Редуктор с конической передачей с карданным валом
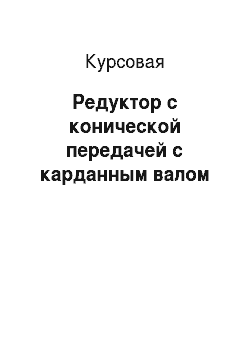
Гидропривод преобразует энергию давления жидкости в механическую энергию вращения вала гидродвигателя. Частота вращения вала передается через карданный шарнир редуктору, выходные валы которого соединены с помощью аналогичных карданных шарниров с винтовыми преобразователями. Последние преобразуют вращательное движение вала редуктора в поступательное перемещение гайки, которое через шток передается… Читать ещё >
Редуктор с конической передачей с карданным валом (реферат, курсовая, диплом, контрольная)
Механизм для перестановки крыльев необходим для изменения угла стреловидности на современных многорежимных самолетах, способных летать на различных скоростях. Для каждой скорости полета существует оптимальная конфигурация крыла, которая зависит от его стреловидности. Для уменьшения сопротивления на сверхзвуковых скоростях стреловидность крыла должна быть максимальна, а на дозвуковых для улучшения посадочных характеристик желательна меньшая стреловидность.
Система состоит из следующих агрегатов: гидропривода; редуктора привода крыла; карданных шарниров, с помощью которых соединены между собой гидропривод, редуктор и винтовые преобразователи; двух винтовых преобразователей.
Гидропривод преобразует энергию давления жидкости в механическую энергию вращения вала гидродвигателя. Частота вращения вала передается через карданный шарнир редуктору, выходные валы которого соединены с помощью аналогичных карданных шарниров с винтовыми преобразователями. Последние преобразуют вращательное движение вала редуктора в поступательное перемещение гайки, которое через шток передается на рычаг поворота крыла.
Редуктор привода крыла предназначен для передачи крутящего момента от гидропривода к винтовым преобразователем и представляет собой зубчатую передачу с коническими колесами. Корпус является основной несущей деталью редуктора. Входной вал приводится во вращение от выходного вала гидропривода. Это движение передается через промежуточный вал на два выходных вала, приводящих в движение винтовые преобразователи.
К преимуществам такой схемы можно отнести:
· Передача движения в перпендикулярном или противоположном направлении;
· Компактность (меньшие габариты), уменьшение массы;
· Надежность работы, постоянство передаточного отношения;
· Высокий КПД.
Недостатками такого редуктора являются необходимость обеспечения высокой точности зубчатой передачи; шумность работы; сложность при производстве и установке конических колес.
Схема механизма приведена на рисунке 1.
1-гидродривод;
2-карданные шарниры;
3-винтовой преобразователь;
4-корпус редуктора;
5-выходные валы редуктора;
6-промежуточный вал;
7-входной вал редуктора.
Рис.1
1. КИНЕМАТИЧЕСКИЙ РАСЧЕТ
1.1 Определение мощности двигателя
Для определения мощности двигателя, найдем потребную мощность по формуле:
Где F-заданная сила, действующая на винте, Н;
V-скорость выпуска крыла (м/с), которая находится как отношение хода винта L (м) к времени выпуска t (с):
;
Находим потребную мощность:
Pпотр=150 000 0.1 167=1751 Вт.
Коэффициент полезного действия всего механизма определяется по формуле:
где КПД муфты;
КПД конической передачи;
КПД винтовой пары;
КПД подшипников;
Учитывая что количество механизмов 2, находим мощность двигателя:
;
.
Для работы механизма необходим двигатель мощностью 4.306кВт.
1.2 Определение общего передаточного отношения редуктора
Частота вращения двигателя задана по условию и равна. Частоту на выходе находим как отношение числа оборотов винта на рабочий ход nx(об) к времени выпуска t (с):
.
Определяем передаточное отношение редуктора:
.
Зная передаточное отношения всего редуктора, можно найти передаточные отношения каждой ступени.
