Тормозная рычажная передача
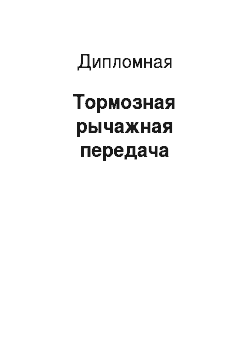
Тормозная рычажная передача является последним звеном в цепи приборов и устройств служащих для обеспечения локомотива тормозами. Только технически исправная и правильно отрегулированная тормозная рычажная передача может обеспечить чёткую работу всего тормозного оборудования локомотива. В процессе развития и совершенствования устройств тормозного оборудования появляются и внедряются в эксплуатацию… Читать ещё >
Тормозная рычажная передача (реферат, курсовая, диплом, контрольная)
СОДЕРЖАНИЕ ВВЕДЕНИЕ
1. Характеристика эксплуатационного локомотивного депо «Новокузнецк»
1.1 Общая характеристика локомотивного депо
1.2 Классификация локомотивных депо
1.3. Организационная структура локомотивного депо
1.4 Территория депо
2. Характеристика рабочего места. (Техническая характеристика электровозов ВЛ10у и 2ЭС4К"Дончак")
2.1 Электровоз постоянного тока ВЛ-10 и ВЛ10У
2.2 Электровоз постоянного тока 2ЭС4К"Дончак"
3. Краткая характеристика буксового узла электровоза ВЛ-10 и ВЛ10У
3.1 Назначение и классификация
3.2 Устройство буксового узла
4. Техническое обслуживание в эксплуатации
4.1 Обслуживание в эксплуатации
4.2 Износы и повреждения
4.3 Осмотр и ревизия
4.4 Разборка буксы
4.5 Ремонт элементов букс ЗАКЛЮЧЕНИЕ СПИСОК ЛИТЕРАТУРЫ ВВЕДЕНИЕ Письменная экзаменационная работа является самостоятельной работой учащегося.
Темы соответствуют рабочим учебным программам по спецпредметам «Автотормоза», «Устройство электровоза», «Эксплуатация электровоза», «Охрана труда».
Целью работы является углубленное изучение тормозной рычажной передачи, принцип её работы, вопросы технического обслуживания тормозного оборудования, схемы расположения пневматического тормозного оборудования на электровозе.
В данной работе мы рассмотрим устройство, принцип действия, а так же регулировку выхода штока тормозного цилиндра рычажной передачи. Отдельное внимание будет уделено ремонту тормозной рычажной передачи и ремонту тормозного цилиндра. Так же в дипломной работе будут присутствовать схемы конструкции и работы тормозной рычажной передачи и тормозного цилиндра.
В работе использовались основные источники:
1. Афонин, Г. С. Устройство и эксплуатация тормозного оборудования подвижного состава [Текст]: учебник для нач. проф. образования/Г.С.Афонин, В. Н. Кондратьев.-2-е изд., стер. М: Издательский центр «Академия», 2006.-304 с.
2. Инструкция по эксплуатации тормозов подвижного состава железных дорог [Текст]: Министерство путей сообщения РФ от 06.06.2002 №ЦТ-ЦВ-ЦЛ-ВНИИЖТ/277.Москва 2002.-116 с.
1. ХАРАКТЕРИСТИКА ЭКСПЛУАТАЦИОННОГО ЛОКОМОТИВНОГО ДЕПО «НОВОКУЗНЕЦК»
1.1. Общая характеристика локомотивного депо Первичные хозяйственные единицы локомотивного хозяйства является локомотивное депо. Оно осуществляет производственно-хозяйственную деятельность в соответствии с государственным планом перевозок на основе хозяйственного расчёта, имеет самостоятельный баланс, выполняет обязанности и пользуется правами установленными Положением о государственном, производственном предприятии.
На депо возложены: своевременная выдача подвижного состава под поезда, в соответствии с графиком движения и планом работы; организация обслуживания электровозов локомотивными бригадами; обеспечение безопасности движения поездов; своевременное выполнение экипировки и ремонта электроподвижного состава.
Для выполнения этих функций локомотивное депо имеет производственные здания и сооружения, технологическое и подъёмно-транспортное оборудование, экипировочные устройства, а так же запасные части и материалы.
Все сооружения и оборудования депо по своим размерам, количеству, устройству и назначению должны соответствовать типом и сериям обслуживаемых электровозов, и обеспечить выполнение всех работ по их содержанию и ремонту, в соответствии с заданным пробегом, программой и сроками ремонта.
Для постановки электроподвижного состава на осмотр и в ремонт в депо сооружают специальные стойла со смотровыми каналами, а так же создают цехи и мастерские с отделениями для ремонта электроаппаратуры, аккумуляторных батарей, деталей механического, электрического и пневматического оборудования.
Эксплуатационный и ремонтный персонал депо укомплектовывают работниками технических специальностей, которые требуются для выполнения всех работ по содержанию электроподвижного состава.
