Комплексная технология формирования поверхностных элементов на плоских и фасонных поверхностях электрофизикохимическими методами
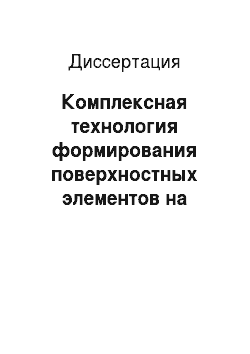
Комбинацией схем формообразования можно добиться приемлемой скорости удаления шлама. Например, при использовании схемы обката электродом-инструментом по поверхности решается задача промывки межэлектродного зазора за время обработки в отличие от схем единовременного формообразования. При этом возникает погрешность формообразования за счет накопления погрешностей перемещений. В данном случае… Читать ещё >
Содержание
- I. АНАЛИЗ СОСТОЯНИЯ ВОПРОСА. АНАЛИЗ ОБЪЕКТА ИССЛЕДОВАНИЯ. ПОСТАНОВКА ЗАДАЧИ ИССЛЕДОВАНИЯ
- 1. 1. Методы получения поверхностных элементов
- 1. 1. 1. Механические методы формирования поверхностных элементов на плоских поверхностях деталей
- 1. 1. 2. Методы формирования поверхностных элементов с использованием лазерного излучения
- 1. 1. 3. Химические и электрохимические методы формирования поверхностных элементов
- 1. 1. 4. Методы формирования с использованием масок на основе бумажных и полимерных защитных материалов
- 1. 1. 5. Методы формирования поверхностных элементов с масками на основе фоторезистивных материалов
- 1. 2. Сравнение методов формирования поверхностных элементов
- 1. 3. Методы формирования поверхностных элементов с масками на основе лакокрасочных и порошковых покрытий
- 1. 4. Методы формирования поверхностных элементов с масками на основе порошковых красок с их последующей полимеризацией по заданной программе или готовой маске
- 1. 5. Методы формирования поверхностных элементов с масками на основе порошковых красок с их последующим испарением по заданной программе
- 1. 6. Обзор методов и оборудования для формирования диэлектрических поверхностных слоев
- 1. 6. 1. Методы формирования однородной полимерной композиции с применением порошковых красок
- 1. 6. 2. Методы формирования защитной маски воздействием лазерного излучения на полимерную пленку
- 1. 1. Методы получения поверхностных элементов
- 2. 1. Математическая модель распределение тепловых полей в тонкопленочном диэлектрическом слое
- 2. 2. Анализ результатов математического моделирования
- 2. 3. Электрохимическое формообразование поверхностных элементов с использованием защитных масок произвольной геометрии
- 2. 4. Выводы по главе
- 3. 1. Разработка методик проведения экспериментальных работ
- 3. 2. Экспериментальные исследования процесса формирования равнотолщинного диэлектрического слоя методом электростатического напыления полимерных композиций
- 3. 2. 1. Методика экспериментальных исследований процесса формирования равнотолщинного диэлектрического слоя
- 3. 2. 2. Экспериментальное оборудование
- 3. 2. 3. Результаты экспериментальных исследований 69 З. ЗЭкспериментальные исследования процесса формирования защитных масок в диэлектрических слоях на неплоских поверхностях
- 3. 3. 1. Методика экспериментальных исследований процесса формирования защитных масок
- 3. 3. 2. Результаты экспериментальных исследований 73 3.4Методика экспериментальных исследований процесса формирования защитных масок с использованием трафаретных предмасок
- 3. 5. Экспериментальные исследования процесса анодного растворения материала с использованием защитных масок
- 3. 5. 1. Методика экспериментальных исследований процесса анодного растворения
- 3. 5. 2. Экспериментальное оборудование
- 3. 5. 3. Результаты экспериментальных исследований
- 3. 5. 4. Анализ параметров сформированных поверхностных элементов на различных поверхностях
- 3. 6. 1. Методика исследования процесса глубокого анодного
- 3. 6. 2. Экспериментальное оборудование
- 3. 6. 3. Результаты экспериментальных исследований 95 3.7Выводы по главе 97 IV. РАЗРАБОТКА И ВНЕДРЕНИЕ ТЕХНОЛОГИЙ И
- 4. 1. Технологическая установка ЛУФМ
- 4. 1. 1. Механизм слежения за эквидистантностью к поверхности
- 4. 1. 2. Блок накачки лазерного диода
- 4. 1. 3. Система сопряжения стоек ЧПУ с современными вычислительными комплексами
