Повышение эффективности сборки и разборки резьбовых соединений путем применения ультразвуковых колебаний
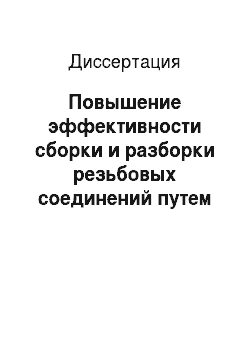
Повышение качества выпускаемой продукции, эффективности производства и создание конкурентно-способной продукции в условиях рыночной экономики неразрывно связаны с разработкой новых технологий, в том числе основанных на введение дополнительных видов энергии в зону формообразования и сборки. К числу эффективных методов сборки относится различные технологические процессы с применением ультразвука… Читать ещё >
Содержание
- 1. Повышение качества сборки соединений. Общее состояние вопроса и актуальность проблемы
- 1. 1. Основные направления повышения качества резьбовых соединений
- 1. 2. Сборка резьбовых соединений
- 1. 2. 1. Нагрузки в резьбовых соединениях
- 1. 3. Применение колебаний для интенсификации процессов сборки
- 2. Экспериментальное исследование процесса сборки резьбовых соединений в ультразвуковом поле
- 2. 1. Методика статистической обработки результатов экспериментов
- 2. 2. Оборудование, контрольно-измерительная аппаратура, образцы для исследований
- 2. 3. Исследование влияния ультразвука на процесс сборки и разборки резьбовых соединений
- Выводы по главе
- 3. Разработка конечно-элементной модели процесса ультразвуковой сборки резьбовых соединений
- 3. 1. Методика применения метода конечных элементов
- 3. 2. Матричная форма записи основных соотношений теории упругости
- 3. 3. Основные этапы практической реализации метода конечных элементов (МКЭ)
- 3. 4. Построение конечно-элементной модели резьбовых соединений
- 3. 5. Методика проведение виртуальных экспериментов сборки соединений на программном комплексе ANSYS
- 3. 5. 1. Методика проведение виртуальных экспериментов сборки соединений двух деталей при помощи резьбового соединения болт-гайкана программном комплексе ANSYS
- 3. 5. 2. Методика проведение виртуальных экспериментов сборки соединений двух деталей при помощи болтана программном комплексе ANSYS
- 4. 1. Управление качеством резьбовых соединений
- 4. 2. Разработка и внедрение устройств для реализации процесса ультразвуковой сборки
Повышение эффективности сборки и разборки резьбовых соединений путем применения ультразвуковых колебаний (реферат, курсовая, диплом, контрольная)
Повышение качества выпускаемой продукции, эффективности производства и создание конкурентно-способной продукции в условиях рыночной экономики неразрывно связаны с разработкой новых технологий, в том числе основанных на введение дополнительных видов энергии в зону формообразования и сборки. К числу эффективных методов сборки относится различные технологические процессы с применением ультразвука. Ультразвуковые методы сборки позволяют получить ряд новых неаддитивных эффектов, способствующих повышению производительности и качества.
Вследствие отклонений размеров, формы, относительного расположения и других параметров состояния поверхностей деталей при сборке приходится решать комплекс проблем, связанных с достижением точности замыкающего звена размерной цепи. Задача еще более усложняется при приложении рабочих нагрузок на соединение, поскольку образованные сборкой размерные связи нарушаются из-за контактных перемещений поверхностей сопряжения, что влечет за собой снижение эксплуатационных показателей соединений. Важная роль в достижении точности замыкающего звена размерной цепи принадлежит резьбовым соединениям.
Большой вклад в развитие науки о сборке внесли ученые Б. С. Балакшин, В. П. Бобров, Л. И. Волчкевич, А. Г. Герасимов, А. А. Гусев,.
