Разработка методологии управления обработкой при точении жаропрочных сталей и сплавов на станках с ЧПУ
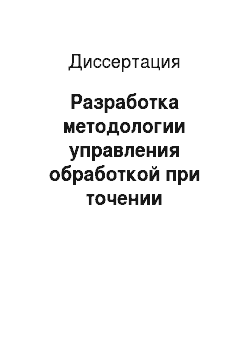
В результате экспериментальных исследований при точении жаропрочных сталей и сплавов с образованием суставчатой стружки установлено распределение напряжений в зоне резания и распределение контактных напряжений на рабочих поверхностях лезвий инструмента при его циклическом нагружении. При этом подтверждено, что обобщающим параметром, характеризующим величины и соотношения контактных напряжений… Читать ещё >
Содержание
- 1. ПРОБЛЕМЫ ОБРАБОТКИ ЖАРОПРОЧНЫХ СТАЛЕЙ И СПЛАВОВ ПРИ ТОЧЕНИИ НА СТАНКАХ С ПРОГРАММНЫМ УПРАВЛЕНИЕМ. СОСТОЯНИЕ ВОПРОСА И ЗАДАЧИ ИССЛЕДОВАНИЯ
- 1. 1. Точение жаропрочных сплавов на станках с ЧПУ, нагружение и прочность инструмента при нестационарном резании
- 1. 2. Проблемы формообразования криволинейным лезвием сложных поверхностей вращения при точении на станках с ЧПУ
- 1. 3. Системы и алгоритмы управления обработкой при точении на станках с числовым программным управлением
- 1. 4. Состояние вопроса и задачи исследования
- 2. ФОРМИРОВАНИЕ МЕТОДОЛОГИИ УПРАВЛЕНИЯ ОБРАБОТКОЙ ПРИ ТОЧЕНИИ ЖАРОПРОЧНЫХ СПЛАВОВ НА СТАНКАХ С ЧПУ
- 2. 1. Методологические проблемы теории и практики управления обработкой жаропрочных сталей и сплавов на станках с ЧПУ
- 2. 2. Формирование структуры методологии решения проблемы
- 2. 3. Модель системы диагностики и управления обработкой при точении жаропрочных сталей и сплавов на станках с ЧПУ
- 2. 4. Выводы по разделу
- 3. НАПРЯЖЕННО-ДЕФОРМИРОВАННОЕ СОСТОЯНИЕ ИНСТРУМЕНТА ПРИ ТОЧЕНИИ ЖАРОПРОЧНЫХ СТАЛЕЙ И СПЛАВОВ
- 3. 1. Лазерная и голографическая нанометрия деформирования режущего клина инструмента
- 3. 2. Установки и методы определения напряженно-деформированного и теплового состояния инструмента в процессе резания
- 3. 3. Модели напряжений, деформации и температуры в режущих элементах инструмента при точении жаропрочных сталей и сплавов
- 3. 4. Выводы по разделу
- 4. ДЕФОРМИРОВАНИЕ СРЕЗАЕМОГО СЛОЯ И НАГРУЖЕНИЕ ЛЕЗВИЙ РЕЖУЩЕГО ИНСТРУМЕНТА ПРИ ТОЧЕНИИ
- 4. 1. Модель деформирования срезаемого слоя и кинематическая модель формирования суставчатой стружки
- 4. 2. Модель системы напряжений в зоне резания во взаимосвязи с параметрами деформирования срезаемого слоя
- 4. 3. Модель системы контактных нагрузок на рабочих поверхностях инструмента при точении жаропрочных сталей и сплавов
- 4. 4. Выводы по разделу
- 5. РАЗРУШЕНИЕ ЛЕЗВИЙ, НАКОПЛЕНИЕ ПОВРЕЖДЕНИЙ И РЕСУРС ИНСТРУМЕНТА ПРИ ТОЧЕНИИ ЖАРОПРОЧНЫХ. СПЛАВОВ
- 5. 1. Модель повреждений режущего инструмента по данным лазерного сканирования разрушений его режущих лезвий
- 5. 2. Модель накопления повреждений инструмента в условиях нестационарного резания жаропрочных сталей и сплавов
- 5. 3. Модель ресурса режущего инструмента по критерию его циклической прочности
- 5. 4. Выводы по разделу
- 6. ДИАГНОСТИКА НАГРУЗОЧНЫХ ХАРАКТЕРИСТИК ПРИВОДОВ И ЭЛЕМЕНТОВ ТС ПРИ ТОЧЕНИИ НА СТАНКАХ С ЧПУ
- 6. 1. Диагностика нагружения приводов станков с ЧПУ и модель составляющих силы резания
- 6. 2. Модели отклонений расположения элементов ТС при их нагружении в процессе нестационарного резания
- 6. 3. Формирование модели оперативных коррекций по траекториям перемещений инструмента в процессе точения на станках с ЧПУ
- 6. 4. Выводы по разделу
- 7. СОВЕРШЕНСТВОВАНИЕ УПРАВЛЕНИЯ ОБРАБОТКОЙ ПРИ ТОЧЕНИИ ЖАРОПРОЧНЫХ СПЛАВОВ НА СТАНКАХ С ЧПУ
- 7. 1. Методология и модель управления нагружением инструмента при наиболее полном использовании его прочностного ресурса
- 7. 2. Синтез структуры программного обеспечения, алгоритмов и интерфейса оператора при управлении обработкой от РСМС