- 4. 1. 4. Специфика написания программного обеспечения для управления стойками ЧПУ современными вычислительными комплексами
- 4. 2. Экспериментальная установка для процесса глубокого анодного растворения
- 4. 3. Разработка технологического регламента формирования поверхностных элементов с использованием трафаретных предмасок
- 4. 4. Разработка технологического регламента формирования поверхностных элементов с использованием процесса припекания защитного слоя
- 4. 5. Выводы по главе
Комплексная технология формирования поверхностных элементов на плоских и фасонных поверхностях электрофизикохимическими методами (реферат, курсовая, диплом, контрольная)
Тенденция постоянной миниатюризации оборудования и соответствующего повышения точности его изготовления обусловила переход значительной части производства на гибкие производственные линии. Подобные комплексы способны обеспечивать воспроизведение геометрических размеров деталей до величин порядка нескольких десятков микрометров при широкой выпускаемой гамме изделий. Создание формующей оснастки для изготовления таких изделий как корпуса и фурнитура сотовых телефонов, плееров, цифровых камер и прочих изделий объясняет необходимость не только точности исполнения, но и быстрой смены производимой номенклатуры в зависимости от требований рынка сбыта.
Важной технологической задачей является воспроизведение на поверхностях деталей заданных поверхностных элементов для придания определенной фактуры. Это необходимо для повышения качественных показателей поверхностного слоя и расширения области применения текстурированных поверхностей.
Решение данной технологической задачи позволяет получить более долговечные в использовании поверхности с улучшенными эксплуатационными характеристиками: меньшая запыливаемость, стойкость к образованию на поверхности жировых пятен от контакта с руками, а также поверхностей, имитирующих натуральные и синтетические материалы.
Около 5 лет назад воспроизведение элементов на поверхностях деталей осуществлялось изготовлением ручными способами защитной маски на основе полимерных материалов и химическим травлением (итальянская технология по созданию элементов на поверхности пресс-форм) или с использованием труда профессионального гравера.
Для новых типов приборов точность воспроизведения поверхностных элементов должна лежать в диапазоне десятков микрометров, что является непреодолимой проблемой для всех ручных операций, требуемая же себестоимость обработки детали должна быть минимальной. Одновременно с этим возникает проблема утилизации химических реактивов, используемых в процессе переноса рисунка защитной маски с трафарета на металлические и иные поверхности.
Использование ручных операций в процессе формировании защитных масок резко ограничивает диапазон поверхностей, на которых возможно создание поверхностных элементов. Дальнейшее развитие данной технологии необоснованно, поскольку это противоречит концепции построения современных автоматизированных производственных линий, в которых участие человека в технологическом процессе сведено к минимуму.
Однако наука не стоит на месте, и поставленная технологами задача была решена следующим образом. Было предложено на поверхность детали наносить защитный слой, обладающий свойством полимеризоваться (или разрушаться) под действием излучения определенной длины волны (например, излучения ультрафиолетовой части спектра) — так называемый фоторезист. Если экспонирование фоторезиста вести через заранее созданную маску, то на поверхности создается слой, комбинацией пробельных и не пробельных элементов которого образуется защитная маска заданной конфигурации. В дальнейшем через эту защитную маску для формообразования на поверхности можно использовать такие процессы, как химическое, электрохимическое растворение материала, осаждение материала, основанное на химических (гальваника, химия) или физических (ионная имплантация, вакуумное осаждение) процессах. При этом одним из необходимых условий является инертность материала защитной маски к осуществляемому процессу формообразования и среде его протекания.
