Разработка процесса формообразования фасонных винтовых поверхностей инструментов на основе применения стандартных концевых и торцевых фрез
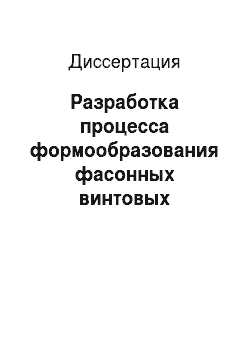
Наиболее распространенный способ обработки фасонных винтовых канавок предусматривает в качестве режущего инструмента фасонную дисковую фрезу. Установка инструмента при обработке детали с винтовой поверхностью определяется относительным положением их осей и характеризуется в общем случае следующими параметрами: у/ — углом (или величиной Г), определяющим положение точки скрещивания осей инструмента… Читать ещё >
Содержание
- Принятые обозначения
- Глава 1. Анализ научно-технической литературы по теме исследования
- 1. 1. Анализ направлений исследований проводённых другими авторами
- 1. 1. 1. Винтовые поверхности
- 1. 1. 2. Анализ направлений развития методов проектирования инструментов для обработки фасонных винтовых поверхностей
- 1. 2. Методы и инструменты для обработки фасонных, в том числе винтовых поверхностей, обоснование необходимости их использования при фрезеровании винтовых поверхностей деталей
- 1. 3. Анализ функциональных связей как между факторами, так и между факторами и показателями процесса формообразования винтовых поверхностей концевыми фрезами
- 1. 4. Постановка цели и задач исследования
- 1. 1. Анализ направлений исследований проводённых другими авторами
- Глава 2. Решение задачи определения профиля стружечной канавки инструмента при известной форме формообразующего инструмента
- 2. 1. Формы профиля винтовых стружечных канавок различных инструментов
- 2. 1. 1. Математическая модель профиля стружечной канавки концевой фрезы
- 2. 1. 2. Математическая модель профиля стружечной канавки сверла
- 2. 2. Форма зубьев концевых фрезы
- 2. 2. 1. Угол наклона винтовых зубьев со концевой фрезы
- 2. 2. 2. Число зубьев концевой фрезы
- 2. 3. Способ формообразования стружечный канавок инструментов. Параметры установки формообразующего инструмента
- 2. 4. Разработка метода решения задачи определения профиля стружечных канавок при известной форме формообразующего инструмента
- 2. 5. Разработка метода определения размеров толщин срезаемых слоев и построение схемы резания при обработки винтовых стружечных канавок стандартными фрезами прямого профиля
- 2. 6. Выводы по главе
- 2. 1. Формы профиля винтовых стружечных канавок различных инструментов
- Глава 3. Программная реализация модели процесса обработки винтовых поверхностей инструментом с прямолинейными режущими кромками
- 3. 1. Разработка и исследование модели обработки стружечной канавки концевой фрезы в среде T-flex (решение обратной задачи профилирования)
- 3. 1. 1. Разработка модели обработки стружечных канавок концевой фрезой
- 3. 1. 2. Разработка модели обработки стружечных канавок торцевой фрезой
- 3. 2. Разработка и исследование модели формирования схемы резания при обработке фасонной винтовой поверхности в среде T-flex
- 3. 3. Исследования влияния параметров установки инструмента с цилиндрической исходной инструментальной поверхностью на профиль винтовой фасонной канавки концевых фрез средствами Mathcad
- 3. 4. Выводы по главе
- 3. 1. Разработка и исследование модели обработки стружечной канавки концевой фрезы в среде T-flex (решение обратной задачи профилирования)
- Глава 4. Экспериментальные исследования обработки фасонных винтовых поверхностей инструментом с прямолинейной образующей исходной инструментальной поверхности
- 4. 1. Определение станочных параметров установки инструмента
- 4. 2. Экспериментальное исследования процесса фрезерования винтовой стружечной канавки концевой фрезы стандартной концевой фрезой за один проход
- 4. 2. 1. Обработка стальной заготовки четырехзубой концевой фрезы
- 4. 2. 2. Определение поля допуска на профиль винтовой стружечной канавки концевой фрезы
- 4. 2. 3. Исследование формы стружки, полученной в процессе обработки стальной заготовки концевой фрезы
- 4. 3. Обработка стружечных канавок инструментов различного профиля
- 4. 4. Выводы по главе
Разработка процесса формообразования фасонных винтовых поверхностей инструментов на основе применения стандартных концевых и торцевых фрез (реферат, курсовая, диплом, контрольная)
Современная промышленность характеризуется значительным увеличением создания, освоения и внедрения в производство новых высокоэффективных технологий, машин и техники, обеспечивающих рост производительности предприятия, улучшение качества выпускаемой продукции, повышение ее конкурентоспособности. Это обеспечивается за счет усовершенствования технологий, что неизбежно влечет за собой усложнение узлов и деталей, разработку и использование новых материалов, которые требуют совершенствования методов обработки, конструкции станков, режущих инструментов и методов их проектирования.
