Оптимизация скорости резания в режиме реального времени при токарной обработке
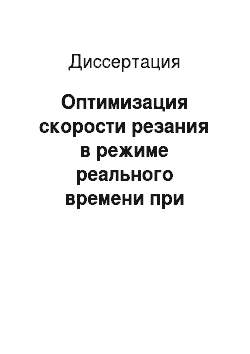
В четвертой главе проведена экспериментальная проверка оптимизации скорости резания в режиме реального времени на статистической модели с использованием предложенного интегрального критерия оценки эффективности процесса самообучения, состоящего в учете себестоимости обработки в режиме самообучения. В результате испытаний различных вариантов процедур самообучения выявлены варианты, дающие… Читать ещё >
Содержание
- 1. АНАЛИЗ МЕТОДОВ НАЗНАЧЕНИЯ РЕЖИМОВ РЕЗАНИЯ НА ОСНОВЕ ЭКОНОМИЧЕСКИХ КРИТЕРИЕВ ОПТИМАЛЬНОСТИ
- 1. 1. Показатели оптимальности режимов резания
- 1. 2. Выбор критерия оптимальности режима резания
- 1. 3. Технические и технологические ограничения режимов резания
- 1. 4. Распределение стойкости и функция надежности режущего инструмента
- 1. 5. Исследование зависимости стойкости от скорости резания
- 1. 6. Процедуры обучения и самообучения в автоматизированных системах реального времени
- 1. 7. Цель и задачи исследований
- 2. ОПТИМИЗАЦИЯ СКОРОСТИ РЕЗАНИЯ В РЕЖИМЕ РЕАЛЬНОГО ВРЕМЕНИ НА ОСНОВЕ ПРОЦЕССА САМООБУЧЕНИЯ. 2.1. Введение
- 2. 2. Процедура стохастической аппроксимации Роббинса-Монро
- 2. 2. 1. Математическая модель процедуры Роббинса-Монро
- 2. 2. 2. Применение процедуры Роббинса-Монро при назначении режимов резания
- 2. 3. Процедура Кифера-Волфовица
- 2. 3. 1. Описание процедуры
- 2. 3. 2. Критерий оптимальности для процедуры
- 2. 4. Процедуры с восстановлением параметров стойкостной зависимости
- 2. 5. Оценка параметров стойкостной зависимости методом наименьших квадратов
- 2. 5. 1. Исходные предположения
- 2. 5. 2. Общая схема метода наименьших квадратов
- 2. 5. 3. Показатель — стойкость инструмента
- 2. 5. 4. Показатель — логарифм стойкости инструмента
- 2. 5. 5. Показатель — относительное отклонение расчетной стойкости от опытной
- 2. 5. 6. Показатель — относительное отклонение расчетной интенсивности износа от опытной
- 2. 5. 7. Показатель — интенсивность износа инструмента
- 2. 5. 8. Показатель — себестоимость операции
- 2. 6. Оценка параметров стойкостной зависимости методом наибольшего правдоподобия
- 2. 6. 1. Исходные предположения
- 2. 6. 2. Функция правдоподобия
- 2. 7. Сравнение методов оценки параметров стойкостной зависимости
- 2. 8. Учет дрейфа условий обработки. 2.9. Выводы
- 2. 2. Процедура стохастической аппроксимации Роббинса-Монро
- 3. СТАТИСТИЧЕСКОЕ МОДЕЛИРОВАНИЕ, АНАЛИЗ И ВЫБОР МЕТОДА ОЦЕНКИ ПАРАМЕТРОВ СТОЙКОСТНОЙ ЗАВИСИМОСТИ
- 3. 1. Ведение
- 3. 2. Моделирование разброса стойкости
- 3. 3. Сравнение по точности методов оценки параметров стойкостной зависимости
- 3. 3. 1. Генерация выборки
- 3. 3. 3. Результаты сравнения
- 3. 3. 4. Учет смещения
- 3. 4. Выводы
- 4. 2. Блок-схема статистической модели самообучения
- 4. 3. Имитация процесса резания
- 4. 4. Оценка параметров стойкостной зависимости
- 4. 5. Управление скоростью резания
- 4. 6. Испытание процедуры самообучения при тейлоровской стойкостной зависимости
- 4. 6. 1. Влияние коэффициента вариации на сходимость
- 4. 6. 2. Влияние вида поисковой последовательности на сходимость. 4.6.3. Сравнение вариантов процедуры самообучения по экономическому критерию
- 4. 7. Испытание процедуры самообучения при нетейлоровской стойкостной зависимости
- 4. 7. 1. Испытание основных вариантов процедуры
- 4. 7. 2. Испытания модификаций процедуры самообучения
- 4. 8. Испытание процедуры самообучения с ограничением на память
- 4. 9. Учет дискретности ряда частот вращения шпинделя
- 4. 10. Выводы
Оптимизация скорости резания в режиме реального времени при токарной обработке (реферат, курсовая, диплом, контрольная)
В машиностроительном производстве станки с числовым программным управлением, автоматические линии и многооперационные станки составляют большую часть оборудования предприятия. В связи с широкой автоматизацией машиностроительного производства огромное значение приобретает задача определения оптимальных режимов работы инструмента. От этого во многом зависят производительность оборудования, себестоимость и точность обработки, расход режущего инструмента, качество поверхностного слоя и другие параметры процесса металлообработки. Тесная взаимосвязь технологических и экономических факторов [24], определяющая влияние режимов работы станков на производство в целом, привела к тому, что расчет режимов резания стал одной из важных задач в машиностроении.