Использование методов электрохимической обработки с применением фоторезистивных или других слоев, наносимых на поверхность в виде защитных масок, делает затруднительным или невозможным процесс формирования поверхностных элементов на сложных криволинейных поверхностях, в том числе, имеющих небольшие размеры (площадью менее 10 мм) и сферических поверхностях. Это обусловлено сложностью формирования равномерного слоя фоторезиста, поскольку раскрой защитного покрытия и укладку фотошаблонов необходимо вести по сложной поверхности, что является трудоемкой задачей. К перечисленному выше следует добавить недостаточную точность воспроизведения заданного рисунка защитной маской после применения фотолитографических методов, поскольку сложно обеспечить равномерность излучения, идущего от источника на сложную криволинейную поверхность.
Одно из ведущих мест в области формирования поверхностных элементов занимают методы, основанные на удалении материала (испарение под действием лазерного излучения, электроэрозионная и электрохимическая обработка). Точность воспроизведения геометрии данными методами составляет десятки микрометров. Применение лазерной обработки позволяет расширить диапазон обрабатываемых материалов (полимеры и керамика).
Данным методам присущ ряд недостатков. Например, для лазерной обработки это термическая модификация поверхности, приводящая к накоплению напряжений в поверхностном слое материала и, как следствие, более низкая долговечность (что существенно, например, для формующих поверхностей оснастки). К тому же существует целый ряд материалов, для которого лазерная обработка неприменима по физическим характеристикам или технологическим показателям.
Для электроэрозионной обработки характерным недостатком является износ электрода-инструмента и, как следствие, невозможность серийного производства. Электрохимическая и электроэрозионная обработка требуют наличия в межэлектродном промежутке циркуляции рабочей среды для удаления продуктов процесса (шлама), что затруднительно обеспечить в случае сложных криволинейных поверхностей.
Комбинацией схем формообразования можно добиться приемлемой скорости удаления шлама. Например, при использовании схемы обката электродом-инструментом по поверхности решается задача промывки межэлектродного зазора за время обработки в отличие от схем единовременного формообразования. При этом возникает погрешность формообразования за счет накопления погрешностей перемещений. В данном случае начинают влиять такие факторы, как точность механических систем, осуществляющих подвод и отвод электрода-инструмента, согласованность электрохимических (электроэрозионных) и механических процессов.
Применение схемы точечного электрохимического (электроэрозионного) формообразования позволяет избежать сложностей при удалении из межэлектродного зазора шлама и использовать ее для формирования заданной геометрии на сложных поверхностях. У данного метода существует ряд недостатков: низкая производительность в случае применения электрода-инструмента малого диаметра (до 100 и менее микрометров) — существенные трудности при закреплении подобного рода электродоввоздействие на электрод тепловых полей и силовых факторов при протекании процесса.
Известна еще целая группа методов формирования элементов на поверхности, не имеющая большого распространения в машиностроении и поэтому не подвергающаяся анализу в данной работе.
Целью настоящей работы является создание технологии и методов комбинированного воздействия на материал для формирования поверхностных элементов на плоских и фасонных поверхностях деталей различного назначения.
Работа состоит из следующих основных частей:
— анализ методов и технологии получения поверхностных элементов на плоских и фасонных поверхностях;
— теоретические исследования возможностей формирования защитной маски лазерным излучениемтеоретические исследования электрохимического формообразования поверхностных элементов на различных поверхностяхэкспериментальные исследования формирования поверхностных элементов на опытных образцах деталейразработка рекомендаций по практическому использованию электрохимического формообразования поверхностных элементов.
ОБЩИЕ ВЫВОДЫ.
