Детали машин
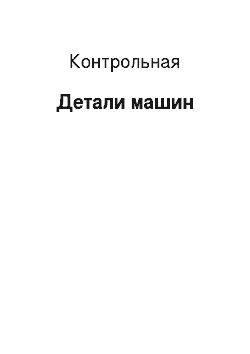
В соответствии с нормами Ростехнадзора по максимальному рабочему усилию ветви каната Fмах и минимальному коэффициенту использования (коэффициенту запаса прочности) каната zр определяется разрывное усилие F0, кН: Кратность полиспаста определяют при одинарном барабане по числу ветвей каната, на которых подвешен груз. При сдвоенном барабане кратность полиспаста равна половине числа ветвей каната… Читать ещё >
Детали машин (реферат, курсовая, диплом, контрольная)
СОДЕРЖАНИЕ Введение
1. Выбор грузового крюка
2. Выбор гибкого тягового органа
3. Определение основных параметров барабанов и блоков
4. Выбор электродвигателя
5. Подбор цилиндрического зубчатого редуктора
6. Расчет тихоходного вала редуктора
7. Подбор подшипников качения тихоходного вала редуктора
8. Выбор муфты тихоходного вала редуктора
9. Выбор и проверка шпонок
10. Выбор тормоза Список использованных источников ВВЕДЕНИЕ Перечень элементов:
1. Электродвигатель; 2. Муфта; 3. Тормоз; 4. Редуктор; 5. Муфта; 6. Барабан; 7. Полиспаст.
Номер схемы полиспаста — 3.
Исходные данные приведены из индивидуального задания:
1. Масса поднимаемого груза, mгр = 2,50 т.
2. Скорость подъема груза, vгр = 63 м/мин.
3. Высота подъема груза, Н = 22,6 м.
4. Группа режима рабочего механизма по ГОСТ 25 835 2 М.
5. Коэффициент выбора минимального диаметра барабана, h1 = 16,0.
6. Минимальный коэффициент использования каната, zp = 4,00.
Принцип работы: после запуска электродвигателя, на котором установлен тормоз, энергия через соединительную муфту передается на редуктор. После редуктора она передается на грузовой барабан, который в свою очередь приводит в действие канатно-блочный полиспаст. Полиспаст осуществляет подъем груза.
1. ВЫБОР ГРУЗОВОГО КРЮКА В соответствии с заданной массой поднимаемого груза 2,50 т принят крюк № 10 с грузоподъёмностью 2,5 т, с резьбой М30 по ГОСТ 6627.
2. ВЫБОР ГИБКОГО ТЯГОВОГО ОРГАНА Наибольшее натяжение Fmax, кН, гибкого тягового органа (стального каната, навиваемого на барабан) определено по следующей формуле:
(2.1)
где Gгр вес поднимаемого груза, кН; Gкп вес крюковой подвески, кН; zб — число рабочих участков на барабане, zб = 1; uп — кратность полиспаста, uп = 3; зп — КПД полиспаста.
Gгр = mгрg, (2.2)
где mгр — масса груза, т; g = 9,81 м/с2 — ускорение свободного падения.
Gгр = 2,509,81= 24,5 кН.
Gкп = гGгр, (2.3)
где г = 0,05.
Gкп = 0,2 524,5 = 0,6 кН.
(2.4)
где бл КПД канатных блоков, равный 0,97…0,98 при подшипниках качения, принято бл = 0,97.
Кратность полиспаста определяют при одинарном барабане по числу ветвей каната, на которых подвешен груз. При сдвоенном барабане кратность полиспаста равна половине числа ветвей каната, на которых подвешен груз.
8,63 кН.
В соответствии с нормами Ростехнадзора по максимальному рабочему усилию ветви каната Fмах и минимальному коэффициенту использования (коэффициенту запаса прочности) каната zр определяется разрывное усилие F0, кН:
F0 = Fmax zp, (2.5)
F0 = 8,63 4,00 = 34,52 кН.
В соответствии с разрывным усилием принят канат двойной свивки типа ЛК-3 с допускаемым разрывным усилием [F0] = 34 800 Н, диаметром каната dк = 8,3 мм, маркировочной группы 1568 МПа по ГОСТ 2688.
