Пароструйная технология с нисходящим потоком для производства порошков цинка, меди, сплава «медь-олово»
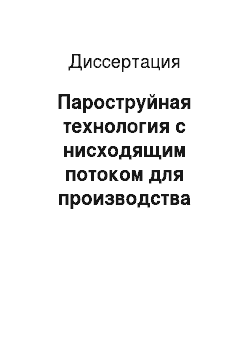
Моделирование широкого диапазона режимов работы испарителей для цинка и меди позволили получить качественные зависимости расхода гора и его основных параметров на выходе из испарителя от температуры испарителя и давления в камере конденсации. Показана возможность в сверхзвуковых режимах (за счет ускорения потока в сопле) достижения высоких пересыщений пара, еще до контакта пара с охлаждающим… Читать ещё >
Содержание
- ГЛАВА 1. Получение порошков методом испарения и конденсации
- 1. 1. Современные технологии получения порошков
- 1. 2. Конструкции испарительных устройств
- 1. 3. Выводы
- ГЛАВА 2. Теоретические основы пароструйной технологии
- 2. 1. Принципиальная схема разрабатываемого технологического процесса
- 2. 2. Закономерности основных стадий процесса получения порсшка
- 2. 3. Методика расчета параметров работы испарителя
- ГЛАВА 3. Моделирование режимов технологического процесса и поиск перспективных технологических решений
- 3. 1. Эксперименты на модельном веществе
- 3. 2. Математическое моделирование режимов работы испарителя
- 3. 3. Пути регулирования дисперсности порошка и оптимизация конструкции аппарата
- 3. 4. Тепловой расчет испарителя. Габариты и температура нагревателя
- 3. 5. Блок-схема зависимостей параметров технологического процесса
- ГЛАВА 4. Разработка технологии получения порошка цинка
- 4. 1. Описание опытной установки
- 4. 2. Разработка конструкции испарительного устройства и поисковые эксперименты
Пароструйная технология с нисходящим потоком для производства порошков цинка, меди, сплава «медь-олово» (реферат, курсовая, диплом, контрольная)
За последние 40 лет в развитых странах наблюдается постоянное увеличение объемов производства металлических порошков. Они находят приле-нение практически во всех ведущих областях промышленности — химии, ш-шиностроении, энергетике, металлургии, радиои электротехнике, медицине и т. п.
Огромный интерес, проявляемый к порошкам, обусловлен их уникальными свойствами в сравнении с массивными металлическими образцами. Прежде всего, это большая удельная поверхность дисперсных систем и связанные с ней высокая химическая активность, адсорбционная способность, пирофорность, бактерицидность и т. п.
В настоящее время все большее распространение получают высокои ультрадисперсные порошки цинка, меди и ее сплавов.
Основным потребителем порошка цинка является химическая промышленность. Он используется как эффективный катализатор химических реакций в органическом синтезе. Например, с его участием получают дионизи-дин-сырье для термостойких полимеров и красок. В триботехнике цинковый порошок включают в состав смазочных композиций для узлов трения, что дает увеличение ресурса работы нагруженных деталей в 1,5−2 раза. В электротехнической промышленности он служит присадкой при производстве скользящих контактов-щеток электродвигателей. Электроконтактные материалы с цинком обладают высокой электропроводностью, большим сопротивлением электроэрозии, износоустойчивостью.
В последние годы приобретает все большую актуальность проблема защиты металлов от коррозии. Связано это с увеличением количества промышленных технологий, использующих агрессивные среды, высокие температуры и давления. По оценкам специалистов разных стран, потери от коррозии составляют от 2 до 4% валового национального продукта. При этом потери металла, включая массу вышедших из строя металлических конструкций, изделий, оборудования, составляют от 10 до 20% годового производства стали.
Одним из наиболее эффективных способов защиты металла является создание антикоррозионных покрытий на основе цинкнаполненных красок, которые одновременно обладают свойствами как традиционных лакокрассн-ных покрытий (хорошая адгезия к стали, простота нанесения, возможность применения для крупногабаритных изделий, ремонтопригодность), так и свойствами цинковых металлических покрытий (высокая атмосферои водостойкость, электрохимические свойства — катодная защита). Цинковые горошки для приготовления грунтов и красок должны содержать частицы дисперсностью 1−10 мкм и не менее 95% металлического цинка.
Учитывая ежегодное увеличение спроса на цинкнаполненные составы, лакокрасочная отрасль промышленности становится крупнейшим потребителем порошка цинка.
