Технология плазменной резки крупногабаритных конструкций
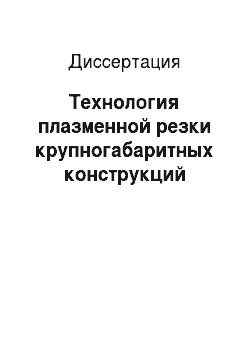
Новые, более широкие возможности открылись в электродуговой технологии в результате появления устройств-плазматронов, генерирующих стабилизированные дуги. Стабилизация электрической дуги, осуществляемая внешним магнитным полем, газовым или водяным потоком, обеспечивает более интенсивный ввод тепла в обрабатываемые дугой объекты и позволяет в широких пределах регулировать плотность энергии… Читать ещё >
Содержание
- 1. Технологические особенности плазменной резки углеродистых и легированных сталей
- 1. 1. Описание экспериментальной установки
- 1. 2. Методики исследований плазменной дуги
- Выводы по разделу
- 2. Тепловые процессы при резке плазмой с использованием бинарных газовых систем
- 2. 1. Влияние режима горения дуги на величину теплового потока в катод
- 2. 2. Тепловой баланс аргоновой дуги с газовой вихревой стабилизацией
- 2. 3. Тепловой баланс аргоно-водородной дуги с газовой вихревой стабилизацией
- Выводы по разделу
- 3. Электрические процессы в дуге при плазменной резке
- 3. 1. Электрические характеристики аргоновой дуги с газовой вихревой стабилизацией
- 3. 2. Электрические характеристики аргоно-водородной дуги с газовой вихревой стабилизацией
- 3. 3. Сравнительные характеристики аргоновой и аргоно-водородной дуги с газовой вихревой стабилизацией
- 3. 4. Исследование влияния магнитного поля на параметры аргоновой и аргоно-водородной дуги
- Выводы по разделу
- 4. Технологические особенности плазменной резки углеродистых и легированных сталей
- 4. 1. Методика исследования плазменной дуги при образовании пор в сварочных швах
- 4. 2. Плазменная резка аустенитных толстолистовых сталей
- Выводы по разделу
Технология плазменной резки крупногабаритных конструкций (реферат, курсовая, диплом, контрольная)
В период интенсивного развития промышленности в конце XX и начале XXI веков электрическая дуга нашла широкое применение, в основном, как элемент электрической цепи, предназначенной для преобразования электрической энергии в тепловую. На основании изобретения Бенардосом и Славяновым электрической дуги сварки, получения Габером азота при разложении воздуха в электрической дуге, разработки дуговой металлизации были заложены основы технологии электродуговой обработки разнообразных материалов. [1].
Новые, более широкие возможности открылись в электродуговой технологии в результате появления устройств-плазматронов, генерирующих стабилизированные дуги. Стабилизация электрической дуги, осуществляемая внешним магнитным полем, газовым или водяным потоком, обеспечивает более интенсивный ввод тепла в обрабатываемые дугой объекты и позволяет в широких пределах регулировать плотность энергии в различных участках столба дуги и нагретого в столбе потока газа. В стабилизированной дуге резко ограничивается возможность ее пространственного перемещения, в том числе и при электродных зонах, что позволяет строго локализовать область максимального выделения ее энергии и обеспечить высокую стабильность параметров дуги в течение длительного времени. [1,2].
Результатом появления стабилизированных электрических дуг явилось расширение области применения электродуговой технологии и появление новых технологических процессов. Это химический синтез, резка, сварка, получение чистых тугоплавких металлов, нанесение металлических и неметаллических покрытий, сфероидизация порошкообразных материалов, выращивание кристаллов, высокотемпературные исследования и т. д. [1].
Широкая практика промышленного применения плазматронов показывает, что введение газов с высокой теплопроводностью, в первую очередь водорода, в состав плазмообразующей газовой смеси приводит к существенному изменению всего процесса плазменной обработки.
С одной стороны, обеспечивается максимальная эффективность использования плазматрона, как нагревателя, за счет повышения теплосодержания газа, прошедшего через дугу, и улучшения условий теплопередачи к нагреваемым дугой объектам. С другой стороны, ухудшаются условия функционирования плазматрона в результате снижения стойкости электродов плазматрона и нарушения устойчивости системы: «источник питания — дуга». [2].
Следовательно, основной задачей, является определение факторов, обеспечивающих стойкость электродов плазматрона и устойчивость дуги при применении плазмообразующих газов с высокой теплопроводностью для обоснования промышленного использования плазматронов. [1,2].
Указанная задача в настоящее время решена применительно к плазменной резке, одному из наиболее распространенных процессов плазменной обработки. В этом случае стойкость электродов обеспечивается в результате введения в состав плазмообразующей смеси, наряду с водородом, — аргона со строго определенным расходом. Устойчивость дуги обеспечивается в результате применения источников питания с крутопадающими внешними статическими характеристиками. Так была внедрена плазменная резка в водородосодержащих смесях, ставшая в результате этого универсальным методом раскроя металлов. [3].
