Формирование поверхностной структуры конструкционных материалов под воздействием газовой и металлической плазмы в процессе вакуумной ионно-плазменной обработки
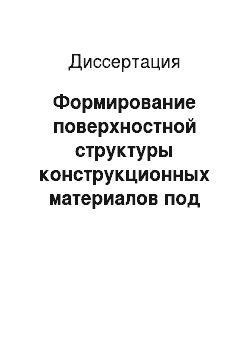
На основе проведённых исследовании разработана новая система размещения источников газовой и металлической плазмы в виде поворотных технологических модулей. На основе этих модулей создана новая компоновочная схема универсальной установки модульного типа, изготовлена установка «Радуга», которая позволяет реализовать комплексные технологии, сочетающие модифицирование и нанесение покрытий… Читать ещё >
Содержание
- Глава I. Состояние вопроса
- 1. 1. Развитие методов и оборудования для вакуумной ионно-плазменной обработки поверхности конструкционных материалов авиационной техники
- 1. 1. 1. Вакуумная ионно-плазменная комплексная обработка поверхности
- 1. 1. 2. Формирование многокомпонентных покрытий
- 1. 1. 3. Формирование многослойных покрытий
- 1. 1. 4. Вакуумное ионно-плазменное оборудование
- 1. 2. Вакуумные ионно-плазменные технологии
- 1. 2. 1. Влияние технологических параметров на процесс формирования покрытий
- 1. 2. 2. Вакуумные ионно-плазменные покрытия различного служебного назначения
- 1. 3. Контроль качества покрытий
- 1. 1. Развитие методов и оборудования для вакуумной ионно-плазменной обработки поверхности конструкционных материалов авиационной техники
Формирование поверхностной структуры конструкционных материалов под воздействием газовой и металлической плазмы в процессе вакуумной ионно-плазменной обработки (реферат, курсовая, диплом, контрольная)
Актуальность работы. Развитие современного машиностроения, в том числе и авиационной техники, невозможно представить без использования технологий поверхностной обработки, позволяющих радикально изменять свойства поверхностных слоев конструкционных материалов и тем самым обеспечивать повышение их работоспособности. Одним из направлений повышения работоспособности изделий является создание модифицированных поверхностных слоев и покрытий различного служебного назначения для защиты рабочих поверхностей деталей. При этом реализуемый новый комплекс физико-химических и эксплуатационных свойств, как правило, не свойственен материалу основы и позволяет обеспечить как работоспособность поверхностных слоев изделий в экстремальных условиях эксплуатации, так и их ремонт.
Вакуумные ионно-плазменные технологии используются в авиационной промышленности с 1986 г., когда впервые был разработан нормативный технологический процесс по нанесению многослойных коррозионно-износостойких покрытий на основе композиции ТьТТЫ на ниппельные соединения трубопроводов гидравлических систем самолётов. Двадцатилетний опыт эксплуатации данного вида покрытий показал его высокую надёжность.
Современные достижения в области оборудования и вакуумных ионно-плазменных технологии позволяют рассматривать их как наиболее перспективные технологии при производстве изделий авиационной техники. Так как они позволяют создавать сложные композиции различных видов покрытий, а также осуществлять комплексную обработку с предварительным диффузионным модифицированием. Это в свою очередь позволяет создавать градиентные структуры поверхностных слоёв со специальными свойствами без ухудшения механических свойств в объеме изделий. При этом модифицирование поверхности дает значительный положительный эффект как за счет повышения ресурса работы изделий, так и за счет снижения затрат на мероприятия по повышению несущей способности основного материала, включая дополнительное легирование и совершенствование технологий производства полуфабрикатов и изделий.
Однако широкое применение вакуумных ионно-плазменных технологий в производстве ответственных деталей авиационной техники сдерживается целым рядом проблем, связанных с обеспечением качественного выполнения различных технологических этапов формирования покрытии и модифицирования поверхности:
— формирование однородного потока плазмы в рабочем объёме вакуумной камеры, как по энергетическим параметрам, так и по его плотностираспределение плазменного потока относительно обрабатываемой поверхности;
— формирование контролируемой текстуры покрытия за счет варьирования плотности и энергии плазменного потока;
— формирование контролируемого состава многокомпонентных покрытий из чистых металлических компонентов или из сплавов при использовании электродуговых испарителей;
— оптимизации технологии подготовки поверхности деталей перед вакуумной ионно-плазменной обработкой.
Самостоятельной проблемой является сохранение исходного уровня механических свойств материала детали после воздействия на него высокоэнергетического плазменного потока. Это делает необходимым разработку таких технологических режимов, которые не только не снижают, но в ряде случаев даже повышают служебные характеристики материала детали за счет создания на поверхности композиционной структуры.
