Исследование и разработка метода автоматизированного назначения режимов обработки для токарных станков с ЧПУ на основе измерения термоЭДС зоны резания
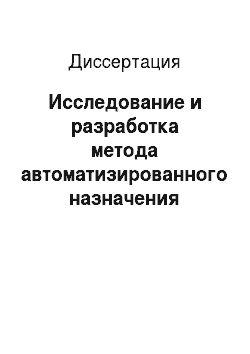
Машинное время, как известно, определяется скоростью резания, величиной подачи и глубиной резания. Глубина резания назначается в зависимости от квалитета детали и квалитета заготовки, т. е. определяется припуском на обработку и количеством переходов. Поэтому при подготовке УП для станков с ЧПУ стоит задача с учетом технических требований к детали, при известной глубине резания, известных… Читать ещё >
Содержание
- ГЛАВА. АНАЛИЗ МЕТОДОВ НАЗНАЧЕНИЯ РЕЖИМОВ РЕЗАНИЯ. ПОСТАНОВКА ЗАДАЧИ ИССЛЕДОВАНИЯ
- 1. 1. Алгоритм определения режимов резания для токарных станков с ЧПУ (на основе существующих методов)
- 1. 2. Проблемы автоматизированного выбора режимов резания для станков с ЧПУ
- 1. 2. 1. Анализ методов назначения параметров процесса резания
- 1. 2. 1. 1. Определение составляющих силы резания Рх, Ру, Р
- 1. 2. 1. 2. Определение допустимой скорости резания V
- 1. 2. 2. Причины расхождения действительного значения составляющих силы резания Р2, Ру, Рх от расчетного
- 1. 2. 3. Причины отклонения действительного периода стойкости инструмента от заданного
- 1. 2. 1. Анализ методов назначения параметров процесса резания
- 1. 3. Возможные пути решения задачи автоматизированного выбора режимов резания программным путем
- 1. 3. 1. Методы оценки свойств обрабатываемых и инструментальных материалов
- 1. 4. Постановка задачи исследования
- ГЛАВА. МЕТОДИКА ПРОВЕДЕНИЯ ЭКСПЕРИМЕНТАЛЬНЫХ ИССЛЕДОВАНИЙ
- 2. 1. Экспериментальная установка, инструментальное обеспечение
- 2. 2. Инструментальные материалы и обрабатываемые стали
- 2. 3. Методика определения режущих свойств твердосплавного инструмента
- 2. 4. Методика исследования контактных процессов при резании
- 2. 5. Методика измерения величины термоЭДС в паре инструмент — изделие
- ГЛАВА. ИССЛЕДОВАНИЕ СИГНАЛА ТЕРМОЭДС ЕСТЕСТВЕННОЙ ТЕРМОПАРЫ ИНСТРУМЕНТАЛЬНЫЙ — ОБРАБАТЫВАЕМЫЙ МАТЕРИАЛ КАК ДАТЧИКА ОБРАТНОЙ СВЯЗИ ИЗ ЗОНЫ РЕЗАНИЯ
- 3. 1. Физические основы термоЭДС, как датчика о свойствах контактируемых пар
- 3. 1. 1. Работа выхода электронов и ее связь со свойствами твердого сплава и стали
- 3. 1. 2. Модель работы выхода электронов из обрабатываемых и инструментальных материалов
- 3. 1. 3. Связь величины термоЭДС с геометрией инструмента
- 3. 2. Связь режущих свойств инструмента с величиной термоЭДС
- 3. 3. Способы и средства измерения величины термоЭДС
- 3. 3. 1. Обоснование «контрольных» режимов резания. Выбор величины скорости резания V, подачи Э и глубины резания
- 3. 3. 2. Анализ электрической цепи естественной термопары
- 3. 4. Разработка программного способа измерения величины термоЭДС
- 3. 1. Физические основы термоЭДС, как датчика о свойствах контактируемых пар
- ГЛАВА. РАЗРАБОТКА МЕТОДА АВТОМАТИЗИРОВАННОГО НАЗНАЧЕНИЯ РЕЖИМОВ РЕЗАНИЯ
- 4. 1. Разработка метода определения составляющих силы резания Р2, Ру, Рх с использованием величины термоЭДС
- 4. 1. 1. Механика процесса резания
- 4. 1. 2. Влияние теплофизических свойств инструментальных и обрабатываемых материалов на величины составляющих силы резания Pz, Ру, Рх
- 4. 1. 2. 1. Влияние изменения фазового состава внутри марочного состава твердого сплава на величины составляющих силы резания Рх, Ру, Р
- 4. 1. 3. Разработка метода определения составляющих силы резания Рх, Ру и Р2 на основе измерения термоЭДС зоны резания
- 4. 2. Исследование способа определения допустимой скорости резания на основе информации из зоны резания для условий токарной обработки на станках с ЧПУ
- 4. 3. Разработка алгоритма автоматизированного назначения режимов резания для токарных станков с ЧПУ
- 4. 1. Разработка метода определения составляющих силы резания Р2, Ру, Рх с использованием величины термоЭДС
Исследование и разработка метода автоматизированного назначения режимов обработки для токарных станков с ЧПУ на основе измерения термоЭДС зоны резания (реферат, курсовая, диплом, контрольная)
В современном машиностроении процессы обработки материалов резанием по своей производительности, экономичности, качеству и точности получаемых деталей преобладают над другими видами обработки. Поэтому эффективность процесса резания является основой высокопроизводительной и качественной эксплуатации станочного оборудования. Прежде всего, это касается работы автоматизированного станочного оборудования и, в частности, станков с ЧПУ.
