Структура и свойства валковых сталей с 5% хрома и выбор рациональных режимов их термообработки
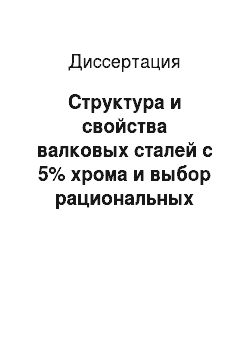
Рабочие валки как инструмент станов холодной прокатки оказывают решающее воздействие на качество и стоимость продукции. Фирма Гонтерманн-Пайперс более 100 лет занимает ведущее место в мире по изготовлению прокатных валков разной модификации. С конца 80-х годов на этой фирме основным материалом рабочих и опорных валков для толстолистовых и широкополосных станов горячей и холодной прокатки является… Читать ещё >
Содержание
- 1. ВЛИЯНИЕ ЛЕГИРОВАНИЯ И СПОСОБОВ УПРОЧНЕНИЯ НА СТРУКТУРНОЕ СОСТОЯНИЕ И СВОЙСТВА СТАЛЕЙ ДЛЯ ВАЖОВ ХОЛОДНОЙ ПРОКАТКИ (АНАЛИТИЧЕСКИЙ ОБЗОР)
- 1. 1. Требования, предъявляемые к валкам холодной прокатки
- 1. 2. Влияние легирующих элементов на свойства валков холодной прокатки
- 1. 3. Основные этапы технологии изготовления валков холодной прокатки
- 1. 3. 1. Ковка заготовок для валков холодной прокатки
- 1. 3. 2. Режимы термической обработки используемые при изготовлении валков холодной прокатки
- 1. 3. 2. 1. Предварительная термическая обработка
- 1. 3. 2. 2. Окончательная термическая обработка
- 1. 4. Пути повышения качества валков холодной прокатки
- 1. 5. Постановка задачи исследования
- 2. 1. Выбор материалов
- 2. 2. Методика исследования
- 3. 1. Экспериментальное и аналитическое определение критических точек исследуемых сталей
- 3. 2. Температура начала мартенситного превращения
- 3. 3. Распад переохлажденного аустенита в изотермических условиях
- 3. 4. Структурные диаграммы исследуемых сталей
- 3. 5. Карбидная фаза в исследуемых сталях
- 3. 6. Прокаливаемость исследуемых сталей
- 3. 7. Выводы по главе
- 4. 1. Количество остаточного аустенита исследуемых сталей
- 4. 2. Рост аустенитного зерна
- 4. 3. Структура исследуемых сталей
- 4. 4. Твердость после закалки
- 4. 5. Износостойкость сталей 9Х5МФС и 65Х5МФС
- 4. 6. Выводы по главе
- 5. 1. Сопротивление разупрочнению при отпуске исследуемых сталей
- 5. 2. Резистометрическое исследование
- 5. 3. Влияние режимов низкого отпуска на коэрцитивную силу 112 5.4 Влияние режимов низкого отпуска на статическую трещиностойкость
- 5. 5. Влияние температуры и времени отпуска на количество остаточного аустенита
- 5. 6. Выводы по главе
Структура и свойства валковых сталей с 5% хрома и выбор рациональных режимов их термообработки (реферат, курсовая, диплом, контрольная)
Совершенствование технологических процессов в современной металлургии определяет рост эффективности производства: повышение производительности труда, экономию материальных и энергетических ресурсов, а также качество продукции. Постоянно повышаются требования к уровню конструктивной прочности материалов, используемых в прокатном оборудовании, наиболее ответственными и нагруженными деталями которого являются валки.
Все изготовленные из стали изделия в процессе их получения и эксплуатации подвергаются воздействию многократно изменяющихся температур, с этим связаны изменения свойств, определяемые структурным состоянием материала. Имеющийся опыт и научное обоснование технологии термической обработки позволяют на отдельных стадиях производства во все возрастающем масштабе использовать изменения температуры для целенаправленного влияния на технологические и эксплутационные свойства материала [1−3]. Это означает, что области использования термической обработки быстро расширяются, а само понятие должно охватывать все термические процессы, целью которых является изменение свойств материала.
Конструкционные свойства валков связаны, в свою очередь, со свойствами материала. Статическая и динамическая прочность, сопротивление хрупкому разрушению, задирои износостойкость, сопротивление усталостному разрушению, физические, коррозионные и прочие свойства материала принадлежат к числу основных факторов, определяющих надёжность и долговечность.
Для целенаправленного создания сталей с требуемыми свойствами необходимо овладеть умением формировать заданную структуру путем подбора химического состава, а также последующей термической обработки.
Для более полной реализации возможностей легирования и термической обработки необходимо детальное изучение особенностей фазовых превращений с целью разработки аналитического описания оптимальных технологических процессов.
Рабочие валки как инструмент станов холодной прокатки оказывают решающее воздействие на качество и стоимость продукции. Фирма Гонтерманн-Пайперс более 100 лет занимает ведущее место в мире по изготовлению прокатных валков разной модификации. С конца 80-х годов на этой фирме основным материалом рабочих и опорных валков для толстолистовых и широкополосных станов горячей и холодной прокатки является высокохромистое литьё. ОМЗ «Спецсталь» и ОАО «Уралмаш» обеспечивают больше половины потребностей металлургических предприятий России в кованых валках. Это такие крупные предприятия, как Магнитогорский, Нижнетагильский, Новолипецкий металлургические комбинаты, Северсталь, Ашинский металлургический завод. В последние годы новыми заказчиками стали Jindal Steel Power Ltd., Lloyds Steel Industrials., Ispat Nova Hut AS. Так как возрастающие требования к интенсивности работы станов определяют необходимость разработки эффективных материалов рабочих валков, то в последние годы на ОМЗ «Спецсталь» и ОАО «Уралмаш» начали выпуск высокохромистых кованых валков холодной прокатки. Одной из основных причин возникновения дефектов продукции является неправильный выбор термической обработки, а также температуры и времени аустенитизации и отпуска. Поэтому разработка технологии термической обработки сталей с повышенным содержанием хрома является актуальной.
