Разработка методов и алгоритмов проектирования процессов формообразования тонкостенных профилей стесненным изгибом с устранением потери устойчивости краевых элементов
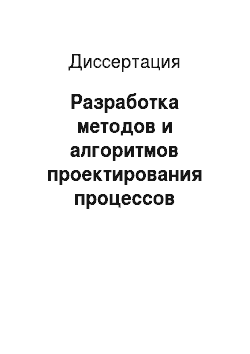
Устранить существующие недостатки гнутых профилей оказалось возможным при изготовлении их гибкой-прокаткой на специальных гибочно-прокатных станках методом стесненного изгиба. Характерной особенностью роликового инструмента является наличие уступа, который позволяет замкнуть рабочий контур с созданием в заготовке дополнительных сжимающих напряжений, компенсирующих растяжение наружных волокон угла… Читать ещё >
Содержание
- Основные обозначения и сокращения, принятые в работе
- 1. СОСТОЯНИЕ ВОПРОСА И ЗАДАЧИ ИССЛЕДОВАНИЯ
- 1. 1. Применение гнутых тонкостенных профилей в конструкциях летательных аппаратов
- 1. 2. Качественные характеристики профилей, изготовляемых различными технологиями и обоснование выбора изготовления методом стесненного изгиба в валковых парах
- 1. 3. Гибочно-прокатное оборудование
- 1. 4. Анализ работ по теоретическим и экспериментальным исследованиям процессов формообразования гнутых тонкостенных профилей в роликовых парах
- 1. 5. Анализ дефектов и причины их возникновения при формообразовании гнутых тонкостенных профилей по интенсивным режимам в валковых парах
- 1. 6. Постановка задач исследований процесса изготовления тонкостенных профилей методом стесненного изгиба с предотвращением потери устойчивости краевыми элементами и пути их решения
- 1. 7. Выводы
- 2. ТЕОРЕТИЧЕСКИЕ ИССЛЕДОВАНИЯ
- 2. 1. Исходные допущения при разработке моделей очагов деформации краевых подгибаемых элементов
- 2. 2. Моделирование процесса формообразования плоского подгибаемого элемента в очаге деформации предварительного перехода
- 2. 3. Критерий устойчивости плоской полки с продольными остаточными деформациями, полученными в процессе профилирования на переходах предварительного формообразования
- 2. 4. Оценка амплитуды кромковой волнистости при подгибке полок тонкостенных профилей на закритические углы
- 2. 5. Модель очага деформации многоэлементной подгибаемой полки тонкостенного профиля
- 2. 6. Модель очага деформации криволинейного подгибаемого элемента и условие устойчивости последнего после отформовки
- 2. 7. Амплитуда периодических изломов криволинейных полок при их подгибке на запредельные углы
- 2. 8. Оценка значений прогибов симметричных профилей и крутки асимметричных профилей от накопленных в процессе формообразования продольных остаточных деформаций
- 2. 9. Моделирование процесса формообразования профиля на окончательных переходах и формирование критерия устойчивости периферийных сжимаемых элементов
- 2. 10. Выводы
- 3. ЭКСПЕРИМЕНТАЛЬНЫЕ ИССЛЕДОВАНИЯ
3.1. Геометрические параметры очагов деформации краевых подгибаемых элементов и в зависимости от ширины элементов, геометрии поперечного сечения профилей, схем формообразования, механических свойств заготовок и межклетьевого расстояния.
3.2. Оценка уровня продольных остаточных деформаций в краевых элементах профилей прямым и косвенным методами.
3.3. Исследование зависимости предельных углов подгибки краевых элементов тонкостенных профилей на предварительных переходах от геометрических параметров элементов, межклетьевого расстояния и механических свойств заготовок.
3.4. Исследование процесса формообразования минимальных внутренних зон сгиба силами торцевого сжатия на окончательных переходах без потери устойчивости краевыми элементами тонкостенных профилей
3.5. Выводы.
4. РАЗРАБОТКА И ВНЕДРЕНИЕ ТЕХНОЛОГИИ И ОБОРУДОВАНИЯ.
4.1. Разработка технологических схем формообразования профилей, используемых в конструкциях летательных аппаратов.
4.2. Разработка оснащения для изготовления специальных тонкостенных профилей сложной формы поперечного сечения.
4.3. Изготовление профилей с заданной продольной кривизной и предотвращением потери устойчивости элементами профилей обращенными внутрь кривизны.
4.4. Оптимизация параметров гибочно-прокатного оборудования для изготовления тонкостенных широкополочных профилей с отсутствием потери устойчивости краевых элементов.
4.5. Изготовление инструмента и требования к нему.
4.6. Внедрение оборудования и технологии изготовления тонкостенных профилей.
4.7. Технико-экономические показатели применения гнутых из листа профилей.
4.8. Выводы.
Разработка методов и алгоритмов проектирования процессов формообразования тонкостенных профилей стесненным изгибом с устранением потери устойчивости краевых элементов (реферат, курсовая, диплом, контрольная)
Авиаи ракетостроение всегда были и остаются отраслями самой передовой науки, техники и технологии, где постоянно ведется поиск новых материалов, прогрессивных технологических процессов и наиболее совершенного оборудования для их реализации.
В связи с повышающимися требованиями к конструкциям летательных аппаратов (ЛА) в части прочности, жесткости и ресурса значительно возросла потребность в производстве узлов и деталей, изготовленных из листовых материалов, особенно плакированных, обладающих повышенными коррозионными свойствами. Отличительной особенностью листовой штамповки является ее высокая производительность, рациональное использование исходного материала, широкие возможности механизации и автоматизации технологических процессов, достаточно хорошая точность воспроизведения размеров деталей, возможность изготовления жестких деталей при небольшой их массе. Тонкостенные профили из традиционных алюминиевых сплавов и высокопрочных авиационных материалов обычно изготавливают в заготовительно-штамповочном производстве штамповкой в прессах. Однако производство штамповкой тонкостенных профилей из высокопрочных сплавов с малыми относительными радиусами зон сгиба затруднено из-за малой стойкости калибра матрицы, низкого качества и больших допусков на толщину. Известные способы изготовления профилей в штампах на кривошипных прессах, в штампах на специальных гибочных прессах, кромкогибочных устройствах и протяжкой являются малопроизводительными, приводят к большим потерям металла. Процесс получения профилей со сложной конфигурацией поперечного сечения весьма затруднителен, узкий диапазон по длине, ширине и толщине исходных заготовок и высокая себестоимость гнутых профилей, полученных штамповкой, гибкой на прессах или протяжкой, резко ограничивает области их применения. Профилирование по традиционным схемам в авиационном производстве не используется из-за малой жесткости профилей, значительных габаритных размеров профилегибочных станов, большого количества роликовых пар и соответственно длительной переналадки.
