Получение полых ступенчатых валов и осей из трубных заготовок с использованием процессов продольного редуцирования через конические матрицы
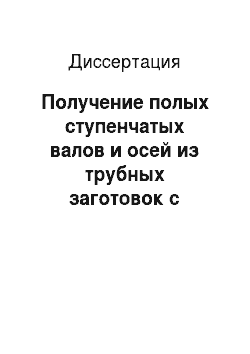
Основная задача, стоящая перед машиностроителями — улучшение технологических показателей, снижение веса машин и механизмов при повышении их долговечности и надежности. Детали типа валов и осей являются одними из наиболее нагруженных деталей машин и механизмов и применяются во всех отраслях машиностроения. С целью повышения их работоспособности и долговечности в настоящее время начали применять… Читать ещё >
Содержание
- Глава 1. АНАЛИЗ ПРОГРЕССИВНЫХ МЕТОДОВ ПОЛУЧЕНИЯ ПОЛЫХ СТУПЕНЧАТЫХ ВАЛОВ И ОСЕЙ
- 1. 1. Конструкции и типы валов и осей, применяемые в промышленности
- 1. 2. Материалы, применяемые при изготовлении валов и осей
- 1. 3. Основные способы изготовления валов и осей
- 1. 4. Использование процессов редуцирования для получения валов и осей ступенчатого профиля
- 1. 5. Исследования процесса редуцирования полых заготовок
- 1. 6. Цель и задачи исследований
- Глава 2. МЕТОДИКА ПРОВЕДЕНИЯ ИССЛЕДОВАНИЙ
- 2. 1. Объект и методы исследования и используемые заготовки
- 2. 2. Исследуемые материалы и их подготовка
- 2. 3. Оборудование и инструмент
- 2. 4. Обработка результатов эксперимента и программное обеспечение
- Глава 3. ТЕОРЕТИЧЕСКИЙ АНАЛИЗ И МЕТОДИКА РАСЧЕТА ПРОЦЕССА РЕДУЦИРОВАНИЯ ТРУБЫ В КОНИЧЕСКОЙ МАТРИЦЕ
- 3. 1. Математическая модель процесса редуцирования труб на основе теории течения нелинейно-вязкой среды
- 3. 2. Определение реологических параметров исследуемых материалов
- 3. 3. Определение характеристик контактного трения
- 3. 4. Расчеты характеристик геометрии и НДС на основе модели
- 3. 5. Результаты и
- выводы по главе 3
- Глава 4. ЭКСПЕРИМЕНТАЛЬНЫЕ ИССЛЕДОВАНИЯ ПРОЦЕССА ПРОДОЛЬНОГО РЕДУЦИРОВАНИЯ ТРУНЫХ ЗАГОТОВОК
- 4. 1. Однопереходное продольное редуцирование по прямой и обратной схемам истечения металла
- 4. 2. Многопереходное редуцирование
- 4. 3. Особенности формоизменения и виды дефектов при редуцировании
- 4. 4. Исследования структуры и свойств опытных полых поковок
- 4. 5. Результаты и
- выводы по главе 4
- Глава 5. РАЗРАБОТКА ТЕХНИЧЕСКИХ И ПРОЕКТНЫХ РЕКОМЕНДАЦИЙ ПО ПРАКТИЧЕСКОМУ ИСПОЛЬЗОВАНИЮ ТЕХНОЛОГИИ РЕДУЦИРОВАНИЯ В ПРОМЫШЛЕННОМ ПРОИЗВОДСТВЕ АВТОМОБИЛЬНЫХ ПОКОВОВ
- 5. 1. Выбор типовой номенклатуры и разработка конструкций полых ступенчатых поковок
- 5. 2. Разработка технологических схем производства полых валов
- 5. 3. Расчет матрицы на потерю жесткости при смятии
- 5. 4. Анализ эффективности применения новой технологии
Получение полых ступенчатых валов и осей из трубных заготовок с использованием процессов продольного редуцирования через конические матрицы (реферат, курсовая, диплом, контрольная)
Основная задача, стоящая перед машиностроителями — улучшение технологических показателей, снижение веса машин и механизмов при повышении их долговечности и надежности. Детали типа валов и осей являются одними из наиболее нагруженных деталей машин и механизмов и применяются во всех отраслях машиностроения. С целью повышения их работоспособности и долговечности в настоящее время начали применять экономичные конструкции полых валов и осей со сквозной рабочей полостью для подачи охлаждающей жидкости или смазки. Наиболее распространенный метод их изготовления — механическая обработка резанием сплошных кованных или катанных заготовок, приводящая к значительным отходам металла и отличающаяся невысокой производительностью. Актуальная задача интенсификации производства этой группы деталей — переход к качественно новой и более совершенной технологии, способной радикально изменить существующие способы их изготовления с целью уменьшения отходов металла, снижения трудоемкости, энергоемкости, сокращение производственных площадей, высвобождение рабочей силы, улучшение качества продукции, условий труда и повышения культуры производства. Один из путей удовлетворения насущных требований металлообрабатывающей промышленности — перевод все большего количества деталей на малоотходные процессы, использующие методы обработки давлением и, в частности, современные технологии кузнечно — штамповочного производства.
