Исследование и разработка пеноалюминия, получаемого методом механического легирования из вторичного сырья
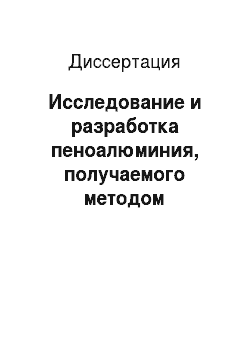
Показана возможность и разработан технологический процесс получения пеноалюминия из механически легированных сплавов АМгб, Д16 и АК12М2 с содержанием TiH2 от 1 до 1,5% по массе. Метод включает в себя: обработку дешевого разнородного вторичного сырья и частиц TiH2 в планетарной или вибрационной мельнице с целью получения гранул — полуфабрикатов с гомогенной структуройконсолидацию гранул различными… Читать ещё >
Содержание
- 1. Обзор научной литературы
- 1. 1. Пенометаллы и пеноалюминий, как наиболее распространенный в промышленности материал этого класса
- 1. 1. 1. Анализ способов получения пеноалюминия по данным патентного поиска и других источников
- 1. 1. 1. 1. Пеноалюминий, получаемый с использованием литейных технологий
- 1. 1. 1. 2. Пеноалюминий, получаемый с использованием порошковых технологий
- 1. 1. 1. Анализ способов получения пеноалюминия по данным патентного поиска и других источников
- 1. 1. Пенометаллы и пеноалюминий, как наиболее распространенный в промышленности материал этого класса
- 1. 2. Механическое легирование
- 1. 2. 1. Общие положения
- 1. 2. 2. Стадии механического легирования твердых веществ
- 1. 2. 3. Процессы, протекающие при механической обработке твердых веществ
- 1. 2. 4. Классификация диспергирующих аппаратов
- 1. 2. 5. Аппараты ударно-истирающего действия
- 1. 3. Механические свойства пеноалюминия
- 1. 4. Порофоры
- 1. 4. 1. СаСОз (мел)
- 1. 4. 2. Гидрид магния
- 1. 4. 3. Гидрид циркония
- 1. 4. 4. Гидрид гафния
- 1. 4. 5. Гидрид титана
- 1. 5. Выводы по обзору литературы
- 2. 1. Объекты исследования
- 2. 2. Оценка факторов, влияющих на процесс получения качественного пеноалюминия из вторичного алюминиевого сырья
- 2. 3. Подготовка исходных материалов для MJ1 и метода «вихревого» перемешивания
- 2. 3. 1. Получение матричных сплавов
- 2. 3. 2. Типы порофора (ТШг) и способы их получения
- 2. 4. Обработка порошковых смесей в аппаратах
- 2. 4. 1. Обработка в планетарной мельнице (ПМ)
- 2. 4. 2. Обработка порошка по методу «вихревого» перемешивания
- 2. 4. 3. Обработка в вибрационной мельнице
- 2. 5. Получение консолидированных образцов
- 2. 6. Методика вспенивания
- 2. 7. Методика исследования структуры и свойств
- 2. 7. 1. Приготовление шлифов из гранул и консолидированных образцов
- 2. 7. 2. Рентгеновский фазовый анализ
- 2. 7. 3. Определение гранулометрического состава и линейных размеров порошка гидрида титана и пор вспененного материала
- 2. 7. 4. Дифференциальный термический анализ
- 2. 7. 5. Оценка количества выделяющегося газа (водорода) из гидрида титана (ТШг)
- 2. 7. 6. Оценка плотности консолидированных образцов и пеноалюминия
- 2. 7. 7. Методика определения механических свойств 74 'V
- 2. 8. Статистическая обработка экспериментальных данных
- 3. 1. Расчет толщины стенки между порами
- 3. 2. Имитационная модель процесса пенообразования
- 3. 2. 1. Имитационная модель пенообразования без учета кристаллизации
- 3. 2. 2. Модель пенообразования с учетом кристаллизации
- 3. 2. 3. Характеристики качества пеноалюминия
- 3. 2. 4. Компьютерное моделирование процесса пенообразования пеноалюминия
- 3. 2. 5. Экспериментальное изучение вспенивания алюминия
- 3. 2. 6. Дальнейшие развитие моделирования вспенивания металлов
- 4. 1. Получение пеноалюминия методом MJI и методом «вихревого» перемешивания
- 4. 2. Влияние технологических параметров на процесс вспенивания
- 4. 2. 1. Влияние агрегатного состояния сплавов во время процесса дегидрирования и ширины их интервала кристаллизации на процесс пенообразования
- 4. 2. 2. Определение оптимального времени выдержки в печи во время вспенивания
- 4. 2. 3. Влияние содержания гидрида титана на процесс вспенивания
- 4. 2. 4. Влияние времени обработки в аппаратах на процесс вспенивания
- 4. 2. 5. Влияние температуры консолидации на процесс вспенивания 109 4.3. Механические свойства пеноалюминия
- 5. 1. Получение гидрида титана из вторичного титанового сырья, с применением метода MJ
- 5. 2. Влияние скорости нагрева консолидированных образцов на структуру и свойства пеноалюминия
Исследование и разработка пеноалюминия, получаемого методом механического легирования из вторичного сырья (реферат, курсовая, диплом, контрольная)
Актуальность работы.
