Повышение эффективности вертикальных компостирующих установок путем разработки устройства снижения уплотнения
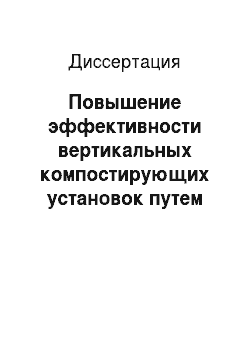
Господствовавшая в последнее время в нашей стране концепция интенсификации сельскохозяйственного производства, в практической ее реализации, слабо учитывала комплекс экологических проблем, возникших в результате резкого возрастания антропогенных нагрузок на природную среду. Начиная с 60-х годов прошлого столетия, земледелие в нашей стране развивалось за счет непрерывного наращивания средств… Читать ещё >
Содержание
ИЗ СОВРЕМЕННЫХ ТЕХНОЛОГИЙ И ТЕХНИЧЕСКИХ СРЕДСТВ £ОТКИ ОТХОДОВ СЕЛЬСКОХОЗЯЙСТВЕННОГО ЮДСТВА. ib навоза в повышении плодородия почв и улучшения экологической ализ технологий и технических средств ускоренного стирования. зор устройств снижения уплотнения компостируемого материала. 27 снологические требования к материалу при его компостировании в: альных установках с устройством снижения уплотнения в виде L тросов.
2.5 Определение значения сводообразующего слоя
2.6 Анализ взаимодействия рабочего органа устройства с материалом в процессе пересыпания.
2.7 Определение массы накопителя потенциальной энергии.
2.8 Выводы.
3 ПРОГРАММА И МЕТОДИКА ЭКСПЕРИМЕНТАЛЬНЫХ ИССЛЕДОВАНИЙ.
3.1 Программа экспериментальных исследований.
3.2 Методика определения физико-механических свойств соломонавозной смеси.
3.3 Определение зависимости максимального расстояния между рабочими органами устройства снижения уплотнения от слоя материала.
3.4 Определение степени спелости компоста.
3.5 Определение изменения влажности соломонавозной смеси по высоте этажа.
3.6 Определение работоспособности устройства снижения уплотнения.
3.7 Методика обработки экспериментальных данных.
4 РЕЗУЛЬТАТЫ ЭКСПЕРИМЕНТАЛЬНЫХ ИССЛЕДОВАНИЙ И ИХ АНАЛИЗ.
4.1 Результаты определения степени спелости компоста на основе соломонавозной смеси.
4.2 Результаты исследования физико-механических свойств соломонавозной смеси.
4.3 Проверка адекватности теоретических зависимостей для определения расстояния между рабочими органами устройства по условиям сводообразования и сводоразрушения.
4.5 Поиск уровней варьирования факторов при оптимизации.
4.6 Определение оптимальных конструктивных параметров устройства снижения уплотнения.
4.7 Сохранение пористости соломонавозной смеси по высоте вертикальной компостирующей установки.
4.8 Выводы.
5 ПРОИЗВОДСТВЕННАЯ ПРОВЕРКА И ЭКОНОМИЧЕСКАЯ ЭФФЕКТИВНОСТЬ РЕЗУЛЬТАТОВ ИССЛЕДОВАНИЙ.
5.1 Опытно-производственная проверка работы вертикальной компостирующей установки с устройством снижения уплотнения.
5.2 Технико-экономическая оценка результатов исследований.
Повышение эффективности вертикальных компостирующих установок путем разработки устройства снижения уплотнения (реферат, курсовая, диплом, контрольная)
Практическая реализация научной концепции использования органического сырья основана на том, что в нем содержится большое количество ценных питательных веществ в виде азота, фосфора, калия, белка, жира, углеводов и других соединений. Поэтому все исследования, направленные на их эффективное повторное использование в качестве удобрений, позволят создать безотходные ресурсосберегающие технологии в АПК и, соответственно, обеспечить дополнительную поставку продовольствия населению РФ [1, 2, 3, 4].
Внесение органических удобрений, произведенных традиционным способом компостирования в буртах на открытых площадках, нецелесообразно из-за потери питательных веществ и наличия личинок гельминтов и семян сорных растений, что в совокупности сводит к нулю положительный эффект их использования [4].
В настоящее время все большее распространение получают способы компостирования в камерных установках, которые имеют теплоизолированный корпус, благодаря чему, за счет лучшего сохранения тепла биотермической реакции (65.85°С), обеспечивается стерилизация конечного продукта. Данные способы позволяют получать органическое удобрение высокого качества в более сжатые сроки. Сокращение времени созревания компоста обеспечивается созданием оптимальных условий для протекания биотермического процесса, одним из которых является активная аэрация компостируемой массы. Эффективность аэрации, в основном, зависит от пористости материала. Поддержание пористости по всей высоте установки достигается различными способами: перемешиванием в медленно вращающихся установках барабанного типа, пересыпанием с этажа на этаж в установках вертикального типа и т. п. Эти операции значительно повышают энергоемкость процесса компостирования. Помимо этого, производительность установок поточно-непрерывного типа в значительной мере сдерживается их объемом, так как увеличение их поперечных размеров неизбежно приводит к значительному увеличению себестоимости конечного продукта.
В связи с этим, задача, заключающаяся в снижении удельных энергозатрат на производство органических удобрений за счет увеличения вертикальных размеров установки, без ухудшения аэрационного режима, является актуальной.
Работа выполнена в соответствии с Федеральной программой фундаментальных и приоритетных прикладных исследований «Разработать высокопроизводительную технику нового поколения для производства конкурентоспособной продукции животноводства и птицеводства, производства комбикормов в хозяйствах, уборки, переработки навоза и подготовки высококачественных органических удобрений» на 2006;2010 гг.
ЦЕЛЬ РАБОТЫ. Повышение эффективности установки для компостирования путем разработки устройства снижения уплотнения. v>
ОБЪЕКТ ИССЛЕДОВАНИИ. Технологический процесс перемещения компостируемого материала в корпусе установки вертикального типа.
ПРЕДМЕТ ИССЛЕДОВАНИИ. Закономерность взаимодействия рабочих органов устройства снижения уплотнения с материалом в процессе его компостирования в установке вертикального типа.
МЕТОДИКА ИССЛЕДОВАНИЙ. Теоретические исследования базируются на теории сводообразования, рубящего и скользящего резания. Физико-механические свойства определяли в соответствии с действующими ГОСТ, ОСТ и частными методиками. Результаты теоретических исследований подтверждали экспериментальной проверкой на лабораторных и опытно-производственных установках. Адекватность теоретических положений проверяли по критериям согласия К. Пирсона и Р. Фишера.
НАУЧНАЯ НОВИЗНА. Научную новизну составляют: закономерность изменения степени уплотнения материала от его слоя и времени слеживаниятеоретическая зависимость конструктивных параметров устройства снижения уплотнения от физико-механических свойств компостируемого материала;
— аналитическая модель взаимодействия рабочего органа устройства с компостируемым материалом в процессе его перемещения в установке.
ПРАКТИЧЕСКАЯ ЦЕННОСТЬ РАБОТЫ заключается в разработке конструкции и обосновании оптимальных параметров устройства снижения уплотнения компостируемого материала, позволяющих повысить эффективность установки вертикального типа за счет увеличения высоты при сохранении пористости, что ведет к увеличению производительности и снижению удельных энергозатрат.
РЕАЛИЗАЦИЯ РЕЗУЛЬТАТОВ ИССЛЕДОВАНИЙ.
Разработанное устройство снижения уплотнения компостируемого материала в установке вертикального типа прошло опытно-производственную проверку при переработке соломонавозной смеси на ферме КРС ФГУП учхоз-племзавод «Комсомолец» ФГОУ ВПО Мичуринский ГАУ (Приложение К).
Предложенная конструкция разработанного устройства снижения уплотнения принята к внедрению в НТЦ «Агроферммашпроект» ГНУ ГОСНИТИ (Приложение М) и научно-производственной фирме ООО «Мичуринское плодородие» (Приложение Л) с целью повышения эффективности работы установок ускоренного компостирования.
Методические материалы по определению конструктивных параметров устройства снижения уплотнения компостируемого материала используются в учебном процессе Тамбовского ГТУ (Приложение Н) и Мичуринского ГАУ.
АПРОБАЦИЯ. Основные положения диссертационной работы доложены и одобрены: на Всероссийском конкурсе среди учащейся молодежи высших учебных заведений РФ ФГОУ ВПО Саратовский ГАУ (г. Саратов, 2004 г.) — на международной науч.-практич. конференции, посвященной 75-летию со дня рождения профессора В. Г. Кобы ФГОУ ВПО Саратовский ГАУ (г. Саратов, 2006 г.) — на международной науч.-практич. конференции «Современные проблемы технологий производства, хранения, переработки и экспертизы качества с/х продукции» ФГОУ ВПО Мичуринский ГАУ (г. Мичуринск, 2007 г.) — на международной науч.-практич. конференции «Научно-технический прогресс в животноводстве — машинно-технологическая модернизация отрасли» ГНУ ВНИИМЖ (г. Подольск, 2007 г.) — на международной науч.-практич. конференции «Научно-технический прогресс в животноводстве — ресурсосбережение на основе создания и применения инновационных технологий и техники» ГНУ ВНИИМЖ (г. Подольск, 2008 г.) — на всероссийском конкурсе на лучшую работу среди аспирантов и молодых ученых высших учебных заведений Министерства сельского хозяйства Российской Федерации ФГОУ ВПО РГСХА (г. Рязань, 2008 г.).
Результаты научной работы использовались при создании оборудования технологической линии для производства высококачественного экологически безопасного органического удобрения, продукция которой отмечена золотой медалью на 3-й Всероссийской выставке «День садовода-2008» (Приложение П).
ПУБЛИКАЦИИ. Материалы диссертации отражены в 15 печатных работах, в том числе 3 работы в изданиях, рекомендованных ВАК РФ. Общий объем публикаций составляет 7,8 п.л., из которых 2,4 п.л. принадлежат лично соискателю. Техническая новизна работы подтверждена наличием 1 патента РФ на изобретение и 2 патентов РФ на полезную модель.
1 АНАЛИЗ СОВРЕМЕННЫХ ТЕХНОЛОГИЙ И ТЕХНИЧЕСКИХ СРЕДСТВ ПЕРЕРАБОТКИ ОТХОДОВ СЕЛЬСКОХОЗЯЙСТВЕННОГО ПРОИЗВОДСТВА.
1.1 Роль навоза в повышении плодородия почв и улучшения экологической среды.
Господствовавшая в последнее время в нашей стране концепция интенсификации сельскохозяйственного производства, в практической ее реализации, слабо учитывала комплекс экологических проблем, возникших в результате резкого возрастания антропогенных нагрузок на природную среду. Начиная с 60-х годов прошлого столетия, земледелие в нашей стране развивалось за счет непрерывного наращивания средств химизации [5]. Огромные, зачастую неконтролируемые дозы минеральных удобрений и ядохимикатов в растениеводстве, позволившие на начальном этапе значительно повысить урожайность сельскохозяйственных культур, долгое время не изучались как антропогенный фактор воздействия на природу [6, 7]. Однако давно известно, что любые антропогенные воздействия на экосистемы неизбежно приводят к нарушению естественного биологического круговорота веществ в природе, и иногда такие нарушения могут стать необратимыми. К результатам такого вмешательства в естественные процессы круговорота веществ в природе можно отнести деградированние и разрушение структуры почвы, ее заражение в крайне опасных дозах нитратами, ядохимикатами и другими веществами, делающими непригодными для здорового питания выращиваемую продукцию [8].