Определим передаточное отношение и мощность каждой из ступеней, частоты вращения на валах. Результаты вычислений занесём в таблицу 1.
Таблица 1-Частоты вращения на валах и мощности степеней.
Тихоходная ступень | Быстроходная ступень | ||
U | |||
n1, мин-1 | =130 | ||
n2, мин-1 | |||
P, кВт | |||
Найдем вращающие моменты на валах:
Вращающий момент на быстроходном валу:
Нм.
Вращающий момент на промежуточном валу:
Нм.
Вращающий момент на тихоходном валу:
Нм.
2. РАСЧЕТ ЗУБЧАТЫХ ПЕРЕДАЧ
2.1 Выбор материала зубчатых колес
Основными видами повреждения зубчатых колес являются усталостное выкрашивание рабочих поверхностей и излом зубьев, поэтому материалы для зубчатых колес следует выбирать по условиям обеспечения прочности зубьев на выносливость при действии контактных и изгибных напряжений.
Зубчатые колеса для агрегатов аэрокосмической техники изготовляют из цементируемых, высоколегированных сталей. С целью уменьшения массы и габаритных размеров выбираем материалы с высокими механическими характеристиками. Для зубчатых колёс наиболее подходящими будут стали — 20Х, 20ХН, 40Х, 40ХН, 30ХГСА. При расчетах возможно незначительное изменение твёрдости материала. Для быстроходной и тихоходной ступеней выбираем материал сталь 20Х с твёрдостью 45…50 HRC, которая достигается путем цементации.
2.2 Расчет зубчатых конических передач
Расчет приведен в таблицах 2−8.
Таблица 2-Исходные данные
Наименование параметра | Шестерня (Колесо) | Обозначение | Значения | ||
Быстр.ст. | Тих.ст. | ||||
Мощность, кВт | P | 4.26 | 2.15 | ||
Передаточное число | U | 1.38 | 1.6 | ||
Частота вращения, мин-1 | Шестерня | n | 97.5 | ||
Колесо | 97.5 | 60.9 | |||
Срок службы, ч. | Lh | ||||
Режим работы | ; | Средний равновероятный | |||
Угол наклона профиля | |||||
Степень точности | 7-В | ||||
Заготовка | Поковка | ||||
Марка стали | Шестерня | 20Х | 20Х | ||
Колесо | |||||
Термообработка | Шестерня | Поверхностное упрочнение | Цементация | ||
Колесо | |||||
Твердость поверхности, HRC | Шестерня | ||||
Колесо | |||||
Смещение | Шестерня | X1 | |||
Колесо | X2 | ||||
Количество зубьев | Шестерня | Z1 | |||
Колесо | Z2= Z1U | ||||
Таблица 3-Определение допускаемых контактных напряжений.
Наименование параметра | Обозначение | Формула | Значения | |||
Быстр.ст. | Тих.ст. | |||||
Кол-во нагружений за один оборот | Ш | с | ||||
К | ||||||
Кол-во циклов нагружений с учетом режима работы, млн. | Ш | Nk | Nk=60•c•n•Lh* | 2.34 | 3.51 | |
К | 1.755 | 1.095 | ||||
Базовое число циклов, млн. | Ш | NHB | NHB=30•(HB)2.4 | 85.903 | 85.903 | |
К | 66.71 | 66.71 | ||||
Показатель степени | Ш | m | если Nk> NHB, то m=20;если Nk< NHB, то m=6. | |||
К | ||||||
Коэффициент долговечности | Ш | ZN | ZN= (при поверхностном упрочнении) | 1.8 | 1.7 | |
К | 1.8 | 1.8 | ||||
Коэффициент запаса прочности | Ш | SH | Для зубчатых колес с поверхностным упрочнением | 1,2 | 1.2 | |
К | 1,2 | 1.2 | ||||
Предел контактной выносливости, МПа | Ш | уHlim | уHlim=17HRC+200 | |||
К | ||||||
Допускаемое контактное напряжение, МПа | Ш | [у]H | ||||
К | ||||||
Принятое | меньшее | |||||
Кh=0.25-коэффициент учитывающий равновероятный режим работы.
