Современные методы восстановления деталей
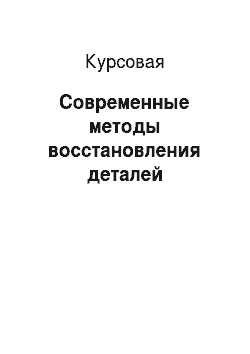
Методы подготовки поверхностей к выполнению восстановительной операции Обязательным условием при выполнении любой операции по восстановлению изношенных поверхностей детали является чистота поверхности. Загрязнение муфты представляют собой масляные отложения, а также на поверхности коррозия. Для удаления коррозии применяем установку ОМ — 9788, с применением чистящего раствора. Для удаления масла… Читать ещё >
Современные методы восстановления деталей (реферат, курсовая, диплом, контрольная)
Федеральное агентство по образованию Государственное образовательное учреждение высшего профессионального образования
«Тихоокеанский государственный университет»
Институт транспорта и энергетики кафедра «Техническая эксплуатация и ремонт автомобилей»
Пояснительная записка к курсовой работе по дисциплине
«Современные методы восстановление деталей»
Выполнил: Нестеренко А.А.
Проверил: Казанников О.В.
Хабаровск 2007
СОДЕРЖАНИЕ ВВЕДЕНИЕ РЕФЕРАТ
1. Разработка и расчет технологического процесса ремонта детали
1.2 Исходные данные
1.3 Выбор рационального способа восстановления
1.4 Дефекты детали и выбор способа ремонта
1.5 Методы подготовки поверхностей к выполнению восстановительной операции
1.6 Выбор установочных баз
1.7 Технологический маршрут ремонта детали
1.8 Схема технологического процесса
1.9 Расчёт и выбор режимов обработки, нормирование технологического процесса
2. Разработка технологического процесса сборки узла СПИСОК ИСПОЛЬЗОВАННЫХ ИСТОЧНИКОВ
ВВЕДЕНИЕ
В процессе эксплуатации автомобилей надежность, заложенная в них при производстве, снижается вследствие изнашивания деталей, коррозии, усталости и старения материала и других вредных процессов, протекающих в технике. Вредные процессы вызывают появление различных неисправностей и дефектов, устранение которых становится необходимым для поддержания автомобиля в работоспособном состоянии. Отсюда возникает потребность в техническом обслуживании и ремонте.
В процессе проведения технического обслуживания и ремонта выполняются работы по устранению возникших неисправностей и замене быстроизнашивающихся деталей. Но при длительной эксплуатации наступает момент, когда надежность оборудования снижается настолько, что восстановление его средствами эксплуатационных предприятий становится невозможным. В этом случае применяют капитальный ремонт, т.к. замена деталей новыми часто менее выгодна по сравнению с восстановлением старых.
В соответствии с ГОСТ 3.1109−82 устанавливаются три вида технологических процессов:
— единичный;
— типовой;
— групповой.
При ремонте автомобилей на ремонтных предприятиях используются все три вида технологических процессов. Разработка того или иного вида зависит от типа предприятия. Для единичного и мелкосерийного производства разрабатываются единичные технологические процессы. Для серийного и крупносерийного производства (специализированные предприятия) групповые технологические процессы. Разработанная типовая технология является основой для разработки единичных и групповых процессов.
Использование типовых процессов облегчает решать такие задачи как выбор способа восстановления, установочных (технологических баз, разработки технологических маршрутов и операций) и т. д. Типизация позволяет сократить сроки разработки и освоения технологических процессов при обеспечении стабильного качества.
РЕФЕРАТ Данный курсовой проект включает в себя 1 лист формата А2, 2 листа чертежей формата А3, 31 лист пояснительной записки на листах формата А4, включающей, 3 таблицы, 8 литературных источников, также технологические процессы на 7 листах формата А4.
АВТОМОБИЛЬ, ВАЛ, ТЕХНОЛОГИЧЕСКИЙ ПРОЦЕСС, РЕМОНТ, СВАРКА, ШЛИФОВАНИЕ, ОСТАЛИВАНИЕ, НАПЛАВКА, ВОСТАНОВЛЕНИЕ, ДЕТАЛЬ.