Для эффективного решения указанного комплекса проблем необходимо создание системы оценки уровня служебных свойств и структурного состояния материалов, подвергнутых различным видам поверхностной обработки, что позволит обеспечить воспроизводимость формирования структуры и свойств поверхностных слоев материалов в технологических процессах.
Таким образом, исследования, направленные на решение проблем применения экологически чистых вакуумных ионно-плазменных технологий, на основе изучения формирования равномерных по плотности и энергии потоков газовой и металлической плазмы, а также анализа закономерностей формирования структуры и свойств модифицированных поверхностей и покрытий на деталях авиационной техники, обеспечивающие гарантированный уровень эксплуатационных свойств, являются актуальными.
Цель работы: Исследование закономерностей влияние воздействия газовой и металлической плазмы на структуру и свойства поверхностных слоев конструкционных материалов на различных этапах технологического процесса вакуумной ионно-плазменной обработки, в зависимости от энергетических характеристик плазмы и компоновки источников плазмы серийных установок типа ННВ-6.6.
Для достижения постановленной цели необходимо было решить следующие задачи:
1. Выявить влияние геометрических, химических и энергетических характеристик газовой и металлической плазмы на структуру и свойства поверхностных слоев конструкционных материалов на различных этапах технологического процесса вакуумной ионно-плазменной обработки, осуществляемой с использованием серийных установок типа «ННВ-6.6»;
2. Разработать метод оценки качества подготовки поверхности и эффективности проведения различных этапов технологического процесса модифицирования поверхности и нанесения покрытий;
3. Разработать технологические способы повышения эффективности очистки и активации поверхности перед проведением модифицирования поверхности и нанесения покрытий;
— 84. На основе установленных закономерностей создать компоновочную схему установки нового поколения и разработать комплекс аппаратурных и технологических мероприятий, обеспечивающих получение требуемой структуры поверхностных слоев и стабильно высокий уровень эксплуатационных свойств.
Научная новизна состоит в следующем:
1. Разработан метод очистки и активации поверхности деталей из конструкционных материалов, путем обработки ускоренной газовой плазмой, что обеспечивает полное удаление оксидов без внесения макрои микроструктурных дефектов в поверхностный слой деталей.
Показано, что эффективность очистки и активации поверхности зависит от шероховатости исходной поверхности и степени замещения атомов металла основы сплава, из которого изготовлена деталь в поверхностном оксиде атомами легирующих элементов сплава. Для поверхностей с параметром шероховатости Яа < 0,3 мкм и низкой степенью замещения энергия ионов плазмы не должна превышать 200 эВ, а для поверхностей с К. а > 0,3 мкм и высокой степенью замещения — 400 эВ.
2. Разработана комплексная система оценки эффективности реализации отдельных этапов технологического процесса вакуумной ионно-плазменной обработки и качества сформированной поверхностной структуры изделий из различных конструкционных материалов. В рамках этой системы показана эффективность метода количественной оценки эффективности процессов очистки и активации поверхности по изменению величины поверхностного потенциала, и рентгеновского флюоресцентного метода неразрушающего контроля толщины покрытия.
3. Установлены закономерности влияния энергетических параметров газовой и металлической плазмы на структурное состояние поверхностного слоя при модифицировании, а также на структуру, кристаллографическую текстуру и когерентность границ слоев при формировании однокомпонентных и многокомпонентных однослойных и многослойных покрытий.
4. Установлен количественный критерий выбора эффективности применения плазмообразующего газа для процессов очистки и активации исходной поверхности, согласно которому, поверхность детали можно считать полностью очищенной и активизированной для реализации процессов модифицирования и нанесения покрытия, если значения поверхностного потенциала находятся в области положительных значений.
5. Показано что, оптимальной температурой ионной очистки является температура, при которой дефектность поверхностных оксидов наибольшая, что соответствует максимальной величине потенциала поверхности. Температура ионной очистки поверхности составляет для титановых сплавов ~400°С, ~350°С для сталей и ~350°С для алюминиевых сплавов, что обеспечивает удаление оксидов с поверхности при минимальном уровне энергетического воздействия плазмы на поверхность.
Практическая значимость работы.
1. Разработана новая схема размещения источников газовой и металлической плазмы в виде поворотных технологических модулей. На основе этих модулей создана новая компоновочная схема универсальной установки модульного типа, изготовлена установка «Радуга», которая позволяет реализовать комплексные технологии, сочетающие модифицирование и нанесение покрытий на поверхности деталей из материалов, применяемых в авиастроении. Результаты разработки защищены двумя патентами.
