Совершенствование технологии процесса гидроэластичной вытяжки деталей цилиндрической формы
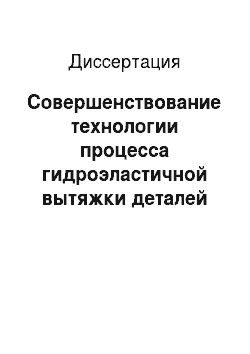
Расширение области применения вытяжки гидроэластичной матрицей может быть осуществлено на основе научно обоснованных рекомендаций по проектированию технологии вытяжки, оптимизации параметров инструмента и давления в полости матрицы применительно к материалам, наиболее часто используемым в промышленности. Для эффективного использования рекомендаций и методик расчета параметров вытяжки, сокращения… Читать ещё >
Содержание
- 1. СОСТОЯНИЕ ВОПРОСА И ПОСТАНОВКА ЗАДАЧ ИССЛЕДОВАНИЯ
- 1. 1. Анализ листоштамповочного производства деталей и изделий оборонной техники
- 1. 2. Управление трением как средство интенсификации процесса штамповки вытяжкой
- 1. 3. Контактное трение эластомеров при гидроэластичной штамповке
- 1. 4. Вытяжка эластичной матрицей
- 1. 5. Цель и задачи исследования
- 2. ТЕОРЕТИЧЕСКИЕ ОСНОВЫ ПРОЦЕССА ГИДРОЭЛАСТИЧНОЙ ВЫТЯЖКИ
- 2. 1. Постановка задачи
- 2. 2. Напряженное состояние заготовки при вытяжке цилиндрических деталей
- 2. 2. 1. Участок фланца
- 2. 2. 2. Торообразный участок
- 2. 2. 3. Цилиндрический участок
- 2. 3. Изменение давления в полости матрицы при гидроэластичной вытяжке
- 2. 3. 1. Определение давления в полости матрицы с помощью уравнения равновесия элемента заготовки
- 2. 3. 2. Определение давления в полости матрицы из условия устойчивости заготовки
- 2. 3. 3. Критический радиус вытяжного ребра матрицы
- 2. 4. Напряженно-деформированное состояние заготовки на начальном этапе гидроэластичной вытяжки
- 2. 4. 1. Изменение толщины заготовки на начальном этапе гидроэластичной вытяжки цилиндрических деталей
- 2. 4. 2. Алгоритм расчета изменения толщины заготовки на начальном этапе гидроэластичной вытяжки цилиндрических деталей
- 2. 5. Определение предельных коэффициентов вытяжки
- 2. 6. Усилие вытяжки
- 2. 7. Выводы
- 3. ЭКСПЕРИМЕНТАЛЬНОЕ ИССЛЕДОВАНИЕ ПРОЦЕССОВ ГИДРОЭЛАСТИЧНОЙ ШТАМПОВКИ
- 3. 1. Экспериментальное исследование коэффициента трения резины диафрагмы
- 3. 2. Установка для гидроэластичной штамповки
- 3. 3. Экспериментальное определение максимального утонения на первом переходе вытяжки цилиндрических деталей
- 4. ТЕХНОЛОГИЧЕСКИЕ ВОЗМОЖНОСТИ ПРОЦЕССА ГИДРОЭЛАСТИЧНОЙ ШТАМПОВКИ
- 4. 1. Расчет и изготовление инструмента
- 4. 1. 1. Испытываемые инструментом напряжения
- 4. 1. 2. Материалы инструмента
- 4. 1. 3. Крепление инструмента в прессе
- 4. 1. 4. Инструмент для метода пуансона
- 4. 1. 5. Дополнительное удерживание заготовки
- 4. 1. 6. Изготовление инструмента
- 4. 2. Нагруженная давлением диафрагма как часть инструмента
- 4. 2. 1. Радиусы, формуемые диафрагмой
- 4. 2. 2. Износ диафрагмы срок ее службы
- 4. 2. 3. Отвод воздуха
- 4. 3. Методика штамповки
- 4. 3. 1. Вспомогательные средства при проверке инструмента
- 4. 3. 2. График предварительного контроля перед проверкой инструмента
- 4. 3. 3. Общая процедура проверки
- 4. 3. 4. Факторы, влияющие на формоизменение
- 4. 3. 5. Скорость пресса
- 4. 3. 6. Модификации инструмента
- 4. 3. 7. Свойства внешней рабочей накладки
- 4. 3. 8. Контроль материала заготовки перед штамповкой
- 4. 3. 9. Смазка
- 4. 3. 10. Кривая рабочего давления
- 4. 3. 11. Уменьшение толщины материала
- 4. 3. 12. Дополнительный прижим заготовки
- 4. 3. 13. Двухслойная заготовка
- 4. 3. 14. Пример построения кривой давления
- 4. 1. Расчет и изготовление инструмента
- 5. 1. Основные цели создания системы
- 5. 2. Функциональное назначение системы
- 5. 2. 1. Требования к функциональной структуре системы
- 5. 2. 2. Требования к техническому обеспечению
- 5. 2. 4. Требование к программному обеспечению
- 5. 3. Основные технические решения проекта системы
- 5. 3. 1. Описание организации информационной базы
- 5. 3. 2. Описание системы программного обеспечения
- 5. 3. 3. Описание технологического процесса обработки данных
- 5. 4. Описание алгоритма расчета давления в полости матрицы
- 5. 5. Описание подпрограммы Raschet
- 5. 6. Описание подпрограммы Main
Совершенствование технологии процесса гидроэластичной вытяжки деталей цилиндрической формы (реферат, курсовая, диплом, контрольная)
Обработка металлов давлением является одним из основных и наиболее перспективных способов производства заготовок и деталей в изделиях оборонной техники. Особая роль при этом отводится совершенствованию существующих, созданию и внедрению новых технологических процессов обработки металлов давлением, позволяющих расширить производство точных заготовок и деталей, требующих минимальной механической обработки или полностью исключающих ее, а также заготовок с высокими механическими и служебными свойствами.
