Исследование и разработка способов снижения газосодержания и пористости отливок из алюминиевых сплавов при литье под давлением
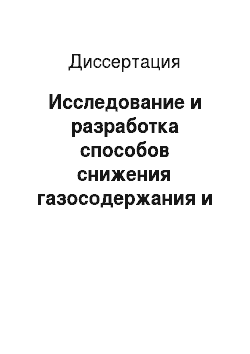
На основе разработанной методики, позволяющей определить газотворность и кинетику газовыделения при термической деструкции различных веществ, установлено, что газотворность наиболее широко используемых при литье под давлением смазывающих материалов о на основе нефти составляет 790−970 см' /г. Наименьшей газотворной способностью среди них обладают гидрофобизатор ГФК-I и смазка ЛД. Установлено, что… Читать ещё >
Содержание
- 1. СУЩЕСТВУЩИЕ ПРЕДСТАВЛЕНИЯ О ВЛИЯНИИ ТЕХНОЛОГИЧЕСКИХ ПАРАМЕТРОВ ЛИТЬЯ ПОД ДАВЛЕНИЕМ НА ГАЗО СОДЕРЖАНИЕ И
- ПОРИСТОСТЬ ОТЛИВОК
- 1. 1. Влияние подпрессовки
- 1. 2. Влияние скоростей заполнения и вентиляции.. II
- 1. 3. Влияние смазок
- 1. 4. Специальные меры по снижению пористости и газосодержания отливок
- 1. 5. Постановка задачи исследований
- 2. ИССЛЕДОВАНИЕ ВЛИЯНИЯ НЕКОТОРЫХ ПАРАМЕТРОВ ТЕХНОЛОГИИ ЛИТЬЯ ПОД ДАВЛЕНИЕМ НА ГАЗОСОДЕРЖАНИЕ И ПОРИСТОСТЬ АЛЮМИНИЕВЫХ ОТЛИВОК
- 2. 1. Методика проведения экспериментов
- 2. 2. Влияние скоростей впуска и прессования, характера заполнения полости формы сплавом на газосодержание и пористость отливок
- 2. 3. Влияние подпрессовки на пористость и газосодержание отливок
- 2. 4. Исследование влияния сопутствующего вакуумирова-ния на газосодержание отливок
- 3. ВЕНТИЛЯЦИЯ ПРЕСС-ФОРМ ПРИ ЛИТЬЕ ПОД ДАВЛЕНИЕМ
- 3. 1. Движение газов в вентиляционных каналах пресс-форм литья под давлением
- 3. 2. Определение скоростей движения газов в вентиляционных каналах пресс-форм литья под давлением
- 3. 3. Влияние параметров процесса литья под давлением на скорость движения газов в вентиляционных каналах пресс-форм
- 3. 4. Экспериментальное исследование скорости движения воздуха в тонких каналах прямоугольной формы
- 3. 5. Расчет площади вентиляционных каналов
- 4. ИССЛЕДОВАНИЕ И РАЗРАБОТКА СМАЗОК ДЛЯ ПРЕСС-ФОРМ ЛИТЬЯ ПОД ДАВЛЕНИЕМ
- 4. 1. Исследование газотворности смазок и их компонентов
- 4. 2. Разработка составов смазок для пресс-форм и прессующего поршня. о. ПРАКТИЧЕСКАЯ РЕАЛИЗАЦИЯ РЕЗУЛЬТАТОВ ИССЛЕДОВАНИЙ
- 6. ВЫВОДИ
- 7. Л И Т Е Р, А Т У Р А
Исследование и разработка способов снижения газосодержания и пористости отливок из алюминиевых сплавов при литье под давлением (реферат, курсовая, диплом, контрольная)
В В Е Д Е Н И Е В «Основных направлениях экономического и социального развития СССР на I98I-I985 годы и на период до 1990 года» указано на необходимость экономии материальных ресурсов за счет совершенствования и широкого внедрения прогрессивных малоотходных и безотходных технологий и повьш1ения качества полуфабрикатов. Большие возможности по выполнению поставленных задач заложены в литейной технологии, с помощью которой народное хозяйство СССР получает около 40 заготовок. Заготовки, полученные с помощью литейной технологии, требуют значительно меньшей механической обработки, чем заготовки других видов. Средний коэффициент использования металла при получении деталей из отливок составляет 0,6, сваркой из проката 0,55, из поковок и слитков 0,3 [il При производстве отливок специальными методами литья и, в частности, литьем под давлением отходы металла в стружку могут быть полностью исключены. Кроме того, при литье под давлением обеспечивается высокая размерная точность и качество поверхности получаемых деталей. К преимуществам литья под давлением следует отнести также высокую производительность процесса, возможность механизации и автоматизации большинства технологических операций. Таким образом, литье под давлением в полной мере соответствует одному из главных направлений развития нашей экономики. Производство отливок литьем под давлением развивается весьма высокими темпами. Так, в период с 1970 по 1980 г. г. объем выпускаемых в СССР отливок возрос более, чем в 2 раза [2] С целью улучшения качества отливок на базе полной или частичной автоматизации технологического цикла разрабатываются и внедряются автоматические линии и промышленные роботы. Теоретические основы процесса литья под давлением в СССР заложены работами В. М. Пляцкого, А. И. Вейника, А. А. Рыжикова и А. К. Белопухова. Большой вклад в развитие и совершенствование теории и практики процесса литья под давлением внесли