Методы оценки вероятности выявления дефектов и повреждений при диагностировании оборудования добычи сероводородсодержащих газа и нефти
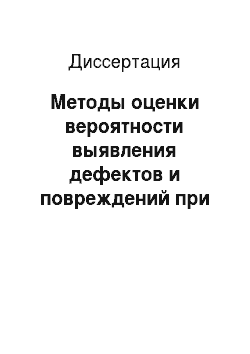
Методика обоснования выбора состава и методов диагностирования внедрена в ОАО «Техдиагностика» с начала 2011 года. Выполненная при этом оценка выявляемое&tradeдефектов оборудования ООО «Газпром добыча Оренбург» методами, включенными в действующие программы диагностирования, показала недостаточную выявляемость внутренних дефектов сварных швов. Соответствующие разделы программ были доработаны… Читать ещё >
Содержание
- 1. ПРИЧИНЫ СНИЖЕНИЯ БЕЗОТКАЗНОСТИ, ЭФФЕКТИВНОСТИ ДИАГНОСТИРОВАНИЯ, ВЫЯВЛЯЕМОСТИ ДЕФЕКТОВ И ПОВРЕЖДЕНИЙ КОНСТРУКТИВНЫХ УЗЛОВ И ЭЛЕМЕНТОВ ОБОРУДОВАНИЯ
- 1. 1. Причины и статистика отказов оборудования, критерии и методы обеспечения безотказности и безопасности его эксплуатации
- 1. 2. Причины снижения выявляемое&trade- дефектов, эффективности диагностирования и безотказности оборудования
- 1. 3. Обзор методов диагностирования и оценки выявляемое&trade- дефектов и повреждений натурных конструкций, образцов и моделей оборудования
- 2. ЭКСПЕРИМЕНТАЛЬНЫЕ ИССЛЕДОВАНИЯ И ОЦЕНКА ВЫЯВЛЯЕМОСТИ ДЕФЕКТОВ ОБОРУДОВАНИЯ НА ЕГО ОБРАЗЦАХ — МОДЕЛЯХ УЗЛОВ И ЭЛЕМЕНТОВ
- 2. 1. Анализ повреждённости, обоснование и разработка экспериментальных образцов — моделей узлов и элементов оборудования
- 2. 2. Определение выявляемое&trade- дефектов на образцах — моделях узлов и элементов оборудования
- 3. МЕТОДЫ ОБЕСПЕЧЕНИЯ ТРЕБУЕМОЙ ВЫЯВЛЯЕМОСТИ ДЕФЕКТОВ, ПОВРЕЖДЕНИЙ И БЕЗОТКАЗНОСТИ ОБОРУДОВАНИЯ ПРИ ЕГО ДИАГНОСТИРОВАНИИ
- 3. 1. Факторы и закономерности изменения выявляемое&trade- дефектов и повреждений оборудования методами диагностирования
- 3. 2. Методы снижения отрицательного влияния человеческого фактора
- 3. 3. Критерий требуемой выявляемое&trade- дефектов, повреждений и безотказности оборудования
- 3. 4. Технические решения и алгоритмы выбора методов диагностирования, обеспечивающие требуемую выявляемость дефектов и эффективность программ ТД
4 РАЗРАБОТКА И ОЦЕНКА ЭФФЕКТИВНОСТИ ПРИМЕНЕНИЯ МЕТОДИКИ ОБОСНОВАНИЯ ВЫБОРА СОСТАВА И МЕТОДОВ ПРОГРАММЫ ДИАГНОСТИРОВАНИЯ ОБОРУДОВАНИЯ ДОБЫЧИ СЕРОВОДОРОДСОДЕРЖАЩИХ ГАЗА И НЕФТИ ПО КРИТЕРИЮ ТРЕБУЕМОЙ ВЕРОЯТНОСТИ ВЫЯВЛЕНИЯ ДЕФЕКТОВ.
4.1 Методика обоснования выбора состава и методов программы диагностирования оборудования добычи сероводородсодержащих газа и нефти по критерию требуемой вероятности выявления дефектов.
4.2 Показатели оценки эффективности применения методики выбора методов диагностирования.
4.3 Апробация и эффективность применения методики выбора методов диагностирования.
Методы оценки вероятности выявления дефектов и повреждений при диагностировании оборудования добычи сероводородсодержащих газа и нефти (реферат, курсовая, диплом, контрольная)
Законодательными и нормативными документами в области промышленной безопасности возможность продолжения эксплуатации оборудования, выработавшего проектный срок эксплуатации, на опасных производственных объектах (далее — оборудования) и, в их числе объектов добычи сероводородсодержащих газа и нефти (ДСГ), определена условием положительной оценки его технического состояния, безотказности и безопасности на прогнозируемый период эксплуатации. Основу для такой оценки составляют результаты диагностирования. Учитывая, что литературные и экспериментальные данные показывают разброс значений вероятности выявления дефектов оборудования методами диагностирования до 30% и более, возникает неопределённость конечного результата программы диагностирования. То есть при жёстком нормировании допустимой вероятности отказа оборудования, оценить и обеспечить необходимую вероятность выявления дефектов при реализации программы диагностирования не представляется возможным. В этих условиях исследования параметров и критериев оценки и обоснования выбора состава и методов программы диагностирования и обеспечения необходимых вероятности выявления дефектов, безотказности и безопасности эксплуатации в прогнозируемом периоде эксплуатации оборудования становятся актуальными и значимыми. Актуальность и значимость этих исследований повышается по мере накопления оборудованием наработки.
