Технико-экономические обоснование технологического процесса доставки непакетированных грузов в мешках на линии Осетрово-Якутск с минимальными затратами
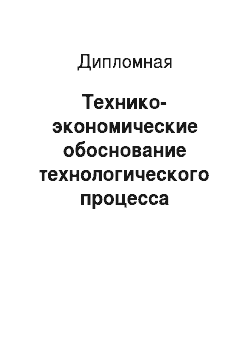
Для грузов перевозимых в районы Дальнего востока, Арктики и Крайнего Севера предъявляются повышенные требования к таре, что связанно с большим числом перевалок, продолжительностью перевозки и хранения. Для обеспечения прочности тару часто дополнительно укрепляют (обтягивают специальной металлической лентой или проволокой, обивают угольниками) Для сокращения внутрипортовой и внутрискладской… Читать ещё >
Технико-экономические обоснование технологического процесса доставки непакетированных грузов в мешках на линии Осетрово-Якутск с минимальными затратами (реферат, курсовая, диплом, контрольная)
1. Общая характеристика и анализ грузопотока непакетированных грузов в мешках и существующих технологических процессов их перегрузки
1.1 Общая характеристика и анализ непакетированного груза в мешках
1.2 Общая характеристика существующих технологических процессов перегрузки непакетированных тарно-штучных грузов
1.3 Характеристика материально-технологической базы по перевозке и перегрузке непакетированных грузов в мешках в Ленском бассейне
2. Разработка вариантов технологического процесса доставки непакетированных грузов в мешках и норм перегрузочных работ
2.1 Исходные данные и принимаемые ограничения технологического процесса доставки груза
2.2 Варианты технологического процесса доставки груза
2.3 Расчет норм перегрузочных работ по вариантам технологического процесса доставки груза
2.3.1 Среднесуточный грузооборот
2.3.2 Потребная емкость склада
2.3.3 Потребная площадь склада
2.3.4 Расчет производительности перегрузочных машин
2.3.5 Расчет минимального количества перегрузочных машин на причале
2.3.6 Максимально возможная механовооруженность причала
2.3.7 Расчет числа перегрузочных машин, работающих совместно с фронтальной машиной в одной технологической линии
2.3.8 Общее время обслуживания судна на причале
2.3.9 Определение числа рабочих комплексной бригады, участвующих в перегрузочном процессе
2.3.10 Расчет продолжительности работы перегрузочных машин и затрат труда для выполнения навигационного грузооборота
2.3.11 Расчет комплексных норм выработки и времени
3. Технико-экономическое обоснование рационального технического процесса доставки непакетированного груза в мешках
3.1 Общие соображения по методике технико-экономического обоснования рационального технологического процесса доставки
3.2 Расчет капиталовложений в строительстве и оборудование причала
3.3 Расчет капиталовложений во флот за время его грузовой обработки и в ожидании обработки
3.4. Расчет капиталовложений во флот за время движения
3.5 Расчет капиталовложений в средства укрупнения «подъема» (СУП)
3.6 Расчет эксплуатационных расходов
3.6.1 Эксплуатационные расходы по порту
3.6.1.1 Расчет расходов на заработную плату портовым рабочим механизаторам комплексной бригады
3.6.1.2 Расчет расходов на амортизацию и текущий ремонт портовых инженерных сооружений
3.6.1.3 Расчет расходов на амортизацию и текущий ремонт по перегрузочному оборудованию
3.6.1.4 Расчет расходов на электроэнергию, топливо, смазку и обтирочные материалы
3.6.1.5 Расчет доходов по содержанию распорядительского персонала и общепроизводственные расходы
3.6.1.6 Расчет распределяемых расходов
3.6.1.7 Общие эксплуатационные расходы по порту
3.6.2 Расчет эксплуатационных расходов по флоту
3.6.3 Расчет эксплуатационных расходов на средства укрупнения «подъема» (СУП)
3.7 Расчет дополнительных показателей
3.7.1 Производительность труда
3.7.2 Интенсивность грузовой обработки флота
3.7.3 Степень механизации труда
3.7.4 Резерв пропускной способности причала
3.8 Расчет удельных приведенных затрат
3.9 Показатель эффективности использования производственных фондов
3.10 Выбор оптимального варианта технологического процесса доставки непакетированного груза в мешках
4. Разработка технологической документации по оптимальному технологическому процессу доставки непакетированного груза в мешках
4.1 Документация технологического процесса работы порта
4.1.1 Техническо-распорядительный акт
4.1.2 Технологические карты обработки судов и вагонов
4.1.3 Типовые циклы полной обработки судов
4.1.4 График обработки судов
5. Охрана труда и окружающей среды
5.1 Техника безопасности при погрузо-разгрузочных работах
5.2 Охрана окружающей среды
6. Технико-экономическая эффективность оптимального технологического процесса доставки непакетированного груза в мешках
7.
Заключение
выводы и рекомендации производству Список использованных источников
В северных районах страны доставка грузов в основном производится водным транспортом. В большинстве случаев доставка груза в порт осуществляется железнодорожным или автотранспортом. Каждая тонна груза в процессе доставки перегружается несколько раз, что значительно увеличивает объем перегрузочных работ и обусловливает их сложность и трудоемкость.
В процессе грузовой обработки транспортных средств одновременно участвуют различные перегрузочные средства и значительное количество людей. Успешное выполнение перегрузочных работ возможно лишь при четкой их организации на основе заранее разработанной технологии, определяющей порядок и последовательность выполнения всех операций и использования технических средств и рабочей силы.
Организация перегрузочных работ — одна из главных функций управления работой порта, позволяющая в различных условиях с наименьшими затратами обеспечить переработку поступающих в порт грузов и максимально сократить стоянки транспортных средств под грузовыми потоками и другими операциями. Она определяет структуру и взаимодействие подразделений порта, рациональное использование его оборудования и трудовых ресурсов.
Перегрузочные работы в портах относятся к наиболее трудоемким и тяжелым работам на речном транспорте. В процессе загрузки и разгрузки транспортных средств осуществляют различные операции, связанные с захватом, укладкой, взвешиванием и перемещением груза в трюме, вагоне, складе и т. п.
Наибольшую трудоемкость в портах создают тарно-штучные грузы, поступающие на перевалку в непакетированном виде и особенно в крытых вагонах.
Для снижения трудоемкости на внутрипортовых работах, по этой категории грузов, порты используют различные средства для формирования «подъемов», как в пунктах перевалки, так и в пунктах назначения.
В данном проекте производится технико-экономические обоснование технологического процесса доставки непакетированных грузов в мешках на линии Осетрово — Якутск с минимальными затратами.
1. Общая характеристика и анализ грузопотока непакетированных грузов в мешках и существующих технологических процессов
1.1 Общая характеристика и анализ непакетированного груза в мешках
К этой категории относятся сыпучие грузы, упакованные мешки или бумажные пакеты.
Характеристика груза в мешках по классам дана в таблице 1.
Для грузов перевозимых в районы Дальнего востока, Арктики и Крайнего Севера предъявляются повышенные требования к таре, что связанно с большим числом перевалок, продолжительностью перевозки и хранения. Для обеспечения прочности тару часто дополнительно укрепляют (обтягивают специальной металлической лентой или проволокой, обивают угольниками) Для сокращения внутрипортовой и внутрискладской трудоемкости, в цехах готовой продукции предприятий-поставщиков, портов перевалки и назначения, на базах грузополучателей используются различные средства укрупнения «подъемов». К таким средствам относятся: грузовые площади, сетки, поддоны, стропы, флеты и т. д.
Наибольшее распространение, как в Росси, так и за рубежом, получили поддоны и стропы.
Характеристика поддонов приведена в таблице 2, характеристика стропов в таблице 3.
Динамика грузопотока пакетопригодных грузов через Осетровский речной порт, следующих в прямом смешанно-водном сообщении представлена в таблице 4.
Таблица 1
Характеристика груза в мешках по классам груза.
