Технологическое обеспечение стойкости металлорежущих пластин при обработке заготовок из специальных материалов
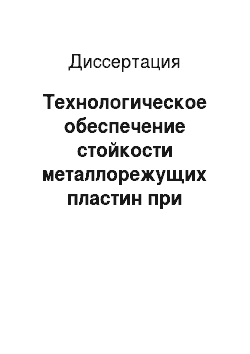
Практическая ценность заключается в создании и внедрении в промышленность оригинальных высокоэффективных технологических процессов упрочнения инструментальных материалов для конкретных условий эксплуатации, а также в разработке рекомендации по режимам резания и областям применения различно упрочнённого инструмента при обработке деталей из специальных материалов. Большое значение для практики… Читать ещё >
Содержание
- Глава 1. Обзор и анализ проблемы повышения работоспособности металлорежущего инструмента. Цель и задачи работы. Методология исследований
- 1. 1. Анализ исследований разрушения инструмента
- 1. 1. 1. Хрупкое разрушение
- 1. 1. 2. Вязкое (пластическое) разрушение
- 1. 1. 3. Износ инструмента
- 1. 2. Современные подходы в исследованиях
- 1. 2. 1. Анализ энергетических теорий исследования процесса резания
- 1. 2. 2. Анализ термодинамического подхода в исследовании процесса резания
- 1. 3. Анализ исследований по повышению работоспособности инструмента за счет нанесения покрытий
- 1. 4. Анализ исследований в области оценки качества инструмента
- 1. 5. Цель и задачи исследования
- 1. 6. Методология проведения исследования
- 1. 7. Методология и концепция повышения работоспособности инструмента
- 1. 1. Анализ исследований разрушения инструмента
- Выводы
- Глава 2. Исследование влияния условий нагружения инструмента на его работоспособность
- 2. 1. Динамическая модель импульсного нагружения инструмента
- 2. 2. Экспериментальное моделирование импульсного нагружения инструмента. Учет непостоянства стружкообразования
- 2. 3. Оценка влияния непостоянства процесса стружкообразования на интенсивность изнашивания инструмента
- 2. 4. Оценка влияния особенностей стружкообразования на усадку стружки и микротвердость обработанной поверхности
- 2. 5. Динамический анализ процесса стружкообразования по положению плоскости сдвига
- 2. 6. Исследование кинематического непостоянства процесса стружкообразования
- 2. 7. Оценка условий смещения положения и поворота плоскости сдвига
- Выводы
- Глава 3. Исследование разрушения инструмента на основе учёта взаимодействия агрегаций инструментального материала
- 3. 1. Оценка прочностных свойств элементов структуры инструментальных материалов
- 3. 1. 1. Результаты оценки прочности элементов структуры твердосплавных материалов
- 3. 1. 2. Результаты оценки прочности элементов структуры инструмента из режущей керамики
- 3. 2. Исследование кинетики взаимодействия элементов структуры инструментального материала
- 3. 2. 1. Оценка кинетического состояния структуры при межзеренных столкновениях
- 3. 2. 2. Оценка кинетики взаимодействия зерен через прослойку
- 3. 3. Исследование закономерностей разрушения инструмента. 3.3.1. Исследование разрушения твердосплавного инструмента
- 3. 3. 1. 1. Оценка роли заточки инструмента
- 3. 3. 1. 2. Характеристика состояния структуры как представление о механизмах разрушения инструментального материала
- 3. 3. 1. 3. Исследование разрушения твердосплавного инструмента с покрытием
- 3. 3. 2. Исследование разрушения инструмента из режущей керамики
- 3. 3. 3. Исследование разрушения и изнашивания инструмента, оснащенного сверхтвердым инструментальным материалом
- 3. 1. Оценка прочностных свойств элементов структуры инструментальных материалов
- Глава 4. Технологические приёмы повышения работоспособности инструмента
- 4. 2. 1. Совокупность технологических приёмов повышения работоспособности твёрдосплавного инструмента путём изменения основы инструментального материала
- 4. 2. 2. Совокупность технологических приёмов повышения работоспособности твёрдосплавного инструмента путём упрочнения основы инструментального материала
- 4. 2. 3. Совокупность технологических приёмов повышения работоспособности твёрдосплавного инструмента путём архитектурирования покрытия
- 4. 2. 3. 1. Технологический приём повышения работоспособности твёрдосплавного инструмента путём управления размером зерна в покрытии
- 4. 2. 3. 2. Технологический приём повышения работоспособности твёрдосплавного инструмента комбинацией методов нанесения покрытия
- 4. 2. 3. 3. Технологический приём повышения работоспособности твёрдосплавного инструмента путём нанесения покрытий для «залечивания» дефектов
- 4. 2. 3. 4. Технологический приём повышения работоспособности твёрдосплавного инструмента путём применения многослойных покрытий
- 4. 2. 3. 5. Технологический приём повышения работоспособности твёрдосплавного инструмента путём нанесения композиционных покрытий
- 4. 2. 4. Совокупность технологических приёмов повышения работоспособности твёрдосплавного инструмента путём упрочнения покрытий
- 4. 2. 5. Результаты оценки зависимости стойкости от элементо режима резания твёрдосплавных инструментов, подвергнутых разным способам упрочнения
- 4. 2. 6. Результаты сравнительной оценки эффективности применения твёрдосплавного инструмента, подвергнутого различным методам упрочнения
- 4. 2. 7. Схема структурирования технологического процесса изготовления твёрдосплавного инструмента в рамках концепции комплексного подхода к повышению работоспособности инструмента
- 5. 1. Методологические основы применения физических методов для оценки свойств материалов
- 5. 1. 1. Методология применения метода экзоэлектронной эмиссии
- 5. 1. 2. Методология применения метода акустической эмиссии
- 5. 1. 3. Методология применения лазерно-акустического метода
- 5. 2. Результаты оценки качества инструмента и исследования инструментальных материалов с использованием метода экзоэлектронной эмиссии
- 5. 3. Методы исследования свойств инструмента с использованием акустической эмиссии
- 5. 3. 1. Метод оценки качества сцепления покрытия с основой при индентировании с выдержкой времени
- 5. 3. 2. Методы оценки качества инструмента по > трещиностойкости
- 5. 3. 3. Методы оценки качества инструмента по трещиностойкости при скрайбировании
- 5. 3. 4. Методы оценки качества инструмента при динамическом нагружении
- 5. 4. Результаты оценки качества инструмента и исследования инструментальных материалов с использованием метода акустической эмиссии при маятниковом скрайбировании
- 5. 4. 1. Метод оценки трещиностойкости инструмента по частоте сигналов акустической эмиссии
- 5. 4. 2. Метод оценки качества инструмента по критерию Кр разделения сигналов акустической эмиссии
Технологическое обеспечение стойкости металлорежущих пластин при обработке заготовок из специальных материалов (реферат, курсовая, диплом, контрольная)
Из отчетов международного научно-технического общества Технологии Машиностроительного Производства (СЖР) известно что, «наиболее слабым звеном» при механической обработке резанием является инструмент, так как. на него приходится более 50% отказов (для сравнения: 3−5% - на узлы и агрегаты станка).
Это выдвигает проблему повышения работоспособности инструмента в число важнейших проблем в области обработки металлов резанием.
Немаловажным также является то обстоятельство, что в условиях современного автоматизированного машиностроительного производства, особенно с применением зарубежного технологического металлообрабатывающего оборудования стоимость инструмента высока и составляет 30% - 70% в цене изделия. Более того, производители оборудования специализируют его только под конкретный металлорежущий инструмент (инструмент конкретного производителя), что ставит потребителя в зависимость и не всегда устраивает по срокам и цене поставок.