Одним из основных способов производства точных заготовок посредством обработки металлов давлением является процесс вытяжки из исходной листовой заготовки. Однако традиционные технологические процессы вытяжки в жестких штампах или не обеспечивают нужного качества и высокой точности изделий, или связаны с необходимостью выполнения большого числа переходов, что повышает трудозатраты и расходы на штамповую оснастку.
Велика отрицательная роль сил трения при вытяжке в жестких штампах. Силы трения повышают деформирующие усилия и растягивающие напряжения в стенке вытягиваемого изделия, что при локализации деформации утонения в опасной зоне приводит к уменьшению предельной степени деформации за переход. Известны также трудности штамповки изделий из материалов, склонных к схватыванию, когда приходится использовать различные защитные покрытия, часто не обеспечивающие полного разделения металла заготовок и инструмента. Многооперационность процесса вытяжки связана также с недостаточной точностью вытягиваемых изделий, имеющих значительную продольную разнотолщинность, разностенность, конусность наружной поверхности. На практике при штамповке ответственных деталей, как правило, стремятся избежать указанных дефектов за счет применения слесарной и механической обработки.
Одним из новых и интенсифицированных процессов вытяжки является вытяжка гидроэластичной матрицей. В этом случае нагруженная давлением диафрагма прижимает заготовку к той части инструмента, которая является носителем формы детали. Данная схема вытяжки характеризуется отсутствием значительных сил трения между заготовкой и диафрагмой и наличием полезных сил трения между пуансоном и заготовкой, возникающих при деформировании заготовки давлением диафрагмы, обжимающей заготовку по жестком пуансону. При вытяжке гидроэластичной матрицей происходит значительное выравнивание деформаций в объеме заготовки, что позволяет увеличивать предельные степени деформации. При отсутствии значительных сил трения по диафрагме, выступающей в роли матрицы, повышается стойкость инструмента и точность штампованных заготовок (особенно уменьшается продольная разнотолщинность).
Использование вытяжки гидроэластичной матрицей в процессах листовой штамповки позволяет повысить допустимые степени деформации за переход, сократить число штамповочных, термических, вспомогательных операций и повысить качество вытягиваемых изделий.
Расширение области применения вытяжки гидроэластичной матрицей может быть осуществлено на основе научно обоснованных рекомендаций по проектированию технологии вытяжки, оптимизации параметров инструмента и давления в полости матрицы применительно к материалам, наиболее часто используемым в промышленности. Для эффективного использования рекомендаций и методик расчета параметров вытяжки, сокращения сроков технологической подготовки, уменьшения ее трудоемкости и стоимости должна быть реализована система автоматизированного проектирования технологического процесса вытяжки гидроэластичной матрицей.
ОСНОВНЫЕ РЕЗУЛЬТАТЫ И ВЫВОДЫ.
В работе приведено решение актуальной научно-технической проблемы, имеющей важное научно-производственное значение и состоящей в исследовании процесса гидроэластичной вытяжки (первый переход) деталей цилиндрической формы, установление зависимости распределения деформации в заготовке и давления в полости матрицы от различных технологических параметров, и на их основе назначение научно-обоснованных технологических рекомендаций обеспечивающих повышение эффективности производства и формирования заданных характеристик качества изделий.