В последние годы наблюдается значительный интерес к разработке новых составов и технологий получения пеноалюминия, что объясняется наличием у изделий из этого материала необычного комплекса свойств: низкая плотность, высокий уровень удельных свойств, низкие значения коэффициентов теплои электропроводности, высокая сопротивляемость воздействию огня, экологическая чистота, способность эффективно поглощать энергию удара. В настоящее время пеноалюминий получают разными способами (жидкофазным и твердофазным) и в основном из первичных материалов. Один из твердофазных (или порошковых) методов, а именно механическое легирование (MJ1), может быть перспективным для внедрения в производство пеноалюминия.
MJ1 является, на данный момент, наиболее перспективным направлением в производстве композиционных материалов (КМ). Это один из самых современных методов получения дисперсноупрочненных керамическими частицами композиционных материалов на основе различных цветных металлов. Пеноалюминий тоже можно рассматривать, как КМ, где вместо керамических частиц — порофор. Поэтому MJI тоже может стать перспективным методом для его получения. Этот метод заключается в обработке порошкообразных компонентов и их смесей различного состава в высокоэнергетических мельницах и последующей консолидации, вновь сформировавшейся активированной смеси, для получения полуфабриката или готовой детали. Как показали исследования, еще одним преимуществом MJI является возможность использования отходов производства и лом алюминиевых сплавов, что значительно удешевляет производство (сырьевая составляющая в стоимости производства снижается от 45 — 65%).
Цель работы: исследовать возможность получения пеноалюминия из вторичного сырья методом MJI. На основе проведенных исследований оптимизировать состав и структуру, а также предложить новую экономичную технологию получения пеноалюминия.
Для достижения поставленной цели в работе решали следующие задачи:
1. Разработать модель пенообразования и последующей кристаллизации пеноалюминия.
2. Исследовать структуру и свойства иеноалюминия па разных стадиях получения.
3. Сформулировать основные принципы выбора матричных сплавов.
4. Выбрать порофоры и определить их оптимальное содержание в исследуемых композициях для достижения наилучшего комплекса свойств.
5. Разработать экономичную технологию получения пеноалюминия.
Научная новизна.
1. Показана возможность получения качественного пеноалюминия с применением метода MJI из низкосортного вторичного сырья. Метод включает в себя: обработку разнородного вторичного сырья и частиц TiH2 в планетарной или вибрационной мельнице с целью получения гранул — полуфабрикатов с гомогенной структуройконсолидацию гранул для получения компактного полуфабриката (прекурсора) — завершающей стадией получения пеноалюминия является вспенивание при температурах выше температуры дегидрирования TiH2.
2. Разработана имитационная модель процесса пенообразования в алюминиевых расплавах с последующей кристаллизацией пеноалюминия. Показано, что модель позволяет визуализировать процесс пенообразования и дает предварительные рекомендации по параметрам получения пеноалюминия с оптимальной структурой.
3. Установлен оптимальный состав шихты для получения качественного пеноалюминия. Показано, что в качестве матричных сплавов могут быть применены сплавы, температура ликвидуса которых должна быть меньше или равна температуре наиболее интенсивной стадии дегидрирования TiH2, а оптимальное содержание этой фазы равно 1 -1,5 масс. %.