Одними из прогрессивных методов заготовительного кузнечно-штамповочного производства при изготовлении полых длинномерных изделий, являются процессы продольного редуцирования обжимом трубных заготовок через матрицы. Эти процессы имеют ряд преимуществ перед традиционными технологиями прессования, продольной и поперечной прокатки, выдавливания, волочения и радиальной ковки, обычно применяемых для этих целей в машиностроении. Они заключаются в меньшей энергоемкости и металлоемкости деформирующего оборудования, более высокой гибкости технологии, более простой конструкции инструмента и др. Кроме того, эти процессы обеспечивают возможность эффективного производства ступенчатых полых поковок типа валов и осей из большинства марок среднелегированных конструкционных сталей на имеющемся специализированном оборудовании цехов и участков кузнечно-штамповочных цехов.
В то же время, хотя процессы редуцирования сплошных заготовок изучены достаточно хорошо, имеющихся данных по схемам и режимам формоизменения при редуцировании полых толстостенных трубных заготовок недостаточно для разработки научно обоснованной эффективной технологии и обоснованию ее практического применения.
В связи с этим настоящая работа посвящена исследованию процессов продольного редуцирования полых трубных заготовок для обоснования типовой технологии и разработки проектных решений по производству полых ступенчатых длинномерных валов и осей для автомобильных двигателей.
Работа является частью комплекса исследований по созданию эффективных технологических процессов обработки металлов давлением для производства трубных заготовок и полых поковок, проводимых Московским государственным институтом стали и сплавов (Технологическим университетом) в рамках госбюджетных и хоздоговорных программ для различных отраслей машиностроения.
Автором выносятся на защиту следующие новые научные и практические положения:
— результаты теоретического анализа влияния основных технологических параметров редуцирования на характеристики напряженнодеформированного состояния и компьютерная методика расчета без составления программы на алгоритмическом языке;
— экспериментальные данные по определению численных значений реологических и трибологических параметров деформации исследуемых модельных и натурных материалов;
— результаты экспериментальных исследований силовых характеристик, особенностей формообразования и видов дефектов трубных заготовок при разных схемах процесса продольного редуцирования;
— оценки изменений структуры и твердости при получении полугорячим продольным редуцированием опытных ступенчатых длинномерных полых поковок из сталей 40Х и 18ХГТ;
— результаты расчетов методом конечных элементов упругопластиче-ских деформаций и напряжений в типовой конструкции конической матрицы для определения участков возможного смятия поверхности и потери жесткости при предельных распорных нагрузках;
— примеры проектных предложений по конструкциям полых поковок для ступенчатых валов автомобильных двигателей, технологическим схемам практической реализации новой технологии и укрупненные оценки ее технико-экономической эффективности.
Работа выполнена на кафедре Обработки металлов давлением Московского Государственного института стали и сплавов (Технологического Университета) под научным руководством доц., к.т.н. Троицкого В. П. и при научной консультации в.н.с., к.т.н. Цепина М.А.