Таблица 4- Определение делительного диаметра и модуля.
Наименование параметра | Обозначение | Формула | Значения | |||
Быстр.ст. | Тих.ст. | |||||
Относительная ширина зубчатого венца | Kбе | Kбе<0.3 | 0.25 | 0.2 | ||
Вспомогательный коэффициент | Kd | Для прямозубых передач | ||||
Коэффициент, учитывающий неравномерность распределения нагрузки по длине контактных линий (зависит от Кбе) | KHB | По графику[2] | 1.16 | 1.14 | ||
Коэффициент, учитывающий внутреннюю динамическую нагрузку | КHV | [2] | 1.1 | 1.1 | ||
Коэффициент, учитывающий форму зуба | Н | Для прямозубых колес | ||||
Межосевой угол передачи, град. | ||||||
Крутящий момент на шестерне, Нм | T | 328.2 | ||||
Расчетный делительный диаметр на внешнем торце, мм | dе1 | 99.27 | 85.74 | |||
Модуль, мм | Расч | m | 3.309 | 3,43 | ||
Прин | 3.5 | 3.5 | ||||
Внешний делительный диаметр | Ш | dе | 87.5 | |||
К | ||||||
Число зубьев плоского колеса | ZE | ZE= | 47.17 | |||
Внешнее конусное расстояние, мм | Re | 87.5 | 82.5 | |||
Ширина венца, мм | Расч | bW | 21.88 | 16.5 | ||
Прин | ||||||
Таблица 5- Определение допускаемых изгибных напряжений
Наименование параметра | Обозначение | Формула | Значения | |||
Быстр.ст | Тих.ст | |||||
Количество циклов нагружения, млн | Ш | Nk | Nk=60•c•n•Lh К* | .2.34 | 3.51. | |
К | 1.755 | 1.095 | ||||
Базовое число циклов, млн | Ш | NFlim | [2] | |||
К | ||||||
Показатель степени | Ш | m | Для цементируемых зубчатых колес | |||
К | ||||||
Коэффициент долговечности | Ш | YN | 1.18 | 1.12 | ||
К | 1.213 | 1.278 | ||||
Коэффициент, учитывающий размеры колес | Ш | Yx | . | 1.04 | 1.04 | |
К | 1.03 | 1.03 | ||||
Коэффициент, учитывающий способ получения заготовки | Ш | Yk | Для поковок [2] | |||
К | ||||||
Предел выносливости при изгибе, МПа | Ш | уFlim0 | Для отнулевого цикла напряжений определяется в зависимости от от химико-термической обработки | |||
К | ||||||
Коэффициент запаса прочности | Sf | Определяется в зависимости от от химико-термической обработки | 1.55 | 1.55 | ||
Допускаемое напряжение при изгибе, МПа | Ш | [уF] | 676.8 | 648.4 | ||
К | ||||||
К=0.1-коэффициент, учитывающий режим работы.
