Технология производства отливок в формах с расплавляемой оснасткой
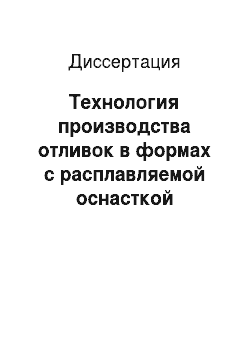
Разработанная на основе экспериментальных данных, оснастка и технология изготовления отливок с применением расплавляемых вставок, приемлема для большого числа других деталей. В том числе и тонкостенных отливок с большой протяженностью стенки. Так как при взаимодействии окисленной поверхности чугунной корочки с оплавленной поверхностью формы происходит экзотермическая реакция с выделением тепла… Читать ещё >
Содержание
- 1. Состояние вопроса
- 1. 1. Математические модели затвердевания отливок
- 1. 2. Применение расплавляемой оснастки при литье в кокиль
- 1. 3. Технология плавки металла для валков
- 1. 4. Сортопрокатные валки
- 1. 4. 1. Классификация прокатных валков
- 1. 5. Цели и задачи работы
- 2. Математическая модель затвердевания отливки в форме с расплавляемой облицовкой
- 2. 1. Постановка задачи и методы ее решения
- 2. 1. 1. Постановка задачи
- 2. 2. Конечностно- разностная аппроксимация уравнения теплопроводности
- 2. 3. Конечностно- разностная аппроксимация граничных условий
- 2. 1. Постановка задачи и методы ее решения
Технология производства отливок в формах с расплавляемой оснасткой (реферат, курсовая, диплом, контрольная)
Современное состояние промышленности, требует применения более совершенных технологий, а также возможности их автоматизации.
Так в прокатном, литейном и кузнечно-прессовом производствах наблюдается недостаток в дешевом и качественном инструменте. В сортопрокатном производстве предусматривается значительное увеличение выпуска облегченных профилей, производство проката из высококачественной и легированной стали, разработке новых стандартов с более жесткими требованиями к качеству поверхности проката и к допускаемым отклонениям от минимальных размеров. Повышение качества продукции необходимо также и в литейном производстве. Необходимо снижение расхода металла на производство отливок и уменьшение затрат на их механическую обработку.
Успешное решение поставленных задач, главным образом, зависит от служебных свойств основного технологического инструмента.
Также на качество продукции и ее конечную стоимость влияет то, на сколько автоматизирован весь процесс производства от стадии разработки самой отливки до ее финишной механической обработки.
Все это требует применения современных методов исследования — математического моделирования процессов, усовершенствования существующих и внедрение качественно новых технологий производства.
5. Выводы.
Анализ литературных источников показал, что есть острая необходимость во внедрении качественно новых технологий производства отливок из чугуна и стали. Существующие методы производства не способны удовлетворить все возрастающие потребности в качественном литье.
Разработанная модель, позволяет применять ее для расчетов параметров форм с использованием расплавляемых вставок, для получения отливок любой сложности и геометрии.
Экспериментально доказано, что данные, получаемые при использовании математической модели, полностью совпадают с практически полученными результатами.
Разработанная модель, позволила изучить более полно процессы, происходящие на границе контакта между металлом отливки и алюминием расплавляемой вставки. Более глубокое изучение этого процесса позволяет внедрять технологию использования легкоплавких частей формы для получения отливок большой массы и достаточно сложной геометрии. Также предложенная программа позволяет моделировать процессы, происходящие не только в момент заливки, но и на протяжении более долгого времени после затвердевания отливки. Следовательно, появляется возможность в проведении термической обработки отливки не посредственно в полости формы за счет теплоты расплавленного алюминия. Контроль за скоростью затвердевания, в данном случае, позволяет достаточно точно получать необходимую микроструктуру отливки.
Усовершенствована и апробирована технология получения чугуна для отливки валков.
Схема применения расплавляемых вставок в паре с математической моделью, при изготовлении отливок из чугуна и стали обладает большими потенциальными возможностями. Интенсивное охлаждение металла отливки приводит к формированию мелкозернистой структуры в поверхностном слое, что благотворно сказывается на механических свойствах отливок.
Разработанная на основе экспериментальных данных, оснастка и технология изготовления отливок с применением расплавляемых вставок, приемлема для большого числа других деталей. В том числе и тонкостенных отливок с большой протяженностью стенки. Так как при взаимодействии окисленной поверхности чугунной корочки с оплавленной поверхностью формы происходит экзотермическая реакция с выделением тепла от 36 до 196 Дж/см2, в зависимости от технологических параметров взаимодействия.