Основным способом достижения необходимой точности и качества поверхностного слоя деталей в металлообработке является механическая обработка и, в частности, обработка резанием. Каждый элемент системы СПИД играет ключевую роль в процессе механической обработки, но режущий инструмент требует особого внимания, так как быстро изнашивается в сравнении с другими элементами системы и в большей мере влияет на качество и эффективность всего процесса обработки.
Особенно возрастает роль режущего инструмента в условиях безлюдных технологий гибкого автоматизированного производства, так как затраты на инструмент с 3−5% при неавтоматизированном производстве в условиях ГПС достигают значительных размеров (20−25% в себестоимости обработки).
Современное направление развития проектирования режущих инструментов связано с созданием систем автоматизированного проектирования (САПР), позволяющих с помощью современных вычислительных систем комплексно решать вопросы, возникающие на всех этапах проектирования и изготовления инструментов на базе лучших решений, полученных в результате целенаправленного поиска.
Среди многообразия типов и форм режущих инструментов значительную часть составляют инструменты со сложными рабочими и, в частности, винтовыми поверхностями. Необходимость в них диктуется не только конструктивными 4 особенностями инструмента, но и обусловлено тем, что, как правило, они обеспечивают более высокие эксплуатационные показатели, позволяющие в ряде случаев повысить производительность обработки, снизить динамические нагрузки на систему СПИД и увеличить тем самым точность обработки, улучшить условия резания, повысить качество обрабатываемой поверхности, обеспечить транспортировку стружки из зоны резания и т. д. Кроме того, на ряде ответственных деталей машиностроения рабочие поверхности также выполнены винтовыми, в частности, на лопатках турбин, роторах и лопастях циклоидальных насосов и др. Проектирование режущих инструментов для обработки этих поверхностей и их изготовление является наиболее сложными вопросами инструментального производства.
Это обстоятельство объясняется тем, что нет однозначного соответствия между профилем инструмента для обработки деталей с винтовой поверхностью и профилем этой поверхности. В связи с этим требуется разработка и использование различных методов профилирования, которые учитывают профили производящей и исходной поверхности, кинематику процесса формообразования, а также параметры установки инструмента на станке относительно заготовки. В связи с этим, при обработке винтовых поверхностей на станке возникают погрешности профиля полученного изделия из-за отличий между расчетными и фактическими размерами профиля инструмента, а также расчетными параметрами установки инструмента и его реальной установкой на станке, которые, кроме того, могут меняться при обработке, например, вследствие износа инструмента или из-за динамических нагрузок вследствие недостаточной жесткости системы СПИД.
Износ инструмента для обработки винтовых поверхностей неравномерный, вследствие того, что нагрузка на различные области режущей части разная из-за рознящихся скоростей резания и объемов срезаемого материала. Это приводит к низкой стойкости инструмента, что в свою очередь серьезно сказывается на себестоимости конечной продукции. До недавнего времени весь инструмент для обработки винтовых поверхностей изготавливался из быстрорежущих сталей, и в силу своих свойств он не обладает высокой стойкостью и производительностью. В настоящее время данный инструмент изготавливают преимущественно цельным твердосплавным. Он отличается повышенной стойкостью и производительностью, но срок службы продлевается не надолго, по причине малого количества возможных переточек или отсутствия таковых вообще.