Для обеспечения надежной и производительной работы металлорежущего оборудования в программном режиме (станок может функционировать автономно или в составе ГПС) среди прочих факторов при составлении управляющей программы (УП) большое значение имеют правильно выбранные режимы резания. При высокой степени автоматизации подготовки геометрической информации в современных отечественных микропроцессорных системах ЧПУ, технологическая информация, касающаяся выбора режимов резания, готовится «вручную». Для этого используются методики расчета, разработанные применительно к универсальным станкам. К настоящему времени прирост производительности станков с ЧПУ получен лишь за счет сокращения вспомогательного и организационно-технического времени, машинное же (основное) время обработки на этом оборудовании не сократилось.
Анализ работы автоматизированного станочного оборудования показывает, что имеются резервы повышения производительности и стабильности его работы за счет научно обоснованных норм назначения режимов резания, выбора режущего инструмента, внедрения систем диагностики процесса резания и т. д.
Вопросы надежности и стабильности автоматически выполняемого процесса резания в режиме расчетной производительности до сих пор остается полностью не разрешенной проблемой.
В ряде случаев для решения этой задачи идут на значительное (до 60−70%) снижение уровня режимов резания относительно нормативных [82] в предположении, что более низкие режимы резания обеспечат более стабильную работу инструмента и, в итоге, повысят общую производительность обработки. При этом при повышенном (заданном) периоде стойкости инструмента выявляется значительный статистический разброс значений стойкости — до.
200%. Следствием этого снижения является увеличение статистического разброса значений стойкости инструмента, недоиспользование инструмента и оборудования, что в совокупности отрицательно сказывается на технико-экономической эффективности этого высокоавтоматизированного оборудования.
Другим путем повышения производительности и надежности работы станков с ЧПУ может быть оснащение этого оборудования адаптивными системами управления процессом резания и его контроля. Большинство способов управления основано на научных положениях процесса резания, разработанных Н. Н. Зоревым, Т. Н. Лоладзе, Г. И. Грановским [70], а также на современных положениях физики процесса резания [84], [82], [34]. Несмотря на положительные результаты многих исследований, на практике способы технологической диагностики и управления процессом резания реализованы не в полной мере. Так режимы резания, обеспечивающие устойчивое стружкод-робление определяются исключительно экспериментальными методами и как следствие необходимостью создания многочисленных нормативов, требующих значительных затрат средств и времени [78].
Уже имеющаяся база нормативов также далека от совершенства. В серийном и массовом производстве в техпроцесс изготовления изделия, составленный на основе упомянутых нормативов, как правило, вносят существенные коррективы по выбору инструмента, режимов резания, программе для системы ЧПУ [97].
Использование указанных нормативов возможно, если оператор управляет работой одного станка с ЧПУ, когда имеется возможность корректировать рассчитанные режимы резания на основе визуального наблюдения, используя личный опыт работы, обеспечивая тем самым приемлемые величины стойкости инструмента, производительности, точности и качества обработки. При многостаночном обслуживании или при работе станков в составе ГПС физической возможности одновременного контроля за ходом процесса обработки на нескольких станках у него нет. В этом случае проблема надежности самого процесса резания становится одной из главных.