За последние 20 лет площадь деградированных земель в России увеличилась в 1,6 раза, запасы гумуса уменьшились на 30−50%, а 88% пашни имеют содержание гумуса ниже оптимального, ежегодно его теряется более.
84 млн. т. Пахотных земель, отвечающих международным стандартам, у нас осталось около 8% [3, 5].
Проблема создания положительного баланса гумуса в почве — одна из наиболее актуальных в земледелии нашей страны. Только при оптимальном гумусовом состоянии почв возможна реализация интенсификации земледелия и получение высокого эффекта от внедрения новых высокоурожайных сортов и высокопродуктивных сельскохозяйственных культур. Высокое содержание гумуса в почве снижает поступление токсических веществ в сельскохозяйственные растения. Благодаря его высокой емкости поглощения, токсические вещества связываются и длительное время удерживаются в почве, не поступая в растения [1, 9, 10, 11].
Другой нерешенной проблемой сельского хозяйства является утилизация сельскохозяйственных отходов. Основным загрязняющим фактором признано считать органические отходы животноводческих ферм и птицефабрик. Увеличение количества крупных хозяйств с поголовьем в несколько тысяч голов, привело к значительной концентрации объемов органических отходов. Отходы животноводческих предприятий обладают высокой биологической активностью, содержат большое количество патогенных микроорганизмов и семян сорных растений, приводящих к возникновению серьезных проблем экологического характера [1,4, 14].
Практическая реализация научной концепции использования данного органического сырья основана на том, что в нем содержится большое количество ценных питательных веществ в виде азота, фосфора, калия, белка, жира, углеводов и других соединений. Поэтому все исследования, направленные на их эффективное повторное использование в качестве удобрений, позволят создать безотходные ресурсосберегающие технологии в АПК и, соответственно, обеспечить дополнительную поставку продовольствия населению РФ [4, 12, 13, 16, 24].
В настоящее время существует множество технологий и технических средств, реализующих переработку органических отходов. Производственная проблема заключается в ограниченности объемов перерабатывающих установок, а так же относительно высокой себестоимости конечного продукта, что делает не выгодным его использование в условиях сельскохозяйственного производства.
В связи с разнообразием территориальных, климатических, почвенных и других специфических условий и особенностей строительства животноводческих комплексов в России, проблема утилизации органических отходов в настоящее время до конца не решена. Сложность реализации инженерно-технических проблем утилизации сельскохозяйственных отходов и повышения плодородия почв выдвинули задачу создания эффективного способа переработки, способного удовлетворить потребности агропромышленного комплекса.
1.2 Анализ технологий и технических средств ускоренного компостирования.
В настоящее время одной из основных технологий биоконверсии сельскохозяйственных отходов является метановое сбраживание (анаэробное компостирование), при котором разложение органического субстрата происходит в закрытых емкостях без доступа кислорода, основным конечным продуктом является метан. Данный способ рекомендуется применять при переработке органических отходов высокой влажности (не менее 92%) [1, 4, 17, 18, 19]. По окончании процесса брожения остаток выносится на поля в качестве жидкого органического удобрения. Органические удобрения, полученные таким способом, обеззараживаются не полностью, имеют низкие питательные свойства. Основным недостатком данного способа является то, что процесс анаэробного сбраживания происходит при температуре минимум +33°С, т. е. необходимо постоянно поддерживать температуру смеси за счет внешнего источника тепла. Как правило, для этого используют теплоту сгорания полученных в результате брожения газов. Другим недостатком анаэробного разложения является высокая стоимость капитальных вложений при строительстве установок [1]. Совокупность недостатков данного способа переработки делает не выгодным его использование в природно-климатических условиях нашей страны, поэтому все больше в настоящее время предпочтение отдается аэробным способам компостирования.
Компостирование — это экзотермический процесс биологического окисления, в котором органический субстрат подвергается аэробной биодеградации смешанной популяцией микроорганизмов в условиях повышенной температуры и влажности [15]. Органическим субстратом служат отходы животноводческих ферм и птицеводческих фабрик (навоз, помет), растительные остатки сельскохозяйственных и пищевых перерабатывающих предприятий (солома, опилки, жом, жмых и т. д.) [22]. В процессе биодеградации органический субстрат претерпевает физические и химические превращения с образованием стабильного гумифицированного конечного продукта — компоста. Этот продукт представляет ценность для сельского хозяйства как органическое удобрение и как средство, улучшающее структуру почвы [4, 6, 7, 14, 23].
Способ аэробного компостирования в буртах на открытых площадках (рисунок 1.1) получил широкое распространение благодаря низкой трудоемкости и высокой производительности процесса. Данный способ реализуется технологией компостирования в валках и статичных буртах [4, 20,21,23,25,26, 27].
Компостирование без усиленной принудительной аэрации является аэробно-анаэробным процессом, поскольку в слое материала на глубине более 15 см недостаток кислорода лимитируется скоростью аэробного процесса, а в глубинных слоях идут анаэробные процессы. Для активной аэрации по всей глубине слоя при компостировании в валках используют мобильные агрегаты, которые перемешивают материал, обогащая его атмосферным кислородом. Периодичность ворошения зависит от степени разложения субстрата и его влажности [28, 29, 30, 31, 42]. Активная аэрация при компостировании в статичном бурте достигается путем укладки в его основание перфорированной трубы по всей длине. Труба подсоединяется к напорному вентилятору, а режим его работы определяется готовностью компоста [25].
Ускоренное компостиробанио органического сырья.
—-L—.
I по способу | б траншеях по принципу дейстдия цикличЕСкаго.
3 |.
1 1 L модульного 1 поточно-НЕпрерыЬного по mujyjcjnoHodKu }.
Вертикального барабанного.
Рисунок 1.1 — Схема классификации способов аэробного компостирования.
К недостаткам компостирования в буртах можно отнести: — потребность в больших площадяхзависимость от погодных условийконечный продукт — низкого качества, так как в нем после переработки сохраняется большое количество всхожих семян сорных растений и патогенная микрофлоранизкую концентрацию питательных веществ в компостной массе, что снижает ее ценность как удобрение, повышая тем самым транспортные расходы при его внесенииналичие резкого неприятного запахапри ненадлежащем улавливании стоков высока вероятность загрязнения грунтовых вод.
Поэтому компостирование в буртах на открытых площадках является малопригодными для производства органических удобрений.
Аэрацию при компостировании в траншеях проводят при помощи специальных агрегатов, которые движутся над траншеей по специальным направляющим, вороша материал таким образом, что он постепенно передвигается от одного края траншеи, где производится загрузка свежего сырья, к другому, где отбирается готовый продукт [32, 33]. Боковые стенки траншеи позволяют сохранять тепло биотермической реакции, благодаря чему биотермический процесс идет более интенсивно, но, вместе с тем, ухудшают условия пассивной аэрации, когда воздух проникает в материал за счет конвекции, как это происходит при компостировании в буртах на открытых площадках. Это увеличивает периодичность ворошения, следствием чего является высокая энергоемкость процесса. К недостаткам данного способа можно так же отнести высокие капительные вложения при строительстве траншей и относительно низкую производительность. В совокупности, недостатки компостирования в траншеях делают его использование не выгодным в условиях сельскохозяйственного производства.
В настоящее время предпочтение отдается способу компостирования в камерных установках, при котором сокращается время компостирования и обеспечивается полное обеззараживание компостируемой смеси [4, 21, 34, 35, 36, 37]. В результате чего получается конечный продукт более высокого качества, помимо этого, процесс компостирования происходит в закрытой емкости (цилиндрической или прямоугольной формы), что позволяет существенно снизить количество выбросов вредных веществ в атмосферу.
Наиболее распространенным камерным способом является компостирование в установке модульного типа (биоферментаторе) циклического действия (рисунок 1.2).
1 — ферментатор размером 5×10×4,5 м- 2 — ворота- 3 — компостная смесь- 4, 5.
— напорный и вытяжной вентиляторы- 6 — система напорных воздуховодов- 7.
— пульт управления- 8 — отверстия для замера температуры и содержания кислорода в смеси.
Рисунок ! .2 — Стационарный биоферментатор для приготовления компоста многоцелевого назначения ГНИУ ВНИИМЗ.
Данная установка разработана творческим коллективом ГНИУ ВНИИМЗ под руководством академика Россельхозакадемии Н. Г. Ковалева [4, 21, 38]. Установка модульного типа представляет собой закрытое помещение с системой аэрации, выполненной в виде перфорированных труб или решет [39]. Принципиально похожую схему имеет технология, разработанная компанией New England (рисунок 1.3) [40, 41]. Заполнение установки осуществляется при помощи фронтального погрузчика, прицепа навозоразбрасывателя или системы транспортеров (рисунок 1.4) [43], после чего материал компостируется в течение 8−12 суток, затем свежий компост полностью выгружают из помещения и закладывают новую партию. Недостатком данной технологии является цикличность, и, как следствие, длительность процесса компостирования. После загрузки необходимо некоторое время, за которое материал саморазогревается до «рабочей» температуры 50−60°С, обеспечивающей обеззараживание материала от личинок гельминтов и семян сорных растений. воздушная рециркуляционная петля, комьютёр-контроллер системы управления воздухо! поступление обогащенного воздуха-8ытяжн0й воздух к системе контроля" 4 бетонные тоннел.
АЭРДЦИОННЫЙ ПЛЕНУМ компостируемая смесь входная дверь.
Рисунок 1.3 — Установка модульного типа фирмы New England приемка транспортировка и подача сырья отгрузка трактором компрессор t D управление бункеры компостирования.
Рисунок 1.4 — Установка модульного типа фирмы Биокомплекс.
Более прогрессивной является технология, основанная на установках модульного типа поточно-непрерывного действия (рисунок 1.5) [44−49]. Порционная выгрузка свежего компоста осуществляется из донной части установки, при этом большая часть компостируемого материала остается внутри, благодаря чему загружаемый сверху свежий слой сырья подогревается уже разогретыми до «рабочей» температуры нижележащими слоями. Система аэрации располагается в нижней части модуля, благодаря чему горячий воздух движется снизу вверх, в противоток компостируемому материалу. Это позволяет снизить время компостирования до 7 суток [4, 32], при удельных энергозатратах 1,5−3 кВт-ч/т (УЭК-5) [4].
Рисунок 1.5 — Схема цеха компостирования на базе установок УЭК-5, разработанных НТЦ «Агроферммашпроект» ГНУ ГОСНИТИ.
Движение воздуха в материале обеспечивает поступление кислорода к микроорганизмам и отвод углекислого газа и других метаболитов, образующихся в процессе их жизнедеятельности. Основным недостатком компостирования в данных установках является то, что постепенное слеживание материала, значительно снижает его пористость, а следовательно, и эффективность аэрации.
Периодическое разрыхление компостируемого материала при пересыпании реализуется в технологии, включающей в себя установку барабанного типа (рисунок 1.6) [4, 32, 50−54]. Основным элементом данной технологии является вращающийся барабан с системой аэрации, распределенной по его цилиндрической поверхности. Данная технология так же является поточно-непрерывной, загрузка происходит с одного конца барабана, выгрузка — с другого. Снижение времени саморазогрева свежего сырья осуществляется за счет передачи ему тепла беотермической реакции при смешивании, во время вращения барабана. За счет периодического вращения барабана создается постоянная довольно высокая пористость компостируемого материала, что значительно повышает эффективность аэрации, а, следовательно, и интенсивность процесса разложения органического вещества. Время компостирования в установках барабанного типа составляет до 12-ти суток [4, 32, 50, 51].