Класс груза | Масса одного места, кг | Погрузочный объем, м3/т | Примечание | |
М-О | Любая | 2,46 и более | Объемистые грузы | |
М-50 | До 51 | До 2,45 | Объемистые грузы | |
М-80 | 52−80 | До 2,45 | Объемистые грузы | |
М-102 | 81−102 | До 2,45 | Объемистые грузы | |
М-125 | 103−125 | До 2,45 | Объемистые грузы | |
М-Т | До 51 | До 0,99 | К данному классу груза не относится цемент, упакованный в бумажные трехслойные пакеты | |
Таблица 2
Характеристики деревянных поддонов, применяемых в Ленском бассейне.
Размер поддона в плане, (мм) | Расход материалов на изготовление | Стоимость одного поддона,(руб.) | Средняя масса пакета по ОРП, (т) | Единовременные затраты на одну тонну груза (руб.) | ||||
пиломатериал | металл на скобы, (кг) | |||||||
доска | брус | всего | ||||||
1200×1600 | 0,12 | 0,03 | 0,15 | 2,5 | 311,0 | 1,2 | 259,2 | |
1600×2000 | 0,21 | 0,048 | 0,258 | 3,1 | 459,4 | 2,1 | 193,8 | |
1600×2600 | 0,32 | 0,06 | 0,38 | 4,1 | 520,0 | 2,8 | 185,7 | |
Примечание: ОРПОсетровский речной порт | ||||||||
Таблица 3
Характеристика пакетирующих стропов, деревянных подкладок и обвязок, применяемых для формирования " подъемов"
1.Проволочные стропы | |||||||
Длина (мм) | Ширина (мм) | Диаметр (мм) | Масса (кг) | Материал | Рабочая нагрузка (кг) | Стоимость (руб) | |
5000+10 | 4,2 | стальная проволока 8,0−1 (СТ-3сп или СТ-3пс) | 64,0 | ||||
2.Деревянные подкладки | |||||||
Длина (мм) | Ширина (мм) | Толщина (мм) | Объем (кв.м) | Материал | Стоимость (руб.) | ||
0,01 | доска необрезная лиственничных и хвойных пород | 10,8 | |||||
3. Проволочная обвязка | |||||||
Длина (мм) | Размер «подъема» в плане, (мм) | Диаметр, (мм) | Масса, (кг) | Материал | Стоимость, (руб.) | ||
8,2 | 1800×1800 | 1,84 | стальная проволока (СТ-3сп) | 27,8 | |||
4.Синтетические стропы | |||||||
Параметры | Единица измерения | Тип стропа | |||||
тип 1 | тип 2 | ||||||
1.Грузоподъмность | т | 1,1 | 1,1 | ||||
2.Масса | кг | 1,2 | 1,6 | ||||
3.Верхний строп Длина стропа | мм | замкнутая лента 2900+50 | замкнутая лента 2900+50 | ||||
4.Нижний строп Длина стропа | мм | замкнутая лента 2650+50 | замкнутая лента с кольцами 2550+50 | ||||
5.Материал ленты | ЛТК-50−2000 | ЛТК-50−2000 | |||||
Таблица 4
Динамика грузопотока пакетопригодных тарно-штучных грузов через Осетровский речной порт.
Поступление пакетопригодных грузов с железной дороги на воду, тыс. тонн | Года | |||||||||||
1.Транспортные пакеты, в том числе в ящиках, в мешках | 337,7 26,0 310,5 | 691,1 99,0 580,3 | 719,3 76,0 615,8 | 537,1 43,5 478,7 | 97,3 8,7 69,2 | 1,2 0,2 1,2 | 11,9 1,8 1,1 | 4,8 2,4 ; | 16,7 ; ; | 10,9 ; ; | 15,2 ; ; | |
2.Технологические пакеты, сформированные портом, в том числе в ящиках, в мешках | 371,2 153,7 180,4 | 212,9 145,6 63,2 | 151,1 108,4 40,3 | 101,1 46,4 53,5 | 23,1 9,2 13,3 | 32,7 1,9 27,2 | 52,1 13,9 27,2 | 44,0 10,1 23,6 | 28,3 6,7 21,6 | 32,6 7,4 25,2 | 40,9 2,5 34,1 | |
3.Всего пакетопригодных грузов | 708,9 | 904,0 | 870,4 | 658,2 | 120,4 | 33,9 | 64,0 | 48,8 | 45,0 | 43,5 | 56,1 | |
Таблица 5
Характеристика основных транспортных средств, используемых для перевозки непакетированных грузов в мешках.
1. Техническая характеристика основных типов речных судов. | ||||||||||||||
Типы судов и номера проектов | Класс речного регистра | Грузоподъемность, т | Габаритные размеры, м | Осадка, м | Вместимость, куб. м, кв. м | Размеры трюма (палубы) груз, м | Размеры люка, м | Мощ ность л.с. | Скорость км/час | |||||
длина | ширина | высота | груженый | порожняк | груженый | порожняк | ||||||||
Грузовые сухогрузные теплоходы | ||||||||||||||
Т/х-площадка Р-40 | О | 68,4 | 14,4 | 11,2 | 1,55 | 0,13/0,81 | ; | ; | ||||||
То же Р-40ТК | Р | 67,4 | 14,0 | 14,4 | 1,78 | 0,2/1,0 | ; | ; | ||||||
Контей-неровоз СК-2000 | Р | 72,9 | 14,3 | 15,2 | 1,5 | 0,2/1,2 | ; | ; | 19,5 | |||||
То же СК; 2000К | Р | 72,5 | 14,4 | 14,1 | 1,73 | 0,06/1,2 | ; | ; | 20,5 | |||||
Т/х-закрыт | М | 108,4 | 15,0 | 14,1 | 2,51 | 0,79/1,69 | 18,0×12,84 | 15,5×10,9 | 19,5 | |||||
То же Р-25А | О | 88,2 | 12,7 | 13,5 | 2,26 | 0,3/1,39 | 58,8×10 | 58,8×10 | ||||||
То же | О | 103,5 | 12,4 | 11,6 | 2,84 | 0,37/1,29 | 18,6×12 | 12,6×8,0 | 22,3 | |||||
То же Р-25Б | О | 97,3 | 12,7 | 14,0 | 2,44 | 0,24/1,57 | 67,2×9,97 | 67,2×9,9 | 19,5 | |||||
Несамоходные сухогрузные суда | ||||||||||||||
Баржа-площадка 942 | О | 66,2 | 14,0 | 3,5 | 1,6 | 0,4 | 55×11 | ; | ; | ; | ; | |||
Баржа с тентом 942Т | Р | 65,4 | 15,3 | 3,4 | 1,6 | 0,4 | 55×11 | ; | ; | ; | ; | |||
Баржа-площадка 16 800 | О | 102,7 | 17,5 | 6,9 | 2,2 | 0,67 | 1107,5 | 84×13,1 | ; | ; | ; | ; | ||
То же Р-56 | Р | 86,0 | 17,8 | 9,0 | 2,6 | 0,41 | 12,8×16,5 | ; | ; | ; | ; | |||
2. Техническая характеристика железнодорожного подвижного состава
Тип подвижного состава | Грузоподъемность, т | Длина вагона по оси автосцепки, м | Внутренние размеры, м | Размеры дверного проема, м | ||||
длина | ширина | высота боковой стенки | объем кузова вагона, куб. м | |||||
4-осный крытый | 14,7 | 13,8 | 2,76 | 2,79 | 120,0 | 2,0×2,26 | ||
То же | 14,7 | 13,8 | 2,76 | 2,40 | 106,0 | 2,0×2,26 | ||
То же | 14,7 | 13,43 | 2,65 | 2,40 | 90,0 | 1,83×2,13 | ||
3. Техническая характеристика автомобилей
Типы автомобилей | Грузоподъемность, т | Внутренние размеры, м | Объем кузова, куб. м | Площадь платформы, кв. м | |||
длина | ширина | высота | |||||
ГАЗ-51А | 2,5 | 3,87 | 6,35 | ||||
ГАЗ-52−03 | 2,5 | 4,40 | 8,10 | ||||
УРАЛ-355М | 3,5 | 4,24 | 7,33 | ||||
ГАЗ-53А | 4,0 | 5,56 | 8,17 | ||||
ЗИЛ-150 и 164 | 4,0 | 4,66 | 7,96 | ||||
ЗИЛ-130 и 130А1 | 5,0 | 5,98 | 8,73 | ||||
ЗИЛ-130Г-66 | 5,0 | 6,27 | 10,90 | ||||
УРАЛ-377 | 7,5 | 7,49 | 10,47 | ||||
МАЗ-200 | 7,0 | 6,70 | 11,16 | ||||
МАЗ-500 | 7,5 | 6,84 | 11,30 | ||||
Краз-219 и 257 | 12,0 | 11,79 | 14,31 | ||||
4. Техническая характеристика прицепов и полуприцепов | |||||||
Марка | Грузоподъем-ность, т | Собственная масса, т | Внутренние размеры платформы, мм | Погрузочная высота, мм | |||
длина | ширина | высота | |||||
прицепы общего назначения | |||||||