П. П. Москвин, М. Ф. Макельский, Ю. А. Степанов, М. Л. Заславский, З. Злотин, В. Д. Швецов, Ю. Ф. Игнатенко, Л. Е. Кисиленко, В. Н. Зеленов. Наряду с отмеченными выше прершуществами процессу литья под давлением присущи и специфичные недостатки повьш1енные газосодержание и пористость изготавливаемых отливок. В значительной мере они обусловлены захватом запрессовываемым металлом воздуха и газообразных продуктов термодеструкции смазок как в полости формы, так и в свободном объеме камеры прессования, а также недостаточной вентиляцией пресс-форм. Поэтому в настоящей работе решались следующие задачи: определение фактора, оказывающего наиболее сильное влияние на газосодержание и пористость отливок, и разработка на основе полученных результатов простого и эффективного способа снижения газосодержания отливокуточнение методики расчета площади поперечного сечения вентиляционных каналов на основе аналитического и экспериментального исследования характера движения газов в тонких каналах прямоугольной формыразработка состава низкогазотворной водорастворимой смазки с целью снижения ее отрицательного воздействия на газосодержание и пористость отливок, создания условий для автоматизации процесса и улучшения санитарно-гигиенических условий труда.I. СУЩЕСТВУЮЩИЕ ПРЕДСГАВЖШЯ О ВЛИЯНИИ ТЕХНОЛОГИЧЕСКИХ ПАРАМЕТРОВ ЛИТЬЯ ПОД ДАВЛЕНИЕМ НА ГАЗОСОДЕРЖАНИЕ И ПОРИСТОСТЬ ОТЛИВОК С освоением процесса литья под давлением четко определились его негативные стороны. Среди них повышенные газосодержание и пористость изготавливаемых отливок, существенно снижающие достоинства этого высокопроизводительного способа литья, В ряду факторов, оказывающих влияние на газосодержание При рассмотрении причин повышенной пористости толстостенных отливок было установлено, что при толщине питателя, равной толщине стенки отливки, основным препятствием подпрессовке является корка затвердевшего металла, образующаяся на внутренней поверхности камеры прессования [19] В результате питание отливки прекращается, несмотря на то, что в центре прессоостатка и литника еще сохраняется жидкая фаза. При этом камера прессования выполняет роль обечайки для слоя затвердевшего металла, значительно повышая его прочность при сжимающих усилиях [20] При уменьшении диаметра камеры прессования, с целью повышения удельного давления на металл, увеличивается потеря прессового усилия, которое расходуется на преодоление возрастающего сопротивления затвердевшего слоя [20| Отмечается, что высокое давление в конечный момент заполнения формы способствует растворению газов в жидком металле. При незначительном снижении давления на металл в результате тормозящего действия затвердевающей корочки в камере прессования создаются условия для выделения газа. Для удержания газа в растворе и ликвидации газоусадочной пористости предлагается использовать двойной поршень [19,21J Указанная конструкция исключает влияние затвердевающей корочки металла, обеспечивая давление подпрессовки свыше 245 МПа, Плотность отливок при этом увеличивается на 3%. Кроме того при подпрессовке внутренним поршнем на участках отливки вблизи питателя наблюдается существенное измельчение структуры. Впервые сдвоенный поршень применен при реализации акурадпроцесса [22] Подпрессовка внутренним поршнем позволяет снизить удельное давление на металл и скорость прессования, что уменьшает разбрызгивание металла и захват воздуха. Если при этом обеспечить направленное затвердевание отливки от периферийных.
ВЫВОДЫ.
1. Основное влияние на газосодержание отливок из числа исследованных факторов оказывает скорость прессования. При ее увеличении уменьшается время заполнения, изменяется режим движения металла как в полости формы, так и в камере прессования, что способствует росту газосодержания отливок.
2. На величину пористости в отливках существенное влияние оказывает усилие подпрессовки. При литье без включения мультипликатора давления с повышением скорости прессования пористость отливок, как и газосодержание возрастают. Включение мультипликатора давления способствует снижению пористости при скорости прессования свыше 0,6 м/с и толщине питателя равного или более половины толщины стенки отливки, но не менее 2 мм. При меньших значениях указанных параметров включение мультипликатора приводит к увеличению пористости отливок.