Режимы резания устанавливаются технологами или нормировщиками на основе принятых на предприятиях для данного вида деталеоперации нормативов режимов резания. Под режимом резания понимают совокупность глубины резания, подачи, скорости резания и периода стойкости [10].
Правильный расчет режимов резания является ответственным и весьма трудоемким делом, на которое технологами затрачивается значительное время.
На производстве режимы резания назначаются в соответствии с нормативами. Однако, производственные условия, как правило, отличаются от нормативных. Здесь сказывается влияние динамического состояния станка, колебания свойств между партиями изделия, колебания свойств между партиями инструмента и т. д. и учесть их на стадии проектирования технологического процесса не представляется возможным. Влияние субъективного фактора оказывается неизбежным при учете реальных условий. В условиях обработки новых материалов, новыми материалами инструмента, при новых технологических процессах, т. е. когда нормативные данные отсутствуют или являются не полными, задача существенно осложняется.
Существующие методы и системы управления и оптимизации режимов резания либо основываются на использовании эмпирических показателей процесса резания, полученных при определенных условиях эксперимента и неадекватно отражающих состояние станочной системы, либо для своей реализации требуют большого объема материальных затрат и дополнительных аппаратных средств при относительно низкой эффективности регулирования. Потеря точности при оценке показателей процесса резания неизбежно приводит к экономическим потерям. Эти потери определяются простоем оборудования и рабочей силы, сверхурочными работами, нарушением ритмичности производственного процесса, повышенным износом режущего инструмента, что отрицательно сказывается на качестве продукции, и чревато штрафными санкциями за невыполнение контрактных обязательств. Экономические потери неизбежно увеличивают себестоимость изделий, а нерациональное использование оборудования снижает его производительность.
Стремление преодолеть указанные недостатки привело к появлению автоматизированных систем управления, которые позволяют оптимизировать процесс металлообработки благодаря получаемой текущей информации по параметрам, определяющим условия и качество процесса резания. Задачей подобных систем управления, которые называются адаптивными [2, 106], является такое изменение управляемых параметров процесса резания, которое в условиях действия случайных возмущающих воздействий обеспечивало бы экстремум выбранного критерия оптимизации — производительности, себестоимости и т. п. Причем изменение параметров процесса резания осуществляется в режиме реального времени [86, 96], под которым в соответствии с ГОСТ 15 971–90 понимается режим обработки информации, обеспечивающий взаимодействие системы обработки информации с внешними по отношению к ней процессами в темпе, соизмеримом со скоростью протекания этих процессов. Обработка резанием обусловливает темп взаимодействия системы обработки информации с внешними процессами, соответствующий периоду стойкости режущего инструмента.
В условиях промышленной реформы и экономического стимулирования задача назначения экономически оптимальных режимов резания непосредственно в производственных условиях приобретает особую актуальность. Решению данной задачи и посвящены выполненные диссертационные исследования.
