Повышение эффективности изготовления поковок сложной формы на основе совершенствования процессов горячей объемной штамповки в разъемных матрицах
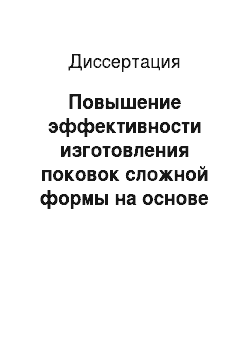
Методы исследования. Компьютерное моделирование конечно-элементным методом применялось для оценки напряженно — деформированного состояния заготовки при сложном течении металла, установления возможных дефектов формообразования и внесения в конструкцию рабочего инструмента корректив для их устранения, а так же для оценки распределения температур в поковке. Математическое моделирование энергосиловых… Читать ещё >
Содержание
- Глава 1. Современное состояние вопроса и задачи исследований
- 1. 1. Ресурсосберегающие технологии горячей объемной штамповки
- 1. 2. Температурная интенсификация процессов объемной штамповки
- 1. 3. Дефекты, возникающие при объемной штамповке
- 1. 4. Методы исследования процессов объемной штамповки
- 1. 4. 1. Инженерные методы оценки НДС очага деформаций
- 1. 4. 2. Энергетические методы расчета НДС и силовых параметров
- 1. 5. Цель исследования и постановка задач
- Глава 2. Разработка технологии безоблойной штамповки деталей типа тройников с увеличенным диаметром фланцевой части
- 2. 1. Описание разработанной технологии штамповки детали тройник с увеличенным диаметром фланца
- 2. 2. Теоретический анализ силовых параметров технологического процесса
- 2. 2. Сравнительный анализ изменения технологической силы процесса деформирования по математическим и компьютерным моделям
- Выводы к главе 2
- Глава 3. Теоретический анализ температурных параметров технологических процессов
- 3. 1. Модель теплообмена в системе «поковка-инструмент» при штамповке
- 3. 2. Определение предельной степени пластичности
- Выводы к главе 3
- Глава 4. Экспериментальное исследование разработанной технологии
- 4. 1. Экспериментальная штамповка корпусных деталей по предложенной технологии
- 4. 2. Экспериментальное исследование силовых параметров
- 4. 2. 1. Регрессионный анализ
- 4. 3. 2. Методика определения сил штамповки
- 4. 4. 3. Обработка результатов экспериментальной штамповки вентильной головки и золотника
Повышение эффективности изготовления поковок сложной формы на основе совершенствования процессов горячей объемной штамповки в разъемных матрицах (реферат, курсовая, диплом, контрольная)
Актуальность работы. В отечественной промышленности распространены детали типа фланцев и тройников, в частности, в арматуростроении, нефтедобывающей и газодобывающей промышленности, строительной индустрии. Отрасль арматуростроения на сегодняшний день вполне продвинута и конкурентоспособна, однако актуален вопрос повышения эффективности производства и снижения себестоимости подобных изделий.
На сегодняшний день освоен ряд технологий горячей объемной штамповки поковок фланцевого типа. Традиционным методом их изготовления является облойная штамповка в открытых штампах. Среди главных преимуществ этого метода можно выделить высокую производительность и возможность получения относительно точных поковок простой формы. Однако у рассмотренного метода есть ряд недостатков: увеличенный расход металла, из-за наличия облоя и больших припусков и напусков, снижающих коэффициент использования металла. Облой является технологической необходимостью, т.к. он обеспечивает заполнение полости штампа, но потери металла при штамповке могут достигать 25% и более. Наличие облоя увеличивает силу деформирования и требует дополнительного оборудования для проведения операции обрезкипотребность в сравнительно больших технологических силах, из-за воздействия инструмента на всю площадь заготовки и наличия облоя требует завышенные мощности нагревательного и штамповочного оборудованияпроизводство деталей сложной формы (типа крестовин зубчатых колес, сплошных и полых ступиц с периферийными элементами в виде ребер, отростков, выступов и др.) средствами облойной штамповки становится особенно затратным из-за высокой трудоемкости последующей механической обработки.
Повысить эффективность изготовления деталей типа фланцев и тройников, а также устранить вышеуказанные недостатки позволяет технология безоблойной штамповки, основанная на методе комбинированного выдавливания в разъемных матрицах. Предложенная технология позволяет повысить коэффициент использования металла с 0,25−0,70 до 0,5−0,85, или на 20−60%, т. е. перевод на штамповку в разъемных матрицах одной тонны деталей дает экономию металла от 0,25 до 0,5 т.