Другими перспективными областями применения плазменной обработки, получающими все более широкое распространение, являются нагрев порошкообразных материалов при нанесении покрытий и сфероидизации, а также сварка и переплав металлов. Условия функционирования плазматрона в этих процессах более тяжелое, чем при плазменной резке в связи с увеличением тепловых потоков в электроды. При плазменной сварке и переплаве это увеличение обусловлено снижением расхода плазмообразующего газа в соответствии с технологическими требованиями процесса. При плазменной же резке расход плазмообразующего газа практически не ограничивается.
При плазменном напылении и сфероидизации тепловые потоки в электроды возрастают в связи с тем, что анодная область дуги располагается внутри плазматрона, тогда как при плазменной резке анодная область находится вне плазматрона, на разрезаемом изделии.
Требования же к стойкости электродов плазматрона при плазменной сварке, переплаве и нагреве порошкообразных материалов более высокие, чем при плазменной резке, в связи с недопустимостью загрязнения обрабатываемых материалов продуктами эроззии электродов. [3,4].
По этим причинам попытки ряда исследователей произвести простой перенос методов сохранения стойкости электродов плазматрона и устойчивости дуги, горящей в бинарной водородосодержащей газовой смеси, разработанных для плазменной резки, на процессы плазменной сварки, переплава, напыления и сфероидизациине дали результата. Поэтому в настоящей работе проводится экспериментальное исследование причин снижения стойкости электродов плазматрона и устойчивости дуги, горящей в бинарной газовой смеси на основе газов с высокой теплопроводностью, и определение методов улучшения условий функционирования плазматрона.
При резке алюминия и его сплавов необходимо учитывать следующие обстоятельства. Пленка окиси алюминия, покрывающая поверхность металла, имеет высокую температуру плавления, в 3 раза превышающая температуру плавления самого металла. [4].
В связи с этим для резки необходим мощный концентрированный источник тепла, способный расплавить пленку тугоплавкой окиси.
Общая характеристика диссертационной работы.
Актуальность работы. Переход на новые современные виды вооружений, которые по своим тактико-техническим характеристикам превосходят старый парк вооружения, приводит к необходимости утилизации большого количества техники, имеющей большие габариты и выполненной из толстолистовой стали и различных сплавов. Одним из наиболее экономичных способов утилизации крупногабаритных корпусов ракет, танков и т. д. является их резка при помощи современных плазматронов. Но основной проблемой применения плазматронов является невозможность разделки толстолистовых стальных (до 200 мм.), бронзовых (до 80 мм.) и медных (до 100 мм.) конструкций. Решение этой проблемы возможно при применении в плазматронах бинарной плазмообразующей смеси высокой теплопроводности (водород и аргон), используя принудительную закрутку анодной области (газово-вихревую, магнитную), что позволяет решить проблему сохранения стойкости электродов плазматрона катода и сопла при утилизации крупногабаритных толстолистовых корпусов (ракет, самолетов, бронированной техники, кораблей, подводных лодок и т. д.).
Цель диссертационной работы. Разработка технологий и технологических режимов резки крупногабаритных конструкций с повышенными толщинами и физико-механическими свойствами материалов плазменной дугой с увеличенной концентрацией аргоно — водородной плазмообразующей смеси.
Задачи диссертационного исследования: 1 Обосновать возможность использования в плазматроне бинарной плазмообразующей смеси газов с повышенной концентрацией водорода для резки крупногабаритных конструкций из специальных материалов с повышенными физико-механическими свойствами и толщинами.
2 Теоретически обосновать и экспериментально подтвердить способы создания плазменной дуги с магнитной и газово-вихревой закруткой анодной области для обеспечения необходимых режимов резки и сохранения стойкости сопла и катода.
3 Определить уровень амплитуды напряжения и частоту колебаний, которые должен обеспечивать источник питания для сохранения устойчивости технологического процесса резки.
4 Разработать технологические режимы плазменной резки корпусов крупногабаритных изделий с разными толщинами и физико-механическими свойствами материалов.
Объектом исследования являются технологические процессы плазменной резки крупногабаритных конструкций вооружения и военной техники (ракеты, самолеты, подводные лодки, надводные корабли, танки и.
ДР-).
Предметом исследования выступают способы сохранения стойкости электродов и устойчивости дуги при работе плазматронов в бинарных плазмообразующих смесях на основе газов с высокой теплопроводностью.
Теоретической и методологической основой исследования послужили труды отечественных и зарубежных ученых в области плазменной резки и плазменной сваркимагнитных полейтепловых балансов, электрических характеристик аргоно — водородной дуги с вихревой газовой стабилизацией и др. В качестве исходной информации использовались результаты исследований промышленного применения плазматронов с введением газов (в т.ч. с высокой теплопроводностью), материалы отраслевых научно — исследовательских институтов, опубликованные монографии, специализированные статьи и др.
Научная новизна и положения, выносимые на защиту:
1 Предложено использовать для плазматронов бинарную смесь газов с соотношением 60% водорода и 40% аргона, что позволяет создать плазменную дугу, способную увеличить толщину разрезаемой специальной толстолистовой крупногабаритной конструкции со 100 мм до 200 мм, бронзы с 30 мм до 80 мм, меди с 40 мм до 100 мм.
