Разработка рациональных режимов десульфурации стали в агрегате ковш-печь с использованием моделей нечеткой логики
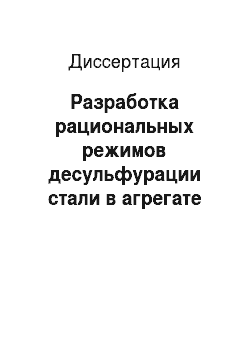
Порядок и время проведения операций определяют затраты энергетических и материальных ресурсов, поэтому схемы организации технологических процессов непрерывно совершенствуются. На развитии концепции построения АКП фокусируют усилия ведущие европейские производители металлургического оборудования: «SMS», «Demag», «VAI-FUCHS» (Германия), «Danielle» (Италия) и т. д. Все эти фирмы свои первые агрегаты… Читать ещё >
Содержание
- 1. Комплексный анализ влияния сырьевых и технологических параметров внепечной обработки стали на процесс десульфурации
- 1. 1. Анализ современной технологии обработки стали на агрегате «ковш-печь»
- 1. 2. Анализ технологических особенностей процессов внепечной обработки
- 1. 3. Влияние организации технологического маршрута ковша на его тепловое состояние перед внепечной обработкой
- 1. 4. Исследование проблемы оценки тепловых потерь через футеровку ковша
- 1. 5. Влияние режима перемешивания расплава аргоном на качество стали
- 1. 6. Влияние состава шлакообразующих на качество выплавляемой стали
- 1. 7. Проблема проведения глубокой десульфурации на АКП 39 1.9. Цели и задачи исследования
- 2. Исследование влияния технологических факторов на тепловое состояния установки печь-ковш путем математического моделирования в среде БипиПпк
- 2. 1. Возможности пакета Бішиїіпк для моделирования теплового состояния расплава стали в АКП
- 2. 2. Основные статьи энергобаланса АКП
- 2. 2. 1. Статьи поступления тепла
- 2. 2. 2. Статьи тепловых потерь агрегата
- 2. 3. Математическая модель АКП 64 2.3.1. Блоки приходных и расходных статей теплового баланса 65 2.3.2 Определение диапазона изменения статей потерь тепла
- 2. 4. Выводы по главе
- 3. Оценка влияния изменения производственных факторов на процесс десульфурации в АКП 79 3.1 Оценка энергоэффективности обработки расплава с помощью программы сортировки базы данных паспортов плавок
- 3. 1. 1. Описание программы сортировки
- 3. 1. 2. Обработка данных сортировки
- 3. 2. Расчет термодинамики и кинетики процесса десульфурации в АКП
- 3. 3. Оценка влияния нечеткоконтролируемых параметров на десульфурацию стали в АКП
- 3. 4. Выводы по главе
- 4. Разработка режима проведения интенсивной десульфурации на АКП с использованием математических моделей, построенных на основе нечеткой логики
- 4. 1. Выбор теоретической модели нечеткой логики для описания процессов обработки в АПК
- 4. 2. Разработка модели работы АКП на основе теории нечетких множеств
- 4. 2. 1. Реализация этапа «Фаззификация»
- 4. 2. 2. Формирование базы правил модели десульфурации
- 4. 3. Разработка технологии усовершенствованных режимов 112 десульфурации стали в АКП
- 4. 4. Выводы по главе 115 Основные
- выводы 116 Библиографический
- список
- Приложение
- Основные обозначения и сокращения
- АКП — агрегат ковш-печь,
- МНЛЗ — машина непрерывного литья заготовок,
- ККЦ — кислородно-конвертерный цех,
- АСУТП — автоматическая система управления технологическим процессом,
- УВС — установка вакуумирования стали,
- УУПС — установка усреднительной продувки стали,
- АДС — агрегат доводки стали,
- ТШС — твердые шлакообразующие смеси,
- ЭДУ — электродуговая установка
Разработка рациональных режимов десульфурации стали в агрегате ковш-печь с использованием моделей нечеткой логики (реферат, курсовая, диплом, контрольная)
Доля стали, обработанной внепечным способом, в мировом производстве ежегодно растет. Рост цен на расходные материалы и энергоносители, повышение требований к качеству стали остро ставят вопросы интенсификации процессов внепечной обработки и снижения их энергои материалоемкости.
