Совершенствование методов ремонта металлоконструкций резервуаров с коррозионными повреждениями
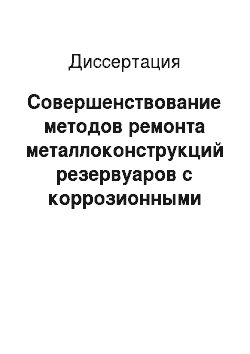
Как известно, образование подтоварной воды в резервуарах с сернистой нефтью приводит к появлению коррозии, носящей электрохимический характер. При этом необходимо отметить, что составные части нефти — парафины, углеводороды ароматические и непредельные — коррозионно не активны к металлам вообще и к железу в частности. Например, резервуары без внутренней антикоррозионной защиты, используемые для… Читать ещё >
Содержание
- ГЛАВА 1. СОСТОЯНИЕ ВОПРОСА. ПОСТАНОВКА ЗАДАЧИ ИССЛЕДОВАНИЯ
- 1. 1. Анализ конструкций резервуаров, эксплуатируемых на объектах трубопроводного транспорта Западно-Сибирского региона
- 1. 2. Методы защиты резервуаров от коррозии
- 1. 3. Анализ отечественной и зарубежной нормативной документации, регламентирующей параметры коррозионных повреждений металлоконструкций
- 1. 4. Анализ методов ремонта резервуаров на примере ОАО «Сибнефтепровод»
- 1. 5. Постановка задачи исследования
- ГЛАВА 2. НАПРЯЖЕННО-ДЕФОРМИРОВАННОЕ СОСТОЯНИЕ РЕЗЕРВУАРА ПРИ КОРРОЗИОННОМ ИЗНОСЕ
- 2. 1. Статистический анализ результатов технического диагностирования резервуаров
- 2. 2. Напряженно-деформированное состояние резервуара при коррозионном износе
- 2. 2. 1. Обзор работ, посвященных коррозионному износу
- 2. 2. 2. Определение напряжений при сплошной коррозии
- 2. 2. 3. Определение напряжений при язвенной коррозии
- 3. 1. Применение наплавки в промышленности
- 3. 2. Методика испытаний
- 3. 3. Результаты испытаний
- 3. 3. 1. Работа наплавленного металла на сжатых волокнах
- 3. 3. 2. Работа наплавленного металла на растянутых волокнах
- 4. 1. Промышленный эксперимент по ремонту стенки РВС-20 000 методом электродуговой наплавки металла
- 4. 2. Результаты металлографического исследования
- 4. 2. 1. Структура наплавленного металла
- 4. 2. 2. Структура слоя неполного расплавления
- 4. 2. 3. Структура слоя перегрева
- 4. 2. 4. Структура слоев нормализации и неполной перекристаллизации
- 4. 2. 5. Структура слоя рекристаллизации
- 4. 2. 6. Выводы по результатам микроструктурного анализа
- 4. 3. Исследование механических свойств металла в месте наплавки
- 4. 4. фрактографический анализ изломов образцов
- 4. 5. Электродные потенциалы в зоне наплавки
- 5. 1. Снижение допустимых уровней налива РВС в зависимости от глубины коррозионных повреждений
- 5. 2. Восстановление несущей способности усилением стенки резервуара бандажами
- 5. 3. Восстановление проектной толщины стенки резервуара электродуговой наплавкой
- 5. 4. Практическая реализация выполненных исследований
Совершенствование методов ремонта металлоконструкций резервуаров с коррозионными повреждениями (реферат, курсовая, диплом, контрольная)
Каждая шестая доменная печь работает на коррозию — таков итог пагубного действия коррозии, приводящей к разрушению конструкций, понижению качества продукции, а также к авариям и несчастным случаям на производстве /33/.
Коррозия — это процесс разрушения металлов вследствие химического, электрохимического или биохимического взаимодействия их с окружающей средой. Коррозия протекает самопроизвольно согласно законам кинетики возможных термодинамических реакций и приводит к понижению свободной энергии металла, в результате чего образуются более устойчивые в термодинамическом отношении соединения. Термин «коррозия» произошел от латинского слова «сошшо» — разъедание.
В России ежегодные прямые убытки от коррозии сопоставимы с вложениями в наиболее крупные отрасли народного хозяйства. Размеры косвенных убытков значительно выше. Принято считать /60/, что около 10% массы ежегодного производства черных металлов расходуется на возмещение потерь металлов от коррозии. Расходы, связанные с изготовлением конструкций, многократно превышают стоимость разрушенного металла. Ремонт сооружений, как правило, исключительно дорогостоящее мероприятие из-за больших затрат труда и применения дорогих дефицитных материалов. Наряду с прямыми и косвенными убытками практически всегда имеются не поддающиеся экономической оценке последствия коррозии: загрязнение окружающей среды (в результате утечки нефти и нефтепродуктов, газов, сточных вод и т. д.), аварийные ситуации в промышленности и на транспорте, обеднение природных ресурсов, понижение плодородия почв и др.