Ультрадисперсные порошки меди высокой чистоты с частицами сферической формы представляют интерес для микроэлектроники при производстве печатных плат, для создания электропроводящих полимерных композиций с дисперсным металлическим наполнителем, для диффузионно-твердеющих припоев и некоторых других специальных областей техники.
Порошок сплава «медь-олово» с частицами сферической формы используется в триботехнике в качестве главного функционального компонента ре-металлизантов — препаратов, предназначенных для восстановления двигателей внутреннего сгорания непосредственно в процессе их эксплуатации.
Методы получения порошков металлов подразделяются на дисперсионные и конденсационные. Первые основаны на механическом дроблении ш-териалов, вторые на физико-химических методах формирования частиц в процессах синтеза на молекулярном уровне. Дисперсионные методы пригодны для производства крупных порошков и тонких, с размером частиц 5−10 мкм. Конденсационные наряду с ними позволяют получать ультрадисперсные материалы [1] и поэтому представляют наибольший интерес. В этом направлении известны обстоятельные работы школы профессора И.В. Фриш-берг.
Постоянно увеличивающийся спрос на порошки цинка, меди и ее сплавов стимулирует работы по совершенствованию технологий и изысканию новых возможностей для производства порошков с заданными свойствами.
При разработке новых технологий, основанных на методе испарения-конденсации следует учитывать различие физических свойств указанных выше металлов. Цинк относится к легколетучим металлам и благодаря его низкой температуре кипения (1180 К) процесс испарения возможно осуществлять при атмосферном давлении инертного газа, что значительно упрощает конструкцию аппарата для его производства. Медь относится к труднолетучим металлам (Ткип=2813 К), вследствие чего для достижения высоких скоростей испарения процесс испарения необходимо проводить при высоких разрежениях инертного газа, вплоть до вакуума.
Целью данной работы является разработка высокоэффективных технологий производства высокодисперсного порошка цинка и ультрадисперсных порошков меди и сплава «медь-олово».
На основе проведенных исследований разработана и внедрена на производстве ООО Hi II1 «Уралавтохим» промышленная технология получения ультрадисперсных порошков меди и бронзы, а также разработана технология получения высокодисперсного порошка цинка и выданы рекомендации для ее промышленного освоения.
Автор выражает благодарность научному руководителю профессору С. С. Набойченко, коллективу кафедры «Металлургия тяжелых цветных металлов» УГТУ-УПИ за внимание и помощь при обсуждении результатов исследований, зам. генерального директора Государственного научного центра РФ ОАО «Уральский институт металлов» Б. Н. Смирнову за участие в обсуждении результатов исследований, к.т.н. М. М. Цымбалисту за неоценимую помощь при выполнении теоретических исследований, коллективу ООО.
НПП «Урапавтохим» за помощь в организации и проведении экспериментов и промышленном освоении результатов работы.
ВЫВОДЫ.
1. Для промышленных технологий получения порошков методом испарения и конденсации, отличающихся, в первую очередь способом нагрева, наиболее предпочтительным является резистивный способ. Возможности ре-зистивного способа расширяются при использовании графита в качестве материала испарительных устройств, ввиду его высокой температурной стойкости и легкой обрабатываемости.
2. Наиболее эффективно для получения порошков методом испарения и конденсации использовать испаритель закрытого типа, нисходящий паровой поток и раздельное расположение камер испарения и конденсации.
3. Теоретический анализ закономерностей основных стадий технологического процесса получения порошка методом испарения и конденсации с привлечением принципов механики сплошных сред выявил доминирующую роль стадии истечения для получения требуемых параметров пара.
4. Для управления параметрами пара наиболее эффективно использовать конструкцию испарителя закрытого типа. Предложенная методика расчета параметров работы испарителя, реализованная в виде пакета программ для ЭВМ, позволяет связать управляющие параметры технологического процесса с параметрами пара на выходе из испарителя.
5. Моделирование широкого диапазона режимов работы испарителей для цинка и меди позволили получить качественные зависимости расхода гора и его основных параметров на выходе из испарителя от температуры испарителя и давления в камере конденсации. Показана возможность в сверхзвуковых режимах (за счет ускорения потока в сопле) достижения высоких пересыщений пара, еще до контакта пара с охлаждающим газом, что обеспечивает образование зародышей конденсированной фазы ргв-номерно по всему сечению струи и получение более однородного пореш-ка. При «дроблении» парового потока на несколько самостоятельных струй и «сжатии» парового потока удается изменять его параметры, а, следовательно, и существенно влиять на свойства получаемого порошка.