2 Теоретически обоснованы и экспериментально подтверждены способы создания плазменной дуги, основанные на магнитной и газовой закрутке смеси газового потока (водород и аргон), который формируется таким образом, что в соплах по центру концентрируется плазменная дуга с максимальной температурой (водород), а в зонах, удаленных от центра температура снижается за счет кольцевой газовой оболочки инертного газа аргона, что позволяет обеспечить более высокие температуру, давление газов и их скорость на выходе, а также стойкость сопла и катода.
3 Определены уровни амплитуды напряжений и частоты колебаний, которые должен обеспечить источник питания плазматрона с крутопадающими внешними статическими характеристиками (70°-75°), для создания устойчивой плазменной дуги при изменении соотношений концентраций в бинарной смеси газов при резке крупногабаритных изделий корпусов из материалов, имеющих различные специальные физико-механические свойства и повышенную толщину.
4 Разработаны технологические режимы резки корпусов крупногабаритных изделий, основанные на создании необходимой плазменной дуги в зависимости от геометрических характеристик и свойств материалов.
Достоверность исследования. Достоверность теоретических положений, выводов и результатов, сформулированных в диссертации, подтверждается результатами экспериментальных исследований и практического применения.
Практическая значимость полученных результатов. Получены экспериментальные данные о влиянии плазмообразующего газа, в том числе с высокой теплопроводностью на стойкость электродов плазматрона и устойчивости дуги, позволяющие разрабатывать системы обеспечения устойчивости дуги, а также способы ее повышения в условиях промышленного производства. Разработана технология плазменной резки крупногабаритных конструкций с применением бинарной системы газов, используемой при утилизации военной техники.
Апробация работы. Результаты работы были доложены и обсуждены на научно-технических семинарах по специальности 05.03.06. «Технологии и машины сварочного производства» при Красноярском государственном техническом университете" в 2002 — 2005 гг., а также на Всероссийской с международным участием научно-технической конференции молодых ученых, посвященной 110-годовщине Дня радио, состоявшейся в городе Красноярске 5−6 мая 2005 года. Все разработки прошли апробацию и внедрение на ФГУП ПО «Электрохимический завод», г. Зеленогорск (ЗАТО) Красноярского края, в воинских частях № 3 059 (г. Красноярск) и № 25 920 (г. Зеленогорск).
Публикации. По теме диссертации опубликовано 12 печатных работ. Из них статей -11, докладов -1, общим объемом 44 страницы.
Объём и структура работы. Диссертация состоит из введения, четырёх разделов, выводов, списка используемых литературных источников. Общий объём диссертации-144 страницы, включающих 73 рисунка, 3 таблицы.
Список литературы
содержит — 84 наименования.
Общие выводы:
1. При введении водорода в состав плазмообразующей смеси мощность дуги увеличивается быстрее, чем суммарные тепловые потоки в электроды.
2. Тепловой поток в катод плазматрона при неизменной величине тока практически не изменяется при переходе от аргоновой к аргонно-водородной дуге, независимо от концентрации водорода в составе плазмообразующей смеси.
3. Тепловой поток в анод плазмотрона с увеличением расхода водорода возрастает, асимпотинически приближаясь к величине, определяемой силой тока.
4. При введении в состав плазмообразующей смеси водорода удельные тепловые потоки в анодной области превосходят допустимые значения для меди независимо от величины тока. Поэтому возможность длительной работы плазмотрона в водородосодержащей плазмообразующей смеси при неподвижной анодной области исключается.
5. При газовой вихревой закрутке анодной области, стойкость анода в водородосодержащей плазмообразующей смеси обеспечивается при ограниченной величине тока и при значительных расходах плазмообразующей смеси.
6. При магнитной закрутке анодной области высокая стойкость анода в водородосодержащей плазмообразующей смеси обеспечивается при практически неограниченных значениях тока и при расходах плазмообразующего газа, значительно меньших, чем при газовой вихревой закрутке анодной области. Однако при увеличении напряжённости магнитного поля до величины, обеспечивающей высокую способность анода, снижаться мощностью дуги и КПД плазмотрона.
7. При увеличении расхода водорода возрастает средняя величина напряжения на дуге и амплитуда характерных для стабилизированной дуги высокочастотных колебаний напряжения.
8. При магнитной закрутке анодной области амплитуда высокочастотных колебаний напряжения снижается при увеличении напряжённости магнитного поля в канале анода до значений, обеспечивающих высокую стойкость анода.
9. При прочих равных условиях устойчивость дуги независимо от химического состава плазмообразующей газовой смеси определяется амплитудой колебаний напряжения. Если каким-либо путём, например изменением способа закрутки анодной области, при неизменном химическом составе плазмообразующей смеси снижается амплитуда колебаний напряжения, то при этом возрастает устойчивость дуги.
Ю.При увеличении амплитуды высокочастотных колебаний напряжения для обеспечения устойчивости дуги должен возрастать угол наклона рабочих участков внешних статических характеристик источника питания.
ЗАКЛЮЧЕНИЕ
.
Целью настоящей работы являлось экспериментальное исследование функционирования плазматронов в бинарных плазмообразующих смесях на основе газов с высокой теплопроводностью с целью обеспечения стойкости электродов плазматрона и устойчивости дуги. Полученные данные должны лечь в основу принципов разработки оборудования и конкретных технологических процессов плазменной обработки.