- 7. 3. Инновационная эффективность методологии управления обработкой жаропрочных сталей и сплавов на станках с ЧПУ
- 7. 4. Выводы по разделу
Разработка методологии управления обработкой при точении жаропрочных сталей и сплавов на станках с ЧПУ (реферат, курсовая, диплом, контрольная)
Модернизация экономики страны обуславливает реализацию в промышленности высоких технологий, связанных в сфере машиностроительного производства с переходом к высокоточной обработке на станках с числовым программным управлением (ЧПУ). В то же время экономика современного производства диктует необходимость максимального повышения производительности процессов обработки, чтобы в короткие сроки окупались затраты на приобретение весьма дорогостоящего высокотехнологичного оборудования.
Однако повышение режимов резания в процессе точения высокопрочных труднообрабатываемых материалов на станках ЧПУ приводит к существенному увеличению силовых и температурных контактных нагрузок и сопровождается нарушением работоспособности инструмента. При этом изменяется характер проявления отказов инструмента и вместо образования фаски износа преобладающими становятся разрушения с накоплением повреждений, которые проявляются в виде выкрашиваний, а также микрои макросколов режущих лезвий.
Точение на станках с ЧПУ сложных поверхностей вращения (СПВ) с прямолинейными и криволинейными образующими (до 70% от общей площади) деталей из высокопрочных труднообрабатываемых материалов, используемых в авиастроении, энергетическом, нефтегазовом машиностроении и др., происходит в специфических условиях нестационарного резания и сопровождается интенсивным разрушением режущих лезвий, что приводит к снижению точности обработки и нерегламентированным отказам инструмента. Обеспечение точности формообразования СПВ деталей из жаропрочных сталей и сплавов на практике достигается за счет «уточнения» выдерживаемых размеров при выполнении дополнительных проходов с «ручным» вводом коррекций, которые устанавливаются на основании накопленного опыта работы.
Проведенный на предприятиях высокотехнологичных отраслей промышленности экспертный опрос специалистов, показал, что наиболее распространенным (до 64%) способом повышения работоспособности при недостаточной прочности инструмента в условиях нестационарного резания является занижение по сравнению с нормативными значений подач, скоростей и глубин резания. Тем не менее, несмотря на существенное увеличение трудоемкости обработки, эти процессы, как правило, сопровождаются потерями по инструментальным расходам, браку и простоям дорогостоящего оборудования' с ЧПУ. Диктуемое условиями, производства обеспечение стабильности обработки на станках с ЧПУ предопределяет с учетом накопления повреждений инструмента необходимость эффективного управления процессами нестационарного резания. Это обуславливает разработку моделей и алгоритмов, а также способов и устройств для диагностики и управления с оперативным вводом коррекций одновременно по режимам резания и по траекториям движения формообразующего режущего инструмента (ФРИ), что при модернизации производства принципиально может быть реализовано с использованием станков, оснащенных современными системами ЧПУ.
Проведенный при выполнении диссертационной работы анализ показал, что комплексное решение актуальных задач современного высокотехнологичного машиностроительного производства может быть реализовано разрешением научной проблемы — максимального повышения производительности обработки жаропрочных сталей и сплавов на станках с ЧПУ, обеспечиваемым разработкой методологии максимального (наиболее полного) использования ресурса режущего инструмента по критерию прочностности при совершенствовании теории и практики управления процессами его нагружения.
