Восстановление и упрочнение деталей машин и оборудования АПК микродуговым оксидированием
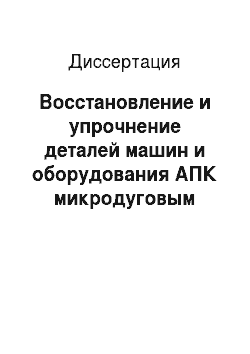
Эксплуатационные испытания показали, что при наработке 1150. 1200 мото-ч у опытных насосов НШ-32У-3 и НШ-10Е с деталями, упрочненными МДО, подача была на 16.23% выше, чем у серийных насосов. Средний ресурс наконечников молочных насосов 50-ЗЦ7Д-20 марки Г2-ОПД, восстановленных ГПН и упрочненных МДО, составил 1200. 1500 ч, а стандартных — 900.960 ч. При испытаниях деталей (поршень гидромуфты КП… Читать ещё >
Содержание
- ГЛАВА 1. СОСТОЯНИЕ ВОПРОСА, ЦЕЛЬ И ЗАДАЧИ ИССЛЕДОВАНИЙ
- 1. 1. Алюминиевые сплавы и коррозионностойкие стали, применяемые для изготовления деталей машин и оборудования АПК
- 1. 2. Алюминийсодержащие порошки, используемые при восстановлении деталей и ремонте узлов и их характеристики
- 1. 3. Анализ способов восстановления и упрочнения деталей из алюминиевых сплавов и коррозионностойких сталей
- 1. 4. Микродуговое оксидирование — как перспективный способ восстановления и упрочнения деталей
- 1. 5. Анализ составов электролитов, применяемых при микродуговогом оксидировании деталей
- 1. 6. Анализ износов основных деталей из алюминиевых сплавов и коррозионностойких сталей на предмет их возможного восстановления и упрочнения микродуговым оксидированием
- 1. 7. Выводы, цель и задачи исследований
- ГЛАВА 2. ТЕОРЕТИЧЕСКОЕ ОБОСНОВАНИЕ ТЕХНОЛОГИЙ ВОССТАНОВЛЕНИЯ И УПРОЧНЕНИЯ ДЕТАЛЕЙ С ПРИМЕНЕНИЕМ МИКРОДУГОВОГО ОКСИДИРОВАНИЯ
- 2. 1. Электрический пробой оксидных пленок при микродуговом оксидировании
- 2. 2. Теоретическое обоснование формирования толстослойных оксидных покрытий способом микродугового оксидирования в электролите типа «K0H-Na2Si03»
- 2. 3. Теоретическое обоснование возникновения сжимающих внутренних напряжений в покрытиях, полученных микродуговым оксидированием
- 2. 3. 1. Обзор гипотез о происхождении внутренних напряжений в покры-(f тиях
- 2. 3. 2. Влияние внутренних напряжений на прочность восстановленных изделий. ф 2.3.3. Механизм образования внутренних напряжений в покрытиях, сформированных микродуговым оксидированием
- 2. 3. 4. Методика определения внутренних напряжений в покрытиях, полученных МДО
- 2. 4. Оценка механизма взаимодействия частицы с основой при газодинамиче-^ ском напылении алюминиевых покрытий
- 2. 5. Выводы
- ГЛАВА 3. ПРОГРАММА И МЕТОДИКА ИССЛЕДОВАНИЙ
- 3. 1. Программа исследований
- 3. 2. Оборудование и материалы для проведения исследований
- 3. 2. 1. Используемые марки сплавов и образцы
- 3. 2. 2. Оборудование и материалы для газопламенного напыления
- 3. 2. 3. Оборудование и материалы для сверхзвукового газодинамического напыления
- 3. 2. 4. Оборудование и материалы для микродугового оксидирования. 108 Ф
- 3. 3. Приготовление, контроль и оценка стабильности электролитов для микродугового оксидирования
- 3. 4. Методики определения адгезии покрытий
- 3. 4. 1. Методика определения адгезии покрытий, полученных газопламенным напылением
- 3. 4. 2. Методика определения адгезии покрытий, полученных сверхзвуковым газодинамическим напылением
- 3. 4. 3. Методика определения адгезии покрытий, полученных МДО
- 3. 5. Методика измерения скорости частиц при сверхзвуковом газодинамическом напылении
- 3. 6. Методика измерения толщины покрытий
- 3. 7. Методика измерения микротвердости покрытий. ф
- 3. 8. Методика исследования равномерности покрытий, полученных МДО
- 3. 9. Методика определения выхода вещества по энергии при МДО
- 3. 10. Методика определения сквозной пористости оксидно-керамических ф покрытий
- 3. 11. Методика проведения рентгеноспектрального анализа
- 3. 12. Методика проведения рентгеноструктурного анализа
- 3. 13. Методика проведения коррозионных испытаний
- 3. 14. Методика определения внутренних напряжений
- 3. 14. 1. Методика определения внутренних напряжений в покрытиях, полученных способами напыления
- 3. 14. 2. Методика определения внутренних напряжений в покрытиях после МДО
- 3. 15. Методика испытаний на изнашивание
- 3. 16. Методика проведения ускоренных стендовых испытаний насосов НШ-10Е и НШ-32У
- 3. 17. Определение ошибки эксперимента и повторности опыта
- 4. 1. Исследование состава и структуры покрытий
- 4. 1. 2. Рентгеноструктурный анализ покрытий, полученных газопламенным напылением с упрочнением МДО в электролите типа «КОН-Na2Si03»
- 4. 1. 3. Рентгеноструктурный анализ покрытий, полученных МДО в электролите типа «КОН-Н3ВО3»
- 4. 1. 4. Микроструктура покрытий, сформированных ГДН. ф
- 4. 2. Исследование прочности сцепления покрытий
- 4. 2. 1. Исследование сцепляемости покрытий, полученных газопламенным напылением
- 4. 2. 2. Исследование сцепляемости покрытий, полученных сверхзвуковым гдн
- 4. 2. 3. Исследование сцепляемости покрытий, полученных МДО
- 4. 3. Оценка скорости полета частиц порошка при сверхзвуковом ГДН. ф
- 4. 4. Исследование влияния параметров МДО на толщину покрытий
- 4. 4. 1. Исследование толщины покрытий, полученных МДО на литейных алюминиевых сплавах в электролите типа «K0H-Na2Si03>>
- 4. 4. 2. Исследование толщины покрытий, полученных МДО на деформируемых алюминиевых сплавах в электролите типа КОН-НзВОз»
- 4. 4. 3. Исследование толщины оксидно-керамических слоев на покрытиях, полученных способами напыления
- 4. 5. Оценка выхода вещества по энергии при МДО
- 4. 6. Оценка стабильности электролита при МДО
- 4. 6. 1. Электролит типа «K0H-Na2Si03»
- 4. 6. 2. Электролит типа «К0Н-Н3В03»
- 4. 7. Исследование микротвердости покрытий, полученных МДО
- 4. 7. 1. Исследование микротвердости покрытий на литейных алюминиевых сплавах, полученных в электролите типа «K0H-Na2Si03>>
- 4. 7. 2. Исследование микротвердости покрытий на деформируемых алю-Ф миниевых сплавах, полученных в электролите типа «КОН
- 4. 7. 3. Исследование микротвердости покрытий, полученных МДО на напыленных поверхностях. 4.8. Исследование равномерности распределения оксидно-керамических покрытий
- 4. 9. Исследование сквозной пористости покрытий, полученных МДО на алюминиевых сплавах
- 4. 10. Исследование коррозионной стойкости оксидно-керамических покрытий
- 4. 10. 1. Коррозионная стойкость покрытий, полученных в электролите типа «K0H-Na2Si03»
- 4. 10. 2. Коррозионная стойкость покрытий, полученных в электролите типа «КОН-Н3ВО3»
- 4. 11. Анализ внутренних напряжений
- 4. 11. 1. Анализ внутренних напряжений в покрытиях, полученных ГДН с упрочнением МДО
- 4. 11. 2. Анализ внутренних напряжений в покрытиях, полученных газопламенным напылением с упрочнением МДО
- 4. 11. 3. Анализ внутренних напряжений в покрытиях, полученных МДО
- 4. 12. Исследование износостойкости оксидно-керамических покрытий
- 4. 12. 1. Износостойкость покрытий, полученных МДО на алюминиевых сплавах
- 4. 12. 1. 1. Износостойкость покрытий, полученных в электролите типа «K0H-Na2Si03»
- 4. 12. 1. 2. Износостойкость покрытий, полученных в электролите типа «КОН-Н3ВО3»
- 4. 12. 2. Износостойкость покрытий, полученных газопламенным напылением с упрочнением МДО
- 4. 12. 3. Износостойкость покрытий, полученных сверхзвуковым ГДН с упрочнением МДО
- 4. 13. Стендовые и эксплуатационные испытания восстановленных и упрочненных деталей
- 4. 13. 1. Стендовые испытания шестеренных насосов НШ-32У и НШ-10Е
- 4. 13. 2. Эксплуатационные испытания шестеренных насосов НШ-32У и НШ-10Е
- 4. 13. 3. Эксплуатационные испытания деталей, восстановленных газопламенным напылением с упрочнением МДО
- 4. 13. 4. Эксплуатационные испытания деталей, восстановленных сверхзвуковым ГДН с упрочнением МДО
- 4. 14. Выводы
Восстановление и упрочнение деталей машин и оборудования АПК микродуговым оксидированием (реферат, курсовая, диплом, контрольная)
Восстановление и упрочнение изношенных деталей сельскохозяйственной техники и перерабатывающих производств АПК многие годы не теряет своей актуальности, поскольку является основным путем снижения себестоимости и повышения качества ремонта техники и оборудования.