При переходе на штамповку в разъемных матрицах производительность труда в среднем увеличивается на 25% за счет сокращения числа переходов штамповки с двух-четырех до одного-двух. Предложенный процесс штамповки, в отличие от облойной, может быть легко автоматизирован, так как выполняется за минимальное число переходов и обеспечивает хорошее центрирование и фиксацию заготовок в ручье. Расположение волокон в теле детали, в силу близости форм поковки и готовой детали, благоприятное. Важным преимуществом процесса является возможность предотвращения пористости деталей (за счет исключения выхода внутренних, загрязненных примесями, слоев заготовки на поверхность детали) и возможность получения монолитной крупногабаритной детали, исключающей последующие операции сварки и дополнительной механической обработки.
Однако, несмотря на большую эффективность, способ безоблойной штамповки долгое время не мог быть внедрен в широкое промышленное применение. Это объяснялось недостаточным техническим уровнем штамповочного производства, отсутствием специализированного оборудования, отсутствием как эмпирических, так и теоретически обоснованных формул для расчета температурных и силовых режимов безоблойной штамповки по переходам и т. п.
Объектом производства, имеющим фланец, для которого разрабатывался технологический процесс в настоящей работе, является тройник. Цель работы: Повышение эффективности изготовления сложнопрофильных деталей методами закрытой объемной штамповки за счет уменьшения коэффициента использования металла на основе применения штампов с разъемными матрицами.
Для достижения указанной цели необходимо решить следующие задачи:
— выявить влияние кинематики течения металла и температурного фактора при комбинированном выдавливании на возникновение дефектов;
— разработать компьютерные модели предложенных технологических процессов горячей штамповки;
— создать математические модели на основе предложенных схем деформирования с получением основных соотношений для расчета энергосиловых параметров;
— разработать рекомендации по проектированию устройств противодавления и конструирования штамповой оснастки, имеющей матрицы с горизонтальным и вертикальным разъемами;
— разработать новые технологии горячего комбинированного выдавливания поковок с развитыми фланцами.
Методы исследования. Компьютерное моделирование конечно-элементным методом применялось для оценки напряженно — деформированного состояния заготовки при сложном течении металла, установления возможных дефектов формообразования и внесения в конструкцию рабочего инструмента корректив для их устранения, а так же для оценки распределения температур в поковке. Математическое моделирование энергосиловых параметров процессов проводилось энергетическим методом. Распределение температуры в поковке определялось решением дифференциального уравнения Фурье при принятых допущениях и граничных условиях. Метод теплового баланса применялся для определения его составляющих в системе «заготовка-инструмент». Достоверность результатов подтверждается соответствием результатов компьютерного и математического моделирования с экспериментом, а также возможностью практического использования результатов работы в промышленности.
— в выявлении влияния геометрических параметров полости штампа, в частности, угла наклона конической части пуансона и радиусов скругления, на кинематику течения металла и заполняемость гравюр полуматриц при комбинированном выдавливании поковок сложной формы с разделением очагов деформации, анализ которых позволил изготавливать детали с увеличенным диаметром фланцевой части без потери устойчивости за меньшее число переходов на одной позиции пресса, а так же избежать дефектов в виде зажимов и недоштамповки;
— в выявлении взаимосвязи и характера изменения величин технологической силы деформирования и силы противодавления при горячем комбинированном выдавливании от геометрических соотношений размеров заготовки и поковки, от изменения относительного диаметра и высоты фланцевой части в процессе деформирования, от условий трения на контактных поверхностях, от температуры нагрева металла и степени его деформации;
— в компьютерных моделях, представляющих собой ЗД модели поковок реальных размеров, позволяющих оценить энергосиловые параметры разработанных технологических процессов горячей штамповки в разъемных матрицах, смоделировать кинематику течения металла и определить вектор направления скорости его течения, проанализировать температурные поля заготовки за цикл обработки, спрогнозировать образование поверхностных дефектов, в частности, в виде трещин на боковой поверхности фланцав математических моделях, основанных на энергетическом методе, и в основных аналитических соотношениях, позволяющих количественно определить необходимые активные и реактивные силы на заключительном этапе деформирования, а так же проанализировать характер их изменения на стадии формообразования фланцевой части.