Коллектив депо должен обеспечивать неуклонный рост производительности труда и повышения эффективности использования производственных фондов, снижение себестоимости перевозок и ремонта, повышения рентабельности предприятия на основе научной организации труда, приобретение новой техники и передовой технологии, строгого соблюдения режима экономии, улучшения условий труда и отпуска локомотивных бригад и повышения их квалификации.
1.2 Классификация локомотивных депо Локомотивные депо подразделены на основные и оборотные. Основное депо наделено основными средствами, в состав которых входит: парк электроподвижного состава, производственно-технические здания, оборудования. Пункты оборота предназначены для осмотра, мелкого осмотра, экипировки электроподвижного состава и выхода его под поезда. Кроме того в пунктах оборота оборудуется комната отдыха локомотивных бригад. В пунктах оборота электровозов посменно дежурят квалифицированные работники (машинисты на прогреве), здесь есть необходимый инструмент, запасные части и материалы. Возглавляет каждую смену дежурный по оборотному депо.
1.3 Организационная структура локомотивного депо Локомотивное депо (ТЧ-15), возглавляет начальник депо. Он несёт полную ответственность за всю производственно-хозяйственную деятельность предприятия, ему непосредственно подчинены отдел кадров, бухгалтерия и группа материально-технического снабжения.
В локомотивном депо имеется цех эксплуатации, обеспечивающий своевременную выдачу электроподвижного состава под поезд и обслуживание его на линии. Работой цеха эксплуатации руководит заместитель начальника депо по эксплуатации. В личный состав цеха входят: машинисты-инструкторы, машинисты и их помощники, дежурная по депо, нарядчики, вызывальщики, расшифровщики скоростимерных лент, а так же стрелочники обслуживающие деповские пути, в том числе и контрольный пост.
Локомотивная бригада назначается для управления локомотивом и его обслуживанием в объеме, предусмотренном соответствующими инструкциями ОАО «РЖД». Возглавляет бригаду машинист, являющийся ответственным за состоянием локомотива и деятельностью остальных членов бригады.
На электровозе локомотивная бригада, как правило, состоит из двух человек машиниста и его помощника. Общие обязанности работников локомотивных бригад их права и ответственность регламентированы должностной инструкцией. [4]
1.4 Территория депо На территории депо располагают здания, экипировочные устройства, трансформаторную подстанцию, котельную, складские и служебные помещения и другие вспомогательные сооружения, а так же соответствующие путевое развитие.
Территорию депо выбирают по возможности ближе к приемоотправочным паркам станции. Путевое развитие на деповской территории имеет не менее двух самостоятельных выходов на станционные пути и обеспечивает выдачу электроподвижного состава на станцию и приём его со станции с минимальным пересечением главных путей, маршрутов отправления и прибытия поездов с наименьшем числом маневровых передвижений. На границе станционных и деповских путей сооружают контрольный пост.
2. ХАРАКТЕРИСТИКА РАБОЧЕГО МЕСТА. (ТЕХНИЧЕСКАЯ ХАРАКТЕРИСТИКА ЭЛЕКТРОВОЗОВ ВЛ-1ОУ И 2ЭС4К «ДОНЧАК»)
2.1 Электровоз постоянного тока серии ВЛ-10 и ВЛ-10У
В 1976 году по заказу Министерства путей сообщения был разработан локомотив серии ВЛ10У («у» — утяжеленный). У этой машины нагрузка от каждой оси на рельсы была увеличена с 23 до 25 тс. Основные части ВЛ10 и ВЛ10У — механическая, электрическая и пневматическая — остались идентичными, если не считать внедряемых в процессе выпуска усовершенствований. НЭВЗ выпускал электровозы ВЛ10У, начиная с № 001, а ТЭВЗ — с № 101. Локомотивы Новочеркасского и Тбилисского заводов этой серии отличаются только декоративным оформлением лобовой части кузова. Механические части ВЛ10У, а также их модификаций ВЛ80К и ВЛ80Т, были максимально унифицированы. Варьировались лишь отдельные конструктивные элементы под установку оборудования в кузове и на крыше, а также передаточные числа тяговой зубчатой передачи, поскольку типы применяемых на них тяговых двигателей различны. Локомотив предназначен для работы на магистральных железных дорогах с питанием от постоянного тока напряжением 3000 В. Его электрическое оборудование рассчитано на надежную работу при амплитуде в контактной сети от 2200 до 4000 В. На ВЛ10У установлено восемь тяговых двигателей ТЛК-2К1, имеющих последовательное возбуждение, опорно-осевое подвешивание, принудительную вентиляцию и мощность при часовом режиме 670 кВт. Вращающий момент от двигателя на колесные пары передается двусторонней одноступенчатой цилиндрической косозубой передачей. Для регулирования частоты вращения тяговых двигателей предусмотрено три вида их соединения: последовательное, последовательно-параллельное и параллельное. Электрические цепи локомотива получают питание от контактного провода через токоприемники, обеспечивающие надежный токосъем при любых скоростях движения.