4. Установлено влияние времени MJI и скорости нагрева до температуры вспенивания на качество пеноалюминия на примере механически легированных сплава,' АМгб. Показано, что оптимальным временем MJI, при котором наблюдается высокая и равномерно распределенная пористость, является 1 ч. Увеличение скорости нагрева прекурсора до 2500 °С/мин приводит к уменьшению среднего размера пор до 0,64 мм, увеличению равномерности их распределения по размерам, а последующее быстрое охлаждение снижает вероятность выхода газа из образца, что приводит, в свою очередь, к снижению плотности пеноалюминия до 0,9 г/см3.
Практическая ценность.
1. Разработан и предложен технологический процесс получения пеноалюминия (НОУ-ХАУ № 66−013−2004) из механически легированных сплавов, АМгб, Д16 и АК12М2 с содержанием ТШг от 1 до 1,5% по массе. Показано, что, например, материал АМгб + 1,5 масс. % Tfflb после 1 ч обработки в ПМ в атмосфере аргона, консолидации при 350 °C и вспенивания со скоростью нагрева 800 °С/мин обладает следующим сочетанием показателей: плотность — 0,94 г/см3, средний размер пор — 0,72 ± 0,04 мм, при коэффициенте равноосности -0,9.
2. Предложен технологический процесс получения пеноалюминия из сплавов АМгб, Д16 и АК12М2 с содержанием ТШг от 0,5 до 1% по массе методом смешивания в потоке газа (метод «вихревого» перемешивания) (НОУ-ХАУ № 109−013−2005). Показано, что, например, материал АМгб + 1 масс. % TiH^ после обработки 7−10 мин в установке «вихревого» перемешивания, консолидации при 350 °C и вспенивании со скоростью нагрева 200 °C /мин обладает следующими сочетанием показателей: плотность — 0,9 г/см3, средний размер пор — 1,6 ± 0,1 мм, при коэффициенте равноосности — 1,0.
3. Предложен технологический процесс получения ТШ2 — порофора, для последующего получения пеноалюминия, из стружки сплава ВТ 1−0 с применением MJI (НОУ-ХАУ № 108−013−2005). Содержание водорода в таком TiH2 достигает 3,6 масс. %.
1. Обзор литературы.
Выводы:
1. Показана возможность и разработан технологический процесс получения пеноалюминия из механически легированных сплавов АМгб, Д16 и АК12М2 с содержанием TiH2 от 1 до 1,5% по массе. Метод включает в себя: обработку дешевого разнородного вторичного сырья и частиц TiH2 в планетарной или вибрационной мельнице с целью получения гранул — полуфабрикатов с гомогенной структуройконсолидацию гранул различными способами для получения компактного полуфабриката (прекурсора) — завершающей стадией получения пеноалюминия является вспенивание при температурах выше температуры наиболее интенсивной стадии дегидрирования TiII2. Показано, что, например, материал АМгб + 1,5 масс. % TiH2 после 1 ч обработки в планетарной мельнице в атмосфере аргона, консолидации при 350 °C и вспенивания со скоростью нагрева 800 °С/мин обладает следующим сочетанием показателей: плотность — 0,94 г/см3, средний размер пор — 0,72 ± 0,04 мм, при коэффициенте равноосности — 0,9.
2. Разработана имитационная модель процесса пенообразования в алюминиевых расплавах с последующей кристаллизацией пеноалюминия. Показано, что визуализация процесса вспенивания, а также данные расчета позволили выработать предварительные рекомендации по параметрам получения пеноалюминия с оптимальной структурой.
3. Предложен технологический процесс получения пеноалюминия из сплавов АМгб, Д16 и АК12М2 с содержанием TiH2 от 0,5 до 1% по массе методом смешивания в потоке газа (метод «вихревого» перемешивания). Показано, что, например, материал АМгб + 1 масс. % TiH2 после перемешивания 7−10 мин, консолидации при 350 °C и вспенивании со скоростью нагрева 200 °C /мин обладает следующими сочетанием показателей: плотность — 0,9 г/см, средний размер пор — 1,6 ± 0,1 мм, при коэффициенте равноосности — 1,0.
4. Установлен оптимальный состав шихты для получения качественного пеноалюминия. Показано, что в качестве матричных сплавов могут быть применены сплавы, температура ликвидуса которых должна быть меньше или равна температуре наиболее интенсивной стадии дегидрирования ТШг, а оптимальное содержание этой фазы равно 1−1,5 масс. %.