Современное состояние науки о резании металлов с позиций применения металлорежущего инструмента базируется на фундаментальных и прикладных знаниях о свойствах и структуре инструментальных материалов, т. е. базируется на триаде «состав — структура — свойства». Однако необходимо отметить, что для решения проблемы повышения работоспособности инструмента использования этой триады недостаточно в силу того, что свойствами инструментальных материалов сегодня можно управлять за счет технологии изготовления инструмента, т. е. необходимо вести речь об использовании парадигмы «состав — структура—технология изготовления — свойства».
В данной работе работоспособность инструмента рассматривается как результат управления технологическими методами изготовления и свойствами инструментального материала. При этом под управлением понимается выбор метода обеспечения требуемых свойств различных групп инструментальных материалов с обеспечением возможности оперативного контроля качества, оценки состояния, диагностики и прогнозирования работоспособности. Обеспечение свойств инструментального материала осуществлено на основе исследования и выявления закономерностей разрушения и изнашивания твердого сплава, режущей керамики и сверхтвердых инструментальных материалов путем разработки новых методов изготовления и упрочнения инструмента с повышенной сопротивляемостью превалирующему механизму разрушения, в том числе за счет нанесения покрытий, а также путем разработки физических методов контроля качества, оценки состояния, диагностики и прогнозирования работоспособности инструмента.
Проблема повышения работоспособности металлорежущего инструмента рассмотрена в работе комплексно, а именно как с позиций разработки методов повышения работоспособности инструмента, так и с позиций контроля его качества. При этом рассмотрен комплекс инструментальных материалов, а именно твердосплавной инструмент, инструмент из режущей керамики и инструмент, оснащённый сверхтвёрдым инструментальным материалом.
Проблема рассмотрена применительно к труднообрабатываемым конструкционным материалам, точнее к условиям токарной и фрезерной обработке нетиповых конструкционных материалов. В частных случаях приведены отдельные результаты по зубофрезерованию (как наиболее нестационарному процессу резания), сверлению (как процессу со стеснёнными условиями стружкоотвода), по упрочнению быстрорежущего инструмента.
В работе созданы и развиты научные и методологические аспекты повышения работоспособности инструмента, включающие:
— принцип комплексного подхода к проблеме, заключающийся в том, что работоспособность инструмента рассматривается как совокупный результат совершенствования свойств инструментального материала и методов контроля его качества;
— исследование закономерностей разрушения инструмента с учетом: а) прочности структурных элементов (зерен, границ) инструментального материала, б) кинетики взаимодействия агрегаций инструментального материала, в) непостоянства условий нагружения инструмента и стружкообразования.
Новизна результатов состоит в :
1). предложенной концепции многостадийного упрочнения материала режущих пластин на различных этапах технологического процесса изготовления, включая стадию изготовления основы из инструментального материала, стадию архитектурирования покрытия и стадию упрочнения покрытия, причём многостадийность упрочнения обеспечивает управление эксплуатационными параметрами режущих пластин по градиенту свойств основы за счёт термообработки, термомеханического воздействия, вакуумной ионной бомбардировки и других приёмов, по градиенту свойств покрытия за счёт слойности покрытия, чередования свойств в слоях покрытия, регулирования размера зёрен в слоях, применения материалов, композиций и методов нанесения покрытий, по снижению дефектности покрытия за счёт ионного азотирования, лазерного воздействия и т. д.;
2). разработанной энергетической модели инструментального материала, позволяющей оценивать его способности накапливать и рассеивать подводимую энергию по критическому числу взаимодействий агрегаций до начала разрушения материала, сформулировать с этих позиций требования к инструментальному материалу, учитывать различия в условиях внешнего нагружения режущей пластины, в том числе, различия из-за непостоянства условий стружкообразования;
3). разработанном арсенале технологических методов повышения периода стойкости металлорежущих пластин, который позволяет создать эффективный технологический процесс изготовления пластин в зависимости от заданных условий эксплуатации инструмента, и включает в себя:
— термообработку, ионное азотирование или другие воздействия на основу,.
— управление количеством, составом, материалами, размером зёрен или толщинами слоёв при архитектурировании покрытия,.
— вакуумную термообработку, ионное азотирование, лазерное воздействие или другие воздействия по снижению дефектности покрытия;
4). установлении вида связи сигналов акустической эмиссии с эксплуатационными показателями металлорежущих пластин и разработке на этой основе совокупности методов оценки качества пластины и прогнозирования ее работоспособности, в том числе за счёт применения разных схем нагружения инструментального материала (индентирования или скрайбирования), одновременного контроля нескольких параметров сигналов акустической или экзоэлектронной эмиссии и выявления превалирующего механизма микроразрушения;
5). разработанных рекомендациях по сочетанию и совокупности технологических методов воздействия на металлорежущие пластины в процессе их изготовления, а также режимной области их применения, которые позволяют управлять эксплуатационными свойствами пластин и обеспечивать требуемую производительность при обработке деталей из конкретных марок специальных материалов назначением экономически целесообразного периода стойкости инструмента.
Вышеизложенное обусловило выполнение работы по координационным планам государственных научно-технических программ «Гибкие автоматизированные производства» (1985), «Авиационная технология» (1982), «Сибирь» (1988), «Дальний Восток России» (1996).
Практическая ценность заключается в создании и внедрении в промышленность оригинальных высокоэффективных технологических процессов упрочнения инструментальных материалов для конкретных условий эксплуатации, а также в разработке рекомендации по режимам резания и областям применения различно упрочнённого инструмента при обработке деталей из специальных материалов. Большое значение для практики имеют разработанные оперативные методы оценки качества инструмента и прогнозирования его работоспособности. Экономический эффект от внедрения разработок в промышленность превысил миллион рублей (в ценах 1987. 1994 годов), что в пересчете на текущий момент только за счёт учёта инфляционных процессов достигает 10 миллионов рублей. Новизна технических решений по конструкции (архитектуре) инструментальных материалов и способам их изготовления или упрочнения защищена более чем 40 изобретениями.
Основные результаты работы получены путем теоретических и экспериментальных исследований с использованием достижений теории резания, механики разрушения, материаловедения и привлечением микрофрактографии, структурного и спектрального анализа, методов внутреннего трения, экзоэлектронной и акустической эмиссии.
Работа доложена на ряде научно-технических конференций различного уровня, по материалам работы опубликовано более 100 работ (в соавторстве и лично), в частности в виде монографий, в центральных периодических изданиях, в виде изобретений.
Автор благодарен ученым ряда ВУЗов и НИИ, оказавшим помощь и консультации при выполнении работы, в первую очередь д.т.н., профессору Верещаке A.C., д.т.н., профессору Кабалдину Ю. Г. и д.т.н., профессору Семашко H.A., к.т.н., сотрудникам ВНИИТС Аникину В. Н. и Аникееву А.И.
12. Результаты работы внедрены в промышленность с экономическим эффектом более миллиона рублей в ценах 1987.1994 годов, что в пересчёте по индексу инфляции на текущую дату превышает 10 миллионов рублей.
ЗАКЛЮЧЕНИЕ
РЕЗУЛЬТАТЫ И ОСНОВНЫЕ ВЫВОДЫ.
На основании выполненного комплекса теоретико-экспериментальных исследований предложены научно обоснованные технологические и технические решения, направленные на повышение периода стойкости металлорежущего инструмента при обработке деталей из специальных материалов, внедрение которых вносит значительный вклад в ускорение научно-технического прогресса.