В настоящее время качество стали — важнейшая характеристика для производителей, особенно это касается стали с низким содержанием серы, необходимой для трубной и танкерной промышленности. Качество стали зависит от множества параметров, характеризующих работу агрегатов в процессе выплавки и доводки стали. Известно, что для выплавки стали определенного сортамента необходимо соблюдать требования технологической инструкции: поддерживать требуемую температуру расплава, следить за химическим составом, обеспечивать режим продувки и т. д.
Обработка стали в агрегате ковш-печь (АКП) является неотъемлемой частью технологии производства высококачественного металла, обеспечивает увеличение производительности сталеплавильных агрегатов, экономию материальных и энергетических затрат, таких как электроэнергия, электроды, огнеупорные материалы и ферросплавы, повышение степени рафинирования стали от вредных примесей, гомогенизацию и стабилизацию металла по температуре и химическому составу, способствует расширению сортамента стали.
Порядок и время проведения операций определяют затраты энергетических и материальных ресурсов, поэтому схемы организации технологических процессов непрерывно совершенствуются. На развитии концепции построения АКП фокусируют усилия ведущие европейские производители металлургического оборудования: «SMS», «Demag», «VAI-FUCHS» (Германия), «Danielle» (Италия) и т. д. Все эти фирмы свои первые агрегаты ковш-печь построили в начале или середине 80-х годов прошлого века. На территории СССР первый агрегат ковш-печь был построен в 1985 г. Л проект ВНИИМЕТМАШ-ЮУМЗ) на Молдавском металлургическом заводе.
В течение последних двух десятилетий АКП непрерывно совершенствовались как в технологическом, так и в конструкционном плане. Это позволило достичь весьма высоких показателей как в части качества стали, так и в части энергои ресурсосбережения в технологической схеме её выплавки и разливки. Более того, на практике убедительно доказана высокая конкурентоспособность АКП практически для всего диапазона вместимости сталеразливочных ковшей: от 12−15 т до 350−360 т.
Цель работы. Повышение эффективности работы АКП при производстве сталей с низким содержанием серы за счет дополнительного учета влияния нечетко определяемых параметров процесса. Для достижения поставленной цели в работе решены следующие задачи:
• исследование влияния различных производственных факторов на технико-экономические показатели работы АКП;
• оценка влияния режима работы на динамику изменения статей энергетического баланса АКП в процессе работы;
• исследование влияния нечетко определяемых параметров на эффективность обработки стали на разработанной комплексной математической модели работы печи-ковша, построенной на основе теории нечетких множеств;
• создание методики разработки эффективных режимов глубокой десульфурации на основе анализа базы данных работы реального АКП с помощью специальной программы — анализатора.
Научная новизна работы заключается в следующем:
• впервые предложена методика оценки влияния нечетких технологических факторов на степень выполнения производственных задач для АКП;
• изучены и классифицированы нечеткие технологические факторы внепечной обработки;
• разработан алгоритм сортировки массивов данных для поиска энергои ресурсосберегающих режимов;
• разработана обучаемая математическая модель теплового состояния АКП, позволяющая оценивать текущую температуру расплава стали с учетом динамической коррекции нечетко измеряемых параметров.
Практическая значимость состоит в следующем:
• разработаны усовершенствованные режимы ведения плавки в АКП садкой 370 т, позволяющие уменьшить расход электроэнергии и материалов, с помощью разработанной математической модели для оценки динамики теплового состояния агрегата ковш-печь;
• разработана усовершенствованная технология ведения выплавки стали на АКП, обеспечивающая достижение максимально возможной степени десульфурации в заданных производственных условиях;
• создана универсальная математическая модель, на основе которой возможно разрабатывать режимы работы внепечных установок, позволяющие учитывать нечеткие технологические факторы.
Основные выводы.
1. Проведено исследование влияния технологической маршрутизации движения ковша по цеху на динамику изменения статей тепловых потерь АКП и на среднемассовую температуру расплава с помощью математической модели. Результаты расчетов показали, что основные потери, которыми можно управлять — это потери тепла в электродах, потери тепла излучением, а также потери с охлаждающей водой.