5. Установлено влияние времени механического легирования и скорости нагрева до температуры вспенивания на качество пеноалюминия на примере механически легированных сплава, АМгб. Показано, что оптимальным временем механического легирования, при котором наблюдается высокая и равномерно распределенная пористость, является 1 ч. Увеличение скорости нагрева прекурсора до 2500 °С/мин приводит к уменьшению среднего размера пор до 0,64 мм, увеличению равномерности их распределения по размерам, а последующее быстрое охлаждение снижает вероятность выхода газа из образца, что приводит, в свою очередь, к снижению плотности пеноалюминия до 0,9 г/см3.
6. Предложен технологический процесс получения TiH2 — порофора, для последующего получения пеноалюминия, из стружки сплава ВТ 1−0 с применением механического легирования. Содержание водорода в таком TiH2 достигает 3,6 масс. %.
Список литературы
- Davies G.J., Zhen S.// J. of Material Science. 1983. V. 18. P. 1899−1911.
- Арбузова Jl.А., Зенина M.B., Шмаков Ю. В., Андреев Д. А. // Цветные металлы. 1997. № 2. С. 611−618.
- Старовойтенко Е.И., Арбузова Л. А., Пасхин Л. Н., Косин В. И. // Технология легких сплавов. 1998. № 5−6. С. 45−51.
- Koch V., Thompson М. S., Nardon V.C. // IV Международная конф. по алюминиевым сплавам. USA. Atlanta. 1995. P. 387−394.
- Арбузова Л.А. и др. Процесс вспенивания плотных полуфабрикатов из пеноалюминия. // Цветные металлы. 2001. № 3. С. 79−82.
- Карпинос Д.М. Новые композиционные материалы. Киев: Вища школа, 1977.
- Evans, A. G. and Hutchinson, J. W., in Metal Foams and Porous Metal Structures, ed. J. Banhart, M. F. Ashby and N. A. Fleck. Verlag Metall Innovation Technologie MIT, Bremen, 1999, p. 45.
- J. Banhart, Progress in Materials Science 46 (2001) 610.
- L.J. Gibson, M.F. Ashby, in: Cellular Solids: Structure and Properties, second ed, Cambridge University Press, Cambridge, UK, 1997.
- S. W. Youn and C. G. Kang, «Fabrication of foamable Prekursors by powder compression and induction heating process», metallurgical and materials transactions, 08 2004.
- US 6,332,907 DECEMBER 25, 2001.42. US6090232 2000−07−18.43. US6094798 August 1, 2000.44. EP0927591 1999−07−07.45. EP0927590 1999−07−07.46. EP0927589 1999−07−07.47. DE19501508 1996−04−25.48. US6444330 2002−09−03.
- US 6,465,111 October 15, 2002.50. EP1004376 2000−05−31.51. DEI9651197 1997−06−19.
- US 5,221,324 June 22, 1993.65. US 5 281 251 1994−01−25.
- US 6,103,397 August 15, 2000.
- JP07−102 330 18.04.1995. 99.09−119 789 06.05.1997.
- US 5,564,064 October 8, 1996.
- US 5,972,521 October 26, 1999.
- US 5,384,203 January 24, 1995.
- US 5,930,580 July 27, 1999.
- US 6,250,362 June 26,2001.
- US 6,308,999 October 30, 2001.
- US 6,464,933 October 15, 2002.139. DE10131041 2002−01−24.140. EP1028169 A3 2000−08−16.141. EP1055470 2000−11−29.142. EP1072839 2001−01−31.143. EP1036616 2000−09−20.144. EP1028283. 2000−08−16.
- US5632319. Shan-Chanq, Kou-Chanq Su. Method for manufacturing environmentally conscious foamed aluminum materials. 1997−05−27.
- US5516592. Yang- Chin-Chan, Su- Kou-Chang, Chen- Wen-Chi, Chueh- Shan-Chang. Manufacture of foamed aluminum alloy composites. 1996−05−14.
- W09325718. Gh Czy Ivan, Saur Erhard. Process for making moldings and use thereof. 199 312−23.148. CH684072. 1994−07−15.
- Патент Ru 2 138 367 CI. Арбузова JI.A., Трубкина E.M. и др. Способ получения пористых полуфабрикатов из порошков алюминиевых сплавов. 1999.09.27.
- Патент Ru 2 153 957 С1. 2000.08.10.
- Тугубалин А. В. Пористые металлы //Литейное производство. 1993. № 10. С. 4−5.