В работе получены следующие основные результаты и выводы:
1. Разработаны методология и концепция комплексного подхода к решению проблемы повышения эксплуатационных свойств металлорежущих пластин инструмента, состоящие в разработке арсенала технологических упрочняющих воздействий на каждой стадии их изготовления. Это позволяет управлять работоспособностью инструмента и выбирать эффективный технологический процесс изготовления металлорежущей пластины применительно к конкретным условиям эксплуатации инструмента и обеспечивает увеличение периода стойкости пластины в 2.6 раз по сравнению с неупрочнённым инструментом и до 2 раз по сравнению с новейшими решениями.
2. Эффективность упрочняющих воздействий существенно различна для разных инструментальных материалов. Например, вакуумная термообработка твёрдого сплава по величине прироста периода стойкости инструмента до 30% менее эффективна, чем вакуумная термообработка режущей керамики или сверхтвёрдого инструментального материала и наоборот, нанесение покрытия до 2 раз более эффективно для твёрдого сплава, чем для режущей керамики и сверхтвёрдых инструментальных материалов.
3. Уровень эффективности одинакового упрочняющего воздействия на режущую керамику и сверхтвёрдые инструментальные материалы сопоставим (отличие в несколько процентов). Это объясняется ограниченными возможностями вовлечения механизмов упрочнения по сравнению с твёрдым сплавом и создаёт предпосылки для применения более дешёвого материала и технологического приёма упрочнения.
4. Степень повышения периода стойкости металлорежущей пластины в результате воздействия на нее совокупности нескольких технологических воздействий не равна алгебраической сумме эффектов его повышения от каждого воздействия в отдельности. Как правило, общий эффект прироста стойкости меньше суммы эффектов повышения стойкости отдельных технологических воздействий. Однако, при реализации смежных механизмов упрочнения в совокупности воздействий общий эффект прироста стойкости значительно выше суммы эффектов повышения стойкости отдельных воздействий. Так чередование в покрытии слоев различной твёрдости по сравнению с таким же количеством слоев одинаковой твёрдости обеспечивает более высокую стойкость.
5. Достижение сверхэффектов повышения периода стойкости осуществимо при реализации смежных механизмов упрочнения (деформационный, твёрдорастворный, субструктурный и дисперсионный, перечислены в порядке роста уровней иерархии). Таким образом, в совокупности воздействий следует использовать сразу нескольких иерархических уровней механизмов упрочнения инструментального материала, причём, чем больше уровней, тем выше эффект, а пропуск хотя бы одной стадии хотя бы на одном из этапов изготовления сопровождается снижением эффекта.
6. Эффективность технологических процессов изготовления твёрдосплавных металлорежущих пластин наиболее значимо растёт:
— на стадии подготовки основы инструментального материала за счет термообработки ионной бомбардировкой — в 1,5 раза, а также в 1,8 раза за счёт удаления дефектных зёрен, образовавшихся при алмазно-абразивной обработке пластин, стабилизации внутренних напряжений в пластине и образования ювенильных химически активных областей;
— на стадии архитектурирования покрытий за счет однократного чередования «мягких» и «твёрдых» слоёв в покрытии в 3 раза, за счет многократного чередования «мягких» и «твёрдых» слоёв в 5 раз вследствие торможения роста трещин вязкой составляющей покрытия;
— на стадии снижения дефектности покрытий в 1,5 раза за счёт лазерного упрочнения, способствующего локальному перераспределению внутренних напряжений в режущей пластине и технологическому заполнению трещин и несплошностей.
7. Разработаны рекомендации по выбору рациональных технологических процессов изготовления металлорежущих пластин в зависимости от требуемого уровня периода стойкости и экономических ограничений. При невысоких требованиях к уровню периода стойкости (увеличение до 1,5 раз) наиболее рациональными являются технологические упрочняющие воздействия на исходную инструментальную основу.
8. Технологические процессы изготовления пластин из режущей керамики и сверхтвёрдых инструментальных материалов обеспечивается теми же приёмами, что и для твёрдого сплава, но для них наиболее эффективны вакуумная термообработка основы (увеличение стойкости в 1,7 раза) и нанесение металлических слоёв покрытия (увеличение стойкости в 1,3 раза).
9. Комбинированием технологической последовательности упрочняющих воздействий возможно частичное перекрытие областей эффектного применения групп инструментальных материалов, в частности, при точении высокопрочных отбелённых чугунов твёрдосплавный инструмент замещён керамическим с увеличением скорости резания в 2 раза без ущерба качеству, а периода стойкости инструмента в 6 раз.
10. Предложенная энергетическая модель взаимодействия агрегаций в инструментальном материале с позиций повышения работоспособности инструмента из всех трёх исследуемых групп позволяет сформулировать следующие требования к инструментальному материалу:
— предпочтительны материалы с многоканальной схемой передачи энергии, что обеспечивается симметричным расположением большего числа зёрен меньшего размера, т. е. мелкозернистой симметричной каркасной структурой сферических зёрен;
— недопустима магистральная схема передачи энергии из зерна в зерно, т. е. неприемлимо осесимметричное расположение зёрен;
— при исчерпании возможности накапливать и рассеивать подводимую энергию инструментальный материал должен обладать возможностью изменения своего состояния: а) • механическим путем за счет раскола зернаб) геометрическим путем за счет изменения угла передачи энергии вследствие смещения зёрен и увеличения расстояния между нимив) физическим путем за счет перестроения структуры, например на дислокационную, создающего дополнительные каналы оттока энергии.
11. Установлены виды связи сигналов акустической эмиссии с эксплуатационными показателями металлорежущих пластин, позволяющие преобразовать функцию контроля и отбраковки инструмента функцией прогнозирования его работоспособности. Разработана совокупность методов оценки качества пластины и прогнозирования ее работоспособности по периоду стойкости, трещиностойкости и прочности сцепления покрытия (метод индентирования, скрайбирования), позволяющая за счёт применения разных схем нагружения инструментального материала и одновременного контроля нескольких параметров сигналов акустической или экзоэлектронной эмиссии, идентифицировать механизмы микроразрушения и выявить превалирующий.
Список литературы
- Болотин, В.В. Объединенная модель разрушения композиционных материалов при длительно действующих нагрузках// Механика композиционных материалов, 1981, № 3, с.405−420.
- Карпинос, Д.М., Максимович, Г.Г., Кадыров, В.Х., Лютый, Е. М. Прочность композиционных материалов. Киев: Наукова думка, 1978, 236 с.
- Каширин, А.И. К вопросу о прочности режущей кромки инструмента при резании труднообрабатываемых материалов/Сб. Трение и износ при резании металлов. М.: Машгиз, 1955, с.37−52.
- Резников, Н.И. Вопросы скоростного фрезерования.// Вестник машиностроения, № 11, 1947, с. 29−34.
- Зорев, Н.Н. Влияние установки заготовки на стойкость фрез при торцевом фрезеровании// Вестник машиностроения, № 8, 1951, с.42−46.
- Зорев, Н.Н. Обработка сталей твердосплавным инструментом в условиях прерывистого резания/ / Вестник машиностроения, № 2, 1963, с.34−36.
- Этин, А.О. Влияние условий врезания торцевой фрезы на ее стойкость/Сб. Динамика процесса резания. -М., Машгиз, 1953, с.53−58.
- Андреев, Г. С. Влияние тепловых и адгезионных явлений на работоспособность твердосплавного инструмента при периодическом резании.// Вестник машиностроения. 1974, № 10, с.71−74.
- Андреев, Г. С. Повышение производительности обработки деталей в условиях периодического прерывистого резания.// Вестник машиностроения. 1978, № 12, с.48−52.
- Зорев, Н.Н., Фетисова З. М. Обработка резанием тугоплавких сплавов. -М.: Машиностроение, 1966,-227 с.
- Бердников, Л.Н. Предупреждение хрупкого разрушения режущего инструмента, обусловленного тепловой нагрузкой. // Вестник машиностроения. 1976, № 11, с.62−65.