На основе анализа возможных методов формообразования поверхностных элементов предложен метод электрохимического формообразования с предварительным формированием защитных масок из диэлектрического слоя, сформированного на поверхности деталей с использованием трафаретных предмасок или процессов напыления мелкодисперсных порошковых композиций с лазерным формированием рисунка. Выполнены теоретические исследования по обоснованию технологических рекомендаций для процессов формирования диэлектрических слоев на плоских и фасонных поверхностях деталей. Для создания равнотолщинного диэлектрического слоя 20 — 30 мкм, необходимого для дальнейшего формирования на его основе защитной маски для процесса анодного растворения рекомендовано использовать рабочее напряжение 40 кВ на электростатическом распылителе. Выполнены теоретические исследования по обоснованию технологических рекомендаций для процессов формирования защитных масок в диэлектрических слоях с различной плотностью элементов, предварительно сформированных на плоских и фасонных поверхностях. Установлено, что приемлемую точность обеспечивает система, оснащенная лазерным диодом мощностью 1 Вт и с фокальным пятном 100×150 мкм.
Теоретически выявлены изменения геометрических размеров формируемых элементов на поверхностях деталей после применения метода анодного растворения материала детали с шириной пробельных участков от 0,1 мм до 10 мм и выше. Полученные зависимости можно использовать для прогнозирования величин подтравливания или коррекции исходной защитной маски с целью увеличения точности воспроизведения формы элементов.
Экспериментально исследовано влияние технологических показателей на процессы анодного растворения материала деталей с использованием диэлектрических защитных масок. Установлено, что для формирования поверхностных элементов на деталях из стали Х18Н10Т с высотой не более 200 — 300 мкм желательно использовать раствор электролита низкой концентрации (5 — 10% NaCl) и плотности тока выше 0,1 А/мм2. Для формирования поверхностных элементов с высотой менее 100 — 200 мкм и высоким требованием к четкости края необходимо использовать концентрированный раствор электролита (10 — 15% NaCl) и плотность тока выше 0,2 А/мм. Для формирования глубоких поверхностных элементов (более 2 мм) на деталях из стали 20X13 рекомендовано использование электролита 10% NaCl и плотности тока 0,01 — 0,05 А/мм2. Разработано экспериментальное оборудование и технология для формирования защитных диэлектрических масок на плоских и фасонных поверхностях. На оборудовании возможно вести обработку деталей с габаритами 150×250×50 мм с точностью 50 мкм.
Разработано экспериментальное оборудование и технология для электрохимической обработки поверхностей деталей с целью получения глубоких (до 2 мм) поверхностных элементов с использованием диэлектрических защитных масок.
Список литературы
- ГОСТ 24 773–81. Поверхности с регулярным микрорельефом. Классификация, параметры и характеристики.
- ГОСТ 2789–73. Шероховатость поверхности. Параметры и характеристики.
- Шнейдер Ю.Г. Эксплуатационные свойства деталей с регулярным микрорельефом. Л.: Машиностроение, Ленингр. отд-е, 1982. — 248с.
- Способы получения графических изображений на промышленных изделиях. Методические рекомендации / ВНИИТЭ- Т. А. Печкова и др. -М., 1980.-64 с.
- М. Datta, D. Landolt. Fundamental aspects and applications of electrochemical fabrication // Electrochimica Acta 45 (2000) 2535−2558.
- D. Landolt, P.-F. Chauvy, O.Zinger. Electrochemical micromachining, polishing and surface structuring of metals: fundamental aspects and new developments // Electrochimica Acta 48 (2003) 3185−3201.
- Басов Н.И., Казанков Ю. В., Любартович B.A. Расчет и конструирование оборудования для производства и переработки полимерных материалов: Учеб. для вузов. М.: Химия, 1986. — 488с.
- Бортников В.Г. основы технологии переработки пластических масс: Учебное пособие для вузов. Л.: Химия, 1983. — 304с.
- Филатов В.И., Корсаков В. Д. Технологическая подготовка процессов формования изделий из пластмасс. Л.: Политехника, 1991. — 352с.