В последнее время для составления управляющих программ и в частности для расчета режимной части УП используют ЭВМ. В качестве математического аппарата используют методы, содержащие известные эмпирические зависимости между скоростью резания, стойкостью инструмента, величиной подачи и глубиной резания с добавлением поправочных коэффициентов, учитывающих условия обработки. Однако, рассчитанные по этим зависимостям технологические величины зачастую отличаются от тех, что имеют место непосредственно на станке.
В разработке новых поколений станочных систем ЧПУ доля автоматизированного контроля, диагностики и управления процессом резания возрастает. Отсюда разработка более точной модели описания процесса резания, применительно к станкам с ЧПУ, становится все более значимой. По мере увеличения степени автоматизации станков с ЧПУ идет перераспределение баланса времени между основным (машинным) и подготовительно-заключительным, вспомогательным временем и временем организационно-технического обслуживания.
Машинное время, как известно, определяется скоростью резания, величиной подачи и глубиной резания. Глубина резания назначается в зависимости от квалитета детали и квалитета заготовки, т. е. определяется припуском на обработку и количеством переходов. Поэтому при подготовке УП для станков с ЧПУ стоит задача с учетом технических требований к детали, при известной глубине резания, известных обрабатываемом и инструментальном материалах выбрать оптимальное значение величины допустимой подачи, обеспечивающей заданную точность и определить значение скорости резания, обеспечивающее заданную стойкость инструмента.
Поколение вновь создаваемых систем ЧПУ отечественного и зарубежного производства ориентировано на диалоговую автоматизированную подготовку управляющих программ непосредственно на рабочем месте [74]. Геометрическая информация в таких системах ЧПУ представлена набором подпрограмм различных видов обработки: продольного точения, поперечного точения, обработка фасок, канавок, скруглений, нарезания резьбы и т. п., из комбинации которых оператор формирует необходимую ему УП. В диалоговых системах ЧПУ предпринята попытка автоматизировать и процесс выбора режимов резания. Так в устройстве ЧПУ для токарной обработки «Fanuc System 3T-Model F» японской фирмы «Фанук» содержится алгоритм расчета режимов резания с результатами которого оператор либо соглашается, либо предлагает свои варианты. То есть окончательное решение о величине скорости резания и подачи (при бесспорном варианте выбора глубины резанияона определяется величиной припуска) принимает оператор на основе своего опыта. В алгоритме автоматизированного расчета режимов резания заложены эмпирические зависимости, которые, как указано в работах [84], [82], [34], [70], страдают серьезным недостатком — низкой надежностью определения заданных параметров.
В отечественных микропроцессорных системах ЧПУ для токарной обработки (2У22, 2Р22, НЦ-31) расчет режимов резания ведется вне станка, на стадии подготовки УП. В последнее время для этих целей используется опыт подготовки технологической информации на ЭВМ. Однако, сокращая время расчета, ЭВМ не решает основного вопроса — повышения надежности автоматически выполняемого процесса резания.
Под надежностью процесса резания следует понимать свойство этого процесса обеспечивать изготовление продукции в заданном объеме и с надлежащими точностью и качеством. При этом о надежности следует говорить только в определенном, наперед заданном периоде времени, т. е. времени, когда система (процесс резания) функционирует нормально.
Надежность процесса резания (как технологическая система) зависит от надежности составляющих эту систему элементов: станка, приспособлений, инструмента и заготовки в процессе их взаимодействия.
Как отмечается в работе [82] физические основы технологической надежности резания (надежности процесса резания) заключаются в нестационарном и случайном характере явлений, протекающих в обрабатываемом материале и режущем инструменте при обработке.
Следовательно, одним из определяющих факторов надежности автоматически выполняемого процесса резания являются свойства обрабатываемого и инструментального материалов и их взаимовлияние друг на друга в процессе обработки. Надежность процесса резания оценивается по стабильности результатов обработки (точность, производительность, качество обработанной поверхности) и надежности работы режущего инструмента, оцениваемой, в свою очередь, по действительному периоду стойкости.
Технологические характеристики процесса резания (скорость резания, подача, глубина резания), а также составляющие силы резания, призванные обеспечить эти критерии оценки в настоящее время могут определяться двумя методами [54], [79]: аналитическим или табличным способом расчета.