В первой главе рассмотрены основные показатели оптимальности режимов резания и методы выбора критерия оптимальности режима резания в соответствии с конкретными производственными условиями и обстоятельствами и техническими и технологическими ограничениями. Выполнен анализ надежности режущего инструмента и зависимости его стойкости от скорости резания. Приведен обзор существующих систем управления в режиме реального времени и методов их обучения и самообучения. В результате сформулированы требования к математической модели и программно-алгоритмической реализации систем управления режимами резания в реальном времени.
Вторая глава посвящена описанию оптимизации скорости резания в режиме реального времени на основе процесса самообучения. На основе анализа известных процедур самообучения при оптимизации процесса резания выявлены их недостатки и предложена процедура управления скоростью резания в режиме реального времени с восстановлением стойкостной зависимости в процессе самообучения.
В третьей главе на основе статистического моделирования процесса резания произведены анализ и выбор метода оценки параметров стойкостной зависимости. Показано, что достаточной точностью при простоте алгоритма оценки обладает вариант метода наименьших квадратов по отклонению логарифмов стойкости. Он и был принят для использования в процедуре самообучения при управлении скоростью резания в режиме реального времени.
В четвертой главе проведена экспериментальная проверка оптимизации скорости резания в режиме реального времени на статистической модели с использованием предложенного интегрального критерия оценки эффективности процесса самообучения, состоящего в учете себестоимости обработки в режиме самообучения. В результате испытаний различных вариантов процедур самообучения выявлены варианты, дающие стабильную эффективность на разных моделях процесса резания и поэтому пригодных для практического использования на станках с развитыми вычислительными возможностями системы ЧПУ. Предложена модификация процедуры управления скоростью резания в режиме реального времени для станков со ступенчатым регулированием частоты вращения шпинделя.
В заключении обсуждены итоги работы и сформулированы общие выводы по диссертации.
Автор защищает следующие теоретические и прикладные результаты работы:
— общий подход к оценке стойкостной зависимости режущего инструмента непосредственно на рабочем месте в режиме реального времени с самообучением;
— теоретико-вероятностную модель процесса резания, позволяющую на основе оценки стойкостной зависимости оптимизировать параметры резания в режиме реального времени;
— инженерную методику и математическое обеспечение самообучающейся процедуры, позволяющие повысить эффективность управления процессом резания в режиме реального времени.
Научная новизна заключается в теоретико-вероятностном представлении процесса резания, раскрывающем зависимость между параметрами процесса резания и стойкостью режущего инструмента.
Автор выражает благодарность научному руководителю д.т.н., профессору Иноземцеву А. Н. и д.т.н., профессору Пасько Н. И. за научные консультации при подготовке диссертационной работы и другим сотрудникам кафедры «Автоматизированные станочные системы» Тульского государственного университета за помощь, поддержку, полезные замечания и предложения, высказанные в ходе обсуждения диссертационной работы.
9. Результаты работы приняты к внедрению на предприятии ОАО «Тяжпромарматура» (г. Алексин, Тульской обл.). т.
ЗАКЛЮЧЕНИЕ
И ОСНОВНЫЕ ВЫВОДЫ ПО РАБОТЕ.
Основным результатом данной диссертационной работы является решение важной научной задачи, имеющей существенное народнохозяйственное значение и заключающейся в назначении экономически оптимальных режимов резания непосредственно в производственных условиях в режиме реального времени.
Результаты проведенных теоретических исследований, математико-статистическая обработка данных о надежности режущего инструмента, а также опыт практического использования разработанного методического и программного обеспечения позволяют сделать следующие основные выводы.
1. В результате обобщения производственного опыта и анализа трудов отечественных и зарубежных исследователей установлено, что существующие методы и системы управления и оптимизации режимов резания либо основываются на использовании эмпирических показателей процесса резания, полученных при определенных условиях эксперимента и неадекватно отражающих состояние станочной системы, либо для своей реализации требуют большого объема материальных затрат и дополнительных аппаратных средств при относительно низкой эффективности регулирования.
2. Обоснована необходимость разработки автоматизированных адаптивных самообучающихся систем управления, которые позволяют оптимизировать процесс металлообработки непосредственно в производственных условиях в режиме реального времени при котором адаптивная система управляет процессом резания в темпе, соизмеримом со скоростью его протекания. Показано, что обработка резанием обусловливает темп взаимодействия системы обработки информации с внешними процессами, соответствующий периоду стойкости режущего инструмента.
