Камеры сгорания газотурбинных двигателей: Математическое моделирование, методология расчета, концепция оптимального проектирования
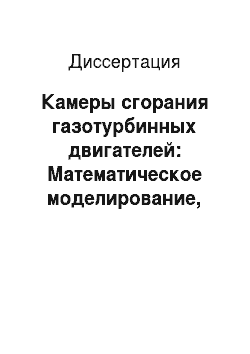
V 3.5 2.5 1.5 0.5 0.4 0.6 0.8 h ж Рис. 3.11. Зависимость величины недожога топлива от относительной длины зоны смешения струй прямого и циркуляционного потока во фронтовом устройстве. IV. Интегральный подход к математическому моделированию камеры егорания. IV.l. Представление о рабочем процессе в камере сгорания. Рабочий процесс в камере сгорания отличается многообразием одновременно протекающих… Читать ещё >
Содержание
- Основные обозначения
- I. Общая характеристика современного состояния проблемы и постановка задачи
- II. Принципы математического моделирования камеры сгорания для расчета характеристик рабочего процесса в ней с помощью предложенной автором критериально-параметрической функции
- III. Применение разработанных интегральных критериев и параметров к изучению и описанию характеристик процессов в камере сгорания газотурбинной установки
- III. I. Принципиальная схема камеры сгорания
- 111. 2. Характерные размеры и безразмерные геометрические критерии камеры сгорания
- 111. 3. Объемы реакционных зон камеры сгорания
- 111. 4. О минимальном поперечном размере камеры сгорания. ф III.5. Экспериментально-теоретическое обоснование выбора величины длины части жаровой е трубы до отверстий смесителя.'
- IV. Интегральный подход к математическому моделированию камеры сгорания
- IV. 1. Представление о рабочем процессе в камере сгорания
- IV. 2. Интегральная математическая модель камеры сгорания
- IV. 3. Анализ физической сущности критериев, определяющих рабочий процесс в камере сгорания
- Выводы к разделу III и IV
- V. Экспериментальное исследование камеры сгорания
- V. 1. Установки и стенды для испытаний камер сгорания
- V. 2. Методика проведения испытаний
- V. 3. Максимальные величины погрешностей при определении параметров в процессе испытаний камер сгорания
- V. 4. Метод обработки экспериментальных данных
- VI. Характеристики камеры сгорания как функции ее критериев
- VI. 1. Эмиссия оксидов азота
- VI. 2. Эмиссия оксидов углерода
- VI. 3. Эмиссия нес горевших углеводородов и бензопирена
- VI. 4. Уровень дымления камеры сгорания
- VI. 5. Взаимосвязь между единицами, характеризующими уровень токсичности газов на выходе из камеры сгорания
- VI. 6. Коэффициент полноты выгорания топлива
- VI. 7. Зависимость величин коэффициентов неравномерности поля температуры газа на выходе из камеры сгорания от ее критериев
- VI. 8. Зависимость величины коэффициента потерь полного давления в камере сгорания от значений ее критериев
- VI. 9. Тепловое состояние стенок жаровой трубы.,
- Выводы к разделу VI
- VII. Oco6eHHocTH применения интегрального подхода к исследованию нестационарных процессов в камере сгорания
- VII. 1. Процессы воспламенения и прекращения горения топливовоздушной смеси в камере сгорания
- VII. 1.1. Процесс воспламенения топливовоздушной смеси в камере сгорания
- VI. 1.1.2. Расчет величины медианного диаметра капель распыленного жидкого топлива на режимах запуска двигателя
- VII. 2. Процесс прекращения горения при обеднении и обогащении топливовоздушной смеси в камере сгорания газотурбинного двигателя
- VII. 3. Критерий стабильного течения потока газа в диффузоре камеры сгорания
- Выводы к разделу VII
- VIII. Физическое моделирование рабочего процесса в камере сгорания
- IX. Система уравнений для расчета характеристик камеры сгорания
- IX. 1. Система математических зависимостей характеристик камеры сгорания от ее критериев
- IX. 2. Анализ влияния критериев на характеристики камеры сгорания
- IX. 3. Оптимальные значения критериев камеры сгорания
- X. Концепция проектирования камеры сгорания газотурбинного двигателя
- X. 1. Анализ технических требований к газотурбинным двигателям
- X. 2. Совершенная конструкция камеры сгорания в зависимости от назначения двигателя
- XI. Практическое применение интегральной математической модели камеры сгорания
- Основные результаты работы
Камеры сгорания газотурбинных двигателей: Математическое моделирование, методология расчета, концепция оптимального проектирования (реферат, курсовая, диплом, контрольная)
В данной работе обоснован интегральный подход к изучению и математическому описанию характеристик потока движущейся сплошной среды при наличии развитых турбулентных пульсаций с источниками тепла и вещества по каналу переменной геометрии. Показано, что этот подход имеет важное прикладное значение для решения технических задач, связанных с проектированием аппаратов, в которых происходят молекулярные, конвективные, турбулентные тепло-массообменные процессы (к таким аппаратам, например, относятся камеры сгорания газотурбинных установок, подогреватели котлов и т. п.).Хотя, общепризнанным является тот факт, что основной задачей науки, изучающей закономерности процессов, происходящих в сплошной среде, является определение параметров (характеризующих состояние среды) в любой момент времени и в каждой точке пространства, занимаемого этой средой, однако, такой подход не позволяет решать технические задачи, связанные с проектированием. Параметры среды в любой точке занимаемого ею пространства можно (с какой-либо степенью достоверности) определить при наличии информации о фаничных условия и размерах проточной части канала. Однако такая задача в данной постановке создает известную долю неопределенности для разработчика аппарата, так как конечный результат заранее неизвестен. Для проектирования, с точки зрения автора, рациональной является иная постановка задачи: задав характеристики потока сплошной среды на выходе из канала переменной геометрии, определить их формирующие размеры проточной части канала. При этом необходимо выявить функциональную взаимосвязь параметров потока от критериев, характеризующих размеры пространства, ограничивающие этот поток (размеры проточной части). Универсальность такой взаимосвязи может быть обоснована на базе физических* представлений о происходящем процессе, подтвержденных математически и экспериментально. Автором накоплен большой экспериментальный материал по испытаниям камер сгорания газотурбинных двигателей различных схем и размерностей. Современные тенденции развития теории камер сгорания свидетельствуют о приоритетном направлении поиска решения «основной задачи гидроаэромеханики» применительно к горению в движущемся потоке сплошной среды (газа) методами численного решения системы дифференциальных соотношений, характеризующих состояние среды в сколь угодно малой области пространства, занимаемой этой средой [42, 46, 60, 69, 72, 88, 94, 99]. Несмотря на развитие вычислительной техники, облегчающей процесс расчета и совершен/-.твование численных методов, из-за сложной взаимосвязи протекания микро и макропроцессов, самой сложности этих процессов в камере сгорания, требуются определенного рода допущения, упрощения, эмпирические поправки, что, в конечном итоге, заставляет отходить от концепции «точного» решения. Для совершенствования этих методов, так или иначе, необходимо проведение испытаний, подтверждающих достоверность расчетов для различных конструкций камеры сгорания. Практическое использование таких методов в настоящее время требует нахождения поправочных коэффициентов, вводимых в расчет для конкретной конструкции камеры сгорания [60,72]. Но, такие способы позволяют анализировать тенденции протекания процессов в камере сгорания. Развитие данного направления позволяет предположить, что в обозримом будущем электронные вычислительные машины заменят собой установки и стенды для экспериментальной доводки камер сгорания. Однако, данное направление можно охарактеризовать термином — «поверочная» методология. Несмотря на постоянное совершенствование и развитие теории камеры сгорания, отсутствие математических зависимостей характеристик протекающего в ней процесса от величин интегральных критериев, определяющих геометрию камеры сгорания, заставляет проектировщиков (как в России, так и за рубежом) при ее разработке традиционно выбирать конкретный прототип ранее отработанной конструкции. Из всех интегральных критериев камеры сгорания, наиболее используемых в настоящее время на этапе проектирования, можно назвать «критерий форсирования» [24,46], в который входит конструктивный параметр — величина объема камеры сгорания. Поэтому, метод создания камер сгорания для проектировщика как в случае «физических», так и «электронных» испытаний можно классифицировать терминологией — «метод проб и ошибок» — проектирование по прототипу. Следующим шагом в развитии теории камер сгорания, по мнению автора, явилась бы разработка универсальной математической модели камеры сгорания, как функции ее геометрических, гидродинамических, термодинамических и теплофизических критериев, позволяющей описать все характеристики рабочего процесса в ней. Наличие такой модели обозначит развитие методологии «целенаправленного» проектирования конструкции, суть которой состоит в том, что по заданным характеристикам рабочего процесса в камере сгорания определяются размеры ее проточной части.15 ' Совместное развитие двух вышеупомянутых направлений — «поверочного» метода и методологии «целенаправленного» проектирования, качественным образом сократит трудоемкость процесса создания камеры сгорания, сведя ее лишь к доводке, не выходящей за рамки изменений размеров конструкции «на бумаге». Представленная работа посвящена развитию метода «целенаправленного» проектирования конструкции камеры сгорания. Наличие большого экспериментального материала по испытаниям камер сгорания в сочетании с использованием положений, полученных в результате анализа и математического преобразования фундаментальных уравнений газовой динамики и тепломассообмена в сплошной движущейся среде, создает предпосылки для успешного решения поставленной автором задачи. '• II. Принципы математического моделирования камеры сгорания для расчета характеристик рабочего процесса в ней с помощью предложенной автором критериально-параметрической функции. Для решения поставленной в работе задачи, с точки зрения автора, целесообразно искать систему функциональных связей следующего вида: Zi<(>)f (Xij, Yij) — (II.1) где Zi — значение критерия или параметра, интегрально характеризующего протекание рабочего процесса в камере сгорания (например, коэффициент полноты сгорания топлива, индекс эмиссии загрязняющего вещества, коэффициент избытка воздуха при воспламенении топливовоздушной смеси или прекращении ее горения, максимальная величина температуры стенки и т. п.) — Xij — значение критериев и параметров, характеризующих режим работы двигателяYij — значение критериев и параметров, характеризующих геометрию проточной части камеры сгорания. Знаки неравенств будут использованы в дальнейшем для исследования нестационарных процессов воспламенения топливовоздушной смеси, прекращения ее горения и при исследовании влияния стабильности течения газа в диффузоре камеры сгорания на стабильность величины коэффициента максимальной окружной неравномерности поля температуры газа на входе в сопловой аппарат турбины (знак равенства используется для описания характеристик стационарного процесса).