Создание технологии производства крупных кузнечных слитков с улучшенными свойствами на основе управления параметрами слитка и процессами разливки стали в вакууме
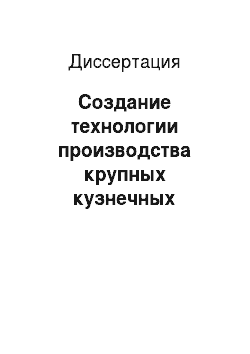
На основании сравнительной оценки эффективности вакуумирования основных и кислых сталей предложена комплексная внепечная обработка жидкого металла, включающая проведение необходимых технологических операций в УДМ, последующую отливку слитков и непрерывнолитых заготовок в вакууме с подачей инертного газа в струю и инокулированием расплава за счёт создания условий для дополнительного распыления… Читать ещё >
Содержание
- Глава 1. Анализ современных концепций процессов вакуумной отливки слитков и формирования качества металла
- 1. Роль геометрических параметров в формировании структуры слитков. П
- 2. Анализ эффективности процессов струйного вакуумирования стали
- 2. 1. Особенности взаимодействия газов с жидким металлом
- 2. 2. Теоретические предпосылки и технологические основы вакуумирования жидкой стали
- 2. 2. 1. Термодинамика и кинетика процессов дегазации
- 2. 2. 2. Особенности механизма удаления газов из расплава в процессе вакуум-углеродного раскисления стали
- 2. 3. Анализ технологических процессов вакуумирования жидкого металла
- 2. 4. Влияние вакуумирования на качество металла
- 2. 5. Анализ механизма процессов дегазации вакуумируемого металла
- 3. Фомирование структуры слитков и принципы управления
- 1. Ш процессами затвердевания металла
- 3. 1. Термодинамические основы затвердевания металлов и роль переохлаждения в процессах кристаллизации
- 3. 2. Влияние перегрева на величину переохлаждения металла для обычных и инокулированых расплавов
- 3. 3. Особенности кристаллизации и формирования структуры инокулированного металла
- 3. 4. Влияние инокуляторов на содержание неметаллических включений в стали
- 1. Исследование влияния параметров слитка и технологических факторов на качество металла
- 1. 1. Анализ особенностей конфигурации промышленных слитков различной массы
- 1. 2. Исследование и моделирование влияния технологических факторов и геометрических параметров слитков на качество Л- металла
- 1. 3. Оптимизация геометрических параметров крупных слитков с целью уменьшения осевых дефектов и получения благоприятной структуры металла
- 1. 4. Анализ связи структуры слитка с механическими свойствами
- 2. Теоретические и промышленные исследования процесса кристаллизации и качества металла слитков с изменённой геометрией донной части
- 2. 1. Математическое моделирование процесса кристаллизации сравнительного и опытного слитков
- 2. 2. Промышленное исследование строения слитка новой конфигурации
- 2. 2. 1. Методика исследований
- 2. 2. 2. Обсуждение результатов исследования
- 1. Исследование влияния технологических параметров разливки на степень дегазации металла
- 1. 1. Технологические особенности выплавки стали для крупных слитков
- 1. 2. Технологические режимы отливки слитков в вакууме
- 1. 3. Методика проведения исследований
- 1. 4. Обсуждение результатов
- 2. Определение вклада струи в процесс дегазации и оценка её реакционной поверхности по данным промышленных исследований
- 3. Оценка эффективности струйного вакуумирования стали и проблемы дегазации при отливке крупных слитков
- 4. Анализ кинетики удаления газов при вакуумной разливке стали и возможности интенсификации этого процесса
- 1. Анализ условий образования газовой фазы в струе
- 2. Проведение исследований на холодной модели
- 2. 1. Физическое моделирование процесса струйного вакуумирования стали
- 2. 2. Методика проведения лабораторных исследований
- 2. 3. Определение оптимальных параметров расположения стопора при продувке струи азотом
- 2. 3. 1. Расчёт высоты подъёма стопора на холодной модели
- 2. 3. 2. Определение высоты подъёма стопора на компьютерной модели
- 2. 4. Исследование процесса интенсификации дегазации струи на водном растворе СО
- 3. Интенсификация вакуумирования металла в промышленных условиях
- 3. 1. Методика исследования
- 3. 2. Отливка опытных слитков с продувкой струи аргоном
- 3. 3. Распределение неметаллических включений в поковках, полученных из сравнительного и опытного слитков
- 3. 4. Анализ механических свойств металла опытных поковок
- 1. Исследование процесса образования инокуляторов
- 1. 1. Расчёт температурных характеристик процесса разливки м’е-~ талла в вакууме
- 2. Математическое моделирование и основы регулирования процесса формирования инокуляторов при разливке металла в вакууме
- 3. Исследование возможности развития окислительных процессов на поверхности падающих в вакууме капель
- 3. 1. Методика проведения исследований
Создание технологии производства крупных кузнечных слитков с улучшенными свойствами на основе управления параметрами слитка и процессами разливки стали в вакууме (реферат, курсовая, диплом, контрольная)
Производство изделий ответственного назначения — роторов турбогенераторов, судовых валов, изделий атомной энергетики является важным направлением в развитии отечественного машиностроения.
Увеличение мощности тепловых и гидроэлектростанций обусловило возрастание требований к качеству поковок валов роторов турбогенераторов. Для изделий атомной энергетики необходимы корпуса реакторов, способные выдерживать мощные потоки ионизирующего излучения, что в большой степени связано с качеством получаемого металла.
Интенсивное развитие нефтедобывающих и других отраслей ставит задачу изготовления современных нефтеналивных супертанкеров, оснащённых мощными силовыми агрегатами, для эксплуатации которых требуются судовые валы весьма больших размеров и с более высоким уровнем механических и специальных свойств.