Практическая значимость работы заключается:
— в разработке ресурсосберегающих технологических процессов безоблойной штамповки сложнопрофильных поковок с увеличенными размерами фланцевой части за ограниченное количество переходов, что повышает производительность при увеличении коэффициента использования металла за счет сокращения припусков и штамповочных уклонов, снижающего затраты на последующую механическую обработку, при снижении энергозатрат за счет уменьшения технологических сил и использования прессов с меньшей номинальной силой;
— в рекомендациях по разработке технологических процессов и конструированию штамповой оснастки при комбинированном выдавливании фланцевых поковок с диаметром фланцевой части до 70 мм и свыше 90 мм;
— в рекомендациях по конструированию специального устройства противодавления, встраиваемого в штамп с разъемными матрицами, позволяющего универсальным прессам работать в режиме прессов двойного действия при штамповке поковок близких типоразмеров, схожей номенклатуры.
Реализация работы. Полученные результаты и рекомендации приняты к использованию ООО «Коммунсельхозтехника» (г. Мценск, Орловской обл.). Апробация работы. Материалы диссертации были доложены и обсуждались:
— на научно — практической конференции студентов и аспирантов «Автоматизация и информационные технологии» 2007 года (ГОУ ВПО МГТУ «СТАНКИН»), 2008 года (почетная грамота), 2009 года (диплом);
— на всероссийской научно — технической конференции «Студенческая научная весна 2008: машиностроительные технологии» (МГТУ им. Н.Э. Баумана), (диплом лауреата 2й степени) — 2010 г. (диплом лауреата 1й степени);
— на XII научной конференции МГТУ «СТАНКИН» и «учебного центра математического моделирования МГТУ „СТАНКИН“ — ИММ РАН» по математическому моделированию и информатике в 2009 года;
— на XIII Международной научно-технической конференции «Новые наукоемкие технологии, оборудование и оснастка для обработки металлов давлением» (ДГМА, Краматорск, 2010 г.);
— на XV Международной научно-технической конференции «Достижения и проблемы развития технологий и машин обработки металлов давлением» (ДГМА, Краматорск, 2012 г.);
— принимали участие в конкурсах:
1) в Открытом конкурсе 2007 и 2008 годах на лучшую научную работу студентов ВУЗов по естественным, техническим и гуманитарным наукам (грамоты);
2) на соискание премии имени академика А. И. Целикова за лучшую научную студенческую работу в области металлургического машиностроения (ВНИИМЕТМАШ — 2008 г.) (диплом III степени);
3) на IX всероссийской выставке Научно — Технического Творчества Молодежи (НТТМ 2009 г.) (грант II степени Правительства РФ). Публикации: основные положения диссертации отражены в 15 публикациях, включая 4 в рецензируемых научно-технических журналах из перечня ВАК, 1 патент на изобретение.
Структура и объем работы. Диссертация состоит из введения, четырех глав, заключения и списка литературы из 101 наименования и приложений. Работа содержит 94 страницы машинописного текста, 51 рисунок, 28 таблиц. Общий объем работы составляет 116 страниц.
Общие выводы.
1. В диссертационной работе изложены научно-обоснованные технологические разработки, связанные с повышением эффективности изготовления поковок сложной формы на примере «тройника», способствующие совершенствованию процессов горячей объемной штамповки за счет использования разъемных штампов, что имеет существенное значение для экономики и обеспечения обороноспособности страны.
2. Выявлено влияние геометрических параметров полости штампа, в частности, угла наклона конической части пуансона и радиусов скругления, на кинематику течения металла и заполняемость гравюр полуматриц при горячем комбинированном выдавливании поковок сложной формы с разделением очагов деформации, что позволило получать детали с увеличенным диаметром фланцевой части без потери устойчивости за меньшее число переходов на одной позиции пресса, увеличить номенклатуру поковок, а так же избежать дефектов в виде зажимов и недоштамповок.
3. На основе математических моделей теплопереноса, основанных на энергетическом методе, проанализировано тепловыделение, сопровождающее процессы деформирования, с получением тепловых полей поковки и расчетом составляющих теплового баланса системы «поковка — инструмент», что дало возможность рассчитать максимально возможный диаметр фланцевой части поковки, который можно получить без образования трещин на боковой поверхности. Полученная модель теплопереноса позволяет определить распределение температуры в самой поковке, а так же в пограничных слоях поковки и инструмента, что позволяет с некоторой степенью приближения определить температуру нагрева инструмента, спрогнозировать долговечность его работы.