Особенно актуален данный вопрос применительно к перерабатывающим отраслям АПК, где важно обеспечить не только технологическое качество восстанавливаемых деталей при сравнительно низкой себестоимости их восстановления, но и строго соблюдать санитарно-гигиенические требования, исключающие загрязнение пищевых продуктов.
В условиях ограничения финансовых и материальных ресурсов, снижения поставок техники, оборудования и запасных частей в сельскохозяйственное производство и ее перерабатывающие сферы, старения и удорожания сельскохозяйственной техники и перерабатывающего оборудования (особенно импортного), нехватки и дороговизны запасных частей возникает необходимость дальнейшего развития и совершенствования технологических процессов ремонта машин и восстановления деталей.
Большой вклад в развитие технологий ремонта машин, в том числе повышения их надежности внесли: Батищев А. Н., Авдеев М. В., Ачкасов К. А., Ерохин М. Н., Воловик E. JL, Кряжков В. М., Курчаткин В. В., Лялякин В. П., Поляченко А. В., Черноиванов В. И., Северный А. Э., Тельнов Н. Ф., Пучин Е. А., Носихин П. И., Мороз В. П., Голубев И. Г., Бурумкулов Ф. Х., Стрельцов В. В., Бугаев В. Н., Кошкин К. Т., Лезин П. П., Некрасов С. С. и другие ученые.
Опыт ремонтно-технических предприятий показывает, что в последние годы наметилась тенденция использования упрочняющих технологий, которые позволяют повысить относительную износостойкость деталей и соединений в несколько раз. Так, например, микродуговое оксидирование (МДО) деталей, изготовленных из алюминиевых сплавов, повышает их износостойкость в 2.6 раз. Данный способ поверхностной упрочняющей обработки деталей является достаточно простым и экологически безопаснымполучаемые покрытия соответствуют санитарным нормам и могут использоваться для контакта с пищевыми продуктами.
Однако широкое применение МДО для восстановления деталей из литейных алюминиевых сплавов и особенно упрочнения стальных, предварительно восстановленных различными способами газотермического напыления, сдерживается отсутствием теоретических основ восстановления и упрочнения. Поэтому разработка технологических основ восстановления и упрочнения деталей машин и оборудования АПК микродуговым оксидированием является актуальной проблемой.
Большой вклад в развитие микродугового оксидирования, как способа повышения долговечности алюминиевых деталей и соединений внесли: Марков Г. А., Гордиенко П. С., Гнеденков С. В., Малышев В. Н., Снежко Л. А., Черненко В. И., Миронова М. К., Федоров В. А., Герций О. Ю., Католикова Н. М., Великосельская Н. Д., Эпельфельд А. В., Атрощенко Э. С., Чуфистов О. В., Барыкин Н. В., Коломейченко А. В. и другие ученые.
Научную новизну исследований составляют:
— обоснованные и уточненные теоретические гипотезы электрического пробоя оксидных пленок, формируемых МДО;
— теоретические обоснования формирования толстослойных оксидных покрытий способом МДО в электролите типа «K0H-Na2Si03»;
— разработанные теоретические гипотезы о происхождении и образовании внутренних напряжений в покрытиях, полученных МДО, их влияние на прочность восстановленных изделий;
— уточненная методика определения внутренних напряжений в покрытиях, полученных МДО;
— теоретическая оценка механизма взаимодействия частицы с основой при сверхзвуковом газодинамическом способе напыления покрытий;
— установленные зависимости толщины, равномерности, микротвердости, пористости, сцепляемости, коррозионной стойкости и износостойкости покрытий, полученных на литейных алюминиевых сплавах и напыленных поверхностях от состава электролитов и режимов МДОзависимости выхода вещества по энергии при МДО и внутренних напряжений в покрытиях от режимов оксидированиярезультаты оценки стабильности электролитов и исследований состава и структуры покрытийзависимости сцепляемости напыленных алюминиевых покрытий от фракции порошковых материалов и режимов ГПН и ГДН.
Работа осуществлялась в соответствии с планами научно-исследовательских работ ФГОУ ВПО РГАЗУ.
Результаты исследований реализованы в пяти руководящих технических материалах (РТМ) и методических рекомендациях, утвержденных Минсельхозом Российской Федерации в 1997 г. и в 2005 г.
Технологические процессы восстановления и упрочнения колодцев корпусов шестеренных насосов типа НШ и НШ-У, поршней гидромуфт КП тракторов типа «Fendt Favorit-824», наконечников молочных центробежных насосов, пробок молочных кранов, седел клапанных коробок насосных установок типа Ж6-ВНП-10/32, внедрены (приняты к внедрению) на ряде ремонтных предприятий агропромышленного комплекса.
Результаты исследований используются в учебном процессе ФГОУ ВПО РГАЗУ и ФГОУ ВПО ОрелГАУ, отражены в учебном пособии, допущенным Минсельхозом РФ в качестве учебного пособия для вузов.
Основные результаты исследований доложены на семинарах, конференциях и т. д.:
— научных конференциях профессорско-преподавательского состава РГАЗУ и ОрелГАУ в 1995;2003 г. г.;
— межвузовских областных конференциях молодых ученых Орловской области (г. Орел, 1996 и 1998 г. г.);
— семинарах (РИИАМА, 1996 г. и г. Москва, 1996 г.);
— двеннадцати международных конференциях (г. Оренбург, ИПК ОГУ, 1997, 2002 г. г.- г. Москва, МГАУ, 1998, 2000 г. г.- г. Москва, ГОС.
НИТИ, 2003, 2004 г. г.- г. Орел, ОрелГАУ, 2000, 2001,2004,2005 г. гг. Белгород, БГСХА, 2001, 2002 г. г.);
— научно-технических и научно-практических конференциях (г. Москва, ВНИИТУВИД «Ремдеталь», 1999 г.- г. Пенза, Приволжский дом знаний, 1998, 2000, 2001 г. г.- г. Москва, МЭИ (ТУ), 2000 г.);
— заседаниях кафедры «Надежность и ремонт машин им. И.С. Левит-ского» ФГОУ ВПО РГАЗУ в 1997, 2003;2005 г. г.