Рисунок 1.6 — Установка барабанного типа поточно-непрерывного действия, разработанная ГНИУ СЗНИИМЭСХ.
Основным их недостатком является высокая металлоемкость конструкции и энергоемкость процесса, при относительно низкой производительности (удельные энергозатраты составляют до 3−4 кВт-ч/т).
Это объясняется тем, что до 25% мощности уходит на вращение корпуса установки.
Установки вертикального (или силосного) типа (рисунок 1.7) представляют собой закрытые емкости. Конструктивной особенностью данных установок является форма их корпуса, который разделен по вертикали на этажи, соответствующие отдельным стадиям процесса. ч ошхг 111.
D™ Q п>
CP гттт пш.
111 It j-i) i i).
Ш~П ^ тшз^.
Направление движения компостируемого материала. —- аэрирующего воздуха.
Рисунок 1.7 — Установка ускоренного компостирования Фертилья.
Подготовленная к компостированию смесь на верхнем этаже устройства попадает в условия, стимулирующие начало интенсивного процесса компостирования. На верхнем этаже компостируемый материал аэрируется воздухом, нагретым в нижележащих этажах. Возможность поэтажного регулирования влажностных, аэрационных, тепловых процессов и внесение на определенных этажах бактериальных заквасок, выгодно отличает этот метод от других. Пористость материала поддерживается постепенным его перемешиванием и пересыпанием с этажа на этаж в процессе компостирования. Данные установки имеют высокие удельные энергозатраты — до 4−6 кВт*ч/т (Фертилья Ирп-Томас), связанные с работой устройств поддерживающих пористость материала [55]. Срок компостирования в установках такого типа составляет не более 4.5 суток.
Основным недостатком таких установок является высокая энергоемкость процесса направленного на перемешивание компостируемого материала и пересыпание его с этажа на этаж.
Другим способом поддержания пористости по высоте установки вертикального типа является внесение в компостируемую массу специального разрыхлителя в виде крупных древесных отходов или синтетических материалов (например, резанных резиновых покрышек). Роль разрыхлителя в данном случая заключается в создании матрицы, своеобразного «скелета», опираясь на который компостируемый материал менее уплотняется [56]. Такой способ разрыхления в своих установках применяют компании The TEG Group pic (рисунок 1.8) и VCU Europe Ltd (рисунок 1.9) [57, 58]. a) 6) a) — технологическая схемаб) — общий вид цеха Рисунок 1.8 -Производство компоста с использованием вертикальных компостирующих установок (TEG Silo cage) компании The TEG Group pic.
Отличительной особенностью установок компании VCU Europe Ltd является применение пассивной аэрации, которая осуществляется за счет эффекта «дымохода». При площади основания установки около 2,5 м² и высоте около 5 м, за счет движения разогретого теплом биотермического процесса воздуха вверх создается тяга, благодаря которой засасывается свежий атмосферный воздух в нижнюю часть установки. В данном случае, помимо разрыхлителя, необходимым условием поддержания пористости на высоком уровне является контроль влажности исходного сырья, которая должна находиться в строгих пределах 50−60% [58]. а) б) а) — технологическая схемаб) — общий вид цеха.
Рисунок 1.9 — Производство компостов с использованием вертикальных компостирующих установок (VCU) фирмы VCU Europe Ltd Недостатком использования разрыхлителя является необходимость равномерного смешивания его с исходным сырьем и отделения его от готового компоста. Данные энергоемкие операции значительно повышают себестоимость конечного продукта [59].
В результате обзора технологий и технических средств, реализующих способ ускоренного аэробного компостирования органических отходов, установлено, что метод компостирования в буртах на открытых площадках не обеспечивает полного обеззараживания компостируемой смеси, поэтому не может быть использован в качестве самостоятельной технологии.
Преимуществом камерных установок, благодаря теплоизолированному корпусу, является гарантированное обеззараживание материала, но его основным недостатком является высокая энергоемкость процесса при малой производительности, которая ограничивается объемом установки. Поэтому полный цикл компостирования в камерной установке не является рациональным. Решением данной производственной задачи является использование технологии, которая включала бы в себя оба способа компостирования.
Процесс компостирования в естественных условиях принято разделять на четыре основные стадии: разогрев (мезофильная) — активное горение (термофильная) — остывание и созревание (гумификация) [1, 15].
Гумификация компоста очень сложный химико-микробиологический процесс, который может длиться годами. Данный процесс можно осуществлять в промышленных условиях при помощи вермикомпостирования [60]. Но данная технология, вследствие своей специфики, мало поддается механизации и автоматизации, и при низкой производительности процесса не оправдывает высоких затрат на ее реализацию для нужд сельского хозяйства. Поэтому промышленная переработка органических отходов в больших объемах включает в себя только три первые стадии компостирования, а гумификация компоста происходит уже после его внесения в почву за счет содержащейся в ней микрофлоры.
При компостировании в буртах в начале процесса подготовленная смесь имеет температуру окружающей среды. На стадии разогрева мезофильные микроорганизмы начинают быстро размножатся [15, 61], благодаря чему температура смеси поднимается до 40 °C (рисунок 1.10). Длительность первой стадии при правильном соотношении компонентов компостной смеси, ее влажности и гомогенности, как правило, не превышает 2 суток. При увеличении температуры выше 40 °C начинают гибнуть исходные мезофилы, и преобладает развитие термофилов. При этом температура поднимается до 60 °C. В течение термофильной фазы быстро потребляются наиболее легко разлагаемые субстраты, такие как сахара, крахмал, жиры, белки [15, 62]. Когда остаются более устойчивые субстраты, активность этих микроорганизмов начинает падать. При этом скорость тепловыделения становится равной скорости теплопотерь, что соответствует достижению температурного максимума. В этой точке материал практически достигает стабильного состояния, перестает привлекать насекомых и иметь неприятных запах. Ряд ученых считает, что спад температуры после достижения максимального значения (около 60°С) связан с гибелью термофилов (некая саморегуляция популяции). Стадия остывания характеризуется вторым пиком микробиологической активности, который проходит в мезофильном режиме, поэтому его температура не превышает 45−50°С. Считается, что при снижении температуры ниже 30 °C, процесс ускоренного компостирования можно считать завершенным, активную аэрацию и контроль за температурой прекращают. Длительность процесса при компостировании в буртах в зависимости от погодных условий составляет от 16 до 21 суток.
Средняя температура —————- окружающей среды.
————- компостной смеси при компостиродании д ffypmax на открытых площадках.
————-компостной сгеси при компостиродании д камерной устанобке,.
— -компостной смеси при комбиниробанном способе компостирования.
Рисунок 1.10 — Диаграмма изменения температур по стадиям в процессе компостирования различными способами.
При компостировании в камерных установках наблюдаются те же микробиологические процессы (два пика активности). За счет теплоизоляции температура смеси в установке на стадии активного горения может достигать более 80 °C (см. рисунок 1.10) [63, 64, 65]. Однако уже при 60 °C термофилы гибнут. Ряд исследователей объясняют это явление присутствием в процессе компостирования бактерий, которые занимают температурную нишу 65−82°С [56, 58, 66]. В результате этих исследований было сделано предположение, что эти гипертеплолюбивые популяции микроорганизмов, которые были так же найдены в геотермальных источниках, играют важную роль в деградации органической материи [58]. За счет сохранения тепла биотермической реакции процесс компостирования в камерных установках идет более эффективно, что позволяет сократить его сроки до 7−12 суток в зависимости от типа установки.
Комбинированное компостирование в камерных установках и буртах на открытых площадках позволит гарантированно обезвредить конечный продукт и при незначительном увеличении сроков компостирования существенно сократить энергозатраты. Данный эффект достигается за счет того, что стадии разогрева (участок 1−2) и остывания (участок 3−4) проходят при компостировании в буртах, так как этот способ является более производительным и менее энергоемким, а стадия активного горения (участок 2−3) — в камерных установках (см. рисунок 1.10). На участке 2−3 основной задачей установки является не компостирование органического субстрата, а гарантированное его обеззараживание в максимально сжатые сроки, что позволяет минимизировать общие энергозатраты всего цикла переработки [67, 68, 69, 70].
Каждая из камерных установок ускоренного компостирования поточно-непрерывного действия имеет свои преимущества и недостатки. Считается, что установка вертикального типа является более рациональной по ряду причин:
— как и установка модульного типа, она в большей степени использует свой рабочий объем, тогда как установка барабанного типа по технологическим причинам заполняется только на 75% [32];
— по сравнению с модульной или барабанной установками, при одинаковых рабочих объемах установка вертикального типа имеет гораздо меньшую производственную площадь, что актуально для сельскохозяйственных предприятий, расположенных в густонаселенных районах;
— несмотря на то, что в установке вертикального типа, по сравнению с модульной, загрузка свежего сырья производиться на большую высоту, затраты компенсируются тем, что в модульной установке после поднятия сырья его необходимо распределить по ее длине, а после прохождения через корпус так же сгруппировать по длине при выгрузке;
— в установке вертикального типа возможна пассивная аэрация, что позволит уменьшить энергоемкость процесса компостирования в целом.
Главным недостатком установок вертикального типа, из-за которого они не получили широкого распространения, является высокая энергоемкость, связанная с поддержанием пористости материала при помощи дополнительных устройств или разрыхлителей [55]. Использование разрыхлителей имеет ряд недостатков, которые не характерны для устройств снижения уплотнения:
— существенно снижается производительность установки, так как разрыхлитель может занимать от 14 до 50% от общей массы компостируемого материала;
— технологические требования предусматривают влажность компостируемого материала в пределах 50−60%, что увеличивает количество влагопоглощающего компонента (для модульных установок допустимая влажность компостируемой смеси до 75%), следствием чего является снижение производительности установки;
— высокий фракционный состав наполнителя помимо энергозатрат на смешивание и сепарацию, увеличивает энергоемкость процесса загрузки и разгрузки установки;
— не обеспечивается достаточно постоянное значение пористости по высоте и поперечным размерам, что приводит к неравномерной аэрации по всему объему установки.
Следовательно, более прогрессивным является повышение эффективности установок вертикального типа, в которых пористость сохраняется за счет устройств снижения уплотнения. Поэтому одной из задач является обоснование конструкции устройства, обеспечивающего сохранение пористости компостируемого материала по высоте установки и имеющего минимальные удельные энергозатры.
1.3 Обзор устройств снижения уплотнения компостируемого материала.
В результате литературно-патентного обзора была определена следующая классификация устройств снижения уплотнения (рисунок 1.11). По энергоемкости все устройства можно разделить на две группы: пассивные и активные. Удельная энергоемкость работы пассивных устройств зависит от привода запирающего механизма или тормоза, и, как правило, не превышает 0,1 кВт-ч/т. Активные устройства, помимо снижения уплотнения, оказывают на компостируемый материал различного рода воздействия, направленные на его разрыхление и перемешивание. Это улучшает его пористость и условия аэрации, но, вместе с тем, значительно увеличивает удельную энергоемкость до 4 кВт-ч/т.