2. Разработаны методические материалы «Комплексная оценка качества формирования ионно-вакуумных покрытий и диффузионного модифицирования поверхности деталей и изделий машиностроения» (ММ 13 430−4-2002), которые используются в производстве деталей авиационной техники.
— 103. Разработано и изготовлено устройство для измерения величины поверхностного потенциала на основе метода контактной разности потенциалов (КРП): «Приспособление для измерения разности потенциалов ПАСП-МК03" — комплект чертежей датчика 3−3430−1-2003; техническое описание и инструкция по эксплуатации 2−3430−1-2003.
4. На основе установленных закономерностей реализована комплексная технологическая схема обработки ниппельных соединений трубопроводов авиационной техники из конструкционных сталей, включающая низкотемпературную очистку и активацию поверхности ниппельных соединений с вакуумным ионно-плазменным нанесением многослойных покрытий, формирующих на поверхности многослойные коррозионностойкие градиентные структуры.
— 11.
ВЫВОДЫ ПО РАБОТЕ.
1. Установлены закономерности воздействия газовой и металлической плазмы на структуру и свойства поверхностных слоев конструкционных материалов в рабочем объёме вакуумной камеры серийных установок, в зависимости от энергетических характеристик и компоновки источников плазмы, а также выявлены факторы, влияющие. на процессы вакуумного ионно-плазменного модифицирования поверхности и формирования покрытий.
Показано, что величина поверхностного потенциала (ср), измеряемая после каждого этапа технологического процесса нанесения покрытия и модифицирования поверхности, является объективным количественным критерием оценки качества поверхности и стабильности эксплуатационных свойств.
2. Установлено, что эффективным способом удаления поверхностных дефектов подложки при ионной очистке и активации поверхности является обработка её ионами газовой плазмы. Показано, что эффективная энергия плазменного газового потока при очистке и активации поверхности зависит от её шероховатости и степени замещения металла основы в поверхностном оксиде сплава легирующим элементом. Для поверхностей с параметром шероховатости Ка < 0,3 мкм и малой степенью замещения энергия ионов не должна превышать 200 эВ, а для поверхностей с Ыа > 0,3 мкм и высокой степенью замещения — 400 эВ.
3. Предложен количественный критерий оценки энергетического состояния поверхности по величине поверхностного потенциала. Установлена зависимость величины потенциала от степени загрязнения поверхности и способа последующей очистки. Определены оптимальные температуры ионной очистки поверхности (~400°С для титановых сплавов, ~350°С для сталей и ~300°С для алюминиевых сплавов), позволяющие обеспечить наиболее полное удаление оксидов с обрабатываемой поверхности с минимальным уровнем энергетического воздействия плазмы на поверхность, что гарантирует сохранение исходной геометрии и структуры изделия.
4. На основе проведённых исследовании разработана новая система размещения источников газовой и металлической плазмы в виде поворотных технологических модулей. На основе этих модулей создана новая компоновочная схема универсальной установки модульного типа, изготовлена установка «Радуга», которая позволяет реализовать комплексные технологии, сочетающие модифицирование и нанесение покрытий на поверхности деталей из материалов, применяемых в авиастроении. Результаты разработки защищены двумя патентами.
5. Разработаны методические материалы «Комплексная оценка качества формирования ионно-вакуумных покрытий и диффузионного модифицирования поверхности деталей и изделий машиностроения» (ММ 13 430−4-2002), которые используются в производстве деталей авиационной техники.
6. Разработано и изготовлено устройство для измерения величины поверхностного потенциала на основе метода контактной разности потенциалов (КРП): «Приспособление для измерения разности потенциалов ПАСП-МК03" — комплект чертежей датчика-3−3430−1-2003; техническое описание и инструкция по эксплуатации-2−3430−1-2003.
7. На основе установленных закономерностей реализована комплексная технологическая схема обработки ниппельных соединений трубопроводов авиационной техники из конструкционных сталей, включающая низкотемпературную очистку и активацию поверхности ниппельных соединений с вакуумным ионно-плазменным нанесением многослойных покрытий, формирующих на поверхности многослойные коррозионностойкие градиентные структуры.
— 174.
Список литературы
- Модифицирование и легирование поверхности лазерными, ионными и электронными пучками (под редакцией Поута Дж.М.) // М. Машиностроение, 1987, 424.
- Абраимов Н.В., Елисеев Ю. С., Крымов В. В. Авиационное материаловедение и технология обработки металлов // М., Высшая школа, 1998, 446 с.