Исследованиям механизма коррозии металлов и вопросами защиты резервуаров и трубопроводов от коррозии посвящены труды отечественных 6 ученых Гутмана Э. М. /26, 27, 28/, Абдулина И. Г. /1/, Ажогина Ф. Ф. /2/, Боро-давкина П.П. /10/, Буренина В. А. /12, 13, 14/, Гоника A.A., Худякова М. А. /22/, Зиневича А. М. /33/, Тарасенко A.A. /86, 90, 92/, Яковлева А. И. /102/ и других, а также зарубежных исследователей Кариуса К. /108/, Эванса У. Р. /111, 112, 113/, Улига Х. Х /123/ и др.
По данным работы /11/, в системе трубопроводного транспорта нефти постоянно находится в ремонте около 20% всех резервуаров, а оставшийся резервуарный парк эксплуатируется с ограничением уровня заполнения в среднем на 15% с целью обеспечения гарантий безаварийной эксплуатации. Таким образом, по причине низкой надежности в системе трубопроводного транспорта нефти не используется около 30% емкостей резерву арного парка, что при недостаточной резервуарной обеспеченности /15, 17, 31, 87/ существенно снижает эффективность системы трубопроводного транспорта в целом.
Некоторыми авторами установлена тенденция увеличения числа внезапных отказов РВС, удорожание ремонтов и увеличение объема ремонтных работ. Исследования, проведенные в /89/, показывают, что основной причиной резкого снижения уровня эксплуатационной надежности и эффективности РВС является изношенность основных фондов. Например, в ОАО «Сиб-нефтепровод» свыше 20 лет, т. е. с превышением нормативного срока эксплуатации, функционируют 74 резервуара (49,7%) общей емкостью 1110 тыс. м (табл. В. 1, рис. В. 1).
Без сомнения существенную помощь в решении проблемы коррозии может оказать прогнозирование процесса развития коррозии металлов на длительные сроки (до 100 лет) на основе сравнительно кратковременных испытаний, а также использование справочных данных. Однако сложность и многообразие форм коррозионных процессов служат серьезным препятствием для научно обоснованного прогнозирования коррозии металлов. Справочные данные и методики, как правило, относятся к технически чистым металлам и стандартным сплавам в простых (чистых) коррозионных средах, а еле.
Рис.В.1. Распределение резервуарной емкости ОАО «Сибнефтепровод» по сроку эксплуатации. 8.
Коррозию относят к поверхностным явлениям и классифицируют по тем изменениям, которые происходят с поверхностью металла в результате протекания процесса коррозии.
При взаимодействии всей поверхности металла с окружающей средой наблюдается общая, или сплошная, коррозия, а при взаимодействии части поверхности — местная, или локальная.
Различают два вида общей коррозии — равномерную и неравномерную. При общей неравномерной коррозии вся поверхность металла покрыта продуктами коррозии, под которыми имеются более глубокие поражения— каверны. К этому же виду, коррозии относится и структурно-избирательная коррозия, когда один из компонентов сплава растворяется с большей скоростью, чем другой.
Местная (локальная) коррозия характеризуется разрушением отдельных участков поверхности металла, причем она бывает нескольких видов /38/:
— коррозия пятнами, когда диаметр пятна значительно превышает глубину проникновения коррозии;
— язвенная коррозия, при которой диаметр пораженного участка соизмерим с глубиной проникновения;
— точечная (питтинговая) коррозия, когда диаметр пораженного участка значительно меньше глубины проникновения;
— межкристаллитная коррозия, когда разрушение сосредоточено по границам зерен.
Местная коррозия более опасна, чем общая, так как при сравнительно небольших потерях металла полностью выходят из строя дорогостоящие конструкции.
Механические воздействия на металл (внешние воздействия, внутренние напряжения, вибрация) ускоряют коррозионный процессв таких случаях наблюдаемое разрушение конструкций называют коррозией под напряжени9 ем (коррозионное растрескивание) и коррозионной усталостью. Разрушение металлов может протекать по границам кристаллитов или в их толще. В последнем случае коррозия называется транскристаллитной.
В зависимости от условий контактирования металла с коррозионно-активными растворами различают коррозию.
— при полном погружении;
— при неполном погружении;
— при периодическом погружении;
— струйную.