Назовем систему функциональных зависимостей (II. 1), преобразованных к определенным математическим зависимостям, позволяющим рассчитать величины Zi для любой и конструкции и любого режима работы — «интегральной математической моделью камеры сгорания». Ххарактерный размер реакционного объема, источников или стоков энергии и веществаW — интенсивность закрутки потока газаG^p — отношение массовых расходов примеси (топлива) в струе к расходу газа в струе. По мнению автора, функция этих критериев позволит описать процесс формирования характеристик рабочего процесса в камере сгорания, в которой он определяется не только скоростью протекания химических реакций окисления горючего, но и процессами испарения топлива (для жидкого топлива), процессами смешения топливных и воздушных, горячих и холодных потоков — т. е. тепломассообменными процессами. В следующем разделе, представлен анализ вышеназванных критериев для конструкции камеры сгорания газотурбинного двигателя. III. Применение разработанных интегральных критериев и параметров к изучению и описанию характеристик процессов в камере сгорания газотурбинной установки. III.1. Принципиальная схема камеры сгорания. Принципиальная конструктивная схема камеры сгорания газотурбинного двигателя представлена на рис. 3.1. Воздух из компрессора по специально спрофилированным каналам поступает внутрь замкнутого объема, образованного стенками обечайки, называемого «жаровой» или «пламенной» трубой. Внутри этого объема происходит процесс химического реагирования топлива и воздуха (горение). За счет превращения химической энергии топлива в тепло, температура воздуха повышается, который, выходя из камеры сгорания, совершает работу в турбине и выходном устройстве двигателя. Топливо Воздух I • ^ t Газ Рис. 3.1. Принципиальная схема камеры сгорания. III.2. Характерные размеры и безразмерные геометрические критерии камеры сгорания. Проанализируем критерии и параметры2″, 1р, 'SF^ Ч ^ т Л, l, W, G"p, входящие в функцию (1.17) (см. Приложение 1 — раздел 1.7) для конструкции проточной части камеры сгорания газотурбинного двигателя.8) dj^ - медианный диаметр капель распыливаемого форсункой топлива. Интенсивность закрутки газового потока в жаровой трубе камеры сгорания будем характеризовать отношением величины тангенциальной W составляющей скорости к осевой — — -^в кольцевой закрученной струе на выходе завихрителя фронтового устройства (рис. 3.4).Условие сохранения тангенциальной составляющей скорости в закрученной струе: = const. или: W, R = const, (III.l) где W, — тангенциальная составляющая скорости, Rтекущий радиус. Тангенциальная составляющая скорости может быть выражена через скорость на выходе из межлопаточных каналов завихрителя W^^ (рис. 3.4): W,=W, sm (p^, (III.2) К где Rj^ - радиус, проходящий через центры тяжести межлопаточных каналов, ^ -угол наклона лопаток к оси на выходе из завихрителя (рисЗ.4).Из уравнения неразрывности: К=^^ (Ш.З) где Fj — объемный расход воздуха через завихритель, Fj^ - площадь на выходе из межлопаточных каналов завихрителя. Объемный расход воздуха через завихритель равен: V,=M^Rs" J^^, (Ш.4) где // - коэффициент расхода через завихритель, R^ -наружный радиус завихрителя (рис. 3.4), АРперепад давления на отверстиях жаровой трубы. Подставим (Ш.З) с учетом (III.4) в (III.2): W, = M—^sm (p-^. (III.5) TuR. Rj, .Комплекс —^—^sin^- есть геометрическая характеристика завихрителя, обозначаемая, А и выведенная таким же образом для центробежной форсунки в [1,4]. Геометрическая характеристика завихрителя является конструктивным критерием подобия. Площадь поперечного сечения турбулентной струи с примесью обозначим через F^, где F^ - определим как элемент площади поперечного сечения жаровой трубы, на который приходится расход топлива через форсунку. К объемам реакционных зон камеры сгорания отнесены следующие: — объемы, в которых происходит формирование газодинамических параметров потока воздуха перед поступлением его внутрь объема жаровой трубыдля камеры сгорания таким объемом является объем диффузора — Уд (подробнее об особенностях течения газа в объеме диффузорасм. раздел о нестационарных процессах в камере сгорания) и объем кольцевого канала камеры сгораниядля этих объемов массовая скорость химической реакции —Wp=0- - объем жаровой трубы, где происходит процесс химического реагирования топлива и воздуха с температурой, имеющей величину >1800Ктаким объемом является объем части жаровой трубы до последнего ряда отверстий в ее боковых стенках — Узг ', для этого объема характерным является максимальное значение скорости протекания химических реакций, максимальная интенсивность образования NO2 и выделения углерода в местных «переобогащенных» топливом зонах- - весь объем жаровой трубы до сечения входа в сопловой аппарат турбины — Уж', во всем объеме жаровой трубы происходят процессы окисления топлива и продуктов его недожога до конечных продуктов реакции — СО2- Н2ОNOx (iVO^ является продуктом окисления N02) объем газосборника жаровой трубы, равный разности величин ¥-ж Узг — в этом объеме происходят процессы окисления углерода, образовавшегося в местных «переобогащенных» топливом зонах Узг и процессы выравнивания температурной неравномерности по длине объема газосборника. («IIL4. О минимальном поперечном размере камеры сгорания. В настоящее время проявляется большой интерес, как в авиации, так и в энергетике к двигателям малой размерности, включая микродвигатели. Для двигателей малой размерности характерно применение центробежных компрессоров с противоточной камерой сгорания, расположенной над турбиной. Анализ показывает, что противоточные камеры сгорания малоразмерных двигателей обеспечивают более равномерное поле температуры газа при более низких потерях по сравнению с прямоточными камерами сгорания. Это объясняется большой конфузорностью и длиной газосборника жаровой трубы и малыми значениями приведенной скорости Х^ за компрессором. В камерах сгорания двигателей малой размерности существенно уменьшается высота жаровой трубы, что однозначно приводит к увеличению площади боковой поверхности жаровой трубы 8ж относительно ее объема. Как показывает опыт, увеличение относительной площади поверхности жаровой трубы отрицательно влияет на тепловое состояние стенки жаровой трубы А^ =Т^-Т^ (Гмаксимальная температура стенки жаровой трубы) и может W «' приводить к снижению эффективности горения. Как следует из графика, наибольшие трудности возникают с охлаждением малоразмерных, особенно противоточных камер сгорания с большим отношением поверхности жаровой трубы к ее объему. Изменение знака градиента функции А/ = / (изображенной на графике рис. 3.6), начиная с величины —^ = 85 м, связано с уменьшением ж W> коэффициента полноты тепловыделения в камере сгорания. Исследования, подтвержденные опытами, включая эксперименты других авторов, показывают, что при этом, из-за снижения температуры газа в реакционной зоне, в связи с интенсивным отводом тепла в стенку, уменьшается скорость химических реакций и увеличивается недожог топлива. Так как максимальная температура стенки жаровой трубы определяется допустимым значением для материала и примерно одинакова для всех камер, то из формулы (III. 19) следует, что для двигателей малой размерности существует ограничение по величине температуры воздуха за компрессором (т.е. по степени повышения давления) из условий теплового состояния стенки. Для камеры сгорания -^^ {h^)'^.На графике рис. 3.7 показана зависимость высоты жаровой трубы от величины отношения —^, полученная статистической обработкой результатов расчета отношений площади поверхности жаровой трубы к ее объему для различных конструкций кольцевых камер сгорания. Из графика на рис. 3.6 и 3.7 следует, что минимально допустимым значением /гж для кольцевой камеры сгорания является {h^)mm 0,045 м. Указанные выше ограничения касаются камер сгорания с металлическим материалом стенок жаровой трубы. Как следует из приведенного анализа, применение керамических материалов, уменьшающих потери тепла из зоны реакции, позволит расширить минимальное ограничение поперечного размера жаровой трубы. I1I.5. Экспериментально-теоретическое обоснование выбора величины длины части жаровой трубы до отверстий смесителя. При проектировании жаровой трубы камеры сгорания важным является правильный выбор расстояния, на котором расположены отверстия для подвода воздуха в зону смешения. С одной стороны, слишком близкое расположение отверстий к фронтовому устройству, т. е. к зоне стабилизации пламени может привести к быстрому «замораживанию» химических реакций окисления топлива. С другой стороны, объем реакционной зоны образования оксидов азота возрастает с увеличением расстояния от торцев форсунок до отверстий подвода воздуха в зону смешения, что приводит к повышению концентрации оксидов азота в продуктах сгорания. Процесс выгорания топлива в жаровой трубе камеры сгорания определяется аэродинамической структурой потока, формируемой конструктивными элементами ее проточной части, например, завихрителем фронтового устройства, создающим зону стабилизации пламени, где происходит наиболее интенсивное протекание химических реакций и процессов тепломассообмена между закрученной струей воздуха, горячими продуктами сгорания (в зоне рециркуляции) и топливом. Аэродинамическую структуру потока закрученной струи воздуха и обратного тока рассмотрим с точки зрения теории смешения турбулентных струй. Соотношение (III.23) показывает, что длину зоны смешения закрученных струй прямого и обратного токов определяют интенсивность крутки W и отношение —-.К На рисунке 3.10 изображена зависимость относительной длины смешения закрученной струи воздуха с газами в зоне обратного тока от интенсивности крутки воздушного потока, рассчитанная по формуле (III.23) для —^ = 0,38 (среднестатистическая величина) и —- = 0,19 (минимальная величина изж реализованных конструкций). Коэффициент А, входяп).ий в формулу (III.23) и характеризующий турбулентность потока, выбран в соответствии с рекомендациями в [52]. На рисунке 3.11 изображен график, построенный на основании данных экспериментальных исследований, где по оси ординат отложены значения величины недожога топлива 1 — тотнесенные к ее минимальному значению. По оси абсцисс — величина относительной длины зоны смешения струй прямого и обратных токов, рассчитанная по (III.23). Из рисунка видно, что минимальный недожог топлива достигается при — = 0,8 ч-1,0. Величина этой относительной К длины является минимально допустимой для расположения отверстий в боковых стенках жаровой трубы.1 — форсунка, 2 — завихритель, 3 — камера предварительного смешения. Н^{м) 0.3 0,25 0,2 0.15 0.1 0,05 О О 10 20 30 40 50 60 70 80 90 100 S яс яс (м-) Рис 3.7. Зависимость высоты жаровой трубы от величины площади ее относительной поверхности для камеры сгорания газотурбинного двигателя.Рис.3.8. К расчету длины зоны смешения закрученного завихрителем потока воздуха с продуктами сгорания рециркуляционной зоны.Рис.3.9. Схема взаимодействия зон прямого и обратного тока в завихрительном фронтовом устройстве. i w Рис. 3.10. Зависимость относительной длины смешения струй прямого и обратного тока от интенсивности крутки потока воздуха на выходе из завихрителя. 1 ^=0,38, 2 —^=0,19 Ж Ж.
