Электрофизический метод снижения энергопотребления и аспирационных выбросов при измельчении неорганических материалов
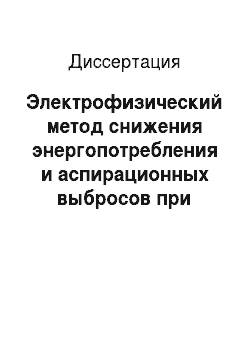
Промышленные испытания генератора ПЧМС, проведенные на цементном предприятии «Cement Hranice» (Чехия) на стадии измельчения сырьевых компонентов для получения портландцемента в цикле с сепаратором, показали, что удается снизить количество материала в цикле «измельчитель — сепаратор» за счет более эффективного удаления готового материала. Расход электроэнергии снижается за счет уменьшения ежечасно… Читать ещё >
Содержание
- 1. Аналитический обзор
- 1. 1. Энергоёмкость процессов измельчения
- 1. 1. 1. Способы расчета удельных энергозатрат при измельчении материалов
- 1. 1. 2. Технологии и оборудование, применяемые в процессах измельчения
- 1. 1. 3. Явления, обуславливающие увеличение удельных энергозатрат в процессах измельчения
- 1. 2. Влияние процессов измельчения на окружающую среду и санитарно-гигиеническую обстановку в производственных помещениях
- 1. 2. 1. Выбросы вредных веществ в атмосферу и их воздействие на окружающую среду
- 1. 2. 2. Загрязнение воздуха пылью и ее воздействие на организм человека при измельчении твердых материалов
- 1. 3. Статическое электричество — как фактор, снижающий производительность размольного оборудования и эффективность работы пылеочистительных установок
- 1. 3. 1. Механизм электризации измельчаемого материала
- 1. 3. 2. Влияние статического электричества на производительность оборудования и на физические свойства готового продукта
- 1. 3. 3. Способы нейтрализации зарядов статического электричества
- 1. 4. Методы интенсификации процессов измельчения и снижения выбросов вредных веществ в атмосферу
- 1. 5. Цель и постановка задач исследования
- 1. 1. Энергоёмкость процессов измельчения
- 2. Характеристика материалов и методики исследований
- 2. 1. Характеристика материалов
- 2. 2. Методики исследования и обработка результатов эксперимента
- 3. Теоретические основы электрофизического метода снижения энергопотребления и аспирационных выбросов в атмосферу
- 3. 1. Зависимость степени измельчения твёрдых материалов от физико-химических свойств
- 3. 2. Влияние электрических и магнитных полей на процесс измельчения
- 3. 3. Механизм образования и воздействия диэлектрического пограничного слоя (ДПС) на накопление и отвод заряда
- 3. 4. Поляризация измельчаемого материала
- 3. 5. Снижение электростатического заряда измельчаемого материала с помощью генератора переменного частотно-модулированного сигнала (ПЧМС)
- 3. 6. Механизмы разупрочнения измельчаемых материалов
- 4. Экспериментальная часть
- 4. 1. Обоснование выбора промышленных материалов для исследования
- 4. 2. Исследования влияния ПЧМС на электрофизические свойства материалов
- 4. 2. 1. Определение удельной электропроводности исследуемых материалов
- 4. 2. 2. Определение диэлектрической проницаемости исследуемых материалов
- 4. 2. 3. Определение емкостного, активного и общего сопротивления диэлектрического пограничного слоя (ДПС) промышленной мельницы
- 4. 3. Исследование влияния ПЧМС на физико-химические свойства, гранулометрический состав и кинетику накопления заряда на измельчаемых материалах
4.3.1 Исследование воздействия ПЧМС на кинетику процесса измельчения, накопление заряда и физические свойства дефторированного фосфата кальция (ДФФ) при измельчении его в шаровой и вибрационной мельницах.
4.3.2 Исследование воздействия ПЧМС на кинетику процесса измельчения, накопление заряда и физические свойства извести в процессе её измельчения
4.3.3 Исследование воздействия ПЧМС на кинетику процесса измельчения, накопление заряда и физические свойства фосфоритной руды в процессе её измельчения
4.3.4 Исследование воздействия ПЧМС на кинетику процесса измельчения, накопление заряда и физические свойства природного цеолита в процессе его измельчения
Электрофизический метод снижения энергопотребления и аспирационных выбросов при измельчении неорганических материалов (реферат, курсовая, диплом, контрольная)
Процесс измельчения твердых неорганических веществ является одной из самых распространенных операций в химической промышленности, в производстве строительных материалов и в ряде других областей народного хозяйства. Эти производства являются высокоэнергоемкими и одними из основных источников загрязнения окружающей среды вредными отходящими газами и пылью, нанося ей тем самым значительный вред. Кроме того, запыленность воздуха в цехах ухудшает санитарно-гигиенические условия труда и вызывает профессиональные заболевания.
В настоящее время мировое производство порошков достигает миллиарда тонн в год, на это затрачивается около 10% всей вырабатываемой электроэнергии, а количество выбросов пыли в атмосферу достигло гигантских размеров: при измельчении извести — 312,4 тыс. т/ггипса — 99,4 тыс. т/гфосфоритной руды — 81,9 тыс. т/г- [1].
Применяемые пылеулавливающие аппараты обеспечивают существенное снижение концентрации пыли в воздухе и отходящих газах, однако запыленность технологических выбросов часто превышает предельно допустимые выбросы, поэтому большинство исследований по снижению техногенной нагрузки и интенсификации процесса измельчения направлены на усовершенствование и создание нового технологического оборудования, а также использование различных интенсификаторов. Однако, при определенной дисперсности измельчаемого материала основное влияние на интенсификацию процесса измельчения оказывает его электризация. Существующие методы отвода электрического заряда направлены на использование антистатиков поверхностноактивных веществ и увлажнение наэлектризованных продуктов. Эти способы малоэффективны, экономически не выгодны и приводят к ухудшению физических свойств готового продукта, кроме того, они не учитывают негативного влияния пограничного буферного слоя, образующегося за счет налипания наэлектризованных частиц на стенках мельницы. Буферный слой препятствует полезной механической работе мелющих тел и отводу электростатического заряда с измельчаемого материала через заземленные стенки мельницы, в результате это приводит к забивке секционирующих решеток мельницы, пневмокамерных насосов, циклонов и рукавных фильтров.