- Красников В.Ф. Технология миниатюрных изделий. М.: «Машиностроение», 1976.-327с.
- Гецас С.И. Декоративная обработка изделий из пластмасс. Л.- Химия, 1978.-120с.
- Пантелеев А.П., Швецов Ю. М., Горячев И. А. Справочник по проектированию оснастки для переработки пластмасс. М.: Машиностроение, 1986. — 400с.
- Филатов В.И. Технологическая подготовка производства пластмассовых изделий. Л.: Машиностроение, 1976. — 272с.
- Татаринов В.Н. Электрохимическое формообразование регулярныхрельефов на деталях инструментальной оснастки: Автореф. Дис. к-та техн. наук: 05.03.01/ В.Н. Татаринов- ТулГУ Тула., 2004. 19с.
- Мишенин Д.И. Электрохимическая размерная обработка методом обката при сверхмалых межэлектродных зазорах в пленке электролита: Автореф. Дис. к-та техн. наук: 05.03.01/ Д.И. Мишенин- ТулГУ Тула., 2003. 20с.
- Дунин-Барковский И.В., Карташова А. Н. Измерение и анализ шероховатости, волнистости и некруглости поверхности. — М.: Машиностроение, 1978. 232с.
- Применение лазеров / под ред. М. Росса. М.: Мир, 1974. — 445с.
- Суминов В.М. Обработка деталей лучом лазера. М.: Машинотсроение, 1969.-220с.
- Справочник по лазерам / Под ред. A.M. Прохорова. М.: Советское радио, 1978. т.1, т.2.
- Григорьянц А.Г. Достижения и перспективы развития лазерной технологии // Сварочное производство. 1996. № 8. С. 2−4.
- Коваленко B.C. Лазерная технология: Учебник, — К.: Выща шк. Головное изд-во, 1989.- 280 с.
- Углов А.А. Состояние и перспективы лазерной технологии // Физика ихимия обработки материалов. 1992. № 4. С. 32−42.
- Давыдов А.Д. Лазерно-электрохимическая обработка металлов / Электрохимия, 1994, т. 30, № 8, с. 965−976.
- Лазерная и электронно-лучевая обработка материалов: Справочник / Н. Н. Рыкалин, А. А. Углов, И. В. Зуев, А. Н. Кокора. М.: Машиностроение, 1985. — 496 с.
- Лазерная поверхностная обработка металлов и сплавов. / Леонтьев П. А., Чеканова Н. Т., Хан М. Г. М.: Металлургия, 1986 г. — 142 с.
- Лазерная техника и технология. В 7 кн. Кн 7. Лазерная резка металлов: Учеб. Пособие для вузов / Григорьянц А. Г., Соколов А.А.- Под ред. Григорьянца А. Г. М.: Высш. Шк., 1988. — 127 с.
- Лазерная техника и технология. В 7 кн. Кн 3. Методы поверхностной лазерной обработки: Учеб. Пособие для вузов / Григорьянц А. Г., Сафонов А.Н.- Под ред. Григорьянца А. Г-М.: Высш. Шк., 1988.-191 с.
- Лазерная техника и технология. В 7 кн. Кн 6. Основы лазерного термоупрочнения сплавов: Учеб. Пособие для вузов / Григорьянц А. Г., Сафонов А.Н.- Под ред. Григорьянца А.Г.-М.: Высш. Шк., 1988.-159 с.
- Горленко О.А., Михеенко Т. А. Свойства поверхностей упрочненных лазерных обработкой /Физика и химия обработки материалов, 1983, № 6, с. 18−23
- Сафонов А.Н. Производство и использование лазерной техники для обработки материалов. // Сварочное производство. 1997. № 2. С.22−26.
- Рэди Дж. Промышленное применение лазеров. М.: Мир, 1981. — 638 с.