Изготовление качественных крупных поковок является до настоящего времени сложной технической задачей, что обусловлено сильным развитием ликвационных процессов, неравномерностью распределения неметаллических включений, физической неоднородностью по объёму слитка, и другими пороками, присущими процессу затвердевания больших масс металла. При этом увеличение массы слитков приводит к усилению развития дефектов. Особой актуальностью обладают научные изыскания и технологические разработки, направленные на уменьшение содержания газов в металле.
Неоднородное строение и неравномерность свойств металла крупных поковок обусловлено повышенным содержанием газов в расплаве и неблагоприятным распределением неметаллических включений по объёму слитка и поковки. Избыточная концентрация газов в жидкой стали является главной причиной снижения механических свойств в готовых изделиях за счёт образования в слитке газовой пористости, флокенов, трещин и других дефектов. Применяемые в настоящее время методы внепечного вакуумирования позволяют существенно снизить остаточное содержание газов в металле до значений, близких к пределу их растворимости в твёрдом железе. Однако повышение требований к служебным и эксплуатационным свойствам изделий современных силовых установок выдвигает задачу получения стальных поковок с более высокими механическими характеристиками, обеспечивающими безотказную работу крупногабаритных агрегатов и систем в течение длительного времени.
Не менее важной проблемой остаётся оптимальный выбор геометрических параметров слитка, обеспечивающий минимальное развитие осевых дефектов, структурной и химической неоднородности и повышение выхода годного в поковку. Выбор той или иной конфигурации слитка в производственных условиях определяется, как правило, имеющейся мощностью прессового оборудования и сложившимися традициями.
Использование методов управления структурой слитка, в частности разливки металла с вводом инокуляторов, предполагает за счёт дозирования и подбора соответствующего химического состава железных порошков осуществлять целенаправленное воздействие на формирование макроструктуры отливаемого металла. Однако наличие окисной плёнки на поверхности вводимых порошков приводит к повышению содержания неметаллических включений и возрастанию концентрации растворённых газов, что не позволяет реализовать все очевидные преимущества суспензионного литья.
Проблему повышения долговечности и надёжности изделий ответственного назначения необходимо решать путём улучшения качества отливаемого металла и, прежде всего, за счёт повышения его чистоты.
Опыт использования струйного вакуумирования стали при отливке крупных слитков на ведущих машиностроительных комплексах — ПО «Баррикады», АО «Ижорские заводы», заводе «Энергомашспецсталь» и др. продемонстрировал высокую эффективность этого метода, однако недостаточная изученность кинетических особенностей этого процесса и неодназначность представлений о механизме дегазации стали затрудняет поиск научных направлений и технологических решений, обеспечивающих проведение вакуумной обработки металла с наибольшей эффективностью. Целью работы являлось: Создание технологии получения крупных стальных слитков высокого качества за счёт оптимизации геометрических параметров слитка и его формы, управления процессом дегазации и разливки металла.
В соответствии с указанной целью были поставлены следующие задачи:
— оптимизация геометрических параметров и формы кузнечных слитков с целью получения в осевой зоне благоприятной структуры с минимальным количеством дефектов и повышения выхода годного;
— исследование качества металла слитков и поковок различной массы;
— установление кинетических закономерностей процесса дегазации при вакуумной отливке крупных слитков;
— разработка методов управления процессом вакуумирования металла на базе интенсификации дегазации струи потоком инертного газа;
— разработка оптимальных технологических режимов вакуумирования слитков различной массы;
— разработка методов управления процессом затвердевания капель в вакууме, обеспечивающих целенаправленное, регулирующее воздействие на формирование структуры слитка.
— оценка перспективы развития внепечного вакуумирования стали с целью повышения качества крупных слитков и непрерывнолитых заготовок.
Поставленные цели обусловили необходимость разработки новых научно-обоснованных решений по созданию комплексной технологии производства крупных стальных слитков, обеспечивающей возможность управления процессами дегазации и кристаллизации отливаемого металла и целенаправленного воздействия на его структуру.
Анализ сложившихся технологических процессов, оценка по результатам проведённых промышленных исследований их преимуществ и недостатков, позволили разработать основные принципы создания комплексной технологии производства крупных слитков для поковок ответственного назначения, обеспечивающей получение металлоизделий с гарантией высокого качества и надёжности.
Разработаны и внедрены научно обоснованные технические и технологи.
11 ческие решения, которые вносят значительный вклад в ускорение научно-технического прогресса и расширяют возможности производства изделий энергетического и крупного машиностроения.
Общие выводы.
1. Анализом влияния геометрических параметров слитка на строение и качество металла определена связь между конфигурацией слитка и особенностями формирования его осевой области. Установлено, что с возрастанием параметра H/D уменьшается угол раскрытия V-образной неоднородности, а конусность слитка и параметр H/D связаны между собой обратной зависимостью. Все крупные слитки по геометрическим параметрам относятся к нормальному типу.
По результатам математического моделирования и оптимизации зависимостей структурных характеристик слитка от его геометрических параметров и технологических факторов выявлено, что высота конуса осаждения, размеры зоны дугообразных трещин, протяжённость области V-образных трещин определяются значениями конусности слитка, относительного объёма прибыли, температурой разливки и скоростью наполнения изложницы металлом.
2. На основе исследования и анализа кинетики кристаллизации слитков с изменённой геометрией донной части (выпуклым поддоном) установлено, что в слитках новой формы протяжённость зоны осевой рыхлости сокращается на 10%, за счёт уменьшения ширины двухфазной зоны и возрастания скорости затвердевания осевых объёмов слитка. По своим структурным и качественным характеристикам слитки с измененной конфигурацией донной части превосходят слитки традиционной формы, и при этом имеют повышенный на 3% выход годного в поковку, что делает их производство экономически целесообразным.
3. Теоретически проанализирован и экспериментально исследован процесс дегазации при вакуумной отливке слитков массой 24,2. 140,0 топределены основные кинетические закономерности вакуумирования. Установлено, что единственным технологическим параметром, влияющим на степень дегазации кислой стали в условиях сложившейся технологии производства крупных слитков, является средняя скорость разливки, с уменьшением которой эффективность дегазации существенно возрастает. При вакуумировании в струе основных сталей полнота выделения газов определяется степенью раскисленности обрабатываемого металла.