2. Создана модель теплового баланса АКП в среде 81тиНпк, способная оценивать динамические характеристики работы конкретного АКП. Адекватность модели подтверждена на 10 контрольных плавках, которые показали неточность оценки текущей температуры не более 5 °C. Модель может быть использована как советчик оператора в условиях временных ограничений на плавку и позволяет рекомендовать минимальное значение мощности, необходимое для получения заданной на выходе температуры.
3. Создана программа сортировки паспортов плавок для оценки влияния производственных факторов, в том числе нечетких, позволяющая находить факторы, определяющие эффективность обработки стали на данном агрегате. Выбраны нечеткие факторы и рассчитаны коэффициенты их влияния на термодинамику процесса десульфурации в АКП. Для условий ККЦ ОАО «ММК» наиболее важным фактором являлась температура на границе металл-шлак.
4. Разработаны усовершенствованные режимы обработки на основе анализа производственных баз данных для разных начальных условий и поставленных задач, созданная на основе математической модели расчета процесса десульфурации в АКП на основе теории нечеткой логики. Достоверность модели подтверждена сопоставлением результатов расчета с опытными плавками.
5. Разработаны технологические режимы проведения глубокой и быстрой десульфурации, которые могут служить основой для их применения на АКП различной емкости.
6. Разработаны усовершенствованные режимы десульфурации стали на АКП садкой 370 т, эффективность которых подтверждена опытными плавками.
Список литературы
- Совершенствование технологии внепечной обработки конвертерной стали / Сарычев А. Ф., Носов А. Д., Коротких В. Ф. и др. // Сталь. 2002. -№ 1. — С. 19−22.
- Основы технологии производства стали: Учебное пособие для вузов. / Поволоцкий Д. Я. 2-ое изд., испр. и дополн. — Челябинск: Изд-во ЮУрГУ, 2004.- 191 с.
- Сквяжин А. Г., Шевченко А. Д. Определение времени выравнивания состава и температуры жидкой стали в ковше при продувке нейтральным газом // Металлы. 1986. — № 1. — С.10−12.
- Внепечная обработка чугуна и стали. Кудрин В. А. М.: Металлургия, 1992.-280 с.
- Ковшевая доводка стали. Вихлевщук В. А., Харахулах B.C., Бродский С. С. Днепропетровск: Системные технологии, 2000 — 190с.
- Исследование процессов нагрева металла при внепечной обработке в агрегате печь-ковш / Харламов Д. А., Меркер Э. Э., Булгаков А. И. // Известия высших учебных заведений. Чёрная металлургия. 2002. -№ 3. С.26−28.
- Бейцун C.B., Жаданос A.B., Михайловский Н. В., Шаталюк C.B. Прогнозирование тепловых потерь через футеровку ковша при внепечной обработке стали // Металлургия: Сборник научных трудов. Запорожье: ЗДИА, 2004. -Вып.9. С.124−126.
- Бейцун C.B., Жаданос A.B. Исследование влияния износа футеровки ковша и массы расплава на тепловые потери через его футеровку// Металлургия: Сборник научных трудов. Запорожье: ЗДИА, 2005. -Вып.11. С.128−132.
- Влияние различных футеровочных материалов на тепловое состояние ковша внепечной обработки стали / Волкова Е., Бахман С. М., Шеллер
- П.Р. // Металлургия и горнорудная промышленность, 2006. № 7. — С. 314−320.
- Перятинский А.Ю. Прогнозирование температуры металла в 385-тонном сталеразливочном ковше при его прохождении от конвертера до MHJ13: Автореф. дис. канд. техн. наук. Магнитогорск: МГТУ, 2000. -23 с.
- Скорость массопереноса в процессах ковшевого рафинирования / Асаи Ш., Кавачи М., Мучи И. // Инжекционная металлургия'83. М.: Металлургия, 1986. — С.106−123.