ГКБ-817В | 5,4 | 2,6 | |||||
ГКБ-817 | 5,5 | 2,5 | |||||
ГКБ-8328 | 6,3 | 2,7 | ; | ||||
ГКБ-8350 | 8,0 | 3,5 | |||||
МАЗ-8926 | 8,2 | 3,8 | |||||
ГКБ-8352 | 10,0 | 3,7 | |||||
ГКБ-8352−01 | 10,2 | 3,5 | ; | ||||
полуприцепы общего назначения | |||||||
КАЗ-9368 | 11,5 | 3,0 | |||||
КАЗ-9370−01 | 14,5 | 4,6 | |||||
МАЗ-9380 | 15,0 | 3,8 | |||||
МАЗ-9385 | 20,5 | 5,3 | |||||
МАЗ-9386 | 20,8 | 5,0 | |||||
МАЗ-9398 | 25,4 | 7,4 | |||||
Таблица 6
Характеристика перегрузочных машин, применяемых на доставке непакетированных грузов в мешках
1. Портальные краны | |||||||||
Обозначение крана | Грузо; подъемность, т | Вылет стрелы максим. (миним.), м | Колея портала, м | Скорости | Суммарная мощность электродвигателей, кВТ | ||||
подъема, м/мин | поворота, об/мин | измен. вылета, м/мин | передвижение /мин | ||||||
КПП-5−30−10,5 (З-ДА ИМ. Кирова) | 30(7) | 10,5 | 1,5 | 228,5 | |||||
КПП-5(6)-30−10,5 («Ганц») | 5(6) | 30(7) | 10,5 | 1,75 | 132,9 | ||||
КПП-10−32−10,5 («Абус») | 32(8) | 10,5 | 1,0 | 37,2 | |||||
КПП-10/20−32−10,5 («Альбатрос») | 10/20 | 16(10) | 10,5 | 1,6 | 63,0 | ||||
КПП-16/27,5−33/21−10,5 («Ганц») | 16/27,5 | 21(9) | 10,5 | 60/30 | 1,5 | 251,7 | |||
2. Плавучие краны | |||||||||
КПЛ-5−30 (з-да «Теплоход») | 30(8,5) | ; | 1,75 | ; | |||||
КПЛ-5−25 («Ганц») | 25(6) | ; | 2,0 | ; | |||||
3. Мостовые краны | ||||||||
Обозначение крана | Грузоподъем; ность, т | Пролет, м | Скорость м/мин | Суммарная мощность электродвигателей, кВТ | ||||
подъема | передвижение тележки | передвижение крана | ||||||
КМГ-5 | 19,5;25,5;31,5 | 40,7 | 32,3;32,3;37,3 | |||||
КМГ-10 | 19,5;25,5;31,5 | 80,4 | ||||||
4.Козловые краны | ||||||||
ККС-10 (вылет консоли 8 и 9 м) | 20 и 32 | 54,2 | ||||||
5.Краны на пневмоколесном ходу | ||||||||
Обозначение крана | Грузоподъем-ность, т | Вылет стрелы макс (мин.), м | Скорость | Суммарная мощность электро-двигателей, л.с. | ||||
подъема м/мин | поворота, об/мин | изменение вылета, м/мин | передви-жение, м/мин | |||||
КС-4362 (К-161) | 0,3/16 | 23 (3,7) | 50/11 | 0,5 | 2,8 | |||
КС-5363 (К-255) | 2,1/25 | 18,5 (3,5) | 0,3 | 1,5 | ||||
6. Погрузчики | |||||||||
Обозначение (модель) | Грузоподъем; ность, т | Высота подъема, м | Скорости | Габаритные размеры, м | Мощность двигателя, л.с. | ||||
подъема, м/мин | передви; жение, км/час | длина с вилами | ширина | высота с опущен-ными вилами | |||||
ЭП-1,0 (ЭП-103,106) | 4,5 | 2,5 | 0,93 | 1,5 | |||||
ЭП-2,0 (ЭП-2012,202) | 4,5 | 2,5 | 1,35 | 1,6 | |||||
ЭП-3,0 (ЭП-303) | 2,8 | 8,6 | 3,6 | 1,5 | 2,3 | 2,3 | |||
ЭП-5,0 (ЭП-501) | 4,5 | 6,0 | 3,9 | 1,55 | 3,1 | ||||
Тойота (Япония) | 1,5 | ; | ; | ; | ; | ||||
ТСМ (Япония) | 1,5 | 25,8 | 14,5 | ; | ; | ; | ; | ||
4,5 | 5,1 | 2,33 | 2,8 | ||||||
4,2 | 7,0 | 2,33 | 3,4 | ||||||
4043 М | 3,2 | 15−20 | 4,65 | 2,1 | 3,2 | ||||
4045 М | 15−25 | 2,25 | 3,3 | ||||||
7,2 | 15−20 | 5,95 | 2,25 | 3,4 | |||||
7,5 | 6,5 | 6,6 | 2,7 | 3,8 | |||||
Кальмар (Швеция) | 5,0 | ; | ; | 5,6 | 2,47 | 4,0 | ; | ||
Таблица 7
Характеристика грузовых и грузозахватных приспособлений, применяемых для перегрузки тарно-тучных грузов в мешках
Наименование, тип и назначение средств и приспособлений | Номер проекта | Грузо-подъем; ность, т | Габаритные размеры, мм | Застропка | Отстропка | Масса, кг | Примечание | |||
длина | ширина | высота | ||||||||
1 Поддон универсальный деревянный, предназначенный для формирования пакетов и блок-пакетов из тарно; штучных грузов | 4089 ОРП | 4,25 | ручная | ручная | ; | |||||
2 Поддон универсальный деревянный, предназначенный для формирования пакетов и блок-пакетов из тарно; штучных грузов ТУ 212 РСФСР 143−86 | 4,25 | ручная | ручная | ; | ||||||
3 Строп проволочный пакетирующий, предназначенный для формирования пакетов и блок-пакетов из тарно-штучных грузов ЦПКБ ТУ 212 РСФСР 169−87 | 1,4 | ; | ; | ; | 4,2 | Из проволоки диаметром 8 мм | ||||
4 Строп проволочный пакетирующий, предназначенный для формирования пакетов и блок-пакетов из тарно-штучных грузов ЦПКБ ТУ 212 РСФСР 169−87 | 0,7 | ; | ; | ; | 2,4 | Из проволоки диаметром 6 мм | ||||
5 Обвязочная проволока диаметром 6 мм | ; | ; | ; | ; | ; | ; | 2,02 | ; | ||
6 Обвязочная проволока диаметром 6 мм | ; | ; | ; | ; | ; | ; | 2,16 | ; | ||
7 Полуавтоматический захват к автопогрузчику для перегрузки груза пакетами в стропах (а.с № 1 439 063) | 3К-53 ОРП | 2,6 3,15 | ручная | автома-тическая | При ширине пакета 1800 мм | |||||
8 Крановый полуавтоматический захват для перегрузки груза пакетами и блок-пакетами в стропах (а.с№ 1 439 063) | 3К-45 ОРП | 5,0 | ручная | автома-тическая | ; | |||||
9 Крановый балочно-траверсный захват для перегрузки груза пакетами и блок-пакетами на поддонах | ОПР | 5,0 | ручная | ручная | Поддон 1600×2000 | |||||
Таблица 8
Характеристика крытых складов
Размеры склада | Площадь склада | Коэффициент использования площади склада для штучных грузов партии | Размеры склада, м | Площадь склада, м | Коэффициент использования склада для штучных грузов, партии | |||||
мелких | средних | крупных | мелких | средних | крупных | |||||
60×120 | 0,30 | 0,55 | 0,65 | 24×60 | 0,30 | 0,50 | 0,60 | |||
36×84 | 0,30 | 0,55 | 0,65 | 18×60 | 0,30 | 0,45 | 0,55 | |||
36×72 | 0,30 | 0,55 | 0,65 | 18×48 | 0,30 | 0,45 | 0,55 | |||
36×60 | 0,30 | 0,55 | 0,65 | 18×36 | 0,30 | 0,45 | 0,55 | |||
30×84 | 0,30 | 0,55 | 0,65 | 12×48 | 0,30 | 0,40 | 0,50 | |||
30×72 | 0,30 | 0,55 | 0,65 | 12×36 | 0,30 | 0,40 | 0,50 | |||
24×84 | 0,30 | 0,50 | 0,60 | 12×24 | 0,30 | 0,40 | 0,50 | |||
24×72 | 0,30 | 0,50 | 0,60 | ; | ; | ; | ; | ; | ||
Таблица 9
Варианты технологического процесса доставки непакетированного груза Осетрово-Якутск
Варианты технологического процесса перегрузки тарно-штучных грузов в мешках | Средства укрупнения «подъема» | Масса «подъема», т | Осетровский порт | Якутский порт | |||||||
вагон (размещение в вагоне) | склад (размещение на складе) | судно (размещение в судне) | судно (размещениена судне) | склад (размещение на складе) | автомашина (размещение на автомашине) | ||||||