На защиту выносятся:
— теоретические основы формирования толстослойных оксидно-керамических покрытий МДО на деталях сельскохозяйственной техники, изготовленных из литейных алюминиевых сплавов;
— теоретическое обоснование возникновения сжимающих внутренних напряжений в покрытиях, полученных МДО, и уточненная методика их определения;
— результаты теоретических и экспериментальных исследований по оценке механизма взаимодействия частиц с основой при сверхзвуковом газодинамическом способе напыления алюминиевых покрытий;
— результаты экспериментальных исследований по получению прочно-сцепленных алюминиевых покрытий газопламенным напылением на деталях, изготовленных из коррозионностойких сталей;
— результаты экспериментальных исследований физико-механических и эксплуатационных свойств деталей, восстановленных и упрочненных МДО и комбинированными способами (включающими МДО, как упрочняющую обработку);
— новые способы и устройства для восстановления и упрочнения деталей МДО, защищенные патентами Российской Федерации;
— рекомендации по применению предлагаемых технологий и разработок в ремонтном производстве и их технико-экономическая оценка.
ОБЩИЕ ВЫВОДЫ.
1. Анализ технического состояния изношенных деталей машин и оборудования АПК позволил разбить детали на группы по значению износа и разработать технологические процессы восстановления и упрочнения каждой группы:
• Детали из алюминиевых сплавов:
I группа: детали, имеющие износ не более 0,06 мм. Рекомендуется технология восстановления и упрочнения МДО.
II группа: детали, имеющие износ свыше 0,06 мм до 3, 0 мм. Рекомендуется комбинированная технология восстановления:
— расточка под ремонтный размер с последующим упрочнением МДО;
— пластическое деформирование с последующим упрочнением МДО;
— сверхзвуковое ГДН с последующим упрочнением МДО.
III группа: детали, имеющие износ свыше 3,0 мм. Рекомендуется комбинированная технология восстановления:
— постановка алюминиевой ДРД, упрочненной МДО.
• Детали из коррозионностойких сталей:
I группа: детали, работающие при небольших контактных нагрузках, имеющие износ до 0,6 мм. Рекомендуется комбинированная технология восстановления:
— газопламенное напыление с последующим упрочнением МДО.
II группа: детали, работающие при небольших и средних контактных нагрузках, имеющие износ до 3,0 мм. Рекомендуется комбинированная технология восстановления:
— сверхзвуковое ГДН с последующим упрочнением МДО.
III группа: детали, имеющие износ свыше 3,0 мм. Рекомендуется комбинированная технология восстановления:
— постановка алюминиевой ДРД, упрочненной МДО.
2. Выявленное при рентгеноспектральном анализе распределение химических элементов по толщине МДО-покрытий в электролите типа «КОН-Nci2Si03» подтверждает теоретические предположения о возможности восстановления деталей МДО за счет компонентов жидкого стекла.
Рентгеноструктурный анализ показал, что независимо от режимов МДО и типа используемого электролита в упрочненном слое присутствуют фазы а-, у — А1гОг. В зависимости от типа электролита в покрытии могут также присутствовать фазы муллита и различные интерметаллидные соединения.
3. Прочность сцепления покрытий, полученных ГЕН на коррозионно-стойких сталях, зависит от дистанции напыления, шероховатости напыляемой поверхности и фракции напыляемого порошка. С учетом этого рекомендованы следующие рациональные режимы ГПН: толщина подслоя (порошок ПТ-Ю5Н) — 100.200 мкм, основного слоя (порошок САС-2) -150.300лшидистанция напыления 180.220ммфракция порошка 60−100 мкмшероховатость напыляемой поверхности Rz = 60−100 мкм. На указанных режимах прочность сцепления подслоя со стальной основой составит 49.53 МПа, основного слоя с подслоем — 12,5. 14 МПа.
4. В ходе исследований установлено, что скорость частиц порошка при сверхзвуковом ГДН составляет около 580.740 м/с. Адгезионная прочность сцепления покрытий, полученных ГДН, определяется температурой частиц напыляемого материала, их скоростью и длительностью их взаимодействия с основой.
На основе теоретической оценки механизма взаимодействия частиц с основой получены формулы (2.92), (2.94) и (2.95) для определения критических скоростей и диаметра частиц порошка, позволяющие подобрать наиболее рациональные режимы напыления.
Напыление порошка А-80−13, фракцией 30.50 мкм, необходимо проводить при давлении воздуха — 0,7 МПа, температуре воздуха — 400 °C, дистанции напылении — 10. 15 мм. При данных условиях прочность сцепления покрытий на алюминиевой основе составит 55.65 МПа, на стальной основе -45.50 МПа.
Качественные исследования прочности сцепления МДО-покрытий, полученных на напыленных поверхностях и алюминиевых сплавах показали, что на контролируемых поверхностях не наблюдалось вздутий и отслаивания покрытий, независимо от типа используемого электролита, плотности тока и продолжительности оксидирования.
5. Установлено, что при МДО наибольшее влияние на толщину покрытия оказывает состав электролита, плотность тока, продолжительность процесса, расстояние между электродом и деталью, и напряжение пробоя. Рациональные значения плотностей тока для оксидирования деталей следующие: литейные сплавы — 25.30 А/дм2- деформируемые сплавы — 15.20 А/дмнапыленные поверхности — 15.20 А/дм2.
Для восстановления алюминиевых деталей МДО рекомендуется электролит следующего состава: КОН — 1,8.2,1 г/л, Na2Si03 — 14.18 г/л. При этом эффективный прирост на сторону составит около 70.90 мкм при общей средней толщине керамики 108. 115 мкммикротвердость покрытий — 7.8 ГПа.
Рациональные составы электролитов для упрочнения напыленных поверхностей следующие: КОН — 2,9.3,6 г/л, Na2Si03 — 4.6 г/л или КОН -4.6 г/л, Н3ВО3 — 20.25 г/л, крахмал — 6. 12 г/л. На покрытиях, полученных ГПН, толщина упрочненного слоя составит около 90. 125 мкм, средняя микротвердость 10.11 ГПана покрытиях, полученных ГДН, — 100.135 мкм и 14. 16 ГПа, соответственно.
Для упрочнения деформируемых сплавов наиболее предпочтителен электролит типа «КОН-Н3ВО3», толщина упрочненного слоя в котором составит около 120. 150 мкм, а микротвердость 16.19 777а.
Рекомендуемая продолжительность МДО составляет 100. 120 минтемпература электролитов 20.40 °С. Анодная составляющая напряжения процесса в конце оксидирования должна составлять не менее 580.620 В.
6. Для получения равномерных МДО-покрытий расстояние между электродом и оксидируемой деталью должно составлять не более 5. 10 мм. При этом электрод должен повторять конфигурацию оксидируемой поверхности.
7. Микротвердость МДО-покрытия неоднородна по толщине и зависит от режимов оксидирования, типа применяемого электролита и его состава. Характер распределения микротвердости по толщине покрытий связан с изменением его фазового состава.
8. Установлено, что энергоемкость МДО зависит от режимов обработки и состава электролита. Эффективный выход вещества по энергии на рациональных режимах оксидирования литейных алюминиевых сплавов составляет 0,13. 0,24 г/кВт ¦ч.
9. Стабильность электролитов зависит от продолжительности работы ванны МДО и режимов процесса. Долговечность электролитов до их корректировки следующая: а) электролит типа «K0H-Nci2Si03», рекомендуемый для восстановления и упрочнения алюминиевых деталей, — около 18 А-ч/л.- б) электролиты для упрочнения напыленных поверхностей: «K0H-Na2Si03» — около 70 А-ч/л- «КОН-Н3ВО3» — около 60 А-ч/л. Добавка в электролит типа «КОН-Н3ВО3» крахмала в количестве 6. 12 г/л повышает его работоспособность примерно в два раза.
10. Сквозная пористость покрытий, сформированных МДО, зависит от.
•у марки сплава и режимов оксидирования и составляет 6−40 пор/см. Сравнительные коррозионные испытания показали, что показатели коррозии деформируемых алюминиевых сплавов, упрочненных МДО в электролите типа «КОН-Н3ВО3», меньше в 3−5 раз, чем у сплавов без покрытий и БрА5, принятых за эталон сравнения.