В процессе теоретического и экспериментального исследований получены следующие результаты:
1. Разработана математическая модель процесса гидроэластичной вытяжки деталей цилиндрической формы, включающая аналитические зависимости для определения закономерности изменения давления в полости матрицы при заданной минимально возможной степени утонения заготовки в опасном сечении. Установлено, что давления в полости матрицы на начальном этапе вытяжки определяется из условия устойчивости участка фланца, затем — из условия устойчивости радиусного участка, и на последнем этапеиз условия необходимого формоизменения детали.
2. Проведен теоретический анализ напряженного состояния заготовки при гидроэластичной вытяжке (первый переход) деталей цилиндрической формы, получены аналитические зависимости для определения технологических параметров процесса — давления в полости матрицы, предельного коэффициента формоизменения, критического радиуса вытяжки и максимального утонения.
Для исследуемого процесса установлено, что силы трения на контакте заготовки и мембраны уменьшают растягивающие напряжения в опасном сечении заготовки.
При анализе напряженного состояния установлено, что, несмотря на наличие сил трения между мембраной и заготовкой, играющих положительную роль, как и при вытяжке в жестких штампах, с увеличением давления эластичной мембраны, степени деформации, механических свойств листового металла (ств) и уменьшением радиуса изгиба заготовки на участке скругления (гизг) растягивающие напряжения в стенке заготовки увеличиваются.
Установлено, что с увеличением радиуса изгиба заготовки на участке скругления, относительной толщины заготовки и пластичности металла (v|/w) предельный коэффициент вытяжки уменьшается (увеличивается степень формоизменения).
3. Установлено, что на начальном этапе гидроэластичной вытяжки утонение в опасном сечении стенки заготовки увеличивается с ростом основных технологических параметров: давления в полости матрицы, пластичности листового металла (уш), степени деформации. Максимальное утонение находится в пределах 15% от исходной толщины заготовки против 25−35% при вытяжке в жестких штампах.
4. В ходе экспериментального исследования получены уравнения регрессии давления в полости матрицы и максимального утонения стенки заготовки с использованием математического планирования эксперимента и статистики. Установлено, что наибольшее влияние на давление в полости матрицы и степень утонения оказывают толщина исходной заготовки и степень формоизменения. Данные уравнения подтверждают результаты теоретического исследования: при определении давления в полости матрицы расхождение не превышало 18%, а при определении для максимального утонения 14−16%.
5. Экспериментально определен коэффициент трения для материала рабочей накладки эластичной мембраны: для стали — 0,07, для алюминиевых сплавов-0,1.
6. Разработан программный продукт, реализующий полученные аналитические зависимости, для определения характера изменения давления в полости матрицы при гидроэластичной вытяжке деталей цилиндрической формы с заданной степенью утонения.
Внедрение полученных результатов позволит шире использовать процесс вытяжки гидроэластичной матрицей в технологии изготовления цилиндрических полуфабрикатов и деталей.
Список литературы
- Айнбиндер С.Б. Свойства полимеров в различных напряженных состояниях. — М.: Химия, 1981. — 184 с.
- Арылянский Ю.М. Определение давления гидроэластичной матрицы в процессе вытяжки эллипсных деталей из анизотропных заготовок // Вестник машиностроения. 1992, № 12. — с. 46−48.
- Бартенев Г. М., Лаврентьев В. В. Трение и износ полимеров. Л.: Химия, 1972.-240 с.
- Беркович И.И., Никитин В. Е., Николаева A.M. Оценка влияния сил контактного трения на процесс штамповки эластичной средой
- Беркович И.И., Никитин В. Е., Николаева A.M. Фрикционное взаимодействие полиуретанов с металлами в условиях штамповки эластичным инструментом // Трение и износ, 1982, 3, № 5, с. 840−849.
- Бирюков Н.М. Выбор удельного давления эластичной матрицей при штамповке деталей из листа // Известия высших учебных заведений. Авиационная техника. 1958. — № 3. — с. 35−40.
- Бирюков Н.М. Определение зависимости удельного давления эластичной матрицей от глубины вытяжки: Дисс. на соиск. уч. степ, к-та техн. наук. М., 1958.- 178 с.
- Бирюков Н.М. Теоретические основы гофрообразования при вытяжке деталей летательных аппаратов из листовых заготовок: Дисс. на соиск. уч. степ, док-pa техн. наук. М., 1974. — 291 с.
- Бирюков Н.М. Усилие прижима при штамповке вытяжке деталей из листового материала // Известия вузов. Машиностроение. — 1960. — № 1. -с. 34−37.
- Бирюков Н.М. Устойчивость листовой заготовки при вытяжке цилиндрических и конических деталей жестким штампом // Известия вузов. Машиностроение. 1973. — № 2. — с. 123−127.
- Бирюков Н.М. Штамповка-вытяжка эластичной матрицей // Известия высших учебных заведений. Авиационная техника. 1958. — № 1.-е. 3742.