Кроме тормозов с пневматическим и ручным управлением, действует система рекуперативного торможения, значительно повышающая безопасность движения поездов и обеспечивающая большую экономию электроэнергии, уменьшение износа бандажей и тормозных колодок. При рекуперативном торможении механическая энергия с вращающихся осей колесных пар передается на валы тяговых двигателей, которые трансформируют ее в электрическую, а та, в свою очередь, возвращается (рекуперируется) в контактную сеть и поступает к другим электровозам или в энергосистему. Электрическое, пневматическое и другое оборудование размещено в сочлененном двухсекционном кузове с концевым расположением постов управления (кабин машиниста). Секции ВЛ10У отличаются друг от друга: ту, в которой установлен быстродействующий выключатель силовых цепей, принято считать 1-й, и кабина машиниста этой секции называется кабиной № 1.В средней части каждой секции расположена высоковольтная камера (ВВК) с электроаппаратурой, предохраняемая сетчатым ограждением. Двери камеры имеют блокировки, обеспечивающие их открытие только при опущенном токоприемнике. Электрическая аппаратура, обладающая высокой надежностью, — блочной схемы, что значительно облегчает ее обслуживание и ремонт. Узлы аппаратуры, сильно нагревающиеся во время работы, находятся под принудительным охлаждением. Воздух к ним подается по воздухопроводу от центробежного вентилятора. Расположение оборудования внутри кузова обеспечивает свободный проход и доступ для осмотра электрической аппаратуры. [3]
2.2 Техническая характеристика электровоза 2ЭС4К «Дончак»
Электровоз 2ЭС4К «Дончак» — это высокоэффективный современный грузовой двухсекционный восьмиосный электровоз постоянного тока с коллекторными тяговыми двигателями, осевой мощностью 750 кВт, максимальной скоростью в эксплуатации 120 км/ч. Электровоз предназначен для вождения грузовых поездов на железных дорогах колеи 1520 мм, электрифицированных на постоянном токе напряжением 3 кВ. 2ЭС4К создаются в ЗАО «Трансмашхолдинг» как выгодная альтернатива проведения МЛП (модернизации локомотивов с продлением сроков эксплуатации) электровозов ВЛ10, ВЛ11, эксплуатируемых ОАО «РЖД» .
Особенности конструкции:
Электровоз состоит из двух секций. Каждая секция электровоза имеет кабину управления и комплект оборудования, обеспечивающий работу одного электровоза, а также работу по системе многих единиц в составе двух электровозов (2×2ЭС4К) или в составе трех секций. Электровоз 2ЭС4К унифицирован с электровозом 2ЭС5К по узлам механической части, кабине управления, пневматическому, тормозному и другому оборудованию. Электрическая схема обеспечивает работу электровоза в режиме тяги, электрического (рекуперативного и реостатного) торможения, выбега и стоянки. В тяговом режиме работы электровоза электрическая схема обеспечивает работу тяговых электродвигателей с независимым и последовательным возбуждением, в режиме рекуперативного и реостатного торможения — с независимым возбуждением при питании от статистического преобразователя. Регулирование скорости электровоза осуществляется ступенчато с тремя группировками тяговых двигателей: последовательное, последовательно-параллельное и параллельное соединение. Электровоз имеет ходовую часть, отвечающую современным требованиям; передача силы тяги и торможения от тележек к кузову осуществляется цельными наклонными тягами. Кузов и тележки связаны между собой в вертикальном и поперечном направлениях с помощью упругих и демпфирующих элементов. Первая ступень подвешивания — винтовые пружины сжатия, вторая ступень — на пружинах «Флексикойл». Современная кабина управления с улучшенными условиями труда локомотивной бригады.
Трехфазные асинхронные электродвигатели для привода вентиляторов охлаждения тяговых двигателей, компрессоров с питанием от статического преобразователя. Предусмотрена возможность регулирования производительности вентиляторов охлаждения тяговых двигателей в зависимости от их температуры. Электровоз оборудован холодильником и сантехническим оборудованием (умывальник, туалет).
Современные системы безопасности движения:
— комплексное локомотивное устройство обеспечения безопасности (КЛУБ-У);
— телемеханическая система контроля бодрствования машиниста (ТСКБМ);
— система автоматического управления торможением поездов (САУТ-ЦМ/485).