Коррозионная стойкость упрочненных слоев, полученных МДО в элек тролите типа «K0H-Na2Si03» на напыленных поверхностях, в 1,4. 1,5 раза выше, чем у коррозионностойкой стали 12Х18Н10Т.
11. В покрытиях, сформированных МДО, возникают напряжения сжатия, не превышающие 12 МПа. Уточнена методика определения значений внутренних напряжений в МДО-покрытиях с учетом специфических особенностей процесса.
12. Скорость изнашивания покрытий, полученных МДО на рациональных режимах, на алюминиевых сплавах и напыленных поверхностях, в 4.6 раз ниже скорости изнашивания неупрочненных деталей. Наибольшей износостойкостью обладают покрытия, полученные в электролите типа «КОН-Н3ВО3».
13. Стендовые испытания шестеренных насосов НШ-32У-3 и НШ-10Е показали, что относительная износостойкость соединений насосов с восстановленными и упрочненными МДО деталями в 1,5. 1,9 раза выше, чем с серийными деталями.
Эксплуатационные испытания показали, что при наработке 1150. 1200 мото-ч у опытных насосов НШ-32У-3 и НШ-10Е с деталями, упрочненными МДО, подача была на 16.23% выше, чем у серийных насосов. Средний ресурс наконечников молочных насосов 50-ЗЦ7Д-20 марки Г2-ОПД, восстановленных ГПН и упрочненных МДО, составил 1200. 1500 ч, а стандартных — 900.960 ч. При испытаниях деталей (поршень гидромуфты КП трактора «Fendt Favorit 824», вал стенда СПО-35−89 для укладки металло-корда автотракторных шин, упорный подшипник турбокомпрессора ТКР-11−238), восстановленных ГДН с упрочнением МДО, в течение заданной наработки каких-либо дефектов покрытий выявлено не было.
14. Разработанные технологические рекомендации по восстановлению и упрочнению деталей машин и оборудования АПК внедрены на ряде предприятий Орловской области, использованы в пяти руководящих технических материалах, одном учебном пособии для вузов, одних нормативных методических рекомендациях, а также в учебном процессе при подготовке инженеров-механиков и руководящих и инженерных кадров АПК в ФГОУ ВПО ОрелГАУ и ФГОУ ВПО РГАЗУ.
По результатам исследований получены дипломы победителей конкурса молодых ученых Орловской области и фонда им. В. Потанина в 1997, 2003 годах.
Экономическая эффективность от внедрения разработанных технологий восстановления и упрочнения деталей на предприятиях Орловской области составит более 13 573,2 тыс. руб.
Список литературы
- Новиков А.Н. Технологические основы восстановления и упрочнения деталей сельскохозяйственной техники из алюминиевых сплавов электрохимическими способами. — Орел: Изд-во ОрелГАУ, 2001. — 233 с.
- Альтман М.Б., Андреев Г. Н., Арбузов Ю. П. и др. Применение алюминиевых сплавов. М.: Металлургия, 1985. — 344 с.
- Конструкционные материалы и покрытия в продовольственном машиностроении. Справочник. -М.: Машиностроение, 1984. 328 с.
- Казаков Н.Ф., Мартынов Г. А. Технология пищевого машиностроения. -М.: Машиностроение, 1982. 295 с.
- Фетисов Г. П., Карпман М. Г., Матюнин В. М. и др. Материаловедение и технология металлов. Учебник для студентов машиностроит. спец. вузов. -М.: Высш. шк., 2001. -638 с.
- Новиков А.Н. Ремонт деталей из алюминия и его сплавов. Учебное пособие. Орел: ОГСХА, 1997. — 57 с.
- Ульянов В.А., Пиманов Г. П. Рекомендации по восстановлению деталей газопламенным напылением. М.: ГОСНИТИ, 1988. — 48 с.
- Кудинов В.В., Бобров Г. В. Нанесение покрытий напылением. Теория, технология и оборудование. Учебник для вузов.- М.: Металлургия, 1992. -432 с.
- Основные виды продукции Торезского завода наплавочных твердых сплавов. Рекламный проспект. Торез: ТЗНТС, 1990. 29 с.
- Коломейцев А.Г., Голубев И. Г., Свищев В. И. Опыт восстановления деталей газотермическими методами. Обзорная информация. / Госкомсель-хозтехника СССР. М.: ЦНИИТЭИ, 1985. 39 с.
- Рекомендации по использованию порошковых материалов при проведении ремонтно-восстановительных работ с оборудованием «ДИМЕТ» моделей 402 и 403. /Рекламный проспект. Обнинск: ОЦПН, 2005. — 1 с.
- Кондратов С.И., Константиновский В. А., Чигарев В. В. Метод высокоскоростного напыления антикоррозионного алюминиевого покрытия. // Сварочное производство. 1992. — № 6, С. 15.
- ГОСТ 28 844–90 Покрытия газотермические упрочняющие и восстанавливающие. Общие требования. «Издательство стандартов», 1991. 15 с.
- Надежность и ремонт машин. / Под ред. В. В. Курчаткина. М.: Колос, 2000. — 776 с.
- Пучин Е.А., Дидманидзе О. Н., Лезин П. П. и др. Надежность технических систем. М.: УМЦ «Триада», 2005. — 353 с.
- Батищев А.Н., Чижикова Т. В., Голубев И. Г. и др. Монтаж, эксплуатация и ремонт технологического оборудования перерабатывающих отраслей АПК. /Справочник. М.: Информагротех, 1997. — 288 с.
- Сварка и свариваемые материалы: ВЗ-х т.Т.2. Технология и оборудование. Справ, изд./ Под ред. В. М. Ямпольского. М.: Издательство МГТУ им. Н. Э. Баумана, 1998. — 574 с.
- Васильев В.А., Югов Д. Н., Сельцер А. А. и др. Техническое обслуживание и ремонт сельскохозяйственной техники. /Справочник. М.: ГОСНИТИ, 1992.-2001 с.
- Есенберлин Р.Е. Восстановление автомобильных деталей сваркой, наплавкой и пайкой. М.: Транспорт, 1994, — 256 с.
- Справочник по пайке. / Под ред. И. Е. Петрунина. 3-е изд., перераб. и доп. М.: Машиностроение, 2003. — 776 с.
- Хромов В.Н., Сенченков И. К. Упрочнение и восстановление деталей машин термоупруго-пластическим деформированием: Орел: Издательство ОГСХА, 1999. — 21 е.- ил.
- Ремонт машин. / Под ред. Н. Ф. Тельнова. М.: Агропромиздат, 1992. -560 е.: ил.
- Черкун В.Е. Ремонт тракторных гидравлических систем. М.: Колос, 1984.-253 с.
- Полухин П.И., Гун Г.Я., Галкин A.M. Сопротивление пластической деформации металлов и сплавов. / Справочник. М.: Металлургия, 1976. -352 с.
- Тельнов Н.Ф., Клочковский Н. Н. Восстановление алюминиевых втулок шестеренных гидронасосов. // Механизация и электрификаци сельского хозяйства.-№ 12, 1988.-43.
- Батищев А.Н., Голубев И. Г., Лялякин В. П. Восстановление деталей сельскохозяйственной техники. М.: Информагротех, 1995. — 296 с.
- Носихин П.И. Повышение качества и ускорение обкатки отремонтированных дизелей на основе современных достижений трибологии. Дис. док. тех. наук. М., 1997.
- Черноиванов В.И., Лялякин В. П. Организация и технология восстановления деталей машин. /Изд. 2-е, доп. и перераб. М.: ГОСНИТИ, 2003. -488 с.
- Курчаткин В.В. Восстановление посадок подшипников качения сельскохозяйственной техники полимерными материалами. Дис. док. тех. наук. -М., 1989.-333 с.
- Батищев А.Н. Восстановление деталей гальваническими покрытиями. /Учеб.пособие. Всесоюзн. с. х. ин-т заоч. образования. М., 1991. — 72 с.
- Новиков А.Н. Технологические основы восстановления и упрочнения деталей сельскохозяйственной техники из алюминиевых сплавов электрохимическими способами. Дис. док. тех. наук. М., 1999. — 346 с.
