Сборные элементы оросительной сети из бетона с микронаполнителем
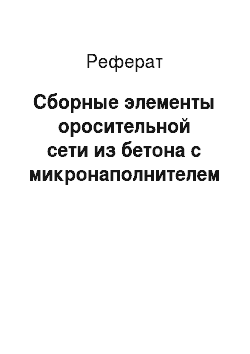
Наиболее желательно было бы применение молотых минеральных материалов. Но использование их в смесях приводит к повышению себестоимости бетонных и железобетонных элементов. Поэтому, учитывая особенности сырьевой базы Северо-Кавказского региона, большой практический интерес представляет изучение возможности применения в качестве микронаполнителей тонкодисперсных промышленных отходов… Читать ещё >
Сборные элементы оросительной сети из бетона с микронаполнителем (реферат, курсовая, диплом, контрольная)
Эксплуатационная надёжность бетонных и железобетонных элементов во многом определяется физико-механическими свойствами бетона, зависящими от качества слагающих его компонентов. Большинство природных заполнителей, особенно песков, в связи с повышенным содержанием пылевидных и глинистых частиц, являются некондиционными. Пылевидные и особенно глинистые частицы создают на поверхности зёрен заполнителя плёнку, препятствующую сцеплению их с цементным камнем. В результате прочность бетона значительно понижается [1]. На практике отрицательное влияние некондиционного заполнителя компенсируют повышением расхода цемента, что недопустимо. В связи с этим, для экономии цемента в состав бетонной смеси предлагается введение микронаполнителя.
Наиболее желательно было бы применение молотых минеральных материалов. Но использование их в смесях приводит к повышению себестоимости бетонных и железобетонных элементов. Поэтому, учитывая особенности сырьевой базы Северо-Кавказского региона, большой практический интерес представляет изучение возможности применения в качестве микронаполнителей тонкодисперсных промышленных отходов. О целесообразности такого направления исследований свидетельствует тот факт, что только на региональных керамзитовых заводах ежемесячно вывозится в отвалы порядка 170 т керамзитовой пыли, а Новочеркасская ГРЭС является крупнейшим поставщиком золы-унос, отгрузка которой может производиться практически в неограниченных количествах.
В связи с вышеизложенным, в задачу исследований входило выявление влияния тонкодисперсных промышленных отходов (золы-унос, керамзитовой пыли) на эксплуатационные качества гидротехнического бетона плит и труб, широко используемых на проводящих сетях оросительных систем.
Железобетонные плиты креплений и плиты покрытий работают в сложных условиях, подвергаясь попеременному водонасыщению и высушиванию, отрицательно влияющих на их эксплуатационные свойства, прежде всего на трещиностойкость и долговечность. Указанные свойства оценивались нами на основе изменения прочности при изгибе бетонных образцов, находящихся в среде с переменной влажностью окружающей среды [2]. При этом сравнивались прочностные показатели при изгибе затвердевших образцов после насыщения их водой с прочностными показателями аналогичных образцов после насыщения их водой и дополнительного выдерживания в воздушно-сухих условиях при относительной влажности воздуха от 40 до 60% в течение от 12 до 36 часов, и по полученным коэффициентам оценивались трещиностойкость и долговечность исследуемых бетонов.
Для выяснения влияния добавки золы-унос на трещиностойкость и долговечность бетона был использован двухфакторный симплекс-суммируемый план на правильном шестиугольнике. Этот план, несмотря на то, что не является оптимальным по статистическим характеристикам, выбран из-за его экономичности. По результатам всего семи опытов он позволяет получить квадратичные двухфакторные модели исследуемых систем. Выбранные в качестве исследуемых факторов расход золы-унос в смесях (фактор) варьировался в диапазоне от 0 до 320 кг/м3, а расход цемента (фактор), с учётом составов бетона плит изменялся в опытах от 180 до 330 кг/м3 (табл. 1). Матрица и результаты эксперимента представлены в таблице 2.
Таблица 1 Кодирование и варьирование факторов.
Факторы. | Код. | Основной уровень,, %. | Интервал варьирования. | Нижний уровень, ««. | Верхний уровень, «+». | |
Зола-унос. | ||||||
Цемент. | ||||||
Таблица 2 Реализация плана эксперимента.
