Высокотемпературное автоклавное выщелачивание низкосортных сульфидных цинковых концентратов
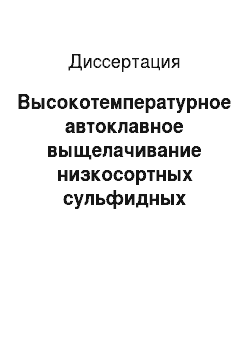
По этой причине, а также в связи с ужесточением во всём мире экологических норм по газовыбросам, актуальной стала проблема по внедрению технологий, не использующих обжиг концентратов. С развитием автоклавных технологий началось внедрение автоклавного выщелачивания в цинковое производство. При автоклавном выщелачивании ферритообразование не происходитсера из сульфидов переводится в серу… Читать ещё >
Содержание
- 1. АНАЛИТИЧЕСКИЙ ОБЗОР ЛИТЕРАТУРНЫХ ИСТОЧНИКОВ
- 1. 1. Автоклавные способы переработки цш 1ковых концентратов
- 1. 2. Данные об автоклавном окислительном выщелачивании
- 1. 2. 1. Химизм процесса
- 1. 2. 2. Параметры ЛОВ
- 1. 3. Практическое применение автоклавного выщелачивания цинковых концентратов
- 1. 4. Данные по кинетике вскрытия минералов
- 1. 4. 1. Основные кинетические характеристики выщелачивания сульфидного цинкового концентрата
- 1. 4. 2. Механизм разложения минералов
- 1. 5. Постановка задачи
- 2. МЕТОДИКА ИССЛЕДОВАНИЙ
- 2. 1. Методика проведения опытов
- 2. 2. Теоретические предпосылки исследования: расчет кинетических характеристик выщелачивания по методике Вигдорчика-Шейнина (методике «кинетической функции»)
- 2. 3. Карта опытов
- 3. ИССЛЕДОВАНИЯ МАКРОКИНЕТИЧЕСКИХ ПОКАЗАТЕЛЕЙ АОВ НЕКОНДИЦИОННОГО ЦИНКОВОГО КОНЦЕНТРАТА
- 3. 1. Исследования одностадиального выщелачивания
- 3. 1. 1. Расчет макрокинетических показателей АОВ на примере одностадиального выщелачивания сфалерита
- 3. 1. 2. Расчет макрокинетических показателей разложения халькопирита
- 3. 1. 3. Исследование влияния «оборотного электролита» на кинетику выщелачивания
- 3. 1. 4. Выводы
- 3. 2. исследования’двустадиального выщелачивания
- 3. 2. 1. Методика исследований двустадиалъного выщелачивания
- 3. 2. 2. Низкокислотное выщелачивание (НКВ)
- 3. 2. 3. Высококислотное выщелачивание (ВКВ) — вторая, стадия противотока
- 3. 2. 4. Анализ возможных причин роста Еа и, а со снижением глубины вскрытия минералов
- 3. 2. 4. 1. Выпадение из раствора вторичных сульфидов в первые минуты выщелачивания
- 3. 2. 4. 2. Осаждение меди сульфидом цинка
- 3. 2. 4. 3. Активирующее влияние ионов меди на выщелачивание цинка
- 3. 2. 4. 4. Осаждение меди сульфидом цинка + активирующее влияние ионов меди на выщелачивание цинка
- 3. 2. 4. 5. Выводы
- 3. 2. 5. Макрокинетические показатели разложения сфалерита и халькопирита в двустадиальном режиме
- 3. 1. Исследования одностадиального выщелачивания
- 3. 3. Окисление пирита
- 3. 3. 1. Постановка задачи
- 3. 3. 2. Окисление пирита при двустадиальном выщелачивании
- 3. 3. 2. 1. Первая стадия — НКВ
- 3. 3. 2. 2. Вторая стадия — ВКВ
- 3. 3. 2. 3. Выводы
- 4. 1. Влияние примесей-катионов
- 4. 2. Влияние расхода кислоты на выщелачивание низкосортного цинкового концентрата
- 4. 2. 1. Зависимость механизма выщелачивания от метода подачи кислоты и её расхода
- 4. 2. 2. Изменение селективности извлечения металлов в раствор при переходе к двустадиалъному режиму выщелачивания
- 4. 2. 3. Влияние расхода кислоты на выход элементарной серы
- 4. 2. 4. Корреляционный анализ влияния расхода серной кислоты на выщелачивание цинка
Высокотемпературное автоклавное выщелачивание низкосортных сульфидных цинковых концентратов (реферат, курсовая, диплом, контрольная)
В середине XX века исходным сырьём для получения цинка в большинстве случаев являлись сульфидные цинковые концентраты, получаемые флотационным обогащением руды й содержащие обычно (%): Zn 48−55- S 30−32- Pb 1−3- Fe 5−10- Си до 2 [1].