- Смоленцев В.П., Смоленцев Г. П., Садыков З. Б. Электрохимическое маркирование деталей / В. П. Смоленцев, Г. П. Смоленцев, З. Б. Садыков. М.: Машиностроение, 1983. — 72 е., ил.
- Румянцев Е.М., Давыдов А. Д. Технология электрохимической обработки металлов: Учеб. пособие для техн. вузов. М.: Высш. шк, 1984- 159 с.: ил.
- Шалкаускас М., Вашкялис А. Химическая металлизация пластмасс. -Л.: Химия, 1977.- 168с.
- Садаков Г. А., Дюбанкова Э. Н. Технология гальванопластики в часовой промышленности // Гальванотехника и обработка поверхности. 1994. -т.З, № 3. — с.38−40.
- Гнидина И.В. Импульсное электролитическое формование микрорельефов // Дисс.. канд. техн. наук. Тула, 1999. — 170с.
- Коваленко B.C. Технология и оборудование электрофизических и электрохимических методов обработки материалов. Киев: Вища шк. 1983.- 176.
- Электроимпульсная обработка металлов / A.JI. Лившиц, А. Т. Кравец, И. С. Рогачев, А. Б. Сосенко. М.: Машиностроение, 1967. — 295с.
- Попилов Д.Я. Электрофизическая и электрохимическая обработка материалов: Справочник 2-е изд., перераб. и доп. — М.: Машиностроение, 1982.-400с.
- Седыкин Ф.В. Размерная электрохимическая обработка деталей машин. -М., 1976.
- Подураев В.Н., Камалов B.C. Физико-химические методы обработки. -М.: Машиностроение, 1973. 346с.
- Петров Ю.Н. и др. Основы повышения точности электрохимического формообразования. Кишинев, Штиница, 1977. — 153с.
- Мороз И.И., Алексеев Г. А., Водяницкий О. А. и др. Электрохимическая обработка металлов. М., 1969. — 208с.
- Де Барр А. Е., Оливер Д. А. Электрохимическая обработка (пер. с англ.). -М., 1973.-184с.
- Головачев В.А. и др. Электрохимическая размерная обработка деталей сложной формы. М.: Машиностроение, 1969. — 198с.
- Справочник по электрохимическим и электрофизическим методам обработки // Г. Л. Амитан, И. А. Байсупов, Ю. М. Барон и др.- под общей ред. В. А. Волосатова.-Л.: Машиностроение. Ленингр. отд-е, 1988.-719с.
- Размерная электрохимическая обработка металлов: Учеб пособие для студентов вузов / Б. А. Артамонов, A.JI. Винницкий, Ю. С. Волков, А.В. Глазков- Под ред. А. В. Глазкова. М.: Высш. школа, 1978. — 336с.
- Станкеев А. А. Станкеева И.Н. Новые методы маркирования деталей. Тула, Приокское кн. изд., 1964. 36 с.
- Смоленцев В.П. и др. Электрохимическое маркирование деталей / В. П. Смоленцев, Г. П. Смоленцев, З. Б. Садыков. М.: Машиностроение, 1983.-72 с.
- Садыков З.Б. Регулирование процесса электрохимической обработки неподвижными электродами. В кн.: Размерная ЭХО деталей машин., Тула, 1975, ч. 2, с. 23−25.
- Волков Ю.С., Лившиц А. Л. Введение в теорию размерного формообразования электрофизико-химическими методами. Киев, 1978.
- Клоков В.В. Электрохимическое формообразование. Казань, 1984.
- Высокоскоростное электрохимическое формообразование / А. Д. Давыдов, Е. Козак. М.: Наука, 1990. — 272 с.
- М. Datta, D. Landolt. Fundamental aspects and applications of electrochemical fabrication // Electrochimica Acta 45 (2000) 2535−2558.
- D. Landolt, P.-F. Chauvy, O.Zinger. Electrochemical micromachining, polishing and surface structuring of metals: fundamental aspects and new developments // Electrochimica Acta 48 (2003) 3185−3201.