В связи со сказанным целью настоящего исследования явилось комплексное решение задачи научно обоснованного выбора режимов термической обработки сталей с содержанием хрома 5% для валков холодной прокатки.
Научная новизна.
1. Определены основные закономерности фазовых и структурных превращений, протекающих в новом классе валковых сталей повышенной прокаливаемости с 5% хрома, в процессе всего цикла термической обработки.
2. Впервые для данных сталей определены кинетические особенности распада переохлажденного аустенита в изотермических условиях: построены изотермические диаграммы распада аустенита, определены критические точки. Для изучаемых сталей показано влияние температуры аустенитизации на устойчивость переохлажденного аустенита.
3. В широком диапазоне температур аустенитизации проведены качественные и количественные исследования остаточного аустенита. Обнаружено, что при закалке в температурном интервале аустенитизации выше 1150 °C, на рост кристаллов мартенсита оказывает влияние размер аустенитного зерна, что приводит к значительному снижению количества остаточного аустенита в структуре.
4. При различных температурно-временных условиях низкого отпуска впервые получены данные по статической трещиностойкости для исследуемых сталей валков холодной прокатки.
5. Установлено, что температура закалки оказывает неоднозначное влияние на абразивную износостойкость валковых сталей с 5% хрома, с повышением температуры закалки (до определенных значений) износостойкость растёт, что связано как с увеличением количества углерода в мартенсите и повышением его твердости, так и с увеличением количества остаточного аустенита, претерпевающего мартенситное превращение при деформации. При дальнейшем повышении температуры закалки стабильность и количество остаточного аустенита повышаются, что приводит к снижению износостойкости.
Практическая значимость.
1. На основании комплексного исследования структуры и свойствтвердости, количества остаточного аустенита, прокаливаемости, характера структуры и размера зерен, физических свойств и статической трещиностойкости — предложены режимы окончательной термической обработки для валков холодной прокатки из сталей 65X5СМФ и 9X5СМФ, изготавливаемых в условиях ОАО «УралмашСпецсталь».
2. По проведенным исследованиям разработаны рекомендации по корректировке технологических инструкций № 25 050.00066, 25 050.00097, 25 050.00104 термической обработки валков холодной прокатки на ОАО «УралмашСпецсталь».
3. Результаты диссертационной работы используются в учебном процессе для практических занятий по курсу «Термическая и химико-термическая обработка сталей и сплавов», «Специальные стали и сплавы» для студентов специальности 150 501.
На защиту выносятся следующие основные положения и результаты:
1. Анализ особенностей фазовых превращений при нагреве и охлаждении исследуемых сталей.
2. Влияние температуры аустенитизации на структуру и свойства сталей 9Х5МФС и 65Х5МФС.
3. Результаты влияния различных температурно-временных условий низкого отпуска на структуру и свойства сталей с 5% хрома для рабочих валков холодной прокатки.
Апробация работы. Материалы диссертации были представлены и обсуждались на конференциях, семинарах и симпозиумах: XVII Уральской школе металловедов — термистов (Киров, 2004 г.) — IV, V, VI Уральской школесеминаре металловедов — молодых ученых (Екатеринбург, 2002, 2003, 2004 г.) — 9 международной конференции «Наука. Технологии. Инновации» (Новосибирск, 2005 г.) — XVIII Уральской школе металловедов — термистов «Актуальные проблемы металловедения сталей и сплавов» (Тольятти, 2006 г.) — VII Уральской школе — семинаре металловедов — молодых ученых (Екатеринбург, 2006 г.), на IV, V, VI, VII, VIII, IX отчетной научной конференции молодых ученых ГОУ ВПО «УГТУ-УПИ», 2003, 2004, 2005 гг., International Conference on Microalloyed Steels, Emerging Technologies And Applications, Kolkata, India, 2007.
Публикации;
По результатам диссертационной работы опубликовано 16 печатных работ, из них 1 статья в ведущих рецензируемых журналах, рекомендованных ВАК для опубликования результатов диссертационных работ, 9 публикации — в сборниках трудов российских и международных конференций, 6 публикации — в сборнике научных трудов ГОУ ВПО УГТУ-УПИ.
Структура диссертации:
Диссертация состоит из введения, шести глав, заключения, списка литературы, включающего 115 наименований. Диссертация содержит 160 страниц основного текста, в том числе 59 рисунков и 8 таблиц.
5.6. Выводы по главе.
1. Стали с 5% хрома обладают высокой устойчивостью к разупрочнению при низком отпуске.
2. Впервые применена методика определения статической трещиностойкости для сталей с повышенным содержанием хрома для валков холодной прокатки после окончательной термической обработки.
3. Показано, что температурно-временные параметры низкого отпуска не оказывают существенного влияния на статическую трещиностойкость.
4. Данные полученные в результате фрактографических исследований показали, что характер разрушения после закалки и низкого отпускаквазискол.
5. При низких температурах нагрева под закалку после низкого отпуска на фрактограммах видны нерастворенные карбиды.