В связи с этим разработка нового электрофизического метода повышения эффективности очистки газовоздушных потоков от пыли и снижения энергопотребления является весьма важной и актуальной проблемой.
Целью данной работы является разработка нового метода отвода электростатического заряда с измельчаемого материала, позволяющего интенсифицировать эффективность очистки отходящих технологических газов от пыли и снизить удельные энергозатраты на стадии измельчения твердых неорганических продуктов. Для достижения поставленной цели в диссертации решены следующие вопросы:
1. Предложен электрофизический метод отвода электростатического потенциала с измельчаемого материала и разработан его механизм воздействия на процесс измельчения.
2. Изучено влияние переменного частотно-модулированного сигнала (ПЧМС) на кинетику накопления электростатического заряда на исследуемых материалах в процессе их измельчения и его отвод через диэлектрический пограничный слой (ДПС).
3. Исследовано влияние генератора ПЧМС на интенсификацию процесса измельчения и на физические свойства измельчаемого продукта.
4. В промышленных условиях испытано влияние генератора ПЧМС на процесс измельчения и стадию очистки газовоздушного потока в производстве дефто-рированного фосфата кальция на ОАО «Фосфорит» и на процесс измельчения портландцементного клинкера на цементных заводах фирмы «Nesher Israel Cement Enterprises Ltd.», (Израиль) и «Cement Hranice», (Чехия).
Выводы
1. Разработан новый электрофизический метод снижения удельного энергопотребления, уменьшения выбросов пыли и токсичных веществ при измельчении неорганических материалов на производствах минеральных удобрений и строительных материалов.
2. Предложен механизм воздействия генератора переменного частотно-модулированного сигнала (ПЧМС) на измельчаемый материал, основной составляющей которого, является снижение общего сопротивления ДПС, за счет появления емкостной проводимости.
3. Исследована кинетика накопления электростатического заряда в процессе измельчения исследуемых неорганических материалов и получены новые данные об отводе заряда при помощи генератора ПЧМС: снижение электростатического заряда при измельчении ДФФ на 19.4%- извести на 14.0%- фосфоритной руды на 10.8% и природного цеолита на 3.2%.
4. Результаты исследований электрофизических свойств измельчаемых материалов показали, что наибольший эффект от воздействия ПЧМС наблюдается у веществ обладающих низкой удельной электропроводностью (порядка 1 10 10 Ом «'см «'), относительной диэлектрической проницаемостью не выше 7 — 8 и способностью к агрегированию при измельчении.
5. Проведенные исследования процесса измельчения с воздействием генератора ПЧМС показали его высокую эффективность снятия электростатического потенциала с измельчаемых продуктов, при этом удельная поверхность измельчаемого материала увеличивается, в среднем, на 12 — 14%, уплотняемость продукта снижается на 7.5%, улучшается текучесть и увеличивается угол естественного откоса, примерно, на 8%.
6. Показано, что использование данного метода в процессе измельчения твердых неорганических материалов позволяет снизить удельные энергозатраты шаровой мельницы в цементном производстве на 8 — 10%, в производстве ДФФ на 10 — 15% что соответствует снижению энергозатрат на измельчение ДФФ, примерно на один млн. кВт-ч/год
7. Промышленные испытания генератора ПЧМС в производстве ДФФ на стадии аспирационной очистки воздуха от пыли показали увеличение эффективности работы системы очистки в целом по тракту, в среднем, на 16.1%, снижение уп-лотняемости продуктов пылеуноса — на 7.5% за счет снижения запыленности воздуха, отсасываемого из мельницы, и исключения забивки бункеров циклонов и рукавных фильтров.
4.3.5 Заключение
Проведенные экспериментальные исследования по влиянию переменного частотно-модулированного сигнала (ПЧМС) на процесс измельчения твердых неорганических материалов полностью подтвердили теоретическое обоснование (глава 3.) положительного его влияния на снижение электростатического потенциала измельчаемых продуктов и улучшение их физических свойств.
Удельный заряд, накапливающийся на измельчаемых образцах под действием ПЧМС, снижается на 2.3% для природных цеолитов и до 19.4% для обесфторенного фосфата кальция. Отвод электростатического заряда через диэлектрический пограничный слой при помощи воздействия ПЧМС существенно влияет на эффективность процесса измельчения, в частности, на увеличение удельной поверхности исследуемых материалов при одном и том же времени измельчения. За 30 минут измельчения удельная поверхность образцов увеличивается благодаря действию ПЧМС для дефторированного фосфата кальция на 6.6%, извести на 7.6%, фосфоритной руды на 5.0%, а для природных цеолитов она практически не меняется. Это также подтверждает наше заключение о наибольшем влиянии ПЧМС на материалы, которые обладают хорошими диэлектрическими свойствами и низкой гигроскопичностью. Уплотняемость образцов снижается под воздействием ПЧМС, что способствует снижению толщины и плотности диэлектрического пограничного слоя, а следовательно, снижения его сопротивления. Это приводит к снижению уровня электростатического потенциала измельчаемого материала и, как следствие, к интенсификации процесса измельчения.
5. Промышленные испытания
Промышленные испытания проводили в цехе дефторированного фосфата кальция на ОАО «Фосфорит» (г. Кингисепп), на цементных заводах фирмы «Nesher Israel Cement Enterprises Ltd.» (Израиль) и «Cement Hranice» (Чехия).
5.1 Промышленные испытания электрофизического метода снижения удельного энергопотребления и аспирационных выбросов в атмосферу в процессе измельчения дефторированного фосфата кальция на ОАО «Фосфорит»
На ОАО «Фосфорит» г. Кингисепп в производстве дефторированного фосфата кальция (ДФФ) на стадии его измельчения с 11 по 17.04.96 года и с 18.06 по 8.07.97 были проведены промышленные испытания по апробации электрофизического метода отвода электростатического потенциала с измельчаемого продукта. Акты промышленных испытаний представлены в приложении 1.
