Оперативно-календарное планирование единичного производства
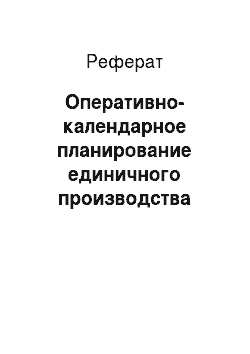
На основе расчетов длительности цикла сборки изделия, продолжительности цикла обработки деталей и изготовления заготовок определяется продолжительность цикла изготовления заказа в целом и разрабатывается цикловой график выполнения заказа, который является важнейшим документом межцехового оперативного планирования в позаказной системе. Если t меньше 1 месяца, то применяется позаказная система, при… Читать ещё >
Оперативно-календарное планирование единичного производства (реферат, курсовая, диплом, контрольная)
В единичном типе организации производства используются три системы оперативно-производственного планирования: позаказная, комплектно-узловая и подетально-складская.
• При позаказной системе планово-учетной единицей производственной программы является заказ или комплект деталей на заказ. Эта система охватывает весь производственный процесс выполнения заказа, включая этап технической подготовки производства, который занимает значительный удельный вес (особенно в машиностроении) в общем цикле изготовления продукции. Так, в станкостроении техническая подготовка производства составляет 50−55% общего цикла изготовления заказа.
Календарно-плановые расчеты производственной программы ведутся в порядке, обратном ходу технологического процесса от выпускающих цехов — к заготовительным. Для каждого цеха планируют сроки выполнения заказа, а также сроки запуска заказа в производственный процесс.
Важнейшими расчетами по календарно-плановым нормативам позаказной системы являются:
- — расчет длительности производственного цикла изготовления изделий (выполнения заказов) и построение цикловых графиков по отдельным изделиям (заказам);
- — определение календарных опережений в работе цехов;
- — составление сводного календарного графика выполнения заказов и уточнение календарных опережений в работе цехов;
- — проверочные расчеты загрузки оборудования (производственных площадей) и корректировка сводного графика в целях выравнивания загрузки по отдельным календарным периодам.
Производственный цикл (важнейший норматив организации производства) — календарный отрезок времени с момента запуска сырья и материалов в производство до момента выпуска готовой продукции.
Длительность цикла (tц) включает время производительной работы и время перерывов (внутрисменных, межсменных). Для изделия tц определяется по трудоемкости ведущего узла (детали, видов работ) и измеряется в календарных днях.
Расчет длительности производственного цикла ведется в порядке, обратном ходу технологического процесса: от выпускающих цехов к заготовительным и рассчитывается по формуле.

где п — число деталей в партии; т — число операций в процессе; tк — норма времени на операцию; с — число рабочих мест, параллельно занятых выполнением операции; s — число рабочих смен в сутках; q — длительность рабочей смены; tmn - межоперационное время; te — продолжительность естественных процессов.
Расчет tц укрупненным методом производится по формуле.

где tчас — трудоемкость ведущего узла (детали) или работ; k — коффициент выполнения норм; g — состав бригады; s — число рабочих смен в сутки; q — длительность рабочей смены.
В календарных днях.

где kк.д - коэффициент календарности работ, равный отношению числа календарных дней в году к числу рабочих дней в году.
На основе расчетов длительности цикла сборки изделия, продолжительности цикла обработки деталей и изготовления заготовок определяется продолжительность цикла изготовления заказа в целом и разрабатывается цикловой график выполнения заказа, который является важнейшим документом межцехового оперативного планирования в позаказной системе.
Цикловые графики по отдельным заказам и сроки сдачи заказов потребителю служат основой разработки сводного графика запуска-выпуска выполнения заказов на плановый период. В этом графике увязывается работа всех подразделений по выполнению заказов.
Разработка сводного графика сопровождается проверочными объемно-календарными расчетами загрузки оборудования (производственных площадей) по выполнению заказов. Эти расчеты должны уточнить, насколько пропускная способность оборудования цехов обеспечивает возможность изготовления заказа в запланированные сроки.
Объемно-календарные расчеты загрузки оборудования проводят в порядке, обратном ходу технологического процесса, т. е. от сборочных цехов к заготовительным производствам.
Важным нормативом позаказной системы являются сроки опережений (О) как по частным производственным процессам, так и по всем цехам предприятия.
Опережение — период времени (в днях), на который предыдущий частный производственный процесс должен опережать последующий процесс с целью его окончания в запланированный срок.
В основе расчета опережений лежит длительность производственного цикла изготовления изделия. Величина опережения равна суммарной длительности производственных циклов от даты окончания изготовления изделия до той технологической стадии, по которой определяется опережение. При этом t рассчитывают в направлении, обратном ходу производственного процесса, с прибавлением резервного времени между стадиями (tрез).
Пример. Деталь проходит обработку на трех стадиях производственного процесса: заготовительной, механической и сборочной длительностью соответственно 7, 11 и 10 дней. Резервное время — 2 дня. Необходимо рассчитать величину опережения.
Определим общую? ц изделия: tц.сб + tрез + tц.мех + tрез + tц.заг = 10 + 2 + 11 + 2 + 7 = 32 дня. Эго означает, что опережение по запуску изделия в производственный процесс относительно поставки его на склад готовой продукции составляет 32 дня. Тогда норматив опережения запуска изделия в сборочный цех Оз. сб составляет 10 дней.
Норматив опережения выпуска по механическому цеху равен: Оп. м = ?ц, б + Ов. м= tц.сб + tрез = 10 + 2 = 12 дней.
Норматив опережения запуска изделия в механический цех равен: Оз. м = tц.сб + tрез + tц.мех =10 + 2 + 11 = 23 дня.
Норматив опережения выпуска изделия в заготовительном цехе равен: Оз. м = tц.сб + tрез + tц.мех + tрез =10 + 2 + 11 + 2 — 25 дней.
Норматив опережения запуска изделия в заготовительном цехе равен: Оз. з = tц.заг = 25 + 7 = 32 дня, т. е. общей длительности производственного цикла (рис. 5.2).
Объектами оперативного учета и контроля при показанной системе являются сроки выполнения цехами заказов, а также их цикловые графики.