С ростом добычи нефти значительно увеличился объем строительства стальных наземных емкостей для хранения нефти и нефтепродуктов. Добыча нефти увеличивалась главным образом за счет крупных нефтяных месторождений восточных районов страны. Отличительной чертой нефтей этих районов является большое содержание в них сернистых соединений, хлоридов, карбонатов, механических примесей и воды.
В настоящее время основной объем нефти добывается методом поддержания пластового давления (ППД) с применением заводнения нефтяных пластов различными поверхностными водами. Повышение нефтеотдачи путем заводнения пластов без стерилизации закачиваемых вод приводит к весьма опасной ситуации — заражению пластов и нефтяных скважин корро-зионно-опасными микроорганизмам, такими как сульфатовосстанавливаю-щие бактерии, тионовые бактерии, углеводородоокисляющие бактерии и другие. При заводнении, попадая через системы ППД в нефтяные пласты, бактерии формируют свой биоценоз, который со временем в значительных количествах продуцирует биогенный сероводород, вызывающий коррозию всего нефтепромыслового оборудования.
Особую тревогу вызывают коррозионные разрушения нижних поясов у резервуаров для хранения нефтепродуктов. Положение осложняется еще и тем, что на нефтяных месторождениях Урала, Поволжья и Западной Сибири.
10 большинство РВС изготовлено из стали 09Г2С, которая характеризуется низкой коррозионной стойкостью.
Результаты бактериологического анализа, выполненного в резервуар-ных парках Нижневартовского УМН показали, что в 1996 г. многие резервуары были заражены микрофлорой: Самотлорский парк — на 92%, Урьев-ский — на 96%, Нижневартовский — на 76%.
Нефти, содержащие большое количество серы (сернистые и высокосернистые нефти), являются весьма агрессивными средами, вызывающими коррозионные разрушения резервуаров изнутри.
Первой подготовкой нефтей к переработке является так называемый холодный отстой в резервуарах, расположенных на промыслах. Это позволяет значительно снизить содержание воды и соли.
При хранении нефти в стальных резервуарах происходит отстой. Вода, содержащаяся в нефти, собирается в нижней части резервуара, образуя так называемый слой подтоварной воды, содержащей соли и сернистые соединения.
Верхние пояса и кровля стальных резервуаров подвергаются коррозии паровоздушной среды. Вопросы коррозии и защиты верхних поясов и кровли стальных резервуаров подробно освещены в литературе и в данной работе не рассматриваются.
Как известно, образование подтоварной воды в резервуарах с сернистой нефтью приводит к появлению коррозии, носящей электрохимический характер. При этом необходимо отметить, что составные части нефти — парафины, углеводороды ароматические и непредельные — коррозионно не активны к металлам вообще и к железу в частности. Например, резервуары без внутренней антикоррозионной защиты, используемые для хранения только малосернистой нефти Шаимского месторождения и эксплуатируемые на НПС «Тюмень-Ш» уже более 30 лет на нефтепроводе Шаим-Тюмень, совер
11 шенно не имеют признаков действия какой-либо коррозии на внутренней поверхности стенки и днища.
Актуальность работы. Опыт эксплуатации резервуаров предприятий трубопроводного транспорта Западной Сибири показал, что коррозионные повреждения нижних поясов и днищ резервуаров наблюдаются весьма часто и уже через 8−10 лет могут привести к сквозным дефектам, при благоприятных для развития коррозии условиях (агрессивные примеси в нефти, повышенное содержание воды и т. п.).
Сквозные дефекты днищ и стенок резервуаров, образовавшиеся в результате коррозии металлоконструкции, могут привести к потере нефти и нефтепродуктов, при этом нарушается нормальная работа резервуаров и создаются условия возникновения пожаров.
Один из способов борьбы с коррозией — это применение антикоррозионной защиты. До недавнего времени в качестве защитного покрытия внутренней поверхности стенки и днища РВС широко использовался материал «Спрут», который на практике оказался низкоэффективным.
В настоящее время большое внимание уделяется антикоррозионной защите резервуаров, но как показывает опыт эксплуатации, возрастает доля ремонтов, связанных с устранением коррозионных повреждений. Это связано с тем, что при сооружении резервуаров антикоррозионной защиты внутренней поверхности стенки и днища не было, либо в ее в качестве использовался материал «Спрут», нанесение которого предполагало высокое качество подготовки поверхности. Однако эти требования зачастую не выполнялись, что сводило практически к нулю эффективность покрытия, а в некоторых случаях, даже усиливало скорость коррозии, вследствие щелевого эффекта.
Ремонт коррозионных повреждений, как правило, выполняется заменой металлоконструкций РВС, что требует значительных материальных и трудовых вложений. Например, за 1998 год был выполнен ремонт 11 резервуаров с заменой части первого пояса стенки, при этом затраты только на металло.