- Синопальников, В.А., Турин, В.Д. Температурное поле в режущем клине инструмента при прерывистом резании. // Вестник машиностроения. 1981, № 4, с.44−47.
- Остафьев, В.А. Учет прочности инструмента при его проектировании и эксплуатации.// Станки и инструмент. 1983, № 7, с.19−20.
- Kaning W. Der Werkrengverschleib bei der spanenden Beareitung von Stahlwarkstoffen. Werkstatechnir, 1966, 56 N5, c.229−234.
- Opitz H., Schilling W. Untersuchung der Verschlei preaktionen bei der Bearbeitung Von Stahl mit Schnellarbeits-stahlwerkzlugen. Forschlungsber. Landes Nordzhein- Westfalen., 1967, N17, 196, c.3−95.
- Остафьев, В.А. Расчет динамической прочности режущей части инструмента. М.: Машиностроение, 1979, — 168 с.
- Лоладзе, Т.Н., Бетанели, А.И. Прочность режущего инструмента. В кн.: Развитие науки о резании металлов./Под ред. Н. Н. Зорева. — М.: Машиностроение, 1967, с. 157−181.
- Бетанели, A.M. Прочность и надежность режущего инструмента. -Тбилисси. Сабцора Сахартвело, 1973. 302 с.
- Андреев, Г. С. Контактные напряжения при периодическом резании. // Вестник машиностроения. 1969, № 8, с.63−66.
- Лоладзе, Т.Н. Прочность и износостойкость режущего инструмента. М.: Машиностроение, 1982, — 320 с.
- Куклин, Л.Г., Сагалов, В.И., Серебровский, В. Б. Повышение прочности и износостойкости твердосплавного инструмента. М.: Машиностроение. 1968. — 140 с.
- Казакова, Т.В., Хает, Л.Г. Выбор рационального метода форсированных испытаний инструмента на основе проверки адекватности его результатов эксплуатации. Экспресс-информация. НИИмаш, 1983, с.5−9.
- Третьяков, И.П., Яцук, Н.В. Прочность режущих кромок твердосплавных пластинок. // Станки и инструмент. 1971, № 1, с.31−32.
- Скибин, В.В. Оценка прочности твердосплавного инструмента методом ступенчато-возрастающей подачи. // Станки и инструмент, 1975, № 12, с. 1516.
- Гордон, М.Б. Исследование трения и смазки при резании металлов. В кн.: Трение и смазка при резании металлов. Чебоксары, ЧТУ, 1972, с.7−137.
- Лоладзе, Т.Н. Износ режущего инструмента. М.: Машгиз, 1958, — 536 с.
- Archibald F.R. Analysis of the stresses in a cutting edge, Trans, of the ASME, 1956, 78, N6.
- Вадачкория, М.П. К расчету напряжений в плоском упругом клине. Труды Грузинского политехнического института. 1973, № 7, с.147−151.
- Макаров, А.Д. Оптимизация процессов резания металлов. М.: Машиностроение. 1976. — 278 с.
- Хает, Г. Л. Прочность режущего инструмента. М.: Машиностроение, 1975, — 168 с.
- Утешев, М.Х., Синюков, В.А. Напряженное состояние режущей части инструмента с округленной режущей кромкой. // Вестник машиностроения, 1970, № 2, с.70−73.
- Кабалдин, Ю.Г. Повышение работоспособности и надежности рабочей части инструмента в автоматизированном производстве. Автореф. диссерт.. доктора технических наук. М., Станкин, 1987, 47 с.
- Кабалдин, Ю.Г. Структура, прочность и износостойкость композиционных инструментальных материалов. Комсомольск-на-Амуре, издательство технического университета, 1994, — 215 с.
- Кабалдин, Ю.Г. Принципы конструирования композиционных инструментальных материалов с повышенной работоспособностью. -Владивосток, ДВО АН СССР, 1990, 58 с.
- Кабалдин, Ю.Г., Шпилев, A.M. Повышение надежности процессов механообработки в автоматизированном производстве. Владивосток: Дальнаука, 1996. — 264 с.
- Синопальников. В.А., Турин, В.Д. Тепловые условия работы быстрорежущего инструмента с покрытием из нитрида TiN. // Станки и инструмент, 1983, № 1, с.14−15.
- Боровский, Г. В. Оценка эффективности применения инструмента, оснащенного сверхтвердыми материалами// Станки и инструмент, 1988, № 2, с.8−11.
- Бобров, В.Ф., Иванов, В.В. Режущие свойства титановых твердых сплавов при непрерывном точении углеродистых и легированных конструкционных сталей.// Вестник машиностроения, 1979,№ 3, с.53−56.
- Жилин, В.А., Стебленко, В.П. Пластический износ режущего инструмента с пластинками из твердого сплава:// Станки и инструмент, 1976, № 3, с.36−38.
- Жилин, В.А. Субатомный механизм износа режущего инструмента. -Ростов-на-Дону, издательство РГУ, 1973, 168 с.
- Талантов, Н.В., Черемушкин, Н.П. Закономерности пластического деформирования при обработке упрочняющих материалов. / В кн.: Теплофизика технологических процессов. Волгоград, издательство ВПИ, 1979, с.3−29.
- Талантов, И.В. Закономерности износа резцов из твердого сплава. Республиканский межведомственный сборник. Сб.: Резание и инструмент. Харьков. Вища школа, 1981, вып.26, с.110−114.
- Клушин, М.И. Резание металлов. Учебное пособие. Горький, ГПИ, 1967. — 103 с.
- Костецкий, Б.М. Стойкость режущих инструментов. М: Машгиз, 1979. -158 с.
- Зорев, H.H. О взаимосвязи процессов в зоне стружкообразования и в зоне контакта передней поверхности инструмента. Вестник машиностроения. 1963, № 12, с.42−51.
- Колев, Н.С. Теоретическое и экспериментальное исследование трения и изнашивания вольфрамо-карбидных и титано-вольфрамо-карбидных сплавов. Автореф. дисс. .докт.техн.наук. Ростов, 1973, 53 с.
- Семенов, А.П. Трение и адгезионное взаимодействие тугоплавких металлов при высоких температурах. М.: Наука, 1972, — 156 с.
- Талантов, Н.В., Дудкин, М.Е. О структурных превращениях в твердом сплаве при резании стали. // Сверхтвердые материалы. 1982, № 1, с.23−27.
- Беккер, М.С. Металлофизика износа режущего*инструмента. Сб.: Теория трения, смазки и обрабатываемости металлов. Чебоксары, ЧТУ, 1978, с.47−58.
- Гуревич, Д.М. Причины образования^ экстремума стойкостной зависимости твердосплавного инструмента.// Вестник машиностроения. 1976, № 12, с.30−32.
- Грановский, Г. И., Панченко, В.Ф. Фасонные резцы. М.: Машиностроение. 1980. — 309 с.
- Клушин, М.И., Беккер, М.С., Гордон, М.Б. К характеристике контактного взаимодействия стружки с инструментом. Сб.: Вопросы теории действия СОЖ в процессах обработки резанием. Горький, 1975, № 3, с.52−56.
- Deederich N. Metallisher Zwischeushichten im Bereich der Aufbanschneidesbildung. Ind. -Anz., 1968, 90, N24, c.457−460.
- Хаккен, Г. Явления перехода и переходные процессы в нелинейных системах. Синергетика/Сб.статей. Пер. с англ.//Под ред. Кадомцева Б. Б., М.: Мир, 1984, с.7−17.
- Кудинов, В.А. Динамика станков, М., Машиностроение, 1967, — 359 с.
- Гуревич, Д.М. Адгезионно-усталостное изнашивание твердосплавного режущего инструмента. Диссертация на соискание ученой степени доктора наук. Иркутск, 1986, 315 с.