Технические данные электровозов ВЛ-10У и 2ЭС4К (см. табл.1)
Таблица 1
Технические данные: | 2ЭС4К | ВЛ-10у | |
Номинальное напряжение, В | |||
Формула ходовой части | 2(2о-2о) | 20−20−20−20 | |
Колея, мм | |||
Нагрузка от оси на рельсы, кН (тс) | 24,0±0,5 | 25±0,5 | |
Разность поколесной (для одной оси) нагрузки, кН (тс), не более | 0,5 | 0,5 | |
Мощность часового режима на валах тяговых двигателей, кВт, не менее | |||
Сила тяги часового режима, кН (тс), не менее | 434(44,3) | 395(39,5) | |
Скорость часового режима, км/, не менее | 48,7 | ||
Мощность продолжителього режима на валах тяговых двигателей, кВт, не менее | |||
Сила тяги продолжительного режима, кН, (тс), не менее | |||
Скорость продолжительного режима, км/ч не менее | 53,4 | 51,2 | |
Максимальная скоростьв эксплуатации, км/ч | |||
КПД в продолжитльном режиме, не менее | 0,88 | 0,9 | |
Масса электровоза с 0,67 запаса песка, т | 192±4 | 200±4 | |
Электрическое торможение | рекуперативное, реостатное | рекуперативное, реостатное | |
Номинальная длина электровоза по осям автосцепок, мм | |||
Номинальная высота от оловки рельса до рабочей поверхности полоза токоприёмника в опущенном положении, мм | |||
Высота от головки рельса до оси автосцепки, мм | 1060±20 | 1040−1080 | |
3. КРАТКАЯ ХАРАКТЕРИСТИКА БУКСОВОГО УЗЛА ЭЛЕКТРОВОЗОВ ВЛ-10 И ВЛ-10У
3.1 Назначение и классификация Через буксовый узел от рамы тележки на колесные пары передаются вертикальные нагрузки, а от колесных пар на раму тележки — горизонтальные продольные и поперечные силы. Передача вертикальных сил происходит через упругие элементы буксового (или 1-й ступени) подвешивания и буксы; для передачи горизонтальных сил, обеспечения вертикальных перемещений рамы тележки относительно колесной пары и параллельности осей колесных пар предназначены буксовые направляющие. Для уменьшения горизонтального воздействия на путь буксовые направляющие должны создавать упругую связь между колесной парой и рамой тележки в поперечном направлении.
Различают буксовые узлы с плоскими (ВЛ8, ВЛ23) и цилиндрическими (ЧС2, ЧС2Т) направляющими, а также с направляющими в виде поводков (ВЛ10, ВЛ11). На конструкцию корпуса буксы влияет тип буксовых направляющих и тип буксовых подшипников. С 1957 г. в буксах отечественных электровозов устанавливают только подшипники качения; буксовые подшипники качения применены также на электровозах ЧС2, ЧС2Т. Роликовые подшипники по сравнению с подшипниками скольжения имеют ряд преимуществ: меньше сопротивление движению электровоза (особенно при трогании), расход смазки уменьшается в 5—10 раз, экономятся цветные металлы (бронза, баббит), не требуется повседневный уход в эксплуатации, уменьшаются свободные разбеги колесной пары, повышается надежность буксового узла. Применяют роликовые подшипники двух типов: с цилиндрическими (ВЛ10, ВЛ11, ВЛ8) и сферическими или бочкообразными (ВЛ8, ВЛ23, ЧС2, ЧС2Т) роликами. Подшипники могут быть однорядными и двухрядными; в буксах устанавливают два однорядных или один, а иногда и два двухрядных роликовых подшипника.
На крышках букс устанавливают токоотводящие (заземляющие) устройства и привод скоростемера
3.2 Устройство буксового узла Буксовый узел электровозов ВЛ10 и ВЛ-10У. Букса 4 (рис. 3.1.) соединена с большим 5 и малым 1 кронштейнами рамы 3 тележки двумя буксовыми поводками 2.
Вертикальная нагрузка передается от рамы на колесные пары через стойки 6, пружины 7, рессору 8, подвешенную к проушинам буксы 4, и буксу.
Относительные перемещения между рамой тележки и колесной парой сопровождаются поворотом поводков в вертикальной (при вертикальных колебаниях) и горизонтальной (при поперечных перемещениях) плоскостях.
Рис. 3.1 — Буксовой узел электровозов ВЛ10 и ВЛ-10У
1-малый кронштейн;2-буксовой поводок;3-рама тележки;4-букса;
5-большой кронштейн;6-стойки;7-пружина;8-рессора Каждый поводок (рис. 3.2.) состоит из литого корпуса или тяги 2, двух сайлентблоков и торцовых резинометаллических шайб 6. Сайлентблок состоит из валика 5 диаметром 65 мм и одной или двух резинометаллических втулок.
Резиновая втулка 9 запрессована в стальную 8, а валик запрессован в
резинометаллическую втулку. Сайлентблоки запрессованы в корпус поводка, а на трапецеидальные концы валиков установлены торцовые шайбы 6. Положение шайб относительно корпуса поводка фиксировано штифтами 7. Концы валиков входят в трапецеидальные пазы кронштейнов 4 рамы и приливов 1 корпуса буксы и затягиваются болтами 3. Поэтому при перемещениях буксы валики одного поводка остаются параллельными и не вращаются, а поворот поводка сопровождается деформациями резины втулок и торцовых шайб, т. е. все относительные перемещения происходят без внешнего трения и износа деталей поводков.
Корпус 3 (рис. 3.3.) буксы отливают из стали 25Л-И; он имеет цилиндрическую форму, две пары приливов для крепления поводков и два прилива внизу для подвешивания рессоры. Внутри корпуса помещены два однорядных подшипника 4 с цилиндрическими роликами, разделенные дистанционными кольцами 11. Наружные кольца подшипников имеют скользящую посадку в корпусе буксы (зазор 0,09 мм), а внутренние насаживают на шейку оси в горячем состоянии (нагрев в масле до температуры 100 — 120° С) с натягом 0,04— 0,06 мм (горячая посадка).