Целью проведенных испытаний было подтверждение полученных лабораторных данных по влиянию ПЧМС на интенсификацию процесса при измельчения ДФФ, увеличение его дисперсности, на изменение гранулометрического состава, насыпного веса и уплотняемости.
Измельчение предварительно обожженного клинкера ДФФ на ОАО «Фосфорит» проводили в шаровой мельнице производительностью 50 т/ч., работавшей в непрерывном режиме. Габаритные размеры: длина -8м., диаметр -2.6 м., высота — 3.2 м. Мощность электропривода — 1000 кВт/ч. При проведении испытаний с 11.04 по 17.04.96 производительность шаровой мельницы по готовому продукту варьировали от 20 до 40 т/ч., при этом через каждый час работы отбирали пробы для анализа поступающего на измельчение клинкера и молотого продукта на выходе из мельницы. Принципиальная технологическая схема производства дефторированного фосфата кальция приведена на рис. 33. При проведении испытаний контролировали:
• выход продукта из мельницы (количество циклов выгрузки пневмокамерных насосов в час).
• амперная характеристика пневмовинтового насоса НПВ — 110 на выгрузке молотого продукта.
• уровень пыли в бункерах рукавного фильтра в системе аспирационной очистки воздуха.
• гранулометрический и химический состав клинкера.
• прочность клинкера.
• гранулометрический состав молотого ДФФ на выходе из мельницы.
• удельную поверхность молотого ДФФ.
• угол естественного откоса молотого ДФФ.
• насыпную плотность молотого ДФФ.
• уплотняемость молотого ДФФ.
Перед запуском мельницы и после окончания испытаний проводили визуальный осмотр сегментной решетки мельницы, установленной между первой и второй секциями.
В процессе измельчения ДФФ наблюдается ряд негативных явлений, рассмотренных в главе 1. В частности при измельчении твердых неорганических материалов на внутренней поверхности мельницы образуется плотный слой, снижающий эффективность измельчения и препятствующий оттоку электростатических зарядов на землю.
В результате накопления электростатического потенциала в объеме измельчаемого ДФФ происходит забивание секционирующей решетки мельницы, снижается эффективность работы пневмокамерных насосов, происходит зависание продукта в циклонах и забиваются рукавные фильтры. Все это приводит к ухудшению физических свойств готового продукта, снижению производительности мельницы и снижению эффективности очистки воздуха от пыли в аспи-рационной системе.
В процессе измельчения ДФФ для снижения электризации материала в мельницу в промышленных условиях подается вода. При проведении испытаний вода, подаваемая в мельницу, была отключена. Для сравнения работы мельницы с ПЧМС и без него предварительно, в течение 8 часов проводились фоновые замеры основных показателей работы мельницы и отбор контрольных проб исходного клинкера и молотого готового продукта при различной производительности мельницы.
После пуска мельницы с нагрузкой в 40 т/ч без подачи воды в зону помола, через час начались неполадки в работе пневмовинтового насоса и мельница была остановлена. Визуальный осмотр сегментной решетки в мельнице при этом показал, что отверстия в решетке были практически полностью забиты, вследствие чего выход готового продукта из мельницы был затруднен. Производительность мельницы оценивали по количеству циклов выгрузки пневмока-мерных насосов, установленных после пневмовинтового насоса НПВ — 110, о равномерности выгрузки продукта из мельницы судили по амперной характеристике насоса.
Электрофизическое воздействие на работу шаровой мельницы осуществляли с помощью генератора ПЧМС, который в начале подключали к течке подачи клинкера, а затем к корпусу мельницы в районе установки сегментной решетки, через специально изготовленный контактный электрод. Контроль гранулометрического состава клинкера и его прочность представлены в табл. 1 (приложение 1). Результаты испытаний представлены в табл. 2 (приложение 1), где приведены значения контролируемых параметров измельчаемого продукта при различной производительности мельницы.
Результаты промышленных испытаний убедительно подтвердили высокую эффективность воздействия ПЧМС на интенсивность процесса измельчения ДФФ и улучшения его физических свойств.
Удельная поверхность измельченного продукта с воздействием ПЧМС при нагрузках мельницы от 20 до 35 т/ч была выше, чем в фоновых замерах. Это наблюдалось даже в тех случаях, когда в мельницу подавалось больше клинкера из силоса № 1, чем молотого некондиционного продукта из силоса № 2. При фоновых замерах, то есть без воздействия ПЧМС, удельная поверхЛ ность готового продукта не превышала 3776 см / г не смотря на то, что в мельницу подавалось от 58.6 до 67.9% продукта фракции — 1.25 мм. В то время как с воздействием ПЧМС она увеличивается в отдельных случаях до 4850 см 2/ г., при подаче в мельницу всего от 21.4 до 50.2% фракции — 1.25 мм. Удельная поверхность молотого ДФФ увеличивается, в среднем, на 12 — 14% по сравнению с фоновыми замерами, в то время как в лабораторных условиях она увеличивалась всего на 6.6%. Эффективность воздействия ПЧМС наиболее значимо проявляется на промышленном оборудовании, когда в процессе измельчения накапливается электростатический потенциал и образуется ДПС значительно большего значения, чем при проведении измельчения в лабораторных условиях. К тому же надо отметить, что при нагрузках выше 35 т/ч без воздействия ПЧМС и без подачи воды, мельницу приходиться останавливать, как было указано ранее.
Уплотняемость готового продукта с воздействием ПЧМС при всех нагрузках мельницы снизилась — от 14.4% до 6.7% при нагрузке 25 т/ч и от 16.7% до 9.9% при нагрузке мельницы 35 т/ч. То же самое наблюдается и при высоких нагрузках мельницы, она в среднем снижается в 2 раза. Снижение уплотняемо-сти молотого ДФФ влияет на его текучесть, что способствует улучшению работы пневмокамерных насосов и всей аспирационной системы и косвенно подтверждает снижение электростатического потенциала на измельчаемом продукте. Улучшение текучести молотого ДФФ под воздействием ПЧМС подтверждается полученными значениями угла естественного откоса для всех отбираемых в процессе испытаний пробах. Он уменьшается от 51 — 53 ° до 48 -50 то есть, примерно, на 8%.
