Оперативное управление процессом пиролиза углеводородов
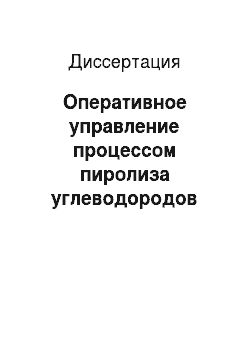
В этих условиях важной и актуальной становится проблема разработки автоматизированной системы оперативного управления на основе непрерывной диагностики (мониторинга) технологического процесса и режимов работы оборудования, способной по результатам контроля объекта выявить возникновение неисправности или нарушения режима, а главное выдавать рекомендации по их устранению оператору до явного… Читать ещё >
Содержание
- ГЛАВА 1. ОПИСАНИЕ ПРЕДМЕТНОЙ ОБЛАСТИ
- 1. 1. ОПИСАНИЕ ТЕХНОЛОГИЧЕСКОГО ПРОЦЕССА ПИРОЛИЗА
- 1. 1. 1. Общие сведения
- 1. 1. 2. Цех пиролиза и первичного фракционирования пирогаза
- 1. 1. 3. Особенности процесса пиролиза как объекта оперативного управления
- 1. 2. ИНФОРМАЦИОННОЕ ОБЕСПЕЧЕНИЕ СИСТЕМЫ УПРАВЛЕНИЯ
- 1. 3. СИСТЕМЫ ОПЕРАТИВНОГО УПРАВЛЕНИЯ (СОУ)
- 1. 3. 1. Положение СОУ в иерархии автоматизированных систем управления
- 1. 3. 2. Классификация методов диагностики
- 1. 4. ВЫВОДЫ. ПОСТАНОВКА ЗАДАЧИ ИССЛЕДОВАНИЯ
- 1. 1. ОПИСАНИЕ ТЕХНОЛОГИЧЕСКОГО ПРОЦЕССА ПИРОЛИЗА
- ГЛАВА 2. СТРУКТУРА СИСТЕМЫ ОПЕРАТИВНОГО УПРАВЛЕНИЯ
- 2. 1. ТИПОВЫЕ СТРУКТУРЫ СОУ
- 2. 2. СТРУКТУРА ДИАГНОСТИЧЕСКОЙ МОДЕЛИ
- 2. 3. СТРУКТУРА ФРЕЙМОВ ДИАГНОСТИЧЕСКОЙ МОДЕЛИ
- 2. 4. СТРУКТУРА МОДУЛЯ МОНИТОРИНГА И ДИАГНОСТИКИ
- ВЫВОДЫ К ГЛАВЕ 2
- ГЛАВА 3. РАЗРАБОТКА АЛГОРИТМА РАБОТЫ СОУ
- 3. 1. ОБНАРУЖЕНИЕ НЕШТАТНЫХ СИТУАЦИЙ
- 3. 1. 1. Метод главных компонент (МГК)
- 3. 1. 2. Обнаружение нарушений с использованием МГК
- 3. 1. 3. Идентификация модели МГК процесса пиролиза
- 3. 2. ИДЕНТИФИКЦИЯ НЕШТАТНЫХ СИТУАЦИЙ В ПРОЦЕССЕ ПИРОЛИЗА
- 3. 2. 1. Методика идентификации нештатных ситуаций
- 3. 2. 2. Сбор экспертной информации
- 3. 2. 3. Фреймы диагностической модели процесса пиролиза
- 3. 3. АЛГОРИТМЫ РАБОТЫ СИСТЕМЫ
- 3. 3. 1. Алгоритм вычисления главных компонент
- 3. 3. 2. Критерии определения близости ситуаций
- 3. 3. 3. Блок схемы алгоритма работы системы
- 3. 1. ОБНАРУЖЕНИЕ НЕШТАТНЫХ СИТУАЦИЙ
- 4. 1. ФОРМИРОВАНИЕ МАССИВА ДАННЫХ ДЛЯ ТЕСТИРОВАНИЯ
- 4. 1. 1. Оценка качества массивов данных
- 4. 1. 2. Выбор совокупности нештатных ситуаций для моделирования
- 4. 2. ИМИТАЦИОННОЕ МОДЕЛИРОВАНИЕ РАБОТЫ СИСТЕМЫ
- 4. 2. 1. Синтез программы имитационного моделирования
- 4. 2. 2. Исследование работы системы при нормальном ходе процесса
- 4. 2. 3. Исследование работы системы при наличии нештатных ситуаций
- 4. 3. ПРОГРАММНАЯ РЕАЛИЗАЦИЯ АЛГОРИТМА РАБОТЫ СИСТЕМЫ
Оперативное управление процессом пиролиза углеводородов (реферат, курсовая, диплом, контрольная)
Развитие производства мономеров (этилен, бензол, пропилен) стимулируется интенсивным ростом российского рынка полимерных материалов. Весь производимый в РФ этилен потребляется внутренним рынком. Увеличение мощностей по выпуску этилена на сегодняшний день является наиболее удачным и перспективным направлением развития нефтехимии. В 2006 году ОАО «Нижнекамскнефтехим» произвел 480 тыс. тонн этилена, в текущем году планируется произвести 520 тыс. тонн этилена, на 2008 год запланировано уже 600 тыс. тонн, а к 2012 году 1 600 тыс. тонн в год.