По традиционной гидрометаллургической технологии концентраты подвергаются окислительному обжигу, огарок — противоточному двустадийному атмосферному выщелачиванию, а из нейтрального раствора после тонких очисток осаждают катодный цинк [1, 2]. Принципиальная технологическая схема «обжиг-выщелачивание-электролиз» показана на Рис. 1. концентрат.
Zn.
Рис. 1. Принципиальная схема производства цинка по технологии «обжиг-выщелачивание-электролиз». Пунктиром выделено двустадийное противоточное выщелачивание.
Недостатком этой технологии является использование громоздких операций обжига и выщелачивания, предполагающих развитые схемы очистки, охлаждения и утилизации серосодержащих газов, отстаивания пульп и промывки кеков, зависимость производства от условий сбыта серной кислоты.
К настоящему времени основным сырьем для производства цинка являются концентраты, получаемые при обогащении полиметаллических руд. Концентраты содержат в среднем: 40−46% Хп, 4−10% Ре, 0,5−3,5% Си, 1−3% РЬ, 0,5−4% БЮо, 26−33% Б, а также редкие (Сс1, Оа, Т1,1п) и благородные (Аи, Ag) металлы.
3].
Снижение в концентратах содержания цинка и увеличение железа и кремнезема ухудшило показатели классической технологии: уменьшился выход растворимых форм цинка из-за образования ферритов при обжиге. Ферриты цинка выщелачиваются при повышенной кислотности, но это приводит к попутному растворению силикатов, что резко осложняет очистку растворов и, как следствие, снижает показатели электролиза [3].
По этой причине, а также в связи с ужесточением во всём мире экологических норм по газовыбросам, актуальной стала проблема по внедрению технологий, не использующих обжиг концентратов. С развитием автоклавных технологий началось внедрение автоклавного выщелачивания в цинковое производство. При автоклавном выщелачивании ферритообразование не происходитсера из сульфидов переводится в серу элементарную, которая является экологически безопасной и легко складируемой (транспортируемой).
В связи с постепенным истощением запасов легкообогатимых цинксодер-жащих руд в переработку вовлекается всё менее сортное полиметаллическое сырье. Как следствие, ухудшается качество цинковых концентратов: снизилось содержание цинка (38−42%), возросло содержание железа (10−14%), меди (24%), кремнезема (6−10%), свинца (4−8%). Можно говорить о качественном изменении сырья: это уже полиметаллические материалы, в которых количество сульфида цинка сравнимо с количеством сульфидов меди и железа. При автоклавном выщелачивании такие концентраты будут вести себя иначе, чем мономинералы.
Т.о., актуальной стала проблема не просто изучения кинетических закономерностей выщелачивания минералов (в первую, очередь — сульфида цинка), а изучение влияния? параметров" процесса (температуры, давления кислородакрупности/ концентрата, продолжительности процессакислотности идр.) на показатели выщелачивания/именно* на фоне взаимодействия минералов цинкажелеза? и: мед", друг с другомвлияния 1 наличия? однихсульфидов, на кинетические показатели вскрытия^ других.
Эти полиметаллические концентраты значительно разнятся по минералогическому составу для разных месторождений^ Технологические закономерности выщелачивания, характерные для одного концентрата, могут коренным образом отличаться от кинетических показателей выщелачивания? другого, что, в свою очередь, требует детального изученияповедения каждого нового низкокачественного концентрата в условиях автоклавной переработки.