3. Установлено, что сопутствующее вакуумирование способствует снижению газосодержания отливок (на 25−30%) при условии плотного смыкания полуформ и сокращения до минимума продолжительности второй фазы прессования. Эффективность действия разработанной вакуумной системы сохраняется при скоростях прессования не превышающих 1,2 м/с.
4. Получены аналитические зависимости критической скорости и средней скорости ламинарного движения газа в вентиляционных каналах от параметров процесса литья под давлением алюминиевых сплавов, позволяющие существенно повысить точность расчетов скоростей движения воздуха в вентиляционных каналах пресс-форм.
5. Выполненные по уточненной методике расчеты, а также полученные экспериментальные данные показали, что величины скоростей движения воздуха в вентиляционных каналах в 2−3 раза ниже, чем значения скоростей, определенные по ранее применявшейся методике .
6. Установлено, что при постоянной площади сечения пропускная способность вентиляционных каналов возрастает с увеличением их глубины и уменьшением длины. При этом снижаются давление газа в полости формы и газосодержание отливок.
7. На основе разработанной методики, позволяющей определить газотворность и кинетику газовыделения при термической деструкции различных веществ, установлено, что газотворность наиболее широко используемых при литье под давлением смазывающих материалов о на основе нефти составляет 790−970 см' /г. Наименьшей газотворной способностью среди них обладают гидрофобизатор ГФК-I и смазка ЛД.
8. Показано, что исследованные смазывающие материалы по увеличению их термической устойчивости можно расположить в следующий ряд: смазка ЛД, воск, вазелин технический, масло Вапор, гидрофобизатор ГШК-1, синтетический каучук CKTB-I.
9. Разработаны смазки для прессующей пары (а.с. 961 842) и для пресс-форм (а.с. 963 688) на основе гидрофобизатора ГФК-1, позволяющие существенно повысить качество отливок из алюминиевых сплавов и улучшить санитарно-гигиенические условия труда.
Результаты исследований внедрены в производство с суммарным экономическим эффектом 95,72 тысячи рублей.
Список литературы
- Резервы экономии металла в литейном производстве. — Литейное производство, 1982, № 10, с.1−3.
- Комиссаров В.А., Серебряков В. В. Направления развития малоотходных технологических процессов производства отливок. Литейное производство, 1983, № 5, с.2−3.
- Бруно Закс. К вопросу о пористости деталей, отлитых под давлением. Литейное дело, 1936, № 7, с.5−10.
- Лоранд Ф.Б. 0 пористости деталей, отлитых под давлением. -Литейное дело, 1936, № 8−9, с.14−16.
- Поляков П.Н. Причины пористости латунных отливок при литье под давлением. Литейное дело, 1937, № 5−6, с.26−28.
- Григоренко Г. А. 0 пористости латунных деталей, отливаемых под давлением. Литейное дело, 1937, № 5−6, с.21−26.
- Лямин П.Е. Проблема пористости алюминиевых сплавов при литье под давлением. Литейное дело, 1936, № 4, с.22−25.
- Передельский К.В. Плотность деталей из электрона, отлитых под давлением. Авиапромышленность, 1935, с.49−55.
- Передельский К.В. Пористость деталей, отливаемых под давлением. Литейное дело, 1936, № 7, с.10−13.
- Ю.Эренбург Э. Е. Неизбежно ли наличие пористости в деталях, отливаемых под давлением? Литейное дело, 1936, № 8−9, с.18−21.
- П.Пляцкий В. М. Литье под давлением. М.: Оборонгиз, 1957. -216 с.
- Белопухов A. Kv Технологические режимы литья под давлением. -М.: Машиностроение, 1967, 240 с.
- Hashiura Masashi, Ichikawa Rici. Shrinkage of aluminium allous on unidirectional solidification.: Гифу когё KOTO СЭЫМОН гакко киё. Met. Gifu Techn.Coll., 1970, № 5, p. 1 — 16.
- Stummer F.G. Welche Probleme kann das Vakuum Verfahren bei Aluminium DruckguB losen. Gisserei, 1977, № 9, S. 236 — 239.
- Ефимычев Ю.И., Прохоров И. И., Святкин Б. К. Корреляционный анализ факторов плотности отливок под давлением. Литейное производство, 1971, № 3, с.24−25.
- Кайнов В.М. Некоторые возможности литья конструкционнопроч-ных деталей. В сб.: Современные цветные сплавы и прогрессивные способы литья. М., 1974, с.163−172.
- Кайнов В.М., Трудаев В. В. Литье под давлением крупногабаритных деталей из алюминиевых сплавов. Литейное производство, 1983, № 2, с.10−12.
- Мухаметжанов Н.Ф. Технологические особенности литья под давлением термоупрочненных отливок. Литейное производство, 1979, № 2, с.21−22.
- Казаринов М.Б. Разработка и исследование способов повышения эффективности питания отливок в период затвердевания при литье под давлением.: Автореф. дисс.. канд.техн.наук. -Горький, 1971. 20 с.