Эта продукция является базовой для создания других нефтехимических производств. Увеличение объема производства этилена и полимеров дает сырьевую основу для выпуска продукции с высокой добавленной стоимостью (этиленгликоль, этилбен-зол, полиэтилентерефталат, поливинилхлорид, полиэтилен, смолы и др.), что позволит производить широкий спектр промышленных товаров и товаров народного потребления (трубы, стройматериалы, упаковки и т. д.).
Этилен впервые был получен немецким химиком Иоганном Бехером в 1680 году. Начало практическому использованию этих соединений положили классические исследования A.M. Бутлерова и его учеников в области непредельных соединений и особенно созданная Бутлеровым теория химического строения. В 1860 году он установил структурную формулу этилена. Этилен представляет собой бесцветный газ, обладающий слабым, едва ощутимым запахом. Этилен горюч, образует с воздухом взрывоопасные смеси. Уже при температурах выше 350 0 С этилен частично разлагается на метан и ацетилен. При температуре около 1200 0 С диссоциирует главным образом на ацетилен и водород. Этилен получают пирогенетическим разложением многих природных соединений, содержащих органические вещества. Процесс пиролиза для получения этилена осуществляется в печах различного устройства пропусканием газообразных углеводородов или их паров в присутствии катализаторов при температуре 760−780° С. Обычно используются печи трубчатого типа.
Несмотря на длительность периода эксплуатации технологии получения этилена, интерес к этому процессу не исчезает. Исследователи крупной корейской нефтяной компании SK Corp и государственного химического института разработали крекинг процесс отделения этилена и пропилена при более низкой температуре. Новая технология, которая называется Advanced Catalytic Olefin (АОС), обеспечивает температуру меньше чем 700 °C. Производительность оптимизированных процессов возрастает на 30%, а потребление энергии уменьшается на 20%. Работы, связанные с усовершенствованием процесса, продолжаются, а значит можно считать актуальным привлечение современных методов к решению вопросов управления процессом.
Потенциальная опасность технологического процесса получения этилена в широком смысле заложена в самом производстве, которое характеризуется применением токсичных, пожарои взрывоопасных продуктов, высоких температур (до 830−855°С), открытого пламени, большой массы пирогаза, закалочного масла и пиробензина, пара высокого давления 14,0 МПа (140 кгс/см2) с температурой 520 °C, высокой скоростью протекания реакции пиролиза порядка 0,3−0,4 секунды, что в совокупности предъявляет повышенные требования к системе управления производством.