- Бирюков Н.М., Сизов Е. С. Исследование процесса штамповки-вытяжки полых деталей из листового металла. Штамповка-вытяжка деталей из листового металла эластичной матрицей // Труды НИАТ 1959. — № 124. -с. 47−53.
- Блинов М.А., Михайловская И. С. Анализ напряженно-деформированного состояния заготовки при штамповке полиуретаном // Кузн-штамп. пр-во, 1997, № 2, с. 20−24.
- Вейлер С. Я., Лихтман В. И. Действие смазок при обработке металлов давлением. М.: Наука, 1960. — 230 с.
- Вольмир А.С. Устойчивость деформационных систем. М.: Наука, 1967.-983 с.
- Вольмир А.С. Устойчивость упругих систем. М.: Физматгиз, 1963. -871 с.
- Вознесенский В.А. Статистические методы планирования эксперимента в технико-экономических исследованиях. М.: Статистика, 1974. — 124 с.
- Губкин С. И. Теория обработки металлов давлением. М.: Метал-лургиздат, 1947. — 532 с.
- Губкин С. И. Пластическая деформация металлов. М.: Ме-таллургиздат, 1961. — Т. II. — 416 с.
- Гуляев А.Г. Металловедение. М.: Металлургия, 1977. — 647с.
- Головлев В.Д. Устойчивость сжато-растянутых участков заготовок при вытяжке // Кузнечно-штамповочное производство. 1964. — № 1.-е. 1620.
- Горбунов М.Н. Штамповка деталей из трубчатых заготовок. М.- Машгиз, 1960.- 190 с.
- Гредитор М.Ф. Давильные работы и ротационное выдавливание. -М.- Машиностроение, 1971. 239 с.
- Деев С.С. Геометрическое моделирование процесса штамповки другой средой в режиме сверх пластичности: Укр. ин-т инж. вод. х-ва. Ровно, 1988.
- Жарков В.А. Математическое моделирование процессов вытяжки листовых материалов // Кузнечно-штамповочное производство. 1990. — № 4.-с. 13−17.
- Жвик И.М., Смирнов В. Е. Исследование процесса вытяжки с проталкиванием // Обработка металлов давлением: Труды Вузов Российской Федерации. Свердловск. — 1976. — Вып. 3. — с. 123−125.
- Зубцов М.Е. Листовая штамповка. Л.: Машиностроение, 1967.151 с.
- Исаченков В.Е. Определение деформирующих давлений при формировании замкнутых поперечно-гофрированных оболочек эластично-жидкостным пуансоном // Кузнечно-штамп. пр-во. 1978, № 7, с. 15−18.
- Исаченков В.Е. Определение деформирующих давлений при формировании деталей из листа эластично-жидкостными и эластичными средами // Кузнечно-штамп. пр-во. 1976, № 10, с. 10−13.
- Исаченков Е.И. Контактное трение и смазки при обработке металлов давлением. М.: Машиностроение, 1976. — 208 с.
- Исаченков Е.И. Развитие технологии штамповки эластичными, жидкостными и газовыми средами // Кузнечно-штамповочное производство. 1976.-№ 7.-с. 2−5.
- Исаченков Е.И. Штамповка резиной и жидкостью. М.: Машиностроение, 1967. — 367 с.
- Исаченков Е.И., Бирюков Н. М., Борисов Ю. Д., Андреев В. М. Перспективы совершенствования листовой штамповки эластичными и жидкостными средами // Кузнечно-штамп. пр-во. 1972, № 1, с. 21−24.
- Исаченков Е.И., Пихтовников Р. В. К вопросу влияния скорости деформирования на процесс штамповки деталей из листа // Вестник машиностроения. 1952. — № 5. — с. 45−50.
- Исаченков Е.И. Развитие технологии штамповки эластичными жидкостными и газовыми средами // Кузнечно-штамп. пр-во. 1976, № 7, с. 2−5.
- Исследование и внедрение процесса гидромеханической вытяжки деталей цилиндрической, конической и коробчатой формы: Отчет по НИР. Ижевский мех. ин-т (ИМИ). Руководитель Казачонок В.И.- № 78 006 240- Инв. № Б847 767. Ижевск, 1979. — 75 с.
- Казаченок В.И., Чаузов А. С. Гидродинамическое трение при вытяжке труднообрабатываемых металлов и сплавов // Кузнечно-штамповочное производство. 1965. — № 1. — С. 25−26.
- Казаченок В.И., Чаузов А. С. О путях предотвращения схватывания при вытяжке листовых материалов // В сб.: Исследование процессов обработки металлов давлением. Ижевск: ИМИ, 1966. — Вып. 1.-е. 40−42.
