Формирование оптимальных структур и свойств при проведении контролируемой прокатки трубных сталей, содержащих ниобий
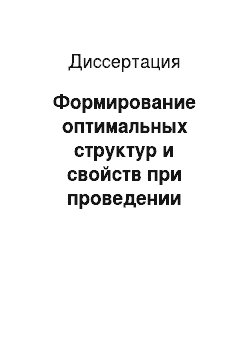
Одним из перспективных российских проектов является создание системы магистральных нефтепроводов Восточная Сибирь — Тихий океан (ВСТО). Проект предусматривает строительство нефтепровода на проектное давление 9,8 МПа, а на ряде участков до 14 МПа, включительно с возможным использованием прямошовных и спиральношовных труб диаметром до 1220 мм класса прочности от К42 до К60 включительно. Помимо… Читать ещё >
Содержание
- Глава I. ЛИТЕРАТУРНЫЙ ОБЗОР
- 1. 1. Контролируемая прокатка микролегированных трубных сталей
- 1. 1. 1. Аустенитизация
- 1. 1. 2. Предварительная стадия контролируемой прокатки
- 1. 1. 3. Разновидности контролируемой прокатки в зависимости от температуры завершения деформации
- 1. 1. Контролируемая прокатка микролегированных трубных сталей
Формирование оптимальных структур и свойств при проведении контролируемой прокатки трубных сталей, содержащих ниобий (реферат, курсовая, диплом, контрольная)
Начало XXI века характеризуется ростом мощностей по производству стали, проката и труб. Мировое производство стали долгое время находилось на уровне 850 млн. тонн в год, внезапно увеличило скорость роста и в 2004 г. прошло границу один миллиард тонн. Рост производства стали 5−7% в год сохраняется и до настоящего времени. Основной движущей силой такого роста является стремление развивающихся стран повысить уровень жизни за счет индустриализации. Интенсивная индустриализация развивающихся стран наряду с конструкционными материалами требует увеличения потребления энергоносителей таких, как нефть и газ, и следовательно развитие транспортных систем доставки их потребителям. Отсюда рост потребности в трубах и строительство новых трубопроводов.
Основным конструктивным элементом современных газонефтепроводных магистралей являются электросварные трубы, по которым транспортируется нефть и газ. Работоспособность газонефтепроводных магистралей зависит главным образом, от качества, уровня свойств и надежности самих труб. Имеющиеся данные свидетельствуют о существенном влиянии уровня свойств и качества основного металла труб большого диаметра на количество и протяженность разрушений трубопроводов. Газонефтепроводные трубы во время эксплуатации работают в условиях, существенно отличающихся от работы других металлических конструкций. Это связано с суровыми природно-климатическими условиями районов их применения, воздействием постоянных (газ) или циклических (нефть) нагрузок, а также с аккумулированием большого количества упругой энергии сжатого газа. Запас внутренней упругой энергии магистрального газопровода возрастает с увеличением диаметра трубы и рабочего давления транспортируемого газа.
Освоение новых перспективных месторождений нефти и газа и строительство трубопроводов для их транспортировки все более и более смещается в труднодоступные районы Севера, Сибири и арктического шельфа. Так в период с 2007 по 2012 г. г. Газпром планирует реализацию 13 крупных проектов строительства газопроводов высокого давления общей протяженностью более 13 тыс. км диаметром 1020−1420 мм.
Одним из перспективных российских проектов является создание системы магистральных нефтепроводов Восточная Сибирь — Тихий океан (ВСТО). Проект предусматривает строительство нефтепровода на проектное давление 9,8 МПа, а на ряде участков до 14 МПа, включительно с возможным использованием прямошовных и спиральношовных труб диаметром до 1220 мм класса прочности от К42 до К60 включительно. Помимо прочностных свойств к металлу труб предъявляются высокие требования по величине ударной вязкости на ударных образцах с острым надрезом — KCV. Предусмотрено использование труб обычного и хладостойкого исполнения, а также труб с повышенной эксплуатационной надежностью и сейсмической устойчивостью. Требования для труб с повышенной эксплуатационной надежностью более жестко регламентируют химический состав стали (значение углеродного эквивалента не должно превышать 0,38) и долю вязкой составляющей в изломе образцов ИПГ.2о не менее 70%.
Высококачественные трубы большого диаметра будут востребованы также при реализации одного из важнейших проектов в газовой отрасли — СевероЕвропейского газопровода. Этот проект позволит наладить прямые поставки природного газа из России в Западную Европу по дну Балтийского моря, минуя территории третьих стран. При строительстве 1-й очереди газопровода (сухопутная часть) предусмотрено использование труб диаметром 1420 мм на давление до 9,8 МПа класса прочности К60. Возможности Волжского трубного завода позволяют обеспечить потребности строительства газопровода в части труб класса прочности К60 с толщиной стенки 21,6 мм.
Кроме перечисленных проектов до 2012 г. планируется сооружение газопровода Бованенково-Ухта и со Штокманского месторождения, подводных трубопроводов — второй нитки голубой поток по дну Черного моря.
Сооружение новых трубопроводов требует решения двух задач: увеличение объемов производства труб большого диаметра, в т. ч. толстолистового проката для их производстваи повышение качественных характеристик металла и труб с учетом строительства газопроводов на давление 11,8 МПа на суше и до 25 МПа — на море, применение в новых проектах труб из сталей с прочностью К65 и повышенных толщин стенок труб с учетом прохождения в сложных климатических и геологических условиях.
Для осуществления этих проектов требуются стальные трубы не только высокого качества, но и дешевые. Наиболее экономичным способом производства листов для труб магистральных газопроводов является контролируемая прокатка, которая обеспечивает требуемый комплекс механических свойств, за счет измельчения структуры без применения дополнительной термообработки. Большой вклад в разработку и внедрение в промышленность контролируемой прокатки и основ легирования и микролегирования сталей для труб большого диаметра внесли труды Д. А. Литвиненко, С. А. Голованенко, M. J1. Бернштейна, Н. П. Лякишева, В. Н. Зикеева, П. Д. Одесского, Л. И. Эфрона, Ю. Д. Морозова и др. ученых.