Рис. 3.2. — Буксовой поводок
1-прилив;2-литой корпус/тяга;3-болт;4-кронштейн;5-валик;
6-сайлентблок/торцовые шайбы;7-штифт;8-стальная втулка;
9-резиновая втулка Рис. 3.3 — Букса электровозов ВЛ-10 и ВЛ-10У
1-заднее упорное кольцо;2-задняя крышка;3-корпус; 4-подшипник; 6 передняя крышка; 7-болт;8-планка;9-гайка; 10-фассоное упорное кольцо;11 дистанционные кольца
4. ТЕХНИЧЕСКОЕ ОБСЛУЖИВАНИЕ В ЭКСПЛУАТАЦИИ
4.1 Обслуживание в эксплуатации В процессе эксплуатации необходимо вести наблюдение за работой буксового узла:
1.Проверять нагрев букс: при нормальной работе роликовой буксы температура ее наружных поверхностей не должна превышать температуру окружающего воздуха более чем на 30С. Наибольшая температура наружных частей буксы во всех случаях не должна превышать 70С. При осмотре буксового узла проверяется нагрев буксы тыльной стороной руки, если рука не терпит, то букса уже нагрелась выше 70С.
Основные причины повышенного нагрева буксовых узлов следующие:
*недоброкачественность и недостаточное количество смазки;
*повреждение роликовых подшипников;
*попадание в подшипники песка и механических примесей;
*неправильная сборка подшипников и других деталей узла;
*заедание в лабиринтном уплотнении или сильное трение уплотнительного кольца и др.
2. Следить за отсутствием течи масла
3. Проверять состояние крепления буксового узла. Путем отстукивания молотком выявляются ослабленные болты, обращая особое внимание на крепление передней крышки, где болты могут ослабевать из-за причины излома пружинных шайб. Обращать внимание на состояние и крепление сайлентблоков, а также листовой рессоры.
Кроме технического обслуживания, буксы должны подвергаться ревизии. Ревизию букс производят в соответствии со специальной инструкции по содержанию и ремонту роликовых подшипников локомотивов и моторвагонного подвижного состава ЦТ2361.
Надежность работы роликоподшипниковых букс, как узлов высокой точности изготовления, во многом зависит от качества монтажных работ и соблюдения при этом всех требований при сборке букс.
4.2 Износы и повреждения Через буксовый узел на раму локомотива передаются горизонтальные (тяговые, тормозные и др.) и вертикальные нагрузки. В зависимости от конструкции буксы и места приложения вертикальных усилий возникает износ рессорных стоек в верхней части буксовой коробки, гнезд под хомуты надбуксовых листовых рессор или отверстий проушины подвески рессор в нижней части буксовой коробки. Общим для челюстных букс является износ наличников на электровозах и боковых пазов букс моторных вагонов электропоездов. Для бесчелюстных букс электровозов характерны выработка резины у поверхности валиков, проворачивание валиков в резине, ослабление шайб на валике, излом и срез штифтов, ослабление крепления поводка буксы к буксовому кронштейну.
На бесчелюстных буксах прицепных вагонов электропоездов возможен износ шпинтонов. У букс с подшипниками скольжения изнашивается задняя стенка от трения с антифрикционным диском, а у букс с подшипниками качения происходит износ лабиринтных колец.
Общими повреждениями для букс всех типов являются трещины, раковины и порча коррозией, а также риски, задиры, заусенцы, связанные с дефектами подшипников. [6]
4.3 Осмотр и ревизия Осмотр букс проводят при техническом обслуживании и текущих ремонтах. Убеждаются в целостности корпусов букс и отсутствии в них трещин. Проверяют плотность прилегания буксовых крышек и надежность их крепления, заменяют оборванные болты и при необходимости восстанавливают их крепление шплинтами. Как правило, буксы с подшипниками качения не вскрывают, если не проводится их ревизия. Причинами снятия крышек могут служить данные о ненормальной работе буксы в виде повышенного нагрева, который проверяется рукой на ощупь и не должен превышать 70С, записи локомотивной бригады о ненормальной работе на линии, наличие подтеков расплавленной смазки Ж.Р.О. и др.
Проверяют крепление буксовых поводков, зазоры между дном паза и валиком поводка. Смазка с резиновых частей амортизатора должна быть удалена. Через один ТР-1 осматривают буксу с приводом скоростемера.
При этом разжиженную смазку удаляют и добавляют свежую. На электровозах восстанавливают правильное положение колесных пар и букс в тележках, зазоры и разбеги, которые нарушаются в течение межремонтного пробега вследствие износа узлов и деталей.
Ревизии букс бывают промежуточными, большими и полными. Промежуточную ревизию выполняют при ТР-2. Для этого буксу осматривают, проверяют целостность корпуса, крышек, сварных швов наличников и других деталей. Очищают от грязи и снимают передние крышки букс, укладывают их в чистый противень или закрывающийся ящик внутренней стороной вверх. Старую загрязненную смазку в доступной части удаляют и детали протирают. Обращают внимание на количество смазки и возможное ее загрязнение. Если при растирании смазки руками в ней обнаруживаются металлическая пыль или кусочки металла, колесную пару выкатывают и буксу демонтируют.