3. Анализ известных процедур самообучения применительно к оптимизации процесса резания показал, что процедура Роббинса-Монро пригодна только для стабилизации процесса резания на заданную среднюю производительность, а процедура Кифера-Волфовица позволяет найти максимум или минимум математического ожидания функции регрессии, но так как критерий оптимальности процесса резания — производительность или себестоимость операции — является отношением двух регрессий, то непосредственно эта процедура к процессу резания не применима. Данные обстоятельства обусловливают необходимость разработки оригинальных процедур управления процессом механической обработки использующих для ускорения процесса самообучения явно вид стойкостной зависимости в области оптимальных скоростей резания. Тогда в процессе самообучения можно в режиме реального времени последовательно уточнять параметры стойкостной зависимости, используя данные всех предшествующих итераций и скорость резания для следующей итерации рассчитывать с учетом уточненной стойкостной зависимости.
4. Разработана самообучающаяся процедура управления процессом резания в режиме реального времени с восстановлением стойкостной зависимости в предположении, что вблизи оптимума стойкостная зависимость может быть аппроксимирована степенной зависимостью Тейлора. Предложены семь вариантов метода оценки параметров стойкостной зависимости и реализующие их алгоритмы, а также модификация самообучающейся процедуры управления процессом резания в режиме реального времени в направлении учета дрейфа условий обработки.
5. В результате сравнения различных вариантов метода оценки параметров стойкостной зависимости, проведенного на статистической модели процесса резания, реализующей разброс стойкости по заданному закону с коэффициентом вариации стойкости, не зависящим от скорости резания показано, что в самообучающейся процедуре управления процессом резания в режиме реального времени ввиду простоты алгоритма оценки целесообразно использовать метод наименьших квадратов по отклонению логарифмов стойкости (1п.
6. Разработан алгоритм испытания предложенной самообучающейся процедуры оптимизации скоростей резания в режиме реального времени, основанный на использовании статистических моделей процесса резания, и интегральный критерий оценки эффективности процесса самообучения, состоящий в учете себестоимости обработки при управлении резанием в режиме реального времени с самообучением.
7. Определена эффективность вариантов самообучающейся процедуры управления процессом резания в режиме реального времени в зависимости от коэффициента вариации стойкости при его значениях от 0 до 1.
8. В результате испытаний различных вариантов процедур самообучения выявлены варианты, дающие стабильную эффективность на разных моделях процесса резания и поэтому пригодных для практического использования на станках с развитыми вычислительными возможностями системы ЧПУ, а также предложена модификация процедуры самообучения для станков со ступенчатым регулированием частоты вращения шпинделя.
Список литературы
- Автоматы и автоматические линии. Ч. I. Основы проектирования / Под ред. Г. А. Шаумяна. М.: Высшая школа, 1976. — 230 с.
- Адаптивное управление металлорежущими станками. Серия I, М.: НИИМаш, 1973.-228 с.
- Адаптивное управление станками. /Под ред. Б. С. Балакшина. М.: Машиностроение, 1973. 688 е., ил.
- Адаптивные системы автоматического управления: Республиканский межведомственный научно-технический сборник. Выпуск 13. К.: Техшка, 1985. — 132 е., ил.
- Акимов И.В. Самообучающаяся система экспресс-оценки трудоемкости изготовления деталей машин: Автореф. дис.канд. техн наук: 05.02.08/ Тульский гос. ун-т, 1999. — 16 с.
- Балакшин Б.С. Использование систем адаптивного управления для повышения точности и производительности обработки// Станки и инструмент. — 1972. № 4.
- Башков В.М. Методы оценки и контроля надежности режущего инструмента: Дис.канд. техн. наук/Москва, 1962.
- Башков В.М., Кацев П. Г. Испытания режущего инструмента на стойкость. -М.: Машиностроение, 1985. 136 е.: ил. ф 10 Бобров В. Ф. Основы теории резания металлов. М.:
- Машиностроение, 1975. 344 с.
- Бровкова М.Б. Оперативная оптимизация процесса чистовой токарной обработки на основе учета динамического состояния оборудования: Автореф. дис.канд. техн наук: 05.03.01/ Саратов, гос. техн. ун-т, 1999. 16 с.