Использование вышеуказанной технологии позволяет значительно сократить затраты на производство деталей из стали и чугуна.
При производстве стальных прессформ возможно использование в качестве шихты отходов инструментального производства (обрези, стружка).
2.5.3.
Заключение
.
Используя конечно — разностную аппроксимацию, был составлен алгоритм решения задачи, на основе которого создан пакет программ на языке Turbo Pascal 7.0, позволяющий численно моделировать тепловые процессы, протекающие в кокиле с расплавляемыми алюминиевыми вставками при заливке его металлом.
Глава 3. Математическое моделирование процесса заливки и затвердевания в форме с расплавляемой вставкой 3.1. Численный эксперимент.
Используя разработанную программу, было проведено численное моделирование процессов теплообмена в кокиле. Результаты некоторых расчетов приведены ниже.
Прежде всего, надо отметить, что все проведенные численные расчеты, показали устойчивость конечно — разностной схемы Дюфорта — Франкела при достаточно сложных граничных условиях первого, второго и третьего рода. Это говорит о том, что данную схему можно успешно использовать при решении задач Стефана.
Для того, чтобы ошибка расчетов не возрастала, необходимо шаг по времени брать достаточно малым, порядка 10~2 .10~3 с, что значительно увеличивает время расчета примера. На ЭВМ типа IBM с процессором 486DX4 время расчета одного примера составило порядка 40.50 минут.
В силу того, что на границе контакта алюминиевой облицовки с чугунной стенкой кокиля возникает большое тепловое сопротивление из-за сильно отличающихся коэффициентов теплопроводности, при малых временных шагах, возможно возникновение неустойчивости. В модель была введена процедура Seredina, которая в случае возникновения неустойчивости дает сообщение на экран и при больших возмущениях останавливает численный расчет для уменьшения шага по времени.
3.2. Результаты расчетов.
Математическая модель, предложенная в данной работе, позволяет моделировать процесс заполнения и кристаллизации отливки в комбинированной форме. Программа позволяет выдавать результаты расчетов наглядно в виде таблиц температурных полей как внутри самой отливки, так и в алюминиевом вкладыше и стальном кокиле. Для эксперимента были выбраны отливки высотой 0,1- 0,15 и 1 м. Толщина и ширина отливки выбирались произвольно. Предварительные расчеты для каждой отливки были выполнены по формулам, приведенным в работе [43].
Следует отметить, что в ходе обработки предварительных результатов программы было проведено несколько расчетов, проверяющих предположение, что значение расчетной скорости подъема металла в форме должно быть несколько выше. Так как при небольшой скорости подъема металла происходил нагрев алюминиевой вставки до температуры плавления, что приводило к ее преждевременному разрушению.
Также при подготовке к экспериментальным расчетам были выбраны толщины алюминиевого вкладыша для каждой отливки. За основу были приняты значения, приведенные в работах С. П. Кожемякина и В. А. Алова. Толщина алюминиевой вставки должна составлять приблизительно 50% от толщины стенки отливки. При этом соотношение толщин алюминиевой вставки и стенки отливки корочка чугуна должна успеть затвердеть на достаточную глубину и выдержать давление жидкой фазы с началом плавления алюминия. На практике, вставка толщиной всего 25% от размера отливки, позволяет получить качественную продукцию без видимых дефектов.
Вставка из алюминия обладает большой теплопроводностью, что способствует первоначально быстрому росту корочки чугуна. На скорость затвердевания оказывала влияние и толщина стенки стального кокиля. При ее увеличении, наблюдалось замедление роста корочки чугуна, а иногда и частичное подплавление. Причиной этого явилось снижение теплопроводности стенки кокиля. Более тонкая стенка способствует более быстрому охлаждению, чем толстая.
Данные по каждой отливке приведены в табл. 1. Толщина алюминиевой вставки, указанная в таблице, минимальная. Скорость подъема металла — расчетная, а в скобках — применяемая в расчетах.
Список литературы
- Булыитейн Р.И., Городчиков В. Н. Противопригарная краска для чугунных оливок // Литейное производство. -1989. — 3. с.26−28.
- Пат. 5 457 424 Япония, МКИ В22С 3/00. Краска для металлических форм / 545 742- Заявл. 17.10.77. Опубл. 9.05.79. МКИ 60 204.