После удаления смазки из передней части буксы проверяют доступные для осмотра детали, состояние стопорных устройств на шейке оси, крепление болтов, наличие и прочность крепления проволоки и легкими ударами слесарного молотка убеждаются в надежности крепления торцовой гайки. Ощущаемое рукой смещение гайки не допускается. Если при затяжке гайка проворачивается на пол-оборота и более, буксу демонтируют для ремонта. Проверяют детали переднего подшипника, убеждаются в отсутствии трещин в подшипниковом кольце, сепараторе и других дефектов.
На буксах с токоотводящим устройством проверяют состояние самого устройства, фасонной изолирующей прокладки между крышкой буксы и корпусом токоотводящего устройства. Зазор между ними должен быть не менее 3 мм.
Болты, крепящие корпус к крышке, не должны соприкасаться с корпусом, поэтому необходимо проверять состояние изолирующих втулок. Стопорные шайбы не должны касаться корпуса токоотводящего устройства.
Проверяют состояние щеткодержателей и щеток, при необходимости щетки заменяют и регулируют нажатие на них. Для надежной работы в токоотводящем устройстве необходимо, чтобы торцовое биение контактного диска не превышало 0,5 мм при полностью выбранном осевом люфте буксовых подшипников.
Добавляют при необходимости смазку Ж.Р.О. так, чтобы было заполнено примерно от 1/3 до ½ передней полости корпуса буксы. При выполнении работ необходимо предохранить внутренность буксы от загрязнения.
Большую ревизию букс проводят при ТР-3. Кроме того, большую ревизию букс колесных пар э.п.с. согласно Инструкции по содержанию и ремонту, роликовых подшипников локомотивов и моторвагонного подвижного состава ЦТ/2361 выполняют при наличии ползуна на поверхности катания колесной пары более 1,5 мм, после схода колесной пары с рельсов при скорости движения свыше 40км/ч, а также при повреждении подшипникового узла после крушения или аварии. Для этого буксы разбирают, оставляя на шейках оси внутренние кольца цилиндрических подшипников. Сферические подшипники оставляют на оси полностью. Подшипники промывают и осматривают. При сборке буксы блоки цилиндрических подшипников и большие дистанционные кольца ставят на прежние места в соответствии с маркировкой. Если же при разборке буксы не обнаруживается нумерация деталей, то маркировку мест их расположения наносят кислотой. Проверяют зазоры и разбеги подшипников.
Отбракованные детали ремонтируют или заменяют. После сборки буксы заправляют свежей смазкой.
Полную ревизию букс выполняют при полном освидетельствовании колесных пар, а также при необходимости замены подшипника. Подшипниковый узел в этом случае разбирают, все детали промывают и осматривают.
Корпуса, роликовые подшипники и их детали при необходимости ремонтируют или заменяют новыми. Замеряют и восстанавливают посадочные натяги и зазоры.
4.4 Разборка буксы При ТР-3 буксы электровозов ВЛ10, ВЛ11 и ВЛ80 разбирают следующим образом: отворачивают гайки, выбивают болты, укрепляющие поводок в пазах, и проверяют резьбу. Детали буксового узла тщательно обмывают в моечной машине. При этом, чтобы не произошло их коррозионного повреждения, не следует допускать длительных (более 6ч) разрывов между окончанием обмывки и началом ремонта. Поводки демонтируют и осматривают. Годные подвергают магнитной дефектоскопии.
После обмывки в моечной машине и протирания корпуса буксы с крышками, дистанционными кольцами, гайкой с планкой и лабиринтное кольцо (если оно снималось с оси) осматривают и ремонтируют.
4.5 Ремонт элементов букс Роликовые подшипники промывают мыльной эмульсией в специальной моечной машине, затем повторно промывают в бензине и насухо протирают салфетками. Осмотр, обмер и дефектоскопию роликовых подшипников проводят согласно Техническим указаниям по эксплуатации и ремонту букс роликовыми подшипниками электровозов и тепловозов ЦТ/2319, а также технологической Инструкции ОТЕ. 412.003 Тбилисского электровозостроительного завода. При осмотре выявляют следы чрезмерного нагрева (по наличию цветов побежалости), трещины на кольцах, роликах и сепараторах, выкрашивания металла и раковины на дорожке качения внутреннего кольца, ползуны (лыски) на поверхности качения роликов.
Не менее важно обнаруживать седловатость, бочкообразность, ступенчатость посадочной поверхности внутреннего кольца подшипника, скол бурта кольца, поперечные глубокие риски на дорожках качения колец, следы коррозии на рабочих поверхностях колец и роликов; ослабление, обрывов и срыв заклепок сепаратора, сколы роликов по торцам и кромкам.