Предложена методика теплового расчета испарителя, реализованная в виде пакета программ для ЭВМ.
6. Предложенная модульная конструкция испарительного устройства с непосредственной передачей тепла расплаву для получения порошка цинка, отличается незначительной материалоемкостью, проста при изготовлении и монтаже, легко настраивается на заданную производительность.
7. Разработанные аппарат и пароструйная технология с нисходящим паровым потоком для получения высокодисперсного порошка цинка, по срж-нению с горизонтальной промышленной установкой, позволят увеличить производительность в 2,6 раза, снизить металлоемкость на 47% и уменьшить площадь занимаемую установкой на 55%.
8. Конструкция испарительного устройства для получения порошков меди и сплава «медь-олово» обеспечивает формирование нисходящего парового потока и возможность организации непрерывного режима работы. Автономное расположение испарителя и нагревателя упрощает техническое обслуживание в процессе эксплуатации и в период профилактического ремонта.
9. Пароструйная технология получения ультрадисперсных порошков меди и сплава «медь-олово» с использованием роторного питателя позволяет организовать процесс испарения-конденсации в непрерывном цикле. Эффективность способа дробления парового потока на несколько самостоятельных струй с целью регулирования дисперсности порошка подтверждена при организации промышленной технологии.
10. Пароструйная технология получения ультрадисперсных порошков меди и сплава «медь-олово» внедрена на предприятии ООО НПП «Уралавтохим» (г. Екатеринбург).
Список литературы
- Фришберг И.В., Кватер Л. И., Кузьмин Б. П., Грибовский С. В. Газофазный метод получения порошков. — М.: Наука, 1978. — 226 с.
- Порошки цветных металлов. Справочное изд./ Под ред. С. С Набойченко. М.: Металлургия, 1997. — 542 с.
- Соколовский П.А., Белов Ю. И. Электротермическое получение цинковой пыли на Беловском цинковом заводе.- Цветные металлы, 1958, № 11, с.20−25.
- Жиман К., Фик Г., Сырычинский 3. Способ получения цинковой пыли с высоким содержанием металлического цинка и применяемый для этого конденсатор. Пат. (Польша), № 40 802, 1958.-РЖМ, 1960, 2Г964П.
- Милков А., Енчев И., Буюклиев Г. Метод и аппарат за получаване на дисперсен цинков прах.- Металлургия, 1972, № 11/12, с.24−26.
- Китала М., Фик Г., Жиман К. Способ конденсации паров кадмия и цинка и устройство для осуществления этого способа. Пат. (Польша), № 49 047, 1964.- РЖМ, 1966, 5Г187П.
- Способ изготовления цинковой пыли. Пат. (Австрия), № 290 861,1969.-РЖМД972, 2Г379П.
- Бабат Г. И. Индукционный нагрев металлов и его промышленное применение. -М.-Л.:Энергия, 1965.- 552 с.
- Донской А.В., Клубникин B.C. Электроплазменные процессы и установки в машиностроении.- Л.: Машиностроение, Ленингр. отделение, 1979. -221с.
- Ушаков В.И., Редькин В. Е., Безруких Г. Ф. Получение высокодисперсных порошков в плазме дугового разряда низкого давления // Сб.тр. V Всероссийской конф. «Физикохимия ультрадисперсных систем», Новоуральск, 2001, ч.1, с. 77−82.
- Способ получения тонких порошков металлов и сплавов и устройство для его осуществления. Пат. (Франция), № 2 035 437 (В), 1971.
- Сахиев А.С., Смелянский М. Я. и др. Разработка и исследование установки для получения аэрозолей в высокочастотном безэлектродном разряде методом испарения и конденсации. — Электротермия, 1965, № 46, с. 10−13.
- Котов Ю.А. Получение нанопорошков методом ЭВП // Сб.тр. IV Всероссийской конф. «Физикохимия ультрадисперсных систем», Москва, 1999, с. 60−66.
- Котов Ю.А., Осипов В. В. Саматов О.М. и др. Получение и характеристики оксидных нанопорошков при испарении мишени импульсным СО^ лазером // Сб.тр. V Всероссийской конф. «Физикохимия ультрадисперсных систем», Новоуральск, 2001, ч. 1, с. 69−76.
- Котов Ю.А., Осипов В. В., Саматов О. М., Иванов М. Г. Получение нанопорошков YSZ при испарении мишени импульсным СОг лазером // Сб.тр. IV Всероссийской конф. «Физикохимия ультрадисперсных систем», Москва, 1999, с. 67−69.