- Ващенко К.И. и др. Биметаллические отливки Fe А1 / К. И. Ващенко, В. В. Жижченко, А. Н. Фирстов. — М.: Машиностроение, 1966. — 150 с.
- Giesserei, 64 /1977/, 14 391/95.
- Кожемякин С.П. Алитирование чугунных отливок при изготовлении их в расплавляемых алюминиевых кокилях // Автореф. дисс. докт. техн наук. Москва, 1987. — 36 с.
- Лакедемонский А. В. Бимиталлические отливки. М.: Машиностроение, 1964. — 318 с.
- Литье в кокиль / Под ред. И. А. Вейника. М.: Машиностроение, 1980. — 250с.
- Паевич М. Б. Структура чугуна при литье в обычные и облицованные кокиля // Литейное производство. 1978. -5. — С. 9 — 10.
- А. с. 582 895 СССР МКИ В 22 Д 15/00. Кокиль для получения полых фасонных отливок / Г. Н. Бейзер, Е. И. Ду-нер и др. (СССР). 1977, Бюл. 45.
- Вейник А. И. Теплообмен между слитком и изложницей. М.: Металлургиздат, 1959. — 357 с.
- Снижение трудоемкости изготовления кокилей / А. А. Бакулев, А. П. Бессчетнов, А. А. Гайдуков и др. //Литейное производство. 1981. — 9. — С. 36 — 37.
- А. с. 656 736 СССР, МКИ В22Д15/00. Выплавляемый стержень/ В. И. Максименко, М. В. Мальцев (СССР). -1979, Бюл. 14.
- А. с. 455 798 СССР, МКИ В22Д15/00. Выплавляемый стержень/ Н. П. Пименов, В. В. Марков, 3. Н. Юшкова (СССР). 1975, Бюл. 1.
- А. с. 450 637 СССР, МКИ В22Д15/00. Металлический выплавляемый стержень/ Ю. А. Караник (СССР). — 1974, Бюл. 43.
- А. с. 476 079 СССР, МКИ В22Д15/00. Металлический выплавляемый стержень/ Ю. А. Караник (СССР). 1975, Бюл. 26.
- Пат. 61- 199 052 Япония, МКИ С 22 С 37/08 Литье биметаллических отливок / Миясита Кендзиро, Ота Киеси. (Япония). 54−13 420 Заявлено 28.02.85- Опубл. 31.01.79. МКИ 60 397.
- А. с. 53 298 СССР, МКИ В22Д15/00. Способ изготовления отливок/ Л. Я. Садогурский (СССР). 1980, Бюл. 12.
- А. с. 540 683 СССР, МКИ В22Д15/00. Металлический выплавляемый стержень/ Ю. А. Караник (СССР). 1976, Бюл. 48.
- Кошеватсчкий В. М., Кобринская Б. Н., Нетес JI. Я. Расплавляемые металлические стержни и формы // Технология и оборудование литейного производства. Выпуск 12. — С. 1 — 9. (экспресс-информ., сер. 4).
- Формирование структуры чугунных отливок в кокилях с расплавляемой облицовкой / В. А. Алов, С. П. Кожемякин, И. М. Чебурахин, В. И. Корсунский // Литейное производство. 1989. 11. — С. 23 — 24.
- Гуляев Б.Б. И др. Выплавляемые стержни при литье под давлением / Б. Б. Гуляев, А. Б. Зуев, А. В. Масюкевич // Литейное производство. 1966. — 5. — С. 5 — 6.
- Рябов В. Р. Алитирование стали. М.: Металлургия, 1973. — 315 с.
- Биметаллические соединения / К. Е. Чарухина, С. А. Голованенко, В. А. Мастеров, Н. Ф. Казаков. М.: Металлургия, 1970. — 412 с.
- Спринг С. Очистка поверхности металлов / Под ред. О. И. Бибикова. М.: Мир, 1966. — С. 207 — 214.
- Окисление металлов. Том I. Теоретические основы/ Под ред. Ж. Бенара. перев. с франц. М.: Металлургия, 1968. -516 с.
- Оно А. Затвердевание металлов. Токио, 1976. Пер. с англ., — М.: Металлургия, 1980, — 260 с.
- Окисление металлов. Том II. Теоретические основы / под ред. Ж. Бенара. перев. с франц. — М.: Металлургия, 1968. 540 с.