При наличии указанных дефектов подшипники ремонтируют, забракованные детали заменяют. При переборке роликов их проверяют на специальном приборе с миниметром 1 (рис 4.1.), установленным на штативе 2, измеряя диаметры роликов 3 в середине и на расстоянии 10−15мм от торцов. Разность диаметров роликов в одном комплекте подшипника не должна превышать 10мкм. Овальность и разность диаметров по краям цилиндрической части допускаются до 5мкм, выпуклость в средней части — до 10мкм, вогнутость ролика недопустима. На этом же приборе проверяют высоту роликов, которая должна соответствовать нормам.
После подбора роликов специальным прессом осуществляют холодную клепку сепараторов. У отремонтированного подшипника, скомплектованного с дистанционными кольцами, определяют индикатором 2 (рис 4.2.) на плителютфомере 2 радиальный зазор.
Рис 4.1 — Измерение диаметра ролика
1-миниметр; 2-штатив; 3-ролик Рис 4.2 — Измерение радиального зазора подшипников
1-плителюфтомер; 2-индикатор; 3-нажимная шайба Для этого внутренние кольца закрепляют нажимной шайбой 3, а наружное кольцо вместе со штифом индикатора перемещают от руки в горизонтальном направлении.
На плите-люфтомере проверяют также осевой зазор подобранного комплекта подшипников. Затем определяют натяг, который образуется при посадке на шейку оси колесной пары внутренних колец роликовых подшипников, он должен быть в пределах 0,04−0,06 мм. Внутренний диаметр измеряют нутромером с индикатором в трех сечениях по ширине кольца по двум взаимно перпендикулярным направлениям. Если натяг менее 0,03 мм, его восстанавливают осталиванием или нанесением клея (эластомера) ГЭН-150 В на внутреннюю поверхность кольца роликового подшипника.
Корпус буксы тщательно осматривают и обстукивают молотком для выявления трещин, надрывов, задиров, заусенцев, следов коррозии и рисок на обработанных поверхностях. При наличии сквозных трещин корпус буксы отбраковывают. Также не допускается заварка трещин и надрывов независимо от их размера в проушинах буксы под валик хомута и в щеках корпуса под поводки.
Мелкие рассредоточенные надрывы разрешается устранять электросваркой на необработанных поверхностях корпуса буксы, за исключением щек и хвостовиков, при условии, что глубина после вырубки трещин не превышает 6 мм, а объем наплавленного металла 8 см3.
Перед заваркой с помощью пневматического зубила осуществляют Vобразную разделку кромок с засверловкой концов надрывов. Заварку выполняют электродом Э50А, при этом следят за тем, чтобы не допускать коробления корпуса буксы вследствие сильного местного нагрева. Для исключения коробления сварочные и наплавочные работы желательно выполнять в ванне с водой.
Проверяют овальность и конусность посадочных поверхностей отверстия корпуса буксы. Измерения выполняются в двух местах по длине корпуса буксы, причем в каждом из них — в двух взаимно перпендикулярных направлениях. При выпуске из ТР-3 диаметр отверстия корпуса буксы должен быть 320+0,3мм. Следы коррозии на внутренней поверхности буксы зачищают шлифовальной бумагой № 5 или 6, не допуская при этом повреждения основного металла. Риски и задиры глубиной более 1 мм зачищают наждачным полотном, если же они имеют меньшую глубину, их разрешается оставлять без исправления. Пазы в щеках корпуса буксы под валики поводков проверяют шаблоном. При необходимости размеры пазов восстанавливают наплавкой электродом Э42А с последующей механической обработкой до чертежных размеров.
Замеряют отверстие под валик в проушинах буксы. В случае износа отверстие растачивают не более чем на 2 мм от чертежного размера или осуществляют наплавку с последующей обработкой.
Резьба в отверстиях корпуса буксы должна быть чистой, без заусенцев, вмятин и раковин. Допускаются отдельные сорванные нитки резьбы при условии, что в сумме они составляют не более 1/3 витка в отверстии. Если же повреждения резьбы большие, то нарезать новую резьбу в корпусе буксы под болты крышки не разрешается. В таком случае старую резьбу рассверливают до полного ее удаления, отверстие заваривают и рассверливают вновь, затем нарезают резьбу чертежного размера. После наплавки пазов и отверстий в буксе и механической обработки проверяют их взаимное расположение в корпусе буксы и соответствие чертежу.
Крышки (переднюю и заднюю) корпуса буксы осматривают. При обнаружении трещин на фланцевой и посадочных поверхностях крышки подлежат замене. Продукты коррозии, заусенцы и задиры глубиной не более 0,5 мм на привалочных поверхностях крышек, лабиринтных пазах и выступах снимают шабером и зачищают шлифовальной бумагой, на нерабочих поверхностях — напильником. Проверяют состояние резьбы в передних крышках для крепления редуктора скоростемера. Допускаются отдельные сорванные нитки резьбы при условии, что в сумме они составляют не более 1/3 витка в каждом отверстии. В случае повреждения или разработки резьбы ее нарезают на следующий размер согласно государственному стандарту.