Таким образом, рост мощностей производства этилена и связанных с этим повышение требований к безопасной эксплуатации, повышение требований к качеству выпускаемой продукции, необходимость снижения затрат энергоресурсов, увеличение потребности в этилене как сырье для последующей переработки требуют развития и совершенствования систем управления.
Управление процессом получения этилена в основном базируется на поддержании регламентных показателей работы печей пиролиза, теплового и материального балансов установки. Технологический процесс получения этилена характеризуются повышенной энергоемкостью и подвержен несанкционированным возмущениям, связанным с суточными и сезонными изменениями температуры, энергетическими потерями в магистралях и оборудовании, а также с изменением состава исходного сырья — прямогонного бензина и накоплением кокса в трубопроводах печи и испарительных поверхностях закалочно-испарительных аппаратов.
Сложность технологической схемы, основного технологического оборудования и взаимосвязь параметров управления приводят к возникновению множества неожиданных, нештатных ситуаций, способных привести к развитию аварийных состояний на процессе. Отсутствие модели поведения процесса в нештатных ситуациях, а также наличие различного рода возмущений приводит к необходимости непрерывного мониторинга процесса. Управление процессом в этих условиях осуществляется эмпирическими методами, т. е. на основании опыта технологов и операторов. Следует отметить, что различные нештатные ситуации, часто имеют сходные условия проявления. Условия информационной перегрузки способствуют несвоевременному обнаружению предпосылок аварий обслуживающим персоналом и причиною ошибочных решений по управлению процессом. Действие системы защиты в таких условиях сводятся в основном к отключению оборудования и переводу процесса в безопасный режим, что ведет к экономическим потерям предприятия.
В этих условиях важной и актуальной становится проблема разработки автоматизированной системы оперативного управления на основе непрерывной диагностики (мониторинга) технологического процесса и режимов работы оборудования, способной по результатам контроля объекта выявить возникновение неисправности или нарушения режима, а главное выдавать рекомендации по их устранению оператору до явного проявления нештатной ситуации. Такая система базируется на комбинации принципов ситуационного управления и диагностики. Диагностическая модель системы строится на основе эмпирической и теоретической информации о процессе, при этом используются теоретические знания о предметной области и экспертные знания о конкретном технологическом процессе. В законченном варианте система управления и диагностики представляет собой подсистему АСУ ТП и реализует функции управления в нештатных ситуациях. В иерархии управления процессом она занимает промежуточное положение между системой регулирования и системой защиты, логично дополняя или предваряя действия последней.
В рамках диссертационной работы поставлены и решены следующие задачи:
1. исследован процесс пиролиза, выделены наиболее опасные участки, оценена степень его автоматизации;
2. осуществлен сбор, обработка и анализ экспертной информации, проведено ранжирование возможных нештатных ситуаций по степени опасности и скорости развития;
3. обосновано применение комбинированного метода диагностики: мониторинг процесса предложено проводить на базе статистического анализа с использованием метода главных компонент (МГК), а определение причин нарушений — на базе экспертной информации;
4. сформирована диагностическая модель процесса и проведена ее идентификация;
5. разработан алгоритм работы системы, осуществляющий:
— непрерывный мониторинг процесса методом «движущегося» МГК по двум моделям, различающимся периодом адаптации;
— определение причины нарушения — по двухуровневой фреймово-продукционной модели;
6. проведена проверка работоспособности системы методом имитационного моделирования.
Диссертационная работа состоит из введения, четырех глав, выводов по работе, списка литературы и приложений.
151 ВЫВОДЫ.
1. Процесс пиролиза углеводородов является потенциально опасным процессом как во взрыво-, так и в пожарном отношении и может сопровождаться достаточно большим числом возможных нештатных ситуаций. В то же время срабатывание аппаратуры ПАЗ влечет остановы процесса и сопровождается материальными потерями.