Таблица 6- Расчет на максимальные перегрузки
Предел выносливости при изгибе, МПа | Ш | уFst | Для стали 20Х | |||
К | ||||||
Коэффициент, запаса прочности | Ш | SFmax | Для стали 20Х | 1,75 | 1,75 | |
К | 1,75 | 1,75 | ||||
Допускаемое контактное напряжение, МПа | Ш | [уH]max | ||||
К | ||||||
Допускаемое напряжение при изгибе, МПа | Ш | [уF]max | 1188.6 1177.1 | 1188.6 1177.1 | ||
К | ||||||
ТаблицаПроверочный расчет на контактную выносливость
Наименование параметра | Обозначение | Формула | Значения | ||
Быстр.ст. | Тих.ст. | ||||
Относительная ширина зубчатого венца | Кбе | 0.25 | 0.2 | ||
Коэффициент, учитывающий распределение нагрузки между зубьями в связи с ошибками изготовления | КН | Для прямозубых передач [2] | |||
Крутящий момент на шестерни, Нм | T1 | 210.1 | |||
Коэффициент, учитывающий неравномерность распределения нагрузки по длине контактных линий (зависит от Кбе) | КНВ | По графику[2] | 1.12 | 1.14 | |
Окружная сила на делительном цилиндре, Н | Ft | ||||
Окружная скорость, м/с | V | 0.6368 | 0.4032 | ||
Коэффициент, учитывающий влияние модификации профиля и вида зубьев | Для прямых передач без модификации[2] | 0.14 | 0.14 | ||
Коэффициент, учитывающий влияние разности шагов зацепления зубьев шестерни и колеса | g0 | Для модуля меньше 3.55[2] | 4.7 | 4.7 | |
Удельная окружная динамическая сила, Н/мм | WH | 5.363 | 3.006 | ||
Коэффициент, учитывающий внутреннюю динамическую нагрузку | КНV | 1.015 | 1.009 | ||
Коэффициент, учитывающий форму зуба | Н | [2] | |||
Действующее контактное напряжение, МПа | 1187.2 | ||||
Сравнение с допускаемым | — 8.863 | — 5.99 | |||
Таблица.8-Расчет на выносливость при изгиб
Наименование параметра | Обозначение | Формула | Значения | |||
Быстр.ст. | Тих.ст. | |||||
Эквивалентное число зубьев | Ш | Zv | ||||
К | ||||||
Коэффициент, учитывающий форму зуба | Ш | YFS | YFS=(3.47+13.2/ZV)*1.2 | 4.58 | 4.7 | |
К | 4.4 | 4.3 | ||||
Коэффициент, учитывающий неравномерность распределения нагрузки по длине контактных линий | КFB | КFB=КHB | 1.12 | 1.14 | ||
Коэффициент, учитывающий внутреннюю нагрузку | КFV | КFV=КHV | 1.015 | 1.009 | ||
Коэффициент нагрузки | KF | KF=KFв KHв | 1,137 | 1.15 | ||
Действующее изгибное напряжение, МПа | Ш | 680.7 653.3 | 655.8 610.2 | |||
К | ||||||
Сравнение с допускаемым | — 0.574 | 1.15 | ||||
Нmax, МПа | ||||||
Сравнение с допускаемым | 0,26 | 0,26 | ||||
Fmax, МПа | ||||||
Сравнение с допускаемым | 0.13 | 0.13 | ||||
2.3 Геометрический расчет конической зубчатой передачи
Основные параметры зубчатых колес мы вычислили: модуль, ширину, делительный диаметр и количество зубьевпри расчете на прочность. Размеры остальных элементов колес и формулы для их определения занесем в таблицу 9
Таблица 9-Геометрические параметры конических колес.
Наименование | Обозначение | Быстроходная ступень | Тихоходная ступень | Размерность | Формула | |
Значение | ||||||
Внешний делительный диаметр шестерни | dе1 | 87.5 | мм | |||
Внешний делительный диаметр колеса | dе2 | мм | ||||
Внешнее конусное расстояние | Re | 87.5 | 82.5 | мм | b kbe | |
Среднее конусное расстояние | R | 77.5 | 84.5 | мм | Re-0.5b | |
Межосевой угол передачи | град | Определяется схемой редуктора | ||||
Угол делительного конуса | град | |||||
Внешняя высота зуба | he | 7.7 | 7.7 | мм | me (2h*а+c*) | |
Коэффициент высоты головки зуба | ha* | мм | cos | |||
Коэффициент радиального зазора | c* | 0.2 | 0.2 | мм | ||
Внешняя высота головки зуба | hae | 3.5 | 3.5 | мм | me | |
Внешняя высота ножки зуба | hfe | 4.2 | 4.2 | мм | 1.2me | |
Диаметр вершин шестерни на внешнем торце | daе1 | 110.6 | 93.45 | мм | de1 +2hae cos | |
Диаметр вершин колеса на внешнем торце | daе2 | 144.2 | 143.7 | мм | de1 +2hae cos | |
Диаметр впадин шестерни | dfе1 | 80.08 | мм | de1 -2haecos | ||
Диаметр впадин колеса | dfе2 | 134.75 | 135.36 | мм | de1 -2hae cos | |
3. ЭСКИЗНОЕ ПРОЕКТИРОВАНИЕ
3.1 Проектировочные расчеты валов
Вал — деталь, предназначенная для передачи вращающего момента вдоль своей оси и для поддержания вращающихся деталей.