- РТМ 70.0009.035−84 Технологический процесс восстановления деталей машин из алюминиевых сплавов. -М.: ГОСНИТИ, 1986.-28 с.
- Гриф З.В., Комаров А. И., Куликов А. И. Плазменное напыление алюминиевых деталей при ремонте импортной строительной техники. // Сварочное производство. № 9, 1990. — С. 18.
- Иванов В.Г., Никитин В. П., Яцечко A.M. Термическая стойкость теплозащитных керамических покрытий на образцах из алюминиевых сплавов. // Сварочное производство. № 12, 1990. — С. 11−12.
- Хасун А. Техника напыления. Пер. с япон. М.: Машиностроение, 1975. -287 с.
- Клубникин B.C. О достижениях в термическом напылении покрытий. //Труды 6-й Международной конференции «Пленки и покрытия-2001». /Под ред. B.C. Клубникина. СПб.: Изд-во СПб ГТУ, 2001. — С. 15−21.
- Полонский Л.Г. Историко-технические аспекты развития газотермического напыления покрытий. //Труды 5-й Международной конференции «Пленки и покрытия-1998». /Под ред. B.C. Клубникина. СПб.: Изд-во Полиплазма, 1998. — С. 47−52.
- Schwetzke R, Kreye Н. High velocity oxy-fuel spraying of tungsten carbide-based coatings-Schweissen and Schneiden, № 2, 2000, E29-E34.
- Коровин А.Я., Хромов В. Н. Оборудование для сверхзвукового газопламенного напыления покрытий. // РГАЗУ агропромышленному комплексу. /Сборник научных трудов. В 2-х частях. Ч. 2. — М.: РГАЗУ, 2000. -С. 183−186.
- Патент РФ № 2 100 474 С 23 С 4/00. Устройство для газодинамического нанесения покрытий из порошковых материалов. / Каширин А. И., Клюев О. Ф., Буздыгар Т. В. Опубл. Б.И. № 36, 1996.
- Клубникин B.C. Сверхзвуковое плазменное напыление высокоплотных и прочных покрытий. //Труды 5-й Международной конференции «Пленки и покрытия-1998». /Под ред. B.C. Клубникина. СПб.: Изд-во Полиплазма, 1998.-С. 35−38.
- Клубникин B.C., Карасев М. В., Петров Г. К. Плазменное напыление покрытий в активных средах. Л.: Об-во «Знание» РСФСР, JTO, ЛДНТП, 1990.-20 е., ил.
- Новиков О.Я., Тамкиви П. И., Тимошевский А. Н. и др. Многодуговые системы. Новосибирск: Наука. Сиб. отд-ние, 1988. — 133 с
- Dewsnap G.G., Heatcote L., Darnbrook G. Improvement in (or) relating to Plasma Jet Torches Patent GB N 959 472 publ. 03.06.64.
- Патент РФ № 2 183 695 С 23 С 24/04. Способ получения покрытий. / Ка-ширин А. И., Клюев О. Ф., Шкодкин А. В. Опубл. Б.И. № 17, 2002.
- Alkhimov А.Р., Kosarev V.F., Nesterovich N.I., Papyrin A.N., Shushpanov M.M. Gas-Dynamic Spraying Method for Applying Coating. // United States Patent N 5 302 414- Apr. 12, 1994.
- Алхимов А.П., Косарев В. Ф., Папырин А. Н. Метод «холодного» газодинамического напыления. // ДАН СССР, т.315,1990. С. 1062−1065.
- Воинов Б.А. Износостойкие сплавы и покрытия. М.: Машиностроение, 1988.- 118 с.
- Любимов В.В., Иванов А. В. Методика формирования многослойных ионно-плазменных покрытий на поверхностях деталей машин. // Упрочняющие технологии и покрытия № 2,2005. — С. 23−27.
- Горленко О.А. Износостойкость поверхностей упрочненных лазерной обработкой.// Трение и износ № 1, 1981. — С. 27−31.
- Коваленко B.C., Головко Л. Ф., Черненко B.C. Упрочнение и легирование деталей машин лучом лазера. К.: Техшка, 1990. — 123 с.
- Бурумкулов Ф.Х., Лялякин В. П., Иванов В. И. и др. Опыт применения электроискрового метода. //Техника в сельском хозяйстве. № 6. — 2001. -С. 22−25.
- Хенли В.Ф. Анодное оксидирование алюминия и его сплавов. Пер. с англ. /Под ред. Синявского B.C. М.: Металлургия, 1986. — 152 с.
- Грилихес С.Я., Тихонов К. И. Электролитические и химические покрытия. Теория и практика. JL: Машиностроение, 1990. — 270 с.
- Васильев В.В., Протасов В. Д., Болотин В. В. и др. Композиционные материалы. / Справочник. /Под общ. ред. В. В. Васильева, Ю.М. Тарнополь-ского. М.: Машиностроение, 1990. — 512 е.- ил.
- Астахов А.С., Буклагин Д. С., Голубев И. Г. Применение технической керамики в сельскохозяйственном производстве. М.: Агропромиздат, 1988.-95 с.
- Черненко В.И., Снежко В. И., Папанова И. И. Получение покрытий анод-но-искровым электролизом. Л.: Химия, 1991. — 128 е.: ил.
- Мамаев А.И., Чеканова Ю. Ю., Рамазанова Ж., М. Получене анодно-искровых покрытий методом микродугового оксидирования. //Физика и химия обработки материалов. № 4. 1999. — С. 41−44.
- Марков Г. А., Белеванцев В. И. и др. Микродуговое оксидирование // Вестник МГТУ. Сер. Машиностроение. № 1, 1992. С. 34−56.
- Корш С.В. Технология микродугового оксидирования из титановых и алюминиевых сплавов. //Прогрессивные материалы и технологии. № 1, 1993.-С. 188−189.
- А. св. СССР № 1 775 507 С 25 D 11/02. Способ микродугового оксидирования алюминиевых сплавов. /B.C. Скифский П. Е. Опубл. Б. И № 42, 1992.
- Тимошенко А. В. Магурова Ю.В. Микроплазменное оксидирование сплавав системы Al-Cu.// Защита металлов, Т. 31. № 5, 1995. С. 523 -531.
- Барыкин Н.В. Разработка технологии восстановления и упрочнения деталей из алюминиевых сплавов микродуговым оксидированием. Авто-реф. дис. канд. техн. наук.: 05.20.03. -М., 1994. 19 е.- ил.
- Коломейченко А.В. Технология упрочнения микродуговым оксидированием восстановленных наплавкой деталей из алюминиевых сплавов. Ав-тореф. дис. канд. техн. наук.: 05.20.03. Орел, 2000. — 16 е.- ил.
- Марков Г. А., Терлеева О. П., Шулепко Е. К. Микродуговые и дуговые процессы и перспективы их практического использования. //Тез. докл. научн.-техн. семинара «Анод-88″. Казань, 1988. — С. 73−75.
- Михеев А.Е., Терехин Н. А., Стацура В. В. и др. Технологические возможности микродугового оксидирования алюминиевых сплавов. //Вестник машиностроения. № 2. 2003. — С. 56−63.
- Николаев А.В., Марков Г. А., Пещевицкий В. И. Новое явление в электролизе. //Изв. СО АН СССР. Сер. „Химические науки“. 1977, вып. 5, № 12. — С32−33.
- Тюрин В. Три тысячи градусов микродуги. //Знание-сила. № 11, 1979. -С. 32−34.
- Бердиков В.Ф., Федоров В. А., Пушкарев О. И. и др. Нанесение корундовых покрытий на алюминиевую подложку методом микродугового оксидирования. //Вестник машиностроения. № 4,1991. — С. 64−65.
- Каракозов Э.С., Чавдаров А. В., Барыкин Н. В. Микродуговое оксидирование перспективный процесс получения керамических покрытий. //Сварочное производство. — № 6,1993. — С. 4−7.