- Казаченок В.И., Чаузов А. С. Методика расчета давлений в смазочном слое // Исследование процессов обработки металлов давлением: Сборник научных трудов. Ижевск: ИМИ, 1967. — Вып. 2. — с. 52−57.
- Казаченок В.И. Штамповка с жидкостным трением. М.: Машиностроение. — 1978. — 78 с.
- Казаченок В.И., Перевозчиков С. Г., Михайлов Ю. О. Штамповка-вытяжка сферических деталей из стали 30ХГСА // Производственно-технический бюллетень. 1978. — № 5. — с. 6−7.
- Казаченок В. И., Михайлов Ю. О., Бородин А. В. и др. Гидравлическая многопереходная вытяжка деталей из стали 30ХГСА // Производственно-технический бюллетень. 1978. -№ 10.-е. 19−21.
- Казаченок В.И., Михайлов Ю. О., Перевозчиков С. Г. Исследование последующих переходов гидромеханической вытяжки цилиндрических деталей // Кузнечно-штамповочное производство. 1979. — № 9. — с. 14−15.
- Казаченок В.И., Михайлов Ю. О., Перевозчиков С. Г. Технологические возможности и опыт внедрения глубокой гидромеханической вытяжки // Штамповка в мелкосерийном производстве: Материалы Всесоюзного семинара. Москва, 1979. — с. 129−132.
- Казаченок В. И., Михайлов Ю. О., Перевозчиков С. Г. Эффективность гидромеханической вытяжки глубоких деталей // Издательство предприятия п/я А-1668. 1979. — № 7. — с. 51−54.
- Казаченок В.И., Михайлов Ю. О., Перевозчиков С. Г. и др. Опыт внедрения глубокой гидромеханической вытяжки // Кузнечно-штамповочное производство. 1981. -№ 10. -с. 15−16.
- Казаченок В. И., Михайлов Ю. О., Сабрикова Т. В. Гидромеханическая вытяжка. -М.: ЦНИИИнформация, 1988. 126 с.
- Казаченок В. И., Михайлов Ю. О., Сабрикова Т. В. Глава I. Гидромеханическая вытяжка. // Интенсификация процессов обработки металлов давлением / Под ред. В. И. Казачонка. Ижевск: Удмуртия, 1989. — 112 с.
- Комаров А.Д., Моисеев В. К. Штамповка эластичной средой деталей товаров народного потребления // Кузн-штамп. пр-во, 1987, № 1, с. 31−34.
- Контактно-гидродинамическая теория смазки и ее практическое применение. Куйбышев, 1973. — 178 с.
- Крагельский И.В. Расчетные методы оценки трения и износа. -Брянск, 1975. 156 с.
- Крагельский И.В., Добынич М.Н., B.C. Комбалов. Основы расчета на трение и износ. -М.: Машиностроение, 1977. 145 с.
- Крагельский И.В., Виноградова И. Э. Коэффициенты трения. М.: Машгиз, 1955.-203 с.
- Курдюмов Г. В., Утевский JI.M., Энтин Р. И. Превращение в железе и стали. М.: Наука, 1977. — 238 с.
- Мастеров В.А. Практика статистического планирования эксперимента в технологии биметаллов. М.: Металлургия, 1974. — 160с.
- Мельников Э.Л. Холодная штамповка днищ. М.: Машиностроение, 1976. — 184 с.
- Методика выбора и оптимизации контролируемых параметров технологических процессов. РДМУ 109 077. М.: Госстандарт, 1978. — 63 с.
- Михайлов Ю.О. Разработка научных основ процесса гидромеханической вытяжки: Дис. на соиск. уч. степ, д-ра техн. наук. Ижевск 1998. -428 с.
- Михайлов Ю.О., Дресвянников Д. Г. Изменение толщины заготовки на начальном этапе гидроэластичной вытяжки цилиндрических деталей // Механика деформируемого твердого тела и обработка металлов давлением. Ч. 1. Тула: Изд-во ТулГУ, 2002. — с. 224−229.
- Моисеев В.К., Комаров А. Д., Шаров А. А. Влияние трения на распределение давления эластичной среды при штамповке трубчатых деталей // Кузнечно-штамповочное производство. 1991. -№ 1. — с. 19−21.
- Налимов В.В., Чернова Н. А. Статистические методы планирования экстремальных экспериментов. М.: Наука, 1965. — 340 с.
- Недорезов В.Е. Глубокая вытяжка листового металла. М.: Маш-гиз, 1949.-с. 106.
- Новик Ф.С., Арсов Я. Б. Оптимизация процессов технологии металлов методами планирования экспериментов. М.: Машиностроение, 1980. -304 с.
- Основы теории обработки металлов давлением / Под ред. Сторожева М. В. и др. М.: Машгиз, 1959. — 539 с.