В пояснительной записке рассмотрены технологические процессы восстановления муфты скользящей вилки. Также рассмотрены этапы ремонта, технологии выбора оборудования и расчета основных параметров технологических процессов восстановления деталей.
1. Разработка и расчет технологического процесса ремонта детали
1.2 Исходные данные Восстанавливаемая деталь представляет собой муфту скользящей вилки с цилиндрическим и шлицевым отверстиями, изготовленная из стали 40Х. Муфта скользящей вилки предназначена для передачи крутящего момента между валами в коробке передач. Конструктивнотехнологической особенностью детали является наличие сквозных цилиндрического и шлицевого отверстий. Основными дефектами являются износ цилиндрического отверстия, погнутость и износ шлицев.
Условия, в которых находится муфта довольно сложные:
— работа в нагруженных условиях
— воздействие масляно-грязевых отложений,
— динамические нагрузки из-за изменений направления вращения
— работа при повышенном температурном режиме
Количество производимых в год деталей равно 1000 шт., поэтому выбираем по таблице 3 мелкосерийный тип производства
Конструкция детали соответствует технологическим требованиям ремонта, содержит необходимые для ремонта и восстановления технологические базы. Имеющиеся дефекты не нарушают технологических баз и позволяют применить передовые способы ремонта, относительные затраты на которые будут ниже по сравнению с изготовлением детали .
1.2 Выбор типового технологического процесса и его краткое описание Для выбора типового технологического процесса необходимо определить классификационную принадлежность восстанавливаемой детали.
По конструкции деталь относится к классу полые стержни.
Типовой технологический процесс характеризуется единством содержания и последовательности большинства технологических операций и переходов для групп изделий с общими конструктивными признаками.
Основное техническое требование, которое необходимо выполнить при восстановлении деталей полые стержни — это обеспечение размеров восстанавливаемых поверхностей, их твердости и прочности, а так же соосности, перпендикулярности и симметричности отверстий, допустимой овальности и конусообразности. Технологический процесс восстановления деталей данного класса начинают с очистки от коррозии, затем следует проверка состояния фасок центровых отверстий, и, при необходимости, их исправление. Затем производят правку детали и механическую обработку изношенных поверхностей под типовые способы восстановления. Выполняют сварочные и наплавочные операции с последующей нормализацией поверхностей при необходимости улучшения их обрабатываемости. Наплавочные поверхности подвергают чистовой и черновой механической обработке, а затем нарезают резьбы, фрезеруют шлицы, шпоночные канавки. Для восстановления физико-механических свойств рабочих поверхностей деталей выполняют термическую обработку. Завершающей операцией является шлифование с последующим суперфинишированием или полированием точных поверхностей, которое выполняется последним с целью предотвращения случайного повреждения окончательно обработанной поверхности.
1.3 Выбор рационального способа восстановления Из существующих способов восстановления изношенных отверстий и шлицов наибольшее распространение получили следующие способы:
Электродуговая наплавка (под флюсом, в углекислом газе, вибродуговая и др.)
Заварка (ручная сварка, газосварка) Электродуговая наплавка обеспечивает восстановление детали с получением слоя достаточной толщины. Механические свойства наплавленного металла соответсвуют требуемым. Автоматической и полуавтоматической наплавкой удобно восстанавливать детали цилиндрической формы, в частности валы, и резьбовые поверхности.
Для защиты наплавляемого слоя от воздействия кислорода и азота воздуха применяют углекислый газ. Этим предотвращается окисление металла и обеспечивается удаление окислов. Для раскисления металла применяется специальная сварочная проволока. Наплавка производится по винтовой линии. Для предотвращения стекания металла необходимы небольшая сила тока и низкое напряжение. Чтобы предотвратить появление трещин при наплавке применяется местный подогрев детали.
Наплавка в среде углекислого газа. Достоинствами этого метода являются: восстановление муфта скользящий вилка
— меньший нагрев деталей;
— возможность наплавки в любом положении детали;
— более высокая производительность;
— возможность наплавки деталей небольшого диаметра (от 10 мм);
— не требуется удалять шлаковую корку;
— стоимость ниже примерно на 20%.
— Недостатки:
— повышенное разбрызгивание металла;
— нужна легированная проволока;
— необходима защита сварщика от излучения дуги.