Целью работы-является изучение закономерностей автоклавного выщелачивания низкосортного цинкового концентрата корпорации «Казахмыс» (Республика Казахстан) — исследование влияния параметров процесса на показатели разложения основных минералов. Это необходимо при разработке технологии АОВ, обеспечивающей глубокое и, по возможности, селективное извлечение цинка в раствор.
Исследование влияния параметров процесса на показатели выщелачивания низкосортных концентратов включает в себя:
Изучение литературных источников по автоклавному выщелачиванию сульфидных материалов, сходных с данныманализ этих источников: какая имеющаяся информация о показателях выщелачиваниясульфидного сырья может быть использована в разрабатываемой технологииа. какая — нет, ввиду её недостаточности и (или) противоречивостиОсобыйинтерес представляют работы, — посвященные изучению влияния основных параметроввыщелачивания: (температуры, давления кислорода, расхода кислоты и т. д.) на скорость, глубину, селективность и механизм разложения" сульфидов цинка меди и железа. В случае недостатканеполноты, противоречивости имеющихся литературных данных необходимо:
2. Изучение кинетики выщелачивания основных минералов низкосортного цинкового концентрата: влияния на показатели выщелачивания температуры, давления кислорода, крупности концентрата, продолжительности процесса, кислотности и т. д.- расчет кинетических констант процесса. Изучение производится в соответствии с традиционной методологией: проведение экспериментовматематическая обработка результатов экспериментованализ полученных результатов — получение нужной информации.
3. Изучение влияния параметров процесса применительно и к одностадиально-му, и к двустадиально-противоточному автоклавному выщелачиванию низкосортного концентрата.
4. Изучение возможности переноса результатов лабораторного исследования на промышленный масштаб.
5. Опираясь на полученную в ходе исследований информацию, определить технологические показатели автоклавного выщелачивания низкосортного цинкового концентрата, «обеспечивающие глубокое селективное извлечение цинка в раствор» .
7.5. Выводы по разделу.
Поскольку показатели выщелачивания данного' цинкового концентрата практически не зависят от конструкции автоклава, тополученные в лабораторных исследованиях результаты могут быть перенесены на заводскую практику— использованы для расчетов заводских процессов.
Полученные в результате исследований кинетические: закономерности окисления сфалерита и халькопирита (Еа, а, т0) позволяют рассчитать продолжительность процессанеобходимую для обеспечения нужной степени извлечения металлов {Ъл, Си) в раствор при заданных температуре и давлении кислорода.
Автоклавный процесс может контролироваться ЕЬ-метрией.
Опираясь на полученные в результате исследований данные, создана математическая модель технологической схемы цинкового завода, использующего двустадиальное автоклавное выщелачивание. С помощью этой модели показана количественная зависимость содержания серной кислоты в «товарном» растворе автоклавного передела одновременно от двух факторов — степени извлечения Ъп в раствор (прямая зависимость) и содержания Ъх в концентрате (обратная зависимость). Расчеты по модели показывают зависимость результатов двустади-ального выщелачивания от качества концентрата.
Заключение
.
В соответствии с поставленными задачами (см. § 1.5) было изучено АОВ низкокачественного цинкового концентрата как для одно-, так и для двустади-альнои технологии.
Научная новизна.
1. Расход-(концентрация), серной кислоты является наиболее значимым фактором автоклавного выщелачивания низкосортного цинкового концентрата при. данных условиях (1°>125°С, рН<1,5). По отношению к этому фактору кинетические функции растворения сфалерита и халькопирита не являются инвариантными. Т. е., активность Н2804 влияет не только на скорость, но и на механизм выщелачивания.
2. Выщелачивание низкосортного цинкового концентрата лимитируется диффузией кислорода внутри твердой частицы к поверхности сульфидареже, совместно и диффузией «внутри твёрдого», и химическим взаимодействием минерала с кислородом.
3. Определены величины кинетических характеристик выщелачивания (Еа, а, т0) основных минералов концентрата: сфалерита, халькопирита и пирита для разных режимов технологии — одностадиальной, и обеих стадий двустадиаль-ной. Установлено, что порядок по кислороду систематическийпричём, чем ниже глубина вскрытия минералов — тем сильнее зависимость скорости выщелачивания от температуры и Ро2. Причиной этой аномалии является образование вторичных сульфидов в результате взаимодействия минералов концентрата.