Целью работы является разработка методов вероятностной оценки выявления дефектов и повреждений при диагностировании оборудования добычи сероводородсодержащих газа и нефти для обеспечения надёжности эксплуатации.
Основные задачи исследования:
1. Анализ методов, результатов выявления дефектов и повреждений, причин снижения безотказности и эффективности диагностирования оборудования.
2. Экспериментальные исследования и оценка вероятности выявления дефектов и повреждений оборудования на его образцах, моделях и натурных конструкциях методами диагностирования.
3. Обоснование методов обеспечения требуемых вероятности выявления дефектов, повреждений и безотказности оборудования при его диагностировании.
4. Разработка и оценка эффективности применения методики обоснования выбора состава и методов программы диагностирования оборудования, обеспечивающей требуемую вероятность выявления его дефектов и повреждений.
Научная новизна:
Обоснованы параметры, критерии и методы оценки достоверности выявления дефектов и повреждений при диагностировании оборудования. Установлено, что разброс значений вероятностей выявления дефектов и повреждений составляет до 30% и более и приводит к недооценке риска продолжения эксплуатации оборудования из-за наличия невыявленных дефектов и повреждений.
Впервые выполнена экспериментальная оценка значений, факторов и закономерностей изменения вероятности выявления по видам/типам дефектов, наиболее часто встречающихся в узлах и элементах оборудования добычи сероводородсодержащих газа и нефти.
Впервые обоснованы значения и разработаны методы и алгоритмы оценки требуемой вероятности выявления дефектов и повреждений по критериям допустимых вероятности и риска отказа оборудованияметоды, показатели, критерии и алгоритмы контроля качества диагностических работ на образцах, моделях и натурных конструкциях оборудования.
Разработаны новые нормативно-методические принципы оценки и обеспечения требуемой вероятности выявления дефектов и повреждений при диагностировании оборудования и качества проведения диагностических работ.
На защиту выносятся следующие положения:
— теоретическое и экспериментальное обоснование параметров, критериев и методов оценки достоверности выявления дефектов и повреждений при диагностировании оборудования;
— расчетно-экспериментальное обоснование: методов оценки, значений и факторов изменения вероятности выявления дефектов и повреждений оборудования на образцах и моделях его конструкциикритериальных значений требуемой вероятности выявления дефектов и повреждений для обеспечения допустимых вероятности и риска отказа оборудованияпараметров и методов контроля качества диагностических работ;
— нормативно-методические принципы оценки и обеспечения: требуемой вероятности выявления дефектов и повреждений при диагностировании оборудованиятребуемого качества диагностических работобоснования выбора состава и методов программы диагностирования оборудования.
Практическая ценность и реализация результатов работы.
Методы оценки, повышения и обеспечения на требуемом уровне значений вероятности выявления дефектов в узлах и элементах оборудования внедрены в ОАО «Техдиагностика» и применяются при диагностировании оборудования ООО «Газпром добыча Оренбург». По результатам внедрения оценены и откорректированы программы диагностирования по видам/типам оборудования, не отвечавших критериям требуемой вероятности выявления дефектов. По откорректированным программам продиагностировано 499 единиц оборудования установок комплексной подготовки газа, выявлено 43 дефекта браковочного уровня. Контроль качества диагностических работ выполняется по обоснованным в работе критериям. Ведётся учёт индивидуальных показателей надёжности специалистов неразрушающего контроля, эти показатели учитываются при распределении работ различной сложности и ответственности. Разработанные и апробированные методы реализованы в СТО-ЭПБ.И-177 «Методика обоснования выбора состава и методов программы диагностирования оборудования добычи сероводородсодержащих газа и нефти по критерию требуемой вероятности выявления дефектов» и используются в учебных процессах подготовки специалистов неразрушающего контроля.
Исследования выполнены в соответствии с п. 3.2 Перечня приоритетных научно-технических проблем ОАО «Газпром» на 2006 — 2010 годы — «Создание методов и технологий для повышения эффективности разработки и безопасной эксплуатации месторождений», отраслевой программой ОАО «Газпром» «Диагностическое обслуживание объектов добычи газа» и «Перечнем научно-технических работ ООО „Газпром добыча Оренбург“».
Объектом исследования является поврежденность оборудования ДСГ.
Предметом исследования являются характеристики методов диагностирования оборудования ДСГ и факторы, определяющие вероятность выявления этими методами существующих дефектов и отклонений параметров технического состояния.
Гипотеза исследования заключается в том, что обеспечение требуемой выявляемое&tradeдефектов методами технического диагностирования (ТД), точности оценки поврежденности и безотказности для оборудования ДСГ становится возможным с применением комплексных экспериментальных моделей оборудования ДСГ в виде совокупности экспериментальных образцов потенциально-опасных узлов и элементов оборудования с заложенными в них моделями наиболее часто встречающихся дефектовпроведения экспериментальных исследований закономерностей, причин и факторов недостаточной выявляемое&tradeдефектов и эффективности ТДобоснования критериев, разработки и внедрения технических решений и методики выбора методов диагностирования, повышения и обеспечения требуемого уровня выявляемое&tradeдефектов и эффективности ТД оборудования ДСГ.
Методологической основой исследования являются общие научно-методические основы: контроля технического состоянияконтроля параметров и свойств металла неразрушающими методами при диагностировании оборудованияоценки частоты и вероятности экспериментальными методами.