- Лякишев Н. П. И др. Алюминотермия / Н. П. Ляки-шев, Ю. Л. Плинер, Г. Ф. Игнатенко. -М.: Металлургия, 1978. 424 с.
- Шварцкопф А. А. Оптимизация нагрева и слитков и отливок. Дис. канд. тех. наук. — Магнитогорск, 1985. -141с.
- Тепловые процессы при непрерывном литье стали / Под ред. Ю. А. Самойловича. М.: Металлургия, 1982. — 260 с.
- Вейник А. И. Теория особых видов литья. М.: Маш-гиз, 1958. — 300 с.
- Вейник А. И. Теория затвердевания отливки. М.: Машгиз, 1960.- 435 с.
- Определение температуры контакта в задача Стефана -Шварца для случая плавящейся формы / В. М. Рябков, А. А. Шварцкопф, Д. Х. Девятов, С. П. Кожемякин // Известия вузов. Черная металлургия. 1986. — 6. — С. 116 — 118.
- Гуляев Б.Б. Теория литейных процессов. М. — Л.: Машиностроение, 1976.-214с.
- Ландау Л.Д., Лифшиц Е. М. Теоретическая физика. Т.6. Гидродинамика. М.: Наука, 1986. — 272 с.
- Попель С. И. и др. Теория металлургических процессов / С. И. Попель, А. И. Сотников, В. Н. Бороненков. М.: Металлургия, 1986. — 462 с.
- Вабищев П. Н. Численные методы решения задач со свободной границей. М.: Московский университет, 1987. — 114 с.
- Самарский А.А. Теория разностных схем. — М.: Наука, 1977. 220 с.
- Самарский А.А., Попов Ю. П. Разностные методы решения задач газовой динамики. — М.: Наука, 1980. — 325 с.
- Флетчер К. Вычислительные методы в динамике жидкостей. Т. I. М.: Мир, 1991. — 420 с.
- Mitchell A. R., Griffiths D. F. (1980). The Finite Difference Method in Partial Differential Equations (Wiley -Interscience, New York).
- Справочник литейщика. Справочник. / Под ред. Лев, Могилев.
- Гиршович Н. Г. Кристаллизация и свойства чугуна в отливках. М.: Л.: Машиностроение, 1966. — 562 с.
- Гун Г. С. И др. Обработка прокатных валков / Г. С. Гун, В. Е. Соколов, Н. Н. Огарков. М.: Металлургия, 1983. — 112 с.
- Будагьянц Н. А., Карсский В. Е. Литые прокатные валки. М.: Металлургия, 1983. — 175 с.
- Полухин П. И. Пути повышения эффективности работы непрерывных многовалковых станов тонколистовой прокатки // Известия вузов, Черная металлургия. 1961. — 7.
- Полухин П. И. Изучение напряжений и деформации валков стана кватро оптическим методом // Известия вузов, Черная металлургия. 1960. — 11.
- Полухин П. И. Повышение эффективности работы валков при холодной прокатке тонких листов // Сталь. 1961. — 7.
- Мерзляков В. И. Обработка и ремонт прокатных валков. М.: Металлургиздат, 1957. — 246 с.
- Кривошеев А. А. Литые валки. — М.: Металлургиздат, 1957. 360 с.
- Горшков А. А. Чугунные закаленные валки. Свердловск.: уралгиз, 1934. — 230 с.
- Кащенко Ф. Д., Фетняева Л. А. Прокатные валки с литыми ручьями. М.: Металлургия, 1987. — 80 с.
- Кривошеев А. Е. Литые валки. — М.: Металлургиздат, 1957. 360 с.
- Третьяков А. В., Гарбер Э. А. Расчет и исследования валков холодной прокатки. М.: Металлургия, 1966, — 178 с.
- Гедеон М. В. и др. Термическая обработка валков холодной прокатки / М. В. Гедеон, Г. П. Соболь, И. В. Паи-сов. М.: Металлургия, 1970. — 344 с.
- Мерло О. Э. Качество чугунных прокатных валков. -М.: Металлургия, 1966. 245 с.
- Бешлык А. С. Чугунные прокатные валки. М.: Ме-таллургиздат, 1955. — 291 с.
- Миляев А. Ф. Плавильные средства литейных цехов. -Магнитогорск, 1989. 92 с.
- Гиршович И. Г. и др. Повышение качества чугуна при выплавке в индукционной печи дуплекс-процессом / И. Г. Гиршович, А. Я. Иоффе, В. А. Белицкий. JL: ЛДНТП, 1976. — 28 с.