вагонные работы | судовые работы | судовые работы | автомобильные работы | ||||||||
Поддон (1600×2000мм) | 1,8 | отдельные грузовые места в штабеле | готовый пакет | готовый пакет | расформирование пакета | формирование пакета | готовый пакет | готовый пакет | расформирование пакета | ||
Поддон (1600×2000мм) | 1,8 | отдельные грузовые места в штабеле | готовый пакет | готовый пакет | готовый пакет | готовый пакет | готовый пакет | готовый пакет | готовый пакет | ||
Проволочные стропы | 2,4 | отдельные грузовые места в штабеле | готовый пакет | готовый пакет | расформирование пакета | формирование пакета | готовый пакет | готовый пакет | расформирование пакета | ||
Проволочные стропы | 2,4 | отдельные грузовые места в штабеле | готовый пакет | готовый пакет | готовый пакет | готовый пакет | готовый пакет | готовый пакет | готовый пакет | ||
1.2 Общая характеристика существующих технологических процессов перегрузки непакетированных тарно-штучных грузов
Для выполнения перегрузочных работ отдельные подъемно-транспортные машины и оборудование на причале объединяют в общую схему механизации.
Под схемой механизации понимают совокупность подъемно-транспортных машин, вспомогательных устройств, объединенных в соответствии с характером и особенностями грузового потока, условиями производства перегрузочных работ на причале и предназначенных для перегрузки грузов по одному или нескольким вариантам.
При выборе схем механизации и подъемно-транспортного оборудования, входящего в ее состав, учитывают следующие общие соображения:
— схема механизации должна соответствовать рациональной структуре перегрузочного процесса на причале, определяющей количество, последовательность, содержание всех основных и вспомогательных операций и, следовательно, типы и характеристики машин, устройств и их расстановку;
— схема механизации должна обеспечивать необходимую пропускную способность причального фронта, складов и железнодорожных перегрузочных путей, позволяющую перерабатывать заданный грузооборот и производить обработку судов и вагонов в установленный срок; учитывая неравномерность подачи судов и вагонов под обработку, при проектировании схемы механизации должен быть, предусмотрен определенный резерв пропускной способности причала;
— перегрузочная установка должна отвечать современным требованиям технического процесса, давать возможность комплексно механизировать перегрузочные работы и автоматизировать управление всеми или частью машин, быть надежной и безопасной для обслуживания персонала;
— обеспечивать сохранность груза при его перемещении и не оказывать вредного воздействия на окружающую среду;
— схема механизации должна быть надежной в работе; не рекомендуется принимать сложные схемы, насыщенные большим количеством разнотипных машин и оборудования, так как это снижает надежность перегрузочных установок и усложняет управление ими и их эксплуатацию;
— если позволяют условия использовать полностью технические возможности машин, то следует отдать предпочтение одной высокопроизводительной перегрузочной установке на причале вместо большого числа менее производительных, так как такое решение в большинстве случаев требует меньших затрат, меньшего числа обслуживающего персонала и меньших эксплуатационных расходов;
— оборудование по возможности должно выбираться в первую очередь по действующей сетке перегрузочных машин, быть однотипным, стандартным;
— не оказывать отрицательного влияния на конструкцию причальной набережной и складов и не повышать чрезмерно их стоимость;
— перегрузочные машины должны быть однотипными, чтобы представлялась возможность в определенные периоды концентрировать перегрузочные средства на обработке одного судна и за счет этого ускорять обработку судов.
Принципиальная схема технологического процесса доставки непакетированного груза в мешках на линии Осетрово — Якутск выглядит следующим образом:
Груженый вагон устанавливается у рампы склада. Портовые рабочие открывают дверь вагона, толкая ее за скобу и откидную ручку, находясь при этом за полотном двери. При необходимости для открытия дверей можно применять ручной лом. Двое рабочих подносят и устанавливают между вагоном и рампой склада деревянный переходной трап. Слева или справа от дверного проема вагона автопогрузчик устанавливает стопу инвентарных грузовых площадок или поддонов. Грузовые площадки (поддоны) в стопке должны располагаться без смещения относительно друг друга, а высота стопки должна быть не более 1,5 метра.
Четверо рабочих берут верхнюю инвентарную грузовую площадку (поддон) из стопки и устанавливают ее на рампе напротив дверного проема вагона. Установку инвентарной грузовой площадки (поддона) перед дверным проемом можно произвести автопогрузчиком. Далее рабочие берут мешки, выносят их из вагона и укладывают на инвентарную грузовую площадку (поддон) в определенном порядке, формируя «подъем», при этом мешки в зависимости от их геометрической формы на инвентарной грузовой площадке (поддоне) укладываются в «перевязку» или стопками, предотвращая этим развал пакета. Разборка штабеля в вагоне производится уступами. Готовые «подъемы» автопогрузчик, оборудованный вилочным захватом, отвозит в склад, где портовые рабочие производят разборку «подъема» и укладывают мешки в штабель уступами.
Для погрузки непакетированного груза в мешках на судно необходимо, на складе с помощью инвентарной грузовой площадки (поддона) сформировать «подъем», как это описано выше. Затем автопогрузчик транспортирует «подъем» на причал. На причале двое портовых рабочих застрапливают «подъем» балочно-траверсным захватом. По команде сигнальщика крановщик поднимает «подъем» на 300 мм от отметки территории. Убедившись в надежности застропки пакета, стропальщики отходят в безопасное место, сигнальщик подает команду на дальнейший подъем пакета. Кран переносит «подъем» в судно, где мешки расформировываются в штабель без уступа. После расформирования «подъема» по команде сигнальщика крановщик поднимает инвентарную грузовую площадку «подъем» на причал.