Опыт производства листов на металлургических комбинатах Азовсталь и Ильича показывает, что контролируемая прокатка не во всех случаях обеспечивает удовлетворительный уровень ударной вязкости и доли вязкой составляющей на образцах ИПГ. В отдельных участках листов образуется неоднородная крупнозернистая структура с баллом ферритного зерна номер 8−10. Кроме этого по толщине листа часто наблюдается неоднородная кристаллографическая текстура. В настоящий момент нет четкого объяснения причин возникновения этих явлений. Скорее всего, это связано с тем, что на заводах используют не оптимальные режимы контролируемой прокатки.
Целью настоящей работы являлось разработка на основе выявленных взаимосвязей аустенитной и конечной структуры, формирующейся под влиянием различных условий температурно-деформационного воздействия, усовершенствованного режима контролируемой прокатки на стане 3600 ОАО «МК «Азовсталь», обеспечивающего повышение показателей хладостойкости, ударной вязкости и прочности микролегированных ниобийсодержащих толстолистовых сталей, предназначенных для изготовления магистральных газо-нефтепроводных труб большого диаметра.
Актуальность обусловлена необходимостью повышения комплекса механических свойств листов из микролегированных сталей для газо-нефтепроводных труб большого диаметра ответственного назначения и выяснения в связи с этим механизмов структурообразования под воздействием горячей пластической деформации и поиска технологических решений, направленных на совершенствование структуры, повышения ее однородности и дисперсности за счет применения оптимальных режимов температурно-деформационного воздействия на толстолистовом стане 3600 ОАО «МК «Азовсталь».
Для достижения поставленной цели необходимо было решить следующие задачи: изучить кинетику превращения деформированного аустенита при непрерывном охлаждении и определить температуру начала полиморфного у-«а-превращения для сталей различного химического состава при скоростях охлаждения, соответствующих скорости охлаждения подкатов между предварительной и окончательной стадиями деформации при проведении контролируемой прокатки в промышленных условиях на стане 3600 ОАО «МК «Азовсталь" — на основе имитации в лабораторных условиях предварительной стадии деформации контролируемой прокатки определить оптимальные температурные интервалы проведения черновой прокатки, обеспечивающие максимальное измельчение аустенитного и ферритного зернавыявить причины разнозернистости ферритного зерна микролегированных сталей в состоянии после контролируемой прокатки с завершением деформации в межкритической у+а-областина основании сравнительной оценки влияния температурно-деформационных режимов на аустенитную и конечную структуру разработать температурные схемы контролируемой прокатки, обеспечивающие повышение хладостойкости и вязкости за счет уменьшения разнозернистости и повышения однородности кристаллографической текстуры толстых листов для сталей с различными системами легирования и микролегирования. опробовать в промышленных условиях на стане 3600 возможность изготовления листов толщиной 21,6 мм для изготовления на Волжском трубном заводе спиральношовных труб диаметром 1420 мм на давление 9,8 МПа класса прочности К60.
Научная новизна. В диссертации получены следующие результаты, характеризующиеся научной новизной:
1. Определено, что в микролегированных ниобийсодержащих сталях во время предварительной стадии контролируемой прокатки, проводимой при температурах >950 °С, в паузах между обжатиями и после охлаждения подкатов до заданной температуры, наряду с первичной рекристаллизацией интенсивное развитие получает собирательная рекристаллизация, вызывающая рост аустенитного зерна, что снижает хладостойкость стали.
Снижение температуры завершения черновой прокатки от 1000 до 900 °C вызывает торможение собирательной рекристаллизации аустенита и приводит к уменьшению размеров аустенитного зерна от балла 6−7 до балла 8−9.
2. Установлено, что в исследуемых сталях на стадии чистовой прокатки протекает собирательная рекристаллизации феррита, деформированного в верхней части у+а-области при температурах на 10−20 °С ниже Аг3, в результате которой происходит укрупнение размеров ферритного зерна на 2−2,5 балла по сравнению с режимом прокатки, предусматривающим завершение деформации в нижней части у-области.
3. Анализ прямых полюсных фигур (110) a-Fe подтверждает протекание собирательной рекристаллизации горячедеформированного феррита в верхней части у+а-области, а также показывает, что при этом не происходит образование новых текстурных компонентов, а лишь ослабление уже возникших, которыми в зависимости от химического состава и режима контролируемой прокатки могут быть: {001}<110>а, {110}<110>а, {110}<001>а, {332}<113>а, {554}<225>а {113}<110>а {112}<110>а, {111 }<112>а, {111 }<110>а.
4. Установлено двойственное влияние молибдена при содержании 0,22−0,25% на протекание процессов структурообразования в микролегированных сталях, подвергаемых контролируемой прокатки, выражающееся повышение температуры начала распада аустенита и торможении собирательной рекристаллизации феррита, деформированного в двухфазной а+у-области, в результате чего в сталях типа 07Г2МФБ образуется структура с размерами ферритных зерен на 0,5−1 балл меньше, чем в сталях без добавок молибдена.
5. Разработана новая четырехстадийная схема контролируемой прокатки, обеспечивающая в листах получение требуемого уровня сопротивления хрупкому разрушению, ударной вязкости и прочности за счет формирования мелкодисперсной однородной структуры и кристаллографической текстуры в листахпредложенная схема предусматривает проведение первого этапа деформации в интервале температур 1000−980 °Свторого — при температурах 920−900 °Стретьего — в нижней части аустенитной области при температурах Агз+(20−40) °С, четвертого — в межкритическом интервале при 740−680 °С.
Практическая ценность и реализация работы. В результате проведенных в диссертационной работе исследований создан новый, четырехстадийный режим контролируемой прокатки, внедренный в промышленное производство на стане 3600 ОАО «МК «Азовсталь» для изготовления листов, предназначенных для газопроводных большого диаметра ответственного назначения. Разработаны и оформлены технологические инструкции для производства проката по четырехстадийному режиму. Изготовлена опытно-промышленная партия листов, размерами 21,6×2650×18 800 мм из стали 07Г2МФБ для спиральношовных труб диаметро1420 мм класса прочности К60, из которых на стане 2520 Волжского трубного завода произведены спиральношовные трубы, отвечающие требованиям спецификации требованиям ВНИИГАЗ и ОАО «Газпром» к трубам класса прочности К60 на 9,8 МПа. и.
Объектом исследований служили микролегированные ниобийсодержащие стали, производимые на «МК «Азовсталь» и используемые для изготовления электросварных труб большого диаметра класса прочности К52-К60,.
Предметом исследований служило установление взаимосвязи аустенитной и конечной структуры с режимами контролируемой прокатки для микролегированных сталей феррито-перлитного и феррито-бейнитного классов. В работе использовали современные металлофизические методы исследования структуры и кристаллографической текстуры металла с помощью оптической и растровой электронной микроскопий, рентгенографического метода.