12 прокат в среднем составили свыше 1,5 млн руб. на 1 РВС. Поэтому совершенствование методов ремонта резервуаров с коррозионными повреждениями является актуальной задачей.
Научная новизна работы заключается в результатах выполненных промышленных и лабораторных экспериментов, впервые полученных автором. Основными из них являются:
1. Выполнен статистический анализ результатов измерения коррозионных повреждений резервуаров системы трубопроводного транспорта Западной Сибири, установлены зависимости геометрических размеров и месторасположения коррозионных язв от глубины поражения;
2. Установлено и изучено влияние глубины наплавки на изменение величины ударной вязкости отремонтированного участка и на работу распространения трещины;
3. Установлены зависимости свойств наплавленного металла от условий и температуры эксплуатации;
4. Исследовано влияние наплавки на изменение механических свойств металла;
5. Обоснована возможность применения наплавки для ремонта коррозионных повреждений резервуаров.
Практическая ценность. Научно обосновано применение электродуговой наплавки — как метода ремонта коррозионных повреждений металлоконструкций резервуаров, позволяющего значительно снизить трудоемкость и стоимость работ.
По результатам исследований разработан проект руководящего документа, регламентирующего применение наплавки при ремонте коррозионных повреждений металлоконструкций резервуаров.
Апробация работы. Основные положения и результаты диссертационной работы были доложены на международной научно-технической конференции «Нефть и газ Западной Сибири» в г. Тюмени, 1996 г.- региональ.
13 ной научно-технической конференции «Новые материалы и технологии в машиностроении» в г. Тюмени, 1997 г.- XIV Уральской школе металловедов-термистов «Фундаментальные проблемы физического металловедения перспективных материалов» в г. Ижевске, 1998 г.- 1-ой международной научно-практической конференции «Безопасность транспортных систем» в г. Самаре, 1998 г. Основное содержание работы опубликовано в 10 печатных работах.
Структура и объем работы. Диссертация состоит из введения, пяти глав, основных выводов, списка литературы и приложений. Общий объем работы составляет 198 страниц, в том числе 73 рисунка, 24 таблицы, список литературы содержит 124 наименований, в том числе 22 — на иностранных языках.
ОСНОВНЫЕ ВЫВОДЫ.
1. В результате статистической обработки результатов экспериментальных исследований получены зависимости условного диаметра и высотного расположения коррозионных повреждений стенки от их глубины.
2. Предложена методика прогнозирования развития сплошной коррозии и степени концентрации напряжений в зоне коррозионной язвы металлоконструкций резервуара.
3. В результате исследования механических свойств основного и наплавленного металла установлено, что при электродуговой наплавке происходит увеличение предела текучести на 17−19%, предела прочности на 4−6% и ударной вязкости на 13%. При этом все значения механических характеристик металла, наплавленного на форсированных режимах и при отсутствии теплоизоляции, выше нормируемых значений для основного металла.
4. Экспериментально доказано, что наплавка глубиной до 3 мм повышает ударную вязкость образца в целом. Дальнейшее увеличение глубины наплавки несколько понижает значения ударной вязкости, однако и в этом случае значения превышают требования ГОСТ 19 282–73. Экспериментальные исследования работы разрушения и распространения трещины в интервале температур минус 60 °C. + 20 °C показали, что при температуре минус 40 °C работа распространения трещины падает до нуля, как у основного, так и у наплавленного металла.
5. Выполнено опытно-промышленное внедрение технологии восстановления проектной толщины стенки резервуара электродуговой наплавкой на ЛПДС «Западный Сургут» при капитальном ремонте РВС-20 000 № 4 и получен подтвержденный экономический эффект в размере 233 252 рубля. По результатам исследований разработан проект руководящего документа, регламентирующий электродуговую наплавку в качестве метода ремонта металлоконструкций резервуаров, имеющих коррозионные повреждения.
СПИСОК ПРИНЯТЫХ СОКРАЩЕНИЙ.
РВС — резервуар вертикальный сварной.
НДС — напряженно-деформированное состояние.
НПС — нефтеперекачивающая станция.
ЛДПС — линейная производственно-диспетчерская станция.
УМН — управление магистральных нефтепроводов.
ОАО — открытое акционерное общество.
ОАО «СНП» — ОАО «Сибнефтепровод».
МН — магистральный нефтепровод.
АК — акционерная компания.
ЛКМ — лакокрасочные материалы.
РК — радиографический контроль.
НТД — нормативно-техническая документация.
СВБ — сульфатовосстанавливающие бактерии.
ППД — поддержание пластового давления.
ИФС — изолирующие фланцевые соединения.