Достоверность и обоснованность полученных научных результатов обуславливается использованием общепризнанных научно-методических основ: контроля технического состоянияконтроля параметров технического состояния неразрушающими методами при диагностировании и оценке работоспособности оборудования. Достоверность подтверждается использованием: передовых методов и средств неразрушающего контроляметрологически поверенных современных приборов для неразрушающего контроляматематических методов и сертифицированных пакетов компьютерных программ математического анализа и статистической обработки экспериментальных данных.
Основные результаты работы доложены на научно-технических конференциях, включая:
— V Международную научно-техническую конференцию «Диагностика оборудования и трубопроводов, подверженных воздействию сероводородсодержащих сред», г. Оренбург, 22−25 ноября 2004 г.;
— VI Международную научно-техническую конференцию «Диагностика оборудования и трубопроводов, подверженных воздействию сероводородсодержащих сред», г. Оренбург, 20−23 ноября 2006 г.;
— V Международную научную конференцию «Прочность и разрушение материалов и конструкций», г. Оренбург, 12−14 марта 2008 г.;
— VII Международную научно-техническую конференцию «Диагностика оборудования и трубопроводов, подверженных воздействию сероводородсодержащих сред», г. Оренбург, 26−29 ноября 2008 г.;
— III Научно-техническую конференцию с международным участием «Основные проблемы освоения и обустройства нефтегазовых месторождений и пути их решения», г. Оренбург, 21−22 мая 2009 г.;
— II Научно-практическую конференцию «Безопасность регионов — основа устойчивого развития», г. Иркутск, 19−21 сентября 2009 г.;
— VIII Международную научно-техническую конференцию «Диагностика оборудования и трубопроводов, подверженных воздействию сероводородсодержащих сред», г. Оренбург, 23−26 ноября 2010 г.
По материалам диссертации опубликовано 30 печатных работ из них 6 в изданиях, входящих в «Перечень.» ВАК Минобрнауки РФ.
Диссертация состоит из введения, четырёх глав, заключенияизложена на 185 страницахсодержит 48 рисунков, 62 таблицы и список использованных источников из 141 наименования.
Выводы главы 4.
В разделе 4.1 главы 4 представлена разработанная методика обоснования выбора состава и методов программы диагностирования оборудования добычи сероводородсодержащего газа, конденсата и нефти для обеспечения требуемых вероятности выявления его дефектов и повреждений. Методика предназначена для обоснования состава методов и работ НК и средств НК для включения их в программу технического диагностирования оборудования ДСГКН, выбора методов повышения выявляемое&tradeи оценки выявляемое&tradeдефектов при техническом диагностировании по критерию требуемой выявляемое&tradeдефектов. Применение методики позволяет оптимизировать программу технического диагностирования по критерию требуемой выявляемое&tradeдефектов, обосновать включение в программу методов повышения выявляемое&trade-, таких как дублирование контроля независимыми операторами, комплексное применение методов НК и методик контроля.
Раздел 4.2 содержит порядок и пример практического применения методики для оптимизации программы работ по неразрушающему контролю и проведению экспертизы промышленной безопасности сосудов, работающих под давлением, установленных на объектах газопромыслового управления (ГПУ) ООО «Газпром добыча Оренбург» с целью продления сроков службы. Применение методики показало, что при использовании рекомендованных НТД и включенных в действующую версию программы методов и объемов НК требуемая выявляемость дефектов СКРН в сварных швах не обеспечивается, поэтому программа технического диагностирования в части проведения НК сварных швов обечаек, днищ и основных технологических штуцеров нуждается в доработке.
По разработанной методике выполнена оптимизация программы и повторная оценка выявляемое&trade-. Это позволило повысить выявляемость дефектов в сварных швах до требуемого уровня. Интегральная оценка эффективности оптимизированной программы показывает снижение риска отказа рассматриваемой единицы оборудования на 48%.
Методика обоснования выбора состава и методов диагностирования внедрена в ОАО «Техдиагностика» с начала 2011 года. Выполненная при этом оценка выявляемое&tradeдефектов оборудования ООО «Газпром добыча Оренбург» методами, включенными в действующие программы диагностирования, показала недостаточную выявляемость внутренних дефектов сварных швов. Соответствующие разделы программ были доработаны, доработанные программы диагностирования согласованы с руководством ООО «Газпром добыча Оренбург», утверждены и введены в действие. Сравнение количественного распределения видов дефектов выявленных при использовании новых программ технического диагностирования с распределением видов дефектов прошлых лет показало увеличение относительного числа внутренних дефектов сварных швов с 18% до 30%. Принимая во внимание неизменность технологического процесса, т. е. действующих на оборудование нагрузок и воздействий, наблюдаемый рост количества дефектов одного из видов подтверждает эффективность применения новых программ и методов диагностирования.
Результаты применения в 2009 — 2011 годах информационной системы ККДР, представленные в разделе 4.3, показывают постепенное снижение относительного числа недостатков, выявляемых при проведении контроля качества, т. е. повышение достоверности и качества контроля и, одновременно с этим, постепенное снижение частоты проведения проверок за счет роста показателей надежности специалистов.
Расчет экономической эффективности представленных в настоящем исследовании разработок и технических решений повышения выявляемое&tradeдефектов показывает, что эффективность применения методов повышения выявляемое&tradeи методики обоснования выбора состава и методов программы диагностирования составляет 7,85 млн. рублей.
ЗАКЛЮЧЕНИЕ
.