- Бронштейн И.Н., Семендяев К. А. Справочник по математике для инженеров и учащихся ВТУЗов. М.: ГИТТЛ, 1956. — 608 с.
- Вазан М. Стохастическая аппроксимация. /Пер. с англ. Э. М. Вайсборда. -М.: Мир, 1972. 295 е.: ил.
- Великанов K.M. и Новожилов В.И. Экономичные режимы резания металлов. — Л.: Машиностроение, 1972 — 120 с.
- Вентцель Е.С. Теория вероятностей. М.: Наука, 1969. — 576 с.
- Вентцель Е.С., Овчаров Л. А. Теория вероятностей и ее инженерные приложения. М.: Наука, 1988. -480 с.
- Войнов К.Н. Прогнозирование надежности механических систем.
- Л.: Машиностроение, 1978. 208 е., ил. il
- Волчкевич Л.И. Некоторые вопросы теории производительности в машиностроении: Автореф. дис.канд. техн наук/ МВТУ им. Баумана, 1963. 18 с.
- Вульфсон И.А., Зусман В. Г., Ратмиров В. А. Автоматическое регулирование режима резания на фрезерных станках с ПУ //Станки и инструмент. 1965. — № 9.
- Высоковский Е.С. Влияние способов заточки на надежность режущего инструмента в автоматическом производстве// Вестник машиностроения. — 1970. № 3.
- Высоковский Е.С. Технологические исследования надежности и производительности многоинструментальных наладок автоматизированного металлорежущего оборудования: Дис. канд. техн. наук/Ростов-на-Дону, 1963
- Грановский Г. И., Грановский В. Г. Резание металлов: Учебник для машиностр. и приборостр. вузов. М.: Высш. шк., 1985. — 304 е., ил.
- Герцбах И.Б., Кордонский Х. Б. Модели профилактики. М.: Советское радио, 1969. 214 е., ил.
- Гильман A.M. и др. Оптимизация режимов обработки на металлорежущих станках. М.: Машиностроение, 1972. 188 е., ил.
- Глебов С.Ф. Теория наивыгоднейшего резания металлов. М.: Госмашметиздат, 1933
- Глинников М. Комплекс CuneiForm Collection// Мир ПК. 1998. -№ 3. — с. 58−59.
- Гнеденко Б.В., Беляев Ю. К., Соловьев А. Д. Математические методы теории надежности. М.: Наука, 1965. — 524 с.
- Городецкий М.С. и др. Числовое программное управление металлорежущими станками. М.: НИИМаш, 1970. 151 е., ил.
- Гордиенко Б.И., Краплин М. А. Оптимальные режимы металлорежущих станков / Под ред. С. С. Четверикова. Ростов-на-Дону, 1969.-423 с.
- Грановский Г. И. О стойкости инструмента как исходном параметре для расчета режимов резания// Вестник машиностроения. 1965. -№ 8.
- Грановский Г. И., Баклунов Е. Д., Панченко К. П. Стабильность работы режущего инструмента на автоматических линиях// Автоматизация и механизация производственных процессов в машиностроении. М.: Машиностроение, 1967. — с. 62 — 85.
- Гришин С. А. Применение алгоритмов самообучения к оптимизации процесса резания на примере токарной и сверлильной обработки: Дис. канд. техн. наук/ ТулГУ, 2000. 238с.
- Гумбель Э. Статистика экстремальных значений /Пер. с англ. В.Ю.
- Татарского М.: Мир, 1965. 450 е., ил.
- Демаков И.П., Балагезен Ю. Г. Организация испытаний нанадежность и обработка их результатов. М.: Машиностроение, 1974.
- Демидович Б.П., Марон И. А. Основы вычислительной математики. -М.: Наука, 1966, 664 с.
- Демьянюк Ф.С. Технологические основы поточного и автоматизированного производства. М.: Машгиз, 1958
- Дрейпер Н., Смит Г. Прикладной регрессионный анализ. М: Статистика, 1973. 392 с.
- Дружинин Г. В. Анализ эрготехнических систем. М.: Энергоатом издат, 1984. — 160 е., ил.
- Дюбуа Д., Прад А. Теория возможностей. Приложение к представлению знаний в информатике: Пер. с фр. М.: Радио и связь, 1990.-288 е.: ил.