Анализ литературы показал, что введение в состав плазмообразующей смеси газов с высокой теплопроводностью приводит к существенному изменению всего процесса плазменной обработки. С одной стороны, обеспечивается максимальная эффективность использования плазматрона как нагревателя благодаря повышению теплосодержания плазмообразующего газа. С другой стороны, ухудшаются условия функционирования плазматрона в связи со снижением стойкости электродов плазматрона и нарушением устойчивости дуги.
Одним из основных путей повышения стойкости электродов плазматрона является применение бинарных плазмообразующих смесей, в которых наряду с газами, обладающими высокой теплопроводностью, применяется аргон. Методом повышения устойчивости дуги является применение источников питания с крутопадающими внешними статическими характеристиками.
Отсутствие систематических исследований не обеспечило создание и широкое применение плазматронов, функционирующих в плазмообразующих смесях на основе газов с высокой теплопроводностью. Как правило, газ с высокой теплопроводностью вводится лишь как добавка к аргону.
В работе приведено описание экспериментальной установки и методики экспериментального исследования.
Экспериментальная установка включает в себя плазматроны с газовой вихревой и магнитной закруткой анодной области, источник питания дуги, приборы для определения электрических параметров дуги и тепловых потоков в электроды плазматрона.
Для сохранения устойчивости дуги в широком диапазоне расхода и состава плазмообразующей смеси и силы тока источник питания имеет крутопадающие рабочие участки внешних статических характеристик.
При разработке схемы электрических измерений учитывалась возможность появления колебаний напряжения и тока различных частот. Поэтому в процессе исследований проводилось определение не только средних, но и мгновенных значений электрических параметров дуги. Выбор типа осциллографа и измерительных вибраторов для исследований мгновенных значений тока и напряжения основывались на предварительных экспериментах, которые показали, что частота колебаний напряжения достигает нескольких килогерц при амплитуде от 1 до 25−30 В. Расчетным путем определено, что для регистрации колебаний с такими параметрами должны применяться вибраторы с собственной частотой колебаний не менее 10 000 Гц, а скорость протяжки пленки должна быть не менее 5,0 м/сек.
Разработка схемы измерений тепловых потоков в электроды плазматрона основывалась на анализе известных типов калориметров: на проточной воде и парового. Основными достоинствами калориметра на проточной воде являются простота работы с ним, возможность применения при исследовании плазматронов любого типа и размера, возможность измерения больших тепловых потоков без опасности разрушения исследуемых электродов, малая длительность одного измерения. Недостатком калориметра на проточной воде является значительная погрешность измерения (не менее 7,5−10%), практически не поддающаяся обсчету и переменная в процессе эксперимента. Паровой калориметр более сложен в изготовлении, велико время проведения одного измерения. При его использовании не удается обеспечить работу электрода без разрушения в условиях больших тепловых нагрузок. Основным достоинством парового калориметра является малая погрешность измерений (2,5−3,0%), определяемая расчетным путем и неизменная в процессе исследований.
В настоящей работе калориметр на проточной воде применялся для исследования процессов, сопровождающихся значительным тепловыделением в электроды, и явился основным измерительным прибором.
Паровой калориметр применялся для уточнения данных, полученных при исследовании процессов на калориметре с проточной водой, сопровождающихся малыми тепловыми потоками в электроды и перегибами в зависимостях тепловых потоков. В связи с тем, что анодная область исследуемой дуги нефиксированная, все результаты экспериментов относились к заданной геометрии электродов плазматрона, неизменность которой в процессе исследований проверялась путем многократного повторения экспериментов.
Для сохранения неизменной геометрии электродов был разработан цикл формирования дуги при выводе ее на режим, который устанавливает определенную временную взаимосвязь основных варьируемых параметров процесса в наиболее напряженных, с точки зрения функционирования плазматрона, переходных режимах.
Предварительные эксперименты показали, что мгновенные и средние значения исследуемых параметров дуги определяются не только соответствующими моменту измерения значениями варьируемых параметров, но и предшествовавшим этому моменту состояния дуги. Поэтому цикл исследований какого-либо параметра на «режим функционирования плазматрона и проверялся при измерении с постоянной скоростью этого параметра от минимума до максимума и обратно без выключения дуги. По окончании каждого цикла измерений, общее число которых в зависимости от разброса полученных результатов составило 5−10, дуга выключилась. Обработка полученных результатов производилась путем определения средней величины исследуемого параметра и среднеквадратичной погрешности измерений.
Анализ точности измерения показал, что максимальные погрешности измерения тока и напряжения составляют ± 3%, тепловых потоков ± 2,5% при работе с паровым калориметром и не менее ± 10% при работе с калориметром на проточной воде, расхода газов ± 2%.
Получены результаты экспериментальных исследований, выполненных по разработанной методике, и приведен анализ этих результатов. Исследовался плазматрон с вольфрамовым стержневым катодом и медным формирующим соплом — анодом. Плазмообразующей служила аргоно-водородная смесь.