И в том и в другом случае определение режимов резания и составляющих силы резания осуществляется по математическим моделям с использованием ряда поправочных коэффициентов, учитывающих переменные факторы процесса обработки (свойства инструментального и обрабатываемого материалов, геометрию инструмента, наличие охлаждения и др.). Отличие между этими двумя методами состоит в том, что в первом случае расчет идет по математическим моделям, записанным в явном виде, во втором случае — в виде таблиц.
Не вдаваясь в анализ алгоритма назначения режимов резания (он будет приведен в главе 1) следует отметить, что существующие методы расчета учитывают переменные факторы процесса резания с помощью усредненных поправочных коэффициентов, следствием чего является значительный разброс расчетной и действительной стойкости инструмента, обеспечивающей надежность его работы, а также разброс составляющих силы резания, призванной обеспечивать точность обработки.
При определении режима резания по существующим математическим моделям установить связь между всеми переменными факторами, влияющими на процесс резания (вибрация, неоднородность инструментального и обрабатываемого материалов, охлаждение и т. д.) не представляется возможным. Расчет режимов резания по этим математическим моделям, в этом случае, приемлем лишь для условий, в которых они были получены [11], [67].
В работе [99] подчеркивается, что «используемые в настоящее время справочные данные для выбора скорости резания, подачи и глубины резания, взятые из различных источников для идентичных условий резания, сильно отличаются друг от друга и не позволяют обоснованно назначать способ обработки.» .
Попытки уточнить эмпирические зависимости «скорость резаниястойкость инструмента» путем применения более сложных математических выражений, учитывающих большее количество факторов, не разрешили проблему выбора оптимальных режимов резания расчетным путем [15], [33].
В данной работе обосновывается возможность разработки и реализации способа автоматизированной подготовки технологической информации применительно к токарным станкам с ЧПУ. В качестве основы информационного обеспечения создаваемого способа принята величина термоэлектродвижущей силы (термоЭДС) естественной термопары инструмент-изделие, фиксируемая в условиях «контрольных» режимов резания (У=100м/мин- 5=0,1 мм/об- ≠1мм). Отличительной особенностью использования величины термоЭДС является то, что в данном методе она используется не как традиционная информация о температуре в зоне резания, а как датчик о свойствах контактируемых пар инструмент — изделие. Все результаты исследований относятся к условиям чистового и получистового точения углеродистых конструкционных и легированных сталей твердосплавными инструментами марок ВК, ТК, ТТК и ТН.
Работа состоит из введения, четырех глав, общих выводов, библиографического списка использованной литературы и приложения. В порядке расположения глав в диссертационной работе решались следующие задачи.
Выводы по работе:
1. Установлено, что основными факторами, влияющими на стабильность автоматически выполняемого процесса резания, являются изменяющиеся свойства обрабатываемых и инструментальных материалов, которые в условиях чистового и получистового точения, в ряде случаев, оказывают значительное влияние на составляющие силы резания и величину периода стойкости инструмента.
Экспериментально показано, что при обработке ряда углеродистых конструкционных и легированных сталей твердосплавными режущими инструментами различных марок свойства расхождение расчетных и измеренных значений достигает, в ряде случаев, по составляющим силы резания 200%, по величине периода стойкости инструмента 300%.
2. Показано, что изменяющиеся свойства контактируемых материалов можно учитывать величиной термоэлектродвижущей силы, измеренной в одинаковых условиях резания (условиях «контрольных» режимов резания: /=100 м/мин- 8=0,1 мм/об- 1=1 мм).
3. Разработан метод измерения величины термоЭДС, позволяющий устранить влияние на полезный сигнал значений вторичных термоЭДС, а также учесть изоляцию одной из ветвей цепи естественной термопары с помощью масляных пленок подшипников станка.
4. Разработано устройство измерения величины термоЭДС с использованием амплитудного выпрямителя (пик-детектора).
5. Разработаны математические модели по расчету составляющих силы резания и допустимой скорости резания, в которых величина термоЭДС является интегральным критерием оценки свойств материала инструмента и заготовки.
6. Разработаны и исследованы методы определения параметров процесса резания на основе предложенных математических моделей. Экспериментально подтверждено, что расхождение теоретических и экспериментальных данных по составляющим силы резания не превышает 20%, по периоду стойкости инструмента не более 15%.
Список литературы
- А. с № 1 009 609 СССР. Способ определения режущих свойств твердосплавных инструментов / А. Л. Плотников, Е. В. Дудкин (СССР). Бюл. № 13, 1983.