A.М.Дальский, Д. Я. Ильинский, Н. И. Камышный, И. И. Капустин, И. М. Колесов, В. В. Косилов, Л. Н. Кошкин, М. С. Лебедовский, А. Н. Малов, К. Я. Муценек, М. ПНовиков, Г. Я. Пановко, А. Н. Рабинович, Б. Л. Штриков,.
B.А.Яхимович и др.
В то же время необходимо отметить, что функциональные параметры машин и приборов во многом определяются показателями качества деталей, образующих соединение. Эта взаимосвязь получила глубокое осмысление благодаря работам А. П. Бабичева, И.В.Дунина-Барковского, Б. А. Кравченко,.
А.А.Маталина, Д. Д. Папшева, А. С. Проникова, Э. В. Рыжова, А. М. Сулимы,.
A.Г.Суслова, Л. В. Худобина, Ю. Г. Шнейдера, А. В. Якимова, П. И. Ящерицина и др. и получила дальнейшее развитие в исследованиях Б. М. Базрова,.
B.Г.Митрофанова, Ю. С. Соломенцева и др., направленных на достижение требуемых показателей изделий путем управления технологическими процессами средствами автоматизации. При этом в основе большинства технологических работ лежат фундаментальные исследования Д. Н. Гаркунова, Н. Б. Демкина, М. Н. Добычина, И. В. Крагельского, B.C. Комбалова, Н. М. Михина, А. В. Чичинадзе и др. по проблеме контактного взаимодействия поверхностей сопряжения.
Вмести с тем, несмотря на известные достоинства и большой интерес, проявляемый к ультразвуковой сборке в нашей стране и за рубежом, ее физико-технологические особенности и область рационального применения раскрыты еще недостаточно и требуют дальнейшего углубленного изучения. Целью настоящей работы являлось повышение эффективности сборки резьбовых соединений путем применения ультразвука на базе теоретических и экспериментальных исследований физического механизма процесса.
Для достижения поставленной цели в работе использованы основные теоретические положения технологии машиностроения, программный пакет ANSYS, основанный на методе конечных элементов. В экспериментальных исследованиях применена методика математического планирования эксперимента. Опыты проведены с использованием специальных и стандартных измерительных устройств на образцах и натурных изделиях. Обработка и анализ экспериментальных данных проводились с использованием ПЭВМ.
Достоверность научных положений, выводов и заключений обусловлена совпадением результатов численных расчетов параметров процесса, напряженно-деформированного состояния соединения с данными экспериментальных исследований и расчетом по известным зависимостям.
Проведенными исследованиями выявлен механизм воздействия ультразвука на процесс сборки резьбовых соединений, их прочность.
С помощью программного пакета ANSYS разработана конечно-элементная модель процесса ультразвуковой сборки резьбовых соединений, позволяющая производить комплексный анализ процесса, включая: расчет сил, возникающих при сборке резьбового соединенияопределение напряженно-деформированного состояние резьбовых соединенийопределение контактных давлений, возникающих при сборке резьбового соединения.
Определены оптимальные параметры процесса ультразвуковой сборки по критериям работоспособности резьбовых соединений и силовым параметрам процесса сборки.
Разработана и внедрена технология ультразвуковой сборки и разборки резьбовых соединений, позволившая существенно снизить силовые параметры процесса и повысить эксплуатационные показатели соединений.
Разработаны методики расчета напряженно-деформированного состояния резьбовых соединений.
Основные положения, выносимые на защиту:
Общие и частные методики моделирования элементов ультразвуковой сборки, позволяющие научно обоснованно подойти к выявлению механизма воздействия ультразвука на основные параметры процесса.
Выявленные теоретическими и экспериментальными исследованиями основные особенности механики формирования контактных связей в соединении.
Разработанные конечно-элементные модели процесса ультразвуковой сборки резьбовых соединенийформирования напряженно-деформированного состояния соединения.