- Гордиенко П.С., Руднев B.C. О кинетике образования МДО-покрытий на сплавах алюминия. //Защита металлов. Т. 26. № 3} 1990. — С. 467−470.
- Марков Г. А., Шулепко Е. К. Токовые режимы и переход к микродуговой стадии оксидирования. //Защита металлов. Т. 31. № 6, 1995. — С. 643 647.
- WENBIN XUE, ZHIWEI DENG, RUYI CHEN, TONGHE ZHANG, HUIMA. Microstructure and properties of ceramic coatings produced on 2024 aluminum alloy by microarc oxidation. //Journal of materials science 36(2001)2615−2619.
- WENBIN XUE, ZHIWEI DENG, RUYI CHEN, TONGHE ZHANG. Grow-thregularity of ceramic coatings formed by microarc oxidation on Al-Cu-Mg alloy. Thin Solid Films 372(2000) 114−117.
- Ерохин A.JI. Физико-химические процессы при плазменно-электролитической обработке сплавов алюминия в силикатных электролитах. Дис. канд. тех. наук: 05.20.03. -ТулГУ: Тула, 1995.-240 с.
- Ефремов А.П., Эпельфельд А. В., Харитонов Б. В. Влияние токовых режимов микродугового оксидирования на повышение коррозионной стойкости деталей из алюминиевых сплавов. //Защита от коррозии и охрана окружающей среды. № 4, 1993. — С. 10−14.
- Чернышов Ю.И., Крылович Ю. Л., Гродникас Г. Х. Формирование покрытий в импульсном режиме микродугового оксидирования. //Сварочное производство. № 9,1991. — С. 7−8.
- Малышев В.Н., Голуб М. В. Структура и триботехнические характеристики износостойких композиционных материалов и покрытий. // В кн. Долговечность трущихся деталей машин. Вып.4. М.: Машиностроение, 1990.-С. 106−109.
- Гаврилин В.И. Формирование защитных характеристик поверхностей алюминиевых сплавов методом микродугового оксидирования. Дис. канд. тех. наук: 05.03.01. ТулГУ: Тула, 2003. — 133 с.
- Федоров В.А., Белозеров В. В., Великосельская Н. Д. и др. Состав и структура упрочненного поверхностного слоя на сплавах алюминия, получаемого при микродуговом оксидировании. //Физика и химия обработки материалов. № 4, 1988. — С. 92−97.
- Малышев В.Н., Марков Г. А., Федоров В. А. и др. Особенности строения и свойства покрытий наносимых методом микродугового оксидирования. //Химическое и нефтяное машиностроение. № 1, 1984. — С. 26−27.
- Петросянц А.А., Малышев В. Н., Федоров В. А. и др. Кинетика изнашивания покрытий, нанесенных методом микродугового оксидирования. //Трение и износ. Т.5. № 2, 1984, — С. 350−353.
- Федоров В.А., Белозеров В. В., Великосельская В. Д. Формирование упрочненных поверхностных слоев методом микродугового оксидирования в различных электролитах и при изменении токовых режимов. //Физика и химия обработки материалов. № 1, 1991, — С. 87−92.
- Баковец В.В., Поляков О. В., Долговесова И. П. Плазменно-электролитическая анодная обработка металлов. Новосибирск: Наука. Сиб. отделение, 1991. — 163 с.
- Новиков А.Н. Перспективы применения микродугового оксидрования для восстановления и упрочнения деталей из алюминиевых сплавов. //Известия ОрелГТУ. Серия „Строительство. Транспорт“. № 3−4, 2004, -С. 115−122.
- Великосельская Н.Д. Повышение долговечности узлов трения подводного нефтегазового оборудования посредством поверхностного упрочнения методом микродугового оксидирования: Автореф. дис.. канд. тех. наук: 05.02.04-М., 1989.- 15 с.
- Батищев А.Н. Пособие гальваника-ремонтника. 2-е изд., перераб. М.: Агропромиздат, 1986. — 192 с.
- Грихилес С.Я., Тихонов К. И. Электролитические и химические покрытия. Теория и практика. Ленинград: Химия, 1990. — 288 с.
- А. св. СССР № 1 706 242 С 25 D 11/02. Щелочной электролит для микродугового анодирования алюминия и его сплавов. / JI. A Снежко и др. Опубл. 1988, гриф ДСП.
- Артемова С.Ю. Формирование микроплазменными методами защитных оксидных покрытий из водных растворов различного химического состава и степени дисперсности: Автореф. дис. канд. техн. наук: 05. 17. 14.-М., 1996.- 17 с.
- Патент РФ № 2 038 428 С 25 D 11/06. Электролит для микродугового оксидирования алюминия и его сплавов. / Малышев В. Н., Булычев С. И., Малышева Н. В. Опубл. Б. И№ 18, 1995.
- Brown S.D., Кипа К.Т., Van Т.В. Anodic spark deposition from aqueous solutions of NaA102 and NaSi03 // J. of American Ceramic Soc.-1971.-V.8, № 54.-P.3 84−390.
- Kurze P., Krusman W., Chechenbach J., Schwars Т., Rabending K. Crystal Res. Technol., 1987, vol. 22, № 1, p. 53−68.
- United States Patent 5 720 866. Method for forming coatings by electrolyte discharge and coatings formed thereby / A. Erokhine, A.A. Voevodin, R.D. Schmertzler. Заявл. 14.06.96., опубл. 24.02.98- МКИ C23 b 9/02.
- Патент № 3 812 023 (США) С 23 b 9/02. Anodic production of pigmented siliceous coatings for aluminous metals / Shardein D.J., Rogers C.M., Craig H.L. -N 314 045. Опубл. 21.05.74.
- Патент № 142 360 (ГДР) С 23 d 11/04. Verfahren zur Erzeugung a-AL203-haltiger Schichten auf Aluminiummetallen / Kurze P., Krysmann W., Marx G.-N211 430. Опубл. 18.06.80.
- Патент № 3 812 021 (США) С 23 b 9/02. Inorganic coatings for aluminous metals / Craig H.L., Coates H.J. -N 314 209. Опубл. 21.05.74.
- Патент № 1 245 820 (Великобритания) С 23 b 9/02. Method of formation dielectric films on aluminium or its alloys by anodic oxidation / Suzuki Taka-shi. -N 57 391. Опубл. 08.09.71.
- Kurze P., Krusman W., Marx G. // Wiss. Z. Techn. Hochsch. (Karl-Marx-Sradt) 1982. V. 24, N 6. P. 665−670.
- Руднев B.C., Гордиенко П. С., Курносова А. Г. и др. Влияние электролита на результат микродугового оксидирования алюминиевых сплавов. // Защита металлов. Т.27.-№ 1, 1991. С. 106−110.
- Tran Bao Van, Brown S.D., Wirtz G.P. Mechanism of Anodic Spark deposition.//J. American Ceramic Society. 1977. Vol. 56, № 6. P. 563−566.
- Кузнецов Ю.А., Коровин А. Я. Электролиты для микродуговой обработки деталей. //Механизация и электрификация сельского хозяйства. — № 1, 2003.-С. 30−32.
- Новиков А.Н., Батищев А. Н., Кузнецов Ю. А., Коломейченко А. В. Восстановление и упрочнение деталей из алюминиевых сплавов микродуговым оксидированием. /Учебное пособие. Орел: Изд-во ОрелГАУ, 2001. -99 с.
- Федоров В.А. Разработка основ применения легких сплавов в качестве материалов триботехнического назначения за счет формирования поверхностного керамического слоя. Автореф. дисс.докт. техн. наук. -М., 1995.-49 с.
- Патент РФ № 2 166 570 С 25 D 11/08. Способ получения покрытий. / Ат-рощенко Э.С., Чуфистов О. Е., Казанцев И. А. и др. Опубл. Б. И № 13, 2001.
- Чуфистов О.Е. Разработка технологии микродугового оксидирования изделий из алюминиевых сплавов на основе исследования структуры и свойств получаемых покрытий: Автореф. дис.. канд. техн. наук: 05.02.01.-Пенза, 1999.-20 с.