- Модель циркуляционного течения в расплавленном металле для специального случая барботажа ванны и ее применение к процессам инжектирования газа / Сано М., Мори К. // Инжекционная металлургия'83. -М.: Металлургия, 1986. С. 124−134.
- Турбулентность и перемешивание в технологических процессах ковшевой металлургии / Эль-Кадах М., Зекели Дж. // Инжекционная металлургия'83. -М.: Металлургия, 1986. С. 90−105.
- Исследование на модели процессов перемешивания и массопереноса при ковшевой продувке / Янг К., Юн JI. Лю JI. // Инжекционная металлургия'83. М.: Металлургия, 1986. — С.135−146.
- Смирнов А.Н., Салмаш И. Н., Ошовская Е. В., Яремко A.B. Изучение процессов перемешивания стали в ковше при помощи физического и математического моделирования// Металлургия и горнорудная промышленность, 2006. № 7. — С.37−42.
- Романенко В.А., Гусев В. И., Кураев П. А., Воробьев В. В., Одайский Р. В. Энергосберегающее управление электрическим режимом дуговых печей// Металлургия: Сборник научных трудов. Запорожье: ЗДИА, 2005. -Вып.11. С.128−135.
- Самарин A.M. Физико-химические основы раскисления стали. -М.:Изд-во АН СССР, 1956. 162 с.
- Повышение качества стали массового назначения путем продувки вковше нейтральными газами / Я. А. Шнееров, А. Н. Чуйко, Е. М. Огрызкин и др. // Сталь. 1975. — № 8. — С.695−698.
- Лузгин В.П., Явойский В. И. Газы в стали и качество металла. М.: Металлургия, 1983. — 230 с.
- Еронько С.П., Биковских C.B. Физическое моделирование процессов внепечной обработки и разливки стали. К.: Техника, 1998. — 136с.
- Массо- и теплоперенос в 140-т установке ковш-печь переменного тока. Пиптюк В. П., Самохвалов С. Е., Павлюченков И. А. и др. // Сталь. -2007. -№ 11.-С. 46−50.
- Гулыга Д.В., Сущенко A.B. Моделирование динамики температуры металла в сталеразливочном ковше на участке конвертер МНЛЗ // Сталь.-2004.-№ 9.-С. 15−19.
- Обработка стали на установке печь-ковш. Технологическая инструкция. ТИ-101 -СТ-ККЦ-83−2008.
- Гомогенизация стали в ковше при продувке аргоном. Кадуков В. Г., Коган А. Е., Фомин H.A. и др. // Известия ВУЗов. Черная металлургия. -1986.-№ 10. С.46−49.
- Бигеев А. М., Бигеев В. А. Металлургия стали. Теория и технология плавки стали. Учебник для вузов, 3-е изд. перераб. и доп.
- Магнитогорск: МГТУ, 2000. 544 с.
- Математическое моделирование процесса перемешивания стали в агрегате печь-ковш / Смирнов А. Н., Салмаш И. Н., Ошовская Е. В., Седуш B.C. // Металлургия: научные труды Донецкого Научного Технического Университета. Вып. 102. Донецк, 2005, С.71−81.
- И.И.Борнацкий, В. И. Мачикин, В. С. Живченко. Внепечное рафинирование чугуна и стали. К.: Техника, 1979. — 168 с.
- Дюдкин Д.А., Бать С. Ю., Глинберг С. Е., Маринцев С. Н. Производство стали на агрегате печь-ковш. Донецк: ООО «Юго-Восток, Лтд», 2003, 300 с.
- Еронько С.П., Биковских C.B. Физическое моделирование процессов внепечной обработки и разливки стали. К.: Техника, 1998. — 136с.
- Основы производства стали: учебное пособие для колледжей, лицеев и техникумов / К. Н. Вдовин, А. Ю. Колесников. Магнитогорск: МГТУ, 2005.-203 с.
- Курагин О.В., Шкирмонтов А. П., Долбилов С. Б. Эффективные способы внепечной обработки специальных сталей. Обзор информ.//Ин-т «Черметинформация». М., 1990, 18 с.
- Асаи Ш., Кавачи М., Мучи И. Скорость массопереноса в процессах ковшевого рафинирования // Инжекционная металлургия'83. М.: Металлургия, 1986. — С. 106−123.