Номер опыта. | План. | Факторы. | Ктр | ||||||||
(З). | (Ц). | ||||||||||
0,5. | — 0,87. | 0,25. | 0,75. | — 0,43. | 31,0. | 30,8. | 1,01. | ||||
— 0,5. | 0,87. | 0,25. | 0,75. | — 0,43. | 47,6. | 46,5. | 1,02. | ||||
45,8. | 39,9. | 1,15. | |||||||||
— 0,5. | — 0,87. | 0,25. | 0,75. | 0,43. | 22,3. | 22,1. | 1,00. | ||||
— 1. | 35,7. | 37,2. | 0,96. | ||||||||
+1. | 46,4. | 54,4. | 0,85. | ||||||||
0,5. | 0,87. | 0,25. | 0,75. | 0,43. | 59,4. | 58,9. | 1,01. | ||||
— 11,0. | 2,0. | — 1,0. | |||||||||
Для каждого из опытов изготавливались шесть образцов-призм 40Ч40Ч160 мм. Далее, образцы пропаривались и погружались в воду для полного насыщения водой. По истечении двух суток по три образца каждого из семи составов испытывались на изгиб (). Остальные три образца после извлечения из воды дополнительно, в течение 36 часов, выдерживались в воздушно-сухих условиях, после чего также испытывались на изгиб (). Трещиностойкость и долговечность согласно [2] оценивалась величиной В результате обработки экспериментальных данных и расчёта по известной методике [3] коэффициентов уравнения регрессии была получена начальная математическая модель.
:
. (1).
Расчёт критических величин коэффициентов и исключение статистически незначимого (), позволили получить конечную математическую модель.
. (2).
Анализ математической модели (2) показал, что равнопрочность () бетонных образцов, находящихся в среде с переменной влажностью окружающей среды наблюдается в широком диапазоне расходов золы-унос. Учитывая целесообразность максимального использования летучих зол в бетонах, независимо от их марки, количество золы-унос на 1 м³ смеси может быть доведено до 240−280 кг. Дальнейшее увеличение расхода золы-унос приводит к снижению трещиностойкости и долговечности бетона. Таким образом, введение летучих зол в бетонные смеси в оптимальных количествах обеспечивает не только экономное расходование цемента, но и повышает трещиностойкость и долговечность бетонных и железобетонных элементов (конструкций), работающих в условиях переменной влажности, характерных для водохозяйственных объектов.
В отличие от обычного бетона использование добавки золы в составе центрифугированного бетона железобетонных труб не привело к повышению эксплуатационных качеств бетона. Возможно, это связано с распределением частиц в процессе центрифугирования бетонной смеси. Под действием центробежных сил мельчайшие частицы золы, близкие по размерам к коллоидным, могут удаляться из бетонной смеси вместе с избыточной водой затворения, отжимаемой при центрифугировании из бетонной смеси. В связи с этим было принято решение отказаться от использования золы в составе центрифугированного бетона железобетонных труб и исследовать влияние добавки керамзитовой пыли на свойства центрифугированного бетона.
Керамзитовая пыль вводилась в бетонную смесь заводского состава взамен части песка (или цемента). Количество воды затворения в каждом опыте подбирали экспериментально из условия получения равноподвижных смесей. Из приготовленных бетонных смесей формовали образцы-призмы 40Ч40Ч160 мм и цилиндры диаметром и высотой 30 мм. Цилиндры формовали на лабораторной центрифуге в специальных формах. Затем образцы подвергались тепловлажностной обработке по режиму 4+3+6+4. Далее, призмы испытывались на изгиб, их половинки на сжатие, а цилиндры испытывали на раскалывание вдоль образующей. Результаты испытаний приведены в таблице 3.
Таблица 3 Влияние керамзитовой пыли на прочность бетона.
№ состава. | Цемент, кг/м3. | Керамзитовая пыль (КП). | Прочность образцов после ТВО. | |||||||
Rизгиб. | Rсжатие. | усилие на раскалывание. | ||||||||
кг/м3. | % от массы Ц | МПа. | %. | МПа. | %. | Н. | %. | |||
; | 2,96. | 12,8. | ||||||||
3,00. | 12,4. | |||||||||
2,72. | 10,1. | |||||||||
3,67. | 17,6. | |||||||||
3,52. | 17,1. | |||||||||
3,78. | 16,2. | |||||||||
3,89. | 16,8. | |||||||||
; | ; | ; | ; | |||||||
3,44. | 14,3. | |||||||||
2,98. | 13,2. | |||||||||
оросительный бетон керамзитовый плита Как следует из представленных в таблице 3 данных, добавка керамзитовой пыли позволяет без снижения прочностных показателей сократить расход цемента на 25%. При введении добавки керамзитовой пыли не за счёт цемента, а за счёт части песка, прочностные показатели балочек повышаются в большей мере, чем центрифугированных цилиндров. Оптимальная дозировка добавки керамзитовой пыли находится в пределах 100−160 кг/м3 (20−30% от массы цемента). При этом прочность центрифугированных образцов на растяжение при раскалывании повышается на 25−40% без снижения расхода цемента.