- А. с. № 347 629 СССР. Способ определения режущих способностей инструментов / Ю. М. Соломенцев (СССР). Бюл. № 18, 1971.
- А. с. № 418 278 СССР. Способ определения допустимой скорости резания при обработке металла / М. М. Ламм, Ю. Ф. Коваль (СССР). Бюл. № 6, 1972.
- A.c. № 549 269 СССР. Устройство для измерения температуры резания методом естественной термопары / А. Л. Плотников, Е. В. Дудкин (СССР).-Бюл. № 9, 1977.
- Аваков А. А. Физические основы теории стойкости режущих инструментов. М.: Машгиз, 1960. — 380с.
- Агеев О. В. Повышение точности обработки сложнопрофильных деталей на металлорежущих станках путем разработки алгоритмов управления формообразованием для распределенных систем ЧПУ. Автореф. дис. канд. техн. наук. Уфа, 1998. — 24с.
- Адаптивное управление станками / Под ред. Б. С. Балакшина. М.: Машиностроение, 1973.-688с.
- Архипова А. В., Куделькин Г. П. Определение обезуглероживания серебрянки из быстрорежущей стали методом термоЭДС // Заводская лаборатория. 1966. — № 6. — С.719−720.
- Бабич М. М. Неоднородность твердых сплавов по содержанию углерода и ее устранение. Киев: Наукова думка, 1975. — 174с.
- Басов В. В. Тарирование естественных термопар // Станки и инструменты. 1972. — № 2. — С.14−16.
- Башков В. М., Кацев П. Г. Испытания режущего инструмента на стойкость. М.: Машиностроение, 1985. — 136с.
- Биргер И. А., Шорр Б. Ф., Иосилевич Г. Б. Расчет на прочность деталей машин: Справочник. 4-е изд., перераб. и доп. — М.: Машиностроение, 1993.-640с.
- Бобров В. Ф. Основы теории резания металлов. М.: Машиностроение, 1975.-344с.
- Бобровский В. А. Влияние термоэлектрических токов на износ инструмента при резании металла // Электрические явления при трении и резании металлов. М.: Наука, 1969. — С.7−26.
- Брахман Л. А., Батищев Д. И., Гильман А. М. Оптимизация режимов обработки на металлорежущих станках. М.: Машиностроение, 1972. -140с.
- Васильеве. В. Измерение температуры резания и эмиссионные свойства стали // Физика и химия обработки материалов. 1987. — № 5. -С.141−145.
- Васильеве. В. ТермоЭДС при резании как характеристика качества твердосплавных пластинок // Станки и инструменты. 1976. — № 5. -С.27−28.
- Виноградов А. А., Муковоз Ю. А., Аносов Ю. Л. Измерение термоЭДС при резании металлов //
- Вульф А. М. Резание металлов. 2-е изд., перераб. и доп. — Л.: Машиностроение (Ленингр. отд-ние), 1973. -496с.
- Глебов С. Ф. Теория наивыгоднейшего резания металлов. М.-Л.: Гос-машметиздат, 1933. -с.
- Грановский Г. И., Грановский В. Г. Резание металлов. М.: Высшая школа, 1985.-304с.
- Грешников В. А., Дробот Ю. В. Акустическая эмиссия. М.: Изд-во стандартов, 1976. -272с.
- Гуляев А. П. Металловедение: Учебник для вузов. 6-е изд., перераб. и доп. — М.: Металлургия, 1986. — 544с.
- Гутников В. С. Интегральная электроника в измерительных устройствах. -Л.: Энергия, 1980. -280с.
- Даниелян А. М. Теплота и износ инструментов в процессе резания металлов. М.: Машгиз, 1954.
- Даниелян А. М., Бобровский В. А. Температура при резании металлов и способы ее измерения. М.: Машгиз, 1952. — 276с.
- Дудкин Е. В., Плотников А. Л. Автоматизированная коррекция режимов обработки на токарных станках с ЧПУ. Тезисы докладов. Л., 1990.
- Дудкин Е. В., Плотникова. Л. К вопросу оценки качества твердосплавного инструмента // Проблемы производства и применения твердых сплавов. Тезисы докладов Всесоюзной конференции. М., 1981.
- Дудкин Е. В., Плотникова. Л. Метод косвенной оценки износостойкости твердосплавных инструментов // Надежность и контроль качества. -1984. № 6. — С.35−41.