Испытания механических свойств опытных сталей предусматривали оценку прочностных свойств и пластичности при статическом растяжении, ударной вязкости, сопротивления хрупкому разрушению, измерение микротвердости структурных составляющих.
Диссертация содержит шесть глав и основные выводы.
Первая глава представляет собой литературный обзор, в которой рассмотрено современное состояние вопроса о влиянии контролируемой прокатки на структурообразование низколегированных трубных сталей и обосновывается выбор направления исследования.
Вторая глава посвящена обоснованию выбора исследуемых сталей, и описанию методов лабораторных и промышленных исследований, проведенных автором при выполнении настоящей диссертационной работы.
В третьей главе изложены результаты изучения кинетики превращения горячедеформированного аустенита при непрерывном охлаждении для сталей 08Г1ФБ и 07Г2МФБ и дифференциальным термическим методом для шести микролегированных сталей определена температура распада аустенита в ферритной области (Аг3) после режима имитирующего черновую прокатку, применяемой на тол стол истовом стане 3600.
Анализ построенных термокинетических диаграмм в сочетании с исследованием микроструктуры показал, что молибденсодержащая сталь 07Г2МФБ относится к феррито-бейнитному классу, так как в широком диапазоне скоростей охлаждения ферритное и бейнитное превращения являются доминирующими. Перлитное превращение не наблюдалось даже при скорости охлаждения 0,5 °С/с. Сталь 08Г1ФБ характеризуется низкой устойчивостью аустенита к ферритному превращению, которое протекает даже при высокой скорости охлаждения 100 °С/с.
Для шести микролегированных сталей различного химического состава определены температуры начала полиморфного у->ос-превращения после режима, имитирующего предварительную стадию деформации подкатов, проводимую в промышленных условиях. На основании зафиксированных температур Агз определены рекомендуемые температуры начала деформации в чистовой клети для исследуемых сталей при проведении контролируемой прокатки на толстолистовом стане 3600 металлургического комбината «Азовсталь». Показано, понижающее влияние молибдена на температуру начала полиморфного превращения Агз.
В четвертой главе рассмотрены вопросы по влиянию предварительной стадии контролируемой прокатки на аустенитную структуру и конечную структуру микролегированных сталей. Показано, что аустенитное зерно перед началом полиморфного у-«а-превращения оказывает решающее влияние на дисперсность и однородность конечной структуры микролегированных сталей при проведении контролируемой прокатки. Из крупного аустенитного зерна формируется весьма крупное и неоднородное ферритное зерно. Напротив, из дисперсного аустенита образуется мелкое и однородное ферритное зерно.
Полученные в настоящей главе экспериментальные данные позволили сделать важное заключение по поводу формирования аустенитной структуры в подкатах после проведения предварительной стадии деформации, которую обычно в промышленных условиях проводят при высоких температурах 1020−950 °С. Вопреки широко распространенному мнению, при прокатке микролегированных ниобийсодержащих сталей в интервале температур 1000−950 °С и при медленном охлаждении подкатов до заданной температуры между черновой и чистовой стадиями контролируемой прокатки интенсивно протекает собирательная рекристаллизация горячедеформированного аустенита.
Проведенное изучение влияния температуры деформации в верхнем интервале у-области и длительности последеформационных, изотермических выдержек на аустенитную структуру трех сталей 08Г1ФБ, 07Г2Б и 07Г2МФБ показало, что при температурах > 950 °C во время паузы между проходами интенсивно протекают первичная и собирательная рекристаллизация аустенита. Установлено, что при снижении температуры деформации рекристаллизационные процессы имеют тенденцию к замедлению, что выражается в увеличении промежутка времени, после которого начинается первичная рекристаллизация аустенита.
Изучение аустенитной структуры при непрерывном охлаждении показало, что с понижением температуры деформации от 1000 до 900 °C размер аустенитного зерна уменьшался на 1−1,5 номера. Уменьшение аустенитного зерна способствовало повышению дисперсности и однородности конечной структуры исследуемых сталей.
На основании выявленных особенностей рекристаллизации аустенита микролегированных ниобийсодержащих сталей предложено деформацию в верхней части у-области при контролируемой прокатке в черновой клети проводить в два этапа. Вначале слябы прокатывать при температурах 1000−960 °С в верхней части аустенитной области, где интенсивно протекает статическая рекристаллизация горячедеформированного аустенита, затем подстуживание раскатов на рольганге до температуры 900−880 °С, далее завершающие 3−4 обжатия в области торможения собирательной рекристаллизации горячедеформированного аустенита.
Пятая глава посвящена изучению влияния окончательной стадии контролируемой прокатки на структурообразования микролегированных сталей. Полученные экспериментальные данные показывают, что наиболее мелкая и однородная зеренная структура в исследуемых сталях образуется из мелкого деформированного аустенитного зерна. Установлено, что для формирования в микролегированных сталях такой структуры пред началом полиморфного у-«а-превращением необходимо при предварительной стадии контролируемой прокатки в у-области проводить деформацию в области торможения рекристаллизации аустенита при температурах 900−880 °С и в нижней части аустенитной области, где рекристаллизация аустенита полностью подавлена при температурах на 20−40 выше температуры Агз.
Показано, что образование мелкого наклепанного аустенитного зерна перед полиморфным у-«а-превращением является необходимым условием, но не достаточным для обеспечения мелкозернистой конечной структуры листов после проведения контролируемой прокатки. Установлено, что деформация исследуемых сталей в двухфазной у+а-области в некоторых случаях приводит к заметному укрупнению ферритного зерна за счет протекания собирательной рекристаллизации наклепанного феррита. Установлено, что мелкое ферритное зерно, образующееся перед началом деформации в межкритическом интервале температур, рекристаллизуется в большей мере по сравнению с крупнозернистым ферритом. В микролегированных сталях с добавками молибдена выявлена тенденция к замедлению рекристаллизации феррита, деформированного в двухфазной у+а-области.