По результатам анализа причин снижения безотказности, выявляемое&tradeдефектов и эффективности диагностирования оборудования ДСГ показано: причинами отказов и аварий при эксплуатации оборудования служат дефекты его узлов и элементовдля обеспечения вероятности отказа менее допустимого уровня необходимо выявлять дефекты с вероятностью более требуемойпричинами недостаточной выявляемое&tradeдефектов служат отрицательное влияние человеческого фактора, недостатки методик, ограниченные возможности приборов, накопление и разброс значений характеристик дефектовследствием накопления и недостаточной выявляемое&tradeдефектов является снижение эффективности диагностирования, переоценка несущей способности, запасов прочности, срока (ресурса) безопасной эксплуатации, уровня безотказности и безопасности и недооценка вероятности отказа эксплуатируемого оборудования.
Обоснованы и разработаны: математическая модель обоснования экспериментальной оценки значений вероятности выявления дефектовэкспериментальные модели оборудования ДСГ в виде совокупности экспериментальных образцов-моделей его узлов и элементов, технические требования и задания их УК в экспериментемодели и способы закладки в экспериментальные образцы дефектов наиболее встречающихся в элементах оборудованиямодель образцового метода оценки и повышения выявляемое&tradeдефектов применяемыми методами НК и других показателей достоверности результатов реализации программы диагностированиятехнические решения по документированию и формализации процессов выбора и настройки параметров УК, позволяющие снизить вероятность ошибки оператора (дефектоскописта) и повысить значения вероятности выявления дефектовпоказатели, критерии, алгоритм и информационная система обоснования и реализации контроля качества диагностических работ, позволяющие снизить отрицательное влияние человеческого фактора на показатель вероятности выявления дефектов, повысить коэффициент надёжности специалистов НК и обеспечить мотивацию повышения навыков специалистов НК с низким коэффициентов надёжностиметодический подход определения значений требуемого уровня вероятности выявления дефектов по узлам и элементам оборудования для наиболее встречающихся в них дефектов с минимальными, подлежащими определению параметрамиалгоритм выбора методов программы диагностирования и оценки соответствия критериальным значениям вероятности выявления дефектов программы диагностирования элементов оборудования с применением их экспериментальных образцов-моделейстандарт предприятия СТО-ЭПБ.И-177 «Методика обоснования выбора состава и методов программы диагностирования оборудования добычи сероводородсодержащих газа и нефти по критерию требуемой вероятности выявления дефектов», позволяющий применить в практике диагностирования оборудования ДСГ результаты диссертационного исследования.
По результатам выполненных экспериментов установлены: значения, факторы и закономерности изменения показателя выявляемое&trade- - вероятности выявления по видам/типам дефектов наиболее встречающихся в узлах и элементах оборудованиязависимости значений вероятности выявления дефектов от стажа (опыта) работы дефектоскопистовнаиболее значимые отклонения (ошибки) допускаемые дефектоскопистами в параметрах УК.
Результаты разработок внедрены в производство, обоснованы новые программы диагностирования, по которым выполнено диагностирование 499 единиц оборудования ДСГ предприятия ООО «Газпром добыча Оренбург». По результатам диагностирования выявлено 43 дефекта браковочного уровня.
По результата внедрения разработок в 2010 году за счёт предупреждения возможных отказов, внеплановых остановок и простоев оборудования получен положительный экономический эффект 7,85 млн. рублей.
Список литературы
- Митрофанов A.B. Методы управления состоянием технологического оборудования по критериям вероятности и риска отказа. М.: Недра, 2007. -380 с.
- ГОСТ Р 51 901.1−2002. Управление надежностью. Анализ риска технологических систем. М.: Стандартинформ, 2005. — 46 с.
- Конституция Российской Федерации. М.: Маркетинг, 2001. — 39 с.
- Об охране окружающей среды: федеральный закон РФ от 10.01.2002 № 7-ФЗ // Собрание законодательства РФ. 2002. — N 2.
- О защите населения и территорий от чрезвычайных ситуаций природного и техногенного характера: федеральный закон РФ от 21.12.1994 № 68-ФЗ // Собрание законодательства РФ. 1994. — N 35.
- О пожарной безопасности: федеральный закон РФ от 21.12.1994 № 69-ФЗ // Собрание законодательства РФ. 1994. — N 35.
- О промышленной безопасности: федеральный закон РФ от 21.07.1997 № 116-ФЗ // Собрание законодательства РФ. 1997. — N 30.
- О техническом регулировании: федеральный закон РФ от 27.12.2002 № 184-ФЗ // Собрание законодательства РФ. 2002. — N 52 (ч. 1).
- Об обязательном социальном страховании от несчастных случаев на производстве и профессиональных заболеваний: федеральный закон от 24.07.1998 Ы125-ФЗ // Собрание законодательства РФ. 1998. -N31.
- Гражданский кодекс Российской Федерации. Часть первая: федеральный закон РФ от 30.11.1994Ы 51-ФЗ (в ред. от 03.01.2006 N 6-ФЗ) // Собрание законодательства РФ. 1994. — N 32.
- СТО Газпром 2−3.5−032−2005. Положение по организации и проведению контроля за соблюдением требований промышленной безопасности и обеспечением работоспособности объектов единой системы газоснабжения ОАО «Газпром». М.: ООО «ИРЦ Газпром», 2005. — 15 с.
- СТО Газпром 2−2.3−491−2010. Техническое диагностирование сосудов, работающих под давлением на объектах ОАО «Газпром». М.: ООО «ИРЦ Газпром», 2010. 167 с.
- Р Газпром 2−2.3−398−2009. Методика проведения экспертизы промышленной безопасности аппаратов воздушного охлаждения газа на КС, ДКС, КС ПХГ, СОГ ОАО «Газпром». М.: ООО «ИРЦ Газпром», — 2009. — 57 с.