- Дудкин М. Е. Исследование контактных явлений и механизмов износа твердосплавного инструмента при обработке конструкционных сталей. Автореф. дис. канд техн. наук. Тбилиси, 1981. — 20с.
- Епифанов Г. И. Физика твердого тела: Учебн. пособие для втузов. 2-е изд., перераб. и доп. — М.: Высшая школа, 1977. — 288с.
- Зорев Н. Н. Вопросы механики процесса резания металлов. М.: Маш-гиз, 1956. -367с.
- Игумнов Б. Н. Расчет оптимальных режимов обработки для станков и автоматических линий. М.: Машиностроение, 1974. -200с.
- Кабалдин Ю. Г. Энергетические принципы управления процессами механообработки в автоматизированном производстве // Вестник машиностроения. 1993. — № 1. — С.37−42.
- Кацев П. Г. Статистические методы исследования режущего инструмента. М.: Машиностроение, 1968. — 156с.
- Кибальченко А. В. Применение метода акустической эмиссии в условиях гибких производственных систем. Технология металлообрабатывающего производства. — Обзорная информация, серия 6. — М.: ВНИИТЭМР, в.1, 1986, с. 57.
- Клушин М. И. Резание металлов. М.: Машгиз, 1958. -454с.
- Коваль Ю. Ф., Вихтинский А. А. Определение режущей способности пластинок из твердого сплава. В кн. Металлорежущий и контрольно-измерительный инструмент, вып. З, М.: НИИМАШ, 1972. -С.4−6.
- Козочкин М. П., Смирнов В. В. Экспериментальное исследование акустических явлений при трении твердых тел // Трение и износ. 1983. Т.4. № 6. С.991−994.
- Козочкин М. П., Смирнов В. В., Сулейманов И. У. Система диагностики состояния инструмента на станках с ЧПУ // Информационный листок МГЦНТИ № 166, 1983.
- Креймер Г. С., Ваховская М. Р. О влиянии содержания углерода в твердых сплавах карбид вольфрама-кобальт на их механические свойства // Порошковая металлургия. -1965. № 6. — С.24−30.
- Кузнецов В. Д. Физика твердого тела: В 3-х т. Томск: Красное Знамя, 1944.-Т.З.-258с.
- Куфарев Г. Л., Окенов К. Б., Говорухин В. А. Стружкообразование и качество обработанной поверхности при несвободном резании. Фрунзе: Мектеп, 1970. — 169с.
- Ладакина Е. П., Николаева Г. С. К вопросу об электрической устойчивости твердых сплавов. В сб. Электрические явления при трении, резании и смазке твердых тел. М.: Наука, 1973. — С.95−102.
- Лоладзе Т. Н. Износ режущего инструмента. М.: Машгиз, 1958. — 358с.
- Макаров А. Д. Износ и стойкость режущих инструментов. М.: Машиностроение, 1966. -264с.
- Марочник сталей и сплавов / В. Г. Сорокин, А. В. Волосникова, С. А. Вяткин и др.- Под общ. ред. В. Г. Сорокина. М.: Машиностроение, 1989. — 640с.
- Металлообрабатывающий твердосплавный инструмент: Справочник / В. С. Самойлов, Э. Ф. Эйхманс и др. М.: Машиностроение, 1988. -368с.
- Мирзаев А. А. Научные основы создания системы автоматизированного определения обрабатываемости металлов резанием. Автореф. дис. докт. техн. наук. Киев, 1995. — 40с.
- Надаи И. Пластичность и разрушение твердых тел. М.: Изд-во Иностр. лит., 1954. — 864с.
- Обработка металлов резанием: Справочник технолога / А. А. Панов, В. В. Аникин, Н. Г. Бойм и др.- Под ред. А. А. Панова. М.: Машиностроение, 1988.-736с.
- Общемашиностроительные нормативы режимов резания. Справочник:
- В 2-х т / А. Д. Локтев, И. Ф. Гущин, В. А. Батуев и др.- Под ред.
- A. Д. Локтева. М.: Машиностроение, 1991. — Т.1. — 640с.
- Общемашиностроительные нормативы времени и режимов резания для нормирования работ, выполняемых на универсальных и многоцелевых станках с ЧПУ: Нормативы режимов резания / ЦБНТ. М.: Экономика, 1990. -474с.