2. Разработана система оперативного управления (СОУ) процессом пиролиза углеводородов, использующая комбинированный метод диагностики состояния процесса: обнаружение нарушений в ходе процесса проводится непрерывным мониторингом его состояния с использованием метода главных компонент (МГК). Идентификация обнаруженных нештатных ситуаций производится на базе экспертной системы реального времени.
3. Разработана структура диагностической модели, положенной в основу функционирования СОУ. Модель включает два блока. Первый блок, используемый при мониторинге, включает совокупность главных компонент и пороговые значения статистик Q и Т, по которым и производится мониторинг.
Второй блок, используемый для определения причины возникновения нештатной ситуации, представляет собой двухуровневую фреймово-продукционную структуру. Во фреймах верхнего уровня сгруппированы знания о группах нештатных ситуаций, которые могут возникнуть в структурной единице, выделяемой при декомпозиции контролируемого объекта. В дочерних фреймах сгруппированы знания о конкретных ситуациях, имеющих общие определяющие симптомы, но вызванных различными причинами. В пределах фрейма нештатные ситуации описываются нечеткими продукционными правилами.
4. Разработан алгоритм работы системы для обнаружения и идентификации нештатных ситуаций. Т.к. на процессе пиролиза на фоне возможного естественного дрейфа параметров могут возникать нештатные ситуации со значительно различающимися скоростями развития, то была разработана модификация метода «движущегося» МГК, использующая две модели МГК. Одна из них строится по окну, ширина которого ориентирована на быстроразвивающиеся ситуации. А вторая модель строится на более широком окне и не адаптируется в течение времени, сравнимого со скоростью нарастания медленно развивающихся ситуаций.
Список литературы
- Venkatasubramanian V., Rengaswamy R., Yin K.,. Kavuri S.N. A review of process fault detection and diagnosis. Part 1. Quantitative model-based methods // Computers and Chemical Engineering, 2003. V. 27. PP. 293−311.
- Gertler, J., Monajemy, R. Generating directional residuals with dynamic parity relations // Automatica, 1995. V.31. PP. 627−635.
- Basseville, M., Nikiforov, I. V. Detection of abrupt changes theory and application (Information and System Sciences Series).- N.Y.: Prentice Hall,. 1993. 275pp.
- Yang Q., Model-based and data driven fault diagnosis methods with applications to process monitoring. Thesis for the degree of Doctor of Philosophy, Case Western Reserve University, 2004, p.203.
- Chang С. Т., Hwang J. I. Simplification techniques for EKF computations in fault diagnosis suboptimal gains.// Chemical Engineering Science, 1998. V.53 № 22, PP.3853−3862.
- Venkatasubramanian V., Rengaswamy R., Yin K.,. Kavuri S.N. A review of process fault detection and diagnosis Part II: Quantitative model-based methods // Computers and Chemical Engineering, 2003. V. 27. PP. 313−326.
- Chang Ch., Yu Ch. On-line fault diagnosis using the signed directed graph // Ind.Eng.Chem.Res. 1990, v.29. N7. P. 1290−1299.
- Александрова H.A.,. Русинов JI. A Использование метода сигнальных направленных графов для верификации экспертных знаний// Ред. журн. «Прикладная химия. РАН». СПб, 2002, 14с. Деп. ВИНИТИ 19.02.03 N 332 В2003
- Kramer М. A., Palowitch В. L. A rule based approach to fault diagnosis using the signed directed graph.// American Inst, of Chem. Engineers J., 1987. V.33 № 7. PP. 1067−1078.
- Tarifa E., Scenna N. Fault diagnosis, directed graphs, and fuzzy logic// Computers and Chem. Eng, 1997. V.21, P.649−654.
- Venkatasubramanian V., Rengaswamy R., Yin K.,. Kavuri S. N. A review of process fault detection and diagnosis Part III: Quantitative model-based methods // Computers and Chemical Engineering, 2003. V. 27. PP. 327−346.
- Isermann R. Supervision, fault-detection and fault-diagnosis methods an introduction// Control Eng. Practice, 1997. V. 5. N 5. PP. 639−652.