С учетом изложенного выше при выполнении диссертационной работы объектом исследований являются процессы накопления повреждений лезвий инструмента при нестационарном резании высокопрочных труднообрабатываемых материалов на станках с числовым программным управлением.
При этом, предметом исследования является нагружение, деформирование, разрушение режущих лезвий и изменение их геометрических параметров, а также взаимосвязь деформирования срезаемого слоя с нагружением инструмента силовыми и температурными контактными нагрузками при точении жаропрочных сталей и сплавов на станках с ЧПУ.
В процессе выполнения диссертационной работы для исследований напряженно-деформированного состояния режущей части инструмента из ме-таллокерамических твердых сплавов и инструментальных сталей созданы установки, а также отработан и применен метод лазерной нанометрии деформирования режущего инструмента (A.C. 1 173 179). Разработаны установки и методики лазерного сканирования прямолинейных и криволинейных лезвий режущего инструмента (A.C.1 089 539). Разработаны основанные на принципах мехатроники способы и устройства для оперативного определения непосредственно в процессе резания параметров деформирования срезаемого слоя по величине усадки стружки (Пат.2 254 210, Пат. 2 311 990). Использованы основные положения, методология и методы технологии машиностроения, теории резания и теории автоматического управления, теории конечных пластических деформаций, теории прочности, фрактографии и механики разрушений, вычислительной математики, математической обработки результатов экспериментов, компьютерного моделирования и программирования. Разработанные вычислительные алгоритмы и программы имеют оригинальное авторское содержание (Свид.ОРП 2 003 611 797, 2 003 611 798, 2 007 613 348, 2 008 610 386, 2 008 610 387, 2 008 610 388). Экспериментальные исследования и их технологическая привязка к условиям производства проведены в лабораториях ГОУ ВПО «ТюмГНГУ», а также на базе ОАО «Тюменские авиадвигатели», ОАО «Газтурбосервис», ОАО «Сибнефтегазмаш», ЗАО «Станкосервис» с использованием современных аттестованных приборов, методов и средств измерений.
Научные положения, выводы и рекомендации, сформулированные в диссертации, обоснованы теоретическими решениями, базирующимися на положениях механики и теплофизики процессов резания, теории упругости, теории пластичности, механики деформируемого тела, физики оптических явлений. Принятые допущения получили мотивированное обоснование. Во всех необходимых случаях осуществлена экспериментальная проверка теоретических решений. При проведении экспериментальных исследований использована аттестованная измерительная техника. Достоверность и обоснованность теоретических выводов подтверждена данными производственных испытаний, а также экспериментальными данными, полученными лично соискателем и при его непосредственном участии.
Научная новизна. «Разработаны теоретические положения и научно обоснована методология обеспечения работоспособности инструмента на основе наиболее полного использования его ресурса по критерию циклической прочности в процессе точения жаропрочных сталей и сплавов.
• С использованием метода лазерной нанометрии деформирования инструмента непосредственно в условиях резания жаропрочных сталей и сплавов определены параметры деформирования, а также установлены закономерности распределения силовых и температурных деформаций и напряжений в режущем клине инструмента из инструментальных сталей и металлокерами-ческих твердых сплавов.
• С использованием метода лазерного сканирования установлен вид и экспериментально подтверждена адекватность моделей накопления повреждений, обусловленных разрушением лезвий инструмента в процессе точения жаропрочных сталей и сплавов. Получены зависимости параметров накопления повреждений от величин контактных напряжений и температур, а также числа циклов нагружения режущих лезвий.
• Научно обоснована, выдвинута и подтверждена результатами экспериментальных исследований гипотеза об условиях перехода от образования сливной к образованию суставчатой стружки при достижении конечных пластических деформаций удлинения в направлении текстуры стружки, формирующейся при резании. Создана кинематическая модель формирования суставчатой стружки, разработаны алгоритмы определения геометрических параметров образующихся при этом элементов. Это позволило схематизировать распределение напряжений, а также получить модели параметров контактного взаимодействия в зоне резания и на рабочих поверхностях лезвий твердосплавного инструмента при его циклическом нагружении.