- Палей С. М. Контроль состояния режущего инструмента по ЭДС резания // СТИН. 1996. — № 10. — С.21−25.
- B.В.Еремеев. № 97 116 947/20- Заявлено 14.10.97- Опубл. Бюл. № 29, 1998.
- Пат. № 2 117 557 Россия, С1 В 23 В 25/06. Способ съема термоЭДС естественной термопары инструмент деталь / А. Л. Плотников. -№ 97 100 992/02- Заявлено 21.01.97- Опубл. Бюл. № 23, 1998.
- Плотников А. Л. Исследование физической природы связи ЭДС естественной термопары с режущими свойствами твердосплавных инструментов и использование величины термоЭДС для управления процессом резания. Автореф. дис. канд. техн. наук. Тбилиси, 1982. -20с.
- Плотников А. Л. Особенности контактных при обработке стали твердым сплавом с различным фазовым составом // Физические процессы при резании металлов: Межвуз. сб. науч. тр. / ВолгГТУ. Волгоград, 1995.
- Плотников А. Л., Диперштейн М. Б., Еремеев В. В. Обеспечение расчетной точности обработки на токарных станках с ЧПУ // Автоматизация технологических процессов в машиностроении: Межвуз. сб. науч. тр. / ВолгГТУ. Волгоград, 1997. — С.5−10.
- Плотникова. Л., Еремеев В. В. Автоматизированный способ определения допустимой скорости резания на токарных станках с ЧПУ //Автоматизация технологических процессов в машиностроении: Межвуз. сб. науч. тр. / ВолгГТУ. Волгоград, 1997. — 4.1. — С.96−102.
- Плотников А. Л., Еремеев В. В. Анализ причин различной обрабатываемости сталей и метод её оперативного учёта // Физические процессы при резании металлов: Межвуз. сб. науч. тр. / ИжГТУ. Волгоград-Ижевск, 1997. — С.5−9.
- Плотников А. Л., Еремеев В. В. Проблемы автоматизированного выбора режимов резания на станках с ЧПУ и пути их решения // Физические процессы при резании металлов: Межвуз. сб. науч. тр. / ВолгГТУ. Волгоград, 1997. -С.57−61.
- Подураев В. Н. Автоматически регулируемые и комбинированные процессы резания. М.: Машиностроение, 1977. -304с.
- Полетика М. Ф. Контактные нагрузки на режущих поверхностях инструмента. М.: Машиностроение, 1969. — 150с.
- Прогрессивные режущие инструменты и режимы резания металлов: Справочник / В. И. Баранчиков, А. В. Жаринов, Н. Д. Юдина, А. И. Садыхов- Под общ. ред. В. И. Баранчикова. М.: Машиностроение, 1990. -400с.
- Развитие науки о резании металлов / В. С. Бобров, Г. И. Грановский, Н. Н. Зорев и др. М.: Машиностроение, 1967. -416с.
- Савицкий Е. М., Буров М. В. Электрические и эмиссионные свойства сплавов. М.: Наука, 1978. — 294с.
- Семко М. Ф. Теплота резания, стойкость инструмента. Харьков: Харьковское кн. изд-во, 1937.
- Сосонкин В. Л. Взгляд на предстоящую эволюцию устройств ЧПУ // Станки и инструмент. 1992. — № 9. — С.27−32.
- Сосонкин В. Л. Микропроцессорные системы числового программногоуправления станками. М.: Машиностроение, 1985. — 290с.
- Сосонкин В. Л., Мартинов Г. М. Концепция систем ЧПУ типа PCNC с открытой архитектурой // СТИН. 1998. — № 5. — С.7−12.
- Сплавы твердые порошковые и керамика. Изделия для режущего инструмента. Метод определения режущих свойств: ОСТ 48−99−84
- Справочник инструментальщика / И. А. Ординарцев, Г. В. Филиппов,
- A. Н. Шевченко и др.- Под общ. ред. И. А. Ординарцева. Л.: Машиностроение (Ленингр. отд-ние), 1987. — 846с.
- Справочник по технологии резания материалов: В 2-х кн. / Под ред. Г. Шпура, Т. Штеферле- Пер. с нем. под ред. Ю. М. Соломенцева. М.: Машиностроение, 1985. — Кн. 1. -616с.
