дефицитным, но в достаточной степени модернизированным
5. В серийном производстве наряду со станками с ЧПУ и обрабатывающими центрами следует применять специализированные станки, гибкие технологические модули, гибкие автоматические линии. На каждом станке в месяц должно выполняться не более 40 операций при смене деталей по определенной закономерности.
6. Оборудование должно отвечать требованиям безопасности, эргономичности и экологии.
Выбор оборудования проводим, используя рекомендации [коил] в следующей последовательности:
1. Исходя из формы обрабатываемой поверхности и метода обработки, выбираем группу станков;
2. Исходя из положения обрабатываемых поверхностей, выбираем тип станка;
3. Исходя из габаритных размеров заготовки, размеров обрабатываемых поверхностей и точности обработки выбираем типоразмер станка.
Данные по выбору оборудования заносим в таблицу 4.1.
Выбор оборудования.
Номер операции | Станок | Наибольшие габариты заготовки, мм | Мощность главного привода кВт | Частота вращения шпинделяоб/мин | Габариты станка, мм | Масса, т | |
Фрезерно-центровальный п/а МР-71М | 125Ч500 | 18,6 | 125−712 238−1125 | 3140Ч1630Ч1740 | 6,1 | ||
Токарно-винторезный станок 16А616П | 160Ч710 | 9−1800 | 2135Ч1225Ч1220 | 1,5 | |||
Токарно-винторезный станок с ЧПУ 16К20Ф3 | 400Ч1000 | 12,5−2000 | 3360Ч1710Ч1750 | ||||
Сверлильно-фрезерныйрасточной станок 225ВМФ4 | 630Ч400 | 6,3 | 32−2000 | 4300Ч3500Ч3800 | 6,5 | ||
Специальный фрезерный консольный станок ГФ-792 | 320Ч1250 | 31,5−1600 | 2560Ч1745Ч1660 | 3,4 | |||
Плоскошлифовальный станок 3П732 | 800Ч320×375 | 3800Ч2130Ч2360 | 7,73 | ||||
055 060 | Круглошлифовальный станок 3М150 | 100Ч360 | 100−2000 | 2500Ч2220Ч1920 | 2,6 | ||
4.2 Выбор приспособлений При выборе приспособлений будем руководствоваться следующими правилами:
1. Приспособление должно обеспечивать материализацию теоретической схемы базирования на каждой операции с помощью опорных и установочных элементов
2. Приспособление должно обеспечивать надежное закрепление заготовки при обработке
3. Приспособление должно быть быстродействующим
4. Зажим заготовки должен осуществляться по возможности автоматически
5. Следует отдавать предпочтение стандартным нормализованным, универсально-сборным приспособлениям, и только при их отсутствии проектировать специальные приспособления Исходя из типа, модели станка и метода обработки выбираем тип приспособления.
Выбор приспособления, используя рекомендации [коил] будем производить в следующем порядке:
1. Исходя из расположения базовых поверхностей и их состояния (точность и шероховатость), формы заготовки и расположения обрабатываемых поверхностей выбираем конструкцию приспособления
2. Исходя из габаритов заготовки и размеров базовых поверхностей, выбираем типоразмер приспособления.
Данные по выбору приспособлений заносим в таблицу 4.2
Таблица 4.2 Выбор приспособлений.
Номер операции | Наименование операции | Приспособление | |
Фрезерно-центровальная | Специальное приспособление | ||
Токарная | Патрон 3-х кулачковый самоцентрирующий ГОСТ 2675–81; центр вращающийся ГОСТ 8472–75 | ||
Токарная | Патрон 3-х кулачковый самоцентрирующий ГОСТ 2675–81; стержень упорный, оправка коническая переходная ГОСТ 16 211–70; люнет неподвижный | ||
Сверлильно-фрезерно-расточная | Специальное приспособление | ||
Фрезерная | Универсально-сборное приспособление | ||
Плоскошлифовальная | Специальная магнитная плита с постоянными магнитами | ||
Круглошлифовальная | Патрон поводковый ГОСТ 2571–71; центр вращающийся ГОСТ 8472–75 | ||
Токарная | Патрон 3-х кулачковый самоцентрирующий ГОСТ 2675–81 | ||
После выбора приспособлений получили следующее:
1. Приспособления обеспечивают материализацию теоретической схемы базирования на каждой операции.
2. Приспособления обеспечивают надежное закрепление заготовки при обработке.
3. Приспособлениябыстродействующие.