- Абраимов Н.В., Елисеев Ю. С., Крымов В. В. Химико-термическая обработка и защитные покрытия в авиадвигателестроении // М., Высшая школа, 1999, 526 с.
- Sillich R.N., Bolster R.N. and Singer I.L. in Hubter G.K., Holland O.W., Clayton C.R. and White C.W. (eds.) Ion Implantation and Ion Beam Processing of Materials // Elsevier, Amsterdam, 1985, p. 637.
- Pope L.E., Yost F.G., Follstaedt D.M., Picraux S.T. and Knapp J.A. in Hubler G.K., Holland O.W., Clayton C.R. and White C.W. (eds.) Ion Implantation and Ion Beam Processing of Materials // Elsevier, Amsterdam, 1985, p. 681.
- Singer I.L. in Hubler G.K., Holland O.W., White O.W., Clayton C.R. and White C.W. (eds.) Ion Implantation and Ion Beam Processing of Materials // Elsevier, Amsterdam, 1985, p. 585.
- Модифицирование и легирование поверхности лазерными, ионными и электронными пучками. Под редакцией Поута Дж.М. // М., Машиностроение, 1987, 424 с.
- Комаров Ф.Ф. Ионная имплантация в металлических материалах // М., Металлургия, 1990, 216 с.
- Плешивцев Н.В., Бажин А. И. Физика воздействия ионных пучков на материалы // М., Вузовская книга, 1998, 392 с.
- Ильин А.А., Петров Л. М., Бецофен С. Я., Спектор B.C. Ионно-вакуумные технологии создания градиентных, нанометрических поверхностных структур в конструкционных материалах // Сборник трудов
- I Российско-Японского семинара «Оборудование и технологии для производства компонентов твердотельной электроники и наноматериалов», М, МИСиС, 2005, с. 251−259.
- Musil J., Vlcek J., Ruzicka M. Recent progress in plasma nitriding // Vacuum № 59, 2000, p.p.940−951.
- Baek W.S., Kwon S.C., Lee S.R. et al A study of the interfacial structute between the TiN film and the iron nitride layer in a duplex plasma surface treayment // Surface and Coatings Technology № 114, 1999, p.p.94−100.
- Da Yung Wang, Chi Lung Chang, Cheng Hsun Hsu, Hua Ni Lin Synthesis of (Ti, Zr) N hard coatings by unbalanced magnetron sputtering // Surface and Coatings Technology № 130, 2000, p.p.64−68.
- Boxman R.L., Zhitomirsky V.N., Grimberg I., Rapoport L., Goldsmith S. Structure and hardness of vacuum arc deposited multi-component nitride coatings of Ti, Zr, and Nb // Surface and Coatings Technology № 125, 2000, p.p.257−262.
- Moller W.C., Parascandola S., Telbizova T. et.al., Surface processes and diffusion mechanisms of ion nitriding of stainless steel and aluminium // Surface and Coatings Technology № 136, 2001, p.p.73−79.
- Ильин A.A., Бецофен С. Я., Скворцова C.B., Петров Л. М., Банных И. О. Структурные аспекты ионного азотирования титановых сплавов // Металлы, 2002, № 3, с.6−15.
- Мубояджян С.А., Каблов E.H., Будиновский С. А. Вакуумно-плазменная технология получения защитных покрытий из сложнолегированных сплавов //МиТОМ, 1995, № 2. с. 15−18.
- Мубояджян С.А., Будиновский С. А. Конденсированные и конденсационно-диффузионные покрытия для лопаток турбин из жаропрочных сплавов с направленной кристаллической структурой // МиТОМ, 1996, № 4, с. 15−18.
- Yagodkin Yu.D., Pastuhov K.M., Muboyadjyan S.A., Kablov E.N. Application of Ion-Beam Treatment in Turbine Blade Production Technology // Surface and Coatings Technology № 84, 1996, p. 590−593.
- Мубояджян C.A., Будиновский С. А. Промышленная установка МАП-1 для нанесения защитных покрытий различного назначения // Авиационная промышленность, 1995, № 7−8, с. 44−48.
- Мубояджян С.А., Помелов Я. А. Вакуумно-плазменная технология высоких энергий // В сб.: Вопросы авиационной науки и техники. Серия «Авиационные материалы», 1983, № 1 с. 64−70 (ВИАМ).
- Дороднов A.M., Мубояджян С. А., Помелов Я. А., Струков Ю. А. Холловский торцевой ускоритель плазмы с холодным катодом // ПМТФ, 1981, № 1, с. 35−41.
