Бережливое производство.
Формирование показателей качества продукции
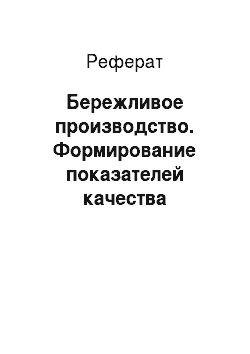
Потери от передвижений. Такие потери, которые связаны с ненужным перемещением персонала, продукции, материалов, которые не добавляют ценности процессу. Часто рабочие совершают лишние перемещения со своего участка до цехового клада и обратно. Ходят вокруг загромождённых участков. Такие перемещения необходимо устранить или минимизировать. Лишние перемещения утомляют своей бесполезностью, уменьшают… Читать ещё >
Бережливое производство. Формирование показателей качества продукции (реферат, курсовая, диплом, контрольная)
Общие сведения
Концепция БП возникла в Японии в 1980;ые и получила название LEAN PRODUCTION. В любой системе во всех процессах существуют скрытые потери. Определение и устранение этих потерь экономит для организации огромные суммы. Скрытые потери подразделяются на 7 категорий: 1) перепроизводство 2) дефекты и переделки 3) передвижение 4) перемещение материалов 5) запасы 6) излишняя обработка 7) простои. Указанные потери увеличивают издержки производства. Необходимо найти причины потерь и разработать меры для их устранения.
Анализ потерь
- 1)потери перепроизводства. Возникают тогда, когда выпускают гораздо больше продукции чем необходимо. Причины: недостаток планирования, большие заделы, недостаточно тесный контакт с заказчиком. Это всё приводит к тому, что продукции производится больше чем надо потребителю. Излишний товар трудно продать, следовательно уценка, след потери. Для минимальных потерь необходимо улучшать работу службы маркетинга и налаживать работу с поставщиками, чтобы получать поставку в нужном количестве и вовремя.
- 2) потери из-за дефектов и необходимых переделок. Возникает тогда, когда нет надёжной системы предупреждающих действий (плохо используется FMEA анализ) Изготовитель дважды тратит средства: когда производит продукцию и когда её перерабатывает, устраняя дефекты, а потребитель платит только один раз. Допустив ошибку на промежуточной операции нельзя передать изделие на следующую. Особенно нежелательна ситуация когда дефект обнаружен потребителем. Вывод: нельзя мириться с дефектом, надо добиваться бездефектного производства.
- 3)Потери от передвижений. Такие потери, которые связаны с ненужным перемещением персонала, продукции, материалов, которые не добавляют ценности процессу. Часто рабочие совершают лишние перемещения со своего участка до цехового клада и обратно. Ходят вокруг загромождённых участков. Такие перемещения необходимо устранить или минимизировать. Лишние перемещения утомляют своей бесполезностью, уменьшают деловой настрой, утяжеляют труд.
- 4) Потери при транспортировке. Возникают когда материалы или заготовки перемещают между операциями, которые разделяются производством. Далеко не редко места операции расположены далеко друг от друга что требует автопогрузки или других транспортных средств. Встречались случаи многоэтапного перемещения материалов. Всё это требует лишних расходов.
- 5) Потери от излишних запасов. Излишние запасы замораживают средства, требуют дополнит. выплат, снижают отдачу от инвестиций. Провоцирует предприятие на выпуск старой продукции, когда пора уже осваивать новое. Излишние запасы могут привести к потере качества материалов при длительном хранении.
- 6) Потери от излишней обработки. Возникают при производстве продукции тогда, когда затраты на обработку превышают тот уровень который требует потребитель. Например добавление функциональной возможности немеющей цены в глазах потребителя. Эти потери происходят от недостатка информации о требованиях потребителя.
- 7) Простои. Потери времени на простои возникают тогда, когда люди, операции или частично готовая продукция должны дожидаться информации о материалах или комплектациях. Это связано с плохой организацией, плохим планированием.
Инструменты и методики реализации бережливого пр-ва Основное назначние — снижение потерь.