4.3 Выбор режущего инструмента
При выборе режущего инструмента будем руководствоваться следующими правилами:
1. Выбор инструментального материала определяется требованиями, с одной стороны максимальной стойкости, а с другой минимальной стоимости.
2. Следует отдавать предпочтение нормализованным и стандартным инструментам.
Выбор режущего инструмента будем производить в следующем порядке:
1. Исходя из типа и модели станка, расположения обрабатываемых поверхностей и метода обработки, определяем вид режущего инструмента
2. Исходя из марки обрабатываемого материала его состояния и состояния поверхности, выбираем марку инструментального материала
3. Исходя из формы обрабатываемой поверхности, назначаем геометрические параметры режущей части инструмента
4. Исходя из размеров обрабатываемой поверхности, выбираем конструкцию инструмента Данные по выбору режущего инструмента заносим в таблицу 4.3
Таблица 4.3 Выбор режущего инструмента
№ операции | Наименование операции | ИМ | Режущий инструмент | |
Фрезерно-центровальная | Р6М5 | Сверло центровочное комбинированное Ш 6 ГОСТ 14 952–75 | ||
Фреза | ||||
Токарная | Т15К6 | Резец для контурного точения с углом в плане 93є, ТУ-2−035−892−82 | ||
Токарная | Т15К6 | Резец вставка для контурного точения с углом в плане 93є, ТУ-2−035−892−82 | ||
Токарная с ЧПУ | Т15К6 | Резец вставка для контурного точения с углом в плане 93є, ТУ-2−035−892−82 | ||
Сверлильная | Р6М5 | Сверло ступенчатое комбинированное под резьбу М12 ОСТ 2И21−1-76 | ||
Р18 | Зенкер четырехперый насадной | |||
Р6М5 | Метчик М12−7Н ГОСТ 3266–81 | |||
Р6М5 | Сверло спиральное Ш 6 с цилиндрическим хвостовиком сверхдлинная серия ТУ 2−035−600−77 | |||
Сверлильно-фрезерно-расточная | Р6М5 | Сверло спиральное Ш 4 с цилиндрическим хвостовиком короткая серия ГОСТ 4010–77 | ||
Р18 | Зенкер Ш 4,5 цельный ГОСТ 12 489–71 | |||
Р6М5 | Метчик М4−7Н ГОСТ 3266–81 | |||
Р6М5 | Сверло спиральное центровочное с коническим хвостовиком для зацентровки под сверление Ш8 ОСТ 2 И21−2-76 | |||
Р6М5 | Фреза специальная Ш 22 | |||
Р6М5 | Фреза специальная Ш 22 | |||
Фрезерная | Р6М5 | Сверло спиральное Ш 2,5 с цилиндрическим хвостовиком короткая серия ГОСТ 4010–77 | ||
Р6М5 | Зенкер Ш 4,5 цельный ГОСТ 12 489–71 | |||
Р6М5 | Фреза шпоночная немерная ТУ 2−035−858−82 | |||
Плоскошлифовальная | Электрокорунд белый | Круг шлифовальный с односторонней выточкой 250×20×50 25А 20 С1 6 К5 35м/с 1 кл, А ГОСТ 2424–75 | ||
Круглошлифовальная | Электрокорунд белый | Круг шлифовальный прямого профиля 200×30×40 25А 10 С2 6 К5 35м/с 1 кл, А ГОСТ 2424–75 | ||
Круглошлифовальная | Электрокорунд белый | Круг шлифовальный прямого профиля 200×30×40 25А 10 С2 6 К5 35м/с 1 кл, А ГОСТ 2424–75 | ||
Токарная | Лента абразивная | |||
4.4 Выбор средств контроля При выборе средств контроля будем, используя рекомендации [коил] и руководствоваться следующими правилами:
1. Точность измерительных инструментов и приспособлений должна быть существенно выше точности измеряемого размера, однако оправданное повышение точности ведет к резкому удорожанию.
2. В мелкосерийном производстве следует применять инструменты общего назначения, специальные и универсальные.
3. Следует отдавать предпочтение стандартным и нормализованным средствам контроля.
Данные по выбору средств контроля заносим в таблицу 4.