- С.С. Yang, Н. Nakae. Foaming characteristics control during production of aluminum alloy foam. Journal of Alloys and Compounds 313 (2000) 188−191.
- Kobashi M., Kantake N. Controlling Technique of Pore Morphology of Highly Reliable Aluminum Foam. Department of Materials Processing Engineering, Graduate School of Engineering. Nagoya University, Furo-cho, Chikusa-ku, Nagoya, 464−8603, Japan.
- Gdoutos E.E., Daniel I.M., Wang K.-A. Failure of cellular foams under multiaxial loading. Composites: Part A 33 (2002) 163 176.
- A.Reyes, O.S.Hopperstad, M.Langseth. Aluminum foam-filled extrusions subjected to oblique loading: experimental and numerical study. International Journal of Solids and Structures 41 (2004) 16 451 675.
- C.C. Yang, Н. Nakae. The effects of viscosity and cooling conditions on the foamability of aluminum alloy. Journal of Materials Processing Technology 141 (2003) 202−206.
- A. Sosnik, US Patent 2 434 775 (1948).
- H. Ueno, S. Akiyama, Light Metal 37 (1987) 42, (in Japanese).
- Asholt, P., in Metal Foams and Porous Metal Structures, ed. J. Banhart, M. F. Ashby and N.
- A. Fleck. Verlag Metall Innovation Technologie MIT, Bremen, 1999, p. 133.
- Miyoshi, Т., Itoh, M., Akiyama, S. and Kitahara, A., Mat. Res. Symp. Proc. 1998, 521, 133.
- Nakajima H, Hyun SK, Ohashi K, OtaK, Murakami K. Colloids Surfaces A 2001 -179:209.
- Michizu S., Hidetoshi U. Unoho J. Jap. Foundrymen’s Soc. 1991. 63. № L. P.9−14
- Ac 558 953 МКИ С 22 С 1/08. Способ получения пористых отливок / Т. П. Борисов, Ю.
- B. Моисеев, А. В. Наривский // Открытия. Изобретения. 1977. № 19.
- Патент Ru 2 121 904 С1, 1998.11.20.
- Е. JI. Фурман, С. П. Казанцев, М. В. Минин. Получение литых пористых материалов. // Литейное производство № 6, 2002.
- Патент Ru 2 154 548 С1, 2000.08.20
- Патент Ru 2 085 339 С1, 1997.07.27
- Патент Ru 2 139 774 С1, 1999.10.20
- Duarte, J. Banhart. A study of aluminium foam formation kinetics and microstructure. // Acta materials. 48 (2000) 2349 — 2362.
- Banhart, J., Foam metal: the recipe. // Europhysics News, 1999, 30, 17.
- Banhart, J. and Baumeister, J., Deformation characteristics of metal foams, J. Material Scientist., 1998, 33, 1431.
- Weaire, D. and Hutzler, S., The Physics of Foams. Oxford University Press, Oxford, 1999.
- Youn S.W., Kang C.G. Fabrication of foamable precursors by powder compression and induction heating process.// J. of Material Science. 2003. V. 18. P. 769−776.
- J. Baumeister, German Patent 4, 018, 360, 1990.
- Филипп Т., Кен С. От частиц к сплошным материалам: «Conform» для вторичного сырья и специальных сплавов. // J. of Aluminium international today. Ноябрь, 2003. С. 18−20.
- Новикова М.Б., Трубкина Е. М., Богданов В. А. Процесс вспенивания плотных полуфабрикатов из пеноалюминия. // Цветные металлы, 2001, № 3. С. 96−98.
- D. М. Elzey and Н. N. G. Wadley. The limits of solid state foaming. Acta mater. 49 (2001) 849−859.
- Аввакумов В.Г. Механические методы активации химических процессов. -Новосибирск: Наука, 1979.
- Боуден Ф. П. Тейбор Д. Трение и смазка твердых тел. Пер. с англ. М.: Машностроение, 1968.
- Хайнике Г. Трибохимия. Пер. с англ. М.: Мир, 1987.
- Молчанов В.И., Селезнева О. Г., Жирнов Е. Н. Активация минералов при измельчении. -М.: Недра, 1988.
- С. Suryanarayana. // Progress in materials science, 46 (2001), P. 1−184.
- Y. Sugimura, J. Meyer, M.Y. He, H. Bart-Smith, J. Grenestedt, A.G. Evans, Acta Mater. 45 (1997)5245.