Список литературы
- Абдуллин КГ. Коррозионно-механическая прочность нефтегазовых трубопроводных систем. Дисс. докт. техн. наук. -Уфа, 1987.-437 с.
- Ажогин Ф.Ф., Иванов С. С. Новые достижения в области теории и практики противокоррозионной защиты металлов. Сб. докл. семинара по коррозии. Звенигород, 1980. -М., 1981, с. 93.
- Аистов A.C., Фокин М. Ф. Расчет элементов магистральных нефтепроводов на малоцикловую долговечность // Транспорт и хранение нефти и нефтепродуктов. 1981, № 6. — С. 19−23.
- Антипъев В.Н., Стояков В. М., Чепурский В. Н., Ченцов А. Н. Методы определения остаточного ресурса нефтепроводов. -М.:Транспресс, 1995. -48 с.
- Арзунян A.C. Резервуары с безмоментной кровлей для хранения нефти и нефтепродуктов. -М.: ЦНИИТЭнефть, 1956. -С. 72
- Артамонов В.В., Асеев A.A. Повышение точности интегрирующих АЦП для тензорезисторных датчиков // Приборы и системы управления, -1985, № 9. -С.28.
- Беляев Б.И., Корниенко B.C. Причины аварий стальных конструкций и способы их устранения. -М.: Стройиздат, 1968. -205 с.
- Березин В.Л., Гумеров А. Г., Ращепкин К. Е., Ясин Э. М. Об эксплуатационной надежности нефтезаводских резервуаров // НТС труды НИ-ИТранспортнефть / Транспорт и хранение нефтепродуктов. -1985, вып.4. -С.204−207.
- Березин В.Л., Шутов В. Е. Прочность, устойчивость резервуаров и трубопроводов. -М.: Недра, 1973.-198 с.
- Бородавкин П.П., Садырин Ю. К. Ремонт металлических резервуаров // Научно-технический обзор ВНИИОЭНГ, 1967. -76 с.152
- Буренин В. А. Прогнозирование индивидуального остаточного ресурса стальных вертикальных резервуаров. Дисс. докт. техн. наук. -Уфа, 1994. -270 с.
- Буренин В.А., Исламгулова Г. Ф. О характере коррозии листов конструкции стального вертикального цилиндрического резервуара // Тез. докл. сб.: Актуальные проблемы нефти и газа. -Уфа, 1984.-е. 89.
- Буренин В.А., Исламгулова Г. Ф., Московская O.A. Определение минимально допустимой толщины поясов корпуса стальных вертикальных цилиндрических резервуаров // Тез. докл. сб.: Актуальные проблемы нефти и газа. -Уфа, 1984. с. 89.
- Буренин В.А., Московская O.A. Определение предельной толщины стенки резервуара // Тез. докл. сб.: Вузовская наука — научно-техническому прогрессу. -Уфа, 1986. с. 4.
- Веревкин Р.И., Ржавский Е. Л. Повышение надежности резервуаров, газгольдеров и их оборудования. М.: Недра, 1980. — 284 с.
- Вороненко Б.И. Коррозионное растрескивание под напряжением низколегированных сталей (обзор) II. Влияние легирующих элементов. Защита металлов, 1997, т. ЗЗ, № 5, с.472−488.
- Галеев В.Б. Эксплуатация стальных вертикальных резервуаров в сложных условиях. -М.: «Недра», 1981. -149 с.
- Галеев В.Б., Сощенко Е. М., Черняев Д. А. Ремонт магистральных трубопроводов и оборудования перекачивающих станций. -М.: Недра, 1965, -208 с.
- Галеев В.Б., Сощенко Е. М., Черняев Д. А. Ремонт магистральных трубопроводов и оборудования перекачивающих станций // 2 издание. -М.: Недра, 1968, -292 с.
- Гоник A.A., Худяков М. А. Хрупкое разрушение нижних листов корпусов резервуаров в результате макрогальванической коррозии // Защита от коррозии и охрана окружающей среды. -1995, № 10.95. -С. 2−5.
- ГОСТ Р 51 164−98. Трубопроводы стальные магистральные. Общие требования к защите от коррозии.
- Гумеров А.Г. Исследование напряженно-деформированного состояния нефтезаводских резервуаров при их эксплуатации. Дисс. канд. техн. наук. -М., 1968. -123 с.
- Гумеров А.Г., Зайнуллин P.C., Ямалеев K.M., Росляков A.B. Старение труб нефтепроводов. -М.: Недра, 1995. 218 с.
- Гутман Э.М. Механохимия металлов и защита от коррозии. -М.: Металлургия, 1981. 270 с.