При большой разработке старую резьбу высверливают, отверстие заваривают, рассверливают и нарезают новую резьбу по чертежу. Проверяют состояние выступов и пазов в задней лабиринтной крышке буксы не менее чем по двум взаимно перпендикулярным направлениям. При необходимости лабиринты наплавляют с последующей механической обработкой или заменяют крышку. Шупом на плите проверяют плоскостность торцовой поверхности задней крышки, а штангенрейсмусом — параллельность ее привалочному фланцу. После этого внутреннюю поверхность лабиринтной крышки окрашивают нитроэмалью или другой маслостойкой краской.
Лабиринтное кольцо осматривают. При обнаружении изломов, трещин, надрывов, коробления, износов, вызывающих ослабление в посадке на предподступичной части оси, лабиринтное кольцо заменяют. Кольцо, годное, но ослабшее в посадке, или изношенное по пазам и выступам лабиринта, разрешается восстанавливать наплавкой с последующей обработкой.
В случаях, когда овальность и конусность кольцо превышает 0,07 мм, а натяг менее 0,05 мм, кольцо можно восстанавливать путем цинкования, осталивания или нанесения клея (эластомера) ГЭН-150 В на внутреннюю поверхность кольца. Натяг на посадку кольца на ось должен быть в пределах 0,02−0,145 мм.
Дистанционные кольца буксы при наличии трещин или сколов заменяют, задиры, забоины, и следы коррозии устраняют, острые кромки притупляют шлифовальной бумагой и напильником.
Поводки очищают от грязи и масла, протирают концами, смоченными в керосине, и насухо обтирают. Обмывать поводки в растворах, содержащих каустик, нельзя.
Валики и корпус (тягу) поводка осматривают, убеждаются в отсутствии износов клиновидной части, отверстий и резьбы в хвостовиках валиков, проворота валиков в резиновых втулках или вместе с втулками в корпусе; изломов штифов или ослабления их посадки в корпусе поводка. При обнаружении таких дефектов в резинометаллических втулках валик в сборе с втулками выпрессовывают и передают в заготовительных цех для переформирования. При этом дефектные втулки удаляют, а годные валики используют для формирования с новыми втулками. Вновь сформированный валик выдерживают в течении 10 дней в светонепроницаемой камере при температуре 15−30С. При не восстановительных дефектах валика в поводок запрессовывают ранее сформированный валик из переходящего запаса.
Осуществляют дефектоскопию средней части тяги (корпуса) поводка для выявления трещин, изломов. При наличии трещин и изломов тягу заменяют, а при износе или срезании штифтов их удаляют, проверяют разверткой отверстия и запрессовывают новые штифты. Годные и отремонтированные тяги (корпуса) используют для сборки с ранее сформированными валиками из переходящего запаса. При этом для обеспечения требуемой жесткости поводка в продольной и поперечной плоскостях убеждаются в наличии на торцах валиков клейма с указанием твердости резиновой втулки в условных единицах. Жесткость двух поводков под нагрузкой 39 кН должна составлять в продольном направлении 78,5 кН/мм ± 20%, в поперечном направлении — 7,85 кН/мм ± 20%.
ЗАКЛЮЧЕНИЕ
Тормозная рычажная передача является последним звеном в цепи приборов и устройств служащих для обеспечения локомотива тормозами. Только технически исправная и правильно отрегулированная тормозная рычажная передача может обеспечить чёткую работу всего тормозного оборудования локомотива. В процессе развития и совершенствования устройств тормозного оборудования появляются и внедряются в эксплуатацию новые системы позволяющие обеспечить всё большую безопасность для передвижения железнодорожного транспорта. К такому оборудованию можно отнести Авторегулятор № 574Б. Авторегулятор сам без вмешательства человека регулирует выход штока тормозного цилиндра, чем обеспечивает постоянно одинаковое расстояние между тормозными колодками и бандажом колеса. Также постепенно начинают заменять чугунные тормозные колодки на композиционные.
В данной дипломной работе были рассмотрены основные узлы тормозной рычажной передачи и принцип её работы, методы её ремонта и регулировки, а так же были представлены подробные схемы.
электровоз тормозной рычажный передача
1. Кикнадзе, О. А. Электровозы ВЛ-10 и Вл-10у [Текст] руководство по эксплуатации/Под ред. О. А. Кикнадзе.- М.: Транспорт, 1981.-519 с.
2. Находкин, В. М. Ремонт электроподвижного состава [Текст] Под ред. В. М. Находкин: Транспорт, 1989. 297 с.
3. Инструкция по содержанию и ремонту роликовых подшипников локомотивов и моторвагонного подвижного состава ЦТ/2361
4. Технические указания по эксплуатации и ремонту букс с роликовыми подшипниками электровозов и тепловозов ЦТ/2319
5. Дубровский, З. М. Электровоз. Управление и обслуживание [Текст] З. М. Дубровский, В. А. Курчашова, Л. П. Томфельд. — М., «Транспорт», 1979. 231 с.
6. Сидоров, Н. И. Как устроен и работает электровоз [Текст]/Н.И.Сидоров, Н. Н. Сидорова.-5-е изд., перераб. и доп.-М.: Транспорт, 1988.-233 с.