• Установлено, что при оценке прочности инструмента напряженное состояние режущего лезвия в различных фазах формирования элементов суставчатой стружки описывается асимметричными циклами сложной системы напряжений. При этом работоспособность инструмента определяется удельной работой и относительным объемом разрушения его лезвий, а также кумулятивной функцией накопления повреждений Пальмгрена-Майнера, являющейся одновременно энергетической и вероятностной характеристикой прочности режущего инструмента.
• Предложена концепция прогнозированияа также модель ресурса режущего инструмента' по критерию циклической прочности при нестационарном резании. Концепция основана на определениидопускаемого прочностью инструментального твердого сплава числа циклов нагружениярежущих лезвий с учетом установленной системы напряжений, действующих в режущем клине инструмента.
• Показано, что стабилизация деформирования срезаемого слоя обеспечивает постоянство контактных напряжений и температур на рабочих поверхностях инструмента в условиях нестационарного резания.
• Разработана модель интегрированной системы (ИСДУ), сочетающей диагностику процессов нагружения приводов станка с ЧПУ и элементов ТС с вводом комплекса коррекций при управлении обработкой. Предложены алгоритмы и программное обеспечение оперативного ввода коррекций одновременно в режимы резания и в траектории движения формообразующего режущего инструмента (ФРИ).
• Установленочто разработанная методология управления, реализующая сочетание коррекций в наибольшей мере компенсирует погрешности, возникающие в ТС при нестационарном резании, и обеспечивает наиболее полное использование ресурса инструмента по критерию циклической прочности при максимальной производительности обработки жаропрочных сталей и сплавов на станках с ЧПУ.
Практическая ценность работы заключается в разработке теоретического, методического и программного комплексов, сформированных для повышения эффективности лезвийной обработки. Практическую значимость имеет также использование установок, устройств и инструментов, обеспечивающих повышение эффективности обработки на станках с ЧПУ, для реализации которых:
• разработаны методы и устройства для определения параметров повреждений инструмента, позволяющие прогнозировать накопление и интенсивность разрушений лезвий режущего инструмента при точении жаропрочных сталей и сплавов на станках с ЧПУ (A.C. 1 173 179, A.C. 1 089 539);
• создана система диагностики деформирования срезаемого слоя на основе оперативного определения кинематической усадки, позволяющая при изменениях сечения срезаемого слоя, скорости и глубины резания, подачи и диаметра обработки, а также при накоплении повреждений режущих лезвий обеспечивать стабилизацию контактных напряжений и температур на рабочих поверхностях лезвий инструмента в условиях нестационарного резания при точении жаропрочных сталей и сплавов на станках с ЧПУ (Пат. 2 009 804, Пат. 2 254 210, Пат. 2 311 990);
• созданы конструкции сборного режущего инструмента, обеспечивающие повышение его работоспособности за счет рационального силового и температурного нагружения сменных режущих пластин (СРП), а также комплекс модулей для определения параметров процесса резания, состояния и диагностики отклонений расположения элементов ТС при их нагружении в процессе нестационарного резания (А.С.901 844, А.С.1 157 601, Пат. 2 009 804, Пат. 2 076 017, Пат. 2 235 622 Пат. 2 238 825, Пат. 2 240 207, Пат. 2 245 226, Пат.2 245 228, Пат.2 309 818, Пат.2 309 819);
• предложен программно-аппаратный комплекс диагностики и управления обработкой, программные продукты для диагностики процесса резания и управления следящим и шаговым приводами исполнительных рабочих органов (ИРО) станков, реализующие при использовании систем числового программного управления класса PCNC (Personal Computer Numerical Control) интерполяцию и оперативный ввод коррекций в траектории движения формообразующего режущего инструмента (ФРИ) в процессе точения СПВ фасонных деталей из жаропрочных сталей и сплавов на станках с ЧПУ (Свид.ОРП. 2 003 611 797, 2 003 611 798, 2 007 613 348, 2 008 610 386,2008610387,2 008 610 388).
Реализация результатов работы. Диссертационная работа выполнялась в рамках комплексных программ: «АВИАЦИОННАЯ ТЕХНОЛОГИЯ», раздел 05.01 — «Методы механической обработки», а также «Общесоюзной целевой комплексной научно-технической программы О.Ц.ОП», раздел 09.01 АН СССР. В 2000 г. работа была поддержана грантом Минобразования РФ, а с 2001 г. разделы работы выполнялись при поддержке грантов Губернатора Тюменской области в соответствии с Региональной целевой программой «РАЗВИТИЕ ПРЕДПРИЯТИЙ МАШИНОСТРОЕНИЯ И МЕТАЛЛООБРА.