1-V 3.5 2.5 1.5 0.5 0.4 0.6 0.8 h ж Рис. 3.11. Зависимость величины недожога топлива от относительной длины зоны смешения струй прямого и циркуляционного потока во фронтовом устройстве. IV. Интегральный подход к математическому моделированию камеры егорания. IV.l. Представление о рабочем процессе в камере сгорания. Рабочий процесс в камере сгорания отличается многообразием одновременно протекающих и взаимосвязанных физико-химических превращений в турбулентном потоке газа со сложной аэродинамической структурой. Рисунок 4.1 графически иллюстрирует представления о физических явлениях, происходящих в камере сгорания. Изображенная на рисунке схема является моделью физических процессов в камере сгорания. Модель построена на основе теоретического анализа явлений с помощью разработанного в предыдущих разделах интегрального подхода и полученных в результате критериев и параметров. Критерии и параметры определяют характеристики потока сплошной среды на выходе из рассматриваемого объема, с учетом интенсивности внутренних молекулярных превращений, молекулярных и молярных процессов обмена энергией, веществом, количеством движения, процессов выравнивания неоднородностей среды в пространстве этого объема и скорости переноса этих процессов потоком сплошной среды от входа к выходу из объема камеры сгорания (рис. 4.1). IV.2. Интегральная математическая модель камеры сгорания. На основании изложенного в Приложении 1 материала по преобразованию дифференциальных уравнений переноса энергии, концентрации и количества движения в неразрывном потоке сплошной среды с развитыми турбулентными пульсациями при наличии стоков и истоков теплоты и массы и анализа полученных критериев применительно к камере сгорания газотурбинной установки, представленного в разделе III, определены основные критерии и параметры, определяющие формирование характеристик рабочего процесса в камере сгорания. Величины температуры и давления определяют скорость химического реагирования веществ в потоке газа и образования конечного продукта реакции, так как она зависит от скорости движения молекул реагирующих веществ и частоты их соударений. Скорость движения молекул пропорциональна квадратному корню значения температуры, а длина свободного пробега молекул обратно пропорциональна величине давления газа. Таким образом, скорость движения молекул и частота их соударений определяются значениями температуры и давления газа. Физико-химические параметры: вид топлива и коэффициент избытка окислителя определяют выделяющуюся при химическом реагировании окислителя и горючего энергию. От вида топлива также зависит скорость его дробления на капли, испарение, диффузия в движущемся потоке газа, т. е. местные величины концентраций, определяющих местное значение скорости протекания химической реакции. Гидродинамический параметр G/Vp характеризует скорость конвективноГО переноса энергии, вещества и количества движения. Размерность параметра такая же как и у массовой скорости образования или расходования вещества в результате химической реакции в единице, объема. С ростом величины G/Vp возрастает «вынос» из реакционного объема энергии, вещества и количества движения, что приводит к снижению температуры, концентрации конечного продукта реакции и росту величины потерь полного давления в этом объеме. Универсальность параметра подтверждается практикой успешного обобщения экспериментальных данных по характеристикам горения как в России, так и за рубежом с помощью параметров, содержащих G/Vp (критерий Дорошенко, Лонгвелла, Лефевра и др.). «' F Степень расширения диффузора камеры сгорания ^^ характеризует стабильность течения потока воздуха на входе в реакционный объем жаровой трубы. При большой степени расширения и малой длине диффузора могут возникать отрывы пограничного слоя с последующим вихреобразованием попеременно то от внутренней, то от наружной стенок, в разных местах по окружности кольцевого диффузора. Отрыв пограничного слоя от стенок происходит под воздействием положительного градиента давлений. Такая нестабильность течения воздуха является причиной значительного изменения температуры стенок жаровой трубы и неравномерности поля температуры газа на входе в сопловой аппарат турбины. F Практика показала [39], что при —^ < 2 удается обеспечить стабильное протекание процессов в камере сгорания, независимо от того безотрывное или отрывное течение воздуха в диффузоре (подробнее о процессе нестабильного течения газа в диффузоре — см. раздел о нестационарных процессах в камере сгорания) Критерии ^— и ^— отражают протекание в камере сгорания таких процессов как проникновение струи в сносящий поток газа с учетом угла наклона этой струи к направлению сносящего потока. F Параметр ^—характеризует аэродинамику процесса смешения холодных струй с горячим потоком и определяет снижение местных максимальных температур газа. Для примера рассмотрим процесс втекания одиночной струи воздуха перпендикулярно сносящему Потоку горячего газа (рисунок 4.2).Обозначим: y = hглубина проникновения струи воздуха в сносящий поток на длине х = 1 (Рис. 4.2) — VQ — скорость воздуха в отверстиях жаровой трубыMf — скорость потока газа в жаровой трубе. Глубина проникновения струи в сносящий поток газа зависит от отношения скоростей потока в струях, которое определяет параметр —, так как ож F V '•ж0 Запишем выражение для потока импульса через поперечное сечение втекающей в объем жаровой трубы через ее бо1? овую стенку струи в виде: где v, dтекущая скорость на оси струи и текущий диаметрх^ - координата, отсчитываемая вдоль оси струи. Примем, что вертикальная составляющая импульса постоянна вдоль струи: v^f{x^) COS 0 = const- 2 w 2 const V fM =—^- COS^ где-угол между касательной к траектории оси и вертикалью. После интегрирования получаем уравнение траектории струи: Из этого выражения следует, что отклонение оси втекающей струи воздуха определяется ее начальным диаметром и отношением скоростных напоров ри потоков —Y. Величина угла 9 определяет глубину проникновения струи в сносящий поток (Рис. 4.2). Увеличение скоростного напора втекающей струи воздуха уменьшает угол в, а следовательно увеличивает глубину ее проникновения в набегающий поток. Проанализируем, как в случае параллельного втекания струи воздуха в горячий поток газа (истечение воздуха через щели охлаждения жаровой трубы) F параметр •=-^— влияет на процессы смешения. Рассмотрим истечение плоской, ограниченной с одной стороны струи воздуха, имеющей начальную скорость UQ В поток горячего газа, движущегося со скоростью щ в ту же сторону, что и воздух (рисунок 4.3).Обозначим:Z)oначальная ширина струи воздухаНначальная ширина горячего потока газаb^ -текуш-ая координата зоны смешения струи воздуха с потоком газа, отсчитываемая от плоскости начального разделения потоков (рисунок 4.3) — / - координата внешней границы зоны смешения, отсчитываемая вдоль оси х. Параметр W характеризует интенсивность процессов смешения, определяющих уровень местной температуры в потоке газа. Значительно улучшить смесеобразование и смешение потоков на меньшей длине в зоне горения позволяют закрученные струи, формируемые завихрителем фронтового устройства. Течение в закрученной струе можно разделить на область прямого и обратного токов, между которыми происходит интенсивный турбулентный обмен. Область обратных токов несет к фронтовому устройству горячие продукты сгорания и обеспечивает стабилизацию пламени. При увеличении параметра W происходит более интенсивное выравниваif ние концентраций реагентов и температуры в зоне взаимодействия прямого и обратного тока в кольцевой закрученной струе воздуха. Для камеры сгорания газотурбинного двигателя характерно комбинированное использование закрученных (завихритель фронтового устройства), поперечных (отверстия для подачи воздуха в стенках жаровой трубы), параллельных (щели пленочного охлаждения стенок жаровой трубы) струй. Параметр —— характеризует равномерность распределения концентрации топлива по всему сечению жаровой трубы. При бесконечно большом количестве форсунок топливовоздушная смесь становится однородной. Проанализируем влияние отдельных конструктивных особенностей горелочных устройств (воздушный завихритель и топливная форсунка) камеры сгорания на процессы смешения топлива с воздухом в ее реакционных объемах. Значения критериев Вебера, Лапласа, критерия М при 5^^ = const на установившихся режимах работы двигателя для конкретной конструкции форсунки зависят только от термодинамических параметров — Р}^, Тк, Т, а и вида топлива. На основании выведенной автором критериально-параметрической функции и анализа конструктивных схем камер сгорания: 1. Обоснованы критерии и параметры, определяющие рабочий процесс формирования характеристик потока газа в камере сгорания газотурбинного двигателя.2. Произведен анализ физической сущности каждого из критериев и параметров камеры сгорания.3. Представлена схема физического процесса в камере сгорания газотурбинного двигателя, иллюстрирующая представление о происходящих в ней физико-химических явлениях.4. Определены „граничные условия“ — минимально допустимая высота жаровой трубы для металлического материала стенок и минимально допустимая длина от завихрителя воздуха фронтового устройства до отверстий поперечного подвода струй воздуха в объем жаровой трубы.Рис.4.1. Модель физического процесса в камере сгорания. Явления пространственного переноса массы, тепла, количества движения в потоке с горением.Парат.тетры кокструицш ВХОД КАМЕРА СГ0РАШ1Я 6F/Fi^-WГидродикат.шческий критерии и параг. тйтры ^1%2G/f-(Sc^r) G/r Тер1<�юдпкз1,шческпе и тегатофизическиа парат. тетры К К, а Б11Д топлива Процессы пространстненкого турбулентного ст. гешеши ПОТОИОЕ (т.годепь зурбупентиостк для KSJitepH сгорания'! турбулентная гш44|узия1 турбулентная ЕДКОСТЬ турбулентная теплопроводность Дробление капель топшаа Молекулярная диффузия Молекулярная БЯЗВОСТЪ Молекулярная теплопроводность Скорость кга11ИЧйСЕ0Й реакции Испарение Влияние на скорость протекания т. хакрои т.шкропроцессоЕ неравколтерности распределения napaiiteTpoE по o6-bei, iaiit каракгернык зонкаг. теры сгорания Скорость протекания т. такропроцессоЕ Скорость протекания т. тюфопроцессоЕ ВЫХОД Характеристики рабочего процесса Б каг. хере сгорания Скорость переноса т, 1атерш{ Рис. 4.2. Схема втекания струи воздуха перпендикулярно сносящему потоку. Экспериментальное исследование характеристик рабочего процесса в камере сгорания проводилось на стендах при автономных испытаниях в составе специальных установок для испытаний как моделей, так и полноразмерных камер сгорания. На стендах для автономных испытаний исследовались такие характеристики как неравномерность поля температуры газа на выходе из камеры сгорания, величина коэффициента полноты выгорания топлива в ней, коэффициент восстановления полного давления (при „холодной продувке“), коэффициент избытка воздуха при „бедном“ срыве пламени, эмиссионные характеристики и характеристики запуска в различных высотно-климатических условиях (термобарокамера).На рис. 5.1 представлена схема стенда с установкой для автономных испытаний камер сгорания и их моделей, на рис. 5.2 — схема термобарокамеры, позволяющей имитировать различные высотно-климатические условия с установкой для исследований нестационарных процессов воспламенения топливовоздушной смеси в камере сгорания, Стендовая система включает в себя: — устройство для подвода или отвода (эксгаустер барокамеры) воздуха — компрессор, баллоны высокого давления, при испытаниях моделей также используется воздух от заводской сети- (# - газовый или электрический подогреватель воздуха- - рессивер- - выхлопная шахта. Установка для испытаний камер сгорания состоит из следующих конструктивных элементов: — входного устройства, с плавным входом и участком для измерения параметров потока газа на входе в камеру сгорания, стыкуемого к фланцу модуля камеры сгорания- - испытываемого модуля камеры сгорания- - выходного устройства с установленными в нем (в зависимости от цели проводимых работ) средствами измерений — термопарами, насадками для измерения полного давления, пробоотборниками. На двигательных стендах исследовались такие характеристики камеры сгорания как неравномерность поля температуры на входе в сопловой аппарат турбины и эмиссионные характеристики. В данной работе использованы также данные по измерению эмиссии, которое проводилось в составе объекта. V.2. Методика проведения испытаний. Методика проведения автономных испытаний камеры сгорания обеспечивает определение всех характеристик рабочего процесса в ней. В процессе испытаний производится измерение следующих параметров: — на входе в камеру сгорания — величин давления, температуры, массового расхода топлива, определение массового расхода воздуха- - на выходе из камеры сгорания — величин температуры, давления потока и химического состава газа в различных точках поперечного сечения (многоточечные гребенки термопар, насадки полного давления, пробоотборники, устанавливаемые как стационарно, так и с организацией непрерывного перемещения в плоскости поперечного сечения камеры сгорания).