- E. Andrews, W. Sanders, L.J. Gibson, Mater. Sci. Eng. A270 (1999) 113.
- F. Simancik, J. Jerz, J. Kovacik, P. Minar, Kovove Materialy 35 (4) (1997) 265−277.
- М.Б. Новикова, E.M. Трубкина, ОАО «ВИЛС». Влияние содержание армирующего компонента и порофора на процесс вспенивания и структуру порового пространства пенокомпозитов на основе алюминиевого сплава. // Цветные металлы, 2001, № 4.
- Youn S.W., Kang C.G. Evaluation of mechanical properties of porous 6061 alloys fabricated by the powder compression and induction heating process.// J. of Material Science. 2004. V. 18. P.2419−2426.
- E. Koza, M. Leonowicz, S. Wojciechowski, F. Simancik. Compressive strength of aluminium foams. Materials Letters 58 (2003) 132-Т35~. 7 .
- A.F. Bastawros, H. Bart-Smith, A.G. Evans. Experimental analysis of.' deformation mechanisms in a closed-cell aluminum alloy foamJournal of the Mechanics and Physics of Solids 48 (2000) 301−322.
- K.C.Chan, L.S.Xie. Dependency of densification properties on cell topology of metal foams.// Scripta Materialia 48 (2003)1147−1152.
- F. Simancik, H.P. Degischer, H. Worz, Euromat '95, Assoziazione Italiana di Metallurgica, Milano, 1995.
- J. W. Paek, В. H. Kang, S. Y. Kim, J. M. Hyun. Effective Thermal Conductivity and Permeability of Aluminum Foam Materials.// International Journal of Thermophysics, Vol. 21, No. 2, 2000.193. www.niistali.ru
- Libowitz, G.G.: Journal. Nuclear Materials, 2, 1 (1960).
- Hagg G., Z. physical Chemistry. 12, 33 (1931).
- Whit wham P., Mem. sclent. Revue Metall., 57, 1 (1960).
- Vaughan D. A., Bridge J. R./ Metals, 8, 528 (1956).
- YaKel H. Г., Acta Crystallography., 11,46 (1958).
- Rundle R. E. C. G. Shull and E. O. Wollan. The crystal structure of thorium and zirconium dihydrides by X-ray and neutron diffraction. Acta Crystallographica. 1952. V. 5, p. 22−24.
- Gulbransen E. A., Andrew K. F., a) Electrochem. Soc, 101, 474 (1954) — 96, 364 (1949) — b) Metals, 7, 136 (1955) — c) Trans. AIMME, 188, 586 (1959).
- BicKol P. W., цитируется Либовицем в 194.
- JacK К. H., 1955 (данные цитируются в 194.).
- Bailey J. Е., Acta Metall., 11, 267 (1963) — Int. Conf. Electron, Microsc, 1, Paper K9, 1962.
- Ells С E., McQuillan A. D., /. Inst. Metals, 85, 89 (1956).
- Hall M. N. A. et al., Trans. Farad. Soc. 41, 306 (1944).
- Douglas Т. В., J. Am. Chem. Soc, 80, 5040 (1958).
- Albrecht W. M" J. Electrochem. Soc, 104, 142 (1957).
- Schwartz С. M" Mallett M. W. Trans. ASM, 46, 646 (1954).
- Martin S. L. H., Rees A. L. G., Trans. Farad. Soc, 50, 22, 343 (1954) — Rees A. L. G., ibid., 335.
- Brown</span> A., Hardy D., /. Nucl. Mater., 4, 110 (1961).
- Sidhu S. S. et al., a) Acta Crystallogr., 9, 607 (1956) — b) 7, 447 (1954) — c) Sidhu S. S" McGuire J. C, J. Appl. Phys., 23, 1257 (1957).2T2. Sidhu S.~S. et al.77,447 (1954). «- ~ «
- Edwards R. K., VelecKis E., J. Phys. Chem., Ithaka, 66, 1657 J. (1962).
- Espagno L. et al., a) Comptes rendus Acad. Sci., Paris, 247, 83 (1958) — b) 249, 1105 (1959) — c) Mem. scient. Revue Metall., 57, 254 (1960) — d) 59, 182 (1962) — e) Comptes rendus Acad. Sci., Paris, 250, 4352 (1960).