- Онуфриев И. А. О развитии электроплавки чугуна в СССР // Литейное производство. 1981. — 7. — С. 2 — 3.
- Halot L. Les fours electriques // Homne et fonderie. -1980. 110. — C. 45 — 49.
- Платонов Б. П. и др. Индукционные печи для плавки чугуна / Б. П. Платонов, А. Д. Акименко, С. М. Богуцкая. М.: Машиностроение, 1976. — 176 с.
- Производство и эксплуатация валков на металлургическом предприятии. Том I. Изготовление валков / А. А. Гостев, К. Н. Вдовин, В. А. Куц и др. М., Москва, Академия проблем качества РФ: 1997, — 185 с.
- Простяков А. А., Свистунова М. Я. Технико-зкономический анализ индукционных тигельных печей для плавки чугуна // Литейное производство. 1981. — 7. — С. 25.
- Пельц Б. Б., Фомин Н. И. Современные тенденции развития индукционных плавильных печей // Исследование и разработка индукционных плавильных печей: Сб. науч. тр. ВНИИЭТО. М.: Энергоатомиздат, — 1986, — С. 126.
- Клецкин Я. Г. Ваграночная плавка чугуна в литейных цехах за рубежом // Литейное производство. 1981. — 12.
- Огородник В. Н., Кремнев Л. А. Современное состояние ваграночной плавки за рубежом // Литейное машиностроение. М.: НИИМаш, — 1978. — С. 82.
- Тарасов В. И. Канальные индукционные печи для выдержки и перегрева чугуна фирмы ASEA // Литейное производство. 1972. — 5. — С. 8 — 11.
- Иванов Г. П. Теплообмен между слитком и изложницей. М.: Машиздат, 1951. — 120 с.
- Гуляев Б. Б. Затвердевание и неоднородность стали. -Л. М.: Металлургиздат, 1950. — 228 с.
- Вейник А. И. Тепловые основы теории литья. — М.: Машгиз, 1953. 220 с.
- Семикин и. Д., Гольдфарб Э. М. Динамика затвердевания отливок // Литейное производство. 1956. — 2. — С. 20 — 22.
- Карский В. Е. Прокатные валки для новых рельсоба-лочных станов // Сталь. 1951. — 12. — С. 10 — 12.
- Иванов Н. И. и др. Совершенствование производства стали / Н. И. Иванов, Ф. Д. Кащенко, Н. А. Мордзилович. Магнитогорск, 1972, вып. 115. С. 117 — 121.
- Северденко В. П., Бахтионов Ю. Б. Валки для профильного проката. М.: Металлургия, 1979. — 240 с.
- Воронцов Н. М., Жатдан В. Т. Эксплуатация валков обжимных и сортовых станов. М.: Металлургия, 1973. -270 с.
- Скобло Т. С. и др. Обработка металлов давлением / Т. С. Скобло, В. К. Перфенюк, Н. И. Сандлер. Москва, 1979, вып. 18. С. 151 — 172.
- Frasek G. Walce hutnicze odlewane formach requlowanej intensywnosci krzepniecia i stygniecia // Przeglad edlewnictwa. 1979. — V. 29. — 4. — P. 118 — 120/
- Лебедев В. Б. и др. Применение алюминиевых вставок в формах для титанового литья / Труды IV научно — технической конференции молодых ученых и специалистов. -Москва, МАТИ. 1980. — 10 с. — Библиогр.: 7 назв. — Деп. ЦНИК 10.10.80, 684.
- Караник Ю. А. Изготовление кокильных отливок с выплавляемыми стержнями / Литейное производство. — 1976. 12. — С. 34 — 35.
- Кожемякин С. П. Кокиль с расплавляемой облицовкой облицовкой / Магнит, горно. — мет. институт. — Магнито-горск, 1984. 6 с. — Деп. в НИИМАШ 14.10.84, 332 мш -Д83.
- Вдовин К. Н. и др. Изготовление отливок с расплавляемыми вставками / К. Н. Вдовин, С. П. Кожемякин, А. П. Воронцов // Литейное производство. 1996. — 6. — С. 10.
- Корсунский В. И. Алитирование чугунных отливок при изготовлении их в расплавляемых алюминиевых кокилях / Ред. журн. «Изв. вузов. Черная металлургия». Магнитогорск, 1987. — 7 с. — Библиогр. 4 назв. — Деп. во ВНИИ-ТЭМР 25.02.87.