Рис. 5.2. Расчет опережений запуска-выпуска деталей в технологическом процессе.
• Комплектно-узловая система идентична по содержанию позаказной системе. Выбор в данном случае одной из двух систем определяется по tц.
Если t меньше 1 месяца, то применяется позаказная система, при которой все необходимые для сборки изделия узлы и детали комплектуются до начала сборочных работ. Если t больше 1 месяца, то применяется комплектно-узловая система, при которой комплектация сборки происходит по мере изготовления комплектующих узлов и деталей.
Планово-учетной единицей по предприятию в этом варианте является технологический узел, а по цехам — комплект деталей для него.
• Подетально-складская система (система максимум-минимум) применяется как в единичном, так и в серийном типах организации производства. Оперативное планирование по этой системе касается производства унифицированных и стандартизированных деталей общего применения.
При этой системе партия изготовленных деталей сдается в цеховой склад. Рассчитываются три типа запасов деталей (заделов): максимальный, минимальный и запас точки заказа. Схема движения запасов (Z) представлена на рис. 5.3.
Функционирование этой системы планирования осуществляется путем постоянного восстановления складских запасов до начального уровня.
Минимальный запас Zmin - это резерв, использование которого необходимо в крайних случаях.

Рис. 5.3. Схема движения запасов.

где Вс.д — среднедневной выпуск деталей; tоп — время изготовле? ния детали.
Максимальный запас деталей равен:

где - размер партии деталей, поступивших из цеха на склад; t — время между двумя очередными поставками на склад партии деталей.
Запас точки заказа равен такому объему деталей на складе, при котором склад выдает цеху заказ на изготовление очередной партии деталей:

На складе должен вестись систематический контроль состояния запасов деталей с помощью специальной подетальной картотеки: на каждую деталь заводится карточка, в которой приводятся номер детали и ее наименование, цех-изготовитель, размер страхового задела. В карточках отмечается движение каждой детали на складе. С их помощью контролируется фактическое состояние заделов и своевременность запуска деталей в производство.
Внутрицеховое оперативно-производственное планирование в единичном производстве выполняет следующие функции:
- — доведение месячной производственной цеховой программы до каждого участка и рабочего места в виде комплекта деталей на заказ или узел;
- — уточнение цехового календарного плана работы по выполнению отдельных заказов;
- — организация разработки сменно-суточных заданий по рабочим местам, т. е. определение времени запуска деталей в производство;
- — обеспечение оперативной подготовки выполнения сменно-суточных планов на рабочих местах, т. е. проверка обеспеченности цеха и каждого рабочего места заготовками и полуфабрикатами в соответствии с выделенными лимитами на материальные ресурсы и технологическую оснастку;
- — контроль выполнения цеховой производственной программы участками и бригадами.
Все эти функции внутрицехового ОКП выполняют работники цеховых производственно-диспетчерских бюро.
Следует отметить, что резервами повышения эффективности единичного типа организации производства является увеличение удельного веса унифицированных и стандартизированных деталей и узлов. Так, в машиностроении удельный вес унифицированных деталей и узлов составляет в среднем 40−70%, что позволяет в условиях единичного производства создавать специализированные участки и многопредметные поточные линии по обработке этих деталей, т. е. привносить в единичное производство элементы крупносерийного типа организации. Значительно повышает технический уровень единичного производства и улучшает его экономические показатели введение системы серийного производства, в частности комплектногрупповой системы ОКП. Суть ее заключается в том, что организуется групповой запуск в производство деталей разного наименования и размеров, но обладающих конструктивно-технологическим сходством.
Такому запуску должна предшествовать большая подготовительная работа по классификации деталей, технологических процессов и технологической оснастки на группы по признаку конструктивно-технологического подобия.
Производственная программа цеха планируется в комплектах деталей, относящихся к той или иной группе.