На материалах завода напорных труб были изготовлены образцы центрифугированных бетонных труб диаметром 180 мм, длиной 300 мм с добавкой керамзитовой пыли в количестве 25% от массы цемента, вводимой за счёт частичной замены песка и для получения сравнительных данных — без керамзитовой пыли. Опытные образцы труб после пропаривания подвергали испытаниям на гидростатическое давление. Образец без добавки выдержал давление 0,5 МПа, а труба с добавкой 25% керамзитовой пыли разрушилась при давлении воды в ней 0,9 МПа. Добавка керамзитовой пыли повысила прочность на растяжение центрифугированного бетона на 80%.
Испытания изготовленных в кольцевых формах одновременно с формованием труб бетонных образцов показали, что опытный состав центрифугированного бетона с добавкой 25% керамзитовой пыли по сравнению с контрольным (заводским) прочнее при раскалывании на 17−20%. Водопоглощение бетона с добавкой на 0,5−0,7% ниже, чем контрольного. Таким образом, введение добавки керамзитовой пыли в состав центрифугированного бетона железобетонных труб позволяет существенно повысить его прочностные показатели, на 15−20% снизить расход цемента без ухудшения прочности бетона, повысить трещиностойкость и водонепроницаемость труб, улучшить их качество и снизить процент брака при изготовлении труб по существующей технологии.
Что касается технологии применения добавки золы или керамзитовой пыли в производственном процессе по изготовлению сборных элементов, то она не имеет принципиальных отличий от применения в производстве других известных порошкообразных материалов, в частности, цемента.
Транспортировка, перегрузочные операции и хранение на складе золы и керамзитовой пыли при поступлении их в россыпи (навалом) сопряжено с большими потерями от распыления и ухудшениями условий труда. В связи с этим, все операции по выгрузке поступающих на завод микронаполнителей и последующему их перемещению по технологической цепочке должны быть комплексно механизированы с использованием оборудования, предназначенного для работы с цементом.
Необходимая ёмкость склада золы (или керамзитовой пыли) зависит от мощности завода по производству сборных элементов и должна обеспечивать не менее 5−7-суточную потребность в микронаполнителе.
Наиболее совершенным средством для доставки микронаполнителя на завод-потребитель являются цементовозы-цистерны с пневматической разгрузкой, позволяющей без дополнительных приёмных устройств подавать золу или керамзитовую пыль в силосный склад на расстояние по горизонтали до 50 м и на высоту до 25 м. Часть микронаполнителя может непосредственно подаваться в расходный бункер, минуя силосы склада.
Для подачи золы (или керамзитовой пыли) в бетоносмесительное отделение, в зависимости от местных условий, может быть использован пневмотранспорт, аэрожёлобы, шнеки, эрлифты, виброжёлобы и другое герметичное типовое оборудование, применяемое в цементоводах.
Дозирование добавки микронаполнителя в бетоносмеситель должно осуществляться дозирующими устройствами, обеспечивающими точность дозирования на замес в пределах ±1% по массе добавки, заданной заводской лабораторией. Оптимальная дозировка золы или керамзитовой пыли, зависящая от особенностей используемых в производстве сборных элементов материалов и специфики технологических процессов на каждом предприятии, должна устанавливаться опытным путём заводской лабораторией и уточняться по мере изменения характеристик сырья и технологических режимов изготовления элементов. Приготовление бетонной смеси с добавкой микронаполнителя можно осуществлять в бетоносмесителях любого типа, обеспечивающих заданную производительность и однородность перемешивания бетонной смеси.
- 1. Баженов Ю. М., Комар А. Г. Технология бетонных и железобетонных изделий. М.: Стройиздат, 1984. 672 с.
- 2. А.С. 346 668, СССР. 1973. С 01n 33/38. Способ определения долговечности бетона.
- 3. Вознесенский В. А. Статистические методы планирования эксперимента в технико-экономических исследованиях. М.: Финансы и статистика, 1981. 262 с.