БОТКИ". В 2003 году выполненные разработки были представлены в г. Москва на Всероссийском выставочном центре (ВВЦ) и отмечены дипломом IX-й Международной выставки научно-технических проектов «ЭКСПО — Наука 2003», а также медалью «ESI — Moskow 2003». Результаты исследований и разработки диссертации в соответствии с Региональной целевой программой внедрены на предприятиях Тюменской области, а именно: ОАО «ТЮМЕНСКИЕ АВИАДВИГАТЕЛИ», ОАО «ТЮМЕНСКИЕ МОТОРОСТРОИТЕЛИ», ОАО «ГРОМ», ОАО «Газтурбосервис», ОАО «Сибнефтемаш», ОАО «Сибтехмаш», ОАО «Нефтепроммаш», ОАО «СТАНКОСЕРВИС», ООО «Сибинструментсервис» и др. При изготовлении фасонных деталей авиадвигателей, турбин и деталей нефтегазового оборудования реализовано переоснащение токарных станков модернизированными системами ЧПУ класса PCNC и диагностическими модулями. Диагностика ТС и оперативный ввод коррекций по траекториям движения ФРИ и режимам резания реализованы с использованием специализированного программно-аппаратного комплекса. Реализовано точение СПВ фасонных деталей из жаропрочных сталей и сплавов, разработаны конструкции сборного режущего инструмента и системы оперативного ввода коррекций при управлении процессами нестационарного резания, что обеспечило наибольшую для конкретных условий производства эффективность обработки на станках с ЧПУ. Экономический эффект, подтвержденный актами внедрения результатов диссертационной работы в производство, составляет свыше 2.146.387 рублей.
Под руководством автора и с использованием основных положений его работы подготовлены и защищены кандидатские диссертации.
Результаты исследований используются в учебном процессе ГОУ ВПО «ТюмГНГУ» в виде 5-и учебных пособий, лекционных материалов, а также в курсовом и дипломном проектировании на выпускающих кафедрах машиностроительного профиля.
Автор выражает глубокую благодарность докторам технических наук, профессорам Артамонову Е. В., Ковенскому И. М., Утешеву М. X. и Шала-мову В. Г. за проявленное внимание, разностороннюю поддержку и ценные замечания по работе.
ОСНОВНЫЕ ВЫВОДЫ И РЕЗУЛЬТАТЫ РАБОТЫ.
В1результате: выполненных, комплексных теоретических и экспериментальных исследований, а также внедрения? результатов исследований: в производство решенакрупная^имеющаяшажное: значение-.проблема максимального повышения?: производительности., обработкижаропрочных сталей и сплавов на станках с ЧПУ.
Актуальная научная проблема решена и поставленная цель достигнута на основе разработанных теоретических и методологических положений по управлению обработкой на станках с ЧПУ при наиболее полном использовании ресурса инструмента и максимальном повышении производительности обработки.
Наиболее полное использование ресурса инструмента по критерию циклической прочности при обработке жаропрочных сталей и сплавов на станках с ЧПУ базируется на полученных решениях поставленных задач, а также следующих результатах исследований и выводах:
1. Установлено, что при точении жаропрочных сталей: и сплавов с образованием суставчатой стружки изменяется характер повреждений лезвий твердосплавного режущего инструмента. Преобладающим видом: отказов вместо изнашивания становится накопление повреждений в виде множественных усталостных и смешанных разрушений режущих лезвий. При оценке повреждений инструмента лазерное сканирование режущих лезвий (A.C. 10 895 390) обеспечивает определение геометрических параметров и получение моделей объема и площади образовавшейся при разрушениях поверхности, что позволяет определять интенсивность и энергию разрушений лезвий инструмента при точении жаропрочных сталей и сплавов.
2. Непосредственно при резании высокопрочных труднообрабатываемых материалов экспериментально с использованием лазерной нанометрии деформирования инструмента.(АС. 1 173 179) установлены закономерности распределения деформаций, напряжений и температур в режущем инструменте из инструментальных сталей и металлокерамических твердых сплавов, а также их взаимосвязь с параметрами деформирования срезаемого слоя в процессе нестационарного резания.