4. Построенные компьютерные модели процессов деформирования на стадии предпроектных расчетов дало возможность смоделировать кинематику течения металла, смыкание полуматриц и движение их как единого инструмента, что позволило спрогнозировать образования дефектов в виде зажимов и недоштамповок, внести необходимые корректировки в геометрию полости штампа, определить оптимальный угол наклона конической части пуансона для получения увеличенного диаметра фланцевой части поковок без потери устойчивости, получить распределение тепловых полей поковки для подтверждения адекватности расчетных зависимостей.
5. Разработанная математическая модель расчета силовых параметров штамповки в разъемных матрицах, основанная на энергетическом методе, позволила установить взаимосвязь активных и реактивных сил при горячем комбинированном выдавливании от геометрических соотношений размеров заготовки и поковки, от изменения относительного диаметра и высоты фланцевой части в процессе деформирования, от условий трения на контактных поверхностях, от температуры нагрева металла и степени его деформации как на заключительной стадии деформирования, так и на протяжении всего процесса формообразования фланцевой части поковки.
6. Полученные аналитические зависимости на основе разработанной математической модели дали возможность определить количественную оценку силы противодавления, необходимой для смыкания разъемных матриц и удержания их в сомкнутом состоянии на протяжении всего процесса деформирования, что позволило обосновать выбор вертикального разъема полуматриц для получения крупногабаритных сложных поковок с увеличенным диаметром фланцевой части (свыше 90 мм).
7. На основа анализа устройств противодавления и опыта их проектирования разработаны рекомендации по выбору рациональных конструкций для реализации технологических процессов штамповки в разъемных матрицах на примере поковок тройник и фланец.
8. Полученные результаты и рекомендации приняты к использованию на ООО «Коммунсельхозтехника» (г. Мценск, Орловской обл.). геометрических.
Список литературы
- Акаро И.Л., Акаро А. И. Малоотходная полугорячая штамповка. -ЦНИИТЭСтроймаш. — 1990. — С.48.
- Акаро И.Л., Балаганский В. И., Смольникова Л. М. Новые технологии и проект автоматизированного комплекса для производства заготовок зубчатых колес, фланцев и колец// Кузнечно-штамповочное производство. 1995. — № 7. — С. 18−21.
- Алиев И.С. Технологические возможности новых способов комбинированного выдавливания// Кузнечно-штамповочное производство. -1990. -№ 2.-С.7−10.
- Алиева Л.И., Жбанков Я. Г., Грудкина Н. С. Формообразование детали в процессе комбинированного радиально-обратного выдавливания//Сб. научных трудов: Обработка металлов давлением. -ДГМА.-2010.-с. 16−19.
- Аркулис Г. Э. Теория пластичности // учебное пособие для вузов- М.: Металлургия. 1987. — 352 с.
- Артес А.Э. Холодная объемная штамповка в мелкосерийном и серийном производстве. М.: НИИмаш, 1982. — 58 с.
- Атрошенко А.П., Федоров В. И. Металлосберегающие технологии кузнечно—штамповочного производства. Л.: Машиностроение. Ленингр. Отделение. — 1990. — 279 с.
- Барков B.C. Безоблойная штамповка в разъемных матрицах поковок с фланцем// Кузнечно штамповочное производство. — 1983 г. — № 9.-С.17−18.
- Басюк С.Т. Изготовление поковок сложной формы в штампах с разъемными матрицами// Кузнечно-штамповочное производство. 1973. -№ 7. — С.8−11.
- Бильчук М.В. Разработка и исследование закрытой объемнойштамповки поковок сложной формы. // Кузнечно-штамповочное производство. 2010. — № 6. — С.9−13.
- Бильчук М.В. Разработка и исследование технологии штамповки вентильной головки// Студенческая научно-практическая конференция «Автоматизация и информационные технологии». Сб. докладов. М: МГТУ «СТАНКИН», — 2008, — С. 17−19.
- Бильчук М.В. Совершенствование технологии изготовления деталей арматуростроения // Электронное научно техническое издание «Наука и образование», 2008. — № 6. — http://technomag.edu.ru/doc/99 358.html
- Бильчук М.В. Совершенствование технологии изготовления деталей арматуростроения// Пятая юбилейная конференция молодых специалистов «Металлургия XXI века» 2009 год. Сб. тезисов докладов. М.:
- АХК ВНИИМЕТМАШ им. акад. А. И. Целикова. 2009. — С.44.