4. Гидротермальная обработка концентрата раствором 2п804 приводит к пассивации сульфидов. В результате уменьшается активная поверхность сульфидов, способная взаимодействовать с протоном и кислородом. Процесс переходит в кинетическую область: самой медленной стадией становится адсорбция-рекомбинация кислорода на поверхности сульфидоввыщелачивание протекает с пониженной скоростью и с половинным порядком по кислороду.
5. Показано, что повышение концентрации Ъхсл Мд2+, Мп2+ препятствует гидролизу ионов Ре (Ш), активируя, таким образом, окисление пирита1.
Практическая ценность.
1. Установлена высокая воспроизводимость, результатов АОВ при переходе к.
1 3+.
Т.о., утверждения различных исследователей о решающей роли Бе в окислении Ре82 находят подтверждение. агрегатам иного объёма и геометрии, что позволяет по результатам лабораторных опытов выбирать параметры промышленного процесса и выполнять расчеты необходимого автоклавного оборудования.
2. Разработаны режимы автоклавного выщелачивания низкокачественного цинкового концентрата обеспечивающие извлечение Ъа в раствор до 99% и выше, при переходе -80% 8 в 8°. Результаты данного исследования заложены в проект автоклавного передела Балхашского цинкового завода на производительность 325 тыс. т/год концентрата, заказаны промышленные автоклавы (рабочий проект инв. № 116 497- дополнение к договору № 11−99 (в «Казахмыс» -№ 1−9/740)).
3. Обоснована целесообразность ведения процесса в две стадии. Помимо повышения извлечения цинка в раствор, и снижения содержания в растворе примесей, что присуще противотоку принципиально, переход к двустадиальному АОВ позволяет рационально распределять подачу кислоты, и, за счёт этого: увеличить выход 8°- уменьшить расход кислородане снижать удельную производительность агрегата.
4. Определена количественная зависимость состава продуктов двустадиально-го АОВ от содержания Ъп в концентрате.
Список литературы
- Лоскутов Ф.М. Металлургия свинца и цинка. М., Металлургиздат, 1956, 528 с.
- Снурников А.П. Гидрометаллургия цинка. М., Металлургия, 1981, 384 с.
- Набойченко С.С., Ни Л.П., Шнеерсон Я. М., Чугаев Л. В. Автоклавная гидрометаллургия цветных металлов. Екатеринбург. 2002, 940 с.
- Набойченко С.С., Болатбаев К. Н. Исследование автоклавного одностадийного высокотемпературного выщелачивания цинковых концентратов. // Цветные металлы, 1985, № 10, с. 39−40.
- Набойченко С.С., Болатбаев К. Н. Автоклавное высокотемпературное выщелачивание медно-цинкового концентрата. // Цветные металлы, 1986, № 10, с. 27−29.
- Bjorling G. Leaching of sulfides minerals under pressure. // Metall 8, 1954, pp. 781−784.
- Parker E.G. Oxidation pressure leaching of zinc concentrates. // CIM Bull, 74, 1981, pp. 145−150.
- Jankola W.A., Martin M.T. Cominco’s Trail Zinc pressure leaching operation. // CIM Bull. 78, 1985, pp. 77−81.
- Jankola W.A. Zinc pressure leaching at Cominco. // Hydrometallurgy, Vol. 39, 1995, pp. 63−70.
- Ozberk E., Bolton G, Masters I. The Sherritt zinc pressure leach process- 15 year after commercialisation. // The future of lead and zinc. Asia and world, Beijing, China, 1996.
- Krysa B.D. Zinc pressure leaching at HMBS. // Hydrometallurgy, Vol. 39, 1995, pp. 71−77. Поступила 27 июня 1995.
- Boissoneault M., Gagnon S., Henning R., Lachance E., Vecchiarelli M. Improvements in pressure leaching at Kidd Creek. // Hydrometallurgy, Vol. 39, 1995, pp. 79−90.
- Ozberk E., Collins M.J., Makwana M., Masters I.M., Pullenberg R., Bahl W. Zinc pressure leaching at the Ruhr-Zink Refinery. // Hydrometallurgy, Vol. 39, 1995, pp. 53−61. Поступила 27 июня 1995 г.