- Змитрович А.И. Интеллектуальные информационные системы. Мн.: НТО «Тетра Системе», 1997. — 368 с.
- Малышев Н.Г., Берштейн JI.C., Боженюк А. В. Нечеткие модели для экспертных систем. М.:Энергоатомиздат, 1991, 136с.
- Асаи К., Ватада Д., Иваи С. и др. Прикладные нечеткие системы: Пер. с япон. -М.: Мир, 1993. 368с
- Kramer М.А. Fault diagnosis and computer-aided diagnostic advisors// AIChE, 1996. V.92, N312. P.12−24.
- Мешалкин В.П. Экспертные системы в химической технологии. Основы теории, опыт разработки и применение. М.: Химия, 1995. — 368 с
- Ramesh T.S. Plant monitor an on-line advisory syste for monitoring polyethylene plants //AIChE Symposium Serres. 1996, v.92, № 312, p. 247−251.
- Qian Yn., Li X., Jiang Y, Wen Y. An expert system for real-time fault diagnosis of complex chemical process// Expert systems with applications, 2003. v.24. p. 425 432.
- Химмельблау Д. Обнаружение и диагностика неполадоек в химических и нефтехимических процессах.- Д.: Химия, 1983, 352с.
- Левин Б.Р. Теоретические основы статистической радиотехники М.: Советское радио, 1975. Т.2. 392с.
- MacGregor J. F., Kourti Т. Statistical process control of multivariate processes.// Contr. Eng. Practice, 1995. V.3 № 3 P 403 414.
- Venkatasubramanian V., Chan K. A neural network methodology for process fault diagnosis.// J. of American Institute of Chemical Engineers, 1989. V.35. № 12. P. 1993−2002.
- Ungar L. H., Powell B. A., Kamens S. N. Adaptive networks for fault diagnosis and process control.// Computers and Chemical Engineering, 1990. V.14 № 4−5. P.561−572.
- Hoskins J. C., Kaliyur К. M., Himmelblau D. M. Fault diagnosis in complex chemical plants using artificial neural networks. // J. of American Institute of Chemical Engineers, 1991. V.37. № 1. P.137−141.
- Venkatasubramanian V., McAvoy T.J. Special issue on neural network applications in chemical engineering. // Computers and Chemical Engineering, 1992. V.16. № 4. P. R5-R6.
- Fan, J. Y., Nikolaou, M., White, R. E. An approach to fault diagnosis of chemical processes via neural networks.// J. of American Institute of Chemical Engineers, 1993. V.39. № 1. P.82−88.
- Becerikli Y. On three intelligent systems: dynamic neural, fuzzy and wanelet networks for training trajectory //Neural comput. & Applic. 2004. V.13 P.339−351.
- Leonard J.A., Kramer M.A. Radial basis function networks for classifying process faults // IEEE Control Syst, 1991. V. 11. P.31 -38.
- Kavuri S. N., Venkatasubramanian V. Representing bounded fault classes using neural networks with ellipsoidal functions.// Computers and Chemical Eng, 1993. V.17 № 2. P. 139−163.
- Application of wavelets and neural networks to diagnostic system development. I. Feature extraction./ B. H. Chen, X. Z. Wang, S. H. Yang, C. Mcgreavy // Computers and Chemical Eng., 1999. V. 23. № 7. P. 899−906.
- Bakshi B.R., Stephanopoulos G. Wave-net: a multiresolution, hierarchical neural network with localized learning. //J. of American Institute of Chemical Engineers, 1993. V.39. № 1.P.57−81.
- Diagnosis of multiple simultaneous fault via hierarchical artificial neural networks./ K. Watanabe, S. Hirota, L. Iloa, D.M.Himmelblau // J. of American Institute of Chemical Engineers, 1994. V. 40. № 5. P. 839−848.
- J.F. MacGregor and T. Kourti. Statistical process control of multivariate processes.// Control Engineering Practice, 1995. V.3 № 3. P.403 ^114.