- Р Газпром 2−2.3−322−2009. Рекомендации по ультразвуковому контролю качества сварных соединений газопроводов и дефектных участков, отремонтированных сваркой (наплавкой). М.: ООО «ИРЦ Газпром», 2009.
- СТО Газпром 2−2.3−184−2007. Методика по расчету и обоснованию коэффициентов запаса прочности и устойчивости магистральных газопроводов на стадии эксплуатации и технического обслуживания. М.: ООО «ИРЦ Газпром», 2007.-21 с.
- СТО Газпром 2−2.3−095−2007. Методические указания по диагностическому обследованию линейной части магистральных газопроводов. М.: ООО «ИРЦ Газпром», 2007. — 75 с.
- СТО Газпром 2−2.3−112−2007. Методические указания по оценке работоспособности участков магистральных газопроводов с коррозионными дефек174тами. M.: ООО «ИРЦ Газпром», 2007. — 39 с.
- СТО Газпром 2−2.4−083−2006. Инструкция по неразрушающим методам контроля качества сварных соединений при строительстве и ремонте промысловых и магистральных газопроводов. М.: ООО «ИРЦ Газпром», 2006.
- ГОСТ 27.002−89. Надежность в технике. Основные понятия. Термины и определения. М.: Издательство стандартов, 1990. — 39 с.
- РД 03−418−01. Методические указания по проведению анализа риска опасных производственных объектов. М.: НТЦ «Промышленная безопасность», 2001. — 17 с.
- Безопасность России. Правовые, социально-экономические и научно-технические аспекты. Анализ рисков и управление безопасностью (Методические рекомендации). Рук. авт. кол-ва Н. А. Махутов, К. Б. Пуликовский, С. К. Шойгу. М.: МГФ «Знание», 2008. — 672 с.
- ГОСТ Р 12.3.047−98. Система стандартов безопасности труда. Пожарная безопасность технологических процессов. Общие требования. Методы контроля. М.: Издательство стандартов, 1998. 77 с.
- Гетман А.Ф., Козин Ю. Н. Неразрушающий контроль и безопасность эксплуатации сосудов и трубопроводов давления. М.: Энергоатомиздат, 1997. -288 с.
- РД 04−355−00. Методические рекомендации по организации производственного контроля за соблюдением требований промышленной безопасности на опасных производственных объектах. М.: НПО ОБТ, 2001. — 28 с.
- Положение о диагностировании технологического оборудования и трубопроводов газонефтедобывающих и перерабатывающих предприятий ОАО «Газпром». Согласовано Госгортехнадзором России письмом № 10−13/910 от 05 декабря 2000 г.
- Положение о диагностировании технологического оборудования и трубопроводов предприятия «Оренбурггазпром», подверженных воздействию серо-водородсодержащих сред. Согласовано Госгортехнадзором России письмом № 10−12/275 от 28.05.1998 г.
- PISC (Programme for Inspection of Steel Components) The PISC III Programme. PISC III Report No. 1, OECD-CEC, 1989.175
- H.H. Коновалов. Нормирование дефектов и достоверность неразру-шающего контроля сварных соединений. M.: НТЦ «Промышленная безопас-ноть», 2004. — 132 с.
- РД 03−421. Методические указания по проведению диагностирования технического состояния и определению остаточного срока службы сосудов и аппаратов. M.: НТЦ «Промышленная безопасноть», 2001. — 131 с.
- Волченко В.Н. Вероятность и достоверность оценки качества металлопродукции. М.: Металлургия, 1979. — 88 с.
- S. Crutzen, M. Certo, Ph. Dombert, R. Murgatroyd. Summary of the PISC Parametric Studies on the Effect of Defect Characteristics (EDC). PISC III Report No.8, OECD-CEC, 1989.
- M. В. Розина, Г. А. Трофимова. О способах задания нормативных требований к качеству продукции при УЗК в различных отраслях российской промышленности // В мире неразрушающего контроля. 2010. — № 4(50). — С. 2427.
- Гурвич А.К. Пути повышения надёжности НК объектов повышенной опасности // В мире неразрушающего контроля. 2005. — № 2 (28). — С. 28−29.
- Махутов H.A., Митрофанов A.B., Барышов С. Н. Научное обоснование методов повышения безопасности и ресурса оборудования добычи и переработки Н28-содержащих сред. // Химическое и нефтегазовое машиностроение. -2008.-№ 9.-С. 36−42.
- Барышов С.Н. Оценка поврежденности, несущей способности и продление ресурса технологического оборудования. Модели. Критерии. Методы. -М.: Недра, 2007.-287 с.
- Экспериментальное исследование характеристик трещиностойкости материала крышки. Результаты испытаний. РАН, ИМАШ, М., 2006. Отчетные материалы. Науч. руководитель Н. А. Махутов, исполнитель М. М. Гаденин.
- Применение показателей достоверности для валидации методик нераз-рушающего контроля / Дымкин Г. Я., Коншина В. Н., Нокеманн К., Тиллак Г. Р. // Дефектоскопия. 2000. — № 3. — С. 75−84.
- Неразрушающий контроль. В 5 кн. Кн. 1: Общие вопросы. Контроль проникающими веществами: Практ. пособие / А. К. Гурвич, И. Н. Ермолов, С.Г. Сажин- Под ред. В. В. Сухорукова. М.: Высш.шк., 1992. — 242 с.
- Работоспособность и неразрушающий контроль сварных соединений с дефектами / Шахматов В. М., Ерофеев В. В, Коваленко В. В. — Челябинск: ЦНТИ, 2000. 227 с.