Автор выражает благодарность сотрудникам кафедры ОМД и НИЛ ДСПМ МГИСиС (ТУ) за помощь в проведении экспериментов и выполнении работы.
ОСНОВНЫЕ РЕЗУЛЬТАТЫ И ВЫВОДЫ ПО РАБОТЕ.
1 .Разработаны математическая модель процесса продольного редуцирования и методика расчета характеристик геометрии и напряженно — деформированного состояния трубной заготовки в зависимости от основных технологических параметров формоизменения. 2. Для исследованных материалов определены реологические параметры уравнения нелинейной вязкости и характеристики контактного трения. Показано, что определяющими параметрами продольного редуцирования трубной заготовки по степени значимости на процесс деформирования являются угол захода матрицы, величина обжатия, скорость перемещения деформирующего инструмента, коэффициент контактного трения и показатель скоростного упрочнения деформируемого материала.
3. Экспериментально установлено, что при однопереходном редуцировании предпочтительной является схема с обратным истечением металла. Показано, что многопереходное редуцирование длинномерных с Lo/Do>3,0 толстостенных трубных заготовок (с ho/D0 > 0,.1) может быть устойчиво реализовано при единичных обжатиях за один переход в пределах КвгТ, 04. 1,06 и суммарном обжатии Kde=1, 25 .1,3.
4. Установлено, что основная группа дефектов при редуцировании связана с потерей устойчивости длинномерных трубных заготовок. Эффект потери поперечной устойчивости может быть использован в качестве формообразующей операции для набора металла в средней части поковки.
5. Показано, что после многократного 6.7 переходного полугорячего редуцирования трубных заготовок из сталей 40Х и 18ХГТ при температурах 800−850 °С поковки соответствуют требованиям ТУ. Микроструктура опытных поковок соответствует 7.8 баллу зерна по ГОСТ 5639–82, а общий уровень твердости по Бринелю превышает требования ГОСТ 4543–71.
6. Определена номенклатура деталей автомобилей, которые целесообразно изготавливать из трубных заготовок методом продольного редуцирования. Для деталей представителей разработаны чертежи полых поковок, технологические схемы штамповки и предложено использовать для получения трубных заготовок прошивку сплошных полуфабрикатов на стане поперечно винтовой прокатки.
7. Выполнен анализ работоспособности штампового инструмента для редуцирования под воздействием максимальных нагрузок при штамповке на ГКМ. Установлено, что возможна потеря устойчивости формы матрицы за счет смятия поверхностных участков в местах максимальных значений интенсивности напряжений. Рекомендованы замена традиционного штампового материала для матриц — стали 5ХНМ на стать ЗХ2В8 или увеличение высоты матрицы.
8. Анализ технико-экономической эффективности новой технологии производства полых автомобильных поковок показал значительное в 1,5.2,0 раза снижение трудоемкости, сокращение на 25.40% расхода металла и уменьшение в 2.3 раза плановой цены на поковки. По результатам работы принято решение организовать производство полых поковок на отдельном самостоятельном участке АОО ХК «Коломенский завод».
Список литературы
- Полые оси и валы. / Л.М., Школьник Ю. Е. Коваленко, Н. И. Мартынов, //- М. Машиностроение, 1968 .- 183 с.
- Прогрессивные технологические процессы и кузнечно-прессовое оборудование для объемной штамповки/ Рекомендация ЭНИКМаш,-Воронеж, 1968 .- 266 с.
- Семендий В.И., Акаро И. Л., Волосов Н. Н. Производственные технологии, оборудование и автоматизация кузнечно-штамповочного производства КАМАЗа.- М. Машиностроение, 1989 .- 303 с.
- Шнейберг Б.М., Акаро И. Л. Кузнечно-штамповочное производство Волжского автомобильного завода.-М. Машиностроение,! 992.-301 с.
- Акаро И.Л. Прогрессивные направления развития кузнечного производства в машиностроении .- Машмир, 1992. 33 с.