В установке ускоренного компостирования Вибо [15] вес материала воспринимается жестко закрепленными наклонными перфорированными решетами (рисунок 1.12, а), под которыми расположена система приточно-вытяжной аэрации. По мере выгрузки из нижней части установки материал под собственным весом сползает (пересыпается) вниз. По замыслу автора данное устройство не потребляет энергию. Но на практике, вследствие того, что отсутствует какое-либо побуждение, материал в процессе компостирования слеживается и образует своды внутри корпуса, что препятствует свободному просыпанию материала. На практике данная конструкция не является работоспособной.
Рисунок 1.11 — Схема классификации устройств снижения уплотнения.
Работа поворотных решет (рисунок 1.12, в), предложенных Брейхаудом Ю. Р. [15], является более надежной: при отводе опорного механизма, устройство открывается под весом материала и происходит пересыпание на нижележащий этаж. Такое устройство практически не потребляет энергии. Основным недостатком данного устройства является нерациональное использование объема биореактора, предполагающее наличие полости, необходимой для свободного перемещения решет при возврате в исходное положение. Помимо этого, материал не разрыхляется, а при падении в большом объеме (даже с малой высоты) уплотняется.
Ч ' ¦ ', Q у — -V ;
SjJ: .
V ¦. Ч г /.
•у. / ¦ / п а) б) 6! г) а) наклонные решетаб) жалюзив) поворотные решетаг) колосниковые решетад) плужки.
Рисунок 1.12- Существующие устройства для снижения уплотнения.
Наиболее эффективной является работа активных устройств для снижения уплотнения, помимо перегрузки с этажа на этаж, они обеспечивают разрыхление материала.
Так при работе устройства снижения уплотнения с рабочим органов в виде жалюзи (см. рисунок 1.12, б), предложенного Мирным А. Н. [55], при открытии жалюзи нарушается структура материала, благодаря чему при пересыпании он частично разрыхляется. Однако, открытие жалюзи шириной около 30 см довольно энергоемкий процесс (1,8 кВт-ч/т), даже при небольшой высоте слоя компостируемого материала, в противном случаепри уменьшении ширины жалюзи, повышается вероятность сводообразования и зависания материала на рабочих органах.
Колосниковые решета (см. рисунок 1.12, г) Виноградова Н. В. при включении начинают совершать возвратно поступательные колебания, при которых компостируемый материал, проходя через них, разрыхляется [15], энергоемкость процесса в данном случае составляет до 3 кВт-ч/т.
Плужки (см. рисунок 1.12, д), запатентованные Томасом [55], установленные на вращающемся валу внутри цилиндрического корпуса, выполнены таким образом, что переваливают материал на каждом этаже от отверстия, выполненного у центра, к отверстию на периферии. Благодаря этому материал хорошо разрыхляется и перемешивается, при этом величина энергозатрат может достигать 4 кВт-ч/т.
В ходе анализа существующих устройств снижения уплотнения компостируемого материала в установках вертикального типа было установлено, что пассивные устройства имеют следующие недостатки: не разрыхляют материал в процессе работыимеют высокую вероятность сводообразования материаладля них характерно нерациональное использование рабочего объема установкиих рабочие органы создают значительное сопротивление аэрируемому воздуху. К основным недостаткам активных устройств можно отнести сложную металлоемкую конструкцию и высокую энергоемкость процесса разрыхления. Поэтому существующие устройства снижения уплотнения компостируемого материала не нашли широкого применения в производстве.
С учетом указанных недостатков нами разработано устройство снижения уплотнения компостируемого материала, принцип работы которого поясняется рисунками 1.13 и 1.14. Новизна данного устройства подтверждается патентом на полезную модель «Установка для компостирования» [71].
Вертикальная установка работает следующим образом. Компостируемый материал 1 при помощи устройства загрузки подается в верхнюю часть корпуса 2 установки. Разделение между этажами происходит при помощи, как минимум, одного устройства снижения уплотнения 3, установленного между каждым из этажей (рисунок 1.13). снижения уплотнения.
Рисунок 1.13 — Установка ускоренного компостирования с устройством снижения уплотнения в виде гибких тросов.
Устройство снижения уплотнения (рисунок 1.14) выполнено в виде двух барабанов 4 и 5, закрепленных на корпусе 2 установки при помощи подшипниковых опор 6. Барабаны синхронно вращаются в противоположные стороны при помощи цепной передачи, состоящей из цепи 7, пары основных звездочек 8, закрепленных на барабанах 4 и 5, и пары паразитных звездочек 9, Рабочие органы устройства для снижения уплотнения выполнены в виде эластичных тросов 10, которые попеременно закреплены одной стороной на корпусе 2 установки, а другой на барабане. На выходном конце вала одного из барабанов установлен шкив 11, к которому крепится накопитель потенциальной энергии 12, а на другом выходном конце установлен тормоз 13, предотвращающий вращение барабанов.
2-корпус установки- 4, 5-барабаны- 6-подшипниковые опоры- 7-цепь- 8, 9-звездочки- 10-эластичные тросы- 11—шкив- 12—накопитель- 13-тормоз Рисунок 1.14 — Устройство снижения уплотнения.
Принцип действия устройства снижения уплотнения основан на сводообразовании трудно сыпучих материалов. Расстояние между тросами 10 и высота этажа (расстояние между соседними устройствами) подобраны таким образом, что после заполнения корпуса установки, материал под собственным весом уплотняется, образуя на каждом этаже на рабочих органах устройства статически устойчивые своды (см. рисунок 1.13). Причем усилия веса материала недостаточно для его саморазрушения о рабочие органы. В процессе загрузки материал постепенно слеживается, увеличивая величину сводообразующего слоя (рисунок 1.15, а).
2 — корпус установки- 4, 5 — барабаны- 7 — цепь- 8 — основные звездочки, 9 -паразитные звездочки- 10 — эластичные тросы- 11 — шкив- 12 — накопитель Рисунок 1.15 — Принцип работы устройства снижения уплотнения.
Действует устройство снижения уплотнения следующим образом. В процессе компостирования тросы находятся в натянутом положении и принимают на себя вес компостируемого материала, благодаря чему, нижерасположенный слой меньше уплотняется, от разматывания их удерживает тормоз 13.
Разрыхление и перемещение материала с этажа на этаж осуществляется за счет разрушения сводообразуюшего слоя рабочими органами устройства в процессе их разматывания и сматывания. Перегрузка осуществляется на опорожненный нижний этаж, у которого рабочие органы находятся в натянутом положении.
При выключении тормоза барабаны 4 и 5 начинают вращаться, под действием веса компостируемого материала GK, тросы 10 разматываются, накопитель 12 поднимается вверх (см. рисунок 1.15, б). При этом соседние тросы движутся навстречу друг другу, возникает эффект скользящего резания, при котором усилия веса материала достаточно для разрушения сводообразующего слоя.
Пласты материала в процессе разрушения отделяются от общей массы и просыпаются на нижний этаж. Из-за чего вес материала, давящий на тросы, постепенно уменьшается (т.е. GK’Gh’R). В процессе разрушения тросами 10 сводообразующего слоя между ними перестают возникать статически устойчивые своды, и материал начинает свободно просыпаться между тросами. При этом его вес, давящий на тросы, становится значительно меньше своего первоначального значения (т.е. GK" «GK), крутящий момент накопителя перевешивает момент от компостируемой массы (т.е. GK» -r.
Далее процесс пересыпания повторяется на этаже, расположенном выше.
Предложенное устройство снижения уплотнения компостируемого материала позволит повысить эффективность работы установки вертикального типа за счет того, что [72—78]:
— при пересыпании обеспечивается разрыхление материала по всей высоте установки;
— работа устройства имеет низкую энергоемкость, так как разрушение (разрыхление) и пересыпание материала происходит под собственным весом;
— малое поперечное сечение рабочего органа минимизирует теплопотери и сопротивление для движения воздуха при аэрации;
— гибкость рабочих органов позволяет снизить требования к фракционному составу компостируемой смеси (допускает наличие крупных включений в виде веток, камней и др. посторонних предметов) без потерь надежности и работоспособности устройства снижения уплотнения.
Необходимо теоретически обосновать конструктивно-режимные параметры устройства (расстояние между рабочими органами, расстояние между соседними устройствами, время между пересыпанием с этажа на этаж) в зависимости от свойств компостируемого материала.
1.4 Технологические требования к материалу при его компостировании, в вертикальных установках с устройством снижения уплотнения в виде гибких тросов.
Одним из основных компонентов, используемых в качестве подстилки, являются опилки. Подстилка поглощает жидкие выделения животных и образующийся при разложении мочи аммиак. Подстилка уменьшает влажность экскрементов, они становятся более рыхлыми, что ускоряет их микробиологическое разложение. Опилки обладают^ лучшей влагопоглощающей способностью по сравнению с соломой [4, 14, 23, 79, 80], но их использование в качестве углеродосодержащего наполнителя при приготовлении компостов на основе навоза является менее эффективным по ряду причин. Во-первых, при приготовлении компостных смесей на основе опилок повышается содержание клетчатки и лигнина, — такая смесь гораздо дольше разлагается и получаемый конечный продукт менее эффективен в первый год после внесения [66]. Во-вторых, опилки имеют меньший размер частиц, упаковываются очень тесно, образуя смесь с высокой плотностью и узкими порами. Это ограничивает диффузию кислорода и углекислого газа, что снижает скорость биотермического процесса [34, 81, 82].
Солома злаков, напротив, благодаря жесткой структуре, которую она не теряет даже при намокании, образует более рыхлую смесь, чем повышает эффективность аэрации [1]. Помимо этого, солома при смешивании с навозом образует смесь, характеризующуюся наличием структурных связей в виде волокон. Такое строение компостируемого материала повышает вероятность его зависания на рабочих органах в процессе сводообразования, что является одним из основных условий работы разработанного нами устройства снижения уплотнения.
1.5 Теоретические предпосылки к обоснованию работы устройства снижения уплотнения.
По мере загрузки корпуса вертикальной установки компостируемый материал начинает постепенно уплотняться снизу вверх, в результате чего он зависает на рабочих органах устройств снижения уплотнения, расположенных на каждом из этажей.
Зависание происходит при опоре на рабочие органы, вследствие возникновения внутреннего напряжения в компостируемом материале образуются статически устойчивые своды, при этом усилия веса материала недостаточно для разрезания его рабочими органами, которые служат опорами при сводообразовании.
В нашем случае нельзя употреблять термин «резание», так как при взаимодействии рабочих органов с материалом, происходит не измельчение его частиц, а разрушение структурных связей. Поэтому в дальнейших рассуждениях мы будем говорить о разрушении материала, основываясь, тем не менее, на теории резания.
Для описания внутренних процессов принимаем следующие допущения:
1. после пересыпания сводообразование на каждом из этажей установки происходит мгновенно;
2. объемная плотность на каждом из этажей одинакова и зависит только от физико-механических свойств материала и его слоя (за исключением самого верхнего этажа);
3. после пересыпания материал разрыхляется до насыпной плотности.
Значительный вклад в исследование и разработку технологий и средств механизации для приготовления органических удобрений внесли: Виноградов Н. Ф., Чересленко В. Н., Ковалев-Н.Г., Афанасьев В. Н., Гриднев П. И., Капустин В. П., Коваленко В. П., Петренко И. М., Макаров В. А., Туваев В. Н., Лопес де Гереню В. О., Гуляев Н. Ф., Мирный А. Н. и др.