- Набойченко С.С. Автоклавная переработка медно-цинковых и цинковых концентратов. М. Металлургия, 1989, 112 с.
- Садыков С.Б. Автоклавная переработка низкосортных цинковых концентратов. Екатеринбург: УрО РАН, 2006, 580 с.
- Forward F.A., Veltman Н. Direct leaching zinc-sulfides concentrates by Sherritt Gordon. // J. Metals, 11, 1959, pp. 836−846.
- Нелень И.М. Автоклавная схема переработки цинкового сырья. Автоклавные процессы в цветной металлургии. М., ЦИИНцветмет. 1966, с. 99−117.
- Ярославцев А.С., Смирнов В. И. Исследование автоклавного выщелачивания цинкового концентрата. // Цветные металлы. 1964, № 2, с. 26−30.
- Набойченко С.С., Болатбаев К. Н. Автоклавное сернокислотное выщелачивание цинковых концентратов. // Цветные металлы. 1985, № 2, с. 23−25.
- Турчанинов В.В., Синакевич А. В. // Научные труды Иргиредмета, 1963, Вып. 11, с. 301−313.
- Ярославцев А.С., Смирнов В. И. // Изв. вузов. Цветная металлургия, 1964, № 5, с. 58−62.
- Нелень И.М. Металлургия цветных металлов и методы анализа. // Сб. Гинцветмета, М.: Металлургия, 1965, № 23, с. 304−322.
- Каковский И.А., Набойченко С. С. Термодинамика и кинетика гидрометаллургических процессов. Алма-Ата, Наука, 1986, 272 с.
- Болатбаев К.Н. Автоклавное сернокислотное выщелачивание цинковых и медно-цинковых концентратов. Автореферат диссертации к.т.н. Свердловск, 1986.
- Mackiw V.N. Current Trends in Chemical Metallurgy. // The Canad. Journ. of Chemical Engineering. Vol 46, 1968, № 1, pp. 3−15.
- Piao Shun Yu, Tozawa Kazuteru. Effect of iron content in zinc sulfide concentrates on zinc extraction on oxygen pressure leaching with elemental sulfur. //
- Mining and Metallurgy Inst. Jap., 1987, № 2, pp. 89−105.
- Chaudhur K. Bhadra, Fisher Holger, Hilbrans Hermann, Gerlach Johannes. Патент ФРГ № 3 031 007.
- Рязанова Т.А. Автоклавное выщелачивание обожжённых пиритных концентратов. // Известия ВУЗов. Цветная металлургия, 1982, № 4, с. 66−69.
- Борисов В.М., Засецкий Л. П. Основные физико-химические свойства серы.- В сб.: Самородная сера, М, Труды ГИГХС, вып. 6, Госгортехиздат, 1960, с. 436−484.
- Велтман X., Болтон Г. Л. Прямое выщелачивание под давлением сфалерита с одновременным получением элементарной серы. Современное состояние. (Перевод Гипроникель, Л., 1982.) // Erzmetall, 1980, Vol. 33, № 2, pp. 78−84.
- Шнеерсон Я.М., Онацкая А. А., Краснов А. Л. Применение поверхностно-активных веществ при автоклавном выщелачивании пирротиновых концентратов. // Цветные металлы, № 9, 1982, с. 26−30.
- Борбат В.Ф., Шнеерсон Я. М., Онацкая А. А. Выщелачивание сульфидных материалов. // Обз. информация ЦНИИЦветмет экономики и информации. М., вып. 2, 1984.33. Патент США № 5 651 947.
- Parker E.G., Romanchuk. S. Pilot plant demonstration of sulfide pressure leaching. //J.M. Cigan, T.S., Lead-Zinc-Tin '80 Symp. AIME, New York, 1979, pp. 408−425.
- Sutherland C.A. Modernization of Cominco’s zinc plant and lead smelter at Trail, British Columbia. // CIM Bulletin 1988, Vol. 912, pp. 85−89.
- Худяков И.Ф. О рациональной схеме переработки сульфидных концентратов. // Комплексное использование минерального сырья, 1987, № 5, с. 55−57.