Наиболее распространенный способ обработки фасонных винтовых канавок предусматривает в качестве режущего инструмента фасонную дисковую фрезу. Установка инструмента при обработке детали с винтовой поверхностью определяется относительным положением их осей и характеризуется в общем случае следующими параметрами: у/ - углом (или величиной Г), определяющим положение точки скрещивания осей инструмента и детали от исходного положения профиля-? — углом скрещивания осейт — межосевым расстоянием.
Однако данный способ обработки обладает рядом недостатков, к которым следует отнести в первую очередь трудоемкость технологической подготовки производства, которая обусловлена:
— сложностью проектирования;
— сложностью изготовления;
— необходимостью в большой номенклатуре режущего инструмента;
— сложностью, а зачастую невозможностью оснащения современными инструментальными материалами.
С целью сократить номенклатуру необходимого инструмента и, в некоторых случаях отказаться от проектирования и изготовления фасонных фрез, предлагается применять способ обработки винтовых фасонных поверхностей концевыми и торцевыми фрезами, в том числе оснащенными современными инструментальными материалами.
Это особенно актуально в условиях единичного и мелкосерийного производства, когда изготовление специального инструмента второго порядка себя не оправдывает. Также применение такого способа наиболее актуально в условиях инструментального цеха машиностроительного предприятия, так как позволяет изготавливать нестандартные инструменты без специального проектирования и изготовления инструмента второго порядка.
Особенностью данного способа является специальное позиционирование режущего инструмента относительно заготовки с последующим фрезерованием винтовой канавки за один проход. В качестве режущего инструмента может использоваться концевая или торцевая фреза.
Таким образом, решение задачи о возможности обработки фасонной винтовой поверхности фрезой с заданным профилем представляет не только научный, но и большой практический интерес.
Принятые обозначения. у/ - угол, определяющий положение точки скрещивания осей инструмента и детали от исходного положения профиля-? — углом скрещивания осейт — межосевым расстоянием;
СПИД — система «Станок — приспособление — инструмент — деталь» (система технологического процесса);
ГПС — Гибкие производственные системыСАПР — система автоматизированного проектированияГ- геликойдВ — диаметр фрезыг— число зубьевк — глубина канавкиу — передний угола — задний угол;
0С1 (ас) — угол наклона касательной к спинке зубар — радиус скругления дна канавки- / — величина фаски. фс — угол наклона главной режущей кромки к оси сверлаПримечание: используются другие локальные обозначения с расшифровкой в тексте.
11. Результаты работы используются в научно-исследовательском и образовательном процессах ФГБОУ ВПО МГТУ «СТАНКИН» в виде программ и методических материалов в рамках учебных курсов «Инструментальные системы интегрированных машиностроительных производств», «Компьютерная графика при проектировании инструментальной техники», «Информатика в инструментальном производстве» кафедры ИТиТФ. Разработка нового способа обработки винтовых канавок инструментов внедрена на ОАО «Станкоагрегат» и представлена для реализации на ОАО «МИЗ» .
Список литературы
- Борисов А.Н. Автоматизация решения вопросов формообразования винтовых поверхностей дисковыми инструментами: Дис.. канд. техн. наук. Тула: ТПИ, 1982, — 191с.
- Борисов А.Н. Геометрическая теория проектирования режущих инструментов: Дис. докт. техн. наук. Тула: ТулГУ, 1993.-284с
- Воробьев В.М. Профилирование фрез для изделий с винтовыми канавками: Учебно-методическая инструкция по проектированию фрез. М.: Мосстанкин, 1962.-42 с.
- Грановский Г. И. Обработка результатов экспериментальных исследований резания материалов. М.: Машиностроение, 1982. — 112с.
- Гречишников В.А., Кирсанов Г. Н., Петухов Ю. Е., Щербаков В. Н. Исследование и разработка подсистемы САПР-сверло. -В сб. Автоматизация расчетов металлорежущих инструментов с помощью ЭВМ. -Челябинск: УДНТП, 1984. -с.33−34.