1. Концепция 5S.
Направлена на улучшение организации труда и улучшение качества на рабочем месте за счет наведения порядка, соблюдения чистоты и дисциплины.
2. Непрерывные улучшения (концепция серии малых улучшений) Постоянный процесс коллективных и индивидуальных усилий по постепенному улучшению орг-ии работы предприятий.
3, Управление потоком создания ценностей Планирование и преобразование процессов с целью минимизации имеющихся ресурсов.
4. Картирование процесса Графическое изображение процесса, как последовательностиопераций с указанием потоков инф и мат-лов.
5. Защита от ошибок Система принятия реш, предусматривающая многократный анализ рисков, возможных отказов и их последствий (близко к FMEA).
6. Сокращение размера партии С точки зрения потерь оптимальным размером партии является поток из 1 предмета. Необходимо минимизиовать число предметов, одновременно обрабатываемых на операции.
7. Средства визуального контроля (партии, схемы) Показывают что и как должен делать оператор
8. Хорошо продуманный план размещения оборудования Составляется исходя из оптимальной последовательности выполнения операций. Обеспечивает близкое и удобное перемещение заготовок и инструмента.
9. Стандартизованная работа Согласованное выполнение задачи в соотаетствии с принятыми методами.
- 10. Командная работа
- 11. Кач-во в процессе работы
Проверка и упр процессами осущ-ся операторами. Они убеждаются, что продукция, поступающая на след этап процесса будет соответствующего кач-ва.
12. Место хранения нужных предметов Сырье, детали, информация, инструменты, рабочие стандарты, описания процедур — должны находиться именно там где необходимо.
13. Гибкость производства Спос-ть быстро переналадить оборудование и поменять инструмент, позволяет на одном и том же оборудовании выпускать большую номенклатуру изделий при одновременном сокращении партии.
14. Пилотный проект Выбирается какое-то «узкое место» в производстве и производится масштабное улучшение. Используется приобретенные навыки применяют развертывание БП на другие узкие места.
15. Анализ общей эффективности оборуд и потерь Строят диаграму Паркто этих потерь, определяют, как получить наибольшую отдачу на вложенные средства.
Cистемы 5S.
Это метод организации рабочей среды, который значительно повышает эффективность и управляемость операционной зоны, улучшая корпоративную культуру и сохраняя время.
От японских слов сортировка, упорядочение, очищение стандартизация, дисциплина.
Сортировка означает четкое разделение предметов на нужные и ненужные, с поледующей их ликвидацией в тчение определенного времени. Часто оставляют предметы «на всякий случай» — это вызывает беспорядок и приводит к появлению препятствий в раб зоне.
Можно использовать метод красных ярлыков! Ненужными могут быть устаревшие документы, неисправные инструменты и т. п.
Упорядочение означает расположение предметов в том порядке, который наиболее отвечает требованиям безопасности, качества и эффективности работы. Часто употребляемые предметы располагают ближе к себе, легкие на верхних полках, тяжелые на уровне поясницы.
Необходимо не только «найти дом для каждого предмета» но и обозначить его, так чтобы другая смена могла поддерживать общий порядок и легко находить нужные предметы. Полезно применять специальные стеллажи с изображение предметов, которые там должны находиться, на полу необходимо сделать разметку для круглых предметов Очищение — создание благоприятной раб среды. Заключается в устранении источников пыли и грязи и сохранении чистоты. Необходимо обращать внимание на скользкий пол, на места утечки масла, на подорванные шланги, отпеч пальцев на оборудовании. Начинают раб день с проверки наличия материалов и инструментов и завершают его уточнением того, что из намеченного сделано, передана ли инф следующему звену тех процесса, заказаны ли расх материалы на след день. Следует завести контрольный лист с описанием мест, подлежащих особому контролю и регулярной уборке.
Стандартизация в области гигиены — это комплекс мер по плддержанию первых 3 принципов конц 5S, кот подразумевают собл работниками гигиены, опрятности в одежде, создание с помощью системы указателей такой ситуации на производстве, что любое отклонение от нормы бросается в глаза.