Анализ распределения тепловых потоков показал, что с увеличением расхода водорода общая мощность дуги возрастает быстрее, чем тепловые потоки в электроды. Благодаря этому при больших расходах водорода увеличиваются тепловая энергия, запасенная в плазмообразующем газе, КПД плазматрона. Тепловая энергия плазмообразующего газа, отнесенная к единице объема или массы плазмообразующего газа, при переходе от однокомпонентной аргоновой к аргоно-водородной дуге значительно возрастает. Благодаря этому повышается эффективность использования плазматрона как нагревателя при плазменной обработке.
Введение
водорода в состав плазмообразующей смеси оказывает различное влияние на величину тепловых потоков в электроды плазматрона, тепловой поток в катод определяется силой тока и практически не зависит от расхода и состава плазмообразующей аргоно-водородной смеси.
Тепловой поток в анод зависит не только от силы тока, но также от расхода и состава плазмообразующей смеси.
Введение
водорода в состав газовой атмосферы дуги вызывает при неизменной величине тока увеличение теплового потока в анод. Однако, само по себе это увеличение не является причиной возможного разрушения анода плазматрона, функционирующего в водородосодержащей плазмообразующей смеси.
Анализ причин разрушения анода плазматрона показал, что при введении в состав плазмообразующей смеси водорода удельные тепловые потоки в анодной области дуги превосходят допустимые значения для меди, независимо от силы тока. Это позволяет сделать следующий вывод: возможность длительного функционирования плазматрона в водородосодержащей плазмообразующей смеси при неподвижной анодной области без разрушения анода исключается. Следовательно, применительно к водородосодержащим дугам, анодная область которых располагается внутри плазматрона, методом обеспечения длительного функционирования плазматрона является перемещение анодной области.
Были исследованы два способа принудительного перемещения анодной области в канале анода плазматрона, функционирующего в аргоно-водородной плазмообразующей смеси: газовая вихревая и магнитная закрутка. [71].
Исследования показали, что в зависимости от способа закрутки анодной области в канале анода изменяются характеристики плазматрона и стойкость анода. При газовой вихревой закрутке тепловая энергия, запасенная в плазмообразующем газе, и КПД плазматрона полностью определяются расходом водорода. Плотность же теплового потока в анод полностью определяется расходом аргона, снижаясь с увеличением его. Условием обеспечения длительного функционирования анода плазматрона без разрушения при газовой вихревой закрутке является значительный расход аргона.
При магнитной закрутке анодной области обеспечивается минимальная плотность теплового потока в анод при расходах аргона, значительно меньших, чем при газовой вихревой закрутке анодной области. Однако при этом снижается тепловая энергия, запасенная в газе, и КПД плазматрона.
Сравнение характеристик плазматронов с газовой вихревой и магнитной закруткой анодной области позволило определить рациональные области их применения.
В тех случаях, когда основным требованием процесса является высокая производительность и допустимо загрязнение конечных продуктов обработки до одного-полутора процентов материалом электродов, целесообразно применение плазматронов с газовой вихревой закруткой анодной области.
Если же основным требованием процесса является минимальное (не более 0,1−0,5%) загрязнение обрабатываемых изделий материалов электродов, то применение плазматронов с магнитной закруткой анодной области. [72,73,74].
Исследование электрических параметров дуги показало, что введение водорода в состав плазмообразующей смеси сопровождается увеличением среднего значения напряжения и амплитуды высокочастотных колебаний напряжения. С увеличением расхода водорода амплитуда колебаний напряжения растет быстрее, чем среднее значение напряжения на дуге.
Средняя величина напряжения на дуге и амплитуда высокочастотных колебаний напряжения зависят не только от состава и расхода плазмообразующей смеси, но и от способа закрутки анодной области. Переход при неизменном составе и расходе плазмообразующей смеси от газовой вихревой к магнитной закрутке анодной области сопровождается снижением среднего значения напряжения и амплитуды высокочастотных колебаний напряжения.
Сравнение функционирования дуг с одинаковым химическим составом газовой атмосферы и с одинаковым углом наклона вольтамперных характеристик, построенных по средним значениям тока и напряжения, позволил сделать следующий вывод. Независимо от химического состава плазмообразующего газа устойчивость дуги зависит от амплитуды колебаний напряжения. Следовательно, меняя тем или иным способом, в частности, изменением метода закрутки анодной области, амплитуду колебаний напряжения можно регулировать устойчивостью дуги с газовой атмосферой постоянного химического состава. [75,76].
С увеличением амплитуды колебаний напряжения при неизменной крутизне вольт-амперных характеристик дуги, пропорционально возрастает и угол наклона рабочих участков внешних статических характеристик источника питания, обеспечивающий устойчивость дуги.
Исходя из условия устойчивости, минимальный угол наклона рабочих участков внешних статических характеристик источника питания аргоноводородной дуги с газовой вихревой закруткой анодной области должен составлять 70−75°, а аргоно-водородной дуги с магнитной закруткой анодной области — 40−45°. [77].
Результаты проведенных исследований легли в основу принципов разработки оборудования и конкретных технологических процессов плазменной обработки.
Список литературы
- Синельков, К.Д. Лекции по физике плазмы / К. Д. Синельков, Б. Н. Рутиевич. Харьков: Харьковский ордена трудового Красного знамени государственный универсистет, 1964. — 234 с.