Необходимость повышения летно-технических характеристик ЛА приводит к использованию в элементах конструкции высокопрочных материалов, обладающих, как правило, малой пластичностью.
Промышленностью освоены профили, гнутые из алюминиевых, титановых и других высокопрочных материалов, имеющие в зоне сгиба внутренние радиусы равные, как правило, трем — пяти толщинам исходной заготовки. Они из-за нерационального соотношения размеров по своим прочностным и жесткостным характеристикам заметно уступают прессованным. Для того чтобы характеристики профилей, гнутых из листа, соответствовали бы характеристикам прессованных и горячекатаных, необходимо их изготавливать с минимальными радиусами и утолщением материала в зонах сгиба. При обычном пластическом изгибе листовых заготовок это сделать не удается из-за опасности разрушения растянутых волокон по внешней поверхности и утонения материала в угловой зоне. Процесс формообразования профилей из листовых труднодеформируемых материалов часто ведут с нагревом заготовок, что повышает трудоемкость и себестоимость, цикл изготовления и металлоемкость технологического оснащения. Коэффициент использования металла обычно не превышает 0,6 -0,7, качество и точность — невысокие.
Устранить существующие недостатки гнутых профилей оказалось возможным при изготовлении их гибкой-прокаткой на специальных гибочно-прокатных станках методом стесненного изгиба. Характерной особенностью роликового инструмента является наличие уступа, который позволяет замкнуть рабочий контур с созданием в заготовке дополнительных сжимающих напряжений, компенсирующих растяжение наружных волокон угла гиба. Деформация осуществляется в условиях сжатия, что позволяет получать профили из высокопрочного листового материала, приближаясь к выгодной геометрии прессованного профиля в зонах сгиба. Оборудование для изготовления гнутых тонкостенных профилей менее сложно, чем прокатное или прессовое, его изготовление дешевле, а обслуживание — легче и проще. Капиталовложения и эксплуатационные расходы при организации производства гнутых профилей значительно меньше, чем при других видах обработки металлов давлением, и первоначальные затраты окупаются в короткий срок.
Однако дальнейшая интенсификация процессов формообразования тонкостенных профилей в роликовых парах ограничивается потерей устойчивости краевых элементов профилей.
Для гарантированного обеспечения качества тонкостенных профилей, в частности, недопущения гофрообразования периферийных участков профилей необходимо назначение расчетных схем и режимов формовки, требуемых параметров роликового инструмента и оборудования, что требует теоретического исследования механизмов возникновения потери устойчивости применительно к формообразованию в валковых парах.
Следовательно, актуальной задачей исследования в настоящей работе становится разработка моделей процессов формообразования краевых элементов профилей на предварительных и окончательных технологических переходах с исследованием факторов интенсификации и предельных возможностей процессов формовки в валках с позиции недопущения гофрообразования по кромкам, повышения качества изготовления катаной продукции и расширения технологических возможностей данного способа изготовления.
Объект исследования — гнутые незамкнутые тонкостенные профили используемые в авиационных конструкциях в качестве подкрепляющих силовых элементов более сложных тонкостенных конструкций: Ъобразные, корытообразные, швеллерные, уголковые и сложных поперечных сечений из листовых алюминиевых сплавов толщиной 5 = 0,4 — 2,0 мм с плакированным поверхностным слоем.
Цель диссертационной работы — разработка на основе комплексных теоретических и экспериментальных исследований научно обоснованных методов и алгоритмов проектирования технологического оснащения и выбора оптимальных параметров малогабаритных гибочно-прокатных станков для формообразования гнутых тонкостенных профилей методом стесненного изгиба с устранением потери устойчивости краевых элементов. Следовательно, основными направлениями исследования являются:
1. Исследование геометрических и деформационных параметров зон плавных переходов подгибаемых полок различной конфигурации поперечного сечения при интенсивных схемах формовки на переходах предварительного формообразования с формированием условия, определяющего предельные режимы подгибки полок по технологическим переходам и минимального числа технологических переходов для изготовления профилей без гофрообразования краевых участков.
2. Исследование влияния геометрических и силовых параметров в зонах передачи сжимающих торцевых усилий на окончательных переходах с выражением критерия устойчивости для краевых участков в целях определения предельных величин осадки кромок полок за проход с минимально достижимыми радиусами зон гиба.
Научной новизной в настоящей работе обладают следующие результаты:
1. Концептуальные математические модели формообразования плоских, многоэлементных и криволинейных в плане подгибаемых полок в очагах деформации предварительных переходов, позволяющие функционально определить геометрические характеристики очагов деформации, продольные деформаций растяжения в подгибаемых элементах, и сделать выбор оптимального межклетьевого расстояния при разработке номенклатурно-ориентированного оборудования для производства тонкостенных профилей с позиции предупреждения гофрообразования.
2. Критерии устойчивости тонкостенных краевых элементов плоского и криволинейного поперечных сечений с накопленными продольными деформациями, разработанные для определения предельных углов подгибки данных элементов за технологический переход при изготовлении прямолинейных профилей и профилей с заданной продольной кривизной.
3. Методика для нахождения минимально необходимого числа технологических переходов предварительного формообразования с целью получения бездефектных тонкостенных профилей и оптимального распределения углов подгибки плоских и криволинейных в поперечном сечении элементов по этим переходам.
4. Априорная модель устойчивости краевых элементов от торцевых сжимающих сил на окончательных переходах с формулировкой критерия, определяющего предельные величины осадки торцов полок за технологический переход и минимально достижимые радиусы зон сгиба при отсутствии гофрообразования периферийных участков профилей.
5. Метод косвенной экспериментальной оценки остаточных продольных деформаций растяжения в элементах отформованных профилей по величинам продольной кривизны симметричных профилей и угла крутки асимметричных профилей.