6. Магнитометрические исследования показали, что в процессе исследуемых температур отпуска количество остаточного аустенита не изменяется.
7. Исследование коэрцетивной силы и резистометрии показали, что на начальной стадии отпуска происходит выделение мелкодисперсных фаз, когерентно связанных с матицей.
6. РЕКОМЕНДАЦИИ ПО ИЗМЕНЕНИЮ ТЕХНОЛОГИИ ТЕРМИЧЕСКОЙ ОБРАБОТКИ ВАЛКОВ ХОЛОДНОЙ ПРОКАТКИ С.
5% ХРОМА.
Результаты проведенных исследований использованы для оптимизации технологии термической обработки валков холодной прокатки с повышенным содержанием хрома в условиях ОАО «УралмашСпецсталь».
За основу взяты технологические инструкции — № 25 050.00066 «Термическая обработка рабочих и опорных валков с индукционным нагревом токами промышленной частоты», № 25 050.00097 «Термическая обработка рабочих валков холодной прокатки с индукционным нагревом токами промышленной частоты», и № 25 050.00104 «Низкотемпературный отпуск рабочих валков холодной прокатки после закалки токами промышленной частоты». Инструкции приведены частично. Изменения распространяются на закалку с индукционным нагревом токами промышленной частоты (тпч) и отпуск рабочих валков из сталей марок 9Х5МФС и 65Х5МФС с диаметром бочки от 500 — 503 мм и 600 — 615 мм.
6.1. Закалка рабочих и опорных валков с индукционным нагревом токами промышленной частоты.
Технологическая инструкция № 25 050.00066 распространяется на закалку с индукционным нагревом токами промышленной частоты (тпч), и отпуск рабочих и опорных валков листовых станов из сталей марок 9Х, 9X2, 9Х2МФ, 9Х2МФШ, 9ХФ, 75ХМ, 8Х2СГФ, 75ХМФ с диаметром бочки от 180 мм до 1600 мм, а также роликов прокатного оборудования, которые изготавливаются по технологии валков холодной прокатки.
1. Основные положения.
1.1. Закалка валков массой до 8 т. с диаметром бочки от 180 мм. до 830 мм. при длине закаливаемой поверхности до 2800 мм. и общей длине до 4000 мм. выполняется на установке ТПЧ-700М.
На установке ТПЧ-2 закаливаются валки массой до 60 т. с диаметром бочки от 831 мм. до 1600 мм. при длине закаливаемой поверхности до 5000 мм. и общей длине до 6000 мм. при закалке в центрах и до 8000 мм. — в центре и люнете.
1.2 Закалка с нагревом тпч производится непрерывно-последовательным методом при вращении валка со скоростью не менее 10 об/мин с использованием как одноили двухфазных индукторов с П-образными магнитопроводами, так и трехфазных секторных и кольцевых индукторов с Ш-образнымн магнитопроводами.
1.3 До закалки тпч валки должны быть подвергнуты предварительной термообработке в соответствии с инструкциями 25 050.00059 и 25 050.00079.
1.4. Настоящая технологическая инструкция предусматривает два способа закалки валков: для рабочих валков, работающих при повышенных контактных нагрузках — с нагревом нейтральной зоны валков до температуры 600−650°С и охлаждением при закалке одновременно наружной поверхности бочки и поверхности осевого канала (закалка с внутренним охлаждением), для прочих рабочих валков и всех опорных валков, а также роликов с прогревом центральной зоны до температуры не выше 450 °C и с охлаждением при закалке только наружной поверхности бочки (закалка без внутреннего охлаждения).
1.5 Руководствуясь настоящей инструкцией, технолог ОГМет на значает конкретные режимы закалки и отпуска в технологической карте термической обработки (КТО) и передает её в цех.
1.6 Закалка валков с нагревом тпч согласно технологической карте и настоящей инструкции производится под руководством бригадира участка. В случае необходимости уточнения режима закалка производится под наблюдением технолога ОГМет, что оговаривается в КТО.
1.7 При установке валков на станок, снятии их со станка и при работе на установках необходимо выполнять все правила эксплуатации и техники безопасности, изложенные в «Инструкции по эксплуатации и технике безопасности при работе на установках ТПЧ-1 и ТПЧ-2» .
1.8 При выполнении режимов термической обработки необходимо руководствоваться следующим:
1) температура в печи контролируется печными термопарами ТХА по ГОСТ 50 431–92 (диапазон измеряемых температур при длительном применении от 0 до 1000°С) с автоматической записью показаний на ленте потенциометра класса не ниже 0,5 по ГОСТ 7164–78,.
2) температуру поверхности валков до 800 °C измерять термопарой ТХК по ГОСТ 50 431–92 (допускаемый предел измерений при кратковременном применении 800 °С) выше 800 °C — пирометром визуальным ПРОМИНЬ по ГОСТ 8335–81 (пределы измерений 800−1400 °С.
3) температуру воды и масла измерять термопарой ТХК по ГОСТ 50 431–92 (диапазон измеряемых температур от 0 до 600°С) с автоматической записью показаний на ленте потенциометра класса не ниже 1,0 по ГОСТ 7164–78 и термометром техническим по ГОСТ 2823–73 (диапазон измеряемых температур от 0 до 100 °С),.
4)расход воды при закалке контролируется дифференциальными расходомерами типа КСД-3 по ГОСТ 25 668–83,.
5)время при нагреве и охлаждении определяется при помощи приборов для измерения времени (часы наручные — ГОСТ 12 932–67, ГОСТ 23 350–83Е, часы настенные — ГОСТ 703–76Е, ГОСТ 23 874–79Е.