Размещение груза на судне в каждом конкретном случае определяется планом загрузки судна.
Выгрузка груза из судна и размещение его на складе в порту Якутск, производится в обратном порядке.
При формировании технологического пакета вместо инвентарной грузовой площадки используется поддон размером 1600×2000мм. Готовые пакеты автопогрузчик, оборудованный съемными удлинителями вил, отвозит в склад и устанавливает их там, в три яруса. В начале и в конце штабеля в третьем ярусе делается уступ в один пакет.
Погрузка пакетов на поддонах на судно производится следующим образом:
На причале двое портовых рабочих застрапливают пакет балочно-траверсным захватом. По команде сигнальщика крановщик поднимает пакет на 300 мм от отметки территории. Убедившись в надежности застропки пакета, стропальщики отходят в безопасное место, сигнальщик подает команду на дальнейший подъем пакета. Кран переносит пакет в судно. Двое рабочих, находящиеся на судне, при помощи шестов помогают крановщику установить пакет в штабель.
Подходить непосредственно к пакету рабочие могут только тогда, когда устранена раскачка пакета, и он находится на высоте не более 1 метра от уровня площадки, на которой стоят стропальщики.
Пакет на судне устанавливается в 3 яруса, причем, между рядом стоящими пакетами должен быть зазор в 200 мм, который необходим для беспрепятственной отстропки (застропки) пакета.
Рабочие вытаскивают балки захвата из уступов поддона и кладут их на верх пакета. По команде сигнальщика крановщик поднимает освободившийся захват.
Выгрузка груза из судна и хранение его на складе в порту Якутск, производится в обратном порядке.
При формировании технологических пакетов вместо поддонов широко используются проволочные стропы. В этом случае против дверного проема вагона на рампе склада устанавливается инвентарная деревянная площадка размером 1600×2000мм. В имеющиеся на площадке прорези укладывается два проволочных стропа. Концы стропов выравниваются относительно площадки по мерной рейке. Рабочие выносят из вагона мешки укладывают их на проволочные стропы.
Общая масса формируемого пакета не должна превышать 2,5 т. Для предотвращения развала пакета во время транспортировки верхний ряд мешковобвязывается проволокой диаметром 4−6 мм, после чего свободные концы проволочных стропов поднимают вверх.
Застропка пакета производится полуавтоматическим захватом. При застропке захват устанавливается над пакетом так, чтобы между ними был зазор в пределах 5 см. Рабочие производят застропку пакета, пропуская грузовые цепи захвата между ветвями стропов и набрасывая зацепы на штыри захвата, после чего уходят в безопасное место. Водитель автопогрузчика приподнимает пакет и, убедившись в правильности застропки, транспортирует его на склад. Отстропка пакета производится автоматически, путем полного опускания захвата на пакет.
Хранение пакета с гигроскопическими грузами в крытом складе производится на специальном секционном подтоварнике, представляющем собой отдельные секции размером 500×500×300 мм, изготовленные их сухого пиломатериала. Под один пакет устанавливается 9 секций. Установку секций производит один портовый рабочий. Хранение пакетов с грузами, не боящимися подмочки, производится в складе без подтоварника.
В штабеле пакеты автопогрузчиком устанавливаются в три яруса, с уступом в третьем ярусе на один пакет с двух сторон по направлению штабелирования.
Доставка пакета со склада на причал производится автопогрузчиками.
Застропку пакетов на складе производит 1 портовый рабочий. Подъем и спуск портового рабочего на штабель производится по приставной леснице.
Перегрузка пакетов на судно осуществляется портальным краном, оснащенным полуавтоматическим захватом. Застропку пакетов на причале производят двое рабочих аналогично застропке к полуавтоматическому захвату автопогрузчика. По команде сигнальщика крановщик делает пробный подъем пакета на 300 мм от оперативной площадки. Убедившись в надежности застропки, стропальщики отходят в безопасное место, сигнальщик подает команду на дальнейший подъем пакета. Кран переносит пакет на судно. Рабочий, находящийся на судне, при помощи шеста помогает крановщику установить пакет в штабель. Подходить непосредственно к пакету рабочий может только тогда, когда устранена раскачка пакета и он находится на высоте не более 1 метра от уровня площадки. Отстропка пакета производится автоматически, путем полного опускания захвата на пакет. При подъеме порожнего захвата краном, стропальщик следит за тем, чтобы грузовые цепи захвата свободно проходили между ветвями проволочных стропов. Концы стропов, возвышающиеся над пакетом, стропальщик пригибает к верхней плоскости пакета.
Пакеты в судне устанавливаются в 3−4 яруса, ровными рядами, без перекосов, вплотную друг к другу. Второй ярус пакетов устанавливается после полного заполнения первого яруса.
Пакеты в судне могут расформировываться в мешки и поштучно укладываться в штабель; проволочные стропы возвращаются в склад для последующих вагонных операций.
Размещение груза на судне в каждом конкретном случае определяется планом загрузки судна.
Выгрузка груза из судна и размещение его на складе в порту Якутск, производится в обратном порядке.
Применение в мировой практике, в качестве средств укрупнения «подъемов», других стропов (в основном из синтетических материалов) ограничено из-за их высокой стоимости и малого срока службы.
Различные типы грузовых сеток (в качестве средств «подъема») нашли применение в основном при перевозке тарно-штучных грузов авиационным транспортном.
Использование в перегрузочных процессах флетов, ролл-трейлеров и др., требует специальных перегрузочных машин.
Применение синтетических стропов, грузовых сеток, флетов, ролл-трейлеров в данном проекте не рассматривается.
1.3 Характеристика материально-технической базы по перевозке и перегрузке непакетированных грузов в мешках в Ленском бассейне
Материально-техническая база транспортных предприятий и грузополучателей Ленского бассейна по доставке непакетированных тарно-штучных грузов в мешках однообразна (по типу перегрузочных машин, транспортных средств и складских помещений) и отличается только масштабами и некоторыми конструктивными элементами.
Характеристика основных транспортных средств, применяемых на доставке непакетированных грузов в мешках, представлена в таблице 5.
Характеристика перегрузочных машин, применяемых на погрузке грузов в мешках в пункте перевалки, портах-пристанях бассейна и на базах грузополучателей дана в таблице 6.
Характеристика грузовых и грузозахватных приспособлений на грузовых работах с тарно-штучными грузами в мешках, показана в таблице 7.
Характеристика складов, используемых для хранения грузов в мешках, дана в таблице 8.
2. Разработка вариантов технологического процесса доставки непакетированных грузов в мешках и норм перегрузочных работ
2.1 Исходные данные и принимаемые ограничения технологического процесса доставки груза
С целью обеспечения сопоставимых условий для всех вариантов технологического процесса доставки непакетированного груза в мешках на линии Осетрово — Якутск принимаются следующие исходные данные:
— Груз непакетированный в мешках относится к классу груза М- 50 по 50 кг;
— Навигационный грузооборот -130 тыс. т;
— Продолжительность физической навигации 120 суток;
— Срок хранения груза на складе пять суток.
— Коэффициент прохождения груза через склад 100%
— Кран портальный (грузоподъемность 6 тонн)
— Судно — Проект Р-25А
— Среднее расстояние по варианту «вагон-склад» — 80 м.
— Среднее расстояние по варианту «склад-судно» — 200 м.
— Продолжительность рабочего дня — 7 ч.
— Количество смен в сутках — две смены
— Длина причала — 110 м.
— Высота поддона — 0,18 м.
— Высота пакета — 1,40 м.
— Масса подъёма — 2,4 т.
2.2 Варианты технологического процесса доставки непакетированного непакетированного груза в мешках на линии ОсетровоЯкутск
Рассматриваются следующие варианты технологического процесса доставки непакетированных грузов в мешках на линии Осетрово — Якутск:
Вариант 1.