- Тезисы докладов пятой Всесоюзной конференции по генераторам низкотемпературной плазмы. / ред. Коллегия. Болотов А. В., Гнездин Л. П., Жеенбаев Ж., Жуков М. Ф., Колонина Л. И., Поповин И. Г., Урюков Б. А., Ясько О. И. Новосибирск. 1972. — 440 с.
- Гарин, Е.Н. Проблемы неустойчивости плазмы / Е. Н. Гарин // Вестник Красноярского государственного технического университета «Машиностроение». Красноярск. 2004. — № 36. — С. 37 — 41.
- Быховский, Д.Г. Плазменная резка / Д. Г. Быховский. Ленинград «Машиностроение»., 1972. — 348 с.
- Технология и оборудование сварки плавлением и термической резки: Учебник для вузов / Сост. А. И. Акулов, В. П. Алехин, С. И. Ермаков др.- Машиностроение. Москва, 2003. 437 с.
- Куликов, В.П. Технология и оборудование сварки плавлением и термической резки / В. П. Куликов. Минск Эноперспектива., 2003. -311 с.
- Медведев, А.Я. Установки плазменной резки / nvertec PC 40, 60, 100 / А. Я. Медведев // Сварочное производство. 1994. — № 4. — С. 39−41.
- Быховский, Д.Г. Электрические параметры водородосодержащей протяженной пространственно ограниченной дуги / Д. Г. Быховский, М. Г. Фридлянд, Ленинград: «Энергия», 1965 — 573 с.
- Быховский, Д.Г. Газоэлектрическая резка металлов в судостроении / Д. Г. Быховский. Ленинград: «Судостроение»., 1964 — 337 с.
- Ю.Трейстер, Р. Сорок четыре источника электропитания / Р. Трейстер, Дж. Мейо. Москва: Энергоатомиздат, 1990. 231 с.
- Норманн, Д. Измерительные приборы для домашней лаборатории /
- Д.Нюрман. Москва: «Энергоатомиздат», 1991 — 162 с. 12. Электротехника и электроника, учебное пособие / Сост. М. К. Бегева, И. Д. Златнев, П. Н. Новиков, Е.В. Шапкин- Высшая школа, — Москва, 1991 — 224 с.
- И.Кутателидзе, С. С. Теплопередача и гидродинамическое сопротивление /
- С.С. Кутателидзе. Москва: Энергоатомиздат., 1990. — 367 с. М. Васильев, К. В. Распределение тепловой энергии при воздушно-плазменной резке / К. В. Васильев // Тр ВНИИАВТОГЕНМАШа. — Москва. — 1982.-№ 12-С. 48−55.
- Быховский, Д.Г. Исследования электрических параметров протяженной пространственно ограниченной дуги, горящей в среде аргона / Д. Г. Быховский, М. Г. Фридлянд, Ленинград: «Энергия», 1964 — 453 с.
- Васильев, К.В. О некоторых свойствах проникающей режущей дуги / К. В. Васильев // Москва. Машгиз. 1960 — № 7. — С. 67 — 86.
- Васильев, К.В. Плазменнодуговая резка в машиностроении / К. В. Васильев. Москва: ЦИНТИМХИМНЕФТЕМАШ., 1967. — 380 с.
- Васильев, К.В. О поведении режущей дуги при плазменно-дуговой резке металлов / К. В. Васильев. Москва: ЦИНТИМХИМНЕФТЕМАШ., 1976. -№ 21.-С. 51 -60.
- Гарин, Е.Н. Влияние режима горения плазменной дуги на величину теплового потока в катод / Е. Н. Гарин, Ю. Г. Новосельцев // Вестник университетского комплекса. Красноярск. 2005. — № 4 (18). — С. 82 — 86.
- Васильев, К.В. О нагреве плазменной в сврочных процессах / К. В. Васильев, А. А. Исадченко // Москва. Машгиз. 1960 — № 6. — С. 147 — 150.
- Ширшов И.Г. Плазменная резка / И. Г. Ширшов, В. Н. Котиков. -Ленинград: «Машиностроение», 1987. 192 с.
- Руссо, В.Л. Дуговая сварка в инертных газах / В. Л. Руссо. Ленинград.: «Судостроение»., — 1984. — 318 с.
- Баядьянов, Б.И. Расчет температур по длине вольфрамого электрода при аргонодуговой сварке / Б. Н. Бадьянов, В. А. Давыдов, А. В. Пантюхин // Сварочное производство. 1994. — № 1. — С. 34 — 35.
- Чемпен, С. Математическая теория неоднородных газов / С. Чемпен, Т.Кулич. Москва: Машгиз., 1960. — 245 с.
- Гарин, Е.Н. Влияние режима горения плазменной дуги на величину теплового потока в атод / Е. Н. Гарин, Ю. Г. Новосельцев // Вестник университетского комплекса. Красноярск. 2005. — № 4 (18). — С. 86 -91.
- Васильев, К.В. Плазменно-дуговая резка перспективный способ термической резки / К. В. Васильев // Сварочное производство. — 2002 -№ 9. — С. 26 — 28.
- Васильев, В.К. Расчет глубины и зоны термического влияния при плазменно-дуговой при плазменно-дуговой резке / К. В. Васильев // Автоматическая сварка. — 1971. № 11. С. 29- 31.