4. Всесторонне исследован и описан процесс дегазации струи в вакууме. Установлено, что на долю струи приходится 70% газов, выделяющихся при разливке металла в вакууме. Промышленными экспериментами и теоретическим расчётом определена величина удельной реакционной поверхности струи, составляющая около 3 м /кг и приближённое значение эффективного коэффициента массопереноса, составляющего 63−10″ 3 см/с. Показано, что для интенсификации процесса дегазации необходимо повышение степени перемешивания металла в струе и создание дополнительной реакционной поверхности за счёт ввода в струю инертного газа.
5. Впервые, по результатам исследований, определена оптимальная форма разливочного стакана для разливки металла в вакууме (в виде внутренней спиральной полости), практически обеспечивающая завершённость процесса дегазации струи. Цилиндрические стаканы, с точки зрения кинетики дегазации обладают наименее выгодной формой.
6. Промышленными исследованиями по интенсификации процесса струйного вакуумирования стали установлено, что при вводе в струю инертного газа с расходом 150. 160 л/мин. и зазоре между пробкой стопора и торцем разливочного стакана 50.60 мм дегазация проходит в оптимальном режиме, характеризующимся возрастанием удельного количества выделяющейся окиси углерода на 20.30%.
7. Металлографическим анализом поковок, полученных как из слитков с продувкой металла инертным газом, так и по обычной технологии, показано изменение характера распределения неметаллических включений, заключающееся в уменьшении их количества в осевой зоне донной части опытных поковок и возрастании в периферийных областях, а также уменьшением среднего размера включений вдвое по сравнению с металлом штатных поковок.
8. Впервые теоретически обоснован и экспериментально исследован процесс кристаллизации капель струи при разливке металла в вакууме и разработаны принципы управления затвердеванием капельной зоны струи. Установлено, что процессы окисления капель в вакууме имеют место, но они не получают достаточного развития за счёт низких концентраций кислорода в каплях и слабого окислительного потенциала газовой фазы вакуумной камеры. Показано, что образующиеся в процессе разливки инокуляторы оказывают благоприятное воздействие на формирование структуры слитка и на свойства готовых изделий.
9. По результатам промышленных исследований установлено оптимальное соотношение между концентрациями серы и кислорода (коэффициент стабильности сульфидных включений (КФс = [S]/[OJ < 2,0), обеспечивающее формирование оксисульфидных включений в вакуумируемых хромоникельмолиб-денованадиевых сталях в достаточных количествах и обеспечивающее высокий уровень пластических характеристик готовых изделий.
10. На основании сравнительной оценки эффективности вакуумирования основных и кислых сталей предложена комплексная внепечная обработка жидкого металла, включающая проведение необходимых технологических операций в УДМ, последующую отливку слитков и непрерывнолитых заготовок в вакууме с подачей инертного газа в струю и инокулированием расплава за счёт создания условий для дополнительного распыления струи. Данная технология позволяет обеспечить глубокую десульфурацию жидкого металла, контролируемый процесс образования оксисульфидных включений, эффективное удаление газов из расплава и целенаправленное воздействие на процесс кристаллизации отливаемых слитков.
11. Полученные в работе теоретические и экспериментальные результаты, установленные зависимости и закономерности являются базой для разработки комплексной технологии производства крупных кузнечных слитков, обеспечивающей управление процессами разливки, дегазации и кристаллизации металла в оптимальных режимах, на основе этого:
11.1. Разработана и внедрена в производство (ПО «Баррикады») технология вакуумной отливки слитков массой до 71,5 т с продувкой струи инертным газом, обеспечивающая повышение пластических и специальных свойств поковок:
— по ударной вязкости — на 10. .20%;
— по относительному удлинению — на 8. .10%;
— по относительному сужению — до 20%- а также снижение переходной температуры хрупкости в среднем на 12 °C, и уменьшение остаточных напряжений в опытных поковках в среднем в 10 раз.
11.2. Внедрён метод отливки слитков с регулированием процесса затвердевания капель в струе, что позволило улучшить структурные и ликвационные характеристики отливаемых слитков и уменьшить разброс механических свойств по длине поковок в следующих пределах:
— для низколегированных конструкционных сталей — в 2.3 раза;
— для углеродистых сталей — от 2 до 10 раз;
11.3. Отливка слитков с изменённой донной частью (выпуклый поддон) массой от 24,2 до 50,3 т обеспечила повышенный на 3% выход годного в поковку, что делает их производство экономически целесообразным.
Всё это позволило машиностроительному объединению «Баррикады» и родственным предприятиям существенно снизить отбраковку крупногабаритных изделий ответственного назначения и увеличить объёмы поставок этих изделий на экспорт. Экономический эффект от внедрения разработок составил 3 млн. 601 тыс. 520 руб.
Заключение
.
По литературным данным проведён обзор использования внепечных методов обработки металла в современных процессах производства стали. На основе этого обзора показана возрастающая роль вакуумирования металла, применяемого в том числе и в массовом производстве для получения качественных непрерывнолитых заготовок.
Для основных сталей кроме вакуумирования необходима внепечная обработка расплава с целью удаления избыточного количества неметаллических включений, в том числе оксидов и оксисульфидов. Вакуум-струйная обработка нераскисленных основных сталей обеспечивает получение металла с содержанием водорода в 1,5 раза меньшим по сравнению с раскисленными сталями. Для нераскисленных сталей остаточная концентрация водорода в вакуумируе-мом металле контролируется только величиной разрежения вауум-камеры.
Сравнительная оценка эффективности вакуум-углеродного раскисления и удаления водорода в процессе струйного вакуумирования основных и кислых сталей показала, что при обычных режимах дегазации (Рост. = 0,26.0,65 кПа) степень удаления газов в обоих случаях является одинаковой и обеспечивает безопасные пределы содержания водорода для флокеночувствительных сталей.