Показано, что в стали с повышенным содержанием ниобия 07Г2Б образуется более острая кристаллографическая текстура по сравнению со сталью 08Г1ФБ. Заметный вклад в формирование текстуры стали 08Г1ФБ внесли ориентировки, характерные для превращения рекристаллизованного аустенита в феррит. Напротив в стали 07Г2Б основными компонентами кристаллографической текстуры после завершения прокатки в аустенитной области являлись ориентировки закономерного у-«а-превращения. При завершении деформации в межкритическом интервале температур к этим ориентировкам добавлялись ориентировки плоской деформации а-фазы. Собирательная рекристаллизация не вызывала появление новых кристаллографических ориентировок в обеих сталях. Полученные экспериментальные данные показали, что формирование конечной микроструктуры и кристаллографической текстуры исследуемых сталей при проведении контролируемой прокатки является довольно сложным процессом. Наиболее важными из них являются температурные режимы предварительной и окончательной стадий контролируемой прокатки, химических состав стали, предопределяющий критическую точку Аг3 и сопротивление наклепанного феррита собирательной рекристаллизации. Для формирования после контролируемой прокатки в листах из низколегированных ниобийсодержащих сталей дисперсной и однородной наклепанной конечной структуры, необходимо деформацию в черновой клети заканчивать при температурах ~910−890 °С, а прокатку в чистовой клети начинать при температуре на 20−30 °С выше точки Агз и далее в межкритической у+а-области подкаты прокатывать так, чтобы подавить развитие собирательной рекристаллизации деформированного феррита.
В шестой главе представлены результаты промышленного опробования на стане 3600 ОАО «МК «Азовсталь» производства листов толщиной 21,6 мм из стали 07Г2МФБ, предназначенных для изготовления на Волжском трубном заводе спиральношовных труб диаметром 1420 мм класса прочности К60. В состоянии после контролируемой прокатки в опытных листах были получены механические свойства, которые полностью соответствовали заданным у л требованиям потребителя: ат=545−575 Н/мм — ств =620−675 Н/мм, 5=21−24%- ат/сгв=0,85−0,90- KCV.20= 156−245 Дж/см2- KCU.60= 171−281 Дж/см2- ИПГ.20 = 95 100%. Показано, что после четырехстадийной схемы контролируемой прокатки в листах из стали 07Г2МФБ наряду с образованием мелкозернистой однородной феррито-бейнитной структуры формируется однородная по толщине листа кристаллографическая текстура. Из опытных листов на Волжском трубном заводе изготовлены спиральношовные трубы диаметром 1420 мм, отвечающие требованиям спецификации к трубам класса прочности К60 на давление 100 атм.
Автор выражает глубокую благодарность и признательность научному руководителю, доктору технических наук Ю. И. Матросову. Диссертант благодарит научных сотрудников ЦНИИчермет им. И. П. Бардина Ю.Д. Морозова, Г. А. Филиппова, В. И. Изотова, Л. И. Эфрона, А. В. Назарова, Т. С. Кирееву, Н.В.
Колясникову, сотрудника кафедры «Термическая обработка металлов» ПГТУ Хестова В. М., а также фирму Niobium Products Company, Германия за содействие в проведении работы и высказанные ценные замечания при обсуждении ее результатов. Автор выражает признательность сотрудникам Центральной лаборатории «МК Азовсталь» за помощь в проведении экспериментов и исследований по диссертационной работе.
По представленной работе на защиту выносятся:
1. Термокинетические диаграммы распада при непрерывном охлаждении деформированного аустенита сталей 08Г1ФБ и 07Г2МФБ по режиму, имитирующему условия проведения контролируемой прокатки в промышленных условиях с завершением деформации в области нерекристаллизованного аустенита.
2. Результаты исследования влияния предварительной и окончательной стадий контролируемой прокатки на аустенитную и конечную структуру листов из микролегированных сталей.
3. Выявленные механизмы возникновения неоднородных разнозернистых структур после проведении контролируемой прокатки с завершением деформации в двухфазной у+а-области и разработанные технологические решения, направленные на повышение однородности и дисперсности листов из микролегированных сталей.
4. Установленная взаимосвязь режимов контролируемой прокатки с формированием кристаллографической текстуры микролегированных ниобийсодержащих трубных сталях.
5. Новый четырехстадийный режим контролируемой прокатки и результаты его опробования в промышленных условиях на стане 3600 ОАО «МК «Азовсталь» при изготовлении листов толщиной 21,6 мм из стали 07Г2МФБ для спиральношовных труб класса прочности К60 диаметром 1420 мм на давление 9,8 МПа.
Основные выводы.
1. Установлены особенности влияния различных вариантов температурно-деформационного воздействия в процессе горячей пластической деформации на взаимосвязь аустенитной и конечной структуры толстолистовых ниобийсодержащих трубных сталейразработан усовершенствованный режим контролируемой прокатки, обеспечивающий получение в листах из стали 07Г2МФБ показателей сопротивления хрупкому разрушению, величины ударной вязкости и прочности, соответствующих требованиям к сталям класса прочности К60 для спиральношовных труб диаметром 1420 мм.
2. Показано, что в опытных сталях в случае окончания предварительной стадии контролируемой прокатки при температурах > 950 °C помимо процессов первичной рекристаллизации протекает собирательная рекристаллизация аустенита, приводящая к формированию крупного зерна аустенита балла 6−7.
3. Установлена необходимость получения мелкого деформированного аустенитного зерна перед началом полиморфного у-«а-превращения для формирования дисперсной конечной структуры. Это достигается прокаткой металла в аустенитной области в интервалах температур 910−890 °С (область торможения собирательной рекристаллизации аустенита) и Агз+(20−40) °С (область отсутствия рекристаллизации аустенита).
4. Выявлено, что при деформации микролегированных сталей в верхней части у+а-области в интервале температур на 10+20 °С ниже Агз протекает собирательная рекристаллизация феррита, приводящая к укрупнению ферритного зерна (на 2−2,5 номера ГОСТ 5639) — показано, что для ее предотвращения необходимо исключать деформацию в окончательной стадии контролируемой прокатки в указанном интервале, проводя ее при температурах ниже 740 °C.
5. Установлено комплексное влияние добавок молибдена на структурообразование в процессе горячей пластической деформации микролегированных сталей, которое заключается: в расширении температурного интервала а-области, что выражается в повышении температуры начала полиморфного у—"а-превращениязамедлении рекристаллизации деформированного феррита при прокатке в двухфазной у+а-областиповышении устойчивости аустенита при непрерывном охлаждении к распаду в перлитной области, что приводит к подавлению перлитного превращения вплоть до скорости охлаждения 0,5 °С/с.