Визуальный осмотр секционирующей решетки в мельнице после ее остановки показал, что она осталась практически чистая. Это показывает, что ПЧМС не дает возможности электризоваться материалу, соответственно снижая образование агломиратов, которые способствуют забиванию решетки. Производительность шаровой мельницы за время работы (с 12.04.96 по 17.04.06) с использованием генератора ПЧМС увеличивается, в среднем, на 9 т/ч, (от 27 т/ч при фоновых замерах до 36 т/ч).
Вторая серия промышленных испытаний (18.06.97 — 08.07.97) являлись продолжением испытаний, проведенных в 1996 году и показавших существенное улучшение качественных характеристик молотого продукта, а также снижение удельной энергоемкости процесса сухого помола клинкера ДФФ и стабилизации работы оборудования на стадии измельчения и очистки газа от пыли при воздействии на работу мельницы ПЧМС. Этими испытаниями контролировались те же параметры, что и в предыдущих испытаниях. Но для более убедительного подтверждения эффективности работы генератора ПЧМС в процессе измельчения ДФФ, дополнительно определялась влажность готового продукта и испытания проводились в более широком диапазоне производительности мельницы (от 20 до 55 т/ч). Результаты испытаний представлены в табл. 3 и 4 (приложение 1).
Более длительные испытания подтвердили, результаты первой серии испытаний, а именно — положительное воздействие ПЧМС на процесс измельчения ДФФ. Размол клинкера ДФФ осуществлен без подачи воды на него, что свидетельствует о снятии заряда статического электричества. При этом не происходило зарастания продуктом решетки мельницы. Производительность шаровой мельницы увеличивается на 7.5 — 9.0%, удельная поверхность молотого продукта возросла на 11.5 — 6.4%, а угол естественного откосауменьшаетсяв, среднем, на 3 — 4 При этом отмечено, что угол естественного откоса имел тенденцию к снижению на 3 -5 ° по мере увеличения нагрузки на мельницу от 30 до 50 т/ч.
Итак, проведенные промышленные испытания полностью подтвердили теоретическое обоснование (глава 3) и результаты лабораторных исследований (глава 4) эффективное воздействие ПЧМС на существенное улучшение физических свойств ДФФ при его измельчении, на увеличение производительности работы шаровой мельницы и оздоровление санитарно — гигиенических условий в рабочем помещении отделения размола за счет стабилизации работы пневмо-камерных насосов.
Принципиальная технологическая схема производства дефторированного фосфата кальция
НъРОу 4 2. воздух Г 1
Гаь
Рис.
ДФФ н Ш
•/2 1' V
Пыль
1 — напорный бак
2 — бункер
3 — смеситель
4 -гранулйтор
5 — печь Г
У4
•/5 аз
10 — силос
11 — циклон
12 — фильтр
13 — бункер
14 — вентилятор
6 — шаройаяМеЛьнкца 15-выхлопная
7 — теплообменник труба
8 — бункер 16 — сейаратор
9 — пневмокамерный Насос
5.2. Определение выбросов в атмосферу и эффективности процесса аспирационной очистки воздуха от пыли ДФФ под воздействием ПЧМС
Испытания проводили на ОАО «Фосфорит», г. Кингисепп, в цехе дефто-рированного фосфата кальция на стадии очистки воздуха от пыли ДФФ с 7 по 16 октября 1998 года. Программа и акты промышленных испытаний представлены в приложении 2.
Во время испытаний нагрузку на шаровую мельницу по клинкеру ДФФ варьировали от 35 до 40 т/ч. Генератор ПЧМС подключали к мельнице в районе секционирующейой решетки и к бункеру циклонов. Во время испытаний замеряли разряжение по тракту газоочистки, определяли массовый расход пылега-зового потока, проходящего через батарею циклонов, рукавные фильтры и на входе в выхлопную трубу. Определяли массовые концентрации пыли в пыле-воздушном потоке по тракту газоочистки, отбирали пробы пыли из бункера циклонов и рукавных фильтров, определяли ее насыпную плотность с уплотнением и без уплотнения, удельную поверхность и гранулометрический состав. Результаты промышленных испытаний представлены в табл. 1,2 и 3 (приложение 2).
Количество просасываемого воздуха через циклоны и рукавные фильтры изменялось в пределах от10 500 до 12 800 нм /ч при температуре от 22 до 70 С. При прохождении такого количества газа через батарею циклонов с его запыл ленностью от 6 до 20 г/нм эффективность работы циклонов за счет воздействия ПЭС увеличивается в, среднем, на 11.6%, рукавных фильтров на — 19.9%, а в целом всей системы очистки на 16.1%. Улучшаются и физические свойства пыли. Уплотняемость продуктов пылеуноса снижается в, среднем, на 7.5%, пыль становится более сыпучей и меньше забиваются рукавные фильтры и коллектор отвода пыли. Удельная поверхность пыли с воздействием ПЧМС незначительно увеличивается, примерно на 4% за счет более интенсивного измельчения в шаровой мельнице.
Таким образом, использование генератора ПЧМС для отвода электростатического потенциала с ДФФ в процессе его измельчения и на стадии очистки газовоздушного потока от пыли позволило снизить на 10 — 15% удельное энергопотребление шаровой мельницы и пневмокамерных насосов, повысить, примерно, на 16% эффективность работы аспирационной системы очистки газа, а также снизить загрязнение окружающей среды и улучшить санитарно-гигиенические условия труда в рабочих помещениях цеха.
5.3 Промышленные испытания влияния генератора ПЧМС в процессе измельчения цементного клинкера
Испытания проводили на цементных заводах фирмы «Nesher Israel Cement Enterprises Ltd.» (Израиль) с 17 по 26 января 1996 года и «Cement Hranice» (Чехия) с 13 по 21 апреля 1999 года.
Целью испытаний была промышленная апробация действия генератора ПЧМС от прибора «TRAL — Экофор» на интенсификацию процесса измельчения цементного клинкера, повышения дисперсности молотого продукта и проверки возможности ведения процесса помола без добавления ПАВ.