- Дубовицкий Д.В. Оптимизация режимов резания на основе экономических критериев // Автоматизация и информатизация в машиностроении. Сб. трудов Второй междунар. электронной науч.-техн. конф. Тула: Гриф и К0, 2001. — С. 77 — 79.
- Елисеев В.А., Прытков В. Г. Система экстремального управления металлорежущим станком.// Труды МЭИ. Электромеханика, вып. 56, 1964.
- Еремеев В.В. Исследование и разработка метода автоматизированного назначения режимов обработки для токарных станков с ЧПУ на основе измерения термоЭДС зоны резания: Автореф. дис.канд. техн наук: 05.03.01/ Волгоград, гос. техн. ун-т, 1999.-20 с.
- Ермаков С.М., Михайлов Г. А. Курс статистического моделирования,— М.:Наука, 1976.- 320 с.
- Зажигаев Л.С., Кишьян A.A., Романов Ю. И. Методы планирования и обработки результатов физического эксперимента. М.: Атомиздат, 1978.-231 е., ил.
- Заренин Ю.Г., Стоянова И. И. Определительные испытания на надежность. М.: Изд-во стандартов, 1978. 168 с.
- Ивахненко А.Г. Самообучающиеся системы с положительным обратными связями: Справочное пособие. Киев: Изд-во АН УССР, 1963.-328 с.
- Ивахненко А.Г. Техническая кибернетика. Киев: Гостехиздат, 1962.
- Ивахненко Е. О. Обеспечение точности обработки на токарных станках посредством выбора рациональных режимов резания с
- Игумнов Б.Н. Расчет оптимальных режимов обработки для станков и автоматических линий. М.: Машиностроение, 1974. — 200 е.: ил.
- Иноземцев А.Н. Структурно-параметрический синтез систем из параллельно работающих станков для токарной обработки изделий массового производства: Диссерт. на соискание ученой степени канд. техн. наук. Тула, 1984. 318 с.
- Иноземцев А.Н. Проектирование процессов и систем механообработки на основе разрешения неопределенности технологической информации: Автореф. дис.докт. техн наук: 05.03.01/ Тульск. гос. техн. ун-т, 1998. 42 с.
- Иноземцев А.Н., Пасько Н. И. Надежность станков и станочных систем.-Тула, ТулГУ, 2002.- 192 с.
- Иноземцев А.Н., Пасько Н. И., Дубовицкий Д. В. Оптимизация режимов резания с применением процедур самообучения //
- Кацев П.Г. Статистические методы исследования режущего инструмента. Изд. 2, М., Машиностроение, 1974.
- Кендал М., Стьюарт А. Статистические выводы и связи.-М.:Наука, 1973.-817 с.
- Козлов Б.А., Ушаков И. А., Справочник по расчету надежности. М.: Советское радио, 1975. 471с., ил.
- Кокс Д.Р., Смит B.JI. Теория восстановления. М.: Советское радио, 1967. 299 с.
- Колесов И.М. Основы технологии машиностроения: Учебник для машиностроительных вузов. М.: Машиностроение, 1997. — 592 е.: ил.
- Краплин М.А. Повышение эффективности металлорежущего оборудования на основе оптимизации режимов его работы. 05,02,08. дтн, Ростов-на-Дону, 1989.
- Лоладзе Т.Н. Прочность и износостойкость режущего инструмента. М.: Машиностроение, 1982. — 320 е., ил.
- Маталин A.A. Технология машиностроения: Учебник для машиностроительных вузов. JL: Машиностроение, Ленингр. отд-ние, 1985. — 496 с.
- Макаров А. Д. Оптимизация процессов резания. М.: Машиностроение, 1976. — 278 е.: ил.
- Макаров М.В. Повышение эффективности точения инструментом из СТМ на основе назначения рациональных режимов резания с учетом ультразвуковой диагностики его свойств: Автореф. дис.канд. техн наук: 05.03.01/РГАТА, 2000. 18 с.
- Методика расчета экономической эффективности новой техники в машиностроении. Под ред. К. М. Великанова. Л.: Машиностроение, 1967.-499 с.
- Надежность режущего инструмента. /Под ред. Г. Л. Хаета. Киев: Вища школа, 1975. — 312 е., ил.
- Невельсон М.Б., Хасьминский Р. З. Стохастическая аппроксимация и рекуррентное оценивание. -М.: Наука, 1972. 304 е.: ил.