6. Моделирование зоны свободного формоизменения и уголковой зоны для автоматизированного расчета энергосиловых параметров формообразования тонкостенных профилей интенсивным деформированием на предварительных переходах (необходимых крутящих моментов и мощности на валах станка).
Диссертационная работа состоит из четырех разделов:
В первом разделе рассмотрены вопросы применения профилей в изделиях отрасли. Проведен анализ теоретических и технологических работ, посвященных производству тонкостенных профилей в валковых парах. Здесь же рассмотрены технологические проблемы, возникающие при попытке интенсификации процесса изготовления тонкостенных профилей в роликах методом стесненного изгиба. В выводе выделен ряд задач, подлежащих решению.
Во втором разделе разработаны модели процесса деформирования краевых подгибаемых элементов различной поперечной конфигурации на переходах предварительного формообразования и критерий устойчивости последних, позволяющий определить предельные значения углов подгибки на каждом технологическом переходе. При режимах формообразования, превышающих предельные, определены значения амплитуды кромковой волнистости для плоских элементов и амплитуды периодических изломов для криволинейных в плане полок. Найдены величины продольных прогибов для симметричных профилей и крутки асимметричных профилей от накопленных в процессе профилирования продольных остаточных деформаций. Рассмотрена модель устойчивости периферийных элементов профиля при формообразовании на окончательных переходах. На базе теоретических исследований разработаны алгоритмы, необходимые для автоматизированной разработки технологии изготовления профилей (назначении углов подгибки за проход для профилей с плоскими в плане подгибаемыми полками и углов подгибки по переходам для профилей с криволинейными полками), вычисления амплитудных значений волнистости кромок или периодических изломов для прямолинейных профилей и поводок для профилей не подвергающихся правке.
В третьем разделе приведена программа экспериментальных исследований по определению предельных возможностей процесса изготовления тонкостенных профилей на переходах предварительного и окончательного формообразования и сопоставления экспериментальных данных с теоретическими результатами. Верификация теоретических зависимостей производится как прямыми, так и косвенными методами в постановочных экспериментах и при помощи методики математического планирования эксперимента по специально разработанной программе для автоматизированного расчета.
Четвертый раздел посвящен определению основных технологических параметров процесса на основе теоретических и экспериментальных исследований. Рассмотрены вопросы проектирования технологического оснащения, в частности, автоматизированного расчета углов подгибки по предварительным переходам элементов и расчета ширины заготовки для зетобразных и корытообразных профилей с отбортовками и без них из условия устойчивости краевых криволинейных в плане элементов. Применительно к тонкостенным профилям сложной конфигурации приводятся конструкции вспомогательной оснастки для воздействия на очаг деформации краевых подгибаемых участков профиля — проводковые устройства качения (роликовые) и скольжения, позволяющие интенсифицировать процесс формообразования на предварительных переходах. На примере изготовления профиля швеллерного сечения определено минимальное количество требуемых технологических переходов для формообразования без возникновения гофрообразования полок. Предложены рекомендации по выбору оптимальных параметров основных частей гибочно-прокатного оборудования: длины валов и межосевого расстояния рабочих клетей станка для определенной номенклатуры профилеймежклетьевых расстояний для направляющего устройства с клетью направленной потери устойчивости. На основе проведенных теоретических и экспериментальных исследований по оптимизации параметров оборудования и энергосиловых параметров процесса формообразования создан алгоритм для автоматизированного проектирования гибочно-прокатного оборудования под конкретный сортамент тонколистовых профилей.
Далее рассмотрены технические условия на профили, подлежащие изготовлению, а также требования к исходным материалам и методам контроля. На основе оценки технологических параметров профилей к внедрению на предприятии по расчетному числу предварительных и окончательных переходов, межклетьевого расстояния и других характеристик назначения оборудования был признан подходящим станок ГПС-500М6. Станки для предприятий-заказчиков были изготовлены на Ульяновском станкостроительном заводе и подвержены автором приемочным испытаниям. В процессе отладки и опытной эксплуатации по предложению автора проведены мероприятия по совершенствованию оборудования, в частности, конструкции межклетьевых неприводных клетей, проводковых устройств, подающей клети и др. Проведенные исследования геометрических параметров поперечного сечения, продольной формы и структуры металла профилей выявили их соответствие требованиям нормативно-технической документации.
Результаты исследований внедрены на трех предприятиях РФ в виде сдачи «ключ» автоматизированных линий и реализованных на них технологий для изготовления тонкостенных профилей, в том числе, используемых в качестве стрингерного набора фюзеляжа самолета АН-70 (ЗАО «Авиакор-Лизинг» г. Самара) и профилей применяемых в строительстве. Здесь же производится расчет экономической эффективности от внедрения оборудования и технологии на предприятии ЗАО «Авиакор — Лизинг» .
В разделе «Заключение: Общие выводы вследствие проведенных исследований и экспериментов, обосновывается научная новизна работы, и формулируются ее результаты.
В списке литературы внесено 159 первоисточников (в т.ч. на 4-х иностранных языках), из которых использовалась хотя бы одна строчка информации для написания настоящей работы.
В приложении имеются акты о внедрении технологии и оборудования на площадях промышленных предприятий-заказчиков.
Автору в настоящей работе принадлежат:
• Математические модели очагов деформации краевых элементов тонкостенных профилей на переходах предварительного формообразования в зависимости от ширины и формы поперечного сечения элемента, угла подгибки за проход и межклетьевого расстояния.
• Алгоритм для автоматизированного расчета предельных углов подгибки за проход для плоских полок и распределения углов подгибки по переходам для криволинейных в плане полок на переходах предварительного формообразования, полученные из критерия устойчивости периферийных элементов с накопленными продольными деформациями, в зависимости от ширины, толщины и формы поперечного сечения элемента, межклетьевого расстояния, радиуса продольной кривизны профиля и механических свойств профилируемой заготовки.
• Алгоритм для автоматизированного расчета предельных величин осадки торцов полок за проход на переходах окончательного формообразования (собственно стесненный изгиб), полученный из критерия устойчивости краевых участков, являющихся зоной передачи торцевых усилий сжатия, в зависимости от ширины и толщины полки, радиуса уступа, величины аксиального натяга и предварительной заготовки, механических свойств заготовки.