2. Требования к закалочным установкам и валкам.
2.1. Закалочная установка должна обеспечивать заданную по технологии скорость перемещения индуктора в пределах от 0,2 до 5,0 мм/с с точностью ±0,1 мм/с, биение поверхности бочки валка не более 3 мм. Все измерительные приборы, которыми оборудованы установки, должны быть исправны и своевременно проверены.
2.2 При ремонте индукторов и спрейеров не допускается изменение размеров, которые входят в расчетные формулы разметки, а также размеров, влияющих на электрические параметры индукторов.
2.3 Валки, поступающие на закалку, должны соответствовать требованиям чертежа, и технологическим указаниям УМет. Не допускаются на закаливаемой поверхности зарезы, грубые риски, черновины, забоины, вмятины, местные зачистки. Способ чалки и транспортировки указывается в КТО.
2.4 Валки, принявшие при перевозке низкую температуру (ниже О °С). должны быть выдержаны перед закалкой в течение 10+50 часов в зависимости от диаметра до достижения бочкой валка температуры в цехе.
3. Подготовка и выполнение закалки.
3.1 Перед закалкой валки должны быть осмотрены технологом и контролером УТК. Валки должны соответствовать требованиям чертежа и требованиям, указанным в пунктах 2.3 и 2.4 настоящей инструкции.
3.2 Нагрев и закалка осуществляется непрерывно-последовательным методом при движении индуктора вверх за один (без подогревов индуктором) или несколько (с подогревами индуктором) проходов. При закалочном проходе производится струйное охлаждение водой наружной поверхности бочки и поверхности осевого канала (закалка с внутренним охлаждением) или только поверхности бочки (закалка, без внутреннего охлаждения).
3.3 При закалке с внутренним охлаждением до установки валка на станок необходимо проверить правильность закрепления шланга, подводящего воду в канал. Шланг должен быть закреплен таким образом, чтобы верхний ряд отверстий охлаждающей трубки был на одном уровне с верхним рядом отверстий спрейера в течение всего процесса закалки.
3.4 Для закалки валки устанавливаются в вертикальном положении в центрах или в центре и люнете. Производится разметка согласно схемы и формул.
3.5 Перед нагревом каждого валка необходимо проверить температуру воды и равномерность подачи воды спрейером (визуально), не допуская попадания воды на бочку. Температура воды должна быть не выше 25 °C.
3.6 Валки диаметром более 731 мм без внутреннего охлаждения перед закалкой предварительно подогреваются до температуры 150-^200 °С на установке ТПЧ-2, в электровоздушной ванне (ЭВВ) или в печи.
3.7 В процессе основных подогревов температура поверхности бочки в момент прохождения индуктора должна быть 600−850 °С.
3.8 Температура закалки для валков из стали марок 9Х, 9X2, 75ХМ — 910−920 °С- 9Х2МФ, 9Х2Ш1, 9ХФ, 75ХМФ — 930−940 °С если нагрев производится индукторами с высотой обмотки 100 мм и на 10−20 °С ниже при высоте обмотки индуктора 200 мм. Фактическая температура контролируется в нижней части бочки до отметки подачи воды, на длине 200 мм после отметки подачи воды, а также на середине длины бочки. Результаты заносятся в КТО.
3.9. В процессе основных подогревов и нагрева под закалку температура нагреваемой поверхности регулируется изменением напряжения на индукторе с помощью РС-560 (плавная регулировка), а при необходимости конденсаторными батареями (ступенчатая регулировка).
3.10. Регулировка процесса нагрева изменением скорости движения индуктора допускается только в исключительных случаях в пределах не более +0,1 мм/с с разрешения ОГМет.
3.11. Расход воды и время окончательного охлаждения при закалке назначается в зависимости от диаметра валка согласно таблицы 6.1.
Примечание. При закалке деталей на твердость < 85 Н5Д время охлаждения сокращается на 10−30% в зависимости от требуемой твердости и температуры бочки в момент окончания охлаждения.
После окончания охлаждения температура верхней части бочки валка должна быть не выше 90 °C для валков с твердостью >90 Н5Д и не выше 150 °C при твердости бочки < 90 Н5Д.
ЗАКЛЮЧЕНИЕ
.
С учетом проведенных исследований сделаны следующие выводы.
1. Исследован новый класс валковых сталей повышенной прокаливаемости с 5% хрома. Методами экспериментального и математического моделирования показано, что в результате закалки эти стали характеризуются высокой прокаливаемостью и благоприятным распределением структуры по сечению валков.
2. Предложен подход, позволяющий на основании изучения структуры, фазового состава и свойств исследованных сталей после различных температур нагрева под закалку определять оптимальные режимы аустенитизации.
3. Показано, что после предварительной термической обработкизакалки и высокого отпуска — в исследуемых сталях присутствуют карбидные фазы М7С3, М23С6 и МС, содержащие карбидообразующие элементы Ре, Сг, Мо и V. Количество карбидных фаз с повышением температуры закалки уменьшается. Полное растворение наступает при температуре выше 1150 °C. Растворение карбидных фаз приводит к резкому росту аустенитного зерна.
4. Количество остаточного аустенита возрастает с повышением температуры закалки. При температуре выше 1100 °C отмечается его некоторое снижение, что может быть связано с резким увеличением размера зерна аустенита и облегчением образования пластин мартенсита.