- Рыжиков А.А., Злотин С. З., Казаринов И. Б. Сопротивление затвердевшего слоя металла усилию прессования при литье под давлением. Изв. вузов. Машиностроение, 1971, № I, с.153−156.
- Рыжиков А.А., Злотин С. З., Казаринов И. Б. Улучшение структуры толстостенных отливок под давлением. Литейное производство, 1973, № 5, с.2−4.
- Acurad die casting. Steel, 1966, 159, № 7, S. 34 -35.
- Diamond G.X. Breakthrough for quality die casters ACURAD. -Mod, Cast., 1966, 50, U°4, p. 52 53.
- Kohle Egbert W. Das Acurad-Verfahren fur hochdichten Druck-guss. Techn.Rdsch., 1970, 62, № 38, S. 29,31.
- Вейник А.И. Теория особых видов литья. М.: Машгиз, 1958, -300 с.
- Woltering J.A. The Acurad-Verfahren fur hochdichten Druck-guss. Techn.Rdsch., 1968, 96, № 6, S. 178 180.
- Литье под давлением. Проблемы подпрессовки. / Под ред.А.К.Бе-лопухова. М.: Машиностроение, 1971, — 168 с.
- Белопухов А.К., Родионов Е. М. Взаимосвязь тепловых условий формирования отливки и подпрессовки при литье под давлением.-Литейное производство, 1969, № 10, с.23−26.
- А.с. 908 509 (ССОР). Механизм прессования машины литья под давлением. / В. А. Антонов, В. И. Юрченко, В. Н. Примаков и др. -Опубл. в Б.И., 1982, № 8.
- Юрченко В.И., Виштак Б. С. Снижение пористости отливок при литье под давлением. Литейное производство, 1984, № 6, с.36−37.
- Белопухов А.К., Кириченко B.C. Освоение толстостенных и не-равностенных отливок. Материалы семинара.: Совершенствование технологии и организации производства литья под давлением. М., 1980, с.51−55.
- Chijiiwa К., Shirahige К. behavior of MQlten Metal with
- Respect to the Pressure in Cavity of Mold in Aluminium Die casting. J.Fac.Eng.Univ.Tokyo, 1981, В 36, № 1, p. 27 — 36.
- Белопухов A.K., Кириченко B.C. Подпрессовка как фактор повышения плотности отливок при литье под давлением. Литейное производство, 1978, № 7, с.29−30.
- Пляцкий В.М. Литейные процессы с применением высоких давлений. М.-Л.: Машгиз, 1954. — 224 с.
- Гаспарян Л.А., Белопухов А. К. Влияние вакуумирования при литье под давлением на плотность отливок из цинковых сплавов.-В сб.: Газы в литом металле. М.: Наука, 1964, с.172−176.
- Белопухов А.К. Заполнение форм и расчет литниковых систем при литье под давлением. Литейное производство, 1958, № 7,с. 3−6.
- Некоторые пути снижения пористости отливок под давлением. / А. К. Белопухов, М. Л. Заславский, Р. А. Коротков, В. А. Трудаев, -Вестн. Харьков, политехи, ин-та, 1973, № 80, с.99−102.
- Белопухов А.К. Критические скорости дисперсного заполнения формы при литье под давлением. Литейное производство, 1974, № 5, с. 24.
- Белопухов А.К. Образование воздушной пористости при литьепод давлением. В сб.: Газы в литом металле. М.: Наука, 1964, с.235−240.
- Москвин П.П. Дефекты отливок при литье под давлением и меры борьбы с ними. В сб.: Дефекты отливок и меры их предупреждения. М., 1962, с.39−42.
- Ruegg Werner, ifber den EinfluB von Gasgehalt auf die Festig-keitseigenschaften von Aluminium-DruckguB. Gisserei, 1961,48, № 19, S. 556 562.
- Макельский М.Ф. Литниковые системы при литье под давлением.-Литейное производство, 1967, № 9, с.11−14.
- Пляцкий В.М. Основы конструирования литниковых систем в литье под давлением. Литейное производство, 1961, № I, с.6−12.
- Wallace J.P. DruckguB-Auschnittechnik. Gisserei-Prax., 1966, № 17, S. 313−322.
- Белопухов А.К., Коротков Р. А. Факторы содержания газов в отливках литья под давлением. Литейное производство, 1969,3, сЛ9−21.
- Пушмашев П.И. Влияние скорости впуска на свойства сплава АЛ2 при литье под давлением. Литейное производство, 1975, с. 4142.
- Luis L., Draper А.В. Effect of overflow wells gating and injection parameters on the porosity of a die casting. -Mod.Cast., 1966, 49, № 6, S. 163 174.
- Рыжиков А.А., Злотин С. З. Исследование плотности и газонасыщенности литья под давлением. Литейное производство, 1964, № 7, с.31−33.