Анализ качества основного и кислого металла показал более высокий уровень и малую анизотропию свойств кислой стали за счёт образования сла-бодеформируемых силикатных включений благоприятной округлой формы. Для основной стали характерно наличие оксидов и сульфидов, располагающихся по границам зёрен в виде плён, и оказывающих неблагоприятное влияние на свойства готовых изделий.
При анализе вакуумированных сталей обоих типов выявлено некоторое снижение ударной вязкости поковок, полученных из этого металла. Это связано с особенностями выделения оксисульфидов, часть которых в результате глубокого вакуум-углеродного раскисления расплава и уменьшения количества оксидных и силикатных включений располагается в виде плён в межзёренных пространствах.
Для оценки влияния концентраций серы и кислорода на характер образующихся неметаллических включений введена формальная характеристика, представляющая отношение [S]/[0], называемая коэффициентом стабильности сульфидных включений.
С учётом особенностей формирования неметаллических включений для получения высококачественного металла необходима комплексная внепечная обработка сталей, включающая проведение необходимых технологических операций в УДМ и последующую отливку слитков и непрерывнолитых заготовок в вакууме с интенсификацией процесса дегазации струи и инокулировани-ем.
Достоинства этой технологии заключаются в том, что она позволяет в одном процессе соединить преимущества кислой стали, так как в ковше-вакууматоре может осуществляться контролируемое формирование оксидов благоприятной формы, и большие технологические возможности основной — за счёт проведения глубокой десульфурации обрабатываемого расплава. Ввод в струю инертного газа обеспечивает создание наилучших условий для эффективного удаления газов из жидкого металла при вакуумной разливке, а дополнительное распыление струи инокулирует расплав и оказывает целенаправленное воздействие на процесс кристаллизации слитков и непрерывнолитых заготовок.
Анализ литературных данных, проведённые практические и теоретические разработки, обусловили создание прогрессивной технологии получения крупных слитков и непрерывнолитых заготовок, открывающей широкие возможности на пути получения из них изделий с уникальными свойствами, существенно расширяющими возможность их эксплуатации в условиях низких температур и агрессивных сред.
Список литературы
- Скобло С. Я., Казачков Е. А. Слитки для крупных поковок. М.: Металлургия, 1973. — 247 с.
- Marburg Е. Journal of Metals. 1953, v. 5, № 2, p. 157−172.
- Вейник А.И. Теплообмен между слитком и изложницей. Металлургиздат, 1959.
- Скороходов Н.Е. Сталь, 1952, № 9, с. 824−828.5. Ефимов В. А. Разливка и кристаллизация стали. М.- Металлургия, 1976. -552 с.
- Жидкие металлы и сплавы и их затвердевание. М.- Металлургиздат, 1962. -434 с.
- Явойский В.И., Близнюков С. А., Вишкарёв А. Ф. и др. Включения и газы в сталях. М.: «Металлургия», 1973. 272с.
- Крок Р., Браунтман Д., Современные композиционные материалы. Пер. с англ. М.: «Мир», 1970. 3672 с.
- Чуйко Н.М., Перевязко А. Т., Даничек Р. Е. Внепечные способы улучшения качества стали. Киев, «Техшка», 1978. 128 с.
- Морозов А.Н., Стрекаловский М. М., Чернов Г. И. и др. Внепечное вакуумирование стали. М.: «Металлургия», 1975. — 278 с.
- Кнюппель Г. Раскисление и вакуумная обработка стали. М.: Металлургия, 1984.-295 с.
- Kinsman G. J. М., Hazeldean G.S. F., Davies M. W. // «J. Iron and Steel Inst.», 1969, v. 207, № 11, p. 1463—1478.
- Явойский В. И., Дорофеев Г. А., Повх И. JI. Теория продувки сталеплавильной ванны. М., «Металлургия», 1974. 495 с.
- Явойский В. Я., Свяжин JL Г., Вшикарев А. Ф. и др. — «Взаимодействие газов с металлами» (Труды III советско-японского симпозиума по физико- химическим основам металлургических процессов). М., «:Наука», 1973. С. 98— 106.
- Кинетика и термодинамика взаимодействия газов с жидкими металлами. (Труды конференции). М., «Наука», 1974.
- Явойский В. И., Свяжин А. Г., Вишкарев А. Ф // «Физико-химические исследования процессов производства стали». М., «Металлургия», 1973. (МИ-СиС. Сб. № 74), с. 21—23.
- U. Pehlke R., Elliott J.//"Trans. Metallurg. Soc. А1МЕ". 1963,.V. 227. № 4. P. 844—855.
- Зюбан H.A., Жульев С. И., Насибов А. Г. Изучение технологических возможностей снижения содержания водорода в стали 35ХНЗМФА, выплавленной в электродуговых печах.. // Материаловедение. 1998. № 10. С. 54−55.
- Новик JI.M. Внепечная вакуумная металлургия стали. М.: «Наука», 1986. — 192с.
- Самарин А .М. Вакуумная металлургия. М.: Металлургиздат, 1962, с. 267 289.
- FogartyJ.E. Trans. Vacuum Metallurgy Conf. New. York, 1964. Boston: Mass. amer. Vacuum Soc., 1965. P. 432−453.
- Венков С.Г. // Вопр. физики кипения.М.: Мир, 1964. с. 13−27, 80−98.
- ЧухловВ.И., Ойкс Г. Н., Аншелес И. И. и др. // Изв. вузов. Чер. металлургия. 1967. № 1, с. 41−45.
- Соколов Г. А. Внепечное рафинирование стали. М.: Металлургия 1977. 206 с.
- Чуйко Н. М., Перевязко А. Т., Иванов В. Г. и др. // «Бюл. ин-та «Черме-тинформация», 1972. № 8. С. 35—37.26. Материалы Всесоюзного совещания сталеплавильщиков. Ч. I. М., Металлургиздат, 1957. 776 с.
