Другие работы
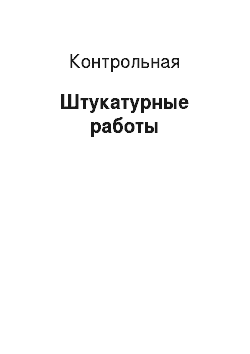
Готовый штукатурный раствор накладывают на специальную доску — сокол. Классический сокол представляет собой квадратный деревянный щит размером примерно 40×40 или 45×45 см из плотно пригнанных досок, толстой фанеры или металлического листа с ручкой. На сокол берут штукатурный раствор и с сокола раствор наносят — набрасывают — небольшими порциями на стену. Но можно использовать сокол и для…
Контрольная 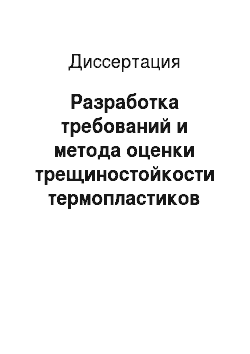
Научная новизна работы заключается в: классификации современных материалов для дорожной разметки на основе принципа формирования структуры, определяющего как технологию их нанесения, так и эксплуатационные свойстваанализе повреждений дорожной разметки с выявлением вызывающих их причинприменении метода статистического моделирования результатов в виде интегральной функции распределения…
Диссертация 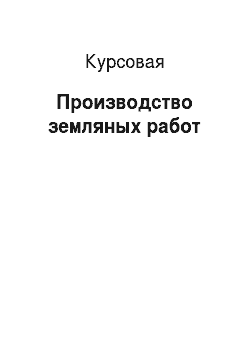
СНиП 12−03. Прогреваемую площадь следует ограждать, устанавливать на ней предупредительные сигналы, а в ночное время освещать. Расстояние между ограждением и контуром прогреваемого участка должно быть не менее 3 м. На участках прогреваемой площади, находящихся под напряжением, пребывание людей не допускается. Линии временного электроснабжения к прогреваемым участкамперемещения электрооборудования…
Курсовая 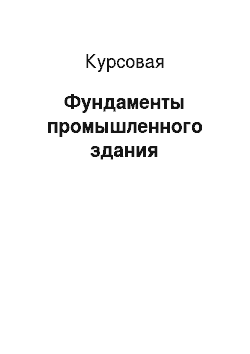
Геологический разрез строится на миллиметровой бумаге масштаба А3 в последовательности: скв.1-скв.2-скв.3-скв.4. По горизонтальной оси вдоль длиной стороны листа откладываются расстояния между скважинами в масштабе, при котором развертка по скважинам составит около 200 мм, и вертикальными линиями выносятся оси скважин. С левой стороны разреза размещается масштабная линейка с указанием абсолютных…
Курсовая 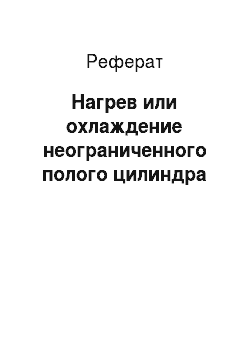
Неограниченный полый цилиндр — это, другими словами, труба большой длины, характеризующаяся двумя радиусами: R1 — внутренний радиус трубы и Т?2 — внешний радиус. В двух задачах, которые мы рассмотрим ниже, требуется найти распределение температуры внутри стенки трубы, т. с. в области 7?, < г < R2 в любой момент времени: T (r, f) в области У?, < г < R2. Будем использовать следующие обозначения…
Реферат 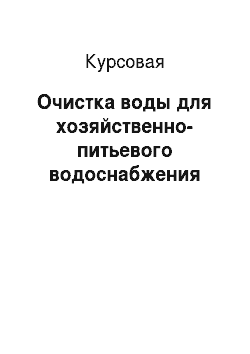
Выбор той или иной технологической схемы очистной станции зависит то качества исходной воды. Воспользовавшись СНиП табл.1, можно подобрать основные сооружения для очистки воды, а затем можно подобрать вспомогательные. Предварительный выбор технологической схемы для осветления и обесцвечивания воды зависит от производительности станции и от условий применения (мутность и цветность) исходной…
Курсовая 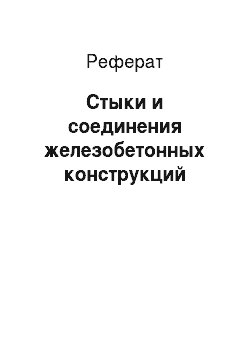
Антикоррозийные покрытия наносятся несколькими способами: цинковые — газопламенным напылением; цинко-лакокрасочные — нанесением цинкового подслоя, по которому лакокрасочные материалы наносятся пистолетами-краскораспылителями или вручную. Протекторные грунты наносятся кистью вручную. При газопламенном способе напыления антикоррозийных покрытий применяются порошки цинка, цинкоаллюминиевого сплава…