Автор приносит свою глубокую признательность научному руководителю доктору технических наук профессору Штрикову Б. Л. за повседневное внимание и руководство работой, а также коллективу кафедры «Автоматизация технологических процессов в машиностроении» Самарского Государственного технического университета за помощь, оказанную при выполнении исследований.
ОБЩИЕ ВЫВОДЫ.
1. В результате комплексных теоретико-экспериментальных исследований решена актуальная задача, направленная на дальнейшее повышение эффективности сборки и разборки резьбовых соединений, с помощью применения ультразвуковых колебаний.
2. Разработана методика и оборудование для исследования ультразвуковой сборки и разборки резьбовых соединений в широком диапазоне прикладываемых моментов и ультразвуковых параметров.
3. На основе приведенных исследований выявлен физический механизм воздействия ультразвука на процессы сборки и разборки резьбовых соединений, позволяющий сделать вывод, что напряженность процессов и выходные параметры соединений определяются количеством акустической энергии, вводимой в зону сопряжения, и схемой ее введения. Установлено, что общими закономерностями при ультразвуковой сборке являются снижение сил и моментов, необходимых для образования соединений, и их развинчивания, а также повышение прочности при свинчивании.
4. Установлено, что возникающее при затяжке резьбового соединения с ультразвуком дополнительное осевое перемещение в резьбе равно амплитуде ультразвуковых колебаний, накладываемых на болт и объясняется изменением его длины. Компенсация изменения размеров болта производится дополнительным его доворотом. При сообщении болту крутильных колебаний эта закономерность сохраняется, но в этом случае величина доворота зависит и от угла крутильных колебаний.
5. Предложен механизм воздействия ультразвука на процесс свинчивания резьбовых соединений. Снижение напряженности процесса происходит благодаря изменению условий контактного взаимодействия поверхностей и снижению сопротивления пластическому деформированию, а причинами повышения прочности являются увеличение фактической площади контакта как за счет дискретности контактирования поверхностей при сборке, так и в результате образования продуктов износа, заполняющих микрорельеф, и интенсификации процесса образования адгезионных связей.
6. Установлено, что применение ультразвуковых колебаний повышает эффективность разборки резьбовых соединений и в случае, когда в соединении присутствуют различные вида наполнители, повышающие его прочность. В зависимости от вида наполнителя момент развинчивания снижается в 5−6 раз.
7. Установлено, что при разборке резьбовых соединений наложение на деталь колебаний приводит к ее упругим продольным деформациям на величину амплитуды ?, и поперечным деформациям диаметра на величину где цкоэффициент Пуассона. Это способствует активному разрушению коррозионных и адгезионных связей, а изменение диаметральных размеров существенно уменьшает момент необходимый для развинчивания.
8. Разработаны конечно-элементные модели соединения двух деталей с использованием резьбового соединения «болт-гайка» при обычной сборке и сборке с продольными ультразвуковыми колебаниями, а также конечно-элементные модели соединения двух деталей с помощью болта.
9. Показано, что использование в процессе сборки ультразвуковых колебаний приводит к возрастанию максимальных контактных давлений в зонах контакта, и как следствие повышение прочности соединения. Установлено, что величина контактных давлений пропорционально зависит от амплитуды колебаний.
Ю.Установлены закономерности изменения давлений в зонах контакта при сборке резьбовых соединений. Определены зоны, в которых устанавливаются максимальные и минимальные контактные давления. Показано влияние геометрических параметров резьбовых соединений на величину контактных давлений и прочности соединений.
И.Разработан комплекс конструкторско — технологических решений и рекомендаций, направленных на повышение эффективности ультразвука при сборке и дающих возможность управления качеством соединений, в том числе и средствами автоматизации, что позволило внедрить в производство ряд новых технологических процессов ультразвуковой сборки и оборудование для их реализации.
Список литературы
- Автоматизация проектирования технологических процессов в машиностроении / Под общ. ред. Капустина Н. М. -М.: Машиностроение, 1985.-304C.