- Гутман Э.М., Амосов Б. В., Худяков М. А. Влияние коррозионной усталости материала нефтепроводов на надежность // Нефтяное хозяйство. -1977. с. 59−61.
- Гутман Э.М., Зайнуллин P.C., Шаталов А. Т. и др. Прочность газопромысловых труб в условиях коррозионного износа. М.: Недра, 1984. — 76 с.
- Дайчик М.Л., Григоровский H.H., Хуршудов Г.Х Методы и средства натурной тензометрии. -М.: Машиностроение, 1989. -234 с.
- Должанский П.Р. Контроль надежности металла объектов котлонадзора: Справочное пособие. -М.: Недра, 1985. 263 с.
- Ентус Н.Р. Техническое обслуживание и ремонт резервуаров. -М.: Химия, 1982.-238 с.
- Закс Jlomap. Статистическое оценивание. -М., Статистика, 1976.154
- Зиневич A.M., Глазков В. И., Котик ВТ. Защита трубопроводов и резервуаров от коррозии. М.: Недра, 1975. — 288 с.
- ЪА. Корниенко B.C., Поповский Б. В. Сооружение резервуаров. -М.: Стройиздат, 1971. -224 с.
- Крамер Г. Математические методы статистики. -М.: Статистика, 1976.
- Куров О.В., Василенко И. И. Защита металлов. 1981, т.17, № 3, с. 266.
- Кушнаренко В.М., Масюто О. М. О механизме серводородного растрескивания сталей //Металловедение и термическая обработка металлов. -1993.-№ 2, с.5−8.
- Кушнир В.Н., Попов Г. И., Неволин В. Г. Коррозия и защита оборудования систем подготовки нефти и сточных вод // Обзорная информация ВНИИОЭНГ / Коррозия и защита в нефтегазовой промышленности. М.: ВНИИОЭНГ, 1978.-72 с.
- Лизин Т., Пяткин В. А. Проектирование тонкостенных конструкций. -М.: Машиностроение, 1985, -202 с.
- Московская O.A. Разработка методов оптимизации сроков технического обслуживания и ремонта стальных вертикальных резервуаров. Дисс. канд. техн. наук. -Уфа, 1984.
- Никишин A.B., Кораблев В. А., Овчар З. Н. Изменение свойств сталей объектов транспорта нефти после длительной эксплуатации. Тез. докл. I ме155жду народной научно-практической конференции «Безопасность транспортных систем». Самара, 1998.
- Никишин A.B., Овчар З. Н., Саяпин М. В. Исследование возможности применения сварки для ремонта резервуаров, пораженных коррозией. Тез. докл. региональной научно-технической конференции «Новые материалы и технологии в машиностроении». Тюмень, 1997.
- Никишин A.B., Овчар З. Н., Саяпин М. В. Ошибки монтажа, приводящие к снижению эксплуатационной надежности резервуаров. Тез. докл. I международной научно-практической конференции «Безопасность транспортных систем». Самара, 1998.
- Никишин A.B., Тарасенко A.A., Макаров А. И. и др. Методы ремонта элементов конструкций стальных вертикальных цилиндрических резервуаров после длительной эксплуатации / Инструкция АООТ «Сибнефтепровод». -Тюмень, 1997.-264 с.
- Никишин A.B., Тарасенко A.A., Прокофьев В. В., Николаев Н. В. и др. Ремонт РВС / Электронный учебник на CD-диске. Тюмень, 1997.156
- Никишин A.B., Хоперский Г. Г., Саяпин M.B. Исследование возможности применения сварки для ремонта коррозионных повреждений металлоконструкций резервуаров // Известия вузов / Нефть и газ. 1997, № 6.
- Отчет по хозяйственному договору № 36/97. Измерение наведенного потенциала в резерву арном парке Нижневартовского УМН ОАО «Сиб-нефтепровод». -Екатеринбург, 1997.
- Попов A.A. Коррозионностойкие стали для морских условий. Защита от коррозии и охрана окружающей среды, 1997, № 4−5, с.46−47.
- Правша и инструкции по технической эксплуатации металлических резервуаров и очистных сооружений. -М.: Недра, 1977. -464 с.
- Правила речного регистра РСФСР, т. 3. М.: Транспорт, 1989.
- Правша технической эксплуатации резервуаров и инструкции по их ремонту. -М: Недра, 1988, -269 с.
- Рассошинский A.A. Металлография сварных швов. -М., «Машгиз», 1961,295 с.
- Рачев X., Стефанова С. Справочник по коррозии: Пер. с болг. / Перевод Нейковского С.И.- под ред. и с предисл. Н. И. Исаева. М.: Мир, 1982. — 520 с.