Реферат 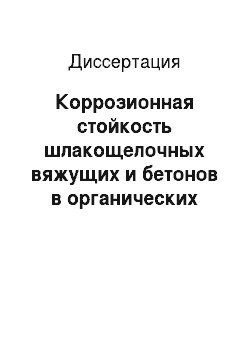
Одной из наиболее актуальных задач, поставленных партией и правительством, является задача комплексного использования С1лрьевых ресурсов. В Основных направлениях экономического и социального развития СССР на I98I-I985 г. г. и на период до 1990 года указывается на необходимость в области естественных и теоретических наук решить несколько важнейших проблем, одной из которых предусмотрено «создание…
Диссертация 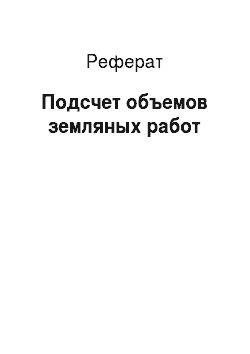
Подсчет объемов земляных работ производят по поперечным профилям. Через 20—40 м по длине дороги строят поперечные профили, на которых показывают проектные отметки и отметки поверхности земли для характерных точек поперечного профиля. На каждом поперечнике отдельно вычисляют площади насыпи и выемки и общую площадь путем разбивки сложного сечения на более простые фигуры (трапеции, треугольники…
Реферат 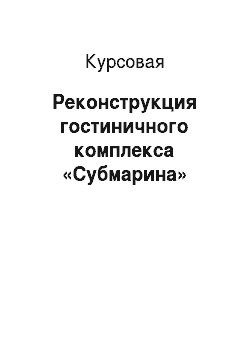
Зубцовский туристский гостиничный комплекс «Субмарина» работает на рынке 34 года. Данное предприятие находится в государственной собственности; было построено в 1975 г. Гостиница располагается недалеко от трассы Москва — Рига, что позволяет всем проезжающим мимо наблюдать это неброское трёхэтажное здание. Данное расположение благоприятно для проезжающих ещё тем, что ненужно долго искать в городе…
Курсовая 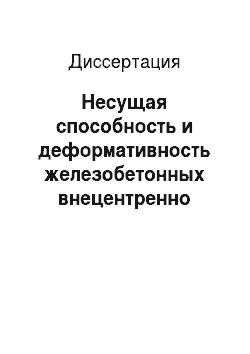
В железобетонных колоннах П-образного сечения под действием внецентренно приложенной нагрузки распределение напряжений в стадии до и после образования трещин происходит как в неупругом теле, особенно в состоянии, близком к предельному. Основной особенностью, влияющей на несущую способность и деформативность колонн, является непропорциональная зависимость между напряжением и деформацией…
Диссертация 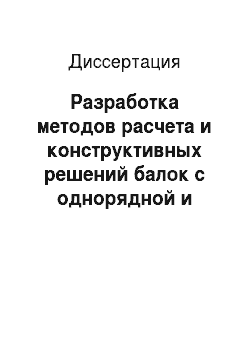
Актуальность исследования. В строительных сооружениях, таких как мосты и многоэтажные административные комплексы, торговые центры и многоярусные гаражи, спортивные сооружения и аквапарки широко применяются перфорированные балки, изготавливаемые по безотходной технологии из прокатных и сварных двутавровых профилей. Распространение получили балки с шестиугольными, восьмиугольными, круглыми…
Диссертация 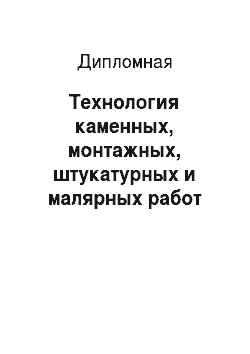
Повышение качества строительства неразрывно связано с его эффективностью. Одним из важнейших резервов повышения эффективности строительного производства является совершенствование технологии и организации монтажа строительных конструкций как одного из ведущих процессов возведения зданий и сооружений. Монтаж строительных конструкций представляет собой сложный комплекс связанных между собой…
Дипломная 
Сколько шире, чем модуля, но это отступление нисколько не должно нас удивлять. Наоборот, оно естественно по следующим причинам. В коринфском ордере, стоящем в ряду других на табл. II, модуль получился наименьшей величины, поэтому половина его дала бы слишком малый размер, но, как видно на изображениях, карниз коринфского пьедестала получил большее по сравнению с другими развитие; здесь под…
Реферат