На вагонных работах «подъем» формируется на поддоне 1600?2000 мм. На складе груз хранится готовыми пакетами, а в судне расформировывается, поддоны возвращаются в склад для дальнейшего использования на вагонных работах.
Вариант 2.
Отличается от предыдущего варианта тем, что груз доставляется в Якутский порт пакетами на поддонах.
Вариант 3.
" Подъем" у вагона формируется в проволочных стропах массой 2,4 т, в складе груз хранится готовыми пакетами, а при погрузке в судно пакеты расформировываются.
Вариант 4.
" Подъем", сформированный у вагона в проволочных стропах следует в Якутский порт без расформирования.
Перегрузка груза в Якутском речном порту по каждому варианту технологического процесса доставки груза осуществляется в обратной последовательности.
Варианты технологического процесса доставки непакетированного груза в мешках по линии Осетрово — Якутск, представлены в таблице 9.
2.3 Расчет норм перегрузочных работ по вариантам технологического процесса доставки груза
2.3.1 Среднесуточный грузооборот
Среднесуточный грузооборот определяется по формуле, т:
(1) | ||
где — навигационный грузооборот, т;
— коэффициент неравномерности прибытия груза, (приложение 2 [4.);
— продолжительность навигационного периода, сут.
Для первого варианта технологического процесса определяем следующим образом:
2.3.2 Потребная емкость склада
Емкость склада определяется по формуле, т:
(2) | ||
где — коэффициент прохождения груза через склад; - время хранения груза на складе, сут. Для первого варианта технологического процесса определяем следующим образом:
2.3.3 Потребная площадь склада
Потребная площадь склада определяется по формуле, м2:
(3) | ||
где — допустимая нагрузка на 1 м2 площади склада;
— коэффициент использования полезной площади склада приложение.
Фактическая нагрузка на 1 м2 площади склада определяется графо-аналитическим способом. Фактические нагрузки на квадратный метр площади склада по вариантам технологического процесса доставки груза приведены в таблице 10. Для первого варианта технологического процесса определяем следующим образом:
Потребные площади по остальным вариантам технологического процесса доставки груза даны в таблице 10.
2.3.4 Расчет производительности перегрузочных машин
Техническая производительность перегрузочной машины определяется по формуле, т/час:
(4) | ||
где — масса груза в одном подъеме, т;
(5) | ||
где — количество грузовых мест в «подъеме», шт; - масса одного места, т;
Таблица 10
Определение фактической нагрузки на квадратный метр площади склада и потребной площади по вариантам технологического процесса доставки груза.
Варианты размещения груза на складе | Габаритные размеры «подъема» или технологического пакета, м | Площадь, занимаемая грузом, «подъема» или технологического пакета в складе с учетом зазоров, кв. м | Количество мешков по высоте, штук | Количество мешков в ряду, «подъема» или технологического пакета, штук | Масса одного мешка, т | Общая масса груза в складе на площади одного «подъема» или технологического пакета, т | Нагрузка на 1 кв. м, т/кв.м | Коэффициент использования полезной площади склада, м | Потребная площадь склада, кв. м | |
На поддонах | 2000×1600×1580 | 3,74 | 0,05 | 7,2 | 2,4 | 0,70 | 3869,0 | |||
В проволочных стропах | 1800×1800×1400 | 3,36 | 0,05 | 7,2 | 2,6 | 0,80 | 3385,4 | |||
— продолжительность цикла работ машины по перегрузке одной порции груза, (сек.) определяется по формуле:
(6) | ||
где — время на захват или застропку груза;
— время на разворот перегрузочной машины с грузом;
— время на доставку груза;
— время на отстропку груза и укладку в штабель;
— время на разворот перегрузочной машины без груза.
Например:
Для ОРП на судовых работах по варианту склад-судно первого технологического процесса для автопогрузчика:
= 13 сек. (карта 54, позиция 2б [3]) Время на захват вилами порожнего поддона автопогрузчиком;
= 27 сек. Время на доставку порожнего поддона на склад (расчетным путем);
= 24 сек. Установка порожнего поддона на складе (карта 54, позиция 15б [3]);
= 18 сек. Время на захват груженого поддона автопогрузчиком (карта 54, позиция 1б [3]);
= 17 сек. Разворот автопогрузчика с грузом (карта 54, позиция 30б [3]);
= 100 сек. Ход автопогрузчика с грузом 200 м (карта 74, позиция 15б [3]);
= 24 сек. Время на установку груженого поддона под краном (карта 54, позиция 15б [3]);
=15 сек. Время разворота автопогрузчика без груза (карта 54, позиция 31б [3]);
=89 сек. Ход автопогрузчика без груза 200 м (карта 74, позиция 15д [3])
Для крана:
= 42 сек. Застропка груженого поддона краном (карта 19, позиция 36а .3.);
= 45 сек. Ход крана с грузом (90−20м) (карта 71, позиция 8е .3.);
= 37 сек. Отстропка груженого поддона вне штабеля на судне (карта 19, позиция 33б .3.);
= 41 сек. Ход крана без груза (90−20м) (карта 71, позиция 40е .3.);
= 8 сек. Отстропка порожнего поддона под краном (карта 19, позиция 14б .3.)
Элементы цикла принимаются по нормативам времени на перегрузочные работы .
Масса груза в одном подъеме по 1 и 2 вариантам технологического процесса:
Продолжительности циклов работ перегрузочных машин по вариантам технологического процесса доставки груза сведены в таблицу 11. Для первого варианта технологического процесса доставки груза по ОРП сменная производительность портального крана по варианту работы склад-судно, т/час:
(7) | ||
где — оперативное время работы перегрузочной установки, час. (принимается по нормативам времени .3.)
Для первого варианта технологического процесса часовая производительность перегрузочной машины, т/смена:
Производительность перегрузочной машины за сутки, т/сут
(8) | ||
где — количество рабочих смен в сутки.
Для первого варианта технологического процесса, определяется:
Часовые, сменные и суточные производительности перегрузочных машин по вариантам технологического процесса представлены в таблицах 12, 13.
2.3.5 Расчет минимального количества перегрузочных машин на причале
Минимальное количество перегрузочных машин на причале, ед.:
(9) | ||
где 1,1- коэффициент, учитывающий затраты времени на расстановку и перестановку линии;
— расчетный суточный грузооборот причала;
= 1,05 — коэффициент, учитывающий затраты времени на плановый ремонт перегрузочных машин;
— расчетная производительность перегрузочной установки;
— продолжительность работы перегрузочной установки в сут., час.
Для ОРП по варианту склад-судно для 3 и 4 варианта технологического процесса минимальное количество перегрузочных машин на причале, единиц:
Таблица 11
Продолжительность циклов работы перегрузочной техники по вариантам технологического процесса.