Автоматическая вибродуговая наплавка. Осуществляется вибрирующим электродом при помощи наплавочной головки в струе жидкости, углекислого газа или воздуха для восстановления стальных деталей.
Достоинства:
— восстановление деталей малого диаметра;
— высокая производительность для тонких слоев;
— не нужна термическая обработка;
— финишная обработка шлифованием без точения;
— небольшой нагрев деталей.
Недостатки:
снижение усталостной прочности;
— необходимы проволоки с большим содержанием углерода (наплавка на воздухе и в жидкости).
Сварка и наплавка под слоем флюса.
Сущность процесса сварки и на плавки. Сварка (наплавка) под слоем флюса представляет собой разновидность электродуговой сварки, при которой дуга горит под слоем сварочного флюса, обеспечивающего, защиту сварочной ванны от воздуха. Наряду с защитными функциями флюс стабилизирует горение дуги, обеспечивает раскисление, легирование и рафинирование расплавленного сплава сварочной ванны.
К достоинствам сварки (наплавки) под слоем флюса относится: высокая производительность процесса, благодаря применению больших токов, большой глубины проплавления, а также почти полного отсутствия потерь металла на угар и разбрызгивание; возможность автоматизации процесса; высокое качество наплавленного металла в результате надеж ной защиты флюсом сварочной ванны; улучшение условий труда сварщика.
К недостаткам этого процесса сварки следует отнести: значительный нагрев детали; невозможность выплавки деталей диаметром менее 40 мм по причине стекания расплавленных наплавляемого металла и флюса с поверхности восстанавливаемой детали; необходимость в отдельных случаях повторной термической обработки детали. При сварке под слоем флюса производительность процесса по машинному времени повышается в 6 — 12 раз по сравнению с ручной дуговой сваркой. Это достигается за счет использования больших плотностей тока в электродной проволоке.
Для восстановления погнутости муфты используется правка.
Из числа возможных способов выбираем способ, который обеспечивает последующий межремонтный ресурс восстановленной детали, т. е. удовлетворяет требуемому коэффициенту долговечности 1.0.Данные способы указаны в таблице 3.
Коэффициенты долговечности
Ручная дуговая сварка | 0,85−0,95 | |
Наплавка под слоем флюса | 0,8−1,00 | |
заварка | 1.0 | |
Из данных способов выбираем способ восстановления, характеризующийся наиболее высоким значением коэффициента технико-экономической эффективности. В данном случае таким является заварка
1.4 Дефекты детали и выбор способа ремонта Карта технических требований на деффектацию детали
Наименование детали (сборочной единицы). Муфта скользящей вилки | ||||||
См. эскиз | Обозначение 6ЗД-2 218 062 | |||||
Материал Сталь 40 Х ГОСТ 4543–48 | ||||||
Твердость HRC 40−48 | ||||||
Позиция на эскизе | Возможный дефект | Способ установления дефекта и средства контроля | Размер, мм | Способ ремонта | ||
По рабочему чертежу | Допустимый без ремонта | |||||
Износ штифтового отверстия | Визуально. микрометр | ?6.1мм | ; | Заварка. | ||
Износ шлицевого соединения | Визуально. микрометр | 6.035мм | ; | Наплавка. | ||
Погнутость | Визуально. Шаблон. | ; | ; | Правка. | ||
Данная деталь подлежит ремонту т. к. :
— имеет незначительные дефекты
— имеет малую протяжённость обрабатываемых поверхностей
— затраты на ремонт детали значительно ниже производства новой детали
— конструкция детали не препятствует подводу режущего и измерительного инструмента
— при восстановлении детали используются распространённые, несложные и высокопроизводительные способы
1.5 Методы подготовки поверхностей к выполнению восстановительной операции Обязательным условием при выполнении любой операции по восстановлению изношенных поверхностей детали является чистота поверхности. Загрязнение муфты представляют собой масляные отложения, а также на поверхности коррозия. Для удаления коррозии применяем установку ОМ — 9788, с применением чистящего раствора. Для удаления масла смолистых отложений применяем очистку погружением в ванне с применением моющих средств МЛ — 52, МС — 8. Подготовка деталей к нанесению покрытия включает следующие операции: механическую обработку поверхностей; обезжиривание в органических растворителях; монтаж детали на подвесные приспособления; обезжиривание деталей с последующей промывкой в воде.