6. Разработан режим четырехстадийной контролируемой прокатки, обеспечивающий получение оптимальных структур в листах из микролегированных ниобийсодержащих сталей. Режим предусматривает проведение первого этапа в области статической рекристаллизации аустенита в интервале температур 1000−980 °Свторого — в зоне торможения рекристаллизации наклепанного аустенита при температурах 920−900 °Стретьего — в нижней части аустенитной области при температурах Аг3+(20−40) °Счетвертого — в межкритическом интервале в области торможения рекристаллизации деформированного феррита при 740−680 °С.
7. Показано, что после четырехстадийного режима контролируемой прокатки в листах из стали 07Г2МФБ в результате закономерного превращения деформированного аустенита при у-«а-превращении и при наклепе феррита в двухфазной у+а-области образуется однородная по толщине листа кристаллографическая текстура с основными ориентировками а-фазы {332}<113>, {554}<225>, {113}<110>, {112}<110>, {111}<112>, {111}<110>, {001}<110>. Ориентировка {332}<113> и близкий к ней текстурный компонент {554}<225>, обеспечивают одновременно высокий уровень прочности, ударной вязкости и сопротивления хрупкому разрушению.
8. По разработанному четырехстадийному режиму контролируемой прокатки проведено промышленное опробование на стане 3600 ОАО «МК «Азовсталь» производства листов толщиной 21,6 мм из стали 07Г2МФБ, предназначенных для изготовления на Волжском трубном заводе спиральношовных труб диаметром 1420 мм класса прочности К60- получены механические свойства, которые полностью соответствовали заданным требованиям потребителя: ат=545−575 Н/мм — сгв=620−675 Н/мм — 5=21−24%- ат/ав=0,85−0,90- KCV.20 = 156−245 Дж/см2- KCU.60 = 171−281 Дж/см2- ИПГ.20 = 95−100%. Из опытных листов на Волжском трубном заводе изготовлены спиральношовные трубы диаметром 1420 мм, отвечающие требованиям спецификации к трубам класса прочности К60 на давление 9,8 МПа.
Список литературы
- Металловедение и термическая обработка стали.: Т. 1.: Справочник. — 3-е изд. / под ред. Бернштейна М. Л., Рахштадта А. Г — М.: Металлургия, 1983. — 352 с.
- Бернштейн М.Л., Займовский В. А., Капуткина Л. М. Термомеханическая обработка стали. — М.: Металлургия, 1983. — 480 с.
- Lips E.M.N., van Zailen Н. Improved Hardening Technigne // Metal Progr.1954. V.66, № 2. — P. 103−107.
- Смирнов M.B., Соколков E.H., Садовский В. Д. Влияние пластической деформации в аустенитном состоянии на хрупкость при отпуске конструкционных легированных сталей. // ДАН СССР. — 1955. — Т. 103, № 4.с. 609−612.
- Бернштейн М.Л. Термомеханическая обработка металлов и сплавов. — М.: Металлургия, 1968. Т 1,2.
- Матросов Ю.И., Литвиненко Д. А., Голованенко С. А. Сталь для магистральных газопроводов — М.: Металлургия, 1989.— 288 с.
- Хайстеркамп Ф., Хулка К., Матросов Ю. И., Морозов Ю. Д., Эфрон Л. И., Столяров В. И., Чевская О. Н. Ниобийсодержащие низколегированные стали.— М.: «СП ИНТЕРМЕТ ИНЖИНИРИНГ», 1999. — 94 с.
- Морозов Ю.Д. Тенденции развития сталей для газопроводных труб большого диаметра // Прогрессивные листовые стали для газопроводных труб большого диаметра и металлоконструкций особого назначения / Сб. докладов.
- М.: Металлургиздат, 2004. — 120 е., ил. С. 28−33.
- Y. Morozov, L. Efron and S. Nasticch The main direction of development of pipe steels and large diameter pipe production in Russia // Proceedings of the international Pipeline Technology Conference, Vol. 4. 2004. P. 1649−1653.
- Носоченко A.O., Матросов Ю. И., Ганошенко И. В., Назаров А. В., Володарский В. В. Свойства бесперлитной трубной стали категории прочности К55-Х70 типа 0,3C-l, 5Mn-0,09Nb // Металлург. 2003. № 12. С. 30−33.
- Tshikawa N., Endo S., Shinmiya Т., Wada Т., Kondo J. High-grade linepipe for heavy sour environment // Proceedings of the international Pipeline Technology Conference, Volume 4. 2004. P. 1633−1648.
- Погоржельский В.И., Литвиненко Д. А., Матросов Ю. И., Иваницкий А. В. Контролируемая прокатка — М.: Металлургия, 1979. 184 с.
- Гладштейн Л.И., Литвиненко Д. А. Высокопрочная строительная сталь. — М.: Металлургия, 1972. — 240 с.
- Пикеринг Ф.Б. Физическое металловедение и разработка сталей. Пер. с англ. — М.: Металлургия, 1982. — 183 с.
- Эфрон Л.И., Литвиненко Д. А. Получение высокопрочных свариваемых сталей с бейнитной структурой с применением термодеформационной обработки // МиТОМ 1994. № 10. С. 28−33.
- Эфрон Л.И. и др. Разработка и промышленное опробование трубной стали повышенной прочности и хладостойкости с преимущественно бейнитной структурой // Сталь 2003. № 9. С. 83−87.
- Эфрон Л.И. и др. Разработка и промышленное опробование трубной стали повышенной прочности и хладостойкости с преимущественно бейнитной структурой // Сталь 2003. № 9. С. 83−87.
- Hulka К., Gray J. М., Heisterkamp F. High temperature thermomechanical processing of pipe-line steels // Proceedings of the International Symposium Niobium 2001 held in Orlando, Florida, USA. December 2−5,2001.
- Полухин П.И., Клименко B.M., Полухин В. П. и др. Прокатка толстых листов. — М.: Металлургия, 1984. — 288 с.
- Беняковский М.А., Богоявленский К. Н., Виткин А. И. и др. Технология прокатного производства: Справочник. В 2-х книгах. Кн. 2. — М.: Металлургия, 1991. — 423 с.
- Быков В.В., Франценюк И. В. Выбор режимов нагрева металла.
- М.: Металлургия, 1980. — 246 с.
- Потемкин В.К., Пешков В. А. Контролируемая прокатка. Термомеханическая обработка листов // Итоги науки и техники. Прокатное и волочильное производство. Т. 14, — М., 1986. С. 3−55.