При исследовании нестационарных процессов — запуска и прекращения горения фиксируются параметры на входе в камеру сгорания в момент воспламенения или погасания топливовоздушнои смеси в камере сгорания. Момент воспламенения или погасания определяется по показаниям термопар в выходном сечении камеры сгорания. V.3. Максимальные величины погрешностей при определении параметров в процессе испытаний камеры сгорания. Максимальные погрешности измеряемых параметров в процессе проведения испытаний камеры сгорания представлены в таблице I. Таблица I.Погрешности измерения давления газа Погрешности измерения температуры Погрешности измерения массового расхода жидкого топлива Погрешности определения массового расхода газа Погрешности измерения концентрации в продуктах сгорания конечных и промежуточных продуктов реакции NO^, CO^, H^O, HC, C ±0,5% измеряемого значения ±1% верхнего предела измеряемого значения ±0,5% измеряемого значения ±0,7% расчетного значения в соответствии с ГОСТ 17.22.04−86 V.4. Метод обработки экспериментальных данных. Удобство такого способа заключается в том, что он дает возможность учесть вид функции (линейная, квадратичная, степенная, экспоненциальная и т. п.) влияния каждого фактора с точки зрения его физической сущности на протекание процесса. Для выявления вида функции влияния и степени значимости каждого фактора использованы способы: 1) графического представления экспериментального материала построением зависимостей в координатах: значение характеристики камеры сгорания — [величина критерия, определяющего характеристику] 2) метод „случайного баланса“, в котором производится оценка величины изменения характеристики камеры сгорания при изменении каждого из критериев от минимального до максимального значения, реализуемого в ходе эксперимента. # стендовая магистраль подвода воздуха к камере сгорания установка средств для измерения характеристик рабочего процесса на выходе из камеры сгорания, газовый или электрический подогреватель рессивер измерение параметров потока газа на входе в камеру сгорания выхлопная шахта стенда Рис5.1. Схема стенда с установкой для автономных испытаний камер сгорания. Измерение давления и температу1зы возд^оса в термобарокамере. Измерение расхода Подвод воздз’ха через камеру топлива сгорания Объект испытаний Измерение температуры Камера сгорания газа на выходе из камеры сгорания Подвод BosfljTca от т>рбодетандера Измерение давления топливоподачи н температ>фы топлива Рис. 5.2. Схема стенда с установкой для проверки запуска камеры сгорания. „' VI. Характеристики камеры сгорания как функции ее критериев. VI.1. Эмиссия оксидов азота. Автором выполнен большой объем исследований камер сгорания с фронтовыми устройствами, охватывающими широкий спектр типовых и перспективных конструкций (завихрительные, аэрационные, микрофакельные, комбинированные) как на газе, так и на жидком топливе, с высоко — и низконапорной подачей топлива. Схема испытанных фронтовых устройств представлена на рис, 6.1.Исследования проводились на моделях и полноразмерных камерах сгорания в условиях автономных испытаний, испытаний двигателей на стендах, на летательных аппаратах и на автономных газотурбинных электростанциях. Испытано более 30-и вариантов фронтовых устройств (включая серийные конструкции) и проведено более 300 экспериментов в рабочем диапазоне режимов двигателей: Рк0, 4 — 2,1 МПа- 7^=300 — 820 КГг=600 — 1700 КТ^ - температура газа на выходе из камеры сгорания. Обработкой экспериментального материала получено: для жидкого топлива (керосин, дизельное топливо): Е1,^=943,6Р, (G У Т (Т ехр зг J 288. Размерности в формулах (VI. 1) и (VL2): Давление — МПатемпература — Кплощадь — мобъем — м — массовый расход — кг /сек.Для образования NOx характерным является объем зоны горения, т. е. область высокой температуры газа. При этом 'длина зоны горения равна расстоянию от среза топливной форсунки до отверстий смесителя, где происходит „замораживание“ химических реакций образования NOxТочность расчета по приведенным формулам представлена на рис. 6.2, откуда следует удовлетворительная сходимость расчетных и экспериментальных данных. VI.2. Эмиссия оксидов углерода. Индекс эмиссии бензо-(„)-пирена связан с индексом эмиссии несгоревших углеводородов следующей зависимостью: Сопоставление расчетных и экспериментальных данных по эмиссии несгоревших углеводородов представлено на рис. 6.3. VI.4. Уровень дымления камеры сгорания. Уровень дымления газов на выходе из камеры сгорания принято оценивать по величине уменьшения отражательной способности бумажного фильтра (в %) при пропускании через него пробы газа определенного объема. Объемом реакционной зоны, определяющей содержание сажи в газах на выходе из камеры сгорания, является объем газосборника жаровой трубы. Насыщение газа кислородом с выгоранием чабтиц углерода происходит в объеме газосборника, равном разности объемов жаровой трубы и зоны горения. При этом функции Рк? Тк и Гг учитывают как химические процессы окисления сажи в газосборнике жаровой трубы, так и физические процессы ее образования в зоне горения. f Точность расчета по приведенной формуле иллюстрируется графиком на рис. 6.4. VI.5. Взаимосвязь между единицами, характеризующими уровень токсичности газов на выходе из камеры сгорания. Взаимосвязь размерностей, выражающих количество загрязняющего вещества в миллионных частях массы пробы [ррт] и концентрации в [мг/м^] описывается соотношениями: NO^ [ppm] = — • СО [ppm] = ЯС[ррт] = 2,05 СО [мг/м'] 1,25 НС [мг/м'] ' 0,715 f VI.6. Коэффициент полноты выгорания топлива. После преобразований, учитывая, что GQIGJ мало, выражение для описания связи полноты сгорания топлива с индексами эмиссии СО и НС можно представить в виде: -т] = {Е1,+0,2Ъ2Е1,) — В такой форме это уравнение приведено в [46]. VI.7. Зависимость величин коэффициентов неравномерности поля температуры газа на выходе из камеры сгорания от ее критериев. Повышенная величина коэффициента окружной неравномерности поля температур газа приводит к перегреву или прогару лопаток соплового аппарата, а эпюра средней температуры по высоте канала определяет работоспособность лопаток турбины. Точность описания экспериментальных данных по измерению максимального значения температуры стенки жаровой трубы для камер сгорания разI личных конструкций, аппроксимирз^ощей их зависимостью, иллюстрируется графиком на рисунке 6.7.Выводы к разделуУ!.Разработана интегральная математическая модель характеристик стационарного процесса в камере сгорания газотурбинного двигателя, позволяющая произвести расчет, в зависимости от режима работы и геометрии проточной части камеры сгорания, значений следующих характеристик рабочего процесса: — коэффициента полноты сгорания топлива- - индексов эмиссии всех составляющих вредных выбросов (оксидов азота, монооксидов углерода, несгоревших углеводородов, бензопирена) и параметра выброса сажи- - коэффициентов окружной и радиальной неравномерности поля температуры газа- - коэффициента потерь полного давления в камере сгорания- - максимальнз^ю величину температуру стенки жаровой трубы камеры сгорания. б) в) г) Рис. 6.1. Конструктивные схемы фронтовых устройств. Двигатели, не участвуюндие в обобщении: Ь^ - ГТН-25 (газовое топливо) — О — ГТУ „Сименс“, модель V 94.2 (газовое топливо) — О НК-86- Т — GF6−50- Л' - модель двухзонной камеры сгорания с „богато-бедным“ горением.Рис.6.2. Сопоставление расчетных и экспериментальных данных по эмиссии рксидов азота. .t EL CO г/кг.топл. (расч.) ь * * * • 40 80 120 EI. CO г/кг.топл. (эксп.) EI f^C г/кг.топл. (расч.) 0.1 ^ (^ • П.. ^ 0,1 10 100 ?:/c г/кг.топл. (эксп.) Рис. 6.3. Сопоставление расчетных и экспериментальных данных по эмиссии оксидов углерода и несгоревших углеводородов, (обозначения точек на графиках соответствуют Рис 6.2) SN (%) расч.ЛГ. ни 'jn n — к' л*', 0 20 40 SN (%) ЭКСП. Рис. 6.4. Сопоставление расчетных и экспериментальных данных по числу дымности отработавших газов двигателя. (обозначения точек на графике соответствуют Рис 6.2.) Цр Й W расч.0.3 0.25 0.2 к. у^ у^ р% 0,2 0.25 0.3шах ^КСП. Рис. 6.5. Сопоставление расчетных и экспериментальных данных по определению коэффициента окружной неравномерности поля температуры газа для разных конструкций камер сгорания.2^ дСг дСг дСг дСг /, ^ Jd’Cr д’Сг д’Сг dt дх ду dzdx ду dz j + dx dx dy dy dz dz где Cj- - концентрация горючего. Процесс воспламенения топливовоздушной смеси в камере сгорания характеризуется резким повышением температуры за короткий промежуток времени и уменьшением концентрации горючего из-за превращения его в # конечные продукты реакции за тот же промежуток времени: dt dt <0 .Условие непрерывности протекания химической реакции при воспламенении топлива, определяющееся превышением скорости поступления горючей смеси с потоком газа в реакционный объем над скоростью ее выгорания в этом объеме выражается неравенством (VIL7).Важнейшей задачей при создании камеры сгорания газотурбинного двигателя является обеспечение надежного воспламенения топливовоздушной смеси в различных высотно-климатических условиях его эксплуатации. Особенно актуально решение проблем запуска для авиационных двигателей, стационарных и транспортных установок, работающих в высокогорных условиях при отрицательной температуре воздуха и топлива. В настоящее время доводка камеры сгорания по обеспечению запуска осуществляется дорогостоящим методом проб и ошибок с привлечением специального оборудования (термобарокамеры) и испытания большого количества вариантов. Для описания процесса воспламенения топливовоздушной смеси в камере сгорания ГТД используем систему неравенств (VILS) и (VII.9) Для процесса запуска, осуществляемого системой непосредственного розжига (от свечи зажигания): J, си' где E^jj = энергия разряда, сосредоточенная в конденсатореС — емкость конденсатораU- напряжение. При нахождении функций, входящих в неравенства, использованы многочисленные экспериментальные материалы по исследованию полноразмерных камер сгорания и моделей на натурных режимах на автономном стенде в термобарокамере. Схема стенда представлена на рисунке 5.2.Объектами испытаний явились камеры сгорания экспериментальных и серийных двигателей: прямоточные (ТВЗ-117, РД-33 и др.), противоточные (ГТД-1250, ТВ7−117, стационарный двигатель для электростанций ГТЭ-1,5 и др.), одиночные (ГТД-350) с завихрительными, аэрационными и микрофакельными фронтовыми устройствами, с вращающейся форсункой. Конструктивные схемы исследованных фронтовых устройств показаны на рис. 6.1.Испытания проводились на керосине, дизельном летнем, зимнем и арктическом топливе, без вдува и со вдувом вспомогательного воздуха во второй контур форсунок с перепадом давления 0,02−0,3 МПа. Воспламенение производилось от свечей поверхностного и кумулятивного разряда с частотой разрядных импульсов от 2 до 25Гц, расположенных на расстоянии от торца форсунки 15… 100 мм по длине и высоте, с погружением внутрь жаровой трубы на 0…35ММ от ее стенок. Параметр переноса, как видно из анализа неравенств (VII. 12), (VII. 13) и рисунка 7.1, вместе с величиной, а определяет область воспламенения топливовоздушной смеси в камере сгорания на запуске двигателя. Неравенство (VII. 12) получено на основе преобразования и решения уравнения энергии в движущемся потоке для нестационарного процесса и отражает условие превышения тепловыделения в результате химических реакций над отводом тепла с продуктами сгорания в движущемся потоке газа. Неравенство (VII. 13) получено решением уравнения концентраций для f нестационарного потока и отражает условие непрерывности протекания химической реакции при запуске, т. е. превышение скорости поступления новых порций горючего в реакционную зону над скоростью выгорания. Величина коэффициента избытка воздуха определяет качество запуска, т. е. температуру газа перед турбиной и надежность воспламенения топливовоздушной смеси в камере сгорания. Запуск без заброса температуры газа на выходе из камеры сгорания происходит при значениях коэффициента избытка воздуха „> 2,5. Если or<2(но не менее а-\ для предотвращения прогаров концов рабочих лопаток турбины при запуске необходимо обеспечить резкий сброс давления топлива после его воспламенения путем соответствующих мероприятий в системе регулирования двигателя. Анализ неравенств (VII.12), (VII.13) и графика на рисунке 7.1 показывает, что запуск камеры сгорания осуществляется при выполнении двух условий: необходимого (кривая „а“) и достаточного (кривая „Ь“).При значениях и максимальном значении df неравенства (VII. 12), чж J opt (VII.IS) обращаются в тождества (точка пересечения кривых „а“ и „Ь“ на графике рис. 7.1). Так как — пропорционально частоте вращения ротора турбокомпрессора на пусковых режимах, то точка пересечения кривых на рис, 7.1 определяет оптимальную частоту вращения ротора, при которой происходит воспламенение топливовоздуп1ной смеси в камере сгорания с минимальной величиной температуры газа перед турбиной. Размерности в (VII. 12) и (VII. 13): давление — в МПа, температура — в К, расход воздуха — в кг/сек, объем — в м“, диаметр капли — в метрах, энергия разряда — в джоулях. Неравенства (VII. 12) и (VII. 13) представляют собой математическую модель процесса воспламенения топливовоздушной смеси в камере сгорания в различных высотно — климатических условиях. Достоверность расчета характеристик запуска подтверждается сравнением с опытными данными, что иллюстрируется на рисунке 7.2.