- Muller Е. et al. // Powder and particle, 1995. № 13. P. 79.
- Бардаханов С.П., Корчагин А. И., Куксанов H.K. и др. Получение нано-дисперсных порошков пучком ускоренных электронов в атмосфере воздуха // Сб.тр. V Всероссийской конф. «Физикохимия ультрадисперсных систем», Новоуральск, 2001, ч.1, с. 64−68.
- Золкин А.С. Источники паров металлов для научных исследований и технологий // РАН Сибирское отделение. Институт теплофизики, 1992, с. 75.
- Пат. 2 113 942 РФ, МПК6 6 В 22 F 9/12. Способ испарения металла и устройство для его осуществления / Фришберг И. В., Ландау М. Б., Брезан-ский В.Г., Ефремов С. Г. № 97 108 534/02- Заявл. 27.05.97- Опубл. 27.06.98. Бюл. № 18.
- А.с. 1 491 032 СССР, МПК4 С 23 С 14/26. Испаритель для металлов и сплавов / Пастухов В. П., Волостнов В. Г., Цимбалист М. М., Фришберг И. В. -№ 4 311 402/24−21- Заявл. 30.09.87- Опубл. 20.11.97. Бюл. № 32.
- Пат. 2 118 398 РФ, МПК6 С 23 С 14/24. Испаритель для металлов и сплавов / Пастухов В. П., Смирноз Б. Н., Селетков А. И. № 97 116 642/02- Заявл. 7.10.97- Опубл. 27.08.98. Бюл. № 24.
- A. S. Zolkin, Yu. G. Shukhov, «Clusters of magnesium from pure vapor expansions», Preprint 263/1992. Inst, of Thermophysics, Academy of Sciences, Novosibirsk, Russia.
- A. Athanasion, O. F. Hagena, «Cesium vapor jettarget produced with a supersonic nozzle. Rarefied Gas Dynamics», Proc. Intern. Symp. on Rarefied Gas Dynamics. Plenum Press, New York, 1985- Novosibirsk. R.S.F.S.R., p. 777, 1982.
- V. G. Dudnikov, V. P. Efimov, G. I. Feksal1, «Pulse cesium target for the analyzer of recharging atoms», Pribory i Tekhnika Eksperimenta, N 6, p. 138, 1983.
- R. D. Mathis, E. Oslon, A. Richardt, «Evaporation de metaux a partir d’une source converte», Vide, V. 30, N 177−178, p. 153, 1975.
- A. J. Kelly, D. Santavicca, «High intensity copper atom beam-preliminary results», Rev. Sci. Instrum., V. 44, N 12, p. 1734,1973.
- A. A. Ivanov, «High temperature cells for the evaporation of difficultly volatile compounds», Pribory i Tekhnika eksperimenta, N 2, p. 237, 1974.
- Pat. N 1 483 966. Specification. England, published 24 Aug. 1977.
- F. R. Jake, D. Saxon, G. D. Stein, «Electron diffraction study of clustered beams obtained with the help of the nozzle», In: Mechanics. Dynamics of rarefied gases, Mir, Moscow, N 6, p. 314,1976.
- A. Herrmann, E. Schumacher, L. Woste, «Preparation and photoionization potential of molecules of sodium, potassium and mixed atoms», J. Chem. Phys., V. 65, N 5, p. 2327, 1978.
- E. Schumacher, М. Kappes, К. Marti, P. Radi, M. Schar, B. Schmidhalter, «Metal-clusters: Preparation, Properties, Theory», Ber. Bunsenges. Phys. Chem., V. 88, p. 220,1984.
- Y. Saito, K. Mihama, T. Moda, «Formation of lead clusters in supersonic nozzle expansion: Effect of Nozzle Geometry», J. Appl. Phys., V. 22, p. L715, 1983.
- Y. Saito, «Production of metal clusters by nozzle beam expansion and analysis by TOF mass-spectrometry», Microclusters. Proc. 1 NEC Symp., Hakone and Kawasaki, Japan, Oct. 20−23, p. 121, 1986.
- R. Weiel, M. Rub, T. Tschudi, К. H. Niederwals, «ICB source design recommendations developed by numerical calculations of the potential inside the source», Proc. 13th Symp. on Ion Sources and Ion-Acc. Techn., Ion Eng. Soc. of Japan, June 1990.
- M. Sosnovski, S. Krommenhoek, J. Sheen, R. Comely, «Study of the properties of Ga beam from the nozzle source», J. Vac. Sci. Technol. A. V. 8, N 3, p. 1458, 1990.