- Водородная технология титановых сплавов / А. А. Ильин, Б. А. Колачев, В. К. Носов, A.M. Мамонов. Москва. МИСиС, 2002.
- Рентгенографическое исследование гидридов титана в промышленных сплавах титана / Н. В. Агеев, А. А. Бабарэко, Е. Б. Рубина, С. Я. Бецофен и др. МиТОМ, 1976, № 2, с. 19−27.
- Рубцов А.Н., Олесов Ю. Г., Антонова М. М. Гидрирование титановых материалов. «Наукова думка». Киев 1971.
- Pat. № 3 017 299- Official Gasette of the U. S. Patent Office, 16/1−1962, 774, 3, 636.
- Pat. № 2 905 547- Official Gasette of the U. S. Patent Office, 22/1X-1959, 746, 4.
- Pat. № 886 002- Abridgement of specifications, 3/1, 62, 2.
- Крылов B.C.- В кн.: Титан и его сплавы, 10. Изд-во АН СССР, 1963, 159.
- Ливанов В.А., Буханова А. А., Колачев Б. А. Водород в титане. ГНТИ, М., 1962.
- Новиков И.И., Строганов Г. Б., Новиков А. И. Металловедение, термообработка и рентгенография. Учебник для вузов. М.: МИСиС, 1994. — 480 с.
- Аксенов А.А. Оптимизация состава и структуры композиционных материалов на медной и алюминиевой основе, получаемых жидкофазными методами и механическим легированием. Автореф. Дис. докт. техн. наук. М.: МИСиС. 2007.
- Шелехов Е.В.// Тр. Нац. конф. по применению рентгеновского, синхротронного излучений, нейтронов и электронов для исследования материалов. Дубна: ОИЯИ, 1997. № 3. С. 316.
- СалтыковС.А. Стериометрическая металлография. -М.: Металлургия, 1970. 375 с ил.
- Пузаков К.С. Фазовые превращения в сплавах системы Al-Cu-Mn-Si-Ti-Zr-Cd и разработка режимов термической обработки сплавов этой системы. Дисс. к.т.н. Москва. 1989.
- Золоторевский B.C. Механические свойства металлов. Учебник для вузов. М.: МИСиС. 1998. 400с.
- Иванов И.А., Дуб А.В. Применение фрактальной параметризации для моделированиягпроцессов формирования первичной кристаллической структуры металлов. // Металлы Москва: ЭЛИЗ, № 4, 2005, С. 17−25.
- Дуб B.C., Дуб А. В., Макарычева Е. В., Иванов И. А. Теоретические основы кристаллизации сплавов на основе железа. // Тезисы докладов IX конгресса сталеплавильщиков -Старый Оскол, 2006.
- Дуб А.В., Дуб B.C., Макарычева Е. В., Иванов И. А. Факторы управления процессами затвердевания. // Электрометаллургия Москва: Наука и технологии, № 11, 2006, С 18−22.
- Дуб А.В., Иванов И. А. Программа имитационного моделирования процесса кристаллизации металлов. // Свидетельство об официальной регистрации программ для ЭВМ № 2 005 613 069,2005.
- Иванов И.А., Иванов Д. О., Аксенов А. А., Дуб А. В. Имитационная модель процесса пенообразования в алюминиевых расплавах. // Металлы Москва: ЭЛИЗ, № 6, 2006, С. 60−65.
- Дуб А.В., Иванов И. А., Аксенов А. А., Иванов Д. О. Программа имитационного моделирования процесса пенообразования алюминиевых расплавов. // Свидетельство об официальной регистрации программ для ЭВМ № 2 005 613 069, 2005.
- Борисов В.Т. Теория двухфазной зоны металлического слитка. Москва: Металлургия. 224 с. (1997).п &
- Филиппова В.Б. Структурные факторы деформации и разрушения пористых материалов. Автореф. дис. конд. техн. наук. М.: МИСиС. 2004.
- Коган Я.Д., Колачев Б. А., Левинский Ю. В. Константы взаимодействия металлов с газами. М.: Металлургия, 1987.
- Колачев Б.А., Елагин В. И., Ливанов В. А. Металловедение и термическая обработка цветных металлов и сплавов. Учебник для вузов /. М.: МИСиС, 1999. 416 с.
- Порошковая металлургия титана./ Устинов B.C., Олесов Ю. Г., Дрозденко В. А., Антипин Л. Н. М.: Металлургия, 1981. V