- Агранат Б.А., Банширов В. И., Китайгородский Ю. И. и др. Ультразвуковая технология. -М.: Машиностроение, 1974.-564 с.
- А.с. 144 8564(СССР) Устройство для сборки резьбовых соединений типа вал-втулка / Николаев В. А., Куликов М. А., Штриков Б.Л.
- А.с. 150 5770(СССР) Способ сборки резьбовых соединений / Николаев В. А., Куликов М. А., Штриков Б.Л.
- А.с. 155 3303(СССР) Способ сборки деталей/ Бакшис Б. П., Повеление А. Б.Б., Скучас И.Ю.
- А.с. 166 4494(СССР) Способ сборки деталей типа вал-втулка/ Николаев В. А., Куликов М. А., Штриков Б.Л.
- А.с. 168 9009(СССР) Устройство для сборки соединений/ Николаев В. А., Куликов М. А., Штриков Б.Л.
- А.с. 170 0352(СССР) Способ контроля параметров резьбы/ Николаев В. А., Куликов М. А., Штриков Б.Л.
- А.с. 1 700 7874(СССР) Способ сборки резьбовых соединений/ Николаев В. А., Куликов М. А., Штриков Б.Л.
- А.с. 173 1568(СССР) Способ сборки прессовых соединений типа вал-втулка/ Николаев В. А., Куликов М. А., Штриков Б.Л.
- Балакшин Б.С. Теория и практика технологии машиностроения: В 2-х кн. -М.: Машиностроение .-1982- Кн.1. Технология станкостроения, 1982. 239с.
- Беляев. Н.М. Сопротивление материалов.-М.Машиностроение.-1971.-856 с.
- Бернштейн М.Л., Займовский В. А. Механические свойства металлов. -М.: Металлургия, 1979.-496 с.
- Берозашвили Г. В., Гудушаури Э. Г., Пановко Г. Я. Напрессовка деталей в условиях дополнительных вибраций //Вестник машиностроения.-1986.-№ 2.-с.51−53.
- Биргер И.А., Иосилевич Г. Б. Детали машин: Справочник М.: Машиностроение, 1968, 308 с.
- Биргер И.А., Иосилевич Г. Б. Резьбовые соединения.-М: Машиностроение, 1973 .-256 с.
- Браславец А.В., Савченко Н. Ф. Интенсификация процесса пластического деформирования металлов за счет наложения ультразвуковых колебаний //Тезисы докладов конференции «Прогрессивные технологические процессы в машиностроении.- Харьков: ХПИ.-1990.-С.11.
- Ваганов И.К. Нелинейные эффекты в ультразвуковой обработке. -Минск: Наука и техника, 1987.-158 с.
- Вилль В.И. Сварка металлов трением. -JT. Машиностроение, 1970,-176 с.
- Волосатов В.А. Ультразвуковая обработка.-Л.:Лениз-дат, 1973.-284 с.
- Гельфанд М.Л., Ципенюк Я. И., Кузнецов O.K. Сборка резьбовых соединений. М.Машиностроение.-1978.-108 с.
- Герасимов А.Г. Точность сборочных автоматов. -М. Машиностроение, 1967.-96 с.
- Гершгал Д.А., Фридман В. М. Ультразвуковая аппаратура промышленного назначения .-М.:3нергия, 1967.-264 с.
- Гибкие производственные системы сборки/ Алексеев П. У., Герасимов А. Г., Давыденко З. П. и др. -Под общ. ред. Федотова А.И.-Л.Машиностроение.-1989.-349 с.
- Горячева И.Г., Добычин М. Н. Контактные задачи в трибологии. -М. Машиностроение.-1988.-256 с.
- Гусев А.А. Адаптивные устройства сборочных машин. -М.: Машиностроение.-1979.-207 с.
- Гусев А.А. Основные принципы построения сборочных гибких производственных систем. М. Машиностроение.-19.88,-68с.28,29.30,31