- Внепечная обработка стали: учебник для вузов. Поволоцкий Д. Я., Кудрин В. А., Вишкарев А. Ф. М: МИСиС, 1995.-256 с.
- Крамаров А. Д., Соколов А. Н. Электрометаллургия сталей и ферросплавов. М.: Металлургия, 1976. — 440 с.
- Пути ресурсосбережения при внепечной обработке стали / Дюдкин ДА., Гринберг С. Е., Грабов A.B. и др. // Сталь. 2002. — № 3. — С.55−56.
- Тахаутдинов Р. С. Производство стали в кислородно-конвертерном цехе Магнитогорского металлургического комбината. Магнитогорск,
- Магнитогорск: МГТУ, 2000. 544 с.
- Математическое моделирование процесса перемешивания стали в агрегате печь-ковш / Смирнов А. Н., Салмаш И. Н., Ошовская Е. В., Седуш B.C. // Металлургия: научные труды Донецкого Научного Технического Университета. Вып. 102. Донецк, 2005, С.71−81.
- И.И.Борнацкий, В. И. Мачикин, В. С. Живченко. Внепечное рафинирование чугуна и стали. К.: Техника, 1979. — 168 с.
- Дюдкин Д.А., Бать С. Ю., Глинберг С. Е., Маринцев С. Н. Производство стали на агрегате печь-ковш. Донецк: ООО «Юго-Восток, Лтд», 2003, 300 с.
- Еронько С.П., Биковских C.B. Физическое моделирование процессов внепечной обработки и разливки стали. К.: Техника, 1998. — 136с.
- Основы производства стали: учебное пособие для колледжей, лицеев и техникумов / К. Н. Вдовин, А. Ю. Колесников. Магнитогорск: МГТУ, 2005.-203 с.
- Курагин О.В., Шкирмонтов А. П., Долбилов С. Б. Эффективные способы внепечной обработки специальных сталей. Обзор информ.//Ин-т «Черметинформация». М., 1990, 18 с.
- Асаи ILL, Кавачи М., Мучи И. Скорость массопереноса в процессах ковшевого рафинирования // Инжекционная металлургия'83. М.: Металлургия, 1986. — С. 106−123.
- Внепечная обработка стали: учебник для вузов. Поволоцкий Д. Я., Кудрин В. А., Вишкарев А. Ф. М: МИСиС, 1995. — 256 с.
- Крамаров А. Д., Соколов А. Н. Электрометаллургия сталей и ферросплавов. М.: Металлургия, 1976. — 440 с.
- Пути ресурсосбережения при внепечной обработке стали / Дюдкин Д. А., Гринберг С. Е., Грабов A.B. и др. // Сталь. 2002. — № 3. — С.55−56.
- Тахаутдинов Р. С. Производство стали в кислородно-конвертерном цехе Магнитогорского металлургического комбината. Магнитогорск, 2001.-148 с.
- Харламов Д.А., Меркер Э. Э. Разработка алгоритма управления шлаковым режимом внепечной обработки стали // Энергосбережение и энергоэффективные технологии 2004. 4.2: Сб. докл. Всерос. науч.-техн. конференции. -Липецк, 2004. С.238−241.
- Смирнов H.A. Оптимизация технологии десульфурации стали на установкепечь-ковш // Электрометаллургия. 2004. — № 1. — С.20−28.
- Прогноз и применение емкостей металлургических шлаков / Соммервиль И. Д. // Инжекционная металлургия'86. М.: Металлургия, 1990. — С.107−120.
- Дюдкин Д.А., Маринцев С. Н. Оптимизация состава рафинировочного шлака // Сталь, 2003, № 5, С. 17−19.
- Д.А.Дюдкин., С. Е. Гринберг. Оптимизация режимов внепечной обработки стали / Труды 8 конгресса сталеплавильщиков, 18−22 октября 2004, Нижний Тагил.
- Сарычев А.Ф., Носов А. Д., Коротких В. Ф., и др. Освоение технологии внепечной обработки стали на установке печь-ковш конвертерного цеха ММК // Совершенствование технологии на ОАО «ММК». Сб. трудов ЦЖ. Магнитогорск. 2001. Вып.6. С.52−57.