• Алгоритм для автоматизированного расчета минимального числа технологических переходов для бездефектного изготовления профилей, энергосиловых параметров профилирования (крутящего момента и мощности) в зависимости от геометрических параметров рассматриваемого профиля, межклетьевого расстояния и механических свойств заготовки.
• Косвенные методы определения уровня продольных остаточных деформаций в элементах отформованных профилей — по величинам прогиба и крутки готовых неправленых профилей.
• Результаты внедрения технологии и оборудования в опытное и серийное производство.
Автор выражает глубокую признательность научному руководителю за ценные рекомендации, сотрудникам «Ульяновского НИАТ» и кафедры «Самолетостроение» института авиационных технологий и управления Ульяновского гостехуниверситета за оказанную помощь в процессе выполнения работы.
Основное содержание диссертации опубликовано в 19 научных работах, включая 2 заявки на патент (положительное решение ФИПС).
ЗАКЛЮЧЕНИЕ
: ОСНОВНЫЕ РЕЗУЛЬТАТЫ И ВЫВОДЫ.
Выполненные в работе исследования и их результаты позволяют сделать следующие выводы:
1. Разработаны алгоритмы для автоматизированного расчета предельных углов подгибки за проход для плоских краевых элементов, распределения углов подгибки по переходам для криволинейных в плане элементов и требуемого числа переходов в зависимости: от ширины, толщины и формы поперечного сечения краевых элементов, межклетьевого расстояния, радиуса продольной кривизны профиля и механических свойств заготовки, что позволило производить выбор схемы формовки и проектировать роликовый инструмент для формообразования тонкостенных профилей на интенсивных режимах формовки с относительной шириной полок в диапазоне 20−100 без их потери устойчивости.
2. Проведены исследования процессов формообразования тонкостенных профилей на окончательных переходах путем рассмотрения комплексной модели устойчивости зоны передачи усилий торцевого поджатия — краевых элементов профиля и формоизменения уголковой зоны данными сжимающими усилиями. Разработан алгоритм для автоматизированного расчета предельных величин осадки торцов полок за проход, минимально достижимых радиусов зон сгиба и требуемого числа окончательных переходов в зависимости от ширины и толщины полки, геометрических параметров роликовых пар и предварительной заготовки с ее механическими свойствами, что позволило проектировать роликовые пары окончательных переходов для изготовления высококачественных широкополочных тонкостенных профилей (без потери устойчивости полками) с относительными радиусами зон сгиба r/s = 1,0 — 3,0.
3. Экспериментально подтверждены адекватность теоретических расчетов предельных углов подгибки полок и предельных величин осадки торцов полок за технологический переход, геометрических параметров очагов деформации подгибаемых краевых элементов, амплитуды гофрообразования и уровней продольных деформаций в полках с точностью 10 — 30% для диапазона ширины и толщины краевых элементов соответственно 10. 60 мм и 0,4. 2,0 мм.
4. Созданы методики расчета технологической валковой оснастки для производства тонкостенных широкополочных профилей Z-образного и корытообразного сечений методом стесненного изгиба с интенсивным деформированием на переходах предварительного формообразования и гарантированным отсутствием гофрообразования краевых элементов.
5. Разработан алгоритм автоматизированного крутящего момента, мощности и др. в зависимости от геометрических параметров профиля, количества переходов, межклетьевого расстояния, геометрических параметров валков и механических свойств заготовки, что позволило оптимизировать параметры специализированного гибочно-прокатного оборудования и произвести выбор имеющегося оборудования для изготовления конкретного сортамента тонкостенных профилей.
6. Созданные алгоритмы и методики расчета оптимальных параметров технологического оснащения и оборудования позволили создать технологию производства высококачественных тонкостенных профилей на изделия АН-70 и АН-140.
7. Результаты проведенных исследований и разработок внедрены на четырех предприятиях РФ, в том числе одна автоматизированная линия в ЗАО «Авиакор-Лизинг» (г. Самара) для изготовления двух типов 2-образных профилей, используемых в качестве стрингеров в фюзеляже самолета АН-70. Окупаемость оборудования достигается менее чем за 1,5 года при минимальной партии профилей 100.000 погонных метров.
Список литературы
- АС 309 761 СССР, МПК6 B21D5/06 Способ изготовления гнутых профилей / И. С. Тришевский, Э. С. Дахновский, В. И. Мирошниченко и др. -Опубл. В Б.И., 1971, № 23
- АС 294 406 СССР, МПК6 B21D5/06 Способ изготовления гнутых профилей коробчатого сечения. / И. С. Тришевский, Э. С. Дахновский, В. В. Клепанда, А. Н. Коновалов Опубл.: Б.И., 1972, № 27.
- АС 385 646 СССР, МПК5 B21D5/06 Устройство для гибки полосы / Г. В.
- Проскуряков, Д.П. Аникин, Н.И. Гурченков Опубл. в Б.И., 1973, № 26.
- АС 679 282 СССР, МПК6 B21D5/06 Способ изготовления гнутых профилей./ Шварцман З. М., Антипанов В. Г., Анисимов В. И. и др. Опубл.: Б.И., 1979, № 30.
- АС 374 906 СССР, МПК6 B21D5/06 Способ производства гнутых профилей проката. / И. С. Тришевский, В. В. Клепанда, Э. С. Дахновский, A.C. Кузнецов Опубл.: Б.И., 1981, № 30.
- АС 1 068 199 СССР, МПК6 B21D5/06 Способ изготовления гнутых профилей проката. / И. С. Тришевский, М. Е. Докторов, Э. М. Темников -Опубл.: Б.И., 1985, № 3.
- АС 1 138 206 СССР, МПК6 B21D5/06 Способ изготовления гнутых профилей. / И. С. Тришевский, А. П. Игнатенко, Я. В. Хижняков, В. Б. Калужский Опубл.: Б.И., 1985, № 5.
- АС 1 114 482 СССР, МПК6 B21D/06 Способ изготовления гнутых профилей из труднодеформируемых листовых материалов и устройство для его осуществления./ И. М. Колганов, С. И. Беляуш. Опубл. в Б.И., 1984, № 35.