- Литье под давлением термоупрочняемых алюминиевых сплавов / С. К. Кантеник, Б. К. Святкин, И. И. Прохоров, Л. И. Романов. Литейное производство, 1974, № 4, с.33−34.
- Мандрик А.А. Влияние стабильности технологических параметров литья под давлением на качество отливок компрессора. Литейное производство, 1980, № 4, с.22−24.
- Исследование свойств металла отливок при литье под давлением с целью изыскания оптимального варианта их определения /
- Н.А.Полушкин, А. Ф. Кириллов, В. Д. Швецов, И. И. Прохоров. Труды Горьк. ин-та инж. водного тр-та, 1980, вып.180, с.48−64.
- Швецов В.Д. Исследование влияния газодинамических режимов литья под давлением на плотность и герметичность отливок из алюминиевых сплавов.: Автореф. дис.. канд. техн. наук. -Горький, 1970. 26 с.
- Игнатенко Ю.Ф., Болховитин В. Н., Жутаев А. И. Уменьшение захвата газов в камере прессования при литье под давлением.- Литейное производство, 1975, № 8, с.25−26.
- Швецов В.Д., Красилов Ю. И., Косинов А. И. Перетекание газов из камеры прессования в полость формы. Литейное производство, 1974, № 4, с.31−33.
- Garber Lester W. Theoretical analysis and experimental observation cold chamer filling of air entrapment during. Die Cast.Eng., 1982, 26, № 3, p. 14 — 15, 18,20, 22.
- Кириллов А.Ф., Швецов В. Д., Джиготта Ю. И. Пути повышения физико-механических свойств металла отливок, получаемых методом литья под давлением. Тр. Горьков, ин-та инж. водн. тр-та, 1978, № 162, ч.1, с.29−36.
- Пат. 578 904 (Швейцария). Способ литья под давлением и устройство для его осуществления / П. Кох, Э.Бэуэр. Приводится по: РЖ «Технология машиностроения», 1977, № 3, ЗГ293П.
- Кох P. «Parashot», der turbulenzarme Vorlauf beim Druck-gieBverfahren. Gisser. — Parx., 1976, № 5, S, 64 — 69.
- Кох П. Система «Парашот» в машинах литья под давлением фирмы «Бюлер». Литейное производство, 1978, № 12, с.15−17.
- Литье под давлением / Под ред. А. К. Белопухова. М.: Машиностроение, 1975, — 400 с.
- Kopf Jiri, Niesyt Pavel, Prurezy odvzdusnovacich. kanalu forem pro liti kovu pod tlakem, Slevarenstvi, 1966, 14, № 1, p. 32.
- Рыжиков А.А., Злотин С. З. Истечение газов из полости формы через вентиляционные каналы при литье под давлением. Литейное производство, 1965, с.35−37.
- Столбов Н.К. Повышение проницаемости пресс-формы как средство борьбы с пористостью в литье под давлением: Автореф. дис.. канд. техн. наук. Горький, 1968. — 23 с.
- Столбов Н.К. Применение металлокерамических фильтров из гранулированной бронзы для вентиляции форм литья под давлением.-Литейное производство, 1971, № 2, с.34−35.
- Игнатик И.К. Применение игольчатых вставок в пресс-формах литья под давлением, В сб.: Охлаждение отливки. Минск: Наука и техника, 1969, с.166−171.
- Вейник А.И., Игнатик И. К. Улучшение качества поверхности и снижение пористости отливок при литье под давлением. В сб.: Повышение качества и надежности литых деталей. Свердловск, 1971, с.108−112.
- Москвин П. П. Пористость в отливках, полученных литьем под давлением, и способы устранения этого дефекта. В сб.: Опыт изготовления деталей методом литья под давлением. М., 1965, с.20−26.
- Брайтингер Р. Удаление воздуха из пресс-форм при литье под давлением. Приводится по ЭИ «Технология и оборудование литейного производства», 1982, № 37, с.16−23.
- Radtke S. F# Zinkdruckguss mit neuem Gesicht. Metall, 1974, 28, № 9, S, 915 т 918.
- Dochter Heinz. Untersuchung des Zusammenhanges zwischen technologischen Parametern beim DruckgieBen und der Gusteil-qualitat• Gissereitechnik, 1978, № 1, S. 1821 *
- Barton H.K. Metal flow in thin-walled die castings. -Machinery, 1962, 101, № 2592, p. 201 211.
- Назаретян Г. JI. Новая высокотемпературная специальная смазка для литейных форм. Промышленность Армении, 1969, № 7, с. 3222.
- Пат. 48 452 (ПНР). Смазка для форм литья под давлением /В.Кай-ох. Приводится по: РЖ «Технология машиностроения», 1966,7, 7Г266П.