Механическая обработка включает шлифование поверхностей деталей для придания им правильной геометрической формы и полирование для получения необходимой шероховатости поверхностей с использованием шлифовальных и полировальных кругов. Обезжиривание деталей предназначено для удаления с поверхностей деталей жировых загрязнений.
Деталь обезжиривают в органических растворителях: тетрахлорэтилене, трихлорэтилене, уайт-спирте и др.
Монтаж деталей осуществляют на специальные подвесные приспособления, которые должны обеспечить надежный контакт с восстанавливаемой деталью и токопроводящей штангой, не допустить экранирование отдельных участков детали.
Изоляция мест, не подлежащих фосфатированию снижает расход материала, электрического тока и повышает производительность ванны. Для защиты поверхностей детали применяют наносимый в несколько слоев цапон-лак в смеси с нитроэмалью в соотношении 1:2. Для изоляции применяют также перхлорвиниловую изоляционную ленту, листовую резину, пластикаты, которыми плотно обматывают защищаемые поверхности. Наиболее целесообразным является применение различных футляров, втулок, экранов из эбонита, текстолита, винилпласта и т. п.
Окончательное электрохимическое обезжиривание в щелочных растворах является наиболее эффективным способом очистки поверхностей деталей. При обезжиривании стальных деталей в электролите, содержащем 35…40 г/л каустической соды NaOH, 25…30 г/л кальцинированной соды Na2CO3, 2…3 г/л жидкого стекла (Na2О· 2SiO2) и 15…20 г/л тринатрийфосфата (Na3PO4· 12H20); при температуре электролита 65…70 С, плотности тока 12…16 А/дм2 продолжительность процесса 5…8 мин. Детали помещают (подвешивают) на катодную штангу. В качестве анодов применяют пластины из стали или никеля. При электролизе на поверхности детали в виде пузырьков выделяется водород, который механически разрушает жировую пленку, ускоряя процесс омыления и эмульгирования жиров. Выделяющийся водород проникает и вовнутрь поверхностного слоя металла, вызывая его хрупкость. Поэтому в конце процесса обезжиривания переходят на анодную обработку деталей в течении 1…2 мин.
Деталь также можно обезжиривать венской известью, состоящей из смеси окиси кальция, окиси магния с добавкой 3% кальцинированной соды или 1,5% каустической соды. Порошок венской извести разводят водой до пастообразного состояния и растирают вручную по поверхности детали волосяными щетками.
После обезжиривания деталь промывают в холодной, затем в горячей воде с целью удаления с поверхности детали остатков щелочных растворов, которые могут загрязнить гальванические ванны. Сплошная без разрывов пленка воды на обезжиренных поверхностях свидетельствует о хорошем качестве очистки. Декапирование (анодную обработку) проводят с целью снятия окисных пленок с обрабатываемых поверхностей деталей, которые образуются во время обезжиривания и промывки, а так же для обнажения структуры металла детали, что способствует прочному сцеплению покрытия с металлом детали. Помещенные в ванну осталивания детали выдерживают без тока в течении 1…2 мин для их прогрева до температуры электролита, а затем подвергают декапированию в течении 30…45 с при анодной плотности тока 25…35 Адм2.
Отделочных операций поверхности не требуют
1.6 Выбор установочных баз При базировании детали должно выполняться основное техническое требование — геометрические оси всех обрабатываемых цилиндрических поверхностей должны лежать на одной прямой.
Установочными базами для процесса восстановления целесообразно принять базы, которые использовались при изготовлении детали.