Во время испытаний ступенчато увеличивали нагрузку на мельницу и через каждые 40 — 60 минут отбирали пробы молотого продукта для анализов в центральной лаборатории, а основные параметры работы мельницы контролировались головным компьютером. Генератор ПЧМС подключали к мельнице и сепаратору, а на мельнице № 8 отключали подачу ПАВ в зону размола клинкера. В мельницу подавали клинкер различного грансостава и шлак. Результаты проведенных испытаний представлены на рисунках 1, 2 и 3 (приложение 3).
Графики на рис. 1 и 2 показывают работу мельницы № 7, а именно, общую нагрузку мельницы и остаток на сите (90 мкм) молотого продукта в зависимости от времени измельчения, а также нагрузку на мельницу отдельно клинкера и шлака. Испытания проводили с подачей в мельницу ПАВ, понижающей механическую прочность клинкера. Остаток на сите при общей нагрузке на мельницу 44 т/ч без воздействия ПЧМС составлял 3.4%. Через 40 минут после подключения прибора при той же нагрузке он снизился до 1.1%. После увеличения нагрузки по клинкеру на 0.5 т/ч и по шлаку на 0.5 т/ч остаток на сите повысился до 1.5%. Последующее увеличение нагрузки по клинкеру на 1 т/ч и по шлаку на 0.5 т/ч привело к росту остатка на сите до 2.4%. При такой нагрузке мельница работала длительное время и остаток на сите колебался в среднем от 1.5% до 2.2%.
Испытания на мельнице № 7 показали, что нагрузку на мельницу, при измельчении цементного клинкера и шлака с подачей ПАВ, можно увеличить на 8 — 10% с помощью воздействия ПЧМС и получить готовый продукт с той же или более высокой дисперсностью.
На рис. 3 представлены графики, соответствующие испытаниям проводимым на мельнице № 8. Испытания проводили без подачи ПАВ. Прибор подключали к мельнице и сепаратору. Остаток на сите 45 мкм — 12%, 90 мкм — 0.5%. Внешняя подача — 118 т/ч, возврат из сепаратора 115 т/ч. Образующийся при измельчении электростатический потенциал в объеме измельчаемого продукта, затрудняет его выход продукта из сепаратора. Частицы даже с размером, позволяющим им проходить через сепаратор, остаются в нем из-за электростатических сил сцепления. В начальных условиях выход из мельницы готового продукта составляет всего 50%, а через определенное время после воздействия генератора ПЧМС он увеличивается до 80%. Испытать работу мельницы в этих условиях с разной внешней нагрузкой на нее нам не удалось по производственным причинам. Подключение прибора к мельнице и сепаратору позволит значительно повысить их производительность и отказаться от применения ПАВ. В России применение жидкости при размоле запрещено экологами, она снижает электросопротивление цемента, электрофильтры на выбросах при этом снижают свою эффективность, цементная пыль в большем количестве попадает в атмосферу.
Промышленные испытания показали высокую эффективность воздействия переменного электрического сигнала специальной формы на процесс измельчения цементного клинкера. Производительность шаровой мельницы можно увеличивать на 8 — 10% и исключить подачу в зону размола экологически вредного ПАВ.
Промышленные испытания генератора ПЧМС, проведенные на цементном предприятии «Cement Hranice» (Чехия) на стадии измельчения сырьевых компонентов для получения портландцемента в цикле с сепаратором, показали, что удается снизить количество материала в цикле «измельчитель — сепаратор» за счет более эффективного удаления готового материала. Расход электроэнергии снижается за счет уменьшения ежечасно потребляемой мощности на приводе мельницы примерно на 30 кВт (при длительности работы в месяц 450 часов экономия составит 13 500 кВт час). За счет снижения количества материала, находящегося в цикле мельница-сепаратор на 8 — 14 т/час, уменьшаются сопутствующие энергозатраты на транспортировку продукции. Некоторые результаты промышленных испытаний на цементном заводе «Cement Hranice» представлены в табл.1, приложение № 3.
5.4 Оценка экономического эффекта от применения генератора ПЧМС в производстве кормовых обесфторенных фосфатов на ОАО «Фосфорит», г. Кингисепп.
Промышленные испытания по воздействию ПЧМС на процесс измельчения клинкера кормового фосфата кальция показали, что улучшаются не только физические свойства готовой продукции, но и существенно повышается производительность шаровой мельницы. Средняя производительность шаровой мельницы увеличивается от 27 т/ч без воздействия генератора ПЧМС до 36 т/ч при работе по новому режиму измельчения и без подачи воды.
Расчет ожидаемого экономического эффекта от внедрения новой технологии измельчения проводится только на основе экономии расхода электроэнергии на шаровой мельнице. Мощность электропривода мельницы равна 1000 кВт/ч. Стоимость 1 кВт/ч на ОАО «Фосфорит» на 1.05.99 г. составляет 0.21 руб.
Средняя годовая производительность цеха КОФ по измельченному фосфату кальция составляет, примерно, 100 000 т/год.
Время работы шаровой мельницы для производства 100 тыс. тонн ДФФ по заводской технологии измельчения будет:
100 000: 27 = 3703.7 часов
Время работы шаровой мельницы по новой технологии для получения 100 тыс. тонн ДФФ:
100 000: 36 = 2777.8 часов
Сокращенное время работы шаровой мельницы: 3703.7 — 2777.8 = 926 ч.
Ожидаемый экономический эффект от внедрения составит:
926×0.21×1000 = 194 460 руб/год
Внедрение нового электрофизического метода снижения удельного энергопотребления не требует дополнительных капитальных затрат и изменений норм цехового технологического регламента.
Список литературы
- Беке Б. Проблемы тонкого измельчения цемента. М.: ВНИИЭСМ, 1971.18 с.
- Интенсификация производства гипсовых вяжущих материалов /В. П.
- Балдин- Под ред. В. Б. Ратинова. М. 1988. — 167 с.
- Охрана окружающей среды в агломерационном производстве / А. К. Елисеев, В. А. Мартыненко, А. И. Караканс, В. И. Колесников. М.: Металлургия, 1994. — 176 с.
- Защита атмосферы от промышленных загрязнений: Справочник в 2 ч. /Подред. С. Калверта, Г. М. Инглумда- Пер. с англ. -М.: Металлургия, 1988. -710 с.