Неравенства (VII. 12) и (VII. 13) апробированы в следующем диапазоне режимных и конструктивных параметров: Рк = 0,0227…0,1 МПа (Н=0…12км) — Тк = 223…296КG=0,181…2,6 кг/секci:=1…15- Есв=0,3…8ДжVж=0,008…0,0405м^- /zF^ =0,044…0,44- F^//zF^^ =5,61…11,4- число (топливных форсунок 1…80- миделевая скорость изменялась в пределах 4,7… 12 м/сек.Влияние режимных и конструктивных параметров на область воспламения топливовоздушной смеси в камере сгорания иллюстрируют графики на рисунках 7.3 — 7.9. Из рисунков видно, что повышение температуры И давления воздуха, увеличение параметра — и энергии разряда свечи ' Z/^ож расширяют область воспламенения в камере сгорания, а увеличение диаметра капель распыленного топлива и числа форсунок, приходящихся на единицу площади, наоборот, сужают эту область. Из графика на рис. 7.7 видно наличие оптимальной величины относительной пропускной способности завихрителей jiiFy, при которой, а максимально. Анализируя неравенства, отметим, что конструктивные параметры /^^и F ^ для обеспечения запуска не могут изменяться в широких пределах, так ож как они имеют оптимальные значения из условий обеспечения минимальной неравномерности поля температур и минимальных выбросов оксидов азота, монооксидов углерода, несгоревших углеводородов и минимального недожога топлива на рабочих режимах (см. раздел VI).Основными параметрами, с помощью которых могут быть достигнуты высокие показатели высотности запуска, являются энергия разряда Е^^ и медианный диаметр капель распыливания топлива d^^. Максимальное значение Есв на серийных отечественных двигателях достигает 6 Джоулей. За рубежом эта величина составляет 16 Джоулей. Повышение энергии разряда свечи является существенным резервом улучшения запуска двигателей. Эффективным средством снижения диаметра капли d^^ является распыливание топлива с помощью воздушного потока. Так, подача воздуха от воздушного стартера во второй контур центробежной топливной форсунки уменьшает диаметр капли в 10 раз при перепаде давления 0,15 МПа и температуре топлива 233К. На рисунке 7.10 иллюстрируются возможности улучшения высотности запуска на примере современного двигателя для истребителя. По оси ординат отложена высота полета, а по оси абсцисс — варианты конструктивного исполнения. Как видно из диаграммы, запуск двигателя без кислорода осуществляется до 8 км. Применение воздушного распыливания повышает высотность запуска до 13,5 км. Дополнительное использование свечи с знергией разряда 16 джоулей повышает высоту запуска до 18 км. Запуск с подводом кислорода реализуется на серийном двигателе до 11 км, а с применением аналогичных мероприятий высота запуска составляет 22 км. При обобщении результатов экспериментальных исследований по воспламенению топливовоздушнои смеси в камере сгорания величина медианного диаметра капель распыленного жидкого топлива d^^ рассчитывалась с помощью следующих зависимостей [45,73,74,75]. 1) Распыливание топлива центробежной форсункой. Устойчивость горения в камере сгорания на переходных режимах работы двигателя является одной из основных ее характеристик, определяющей диапазон работы двигательной установки в целом. В литературе отсутствуют данные о влиянии геометрии проточной части камеры сгорания на пределы устойчивого горения в ней, характеризуемых максимальной и минимальной величиной коэффициента избытка воздуха при срыве-аг'“ ^иа^,“.При обеднении или обогащении смеси горение поддерживается в отдельных очагах за счет уровня местной температуры газа. Размер очага будем характеризовать тепловой шириной зоны горения [28,33,95,105]: S —- СрРи&bdquoгде Uj^ -нормальная скорость распространения пламени: и и = /(Рд., Т^, Т2, а, вид топлива).Из анализа неравенств (VII. 14), (VII. 15), (VII. 16) и графика на рисунке 7.17 следует, что срыв горения в камере сгорания осуществляется, как и процесс запуска при выполнении двух условий: необходимого (кривая и линия „а“ для „бедной“ и „богатой“ границы) и достаточного (кривая „Ь“).Неравенства (VII.14), (VII.15), (VII.16) представляют собой математическую модель для описания устойчивости горения в камере сгорания при обеднении и обогащении топливовоздушной смеси. Влияние режимных и конструктивных параметров на фаницы устойчивого горения (по „бедному“ срыву) в камере сгорания иллюстрируется графиками на рисунках 7.20 — 7.22.Из рисунков видно, что увеличение температуры (рис. 7.20 а) и давления (рис. 7.20 б) воздуха на входе в камеру сгорания расширяют границы „бедного“ срыва пламени. Увеличение относительной пропускной способности завихрителя, характеризуемого. величиной параметра- /JF^ (рис7.21а, в), увеличение параметра F^l /JF^^ (рис. 7.21 б) и уменьшение закрутки воздушного потока на выходе из завихрителя (рис. 7.22) приводит к сужению границ области устойчивого горения в камере сгорания. Главной задачей при создании камеры сгорания газотурбинного двигателя является обеспечение стабильности протекающих в ней процессов. Источником нестабильности может явится диффузор камеры сгорания при неправильном его проектировании. Нестабильность течения потока газа в диффузоре приводит к повышению неравномерности поля температуры газа на выходе из камеры сгорания, причем проявление повышенной неравномерности отличается нестационарным характером. Диффузоры, испытанных камер сгорания газотурбинных двигателей представлены на рисунке 7.23: — кольцевые диффузоры с центральным телом — рис. 7.23 а) — - кольцевые ступенчатые диффузоры (фиксированный „отрыв“) с центральным теломрис.7.23 б) — - криволинейные ступенчатые диффузоры — рис. 7.23 в) — кольцевые диффузоры — рис. 7.23 г). в качестве критерия, характеризующего стабильность характеристик рабочего процесса в камере сгорания, которая зависит от стабильности процесса течения газа в диффузоре, примем величину, равную отношению где Абтах- „разброс“ значения коэффициента окружной неравномерности поля температуры газа от экземпляра к экземпляру камеры сгорания с определенной геометрией проточной части (т.е одинаковой конструкции) — (0тах)ср — Среднестатистическая величина коэффициента окружной неравномерности поля температуры газа, характерная для камеры сгорания определенной конструкции. График на рисунке 7.24 иллюстрирует зависимость нестабильности характеристик (относительного „разброса“ величины окружной неравномерности поля температуры газа) камер сгорания серийно изготавливаемых и опытных двигателей от значения конструктивного параметра диффузора, представляющего собой левую часть неравенства (VII. 17), условно обозначенного Кд и характеризующего условие стабильности течения газа в нем. Из графика следует, что для диффузоров камер сгорания, выполненных с учетом условия (VII. 17) „разброс“ характеристик на выходе из камеры сгорания минимален и обусловлен только разбросом геометрических размеров проточной части камер сгорания при их изготовлении в пределах полей допусков, оговоренных чертежом. При отрывном течении газа в диффузоре, т. е. при: Кд > 0,374, значение относительного разброса величины коэффициента окружной неравномерности поля температуры газа на выходе из камеры сгорания, определяется величиной критерия Кд — pHC.7i24. ' Нестабильность течения газа в диффузоре камеры сгорания, приводяпдая к нестабильности поля температуры газа на выходе из камеры сгорания, может явиться причиной дефектов конструктивных элементов турбины, проявляющихся в процессе эксплуатации двигателя. Выводы к разделу VTI.1. Разработана система критериально-параметрических зависимостей в виде неравенств, позволяк^щая производить расчет границ области воспламенения топливовоздушной смеси в камере сгорания и устойчивого горения в ней в зависимости от режимных и конструктивных параметров, 2. Произведен анализ критериев и параметров камеры сгорания на положение границ обдасти воспламенения и устойчивого горения топлива в ней. Энергия разряда свечи 6 Джоулейзапуск на земле (О км).Высота запуска 4 кмтемпература воздуха и топлива 233К. 10 20 30 G К кг/(с м^) ж Рис. 7.3.Влияние на границы области воспламенения топливовоздушной смеси в камере сгорания высоты запуска. Энергия разряда свечи 6 Джоулейтемпература воздуха и топлива 233К. Энергия разряда свечи 6 (Джоулейвысота запуска 7кмтемпература воздуха и топлива 23 ЗК. Энергия разряда свечи 6 Джоулейвысота запуска 4кмтемпература воздуха и топлива 233 К. Энергия разряда свечи 6 Джоулейвысота запуска 4кмтемпература воздуха и топлива 233КjjF^ = 0,16.1 — завихритель- 2 — кольцевая закрученйая струя воздуха- 3 — топливная форсунка- 4 — коническая пелена жидкости на выходе из сопла центробежной форсунки. !^ Рис. 7.14. Схема взаимодествия воздушного и топливного потока в „аэрационном“ фронтовом устройстве.1 — сопло пневматической форсунки- 2 — жидкостная пленка- 3 воздушный поток. i.Рис.7.18. Сопоставление расчетных и экспериментальных данных по „бедному“ срыву. ПИП /: эксп > ж й у^ X пУ [ > ^ п 02 04 06 [а) Iran /1 расч Различные обозначения точек на графике соответствуют испытанным вариантам пусковых воспламенителей и моделей камер сгорания.6)l-F^/2/zF^^=6,5−2-F^/X//F,^=ll.154а, а {^т^) opt -1 .ГТД-1000- Ж — ГТД-1250- Х-ТВ7−117- А-ТВЗ-117- П-РД-33- О-ТВ2−117- ОГТД-350- • - камера сгорания экспериментального двигателя. ф ф VIII. Физическое моделирование рабочего процесса в камере сгорания. При работе стенда в камеру сгорания подается подогреваемый воздух. Воздух подогревается в газовом или электрическом подогревателе. Регулирование расхода воздуха осуществляется с помощью крана, установленного перед подогревателем. В выходном сечении камеры сгорания устанавливаются, в зависимости от цели проводимых работ, соответствующие средства измерения (пробоотборники, хромель-алюмелевые термопары, гребенка полного давления).Доказательством применимости данного метода моделирования характеристик рабочего процесса камеры сгорания служит сопоставление результатов испытаний полноразмерных прямоточных и противоточных камер сгорания и их моделей, с одинаковыми величинами их критериев. Это сопоставление представлено на графике, изображенном на рисунке 8.2, где по оси ординат отложены величины характеристик рабочего процесса, полученные при испытании моделей камер сгорания, а по оси абсцисс величины характеристик рабочего процесса, полученные при испытаниях натуральных камер сгорания. Применение простейшей модели камеры сгорания, созданной на основе интегральной математической модели в виде критериальной функции, описанной выше, с учетом возможности пересчета режимных параметров по уравнениям разделаVI, полностью исключает необходимость проведения автономных, дорогостоящих испытаний полноразмерной конструкции на рабочих режимах для исследования всех ее характеристик. BbIZ вых Рис. 8.1. Схема одногорелочной модели полноразмерной камеры сгорания. П 0.1 0.01 л к X (о • 0.01 0.1 10 100 Рис. 8.2. Сопоставление характеристик рабочего процесса при испытании физической модели и полноразмерной камеры сгорания. I — Характеристики полноразмерных камер сгоранияII — характеристики камер сгорания, полученные при испытании их моделей. Х, Л, А — индексы эмиссии загрязняющих веществ NOx, СО, НС, г/кг топлива (двигатели ТВ7−117, TB3−1I7, ГТЭ-1,25- керосин, дизельное топливо, метан) — • число дымности, %(модификации камер сгорания двигателя РД-33- керосин)-О,• — коэффициент окружной неравномерности поля температуры газа (двигатели ТВ7−117, РД-33- керосин, дизельное топливо) — • - коэффициент потерь полного давления, % (двигатель РД-33)-0 — коэффициент избытка воздуха при „бедном“ срыве пламени (двигатель РД-33, керосин.). IX. Система уравнений для расчета характеристик камеры сгорания. IX.1. Система математических зависимостей характеристик камеры сгорания от ее критериев. При проектировании камер сгорания решается задача эффективного превращения химической энергии топлива в тепло с обеспечением устойчивости горения, надежного воспламенения топливовоздушной смеси при низких температурах и давлениях газа. Должны быть рассмотрены проблемы экологичности окружающей среды, неравномерности распределения температур газа на выходе из камеры сгорания и потерь полного давления в ее проточной части. Процессы в камере сгорания газотурбинного двигателя отличаются крайней сложностью в связи с одновременным протеканием в ней физикохимических превращений, таких как распыливание топлива, смешение топлива с окислителем и продуктами сгорания, смешение холодных и горячих струй газа в турбулентном потоке со сложной аэродинамической структурой, которая оказывает влияние на протекание химических реакций окисления топлива в реакционных зонах жаровой трубы. Для их описания необходимо привлечение исследований из области химической кинетики, термодинамики, тепломассообмена, механики жидкости и газа. На основе анализа фундаментальных уравнений тепломассообмена для химически реагирующей смеси в потоке газа, автономных испытаний камер сгорания, исследований моделей и обобщения материалов по созданию большого числа серийных двигателей разработан интегральный метод решения этих уравнений с введением критериев подобия камеры сгорания, определяющих протекание и взаимодействие вышеописанных процессов, позволивший математически описать характеристики камеры сгорания. Получены уравнения, позволяющие определить изменение характеристик камеры сгорания в зависимости от режима работы и параметров конструкции: / -г! = (Е1нс + 0,232Е1со)10-'- Е1со=В (Р^-''' V ехр (Т Л 288/^''' хехр (N Ф (N + с. Ф ж [1 + d^^Fj + d. ifPsfl с —d. ж + d. Система уравнений и неравенств является математической моделью характеристик рабочего процесса в камере сгорания и дает возможность оптимизировать конструкцию в процессе ее автоматизированного проектирования с учетом ограничений, включающих и нестационарные режимы работы. Приведенные зависимости представлены в виде произведений функций режимных и конструктивных параметров, что дает возможность проанализировать влияние этих параметров на характеристики камеры сгорания. IX.2. Анализ влияния критериев на характеристики камер сгорания. Проявление химической кинетики в работе камеры сгорания связано с изменением температуры и давления. Изменение характеристик рабочего процесса в камере сгорания от давления и температуры приведено на рисунке 9.1 и 9.2. По оси ординат отложены отношения текущего значения характеристики к его значению при заданных условиях. С ростом Рк и Тк наблюдается снижение недожога топлива, увеличение выбросов NOx и уменьшение содержания СО и НС, потому что NOx представляет собой конечный продукт реакции (исходные — азот и кислород), а СО и НС — исходные продукты (конечные продукты на выходе из камеры сгорания — СОг и Н2О).