- Виноградов В.Е., Меркулов А. В. Гибкий роботизированный автоматический комплекс для производства поковок легкового автомобиля // Эффективная технология и техническое перевооружение кузнечного и листопггамповочного производства .- МДНТИ, 1989 .- с. 30−35.
- Деордиев Н.Т. Обработка деталей редуцированием. М.: — Машгиз., 1960, -154 с.
- Лазуткин Г. С., Гринфельд Л.А Совершенствование технологии изготовления заготовок колец подшипников // Кузнечно-штамповочное производство .- 1996 .- № 7 .- с. 13.
- Изготовление полых профилированных заготовок / Б. А. Романцев, И. Н. Потапов, А. В Гончарук В. А. Попов. //- НПО ИТАИ, 1992, — 264с.
- Богатов А.А., Харитонов В. В. Производство экономичных видов толстостенных труб для машинострония // Кузнечно-штамповочное производство .- 1996 .- № 7 .- с. 8−9.
- Радиальное обжатие прутковых заготовок в горячем состоянии / Рекомендации ЭНИКМаш .- Воронеж, 1980 .- 97с.
- Акаро И.JI., Акаро А. И. Малоотходная полугорячая штамповка / ЦНИТЭСтроймаш, 1990 .-51с.
- Бородин Н.А. Сопротивление материалов. М.: Машиностроение, 1992 .- 224 с.
- Сторожев М.В., Попов Е. А. Теория обработки металлов давлением. -М.: Машиностроение, 1977 .- 423с.
- Степанский Л.Г. Расчеты процессов обработки металлов давлением. -М.: Машиностроение, 1979 .- 214с.
- Теория ковки и штамповки: Справочник / Под ред. Е. П. Унксова, А. Г. Овчинникова .- М.: Машиностроение, 1992 .- 720 с.
- Джонсон У., Меллор П. Теория пластичности для инженеров .- М.: Машиностроение, 1979 .- 567 с.
- Томсен Э., Янг Ч., Кобаяши Ш. Механика пластических деформаций при обработке металлов .- М.: Машиностроение, 1969 .- 503 с.
- Тарновский И.Я., Поздеев А. А. Теория обработки металлов давлением .- М.: Металлургиздат, 1963 .- 672 с.
- Пластическое формоизменение металлов /Г.Я. Гун, П. И. Полухин, В. П. Полухин и др. // М. Металлургия, 1968.- 416 с.
- Ковка и штамповка: Справочник т. З- М.: Машиностроение, 1987. -386 с.
- Ковка и штамповка: Справочник т.4- М. Машиностроение, 1987.-544 с.
- Аверкиев Ю.А., Аверкиев А. Ю. Технология холодной штамповки. М.: Машиностроение, 1989 .- 303 с.
- Семенов Е.И., Овчинников А. Г. Способ выдавливания полых изделий / Авторское свидетельство СССР № 326 997- B21J5/12, опубликовано 21.01.72 (Бюл. № 5)
- Воробьев И.А. и др. Способ изготовления стержневых деталей с головками. / Авторское свидетельство СССР № 543 454- B21J5/08, В21К1/44, опубликовано 25.01.77 (Бюл. № 3)
- Алиев ИС. Способ изготовления полых изделий с утолщениями. / Авторское свидетельство СССР 751 490- В21 J5/12, опубликовано3007.80 (Бюл. № 28)
- Иванов А.Г. Способ изготовления из прутка изделий типа стержней с головками. / Авторское свидетельство СССР№ 716 698- В21 J5/08, В21 К1/46, опубликовано 25.02.80 (Бюл. № 7).
- Иванов М.В., Бакаев Е.И Способ получения ступенчатых валов /. Авторское свидетельство СССР № 821 015- В21 J5/08, опубликовано1504.81 (Бюл. № 14).
- Богораз Л. Е и др. Способ изготовления ступенчатых деталей /Авторское свидетельство СССР № 821 014- B21J5/06, опубликовано 15.04.81 (Бюл. № 14).