- Fukumoto М., Taniguchi К. // «J. Vac. Science a. Technology». 1970. V. 7. № 6. P. 158—161.
- Proc. Intern. Conf. on the Sci. a Techn. of Iron and Steel Tokyo, Japan, September, 7—11, 1970, Part. I. Tokyo, 1971.
- Proc. Fourth. Intern. Conf. on Vacuum Metallurgy, Tokyo, Japan June, 1973 (Iron and Steel Inst, of Japan), 1974. P. 100.
- Stol 1 Z. H. // «Blast Furn. and Steel Plant», 1958 V. 46. № 6. P. 595—605.
- Лебедев B.H., Коровина B.M., Варакин П. И. Крупные поковки для валов турбогенераторов. -М.: «Машиностроение», 1968. 120 с.
- Поляков А.Ю., Самарин A.M., Сюй Цзен-цзи. //Изв. АН СССР. ОТН. Металлургия и топливо. 1961. № 1. С. 3−9.
- Sawamura Н., Matoba S. // Stud. Metallurgy, Sendai. 1969. P. 44−52.
- Chedaille J., Sivet M.L. de Saint-Martin. Buseppe pour e Coulle vide de L! Acier. // Revue de Metallurgie. 1963. V. 60. № 7−8.
- Аншелес И.И. Теоретические основы и технология внепечного вакуумирования жидкой стали. Дисс. докт. техн. наук. Москва, 1969. — 375 с.
- Кройцер Г. В. Вакуумная обработка жидкой стали. // Чёрные металлы. 1972. № 15.С. 9−18.
- Hobson C.D. // J. Iron and Steel Inst. 1966. Vol. 73.
- Фаткуллин O.X., Ойкс Г. Н., Аншелес И. И. Кинетика дегазации жидкой стали в вакууме. // Труды МИСиС, Металлургиздат, 1966. Т. 11. С. 51−60.
- Zors Т. И. Jernkontorets Annoler. 1960. Bd. 144. № 10. S. 717−771, 771−793.
- Казаков А.А., Ильяшенко Б. Ф. // Изв. АН ССР. Металлы. 1971. № 5. С. 1012.
- Чуйко Н.М., Перевязко А. Т., Рутковский Б. Б. и др. Дегазация жидкой стали при вакуумировании в ковше при переливе и при продувке металла инертными газами под вакуумом. // Газы в литом металле. М.: Наука, 1964. С. 28−35.
- Берве И., Гравенхорст Ж. Изменение содержания кислорода и азота при разливке стали на воздухе, в защитной атмосфере и в вакууме. // Черные металлы. 1962. № 5. С. 35−44.
- Соколов Г. А., Захарович В. Ф. Оценка участия струи в процессе дегазации жидкой стали. // Изв. вуз. Черная металлургия. 1968. № I, С. 39−42.
- Зюбан Н. А., Кряковский Ю. В. Моделирование зависимости содержания азота в крупных слитках от технологических параметров разливки. // Совершенствование металлургической технологии в машиностроении: Волгоград, 1990.-С. 87−88.
- Зюбан Н.А. Особенности струйного вакуумирования стали и проблемы дегазации при отливке крупных слитков. // Изв. вуз. Чёрная металлургия. 2003. № 5. С. 32−35.
- Калинников Е.С., Забалуев И. П. К вопросу о содержании водорода в легированной электростали. // Изв. вуз. Чёрная металлургия. 1961. № 2. С. 45−50.
- Hunter С J. Blast Furnace and Steel Plant, 1965, v. 53, № 8. p. 699.
- Taylor K.C. Vacuum Degassing. Today and Tomorrow. // Jron and Steel Engineer. 1963. Vol. 40. № 5. P. 111−116.
- Vacuum Deoxidation of Steel A Growing Practice. // Jndustrial Heating. 1965. V. 32. № 7. P. 1285−1286, 1300.
- Hornak J.N. Vacuum Degassing Why and How? // Jron and Steel Engineer. T 1965. V. 42. № 6. P. 73−80.
- Затуловский С.С. Суспензионная разливка. Киев.: «Наукова думка», 1981. — 260 с.
- Затуловский С.С., Ефимов В. А. Некоторые вопросы теории и технологии суспензионного литья // Суспензионное литьё. Сб. науч. тр. ИПЛ. Киев.: Издательство ИПЛ, 1977. С. 3−29.
- Гаврилин И.В. Регулирование процесса образования центров кристаллизации в отливках на основе анализа структуры и свойств металлических расплавов. Автореф. дис.. д-ра техн. наук. JL: ЛИИ, 1978. — 35 с.
- Turnbull D. Phase Changes. Solid State Physics, 1956, 3, p. 225 — 306.
- Флеминге M.C. Процессы затвердевания. M.: Мир, 1977. — 424 с.
- Turnbull D., Fischer J.C. Rate of nucleation in condensed systems. J. Chem. Phys., 1949, № 17, p. 71−73.
- Баландин Г. Ф. Основы теории формирования отливок. М.: Машиностроение, 1979.-335 с.
- Вайнгард У. Введение в физику кристаллизации металлов. — М.: Мир, 1967.- 160 с.
- Чижиков А.И. // Изв. вуз. Чёрная металлургия. 1970. № 6. С. 48−53.
- Гаврилин И.В., Ершов Г. С. Изменение первичной кристаллической структуры литой стали при суспензионном модифицировании. //Сб. Суспензионное литьё. АН УССР. ИПЛ. Киев. 1977. С. 84−89.
- Старосельский М.А., Чуднер Р. В., Гаврилин И. В. Исследование железных порошков и их влияния на содержание неметаллических включений в металле при суспензионной разливке // Сб. Суспензионное литьё. АН УССР. ИПЛ. Киев. 1977. С. 40−49.