Определим диаметры валов из условия прочности на кручение:
(1)
Где T-крутящий момент на валу,
Wp-полярный момент сопротивления,
— отношение внутреннего диаметра вала к внешнему (все валы редуктора полые),
[] -допускаемое напряжение на кручение, которое принимают из диапазона МПа. Принимаем []=50 МПа.
Из формулы (1) выражаем диаметр и находим его значения на каждом валу.
;
Быстроходный вал:
Принимаем d1=35 мм.
Промежуточный вал:
Принимаем d2=38 мм.
Тихоходный вал:
Принимаем d3=35 мм.
После определения диаметров валов разрабатываем их конструкцию, т. е. формируем ступени, опорные буртики, предусматриваем соединения вала с муфтой и зубчатыми колесами. Ступенчатая форма вала позволяет свободно передвигать каждую деталь вдоль вала до ее посадочного места и просто фиксировать ее на этом посадочном месте в осевом направлении. Шестерня и входной вал выполнены заодно, образуя вал-шестерню, аналогично поступаем и с колесами тихоходной ступени и выходными валами.
Соединение зубчатых колес с промежуточным валом выполняем с помощью эвольвентных шлицов. Подбор шлицевых соединений будем производить по ГОСТу 6033−80.Исходить будем из внешнего диаметра валов и оптимального числа зубьев.
С колесом быстроходной ступени:
Шлицы ,
Число зубьев z=29;
С шестерней тихоходной ступени:
Шлицы ,
Число зубьев z=36;
3.2 Выбор типа и схемы установки подшипников
Выбирая подшипники, на первом этапе конструирования редуктора исходят из ориентировочных значений диаметров валов. Затем, параллельно с уточнением размеров валов по длине и по диаметру и уточнением нагрузки подшипника, пересматриваем первоначальный вариант и выбираем наиболее рационально подшипники, обеспечивающие необходимые требования.
Выбираем шариковые радиальные однорядные подшипники. Этот тип в основном предназначен для восприятия радиальных нагрузок, но может воспринимать и осевые нагрузки. На быстроходный, тихоходный и промежуточные валы, в первом приближении, выбираем подшипники из легкой серии.
На быстроходный вал:
206 ГОСТ 8338–75;
На тихоходный вал:
207 ГОСТ 8338–75−2 шт.;
На промежуточный:
207 ГОСТ 8338–75.
На быстроходном и тихоходных валах опоры устанавливаем по схеме враспор (рис2), используя регулировочные кольца и распорные втулки. Кольца подшипников должны закрепляться на валу и в корпусе, чтобы фиксировать вал в осевом направлении, воспринимать осевую нагрузку и предотвращать проворот колец при динамических нагрузках. На промежуточном валу ставим систему фиксирующей и плавающей опор (рис 3 а, б).
Рис.2
а) б) Рис.3
4. ВЫБОР МУФТ
Наш редуктор соединен с гидроприводом и винтовыми преобразователями с помощью шарнирных муфт. Такие муфты предназначены для передачи вращающего момента между валами, имеющими угловое смещение осей, которое может изменяться в процессе вращения муфты. При малых частотах вращения (до 200 мин-1) подбор муфт осуществляется по номинальным вращающим моментам.
Вращающие моменты и диаметры на выходных и входном валах:
T1=313 Нм, d=25 мм;
T2=328 Нм, d=30 мм.