Одной из важнейших характеристик материала при компостировании является пористость, которая зависит от его физико-механических свойств и влажности. Пористость, согласно работам многих исследователей [28, 29, 36, 39], принято рассчитывать по формуле:
Пв =1−0,OW^—(l-o, OW)^*-, (1.1).
Pw Рт где роб — объемная плотность материала, кг/м ;
W— влажность материала, %- pw— плотность воды, кг/м — рт — плотность твердых частиц материала (плотность твердой фазы), кг/м3.
Первые теоретические исследования по определению объемной плотности в зависимости от слоя материала были сделаны Туваевым В.Н.
28], а в дальнейшем дополнены Гридневым П. И. [29]. В своих работах по определению объемной плотности они использовали следующую зависимость: где уоб — объемная плотность материала при высоте слоя h м, кг/м3- ci, с2, с3 — экспериментальные коэффициенты.
Для практических расчетов нас интересует максимальная высота слоя, при которой возможно наличие порового пространства в его нижней части, т. е. нас интересует значение плотности у основания этажа, т.к. туда, как правило, подводится система аэрации.
Поэтому в уравнение (1.1) необходимо подставлять значение не объемной, а локальной плотности — это плотность некоторого элементарного объема, расположенного на заданной глубине в материале. Объемная плотность — это весовая характеристика материала, она определяет, какое количество массы располагается в заданном объеме при заданной высоте слоя.
Уравнение (1.2) не учитывает изменение плотности материала в процессе самоуплотнения (слеживания). Общеизвестно, что в процессе компостирования физико-механические свойства материала могут значительно изменятся, что также необходимо учитывать.
Следовательно, закон изменения локальной плотности компостируемого материала от слоя с течением времени, в зависимости от степени спелости компоста в настоящее время мало изучен.
Разработкой и обоснованием устройств снижения уплотнения занимались Мирный А. Н. [55] (для компостируемых материалов) и Тимочкин А. В. [83] (для сухих трудно сыпучих материалов). Но результаты их исследований мало пригодны для обоснования разработанного устройства из-за значительных различий в конструкции.
Описанием процесса сводообразования трудно сыпучих материалов занимались следующие ученые [84−92]: Гячев Л. В., Иванов М. Г., Цимбаревич Г. М., Горюшинский B.C., Варламов А. В., Тимочкин А. В., Стальной В. П., Комченко Е. В. и др. В основе их исследований лежит формула для определения размеров сводообразующего отверстия, полученная Зенковым Р. Л. [93]:
2 • та • (l + sin ер} max.
1.3) p-g где (p — угол внутреннего трения материала, градл т0 — начальное сопротивление сдвигу материала, Н/м. р — объемная плотность материала, кг/м3- g — ускорение свободного падения, м/с2.
Уравнение (1.3), для связных грузов, не учитывает изменение физико-механических свойств материала при увеличении его слоя. Однако, как известно из практики, при засыпании компостных смесей в установки, с увеличением высоты слоя материала размер выгрузного окна необходимо увеличивать. Для сыпучих материалов т прямо пропорционально коэффициенту внутреннего трения, однако, для трудносыпучих материалов характерна междуслойная взаимосвязь, которая возрастает при их уплотнении и наличии волокнистых включений. Начальное сопротивление сдвигу и коэффициент внутреннего трения меняют свое значение в зависимости от нагрузки. Таким образом, мы приходим к выводу, что формулу (1.3), полученную Зенковым Р. Л. для определения расстояния между рабочими органами, на которых образуются статически устойчивые своды, применительно к компостным смесям, характеризующимся связной волокнистой структурой, применять нельзя.
Способность рабочих органов устройства снижения уплотнения в статическом состоянии разрушать компостируемый материал характеризуется разрушающим контактным напряжением, которое зависит от плотности и физико-механических свойств материала.
Для осуществления процесса разрушения материала необходимо, чтобы критическая сила, с которой рабочий орган действует на него, преодолела сумму сил, действующих на лезвие в плоскости, перпендикулярной плоскости резания.
Критическую силу Ркр можно определить как произведение площади режущей кромки лезвия F (мм) на разрушающее контактное напряжение ар
Н/мм2) [94, 95, 96]:
Ркр=Р-<7р=М-1-&р, (1.4) где ц — толщина лезвия, мм- - длина лезвия, взаимодействующая с материалом, мм. В разработанном нами устройстве лезвие (рабочий орган) в сечении имеет вид окружности. Поэтому для дальнейших рассуждений принимаем величину ц равную диаметру рабочего органа. а=0 а>0 а) — без продольного перемещения лезвияб) — с продольным перемещением лезвияАВ — лезвиеМ— материалРп —сила нормального давления лезвия на материалs—перемещение точки лезвия, соприкасающейся с материалом М.
Рисунок 1.16 — Схемы способов разрушения.
Разрушение сводообразующего слоя материала при работе устройства снижения уплотнения происходит вследствие того, что его рабочие органы начинают встречное движение друг к другу относительно материала. При этом материал начинает испытывать уже не рубящее (см. рисунок 1.16, а), а скользящее разрушение (см. рисунок 1.16, б), при котором, как известно, усилие, необходимое для нарушения структурных связей материала, значительно меньше [94].
Если угол, а между нормалью к линии лезвия и направлением перемещения s равен нулю, то это будет рубящее разрушение. Если же, а > О, то происходит разрушение с продольным перемещением лезвия. Преимущество разрушения с продольным перемещением перед рубящим заключается в меньшем значении критической силы, требуемой для осуществления резания [94].
Зависимость между усилием Ркр и продольным перемещением st лезвия по материалу В. П. Горячкин выразил уравнениями [94, 95]: st=A-e~P" t (1.5) оговорив, что предложенная им зависимость не является окончательной. Для количественного определения скольжения лезвия в процессе разрушения В. П. Горячкин ввел понятие коэффициента скольжения е, представляющее собой отношение тангенциальной составляющей v, полной скорости лезвия к нормальной составляющей v" этой скорости [95]: е = — = tga. (1.6) v".
Следуя рекомендациям В. П. Горячкина, В. А. Желиговский [96] экспериментально установил взаимную зависимость между нормальным усилием Р&bdquo- (рисунок 1.17) лезвия на материал, тангенциальной силой Pt, необходимой для возбуждения тангенциального перемещения s, лезвия по материалу, и величинами s, тангенциального и sn нормального перемещения лезвия относительно материала. Установлено, что по мере убывания силы Рп, необходимая для нарушения структурных связей сила Р, возрастает в размерах, при которых их равнодействующая R сохраняет приблизительно постоянную величину [94]:
R = д/i5,2 + Pt2 «const.
1.7).
Рисунок 1.17 — Схема по определению взаимосвязи между нормальной силой Рп, касательной силой Pt, касательным st и нормальным sn перемещениями лезвия в процессе скользящего резания.
При этом изменение угла <р наклона равнодействующей R относительно нормали к лезвию совпадает с изменением угла направления перемещению s лезвия, т. е. углы, а и ^ до определенных пределов равны. Совпадение направления силы R с направлением перемещения .у лезвия, по мнению В. А. Желиговского, свидетельствует об отсутствии скольжения лезвия по материалу в определенных пределах угла (р: = tga (1.8).
Поэтому данное отношение автор назвал коэффициентом продольного перемещения.
При некотором дальнейшем уменьшении силы Рп и росте силы Pt углы, а и (р не остаются равными друг другу, быстро растет их разность. При, а > ср возникает скольжение лезвия по разрезаемому материалу. Условием возникновения скользящего разрушения по мнению В. А. Желиговского является способность разрушаемого материала к деформации под давлением лезвия до нарушения структурных связей.
В.А. Желиговскому удалось обнаружить важную особенность процесса разрушения лезвием — в зависимости от некоторых физико-механических свойств перерезаемого материала эффект от скользящего движения лезвия может быть значительным только при определенных углах скольжения. Эффект скользящего разрушения он объясняет тем, что при скольжении лезвия по материалу, оно захватывает неровностями частицы материала, стремится сдвинуть их с места и увлечь за собой [97]. Между смещаемыми и соседними частицами материала возникают нормальные напряжения растяжения или касательные напряжения сдвига вместо напряжений смятия, т. е. сжатия. Подавляющее большинство материалов оказывает меньшее временное сопротивление на растяжение и сдвиг, чем на сжатие (смятие) [94].
Теоретические зависимости, описывающие процесс скользящего разрушения прямым лезвием, показанные во многих работах [98−101], в нашем случае использовать нельзя, так как в процессе разматывания гибкий трос меняет свою кривизну, что сказывается на неодинаковой глубине разрушения по его длине.
Анализ теоретических предпосылок к обоснованию разработанного устройства снижения уплотнения выявил их недостаточность, использование существующих закономерностей требует соответствующих доработок и корректировок.
Для математического моделирования процесса работы предложенного устройства снижения уплотнения необходимо проведение дальнейшего научного исследования.
1.6 Выводы, цель и задачи исследования.
1. Компостирование органических отходов традиционным способом не соответствует современным санитарно-эпидемиологическим требованиям.
2. Полное обеззараживание компостной массы по всему объему возможно только камерным способом, в стационарных установках, имеющих теплоизолированный корпус, благодаря которому достигается высокая температура биотермического процесса в течение всего цикла переработки в ней (свыше 53 °C до 4 суток).
3. Эффективной технологией переработки органических отходов является комбинация традиционного и камерного способов компостирования, причем обеззараживание компостируемого материала в стационарных установках должно проходить не более чем за 5. 7 суток.
4. Наиболее рациональной установкой, реализующей камерный способ компостирования, является установка вертикального типа поточно-непрерывного действия с дополнительными устройствами снижения уплотнения материала, установленными по высоте установки.
5. Повысить эффективность работы установки вертикального типа можно путем использования в ней устройства снижения уплотнения компостируемого материала с рабочими органами, выполненными в виде гибких тросов.
6. Существующих теоретических исследований недостаточно для описания процесса взаимодействия компостируемого материала с рабочими органами устройства снижения уплотнения и обоснования конструктивно-режимных параметров его работы.
В соответствии с вышеизложенным, целью настоящей работы является повышение эффективности работы установки ускоренного компостирования вертикального типа путем разработки и обоснования конструктивно-режимных параметров устройства снижения уплотнения.
Для достижения поставленной цели необходимо решить следующие задачи: провести теоретические исследования процесса взаимодействия рабочих органов устройства снижения уплотнения с компостируемым материаломисследовать изменение физико-механических свойств компостируемого материала в зависимости от величины слоя, времени слеживания и степени спелости компостаобосновать конструктивные параметры устройства из условия зависания компостируемого материала на рабочих органах;
— обосновать конструктивно-режимные параметры устройства, необходимые для обеспечения пересыпания материала с этажа на этаж сверху вниз;
— провести производственную проверку устройства и определить экономический эффект его использования.
Рабочая гипотеза: существует определенное сочетание управляемых факторов, обеспечивающих работу устройства снижения уплотнения.
2 ТЕОРЕТИЧЕСКИЕ ИССЛЕДОВАНИЯ ПРОЦЕССА ПЕРЕМЕЩЕНИЯ КОМПОСТИРУЕМОГО МАТЕРИАЛА В ВЕРТИКАЛЬНОЙ УСТАНОВКЕ С РАЗРАБОТАННЫМ УСТРОЙСТВОМ СНИЖЕНИЯ УПЛОТНЕНИЯ.
2.1 Теоретическое исследование изменения пористости компостируемого материала по высоте слоя и времени созревания.