5. Показано, что температура закалки оказывает неоднозначное влияние на абразивную износостойкость валковых сталей с 5% хрома, с повышением температуры закалки, до определенных значений, износостойкость растёт, что связано как с увеличением количества углерода в мартенсите и повышением его твердости, так и с увеличением количества остаточного аустенита, претерпевающего мартенситное превращение при деформации. При дальнейшем повышении температуры нагрева под закалку.
146 количество и стабильность остаточного аустенита возрастают, что приводит к снижению износостойкости.
6. Увеличение содержания хрома в валковых сталях приводит к повышению их отпускоустойчивости. При всех исследованных температурах низкого отпуска (120, 150 и 180 °С) идут процессы образования предвыделений, выделение карбидных фаз не обнаружено. Количество и состав остаточного аустенита не меняются.
7. При различных температурно-временных условиях низкого отпуска впервые получены данные по статической трещиностойкости для исследуемых сталей валков холодной прокатки. Склонность к хрупким разрушениям исследованных сталей после закалки и низкого отпуска в значительной степени определяется температурой закалки. Изменение температуры отпуска со 120 °C до 180 °C приводит к незначительному повышению значений Кю и увеличению доли участков вязкого разрушения. Это позволяет повысить температуру низкого отпуска сталей и несколько понизить их склонность к хрупким разрушениям.
8. Внесены изменения в технологию термической обработки валков холодной прокатки из сталей с 5% хрома, которые приняты к использованию на ОАО «УралмашСпецсталь».
Список литературы
- Гольдштейн М. И. Специальные стали : учеб. для вузов / М. И. Гольдштейн, С. В. Грачёв, Ю. Г. Векслер. 2-е изд., перераб. и доп. — М.: МИСИС, 1999.-408 с.
- Гедеон М. В. Термическая обработка валков холодной прокатки / М. В. Гедеон, Г. П. Соболь, И. В. Паисов. М.: Металлургия. — 1973. — 344 с.
- Геллер Ю. А. Инструментальные стали / Ю. А. Геллер. М.: Металлургиздат, 1961. — 526 с.
- Надёжность и долговечность валков холодной прокатки / В. П. Полухин, В. А. Николаев, П. Т. Шульман и др. М.: Металлургия, 1971. — 503 с.
- Надёжность и долговечность валков холодной прокатки / В. П. Полухин, В. А. Николаев, М. А. Тылкин и др. 2-е изд. — М.: Металлургия, 1976. -448 с.
- Производство и эксплуатация крупных опорных валков / Н. П. Морозов, В. А. Николаев, В. П. Полухин, А. М. Легун. М.: Металлургия, 1977. -128 с.
- Полухин П. И. Производство крупных опорных валков и пути повышения их стойкости / П. И. Полухин, Г. И. Пименов, В. А. Николаев. М.: НИИинформтяжмаш, 1974. — 48 с.
- Повышение надёжности и стойкости прокатных валков / И. С. Тришевский, Н. М. Воронцов, В. А. Воронина и др. // Черная металлургия. Бюл. Ин-та Черметинформация. 1984. — № 2. — С. 24−37.
- Полухин В. П. Составной рабочий инструмент прокатных валков / В. П. Полухин, П. И. Полухин, В. А. Николаев. М.: Металлургия, 1977.
- Боровков И. В. Исследование стойкости рабочих валков станов холодной прокатки / И. В. Боровков, П. Б. Соколов, Ю. Д. Макаров // Сталь. 2005. -№ 2.-С. 58−60.
- Немзер Н. А. Современное состояние производства и эксплуатации прокатных валков / Н. А. Немзер — ЗАО «Термосталь» // Металлург. -2000.-№ 10.-С. 47−53.
- Штайнхофф К. Предотвращение повреждений и улучшение эксплутационных свойств валков / К. Штайнхофф // Сталь. 2001. — № 8. -С. 37−41.
- Штайнхофф К. Современные валковые стали для холодной прокатки / К. Штайнхофф, X. Брунс // Сталь. 2001. — № 8. — С. 41−43.
- Исследование причин хрупкого разрушения цельнокованых прокатных валков / Н. П. Морозов, Р. С. Фазлиахметов, Е. Г. Моисеева и др. // Материалы и дефекты стальных конструкций: сб. Марианске Лазне, 1973.-С. 111−125.
- Опорные валки станов холодной прокатки / П. В. Склюев, Б. Д. Петров, Б. Д. Титоров и др. М.: ЦНИИинформтяжмаш, 1967. — 64 с.
- Трейгер Е. И. Повышение стойкости прокатных валков / Е. И. Трейгер, А. 3. Комановский Киев: Техника, 1984. — 146 с.
- Стойкость опорных валков клети кварто толстолистового стана 2300 / А.
- A. Паршин, Я. Д. Троскунов, Ю. П. Литвиненко и др. // Сталь. 1973. — № 1.-С. 63−65.
- Технология производства валков холодной прокатки / В. А. Дзюба, С. П. Пономарева, А. В. Тырышкин и др. М.: ЦНИИТЭИтяжмаш, 1979. — 39 с.
- Современные толстолистовые станы ведущих капиталистических стран /
- B. Л. Митрюхин, В. С. Грановская, С. М. Овчинникова и др. М.: НИИинформтяжмаш, 1976. — 56 с.
- Петров Б. Д. Термическая обработка и свойства валков холодной прокатки / Б. Д. Петров // Металловедение и термическая обработка металлов. 1983.-№ 6.-С. 36−41.
- Поверхностный наклеп опорных валков / А. Ю. Фиркович, А. М. Цун, А. И. Добронравов и др. // Металлург. 1982. — № 1. — С. 39−40.