Выбираем в обоих случаях:
Муфта шарнирная 560−1-30−1-У3 ГОСТ 5147–80,у которой номинальный вращающий момент 560 Нм, внутренний диаметр 30 мм и внешний диаметр 60 мм. Соединение вала с муфтой выполняем с помощью фланцев, которые в свою очередь соединены с валами при помощью эвольвентных шлицов. Выбираем их по наружному диаметру и оптимальному количеству зубьев:
С входным валом:
Шлицы ,
Число зубьев z=30;
С выходными валами:
Шлицы ,
Число зубьев z=36;
5. ПОДБОР ПОДШИПНИКОВ КАЧЕНИЯ НА ЗАДАННЫЙ РЕСУРС
В качестве опор валов используем стандартные подшипники качения. Нагрузочная способность подшипников заданного диаметра и серии зависит от типа подшипника. С увеличением диаметра подшипника, а также при переходе от легких серий к более тяжелым нагрузочная способность возрастает, но увеличивается стоимость.
Ранее мы уже выбрали шариковые радиальные однорядные подшипники.
Нужно определить необходимую динамическую грузоподъемность, и сравнить с допускаемой грузоподьемностью выбранных подшипников.
Динамическая грузоподъемность подшипника
где
— расчетный ресурс,
— для шариковых подшипников, — для роликовых;
— коэффициент, вводимый при необходимости повышения надежности;
— коэффициент, учитывающий качество материала подшипников, смазочный материал и условия эксплуатации (для обычных условий работы)[7],
— эквивалентная нагрузка;
— радиальная нагрузка;
Fa-осевая нагрузка;
— коэффициент вращения;
— коэффициент безопасности, учитывающий характер нагрузки;
При температурный коэффициент .
Kе=0.63-коэффициент, учитывающий равновероятный типовой (средний) режим работы.
При проектировании опор передач исходными для определения нагрузок, действующих на подшипник, являются силы в зацеплении: нормальная сила и сила трения. Силами трения пренебрегаем, так как коэффициент трения между хорошо смазанными и чисто обработанными зубьями весьма мал. За радиальную нагрузку принимаем наибольшую из рассчитанных суммарных радиальных реакций в опорах. За осевую нагрузку принимаем суммарную осевую нагрузку.
Для определения нагрузок, действующих на опоры, вал на подшипниках заменяем балкой на опорах.
Размеры а, в, с указанные на рисунке 3 взяты из чертежа.
Найденные силы и формулы для их нахождения занесем в таблицу10.
Таблица 10-Усилия, действующие на валах
Вал | Разм. | Формула | Быстр. | Промеж. | Тихоход. | |
a | мм | |||||
в | ||||||
c | ||||||
Ft1/Ft2 | Н | 6702/5317 | ||||
Fr1/Fr2 | 1468/1641 | |||||
Fa | 1948/1026 | |||||
Fm | Для шарнирной муфты: | ; | ||||
M | Нм | 68.7 | 121.7 | 103.4 | ||
Из условия равновесия балки найдем реакции в опорах:
На входном валу:
.
На промежуточном валу:
.
На тихоходном валу:
.
Теперь найдем суммарные реакции в опорах, эквивалентные нагрузки и расчетную динамическую грузоподьемность, результаты занесем в таблицу 11.
Таблица 11-Проверочный расчет подшипника
Вал | Разм. | Формула | Быстр. | Промеж. | Тихоход. | |
Ra | Н | |||||
Rв | ||||||
Fa/ Co | 0.147 | 0.22 | 0.2 | |||
Fa/ Fr | 0.15 | 0.74 | 0.26 | |||
e | 0.33 | 0.36 | 0.35 | |||
X/Y | Если Fa/Fr Если Fa/Fr>e, то 1.21/0.56 | 1/0 | 1.21/0.56 | 1/0 | ||
L | 9.36 | 7.02 | 4.38 | |||
F | Н | |||||
Cp | Н | |||||
№подшипника /Ск | Справочные данные | 206/19 500 | 207/25 500 | 207/25 500 | ||
Из таблицы видно что выбранные нами подшипники выдержат ту нагрузку, которая приложена на валы.