- Аваков, A.A. Физические основы теорий стойкости режущих инструментов. М.: Машгиз, 1960. — 320 с.
- Развитие науки о резании металлов./ Под. ред. Боброва В. Ф., Г. И. Грановского, Н. Н. Зорева и др. М.: Машиностроение, 1967, 416 с.
- Кремнев, JI.C., Синопальников, В.А. Изменение структуры и свойств в режущей части инструмента из быстр орежущей стали в процессе непрерывного точения // Вестник машиностроения, № 8, 1976, с.46−51.
- Zhijun Lin, Lin Wang, Jianzhong Zhan, Ho-kwang Mao, Yusheng Zhao. Nanocrustalline tungsten carbide: As incompressible as diamond. Applied Physics Letters 95, 211 906 (2009).
- Fuch M., Scheffer M. Ab initio pseudopotentieals for electronic structure calgulations of polu-atomic sustems using density-finctional theory .//Сотр. Phys. Commun. 1999. Vol. 119.P.67−11.
- Zavodinsy V.G. Small tungsten carbide nanoparticles: Simulation of structure, energetics, and tensile strength. Int. Journal of Refractory Metals & Hard Materials 28(2010) 446−450.
- Iochen M. Schneider. Effect of transition metal additives on electronic structure and elastic properties of TiAl and Ti3Al. Phys. Rev. В 74, 174 110, 2006.
- Gunterrez G., Taga A., Johansson B. Phus. Rev. В 65, 12 101 (2001).
- Fernandez E.M., Borstel G., Soler J. and Balbas L.C. Study of Eur. Phus. J. D 24, 245−248 (2003).
- Gunterrez G., Johansson B. Phus. Rev. В 65, 104 202 (2002).
- M. Christensen, G. Wahnstrom, C. Allibert, S. Lay. Quantitative Analysis of WCaien Share in Sintered WC-Co Cemented Carbides. Physical Review Latters 94 (2005)066105.
- H. Gleiter. Nanostructured materials: basic concepts and microstructure. // Acta mater. 2000, v. 48, pp. 1 29.
- Платонов, Г. Л., Аникин, B.H., Аникеев, А.И. и др. Влияние состава твердых сплавов на кристаллохимические характеристики нанесенных на них покрытий из карбида титана.// Порошковая металлургия. 1982, № 11, с.69−75.
- Верещака, А.С., Табаков, В.П., Жогин, А. С. Износ твердосплавных инструментов с покрытием.// Вестник машиностроения, 1981, № 4, с.45−47.
- Верещака, А.С., Третьяков, И.П. Режущие инструменты с износостойкими покрытиями. М.: Машиностроение, 1986, — 192 с.
- Табаков, В.П., Порохин С. С. Применение многослойных покрытий для повышения эффективности режущего инструмента, работающего в стеснённых условиях//Металлообработка, № 3, 2010, с.40−44.
- Григорьев С.Н. Методы повышения стойкости режущего инструмента (учебник для студентов втузов) М.: Машиностроение, 2009. — 368 с.
- С. Ducros, V. Benevent, F. Savchette. Deposition, characterisation and mashining performance of multilayer PVD coatings on cemented carbide cutting tools. // Surface and Coatings Technology. 2003, v. 163 164, pp. 681 — 688.
- P.H. Mayrhofer, H. Willmann, С. Mitterer. Recrystallisation and grain growth of nanocomposite Ti-B-N coatings. // Thin Solid Films. 2003, v. 440, pp. 174 -179.
- Panckow, A.N. Application of novel vacuum-arc ion-plating technologies for the design of advanced wear resistant coatings. /A.N. Panckow, J. Steffenhagen, D. Wegener, L. Dubner, F. Lierath. //Surface and Coating Technologies 138 (2001). -P. 71−76.
- Okumiya, M. Mechanical properties and tribological behavior of TiN-CrAIN and CrN-CrAIN multilayer coatings. /М. Okumiya, M. Gripentrog.// Surface and Coating Technologies 112 (1999). P. 123−128.
- Byrne, G. Advancing Cutting Technology. / G. Byrne, D. Dornfeld, B. Denkena. // CIRP Annals. Vol 52/2/2003.
- Gleiter H. Nanostructured materials: basic concepts and microstructure // Acta mater. 2000. V.48.P.1−29.
- Simultaneously Increasing the Ductility and Strength of Nanostructured Alloys //Yong-Hao Zhao, Xiao-Zhou Liao, Sheng Cheng, En Ma, and Yuntian T. Zhu. 2006 WILEY-VCH Verlag GmbH & Co. KGaA, Weinheim.P. 123−132.
- Scherbarth S. Moderne Schneidstoffe und Werkzeunge-Wege zur gesteigerten Produktivitat // Sandvik Coromant Gmbh. 7. Schmalkalder Werkzeugtagung. 2005).
- Holleck H. 1990. «Basic principles of specific application of ceramic materials as protective layers». Surface and coatings Tecnnology, 43/44 245 258.
- Horst-Dieter Tietz. Technische keramik. VDI Verlag GmbH, Dusseldorf, 1994. 364 s.
- Фляйшер, Г. К. К связи между трением и износом. Контактное взаимодействие твердых тел и расчет сил трения и износа. М.: Наука, 1968, — 199 с.
- Крагельский, И.В. Основы расчетов на трение и износ. М.: Машиностроение, 1977, — 626 с.
- Костецкий, Б.И. Структура и поверхностная прочность материалов при трении // Проблемы прочности. 1981, № 3, с.90−98.
- Rabinowier Е. Friction and wear Materials. New Iork.I.Wileg, 1965, 301 c.
- Постников, B.C. Внутреннее трение в металлах. М., Металлургия, 1969, 329 с.
- Якубов, Ф.Я. Энергетические соотношения процесса механической обработки материалов. Ташкент, ФАН, 1965, — 112 с.
- Старков, В.К. Дислокационные представления о резании металлов. М.: Машиностроение, 1979, — 160 с.
- Ким, В. А. Принципы системного подхода к термодинамике резания при решении проблемы упрочнения металлорежущего инструмента. Диссертация на соискание ученой степени доктора технических наук. г. Ростов-на-Дону, 1994.
- Roth R.H. The Range of Pemissible Shear Angles in Orthogonal Machining Allowing for Voriable Hydrostatic Stress on the Shear Plane and Variablt Friction Angle Along the Rake Fals. Int.I.of Machine Tool Desing and Research, Vol.15, 1975, pp.161−177.
- Rowe G.W., Walstencroft F., «A Mechanical Approach to the Metallurgy of Machining», J. of the I nst. ol Metals, Vol. 98, 1970, pp. 33−41.
- Wright P.K., «Metallurgical Effects at High Strain Rates in the Secondary Shear Zone of the Machining Operation», Metallurgical Effects at High Strain Rates, ed. R.W. Rhode et al., Plenum Press, 1973, pp.547−558.
- Кабалдин, Ю.Г., Шпилев, A.M. Синергетика. Управление процессами механообработки в автоматизированном производстве. Комсомольск-на-Амуре: изд-во КнАГТУ, 1997, — 260с.
- Кабалдин, Ю.Г., Мокрицкий, Б.Я., Семашко, Н.А., Тараев, С. П. Современные методы конструирования, контроля качества и прогнозирования работоспособности режущего инструмента. Владивосток, ДВГУ, 1990, — 122 с.
- Рыжкин, A.A. Термодинамические основы повышения износостойкости инструментальных режущих материалов. Автореферат диссетрации на соискание ученой степени доктора наук, -Ростов-на-Дону, 1983, 33.