- Бильчук М.В., Сосенушкин E.H. Прогнозирование образования поверхностных дефектов фланцевой части поковок при горячей объемной штамповке// Вестник МГТУ «СТАНКИН». Научный рецензируемый журнал. М.: МГТУ «СТАНКИН».- 2012. — № 4(23). — с. 44−48.
- Бильчук М.В., Артес А. Э., Третьюхин В. В. Применение безоболойной штамповки в разъемных и полузакрытых штампах// Известия Самарского научного центра Российской академии наук, 2012. том 14. — № 45.-с. 1199- 1201
- Бильчук М.В., Артес А. Э., Третьюхин В. В. Преимущества технологии безоблойной штамповки// Обработка металлов давлением, 2013. № 2(35). — с. 76−79.
- Бровман М.Я. Особенности процесса прокатки привозникновении внутренних трещин // Изд. Ан СССР. Металлы. 1982. — № 4.-с. 60−64.
- Волик Ю.П., Бойцов В. В. Штамповка поковок автомобильных крестовин в разъемных матрицах//Автомобильная промышленность. -1962. -№ 4.
- Воронцов А.Л. Деформационное состояние заготовки при радиальном выдавливании// Вестник машиностроения. 1999.- № 10. — с. 3639.
- Воронцов А.Л. Метод расчета накопленных деформаций при выдавливании полых изделий типа стакан// Вестник машиностроения. -1999.-№ 7. -с. 41−45.
- Воронцов А.Л. Напряженное состояние заготовки при выдавливании полых изделий цилиндрическим пуансоном с радиусными фасками// Вестник машиностроения. 2000.- № 9. — с. 46−49.
- Воронцов А.Л. Напряженное состояние заготовки при выдавливании с раздачей// Кузнечно-штампововчное производство. 1997.-№ 7.-с. 15−19.
- Воронцов А.Л. Напряженное состояние заготовки с учетом упругой деформации матрицы при выдавливании полых изделий с реактивными и активными силами трения// Вестник машиностроения. -2001.-№ 6. с. 51−56.
- Воронцов А.Л. Определение технологических параметров выдавливания стаканов с активными силами трения и в незакрепленной матрице// Вестник машиностроения. 2003.- № 12. — с. 61−67.
- Воронцов А.JI. Теория выдавливания цилиндрических стаканов с противонапряжением// Производство проката. 2004. № 11. С. 29−33.
- Воронцов А. Л. Теория малоотходной штамповки. М.: Машиностроение. 2005. 859 с.
- Воронцов А. Л. Теория штамповки выдавливанием. М.: Машиностроение. 2004. 721 с.
- Воронцов А.Л., Морозова Ю. Д., Сафонова Г. Г. Анализ образования утяжины при радиальном выдавливании трубных заготовок// Вопросы исследования прочности деталей машин: Межвузовский сборник научных трудов. Вып. 6. М.: МАМИ. 2000.-c.3−6.
- Губкин С.И. Пластическая деформация металлов, Т.2. М.: Металлургиздат, 1960.
- Дель Г. Д., Томилов Ф. Х., Дель В. Д., Анфилофьев A.B., Огородников В. А. Определение поля температур в пластической области при прессовании// Кузнечно-штамповочное производство. 1973. — № 12 — С. 1−3.
- Демидов Л.Д. Исследование условий теплопередачи от заготовки к штампу//Кузнечно-штамповое производство. 1966. — № 9.
- Джонсон У. Теория пластичности для инженеров // Пер. с англ. А. Г. Овчинников. -М.: Машиностроение. 1979. — 567 с.
- Довнар С.А. Термомеханика упрочнения и разрушения штампов объемной штамповки. М.: Машиностроение, -1975. -247с.
- Драйпер Н., Смит Г. Прикладной регрессионной анализ: В 2кн.: пер. с англ. 2-е изд., перераб. и доп. Кн. 1 М.: Финансы и статистика. 1986. -366 с.
- Залесский В.И., Тюрин Н. И. Исследование процесса штамповки металла в закрытых штампах// Кузнечно-штамповочное производство. -1959. -№ 1.-С.4−8.