- Романов, Б.П. Теплообмен плазмы дуги с керамическим соплом аргоновой горелки. / Б. П. Романов, В. Ю. Евтюшкин, А. Н. Березтн // Сварочное производство. 2004. — № 3. — С. 9 — 11.
- Васильев, К.В. Скорости потоков плазмы и расплава при плазменной резке / К. В. Васильев // Тр ВНИИАВТОГЕНМАШа. Москва. — 1980. — С. 9−19.
- Гарин, Е.Н. Тепловой баланс аргоно-водородной дуги с газовой вихревой стабилизацией / Е. Н. Гарин, Ю. Г. Новосельцев // Вестник университетского комплекса. Красноярск. 2005. — № 4 (18). — С. 91 — 99.
- Сидоров, В.П. Расчет теплоотвода в сопло > плазмотрона от столба плазменной аргоновой дуги / В. П. Сидоров // Сварочное производство. -1987.-№ 2.-С. 36−37.
- Шицин Ю.Г. Влияние полярности на тепловые нагрузки плазмотрона / Ю. Г. Шицин, О. А. Носолаков // Сварочное производство. 1997. — № 3. -С. 23−25.
- Васильев, К.В. Исследование теплового К.П.О. плазменно дуговой резки / К. В. Васильев // Тр ВНИИАВТОГЕНМАШа. Воронеж. — 1976. — № 20. -С.З- 16.
- Васильев, К.В. Исследование кислородно-дуговой резки сталей / К. В. Васильев // Москва. Машгиз. 1960. — № 6. С. 49 — 79.
- Головченко, B.C. Тепловая резка металлов в судостроении / B.C. Головченко. Ленинград: Судостроение., 1975. 417 с.
- Чернышев, Г. Г. Сварочное дело: Сварка и резка металлов: Учебник для нач. проф. образования / Г. Г. Чернышев. Москва: И РПО- Проф. обр. издат., 2002−338 с.
- Шоек П.А. Исследование баланса энергии на аноде сильнотечных дуг, горящих в атмосфере / П. А. Шоек. Москва: «Энергия» Современные проблемы теплообмена, — 1966. — 272 с.
- Васильев, К.В. Исследование теплопередачи в металл при плазменно-дуговой резке / К.В. Васильев// Тр ВНИИАВТОГЕНМАШа. Москва. -1970.-№ 17-С. 74−85.
- Минич, К. П. Угловые коэффициенты излуения между торцевой плоской стенной и внешней поверхности плоскости, образованной поаксиальными целиндрами / К. П. Минич // Ракетная техника и космонавтика. 1979. № 12. С. 123- 125.
- Гарин, Е.Н. Электрические характеристики аргоно-водородной дуги с газовой стабилизацией / Е. Н. Гарин, Ю. Г. Новосельцев // Вестник Красноярского государственного технического университета «Машиностроение». Красноярск. 2005. — № 38. — С. 83 — 85.
- Васильев, К.В. О процессе резки сосредоточенной дугой / К. В. Васильев. -Москва: НТО Машпром, 1958. 328 с.
- Васильев, К.В. Смесевые технологии — прогрессивное направление развития воздушно плазменной резки / К. В. Васильев // Москва: ЦИНТИМХИМНЕФТЕМАШ. — 1991. — С. 45 — 53.
- Пикин, Ю.А. Шумовой фактор при плазменной резке металла / Ю. А. Пинин, О. И. Стеклов // Сварочное производство. 2002. — № 9. — С. 51 -53.
- Микроплазменная сварка / под редакцией Б. Е. Потона-Наукова думка. -Киев, 1979−245 с.
- Severance, W. How plasma Arc Cuting cases / W. Severance, D Adeerson // Schweisste chnik. 1972. -№ 12. S. 555 — 558.
- Седов, E.A. мир Электрошин / E.A. Седов. Москва: Молодая гвардия., -1990.-444 с.
- Наука и человечество. / Сост. А. А. Логунов, А. П. Александров, Н. Г. Басов, Н. Н. Блохин, Б. В. Гнеденко и др.- «Знание». Москва, 1980 — 372 с.
- Аквельт, М.Ю. Электротехника / М. Ю. Аквельт, Ю. Х. Пухляков, М. А. Ушаков. Москва: «Просвещение», 1964. — 534 с.
- Франк Каменский, Д. А. Плазма — четвертое состояние вещества / Д. А. Франк — Каменский — Мостква: «Атомиздат»., 1975. — 152 с.
- Арцимович, Л.А. Элементарная физика плазмы / Л. А. Аруимович. -Москва: «Просвещение»., 1986. 121 с.
- Гарин, Е.Н. Методика исследования плазменной дуги / Е. Н. Гарин // Вестник Красноярского государственного технического университета «Машиностроение». Красноярск. 2005. — № 38. — С. 74 — 77.
- Григорьев, JI.H. Расчет выхода оксидов азота при сварке / JI.H. Григорьев // технология судостроения. 1991. — № 6. — С. 58 — 61.