- Технические средства диагностирования. Справочник. Под общей редакцией чл.-корр. АНН СССР В. В. Клюева. М.: Машиностроение, 1989. -672 с.
- Гафаров H.A., Гончаров A.A., Кушнаренко В. М. Определение характеристик надежности и технического состояния оборудования сероводородсодер-жащих нефтегазовых месторождений. М.: Недра, 2001. — 239 е.: ил.
- Безопасность России. Правовые, социально-экономические и научно-технические аспекты. Человеческий фактор в проблемах безопасности. / Рук. авт. кол-ва H.A. Махутов. М.: МГФ «Знание», 2008. — 688 с.177
- Петрин C.B., Петрина JT.C. Об учете человеческого фактора при анализе безопасности опасных производственных объектов // Безопасность труда в промышленности. 2011. — № 2. — С. 11−15.
- Ермолов И.Н. Дифракционно временной метод контроля // В мире не-разрушающего контроля. — 2001. — № 2 (12). С. 7−11.
- ГОСТ 18 353–79. Контроль неразрушающий. Классификация видов и методов. M.: Издательство стандартов, 1980. — 40 с.
- Приборы для неразрушающего контроля материалов и изделий. Справочник. 1, 2 книги / A.C. Боровиков, И. С. Вайншток, В. И. Горбунов, и др. М.: Машиностроение, 1976.
- Ланчаков Г. А., Зорин Е. Е., Степаненко А. И. Работоспособность трубопроводов: В 3-х ч. М.: Недра, 2003. — Ч. 3. Диагностика и прогнозирование ресурса. — 291 е.: ил.
- ПНАЭ Г-7−016−89. Унифицированные методики контроля основных материалов (полуфабрикатов), сварных соединений и наплавки оборудования и трубопроводов АЭУ. Визуальный и измерительный контроль. М., 1990. — 4 с.
- Визуальный и измерительный контроль / В. В. Клюев, Ф. Р. Соснин, В. Ф. Мужицкий, А. И. Маслов, A.A. Кеткович, Ю. А. Глазков. М., 1998.
- РД 03−606−03. Инстукция по визуальному и измерительному контролю. М.: НТЦ «Промышленная безопасность», 2003. — 92 с.
- ГОСТ 23 479–79. Контроль неразрушающий. Методы оптического вида. Общие требования. М.: Издательство стандартов, 1979. — 13 с.
- Визуальный и измерительный контроль. Учебное пособие для предварительной подготовки по неразрушающему контролю специалистов. «СертиНК» ФГУ НУЦ «Сварка и контроль». М., 2006 г.
- Dietmar F.W. Henning. Визуальный контроль как метод неразрушающего контроля // В мире неразрушающего контроля. 2001. — № 3 (13).
- В.В. Шлейзман, H.H. Песчанская. Использование интерферометриче178ского метода измерения величины и скорости перемещений для неразрушающе-го контроля материала. Физика твердого тела, 2007, том 49, вып.7.
- Плетнев C.B. Марков А. П. " Волоконно-оптические методы и средства дефектоскопии". СПб.: Лита, 2001.
- Неразрушающий контроль. Россия. 1990 2000 гг.: Справочник /
- B.В. Клюев, Ф. Р. Соснин, C.B. Румянцев и др.- Под ред. В. В. Клюева. М.: Машиностроение, 2001. 616 е.
- Приборы и технические средства контроля сварных соединений газопроводов: Справочное пособие / В. В. Салюков, Е. М. Вышемирский, A.B. Ши-пилов, С. П. Алексашин, В. И. Федорич. М.: ООО «ИРЦ Газпром», 2007. — 344 с.
- ГОСТ 14 782–86. Контроль неразрушающий. Соединения сварные. Методы ультразвуковые. М.: Издательство стандартов, 1986. — 40 с.
- Химченко Н.В., Бобров В. А. Неразрушающий контроль в химическом и нефтяном машиностроении. М.: Машиностроение, 1978. 264 с.
- Самокрутов A.A., Шевалдыкин В. Г. (ООО «АКС»), Бобров В.Т., Алехин
- C.Г., Козлов В. Н. (ЗАО НИИИН МНПО «Спектр»). ЭМА преобразователи для ультразвуковых измерений // В мире неразрушающего контроля. — 2008. — № 2 (40).-С. 22−25.
- Сясько В.А. Новейшие тенденции в области разработки фазированных антенных решеток // В мире неразрушающего контроля. 2009. — № 4 (46). -С.48−49.
- ГОСТ 18 442–80. Контроль неразрушающий. Капиллярные методы. Общие требования. -М.: Издательство стандратов, 1980. 39 с.
- Сайфутдинов С.М. Капиллярный контроль: история и современность.
- Неразрушающий контроль. Справочник в 7 томах под общей редакцией В. В. Клюева. Том 2 (книга 1 Контроль герметичности, книга 2 — Вихретоковый контроль). — М.: Машиностроение, 2003.
- Герасимов В.Г., Клюев В. В., Шатерников В. Е. Методы и приборы электромагнитного контроля промышленных изделий.
- СТБ ЕН 1711-ПР1. Государственный стандарт республики Беларусь (перевод стандарта EN 1711:2000, IDT) Контроль неразрушающий сварных соединений. Контроль вихретоковый посредством анализа сигнала на комплексной плоскости.
- РД-13−03−2006. Методические рекомендации о порядке проведения вихретокового контроля технических устройств и сооружений, применяемых и эксплуатируемых на опасных производственных объектах.