- Пат. 98 298 (СРР). Способ получения разделительного и смазывающего состава для форм литья под давлением алюминия и его сплавов / И. Калал, Ю.Круспин. Приводится по: РЖ «Технология машиностроения», 1962, № 21, 21Г120П.
- Пат. 54I4I (ПНР). Покрытие для форм при литье под давлением латуни / В. Кайох Приводится по: РЖ «Технология машиностроения», 1969, № I, 1Г281П.
- Кисиленко Л.Е. Влияние смазок пресс-форм литья под давлением на качество поверхности отливок. В сб.: Формирование качества поверхности отливок. М.: Наука, 1969, с.54−57.
- А.с. 465 259 (СССР). Смазка для пресс-форм литья под давлением / Ю. Д. Кузьмин, В. А. Егоров, В. В. Емельянов. Опубл. в Б.И., 1975, № 12.
- А.с. 508 326 (СССР). Олазка для постоянных металлических форм / Кузьмин Ю. Д., Е. Е. Цивадиц, В. И. Валковская, А. К. Проскуряков. Опубл. в Б.И., 1976, № 12.
- А.с. 555 967 (СССР). Смазка для пресс-форм / В. Т. Голев, В. Н. Крылов. Опубл. в Б.И., 1977, № 16.
- А.с. 859 009 (СССР). Сказка для пресс-форм литья под давлением / М. М. Рахманкулов, Р. Н. Гимаев. Опубл. в Б.И., 1981, № 32.
- Лебедев Е.А., Гудина В. Н. Олазка для пресс/форм. Литейное производство, 1961, № II. — с.41−42.
- А.с. 150 989 (СССР). Смазка для пресс-форм и деталей камеры прессования / А. А. Портной. Опубл. в Б.И., 1962, № 20.
- А.с. 153 546 (СССР). Сказка для пресс-форм литья под давлением / А. А. Портной. Опубл. в Б.И., 1963, № 6.
- Пат. 3II65 (ГДР). Сказка для литья под давлением / Г. Фритши, Р. Аух, К. Кналпе К. Приводится по: РЖ «Технология машиностроения», 1965, № 6, 6Г283П.
- Пат. 35 077 (ГДР). Смазка для форм литья под давлением /В.Пре-стинг, К. Стайбах, К.Шефер. Приводится по: РЖ «Технология машиностроения», 1965, № 12, 12Г298П.
- А.с. 243 124 (СССР). Смазка для литья металлов под давлением / В. В. Лобанов, А. И. Вычужанин, В. П. Вахаренко и др. Опубл. в Б.И., 1969, № 16.
- А.с. 859 009 (СССР). Смазка для пресс-форм литья под давлением / М. М. Рахманкулов, Р. Н. Гимаев. Опубл. в Б.И., 1981, № 32.
- А.с. 730 448 (СССР), Смазка для пресс-форм / М. М. Рахманкулов, Р. Н. Гимаев, А. Н. Мочалов, Л. И. Жутаев. Опубл. в Б.И., 1980, № 16.
- А.с. 850 256 (СССР). Смазка для пресс-форм и прессующего узла машин литья под давлением / А. А. Портной, Опубл. в Б.И., 1981, № 28.
- Особенности газового режима формы при литье под давлением крупногабаритных деталей / А. А. Рыжиков, И. И. Прохоров, С. З. Злотин, Г. И. Корякин. Литейное производство, 1969, № 3, с.27−29.
- Прохоров И.И.разработка технологии литья под давлением /-образного восьмицилиндрового блока. В кн.: Специальные способы литья. Л.: Машиностроение, 1971, с.195−202.
- Зеленов В.Н. Влияние смазок на газовый режим форм при литье под давлением. Литейное производство, 1980, № 4, с.20−22.
- А.с. 244 573 (СССР). Смазка для пресс-форм и деталей камеры прессования / В. С. Лебедев. Опубл. в Б.И., 1969, № 18.
- А.с. 487 932 (СССР). Смазка для литья металлов под давлением / А. П. Таразов. Опубл. в Б.И., 1975, № 38.
- А.с. 973 212 (СССР). Олазка для пресс-форм литья под давлением / А. Е. Гаевский, Е. В. Бугай, В. А. Щур и А. Ф. Бурлацкий. -Опубл. в Б.И., 1982, № 42.
- Храмов С.С., Филиппов Э. Е., Корякин Г. И. Влияние разделительных смазок на качество отливок при литье под давлением. -Литейное производство, 1976, № II, с.28−29.
- А.с. 466 064 (СССР). Олазка для литья металлов под давлением / К. И. Дворкин, С. Я. Комеко, Е. А. Либозаева и др. Опубл. в Б.И., 1975, № 13.
- А.с. 921 662 (СССР). Олазка для пресс-форм / Н. П. Жаботинский, Ю. Н. Цопик, В. И. Клочко, Э. Ф. Мордвинов. Опубл. в Б.И., 1982, № 15.