- Невельсон P.A. Вероятностный анализ процесса изнашивания сверл и законы распределения стойкости// Надежность режущего инструмента. Киев: Техника, 1972. — 258 е., ил.
- Никин А.Д. Адаптивная система управления температурно-силовыми режимами процесса резания металлов: Автореф. дис.канд. техн наук: 05.13.07/УГАТУ, 1999.- 17 с.
- Никифоров А.Д. и др. Процессы управления объектами машиностроения: Учеб. пособие для машиностроит. спец. вузов. / А. Д. Никифоров, А. Н. Ковшов, Ю. Ф. Назаров. — М.: Высшая школа, 2001.-455 с.
- Обработка нечеткой информации в системах принятия решений /А.Н.Борисов, А. В. Алексеев, Г. В. Меркурьева и др. М.: Радио и связь, 1989. — 304 с.
- Общемашиностроительные нормативы режимов резания: Справочник: В 2-х т.: Т1/ А. Д. Локтев, И. Ф. Гущин, В. А. Батуев идр. — М.: Машиностроение, 1991. — 640 е.: ил.
- Оптимизация режимов обработки на металлорежущих станках /Гильман А.М. и др. М.: Машиностроение, 1972. 188 с.
- Пасько Н.И. Некоторые вопросы статистической теории рядов скоростей и подач и оптимального управления режимом резания: Дис. канд. техн. наук/ ТПИ, 1963.
- Пасько Н.И. Научные основы машинно-ориентированного анализа и оптимизации станочных систем для обработки тел вращения. Дис. докт. техн. наук / Тула. 1983.
- Пасько Н.И. Надежность станков и автоматических линий. Тула: ТПИ, 1979.- 106 с.
- Пасько Н.И. Некоторые вопросы статистической теории рядов скоростей и подач и оптимального управления режимом резания: Дис. канд. техн. наук/ТПИ, 1963
- Пасько Н.И. О средней стойкости многоинструментной наладки //Вестник машиностроения. 1969. — № 2
- Пасько Н.И., Иноземцев А. Н., Акимов И. Н. К методике вероятностного расчета времени выполнения партии деталей //Известия ТулГУ. Серия «Машиностроение», Вып. 3. Тула, 1998.
- Попов М.А. Структура самообучающейся адаптивной технологической системы прогнозирующего типа длямногопроходной токарной обработки: Автореф. дисканд. техннаук: 05.02.08/ Тул. техн. ун-т, 1999. 23 с.
- Применение управляющих вычислительных машин / А. Н. Морозевич, A.B. Николаев, А. П. Пашкевич, A.A. Петровский. — Мн.: Выш. шк., 1988.-238 с.
- Режимы резания металлов. Справочник. Подред. Ю. В. Барановского." М. Машиностроение, 1972.- 410 с.
- Садов В.А. Оптимизация процесса многопроходного нарезания резьбы резцом: Автореф. дис.канд. техн наук: 05.03.01/ ТПИ, 1983.-20 с.
- Самонастраивающиеся станки. /Сб. под ред. B.C. Балакшина. М.: Машиностроение, 1970.
- Самоорганизующиеся стохастические системы управления. /Дж.Саридис /Пер. с англ./Под ред. Я. З. Цыпкина. М.: Наука, 1980. -400 с.
- Сандлер A.C. Электропривод и автоматизация металлорежущих станков. М.: Высшая школа, 1972. 439 с.
- Семибратова М.В. Диагностика и управление контактнымипроцессами при резании: Автореф. дисканд. техн наук: 05.03.01/
- К.-А. гос. техн. ун-т, 2000. 19 с.
- Смирнов Н.В., Дунин-Барковский И.В. Курс теории вероятностей и математической статистики для технических приложений. М.: Наука, 1965. — 512 с.
- Старков В.К. Обработка резанием. Управление стабильностью и качеством в автоматизированном производстве. — М.: Машиностроение, 1989. 296 с. ил.
- Старков В.К. Технологические методы повышения надежности обработки на станках с ЧПУ. М.: Машиностроение, 1984. — 120 с.
- Строганов Р.П. Управляющие машины и их применение. — М.: Выш. шк., 1986.-240 с.
- Тверской М.М. Автоматическое управление режимами обработки деталей на станках. М.: Машиностроение, 1982. — 208 е.- ил.