- Морозов Ю.Д. и др. Повышение хладостойкости стали 09Г2С// Сталь. 1994. № 12. С. 54−59.
- Шабалов И.П., Морозов Ю. Д., Эфрон Л. И. Стали для труб и строительных конструкций с повышенными эксплуатационными свойствами.
- М. ЗАО «Металлургиздат», 2003. — 520 с.
- Погоржельский В.И., Чистяков Ю. И., Утевский Л. М. и др. Влияние температуры аустенитизации на структуру низколегированной стали после контролируемой прокатки //Изв. АН СССР. Металлы. 1980. № 5. С. 105−107.
- Матросов Ю.И., Филимонов В. Н. Структура и свойства стали 09Г2ФБ после контролируемой прокатки // Изв. вузов. Черная металлургия. 1981. № 1.С. 92−96.
- Pastrnak Z. Rizene valcovani pasu pro velkoprumerove trubky se svaren ve sroubovici// Hutnik. 1986. V. 36. № 1. P. 24−30.
- Tanaka Т., Funakoshi Т., Veda M. et. al. Microalloying'75. Proc. Int. Symp. Union Carbide Corp. New York. 1977. P. 399−408.
- Pastrnak Z., Wozniak J. Rizene valcovni mikrolegovnych oceli a moznosti aplikace v CS valcovani // Hutnicke aktuality. 1984. V. 25.
- Келлер M, Хилленбранд Х-Г, Клостер Г. и др. Магистральные стальные трубы для транспортировки ископаемых энергоносителей // Черные металлы. 2002. № 10. С.43−51. (34).
- Накасуги X., Матсуда X., Тамехиро X. Сверхнизкоуглеродистые бейнитные стали для трубопроводов. — В кн.: Стали для газопроводных труб и фитингов//Пер. с англ. — М.: Металлургия, 1985. С. 108−116.
- Массип А., Мейер Л. Толстый лист и горячекатаная полоса из бейнитных сталей с очень низким содержанием углерода // Черные металлы (Stahl und Eisen). 1978. № 19. С. 12−18.
- Sellars С.М., Whiteman J.A. Recrystallization and Grain Growth in Hot Rolling//Metal Science. 1979. № 13. P. 187−194.
- Yada H. Prediction of Microstructural Changes and Mechanical Properties in Hot Strip Rolling. Proceeding of the International Symposium on Accelerated Cooling of Rolled Steel. Winnipeg. Canada. 1988. P. 105−119.
- Roberts W., Sandberg A., Siweski Т., Werlefors T. Prediction of Microstructure Development during Recristallization Hot Rolling on Ti-V-steels. Proceeding Int. Conf. of Technology and Applications of HSLA Steels. 1983. P. 6784.
- Матросов Ю.И. Влияние условий контролируемой прокатки на структурные превращения и свойства малоперлитных сталей // Сталь. 1985. № 2. С. 68−72.
- Palmiere Е. J. Suppression of Recrystallization during the Hot Deformation of Microalloyed Austenite. PhD Thesis, University of Pittsburgh, 1991.
- Palmiere E. J. et al. The Influence of Niobium Supersaturation in
- Austenite on The Static Recrystallization Behavior of Low Carbon Microalloyed Steels // Metall. Trans., 27A (4) (1996), 951.
- Kwon O. and DeArdo A. J. Interactions Between Recrystallization and Precipitation in Hot-Deformed Microalloyed Steels // Acta Met., 39 (1991), 529.
- Cuddy L. J. The Effect of Microalloy Concentration on the Recrystallization of Austenite During Hot Deformation // Thermomechanical Processing of Microalloyed Austenite. Warrendale, PA: TMS-AIME, 1984. P. 129 140.
- Kwon O., DeArdo A. J. Interactions Between Recrystallization and Precipitation in Hot-Deformed Microalloyed Steels // Acta Met., 39, 1991, 529.
- Palmiere E. J. et al., Suppression of Static Recrystallization in Microalloyed Steels by Strain-Induced Precipitation // Proc. Low Carbon Steels for the Nineties, Warrendale, PA: TMS-AIME, 1993, 121.
- Sellars C.M., Witerman J.A. // Metal Science. 1979. № 3−4. P. 187−194.
- Boretto F., Borbasa R., Yue, S. Jonas T.J. Thermomechanical Processing of Steels and Other Materials, Isis, Tokyo, 1988.
- Tegart W.J., Gittins A. The Hot Deformation of Austenite. Conf. of Hot Deformation of Austenite. London. 1977. P. 1−46.
- Погоржельский В.И., Литвиненко Д. А., Матросов Ю. И., Иваницкий А. В. Контролируемая прокатка. — М.: Металлургия, 1979. — 184 с.
- Khlestov V.M., Konopleva Е.А., McQueen H.J. Effect of deformation in controlled rolling on ferrite nucleation // Canadian metallurgical Quarterly. 200l.V. 40. N2. P. 221−233.
- Yang H. Bae, Jae Sang Lee, Jong-Kyo Choi at all. Effect of austenite/Ferrite Phase Transformation of HSLA Steel // Materials Transactions, Vol. 45, No. 1 (2004) pp. 137−142.
- Хулка К., Петере П., Хайстеркамп Ф. Тенденции развития сталей для труб большого диаметра // Сталь. 1997 № 10. С. 62−67.
- Hillenbrand Н., Gras М., Kalwa С. Development and production of high strength pipeline steels // Proceedings of the International Symposium Niobium 2001 held in Orlando, Florida, USA. December 2−5, 2001. P. 543−569.
- Hulka К., Bordignon P., Malcolm G. Experience with low carbon HSLA steel containing 0.06 to 0.10 percent niobium. Niobium Technical Report. Summary of international seminar Araxa', October 2003. P.27.
- DeArdo J. Fundamental metallurgy of niobium in steel // Proceedings of the International Symposium Niobium 2001 held in Orlando, Florida, USA. December 2−5, 2001. P. 571−586.
- Ouchi С et al. Microstructural Changes of Austenite During Hot Rolling and Their Effects on Transformation Kinetics // The Hot Deformation of Austenite, ed. John B. Balance, New York, NY: AIME 1977, 316−340.
- Hansen S. et al. Niobium Carbonitride Precipitation and Austenite Recrystallization in Hot-Rolled Microalloyed Steels // Metall. Trans. A 11A (3), 1980, P. 387−402.