- РД 153−39−030−98. Методика ремонта дефектных участков магистральных нефтепроводов по результатам внутритрубной диагностики.157
- РД 34.10.130−96. Инструкция по визуальному и измерительному контролю. -М., 1996.
- РД 34.17.439−96. Методические указания по техническому диагностированию и продлению срока службы сосудов, работающих под давлением. -М., 1996.
- РД 39−147 103−360−89. Инструкция по безопасному ведению сварочных работ при ремонте нефте- и продуктопроводов под давлением. Уфа: ВНИИСПТнефть, 1989.
- РД 39−147 103−356−85. Инструкция по определению периодичности технического обслуживания, ремонта и норм отбраковки стальных вертикальных цилиндрических резервуаров. Уфа, 1986. 44 с.
- РД 39−147 103−385−87. Правила технической эксплуатации резервуаров магистральных нефтепроводов. Уфа: ВНИИСПТнефть, 1988. — 282 с.
- РД 39−110−91. Инструкция по ликвидации аварий и повреждений на магистральных нефтепроводах. Уфа: ИПТЭР, 1992.
- РД 39−30−1284−85. Руководство по обследованию и дефектоскопии вертикальных стальных резервуаров. -М.:1985.
- РД 51−108−86. Инструкция по технологии сварки и резке труб при производстве ремонтно-восстановительных работ на магистральных газопроводах. М.: ВНИИГАЗ, 1986.
- РД-08−95−95. Положение о системе технического диагностирования сварных вертикальных цилиндрических резервуаров для нефти и нефтепродуктов. -М.: 1995.
- Рекомендации по восстановлению несущей способности цилиндрических резервуаров способом усиления стенки стальными кольцевыми бандажами. -Астрахань, ЦНИИЛ, 1984.
- Рекомендации по эксплуатации резервуаров, усиленных методом постановки кольцевых бандажей. -Астрахань, ЦНИИЛ, 1984.158
- Розенштейн КМ. Аварии и надежность стальных резервуаров. -М.: «Недра», 1995. -253 с.
- Румшинский Л.З. Математическая обработка результатов эксперимента. -М.: «Наука», 1971. -192 с.
- Сафарян М.К. Металлические резервуары и газгольдеры. -М. Недра, 1987.-200 с.
- Сафарян М.К. Сооружение металлических резервуаров. -М.: Недра, 1988. -163 с.
- Сафарян М. К, Иванцов О. М. Проектирование и сооружение стальных резервуаров. -М., Гостоптехиздат, 1961, -328 с.
- Сварка в машиностроении: Справочник в 4-х т. / Редкол.: Г. А. Николаев (пред.) и др. М.: Машиностроение, 1979.
- СНиП2.05.06−85. Магистральные трубопроводы. -М., 1985.
- СНиП 3.03.01−87. Несущие и ограждающие конструкции // Госстрой СССР. -М., ЦИПТ Госстроя СССР, 1988. -192 с.
- СНиП 11−23−82. Стальные конструкции. // Госстрой СССР. -М., ЦИПТ Госстроя СССР, 1982.
- СНиП 2.01.07−85. Нагрузки и воздействия // Госстрой СССР. -М., ЦИПТ Госстроя СССР, 1985.
- Сотников С.Н., Мангушев Р. А. Проектирование и строительство резервуаров на слабых грунтах. М.: ВНИИОЭНГ, -51 с.
- Справочник по объектам котлонадзора. Под ред. И. А. Молчанова. -М: Энергия, 1974.
- Тарасенко А.А. Измерительный комплекс ИСД-ТТ. Информационный листок // Экспонат ВДНХ СССР / Павильон «Газовая промышленность» (серебряная медаль).-М., 1991, 4 с.
- Тарасенко А.А. Исследование свойств защитных покрытий для РВС, применяемых в ОАО «Сибнефтепровод» // Тез. докл. международного семи159нара-совещания «Новые технологии обслуживания и ремонта резервуаров». • М., АК «Транснефть», 1997.
- Тарасенко A.A. Напряженно-деформированное состояние вертикальных стальных резервуаров при ремонтных работах. -М. Недра, 1999. -286 с.
- Тарасенко A.A. Напряженно-деформированное состояние крупногабаритных резервуаров при ремонтных работах: Дисс. канд. техн. наук. -Тюмень, 1991,254 с.
- Тарасенко A.A. Разработка научных основ методов ремонта вертикальных стальных резервуаров: Дисс. докт. техн. наук. -Тюмень, 1999, 297 с.
- Тарасенко A.A., Зыкова В. К. Исследование коррозии металла резервуара для хранения нефтепродуктов // Тез. докл. региональной научно- технической конференции «Новые материалы и технологии в машиностроении», -Тюмень, ТюмГНГУ, 1997.