- Martens H., Naes T. Multivariate calibration N.Y. John Willey& Sons, 1998, 419p.p.
- Эсбенсен К. Анализ многомерных данных: Сокр. пер. с англ./ Под ред. О. Родионовой .- М.: Издательство ИПХФ РАН, 2005. 252 с.
- Lee С. Fault detection of batch processes using multiway kernel principal component analysis.// Computers & Chem. Eng. 2004.V.28. P.1837−1847.
- Huang Te-Ming, Kecman V., Kopriva I. Kernel Based Algorithms for Mining Huge Data Sets Berlin: Springer Verlag, 2006 Series Studies in Computational Intelligence, Vol 17. 260 pp.
- Yang Q., Model-based and data driven fault diagnosis methods with applications to process monitoring. Thesis for the degree of PhD. Case: Western Reserve University, 2004, 203 pp.
- McNabb C.A. MIMO Control Performance Monitoring Based on Subspace Projections. Dissertation for the degree of PhD. AUSTIN: University of Texas, 2002. 203 pp.
- MBPCA Application for Fault Detection in NMOS Fabrication / S. Lachman-Shalem, N. Haimovitch, E.N. Shauly, D.R. Lewin // IEEE Trans, on Semiconductor Manufacturing, 2001
- Narasimhan S., Gudi R. Monitoring and fault diagnosis // Proc. CEP Workshop on Multivariate Data Analysis Techniques & Applications. 2005 July 22 P. 13−26.
- Luo R., Misra M., Himmelblau D.V. Sensor fault detection via multiscale analysis and dynamic PCA.// Ind.Eng.Chem.Res., 1999. V.38. P. 1489−1495.
- Contribution Plots for Fault Identification Based on the Dissimilarity of Process Data / M. Kano, S. Hasebe, I. Hashimoto etc.// AIChE Annual Meeting, Los Angeles, CA, 2000 P. 255 -271.
- Li Y., Xie Z., Zhou D.H. Fault detection and isolation based on abnormal sub-regions using improved PCA // J. of chem.eng.of Japan, 2004. V.37. № 4. P.514−522.
- Yoon S., MacGregor J.F. Fault diagnosis with multivariate statistical models using steady state fault signatures. Part I: J. Proc. Cont., 2001. V.ll. P. 387-^00.
- Comparison of statistical process monitoring methods: application to the Eastman challenge problem / M. Kano, H. Ohno, S. Hasebe, I. Hashimoto // Computers. Chem. Eng., 2000.V. 24. P. 175−181.
- Змитрович А.И. Интеллектуальные информационные системы. -Мн.: НТО «ТетраСистемс», 1997.-368с.
- Черноруцкий И.Г. Методы принятия решений. СПб.: БХВ-Петербург, 2005. -416с.
- Искусственный интеллект. В 3-х кн. Кн. 2. Модели и методы: Справочник / Под ред. Поспелова Д.А.-М.: Радио и связь, 1990. 220с.
- Кравченко Т. К., Перминов Г. И. Экспертная система принятия решений- Учеб. метод. Пособ. М.: ВШЭ, 1998. — 209 с.
- Гаврилова Т.А. Извлечение и структуризация знаний для экспертных систем. -М.: Радио и связь, 1992. 235с.
- Батыршин И.З. Методы представления и обработки информации в нечетких системах // Новости искусственного интеллекта, 1996. № 1 С.9−65.
- Гаврилова Т.В. Состояние и перспективы разработки баз знаний // Новости искусственного интеллекта, 1996. № 2. С.5−44.
- Малышев Н.Г., Берштейн JI.C., Боженюк А. В. Нечеткие модели для экспертных систем. М.:Энергоатомиздат, 1991, 136с.
- Асаи К., Ватада Д., Иван С. и др. Прикладные нечеткие системы: М.: Мир, 1993. 368с
- Yeung D.S., Tsang Е.С. Weighted fuzzy production rules // Fuzzy sets and systems, 1997. Vol. 88. P. 299−313.