- Полухин В. П. Контактная прочность и изнашиваемость стали 150ХНМ / В. П. Полухин, Д. П. Галкин, А. Ю. Фиркович // Изв. вузов. Черная металлургия. 1974. — № 10. — С. 65−68.
- Влияние твердости опорных валков на их стойкость / В. А. Николаев, Г. А. Морозова, А. М. Легун и др. // Пластическая деформация металлов и сплавов: тр. Московского ин-та стали и сплавов, № 85. М.: Металлургия, 1975. — С. 221−226.
- Влияние твердости на износ опорных валков станов 1450 и 2500 горячей прокатки ММК / В. П. Полухин, Л. Ш. Новак, А. Ю. Фиркович и др. // Изв. вузов. Черная металлургия. 1985. — № 1. — С. 71−73.
- Повышение стойкости опорных валков первой клети стана 1680 / В. А. Николаев, В. М. Целовальников, В. С. Мовшович и др. // Металлург. -1977,-№ 4.-С. 34−35.
- Склюев П. В. Термическая обработка крупных поковок / П. В. Склюев. -М.: Машиностроение, 1976. -48 с.
- Прочность прокатных валков / П. И. Полухин, В. А. Николаев, В. П. Полухин и др. Алма-Ата: Наука, 1984. — 295 с.
- Мартин А. Двухслойные литые опорные валки с рабочим слоем из стали AST 7Х / А. Мартин // Металлург. 1999. — № 9. — С. 40−43.
- Полухин В. П. Исследование циклической контактной прочности стали 9Х / В. П. Полухин, Г. А. Морозова // Труды Московского института стали и сплавов. № 80. — С. 115−120.
- Устранение отслоений поверхности рабочих валков стана 2500 / А. Ф. Фиркович, А. И. Антипенко, С. Ю. Спирин, и др. // Сталь. 1999. — № 11. — С. 47−48.
- Поздняк JI. А. Штамповые стали / JI. А. Поздняк, Ю. М. Скрынченко, С. И. Тишаев. М.: Металлургия, 1980. — 244 с.
- Тылкин М. А. Справочник термиста ремонтной службы / М. А. Тылкин. -М.: Металлургия, 1981.-648 с.
- Гудремон Э. Специальные стали. Т. 2. / Э. Гудремон. М.: Металлургия, 1960.-С. 953−1638.
- Sloviak К. Wliv molibdenu i chromu na niektore wlasnosei eksploatasynie stali na walce do pracy na jimna / K. Sloviak, B. Cisjewski, К Plucinski //Hutnik. -1977.-V. 44, № l.-S. 121−128.
- Гуляев А. П. Металловедение : учебник для вузов / А. П. Гуляев. 6-е изд., перераб. и доп. — М.: Металлургия, 1986. — 544 с.
- Стали и сплавы. Марочник: справоч. изд. / В. Г. Сорокин и др.- науч. ред.: В. Г. Сорокин, М. А. Гервасьев М.: Интермет Инжиниринг, 2003. — 608 с.: ил.
- К. Штайнхофф Современные валковые стали для холодной прокатки / К. Штайнхофф, X. Брунс // Сталь. 2001. — № 8. — С. 41−43.
- Вороненко Б. И. Составы и термическая обработка современных валковых сталей / Б. И. Вороненко // МиТОМ. 1995. — № 11. — С. 17−23.
- Улучшение качества металла для отливки валков чистовых клетей проволочных станов / В. Н. Рябко, В. К. Парфенюк, А. Г. Бальва и др. // Черная металлургия. Бюл. ин-та Черметинформация. 1978. — № 8. — С. 52−53.
- Информационные материалы фирмы «Hitachi», .Япония, 1982. 20 с.
- Дымченко В. В. Оценка интенсивности охлаждения и глубины закаленного слоя на валках холодной прокатки из стали 9Х2МФ / В. В. Дымченко, С. А. Балуев // Тяжелое машиностроение. 1992. — № 6. — С. 20−22.
- Износ и эксплуатационная стойкость валков из заэвтектоидной стали/ Т. С. Скобло, JI.A. Малашенко, Л. П. Косик и др. // Сталь. 1988. — № 1. — С. 5659.
- Magnee A. New Highchromium alloys for rolling mill rolls / A. Magnee, D. Totolidis, J. P. Breyer, J. Purnode // Bull. Cercle etud. Met.- 1985. V. 15, — № 10. P. 1/1−1/22.
- Склюев П. В. Водород и флокены в крупных поковках / П. В. Склюев -М.: Машгиз, 1963.-188 с.
- Башнин Ю. А. Технология термической обработки стали / Ю. А. Башнин, Б. К. Ушаков, А. Г. Секей- М.: Металлургия, 1986. 424 с.
- Петров Б. Д. Валки с повышенной глубиной закалки / Б. Д. Петров, О. А. Журавлева // Тяжелое машиностроение. 1991. — № 9. — С. 24−26
- Сталь для производства литых валков ТЭСС / Е. Н. Вишнякова, В. Ф. Коробейник, В. Г. Козлов и др. // Сталь. 1992. — № 7. — С. 76−79.
- Битюков М. В. Сталь для формообразующего инструмента агрегатов бесслитковой прокатки цветных металлов/ М. В. Битюков, А. Е. Клеменьтъева, Л. Т. Ермолаева // Тр. ЦНИИТМАШ. 1991. — № 226. — С. 21−23
- Сталь повышенной контактной выносливости для валков холодной прокатки / М. С. Потапова, X. К. Шайдулина, В. Т. Козлов и др. // Сталь. 1986.-№ 2.-С. 80−82.