- Овчинников А.Г., Тетерин Г. П., Жарков В. А. Алгоритмы исследования методом конечных элементов вытяжки листовых материалов // Вы-числ. техн. в машиностр. Минск, 1984, № 3, с. 36−50.
- Перевозчиков С.Г., Попков В. М. Исследование точности цилиндрических деталей, изготовленных обычной и гидромеханической вытяжкой // Кузнечно-штамповочное производство. 1982. — № 7. — с.21−23.
- Пихтовников Р. В. Давление прижима в процессе глубокой вытяжки листового металла: Дисс. на соиск. уч. степ, к-та техн. наук. М., 1939. -178с.
- Платонов М.А. Вытяжка конических деталей в штампах без склад-кодержателя // Кузнечно-штамповочное производство. 1968. — № 11. — С.21−22.
- Планирование эксперимента / Под ред. В. В. Налимова. М.: Наука, 1966.-423 с.
- Погорелов Ю.М. Исследование процессов глубокой вытяжки осе-симметричных деталей жидкостной матрицей: Дисс. на соиск. уч. степ, к-та техн. наук. Челябинск, 1972. — 164 с.
- Покрас И. Б., Угланов Г. П. Изменение шероховатости заготовки при вытяжке // Исследование машин и технологии обработки металлов давлением: Сборник научных трудов. Ижевск: ИМИ, 1978. — Вып. 3. — с. 3−9.
- Поляков Ю.Л. Листовая штамповка легированных сплавов. М.: Машиностроение. — 1980. — 96 с.
- Попков В.М., Лапин С. В. Изменение размеров заготовки в процессе однопереходной гидромеханической вытяжки // Кузнечно-штамповочное производство. 1988. — № 7. — с. 16−20.
- Попов Е.А. Вытяжка с обжимом // Вестник машиностроения. -1954.-№ 12.-с. 57−60.
- Попов Е.А. Основы теории листовой штамповки. М.: Машиностроение, 1977. — 278 с.
- Попов Е.А. Роль теории в повышении эффективности обработки металлов давлением и качества продукции // Качество и эффективность при листовой и объемной штамповке. М.: МДНТП им. Ф. Э. Дзержинского, 1977. -с. 9−15.
- Попов С.П., Томилов М. Ф., Шагунов А. В. Определение коэффициента трения и распределения давления при листвой штамповке эластичными средами // Кузнечно-штамповочное производство. 1999. — № 3. — с 13−16.
- Прогрессивные технологические процессы холодной штамповки. / Под ред. А. Г. Овчинникова. -М.: Машиностроение, 1985. 184 с.
- Пустыльник Е.А. Статистические методы анализа и обработки наблюдений. М.: Наука, 1968. — 178 с.
- Решетов В.Ф., Свидетелева А. И., Черемухина Л. Г. Анализ деформированного состояния начальной стадии процесса вытяжки // Исследование машин и технологии кузнечно-штамповочного производства. Челябинск, 1971.-Вып. № 89.-с. 136−160.
- Романовский В.П. Анализ напряженно-деформированного состояния в начальной стадии процесса глубокой вытяжки // Кузнечно-штамповочное производство. 1967. — № 12. — с. 13−17.
- Романовский В.П. Процесс образования и расчет прочности опасного сечения при глубокой вытяжке // Кузнечно-штамповочное производство. -1968.-№ 9.-с. 24−28.
- Сабрикова Т. В. Повышение эффективности штамповки конических деталей: Дисс. на соиск. уч. степ, к-та техн. наук. Ижевск, 1981. — 182 с.
- Седов Л. И. Методы подобия и размерности в механике. М.: Наука, 1977.-440 с.
- Семенов А.П. Схватывание металлов. -М.: Машгиз, 1958. 175 с.
- Сизов Е.С., Антонов Е. А., Бирюков Н. М., Петров С. А. Возможности и особенности процесса глубокой вытяжки с противодавлением // Куз-нечно-штамповочное производство. 1971. — № 9. — с. 21−23.
- Сизов Е.С., Бабурин М. А. Штамповка листовых деталей сложнойформы пластично-эластичными средами. // Кузнечно-штамповочное производство. 1994. — № 8. — с. 9−11.
- Сизов Е.С., Свиридов В. М., Кашевец A.M., Эрбейгель С. А. Особенности глубокой вытяжки деталей сложных форм гидроэластичной матрицей // Кузнечно-штамп. пр-во. 1976, № 7, с. 9−11.
- Солонин И. С. Математическая статистика в технологии машиностроения. М.: Машиностроение, 1972. — 216 с.
- Спиридонов А.А. Планирование эксперимента при исследовании технологических процессов. М.: Машиностроение, 1981. — 184с.
- Сторожев М.В., Попов Е. А. Теория обработки металлов давлением. М.: Машиностроение. — 1977. — 423 с.