- Vankatashala man S.N. // Trans. Indian. Inst. Met, 1986, Vol. 39, № 6. pp. 545−550.
- Масленицкий И.Н., Доливо-Добровольский B.B., Чугаев Л. В. и др. Автоклавные процессы в цветной металлургии. М., Металлургия, 1969, 350 с.
- Доброхотов Г. Н., Самсонова А. Ф. Аэрационные характеристики автоклавов различных конструкций. // Труды института Гипроникель, вып. 24, Л., 1965, с. 3−23.
- Набойченко С.С., Болатбаев К. Н. // Изв. вузов. Цветная металлургия, 1985- № 4, с. 104−106.
- Veltman Н., O’Kane Р.Т. // 97-th Annual Meeting of the AIME, N.-Y., 1968.
- Dutrizac J.E. and Chen T.T.: CANMET, Ottawa, ON, unpublished research, 1983.
- Jankola W.A. Zinc pressure leaching at Cominco. // Hydrometallurgy, 1995, Vol. 39, pp. 63−70. Поступила 27 июня 1995.
- Ashman D.W., Jankola W.A. Recent experience with zinc pressure leaching at Cominco. (Перевод Гипроникель, С-Пб., 2000.) //Lead-Zinc '90, Warrendale, PA: TMS, 1990, pp. 253−275.
- Parker E.G., McKay D.R., Salomon-de-Friedberg. Zinc pressure leaching at Cominco’s Trail Operation. // Proc. 3rd Int. Symp. Hydrometallurgy 112th AIME Annual meeting, 1983, pp. 927−940.
- Boissoneault M., Gagnon S., Henning R., Lachance E., Vecchiarelli M. Improvements in pressure leaching at Kidd Creek. // Hydrometallurgy, Vol. 39, 1995, pp. 79−90. Поступила 27 июня 1995 г.
- Mollison A.C., Moore G.W. Автоклавное выщелачивание сульфида цинка на заводе Kidd Kreek. // Canada. Lead Zink90, PA: TMS, 1990, pp. 277−291.
- Collins M.J., Ozberk E., Makwana M., Masters I.M., Pullenberg R., Bahl W. Integration of the Sherritt zinc pressure leach process at the Ruhr-Zink refinery. // Hydrometallurgy '94, IMM, 1994, pp. 869−885.
- Von Ropenack A. Future changes in the physic-chemistry of the zinc elec-trowining. // T.S., Lead-Zinc '90. TMS, Warrendale, Pa., 1990, pp. 641−652.
- Von Ropenack A. Hematite the solution to a disposal problem — an example of the zinc industry. // J.E., Iron Control in Hydrometallurgy, Chichester, 1986, pp. 730−741.
- Barth T.R., Hair A.T.C., Meier T.P. Работа завода автоклавного выщелачивания цинка HBM&S. // Zinc and Lead Processing, The Metallurgical Society of CIM, 1998.
- Austin E., McFadden W.E. The electrolytic zinc plant of the HBM&S. // Trans.
- Can. Min. Met., Vol. 59- 1956, pp. 208−223.
- Collins M.J., McConaghy E.J., Stauffer R.F., Desroches G. J, Krysa, B.D. Starting up the Sherritt pressure leach process at Hudson Bay. // JOM, 46(4), 1994, pp. 51−58.
- Chalkley M.E., Collins M.J., Ozberk E. The Behaviour of Sulphur in the Sherritt Zinc Pressure Leach Process. // World Zinc '93. Ed. I.G. Matthew, Australia’s. Inst. Min. Metall., Parkville, Australia, 1993, pp. 325−331.
- Жуховицкий А.А., Шварцман JI.А. Курс физической химии. М., Металлургия, 1979, 368 с.
- Corrion J-P., Gely R., Viers P. // Hydrometallurgy, 1988, Vol.21, № 1, pp. 85−102:
- Jan R. J., Hepworth M.T., Fox V.G. // Metall. Trans. B, 1976, Vol. 7, № 9, pp. 353−361.
- Pawlek F. // J.S. Afric. Inst Metal, 1969, № 7, pp. 632−654.
- Такала X. Выщелачивание цинковых концентратов на заводе в Коккола. (Outokumpu Research Оу) // «Обогащение руд"-«Цветные металлы», 2001. Июнь. Специальный выпуск, с. 65−68.