Элементы цикла | № карты Позиция (3) | Время операций, сек | Время на грузовые операции по вариантам технологического процесса доставки груза | ||||
Осетровский речной порт. Вариант вагон-склад | |||||||
1.Время на захват вилами порожнего поддона автопогрузчиком | 54−2б | ; | ; | ||||
2.Доставка порожних поддонов к вагону (6 штук) | расчетный | ; | ; | ||||
3.Установка порожних поддонов у вагона | 54−15б | ; | ; | ||||
4.Время на захват вилами груженого поддона автопогрузчиком | 54−1б | ; | ; | ||||
5.Разворот автопогрузчика с грузом | 54−30б | ||||||
6.Ход автопогрузчика с грузом 80 м | 74−8б | ||||||
7.Время на установку груженого поддона в складе | 54−15б | ; | ; | ; | ; | ||
8.Время на установку груженого поддона на складе в штабель | 54−16б | ; | ; | ||||
9.Разворот автопогрузчика без груза | 54−31б | ||||||
10.Ход автопогрузчика без груза 80 м | 74−8б | ||||||
11.Застропка технологического пакета в проволочных стропах у вагона | хронометражный | ; | ; | ||||
12.Время на установку в штабель и отстропку технологического пакета на складе | хронометражный | ; | ; | ||||
Всего | ; | ; | |||||
Осетровский речной порт. Вариант склад-судно | |||||||
1.Время на захват вилами порожнего поддона автопогрузчиком | 54−2б | ; | ; | ||||
2.Доставка порожних поддонов (6 штук) на склад | расчетным | ; | ; | ||||
3.Установка порожних поддонов на складе | 54−15б | ; | ; | ||||
4.Время на захват вилами груженого поддона автопогрузчиком | 54−1б | ; | ; | ||||
5.Разворот автопогрузчика с грузом | 54−30б | ||||||
6.Ход автопогрузчика с грузом 200 м | 74−15б | ||||||
7.Время на установку груженого поддона под краном | 54−15б | ; | ; | ||||
8.Время разворота автопогрузчика без груза | 54−31б | ||||||
9.Ход автопогрузчика без груза 200 м | 74−15д | ||||||
10.Застропка технологического пакета в проволочных стропах в штабеле склада автопогрузчиком | хронометражный | ; | ; | ||||
11.Отстропка технологического пакета в проволочных стропах под краном | хронометражный | ; | ; | ||||
Всего | ; | ; | |||||
12.Застропка груженого поддона краном | 19−36а | ; | ; | ||||
13.Ход крана с грузом (90 градусов-20м) | 71−8е | ||||||
14.Отстропка груженого поддона на судне и установка в штабель | 19−17б | ; | ; | ; | |||
15.Отстропка груженого поддона вне штабеля на судне | 19−33б | ; | ; | ; | |||
16.Ход крана без груза (90 градусов-20м) | 71−40е | ||||||
17.Отстропка порожнего поддона на причале под краном | 19−14б | ; | ; | ; | |||
18.Застропка технологического пакета в проволочных стропах под краном | хронометражный | ; | ; | ||||
19.Отстропка технологического пакета на судне и установка в штабель | хронометражный | ; | ; | ; | |||
20.Отстропка технологического пакета на судне | хронометражный | ; | ; | ; | |||
Всего | ; | ; | |||||
Якутский речной порт. Вариант судно-склад | |||||||
1.Застропка порожних поддонов краном | 19−14а | ; | ; | ; | |||
2.Ход крана без груза (90 градусов-20м) | 71−40е | ||||||
3.Отстропка порожних вагонов на судне | 19−10б | ; | ; | ; | |||
4.Застропка груженого поддона на суде | 19−2а | ; | ; | ; | |||
5.Застропка груженого поддона на судне из штабеля | 19−17а | ; | ; | ; | |||
6.Ход крана с грузом (90 градусов- 20м) | 71−8е | ||||||
7.Отстропка груженого поддона под краном | 19−6б | ; | ; | ||||
8.Застропка технологического пакета в проволочных стропах на судне | хронометражный | ; | ; | ; | |||
9.Застропка технологического пакета в проволочных стропах на судне из штабеля | хронометражный | ; | ; | ; | |||
10.Отстропка технологического пакета в проволочных стропах под краном | хронометражный | ; | ; | ||||
Всего | ; | ; | |||||
11.Время на захват вилами груженого поддона под краном автопогрузчиком | 54−16 | ; | ; | ||||
12.Разворот автопогрузчика с грузом | 54−30б | ||||||
13.Ход автопогрузчика с грузом 200 м | 74−15б | ||||||
14.Время на установку груженого поддона на складе | 54−15б | ; | ; | ; | ; | ||
15.Время на установку груженого поддона в штабель на складе | 54−16б | ; | ; | ||||
16.Разворот автопогрузчика без груза | 54−31б | ||||||
17.Ход автопогрузчика без груза 200 м | 74−15б | ||||||
18.Застропка технологического пакета в проволочных стропах под краном автопогрузчиком | хронометражный | ; | ; | ||||
19.Отстропка технологического пакета в проволочных стропах в штабель на складе | хронометражный | ; | ; | ||||
Всего | ; | ; | |||||
Якутский порт. Вариант склад-автомашина | |||||||
1.Время на захват вилами порожнего поддона автопогрузчиком | 54−2б | ; | ; | ; | ; | ||
2.Доставка порожних поддонов (6 штук) на склад | расчетный | ; | ; | ; | ; | ||
3.Установка порожнего поддона на складе | 54−15б | ; | ; | ; | ; | ||
4.Время на захват груженого поддона вилами на складе автопогрузчиком | 54−1б | ; | ; | ; | ; | ||
5.Время на захват груженого поддона вилами со штабеля склада автопогрузчиком | 54−3б | ; | ; | ||||
6.Разворот автопогрузчиком с грузом | 54−30б | ||||||
7.Ход автопогрузчика с грузом (10м) | 74−1б | ||||||
8.Время на установку груженого поддона на рампе склада | 54−15б | ; | ; | ; | |||
9.Время на установку груженого поддона на автомобиль в штабель | 19−8б | ; | ; | ; | |||
10.Разворот автопогрузчика без груза | 54−31б | ||||||
11.Ход автопогрузчика без груза (10м) | 74−1б | ||||||
12.Застропка технологического пакета в проволочных стропах со штабеля склада | хронометражный | ; | ; | ||||
13.Отстропка технологического пакета в проволочных стропах на рампе склада | хронометражный | ; | ; | ; | |||
14.Отстропка технологического пакета в проволочных стропах на автомашину и установка в штабель | хронометражный | ; | ; | ; | |||
Всего | ; | ; | |||||
Принимаем к расчету 2 перегрузочные машины.
Минимально необходимое число машин (технологических линий) на обработку одного судна необходимо проверить из условия обеспечения действующих судо-часовых норм .6. с увеличением их на перспективу на 15−20%. Судо-часовая норма для данного рода груза с увеличением ее на перспективу на 15% составляет 36 т/час, что соответствует поставленному условию.
2.3.6 Максимально возможная механовооруженность причала
Максимально возможное по технологическим условиям число перегрузочных машин на обработке одного судна — (максимально возможная механовооруженность причала) для портальных кранов подбирается по данным таблицы. Принимаем три портальных крана.
2.3.7 Расчет числа перегрузочных машин, работающих совместно с фронтальной машиной в одной технологической линии
Число машин, работающих совместно с фронтальной машиной в одной технологической линии, единиц:
(10) | ||
где — производительность фронтальной машины, т/час;
— производительность тыловой машины, т/час.