- РД РОСЭК-007−97. Машины грузоподъемные. Контроль вихретоковый. Основные положения.
- Инструкция по вихретоковому контролю линейной части магистральных газопроводов. РАО «Газмпром», Москва, 1997 г.
- Неразрушающий контроль. В 5 кн. Кн. 3 Электромагнитный контроль: практическое пособие/ В. Г. Герасимов, А. Д. Покровский, В. В. Сухорукое. Под ред. В. В. Сухорукова. М.: Высш. шк., 1992. — 312 с.
- Начальник Департамента вагонного хозяйства ОАО «РЖД» Г. С. Боярских. «Повысить эффективность неразрушающего контроля» // Транспортная газета «Евразия Вести». 2004. — № 1 (www.eav.ru).
- РД 32.150−2000 Вихретоковый метод неразрушающего контроля деталей вагонов Министерство путей сообщения Российской Федерации департамент пассажирских сообщений. М., 2000.
- Клюев В.В., Фидосенко Ю. К. Вихретоковый контроль: современное состояние и перспективы // В мире неразрушающего контроля. 2007. — № 2 (36).
- Вихретоковый контроль с использованием матрицы датчиков / С. Eddie, J. Bittner, В. Lepage // В мире неразрушающего контроля. 2007. — № 2 (36).
- ГОСТ 24 450–80. Контроль неразрушающий магнитный. Термины и определения.
- Неразрушающий контроль. Справочник в 7 томах под общей редакцией В. В. Клюева. Том 4 (книга 1- Акустическая тензометрия, книга 2 Магнитопо-рошковый метод контроля, книга 3 — Капиллярный контроль). — М.: Машиностроение, 2004.
- Неразрушающий контроль. Справочник в 7 томах под общей редакцией
- B.В. Клюева. Том 6 (книга 1- Магнитные методы контроля, книга 2 Оптический контроль, книга 3 — Радиоволновой контроль). — М.: Машиностроение, 2004.
- Магнитная диагностика газонефтепроводов A.A. Абакумов, A.A. Абакумов (мл.)
- Инструкция по диагностированию неразрушающим магнито-шумовым методом напряженно-деформированного состояния трубопроводов и сосудов давления. Челябинск, 1996.
- МДС 53−2.2004. Диагностирование стальных конструкций неразрушающим методом на основе явления магнитной анизотропии. М.: Димен-стест, 2005 г.
- Болтон У. Карманный справочник инженера-метролога М.: Издательский дом «Додэка-ХХ1», 2002. 384 с.
- Козлов М.Г. Метрология и стандартизация: Учебник М., СПб.: Изд-во «Петербургский ин-т печати», 2001. 372 с.
- Кузин Ф.А. Кандидатская диссертация. Методика написания, правила оформления и порядок защиты: Практическое пособие для аспирантов и соискателей ученой степени. 10-е изд., доп. — М.: Ось-89, 2008. — 224 с.
- Бернштейн М. Л. Структура деформированных металлов. М.: Металлургия, 1977 г.
- Усталостное разрушение высокопрочных болтов в строительных стальных конструкциях / Гладштейн Л. И., Кельберин Н. И., Мейтин В. И., Милиев-ский P.A. (ЦНИИПСК им. Мельникова) // Промышленное и гражданское строительство. 2007. — № 12.
- Оптико-структурный анализ фотонных кристаллов на основе опалов / Богомолов В. Н., Прокофьев A.B., Шелых А. И. // ФТТ. 1998. — т. 40, вып. 4.1. C. 648−650.
- Применение электронной спектроскопии в химии. Уч. пособие. Зайцев Б. Е., Страшнова С. Б., Ковальчукова O.B. М.: РУДН, 2003.
- Использование стандартных образцов для контроля качества результатов количественного анализа. М.: ФЦ ГСЭН МЗ РФ, 1998.181
- СП 3.3.2.561−96. САНИТАРНЫЕ ПРАВИЛА. Государственные испытания и регистрация новых медицинских иммунобиологических препаратов. Утв. приказом Госкомсанэпиднадзора РФ от 31.10.96 № 33.
- Ультразвуковой контроль толстостенных аустенитных сварных соединений с узкой разделкой в рамках проекта ИТЭР / Базулин Е. Г, Базулин А. Е., Коваль Д. А., Тихонов Д. С. (НПО «Эхо+») // В мире неразрушающего контроля. 2009. — № 4(46). — С. 30−35.
- ПБ 03−440−02. Правила аттестации персонала в области неразрушающего контроля. М.: НТЦ «Промышленная безопасность», 2002. — 26 с.
- EN 473:2000. Квалификация и сертификация персонала неразрушающего контроля.
- ASME. Boiler and Pressure Vessel Code an American National Standard, Section XI. ASME. N.-Y.: Ibid., 1995.
- Методика диагностирования технического состояния фонтанных арматур скважин, подверженных воздействию сероводородсодержащих сред на объектах газодобывающих предприятий ОАО «Газпром». М.: ОАО «Газпром», Госгортехнадзор России, 2000. — 42 с.
- Бабаджанов Л.С. О статусе образцов для метрологического обеспечения средств неразрушающего контроля // Измерительная техника. 2005. — № 6.
- Бабажданов Л.С., Бабаджанова М. Л. О поверочной схеме в области измерений геометрических параметров дефектов материалов и изделий средствами неразрушающего контроля // Контроль. Диагностика. -2009. -№ 8.
- Бабаджанов Л.С., Бабаджанова М. Л. Меры и образцы в области нераз182рушающего контроля. М.: Стандартинформ, 2007.