Дисциплина. Должна создаваться система товарищеской взаимопомощи, доброжелательности в отношениях между людьми. У каждого сотрудника должен постоянно формироваться настрой на развитие своих способностей.
Cистема упорядочения Истоки системы:
- — отечественная теория и практика научной организации труда
- — опят японский предприятий (система 5S)
Система упорядочения позволяет повышать производительность, сократить потери, снизить уровень брака и травматизма.
Влияние СУ на безопасность и производительность Безопасность:
- — сокращение числа аварий
- — улучш санитарных условий
- — соблюдение правил охраны труда
- — предотвращение утечек
Производительность:
- — сокращение ненужных запасов
- — эффективное использование рабочих мест
- — предотвращение потерь ресурсов
- — сокращение простоев
Качество:
- — сокращение потерь от брака из-за невнимания персонала, неиспраности оборудования, загрязнения рабочей зоны
- — обеспечение требумого уровня качества
Принципы СУ:
- — удаление лишних предметов
- — рациональное размещение и наглядное обозначение предметов
- — уборка, проверка, устранение неисправностей
- — стандартизация правил
- — соблюдение технологических требований
- — высокая дисциплина персонала
- — слаженная работа персонала
Система производительного обслуживания оборудования с участием всего персонала (TPM).
В концепции ТРМ выдвигается идея, что обслуживанние оборудования так же является деятельностью, приносящей прибыль за счет сведения к минимуму времени, тэкстренного обслуживания и ремонта оборудования, что тормозит основной технологический процесс Сущность:
Если у какой то машины случается сбой, то остальные продолжают работать. Устранение неисправностей у одной машины не нарушает существенно всего процесса.
На фирме Toyota решили уменьшить промежуточные запасы. Стала важна готовность к работе каждой машины. Причем общая готовность — пооизведение вероятностей нахождения в рабочем состоянии Надо максимально повышать готовность к работе каждой машины. Это и привело к появлению ТРМ.
Готовность оборудования не полностью определяет эффективность производства.
КОЭ — коэффициент общей эффективности (всегда меньше 100%).
При развертывании ТРМ ориентируются на КОЭ около 85%.
Принципы ТРМ:
- — повышение эффективности оборудования
- — самостоятельное обслуживание оборудования операторами
- — плановое обслуживание
- — повышение квалификации производственного и ремонтного персонала
- — улучшение работы обеспечивающих подразделений и качества планирования производственной деятельности
- — управление качеством продукции
- — обеспечеие благоприятного состояния окружающей среды и обеспечение производственной безопасности
Конц ТРМ похожа на TQM по нескольким аспектам:
- — требуется полная заинтересованность высшего руководства в данной программе
- — должна быть одобрена долгосрочная перспектива
- — работники должны получить полномочия для проведения корректирующих действий
- — работники должны переосмыслить отношение к соим обязанностям
Освоение методики решения типичной задачи обработки данных, полученных в шкале наименований.
Частость появления признака х:
СКО величины n:
Доверительный интервал значений, в который с заданной вероятностью Р укладывается фактическое значение оцениваемой величины nо в любой совокупности из М объектов:
Где t — коэффициент Стьюдента, выбираемый в зависимости от доверительной вероятности Р.
ОПРЕДЕЛЕНИЕ КОЭФФИЦИЕНТОВ ВЕСОМОСТИ ПОКАЗАТЕЛЕЙ КАЧЕСТВА СПОСОБОМ РАНЖИРОВАНИЯ Степень согласованности определяют с помощью коэффициента конкордации Где — средняя сумма рангов, полученных одним показателем, — сумма рангов, полученная данным показателем во всех ранжировках ПОРАСЧЕТ ЧИСЛА ЭКСПЕРТОВ И ОЖИДАЕМОГО ЧИСЛА ПРЕДЛОЖЕНИЙ.
— Коэффициент vвероятности появления нов предлож от 4к 5 Э-ам.