- Тарасенко A.A., Тнмербулатов Г. Н. Устройство для измерения деформаций растяжения и изгиба // Патент Российской федерации № 2 047 084.
- Тензорезисторы КФ4 и КФ5. Техническое описание и инструкция по наклейке. -Киев: ПО «Веда», 1988.
- Тесов H.H. Повышение надежности и долговечности устройств электрохимической защиты подземных трубопроводов от коррозии // Обзорная информация ВНИИОЭНГ / Коррозия и защита в нефтегазовой промышленности. М.: ВНИИОЭНГ, 1979. — 44 с.
- Халдеев Г. В., Сюр А.Н., Харламов Ю. А., Дорофеев А. Г. Оценка скорости коррозии металла по данным электрохимических измерений // Обзор160ная информация ВНИИОЭНГ / Коррозия и защита в нефтегазовой промышленности. М.: ВНИИОЭНГ, 1979. — 44 с.
- Хомикомб Р. Пластическая деформация металлов. -М., Изд-во Мир, 1972, 396 с.
- Черняев В. Д. Состояние и перспективы развития системы магистральных нефтепроводов России // Трубопроводный транспорт нефти. 1995, № 2. — С. 2−8.
- Черняев В.Д., Черняев КВ., Березин В. Л., Стеклов О. И., Васильев Г. Г. Системная надежность трубопроводного транспорта углеводородов. -М.: Недра, 1997.-517 с.
- Чикинева Т.Н. О показателях надежности стальных резервуаров для нефтепродуктов // Транспорт и хранение нефти и нефтепродуктов. 1982, вып. 11.-С. 16−18.
- Чикинева Т.Н. Оценка долговечности и безотказности стальных резервуаров для нефтепродуктов / Сер. Транспорт и хранение нефти и нефтепродуктов. М.: ВНИИОЭНГ, 1977. — 28 с.
- Шутов В.Е. Оптимизация резервуарных конструкций для хранения нефтепродуктов. Автореферат дисс. на соиск. уч. ст. докт. техн. наук. -М&bdquo- МИНХ и ГП, 1983, -37 с.
- Яковлев А.И. Коррозионное воздействие сероводорода на металлы. -М., ВНИИЭгазпром, 1972. -42 с.
- API specification for welded oil storage tanks. API Std. 12c, 13th ed" September 1955. -API. Dallas, 1955, 83 pp. 15 ill., Supplement, 6 pp.161
- API Standard 650. Welded Steel Tanks for Oil Storage. Ninth Edition, July 1993. Addendum 1, December 1994. Addendum 2, December 1995. Addendum 3, December 1996.
- API Standard 653. Tank Inspection, Repair, Alteration, and Reconstruction. Manufacturing, Distribution and Marketing Department. Second Edition, December 1995. Addendum 1, December 1996.
- Carius C. Ber. uber die Korrosiostagung. 1935 (VDI-Verlag), 5, 1936, s.61−72.
- CAN3-Z183-M86. Oil pipeline system.
- Denham J.B., Russel J., Wills C.M.R How to design a 600 000 lbs tank. -Hydracarbon Projess, 1968, V, vol.47, № 5.
- Evans U.R. An Introduction to Metallic Corrosion, Arnold, London, 1963.
- Evans U.R. Metallic Corrosion, Passivity and Protection, 2nd edn., Arnold, London, 1946.
- Evans U.R. The Corrosion and Oxidation of Metals, Edward Arnold, London, 1969.
- Gackenbach R. E. Materials Selection for Process Plants, Reinhold, New York, 1960.
- Hepner I.L. Materials of Construction for Chemical Plant. Leonard Hill, London, 1962.
- Noordhof G. S., reported by U. R. Evans. Proc. International Congress of Pure and Applied Chemistry, London, 5, 743, 1947.
- Polar I.P. A Guide to Corrosion Resistance, Climax Molybdenum Company, New York, 1961.
- RabaldE. Corrosion Guide, Eisevier Publishing Company, Amsterdam, 1968.
- Ritter P. Korrosionstabellen nichtmetallischer Werkstoffe SpringerVerlag, Wien, 1956.162
- Semikawo O.J. Iron and steel Inst. Jap. 1983, № 13, p.1357.
- Sverepa Cf. O. Werkst, u. Korrosion, 9, 533 (1958).
- Thompson A.W., Bernstein I.M. Advances in corrosion sienca and technology. Ed. Fontana M.G., Staehle R.W.N.Y.- Plenum Press, 1980.
- UhligH. H. Corrosion and Corrosion Control, Wiley, New York, 1963.
- Werner M. Werkst, u. Korrosion, 3, 347 (1952).166