- Белкин М. Я. Исследование стали с повышенной хрупкой прочностью для бандажей составных опорных валков / М. Я. Белкин, В. 3. Камалов, JI. М. Белкин //Валки прокатных станов. М.: Металлургия, 1989, — С. 16−24
- Белкин М. Я. Трещиностойкость как критерий работоспособности волковой стали / М. Я. Белкин, В. 3. Камалов, Л. М. Белкин // МиТОМ. -1986.-№ 4.-С. 57−61.
- Прокошкин С. Д. Структура и свойства валковой стали после комбинированной (лазерной и термомеханической) обработки / С. Д.
- Прокошкин, И. А. Морозов, М. Я. Белкин // Лазерная обработка сталей и титановых сплавов. Перм: Изд-во Политехнического института. 1991. -С. 27−33
- Пат. 2 015 757 Россия, МКИ В21 В28/02. Способ эксплуатации прокатного валка / Ветер В. В., Гриднев А. Т., Настич В. П. и др. Новолипецкий металлургический комбинат. № 5 055 733/27- заявл. 21.07.92. Опубл. 15.07.94.
- Rolls 2003. Stahl and Eisen. 2003. — № 2, 12 с. Англ. 9−11 апреля 2003 г. Бирмингем
- Выбор режимов термической обработки для восстановления валков из стали 9Х2МФ / В. В. Ветер, Е. Л. Торопцева, Г. В. Лихачев и др. // Сталь. 2000. — № 2. — С. 63−66.
- Брусиловский Б. А. Особенности изменения структуры и твердости закаленных крупногабаритных валков из стали 9Х2МФ при отпуске / Б. А. Брусиловский // Металловедение и термическая обработка металлов. -1998.-№ 12.-С. 4−6.
- Адамова Н. А. Сокращенные режимы отпуска крупных прокатных валков / Н. А. Адамова, Е. М. Векслер // Сталь. 1922. — № 1. — С. 78−80.
- Металлы. Методы измерения твёрдости по Роквеллу: ГОСТ 9013–59. -Введ. 1969−01−01.-М., 1989.
- ГОСТ 8.064−94. ГСИ Государственный специальный эталон и государственная поверочная схема для средств измерения твердости по шкалам Роквелла и Супер-Роквелла.
- Измерение микротвёрдости вдавливанием алмазных наконечников: ГОСТ 9450–76.-Введ. 1977−01−01 -М., 1993.
- Беккерт М. Способы металлографического травления : справ, изд.: пер. с нем. / М. Беккерт, X. Клемм. 2-е изд., перераб. и доп. — М.: Металлургия, 1988. — 400 с.
- Спектор А. Г. Статистический анализ структур с шарообразными зернами / А. Г. Спектор // Заводская лаборатория. 1955. — № 2. — С. 193−194.
- Салтыков С. А. Стереометрическая металлография / С. А. Салтыков М.: Металлургия, 1976. — 375 с.
- Черепин В. Т. Эксперементальная техника в физическом металловедении / В. Т. Черепин. Киев: Техшка, 1968. — 198 с.
- Берлин Г. С. Электронные приборы с механически управляемыми электродами / Г. С. Берлин. М.: Энергия, 1970. — 160 с.
- Уманский Я. С. Рентгенография металлов и полупроводников / Я. С. Уманский. М.: Металлургия, 1969. — 496 с.
- Фазовый рентгеноструктурный анализ: метод, указания. Свердловск: УПИ, 1980.- 18 с.
- Горелик С. С. Рентгенографический и электроннооптический анализ : учеб. пособие для студентов вузов / С. С. Горелик, Л. Н. Расторгуев, Ю. А. Скаков 4-е изд., перераб. и доп. — М.: МИСИС, 2002. — 360 с.
- Люты В. Закалочные среды : справ. / В. Люты: пер. с польск. Челябинск: Металлургия, 1990. — 192 с.
- Исследование процессов старения в сталях типа 20Х2Н4М2ФСЮ / М. Р. Немировский, Ю. Р. Немировский, В. Д. Кибальник, М. С. Хадыев, Л. Р. Дудецкая, В. А. Ткачева // Физика металлов и металловедение. 1992. -№ 1. — С. 100−110.
- Кристиан Дж. У. // Физическое металловедение. Вып. II. М.: Мир, 1968. -С. 227−341.
- Гольдштейн М. И. Дисперсионное упрочнение стали / М. И. Гольдштейн, В. М. Фарбер. М.: Металлургия, 1979. — 208 с.
- Уэндландт У. Термические методы анализа / У. Уэндландт. М.: Мир, 1978.-526 с.
- Производство и эксплуатация крупных опорных валков / Н. П. Морозов, В. А. Николаев, В. П. Полухин и др. М.: Металлургия. — 1977. — 128 с.
- Третьяков A.B. Расчет и исследование валков холодной прокатки / A.B. Третьяков, Э. А. Грабер М.: Машиностроение, 1966. — 180 с.
- Немчинский А.Д. Методика экспериментального определения прокаливаемости / А. Д. Немчинский // Вестник машиностроения. 1952. -№ 2. — С. 30 — 32.
- Иванова В. С. Количественная фрактография: Усталостное разрушение / В. С. Иванова. Челябинск: Металлургия, 1988. — 396 с.
- Оценка применимости критериев хрупкого разрушения в расчетах термонапряженного состояния прокатных валков при термической обработке / Н. В. Савельева, Ю. А. Карасюк — ЦНИИМ // Металловедение и термическая обработка металлов. 1990. — № 11. — С. 42 — 46.