- Патент РФ № 2 229 542 С 25 D 11/08. Электролит микродугового оксидирования алюминия и его сплавов. / Батищев А. Н., Кузнецов Ю. А., Се-востьянов А.Д., Ферябков А. В. Опубл. БИ № 15,2004.
- Ермолов А.С., Кряжков В. М., Черкун А. Е. Основы надежности сельскохозяйственной техники. М.: Колос, 1982. — 271 с.
- Детлаф А.А., Яровский Б. М. Курс физики. М.: Москва: Высшая школа, 2000.-718 с.
- Физический энциклопедический словарь / Гл. ред. Прохоров A.M. -М.: Сов. энциклопедия, 1983. 928 с.
- Фистуль В.И. Введение в физику полупроводников: Учеб. пособие. -М.: Высшая школа, 1984. 1984. — 352 с.
- Тареев Б.М. Физика диэлектрических материалов. М.: Энергия, 1973. — 128 с.
- Кусков В.Н., Кусков Ю. Н., Ковенский И. М. Особенности роста покрытия при микродуговом оксидировании алюминиевого сплава. //Физика и химия обработки материалов. № 5,1991. — С. 154−156.
- Руднев B.C., Гордиенко П. С. Зависимость толщины покрытий от потенциала МДО. //Защита металлов. Т.29. № 2, 1993. — С. 304−307.
- Снежко JI.A., Черненко В. И. Энергетические параметры процесса получения оксидных покрытий на алюминии в режиме искрового разряда. //Электронная обработка материалов. № 2, 1983. — С. 25−28.
- Епифанов Г. И. Физика твердого тела.-М.: Высшая школа, 1977.-288 с.
- Гороновский И.Т., Назаренко Ю. П., Некряч Е. Ф. Краткий справочник по химии. Киев: Наук, думка, 1974. — 985 с.
- Albella J.M., Montero I., Martinez-Duart J.M. // Ibid. 1987 V. 32. № 2. P. 255−258.
- Технология тонких пленок: Справочник. /Под ред. JI. Майселла, Р. Гленга. Т.2. М.: Сов. радио, 1977. — 768 с.
- Lhymn С., Kosel Р.В., Vaughan R. // Thin Solid Films. 1986. Vol. 145 № 1. P. 69−74.
- Кузнецов Ю.А., Фроленков К. Ю. Исследование электрического пробоя толстослойных оксидных покрытий, сформированных на литейных алюминиевых сплавах методом микродугового оксидирования. //Упрочняющие технологии и покрытия. № 2, 2005. — С. 27−31.
- Gruss L. L., MeNeil W. Anodic spark reaction products in aluminate, tang-state and silicale solutions. Electrochem. Tecnol., 1963, N 9, p. 283−287.
- Севостьянов A.JI. Внутренние напряжения происхождение, влияние их на работоспособность восстановленных изделий. //Научные труды РГАЗУ (Агроинженерия). -М.: РГАЗУ, 2002. — С. 102−104.
- Иоффе B.C. Успехи химии. Т. 13. Вып. 1, 1944. С. 50.
- Немнонов С.А. Журнал технической физики, 1948, т. 18, вып. 2.
- Дегтярь Л.И., Андрейчук В. К. Остаточные напряжения в неоднородных деталях сельскохозяйственной техники (методы расчета): Учеб. пособие. /Кишиневский СХИ. Кишинев, 1988. — 98 с.
- Ваграмян А.Т., Петрова Ю. С. Физико-механические свойства электролитических осадков. М.: Изд. АН СССР, 1960.
- Hoar F., Arroewsmith D. Trans. Inst. met. Fin., 1958, v. 38 № 1. p 1−2.
- Варма А. Рост кристаллов и дислокации. М. Ил. 1960.
- Soderburg Н., Craham A., Proc. Amer. Electroplat. Soc., 1947, V. 34, p. 74.
- Карпенко Г. В., Похмурский В. И. Влияние температуры на изменение внутренних напряжений и усталостной прочности углеродистых сталей с диффузионными покрытиями. //В Сб. „Жаростойкие и теплостойкие покрытия“. Л.: Наука, 1969. С. 79−85.
- Ляшенко Б.А., Ришин В. В., Шаривкер С. Ю. и др. К анализу напряженного состояния покрытий. //В Сб. „Жаростойкие и теплостойкие покрытия“. Л.: Наука, 1969. С. 454−456.
- Бояршинова И.Н. Механика и оптимизация процесса формирования остаточных напряжений при поверхностном пластическом деформировании: Дис. канд. техн. наук: 01.02.04. Пермь, 1996. — 116 с.
- Бабичев М.А. Методика определения внутренних напряжений в деталях кольцевого сечения и ее применение. М., 1954. Дис.. канд. техн. наук: Утв. в ин-те машиностроения Акад. Наук СССР 16.11.1955.
- Дегтярь Л.И. Определение остаточных напряжений в покрытиях и биметаллах. Кишинев: Картя Молдовенскэ, 1968. 175с.
- Огнева Е.Г. Исследование влияния внутренних напряжений в поверхностных слоях деталей на их износ применительно к восстановлению сопряжений сельскохозяйственных машин с помощью дополнительных ремонтных деталей: Дис. канд. техн. наук: М., 1960. 147с.
- Мелехов Р.К. Коррозионное растрескивание титановых и алюминиевых сплавов. Киев: Техшка, 1979. — 128 с.
- Одынец Л.Л., Платонов Ф. С., Прокопкук Е. Н. Искрение при анодном окислении тантала и ниобия. //Электронная техника. Сер. № 5. Радиодетали и радиокомплекты. 1972. — Вып. 2(27). С. 37−42.
- Рюнгенен Т.И., Орлов В. М. Влияние примесей на кинетику формовки тантала и ниобия. // Анодные оксидные пленки. Петрозаводск, 1978. -С. 132−137.
- Малышев В.Н. Упрочнение поверхностей трения методом микродугового оксидирования: Дис.. доктора техн. наук: 05.02.04. -М., 1999. -477 с.
- Сафодьев А.В. Фазовый состав и свойства поверхности упрочненной плазменно-электролитическим оксидированием: Дис.. канд. техн. наук: 05.02.01.-М., 2000. 195 с.
- Батищев А.Н., Севостьянов А. Л., Кузнецов Ю. А. Образование внутреннего напряжения в покрытии, сформированным микродуговым оксидированием. //Механизация и электрификация сельского хозяйства. № 2, 2004.-С. 23−24.
- Бобкова Н.М. Физическая химия силикатов и тугоплавких соединений: Мн.: Высш. шк., 1984. 256 с.
- Батищев А.Н., Севостьянов A.JL, Кузнецов Ю. А. Определение внутреннего напряжения в покрытии, сформированным микродуговым оксидированием. //Механизация и электрификация сельского хозяйства. -№ 5,2004.-С. 28.
- Ландау Л.Д., Лифшиц Е. М. Теоретическая физика. T.III. Квантовая механика. -М.: Наука, 1989.-С. 312−317.
- Дедков Г. В. Межатомные потенциалы взаимодействия в радиационной физике //УФН. Т. 165. № 8. 1995. — С. 919−953.
- Ландау Л.Д., Лифшиц Е. М. Теоретическая физика. Т.VII. Теория упругости. М.: Наука, 1987. — С. 44−49.
- Шоршоров М.Х., Харламов Ю. А. Физико-химические основы детона-ционно-газового напыления покрытий. -М.: Наука, 1978.-224 с.
- Кудинов В.В., Иванов В. М. Нанесение плазмой тугоплавких покрытий. -М.: Машиностроение, 1981. 192 с.
- Епифанов Г. И. Физические основы микроэлектроники. -М.: Советское радио, 1971. 116 с.
- Осипов К.А. Некоторые активируемые процессы в металлах и сплавах. М.: Изд-во АН СССР, 1962. — 123 с.
- Кудинов В.В. Плазменные покрытия. -М.: Наука, 1974. 184 с.