- Вальская, Э.Н. Образования окислов азота при плазменной резке металлов и их контроль / Э. Н. Вальская, JI.H. Григорьев, Ю. П. Губаков // Технология судостроения. 1984. — № 8 — С. 76 — 79.
- Васильев, К.В. К проблеме пор в сварочных швах после воздушно-плазменной резке / К. В. Васильев, JI.O. Нохлинян // 2 международный симпозиум общества сварщиков Японии. 1975. — С. 591 — 596.
- Григорьев, JI.H. Сокращение выбросов оксидов азота при плазменной резке металлов / JI.H. Григорьев, И. Д. Иванов, JI.M. Матвеев // Технология судостроения. 1990 — № 5. — С. 53 — 56.
- Фролов, В.В. Физико-химические процессы в сварочной дуге / В. В. Фролов. Москва: Машгиз., 1954. — 327 с.
- Григорьев, JI.H. Выбор способа очистки и обезвреживания выбросов в атмосферу / JI.H. Григорьев, M.JI. Молочников // технология судостроеия. -1991-№ 6.-С. 56−58.
- Походня, И.К. Газы в сварных швах / И. К. Походня., Москва: «Машиностроение»., 1972 — 202 с.
- Горбач, В. Д Снижение вредных выделений и отходов при плазменной резке металлов / В. Д. Горбач, Ю. А. Евдокимов, JI.H. Григорьев, JI.M. Исяков // «Сварочное производство». 2004 — № 2. С. 47−53.
- Поляков, В.А. Электротехника / В. А. Поляков. Москва: «Просвещение»., 1986.-421 с.
- Петухов, Б.С. Теплообмен и сопротивление при ламинированном течении жидкости в трубах / Б. С. Петухов. Москва: «Энергия»., 1967. — 411 с.
- Гарин, Е.Н. Электрические характеристики аргоновой дуги с газовой вихревой стабилизацией / Е. Н. Гарин, Ю. Г. Новосельцев // Вестник Красноярского государственного технического университета «Машиностроение». Красноярск. 2005. — № 38. — С. 54 — 57.
- Повышение устойчивости плазмы при обработке металлов: «Современные проблемы радиоэлектроники». / Гл. ред. Громыко А.И.- Красноярский государственный технический университет, институт радиоэлектроники. -Красноярск, 2005. 408 с.
- Эсибян, Э.М. Плазменно-дуговая аппаратура / Э. М. Эсибян. Киев: «Техники», 1971. — 164 с.
- Шницин, В.Ю. Влияние полярности на тепловложение в сопло плазмотрона / В. Ю. Шницин, В. М. Язовских // Сварочное производство. -2002. -№ 1. -С. 17- 19.
- Васильев, К.В. Воздушно-плазменная резка / К. В. Васильев // Москва: Машиностроение, 1976. 482 с.
- Васильев, К.В. Промышленное примение высокоэффективного процесса супервоздушно-плазменной резки / К. В. Васильев, В. И. Кожевников, JI.O. Кохлинян // Сварочное производство. 1982. — № 6. С. 13−14.
- Корнелюк, Ю. М. Сварка меди под флюсом / Ю. М. Корнелюк. Москва: Машиностроение, 1967. — 368 с.
- Васильев, К.В. Современные задачи и перспективы развития плазменно-дуговой резки / К. В. Васильев // Международная конференция ЭЛТЕХ2001. С.Петербург. — 2001. -С. 27 — 29.
- Гузов, С.Г. Исследование влияния частоты кислорода на производительность и качество разделительной кислородной резки / С. Г. Гузов // Кислородной резка, сварка. Напыление пластмасс. ВНИИАВТОГЕНМАШ. 1954. — № 4. С. 34 — 49.
- Васильев, К.В. Плазменно-дуговая резка сталей / К. В. Васильев, А.А. Исаченко// Тр ВНИИАВТОГЕНМАШа. Москва. — 1967. — № 14. — С. 37 -53.
- Васильев, К.В. Применение кислородно-плазменной дуги для резки металлов / К. В. Васильев // Москва. Стройдор коммуникации. 1967. -№ 7.-С. 17−26.
- Григорьев, Л.Н. Основные направления аспирационных выбрасов / Л. Н. Григорьев, Ю. А. Евдокимов, Л. М. Исяков // Охрана окружающей среды от загрязнений промышленными выбрасоми ЦБПП ПТА. 1981. — № 9. — С. 149−152.
- Рубцов, Н.А. Геометрические инварианты излучения / Н. А. Рубцов, В. А. Лебедев. Новосибирск: И.Т.СОАН СССР., — 1989 — 243 с.
- Излучательные свойства твердых материалов. / Справочник под редакцией Л.Е. Шейдлина- «Энергия», МоскваО 1974. — 471 с.
- Дюрренс, У.Х. Гиперзвуковые течения вязкого газа / У. Х. Дюрренс. -Москва: Мир, 1966. 443 с.
- Арцимович, Л.А. Элементарная физика плазмы / Л. А. Аруимович. -Москва: «Атомиздат»., 1969. 188 с.
- Новожилов, Н.М. Основы металлургии дуговой сварки в газах / Н. М. Новожилов. Москва: «Машиностроение»., 1979. — 324 с.
- Думов, С.И. Технология электрической сварки плавлением / С. И. Думов, 159