- A. I. Krylov, «Design and investigation of vapor flow sodium target to obtain intensive beam of negatively charged hydrogen ions», Autoref. Thesis Cand. Phys. Math. Sci., Kurchatov IAE., Moscow, 1990.
- A. I. Krylov, V. V. Kuznetzov, «Supersonic vapor jet as vacuum lock», Preprint Kurchatov IAE N 3330/7. Moscow, 1980.
- B. A. Dyatchkov, V. M. Nesterenko, V. Yu. Petrusha, «Lithium neutralizer of ions», Pribory i Tekhnika Eksperimenta, N 2, p. 35, 1974.
- A.S. Zolkin, «Peculiarities in construction of vapor-source of substances, used for ionic-cluster deposition of films». Tekhnika sredstv svyazy, (Technology and equipment) N1−2, p.96, 1992.
- Несмеянов A.H. Давление паров химических элементов.- М.: Изд. АН СССР, 1961.-393 с.
- Теоретические основы теплотехники. Теплотехнический эксперимент.: Справочник / Под общ. ред. Григорьева В. А., Зорина В. М. М.: Энерго-атомиздат, 1988. — 560 с.
- Лыков А.В. Теория теплопроводности. М.: Высшая школа, 1965. — 600 с.
- Кутателадзе С.С. Теплопередача и гидродинамическое сопротивление. Справочное пособие. -М.: Энергоатомиздат, 1990. -367 с.
- Кутателадзе С.С. Основы теории теплообмена. Новосибирск: Наука, 1970.-660 с.
- Эккерт Э.Р., Дрейк P.M. Теория тепло- и массообмена. М., Л.: Государственное энергетическое издательство. 1961. — 680 с.
- Лойцянский Л.Г. Механика жидкости и газа. М.: Наука, 1987. — 840 с.
- Седов М.М. Механика сплошных сред. М.: Наука, 1988, Т.2. — 655 с.
- Вукалович М.П., Новиков И. И. Техническая термодинамика. М.-Л.: Наука, 1962. -304 с.
- Дейч М.Е. Техническая газодинамика. М.: Энергия, 1974. — 592 с.
- Кириллин В.А., Сычев В. В., Шейндлин А. Е. Техническая термодинамика. М.: Энергия, 1974. -477 с.
- Юдаев Б.Н. Техническая термодинамика. Теплопередача. М.: Высшая школа, 1988.-479 с.
- В.И. Крутов, С. И. Исаев, Н. П. Кожинов и др. Техническая термодинамика. М.: Высшая школа, 1991. — 384 с.
- Г. Н. Абрамович, Т. А. Гиршович, С. Ю. Крашенинников. Теория турбулентных струй. М.: Наука, 1984. — 715 с.
- Вавилов Д.О. Управление структурой сверхзвуковой струи в технологических процессах // Вестник Севастопольского технического университета, серия «Механика, энергетика, экология», 1999. С.23−24.
- Кудинов П.И. Численное моделирование пространственных течений вязкой несжимаемой жидкости // Вюник Дншропетровського ушверситету. Сер1я Мехашка. -2001. Випуск 4. -Т.1. С.89−99.
- Кудинов П.И., Еричева В. А. Применение алгоритмов на неструктурированных сетках для расчета задач тепломассообмена // Труды III российской национальной конференции по теплообмену. -М: Издательство МЭИ. 2002. Т.2. С.186−189.
- Kjellgren P., Hyvarinen J. An arbitrary Lagrangian-Eulerian finite element method // Comput. Mechanics. -1998. -Vol.21, № 1. -P.81−90.
- Дейч M.E., Филлипов Г. А. Газодинамика двухфазных сред. М.: Энерго-издат, 1981.-472 с.
- Горбунов В.Н., Пирумов У. Г., Рыжов Ю. А. Неравновесная конденсация в высокоскоростных потоках газа. М.: Машиностроение, 1984. -200 с.
- Давыдов Л.М. Исследование неравновесной конденсации в сверхзвуковых соплах и струях // Изв. АН СССР. МЖГ. 1971, № 3. С.419−425.
- Абрамович Г. Н., Бузов А. А., Зуев Ю. В., Лепешинский И.А., Эпштейн
- B.И. Исследование конденсации пара в паровоздушной струе // Изв. АН СССР МЖГ, 1976. № 3. С. 142−144.