- АС 1 215 792 СССР, MTIK6B21D/06 Способ изготовления тонкостенных профилей и устройство для его осуществления / И. М. Колганов, Г. В. Проскуряков, В. И. Колганов. Опубл. В Б.И., 1986, № 9.
- АС 1 248 690 СССР, МПК6 B21D/06 Способ изготовления листовых профилей с отбортовками./ И. М. Колганов, Г. В. Проскуряков, В. И. Филимонов и др. Опубл. в Б.И., 1986, № 29.
- АС 1 319 967 СССР МПК6 B21D/06 Устройство для изготовления тонкостенных профилей. / И. М. Колганов, В. И. Колганов, К. С. Собакинский. Опубл. в Б.И., 1987, № 24.
- АС 1 660 288 СССР, МПК6 B21D5/06 Способ изготовления гнутых профилей. / В. И. Филимонов, Г. В. Коновалов Опубл.: Б.И., 1990, № 7.
- Абдулин Ф.З., Филимонов В. И., Проскуряков Г. В. Изготовление тонкостенных гнутых профилей из сплава 1 420. // Авиационная промышленность, 1987, № 3, С. 34 36.
- Алфутов Н.А. Основы расчета на устойчивость упругих систем. 2-е изд., перераб. и доп. — М.: Машиностроение, 1991. — 336 с.
- Анурьев В.И. Справочник конструктора-машиностроителя. Т. 1,2,3. М.: Машиностроение, 1982, — 576 е., 584 е., 736 с.
- Антипенко А.П. К вопросу определения минимальных внутренних радиусов мест изгиба замнутых сварных профилей. В сб.: Освоение производства и повышение качества гнутых профилей проката. Харьков: УкрНИИМет, 1985, С.30−34.
- Арышенский Ю.М., Гречников Ф. В. Теория и расчеты пластического формоизменения анизотропных материалов. М.: Металлургия, 1990.- 304 с.
- Белянин П.Н. Производство широкофюзеляжных самолетов. М.: Машиностроение, 1979. — 360 с.
- Берлет Ю.Н., Марковцев В. А., Филимонов В. И., Филимонов C.B. Деформационные характеристики подгибаемых полок и оптимизация углов подгибки при профилировании // Кузнечно-штамповочное производство. -2002,№ 6.-С. 8−16
- Бидерман B.JI. Механика тонкостенных конструкций. Статика. М.: Машиностроение, 1977. — 488 с.
- Биргер И.А., Мавлютов Р. Р. Сопротивление материалов. Учебное пособие.- М.: Наука. Гл. ред. физ.-мат. лит., 1986. 560 с.
- Богоявленский К.Н., Григорьев А. К. Изготовление тонкостенных профилей из титана и его сплавов на профилегибочном стане В кн.: Обработка металлов давлением. Труды ЛЕИ, M.- JL: Машгиз, 1963, вып.222 ф. С.148−150.
- Братухин А.Г. Развитие авиационной промышленности в условиях конверсии и рыночной экономики. // Авиационная промышленность, 1992, № 5, С. 3 7.
- Высокоэкономичные гнутые профили проката. / Под ред. И. С. Тришевского.- М.: Металлургия, 1965, — 240 с.
- Гайнутдинов Р.Г. Усталостная прочность и коррозионная стойкость фюзеляжных стрингеров из прессованных и катаных полуфабрикатов. // Авиационная промышленность, 1985, № 5, С. 19 20.
- Гарбуз В.Ф., Юрченко А. Б. Некоторые особенности формы очага деформации при профилировании и их связь с энергосиловыми napiaMerpaMH процесса. В. сб.: Теория и технология производства гнутых профилей проката. Харьков: УкрНИИМет, 1982, С. 12 -18.
- Гиммельфарб A.JI. Основы конструирования в самолетостроении. М.: Машиностроение, 1980.- 367 с.
- Гнутые профили проката. Справочник. И. С. Тришевский, Н. М. Воронцов, В. В. Клепанда и др. М.: Металлургия, 1967. — 379 с.
- Горбунов М.Н. Технология заготовительно-штамповочных работ впроизводстве летательных аппаратов. — М.: Машиностроение,! 981 224 с.
- ГОСТ 12.1.030−81. ССБТ. Электробезопасность. Защитное заземление, зануление. М.: Изд-во стандартов, 1981. — 17 с.
- Григолюк Э.Г., Кабанов В. В. Устойчивость круговых цилиндрических оболочек. Итоги науки и техники. Механика твердых деформируемых тел. 1967.-М.: ВИНИТИ, 1969.-348 с.
- Григолюк Э.Г., Кабанов В. В. Устойчивость оболочек. М.: Наука, 1978. -360 с.
- Григолюк Э.Г., Мамай В. И. Нелинейное деформирование тонкостенных конструкций. М. Наука. Физматлит, 1997. — 272 с.
- Громов Н.П. Теория обработки металлов давлением. М.: Металлургия, 1978.- 360 с.
- Гуляев A.A., Проскуряков Г. В., Филимонов В. И. Граничные условия в задачах гибки с торцевым поджатием // Авиационная промышленность, 1987, № 4, С. 54 -55.
- Гурченков Н.И. Исследование процессов формообразования листовых профилей стесненным изгибом при гибке-прокатке. Дис. канд. техн. наук, Куйбышев, 1975.- 197с.
- Давыдов В.И., Максаков М. П. Производство гнутых тонкостенных профилей. М.- Металлургиздат, 1959. — 240 с.
- Дель Г. Д. Технологическая механика. М., «Машиностроение», 1978.- 174 с.
- Докторов М.Е., Пшеничная Н. В. Некоторые особенности технологии изготовления гнутых профилей с отбортовками. В. сб.: Теория и технология производства гнутых профилей проката. Харьков: УкрНИИМет, 1982, С.47−52.
- Ершов В.И. Изгиб со сжатием в тангенциальном направлении листов из титановых сплавов и стали ВНС-2 // Авиационная промышленность, 1974, № 8, С. 46 48 .
- Ершов В.И. К расчету процессов формоизменения под действием нескольких нагрузок // Изв. ВУЗов. Сер. Авиационная техника. Казань, 1980,№ 1,С.103−117.