1.7 Технологический маршрут ремонта детали Дефект № 3
Операция 05: Правка Оборудование:
Пресс гидравлический, А установить снять
Переход 1: Правка по шаблону Дефект № 1
Операция 010: Заварка Оборудование:
Переоборудованный токарно-винторезный станок 16К20
Сварочный выпрямитель ВС-300
Наплавочная головка А-825М переход 1: заварить отверстия наглухо Операция 015: Кругло — шлифовальная Оборудование:
— кругло — шлифовальный станок 3М163 В, А установить и снять переход 1: шлифовать поверхность (внешнюю) в размер? 30.1 мм переход 2: шлифовать поверхность (внутреннюю) в размер? 20.1 мм Операция 020: Разметка Разметочный стол Операция 025: Вертикально-сверлильная
Оборудование:
— вертикально-сверлильный станок 2Н118
А установить и снять переход 1: высверлить отверстие поз.1 до? 6 мм
сделать фаскисверло? 6,1 мм
Операция 030: Зенкерование Вертикально-сверлильный станок 16 К20
Зенкер? 6 мм Сталь 40Х
Операция 035: Развертывание Развертка 2363−3592 Н7 ГОСТ 19 268–73
Дефект № 2
Операция 040: Точение Оборудование:
Сверлильно-фрезерный — расточной 2202ВМФ4
А установить и снять переход 1: точить поз.2 до? 18 мм Операция 045: Заварка Оборудование:
Переоборудованный токарно-винторезный станок 16К20
Сварочный выпрямитель ВС-300
Наплавочная головка А-825М переход 1: наплавить до? 13,9 мм Операция 050: Кругло — шлифовальная Оборудование:
— кругло — шлифовальный станок 3М163 В, А установить и снять переход 1: шлифовать поверхность поз.2 в размер? 14 мм Операция 055: Разметка Разметочный стол Операция 060: Прошивка Черновая Чистовая Прошивка по ГОСТ 24 818–81
переход 1: прошить шлицы на поверхности 2
переход 2: сделать заходную фаску (1×45)
Операция 065: Слесарная обработка Щетка металлическая
1.8 Схема технологического процесса
1) Правка (поз.№ 3)
2) Токарная (поз.№ 2)
3) Сварочно-наплавочная (поз.№ 1,2)
4) Токарная (поз.№ 1,2)
5) Разметочная (поз.№ 1,2)
6) Вертикально-сверлильная (поз.№ 1)
7) Прошивка (поз.№ 2)
8) Слесарная (поз.№ 1,2)
1.9 Расчёт и выбор режимов обработки, нормирование технологического процесса Операция 005: Вертикально-сверлильная
переход 1: высверлить отверстие до? 6 мм глубина резания t = 0,5D=0,5.3=1,5 мм подача S = 0,66 мм/об скорость резания
где
— коэффициент, учитывающий конкретные условия обработки, материал и форму резца.
Т = 60 минпериод стойкости резца
— сила резания, где
поправочный коэффициент крутящий момент
где — диаметр детали частота вращения
— мощность, затрачиваемая на резание
величина врезания и выхода сверла, мм
Dдиаметр сверла
2 Разработка технологического процесса сборки узла Анализ конструкции.
Гидравлический лопастной насос гидроусилителя рулевого управления Устройство и действие лопастного насоса гидроусилителя.
Наибольшее применение в гидравлических усилителях получил насос лопастного типа двойного действия. Его конструкция для автомобилей различных марок, снабженных гидроусилителями, в основном унифицирована и отличается лишь некоторыми незначительными изменениями. Ниже рассматривается устройство и действие лопастного насоса производства ЗИЛ.
В корпусе 24 (рис. 329) насоса, отлитом из чугуна, установлен на шариковом 28 и игольчатом 25 подшипниках вал 26, * на наружном конце которого закреплен на шпонке гайкой приводной шкив 29. Вал уплотнен в корпусе сальником 27. На шлицах внутреннего конца вала закреплен ротор 21, изготовленный из стали. В радиальные пазы ротора свободно вставлены стальные лопасти 22 (10 шт.). Ротор с лопастями расположен внутри статора 23, который вместе с распределительным диском 18 и чугунной крышкой 16 крепится к корпусу болтами. Положение статора с распределительным диском относительно корпуса фиксируется двумя установочными шпильками.
Статор уплотнен между корпусом и крышкой резиновыми кольцевыми прокладками.