- Мубояджян С.А., Помелов Я. А., Будиновский С. А., Шалин М. Р. Состояние и перспективы развития вакуумно-плазменной технологии высоких энергий // Авиационная промышленность, 1987, приложение № 3, с. 41−42.
- Афанасьев Н.И., Бушнев JI.C. Мубояджян С. А. и др. Структура и свойства жаростойких покрытий из сплава Ni-Cr-Al-Y // Известия вузов MB и ССО СССР, Физика, 1986, № 12, с. 22−25.
- Барабанов Б.Н., Блинов И. Г., Дороднов A.M., Дулова C.B., Минайчев В. Е., Мирошкин С. И., Мубояджян С. А. и др. Аппаратура плазменной технологии высоких энергий «холодные» системы для генерации плазм проводящих твердых веществ // ФХОМ, 1978, № 1, с. 44−51.
- Верещака A.C., Третьяков И. П. Режущие инструменты с износостойкими покрытиями //М.: Машиностроение, 1986, 192 с.
- Волин Э.М. Ионно-плазменные методы получения износостойких покрытий // Технология легких сплавов, 1984, № 10, с. 55−88.
- Григоров А.П., Дороднов A.M., Киселев М. Д. Некоторые физические основы установок Пуск-77 // Технология автомобилестроения, М.: НИИавтопром, 1978. т.2, с. 42−48.
- Данилин Б. С, Сырчин В. К. Магнетронные распылительные системы // М.: Радио и связь, 1982, 72 с.
- Падалко В.Г., Толок В. Т. Методы плазменной технологии высоких энергий // Атомная энергетика, 1978, т.44, вып.5, с. 476−478.
- Физика и применение плазменных ускорителей. Под ред. А. И. Морозова // Материалы 2-й ВНТК по плазменным ускорителям, Минск: Наука и техника, 1974, 390 с.
- Benning Hoff Hanns Физические методы нанесения твердых покрытий // Technische rundschau. 1986, № 78.
- Shengli Ma, Yanhuai Li, Kewei Xu The composite of nitrided steel of H13 and TiN coatings by plasma duplex treatment and the effect of pre-nitriding // Surface and Coatings Technology, № 137, 2001, p.p. 116−121.
- Sonoda T. and et. al Coating and superplastic Ti-alloy substrates Ti and Ti-0 films by magnetron DC sputtering // Thin Solid Films, № 386, 2001, p.p. 227 232.
- Manory Rafael R., Perry Anthony J. Some effects of ion beam treatments on titanium nitride coatings of commercial quality // Surface and Coatings Technology, № 114, 1999, p.p. 137−142.
- Itoh Y., Itoh A., Azuma H., Hioki T. Improving the tribological properties of Ti-6A1−4V alloy by nitrogen-ion impantation // Surface and Coatings Technology, № 111, 1999, c. 172−176
- Rudenija S. Duplex TiN coatings deposited by arc plating for increased corrosion resistance of stainless steel substrates // Surface and Coatings Technology, № 114, 1999, p.p. 129−136.
- Hasegava H., Kimura A., Suzuki T. TiixAlxN, TiixZrxN and TiixCrxN films synthesized by the AIP method // Surface and Coatings Technology, № 132, 2000, p.p. 76−79.
- Discerens M., Patscheider J., Levy F. Improving the properties of titanium nitride by incorporation of silicon // Surface and Coatings Technology № 108−109, 1998, p.p. 241−246.
- Nose M., Zhou M., Nagae T., Mae T., Yokota M., Saji S. Properties of Zr-Si-N coatings prepared by RF reactive sputtering // Surface and Coatings Technology, № 132, 2000, p.p. 163−168.
- Lewis D.B., Donohue L.A. The influence of the yttrium content on structure and properties of Ti.x.y.zAlxCryYZN PVD hard coatings // Surface and Coatings Technology № 114, 1999, pp. 187−199.
- Menzel S., Gobel Th., Bartsch K., Wetzig K. Phase transitions in PACVD-(Ti, A1) N coatings // Thin solid films. 1999. № 345, p.p. 263−269.
- Leoni M., Scardi P., Rossi S. et al (Ti, Cr) N and Ti/TiN PVD coatings on 304 stainless steel substrates: Texture and residual stress // Thin solid films, 1999, № 345, p.p. 187−199.
- Musil J., Karvankova P., Kasl J. Hard and super Zr-Ni-N nanocomposite films // Surface and Coatings Technology № 139, 2001, p.p. 101 109.
- Andersen K.N., Bienk E.J., Schweitz K.O., Reitz H., Chevallier J. Deposition, microstructure and mechanical and tribological properties ofmagnetron sputtered TiN/TiAIN multilayers // Surface Coating and Technology № 123, 2000, p.p. 219−226.