- Бабушкин В. Г Екимов В. А. Способ изготовления полых ступенчатых деталей с фланцем в средней части и внутренним кольцевым выступом в зоне фланца. Авторское № 2 021 073- В21К21/08, опубликовано 15.10.91 (Бюл. № 19).
- Оленин Л.Д., Дериволков Д. И. Способ выдавливания полых ступенчатых изделий с многогранным фланцем в средней части Авторское свидетельство СССР № 2 069 120- В21К21/08, опубликовано 20.11.96 (Бюл. № 32).
- Чиченев Н.А., Кудрин Б. А., Полухин П. И. Методы исследования процессов обработки металлов давлением— М.: Металлургия, 1977, — 311 с.
- Полухин П.И., Гун Г.Я., Галкин A.M. Сопротивление пластической деформации металлов и сплавов .- М.: Металлургия, 1983. 352 с.
- Большая советская энциклопедия. Издание 3-е, -М. «Советская энциклопедия, 1975, Том 19, с 608.
- Румшинский Л.З., Смирнов С. Н. Методы обработки результатовэксперимента М.: МИСиС, 1973- 162 с.
- Математическая статистика. / В. М Иванова., В. М. Калинина, JI.A. Нешумова и др. // М.: Высшая школа, 1981.-371 с.
- Костылев А. А, Миляев П. В., Дорский Ю. Д. Статистическая обработка результатов экспериментов на ЭВМ. -JL: Энергоатомиздат, 1991.-294с.
- Новицкий П.В., Зограф И. А. Оценка погрешностей результатов измерений .- JL: Энергоатомиздат, 1991. -304 с.
- Чумаченко Е.Н., Семянистый А. В., Грунин Н. Н. Автоматизированное проектирование технологических процессов изотермической штамповки на базе программного комплекса SPLEN // Кузнечно-штамповочное производство, 1983, № 2, с.13−15.
- Чумаченко Е.Н., Скороходов А. Н., Александрович А. И. К вопросу о применении МКЭ в задачах о деформировании несжимаемых сред. //Изв. вузов. Черная металлургия. -1985, № 9, с.89−92.
- Чумаченко Е.Н., Александрович А. И. Применение МКЭ в расчетах узлов металлургических машин в задачах ОМД: Учебное пособие. М.: МВТУ, 1989, — 72 с.
- Ефимов А.Б., Чумаченко Е. Н. Решение задач теории упругости методом конечных элементов на базе пакета SPLEN-K. Структура и функциональные возможности пакета: Учебн. пособие. М.: МИЭМ, 1992, 32 с.
- Качанов Л.М. Основы теории пластичности. М .: Наука, 1969. -420 с.
- Малинин Н.Н. Прикладная теория пластичности и ползучести. М.: Машиностроение, 1975. 400 с.
- Малинин Н.Н. Ползучесть в обработке металлов давлением. М.: Машиностроение, 1986. -221 с.
- Романов К.И. Механика горячего формоизменения металлов. М.: Машиностроение, 1993. -240 с.
- Пластичность и разрушение/ B.JI. Колмогоров, А. А. Богатов, Б. А. Мигачев и др. // М.: Металлургия, 1977. — 336 с.
- Колмогоров В.Л. Напряжения, деформации, разрушение. М.: Металлургия, 1970. — 929 с.
- Колмогоров В.Л. Механика обработки металлов давлением. М.: Металлургия, 1986. — 688 с.
- Полухин П.И., Горелиг С. С., Воронцов В. К. Физические основы пластической деформации. М.: Металлургия, 1982, — 584 с.
- Джонсон У., Меллор П. Теория пластичности для инженеров. М.: Машиностроение, 1979. 567 с.
- Томсен Э., Янг Ч., Кобаяши III. Механика пластической деформации при обработке металлов. М.: Машиностроение, 1969.- 503 с.
- Чижиков Ю.М. Теория подобия и моделирование процессов ОМД. -М.: Металлургия, 1970, 285 с.
- Смирнов О.М. Обработка металлов давлением в состоянии сверхпластичности. -М.: Машиностроение, 1979. 184 с.