- Тарг С.М. Основные задачи теории ламинарных течений. М. -Л.: ГОНТИ, 1951.-418 с.
- Тимирханов Д.Д. Определение предельных коэффициентов вытяжки с противодавлением эластичной или жидкостной средами. // Кузнечно-штамповочное производство. 1979. — № 5. — с. 15−17.
- Тимирханов Д.Д. Теоретическое и экспериментальное исследование гидромеханической вытяжки: Дисс. на соиск. уч. стен, к-та техн. наук. -Л., 1975.-225 с.
- Тимошенко С.П. Устойчивость стержней, пластин и оболочек. -М.: Наука. 1971.-808 с.
- Тимошенко С.П., Гудьер Дж. Теория упругости: Пер. с англ. / Под ред. Шапиро Г. С. М.: М.: Наука. — 1979. — 560 с.
- Усаченко В.Е. Определение деформирующих давлений при формировании деталей эластично-жидкостными и эластичными средами // Кузнечно-штамп. пр-во. 1976, № 10, — с. 10−13.
- Чаузов А. С. Определение усилия прижима при вытяжке с противодавлением и жидкостным трением // Производственно-технический бюллетень. 1974. — № 12. — с. 19−20.
- Чаузов А. С. Усилие прижима и предельные коэффициенты первого перехода гидромеханической вытяжки // Кузнечно-штамповочное производство. 1978. — № 11. — с. 28−30.
- Чаузов А. С. Интенсификация гидромеханической штамповки-вытяжки // Кузнечно-штамповочное производство. 1976. — № 7. — с. 11−14.
- Чаузов А.С., Ульянов В. Г. Качество цилиндрических деталей при гидромеханической вытяжке // Кузнечно-штамповочное производство. -1979.-№ 9.-с. 11−14.
- Шалаев В.Д. К расчету изменения толщины заготовок в формоизменяющих операциях холодной штамповки // Машины и технология обработки металлов давлением: Сборник научных трудов. М.: Машиностроение, 1967.-с. 148−155.
- Шалаев В.Д. Об установившихся и неустановившихся процессах деформирования в формоизменяющихся операциях холодной штамповки // Машины и технология обработки металлов давлением: Сборник научных трудов. М.: Машиностроение, 1967. — с. 185−189.
- Шалаев В.Д. К расчету изменения толщины стенки труб при редуцировании // Машины и технология обработки металлов давлением: Сборник научных трудов. М.: Машиностроение, 1967. — с. 198−204.
- Шелкунин А.С., Исаченков Е. И. Точностные возможности глубокой вытяжки эластичной матрицей с политропическим регулированием давления //Кузнечно-штамп. пр-во. 1975, № 11, с. 23−25.
- Шелухин А.С. Глубокая вытяжка эластичной матрицей с политропическим регулированием давления // Кузнечно-штамповочное производство. 1972. -№ 1. — с. 24−26.
- Шелухин А.С., Исаченков Е.И. Точностные возможности глубокой вытяжки эластичной матрицей с политроническим регулированием давления
- Кузнечно-штамповочное производство. 1975. — № 11. — с. 23−25.
- Шофман J1.A. Теория и расчеты процессов холодной штамповки. -М.: Машиностроение, 1964. 375 с.
- Эрбейгель С.А., Письменный Э. И., Запоражан Л. Д. Схемы формирования осесимметричных деталей из трубчатых заготовок эластичной средой на гидропрессе // Кузнеч-штамп. пр-во. 1988. — № 12. — с. 21−23.
- Astrop A.W. Deep drawing and ironing tubular components. Mach. and Prod. Eng., 1976, № 3337, 583−587.
- Avitzur B. Ironing with unlimited reduction. Proc. 18th Int. Mach. Tool Des. and Res. Conf., London, 1977. London-Basingstoke, 1978, 145−150.
- Brambauer F. Deep drawing without blankholder on hydraulic single-column presses. Sheet Metal Ind., 1978, № 12, 38−40.
- Buerk E. Hydromechanical drawing. Sheet Metal Inds, 1967, № 479, 182−188.
- Campion D.J. The importance of deep drawing and ironing in the world’s metalforming technology. Sheet Metal Ind., 1979, № 3, 276−278.
- Cylinder forming an economic production route to high strength precision parts. — Eng. Mater, and Des., 1977, № 9, 66−67.
- Formability of strainless steel sheet. Prod. Des. Eng., 1970, 61−62.
- Guillot R. L’emboutissage de Г aluminium. Quelques reigles pratiques. -Rev. aluminium, 1966, № 338,97−106.
- Herold U. Hydromechanisches Tiefziehen ergibt genauere Formen und Mape. Bander — Blech — Rohre, 1981, № 3, 45−49.