- Li T.S., Li H., Pan F. Microstructure and nanoidentation hardness of Ti/TiN multilayered films // Surface Coating and Technology № 137, 2001, p.p. 225−229.
- Kaelson L., Haltman L., Sundgren J.E. Influence of residual stresses on mechanical properties TiCxN! x // Thin Solid Films, 2000, № 371, p.p. 167−177.
- Патент США № 2 157 478 (1937).
- Патент США № 2 239 642 (1937).
- Патент США № 3 625 848 (1968).
- Патент США № 3 836 451 (1970).
- Патент Великобритании № 1 322 670 (1973).65. А.с. СССР № 284 883 (1969).
- А.с. СССР № 359 977 (Бюл. изобр. № 18, 1976).
- А.с. СССР № 367 755 (Бюл. изобр. № 18, 1976).
- А.с. СССР № 1 491 039 Беляев В. Н., Власов А. Д., Моляр А. Г., Петров JI.M. и др. Многслойное покрытие изделий из нержавеющих и конструкционных сталей
- Петров JI.M., Бецофен С .Я., Роняк Р.Н Формирование структуры многослойных ионно-вакуумных покрытий // Тезисы докладов научно-технич. конф. «Покрытия, упрочнение, очистка. Экологичеки безопасные технологии и оборудование», М., 1995, с.43−44.
- Богданович В.И., Барвинок В. А., Козлов Г. М. и др. Исследование износостойкости покрытий плазменного вакуумного напыления // Ракетно-космическая техника//М.: ЦМТИ «Поиск», 1985, сер. 8, вып. 1, с.11−16.
- Богданович В.И., Малкин В. И. Докукина И.А. Применение титана в узлах пар трения космических аппаратов // Проблемы машиностроения и автоматизации, 1998, № 2−3, с. 100−104.
- Богданович В.И., Снопов С. Г., Лебедев А. П. Износостойкость конструкционных материалов с тонкими покрытиями // Передовой технический опыт, 1986, № 3, с.46−48.
- Барвинок В.А., Богданович В. И., Цидулко А. Г. Опыт разработки и внедрения технологий напыления защитных покрытий // В кн.: Защитные покрытия в машиностроении, Киев: ИЭС им. Патона, 1987, с. 172−175.
- Богданович В.И., Малкин В. И. Исследование ионно-плазменной технологии для металлизации композиционных материалов // Вопросы авиационной науки и техники. Сер. Технология авиационного двигателестроения, 1989, вып.1, с.86−88.
- Богданович В.И., Плотников А. П., Корнилов В. Б. Исследование механизма возникновения отслаивающих напряжений в покрытиях // Вопросы специальной радиотехники. Сер. Теория и техника антенн, 1990, вып. 2(45), с.57−61.
- Богданович В.И., Барвинок В. А., Юмашева Т. Л. Перспективность разработок в области получения новых материалов методами вакуумной ионно-плазменной технологии // Рыночная экономика: Сб. науч. Трудов, Самара, 1998, с.448−453.
- A.c. № 1 737 933 Катодный узел 10.02.96.
- А.с.№ 2 061 787 Катодный узел электродугового испарителя 10.06.96.
- A.c. № 2 059 737 Электродуговой испаритель металлов 10.05.96.
- A.c. № 2 046 836 Способ локализации области перемещения катодных пятен вакуумной дуги на поверхности испарения протяженного катода 27.10.95.
- A.c. № 93 043 133/02 Установка для вакуумно-плазменной обработки изделий в среде рабочего газа. 31.08.93.
- A.c. № 2 001 972 Установка для нанесения упрочняющих покрытий методом электродугового испарения. 30.10.93.
- A.c. № 2 036 245 Способ химико-термической обработки изделий ионно-плазменным методом в среде реакционного газа. 27.07.95.
- A.c. № 2 026 414 Способ обработки изделий. 10.01.95.
- A.c. № 2 039 843 Способ комплексной обработки изделий. 20.07.95.
- A.c. № 2 037 599 Способ нанесения покрытий на изделия методом ионного распыления и устройства для его осуществления. 19.06.95.
- A.c. № 2 033 475 Способ вакуумного конденсационного нанесения покрытий. 20.04.95.
- A.c. № 2 037 558 Вакуумная печь. 19.06.95.
- A.c. № 2 026 431 Способ нагрева электропроводящих изделий в рабочей камере. 10.01.95.
- A.c. № 1 552 687 Электродуговой испаритель. 15.12.94.