- Гречишников В.А., Колесов Н. В., Петухов Ю. Е. и др. Методика научных исследований в инструментальном производстве. Учебн. пособие. Пенза., 1997 г., ПГТУ. — с.220
- Гречишников В.А. Системы автоматизированного проектирования режущих инструментов. -М.: ВНИИТЭРМ. 1988. -50 с.
- Гречишников В.А. Некоторые вопросы профилирования инструмента для обработки винтовых поверхностей. Диссертация на соискание ученой степени кандидата технических наук. М.: Мосстанкин, 1964.-205с.
- Гречишников В.А., Орлов В. Ф., Петухов Ю. Е. Рекомендации по унификации автоматизированного проектирования металлорежущего инструмента.М.:НИАТ, 1983.-34 с.
- Гречишников В.А., Орлов В. Ф., Каилук В. А., Петухов Ю. Е., Нилова Н. П. Основные положения и рекомендации по унификации проектирования и изготовления металлорежущего инструмента в условиях единичного и мелкосерийного производства. М.: НИАТ, 1983. — 44 с.
- Гречишников В.А. Профилирование инструмента для обработки винтовых поверхностей деталей по методу совмещенных сечений. М.: Мосстанкин, 1979.-27с.
- Гречишников В. А., Григорьев С. Н., Седов Б. Е. и др. /Режущий инструмент/ Учебное пособие, М.: Машиностроение, 2007.
- Гречишников В.А. и др. Проектирование дисковых инструментов для обработки винтовых поверхностей. Машиностроение, № 10,1978. — с.16−17.
- Гречишников В.А., Петухов Ю. Е. Автоматизированное и механизированное проектирование металлорежущего инструмента. М.: Мосстанкин, 1983. — 46с.
- Гречишников В.А., Петухов Ю. Е. Способ определения профиля инструмента. A.c. № 844 129 от 17.11.78.
- Гречишников В.А., Петухов Ю. Е. Устройство для профилирования сопряженных поверхностей. A.c. № 870 202 от 28.12.79
- Гречишников В.А. Повышение эффективности проектирования и эксплуатации инструмента для механообработки на основе системного моделирования: Дис. докт. техн. наук. -М.: Мосстанкин, 1998. 420 с.
- Домнин П.В., Ю.Е.Петухов /Точность профилирования при обработке винтовой фасонной поверхности / Журнал СТИН № 7−2011, Москва, с. 14−17.
- Домнин П.В., Ю.Е.Петухов /Способ формообразования фасонной винтовой поверхности стандартным инструментом прямого профиля./ / Вестник МГТУ «Станкин» № 3 (15), 2011, с.102−106.
- Домнин П.В., Петухов Ю.Е./ Компьютерное моделирование обработки винтовой канавки на заготовке концевой фрезы / «Известия МГТУ МАМИ» № 2 (12) -2011. М. С 156−164.
- Домнин П.В., Петухов.Ю.Е./ Решение обратной задачи профилирования на базе схемы численного метода заданных сечений / «Инженерный журнал СПРАВОЧНИК» № 11 2011, с. 26−29.
- Домнин П.В., Петухов Ю. Е. «СПОСОБ ИЗГОТОВЛЕНИЯ ФАСОННОЙ ВИНТОВОЙ СТРУЖЕЧНОЙ КАНАВКИ КОНЦЕВОЙ ФРЕЗЫ», заявка на изобретение № 2 010 125 848 от 24.06.10/25 .Дихтяръ Ф. С. Профилирование металлорежущего инструмента. -М.: Машиностроение, 1965. 152с.
- Илюхин С.Ю. Каркасно-кинематический метод моделирования формообразования поверхностей деталей машин дисковым инструментом: Дис. докт. техн.наук. Тула: ТГУ, 2002. — 390 с.
- Иноземцев Г. Г., Беляев А. Е. Алгоритмизация процесса профилирования поверхностей стружечных канавок плоских протяжек дисковыми угловыми фрезами. Исследование зубообрабатывающих станков и инструментов. Межвуз. научн. сб. — СПИ, 1983. — с. 3−8.
- Кирсанов Г. Н. Проектирование инструментов. Кинематические методы. Учебное пособие по курсу режущего инструмента. М.: Мосстанкин, 978. — 70с.