6. РАСЧЕТ ВАЛОВ
6.1 Расчет валов на статическую прочность
Для проверочного расчета валов составим расчетные схемы. Рассмотрим промежуточный вал (рис.4) как наиболее нагруженный Вал представим как балку на двух опорах. Построим эпюры изгибающих и крутящих моментов.
Устанавливаем опасные сечения промежуточного вала (рис. 5). Опасным является сечение 1 (под колесом быстроходной ступени). Выполним проверку вала на прочность в этом сечении.
Усилия, действующие на шестерне тихоходной ступени, не влияют на значение изгибающих моментов, что видно из рисунка.
В опасном сечении:
изгибающий момент в горизонтальной плоскости
(Нмм);
изгибающий момент в вертикальной плоскости суммарный изгибающий момент
(Нмм);
Н•мм — максимальное значение изгибающего момента, возникающее в момент пуска двигателя;
где .
Крутящий момент
(Н•мм).
Напряжение изгиба
МПа, где ,
d-диаметр вала, d=38 мм.
Напряжение кручения:
МПа.
Эквивалентное напряжение:
МПа.
Предел текучести для материала валастали 45 — МПа, Коэффициент запаса прочности:
.
Условие прочности удовлетворяется.
6.2 Расчет валов на усталостную прочность
Расчет на сопротивление усталости проводят в форме проверки коэффициента запаса прочности по усталости.
При совместном действии изгиба и кручения запас усталостной прочности определяется по формуле
где
— коэффициент запаса по нормальным напряжениям;
— коэффициент запаса по касательным напряжениям;
— предел выносливости материала при изгибе, МПа;
— предел выносливости материала при кручении, МПа;
— коэффициенты чувствительности к асимметрии цикла напряжений;
— амплитудные напряжения, МПа;
— средние значения напряжений, МПа.;
— суммарные коэффициенты, учитывающие влияние всех факторов на сопротивление усталости при изгибе и кручении;
— коэффициент абсолютных размеров поперечного сечения;
— коэффициент влияния шероховатости поверхности;
— коэффициент влияния упрочнения, вводимый для валов с поверхностным упрочнением;
— эффективные коэффициенты концентрации напряжений.
Механические характеристики стали 45: твердость НВ не менее 240;
МПа, МПа, МПа, МПа;
.
Проведем расчет на усталостную прочность валов. Коэффициенты в формулах выбираются в зависимости от концентратора напряжений. Результаты расчета сведем в таблицу12.
Таблица 12-Расчет валов на усталостную прочность
Опасное сечение № 1 | ||
Место расположения | Шлицы под колесом на промежуточном валу | |
Н•мм | ||
Т, Н•мм | ||
d, мм | ||
МПа | ||
МПа | ||
МПа | ||
МПа | ||
0.85 | ||
1,1 | ||
1,5 | ||
2,05 | ||
1,9 [7] | ||
Условие прочности удовлетворяется
7. РАСЧЕТ ШЛИЦЕВЫХ СОЕДИНЕНИЙ
самолет редуктор стреловидность кинематический
Для обеспечения необходимой работоспособности шлицевых соединений выполним проверочный расчет по условию прочности на смятие:
где — крутящий момент;
— длина соединения;
— высота зуба;
1. Рассчитаем эвольвентные шлицы на входном валу. Материал 20Х, для которого; ().
;
;
;
.
2 Рассчитаем эвольвентные шлицы на выходных валах Материал 20Х, для которого; ().
;
;
;
.
3. Рассчитаем эвольвентные шлицы на промежуточном валу и колесе быстроходной ступени ().МатериалСталь 45, для которого .
;
;
;
4. Рассчитаем эвольвентные шлицы на промежуточном валу и колесе тихоходной ступени ().МатериалСталь 45, для которого .
;
;
; ;