- A.c. № 1 531 830 Электродуговой испаритель с магнитным управлением зоной испарения. 30.03.94.
- A.c. № 1 505 064 Электродуговой испаритель 15.12.94.
- A.c. № 93 044 940/02 Электродуговой испаритель ферромагнитных материалов. 10.09.93.
- A.c. № 2 001 159 Установка электродугового нанесения металлических покрытий в вакууме. 15.10.93.
- A.c. № 2 013 464 Способ комплексной обработки изделий. 30.05.94.
- Бабад-Захряпин A.A. Дефекты покрытий // М., изд. Энергоатомиздат, 1987, 152с.
- Петров JI.M., Чертов С. И., Ильин A.A., Назимов О. П. Исследование кинетики окисления* титанового сплава ТС-6 // В сб. тезисов научно-технической конференции молодых ученых и специалистов, М., 1983, с. 1.
- Петров JI.M., Чертов С. И., Ильин A.A., Назимов О. П. Исследование влияния газонасыщения на структуру и свойства листов изтитановых сплавов. // Тезисы докладов научно-методической конференции 25-летия СФМАТИ, Ступино, 1982, с. 2.
- Моляр А.Г., Мних В. Н., Ткаленко Д. А., Петров Л. М. Исследование методов очистки деталей под вакуумную обработку // Тезисы докладов отраслевой конференции «Прогрессивные технологические процессы и оборудование для термообработки», Тбилиси, 1988, с. 11.
- Спроул Роберт Л. Современная физика // М.: Наука, 1974, 86 с.
- Епифанов Г. И. Физика твердого тела // М.: Высшая школа, 1977,230 с.
- Царев Б.И. Контактная разность потенциалов // М. Гостехиздат, 1949−184 107. Черепин В. Т. Итоги науки и техники. Металловедение и термическая обработка // М., том 14, 1980, с. 19.
- Черепин В.Т., Васильев И. А. Методы и приборы для анализа поверхности материалов. Справочник // Наукова думка, 1982, с.ЗЗ.
- Грин М. Поверхностные свойства твердых тел // М.: Мир, 1972, с. 195.
- Кальницкий А.П., Файнштейн А. И. // Измерительная техника, № 5, 1980, с.56.
- С.М. Сарычев, А. И. Чернявский, JI.M. Петров, B.C. Спектор. Оценка энергетического состояния поверхности методом измерения контактной разности потенциалов. Научные труды МАТИ, в.5(77), 2004, с. 96−100.
- Бецофен С .Я., Петров JI.A. Особенности рентгеновского измерения остаточных напряжений в TiN тонких покрытиях // Изв. АН СССР. Металлы, 1991, № 1, с. 179−185.
- Ягодкин Ю. Д., Пастухов К. М., Миляева Е. В., Мубояджанян С. А., Будиновский С. А. Рентгенографическое исследование остаточных макронапряжений в защитных покрытиях для лопаток газовых турбин // МиТОМ, № 11, 1997, с. 30−34.
- Betsofen S.Ya., Petrov L.M. The Texture & Macrostress for Cutting Tool PVD Proceedings of the International Conference on Texture and Anisotropy Polycrystals // Clausthal, Germany, 1997, Edited by R.A. Schwarzer, p.p. 641 647.
- Betsofen S.Ya. Nondestructive X-ray methods of quality control for thin ceramic coatings // Refractory Metals & Hard Materials, v. 14, 1996, p.p.213−221.
- Manory Rafael R., Perry Anthony J. Some effects of ion beam treatments on titanium nitride coatings of commercial quality // Surface and Coatings Technology, № 114, 1999, p.p.137−142.
- Бецофен С.Я., Петров JI.M., Лазарев Э. М., Коротков Н. А. Структура и свойства ионно-плазменных TiN покрытий // Изв. АН СССР, Металлы, 1990, № 3, с. 158−165.
- Thomas A. Microhardness measurement as a quality control technique for thin, hard coatings // Surface Engineering, 1987, v.3, № 2, p. l 17.
- Бецофен С .Я. Исследование характеристик тонких керамических покрытий с помощью измерения микротвердости // Изв. РАН, Металлы, 1993, № 2, с. 181−186.
- Jehn Н.А., Kopacz U. Ultramikrohartemessungen an aufgestaubten hartstoffschichten // Proc. l 1th Plansee-Seminar, 1985, pp. 1−19.
- Бецофен С.Я., Петров Л. М. Прибор для неразрушающего определения толщины покрытий // Тезисы докладов научно-технической конференции «Покрытия, упрочнение, очистка. Экологически безопасные технологии и оборудование», М, 1995, с. 45.