- Исследование причин хрупкого разрушения цельнокованых прокатных валков / Н. П. Морозов, Р. С. Фазлиахметов, Е. Г. Моисеева и др. // Материалы и дефекты стальных конструкций: сб. Марианске Лазне, -1973.-С. 111−125.
- ГОСТ 25.506−8. Расчёты и испытания на прочность. Методы механических испытаний металлов. Определение характеристик трещиностойкости (вязкости разрушения) при статическом нагружении. -Введ. 01.01.86 Госстандарт СССР М.: Изд-во стандартов, 1985. — 61 с.
- Апаев Б. А. Фазовый магнитный анализ сплавов / Б. А. Апаев. М.: Металлургия, 1976.-281 с.
- Металлы. Метод испытания на абразивное изнашивание при трении озакрепленные абразивные частицы: ГОСТ 17 367–71. Введ. 2001−01−73. -М., 1972.-С.
- Румшиский Л. 3. Математическая обработка результатов эксперимента / Л. 3. Румшиский М.: Наука, 1971.- 192 с.
- Корн Г. Справочник по математике / Г. Корн, Т. Корн. М.: Наука, 1974.831 с.
- Винокур Б. Б. Структура конструкционной легированной стали / Б. Б. Винокур, В. Л. Пилюшенко, О. Г. Касаткин. М.: Металлургия. 1983. -216 с.
- Винокур Б. Б. Прочность и хрупкость конструкционной легированной стали / Б. Б. Винокур, В. Л. Пилюшенко. Киев: Наукова думка. 1983. -283с.
- Винокур Б. Б. Прокаливаемость конструкционных сталей / Б. Б. Винокур, В. Л. Пилюшенко. Киев: Наукова думка, 1970, — 108с.
- Попова Л.Е. Диаграммы превращения аустенита в сталях и бета-раствора в сплавах титана: справочник термиста/ Л. Е. Попова, А. А. Попов. 3-е изд., перераб. И доп. — М.: Металлургия, 1991. — 503 с.
- Изучение кинетики распада переохлажденного аустенита в валковых сталях / Ю. В. Худорожкова, JI. А. Махмутова, Е. С. Пятырова, М. А. Гервасьев // Сб. трудов X отчётная конф. мол. учёных ГОУ УГТУ-УПИ. -Екатеринбург, 2006. С. 352.
- Известия вузов «Энергетика», 1963, № 5, с. 85−91 Аксенов Г. И. и др. Числовой метод расчета температурного поля при термической обработке цилиндра с учетом выделения скрытой теплоты превращения и зависимости теплофизических характеристик от температуры.
- Синнаве M. Новые марки прокатных валков и тенденции развития их производства / М. Синнаве // Сталь. 2003. — № 7. — С. 48−52.
- Петров Б. Д., Валки с повышенной глубиной закалки / Б. Д. Петров, О. А. Журавлева // Тяжелое машиностроение. -1991. № 9. — С. 24−26
- Нагорнов Н.П. Технология изготовления и результаты исследований валков холодной прокатки на УЗТМ / Н. П. Нагорнов. М.: ГНТК, 1959. -63 с.
- Брусиловский Б. А., Исследования остаточного аустенита в поверхностном слое валков холодной прокатки / Б. А. Брусиловский, В. Н. Заика, Т. Е. Пискарева // ФММ, 1989. — том 67. — вып 6.
- Садовский В.Д. Остаточный аустенит в закаленной стали / В. Д. Садовский, Е. А. Фокина. М.: Наука, 1986. — 113 с.
- Беликов С. В. Влияние легирования на параметры кинетики распада переохлажденного аустенита и свойства Cr-Mo-V валковых сталей :
- Автореф. дис. на соиск. учен. степ, к.т.н. / С. В. Беликов -Екатеринбург. -2001.-22 с.
- Счастливцев В.М. Роль принципа метастабильности аустенита Богачёва-Минца при выборе износостойких материалов / В. М. Счастливцев, М. А Филиппов // МиТОМ. -2005. № 1. -С. 6−9.
- Белоус М.В. Превращения при отпуске стали / М. В. Белоус, В. Т. Черепин, М. А. Васильев М: Металлургия, 1973.-231с.
- Новиков И.И. Теория термической обработки металлов / И. И. Новиков. -М.: Металлургия, 1986. 480 с.
- Смирнов М.А. Основы термической обработки стали: Учебное пособие/ М. А. Смирнов, В. М. Счастливцев, Л. Г. Журавлёв. -М: Наука и технологии, 2002. -519 с.
- Фазовые превращения в процессе отпуска валковых сталей / М. А. Гервасьев, М. А. Филиппов, Б. Д. Петров, В. С. Палеев, Ю. В. Худорожкова // Металловедение и термическая обработка металлов. -2005.-№ 1.-С. 12−15.
- Савельева Н.В. Оценка применимости критериев хрупкого разрушения в расчетах термонапряженного состояния прокатных валков при термической обработке / Н. В. Савельева, Ю. А. Карасюк // МиТОМ -1990.-№ 11.-С. 42−46
- Ежов А. А. Изломы конструкционных сталей / A.A. Ежов, Л. П. Герасимова, A.M. Каток // Металловедение и термическая обработка металлов. 2004. — № 4. — С. 34−40.
- Курдюмова Г. Г. К вопросу о классификации микромеханизмов разрушения по типам / Г. Г. Курдюмова, Ю. В. Мильман, В. И. Трефилов //Металлофизика. 1979. — № 2. — том 1. — С. 55−62