- Кудрин В.А. Теория и технология производства стали: Учебник для вузов. М.: Мир, 2003. — 528 с.
- Holappa L. Rewiev of ladle metallurgy // Japan Journal of Metals. 1980. -9. — № 6. — P.261−266.
- Дюдкин Д.А., Бать С. Ю., Глинберг C.E., Кислиенко В. В., Онищук В. П. Внепечная обработка расплава порошковыми проволоками Донецк: ООО «Юго-Восток, Лтд», 2002, 296 с.
- Методика расчета технологических параметров работы ДСП-60 для снижения расхода электроэнергии и увеличения выхода годного / Страшное М. М., Кац Я. Л. // Черные металлы. 2006. — № 4. — С.14−16.
- Некоторые аспекты технологии и конструкции агрегатов ковш-печь / Д. А. Дюдкин., С. Е. Гринберг // Труды 8 конгресса сталеплавильщиков, 18−22 октября 2004, Нижний Тагил.
- Энергетический баланс печи-ковша / Хопман В., Фетт Ф. Н., Клагес Т. // Чёрные металлы. 1988. № 18. С. 18−25 .
- Егоров А. В. Расчет мощности и параметров электропечей черной металлургии. Учеб. пособие для вузов. М.: Металлургия, 1990, 280 с.
- Тепловые потери в четырехсоттонных ковшах / Миляев А. Ф., Перятинский А. Ю. // Научно-техническая конференция «Новые технологические процессы в литейном производстве», Омск, 1997. -С.36−37.
- П.П.Арсентьев. Аргон в металлургии. М.: Энергоатомиздат, 1971 -118 с.
- Ячиков И.М. Интенсификация массопереноса в электропечах постоянного тока: Монография. Магнитогорск: МГТУ, 2002. — 130 с.
- Гомогенизация стали в ковше при продувке аргоном / Электрометаллургия стали и ферросплавов / В. Г. Кадуков, А. Е. Коган, Н. А. Фомин, М. Б. Оржех, Е. Ф. Демичев // Известия высших учебных заведений. Черная металлургия 1986. — N 10. — С.46−49.
- Сквяжин А. Г., Шевченко А. Д. Гомогенизация жидкой стали в ковшепри продувке нейтральным газом // Металлы, № 3, 1988 г, С. 17−21.
- Дюдкин Д.А., Гринберг С. Е. Оптимизация режимов внепечной обработки стали на выпуске и в агрегате ковш-печь // Электрометаллургия. 2005. — № 12. — С.23−25.
- Совершенствование технологии внепечной обработки стали на белорусском металлургическом заводе. Гуненков В. Ю., Тищенко В. А., Пивцаев В. В. и др. // ОАО «Черметинформация». Бюллетень «Черная металлургия». 2004. — № 11. — С. 26−30.
- Вихлевщук В.А., Харахулах B.C. Обработка стали на внепечных установках: Днепропетровск: Системные технологии, 2001 — 175 с.
- Коваленко А.Ю. Расчет электрических потерь энергии в питающей сети при работе агрегата «ковш-печь» //Вестник МГТУ им. Г. И. Носова, 2006.-№ 2.-С. 26−28.
- Н. Katayama, Н. Kajioka. Dephosphorization of high chromium molten steel with CaC2-CaF2 flux. ISIJ Int. 1979. vol. 19 p. 635−643.
- G. J. Kor, E. T. Turkdogan. Vaporization of iron and phosphorous from iron-phosphorous melts in oxygen bearing gas systems.// Met. Transactions B, 1975. vol. 1. 6B.
- A. Gustavson, B. Melburg. Termodinamics of reducing Desolphorization of manganese and manganese ferroalloys. ISIJ Int. 1992. vol. 32 p. 1076−1080.
- H. Suito, R. Inoue and M. Takada. ISIJ International //vol. 21, 1981, p. 25 047. H. Suito, R. Inoue and M. Takada. ISIJ International //vol. 24, 1984, №l, p 40−53.