Существенное влияние относительного количества форсунок на процессы в камере сгорания иллюстрируется на рисунке 9.3. Здесь и на последующих рис. 9.4, 9.5, 9.6 по оси абсцисс отложены отношения текущего значения критерия к его значениюсоответствующему минимальному недожогу топлива (максимальной полноте сгорания топлива). По оси ординат — отношение текущего значения характеристики к его значению в точке, соответствующей минимальному недожогу топлива. По физическому смыслу увеличение количества форсунок на единицу 171 I площади означает приближение состояния топливовоздушной смеси к однородной, что определяет протекание приведенных на графике характеристик. Из графика следует, что наивыгоднейщие условия запуска (максимальное значение коэффициента избытка воздз^а на запуске, соответствующее минимальному забросу температуры газа) обеспечивается вполне определенным количеством форсунок. Существует, оптимальное' количество форсунок, обеспечивающее максимальную полноту сгорания топлива (минимальный недожог) при оптимальных значениях выброса NOx и числа дымности. Снижение дымления и выброса NOx путем увеличения количества форсунок выше оптимального значения связано с увеличением недожога топлива. Критерий fiFj определяет долю воздуха, участвующего в формировании топливовоздушной смеси в отдельной горелке, а критерий W характеризует интенсивность этого процесса, рис. 9.4 и 9.5. Совместное проявление этих факторов характеризует процессы смешения топливных и воздушных потоков и процессы тепломассообмена между зоной обратных токов и закрученной струей воздуха, сформированных завихрителем в отдельной горелке. Как видно из графиков, существует оптимальное значение критерия 1лР^, при котором процесс протекает с минимальным недожогом топлива, при этом запуск камеры сгорания осуществляется с минимальным забросом температуры газа перед турбиной {а максимален).Из графиков же следует, что обеспечение снижения выброса NOx и дымления приводит к резкому снижению устойчивости рабочего процесса (а&trade-» уменьшается) и высотности запуска Н, определяемой атмосферными условиями. Из рисунка следует, что интенсивность крутки завихрителя оказывает существенное влияние на устойчивость горения. Как и в случае //F^ имеется значение этого критерия, при котором недожог топлива и уровень дымления минимальны, а уменьшение этого критерия приводит к увеличению выброса NOx. Процессы перемешивания и взаимодействия холодных и горячих турбулентных струй, оказывающих существенное влияние на протекание химических реакций и выравнивание температур в камере сгорания, представляющей собой термогазодинамическую решетку, управляются F .Ж / важнейшим критерием у^ ' р Универсальность критерия и его влияние на характеристики камеры сгорания иллюстрируется графиками на рис. 9.6. При оптимальной величине критерия имеет место не только максимальное значение полноты сгорания топлива, но и минимальная неравномерность поля температур перед турбиной. Минимальному значению недожога топлива и минимальной неравномерности температурного поля всегда соответствует вполне определенное значение потерь полного давления. Как снижение, так и увеличение потерь полного давления ухудшает основные характеристики, в том числе выбросы NOxУменьшение критерия приводит к большей устойчивости горения, но снижает высотность запуска. На рисунке показана область устойчивого горения при максимальном обеднении смеси, описанная (IX. 1) и (IX.2). По оси абсцисс отложено отношение коэффициентов скорости в отверстиях жаровой трубы к их величине при максимальном значении коэффициента избытка воздуха при срыве пламени. По оси ординат отложено' отношение коэффициента избытка воздуха при срыве пламени к его максимальному значению. Физический смысл значения коэффициента скорости в отверстиях жаровой трубы состоит в том, что его величина пропорциональна отношению 4vr для очага, / ''^ог поддерживающего горение при обеднении топливовоздушной смеси в камере сгорания. В соответствии с приведенным анализом, сужение границ по левой ветке кривой обусловлено «проскоком» пламени, а по правой ветке — «выносом» пламени из зоны стабилизации. Эмпирическое уравнение (IX.5) описывает тепловое состояние стенки жаровой трубы камеры сгорания. Влияние величины h^ на значение максимальной температуры стенки жаровой трубы получено из уравнения теплового баланса между теплом, отдаваемым стенкам жаровой трубы из ее объема, и теплом, отводимым воздухом, поступающим на охлаждение стенок жаровой трубы. Рассмотренная система уравнений явилась базой для разработки алгоритма и программ проектирования оптимальной конструкции конструкции камеры сгорания. Графическое представление уравнений и анализ физической сущности протекания процессов вооружают проектировщика знаниями о влиянии важнейших конструктивных критериев и термодинамических параметров в их взаимосвязи на изменение характеристик камеры сгорания. IX.3. Оптимальные значения критериев камеры сгорания. Оптимальные значения критериев камеры сгорания положены в концепцию ее проектирования для газотурбинных двигателей различного назначения.1 — г, NO, SN a тех. К > / / {w Hw X, Рис. 9.5. Влияние параметра W на характеристики камеры сгорания.1 -i^-2- NO-3- SN -4-а'" '^.Х.1. Анализ технических требований к газотурбинным двигателям. Можно выделить следующие области использования газотурбинного двигателя: — привод для стационарной энергетической установки- - привод для транспортной машины (наземной, судовой, авиационной) — - привод для высокоманевренной машины (истребительная военная авиация).' В соответствии с назначением, предъявляются различные требования к газотурбинным приводам. От стационарной энергетической установки в настоящее время требуется максимальная чистота отработавших газов, т. е. минимальная концентрация в них вредных веществ, обеспечивающая экологические требования к окружающей среде (особенно для энергетических установок, располагаемых в районах населенных пунктов) и высокая экономичность работы. От двигателя для транспортной машины требуется максимальная экономичность, устойчивость работы на переходных режимах и низкая концентрация загрязняющих атмосферу веществ в отработавших газах. Двигатель для высокоманевренной машины должен обладать наилучшими характеристиками запуска в различных высотноклиматических условиях, обеспечивающими его надежность, максимальной устойчивостью работы на переменных режимах и минимальным уровнем дымления.Х.2. Совершенная конструкция камеры сгорания в зависимости от назначения двигателя. Требования, изложенные в предыдущем разделе, определяют конструктивный облик камеры сгорания для двигателя, в зависимости от его назначения. Организация процесса горения в камере сгорания привода энергетической установки должна обеспечить минимальную концентрацию NOx, СО, НС в газах на выходе из нее. Значения критериев камеры сгорания, обеспечивающие минимальный выброс NOx, выбираются из диапазона их изменения на основании анализа отработанных серийно реализованных конструкций камер сгорания и расчетных зависимостей раздела VI: //Гз =0,6- ^ = 2 — ^ = 1—^10-' =4,5…5.В соответствии с материалами раздела VI, минимальный выброс NOx ' G может быть обеспечен при максимальной величине параметра —. С другой стороны, для камеры сгорания (Я^ -^ = 0,15-г 0,3) справедливо соотнощение: V F I ' ЗГ •* Ж^3r По материалам раздела III.5, минимальная величина длины части жаровой трубы до отверстий смесителя: /з^=0,8-Ы, 0Л^.Тогда: Гэг ^ ^ h ж ож I Отсюда следует, что для минимизации выбросов оксидов азота, величина параметра Д^ ж должна быть наибольшей, а величины параметров F ^ ,/Zj-j.-наименьшими. Минимально допустимая величина высоты.
Основные результаты работы.
1. Теоретически обоснованы интегральные гидродинамические и геометрические критерии и параметры, определяющие процесс формирования характеристик движущегося потока газа в камере сгорания с происходящими в нем химическими реакциями окисления (горения) топлива.
2. Разработана интегральная математическая модель камеры сгорания газотурбинного двигателя.
Модель представляет систему математических зависимостей величин, характеризующих протекание рабочего процесса в камере сгорания газотурбинного двигателя от значений ее режимных и конструктивных параметров. I.
Система состоит из уравнений для расчета:
— коэффициента полноты выгорания топлива,.
— коэффициентов максимальной окружной и радиальной неравномерности поля температуры газа на выходе из камеры сгорания,.
— величины коэффициента потерь полного давления,.
— пределов воспламенения топливовоздушной смеси в камере сгорания для различных высотно-климатических условий,.
— пределов устойчивого горения топлива в камере сгорания,.
— степени токсичности продуктов сгорания (характеризуемой индексами эмиссии загрязняющих атмосферу веществ — оксидов азота, монооксидов углерода, несгоревших углеводородов, бензо- (а)-пирена, частиц углерода),.
— максимальной величины температуры стенок жаровой трубы.
3. На базе разработанной математической модели камеры сгорания найдены оптимальные значения таких параметров ее конструкции как число топливных форсунок, относительная пропускная способность, интенсивность крутки потока воздуха на выходе из завихрителя фронтового устройства, относительная площадь отверстий жаровой трубы, а также параметров, учитывающих особенности конструкции фронтовых устройств и форсунок. В частности, оптимизация конкретной конструкции камеры сгорания авиационного двигателя по ряду вышеназванных параметров, увеличит высотность запуска двигателя более чем на 50% или снизит эмиссию оксидов азота более чем в 2 раза. Оптимальные величины геометрических параметров и критериев положены в основу концепции проектирования камеры сгорания для различных типов двигателей.
4. Обоснована концепция оптимального проектирования камеры сгорания для газотурбинного двигателя различного назначения — энергетическая установка, двигатель транспортной машины, двигатель высокоманевренной транспортной машины (военный истребитель). Суть концепции проектирования заключается в определении размеров камеры сгорания с помощью установленных значений ее критериев и параметров, обеспечивающих такие значения характеристик камеры сгорания, которые в наибольшей степени отвечают предъявляемым к двигателю требованиям.
5. Разработан алгоритм расчета размеров камеры сгорания для каждого из трех типов двигателей.
6. Выполнен анализ системы дифференциальных уравнений переноса субстанции в потоке сплошной среды с наличием источников (стоков) энергии, вещества и силы. Произведено преобразование исходной системы дифференциальных уравнений. Преобразованная форма уравнений позволяет обосновать критерии и параметры, определяющие процесс формирования характеристик потока сплошной среды с источниками (стоками) энергии и вещества в объеме рассматриваемого канала.
7. На основании преобразований уравнений Рейнольдса для установившегося турбулентного течения и уравнения Навье-Стокса для нестационарного процесI са, обоснована критериальная модель турбулентности для потока сплошной среды в канале переменной геометрии, каковым является проточная часть камеры сгорания.
8. Теоретически обоснована и определена связь температурного состояния стенок жаровой трубы с ее размерностью и формой. Получена количественная зависимость максимального значения температуры стенок жаровой трубы (с металлическим материалом стенок) от величины размера — высоты жаровой трубы в поперечном сечении.
9. На базе теоретических и экспериментальных исследований определены минимально допустимые размеры — высота поперечного сечения жаровой трубы и длина «зоны горения» жаровой трубы камеры сгорания.
10. Теоретически обоснованы и экспериментально подтверждены принципы физического моделирования рабочего процесса в камере сгорания. Принцип физического моделирования основан на равенстве величин разработанных критериев и параметров, определяющих характеристики рабочего процесса в камере сгорания для физической модели и полноразмерной камеры сгорания.