- Изотермическое деформирование металлов. // Фиглин С. З., Бойцов В. В., Калпин Ю. Г., Каплин Ю. И. -М.: Машиностроение, 1978. 239 с.
- Охрименко Я.М. Технология кузнечно-пггамповочного производства. -М.: Машиностроение, 1978, 560 с.
- С.П.Тимошенко. Устойчивость стержней, пластин и оболочек. -М.: Наука, 1971. -808 с. ил.
- Горбунов М.Н. Штамповка деталей из трубчатых заготовок. М.: Машгиз, 1960.-190 с.
- Попов О.В. Изготовление цельноиггампованных тонкостенных деталей переменного сечения. -М.: Машиностроение, 1974. 120 с.
- Поздняк JI.A., Скрынченко Ю. М., Тишаев С. И. Штамповые стали. -М.: Металлургия, 1980. 224 с.
- Томленов А.Д. Теория пластического деформирования М.: Металлургия, 1972. 408 с.
- Геллер Ю.А. Инструментальные стали. -М.: Металлургия, 1975. -584с.
- Зенкевич O.K., Морган К. Конечные элементы и аппроксимация. Пер. с англ. М.: Мир, 1986, 318 е.
- Зенкевич O.K. Метод конечных элементов в технике. Пер. с англ., М.: Мир, 1985, 541 с.
- Дзугутов М.Я. Пластическая деформация высоколегированных сталей и сплавов. М.: Металлургия, 1971. -424 с.
- Лахтин Ю.М., Леонтьев В. П. Материаловедение: Учебник для машиностроительных ВУЗов -2-е изд., перераб и доп. -М.: Машиностроение, 1980. 493 с.
- Гуляев А.П. Металловедение. М.: Металлургия, 1978. — 648 с.
- Металловедение и термическая обработка стали: Справ, изд. 3-е изд., перераб. и доп. в 3-х т. Т. 1. Методы испытаний и исследования /Под ред. Бернштейна М. Л., Рахштадта А. Г. — М.: Металлургия, 1983. -352 с.
- Норицын, И.А., Шехтер В. Я., Мансуров А. М. Проектирование кузнечных цехов и холоднопггамповочных заводов . Учеб. Пособие для вузов. -М.: Высшая школа, 1977. -423 с.
- Троицкий В.П., Мохов В. И., Кобелев А. Г. Проектирование цехов163обработки металлов давлением. -Волгоград, Волг ГТУ, 1997. 528 с.
- Расчеты экономической эффективности новой техники /Справочник Д.: Машиностроение, 1989. 448 с.
- Хачатуров Т.С. Эффективность капитальных вложений. -М. Экономика, 1979. 336 с.
- Качество продукции и эффективность производства. Под ред А. В. Гличева и Л. Я. Шухгальтера. М.: Машиностроение, 1977. -247 с.
- АООТ-ХКчЖЬломенский Завод» v. —., →>Маслов В.В., 1999 г.
- TEX№I4EOvtM АКТ БИЩРЕНИЯ результатов совместных работ
- АООТ-ХК <4йЬломенский Завод», МГИСиС (ТУ) и ООО НПО «ПАРШЕР-М> по программе разработки першекшшюй технологии производства гюковок полых валов и осей для автомобильных двигателей
- В период с 01,01.1996 г. по 31.05.1999 г. МГИСнС (ТУ) совместно с АООТ-ХК «Коломенский Завод», ООО НПО «ПАРТНЕР-М>> выполнил следующие работы :
- Этапы выполненных работ и полученные результаты Исполнитель1 2 3
- АООТ-ХК Коломенский Завод»,
- Гл. металлург Огуенко В. Н., 1. Нач. цеха Заикин А.И.1. МГИСиС (ТУ)
- НЁф*чный руководитель- член корр. РАЕН, проф., д.т.н.
- Ошегствшный исполните доц., кт. н Троицкий В. П3
- Наполнители- аспирант Финько B. Rат-Кисилев В. В. аспирант Киса