- Кирсанов Г. Н. Развитие некоторых вопросов теории инструмента. Вестник машиностроения, 1978, № 9. — с.53−58.
- Кирсанов Г. Н. Математическое моделирование металлообрабатывающих инструментов как основа их систематизации и САПР// «Конструкторско-технологическая информатика» КТИ-96: Тр.3-го Международного конгресса. -М.МГТУ «СТАНКИН», 1996. — с.71.
- Колесов Н.В., Петухов Ю. Е., Филин М. И. САПР фасонных резцов. САПР фасонных резцов. Инструкция и программа. Тема И88−2, 1991. с. 42.
- Колесов Н.В. Решение на ЭВМ некоторых задач профилирования режущих инструментов. Научные труды ВЗМИ. М.: ВЗМИ, т II, вып.1, 1974. с.54−59.
- Корн Г., Корн Т. Справочник по математике для научных работников и инженеров. М.: Наука. 1984. — 832 с.
- Лашнее С.И. Основы теории формообразования поверхностей дисковыми реечными и червячными инструментами. Диссертация на соискание ученой степени доктора технических наук. Тула, ТЛИ, 1968. — 268 с.
- Лашнее С.И. Профилирование инструментов для обработки винтовых поверхностей. М. Машиностроение, 1965. — с. 151.
- Лашнее С.И., Юликое М. И. Проектирование режущей части инструмента с применением ЭВМ. -М.Машиностроение, 1980.-208с.
- Люкшин B.C. Теория винтовых поверхностей в проектировании режущих инструментов. М.: Машиностроение, 1969. — 372с.
- Литвин Ф.Л. Теория зубчатых зацеплений. Изд.2-е, перераб. и доп. М.: Наука, 1968.-584с.
- Перепелица Б.А. Режущие инструмента как аффинные многообразия. -Резание и инструмент, вып. 14, 1975.-е.36−40.
- Перепелица Б.А. Управление инструментальной поверхности для сложных схем формообразования. Резание и инструмент, вып.12, 1975,-с.43−46.
- Петрухин С. С. Основы проектирования режущей части металлорежущих инструментов. М.: Машгиз, 1960. — 163с.
- Петухов Ю.Е. Математическая модель поверхности резания фасонных инструментов при обработке сложных поверхностей.//4-я Международная научно-техническая конференция «Компьютерное моделирование 2003»: СПб.: СПбГТУ, 2003.-с. 181−184.
- Петухов Ю.Е. САПР процесса формообразования.//Сборник трудов VI Всероссийской научно-технической конференции «Новые информационные технологии»: Т.1 М.: МГАПИ, 2003. — с.238−243
- Петухов Ю.Е., Колесов Н. В. Численные модели режущего инструмента для обработки сложных поверхностей //Вестник машиностроения, № 5,2003.- с.61−63
- Петухов Ю.Е. Проектирование производящей инструментальной и исходной поверхностей на основе методов машинного моделирования: Дис. .канд. техн. наук. -М.: МОССТАНКИН, -1984. -с. 240.
- Петухов Ю.Е. Проектирование инструментов для обработки резанием деталей с фасонной винтовой поверхностью на стадии технологической подготовки производства.// Дис. докт. техн. наук., Москва, 2003. с. 393.
- Петухов Ю.Е. Применение концевых фрез для обработки винтовых канавок инструментов. В сб. Повышение эффективности технологических процессов сложного формообразования деталей машиностроения. -Фрунзе, 1983. — с. 13−15.
- Петухов Ю.Е. Фрезерование винтовых канавок режущих инструментов. -Обработки резанием. М.:НИИмаш, вып. 12, 1983. — с. 1−3.
- Петухов Ю.Е. Формообразование численными методами. -М.: «Янус-К», 2004. -200 с.
- Радзевич С.П. Способы фрезерования фасонных поверхностей деталей. М.: ВНИИТЭРМ, 1989. -с.72
- Родин П.Р. Металлорежущие инструменты. Киев: Вища школа, 1974, — 400с.
- Родин П.Р. Основы теории проектирования режущего инструмента. Москва -Киев: Машгиз, 1960. — 160с.56