- Вейко В.П. Лазерная обработка пленочных элементов. Л.: Машиностроение, Ленингр. Отд-ние, 1986. — 248 е., ил.
- Вейко В. П. Контурно-проекционный метод лазерной обработки материалов. — Квантовая электрон., 1978, т. 5, № 12, с. 2602— 2610.
- Вейко В. П. Лазерная обработка пленочных элементов. — Тр. ЛИТМО. Л.: 1980, с. 36—45.
- Вейко В. П. Лазерная обработка тонкопленочных элементов: Материалы школы «Применение лазеров в промышленности». Л.: ЛДНТП, 1974, с. 3—11.
- Вейко В. П. Опыт внедрения лазерной обработки тонких пленок в микроэлектронике. Л.: ЛДНТП, 1977. 32 с.
- Вейко В. П., Кайданов А. И., Яковлев Е. Б. Двухфазная модель разрушения поглощающих пленок мощными световыми импульсами. — Квантовая электрон., 1980, т. 7, № 1, с. 34—41.
- Вейко В. П., Кокора А. Н., Либенсон М. Н. Экспериментальная проверка распределения температур в зоне воздействия излучения ОКГ па металл. — Докл. АН СССР, 1968, т. 179, № 1,с. 68—71.
- Вейко В. П., Котлецов Б. Н., Либенсон М. Н. Лазерная литография. Л.: Знание, 1971. 48 с.
- Вейко В. П., Котов Г. А., Либенсон М. Н. Окисление тонких пленок хрома при нагревании импульсным лазерным излучением. — Электрон, техн., сер. 3, 1973, вып. 4, с. 48—56.
- Вейко В. П., Котов Г. А., Либенсон М. Н. Термическое действие лазерного излучения на некоторые полимерные материалы. — Физика и химия обраб. материалов, 1973, № 2, с. 16—18.
- Вейко В. П., Котов Г. А., Шандыбина Г. Д. Термохимический метод лазерной обработки тонких металлических пленок. — Тр. ЛИТМО. Л.: 1980, с. 106—112.
- Вейко В. П., Крутенкова Е. А., Котов Г. А. К расчету термических искажений рисунка при лазерной обработке пленок. — Физика и химия обраб. материалов, 1980, № 5, с. 37—43.
- Вейко В. П., Либенсон М. Н. Лазерная обработка. Л.: Лениздат, 1973. 190 с.
- Судник В.А., Ерофеев В. А., Радаи Д. Компьютерная имитация формирования шва при лазерно-лучевой сварке с зазором //Сварочное производство. 1999. № 8. С. 9−14.
- Вейко В. П., Либенсон М. Н. Об использовании гигантского импульса ОКГ для обработки материалов. — Вопросы радиоэлектроники, сер. 4, 1966, вып. 4, с. 20—21.
- Вейко В. П., Либенсон М. Н. Применение лазеров в микроэлектронике. — Вопросы радиоэлектроники, сер. 3, 1964, № 5, с. 99—104.
- Вейко В. П., Либенсон М. Н. Проекционный способ обработки материалов излучением ОКГ. — Физика и химия обраб. материалов, 1968, № 4, с. 44—50.
- Вейко В. П., Либенсон М. Н., Суслов Г. П. Исследование стабильности параметров излучения ОКГ на стекле с неодимом. — Физика и химия обраб. материалов, 1967, № 2, с. 26—30.
- Вейко В. П., Соболев П. Н., Яковлев Е. Б. Прецизионная обработка тонких пленок непрерывным излучением. — В кн.: Опыт применения лазеров в приборостроении и машиностроении. Л.: ЛДНТП, 1983, с. 56—59.
- Вейко В. П., Суслов Г. П. Исследование равномерности излучения ОКГ на стекле с неодимом. — Жури, прикладной спектроскопии, 1971, т. 17, № 2 с. 223—227.