- Изготовление гнутых листовых профилей повышенной жесткости из труднодеформируемых материалов. / И. М. Колганов, Ф. З. Абдулин, Г. В. Проскуряков и др. // Кузнечно-штамповочное производство, 1987, № 3, С. 18 21.
- Изготовление профилей методом стесненного изгиба из листовых заготовок сплавов марки 1430 и 1451 (Технологические рекомендации, временные) /
- И.М.Колганов, Н. И. Колобнев, В. И. Филимонов и др. НИАТ, Ульяновск, 1992.- 32 с.
- Изготовление уголковых профилей гибкой с осадкой листовых заготовок В. И. Ершов, В, Д. Гаврилин, Ю. Р. Медведев. // Авиационная промышленность, 1993, № 6, С. 39 41.
- Исследование анизотропии заготовок и интенсификация процессов получения профилей методом стесненного изгиба (Техн. отчет). Рук. Арышенский Ю. М., № гос. регистрации 186 009 208, инв. № 4084 -Куйбышев, КуАИ, 1988. 81 с.
- Калибровка валков для производства гнутых профилей проката. / Под ред. Тришевского И. С. Киев: Техника, 1980. — 535с.
- Калужский И.И., Проскуряков Г. В. Гибка листов на малые радиусы (стесненный изгиб). В кн.: Теоретические основы расчетов технологических процессов кузнечно-штамповочного производства. -Куйбышев (КуАИ), 1973, С. 74 — 81.
- Камке Э. Справочник по обыкновенным дифференциальным уравнениям. -М.: Наука, 1976.-576 с.
- Клепанда В.В., Тришевский И. С. Механические свойства гнутых профилей проката. Киев, Техника, 1977, — 144 с.
- Колганов И. М, Беляуш С. И. Волочильно-прокатная установка модели ВПУ-120/5,5 // Авиационная промышленность, 1987, № 12, С. 11−12.
- Колганов И.М. Исследование процесса волочения тонкостенных профилей из листа в условиях стесненного изгиба.//Кузнечно-штамповочное производство, 1985, № 6, С. 29 31.
- Колганов И.М. О достижениях и перспективах развития стесненного изгиба. // Сб. Состояние и перспективы изготовления и применения листовых профилей в изделиях отрасли. НИАТ, 1992, С. 5 -10.
- Колганов И.М. Разработка и внедрение процессов формообразования листовых профилей авиационных конструкций стесненным изгибом при волочении. Дисс. канд. техн. наук. Куйбышев, изд-во КуАИ, 1983. — 296 с.
- Колганов И.М., Проскуряков Г. В., Колганов В. И. Формообразование профилей повышенной жесткости при волочении // Кузнечно-штамповочное производство. 1982. — № 5. — С.21 — 23.
- Колганов И.М., Проскуряков Г. В., Ломакин В. П. Исследование процесса формообразования профилей стесненным изгибом в роликовых фильерах.//Авиационная промышленность, 1982, № 7, С. 32 39.
- Колганов И.М., Филимонов В. И., Филимонов C.B. Применение модели пластического формоизменения профилирования // Авиационная промышленность. 1996. — № 3 — 4. — С.26−30.
- Комаров А.Д., Барвинок В. А., Моисеев В. К., Хромова Е. А. Пружинение прямолинейных бортов при стесненном изгибе листовых деталей эластичной средой // Авиационная техника. 2000. — № 3.- С. 46 — 48.
- Корн Г. и Корн Т. Справочник по математике для научных работников и инженеров. М.: Наука, 1974. — 832 с.
- Коцарь С.Л., Третьяков В. А., Цупров А. Н., Поляков Б. А. Динамика процессов прокатки: Учебное пособие. М.: Металлургия, 1997. — 255 с.
- К расчету технологических параметров гибки-прокатки с аксиальным сжатием./ В. И. Филимонов, Г. В. Проскуряков, В. А. Марковцев, И.М. Колганов//Вопросы авиационной науки и техники. Сер. Авиационная технология, 1986, № 2, С. 30 -35.
- Куприн П. Н, Колганов И. М. Влияние аксиального натяга полосы на устойчивость тонких краевых элементов заготовки при их торцевом сжатиив роликовых парах окончательных переходов // Сборник научных трудов ИАТУ. Ульяновск, 2002. — С.123 — 129.
- Куприн П. Н, Колганов И. М. Критические углы подгибки плоских тонкостенных полок при профилировании // Сборник научных трудов ИАТУ. Ульяновск, 2003. — С. 78 — 81.
- Куприн П. Н, Колганов И. М. Математическая модель устойчивости сжатой полки в рабочем калибре роликовой оснастки // Авиационная техника. -2003, № 2.-С. 51−54.
- Куприн П. Н, Колганов И. М. Оптимизация основных параметров гибочно-прокатных станков // Авиационная промышленность.- 2003, № 8, С. 79 82.
- Куприн П. Н, Колганов И. М. Факторы, гарантирующие качество гнутых тонкостенных профилей проката // Сб. Современные технологии в машиностроении. Научно-практическая конференция. Пенза, 2001. — С. 98 -102.
- Куприн П. Н, Колганов И. М, Антонов А. Н. Повышение ресурса и снижение массы транспортных самолетов важнейшая задача ОКБ и производства: Сборник научных трудов. — Ульяновск: УлГТУ, 1999. — С.45 -52.
- Куприн П.Н., Колганов И. М., Антонов А. Н. Снижение массы и повышение ресурса JTA при внедрении гнутых профилей и перспективных материалов тезисы МАТИ, 1999, № 4, С. 838 — 839 (тезисы).
- Куприн П.Н., Колганов И. М., Киселев A.B. Создание условий повышения качества гнутых профилей. УлГТУ, 33 к/т кон., 2001. — С. 69 (тезисы).
- Куприн П.Н., Колганов И. М., Мансуров Е. В. Дефектность и бездефектность гнутых профилей и пути повышения их надежности. Ульяновск, УлГТУ, 2000. — С. 39 — 40. (тезисы).
- Куприн П. Н, Колганов И. М., Мансуров Е. В. Проблемы устойчивости краевых элементов и повышение качества гнутых профилей. // Сб. Современные технологии в машиностроении. Научно-практическая конференция. Пенза, 1999. — С. 117 — 121.