Таблица 4.4 Выбор средств контроля
Номер операции | Наименование операции | Средство контроля | |
Фрезерно-центровальная | Штангенциркуль ШЦ-III ГОСТ 166–80 Калибр-пробка гладкий ГОСТ 24 853–81 | ||
Токарная | Штангенциркуль ШЦ-III ГОСТ 166–80 Скоба-рычажная ГОСТ 11 098–75 | ||
Токарная | Штангенциркуль ШЦ-III ГОСТ 166–80 Скоба-рычажная ГОСТ 11 098–75 | ||
Токарная с ЧПУ | Штангенциркуль ШЦ-III ГОСТ 166–80 Скоба-рычажная ГОСТ 11 098–75 | ||
Токарная | Штангенциркуль ШЦ-III ГОСТ 166–80 Калибры-пробки гладкие ГОСТ 24 853–81 Калибр — резьбовой ГОСТ 24 939–81 | ||
Сверлильно-фрезерно-расточная с ЧПУ | Штангенциркуль ШЦ-III ГОСТ 166–80 Штангеглубиномер ШГ-160 ГОСТ 1 62−80 Калибры-пробки гладкие ГОСТ 24 853–81 Калибр — резьбовой ГОСТ 24 939–81 | ||
Фрезерная | Калибры-пробки гладкие ГОСТ 24 853–81 Штангенциркуль ШЦ-III ГОСТ 166–80 | ||
Плоскошлифовальная | Штангенрейсмас ШР ГОСТ 164–90 | ||
Круглошлифовальная | Датчик активного контроля БВ-4100 Микрометр рычажный ГОСТ 4381–87 | ||
Круглошлифовальная | Датчик активного контроля БВ-4100 Микрометр рычажный ГОСТ 4381–87 | ||
Токарная | Профилограф-профилометр А1 ГОСТ 19 299–73 | ||
Контрольная | Приспособление специальное для контроля биения отверстия; Профилограф-профилометр А1 ГОСТ 19 299–73 | ||
5. Размерный анализ в радиальном направлении Для выполнения размерного анализа будем использовать упрощенный вид детали без фасок, канавок для выхода инструмента, т. е. без тех поверхностей, которые не влияют на эксплуатационные качества детали. Также исключим из рассмотрения отверстия для крепления вала к фланцу, так как заданные чертежом детали технические требования дают основание предположить, что они будут обеспечены без особого труда.
5.1 Размерные цепи и их уравнения Уравнения операционной размерной цепи (ОРЦ) составляем из размерной схемы в радиальном направлении, основанной на плане изготовления детали. Размерная схема представляет собой графическую информацию об операционных размерах, припусках, размерах детали и заготовки. Уравнения ОРЦ записываются относительно замыкающего звена, которым может быть либо припуск, либо чертежный размер (размер детали) полученный косвенно в результате выполнения операционных размеров. Более одного замыкающего звена в уравнении быть не должно. Уравнения ОРЦ составляются по замкнутому контуру с учетом знаков увеличивающих и уменьшающих звеньев.
Уравнение номиналов в общем виде:
[A] = , (5.1.)
где [A] - номинальное значение замыкающего звена;
Ai — номинальные значения составляющих звеньев;
i — порядковый номер звена;
n — число составляющих звеньев;
i — передаточные отношения, характеризующие расположение звеньев по величине и направлению.
Для линейных цепей с параллельными звеньями передаточные звенья равны: i = 1 (увеличивающие звенья); i = -1 (уменьшающие звенья).
Знак составляющего звена определяем по правилу: составляющее звено является увеличивающим (i = 1), если вектор движения по нему при обходе размерного контура противоположен вектору движения по замыкающему звену.
Число уравнений ОРЦ должно быть равно числу замыкающих звеньев. Уравнения ОРЦ в радиальном направлении имеют одну особенность: звенья-несоосности в уравнении номиналов должны иметь только положительные знаки (т. е. принимаем за худший тот случай, когда звенья-несоосности будут направлены в одну сторону с припуском).
Составим уравнения ОРЦ замыкающих звеньев в радиальном направлении. В данном случае замыкающими звеньями являются припуски и отклонения от соосности, полученные в результате выполнения операционных размеров.
Уравнение замыкающего звена:
[Е 11, 6] = Е 1140 4505 + Е 660 4505.