- Зимин В.В., Лозовский В. А. Зависимость коэффициента контактного теплообмена от некоторых условий штамповки// Кузнечно-штамповочное производство, 1975.-№ 10. с.37−40.
- Карпов C.B. Разработка математической модели кузнечной операции осадки (осесимметричный случай) // Автореф. дисс. канд. техн. наук. Свердловск. — 1979. — 24с.
- Катрич Ю.П. Штамповка в закрытых штампах с разъемными матрицами (в порядке обсуждения)// Кузнечно-штамповочное производство. -2010. -№ 12.-С.23−28.
- Кенбаев A.C., Ланской E.H., Сосенушкин E.H. Расчет теплопроводности при полугорячем выдавливании//Кузнечно-штамповочное производство. 1992. — № 3. С. 20−22.
- Ковка и объемная штамповка стали: справочник/под редакцией М. В. Сторожева. -М.: Машиностроение. 1967. — 457 С.
- Ковка и штамповка: Справочник в 4-х т./Ред. Совет: Е. И. Семенов (пред.) и др. М.: Машиностроение. — 1986. — т.2. Горячая штамповка/Под ред. Е. И. Семенова. — 1986. — 592 с.
- Колмогоров В.Л. Механика обработки металлов давлением, 2-е издание, перераб. и доп./ В. Л. Екатеринбург: Издательство Уральского государственного университета УПИ. — 2001. — 836 с.
- Колмогоров В.Л. Принцип возможных изменений напряженно -деформированного состояния //Инженерный журнал. Механика твердого тела. 1967. — № 2. -С.143−148.
- Коцюбивская Е.И. Повышение эффективности процессов холодного выдавливания осесимметричных деталей с фланцем за счет применения противодавления//Дис. на соиск. уч. ст. к.т.н., Винница. -2007. -С.260.
- Кузнецов A.B., Протопопов O.B. Двухпереходный технологический процесс горячего выдавливания стальных поковок в разъемных матрицах//Кузнечно-штамповочное производство. № 7.-1966. -С. 18−20.
- Кузнецов A.B., Протопопов О. В., Клочков В. Т. Штамповка поковок выдавливанием в разъемных матрицах (состояние и перспективы)// Кузнечно-штамповочное производство. 1980. — № 11. — С.2−6.
- Кузнецов Г. В., Мирошниченко В. М., Канзберг Ю. И. Комбинированное выдавливание деталей с фланцем// Кузнечно-штамповочное производство. 1974. — № 5. — С.21−23.
- Кутышкин A.B. Экспериментальные исследования формоизменения заготовок при штамповке круглых в плане поковок// Кузнечно штамповочное производство. — 1989. — № 6. — С.25−30.
- Ланской E.H. 50 лет развития технологии обработки металлов давлением в Московском государственном технологическом университете «Станкин» // Кузнечно штамповочное производство. — 1993. — № 4.- С.2−3.
- Лыков A.B. Теория теплопроводности. М.: Высшая школа, 1967.
- Лясников A.B., Агеев Н. П., Кузнецов Д. П. и др. Сопротивление материалов пластическому деформированию в приложениях к процессам обработки металлов давлением СПБ.: БГТУ, ГП «Внештогргиздат -Петербург». — 1995. -527с.
- Лях А.П., Белоусова C.B. Исследование напряженного состояния штампов для многоплунжерной штамповки// Кузнечно-штамповочное производство, 1989. — № 12. — с. 2−4.
- Марков A.A., О вариационных принципах в теории пластичности // ЦММ. 1947. -T.XI. — С.239−250.
- Морковкин Б.В. Штамповка поковок в закрытых штампах// Автомобильная промышленность.-1967.-№ 2.-с. 5−15.
- Натанзон Е.И., Темянко A.C., Губин Ю. А. Полугорячая штамповка шестерен на автоматической линии // Кузнечно-штамповочное производство. 1989. — № 3. — С.3−8.
- Непершин Р.И. Пластическое течение при осадке в конических плоскостях//Машиноведение. 1967. — № 4. — стр. 124−133.
- Непершин Р. И Плоское пластическое течение в полости с наклонными стенками// Машиноведение. 1966. — № 6. — стр.115−119.
- Непершин Р.И. Модели горячей объемной штамповки поковки шестерни на КГШП и молоте// Кузнечно-штамповочное производство. Обработка металлов давлением. 2011. — № 7. — стр. 42−45.