3. Определение основных параметров барабана и блоков Рисунок 3.1 — Схема барабана Диаметр барабана:
Dб = dк(h1 1), (3.1)
где dк диаметр каната; h1 коэффициент выбора минимального диаметра барабана, из задания берем значение равное 16 мм.
Dб = 8.3(16 1) = 124,5 мм.
Dб принят равным 130 мм.
Диаметр блоков:
Dбл = 1,2D, (3.2)
Dбл = 1,2130 = 156 мм.
Длина нарезной части барабана:
Lн = (zр+ zз)t, (3.3)
где zр число рабочих витков каната на барабане; zз — число запасных витков, равное 2; t шаг нарезки, мм.
t = 1,1dк, (3.4)
t = 1,18,3 = 9,13 мм.
t принимаем равным 10 мм.
(3.5)
где lк длина каната, мм.
lк = Huп103, (3.6)
lк = 1 610 003 = 48 000 мм.
= 110,5
Lн = (110,5+2)9,13 = 1024,4 мм.
Общее число витков:
z = zр + zз, (3.7)
z = 110,5 + 2 =112,5
Длина участка барабана, используемая под крепления каната:
L1 = 4t, (3.8)
L1 = 49,13 =36,5 мм.
Полная длина барабана:
L = Lн + L1 + 2L2, (3.9)
где L2 толщина реборды, равная 15 мм.
L = 1024,4 + 36,5 + 215 = 1030,9 мм.
4. ВЫБОР ЭЛЕКТРОДВИГАТЕЛЯ При кинематическом расчете механизма в первую очередь выбирается электродвигатель. Для этого определена требуемая мощность при установившемся движении механизма подъема груза из следующего соотношения:
(4.1)
где Рс — расчетная статическая мощность двигателя, кВт; Vгр — скорость подъема груза, м/мин; зобщ — общий КПД механизма.
зобщ = зрзбзп, (4.2)
где зр КПД редуктора, равное 0,97; зб — КПД барабана, равное 0,97; зп — КПД полиспаста, равное 0,97.
зобщ = 0,970,970,97 = 0,91
= 28,96 кВт.
В соответствии с потребной мощностью и заданной группой режима принят крановый электродвигатель МТKF 411−6 со следующими характеристиками: мощность на валу от группы режима рабочего механизма Рэд=30 кВт; частота вращения nэд=905 мин-1; диаметр dэд=65 мм[1].
5. ПОДБОР ЦИЛИНДРИЧЕСКОГО ЗУБЧАТОГО РЕДУКТОРА Частота вращения барабана:
103, (5.1)
435,2 мин.-1
Передаточное число редуктора:
(5.2)
Принимаем uр равным 2 для одноступенчатого редуктора.
Максимальный крутящий момент на тихоходном валу редуктора:
(5.3)
где D — средний диаметр вала:
D=Dб+dк, (5.4)
D=130+8,3=138,3 мм.
596,8 Нм.
В соответствии с потребным крутящим моментом и передаточным числом принят редуктор 1ЦУ-160 со следующими характеристиками: передаточное число на тихоходном валу редуктора uр = 2; номинальный крутящий момент на тихоходном валу [Твых] = 1250 Нм; КПД 0,98; масса m, кг 78; межосевое расстояние тихоходной ступени aw, мм 160; габаритные размеры, мм L = 1030,9 B = 331, H = 335; расстояние до конца валов, мм lвх = 136, lвых = 195; диаметры хвостовиков валов, мм dвх = 40, dвых = 50; расстояние между подшипниками l, мм 200.
6. РАСЧЕТ ТИХОХОДНОГО ВАЛА РЕДУКТОРА Окружное усилие в зацеплении:
(6.1)
где d2 делительный диаметр колеса
(6.2)
213,3 мм.
5,59 кН.
Радиальное усилие в зацеплении:
(6.3)
где б угол зацепления, равный 200.
Fr =5,590,36 = 2 кН.