- Сиденко П. М. Измельчение в химической промышленности. М.: Химия, 1977.-368 с.
- Ходаков Г. С. Тонкое измельчение строительных материалов. -М.: Стройиздат, 1972. 239 с.
- Гийо Р. Проблема измельчения материалов и ее развитие / Пер. с франц. -М.: Стройиздат, 1964. 112 с.
- Шенерт К., Румпер Г. Труды европейского совещания по измельчению. -М.: Стройиздат, 1966. 602 с.
- Ходаков Г. С. Физика измельчения. М.: Наука, 1972. — 307 с.
- Совершенствование существующих и разработка новых способов производства цемента/ Отв. ред. А. М. Дмитриев. -М., 1984. 138 с.
- Совершенствование и интенсификация процессов переработки сырья: Труды НИИ цемент. Вып. 82 / Науч. ред. А. И. Здорова. М., 1984. — 146с.
- Совершенствование техники и технологии измельчения портландцементного клинкера и добавок / Науч. ред. В. 3. Пироцкого.
- М.: НИИ цемент, 1986. 164 с.
- Физико-химическая механика дисперсных структур: Сб. /Отв. ред. П. А. Ребиндер. М.: Наука, 1966. — 400 с.
- Совершенствование химии и технологии строительных материалов: сб. науч. тр. / Редкол.: А. Т. Терещенко (гл. ред.) и др.- Моск. инж.-строит, ин-т- Белгород, технол. ин-т строит, м-ов. М., 1984. — 268 с.
- Пироцкий В. 3., Хохлов В. К. Процессы измельчения в технологии цемента и пути повышения их эффективности / Всесоюз. ин-т пов. квал. рук. раб-ков. -М., 1988.- 147 с.
- Пироцкий В. 3. Состояние и направление развития техники измельчения и интенсификации процессов помола цемента: Обзор. М., 1973. — 65 с.
- Совершенствование техники и технологии измельчения портландцементного клинкера и добавок: Сб. / Науч. ред. В. 3. Пироцкого. М.: НИИ цемент, 1986, 164 с.
- Вопросы измельчения в цементной промышленности: Сб. / Отв. ред. И. В. Кравченко. М.: Стройиздат, 1972. — 189 с.
- Измельчение цементного сырья и клинкера / Всесоюз. науч.-исслед. ин-т цементной пром-ти. М., 1976. — 161 с.
- Зимон А. Д. Что такое адгезия. М.: Наука, 1983. — 176 с.
- Нудель Марк Э. Физико-химическое исследование процесса измельчения сырья при сухом способе производства цемента: Автореф. дис.. канд. техн. наук / Гос. науч.-иссл. ин-т цемент, пром-ти. М., 1975. — 21 с.
- Лапшин А. Б. Обеспыливание в производстве извести. М.: Стройиздат, 1988.-c.69.
- Лапшин А. Б. Обеспыливание в производстве гипса. Киев: Будивэльнык, 1990. — 114 с.
- Лапшин А. Б. Технология обеспыливания в производстве цемента. М.:
- Концерн «Цемент», 1996. 149 с.
- Скалин Ф. В., Канаев А. А., Коил И. 3. Энергетика и окружающая среда. -Л.: Энергоиздат, 1981.-280 с.
- Рихтер Л. А., Волков Э. П., Покровский В. Н. Охрана воздушного бассейна от выбросов тепловых электростанций. М.: Энергоиздат, 1981. — 295 с.
- Балтренас П. Б. Обеспыливание воздуха на предприятиях стройматериалов. -М.: Стройиздат, 1990. 181 с.
- Абсорбция и пылеулавливание в производстве минеральных удобрений / О. С. Ковалев, И. П. Мухленов, А. Ф. Туболкин и др.- Под ред. И. П. Мухленова, О. С. Ковалева. М.: Химия, 1987. — 208 с.
- Коузов П. А., Скрябина Л. Я. Методы определения физико-химических свойств промышленных пылей. Л.: Химия, 1983. — 144 с.
- Указания по расчету рассеивания в атмосфере вредных веществ, содержащихся в выбросах предприятий: СН 369−74. М.: Стройиздат, 1975. -41 с.
- Румянцева Г. И., Вишневская Е. П., Козлова Г. А. Общая гигиена. М.: Медицина, 1985. — 432 с.
- Пироцкий В. 3., Богданов В. С., Севастьянов В. С. Аспирация цементных мельниц. М.: ВНИИЭСМ, 1984. — 51 с.
- Банит Ф. Г., Мальгин А. Д. Пылеулавливание и очистка газов в промышлен ности строительных материалов. -М.: Стройиздат, 1979. 352 с.
- Артамонова В. Г., Шаталов Н. Н. Профессиональные болезни. М.: Медицина, 1982. — 416 с.
- Популярная медицинская энциклопедия / Гл. ред. В. И. Покровский. 3-е изд., перераб. и доп. — М.: БСЭ, 1992. — 688 с.
- Статическое электричество в химической промышленности / Б. Г. Попов, В. Н. Веревкин, В. А. Бондарь, В. И. Горшков- Под ред. Б. И. Сажина. -2-е изд., перераб. и доп. Л.: Химия, 1977. — 238 с.
- Статическое электричество в химической промышленности / Б. Г. Попов, В. Н. Веревкин, В. А. Бондарь, В. И. Горшков- Под ред. Б. И. Сажина. -2-е изд., перераб. и доп. JL: Химия, 1977. -238 с.
- Зимон А. Д. Адгезия пыли и порошков. JL: Химия, 1967. — 372 с.
- Дроздов Н. Г. Статическое электричество в промышленности. M. — JL: Госэнергоиздат, 1949. -173 с.
- Балабанов Е. М. Дисперсные системы в электрическом поле коронного разряда: Автореф. дис.. д-ра физ.-мат. наук. -М., 1954. 18 с.
- Епифанов Г. И. Физика твердого тела. М.: Высшая школа. 1965. — 276с.
- Жданов Г. С. Физика твердого тела: Учеб. пособие для вузов. М.: Моск. гос. ун-т, 1961.-501 с.
- Максимов Б. К., Обух А. А. Статическое электричество в промышленности и защита от него. М.: Энергия, 1978. — 20 с.