Как показали предварительные исследования, характер изменения пористости материала в зависимости от величины его слоя с течением времени мало изучен. Однако зависимость пористости от времени очевидна, так как большинство материалов склонны к слеживанию [102, 103].
Рассмотрим уплотнение слоя материала под собственным весом в процессе увеличение его высоты (рисунок 2.1).
Пусть элементарный объем материала имеет некоторую высоту Ип (м), при которой он имеет начальную насыпную плотность (минимальную плотность) (рисунок 2.1, а).
Если нагрузить его вторым слоем в том же объеме, то первый (нижний) слой деформируется (сожмется) на некоторую величину и2 (рисунок 2.1, б) (для удобства рассуждений принимаем, что щ =0). При дальнейшем нагружении нижний слой будет деформироваться на соответствующие величины м3, м4 и т. д.
Тогда при некоторой нагрузке в / слоев локальная плотность у основания будет равна: н I где ui — /-я деформация слоя соответствующая нагрузке равной i слоям, м.
Уравнение (2.1) отражает состояние материала в начальный момент времени, но известно, что с течением времени компостируемый материал уплотняется, следовательно, значение локальной плотности на i-ом слое по истечении времени t определится по формуле:
P (H^Pi (H).hH~Ui ,—^-j", (2.2) пи—и- — и¦ пи—и.-и. U-+U.
1 I н i i 1 i i К где и — линейная деформация относительно начальной /-ой деформации слоя при соответствующем нагружении в i слоев по истечении времени t.
Рисунок 2.1 — Схема уплотнения материала под собственным весом.
При этом общая высота материала в результате естественного самоуплотнения с течением времени будет равна:
H (t)=n-h!l-fj (ui+u'i) I.
2.3).
Объемная плотность материала по истечении времени t при общей высоте Н, определяем по формуле:
Ри 'п.
V «=1) ы ut + и * к J (2.4) где т — масса материала, кг;
VH и VK — соответственно, начальный объем материала и его конечный объем после естественного уплотнения с течением времени, м3- S — площадь основания слоя, м2. С учетом формулы (2.2) уравнение (2.4) примет вид:
РЛиА=— р" 'п — р' п I.
1=1 1.
Ри рУ.
1 IvAl.
1—1 л п Ы Д.
2.5).
Степени уплотнения — материала на глубине Н по истечении времени t определяем как отношение насыпной плотности материала к локальной плотности на глубине if спустя время t при естественном уплотнении: н g Pi h.
1 Рн hH-{ui+uti).
2.6).
Тогда.
2.7) где? cp{H, t) — среднее значение степени уплотнения материала при естественном уплотнении за время t на глубине от 0 до if мм.
После установления закономерности изменения степени уплотнения материала от высоты с течением времени ?(H, t) его среднее значение сможем определить по формуле [104]:
Zcp{H, t) = -^-")z (H, t) dHdt (28) п 1 о о.
Данная зависимость косвенно подтверждается работами Репниковой Е. А. [105].
С учетом формулы (1.1) пористость материала в основании слоя определяем по формуле: гг 1 zfrг (0,01 -W 1−0,01-иО ne=l-pH.?(H, t) — —+ —2.
V Pw Рт) К.
В итоге приходим к выводу, что пористость соломонавозной смеси, с заданным гранулометрическим составом и соотношением соломы и навоза, есть сложная функция, зависящая от общей высоты слоя, времени слеживания и исходной влажности смеси.
В уравнении (2.9) изменение физико-механических свойств материала в процессе биотермического разложения учитывается аргументами ptt и рт, значение которых соответствует определенным стадиям компостирования.
Зависимость степени уплотнения от глубины слоя и времени разложения необходимо определить в ходе экспериментов. При этом неизвестно распределение влаги в материале по высоте, что также необходимо исследовать экспериментально.
2.2 Определение максимального расстояния мезвду рабочими органами устройства при условии образования статически устойчивого свода.
Задача обеспечения гарантированного зависания материала, при котором возникает статически устойчивый свод, решается нахождением максимального расстояния а™ах между рабочими органами, обеспечивающее минимальное количество рабочих органов.
На рисунке 2.2 изображен свод, образовавшийся между двумя соседними рабочими органами.
Рисунок 2.2 — Схема образования свода.
Согласно теории Зенкова P.JI. размер сводообразующего отверстия можно определить по формуле:
2 • г.
2.10).
Poo’g где т — касательное напряжение в слое материала на уровне отверстия, НУм. Зависимость предельного касательного напряжения от нормального для влажных и трудносыпучих грузов, имеет вид [93]: т = [(ст + с)-Л]%, (2.11) где сгнормальное напряжение (вертикальное давление со стороны вышележащих слоев), Н/м — с, Я, z — константы, характеризующие свойства данного материала. С учетом изменения локальной плотности по высоте слоя в начальный момент времени (t=0), изменение нормального напряжения в основании слоя в зависимости от его высоты определяем зависимостью: e{H)=Po6{H)-g-H = Pl1-tcp{H)-g-H, (2.12) где Н— высота слоя материала, м.
Подставляя значение сг (н) из уравнения (2.12) в (2.11), найдем зависимость предельных касательных напряжений в основании слоя от его высоты: т (н) = [{рн • g ¦ Н + с)-(2.13).
Тогда максимальное расстояние между рабочими органами с учетом условия сводообразования (2.10) в зависимости от слоя определяем по формуле:
2 (p, rtcp{H)-g-H + c)-A?= св (тт LV" Ьср J 6 ' ^ J a-{Hh-^Цдй- (2Л4).
2.3 Определение максимального расстояния меяеду рабочими органами устройства при условии разрушения материала.
Необходимо аналитически определить количество рабочих органов, необходимых для удержания материала определенной плотности в объеме двух этажей. Разрушение материала рабочими органами осуществляется за счет гравитационного подпора [94], т. е. за счет усилия собственного веса. Процесс взаимодействия рабочего органа с компостируемым материалом в статическом состоянии описывается теорией рубящего разрушения.
Вес материала (рисунок 2.3), приходящийся на один рабочий орган определяем по формуле: г- — —, (2.15) пп к J где Р — вес материала, давящий на устройство снижения уплотнения, НpjH) — объемная плотность материала с высотой слоя Н, кг/м3;
V— объем материала, расположенного над устройством, м3- п — количество рабочих органов, шт. кр ' кр ' кр
Рисунок 2.3 — Схема сил, действующих на рабочий орган при внедрении в материал.
С учетом формулы (1.4) критическое усилие, необходимое для нарушения структурных связей в материале равно:
PKp=n-jLi-l'Crp, (2.16) где / - ширина этажа (длина части рабочего органа в натянутом состоянии, взаимодействующая с материалом), м.
При заполнении этажа, когда вес, с которым материал действует на рабочие органы устройства, достигнет значения критического усилия, начнется процесс разрушения структурных связей (Р = Ркр).
Вес материала, давящий на рабочие органы устройства снижения уплотнения равен:
P = Po6{H)-g-H-l.n*a (2.17) где а^ — расстояние между рабочими органами из условия рубящего разрушения, м.
Материал будет разрушаться о рабочие органы под собственным весом, если выполняется условие:
Po6(H)'g'H-l-n-apmXi =п-/л-1-стр (2.18).
Из уравнения (2.18) находим максимальное расстояние между рабочими органами, исходя из условия разрушения материала, в зависимости от его слоя: а шах.
Я) = fi-ot или а" .
2.4 Определение конструктивных параметров устройства снижения уплотнения в установке ускоренного компостирования вертикального типа.
Полученные нами уравнения (2.14) и (2.19) определяют зависимость расстояния между рабочими органами от высоты слоя материала, а не от высоты этажа (расстояния между соседними устройствами снижения уплотнения).
Рассмотрим механизм зависания компостируемого материала на рабочих органах устройства по мере заполнения установки. Пусть высота этажа равна Нк, а расстояние между рабочими органами — а. По мере заполнения этажа установки, при достижении некоторой высоты слоя S, на рабочих органах устройства начинается процесс сводообразования, благодаря чему материал перестает просыпаться между ними (рисунок 2.4, а). Данное явление описывается уравнением (2.14) при Н=8 расстояние между рабочими органами, а = (S).
При дальнейшей засыпке материала внутрь установки (рисунок 2.4, б) до тех пор, пока его высота на следующем этаже не достигнет значения S, т. е. не произойдет «отсечение потока» материала, расстояние между рабочими органами первого этажа должно находиться в таких пределах, чтобы материал с общей высотой слоя равной Нк+д не разрушался под собственным весом, при этом значение, а определяется по уравнению (2.19).
Значение конструктивных параметров установки находим графоаналитическим методом (рисунок 2.5). Существует такое расстояние между рабочими органами а, при котором значения Нкъд удовлетворяют условию:
Cax () = <ах + Нк) (2.20) а) б) а) — зависание материала на первом этажеб) — зависание материала на втором этаже .
.Рисунок 2.4 — Схема работы устройства снижения уплотнения.
Согласно разработанной нами конструкции устройства, процесс сводообразования происходит при достижении высоты слоя материала, не превышающей высоту этажа, т. е.
8<НК. (2.21).
Максимальное расстояние между рабочими органами атах, находим из условия, что S = HK, при этом существуют такие значения S = <^тах и.
Нк = Н^ (рисунок 2.5, а), для которых выполняется условие (2.20).
Минимальное расстояние между рабочими органами amin ограничивается условием максимальной высоты слоя Нтах, при которой возможно наличие порового пространства в его основании. Для amin существуют такие значения 2 =c>min и Нк = НК (рисунок 2.5, а), для которых так же выполняется условие (2.20). а) — зависимость расстояния между рабочими органами устройства от высоты слоя из условия сводообразования и разрушения компостируемого материалаб) — область значений конструктивных параметров устройства, обеспечивающих пористость материала.
Рисунок 2.5 — Схема определения конструктивных параметров устройства графо-аналитическим методом.
Учитывая условие (2.21), приходим к выводу, что при расстоянии между рабочими органами равном, а. компостируемый материал зависнет, если высота этажа будет находиться в следующих пределах.
8 .
Список литературы
- Винаров, А.Ю. Биотехнология переработки отходов животноводства и птицеводства в органическое удобрение Текст. / А. Ю. Винаров, А. А. Кухаренко, Т. В. Ипатова, Б. В. Бурмистров. М.: ФИГТС, 1998. -114 с.
- Власенко, В.М. Экологические требования к охране почв от загрязнения минеральными удобрениями Текст. / В. М. Власенко // Тракторы и сельхозмашины. 1995. — № 1. — с. 8−10.
- Добровольский, Г. Плодородие почв России Текст. / Г. Добровольский, Г. Куст // Евразия. Природа и люди. 1997. — № 4. — с.56−61
- Ковалев, Н.Г. Органические удобрения в XXI веке (Биоконверсия органического сырья) Текст.: Монография / Н. Г. Ковалев, И. Н. Барановский. Тверь, Чу До, 2006. — 304 с.
- Ковда В.А. Факторы, снижающие плодородие черноземов и меры их устранения Текст. / В. А. Ковда // Механизация и электрификация сельского хозяйства. — 1987. — № 3. — с. 3−6.
- Зуев, В.М. Восстановление структуры и плодородия почвы Текст. / В. М. Зуев // Механизация и электрификация сельского хозяйства. -1998.-№ 7.-с. 8−10.