Реакции в опорах 1 и 2 на ось Z:
кН. (6.4)
Изгибающий момент на ось Z:
Нм. (6.5)
Реакции в опорах 1 и 2 на ось Х:
кН. (6.6)
Изгибающий момент на ось Х:
Нм. (6.7)
Суммарный изгибающий момент:
(6.8)
296,6 Нм.
Приведенный момент в опасном сечении:
(6.9)
666,4 Нм.
Диаметр опасного сечения:
(6.10)
где [] допускаемое изгибное напряжение, равное 55 МПа.
48,6 мм Диаметр опасного сечения принят равным 50 мм.
d// = d/ 10, (6.11)
d// = 50 10 = 40 мм.
d/// = d// 10, (6.12)
d/// = 40 10 = 30 мм.
Диаметр вала из ориентировочного расчета:
(6.13)
где [] допускаемое касательное напряжение, равное 25 МПа.
48,06 мм.
7. ПОДБОР ПОДШИПНИКОВ КАЧЕНИЯ Исходные данные:
кН.
FR2 = FR1 =2,79 кН.
n = nб = 435,18 мин.-1
Диаметр шейки d = d// = 40 мм.
Ресурс подшипника Lh = (5…10) 103 ч, принят 7103 ч.
Приведенная нагрузка:
Pэ = FRkб, (7.1)
где kб коэффициент режима нагрузки, равный 1,4.
Pэ = 2,79 1,5 = 4,19 кН.
Потребная динамическая грузоподъемность:
(7.2)
5,7 кН.
C>Cп
В соответствии с потребной динамической грузоподъемностью приняты подшипники 210 по ГОСТ 8338 со следующими характеристиками: dхDхB = 40×68×15, динамическая грузоподъемность С = 16,8 кН, статическая грузоподъемность С0 = 9,3 кН.
8. ВЫБОР МУФТЫ ТИХОХОДНОГО ВАЛА Расчетный крутящий момент на выходном валу редуктора:
Тр2 = Твыхk1k2, (8.1)
где k1 коэффициент, учитывающий степень ответственности механизма, для подъемного механизма принято k1=1,3[1]; k2 коэффициент, учитывающий группу режима, для группы режима 4 М принято k2=1,0[1].
Тр2 = 569,81,31,1 = 775,84 Нм.
В соответствии с расчетным моментом принята муфта 2000;40 по ГОСТ 21 424 со следующими характеристиками: номинальным вращающим моментом [T]=2000 Нм; d=40 мм; наибольший диаметр муфты D=250 мм; длина муфты L= 288 мм; длина полумуфты l=140 мм.
9. ВЫБОР И ПРОВЕРКА ШПОНОК Принята по диаметру вала хвостовика 40 мм призматическая шпонка сечением bxh = 12×8 мм.
Глубина паза в ступице: t2 = 3,3 мм Длина хвостовика: l = 140 мм Длина шпонки: l/ = l 10, (9.1)
l/ = 140 10 = 130 мм.
Принято l/ =125 мм.
Расчетная длина шпонки:
lр = l/ b, (9.2)
lр = 125 12 = 113 мм.
Расчетное напряжение смятия:
(9.3)
79,8 МПа.
[см] = 80 Мпа, см < [см]
Принята шпонка bxhxl/хt = 14x9x160×3,3 по ГОСТ 23 360.
10. ВЫБОР ТОРМОЗА Статический вращающий момент на тормозном валу:
(10.1)
=247,4 Нм.
Необходимый тормозной момент:
Тт = ТсК, (10.1)
где К коэффициент запаса торможения, для группы режима 2 М К=1,5.
Тт = 247,41,75 = 371,1 Нм.
В соответствии с требуемым тормозным моментом принят тормоз ТКТ-300 со следующими характеристиками: тормозной момент, Нм 500; ширина колодки Bк, мм 140; диаметр тормозного шкива Dт, мм 300.
СПИСОК ИСПОЛЬЗОВАННЫХ ИСТОЧНИКОВ
редуктор подшипник вал тормозной Татаринцев Б. Е., Гендлина Л. И., Воронцов Д. С. Прикладная механика: Практикум к выполнению домашнего задания и контрольной работы по специальностям 653 400 «Организация перевозок и управление на транспорте». 2-е изд. Нск.: Издательство СГУПСа, 2009. 83 с.