Сверху на корпусе и крышке установлен на прокладке и закреплен болтами стальной штампованный бачок / вместе с направляющим коллектором 30. В бачке сверху установлен заливной сетчатый фильтр 4 и бачок закрыт крышкой 2. Между крышкой и корпусом установлена прокладка. Крышка надевается на шпильку, ввернутую в коллектор, и с помощью барашка притягивается к корпусу. Полость бачка сообщается с атмосферой через сапун 3, расположенный на крышке. Через канал коллектора 30 полость бачка сообщается с полостью корпуса 24 и каналом крышки 16, в которой установлены перепускной 10 и предохранительный 12 клапаны с пружинами. Сбоку в бачок вварен штуцер 7 сливного маслопровода, на внутреннем конце которого расположен сливной сетчатый фильтр 5. Фильтр снабжен тарельчатым предохранительным клапаном 6 с пружиной, пропускающим масло из сливного штуцера в бачок, минуя фильтр в случае его сильного загрязнения. К штуцеру присоединяется сливной маслопровод (гибкий шланг) распределителя управления гидроусилителем.
В цилиндрической выточке статора 23 имеются две выемки, заходя в каждую из которых лопасти 22 ротора 21 обеспечивают всасывание и нагнетание жидкости. Передняя часть каждой полости (по ходу вращения ротора) через отверстия 8 в статоре и выемке на распределительном диске сообщается с полостью корпуса, откуда к лопастям ротора подходит масло. Задняя часть каждой полости через сквозные продолговатые отверстия 19 в распределительном диске 18 сообщается с полостью высокого давления в крышке 16. Эта полость через конусные продолговатые отверстия 9 в распределительном диске 18 и два канала 20 сообщается с пазами ротора 21 под лопастями 22, что обеспечивает дополнительное прижатие лопастей к стенке камеры статора, которые при вращении ротора прижимаются к стенке камеры в основном действием центробежной силы.
Нагнетательная полость крышки 16 через калиброванное отверстие (жиклер) 17 соединена с каналом 14, к которому при помощи штуцера присоединяется нагнетательный маслопровод (гибкий шланг), идущий к распределителю управления гидроусилителем.
В канале крышки корпуса, установлен плунжерный перепускной клапан 10 с пружиной 13, упирающийся в нерабочем состоянии в диск 18 распределителя и закрывающий проходное отверстие вертикального канала. Внутри перепускного клапана установлен шариковый предохранительный клапан 12 с толкателем, нагруженный малой пружиной 11. Канал перепускного клапана сообщается с нагнетательным каналом через отверстие 15.
Работа насоса происходит следующим образом. При вращении вала насоса вместе с ротором 21 лопасти 22 под действием центробежной силы и давления масла в пазах постоянно прижимаются к внутренней поверхности камеры статора 23, перемещаясь радиально в своих пазах. При этом лопасти 22 захватывают масло, поступающее из полости корпуса, и подают его под большим давлением через отверстия в распределительном диске 18 в нагнетательную полость крышки 16, откуда масло через жиклер 17 и канал поступает в нагнетательный маслопровод усилителя.
Из гидроусилителя масло по сливному маслопроводу поступает через сливной фильтр 5 обратно в бачок.
Перепускной клапан 10 ограничивает предельную производительность насоса в случае повышения числа оборотов коленчатого вала двигателя и связанного с ним вала насоса. При повышений числа оборотов ротора 21 давление в полости нагнетания возрастает в большей степени, чем в канале 14, из-за калиброванного отверстия 17, соединяющего их. Под этим повышенным давлением перепускной клапан 10 открывается и перепускает масло из нагнетательной полости обратно в бачок /, что ограничивает количество масла, поступающего в магистраль к усилителю.
В случае чрезмерного повышения давления масла в нагнетательной магистрали 14 это давление через отверстие 15 передается в полость под перепускным клапаном 10. При этом предохранительный клапан 12 открывается, пропуская масло в бачок, что вызывает падение давления под перепускным клапаном 10 и его большее открытие. Вследствие усиленного перепуска масла ограничивается предельное давление в системе (65—70 кгс/см2).
СПИСОК ИСПОЛЬЗОВАННЫХ ИСТОЧНИКОВ
1. Улашкин А. П., Тузов Н. С. Учебное пособие по курсовому проектированию восстановления деталей. Хабаровск. ХПИ. 1979
2. Дажин В. Г Таблицы по расчету режимов обработки деталей. Хабаровск. ХПИ. 1979
3. Справочник технолога — машиностроителя. под ред. А. Г. Косиловой в 2 т. М.: «Машиностроение» 1986
4. Справочник технолога авторемонтного производства. под ред. Г. А. Малышева М.: Транспорт 1977.