- Определение температуры контакта в задаче Стефана -Шварца для случая плавящейся формы / В. М. Рябков, А.
- А. Шварцкопф, Д. X. Девятов, С. П. Кожемякин // Известия вузов. Черная металлургия. — 1986. 6. — С. 116 — 118.
- Кожемякин С. П. Экспериментальное исследование процесса изготовления чугунных отливок в расплавляемых кокилях / Ред. журн. «Изв. вузов. Черная металлургия». — Магнитогорск, 1984. 20 с. — Деп. во ВНИИТЭМР 10.11.84,209 мш 84 Дш.
- Носков Б. А. Производство литых молотовых штампов.- Киев Москва.: Машгиз, 1953. — 150 с.
- Иванов В. Н., Зарецкая Г. М. Литье в керамические формы по постоянным моделям. М.: Машиностроение, 1975. — 136 с.
- Короткое А. Н. и др. Точное литье кузнечных штампов / А. Н. Короткое, А. Н. Матвеев, А. В. Орлов // Автомобильная промышленность. — 1975. 2. — С. 30 — 32.
- Крутиков В. К. и др. Долговечность стальных ковочных штампов, отлитых в формы со стержнями из ХТС / В. К. Крутиков, В. В. Купиловский, Л. А. Губарев // Литейное дело. 1978. — 11. — С. 33 — 34.
- Щербаков К. Л. Современное состояние вакуумно -пленочного способа изготовления песчаных форм // Литейное производство. 1976. — 4. — С. 27 — 28.
- Караник Ю. А. Изготовление кокильных отливок с выплавляемыми стержнями // Литейное производство. 1976.- 12. С. 34 — 35.
- Штальман Н. В. Рентгенографическое определение напряжений в чугунных отбеленных валках // Металловедение и термическая обработка. 1962. — 8. — С. 19 — 21.
- Marghescu M., Mitrofan A. Posibilitati demarire a rezistentei la usura a cilindrilor de laminor pentru profil grele // Metalurgia. 1971. — 23. — 11. — C. 377 — 381.
- Бунина Ю. К., Руднев О. Н. Влияние профиля калибров на структуру отбеленных сортопрокатных валков. в кн.: Металлургия и коксохимия. — Киев.: Наукова дум-ка, 1970. — С. 111 — 116.
- Кривошеев А. Е. Влияние температурных условий работы кокилей на качество отбеленных валков // Металлургическая и горнорудная промышленность, 1973. — 6. — С. 39 — 41.
- Выдрин В. Н., Ситников JI.JI. Стойкость прокатных валков. — Челябинское книжное издательство, 1964. С. 72 с ил.
- Княжанский М. У. Отливка крупносортных профилированных валков повышенной твердости // Сталь, 1964. -5. — С.438 — 440.
- Кривошеев А. Е., Котешов Н. П. Влияние калибровки кокилей на скорость охлаждения отбеленных сортопрокатных валков // Изв. вузов. Черная металлургия, 1966. -12. — С. 122 — 126.
- Цыцкина Н. П. Отливка профилированных чугунных прокатных валков для рельсобалочных и крупносортовых станов // Металлургическая и горная промышленность, 1961. 2. — С. 30 — 34.
- Гунин И. В., Павловский В. Я., Шнееров Б. Я. Анализ причин поломок и перевалок валков при прокатке облегченных профилей. В кн.: Технология производства и свойства черных металлов. — М.: 1968, с. 183 — 188.
- Кривошеев А. Е., Котешов Н. П. Повышение стойкости сорто-трубопркатных чугунных валков легированием чугуна и отливкой их с готовыми калибрами. В кн.: Металлургия и коксохимия. Киев, 1966, вып. 6, с. 121 — 132.
- Шнееров б. Я., Несмачный А. Н. Сортопрокатное производство. Харьков.: 1973. С. 156 — 158.
- Кащенко Ф. Д., Мордзилович Н. А. Повышение стойкости сортовых валков с литыми ручьями // Изв. вуз. Чур-ная металлургия, 1976. — 1. — С. 94 — 95.
- Хинчин А. С., Фрейдель Р. Р. Устройства для измерения и регулирования температуры крупной отливки // Приборы и системы управления, 1967. — 11. — С. 47 — 48.
- Вабищевич П. Н. Численные методы решения задач со свободной границей . М.: МТУ, 1987