Уравнения замыкающих звеньев-припусков:
операция 010: [Z210-Б] = А00 + Е 200 600 + Е 610-Б 4505 + Е 210-Б 4505— А10-Б;
[Z410-Б] = Б00 + Е 400 600 + Е 610-Б 4505 + Е 410-Б 4505— Б10-Б;
[Z610-Б] = В00 — В10-Б;
операция 015: [Z215-Б] = А10-Б + Е 210-Б 4505+ Е 215-Б 4505-А15-Б;
[Z415-Б] = Б10-Б + Е 410-Б 4505+ Е 415-Б 4505-Б15-Б;
[Z615-Б] = В10-Б + Е 610-Б 4505+ Е 615-Б 4505-В15-Б;
[Z1115-А] = Е10-А + Е 1110-А 4505+ Е 1115-А 4505-Е15-А;
[Z1315-А] = Ж10-А + Е 1310-А 4505+ Е1315-А 4505-Ж15-А;
операция 020: [Z420-Б] = Б15-Б + Е 415-Б 4505+ Е 420-Б 4505-Б20-Б;
[Z620-Б] = В15-Б + Е 615-Б 4505+ Е 620-Б 4505-В20-Б;
[Z1120-А] = Е15-А + Е 1115-А 4505+ Е 1120-А 4505-Е20-А;
[Z1320-А] = Ж15-А + Е 1315-А 4505+ Е1320-А 4505-Ж20-А;
операция 055: [Z655] = В20-Б + Е 620-Б 4505+ Е 640 4505-В55;
[Z1355-А] = Ж20-Б + Е 1320-Б 4505+ Е 1340 4505-Ж55-Б;
операция 060: [Z660] = В55 + Е 655 4505+ Е 660 4505-В60-Б;
[Z1360-А] = Ж55-Б + Е 1355-Б 4505+ Е 1360 4505-Ж60-Б.
5.2 Проверка условий точности изготовления детали Производим проверку обеспечения требований рабочего чертежа детали (по несоосности). Для этого должно соблюдаться условие корректности звеньев размерной цепи:
(5.3.)
где? Ai— погрешность iтого звена;
nчисло составляющих звеньев.
Значения эксцентриситетов принимаем приближенными к значениям половины радиального биения с плана изготовления детали, для соответствующих поверхностей и операций.
Ечерт [11, 6]? ??11, 6];
Ечерт [11, 6]=0,04;
Ечерт [11, 6]? Е 1140 4505 + Е 660 4505;
??11, 6]=;
0,02? ;
0,02? 0,16-условие не выполняется.
Вывод: условие корректности размерных звеньев цепи не выполняется, необходимо ввести дополнительную обработку размера 2Е. Соответственно уравнение замыкающего звена размерной цепи будет выглядеть следующим образом:
[Е 11, 6] = Е 1155 4505 + Е 660 4505.
Тогда: Ечерт [11, 6]? Е 1155 4505 + Е 660 4505;
??11, 6]=;
0,02? ;
0,02? 0,013-условие выполняется.
Вывод: условие корректности размерных звеньев цепи выполняется.
Кроме того появляется необходимость расчета дополнительного припуска на операции 055: [Z1155-Б] = Е20-Б + Е 620-Б 4505+ Е 640 4505-Е55-Б.
5.3 Расчёт радиальных припусков Определим минимальные значения операционных припусков по формуле:
— до черновых операций (операция 010):
Zimin=(Rz.+hi-1)+с.ш.; (5.4.)
— до чистовых операций (операция 015, 020):
Zimin=(Rz+h)i-1 (5.5.)
где Rz — шероховатость поверхности (с плана изготовления детали);
iномер операции;
hвеличина дефектного слоя [РАЗМ, приложение 5].
Для удобства расчетов сведем составляющие минимального припуска в таблицу 5.1.
Таблица 5.1. Составляющие минимального припуска Zmin
Наименование операции | Установ | Шероховатость | Дефектный слой, мм | Смещение на заготовительной операции, мм | ||
RZ, мм | Ra, мкм | |||||
000 Заготовительная | ; | 0,128 | 0,25 | 0,3 | ||
010 Токарная | Установ А, Установ Б | 0,05 | 12,5 | 0,1 | ||
0,05 | 12,5 | 0,1 | ||||
015 Токарная | Установ А | 0,0252 | 6,3 | 0,04 | ||
Установ Б | 0,0252 | 6,3 | 0,04 | |||
020 Токарная с ЧПУ | Установ А | 0,01 | 2,5 | 0,03 | ||
Установ Б | 0,01 | 2,5 | 0,03 | |||
055 Круглошлифовальная | Установ А | 0,005 | 1,25 | 0,02 | ||
Установ Б | 0,005 | 1,25 | 0,02 | |||
060 Круглошлифовальная | Установ А | 0,252 | 0,63 | 0,01 | ||
Установ Б | 0,252 | 0,63 | 0,01 | |||
операция 010: [Z210-Б] min = 0,128+0,25+0,3=0,678 мм;
[Z410-Б] min = 0,128+0,25+0,3=0,678 мм;
[Z610-Б] min = 0,128+0,25+0,3=0,678 мм;
операция 015: [Z215-Б] min = 0,05+0,1 = 0,15 мм;