- Тейлор Ф. Искусство резать металл. Изд. 2, 1902 г.
- Темчин Г. И. Теория и расчет многоинструментных наладок. — М.: Машгиз, 1957. 557 с.
- Терешин М.В. Повышение надежности обработки отверстий на основе диагностирования состояния осевого инструмента: Автореф. дисканд. техн наук: 05.03.01/ Станкин, 1986. — 16 с.
- Фаронов В. В. Турбо Паскаль 7.0.- М.:"Нолидж", 2001.- 576 с.
- Феллер Б. Введение в теорию вероятностей и ее приложения. В 2-х т. Т.1. М.: Мир, 1984. — 527 е., ил.
- Хает Г. Л. Повышение эффективности обработки на тяжелых станках на основе исследований надежности, многокритериальной оптимизации параметров и режимов эксплуатации инструмента: Дис.докт. техн наук: 05.03.01/ Станкин, 1992. 33 с.
- Хает Г. Л. Прочность режущего инструмента. — М.: Машиностроение, 1975. 168 е., ил.
- Центер Л.С. Исследования надежности режущего инструмента металлообрабатывающего автоматизированного оборудования: Дис. .канд. техн наук/ Минск: АН БССР, ОТН, 1962
- Цыпкин Я.З. Основы теории обучающихся систем. М.: Наука, 1970.-252 с.
- Цирлин A.M. Оптимальные циклы и циклические режимы. — М.: Энергоатомиздат, 1985. 264 е., ил.
- Чавчанидзе В.В., Кумеишвилли В. А. Об определении распределения на основе малого числа наблюдений. В сб. «Применение вычислительной техники для автоматизации производства» /Под ред. Солодовникова В. В. М.: Машгиз, 1961. — 536 с.
- Червяков Л.М. Управление процессом обеспечения точности изделий машиностроения на основе когнитивных моделей принятиятехнологических решений: Автореф. дисдокт. техн наук:0502.01/Москва, 1999
- Чернышев Н.М. Оптимизация скорости резания при изменяющихся условиях фрезерования: Автореф. дис.канд. техн наук: 05.03.01/ Горьковск. политехи, ин-т, 1979. — 24 с.
- Шаумян Г. А. Автоматы и автоматические линии. М.: Машгиз, 1961.-552 е., ил.
- Шаумян Г. А. Основы теории проектирования станков-автоматов и автоматических линий. М.: Машгиз, 1949. — 262 с.
- Шор Я. Б., Кузьмин Ф. И. Таблицы для анализа и контроля надежности. М.: Советское радио, 1968. — 288 с.
- Щелкунова М.Е. Диагностика состояния режущего инструмента на основе вероятностных и информационных параметров акустической эмиссии и термоЭДС: Автореф. дис.канд. техн наук: 05.03.01/ К.-А. гос. техн. ун-т, 2000. 20 с.
- Ямпольский JI.C., Тараненко В. А., Евдокимов В. Д. Средства и методы автоматического управления режимами обработки металлов резанием. К.: УкрНИИНТИ, 1975. 62 с.
- Янке Е., Эмде Ф., Леш Ф. Специальные функции. Формулы, графики, таблицы.- М.: Наука, 1968.- 344 с.
- Anil К., JianchangM., Mohiuddin К. М. Введение в искусственные нейронные сети М.: Открытые системы, 1997. — № 4. — С. 16−24.
- DNC Kit// Manufacturing Engineering (USA). 1996. — 116, № 6. — p.84
- Kneppelt L.R. Planning: The Challenge in a CIM Environment // Automation, Jan. 1991, p. 34−35
- PC-based DNC for 16 mashines.//Metalwork. Prod. 1995. — 139, № 2. -p.22
- Robbins H., Monro S. A stochastic approximation method. Ann. Math. Statist., 22, 1 (1951), 400−407
- The Latest generation// Machine and Product Engineering. — 1998. -156, № 3956.-p. 64
- Venter J.H. An extension of the Robbins — Monro procedure. Ann. Math. Statist., 38, 1, 1967. p. 181 190.
- Wager J.G., Barash M.M. Study of the Distribution of the Life of HSS Tools. //Journal of Engineering for Industry, January 4, 1971.
- Wilde D. Optimal Seeking Methods. New York: Prentice-Hall, 1963.