- Umhofer Е., VVunsch F. Trenn-und-Schmierstoffe fur Druck-gieBereien nach dem heitigen S-^and. Gisserei, 1975, 62, № 10, S. 267 — 273.
- Flick W. Moderne F0rmtrennmittel, Schmierstoffe und Schmiergerate fur DruckguB. Gisser. Prax., 1966, № 7, s. 131 — 134.
- Смазочно-охлаждающие жидкости и технологические смазки пресс-форд / Н. И. Трофимов, В. Е. Бахтин, В. А. Водопьянова, Ю.С.Копы-лов. Материалы семинара: Совершенствование технологии и организации производства литья под давлением. М., 1980, с.65−72.
- А.с. 557 861 (СССР). Смазка для форм литья под давлением / А. А. Рыжиков, С. З. Злотин, Э. Е. Филиппов, С. С. Храмов и др. -Опубл. в Б.И., 1977, № 18.
- Новые водорастворимые разделительные смазки для форм литья под давлением / А. А. Рыжиков, С. С. Храмов, Э. Е. Филиппов и др.-Литейное производство, 1976, № 6, с.22−23.
- Храмов С.С., Филиппов Э. Е., Корякин Г. И. Влияние разделительных смазок на качество отливок при литье под давлением.-Литейное производство, 1976, № II, с.28−29.
- Зеленов В.Н., Кисиленко Л. Е. Сказка пресс-форм. Материалы семинара: Совершенствование технологии и организации производства литья под давлением. М., 1980, с.72−78.
- Олазки для форм литья под давлением на КамАЗе / В. Н. Зеленов, Л. Е. Кисиленко, В. Е. Бахтин, Б. Л. Кузнецов. Литейное производство, 1979, № 6, с.18−19.
- Зеленов В.Н., Кисиленко Л. С. Олазка пресс-форм литья под давлением. М.: Машиностроение, 1983. — 144 с.
- Храмов С.С. Разработка, исследование и внедрение водных разделительных смазок в литье под давлением алюминиевых сплавов: Автореф. дис.. канд. техн. наук. Горький, 1979.19 с.
- Зеленов В.Н., Печенкин В. Л. Охлаждающая способность смазок для форм литья под давлением. Литейное производство, 1980, № 5, с. 19−20.
- Болховитин В.Н., Сырин В. А. Температурные условия нанесения водно-эмульсионных смазок на формы литья под давлением. -Литейное производство, 1983, № 2, с. 30.
- Решение задачи нестационарной теплопроводности для процесса литья в металлические формы / Э. А. Гурвич, Р. И. Есьман, В.А.Ан-тонов, Е. С. Матюш. В сб.: Металлургия. Минск: 1984, вып.18, с.35−38.
- Рожнов С.П., Кисиленко Л. Е., Недошивин М. В. Литье под давлением частично затвердевшего сплава АЛ-9. Литейное производство, 1978, № 8, с.24−25.
- А.с. 224 008 (СССР). Способ получения отливок / А. А. Рыжиков, С. З. Злотин. Опубл. в Б.И., 1968, № 38.
- Филиппов Э.Е., Швецов В. Д., Злотин С. З. Окислительные процессы при литье под давлением. Литейное производство, 1974, № 10, с.23−25.
- Рыжиков А.А., Злотин С. З. Новые технологические процессы литья под давлением. В сб.: Прогрессивная технология литейного производства. Горький, 1969, с.395−398.
- Green Robert Е# P0rosity in die castings. Die Cast.Eng. 1971, 15, № 16, S, 4, 23 — 28.
- Гаспарян Л.А., Белопухов А. К. Влияние вакуумирования при литье под давлением на плотность отливоксиз цинковых сплавов. В сб.: Газы в литом металле. М., 1964, с.172−176.
- Специальные виды литья / Ю. А. Степанов, М. Г. Анучина, Г. Ф. Баландин, Л. С. Константинов. М.: Машиностроение, 1970, -224с.
- Калиш P.M. Применение вакуума в литье под давлением. Материалы Всесоюзного семинара. Опыт изготовления деталей методом литья под давлением. М.- НИИМАШ, 1965, с.27−31.
- Калиш P.M. Влияние вакуумирования полости формы на свойства отливок при литье под давлением. Литейное производство, 1973, № 8, с.14−16.
- Айнбиндер А.Б., Еременко А. Т., Мельников B.C. Автоматическая установка для вакуумирования полости формы при литье под давлением. Литейное производство, 1963, № 8, с.7−8.
- Изготовление волноводов радиоэлектронной СВЧ аппаратуры методом литья под давлением. В сб.: Развитие и совершенствование литья под давлением, М.- МДНТП, 1975, с.25−29.
- Мухаметжанов Н.Ф. Литье ответственных деталей с применениемэффективного метода повышения плотности отливок. В сб.: Развитие и совершенствование литья под давлением. М., МДНТП, 1975, с.54−59.