11. Теоретически обоснован безразмерный геометрический критерий, характеризующий стабильность течения газа в диффузоре камеры сгорания. Получена связь величины этого критерия со стабильностью окружной неравномерности поля температуры газа.
12. Разработана математическая модель для расчета характеристик нестационарных процессов: областей воспламенения топливовоздушной смеси в различных высотно-климатических условиях и устойчивости горения при обеднении топливовоздушной смеси в камере сгорания.
13.Материалы работы использованы при создании камер сгорания двигателя ТВа — 3000, малоразмерного турбовального вертолетного двигателя, высокотемпературного турбореактивного двигателя пятого поколения, приводов стационарной установки ГТП— 1.5, ГТЭ — 100 и при модернизации камер сгорания серийно изготавливаемых турбовальных и турбореактивных двигателей: ТВЗ-117, РД-33, вспомогательной силовой установки ГТДЭ-117.
14. Гидродинамические, геометрические критерии и параметры, полученные в I работе, по мнению' автора, могут быть применены для изучения и описания процессов, протекающих в жидкостных реактивных двигателях и других теп-ломассообменных аппаратах.
Список литературы
- Абрамович Г. Н. Прикладная газовая динамика. М.: Наука. 1969. 824с.
- Абрамович Г. Н. Теория турбулентных струй. М.: Наука. — 1986. — 716с.
- Абрамович Г. Н. Теория центробежной форсунки. М., ЦАГИ, 1944. 114с.
- Абрамович Г. Н. Турбулентные свободные струи жидкостей и газов. М. -Л.: Госэнергоиздат. — 1948. — 288с. '
- Авиационные ГТД в наземных установках. С. П. Изотов, В. В. Шашкин, В. М. Капралов и др. Под общ. ред. В. В. Шашкина. Л. Машиностроение. Ленинград, отделение. 1984. 288с. (Экономия топлива и электроэнергии).
- Адамов В.А. Сжигание мазута в топках котлов. Л.: Недра. 1989. — 304с.
- Акатнов Н.И., Лавров А. В. О влиянии пульсаций температуры на образование NOx в высокотемпературной среде // Тр. ЛПИ. Сер. Механика иIмашиностроение. — Л. — 1976. — № 352. с. 46 51.
- Ахмедов Р.Б. Дутьевые горелочные устройства. М. Недра. 1977. 272с.
- Ахназарова С.Л., Кафаров В. В. Оптимизация эксперимента в химии и химической технологии. М.: Высш. школа. 1978. 319с.
- Аэродинамика закрученной струи. Под ред. Р. Б. Ахмедова. М. Энергия. 1977. 240с.
- Бронштейн И.Н., Семендяев К. А. Справочник по математике для инженеровIи учащихся вузов. Москва. Наука. 1980.
- Влияние ввода влаги в топку БКЗ 320 — 140 ГМ на выбросы окислов азота/
- А.Д.Горбаненко, С. П. Титов, В. П. Лукашявичус и др.// Электрические станции. 1984. № 5. С. 59 60.
- Тумановский А.Г., Тульский В. Ф. /Влияние впрыска воды на образование окислов азота за камерой сгорания с последовательным вводом воздуха в зону горения // Теплоэнергетика. 1982. № 6. С. 34 36.
- Внуков А.К., Алыневский В. Н. Влияние двухступенчатого сжигания и рециркуляции газов на генерацию оксидов азота и серного ангидрида. -Электрические станции. 1980. № 7. С. 15 18.
- Котлер В.Р. /Выбросы оксидов азота при совместном сжигании угля с газом или мазутом // Теплоэнергетика. 1996. № 5. — С.47 — 57.
- Гаврилов А.Ф., Горбаненко А. Д., Туркестанова Е. А. /Влияние влаги, вводимой в горячий воздух, на содержание окислов азота в продуктах сгорания газа и мазута// Теплоэнергетика. 1983. № 9. С. 13 15.
- Методика нормирования эмиссии вредных веществ турбореактивными двигателями дозвуковых самолетов гражданской авиации в зоне аэропорта/ Горбатко А. А., Щербаков В. И., Худяков Е. И. и др. // Труды ЦИАМ. 1982.
- Горбунов Г. М. Выбор параметров и расчет основных камер ГТД. Учебное пособие. М. Изд. МАИ им. Орджоникидзе. 1972. 229с.
- Горелочные устройства с пониженным выходом NOx // Механика и энергетика. Выпуск 5. Москва. 1991.
- ГОСТ 17.22.04.86. Двигатели газотурбинные самолетов гражданской авиации. Нормы и методы определения выбросов загрязняющих веществ.
- Груздев В.Н. Концентрация токсичных компонентов в продуктах сгорания керосино-воздушных смесей // Изв. ВУЗ. Сер. Авиационная техника. 1978. — № 1. — С.49 — 52.
- Длин A.M. Факторный анализ в производстве. М. «Статистика». 1975.
- Дорошенко В.Е. О процессе горения в камере ГТД // Тр. ЦИАМ. 1959. № 354.
- Дрегалин А.Ф., Черенков А. С. Общие методы теории высокотемпературных процессов в тепловых двигателях. — М. «Янус — К». 1997. 328с.
- Зависимость эмиссии NOx от конструктивных и режимных параметров камеры сгорания газотурбинного двигателя /А.А.Саркисов, О. А. Рудаков, Н. Д. Саливон, Ю. В. Сигалов, В. А. Митрофанов // Теплоэнергетика. 1999. № 12.I
- Зельдович Я.Б., Садовников П. Я., Франк-Каменецкий Д.А. Окисление азота при горении. М.: Изд-во АН СССР. 1947.
- Зуев B.C., Скубачевский JI.C. Камеры сгорания воздушно-реактивных двигателей. М. Изд. МАИ им. Орджоникидзе. 1958.
- Идельчик И.Е. Справочник по гидравлическим сопротивлениям. М.: Машиностроение. 1975.-559с.
- Тумановский А.Г. /Испытание кольцевой камеры сгорания авиационного двигателя НК-8 на природном газе // Теплоэнергетика. 1976. № 8. — С.60 -64.
- Исследование области воспламенения топлива в камере сгорания /А.А.Саркисов, О. А. Рудаков, Н. Д. Саливон, В. А. Митрофанов // Теплоэнергетика. № 3. 2003.
- Камеры сгорания авиационных газотурбинных двигателей./ Под редакцией Б. П. Лебедева, Г. Н. Абрамовича и Ю. Ф. Дитякина // Министерство авиационной промышленности СССР. Институт им. П. И. Баранова.
- Канило П.М., Подгорный А. Н., Христич В. А. Энергетические иэкологические характеристики ГТД при использовании углеводородныхtтоплив и водорода. Киев: Наукова думка. 1987. -224с.
- Котлер В.Р. Оксиды азота в дымовых газах котлов. М. Энергоатомиздат. 1987.- 144с.
- Кропп Л.И. Пути сокращения вредных выбросов ТЭС // Теплоэнергетика. -1978. № 11. — с.2 — 7.
- Круглов М.Г., Меднов А. А. Газовая динамика комбинированных двигателей внутреннего сгорания. Учебное пособие. — М.: Машиностроение. 1988. -360с.
- Кузнецов В.Р. Аналитические методы определения концентрации окиси азота в камерах сгорания газотурбинных двигателей. Новое в зарубежном авиадвигателестроении. 1973. № 2.
- Ландау Л.Д., Лифшиц Е. М. Теоретическая физика: Учебное пособие. TVI.
- Гидродинамика. М.: Наука. 1988. — 736с.
- Ластовцев A.M. Гидродинамический расчет вращающихся распылителей. Труды МИХМ т. 11. Москва. 1957.
- Лефевр А. Процессы в камерах сгорания ГТД. М.: Мир. 1986. 566с. I
- Лукачев В.П., Белоусов А. Н., Ланский A.M. Влияние конструктивных параметров вихревых газовых горелок на характеристики кольцевой авиационной камеры сгорания. // Горение в потоке. Казань. КАИ. 1982.
- Малотоксичные камеры сгорания для энергетических ГТУ/ Тумановский А. Г., Гутник М. Н., Соколов К. Ю. // Теплоэнергетика. 1997. № 3. С. 48 52.
- Математическая модель процессов образования и расчета загрязняющих веществ и оптимизация камер сгорания ГТД/А.А.Саркисов, О. А. Рудаков, Н. Д. Саливон, Ю. В. Сигалов, В. А. Митрофанов // Теплоэнергетика. 2000. № 5. С. 52 55.
- Постников A.M. /Методика обработки результатов измерений выбросов вредных веществ газотурбинными двигателями // Теплоэнергетика. 1992. № 9.С.64 66.
- Камера сгорания ГТД с низким уровнем эмиссии/ Митрофанов В. А., Федоров A.M., Рудаков О. А' ., Сигалов Ю.В.// Тезисы докладов XLIII Научно-технической сессии по проблемам газовых турбин. 25−26 июня Санкт- Петербург 1996 года.
- Рабочий процесс и расчет камер сгорания газотурбинных двигателей /Михайлов А.И., Горбунов Г. М., Борисов В. В., Квасников Л. А., Марков Н.И.
- Тр. МАИ им. Орджоникидзе. 1959. Вып. 106. 285с.
- Некоторые вопросы математического описания и оптимизацииIмногофакторных процессов. Г. К. Круг и др. Труды МЭИ. 1963. Вып.51.
- Тумановский А.Г./ Некоторые особенности образования окислов азота в высокофорсированных камерах сгорания с последовательным вводом воздуха в зону горения/ // Теплоэнергетика 1977. — № 12. С. 70 — 72.
- Новое в зарубежном авиадвигателестроении. № 1. 1978.
- Новые газотурбинные установки фирмы Семенз /КВУ./ Новостизарубежной науки и техники. Серия «Двигатели для авиации иtкосмонавтики» № 5 6. 1992. С. 15 — 20.
- Новый газотурбинный двигатель мощностью 110 МВт для стационарных энергетических установок/ Романов В. И., Рудометов С. В., Жирицкий О. Г., Романов В. В. // Теплоэнергетика. 1992. № 9. С. 27 — 31.
- Обобщенная эмиссионная характеристика ГТД как функция конструктивных и режимных параметров камеры сгорания /А.А.Саркисов, О. А. Рудаков, Н. Д. Саливон,' Ю. В. Сигалов, В. А. Митрофанов // Теплоэнергетика. 2000. № 3.
- Образование и разложение загрязняющих веществ в пламени: Пер. с англ. //
- Ред. Н. А. Чигир. М.: Машиностроение. 1981. — 407с.
- Основы практической теории горенйя: Учебное пособие для вузов/ В. В. Померанцев, К. М. Арефьев, Д. Б. Ахмедов и др. Л.: Энергия. 1973. 264с.
- Отчет о научно-исследовательской работе «Исследование экологических характеристик двигателей ТВ2−117, ТВЗ-117 и ГТД-350″. Центр социальной экспертизы республиканского инновационного фонда СМ РСФСР. 1991.
- Отчет экспертизы по выбросам изделиями 88, 21, 55Б (77) веществ, загрязняющих окружающую среду. ЭД85.90. ТМКБ „Союз“. 1990.
- Павлов В.А., Штейнер И. Н. Условия оптимизации процессов сжиганияжидкого топлива и газа в энергетических и промышленных установках.: Л.
- Энергоатомиздат. 1984. 120с.
- Перемешивание поперечной натекающей на стенку струи с основным потоком./ Новости зарубежной науки и техники. Серия „Двигатели дляавиации и космонавтики“ 1992. № 5 6. С. 32 — 36.
- Перспективные проекты газовых турбин в Японии./ Новости зарубежной науки и техники. Серия „Двигатели для авиации и космонавтики“ 1992. № 5 -6. С.32−36. ' |
- Применение концепции двухзонной камеры сгорания с низким уровнем эмиссии NOx-/ Новости зарубежной науки и техники. Серия „Двигатели для авиации и космонавтики“ 1992. № 3. С. 34 39.
- Пчелкин Ю.М. Камеры сгорания газотурбинных двигателей. Учебноепособие.- 3-е изд. перераб. и доп. М. Машиностроение. 1984. 280с.