- Herold U. Hydromechanisches Tiefziehen eriaubt das Opti-mieren von Mapen, Form und Toleranzen. Maschinenmarkt, 1981, № 45,920−923.
- Herold U. Hydromechanisches Tiefziehen von Tiefziehstahl und Edel-stahl. Bander — Blech — Rohre, 1981, № 4, 88−91.
- Hudd R.C., Lyons K. Effect of cup geometry on ear height and thickening in cylibdrical flat bottomed steel cups. — Metals Technol., 1975, № 9, 428 432.
- Hydromechanisches Tiefziehen ohne Dichtungsprobleme Neues Ver-fahren arbeitet schneller und reduziert Stempelkraft auf die Halfte. Fachber. Hut-tenprax. Metallweiterverarb., 1978, № 11, 996.
- Kasuga J., Nozaki N. and Kondo K. Pressure Lubricated Deep Drawing. Bulletin of JSME, 1961, v. 4, № 14, 394−405.
- Kasuga J. and Tsutsumi S. Pressure Lubricated Deep Drawing (conclusions-Bulletin of JSME, 1965, v. 8, № 29, 120−131.
- Kramer W., Schelosky H. Genauigkeit abgestreckter und druckgewaiz-ter Napfe. Ind. — Ans., 1970, № 84, 2001−2002.
- Lange L., Bush R., Kramer W. Etude de Fetirage de godets par une ou plusieurs bagues en relation avec la precision dimensionelle. Formage et trait, metaux, 1972, № 38,19−24.
- Lawrens К J. Berechnung der Umformspannungen in der freien Um-formzone beim hydromechanischen Tiefziehen. Bander- Bleche-Rohre, 1979, № 11,509−525.
- Lawrens K.J. Blechumformung durch hydromechanisches Tiefziehen. -Ind.-Anz. 1978, № 19,22−23.
- Lawrens K.J. Ermittlung der versagensgrenzen beim hydromechanischen Tiefziehen. Ind. — Ans., 1979, № 102, 71−72.
- Mellor P. B. Deep drawing and redrawing of thin sheet materials. -Sheet Metal Ind., 1977, № 12,1184−1186.
- Oehler G. Hydromechanisches Tiefziehen. Klepzig Fachber., 1969, № 11,687−692.
- Ralbe O., Schacher H.D. Fertigung von Werkstuchen aus dicken Blechen durch Umformen und Schneiolen. Blech-Rohre-Profile, 1980, № 10, 657−662.
- Schlosser D. Geometrical properties of deep-drawn, circular cylindrical cups. Part III. Blech-Rohre-Profile, 1979, № 9,484−493.
- Schlosser D. Geometrical properties of deep-drawn, circular cylindrical cups. Part IV. Blech-Rohre-Profile, 1979, № 12, 688−695.
- Schlosser D. Geometrical properties of deep-drawn, circular cylindrical cups. Part V. Blech-Rohre-Profile, 1980, № 2,130−137.
- Strasser F. How to get more from drawing dies. Tooling, 1978, № 4, 812.
- Uttinger H. Das Tiefzienen Fortsetzung aus «TR» 38 vom 11.9.1964. -Techn. Rundschau, 1964, № 45,17,19, 21, 29.
- Wick C. Cold Forming Stainless Steels. Manuf. Eng. (USA), 1978, № 2,44−49.
- Cincinate Hydroform Metal Forming Machines. Machines (USA), 1952, № 30, 41−42.
- High-production hydroforming cuts tooling and finighing cfsts. Machinery (USA), 1963, vol. 70, № 4,10−14.
- Baker hydroform process. Sheet Metal Industries, 1966, № 3.
- Burk E. Das hydromechanische ziechverfahren. Blech, 1963, № 19.
- Buerk E. Hydromechanical drawing. Sheet Metal Inds., 1967, № 479, 182−188.
- Hydromechaniches Tiefziehen ohne Dichtungsprobleme Neues Ver-fahren arbeitet schneller und reduziert Stempelkraft auf die Halfte. Fachber. Hut-tenprax. Metall weitervererb., 1978, № 11, 996.
- Lawrenz K.I. Berechmmg der Umformspannimgen in der freien Um-formzone beim hydromechanischen Tiefziehen. Bander-Bleche-Rohre, 1979, № 11,509−525.
- Lawrenz K.I. Blechumformung durch hudromechanisches Tiefziehen. -Ind.-Anz. 1978, № 19,22−23.
- Lawrenz K.I. Ermittung der versagensgrenzen beim hydromechanischen Tiefziehen. Ind. — Ans., 1979, № 102, 71−72.
- Oehler G. Hydromechanisches Tiefziehen. Klepzig Fach-ber., 1969, № 11,687−692.