- Григорьев, С.Н. Повышение надежности режущего инструмента путем комплексной ионно-плазменной поверхностной обработки. Автореф. диссертации, на соиск. уч. степени доктора технических наук. Москва, Станкин, 1995, 54 с.
- Фадеев, B.C. Научные основы разработки и получения слоистых материалов на поверхности твердых сплавов и оксидной керамики для повышения работоспособности режущего инструмента. Автореферат диссерт. на соиск. уч. степени докт. наук. Якутск, 2005, 44с.
- A.c. СССР № 1 626 132, МКИ G 01 N 19/04. Способ определения адгезии покрытия к подложке/ Вялко А. Г., Геворкян А. Р., 1988.
- A.c. СССР № 1 693 439, МКИ G 01 N 3/00. Способ определения вязкости разрушения материала/ Бякова A.B., Горбач В. Г., 1989.
- Постников, B.C., Родионов, A.A. Прибор для измерения внутреннего трения и модуля сдвига при свободных и вынужденных колебаниях// Заводская лаборатория, 1966, № 6, с. 763.
- Шоршоров, М.Х. Физико-химическое взаимодействие компонентов в композиционных материалах// Композиционные материалы. М., Наука, 1981, с.11−18.
- Карпинос, Д.М., Максимович, Г.Г., Кадыров, В.Х., Лютый, Е. М. Прочность композиционных материалов. Киев: Наукова думка, 1978, 236 с.
- A.c. СССР № 1 240 505, МКИ В 23 В 25/06. Устройство для контроля работоспособности резцов./ Козочкин М. П. и др., 1986.
- Иванова, B.C., Копьев, И.М., Овчинский, A.C. К вопросу о распределении напряжений при деформировании композиций различного типа// Физ.-хим. механика материалов, 1974, № 4, с.23−26.
- Иванов, В.И. Применение метода акустической эмиссии для неразрушающего контроля и исследования материалов. //Дефектоскопия, № 5, 1980.
- Кунченко, В.В., Кудрявцева, Е.Е., Сапрыкин, Л.И. и др. О взаимосвязи структурного состояния материала и характера акустической эмиссии, возникающей при деформации сосредоточенной нагрузкой. // Дефектоскопия, № 3, 1994.
- Муравин, Г. Б., Синкин, Я.В., Мерман, А.И. Идентификация* механизма разрушения методами спектрального * анализа сигналов акустической эмиссии.//Дефектоскопия, № 1, 1989.
- Пятыхин, Л.И., Кунченко. В.В., Турин, Е.П. и др. Обнаружение микротрещин в покрытиях методом акустической эмиссии.// Дефектоскопия № 11, 1988.
- Вайнберг, В.Е., Клейман, А.Ш., Берман, С.Х. и др. Акустико-эмиссионный контроль газотермических покрытий. // Дефектоскопия, № 7, 1990.
- Новиков, Н.В., Лысенко, О.Г., Девин, Л. В. Диагностика разрушения поликристаллических сверхтвердых материалов методом АЭ.// Сверхтвердые материалы, № 4, 1991.
- Гольдемит, В. Удар. Теория и физические свойства соударяемых тел. -Ml, Стройиздат, 1965, 448 с.
- Кильчевский, H.A. Динамическое контактное сжатие твердых тел. Удар. Киев, Наукова думка, 1976, — 319 с.
- Мигиренко, Г. С., Евграфов В. Н., Рыков A.A. и др. Ударные стенды для испытания малогабаритных изделий. Иркутск, издательство Иркутского университета, 1987, 216 с.
- Коровайченко, В.В., Коровайченко, Ю.Н., Шкурки, A.A. и др. Прогнозирование стойкости быстрорежущего инструмента методом внутреннего трения // Технология и организация производства. 1984, № 1, с.33−34.
- Кортов, B.C. Методологические основы изучения экзоэлектронной эмиссии.// Техника и методика измерения экзоэлектронной эмиссии. Свердловск: УПИ, 1973, с.7−17.
- Семашко, H.A., Ляховицкий, М.М., Орлов. A.C. и др. Экспериментальное исследование акустических свойств никеля в области магнитного фазового перехода.// Теплофизические свойства веществ и материалов. М.: Изд-во стандартов, 1983, Вып.19, с.100−108.
- Стрижало. В.А., Пономаренко, И.А., Лихицкий. С.И. и др. Принцип построения аппаратуры обработки сигналов акустической эмиссии для исследования прочности материалов.// Проблемы прочности. 1986, № 1, с.102−105.
- Кабалдин, Ю.Г., Кортов. B.C., Мокрицкий, Б.Я. и др. Оценка износостойкости твердых сплавов с покрытием. // Машиностроитель, 1985, № 10, с.20−21.
- Кабалдин, Ю.Г., Мокрицкий, Б.Я, Молоканов, Б. И. Повышение надежности инструментального обеспечения'- гибких производственных станочных систем. Комсомольск-на-Амуре, ЦНТИ, 1988,.64 с.
- Кабалдин, Ю.Г., Мокрицкий. Б.Я., Семашко. H.A. и др. Определение трещиностойкости.инструментов.// Машиностроитель, 1986, № 9- с. 10.
- Кабалдин, Ю.Г., Семашко. H.A., Мокрицкий, Б.Я. и др. Исследование термической стабильности инструментальных материалов методами акустической эмиссии. // Теплофизические свойства веществ и материалов. Выш26, М., издательство стандартов, 1989, с.64−68-
- Кабалдин, Ю.Г., Мокрицкий, Ь.Я., Изотов, С. А. Повышение работоспособности и надежности рабочей части инструмента с покрытием. // Известия ВУЗов. Машиностроение, 1987, № 1, с141 143. •.
- Мокрицкий, Б.Я.,. Кабалдин, Ю. Г. Технологическое обеспечение термомеханического упрочнения инструмента.,// Машиностроитель, 1990, № 2, с. 17.. .
- Фадеев. B.C., Мокрицкий, Б.Я., Аникин, В.Н. и др. Обработка высокопрочных сталей и сплавов резанием //Машиностроитель, 1985, № 6, с. 38−39.
- Кабалдин, Ю.Г., Мокрицкий, Б.Я. Разрушение режущей керамики и пути. повышения. ее работоспособности.// Известия ВУЗов. Машиностроение, 1992,10.12, с.1'18−126... ¦
- Кабалдин, Ю.Г., Аникин, В.Н, Мокрицкий, Б. Я. Повышение надежности инструмента из оксидно-карбидной: керамики.// Станки и инструмент, 1989,. № 6, с.27−28. -
- Кабалдин, Ю.Г., Мокрицкий, Б.Я., Пронин, А. И. Стойкость режущего инструмента, оснащенного керамикой и сверхтвердыми материалами. // Станки и инструмент, 1991, № 12, с.19−21.
- Эффективное применение режущего инструмента, оснащенного синтетическими сверхтвёрдыми материалами и керамикой, в машиностроении: Методические рекомендации. М.: ВНИИТРЭМ, 1986, -208 с.
- Номенклатура режущего инструмента из минералокерамики и сверхтвёрдых материалов на основе нитрида бора, выпускаемого заводами Минстанкопрома. -М: НИИмаш, 1984, 44 с.
- Мокрицкий, Б .Я. Повышение работоспособности металлорежущего инструмента путём управления свойствами инструментального материала: моногр./Б.Я. Мокрицкий. Владивосток: Дальнаука, 2010. -232 с.
- Мокрицкий, Б.Я., Мокрицкая, Е.Б. К вопросу об управлении работоспособностью металлорежущего инструмента.// Вестник машиностроения, № 12, 1998, с.40−47.
- Мокрицкий, Б.Я. Технологическая система резания как система преобразования входных параметров в выходные.// Известия ВУЗов.. Машиностроение. № 4−6, 1992, с. 102−108.