- Машков В. М., Куликов В. И., Шервуд Л. Я. Статическое электричество в промышленности: Обзор инф-ии / Моск. НИИ охраны труда. М.: Имидж, 1992.-48 с.
- Дерягин Б. В., Коротова Н. А., Смилга В. П. Адгезия твердых тел. М.: Наука, 1973.-280 с.
- Статическое электричество при переработке химических волокон / Пер. с нем.- Под общ. ред. И. П. Генца. М.: Легкая индустрия, 1966. — 345 с.
- Лившиц M. Н., Моисеев В. М. Электростатические явления в аэрозолях и их применение. М.: Энергия, 1965. — 153 с.
- Статическое электричество в химической промышленности (Процессы электризации и предупреждение загораний) / Б. Г. Попов, В. Н. Веревкин, В. А. Бондарь, В. И. Горшков- Под ред. Н. Г. Дроздова. Л.: Химия, 1971.-208 с.
- Староба Й., Шиморда Й. Статическое электричество в промышленности. М.: Госэнергоиздат, 1960. — 248 с.
- Herper W. R. Contact and Frictional Electrification. Oxford, 1967. — 621p.
- Богоцкий В. С. Физический энциклопедический словарь. М.: БСЭ, 1960. -с. 517−518.
- Жданов Г. С., Хунджуа А. Г. Лекции по физике твердого тела: Принципы строения, реальная структура, фазовые превращения. М.: Моск. гос. ун-т, 1988. — 229 с.
- Адам Н. К. Физика и химия поверхностей. М.: Гостехиздат, 1949. — 419с.
- Органические полупроводники / Под ред. А. В. Топчиева. М.: Изд-во АН СССР, 1963.-318 с.
- Изгарышев Н. А., Горбачев С. В. Курс теоретической электрохимии: Уч-к для хим. техн-х вузов. М. — Л.: Госхимиздат, 1951. — 504 с.
- Скорчилетти В. В. Теоретическая электрохимия. Л.: Химия, 1974. — 428 с.
- Воюцкий С. С. Курс коллоидной химии. М.: Химия, 1975. — 512 с.
- Gavis J., Koszman J. Development of charg in low conductivity liquids flowing past surfaces: a theory of the phenomenon in tubes // Colloid Sci. 1961. — v. 16. № 4.-p. 375−381.
- Koszman J., Gavis J. Development of charg in low conductivity liquids flowing past surfaces: engineering predictions from the theory developed tube flow // Chem. Eng. Sci. 1962. — v. 17. — p. 1013 — 1023.
- Веревкин В. H., Попов Б. Г., Баклыгин В. Н. Защита от вредного воздействия статического электричества. М.: НИИТЭХИМ, 1975. -с. 86−89.
- Духин С. С. Электропроводность и электрокинетические свойства дисперсных систем. Киев: Наук, думка, 1975. — 248 с.
- Левин Л. М. Исследование по физике грубодисперсных аэрозолей / АН СССР, Ин-т прикладной геофизики. М., 1961. — 267 с.
- Предупреждение взрывов и пожаров и техника безопасности в химической, нефтехимической и других областях промышленности:
- Материалы семинара, 1961 г., Дзержинск / Гос. ком. СМ РСФСР по коорд. науч.-исслед. работ, ГИНТИ. М., 1961. — 425 с.
- Хорварт Т., Берта И. Нейтрализация статического электричества / Пер. с англ. М.: Энергоатомиздат, 1987. — 102 с.
- Ребиндер П. А. Поверхностно-активные вещества. М.: Знание, 196 146 с.
- Полоник П. А. Борьба со статическим электричеством в текстильной и легкой промышленности. М.: Легкая индустрия, 1966. — 166 с.
- Каверзнев В. А., Зайцев А. А., Овечкин Ю. А. Статическое электричество в полупроводниковой промышленности. М.: Энергия, 1975. — 112 с.
- Леб Л. Статическая электризация. М. — Л.: Госэнергоиздат, 1963. — 408 с.
- Интенсификация переработки минерального сырья: Сб. / отв. ред. Г. Д. Краснов. М.: Наука, 1975.- 128 с.
- Повышение эффективности процессов измельчения портландцементного клинкера и добавок: сб. / Науч. ред. В. 3. Пироцкого. М.: НИИ цемент, 1983.- 151 с.
- Крыхтин Г. С., Кузнецов Л. Н. Интенсификация работы мельницы. -Новосибирск: Наука, 1993. 239 с.
- Piret L. Freeze grinding // Chem. and Process Engning. -1957. Vol. 38, № 6. — p. 243- 249.
- Кузьмин В. А. Разработка способов разупрочнения фосфоритных руд тепловыми и электромагнитными полями с целью повышения эффективности их измельчения: Автореф. дис. канд. техн. наук / Моск. горный ин-т. М., 1980. — 16 с.
- Руководство к практическим занятиям по технологии неорганических веществ: Учеб. пособие для вузов / Под ред. проф. М. Е. Позина. 4-е изд., перераб. и доп. — Л.: Химия, 1980. — 368 с.
- Определение гранулометрического состава и удельной поверхностипорошкообразных материалов: Метод, указания / сост.: Ю. П. Карпов, Е. П. Коваленко, Л. М. Свиридов, А. М. Головчак, К. А. Суворов- ЛТИ им. Ленсовета. Л., 1986. — 23 с.
- Практикум по коллоидной химии: Учеб. пособие для хим.-технол. спец. вузов / В. И. Баранова, Е. Е. Бибик, Н. М. Кожевникова и др.- Под ред. И. С. Лаврова. М.: Высш. шк., 1983. — 216с.
- Кельман Ф. Н., Бруцкус Е. Б., Ошерович Р. X. Методы анализа при контроле производства серной кислоты и фосфорных удобрений. М.: Госхимиздат, 1963. — 260 с.
- ГОСТ Р 50 820−95. Оборудование газоочистное и пылеулавливающее. Методы определения запыленности газопылевых потоков. М.: Изд-во стандартов, 1996. — 32 с.
- Эме Ф. Диэлектрические измерения / Пер. с нем. М.: Химия, 1967. -224 с.