- РОСС RU. Г426.04ФФОО. Система добровольной сертификации образцов дефектов. -М.: ФГУП «ВНИИМС», 2007 г.
- Неразрушающий контроль и диагностика: Справочник / В. В. Клюев, Ф. Р. Соснин, В. Н. Филинов и др.- Под ред. В. В. Клюева. М.: Машиностроение, 1995.-488 с.
- ГОСТ 20 911–89. Техническая диагностика. Термины и определения.
- Лукьянов В.Ф. Технологическая наследственность как фактор надежности сварных соединений // Вестник ДГТУ. 2005. — № 3. — С. 388 — 399.
- Вероятностный риск-анализ конструкций технических систем / Лепи-хин A.M., Махутов H.A., Москвичев В. В., Черняев А. П. Новосибирск: Наука, 2003. — 174 с.
- Металл и оборудование для сероводородсодержащих нефтей и газов / Перепеличенко В. Ф., Рубенчик Ю. И., Щугорев В. Д., Гераськин В. И., Елфимов В. В. М.: Недра, 2001. — 359 с.
- В.Г. Щербинский. Как ультразвуковая дефектоскопия завоевала право на самостоятельность.
- И.Э. Власов, В. И. Иванов. Полезность многократного НК // Безопасность труда в промышленности. 2005. — № 12. — С. 50−53.
- ГОСТ Р 5725−1-2002 Точность (правильность и прецизионность) методов и результатов измерений. Часть 1. Основные положения и определения.
- ГОСТ Р 5725−2-2002 Точность (правильность и прецизионность) методов и результатов измерений. Часть 2. Основной метод определения повторяемости и воспроизводимости стандартного метода измерений
- ПНАЭ Г-7−014−89. Унифицированные методики контроля основных материалов (полуфабрикатов), сварных соединений и наплавки оборудования и трубопроводов АЭУ. Ультразвуковой контроль. Часть I. Контроль основных материалов полуфабрикатов). М., 1990. — 41 с.
- СТО 220 256−005−2005. Швы стыковых, угловых и тавровых сварных соединений сосудов и аппаратов, работающих под давлением. Методика ультразвукового контроля. М.: ОАО «НИИХИММАШ», 2005.
- ВСН 012−88. Строительство магистральных и промысловых трубопроводов. Контроль качества и приемка работ. Часть 1. М., 1988.
- ГОСТ 17 410–78. Контроль неразрушающий. Трубы металлические бесшовные цилиндрические. Методы ультразвуковой дефектоскопии. М.: Издательство стандартов, 1987.
- Тютерева JI.H. Контроль качества результатов анализа для подтверждения технической компетенции испытательной лаборатории // Безопасность труда в промышленности. 2009. — № 4. С. 13−18.
- ГОСТ Р 8.563−96. Методики выполнения измерений. М.: Издательство стандратов, 1996. — 39 с.
- Количественное описание неопределенности в аналитических измерениях. Руководство ЕВРАХИМ/СИТАК. Второе издание.
- Дворкин В.И., Болдырев И. В. Понятие неопределенности и его использование в лабораторной практике.
- ГОСТ Р 5725−4-2002 Точность (правильность и прецизионность) методов и результатов измерений. Часть 4. Основные методы определения правильности стандартного метода измерений.
- ISO/TS 21 748:2004 «Guidance for the use of repeatability, reproducibility and trueness estimates in measurement uncertainty estimation».
- Коробцов A.C. Методологические основы обеспечения качества систем машиностроения, включающие человеческий фактор (на примере сварных конструкций): Автореф. дис. д-ра техн. наук. М., 2007.
- Колемаев В.А., Калинина В. Н. Теория вероятностей и математическая статистика: Учебник для вузов. 2-е изд., перераб. и доп.- М.: ЮНИТИ-ДАНА, 2003.-352 с.
- Факторный анализ в геологии: Учебное пособие к лабораторным занятиям / А. И. Бахтин, Н. М. Низамутдинов, Н. М. Хасанова, Е. М. Нуриева. Казань, Казанский государственный университет, 2007 г.
- Методические указания по применению ультразвуковых дефектоско184пов. / Воронков В. А., Воронков И. В. М.: ООО «Акустические контрольные системы», 2007. — 90 с.
- Испытания и контроль качества материалов и конструкций: Учеб. пособие / В. М. Баранов, А. М. Карасевич, Г. А. Сарычев. — М.: Высш. школа, 2004. -688 с.
- Костюков А.Н. В XXI век с новыми подходами к эксплуатируемому оборудованию // Нефть России. — 2004. — № 9. — С. 35 — 36.
- Управление персоналом: Работник самый эффективный ресурс компании: Учебное пособие для вузов / Герчиков В. И. — М.: Инфра-М, 2008. — 282 с.
- ПБ 03−372−00. Правила аттестации и основные требования к лабораториям НК. М.: НТЦ «Промышленная безопасность», 2000. — 18 с.
- Митрофанов A.B., Вдовин A.A. Образцовый метод вероятностной оценки выявляемости дефектов оборудования добычи сероводородсодержащеш газа, конденсата, нефти // Автоматизация, телемеханизация и связь в нефтяной промышленности. 2011. — № 6. — С. 7−11.
- Нормативы трудоемкости на выполнение работ по технической диагностике. М.: ОАО «Газпром», 2004.
- Митрофанов A.B. Разработка методов предупреждения чрезвычайных ситуаций при эксплуатации технологического оборудования объектов добычи и переработки сероводородсодержащего газа: Дис. д-ра техн. наук: 05.26.02. -М., 2006 378 с.