- Макаров, В.А. Агрохимическая модель гумусообразования почв сельскохозяйственного предприятия Текст.: Новые разработки в механизации кормоприготовления / В. А. Макаров. Рязань: СХИ, 1990. — С. 116−124.
- Макаров, В.А. Производство и применение органических удобрений в хозяйствах Владимирской области Текст.: Рекомендации / В. А. Макаров и др. Владимир: ВНИПТИОУ, 1989. — 148 с.
- Макаров, В.А. Теория и практика производства и применения органических удобрений Текст.: Проблемы наращивания продуктивности земледелия в колхозах и совхозах Рязанской области / В. А. Макаров. — Рязань: СХИ, 1990 с. 66−68.
- Макаров, В.А. Обоснование проблемы дифференциального применения удобрений Текст. / В. А. Макаров / Техника в сельском хозяйстве. М.: 2003, № 3. — С. 17−19.
- Макаров, В.А. и др. Целевая комплексная программа производства и применения органических удобрений в Рязанской области Текст. / В. А. Макаров и др. Рязань: ВНИПИагрохим, 1990. — 98 с.
- Небаевский, В.А. Ресурсосбережение при производстве продукции растениеводства Текст. / В. А. Небаевский // Механизация и электрификация сельского хозяйства. — 2003. № 9. — с.7−8.
- Научные основы и рекомендации по эффективному применению органических удобрений. М.: ВАСХНИЛ, 1991. — 216 с,
- Мишустин, Е.Н. Термофильные микроорганизмы в природе и практике Текст. / Е. Н. Мишустин. М.- Д.: Изд-во АН СССР, 1950. — 391 с.
- Ковалев, Д. А. Анаэробная обработка отходов животноводства /Д.А. Ковалев // Сельский механизатор. 2007, № 3. — С. 35
- Barrington, Suzelle Compost Airflow Resistance Text. / Suzelle Barrington, Denis Choiniere, Maher Trigui, William Knight // Biosystems Engineering. 2002. — № 4. — pp. 433−441
- Baumann, E. Untersuchungen zum Abbauverhallen organischer Dungestaffe Text. / E/ Baumann, R. Schmidt // Archiv fur Gartenbau. 1987. -Vol.35, № 3 -s. 105−114
- Рабинович, Г. Ю. Микробиологическое обоснование выбора сырья для аэробной биоферментации Текст. / Г. Ю. Рабинович, Н. Г. Ковалев // Доклады Россельхозакадемии. 1998. — № 4. — с. 24−25.
- Концепция развития механизации и автоматизации процессов в животноводстве на период до 2015 года /Под науч.-метод. рук. Л. П. Кормановского, Н. М. Морозова. Подольск: ГНУ ВНИИМЖ, 2003. — 100 с.
- Leton, T.G. Control of aeration in static pile composting Text. / T.G. Leton, E.Y. Stentiford // Waste management and reseach. 1990. — Vol.8, № 4.-p. 199−318.
- Backhus Turner Windrow 14.28, 16.36 6.75- Backhus GmbH Электронный ресурс. Электрон, дан. — 2008. — Режим доступа: http://www.backhLis.com
- Rotating drums compost technology. Bedminster Cobb Corporation Электронный ресурс. Электрон, дан. — 2008. — Режим доступа: http://www.bedminster.com
- Гриднев, П.И. Механо-технологическое обоснование эффективного функционирования технических систем подготовки навоза к использованию Текст.: дис.. док. тех. наук: 05.23.04. -М., 1997.-381 с.
- Макаров, В. А. Повышение качества функционирования механизации производства и применения органических удобрений в с/х производстве Текст.: дис. док. техн. наук: 05.23.04. Рязань, 1997 — 425 е.: ил.
- Спевак, Н.В. Совершенствование технологического производства компостов с разработкой и обоснованием параметров устройства для измельчения ТОУ Текст.: дис. канд. техн. наук:: 05.20.01. Саратов, 2005 — 179 е.: ил.
- Рекомендации по системам удаления, транспортирования, хранения и подготовки к использованию навоза для различных производственных и природно-климатических условий. — М.: ФГНУ «Росинформагротех», 2005. 180 с.
- Dougherty, М. Composting for municipalities Text.: planning and desing considerations / Mark Dougherty. NRAES, 1998. — November — 126 p. -ISBN 0−935 817−20−4
- Коваленко, В.П. Компостирование отходов животноводства и растениеводства Текст.: Монография / В. П. Коваленко, И. М. Петренко. -Краснодар: Изд-во КГАУ. 2001. 148 с.
- Петренко, И.М. Процессы компостирования отходов животноводства и растениеводства Текст.: Монография (КГАУ) / И. М. Петренко. Краснодар: Агропромполиграфист, 2002. — 328 с.
- Миронов, В. В. Совершенствование технологии приготовления компоста с обоснованием параметров аэратора Текст.: дис.. канд. техн. наук: 05.20.01. Мичуринск, 2003 — 171 с. ил.
- BioCycle. Journal of composting & organics recycling. — Vol. 37, N0.8, August, 1996.
- Петренко О.И. Параметры процесса компостирования пометосоломенных смесей в камерных ферментаторах Текст.: дис.. канд. техн. наук: 05.20.01. Краснодар, 2003 — 160 с. ил.
- Guide to In-vessel Composting. The Composting Association. ISBN: 0−9 532 546−8-2 Электронный ресурс. Электрон, дан. — 2008. — Режим доступа: http://www.compost.org.uk
- New England Organics. Compost, Mulch and Soils Электронный ресурс. Электрон. дан. — 2008. — Режим доступа: http://www.newenglandorganics.com
- The Containerized Compost System. Mixed organics composting facility. Green Mountain Technologies, Inc Электронный ресурс. Электрон, дан. — 2008. — Режим доступа: http://www.gmt-organic.com
- Биоконверсия отходов животноводства и птицеводства Текст. // Сельский механизатор. 2007. — № 12. — с. 30−31.
- Мхитарян, Г. А. Опыт эксплуатации установок УЭК-5 для компостирования органических отходов / Г. А. Мхитарян, А. Г. Пузанков // Машинно-технологическая станция. — 2006, № 9. — С. 64−65
- Мхитарян, Г. А. Разработка и обоснование конструктивно-технологических параметров установки для термохимического обеззараживания навоза КРС Текст.: дис.. канд. техн. наук: 05.20.01. М, 1985−205 е.: ил.
- Пат. 2 098 934 Российская Федерация, МПК6 С05 F17/02.
- Пат. 2 244 697 Российская Федерация, МПК7 С05 F3/06. Устройство для приготовления компостов Текст. / Завражнов А. И., Гордеев
- A. С., Михеев Н. В., Хмыров В. Д., Миронов В. В.: заявитель и патентообладатель ФГОУ ВПО Мичуринский Гос. Аграрный ун-т. -2 003 107 358/12- заявл. 17.03.2003- опубл. 10.10.2004, Бюл.№ 2. 5с.: ил.
- Пат. 2 291 136 Российская Федерация, МПК7 С05 F3/00. Поточный способ производства компоста Текст. / Миронов В. В., Хмыров
- B.Д., Гордеев А. С.: заявитель и патентообладатель ФГОУ ВПО Мичуринский Гос. Аграрный ун-т. 2 004 132 638/12- заявл. 09.11.2004- опубл. 20.04.2006, Бюл.№ 1. -5с.: ил.
- Пат. 2 170 719 Российская Федерация, МПК7 С05 F3/06.
- Установка для переработки органических отходов Текст. / Еникеев В. Г., Малаков Ю. Ф., Липов А. В.: заявитель и патентообладатель Санкт-Петербургский Гос. Аграрный ун-т. 99 120 599/13- заявл. 29.09.99- опубл. 20.07.2001, Бюл.№ 12. — 7с.: ил.
- Лопес де Гереню, В. О. Повышение эффективности производства твердых органических удобрений на основе навоза КРС вусовершенствованных биореакторах барабанного типа Текст.: дис.. канд. тех. наук: 05.20.01. С.-Пб.-Пушкин, 1995.- 172 с.
- Мирный, А.Н. Инженерные основы аэробного биотермического компостирования твердых бытовых отходов Текст.: дис.. доктора техн. наук: 05.23.04. -М., 1996 242 с.
- Афанасьев, А.В. Повышение эффективности производства удобрений путем оптимизации параметров двухстадийной биоферментации навоза и помета Текст.: дис.. канд. тех. наук: 05.20.01. — С.-Пб.-Пушкин, 2000.-133 с.
- Пат. 2 071 458 Российская Федерация, МПК7 С05 F9/00,3/00.
- Способ получения удобрения из органических отходов и устройство для его осуществления Текст. / Келер К. И.: заявитель и патентообладатель Келер Константин Иоанесович. 925 057 871/15- заявл. 06.08.92- опубл. 10.01.97, Бюл.№ 1. -2с.: ил.
- Мирный, А.Н. Исследование физико-механических процессов аэробного компостирования в многоэтажных ферментаторах Текст.: дис.. канд. тех. наук: 05.20.01. -М., 1966. 185 с.
- Guide to Selecting an In-Vessel Composting System. Researched and written by Dr Joe Short PhD for the CMC, January 2005, P. 8.
- TEG Silo Cage. THE TEG GROUP PLC. Электронный ресурс. -Электрон, дан. 2008. — Режим доступа: http://www.theteggroup.plc.uk
- Vertical Composting Unit. VCU Europe Ltd. Электронный ресурс. Электрон, дан. — 2008. — Режим доступа: http://www.vcutechnology.com
- Петунов, С.В. Совершенствование технологии приготовления компоста из отходов животноводства и деревообработки Текст.: дис.. канд. техн. наук: 05.20.01. -Улан-Удэ, 2006 161 с. ил.
- Зеников, В.И. Микробиологический процесс аэробной переработки органического сырья Текст. / В. И. Зеников, Н. С. Паников // Агрохимические исследования и технологии: Труды ВНИПТИХИМ, 1999. — T.l.-c. 281−286.
- Бидлстон, А. Компостирование и биодеградация соломы Текст. / А. Бидлстон, К. Грей, К. Дейк // Экологическая биотехнология. JI.: Химия, 1990.-235−264 с.
- Завражнов, А.И. Приготовление органических удобрений в аэрационном биореакторе модульного типа Текст. / А. И. Завражнов, В. В. Миронов, М. С. Колдин, П. С. Никитин // Вестник Саратовского ГАУ. — Саратов: Изд-во Сар. гос. агр. ун-т, 2006. — № 4. — с. 20−24.
- Миронов, В.В. Поточный способ производства компоста Текст. / В. В. Миронов, М. С. Колдин, П. С. Никитин // Материалы 55-й научной конференции молодых ученых. — Мичуринск: Изд-во Мич. гос. агр. ун-т, 2005.-с. 135−138.
- Экологическая биотехнология: Пер. с англ. Текст. / Под ред. Фостера К. Ф. и Вейза Д.А.Д. — Д.: Химия. Ленингр. отд-ние, 1990. — Пер. изд.: Великобритания, 1987. 384 е.: ил. ISBN 5−7245−0418−9
- Мичуринское плодородие". № 2 007 125 749/22 — заявл. 06.07.07 — опубл. 27.02.08 — Бюл. № 6. — 2 с.: ил.
- Завражнов, А.И. Конструктивные параметры устройства для снижения уплотнения в установках ускоренного компостирования Текст. / А. И. Завражнов, В. В. Миронов, П. С. Никитин // Достижения науки и техники АПК, 2008. № 8. — с. 45−47.