- Справочник технолога-машиностроителя: В 2-х т / В. Б. Борисов, Е. И. Борисов, В. Н. Васильев и др.- Под ред. А. Г. Косиловой, Р. К. Мещерякова. 4-е изд., перераб. и доп. — М.: Машиностроение, 1985. -Т.2. — 656с.
- Справочник технолога-машиностроителя: В 2-х т / В. Н. Гриднев,
- B. В. Досчатов, В. С. Замалин и др.- Под ред. А. Н. Малова. 3-е изд., перераб. — М.: Машиностроение, 1972. -Т.2. -568с.
- Справочник химика. М.:Госхимиздат, 1963. — Т.1. — 866с.
- Старков В. К. Обработка резанием. Управление стабильностью и качеством в автоматизированном производстве. М.- Машиностроение, 1989. -296с.
- Талантов Н. В. Исследование контактных процессов, тепловых явлений и износа инструмента. Автореф. дис. д-ра техн. наук. Ижевск, 1970. -38с.
- Талантов Н. В. Физические основы процесса резания, изнашивания и разрушения инструмента. М.: Машиностроение, 1992. — 240с.
- Талантов Н. В., Мансуров И. И. Контактные напряжения на передней поверхности инструмента // Совершенствование процессов резания и повышение точности металлорежущих станков / ИжМИ. Ижевск, 1969. — Вып. III. — С.23−39.
- Талантов Н. В., Черемушников Н. П., Уткин Е. Ф. Метод фиксации следов контактных процессов на передней поверхности инструментов // Вопросы оптимального резания металлов: Межвуз. сб. науч. тр. Уфа, 1976.-С.113−117.
- Ташлицкий Н. И. Влияние механических свойств и теплопроводности сталей на их обрабатываемость. М.: Машгиз, 1952. — 86с.
- Теплофизические свойства веществ: Справочник / Под ред. Н. Б. Варгафтика. М. — Л.:Госэнергоиздат, 1956. — 367с.
- Трент Е. М. Резание металлов / Пер. с англ. М.: Машиностроение, 1980.-264с.
- Третьяков В. И. Основы металловедения и технологии производства спеченных твердых сплавов. 2-е изд., перераб. и доп. — М.: Металлургия, 1976. -527с.
- Туманов В. И. Свойства сплавов системы карбид-вольфрам-кобальт. -М.: Металлургиздат, 1971. 96с.
- Функе В. Ф., ШуршаковА. Н. и др. Влияние состава и термической обработки сплавов NC-Co на их структуру и свойства // Твердые сплавы, ВНИИТС. № 4. — М.: Металлургия, 1962. — С. 184−196.
- Хейзель У. Методы контроля инструмента и обрабатываемой детали в гибком автоматизированном производстве // Станки и инструмент. -1985.-№ 2.-С.27−29.
- Цоцхадзе В. В. Температура при резании металлов. Тбилиси, Изд-во Грузинского политехнического института, 1965.
- Чапорова И. Н., Чернявский К. С. Структура спеченных твердых сплавов. М.: Металлургия, 1975. — 247с.
- Черемушников Н. П. Исследование процесса пластического деформирования и его неустойчивости при резании металлов. Автореф. дис. канд. техн. наук. Саратов, 1980. — 22с.
- Шарин Ю. С. Технологическое обеспечение станков с ЧПУ. М.: Машиностроение, 1986. — 176с.
- Юферов В. М., Кузнецов М. П. Экспресс-анализ бессемеровской стали методом измерения термоэлектродвижущей силы // Заводская лаборатория. 1956. — № 4. — С.397−400.
- Dudkin Е., PlotnikovA., Diperstain М. Non-distructive phase composition and cutting properties control of cemented Carbide tool inserts. Prossiding of World Congress «Poweder Metallurgy 98, V4 P69−74 the 18−22 October, Granada Spain, 1998.
- Khair A. W. Study of Acoustic Emission during Laboratory Fatigue Tests on Jennessee Sandstone И Ebenda. P.57−86.
- Suzuki H., Hayashi K. // Transections of the Japan institute of Metals. -1966.-№ 7. p. 199−207.
- Suzuki H., Kubota H. // Planseeberichte fur Pulvermetallurg. 1966.-№ 14. — p.96−109.
- Trigger К. Transactions of the ASME, February, 1948, p.91−98.
- Uehara Kunio, Kanda Yuichi. Identification of Chip Formation Mechanism through Acoustic Emission Measurement //Annals of the CJRP. V.33. No1. 1984. P.71−74.