- Brown E.L., DeArdo A. J., Bucher J.H. The Microstructure of Hot Rolled High-Strength Low Alloy Steel // The Hot Deformation of Austenite, ed. John B. Balance, New York, NY: AIME, 1977, P. 250−285.
- Davenport A.T., Miner R. E. and Kot R. A. The Reciystallization of Austenite During the Hot Rolling of a Nb-Bearing HSLA Steel // The Hot Deformation of Austenite, ed. John B. Balance, New York, NY: TMS-AIME, 1976, P. 186−203.
- Jonas J.J., Weiss I. Effect of Precipitation on Recrystallization in Microalloyed Steels // Metal Science. 13 (1979), P. 238−245.
- Bodanar R. L., Adebanjo R. O., and Hansen S. S. 37th MWSP Conf. Proc., ISS, vol. XXXIII, 1996, P.743−757.
- Barbosa R., et al. Conf. Proc. Processing, Microstructure and Properties of HSLA Steels, 1988, Ed. A.J. DeArdo, (TMS-AIME), P. 51−61.
- Boratto F., et al. Conf. Proc. THERMEC-88, 1988, P. 383−390.
- Хлестов B.M., Фролова З. В. Влияние параметров контролируемой прокатки на аустенитную структуру стали 10Г2ФБ // Изв. вуз. Черная металлургия. 1989. № 4 С. 68−71.
- Хлестов В.М., Мурашкин А. В., Фролова З. В., Рубец А. С. Влияние черновой прокатки на структуру штрипсовой стали Х70 // Вестник ПГТУ. 2006 № 14. С. 6−12.
- Эфрон Л.И. Формирование структуры и механических свойств конструкционных сталей при термомеханической обработке в потоке прокатного стана//Сталь. 1995. № 8. С. 57−64.
- Sekine Н., Maruyama Т., Fundamental Research on Manufacturing of High-Tough, High Tension Steel by Controlled Rolling // Seitetsu Kenkyu, 289, 1976, P. 43−61.
- Sekine H. et al. Grain Refinement Through Hot Rolling and Cooling After Rolling // Proc. Thermomechanical Processing of Microalloyed Austenite, Warrendale, PA: TMS-AIME, 1984. P.141.
- Эфрон Л.И., Мельник Н. П., Литвиненко Д. А. Высокотемпературная контролируемая прокатка низколегированной стали повышенной прочности // Сталь. 1992. № 3. С. 63−65.
- Yang-Zeng Z, De Ardo A.J. et al Achieving grain refinement through recrystallization controlled rolling and controlled cooling in V-Ti-N microalloyed steels. // Int. Conf. on Technology and Application of HSLA Steels. 3−6 Oct. 1983. P. 85−94.
- Siweski T. Evolution of microstructure during recrystallization hot rolling. Microalloyed vanadium steels. Proceeding of Symposium. Cracow. 1990. P. 63−78.
- Underwood E. E. Quantitative stereology // Addison-Wesley, ed., USA, 1970.
- Ouchi C., Okita Т., Yarnamoto S. The Effect of Interrupted Accelerated Cooling after Controlled Rolling on the Mechanical Properties of the Steel // Trans. ISIJ, 22, 1982. P. 608−616.
- Tamehiro H., Yamada N., Matsuda H. Effect of the Thermo-Mechanical Control Process on the Properties of HSLA Steel // Tram. ISIJ. 25, 1985. P. 54−61.
- Kozasu I. Recent Development of Microalloyed Steel Plate // Int. Conf. on Technology and Appl. of HSLA Steels, Philadelphia, 1983. P. 593−607.
- Zajac S., Siwecki Т., Hutchinson В., Attlegard M. Recrystallization Controlled Rolling and Accelerated Cooling as the Optimum Processing Route for High Strength and Toughness in V-Ti-N Steels // Met. Trans., 22A, 1991. P. 2681−1693.
- De Ardo A.J. Proceeding of the Int. Symp. on Accelerated Cooling of Rolled Steel. Winnipeg. Canada. 1988. P. 3−27.
- Ouchi C, Tanaka J., Kozasu I., Tsukada K. Micon'78. ASTM. Philadelphia (PA), 1979. P. 105−125.
- Литвиненко Д.А., Эфрон Л. И. // Сталь. 1994. № 1. С. 53−58.
- Lorenz К., Hof W.M., Hulka К. et al. //Stahl und Eisen. 1981. Bd. 101. P.593−600.
- Kozasu I. Accelerated Cooling of Steel. 1986, TMS-AIME, Warrendale (PA). P. 15.
- Reed-Hill R.F. Physycal Metallurgy Principles, 1973, Van Nostrand, NY.
- Cuddy L.J. Accelerated Cooling of Steel. TMS-AIME. Warrendale (PA), 1986. P. 235−243.
- Hot W.M., Graef M.K., Hillenbrand H.G. et al. HSLA Steels Metallurgy and Applications. ASM Int. USA, 1986. P. 467−474.
- Morgan E. R., Dancy Т. E., Korchynski M. // AISI Yearbook. 1965. V. 53. P. 921−929.
- Ouchi C., Tanaka J., Kozasu I., Tsukada K. // Micon'78: ASTM. Philadelphia (PA), 1979. P. 105−125.
- Литвиненко Д.А. Влияние легирования и режимов контролируемой прокатки на свойства сталей для газопроводных труб // Сталь, 1984, № 1. С. 68−73.
- Матросов Ю.И. Влияние условий контролируемой прокатки на структурные превращения и свойства малоперлитных сталей // Сталь, 1985, № 2. С. 68−72.
- Большаков В.И., Погребная Н. Э. Повышение качества и надежности строительных сталей в результате субструктурного упрочнения // МиТОМ, 1985, № 8. С. 42−46.
- Kim G., Kwon О.: Proc. Thermec 88, ed. by Tamura I., ISIJ, Tokyo, 1988, P. 668−675.
- Vanderschueren D., Kestens L., et al: Mater. Sci and Technology, Vol. 6, 1990, P. 1247−1259.
- Bodin A., Sietsma J., et al: Mater. Trans. A Vol. 33, No 6, 2002, P. 1589- 1603.
- Bodin A., Sietsma J. et al: Mater. Charact., Vol. 47, 2002, P. 1589 1603.
- В leek W., Herzig C., Lorenz U.: Steel Research, Vol. 72, No 10, 2001, P. 406−410.
- Petrov R., Kestens L.: ISJI International, Vol.43, No 3, 2003, P. 378−385.