- Жульев С.И., Зюбан Н. А. Производство и проблемы качества кузнечного слитка. Волгоград, ВолгГТУ, РПК «Политехник», 2003. 168 с.
- Сиденко В.М., Грушко И. М. Основы научных исследований. Харьков, «Ви-ща школа», 1977. 200 с. .
- Джонсон Н., Лион Ф.Статистика и планирование эксперимента в технике и науке. М.: «Мир», 1980. 513 с.
- Watanabe S. Trans. Japan Inst, of Metals, 1971, v. 12, № 1, p. 57−68.
- Колосов M. И., Строганов, Смирнов Ю. Д., Охримович .Б. П. Качество слитка спокойной стали. М.: Металлургия, 1973. — 408 с.
- Штейнберг С. С. Слиток стали. Свердловск: УралОГИЗ, 1933. — 56 с.
- Колпишон Э. Ю., Новицкий В. К., Соболев В. В., Соболев Ю. В. Изготовление 200-т кузнечного слитка роторной стали. // Оптимизация металлургических процессов. М.: Металлургия, 1972. С. 50−52.
- Жульев С.И. Оптимизация процессов производства кузнечных слитков для поковок ответственного назначения с использованием САПр технологий. Докторская диссертация. — Донецк. — 1991. — 365с.
- Ефимычев Ю.И., Михайлов С. К., Святкин Б. К. и др. Регрессионный анализкачества сталей и сплавов. — М.- Металлургия, 1976. 224с.
- Жульев С.И., Зюбан Н. А. Влияние параметров изготовления крупных кузнечных слитков на формирование оптимальной структуры осевой зоны. // Металлург. 2001. № 12. С. 38−39.
- Бакуменко В.Я., Новицкий В. К., Амельянчик А. В. др. Исследование процесса затвердевания кузнечных слитков. // Проблемы стального слитка. Труды 6 конференции по слитку. М.: «Металлургия», 1976. С. 74 75.
- Маслов A.M. Некоторые направления улучшения свойств крупного стального слитка. // Проблемы стального слитка: Сб. науч. тр. III конф. по слитку. -М.: Металлургия, 1969. С. 245 248.
- Пименов Г. А., Мишулин А. А., Лебедев В. Н. и др. Кузнечный слиток. Авт. свидетельство СССР № 668 753.
- Макаров И.И. Расчёт температурных полей при затвердевании стального слитка с учётом перераспределения примесей // В кн. НИИНФормтяжмаш, 1975, 15−75−2, с. 20−25.
- Амельянчик А.В., Макаров И. И., Широлапова Т. Б., Прохорова Е. А. Расчётна ЭВМ температурных полей при затвердевании стального слитка в изложнице. ИФЖ, 1974, т. 26, № 4, с. 705−713.
- Макаров И.И. Исследование влияния параметров прибыли на кинетику затвердевания стали и формирование усадочных дефектов в крупных слитках. -Дисс. канд. техн. наук. М.-: 1976. — 158 с.
- Зюбан Н. А., Лебедев В. Н., Жульев С. И., Булгаков Г. В. Кузнечный слиток с измененной геометрией донной части. // Сб. науч. тр. «Разливка стали в изложницы и качество слитков». М.: «Металлургия», 1984. — С. 16−19.
- Бакакин А.В., Гальперин Г. С., Подгорчук Ю. Г. и др. Математическая модель течения металла в канале сталеразливочного устройства с учётом газовой кавитации. Сообщ. 1 //Изв. Вузов. Чёрная металлургия. 1980. № 7. С. 36−39.
- Филиппов С.И. Теория процессов обезуглероживания стали. М.: Металлургиздат, 1956. — 166 с.
- Schenk Н., Steinmetz Е., Chand-Hee Rhee. Die Beeinflussing der gleichgewichte zwichen Kohlenstoff und Sauerstoff im flussigen Eisen durch Nickel, Chrom und Silizium. // Archiv fur Eisenhuttenwessen, 1968. Bd 39. № 11. S. 803−809.
- Казаков А.А. Кислород в жидкой стали. М.: Металлургия, 1972. — 199 с. ^ 88. Sawamura Hiroshi, Matoba Sachio. Recommended Equilibrium Values for the
- Reactions: О + CO = C02, С + C02 = 2CO and С + О = CO. Studies in Metallurgy, Sendei, 1969. P. 44−52.
- Hilty D.C., Crafts W. Solubility Oxygen in Liquid Jron Containing Silicon and Manganese. // Transactions AJME. 1950. V. 188. P.425−436.
- Яковлев Ю.Н. Гидродинамические процессы в струе при разливке стали. // Проблемы стального слитка: Сб. науч.тр.У конф. по слитку. — М.: Металлургия, 1974. С.154−159.
- Ершов Г. С., Черняков Г. А. Строение и свойства жидких и твёрдых металлов. М.: Металлургия, 1978. — 248 с.
- Левин В.Г. Физико-химическая гидродинамика. М.: Физматгиз, 1959. — 699 с.
- Левин Е.С., Курочкин К. Т., Умрихин П. В. // Экспериментальная техника и методы высокотемпературных измерений. М.: Наука, 1966. С. 104−113.
- Морозов А.Н. Водород и азот в стали. М.: Металлургия, 1968. 281 с.
- Филиппов С.И., КрашенинниковМ.Г., ИоффеИ.И. // Изв. вуз. Чёрная металлургия. 1963. № 1.С. 8−16.96. Френкель И. Я. Собрание избранных трудов, т.2. М.: Машиностроение, 1959.- 460 с.
- Сиов Б.Н. Истечение жидкости через насадки с противодавлением. — М.: Машиностроение, 1968. 140 с.
- Яковлев Ю.Н., Потебня В. Н., Щастный П. М., Харченко С. В., Сидоренко О. А. Сталеразливочные стаканы для разливки стали сверху. // Труды 6 конференции по слитку. М.: Металлургия, 1976. С. 219−221.