- A.c. СССР № 1 495 005. Устройство для термомеханической обработки инструмента./ Мокрицкий Б. Я., Червяков А. Е., Желтухин A.C., Фадеев B.C., Кабалдин Ю. Г. 0публ.23.07.1989. Бюл.№ 27.
- A.c. СССР № 1 371 846. Устройство для закрепления деталей./ Мокрицкий Б. Я., Фадеев B.C., Кабалдин Ю. Г. Опубл. 07.02.1988. Бюл.№ 5.
- A.c. СССР № 1 319 424. Способ изготовления режущего инструмента./ Мокрицкий Б. Я., Кабалдин Ю. Г., Лиманов C.B., Васюхно А. И., Ворончихин
- A.Н. 0публ.27.01.2010. Бюл.№ 3.
- Мокрицкий, Б.Я. Повышение работоспособности металлорежущего инструмента.// Технология машиностроения, № 8, 2010, с. 33−36.
- A.c. СССР № 1 292 995. Способ термомеханического упрочнения твёрдосплавного инструмента с износостойким покрытием./ Кабалдин Ю. Г., Мокрицкий Б. Я., Изотов С. А., Андреев A.A., Фадеев B.C.
- A.c. СССР № 1 436 347. Способ изготовления режущего инструмента./ Кабалдин Ю. Г., Шепелев A.A., Мокрицкий Б. Я., Дунаевский Ю. В., Аникин
- B.Н. Опубл. 10.04.2010. Бюл.№ 10.
- A.c. СССР № 1 446 769- Способ изготовления твёрдосплавного материала для режущего инструмента./ Кабалдин ЮГ., Шепелев- A.A., Мокрицкий Б .Я., Дунаевский Ю. В., Аникин В. Н. Опубл. 10.04.2010. Бюл.№Ю
- A.c. СССР № 1 670 876. Способ обработки металлорежущего инструмента/ Мокрицкий Б. Я., Кабалдин Ю. Г., Аникеев А. И., Леонов ЕЮ., Киле A.A. Опубл. 27.01.2010. Бюл.№ 3.
- A.c. СССР № 1 767 773. Способ обработки металлорежущего инструмента/ Мокрицкий Б. Я., Кабалдин Ю. Г., Аникеев А. И., Андреев A.A. Опубл. 20.01.2010. Бюл.№ 3.
- A.c. СССР № 1 342 047. Способ изготовления твёрдосплавного инструмента/ Кабалдин Ю. Г., Мокрицкий Б. Я., Фадеев В: С., Изотов С. А., Андреев A.A., Аникин B. Hi, Бурков A.A. Опубл. 17.01.2010. Бюл.З.
- Ах. СССР № 1 354 757. Многослойное покрытие инструмента/ Кабалдин Ю. Г., Мокрицкий Б. Я., Аникин В. Н., Андреев A.A., Кирюхин С. А., Семибратова М. В. Опубл. 27.01.2010. Бюл.№ 3.
- A.c. СССР № 1 372 976. Многослойное покрытие и способ его получения/ Кабалдин Ю. Г., Мокрицкий Б. Я., Изотов С. А., Бурков A.A., Аникин В. Н., Семашко H.A., Щелкунов Б. П. Опубл. 27.01.2010. Бюл.№ 3.
- A.c. СССР № 1 354 557. Многослойный инструментальный материал./ Кабалдин Ю. Г., Мокрицкий Б. Я., Аникин В. Н., Андреев A.A., Семашко: H.A., Кирюхин С. А. Опубл. 27.01.2010. Бюл.№ 3.
- Мокрицкий, Б.Я. Управление работоспособностью металлорежущего инструмента путём нанесения покрытий, механической упрочняющей обработки и контроля качества.// Упрочняющие технологии и покрытия- № 9, 2010, с. 38−47.
- В. Ya. Mokritsii. Estimating Tool Properties on the Basis of Acoustic Emission//RussuanEnjneering Research, 2010, Vol.30, № 10, pp, 1026−1028.
- A.c: СССР № 1 367 529. Способ изготовления твёрдосплавного • инструмента/ Кабалдин KD .F., Мокрицкий Б. Я-, Бурков A.A., Изотов С. А., Андреев A.A., Аникин В-Н., Щелкунов Б. П. Опубл. 27.01.2010. Бюл.№ 3.
- A.c. СССР № 1 324 325. Твёрдосплавный режущий материал/ Кабалдин Ю. Е., Мокрицьсий Б. Я., Кожевников Н. Е., Изотов С. А., Андреев A.A., Фадеев B.C. Опубл. 27.01.2010. Бюл,№ 3.
- A.c. СССР № 1 610 920. Способ нанесения износостойкого покрытия/ Мокрицкий Б. Я., Кабалдин Ю. Г. Опубл.27.01.2010. Бюл.№ 3.
- A.c. СССР № 1 394 745. Многослойный материал для режущего инструмента/ Кабалдин Ю. Г., Мокрицкий Б. Я., Изотов С. А., Андреев A.A., Кожевников Н. Е., Лазовский М. Р. Опубл. 27.01.2010.Бюл.№ 3.
- A.c. СССР № 1 351 154. Способ обработки режущего инструмента/ Кабалдин Ю. Г., Мокрицкий Б. Я., Андреев A.A., Изотов С. А., Кожевников Н. Е., Бурков A.A., Дунаевский Ю. В. Опубл. 27.01.2010. Бюл.№ 3.
- A.c. СССР № 1 412 370. Способ получения многослойного твердосплавного материала для режущего инструмента/ Кабалдин Ю. Г., Мокрицкий Б. Я., Андреев A.A., Дунаевский Ю. В., Изотов С. А., Аникин В. Н. Опубл. 27.01.2010. Бюл.№ 3.
- A.c. СССР № 1 593 091. Материал для режущего инструмента/ Кабалдин Ю. Г., Кравчук К. В., Кожевников Н. Е., Лазовский М. Р., Мокрицкий Б. Я., Верещака A.C. Опубл. 10.04.2010. Бюл.№ 10.
- A.c. СССР № 1 549 103. Катод для нанесения композиционных покрытий/ Мокрицкий Б. Я., Кабалдин Ю. Г., Кожевников Н. Е., Аникеев А. И. 0публ.27.01.2010. Бюл. № 3.
- A.c. СССР № 1 468 002. Материал катода для нанесения износостойкого покрытия на режущий инструмент/ Мокрицкий Б. Я., Кабалдин Ю. Г., Кожевников Н. Е., Мельниченко А. Ф., Андреев A.A., Козлов В. К. Опубл. 27.01.2010. Бюл.№ 3.
- A.c. СССР № 1 385 641. Материал для покрытия на режущий инструмент/ Кабалдин Ю. Г., Мокрицкий Б. Я., Кожевников Н. Е., Андреев A.A., Мельниченко А. Ф., Щелкунов Б. П., Киле A.A. Опубл. 27.01.2010. Бюл.№ 3.
- A.c. СССР № 1 383 620. Металлорежущий инструмент/ Кабалдин Ю. Г., Мокрицкий Б. Я., Кожевников Н. Е., Изотов С. А., Андреев A.A., Бурков A.A., Лозовский М. Р. Опубл. 10.04.2010. Бюл № 10.
- A.c. СССР № 1 413 839. Многослойная режущая пластина/ Кабалдин Ю. Г., Мокрицкий Б. Я., Изотов С. А., Андреев A.A., Кожевников Н. Е., Лазовский М. Р. Опубл. 27.01.2010. Бюл.№ 3.
- A.c. СССР № 1 556 013. Многослойный материал для режущего инструмента/ Кабалдин Ю. Г., Мокрицкий Б. Я., Изотов С. А., Андреев A.A., Кожевников Н. Е., Лазовский М. Р. Опубл. 27.01.2010. Бюл.№ 3.