- Заславский М.Л., Ферштатер И. Б., Мышалов С. В. Исследование литья под давлением термоупрочняемого алюминиевого магниевого сплава АЛ27. Изв. вузов. Машиностроение, 1971, № 9, с.173−178.
- Прибор для определения газосодержания в отливках / А. А. Рыжиков, С. З. Злотин, Б. П. Хренов и др. Технология машиностроения, М., 1966, вып.2, с.6−8.
- Швецов В.Д. Факторы эффективности вентиляционных устройств при литье под давлением. Литейное производство, 1975, № 5, с.26−28.
- Коротков В.Г. Рафинирование литейных алюминиевых сплавов. -М., Свердловск: Машгиз, 1963. 127 с.
- Курдюмов А.В., Пикунов М. В., Чурсин В. М. Литейное производство цветных и редких металлов. М.: Металлургия, 1982. -352 с.
- Альтман М.Б. Неметаллические включения в алюминиевых сплавах. М.: Металлургия, 1965. — 127 с.
- Зеленов В.Н., Кисиленко Л. Е., Петрова Н. К. Некоторые факторы, влияющие на формирование служебных свойств отливок при литье под давлением. Труды МВТУ им. Н. Э. Баумана, 1975, вып.187, с.26−55.
- Проблемы фиксации азота / Редакторы Р. Харди, Ф. Боттомли, Р.Бёрнс. Пер. с англ. М.: Мир, 1982. — 735 с.
- Альтшуль А.Д., Киселев П. Г. Гидравлика и аэродинамика. Изд. 2-е, перераб. М.: Стройиздат, 1975. 323 с.
- Идельчик И.Е. Справочник по гидравлическим сопротивлениям.-М.: Госэнергоиздат, I960. 369 с.
- Шлихтинг Г. Теория пограничного слоя. Пер. с нем. М.: Наука, 1974. — 711 с.
- Kajoch Wladislaw. Metoda badania kinetici wydzielania ga-zow z powlok do form cisnieniowych" Przeglad adlewnict-wa, 1965, № 15.
- Айнбиндер А.Б., Дровосеков Б. Г. Влияние газотворной способности смазок на характер заполнения и качества отливок при литье под давлением. Сб. научн. тр. Пермск. политехи. ин-та, 1969, № 55, с.19−22.
- Швецов В.Д., Красилов Ю. И., Храмов С. С. Выделение газов из смазок в скоротечных технологических процессах. Изв. вузов. Машиностроение, 1975, № 9, с.182−186.
- Бахмат В.А., Михальцов A.M., Полищук Т. А. Определение газотворной способности смазок при литье под давлением. Металлургия, Минск: Вышэйшая школа, 1978, вып.12, с.34−36.
- А.С. 638 416 (СССР). Смазка для литейных форм / Д.Н.Худокор-мов, В. А. Бахмат, A.M.Михальцов. Опубл. в Б.И., 1978, № 47.
- А.с. 710 745 (СССР). Смазка для пресс-форм литья под давлением / В. А. Бахмат, A.M.Михальцов, Д. К. Макрецкий. Опубл. в1. Б.И., 1980, № 3.
- Бернштейн Г. Д. Топливо и смазочные материалы. М.: Сельхоз-гиз, 1956. — 295 с.
- Ахматов А.С. Молекулярная физика граничного трения. М.: Физмашгиз, 1963. — 472 с.
- Груднев А.П., Тилик В. Т. Технологические смазки в прокатном производстве. М.: Металлургия, 1975. — 368 с.
- Матвеевский P.M., Буяновский И. А., Лазовская О. В. Противо-задирная стойкость смазочных сред при трении в режиме граничной смазки. М.: Наука, 1978. — 192 с.
- Смазочные свойства отдельных групп углеводородов и их композиций / Р. А. Агаева, Р. Ш. Кулиев, И. С. Кеворкова, А.М.Аниси-мова. Азербайджанское нефтяное хозяйство, 1967, № I, с.38−40.
- А.с. 961 842 (СССР). Олазка для пресс-форм и прессующего поршня машин литья под давлением / В. А. Бахмат, Ю. В. Маркаров,
- A.М.Михальцов, В. Г. Сташкевич. Опубл. в Б.И., 1982, № 36.
- А.с. 963 688 (СССР). Смазка для форм литья под давлением / Д. Н. Худокормов, В. А. Бахмат, А. М. Михальцов, Ю. В. Маркаров,
- B.Г.Сташкевич. Опубл. в Б.И., 1982, № 37.
- Вейцер С.И., Лубэ В. М. Приготовление эмульсии олифы с помощью ультразвука. В кн.: Акустические установки для приготовления эмульсий олифы. М., 1961, с.4−15.
- Залесский В.А. Ультразвуковой эмульсатор. Там же. с.16−21.