- Baldwin S. A., Demopoulos G. P., Papangelakis V. G. // Mathematical Modeling of the Zinc Pressure Leach Process. // Metallurgical and Materials Transactions В., Vol. 26B, 1995, pp. 1035−1047.
- Набойченко C.C., Болатбаев K.H. (УПИ им. С. М. Кирова, 1987). Ссылка: Набойченко С. С., Ни Л. П., Шнеерсон Я. М., Чугаев Л. В. «Автоклавная гидрометаллургия цветных металлов.» Екатеринбург. 2002. с 174.
- Елисеев Е.И., Худяков И. Ф., Смирнов В. И. (УПИ им. С. М. Кирова, 19 651 967). Ссылка: Набойченко С. С., Ни Л. П., Шнеерсон Я. М., Чугаев Л. В. «Автоклавная гидрометаллургия цветных металлов.» Екатеринбург. 2002. с 176.
- Perez I. Palencia, Dutrizac J.E. The effect of iron content of sphalerite on its rate of dissolution in ferric sulphate and ferric chloride media // Hydrometallurgy, 1991, Vol. 26, pp. 211−232.
- Crundwell F.K. Effect of iron impurity in zinc sulfide concentrates on the rate of dissolution. // AlChE J., 1988, Vol. 34 (7), pp. 1128−1134.
- Нелень И.М., Соболь С. И. // Обогащение и металлургия цветных металлов, 1959, № 15, с. 447−475.
- Шнеерсон Я.М., Фрумина Л. М., Ивановский В. В., Касаткин С. В. // Гипро-никель: Сб.науч.тр. Л., 1981, с. 53−61.
- Hackl R.P., Dreisinger D.B., Peters Е., King J.A. // Hydrometallurgy, 1995, Vol.39, № 1−3, pp. 25−49.
- Baur J.R., Gibbs H.L., Wadsworth M.E. Initial-stage sulfuric acid leaching kinetics of chalcopyrite using radiochemical techniques. // Report Invest. (US Bur.Mines. Dep. Intern.), 1974, RI 7823.
- Доброхотов Т.Н., Майорова E.B. // ЖПХ, 1962, Т. 35, № 8, с. 1702−1709.
- Oprea F., Taloi D. // Metallurgia, 1971, Vol. 23, № 1, pp. 33−35.
- Majima H., Peters E. // Trans.Met.Soc. AIME, 1966, Vol.236, № 10, pp. 1403−1413.
- Majima H. // Flotation, 1967, № 32, pp. 31−36.
- Jange J.H., Wadsworth M.E. Extractive Metallurgy of Copper, Nickel, Cobalt // TMS, 1993, Vol. 1, pp. 689−707.
- Warren I.H. // Austral. J. Appl. Sci., 1958, Vol. 9, № 1, pp. 36−51.
- Доброхотов Г. Н, Майорова E.B. //ЖПХ, 1963, T.36, № 10, c.2148−2154.
- Чугаев Л.В., Масляницкий И. Н. // Науч. тр. (Гипроникель). Л., 1965, Т. 24, с. 31−47.
- Darms J. Gerlach, Pawlek F.Z. Erz. U I I Metallhutenw, 1967, Bd: 2, № 5, pp- 203−208.
- Соболь С.И., Горячкин В. И., Нелень И. М. и др. // Металлургия цветных металлов: Сб. научн. тр. Гинцветмета, М., Металлургия, 1969, № 29, с. 137−146.
- Мао М.Н., Peters Е. Hydromet. // Res. Dev. A. Plant Pract. Proc., 3 Int. Symp. Hydromet., 112 AIME Ann. Meet., 1983, pp. 243−260.
- Эргашев У., Набойченко С. (УГТУ-УПИ, 1992). Ссылка: Набойченко С. С., Ни Л. П., Шнеерсон Я. М., Чугаев Л. В. «Автоклавная гидрометаллургия цветных металлов.» Екатеринбург. 2002. с 156.
- OpreaF., Taloi D., Moldovan P. // Stud.cerc.metal., 1971, Vol. 6, № 1, pp. 13−16.