- Междунар. науч.-практ. конф. 15−16 ноября 2007 г. Мичуринск: Издательство МичГАУ, 2008. — с. 90−94.
- Зеников, В.И. Технологические и технические решения по подготовке компонентов и смеси для биоконверсии Текст. / В. И. Зеников // Агрохимические исследования и технологии: Труды ВНИПТИХИМ, 1999. — T.l.-c. 287−293.
- Лопес де Гереню, В. О. Изменение ОВП при биотермическом разложении органических субстратов в аэрируемых биореакторах Текст. / В. О. Лопес де Гереню, И. Н. Курганова // Доклады Россельхозакадемии. — 1998.-№ 4.-с. 26−27
- Чересленко, В.Н. Исследование физико-механических свойств твердых бытовых отходов с целью расчета пневмоаэрационных систем мусороперерабатывающих заводов Текст.: автореф. дис.. канд. тех. наук. -М., 1973.-29 с.
- Тимочкин, А.В. Совершенствование разгрузочного процесса в транспортно складских комплексах Текст.: дис.. канд. техн. наук: 05.20.01. — СПб, 2003 — 147 е.: ил.
- Гячев, JI.B. Движение сыпучих материалов в трубах и бункерах. -М.: «Машиностроение», 1968. 210 е.: ил.
- Иванов, М.Г. Исследование процесса сводообразования в бункерах и рудоспусках Текст.: дис. канд. техн. наук: 05.20.01.— Д., ЛГИ, 1964. 183 с.
- Цимбаревич, П.Н. Механика горных пород/ П. Н. Цимбаревич -М., 1948. С. 15−18.
- Варламов, А.В. Повышение эффективности процесса выпуска компонентов комбикорма бункером с донными щелевыми отверстиями и механическим сводообрушителем Текст.: дис. канд. техн. наук: 05.20.01 — Саратов, 1999. 141 е.: ил.
- Горюшинский, И.В. Совершенствование рабочего процесса и обоснование параметров бункерного устройства с побудителем выгрузки Текст.: дис. канд. техн. наук: 05.20.01. Саратов, 1997. — 139 е.: ил.
- Горюшинская, Е.В. Повышение эффективности выпуска компонентов комбикорма бункерными устройствами со щелевым отверстием по периметру дна и механическими питателями-побудителями Текст.: дис.. канд. техн. наук: 05.20.01— Саратов, 1999. — 153 е.: ил.
- Комченко, Е.В. Совершенствование процесса истечения мелких сыпучих материалов из бункеров с/х назначения Текст.: дис.. канд. техн. наук: 05.20.01. Ростов на Дону, 2003. — 192 е.: ил.
- Стальной, В.П. Повышение эффективности процесса выгрузки влажных зерновых материалов из бункеров с/х назначения Текст.: дис.. канд. техн. наук: 05.20.01 Зерноград, 2004 — 138 е.: ил.
- Кожевников, В.А. Совершенствование процесса выпуска трудносыпучих материалов из бункеров с/х назначения Текст.: дис.. канд. техн. наук: 05.20.01. Самара, 2005 — 148 е.: ил.
- Зенков, Р.Л. Механика насыпных грузов (основания расчета погрузочно-разгрузочных и транспортирующих устройств) Текст. / Р. Л. Зенков. М.: Машгиз, 1952.-216 с.
- Резник, Н.Е. Теория резания лезвием и основы расчета режущих аппаратов Текст. / Н. Е. Резник. М.: Машиностроение, 1975. — 311с.
- Горячкин, В.П. Собрание сочинений Текст. / В.П. Горячкин- под ред. Н. Д. Лучинского. — 2-е изд. — М.: Колос, 1968. — Т. 3. с. 26−133.
- Желиговский, В.А. Экспериментальная теория резания лезвием Текст. / В. А. Желиговский // Труды МИМЭСХ: Вып. 9. М., 1940. — 27 с.
- Ивашко А.А. Вопросы теории резания органических материалов лезвием Текст. / А. А. Ивашко // Тракторы и сельхозмашины, 1958. — № 2. — с. 34−37.
- Даурский, А.Н. Резание пищевых материалов: Теория процесса машины, интенсификация Текст. / А. Н. Даурский, Ю. А. Мачихин. М.: Пищевая промышленность, 1980. — 240 с.
- Трубилин, Е.И. Анализ процесса резания соломы и его энергетические показатели Текст. / Е.И. Трубилин- Кубанский ГАУ. — Краснодар, 1987. с. 18. — Деп. в ВНИИТЭИ Агропром 29.12.1995, № 219
- Борисенко, А.А. Режущие механизмы пищевой промышленности Текст.: Монография / А. А. Борисенко, А. Г. Бареян, Л. А. Борисенко. -Ставрополь: Изд-во Сев.-Кавказ. гос. тех. ун-т, 2004. 208 с. — ISBN 5−10 003 567−6.
- Цытович, Н.А. Механика грунтов (краткий курс) Текст. / Цытович Н. А. 2-е изд. доп., учебн. для вузов. — М.: Высшая школа, 1973. — 280 с. с ил.
- Дубинин, В.Ф. Физико-механические и перегрузочные свойства сельскохозяйственных грузов: учебное пособие Текст. / В. Ф. Дубинин, П. И. Павлов. — Саратов: Изд-во Сарат.гос.с.-х.акад., 1996. — 100 с.
- Репникова, Е.А. Пористость материалов и методы ее определения Текст.: Учеб. пособие / Е. А. Репникова, В. В. Петрова. -Петрозаводск: Изд-во ПетрГУ, 2007. 97 с.
- Жуковский, Н.Е. Механика системы. Динамика твердого тела Текст. / Н. Е. Жуковский / Под ред. А. П. Котельникова. — Изд. 2-е, стереотипное. М.: КомКнига, 2005. — 296 с. ISBN 5−484−33−5
- Левин, В.Е. Деформирование криволинейных стержней. Часть 1. Статика плоских криволинейных стержней: Учеб. пособие. Текст. / В. Е. Левин. Новосибирск: Изд-во НГТУ, 2004. — 84 с.
- Светлицкий, В.А. Механика абсолютно гибких стержней Текст. / В. А. Светлицкий / Под ред. А. Ю. Ишллинского. — М.: Изд-во МАИ, 2001. — 432 е.: ил. ISBN 5−7035−2482−2
- Смирнов, В.И. Курс теоретической механики: Учебник Текст. / В. И. Смирнов, Г. И. Чистобородов, М. С. Губерман. — Иваново: ИГТА, 2004. -536 с. ISBN 5−88 954−167−6
- Ковалев, Н.Г. Сельскохозяйственные материалы: виды, состав, свойства Текст.: учебное и учеб. пособие для высших учеб. заведений / Н. Г. Ковалев, Г. А. Хайлис, М. М. Ковалев. М.: ИК «Родник», журнал «Аграрная наука», 1998.-208 с.
- Павлов, П.И. Научно-технические решения проблемы ресурсосбережения при использовании навозопогрузчиков непрерывного действия Текст.: дис.. док. тех. наук. — Саратов, 2002. — 374 с.
- Ягодин, Б.А. Агрохимия Текст. / Ягодин Б. А., Жуков Ю. П., Кобзаренко В. И. / Под ред. Б. А. Ягодина. М.: Колос, 2002. — 584 е.: ил. — ISBN 5−10−3 588−9
- Методы анализов органических удобрений Текст. / Составители: Л. И. Еськова, С. И. Тарасов / Под общ. ред. А. И. Еськова. М.: Россельхозакадемия — ГНУ ВНИПТИОУ, 2003. -552 с. — ISNB 5−85 941−025−5
- Eneji, А.Е. Physico-chemical changes in livestock teces during composting Text. / A.E. Eneji, S. Yamamotos, T. Honna, A. Ishiguro // Communic. in Soil Sc. Plant Analysis. 2001. — Vol.32 №¾ — p.471−489.
- Forster, J. Comparison of chemical and microbiological methods for characterization of the maturity of composts from confrasting sourses Text. / J. Forster, W. Zech //Biol. Fertil. Soils. 1993. — Vol.16, № 2 — p.93−99.
- Goddeu, B. On the use of biological and chemical indexes for determining agricultural compost maturity: extension to the field scale Text. / B. Goddeu, M.-J. Pennincks // Agr. Wastes. 1986. — Vol.15, № 3 — p.169−178.
- Harada, Y. The measurement of cation-exchange capacity of compost for the estimation of the degree of maturity Text. / Y. Harada, A. Inoko // Soil Science and Plant Nutrition. 1980. — Vol.26, № 1 — p. 127−134.
- Hirohisa, H. Evaluation method of compost humification Text. / H. Hirohisa, T. Diazo // Kawasaki seitetsu giho. 1995. — Vol.27, № 1 — p. 131−134.
- Inoko, A. Evaluation of maturity of various composted materials Text. / Akio Inoko // JARQ. 1985. — Vol.19, № 2 — p.103−108.
- Jacas, J. Cation-exchange capacity variation during the composting of different materials Text. / J. Jacas, J. Marza, P. Florenza // Compost: production, quality and use. Proc. Symp. Udine, 1985. N.Y., 1986. — p.309−320.
- Lomax, Ken M. Air movement within compost Text. / Ken M. Lomax // Mushroom News. 1999. — May. — pp. 34−36.
- Morel, J. Methods for the evalunion of the maturity of the municipal refuse compost Text. / J. Morel, F. Colin, J. Germon // Composting of agricultural and other wastes. Proc. Symp. Udine, 1985. N.Y., 1986. — p.56−71.
- Osada, Т. Composting of animal wastes: Methods for estimation of maturity Text. / T. Osada, K. Haga, Y. Harada // Trans. 14th Int. Congr. Soil Sci.- Kyoto. 1990. — Vol.4, Cominis 4. — p.553−554.
- Saviozzi, A. Compost maturity by water extract analysis Text. / A. Saviozzi, R. Riffaldi, R. Levi-Minzi // Composting of agricultural and other wastes. Proc. Symp. Udine, 1985. -N.Y., 1986. p.81−92.
- Thirion, F. Physical characterization of animal manure Text. / F. Thirion, F. Chabot, P. Adelen // Ramiran 98. Rome: Antony, 1999. — p.457−469
- Vana, J. The influence of aeration on compost maturity Text. / J. Vana, J.OJ. Munoz, B. Havrland // Agricultura tropica et subtropica. — 2003. — Vol. 36. pp. 88−90.
- Мельников, С.В. Планирование эксперимента в исследованиях сельскохозяйственных процессов Текст. / С. В. Мельников, В. Р. Апешкин, П. М. Рощин. 2-е изд. Перераб. И доп. — Л.: Колос, 1980. — 168 е., ил.
- Саутин, С.Н. Планирование эксперимента в химии и химической технологии Текст. / С. Н. Саутин. — Л.: Химия, 1975. 48 с.
- Коновалов, В.В. Практикум по обработке результатов научных исследований с помощью ПЭВМ Текст.: Учебное пособие / В. В. Коновалов.- Пенза: ПГСХА, 2003. 176 с.
- Методика определения экономической эффективности технологий и сельскохозяйственной техники Текст. М.: «Минсельхозпрод», 1998. — 219 с.
- Каталог транспортирующего и перегрузочного оборудования Электронный ресурс. Электрон, дан. — 2009. — Режим доступа: http://www.elevatormash.net