- S.Y .Betsofen Film Thickness Measurements Make TiN Coatings Reliable // Advanced Coatings & Surface Technology, Technical Insights INC. Copyright, 1996, p.p.3−4.
- Петров Л.М., Лантух А. Ю. Некоторые аспекты поверхностных энергетических процессов, протекающих на катоде электродугового разряда вакуумных установок // Научные труды МАТИ-60 лет, вып. 3(75), изд. Латмэс, 2000., с. 61−65.
- Палатник J1.C., Фукс М. Я., Косевич В. М. Механизм образования и субструктура конденсированных пленок. М., Наука, 1972, с. 320.
- Петров JI.M., Бецофен С. Я., Дервук В. В. Формирование композиционных износостойких покрытий: состав, технология, состояние подложки, структура // Научные труды МАТИ, вып. 1(73), 1998, изд. Латмэс, с.67−71
- Петров Л.М., Сарычев С. М., Спектор B.C., Иванчук С. Б. Влияние ионного азотирования на процесс окисления титановых сплавов // Тезисы докладов Всероссийской научно-технической конференции «Новые материалы и технологии» (НМТ-2004), с. 82−83.
- Ильин A.A., Спектор B.C., Петров J1.M. Комплексная оценка обеспечения работоспособности титановых сплавов методами вакуумной, ионно-плазменной обработки // Авиац. пром., № 2, 2005, с.27−32.
- Бецофен С.Я., Петров JI.M., Сарычев С. М., Спектор B.C. Дифракционные методы исследования модифицированных поверхностных слоев титановых сплавов // Научные труды МАТИ, в.5(77), 2004, с. 14−18.
- Ильин A.A., Романовский Е. А., Бецофен С. Я., Петров J1.M., Спектор B.C., Серков М. В. Исследование структуры TiN покрытий методами ядерного обратного рассеяния протонов и рентгеноструктурного анализа // Металлы, 2005, № 2, с. 33−37.
- Ильин A.A., Плихунов В. В., Петров J1.M., Иванчук С. Б., Карпов В. Н., Соколов И. В., Федорова Т. В. Особенности подготовки поверхности титановых сплавов при вакуумной ионно-плазменной обработке // Авиационная промышленность, 2006, № 4, с. 23−26.
- Петров Л.М., Чернявский А. И., Сарычев С. М., Иванчук С. Б. Комплексная оценка качества формирования ионно-вакуумных покрытий и диффузионного модифицирования поверхности деталей и изделий машиностроения // Научные труды МАТИ, вып.5(77), 2002, с.85−90.
- ФУНДАМЕНТАЛЬНЫЕ И ПРИКЛАДНЫЕ ПРОБЛЕМЫ", 19−21 ноября 2003 года, Москва, Россия, с. 84−89
- Ильин A.A., Плихунов В. В., Петров Л. М., Иванчук С.Б., Гаврилов
- A.C., Спектор B.C. Вакуумная ионно-плазменная обработка конструкционных материалов авиационной техники // Авиационная промышленность, 2007, № 1, с. 31−34.
- Ильин A.A., Плихунов В. В., Петров Л. М., Иванчук С. Б., Сарычев С. М., Спектор B.C. Вакуумная ионно-плазменная поверхностная обработка и перспективы применения ее в машиностроении //Технология машиностроения, 2007, № 9, с.33−35.
- Ильин A.A., Плихунов В. В., Петров Л. М., Иванчук С.Б., Гаврилов
- A.C. Вакуумные ионно-плазменные технологии перспектива их применения в аэрокосмической технике // 5 Международный аэрокосмический конгресс IAC'06 Тезисы докладов, Москва, 27−31 августа 2006 г., с. 160−161.
- Ильин A.A., Петров Л. М., Иванчук С. Б., Карпов В.Н., Спектор
- B.C., Федорова Т. В. Газонасыщение титановых сплавов при вакуумной ионно-плазменной обработке Международная конференция «Ti -2006 в СНГ"21.24 мая г. Суздаль Россия, Киев, сб. докл., Наукова думка, 2006, стр. 301 305.
- Плихунов В.В., Петров JI.M., Матвеев Н. В., Иванчук С. Б., Гаврилов A.C., Аркусский Л. Ю., Никоноров А. Н. Установка для вакуумной ионно-плазменной обработки поверхностей, ПАТЕНТ 2 294 395.
- Плихунов В.В., Петров Л. М., Иванчук С. Б., Гаврилов A.C., Аркусский Л. Ю., Обознов В. В., Никоноров А. Н. Установка вакуумного ионно-плазменного нанесения покрытий, ПАТЕНТ 2 287 610.