Способы повышения прочности и износостойкости коленчатых валов
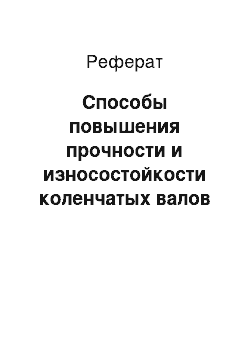
Поверхностная закалка токами высокой частоты (ТВ Ч). Поверхностной закалке ТВЧ подвергаются стали с достаточно высоким содержанием углерода, например 40, 45, 40ХН, 40ХНМЛ и др. Наиболее часто этот способ применяется для шатунных и коренных шеек КВ. После быстрого разогрева поверхности ТВЧ шейки КВ подвергаются быстрому охлаждению. Такая термическая обработка создает в обрабатываемом поверхностном… Читать ещё >
Способы повышения прочности и износостойкости коленчатых валов (реферат, курсовая, диплом, контрольная)
Для повышения прочности и износостойкости КВ применяются соответственно конструктивные и технологические способы.
Существенное повышение прочности коленчатых валов достигается за счет снижения эффективных коэффициентов концентрации напряжений ?о/ео и кх/ ет. Для повышения прочности при сохранении неизменной длины КВ применяются следующие конструктивные способы:
1) увеличение перекрытия шеек КВ. Наиболее широко этот способ применяется для КВ обычной конструкции, которые устанавливаются на автомобильные дизельные двигатели.
Наличие перекрытия шеек вала повышает запас прочности щеки п} в зоне точки С (см. рис. 2.1). Это обусловлено тем, что при наличии перекрытия изгиб щеки происходит по наклонному (увеличенному) сечению Х-Х(рис. 2.4).
Значение перекрытия шеек КВ рассчитывается по выражению.

В соответствии с выражением (2.29) перекрытие шеек, показанное на рис. 2.4, а, имеет отрицательное значение (шейки не перекрываются), а перекрытие, соответствующее рис. 2.4, б, — положительное.

Рис. 2.4. Положение сечения Х-Х щеки КВ обычной конструкции: а — при отсутствии перекрытия шеек; б — при наличии перекрытия шеек В дизельных двигателях с диаметром цилиндра D- 130… 180 мм положительный эффект наличия перекрытия шеек начинает сказываться при значении перекрытия Д = 20…30 мм.
У коленчатых валов бензиновых двигателей в связи с более низкими значениями действующих в КШМ сил перекрытие шеек может отсутствовать;
2) увеличение радиуса галтели перехода от шейки к щеке. Увеличение радиуса сопряжения шеек КВ со щеками понижает значение эффективного коэффициента концентрации напряжений &G/ec— При неизменной длине КВ и сохранении прежней толщины щек Лщ это неизбежно ведет к уменьшению рабочей дли;

Рис. 2.5. Галтель перехода от шейки к щеке: г,…г3 — радиусы дуг перехода; Х-Х — сечение изгиба щеки ны подшипников скольжения и соответствующему возрастанию удельных нагрузок в зоне сопряжения подшипников с шейками.
Для понижения значения ка/еа при сохранении рабочей длины подшипников скольжения галтель перехода от шейки к щеке выполняют дугами нескольких радиусов (обычно не более трех дуг). Пример галтели перехода, выполненной дугами трех радиусов, показан на рис. 2.5.
Такое конструктивное решение позволяет увеличить сечение изгиба щеки Х-Х. При определении значения ко/ ео по табл. 2.5 в этом случае следует использовать отношение г, /Ащ, т. е. наибольшее из возможных отношений г/Лщ;
3) придание внутренним полостям шеек КВ бочкообразной формы. Если в шейках КВ возможно выполнить полости, то этим полостям целесообразно придать бочкообразную форму. Переход от цилиндрической части полости к конической должен лежать в плоскости, перпендикулярной оси КВ и проходящей через радиус галтели сопряжения шейки со щекой (рис. 2.6).
Такая форма полостей повышает запас прочности КВ за счет снижения эффективных коэффициентов концентрации касательных напряжений;
4) эксцентричное расположение внутренней полости в шатунной шейке. При удалении оси внутренней полости в шатунной шейке от оси вращения КВ запас прочности шейки на изгиб в плоскости колена повышается на 10… 15%. Расположение полости диаметром 8Ш в шатунной шейке с эксцентриситетом е показано на рис. 2.7. К такому решению, как правило, прибегают при наличии значительного перекрытия шеек вала Д.

Рис. 2.6. Коленчатый вал с полостями бочкообразной формы.
Очевидно, что это конструктивное решение позволяет реализовать одновременно два способа повышения прочности: увеличение перекрытия шеек и эксцентричное расположение полости в шатунной шейке.
Кроме того, при наличии эксцентриситета уменьшается приведенная вращающаяся масса колена /лк и, следовательно, уменьшается центробежная сила инерции, нагружающая коренные подшипники КВ;
5) расположение под прямым углом к плоскости колена оси отверстия для подвода масла из полости шатунной шейки. Такое конструктивное решение принимается по двум причинам.
Во-первых, отверстие выполняется в зоне минимального давления на шатунную шейку, что следует из векторной диаграммы давлений (см. рис. 1.17).
Во-вторых, опытным путем установлено, что при воздействии на шатунную шейку скручивающего момента в теле шейки возникают касательные напряжения, экстремальные значения которых расположены в плоскости колена. Таким образом, сверление отверстия в зоне минимальных касательных напряжений позволяет повысить прочность шатунной шейки на кручение (рис. 2.8).
Края масляного отверстия у поверхности шатунной шейки являются концентраторами напряжений. Эти края желательно выполнять с максимально возможным радиусом и последующей полировкой.