- Рабинович Б.В. Введение в литейную гидродинамику. Свойства расплавов. Особенности течения. Литниковые системы. — М.: Машиностроение, 1966. — 423с.
- Исаев С.И., Кожинов И. А., Кофаров В. И. и др. Теория тепломассообмена. -М.: Высшая школа, 1979. — 495 с.
- Гречко А.В., Нестеренко Р. Д., Кудинов Ю. А. Практика физического моделирования на металлургическом заводе. М.: Металлургия, 1976. — 224 с.
- Самсонов Г. В., Борисова А. Л., Жидкова Т. Г. Физико-химические свойства окислов. М.: Металлургия, 1978. — 471с.
- Смирнов Н.И., Полюта С. Е. Истечение пузырьков воздуха в окружающую среду.//ЖПХ. 1949. т. 22. № 11. С. 1208−1210.
- Стяжин В.Н., Зюбан Н. А. Компьютерная модель дегазатора.// Сборник трудов XVII Международной научной конференции «Математические методы в технике и технологиях». Том 9. Кострома, 2004. С. 67−68.
- Coupette W. Die Vakuumbehandlung des flussigen Stahles. Wiesbaden, 1967. 169 S.109. Новик Ф. С., Арсов Я. Б. Оптимизация процесса в технологии металлов методами планирования экспериментов. -М.: София.: Техника, 1980. 304 с.
- Зюбан Н.А., Жульев С. И., Титов К. Е. Огнеупорный разливочный стакан для отливки слитков и непрерывнолитых заготовок в вакууме. Патент РФ на полезную модель № 46 694 // Опубл. Б.И. № 21, 2005.
- Перник А.Д. Проблемы кавитации. 2-е изд., перераб. и доп. — JL: Судостроение, 1966. — 439 с.
- Абрамович Г. Н. Прикладная газовая динамика. —3-е изд. перераб. и доп. -М.: Наука, 1969.-824 с. •
- Лойцянский Л.Г. Механика жидкости и газа. -5-е изд. перераб. и доп. -М.: Наука, 1978.-736 с.
- Таблицы физических величин. / Под ред. акад. Кикоина И. К. М.: Атом-издат, 1976.- 1006 с.
- Зюбан Н. А., Кряковский Ю. В., Лебедев В. Н. и др. Интенсификация струйного вакуумирования стали при отливке крупных слитков. //Физико- химические основы вакуумных процессов в черной металлургии. М.: Издательство «Наука», 1984. — С. 154−158.
- Зюбан Н.А. Повышение эффективности дегазации металла крупных слитков при их отливке с применением вакуума. // Металлург. 2002. № 5. С. 43−44.
- Зюбан Н.А., Жульев С. И. Пути повышения эффективности вакуумной обработки стали при отливке крупных слитков. // Электрометаллургия. 1999. № 2. С. 17−20.
- Нарита К. Кристаллическая структура неметаллических включений в стали. Пер. с япон. М.: Металлургия, 1969. — 191 с.
- Георгиев М.Н. Вязкость малоуглеродистых сталей. М.: Металлургия, 1973.-224 с.
- Шульте Ю.А., Волчок И. П., Пинчук Е. И. //Литейное производство. 1971. № 3. С. 29−31.
- Явойский В.И., Близнюков С. А., Вишкарёв А. Ф. и др. // Сталь. 1975. N° 1. С. 25−31.
- Крюссар Ш., Плато Ж., Тамхонкар Р. и др. Сравнение вязкого и усталостного разрушений // Атомный механизм разрушения. М.: Металлургиздат, 1963. С. 535−574.
- Passoja D.E., Hill D.C. // Metallurgical Transaction. 1974. V.5. № 8. P. 18 511 854.
- Иванов В.П., Мордухович A.M., Финель В. М. Степень опасности неметаллических включений в стали // Проблемы разрушения металлов. М.: МДНТП, 1975. С. 172−181.
- Жульев С.И., Зюбан Н. А. Устройство для отливки слитков в вакууме с инокуляторами (варианты). Патент РФ № 42 454// Опубл. Б.И. № 34, 2004.
- Зюбан Н.А., Жульев С. И. Особенности процесса формирования эндогенных инокуляторов в струе при отливке крупных слитков. // Металлург. 2000. № 10. С. 42−43.
- Грузин В.Г. Температурный режим литья.- М.: Металлургиздат, 1952. -351с.
- Хорунжий Ю.Г., Ефимов В. А., Легенчук В. И. и др. Температурный режим разливки в вакууме крупных кузнечных слитков // Проблемы стального слитка: Сб. науч. тр. IV конф. по слитку. М.: Металлургия, 1969. С. 157−160.
- Справочник по гидравлическим расчетам./ Под ред. П. Г. Киселева. М.: Энергия, 1972.-312 с.
- Зюбан Н.А., Жульев С. И., Федянов Е. А. // Изв. вузов. Чёрная металлургия. 2002. № 1. с. 14 18.
- Ключников А. Д., Иванцов Г. П. Теплопередача в огнетехнических установках. М.: Энергия, 1970. — 400с.
- Зюбан Н.А., Жульев С. И., Федянов Е. А. // Изв. вузов. Чёрная металлургия. 2004. № 7. С. 70−73.
- Зюбан Н.А., Жульев С. И. // Сталь. 2001. № 6. С. 57 60.
- Ефимов В.А., Легенчук В. И., Хорунжий Ю. Г. и др. Динамика плавления частицы металлической добавки в объёме расплава // Проблемы стального слитка: Сб. науч. тр. VII конф. по слитку. М.: Металлургия, 1978. С. 110−112.
- Жульев С.И., Зюбан Н. А. // Технология металлов. 2001. № 2. С. 18−21.
- Рыжиков А.А., Рощин В. И., Фокин В. И. и др. Совершенствование технологии стального литья. М.: «Машиностроение», 1977.-144с.