- Непершин Р.И. Модели горячей объемной штамповки поковки шестерни на КГШП и молоте (продолжение)// Кузнечно-штамповочное производство. Обработка металлов давлением. 2011. — № 8. — стр. 23−32.
- Николаев В.В. Разработка технологии горячей штамповки фланцев с развитой втулочной частью// Кузнечно-штамповочное производство ОМД. 2004. — № 6. — С. 13−15.
- Оленин Л.Д. К расчету технологических переходов при холодном комбинированном выдавливании. // Сб. «Объемная штамповка». -МДНТП. 1967.
- Поляков И.С., Золотницкий В. А. Штамповка поковок типа крестовин в закрытых штампах// Кузнечно-штамповочное производство. -1964. № 4.-С.
- Прандтль JI.O. О твердости пластических материалов и сопротивлении резанию. М.: Гос. изд. иностр. лит. — 1948. — С.70−79.
- Примеры использования обобщенного вариационного принципа для идеальной пластической среды/Юбработка металлов давлением. -ВИЛС. 1976. — с.63−68.
- Расчеты процессов обработки металлов давлением в Matchcad. H.A. Шестаков. М.: МГИУ, 2008. — 344с.
- Ребельский A.B. и др. Изготовление поковок в штампах с разъемными матрицами.// Сб. «Опытные работы по штамповке выдавливанием».
- Рожков С.И., Кирсанов К. А. Об одно- и двустороннем выдавливании заготовок корпусов энергетической арматуры// Кузнечно-штамповочное производство. 1974. — № 6. — С.5−7.
- Сегал В.М. Обзор современного состояния теории ОМД // Кузнечно штамповочное производство. — 1970. — № 9. -С.2−7.
- Семендий В.И., Акаро И. Л., Волосов H.H. Прогрессивные технологии, оборудование и автоматизация кузнечно-штамповочного производства КамАЗа. М.: Машиностроение. — 1989. — 304 с.
- Семенов Е.И. Технология и оборудование ковки и горячей объемной штамповки. М.: Машиностроение, 1999. — 384 с.
- Семинар «Современные высокопроизводительные металлообрабатывающие технологии и оборудование к ним» //Кузнечно -штамповочное производство. 2005 — № 7. — С.34−43.
- Смирнов Аляев Г. А. Сопротивление материалов пластическому деформированию — Л.: Машиностроение, 1978. — 368 С.
- Смирнов Аляев Г. А., Розенберг В. М. Теория пластических деформаций металлов. — М., Л. Машгиз. — 1956. -357 с.
- Соколовский В.В. Теория пластичности— М.: Высшая школа. -1969.-608 с.
- Степанский JI.Г. Расчетная оценка температурных условий прессования жаропрочных сплавов// Кузнечно-штамповочное производство.- 1970. -№ 1.-С.
- Степанский Л.Г. Расчеты процессов обработки металлов давлением -М.: Машиностроение. 1979. -215 с.
- Степанский Л.Г. Энергетический критерий разрушения металла при обработке давлением// Кузнечно-штамповочное производство. № 9 -1988.-с. 1−5.
- Степанский Л.Г., Петров А. И., Яхнис М. А. Расчеты формоизменения при облойной штамповке круглых в плане поковок // Кузнечно-штамповочное производство. 1985. — № 1. — С. 18−19.
- Стерник Ю.Л. Расчет температурного поля при прессовании// Кузнечно-штамповочное производство. — 1966. № 7 — С.
- Сторожев М.В., Попов Е. А. «Теория обработки металлов давлением». М.: Машиностроение, 1977. — 423с.
- Таблицы математической статистики. М.: Наука. 1983. — 416 с.
- Теория обработки металлов давлением/ И. Я. Тарновский, А. А. Позднеев, O.A. Ганаго и др. М. Металлургия, 1963.
- Теория пластических деформаций металлов/ Е. П. Унксов, У. Джонсон, В. Л. Колмогоров и др.- под редакцией Е. П. Унксова, А. Г. Овчинникова. М.: Машиностроение.- 1983. — 598 с.
- Технология кузнечно-штамповочного производства/ Я. М. Охрименко. М.: Машиностроение. — 1976. — 560 с.
- Томлёнов А.Д., Теория пластического деформирования металлов— М.: Металлургия. 1972. — 408с.