Рис. 2.7. Эксцентричное расположение полости в шатунной шейке.

Рис. 2.8. Расположение эпюры касательных напряжений и оси масляного отверстия.
Для повышения износостойкости КВ применяются следующие технологические способы:
1) поверхностная закалка токами высокой частоты (ТВ Ч). Поверхностной закалке ТВЧ подвергаются стали с достаточно высоким содержанием углерода, например 40, 45, 40ХН, 40ХНМЛ и др. Наиболее часто этот способ применяется для шатунных и коренных шеек КВ. После быстрого разогрева поверхности ТВЧ шейки КВ подвергаются быстрому охлаждению. Такая термическая обработка создает в обрабатываемом поверхностном слое остаточные напряжения сжатия, благодаря чему предел усталости шеек КВ повышается. В зависимости от времени разогрева, а также с учетом возможного перешлифования глубина закаленного слоя у шеек может достигать 2,5 мм (у галтелей — 1,5 мм) при поверхностной твердости HRC 50…65. При этом сердцевина детали остается пластичной.
При отсутствии концентрации напряжений усталостная прочность шеек КВ повышается не более чем на 15%, а при наличии концентрации напряжений повышается в два и более раза;
2) наклеп поверхностного слоя. Наклепу подвергают поверхности в местах концентрации напряжений. В зоне наклепа в поверхностном слое детали возникают остаточные напряжения сжатия, способствующие повышению предела усталости.
Наклеп в зависимости от формы обрабатываемой поверхности может выполняться обкаткой роликами, обдувом стальной дробью (галтели перехода от шеек к щекам), обжатием шариком (края масляных отверстий). Применение наклепа для КВ высокооборотных двигателей повышает предел усталости валов при изгибе на 35…45%, а при кручении — до 20%. С этой же целью наклепу и полировке могут подвергаться внутренние и наружные поверхности отверстий;
3) насыщение поверхностного слоя азотом. Насыщение тонкого поверхностного слоя деталей азотом (азотирование) применяют для повышения твердости и износостойкости этого слоя. В результате азотирования в поверхностном слое создаются напряжения сжатия, повышающие предел усталости. Кроме того, при азотировании повышается коррозионная стойкость поверхностного слоя.
Для валов из легированной стали азотирование позволяет повысить т_| на 30. .40%, а — на 30…60%.
Азотирование может осуществляться в газовой или в жидкостной среде.
Газовое азотирование, длительность которого может составлять 24…60 ч, применяется обычно для легированных сталей 18Х2Н4МА, 35ХМЮА, 35ХЮА и др. Хром, молибден и алюминий, являющиеся легирующими элементами этих сталей, дают устойчивые дисперсные нитриды. Хорошо азотируются в газовой среде также нержавеющие и жаропрочные стали.
Глубина азотированного слоя зависит от температуры и длительности процесса. Например, для азотирования поверхности на глубину до 0,25 мм при температуре около 510 °C требуется примерно 24 ч.
Азотирование производится после окончательной механической обработки закаленных и отпущенных деталей. Механическая обработка после азотирования неизбежно понижает усталостную прочность КВ.
По сравнению с закалкой ТВЧ азотирование КВ позволяет повысить их усталостную прочность в 1,5…2,0 раза, а износостойкость шеек примерно на 20%. Одновременно улучшаются антифрикционные свойства и коррозионная стойкость материала, уменьшается склонность КВ к короблению в процессе эксплуатации.
Сравнительно небольшая глубина азотированного слоя исключает возможность азотирования шеек КВ, если они должны работать в паре с подшипниками качения. Высокие локальные нагрузки со стороны роликов подшипника «продавливают» твердый, но хрупкий тонкий слой азотированной поверхности, в результате чего двигатель выходит из строя. Для защиты поверхностей от азотирования на них предварительно наносятся защитные покрытия, например тонкий слой меди. В резьбовые отверстия устанавливаются технологические заглушки.
Жидкостное азотирование позволяет существенно сократить длительность процесса: аналогичный результат достигается примерно за 3 ч.
Будучи одним из наиболее эффективных способов повышения усталостной прочности, азотирование является достаточно дорогостоящим процессом, значительно повышающим стоимость КВ (иногда на 30. .50%);
4) насыщение поверхностного слоя углеродом. Насыщение поверхностного слоя углеродом (цементация) применяется для КВ из низкоуглеродистой стали (с содержанием углерода 0,10…0,25%).
В результате цементации и последующей закалки с отпуском на поверхности деталей возникают остаточные напряжения сжатия, способствующие повышению усталостной прочности. Поверхностная твердость цементированного слоя составляет HRC 55…60, а его глубина в зависимости от длительности процесса может составлять 0,5. .2,0 мм.
Если требуемая глубина упрочняемого слоя не должна превышать 0,1 …0,2 мм, цементацию заменяют цианированием.
Цианирование является комбинацией азотирования и цементации. Это процесс насыщения поверхностного слоя деталей одновременно углеродом и азотом в ванне с расплавленными солями цианистой кислоты при температуре примерно 570 °C.
Цианирование позволяет шире использовать для КВ нелегированные и малолегированные низкоуглеродистые и среднеуглеродистые стали.
При цианировании на поверхности детали образуются два слоя. При длительном цианировании глубина верхнего слоя может достигать 1,2… 1,6 мм при твердости HRB 800. Этот слой содержит 6,5…8,0%Л^2 и 0,8… 1,0% С, что обеспечивает материалу высокую износостойкость. Нижний слой глубиной 0,3…0,5 мм является диффузионным, способствующим повышению усталостной прочности.