- Клюева A.B., Худяков И. Ф., Смирнов В. И. // Изв. Вузов. Цветная металлургия, 1964, № 1, с. 61−65.
- Пономарева Е.И., Соловьева В. Д., Ундасынова З. Д. Щелочные гидрохимические способы переработки полиметаллических продуктов. // Алма-Ата, Наука, 1969, с.45−49.
- Nagai Т., Kiuchi Н. // J. Ming. Inst. Jap., 1975, Vol. 91, № 1050, pp. 547−553.
- Bailey L.K., Peters E. // Canad. Metal. Quart., 1976, Vol. 15, № 4, pp. 333−334.
- Corriou J.P., Kikindai T.J. // Inorg. Nucl.Chem., 1981, Vol.43, № 1, pp. 9−12.
- Lowson R.T. // Chem.Rew., 1982, Vol.82, № 4, pp. 461−469.
- Huskey J.B., Schlitt W.J. // Interfacing Technologies in Solution Mining, SME-AIME, 1982, pp. 55−64.
- Cimenelli V.S.T., Osseo-Asare K. // Hydrometall. Reactor Design a. Kinetics, SME-AIME, Warrendale, Pa., 1986, pp. 129−147.
- Papangelakis V.G., Demopoulos G.P. Acid pressure oxidation of pyrite: reaction kinetics. // Hydrometallrgy, 1991, Vol.26, pp. 309−325.
- Georgiou D., Papangelakis V.G. Sulphuric acid pressure leaching of a limonitic laterite: chemistry and kinetics. // Hydrometallrgy, 1998, Vol.49, pp. 23−46.
- Susan A. Baldwin, George P. Demopoulos, and Vladimiros G. Papangelakis:
- Mathematical Modeling of the Zinc Pressure Leach Process. // Metallurgical and Materials Transaction B, Vol. 26B, 1995, pp. 1035−1047.
- Белоглазов И.Н., Морачевский А. Г., Жмарин E.E. Кинетические закономерности процессов растворения и выщелачивания. Москва, ГУЛ Издательский дом «Руда и металлы», 2000.
- Papangelakis V.G., Demopoulos G.P. Acid Pressure Oxidation of Arsenopyrite: parts I, II. // Can. Met. Quart 29, № 1, 1990, pp 1- 13.
- Dutrizac J.E., Pratt A.R., Chen T.T. Механизм растворения сфалерита в сернокислой среде содержащей сульфат железа (III). // Yazawa International Symposium, Metallurgical and Materials Processing: Principles and Technologies, Vol III, 2003, 440 p.
- Вигдорчик E.M., Шейнин А. Б. Математическое моделирование непрерывных процессов растворения. JL, Химия, 1971, 248 с.
- Вигдорчик Е.М., Шейнин А. Б., Фаянс В. Г. Математическое моделирование и оптимизация процессов автоклавного выщелачивания. // Труды ин-та Ги-проникель, № 35, 1967, с. 173−196.
- Шнеерсон Я.М., Вигдорчик Е. М., Ивановский В. В., Касаткин C.B. Кинетика автоклавного выщелачивания пирротиновых концентратов. // Цветные металлы, № 3, 1981, с. 34−37.
- Филиппов B.C., Шнеерсон Я. М. Выбор типа автоклава для окислительного выщелачивания пирротиновых концентратов. // Цветные металлы, № 9, 1982, с.22−25.
- Шнеерсон Я.М., Краснов А. Л., Кукин A.B., Вигдорчик Е. М., Филиппов Г. Ф., Сиркис А. Л. Кинетика высокотемпературного выщелачивания пирротиновых концентратов. // Цветные металлы, № 1, 1989, с. 17−20.
- Боровиков В.П. Популярное введение в программу STATISTICA. М, 1998, 267 с.
- Тюрин Ю.Н., Макаров А. А. Анализ данных на компьютере. М, 1995, 384 с.
- Filippou D., Rao Konduru, Demopoulos G. P. A kinetic stady on the acid pressure leaching of pyrrhotite. // Hydrometallurgy, 1997, Vol.47, pp.1−18.
- Краткий справочник физико-химических величин. Под редакцией Равде-ля А. А и Пономаревой A.M. Л.: Химия, 1983, 232 с.