- Кассандрова О. М., Лебедев В. В. Обработка результатов измерений. М.: Наука, 1970. -104 с.
- Щекотова И. А., Ивахнюк Г. К. Получение древесных активных углей методом совмещенного пиролиза парогазовой активации // ЖПХ. — 1996. -Т. 69, № 6.-с. 1050- 1052
- Николаев В. А. Закономерности и интенсификация процесса сухого измельчения цементного сырья в барабанных шаровых мельницах: Автореф. дис.. канд. техн. наук / НИИ цемент. М., 1993. — 20 с.
- Урьев Н. Б. Физико-химические основы технологии дисперсных систем и материалов. М.: Химия, 1988. — 288 с.
- Урьев Н. Б. Высококонцентрированные дисперсные системы. М.: Химия, 1980.-319 с.
- Patat F., Schmid N., Haftvermogen von Pulvern // Chem. Ind. Techn., 32, № 1, 8 (1960)
- Губкин А. М. Физика диэлектриков. Теория диэлектрической поляризации в постоянном и переменном электрическом поле: Учеб. пособие для вузов. М.: Высш. шк., 1971. — 272 с.
- Браун В. Диэлектрики / Пер. с англ. М.: ИЛ, 1961. — 326 с.
- Хиппель А. Р. Диэлектрики и волны / Пер. с англ. М.: ИЛ, 1960. — 438 с.
- Браун Т., Лемей Г. Ю. Химия в центре наук: В 2 ч. / Пер. с англ. — М.: Мир, 1983.-448 с.
- Касаткин А. С. Основы электротехники. М. — Л.: Энергия, 1966. — 712 с.
- Власов В. Ф. Электронные и ионные приборы: Учеб. пособие для радиотехнических вузов и факультетов. 3-е изд., перераб. и доп. — М.: Связьиздат, 1960. — 734 с.
- Зимон А. Д. Адгезия пленок и покрытий. М.: Химия, 1977. — 352 с.
- Зимон А. Д. Адгезия пыли и порошков. М.: Химия, 1967. — 372 с.
- Москвитин Н. И. Физико-химические основы процессов склеивания и прилипания. М.: Лес. пром., 1974. — 191 с.
- Зимон А. Д., Андрианов Е. И. Аутогезия сыпучих материалов. М.: Металлургия, 1978. — 287 с.
- Лапшин А. Б. Физическая сущность электрозаряженности пыли // Труды НИПИОТ строй. 1981. — Вып. 21.-е. 92
- Голубева А. В., Малая Г. М. Физико-химические свойства пыли промышленности нерудных строительных материалов / НИПИОТ строй. Новороссийск, 1974. — 79 с.
- Бретшнайдер Б., Курфюрст И. Охрана воздушного бассейна от загрязнений:технология и контроль / Пер. с англ. Л.: Химия, 1989. — 288 с. 1. Утверждаю:
- Зам.генерального директора по новой техншш и технологии1. АКТпромышленных испытаний работы устройства «Экофор» в цехе КОФ
- Устройство отработало в непрерывном режиме в течение 15 часов. Воду на клинкер при поступлении последнего в мельницу не подава ли.
- Производительность мельницы оценивали по количеству циклон выгрузки пневмокамерных насосов поз.374/1 и 2, установленных после пневмовинтового насоса НЯ:6 НО, равномерность выгрузки продукта из мельницы судили по амперной характеристике насоса.
- Была проведена ревизия пневмовинтового насоса (удалены из карманов остатки мелющих тел). После остановки и чистки решеток мельницы в течение четырех часов производительность ее по готовому продукту в среднем составила 27 т/ч (20-^35 т/ч) .
- Несмотря на то, что от 58,6 до 67,9% клинкера, подаваемого на мельницу, составлял продукт фракции 1,25 мм, удельная поверхность готового. молотого продукта не превышала 3776 см^г.
- Мельница с устройством «Экофор» отработала в течение 15 часов, прибор. был подключен к течке подачи клинкера, а затем перенесен в район установки решетки мельницы, где через контактный электрод выведен на корпус мельницы.
- При работе данного устройства отмечено улучшение физических свойств молотого продукта:
- Снижение уплотняемости продукта после мельницы ~в 2 раза, что. свидетельствует о повышении его текучести.
- Увеличение удельной поверхности молотого продукта р> 4000 см /г) через 6,5 часов при максимальной производительности мельницы 40 т/час.
- Производительность мельницы за время испытаний в среднем составила 36 т/ч против фоновых 27 т/час.
- Питание мельницы во время работы с прибором было представлено смесью клинкера и некондиционного молотого продукта с большей долей фр. +1,25 мм: 49,8т78,6% по сравнению с 32,1т41,4% в фоновых опытах.
- Считаем целесообразным испытать устройство «Экофор» в производстве огнетушащего порошка «Пирант-А» в цехе аммофоса. от АООТ"Фосфорит" I — -/
- Начальник цеха КОФ / Н.С.Баулин
- Зам.начальника ЦЛ ТЦалЩ^ Т.В.Николенко
- Начальник ОТК , —< / ^ — ' К. А. Вдовина
- Начальник ТО Ж/:^'' ' Р-В.Нигматулинот СПбТИ • А.В.Сукманов1. Утверждаю"
- Заместитель генерального директора АООТ’Фосфориг мйЩ$&5Е<�жнике и технологии1. В.И.Юрьева1. АКТпромышленных испытаний режима измельчения дефторированного фосфата с использованием эффекта электоимпульсного воздействия в цехе КОФ АООТ"Фосфорит".
- В результате электроимпульсного воздействия на систему продукт-мельница отмечено улучшение физико-механических свойств готового продукта:
- При работе на производительности 20 35 т/ч на 4,7 — 6,4% снизилась угоютняемость продукта.
- Величина угла естественного откоса имела тенденцию к снижению (на 3 5 град) при более высокой загрузке мельницы продуктом (в интервале нагрузок 30−45 т/ч).
- Прилохсение: таблицы результатов обследования (выборка из контроля часовых параметров при обследовании мельницы размола дефторированного фосфата и средние значения физических характеристик молотого продукта).от АООТ’Фосфорит"