- Вейко В. П., Суслов Г. П. О стабильности энергии излучения импульсных твердотельных ОКГ. — Журн. прикладной спектроскопии, 1970, т. 12, № 1, с. 41—44.
- Вейко В. П., Табачник Е. М., Тучкова Е. А. Экспериментальное исследование кинетики лазерного нагревания тонких металлических пленок. — Электрон, обраб. материалов, 1986, № 1, с. 22—25.
- Вейко В. П., Тучкова Е. А. Неравномерность фронта разрушения металлических поверхностей под действием лазерного излучения. — Поверхность, 1983, № 5, с. 15—22.
- Вейко В. П., Тучкова Е. А., Юркевич Б. М. Расчет толщины прогретого слоя в подложке при лазерном нагревании тонких пленок. — Физика и химия обраб. материалов, 1982, № 3, с. 21−24.
- Вейко В. П., Тучкова Е. А., Яковлев Е. Б. О разрешающей способности лазерной литографии на тонких металлических пленках. — Квантовая электрон., 1984, т. 11, № 4, с. 661—665.
- Вейко В. П., Юркевич Б. М. Подгонка частоты кварцевых резонаторов при помощи лазерного излучения. Л. гЛДНТП, 1974. 32 с.
- Вейко В. П., Юркевич Б. М., Юхно И. Н. Подстройка монолитных кварцевых фильтров при помощи лазерного излучения. —Электрон, техн., сер. 5,1977, № 2 (21), с. 69—76.
- Павеле Л.А. Анализ газогидродинамических процессов при компьютерном проектировании технологии газолазерной резки. // Дисс. к.т.н. Тула, 1999. — 160 с.
- Глинка Н.Л. Общая химия: Учебное пособие для вузов. 23-е изд., испр./Под ред. В. А. Рабиновича. — Л.: Химия, 1983. — 704 е., ил.
- Вейко В. П., Яковлев Е. Б. Взрывное разрушение тонких пленок лазерным излучением. Тезисы докл. VI Всесоюзной конференции по нерезонансному взаимодействию оптического излучения с веществом. Паланга—Вильнюс, 1984, с. 211.
- Вейко В. П., Яковлев Е. Б. О некоторых особенностях разрушения тонких пленок под действием лазерного излучения. — Физика и химия обраб. материалов, 1979, № 2, с. 33—36.
- Гуревич Г. Л., Муравьев В. А. Воздействие излучения ОКГ на тонкие пленки. — Физика и химия обраб. материалов, 1973, № 1, с. 3—8.
- Гуревич Г. Л., Муравьев В. А. К теории разрушения тонких пленок излучением ОКГ. Физика и химия обр. материалов, 1973, № 3, с. 5−11.
- Котлецов Б. Н. Микроизображение. JI.: Маш-е, 1985.
- Лазерный генератор изображений/И. М. Карпмап, Б. Н. Котлецов, М. Н. Либеисон и др. — В кн.: Проблемы и перспективы использования оптико-механических средств в технологии производства микросхем. Л.: ЛДНТП, 1973, с. 12—19.
- Либенсон М. Н. Нагрев и разрушение тонких пленок излучением ОКГ. — Физика и химия обраб. материалов, 1968, № 2, с. 3—11.
- Дэниел К. Применение статистики в промышленном эксперименте. -М.: Мир, 1979.-299 с.
- Лавренчик В.Н. Постановка физического эксперимента и статистическая обработка его результатов: Учеб. Пособие для вузов. — М.: Энергоатомиздат, 2986. 272 с.
- Зарубин B.C. Инженерные методы решения задач теплопроводности. -М.: Энергоатомиздат, 1983. 328 е., ил.
- Бреславский П.В., Мажукин В. И., Такоева Л. Ю. Математическое моделирование лазерного плавления и испарения однородных материалов. Препринт ИПМ им. М. В. Келдыша АН СССР, № 22, 1991.45 с.