Например: Для ОРП по варианту склад-судно для первого варианта технологического процесса:
Таблица 12 доставка непакетированный груз флот
Часовая производительность перегрузочных машин и потребное количество портовых рабочих на одну технологическую линию
Варианты технологического процесса доставки груза | Масса пакета , т | Кран | Погрузчик | Количество необходимых погрузчиков на 1 технологическую линию для работы 1 крана Пк, ед. | Количество портовых рабочих, чел | ||||||
Цикл работы, Тц, сек | Часовая произво-дительность , Рч, т/час | Цикл работ, Тц сек | Часовая произво-дительность, Рч т/час | ||||||||
Формирование пакета по вариантам | Застропка и отстропка по вариантам | Расформирование пакета по вариантам | всего | ||||||||
Осетровский речной порт. Вариант вагонсклад | |||||||||||
1,8 | ; | 27,1 | ; | ; | ; | ; | |||||
1,8 | ; | 27,1 | ; | ; | ; | ; | |||||
2,4 | ; | 44,8 | ; | ; | ; | ; | |||||
2,4 | ; | 44,8 | ; | ; | ; | ; | |||||
Осетровский речной порт. Вариант склад-судно | |||||||||||
1,8 | 37,5 | 19,8 | ; | ||||||||
1,8 | 35,2 | 19,8 | ; | ; | |||||||
2,4 | 60,8 | 29,7 | ; | ||||||||
2,4 | 59,2 | 29,7 | ; | ; | |||||||
Якутский речной порт. Вариант судно-склад | |||||||||||
1,8 | 34,5 | 23,1 | ; | ||||||||
1,8 | 30,9 | 23,1 | ; | ; | |||||||
2,4 | 60,8 | 28,9 | ; | ||||||||
2,4 | 55,4 | 28,9 | ; | ; | |||||||
Якутский речной порт. Вариант склад — автомобиль | |||||||||||
1,8 | ; | 57,9 | ; | ; | ; | ; | |||||
1,8 | ; | 48,4 | ; | ; | ; | ; | |||||
2,4 | ; | 72,0 | ; | ; | ; | ||||||
2,4 | ; | 70,8 | ; | ; | ; | ||||||
Таблица 13
Сменная производительность перегрузочных машин и их потребность по вариантам технологического процесса, потребное количество портовых рабочих
Вариант техноло-гического процесса доставки груза | Часовая производитель-ность, Т/час | Опера-тивное время, Топ, час | Сменная производ., Рсм, т/см | Кол-во рабо-чих смен в сут., п см | Производ. перегруз. машин за сутки Р сут., т/сут | Миним. кол-во Гл. автом. Пу, ед | Потреб-ное кол-во тыл. машин П т.м., ед. | Количество портовых рабочих по вариантам работ | ||||||
рабоч | Меха-низа-торов | Всего | ||||||||||||
Гл. маш. | Тыл. маш. | Гл. маш. | Тыл. маш. | |||||||||||
Гл. маш. | Тыл. Маш. | |||||||||||||
Осетровский речной пот. Вариант вагон — склад | ||||||||||||||
27,1 | ; | 5,5 | 149,1 | ; | 2,0 | 298,2 | ; | ; | ||||||
27,1 | ; | 5,5 | 149,1 | ; | 2,0 | 298,2 | ; | ; | ||||||
44,8 | ; | 5,5 | 246,4 | ; | 2,0 | 492,8 | ; | ; | ||||||
44,8 | ; | 5,5 | 246,4 | ; | 2,0 | 492,8 | ; | ; | ||||||
Осетровский речной порт. Вариант склад-судно | ||||||||||||||
37,5 | 19,8 | 5,8 | 218,6 | 115,4 | 2,0 | 437,2 | 230,8 | |||||||
35,2 | 19,8 | 6,1 | 215,8 | 121,4 | 2,0 | 431,6 | 242,8 | |||||||
60,8 | 29,7 | 5,8 | 354,5 | 173,2 | 2,0 | 709,0 | 346,4 | |||||||
59,2 | 29,7 | 6,1 | 362,9 | 182,1 | 2,0 | 725,8 | 364,2 | |||||||
Якутский речной порт. Вариант судносклад | ||||||||||||||
34,5 | 23,1 | 5,8 | 201,1 | 134,7 | 2,0 | 402,2 | 269,4 | |||||||
30,9 | 23,1 | 6,1 | 189,4 | 141,6 | 2,0 | 378,8 | 283,2 | |||||||
60,8 | 28,9 | 5,8 | 354,5 | 168,5 | 2,0 | 709,0 | 337,0 | |||||||
55,4 | 28,9 | 6,1 | 339,6 | 177,2 | 2,0 | 679,2 | 354,4 | |||||||
Якутский речной порт. Вариант склад-автомашина | ||||||||||||||
57,9 | ; | 5,5 | 318,5 | ; | 2,0 | 637,0 | ; | ; | ||||||
48,4 | ; | 5,5 | 266,2 | ; | 2,0 | 532,4 | ; | ; | ||||||
72,0 | ; | 5,5 | 396,0 | ; | 2,0 | 792,0 | ; | ; | ||||||
70,8 | ; | 5,5 | 389,4 | ; | 2,0 | 778,8 | ; | ; | ||||||
Принимаем 2 машины.
Расчетные данные потребности перегрузочных машин по вариантам работ и вариантам технологического процесса доставки груза представлены в Таблице 13.
2.3.8 Общее время обслуживания судна на причале
Общее время обслуживания судна на причале, ч:
(11) | ||
где — время грузовой обработки судна, ч;
— вспомогательное время обслуживания судна у причала, ч.
(12) | ||
где — количество груза в судне, т;
— коэффициент учета дополнительных работ, не предусмотренных нормами (для смены 7 часов = 1,1);
— коэффициент, учитывающий время на техническое обслуживание машин, принимаемый для крюковых кранов- 1,2;
— число фронтальных машин, ед.;
— часовая производительность машин, т/час.
Вспомогательное время обслуживания судна у причала () ч, зависит от типа судна, вида груза, направления грузопотока и другого. Для наиболее распространенных типов судов и видов грузов принимается, укрупнено, по Приложению 9 4.
Для грузового теплохода грузоподъемностью 1001−1800 принимаем 1 час 48 минут или 1,8 часа.
Количество груза в судне для каждого варианта технологического процесса доставки определено графо-аналитическим способом.
Время грузовой обработки судна () для ОРП по первому варианту технологического процесса, час:
Общее время обслуживания судна у причала, час:
Расчетные данные эксплуатационной грузовместимости судна и общего времени обслуживания судна на причале по вариантам технологического процесса показаны в таблице 14.
2.3.9 Определение числа рабочих комплексной бригады, участвующих в перегрузочном процессе
В технологическом процессе доставка непакетированного груза в мешках, перегрузочные работы в зависимости от варианта работ и условий (перегрузка «подъемами» или технологическими пакетами) могут относится к ручным, механизированным и комплексно-механизированным работам.
Состав механизаторов определяется числом различных перегрузочных машин в механизированной линии. Количество портовых рабочих на каждой операции технологического процесса зависит от конкретно выполняемой работы, захватных приспособлений и так далее.
Потребное количество портовых рабочих по технологическим линиям и их расстановка по операциям всех вариантов технологического процесса дано в таблице 13.
2.3.10 Расчет продолжительности работы перегрузочных машин и затрат труда для выполнения навигационного грузооборота
Количество часов работы перегрузочных машин на выполнение навигационного грузооборота определяется по формуле, час:
(13) | ||
Например:
Для ОРП по варианту склад-судно по первому варианту технологического процесса доставки груза, число часов работы портального крана составит:
Таблица 14
Эксплуатационная грузовместимость судна и общее время обслуживания по вариантам технологического процесса
Варианты технологического процесса | Часовая производительность фронтальной машины, т/час | Число фронтальных машин П, ед | Количество груза в судне, т | Время грузовой обработки судна, час | Вспомогательное время обслуживания судна на причале, час | Общее время обслуживания судна на причале, час | |
Осетровский речной порт | |||||||
37,5 | 1333,6 | 23,5 | 1,8 | 25,3 | |||
35,2 | 1022,4 | 19,2 | 1,8 | 21,0 | |||
60,8 | 1333,6 | 14,5 | 1,8 | 16,3 | |||
59,2 | 1317,6 | 14,7 | 1,8 | 16,5 | |||
Якутский речной порт | |||||||
34,5 | 1333,6 | 25,5 | 1,8 | 27,3 | |||
30,9 | 1022,4 | 14,6 | 1,8 | 16,4 | |||
60,8 | 1333,6 | 14,5 | 1,8 | 16,3 | |||
55,4 | 1317,6 | 15,7 | 1,8 | 17,5 | |||
Затраты труда в человеко-сменах на выполнение навигационного грузооборота определяются по формуле, чел. см:
(14) | ||
где — выработка одного рабочего комплексной бригады, определяется по формуле, т/смену:
(15) | ||
где — число рабочих в технологической схеме, чел.
Например:
Для ОРП по варианту работ склад-судно по первому варианту технологического процесса доставки груза, затраты труда в человеко-сменах на выполнение навигационного грузооборота составят:
Расчетные данные по продолжительности работы перегрузочных машин и затрат труда на выполнение навигационного грузооборота по вариантам технологического процесса приведены в таблице 15.
2.3.11 Расчет комплексных норм выработки и времени
Комплексная норма выработки определяется по формуле, т/см:
(16) | ||
гдевремя основной оперативной работы в течение смены, час.;
— продолжительность цикла перегрузочной машины, сек.;