- Кириевский Б.А., Черкасский B.JI. // Литейное производство. 1978. № 9. С. 25−27.
- Молонов Г. Д., Сапелкин Н. Ф., Лепорский С. В. и др. Кинетика кристаллизации крупных листовых слитков, отлитых с применением металлического порошка // Проблемы стального слитка: Сб. науч. тр. VII конф. по слитку. М.: Металлургия, 1978. С.118−121.
- Сталь на рубеже столетий. Под ред. проф. Карабасова Ю. С. М.: «МИСиС», 2001.-664 с.
- Гуляев Б. Б. Затвердевание и неоднородность стали. М, Металлургиздат, 1950. 228 с.
- Материалы Всесоюзного совещания сталеплавильщиков. Ч. I. М., Металлургиздат, 1957. 776 с.
- Taylor К. С. 1957. 4th Nat. Sympos. Vacuum. Technol. Trans London-New-York — Paris — Los-Angeles, Pergamon Press, 1958. P. 157 — 159.
- Proceedings of the Elec. Furn. Conf. Pittsburg, AIME, 1965 V. 23. P. 325 -341.148. «Industrial Heating». 1965. V. 35. № 7. P. 1300−1302.
- Taylor К. C. «Iron and Steel Engr.», 1963. V. XL. № 5. P. 73 — 80.
- Hornak J. N. «Iron and Steel Engr». 1965. V. XLII. № 6. P. 73 — 80.151. «J. Metals», 1958. V. 10. № 7. P. 471-^75.
- Геллер В., Вебер Л., Хаттершмид П. и др. «Черные металлы», 1972. № 19. С. 17−24.
- Winkler О., Bakish R. // Vacuum Metallurgy. Amsterdam etc. Elsevier Publ., 1971.
- Херцберг Р.В. Деформация и механика разрушения конструкционных материалов. М.: «Металлургия», 1989. 576 с.
- Volmer М. Kinetik der Phasenbildung. Dresden Leipzig, 1939.
- Явойский В.И., Горохов JI.C., Выонг Минь Тыонг. «Сталь», 1970. № 3. С. 228−233.
- Явойский В. И., Горохов Л. С., Купцов Г. В. и др. — «Физико-химические исследования процессов производства стали», М.: «Металлургия», 1973 (МИСиС. Сб. № 24), С. 69—75.
- Явойский В.И., Близнюков С. А., Вишкарев А. Ф. и др. «Сталь», 1975. № 1. С. 25—31.
- Bergh S. «Jernkont. Ann.», 1962. № 9. V. 146. p. 748 — 762.
- Романенко Д.Г. Качество поковок из смешанной, кислой и основной стали. Дисс. канд. техн. наук: 05.16.02. -М.: МИСиС, 1974.
- Романенко Д.Г., Кряковский Ю. В., Явойский Ю. В. и др. // Изв. вузов. Чёрная металлургия. 1972. № 7. С. 34 — 39.
- Явойский В.И., Кряковский Ю. В., Чухлов В. И. // Изв. вузов. Чёрная металлургия. 1977. № 1. С. 38 -41.
- Крючков О.Б. Повышение однородности свойств деформированной стали для изделий ответственного назначения. Дисс. канд. техн. наук: 05.16.02. -М.: МИСиС, 1988. 220 с.
- Sims С.Е., Dahl F.B. Trans. Amer. Foundromens Assoc., 1938, V. 46, p. 65.
- Воробьёв Н.И., Н.И., Токовой O.K., Мокринский A. B и др. // Изв. вузов. Чёрная металлургия. 2003. № 2. С. 18−20.
- Воробьёв Н.И., Токовой O.K., Мокринский А. В. и др. // Изв. вузов. Чёрная металлургия. 2003. № 3. С. 17−19.
- Алтыкис А.В., Колосков М. М., Назарьян В. А. // Кузнечно-штамповочное производство.- 1973. № 8. С. 3−8.
- Веретенников Э.В. // Кузнечно-штамповочное производство, — 1979. № 8. С. 5−7.
- Тарновский И.Я., Трубин В. Н., Златкин М. Г. Свободная ковка на прессах. М.: Машиностроение, 1967. — 328 с.
- Тюрин В.А., Куликов В. А. // Кузнечно-штамповочное производство. — 1988. № 5. С. 2−3.
- Соколов JI.H., Пестов B.C., Ефимов В. Н., и др. // Кузнечно-штамповочное производство. 1985. № 2. С. 25−27.
- Унксов Е.П., Тихомиров Н. В. // Кузнечно-штамповочное производство. — 1970. № 4. С. 10−13.
- Охрименко Я.М., Недосекин Л. И., Файбисович Л. И., Троицкий В. П., Бир-ченко Е.П. // Кузнечно-штамповочное производство. 1965. № 12. С. 3 — 5.
- Гринюк А.И., Лебедев В. Н., Охрименко Я. М. // Кузнечно-штамповочное производство. 1968. № 7. С. 3 — 7.
- Тюрин В.А., Балуев С. А. // Кузнечно-штамповочное производство. 1979. № 8.С. 8−9.
- Михайленко Б.Е., Сорокин И. Т., Гребенюк Г. С., Королёв В. П. // Кузнечно-штамповочное производство.-. 1979. № 8. С. 10−12.
- Адно Ю. // Металлы Евразии. 2004. № 6. — С. 20−24
- Theol L.L. Steel Times International, May. 1995. — P. 39−42.
- Техническая Годовой экономический эффект, тыс. руб.
- Внедрена технология отливки крупных слитков с использованием направляющей трубы с графито-муллито-корундовой футеровкой. Устранение брака заготовок по внутреннему дефекту «светлая корочка» 1107,7
- Итого: Один миллион сто семь тысяч семьсот рублей
- Заведующий кафедрой литейного производства Волгоградского государственного технического университета, декан факультета ТКМ -Зюбан Н.А.
- Главный металлург ПО «Баррикады» Бузинов И.Г.