- Куприн П.Н., Колганов И. М., Мансуров Е. В. Решение одной задачи провышения качества гнутых профилей. // Сб. Прогрессивные технологии, материалы и конструкции. Ульяновск, УлГТУ, 1999. — С. 89−93.
- Куприн П.Н., Колганов И. М., Мансуров Е. В. Факторы, определяющие качества и точностные характеристики гнутых профилей. // Сб. Современные технологии в машиностроении. Научно-практическая конференция. Пенза, 1999, С. 73−75.
- Куприн П.Н., Пакшин П. Ю. Устранение кромковой волнистости при изготовлении гнутых тонкостенных профилей // Тезисы международной молодежной научной конференции «XXVII Гагаринские чтения».- Москва, 2001.-С. 151.
- Лизин В.Т., Пяткин В. А. Проектирование тонкостенных конструкций. -М.?Машиностроение, 1976.- 408 с.
- Марковцев В.А. разработка и внедрение технологии и оборудования для изготовления листовых профилей для изготовления авиационных конструкций методом стесненного изгиба. Дисс. канд. техн. наук. М., 1991.-202 с.
- Марковцев В.А., Проскуряков Г. В., Коновалов Г. В. Выбор диаметров роликов при формообразовании профиля стесненным изгибом. // Авиационная промышленность, 1990, № 8, С. 8 11.
- Марковцев В.А., Проскуряков Г. В., Филимонов В. И. Выбор конструктивных параметров правильного устройства на основе анализа динамического режима. // Авиационная промышленность, 1988, № 9, С. 32 35.
- Математическое моделирование процессов обработки металлов давлением. / Ю. Г. Гуляев, С. А. Чукмасов, А. В. Губинский. Киев: Наукова думка. 1986. -240 с.
- Мударисов З.Х. Гибочно-прокатный станок ГПС-200М // Состояние и перспективы изготовления и применения листовых профилей в изделиях отрасли: Материалы совещания. НИАТ, 1990. — С. 23 — 25.
- Мударисов З.Х., Проскуряков Г. В., Пигалов Б. М. Гибочно-прокатный станок ГПС-200М // Авиационная промышленность, 1989, № 12. С. 9 — 11.
- Несис Е.И. Методы математической физики: Учебное пособие. М.: Просвещение, 1977. — 199 с.
- Никольский Л.А., Фиглин С. З., Бойцов В. В., Калинин Ю. Г., Бахарев A.B. Горячая штамповка и прессование титановых сплавов. М.: Машиностроение, 1975 — 285 с.
- Определение технологических параметров при стесненном изгибе./ Ю. М. Арышенский, А. В. Цветков, А. Ю. Матвеев и др. // Сб. Состояние и перспективы изготовления и применения листовых профилей в изделиях отрасли.- НИАТ, 1992, С. 26 30. т
- Патент 2 148 455, МПК' B21D/06 Устройство для изготовления тонкостенных профилей из листовых заготовок. / И. М. Колганов, П. Н. Куприн, H.A. Щавлева, Е. В. Мансуров Опубл.: в БИ, 2000, №
- Патент 2 179 598, МПК7 B21D/06 Способ термомеханической обработки листовых труднодеформируемых алюминиевых сплавов / И. М. Колганов, П. Ю. Пакшин, П. Н. Куприн, A.B. Киселев Опубл.: в БИ, 2000, № 5
- Попов Е.А. Основы теории листовой штамповки. -М.:Машиностроение, 1977, — 273.с.
- Предотвращение волнистости на профилях с покрытием. Стукалов В. П., Дахновский Э. С., Мирошниченко В. И., Юрченко А. Б. В сб.: Разработка и исследование технологии производства гнутых профилей проката. Харьков: УкрНИИМет, 1984, с. 99 -100.
- Применение осевого подпора при формообразовании профилей из листа гибкой-волочением в условиях стесненного изгиба./Ф.З.Абдулин, И. М. Колганов, Г. В. Проскуряков, В. И. Филимонов. // Авиационнаяпромышленность, 1984, № 8, С. 36 -38.
- Производство гнутых профилей (оборудование и технология). / Под общ. ред. И. С. Тришевского и др. -М.: Металлургия, 1982, — 384 с.
- Производство и применение гнутых профилей проката. Справочник. / Под общ. ред. И. С. Тришевского и др. М.: Металлургия, 1975. — 536 с.
- Проскуряков Г. В. Исследование стесненного изгиба. Дисс. канд. техн. наук. Харьков, 1966. — 195с.
- Проскуряков Г. В. Стесненный изгиб. // Авиационная промышленность, 1966, № 2, С. 9−13.
- Разработка, изготовление и внедрение технологии и оборудования для производства гнутых профилей (Техн. отчет). (УлНИАТ), г. Ульяновск. Рук. Марковцев В. А., инв.№ 806.27.08.98,1999.- 42 с.
- Романовский В.П. Справочник по холодной штамповке. -JI.Машиностроение, 1979.- 520 с.
- РТМ 1.4.2005 90. Изготовление профилей из листовых алюминиевых материалов Д16, В95,1420 методом стесненного изгиба. — НИАТ, 1990.
- Самолеты ближайшего будущего // Гражданская авиация. 1990. — 3. С. 22−27.
- Свиницкий A.M., Воронкин Н. Ф., Карлашов A.B., Гайнутдинов Р. Г. Исследование коррозионной активности фюзеляжного конденсата пассажирских самолетов. // Физико-химическая механика материалов. -1982.-5-С. 70−72.
- Смирнов-Апеев Г. А. Сопротивление металлов пластическому деформированию. Л.:Машиностроение, 1978, — 368 с.
- Скрипачев A.B. Изготовление из листа профилей повышенной жесткости стесненным изгибом на кромкогибочных машинах. Дисс. канд. техн. наук. -Тула, 1983.-242 с.
- Современные технологии авиастроения / Коллектив авторов- Под. Ред.
- Братухина А.Г., Иванова Ю. Л. М.: Машиностроение, 1999.- 832 с.
- Спиридонов A.A. Планирование эксперимента при исследовании технологических процессов. -М.: Машиностроение, 1981.- 184 с.