- A.c. СССР № 1 383 621. Способ нанесения покрытия/ Кабалдин Ю. Г., Мокрицкий Б. Я., Селезнёв В. В., Семашко H.A., Тараев С. П. Опубл. 27.01.2010. Бюл.№ 3.
- A.c. СССР № 1 385 393. Способ нанесения многослойного покрытия на твёрдосплавный инструмент/ Мокрицкий Б. Я., Кабалдин Ю. Г., Селезнёв В. В., Семашко H.A., Тараев С. П. Опубл. 27.01.2010. Бюл.№ 3.
- A.c. СССР № 1 642 692. Способ изготовления режущих пластин из оксидной керамики/ Кабалдиш ЮїГ., Мокрицкиш Б-Я, Аникин В: Н-, — Вёрещака A.C., Ковалёв 0: Б-, Григорьев C. HV Опубл. 27:01.2010- Бюл.ЖЗ.
- A.c. СССР № 1 616 056. Способ изготовления- режущего инструмента. Мокрицкий ЪЩ Кабалдин ЮЛГ., Ковалёву 0-Б, Мельников-Р:Д. Опубл. 27.01.2010- Бюл.№ 3.
- Кабалдин, Ю.Г., Мокрицкий, Б.Я., Аникин, В.Н., Ковалёв, О. Б. Надёжность инструмента из оксидно-карбидной керамики.//. Машиностроитель, 19S9, № 5, с. 34.
- А.с- СССР № 1 723 828- Способ- изготовления* инструмента из кубического нитрида бора/ Кабалдин Ю-Г., Шепелев A.A., Киле A.A., М0криці^й'Б.:Яї,.Єа Бюл-.№ 10'-.
- A.c. СССР № 1 670 880- Способ- изготовления? инструмента из кубического нитрида бора/Кабалдин Ю.Г., Шепелев A.A., Киле A.A.,. Мокрицкий Б. Я-,. Савчук ВТ., Хрульков Н. В., Матвеев Ю. Ф. Опубл. 10.04.2010. Бюл.№ 10.
- Мокрицкий, Б.Я. Повышение работоспособности металлорежущего инструмента.//Технология машиностроения, № 8, 2010, с. 33−36.
- A.c. СССР № 1 232 380, МКИ В 23 В 25/06. Способ прогнозирования стойкости режущего инструмента.// Подураев, ВН., Кибальченко A.B., Алтухов В Н., 1984.
- A.c. СССР № 1 282 979, МКИ В23В47/24. Устройство для контроля поломки стержневого инструмента./ Зусман Б. М., Шигалев F.A., 1985-
- A.c. СССР № 1 310 692, МКИ G 01 N 3/58. Способ контроля качества режущего инструмента./ Базаров A.A., Вдовин А. И., Вирский A.A. и др., 1987.
- Кабалдин, Ю.Г., Мокрицкий, Б.Я. Приборы для контроля качества инструмента.// Станки и инструмент, 1990, с. 18−19.
- Мокрицкий, Б.Я., Алешин, С.Д. Диагностика разрушения инструмента.// Известия ВУЗов. Машиностроение, 1992, № 7−9, с.141−146.
- A.c. СССР № 1 382 175. Способ определения качества сцепления покрытия с основой/ Семашко H.A., Кабалдин Ю. Г., Мокрицкий Б. Я., Тараев С. П. 0публ.27.01.2010. Бюл.№ 3.
- Мокрицкий, Б.Я., Федоров, A.B., Мокрицкая, Е. Б. Оценка сопротивляемости стальных изделий усталостному разрушению по критерию трещиностойкости.// Известия ВУЗов. Машиностроение, 1996, № 7−9, с.97−108.
- A.c. СССР № 1 342 227. Способ акустического контроля физико-механических свойств изделий/ Семашко H.A., Мокрицкий Б. Я., Кабалдин Ю. Г., Гайнулин И. Ф. 0публ.27.01.2010. Бюл.№ 3.
- A.c. СССР № 1 522 913. Способ акустического контроля трещиностойкости изделий/ Кабалдин Ю. Г., Семашко H.A., Мокрицкий Б. Я., Тараев С. П., Селезнёв В. В. Опубл. 27.01.2010. Бюл.№ 3.
- A.c. СССР № 1 711 569. Способ оценки трещиностойкости покрытий/ Мокрицкий Б. Я., Сергеев В. А., Медакин В. Н., Южаков Н. И. Опубл. 27.01.2010. Бюл.№ 3.
- A.c. СССР № 1 752 060. Способ динамической оценки качества сцепления покрытия с подложкой/ Мокрицкий Б. Я., Медакин В. Н., Сергеев В. А., Шанин В. М. 0публ.27.01.2010. Бюл.№ 3.
- A.c. СССР № 1 711 568. Способ оценки трещиностойкости покрытия/ Мокрицкий Б. Я., Медакин В. Н., Сергеев В. А., Алексеев Ю. К. Опубл. 27.01.2010. Бюл.№ 3.
- A.c. СССР № 1 752 059. Способ динамической оценки качества сцепления покрытия с подложкой/ Мокрицкий Б. Я., Медакин В. Н., Сергеев В. А., Шанин В. М. Опублю27.01.2010. Бюл.№ 3.
- A.c. СССР № 1 667 497. Устройство для определения физико-механических свойств образцов материалов/ Мокрицкий Б. Я., Кабалдин Ю. Г., Семашко H.A., Зиновьев М. Н. Опубл. 27.01.2010. Бюл. № 3.
- Мокрицкий, Б.Я. Акустическая эмиссия как средство оценки и прогнозирования свойств инструментальных материалов. // Вестник машиностроения, № 10, 2010, с. 76−78.
- Мокрицкий, Б.Я. Метод оценки свойств инструментальных материалов и диагностики работоспособности инструмента. // Заводская лаборатория. Диагностика материалов., № 9, 2010, с.41−44.
- Патент РФ № 2 147 737. Устройство для испытания материалов/ Мокрицкая Е. Б., Семашко H.A., Мокрицкий Б. Я. 0публ.20.04.2000. Бюл.№ 11.
- Патент РФ № 2 140 076. Способ акустического контроля трещиностойкости изделий/ Мокрицкая Е. Б., Семашко H.A., Мокрицкий Б. Я., Вахрушев О. М. 0публ.9.07.1998, Бюл.№ 29.
- Наумов, A.B., Калайдо, В.В., Красико, В. Н. Методика оценки трещиностойкости материалов// Заводская лаборатория, 1992, № 7, с.22−24.
- Патент РФ № 2 140 075. Способ исследования свойств материала изделий. Семашко H.A., Мокрицкая Е. Б., Мокрицкий Б. Я., Селезнёв В. В., Фролов Д. Н. Опубл. 9.07.1999. Бюл. № 29.
- Патент РФ № 2 138 039. Способ контроля свойств и диагностики разрушения изделия/ Семашко H.A., Мокрицкая Е. Б., Мокрицкий Б. Я., Филоненко С. Ф. Опубл. 20.09.1999. Бюл. № 26.
- Патент РФ № 2 138 038. Способ контроля физико-механических свойств изделий/ Семашко H.A., Мокрицкая Е. Б., Мокрицкий Б. Я., Филоненко С. Ф., Вахрушев О. М. Опубл. 20.09.1999. Бюл. № 26.
- Мокрицкий, Б.Я. Управление работоспособностью металлорежущего инструмента путём нанесения покрытий// Металлообработка, № 3, 2010, с. 1215.
- Мокрицкий, Б.Я. Оценка прочности структурных элементов инструментальных материалов// Технология металлов, № 5, 2010, с.38−43.