- Petrov R., Kestens L., and Houbaert Y.: Proc. of COM, 2003, Vancouver, CA, 2003, P. 315−329.
- Schmickl A., Yu D., Killmore C., Langley D., Chandra T. Prediction of ferrite grain size after warm deformation of low carbon steel // ISIJ International, Vol. 36. 1996, No. 10. P. 1279−1285.
- Okaguchi S., Hashimoto Т., Ohtani H. Effect of Nb V and Ti on Transformation Behavior of HSLA Steel in Accelerated Cooling // Thermec '88, vol. 1, Tokyo, Japan: Iron and Steel Institute of Japan, 1988, P. 330−336.
- Tamehiro H. et al. Properties of Large Diameter Line Pipe Steel Produced by Accelerated Cooling After Controlled Rolling // Accelerated Cooling of Steel, ed. Southwick P.D., (Warrendale, PA: TMS-AIME, 1986), P. 401−413.
- Fazackerley W.J., Bordignon P., Hulka K., Siciliano F. Overview of development and commercialization of XI20 ultra-high strength uoe linepipe // International Symposium on Microalloyed Steels for the Oil and Gas Industry. Brazil. 2006. P. 281−293.
- DeArdo A. J., Marraccini R., Hua M. J., Garcia С. I. Producing High Quality Niobium-Bearing Steels Using the CSP Process at Nucor Steel Berkeley // International Symposium on Microalloyed Steels for the Oil and Gas Industry. Brazil. 2006. P. 181−195.
- Матросов Ю. И, Ганошенко И. В., Багмет О. А., Иванова Т. Ю. Возможности повышения предела текучести листов из высокопрочных трубных сталей Х70 и Х80 // Сталь. 2005. № 2. С. 74−78.
- Матросов Ю.И., Носоченко А. О., Володарский В. В., Багмет О. А. Создание высоконадежной трубной стали 08Г1Б для газопроводных труб категории прочности К52 // Металлы и литьё Украины. 2001. № 12. С.6−9.
- Багмет О.А., Володарский В. В., Носоченко А. О., Матросов Ю. И. Опробование производства высокопрочной толстолистовой стали для сосудов высокого давления // Сталь. 2005. № 12. С. 65−70.
- Белый А.П., Матросов Ю. И., Ганошенко И. В., Носоченко О. В., Багмет О. А. Толстолистовая сталь для газопроводных труб категории прочности Х80 // Сталь. 2006. № 5. С. 106−110.
- Горелик C.C., Скаков Ю. А., Расторгуев JI.H. Рентгенографический и электронно-оптический анализ: Учеб. Пособие для вузов. — 4-е изд. Доп. И перераб. — М.: МИСИС, 2002. — 360 с.
- Бородкина М.М., Спектор Э. Н. Рентгенографический анализ текстуры металлов и сплавов: «Металлургия», 1981. — 272 с.
- Хлестов В.М., Дорожко Г. К. Превращения деформированного аустенита в стали. Монография. — Мариуполь: Издательство ПГТУ, 2002. 407 с.
- Черепин В.Т. Экспериментальная техника в физическом металловедении. — К.: Техника, 1969. 280 с.
- Багмет О. А., Емельянов В. В., Ефимов С. К. Практическое использование системы анализа изображения SIAMS 600 в лаборатории металловедения МК «Азовсталь» // Материалы школы-семинара «Цифровая микроскопия» Екатеринбург, 2001. Ч. 1. С. 75−79.
- Багмет О. А., Носоченко А. О. Использование анализатора изображения SIAMS 600 для определения структурных составляющих в штрипсовых сталях // Материалы школы-семинара «Цифровая микроскопия», Екатеринбург, 2002. Ч. 2. С. 25−27.
- Багмет О.А., Ганошенко И. В., Носоченко А. О. Исследование кинетики превращения горячедеформированного аустенита низколегированных сталей 07Г2МФБ и 08Г1ФБ // Материалы международной научно-технической конференции. — Мариуполь: ПГТУ. 2007.
- Ghasemi Banadkouki S.S., Dunne D.P. Formation of Ferritic Products during Continuous Cooling of a Cu-bearing HSLA Steel // ISIJ International, Vol. 46 (2006), No. 5, P. 759−768.
- Krauss G., Steven W. Ferritic Microstructures in Continuously Cooled Low- and Ultralow-carbon Steels // ISIJ International. Vol. 35 (1995). No.8, P. 937−945.
- Багмет О.А., Заиченко Г. Н. Исследование кинетики распада аустенита малоуглеродистой низколегированной стали 06Г2МФБ // Тезисы докладов международной научно-технической конференции молодых специалистов «Азовсталь — 2005». — Мариуполь. 2005. С. 99.
- Мозберг Р.К. Материаловедение: Учебн. Пособие. — 2-е перераб.
- М.: Высш. шк., 1991. —448 с.
- Tamura I., et al. // Thermemechanical Processing of High Strength Low Alloy Steels. Butterworths, 1988, P. 162.
- Багмет О.А., Носоченко A.O., Ганошенко И. В. Влияние контролируемой прокатки на формирование структуры и текстуры в микролегированной C-Mn-Nb-V-стали // Материалы 13-й международной конференции по металлографии. — Словакия. 2007. С. 342−351.
- Khlestov V.M., Konopleva E.V., McQueen H.J. Effect of deformation in controlled rolling of ferrite nucleation // Canadian Metallurgical Quarterly, Vol. 40. № 2.2002. P. 221−234.
- Матросов Ю.И., Багмет О. А., Носоченко A.O. Развитие современных толстолистовых сталей для трубопроводов // Материалы международной конференции «Thermec 2006». — Ванкувер. Канада. 2006.
- Матросов М.Ю., Кичкина А. А., Ефимов А. А., Эфрон Л. И., Багмет О. А. Имитация процессов структурообразования в трубных сталях приконтролируемой прокатке с ускоренным охлаждением // М. Металлург. № 7. 2007 г. с. 52−58.
- Носоченко А.О., Багмет О. А., Мельник С. Г. Водородное разрушение и сероводородное растрескивание непрерывнолитых трубных сталей // Химическое и нефтегазовое машиностроение. 2004. № 8. С. 48−50.
- Матросов Ю.И., Носоченко А. О., Емельянов В. В., Кирсанова Г. Б., Багмет О. А. Исследование центральной неоднородности в непрерывнолитых трубных сталях//Сталь. 2002. № 3. С. 107−110.