- Разработка критериев запуска камер сгорания ГТД./ Саркисов А. А., Рудаков1
- О.А., Саливон Н. Д., Сигалов Ю. В., Митрофанов В.А.// Вестник СГАУ. Сер. Процессы горения, теплообмена и экология тепловых двигателей. Самар. Гос. Аэрокосм. Университет. Самара. 1999. Вып.2. -С.177−183
- Разработка методов снижения эмиссии загрязняющих веществ стационарными газотурбинными установками на природном газе. Научно-технический отчет 95−001 ЦИАМ. „Эколэн“. 1995.
- Распыливание жидкостей / В. А. Бородин, Ю. Ф. Дитякин, Л. А. Клячко, В. И. Ягодкин — М. 1967.
- Распыливание жидкостей / Ю. Ф. Дитякин, Л. А. Клячко, Б. В. Новиков, В. И. Ягодкин. М., Машиностроение. 1977. 208с.
- Распыливание топлива центробежными форсунками турбореактивных двигателей / В. А. Бородин, Ю. Ф. Дитякин, Л. А. Клячко, Н. Н. Струлевич М.1. ЦИАМ. 1952.
- Расчет устойчивости горения в ГТД / Саркисов А. А., Рудаков О. А., Саливон Н. Д., Сигалов Ю. В., Митрофанов В.А.// Вестник СГАУ. Сер. Процессы горения, теплообмена и экология тепловых двигателей. Самар. Гос. Аэрокосм. Ун-т. Самара. 2000. Вып.З.-С.262−266.
- Рудаков О.А. Методика расчета оптимальных параметров камеры сгорания высокотемпературного ГТД. Научно-технический сборник. Серия XX. 1978. Выпуск 80. С. 8- 11.
- Рудаков О.А., Пыховский JI.JI. Расчетная оптимизация камеры сгорания по удельному расходу топлива ГТД /Автоматизация проектирования авиационных двигателей// Тезисы докладов IV отраслевой конференции. Труды ЦИАМ № 1095. 1984. С. 81 82.
- Руководящий технический материал авиационной техники. Р.Т.М. 1626−80. Камеры сгорания газотурбинных двигателей. Метод поверочного гидравлического расчета на ЭВМ. 1980. 39с.
- Салливан Е. Простое уравнение для расчета выбросов NOx из камеры сгорания газотурбинного двигателя, учитывающее загрязнение воздуха./ Труды американского общества инженеров-механиков. Сер. Энергетические машины и установки. 1978. № 2. С. 1 8. I
- Сжигание жидкого топлива в кольцевой камере сгорания конструкции H3JI/ А. Г. Тумановский, А. В. Сударев, В. В. Маев и др. // Теплоэнергетика. 1986. № 3. С. 37 —42.
- Система уравнений для расчета характеристик камеры сгорания. / Саркисов А. А., Рудаков О. А., Саливон Н. Д., Митрофанов В.А.// Промышленная теплотехника. 2001.-Т.23.- № 3.- С.83−88.
- А.Г.Тумановский, М. Н. Гутник, К. Ю. Соколов /Снижение выбросов оксида углерода и углеводородов на пусковых и переменных режимах энергетических ГТУ при сжигании жидких и газообразных топлив // Электрические станции. 1991. № 11. С. 2 6.
- Совершенствование ГТУ для электростанций. / Г. Г. Ольховский, А. Г. Тумановский, А. И. Механиков и др. // Теплоэнергетика. 1991. № 6. С. 66 -73.
- Современное состояние развития газотурбинных установок в Европе./ Новости зарубежной науки и техники. Серия „Двигатели для авиации и космонавтики“ 1992. № 5 6.С.37 — 40.
- Создание перспективных газовых турбин в США./ Новости зарубежной науки и техники. Серия „Двигатели для авиации и космонавтики“ 1992. № 5 -6. С.7−11.
- Соколов К.Ю. Совершенствование камер сгорания ГТУ на основеIматематического моделирования рабочего процесса. // Авторефератдиссертации на соискание ученой степени кандидата технических наук. -Москва: ВТИ. 1989. 23с.
- Спейшер В.А., Горбаненко А. Д. Повышение эффективности использованияIгаза и мазута в энергетических установках. М. Энергоиздат. 1982. 239с.
- Сторожук Я.П. Камеры сгорания стационарных газотурбинных и парогазовых установок. — JL: Машиностроение. 1978. 231с.
- Сторожук Я.П., Ожигов Г. Е. Обзор материалов по газомазутным горелочным устройствам зарубежных фирм. JI. Тр. ЦКТИ. 1975. Вып. 128.
- Сторожук Я.П., Павлов В. А. Процессы распыливания и смесеобразования при сжигании мазута в топках паровых котлов. — В кн.: Опыт сжигания мазута и газа на электростанциях. М. Энергия. 1968. С. 46 71.
- Сударев А.В. Перспективы создания для стационарной энергетики экологических газотурбинных двигателей // Изв. РАН. Энергетика 1992. № 1.
- Сударев А.В., Маев В. А. Камеры сгорания газотурбинных установок. Интенсификация горения. JL: Недра. 1990. — 274с.
- Талантов А.В. Горение в потоке. М.: Машиностроение. 1978. 160с.
- Теория двухконтурных турбореактивных двигателей/ Под ред. д-ра техн. наук проф. С. М. Шляхтенко, д-ра техн. наук проф. В. А. Сосунова. М. Машиностроение. 1979. 432с.
- Теория и расчет воздушно-реактивных двигателей./ Под ред. С. М. Шляхтенко. Учебное пособие. 2-е изд. перераб. и доп. — М. Машиностроение. 1987. 568с.
- Теория и расчет образования вредных выбросов в камерах сгорания ГТД/ А. А. Саркисов, О. А. Рудаков, Н. Д. Саливон, Ю. В. Сигалов, В. А. Митрофанов. // Промышленная теплотехника. 1999. Т.21.- № 6. — С.34−38.
- Тишин А.П., Худяков В. А., Артамонов А. К. Исследование возможностей уменьшения концентрации окислов азота при сжигании топлив в теплоэнергоагрегатах./ Калининград. М.О. ЦНИИмаш. 1994. 60с.
- Тумановский А.Г. Исследование камер сгорания ГТУ и разработка мероприятий по снижению концентраций окислов азота // Автореферат диссертации на соискание ученой степени кандидата технических наук. — Москва: ВТИ. 1971.
- Тумановский А.Г. Образование окислов азота в камерах сгорания ГТУ при сжигании природного газа // Теория и практика сжигания газа. — Вып.5. Л.: Недра. 1972. — С.330 — 340. t
- Тумановский А.Г. Предотвращение загрязнения атмосферы ГТУ // Энергетика и охрана окружающей среды. М.: Энергия. 1975. С. 223 -234.
- Устименко Б.П., Ткацкая О. С. Аэродинамика закрученной струи. В кн.:<
- Проблемы теплоэнергетики и прикладной теплофизики. Алма-Ата. „Наука“. 1970. Вып.6. С.211−216.
- Физические основы рабочего процесса в камерах сгорания ВРД/
- Б.В.Раушенбах, С. А. Белый, И. В. Беспалов и др. М.: Машиностроение. 1964.525с.
- Франк-Каменецкий Д. А. Диффузия и теплопередача в химической кинетике. Изд-во АН СССР. 1947.
- Христич В.А., Тумановский А. Г. Газотурбинные двигатели и защита окружающей среды. Киев: Техника. 1983. 144с.
- Шаулов Ю.Х., Лернер М. О. Горение в жидкостных ракетных двигателях./ Государственное научно-техническое издательство ОБОРОНГИЗ. Москва. 1961.
- Щуровский В.А., Синицын Ю.Н.' Экологические характеристикигазотурбинных агрегатов на переменных режимах. // Газовая промышленность. 1991. № 11.
- Экспериментальное исследование фронтового устройства камерыIсгорания ГТЭ-115 с предварительным образованием гомогенной топливо-воздушной смеси./ А. Г. Тумановский, К. Ю. Соколов, М. Н. Гутник и др. // Теплоэнергетика. 1993. № 7. С. 42 48.
- Яворский Б.М., Детлаф А. А. Справочник по физике. М., 1977., 944с.
- Зысина-Моложен Л.М., Зысин Л. В., Поляк М. В. Теплообмен в турбомашинах."Машиностроение» (Ленинград, отд-ние). 1974. 336с.
- Технический отчет ЦИАМ № 5836. Исследование течения в моделяхдиффузоров камер сгорания. Авторы: Безменов В. Я., Асеев Г. Д., Тарараксина А. П. 1967.
- Лойцянский Л.Г. Механика жидкости и газа. М.: Наука. 1970. 847с.
- Верцинский 3., Супрун Т. Т., Эпик Э. Я. Характеристики ламинарно-турбулентного перехода, индуцированного следом одиночного движущегося цилиндра // Промышленная теплотехника. 2001. Т. 23.№ 3. С. 22 30.
- Appleton J.P., Heywood J.B.< The effects of Imperfect Fuel-air Mixing in a Burner on NO Formation from Nitrogen in the Air and Fuel. 14-th Symposium (international) on Combustion.
- Bahr D.W., Control and Reduction of Aircraft Turbine Engine. Exhaust Emissions, in W. Cornelius and W.G.Agnew (eds.), Emissions from Continous Combustion Systems. Plenum. New York. 1972. P. 345 372
- Bowmann C.T. Kinetics off pollutant formation and distinction in combustion. Progress in Energy and Combustion Sc. 1975. Vol.1. № 1.
- Brandon D.B. I.S.A. Journal. 1959. 6. № 7.
- Buchheim R. Influences on Exhaust Emissions from Automotive Gas Turbines, ASME. 1978. Paper 78 GT — 85i
- Gleason C.C., Rogers D.W., Bahr D.W. Experimental clean combustor program, phase 2. NACA. CR- 13 1971, 1976.
- Grobman J. Effect of Operating Variables on Pollutant Emissions from Aircraft Turbine Combustors, in W. Cornelius and W.G.Agnew (eds.), Emissions from Continous Combustion Systems. Plenum. New York. 1972. P. 279 303
- Hey wood J.B. Gas Turbine Combustor Modelling for Calculating Nitric Oxide Emissions, AIAA. Paper 1971. № 712.i
- Lavoie G.A., Heywood J.B., Keck J.C. Experimental and Theoretical Study of Nitric Oxide Formation in Internal Combustion Engines, Combust. Sci. Technol. 1970. Vol.l.P. 313−326
- Lipfert F.W. Correlation of Gas Turbine Emission data. ASME Publication. 1972. Paper 72-GT-60.
- Morton H.L., Marshall R.L. Impact of emission regulations on gas turbine combustion design. Canad. Aeronaut. Space, Journal. 1974. Vol.20, № 3.
- Quan F., Marble F.E., Klilgel J.R. Nitric Oxide Formation in Turbulent Diffusion Flames. 14-th Symposium (international) on Combustion.
- Roberts R., Fiorentino A.J., Diehl L.A. The pollution reduction technologyprogramm for can-annular combustor engines. AIAA. 1976. Paper№ 76 761.
- Roberts R., Peduzzi A. Low pollution combustor for GTOL engines. AIAA. 1976. Paper № 76−761.
- Verkamp E.J., Verdouw A.J., Tomlinson J.G. Impact of emission regulations on Future Gas Turbine Engine Combustors. AIAA. 1973. Paper № 73 1277.
- Westenberg A.A. Combust. Sci. Technology. 1971. 59.Vol. 4.1. Патенты.
- Патент на изобретение № 2 094 705 /Камера сгорания авиационного или энергетического газотурбинного двигателя. Сигалов Ю. В., Рудаков О. А., Ефимов Е. В., Гурский С. Э., Митрофанов В. А., Федоров A.M.
- Патент на изобретение № 2 145 669 /Способ работы газотурбинного двигателя и огневой блок для сжигания смеси топлив. Саркисов А. А., Митрофанов В. А., Рудаков О. А., Саливон Н. Д., Сигалов Ю.В.I
- Патент на изобретение № 2 171 432/Камера сгорания с оптимальным числом форсунок. Саркисов А. А., Митрофанов В. А., Рудаков О. А., Саливон Н. Д., Сигалов Ю.В.