- Шаривкер С.Ю., Астахов Е. А., Гарда А. П. Влияние скорости полета напыляемых частиц на прочность сцепления напыленных покрытий. //ФХОМ, № 5. 1974. — С. 157−158.
- Джонсон К. Механика контактного взаимодействия. М.: Мир, 1989. -506 с.
- Кулик А.Я., Борисов Ю. С., Мухин А. С. и др. Газотермическое напыление композиционных порошков. Л.: Машиностроение, Лен. отделение, 1985.- 199 с.
- Крешков А.П., Ярославцев А. А. Курс аналитической химии. „Химия“. -М., 1964.-280 с.
- Воловик E. JL Восстановление деталей, ремонт и диагностика машин. /Сборник. Калуга, 1977. — 332 с.
- ГОСТ 9.304−87. Единая система защиты от коррозии и старения. Покрытия газотермические. Общие требования и методы контроля. ИПК „Издательство стандартов“, 1988. 20 с.
- Зимон А.Д. Адгезия пленок и покрытий. М.: Химия, 1977. — 352 с.
- Ермаков С.М., Бродский В. З., Жиглявский А. А. и др. Математическая теория планирования эксперимента. /Под ред. С. М. Ермакова. — М.: Наука, 1983.-392 с.
- Колемаев В.А., Староверов О. В., Турундаевский В. Б. Теория вероятностей и математическая статистика. М.: Высшая школа, 1991. — 400 с.
- Захаров Б.М., Новиков В. Н. Определение свойств газотермических покрытий. /Методическое руководство MP 1.595−27−001−93. М.: ВИАМ, 1993.-90 с.
- Алхимов А.П., Бойко В. М., Папырин А. Н. Применение лазер-доплеровских и стробоскопических анемометров для исследования быс-тропротекающих процессов. //Автометрия. -№ 3, 1982. С. 38−45.
- Косарев В.Ф. Экспериментальное исследование процесса „холодного“ газодинамического напыления. Дис. канд. физ.-мат. наук, гриф ДСП. -Новосибирск, 1991.-161 с.
- Богомолова Н.А., Гордиенко JI.K. Металлография и общая технология металлов. -М.: Высшая школа, 1983. 270 с.
- Богомолова Н.А. Практическая металлография. М.: Высшая школа, 1983.-78 с.
- Харитонов Л.Г. Определение микротвердости. М.: Металлургия, 1967. -45 с.
- Ревенко А.Г. Рентгеноспектральный флуоресцентный анализ природных материалов. Новосибирск: В.О. „Наука“. Сибирская издательская фирма, 1994.-264 с.
- Лосев Н.Ф., Смагурова А. Н. Основы рентгеноспектрального флуоресцентного анализа. М.: Химия, 1982. — 282 с.
- Миркин Л.И. Рентгеноструктурный контроль в машиностроении. /Справочник. -М.: Машиностроение, 1979. 134 с.
- Калоша В.К., Лобко С. И., Чикова Т. С. Математическая обработка результатов эксперимента. Минск: Высшая школа, 1982. — 103 с.
- Веденякин Г. В. Общая методика экспериментальных исследований и обработка опытных данных. М.: Колос, 1973. — 199 с.
- Шоркин B.C., Кузнецов Ю. А., Батищев А. Н. Анализ напряженного состояния износостойких покрытий восстановленных деталей. // Механизация и электрификация сельского хозяйства. № 3, 2003. — С. 28−30.
- Снежко Л.А., Удовиченко Ю. В., Тихая Л. С. Свойства анодно-искровых покрытий, сформированных на сплавах алюминия из щелочных электролитов. // Физика и химия обработки материалов. — № 3, 1989. С. 9396.
- Новиков А.Н., Коломейченко А. В. Электроплазмохимический способ восстановления и упрочнения деталей из алюминиевых сплавов. // Материалы 4-го собрания металловедов России, часть 2. — Пенза, 1998. — С. 116−118.
- Русаков А.А. Рентгенография металлов. -М.: Атомиздат, 1977.-480 с.
- Кузнецов Ю. А., Батищев А. Н., Денисьев С. А. Адгезия и износостойкость керамических покрытий на коррозионностойких сталях. // Механизация и электрификация сельского хозяйства. № 6,2003 — С.23−24.
- Кузнецов Ю. А. Исследование адгезионной прочности покрытий, полученных комбинированным способом. //Механизация и электрификация сельского хозяйства. № 7, 2005.- С. 32−33.
- Патент РФ № 2 026 890 С 25 D 11/02. Способ формирования износостойких покрытий. / Малышев В. Н., Малышева Н. В., Богданов А. К. Опубл. Б. И№ 2, 1995.
- Батищев А. Н., Новиков А. Н., Кузнецов Ю. А. Восстановление алюминиевых деталей сельскохозяйственной техники микродуговым оксидированием. // Инженерно-техническое обеспечение АПК. № 4, 1996. -С. 18−19.
- Батищев А. Н., Севостьянов А. Д., Ферябков А. В., Кузнецов Ю. А. Упрочнение деталей микродуговым оксидированием. //Механизация и электрификация сельского хозяйства. № 9,2003 — С.25−26.
- Новиков А. Н., Кузнецов Ю. А. Взаимосвязь фазового состава и свойств упрочненного слоя, нанесенного микродуговым оксидированием на алюминиевую деталь. //Механизация и электрификация сельского хозяйства. -№ 2, 1998 С. 27−28.
- Ферябков А.В. Разработка технологии восстановления деталей перерабатывающей промышленности микродуговым оксидированием. Дис. канд. тех. наук. -М., 2005. 129 с.
- Кузнецов Ю.А. Комбинированная технология получения керамических покрытий. // Сварочное производство». № 6, 2005. — С. 37−39.
- Розенфельд И.Л. Коррозия и защита металлов. -М.: Металлургия, 1970. -237 с.
- Католикова Н.М. Модифицирование поверхности алюминиевых сплавов для повышения коррозионно-механической износостойкости. Дис. .канд. тех. наук: 05.17.14.-М., 1991.-121 с.
- Кузнецов Ю. А. Износостойкость покрытий при микродуговом оксидировании алюминиевых литейных сплавов. //Материалы Международной научно-практической конференции. В 2-х томах. Т.2. Орел: ОрелГАУ, 2000.-С. 119−120.
- Кузнецов Ю.А. Повышение износостойкости покрытий, нанесенных газодинамическим напылением. // Механизация и электрификация сельского хозяйства. № 6, 2005 — С. 27−28.
- Кузнецов Ю.А., Кулаков К. В., Тарасов К. В., Батищев А. Н. Теоретическая оценка деформации частиц и подложки при газодинамическом напылении. // Механизация и электрификация сельского хозяйства. № 9, 2005.- С. 32−34.
- Батищев А.Н., Кузнецов Ю. А., Денисьев С. А. Ресурс увеличивается вдвое. // Сельский механизатор. № 6, 2001. — С. 27.
- Мороз В.П. Вибрационная очистка машин: Учеб. пособие. М.: Агро-промиздат, 1987. — 85 с.
- Патент РФ № 2 215 831 С 25 D 11/02. Устройство для микродугового оксидирования колодцев корпуса шестеренного насоса. / Кузнецов Ю. А. Опубл. Б.И. № 31, 2003.
- Кузнецов Ю.А. Восстановление и упрочнение колодцев корпусов насосов типа НШ-У микродуговым оксидированием. // Ремонт, восстановление, модернизация. № 9, 2005. — С. 29−32.
- Белкин И.М. Допуски и посадки (Основные нормы взаимозаменяемости): Учеб. пособие для студентов машиностроительных специальностей высших технических заведений. М.: Машиностроение, 1992. — 528 с.
- Батищев А.Н., Кузнецов Ю. А., Севостьянов A.JI. и др. Слабое звено -клапанная коробка. // Сельский механизатор. № 10, 2002. — С. 29.
- Методика определения экономической эффективности технологий и сельскохозяйственной техники. (Утверждена 23 июля 1997 г. Министерством сельского хозяйства и продовольствия). / Под редакцией А. В. Шпилько.-М., 1998. -Ч. 1.-219с.