- Сутугин А.Г., Пучков А. С., Лушников А. А. Спонтанная конденсация в турбулентной затопленной струе // Коллоидный журнал, 1978, т.40, № 2.1. C.285−291.
- Ватажин А.Б., Валеев Р. С., Лихтер В. А. и др. Исследование турбулентных паровоздушных струй при наличии конденсации и введении в поток посторонних частиц //Изв. АН СССР. МЖГ, 1984. № 3. С.53−61.
- Ватажин А.В., Лебедев А. Б., Мареев В. А. Математическое моделирование различных режимов конденсации в турбулентных изобарических струях // Изв. АН СССР. МЖГ, 1985, № 1. С.59−67.
- Гордиец Б.Ф., Шмоткин Ю. С. Кинетика конденсации в охлаждающихся газах // Хим. физика, 1985, т.4. № 4. С.484−492.
- Швыдкий B.C., Швыдкий Д. В., Шаврин B.C. Математические методы теплофизики. Екатеринбург: Изд-во УГТУ, 2000. — 155 с.
- Патент № 2 183 693 РФ, МПК 7 С 23 С 14/24. Испаритель для металлов и сплавов / Пастухов В. П., Лубнин А. А., Смирнов Б. Н., Пастухов А. В. -2 000 101 071/02- Заявлено 12.01.2000- Опубл. 20.06.2002. Бюл. № 17.
- Заявка на пат. РФ 2 004 105 752, приор, от 25.02.2004. МПК 7 С23 С13/12, В22 F 9/12 / Пастухов В. П., Пастухов А. В., Набойченко С.С.
- Пат. 2 219 283 РФ, МПК7 С 23 С 14/26, В 22 F 9/12. Испаритель для металлов и сплавов / Пастухов В. П., Пастухов А. В. № 2 002 101 471/02- Заявл. 11.01.2002- Опубл. 20.12.2003. Бюл. № 35.
- Технико-экономическая и коммерческая оценка разработанных технологий.
- Технология получения высокодисперсного порошка цинка.
- Технология получения ультрадисперсных порошков меди и сплава «медь-олово «.
- По сравнению с «Туманом-ЗМ» металлоемкость аппарата по получению порошков меди и сплава «медь-олово» практически не изменилась.
- Вертикальная конструкция аппарата позволила уменьшить занимаемуюлплощадь до 8 м, т. е. привела к снижению на 60% по сравнению с «Туманом-ЗМ».
- Новые композиционные материалы на основе высоко- и ультрадисперсных порошков.
- В 2005 г. ООО HI 111 «Уралавтохим» планирует промышленное освоение пароструйной технологии получения высокодисперсного порошка цинка, ж-обходимое для расширения производства антикоррозионных цинкнаполнен-ных красок для технологии «холодного цинкования».
- ИСПЫТАТЕЛЬНЫЙ ЦЕНТР «СТА В АН-ГЕСТ» (Апесrai аккредитации № РОСС КЬ.0001.22ЭФ05 действителен до 05.04.2007 г.) к. 326. тел.374−03−70. 37S-76- 44
- Мронжол испытаний № от .-----(19 tv
- Заказчик: ООО ППМ «Уралавтохим»
- Объект анализа: порошки бронзовые марки 11НУ
- Результаты анализа: массовые юли, %1. Олово Углеродi 1роба № 1. начало процесса 7.95
- Проба X» 2. конец процесса 7,691. Средняя проба 0,115f/lt 4. / ,? J& ь у, а с /С /Т «1. Л/f
- MimcTCpcTBO падине та смсргетикн УьграТни ДЕРЖАВИН ШЯПРИСМСТВО
- УкраТнсьмш иаукоао-дослщпнй шституг нафтопсреробпоУ промнсловос-ri «МЛСМЛ»
- Техническому директору НПО «УРАЛАВТОХИМ» госп. Пастухову В. П. 620 219, г Екатеринбург, пр Ленина, 101/1
- Направляем Вам результаты испытаний трибологических свойств металлонаполненной пластичной смазки марки Суперлит (ТУ 0254−650 316 079−2002), разработанной государственным научным центром РФ «Уральский институт металлов»
- Трибологические свойства, определенные на четырехшариковой машине трения по ГОСТ 94 901. Наименование смазки
- Наименование показателей Литол-24 (базовая) Суперлит
- Нагрузка критическая, Рк, Н 630 980
- Нагрузка сваривания, Рев, Н 1410 3090
- Индекс задира, Из, Н 296 399
- Диаметр пятна износа, Ди при 392 Н, мм 0,90 0,70
- Зам. директора по научной работе6