- Yeung D.S., Tsang E.C. Improved fuzzy knowledge representation and rule evaluation using fuzzy Petry nets and degree of subsethood // Int. J. of intelligent systems, 1994. Vol.9. P.1083−1100.
- Рудакова И.В., Куркина B.B., Русинов JI.А. Алгоритмическое обеспечение систем диагностики для режима обнаружения нештатных ситуаций на контролируемом объекте // Прикладная химия. РАН, 2003, 17с. Деп. ВИНИТИ 06.02.03 N 237-В2003
- Turksen I.B., Zhong Z. An approximate analogical reasoning schema based on similarity measures and interval valued fuzzy sets // Fuzzy sets and systems, 1990. Vol.34. P. 323−346.
- Chen S. M. A new approach to handling fuzzy decision-making problems // IEEE trans. On systems, man and cybernetics, 1988. Vol. SMC-18, N6. P.1012 1016.
- Русинов JI.A., Куркина B.B., Панов Г. Д. Диагностика и управление периодическими технологическими процессами на примере биосинтеза лимонной кислоты //Автоматизация и современные технологии, 1997. № 5. С.11−16.
- Коростиль Ю.М. Некоторые особенности решения задач диагностирования сложных технологических объектов. Киев.:, 1994. — 54 с
- Esbensen К.Н. Multivariate data analysis in practice — Oslo: САМО, 2000. 598p.
- Русинов JI.A. Автоматизация аналитических систем определения состава и количества веществ Л.: Химия, 1984. 160с.
- Ицкович Э.Л., Соркин Л. Р. Оперативное управление непрерывным производством: задачи, методы, модели.- М.: Наука, 1988. 160 с.
- Нестерова A. MES системы управления производством. // http://www.asutp.ru/go/?id=600 358&url=www.rtsoft.ru
- Гараева Ю., Загидуллин Р., СунКай Цин. Российские MES-системы
- Гершберг А. Ф. и др. Концептуальные основы информационной интеграции АСУ ТП нефтеперерабатывающего предприятия./ А. Ф. Гершберг, А.А. Муса-ев., А. А. Нозик, Ю. М. Шерстюк СПб.: Альянс-строй, 2003, 128с
- Venkatasubramanian V. Abnormal Events Management in Complex Process Plants: Challenges and Opportunities in Intelligent Supervisory Control
- Уотерман Д. Руководство по экспертным системам: Пер. с англ. М.: Мир, 1989. 388 с.
- Козин и.о. Элементы теории выборами принятия решений- Обнинск: Ин-т1. Аатомной энергетики, 1991 74 с
- Степанов А.В. «Производство этилена» Киев, издательство У’Наукова думка" 1973г
- Угрюмов П.Г., Авербух А. Я. «Органический синтез в промышленно-сти"Москва, издательство У’ПросвещениеУ 1964г.
- Р. М. Афлятунов, A. JI. Фокин, В. Г. Харазов Робастная стабилизация теплового режима работы трубчатых нагревательных печей нефтеперерабатывающей промышленности // Автоматизация в промышленности. 2004.№ 7.С.25−28.
- Афлятунов P.M., Рудакова И. В., Русинов J1.A. Диагностическая модель для системы диагностики состояния процесса пиролиза //Изв. /Орловский ГТУ, 2006.,№ 1(2) С. 15−20.
- Русинов JI.A., Рудакова И. В., Куркина В. В., Афлятунов P.M. Диагностика состояния непрерывных технологических процессов// Мехатроника, автоматизация, управление 2006, № 7 (Приложение) С. 18−21.
- Афлятунов P.M., Рудакова И. В. Совершенствование системы управления производством этилена ОАО «НИЖНЕКАМСКНЕФТЕХИМ» // 7-й Международный форум. Топливно-энергетический комплекс России. Сборник материалов. 2007.-С.20−23.i ou