- Способ гибки профилей проглаживанием по пуансону. Арышенский А. Ю., Ненашев В. Ю., Матвеев А. Ю, Гречников Ф.В.// Состояние и перспективы изготовления и применения листовых профилей в изделиях отрасли: Материал совещания. НИАТ, 1990. — С. 30- 33.
- Сторожев М.В., Попов Е. А. Теория обработки металлов давлением. М.: Машиностроение, 1977, — 428 с.
- Тарновский И.Я., Поздеев A.A., Ганаго O.A. Теория обработки металлов давлением. М.: Металлургиздат, 1963. — 672 с.
- ТР.1.2.1910−88. Изготовление деталей из профилей, гнутых методом стесненного изгиба из плакированных листовых материалов Д16, 1163, В95./A.C.Москвин, В. И. Филимонов, О. Г. Сенаторова. НИАТ, 1988.
- Тришевский И.С., Докторов М. Е. О возникновении гофров в процессе образования гнутых профилей проката. В сб. «Обработка металлов давлением в машиностроении», вып. 9. Харьков, изд-во ХГУ, 1973, С. 23−30.
- Тришевский И.С. Исследование профилирование в валках, создание и освоение промышленной технологии производства гнутых профилей проката. / Автореферат, дисс. д- ра техн. наук, 1967.- 42 с.
- Тришевский И.С., Докторов М. Е. Теоретические основы процессов профилирования. М.: Металлургия, 1980.- 288 с.
- Уманский A.A. Строительная механика самолета. Изд-во.: Оборонгиз, 1961.-521 с.
- Филимонов В.И. Интенсификация процесса формообразования стесненным изгибом профилей для авиационных конструкций. Дисс. канд. техн. наук. -Самара, СГАКУ, 1993.- 190 с.
- Филимонов В.И., Марковцев В. А., Москвин A.C. Определение протяженности зоны плавного перехода при формообразовании стесненным изгибом .//Авиационная промышленность, 1992, № 7, С. 5 7.
- Формующий инструмент определяет качество гнутых профилей. Куприн П. Н., Колганов И. М., Антонов А. Н., Киселев A.B. Пенза, НТЗ, 1999.-С.43−44.
- Фридман Я.Б. Механические свойства металлов. М.: Машиностроение, 1974,4.1−472,4.2 — 368 с.
- Чекмарев А.П., Калужский В. Б. Гнутые профили проката. М.: Металлургия, 1974.- 264 с.
- Шалин P.E. Новые материалы для самолетов и двигателей. // Авиационная промышленность, 1981, № 3, С. 17−20.
- Шофман JI.A. Теория и расчеты процессов холодной штамповки. М.: Машиностроение, 1964, — 375с.
- Экспресс-информация. Сер. Авиастроение, 1998 2003.
- Энциклопедия машиностроения. Динамика и прочность машин. Теория механизмов и машин. Т2. В 2-х кн.1 / Колесников К. С., Александров Д. А., Асташев В. К. и др., Под. общ. ред. Колесникова К. С., 1994.
- Шенх Х.Я. Теория инженерного эксперимента. М.: Мир, 1972 — 381с
- Aluminum alloy development well improve performance // Aviation week and space technology. 1988. — v.129. — 14. — P. 57 — 58.
- Centre of attention// Sheet metal industry, 1999. № 9. — P.6.
- Developments in roll forming and bending // Welding and metal fabrication. -1986. V. 54. — 8. — P. 354 — 356.
- Erweiterte Fertigungsmoglichkeiten beim Stanz-Biegen // Blech, Rohre, Pro file, 1997.44, № 6.-S. 28−29.
- Hosford William, Duncan John Sheet metal forming: a review // Journal of minerals, metals and materials society, 1999−51, 11. P. 39−44.
- Kopp Reiner, Bemrath Gottfried The determination of formability for cold and hot forming conditions. // Steel Res., 1999.-70, № 4−5. C. 147 — 153.
- Lignes de profilage // Machines et production, 1999, 706e. P. 67.
- Nuevas tecnologias para el perfilado en frio // Novamaquina. 1986. — 126. — P. 133−137.
- Pat. 19 718 844 Ger., МПК6 B21D5/14 Maschine zum Proflieren der Randbereiche von Blechen//Bartolosch Friedhelm. Ver. 12.11.98.
- Pat. 19 708 488 Ger., МПК6 B21D1/05 00 Vorrichtung zum Biegerichten von Metallband //Mucke Gert, Neuershutz E., Thies H. Ver. 10.09.98.153. 2.500 000 pounds contract // Sheet metal industry, 1992. 69, № 1. P. 26.
- Pfeiffer W. Eigenspannungen messen, berechnen end nutzen. Optimiertes Vorgehen macht Bauteile stabiler. // Industrie Anzeiger. 1999 — 121, № 27 — 28. -S.363.
- Profil Walzanlagen van Otterloo // Blech — Rohre — Profile. — 1985. — V 32. -10. S. 569−571.
- Roll forming automotive components // Fabricator. 1998. — 5. — № 2. — P. 12 -16.
- Roll forming line for USSR // Sheet metal industry, 1992. № 9. p.40.
- Stelson K.A., Kramer A. Distortion of V-channel stctions in plastic bending // Trans. ASME: J. Manuf. Sei. And Eng., 1999−121, № 2. P. 208 — 213,
- Yang S., Nezu K. Concurrent design of sheet metal forming product and process // Trans. ASME: J. Manuf. Sei. And Eng., 1999 121, № 2 — P. 189 — 194.1. Главку^ инженерийкор-авиационны й2001 г. 1. ТЕХНИЧЕСКИЙ АКТ ВНЕДРЕНИЯ"2001 г.
- Перечень выполненных работ1. Наименование Исполнитель
- Проведение теоретических и экспериментальных исследований и разработка технологических схем и режимов формообразования Марковцев В. А. Филимонов C.B. Филимонов В.И.
- Проектирование технологического оснащения Куприн П. Н. Филимонов C.B.
- Доработка, отладка оборудования и внедрение технологического оснащения. Внедрение технологического процесса Куприн П. Н. Лапшин В.И. Филимонов C.B.
- От ФГУП «Ульяновский НИАТ» Руководитель темы, зам. ген. директора, к.т.н.1. ВтАгМарковцев1. Начальник ОХШ6АО «Авиакор-авиационный завод"+