3. На основании выдвинутой гипотезы предложена концепция и модель перехода от образования сливной к образованию суставчатой стружки при достижении конечных пластических деформаций удлинения, в направлении формирующейся в процессе резания текстуры стружки. Создана кинематическая модель формирования суставчатой стружки, получены зависимости, позволяющие определять геометрические параметры образующихся при этом элементов.
4. В результате экспериментальных исследований при точении жаропрочных сталей и сплавов с образованием суставчатой стружки установлено распределение напряжений в зоне резания и распределение контактных напряжений на рабочих поверхностях лезвий инструмента при его циклическом нагружении. При этом подтверждено, что обобщающим параметром, характеризующим величины и соотношения контактных напряжений и температур на рабочих поверхностях лезвия инструмента является относительный сдвиг обрабатываемого материала. В условиях нестационарного резания это позволяет при неизменной геометрии лезвия и стабилизации кинематической усадки-стружки реализовать постоянство условий нагружения режущего инструмента (Пат. 2 254 210, Пат. 2 311 990) и тем самым обеспечивать надежность прогнозирования его работоспособности.
5. Показано, что режущий клин инструмента при точении жаропрочных сталей и сплавов с образованием суставчатой стружки нагружается асимметричными циклами сложной системы напряжений и его ресурс при стабилизации контактных нагрузок определяется числом циклов нагружения режущего лезвия. При этом в соответствии с разработанной концепцией, работоспособность инструмента определяется удельной работой и относительным объемом разрушений режущих лезвий, а также кумулятивной функцией накопления повреждений Пальмгрена — Майнера, сочетающей энергетическую и вероятностную характеристики критерия прочности.
6. Предложены модель и алгоритм управления, разработаны защищенные патентами на изобретения и свидетельствами об официальной регистрации программ ЭВМ устройства и программные продукты, для оперативной диагностики и стабилизации параметров деформирования срезаемого слоя (усадки стружки) путем оперативного ввода коррекций режимов резания (Сеид. ОРП. 2 007 613 348, 2 008 610 386, 2 008 610 388). Это обеспечивает рациональное на-гружение и повышение работоспособности инструмента при точении жаропрочных сталей и сплавов на станках с ЧПУ в условиях нестационарного резания. Разработаны защищенные патентами на изобретения конструкции сборного инструмента, обеспечивающие в условиях нестационарного резания рациональное нагружение сменных режущих пластин (СРП) и повышение работоспособности твердосплавного инструмента при точении высокопрочных труднообрабатываемых материалов на станках с ЧПУ (A.C. 778 940, Пат. 2 076 017, 2 235 622, 2 240 207, 2 238 825, 2 245 228, 2 309 819).
7. Разработаны, математические модели, алгоритмы и программное обеспечение ИСДУ, позволяющие с использованием PGNC реализовать диагностику деформирования срезаемого слоя, отклонений расположения элементов ТС, управление следящими приводами станков с ЧПУ (Сеид. ОРП. 2 003 611 797, 2 003 611 798), а также формирование и оперативный ввод коррекций в процесс обработки. На основании разработанных методологических положений установлено, что сочетанием оперативных коррекций одновременно по режимам резанияи по траекториям движения исполнительных рабочих органов станков достигается наибольшая точность формообразования сложных поверхностей вращения деталей в конкретных ТС. При этом также обеспечивается наиболее полное использование ресурса режущего инструмента по критерию циклической прочности при точении жаропрочных сталей и сплавов в условиях нестационарного резания на станках, оснащенных системами ЧПУ класса PCNC.
Список литературы
- Аваков, А. А. Физические основы теории стойкости режущих инструментов Текст. / А. А. Аваков. М.: Машгиз, 1960.- 308 с.
- Адаптивное управление станками Текст. / под ред. Б. С. Балакшина.- М.: Машиностроение, 1973. 688 с.
- Адлер, Ю. П. Планирование эксперимента при поиске оптимальных условий Текст. / Ю. П. Адлер, Е. В. Маркова, Ю. В. Грановский. М.: Наука, 1976.- 279 с.
- Александров, А. Я. Поляризационно-оптические методы механики деформируемого тела Текст. / А. Я. Александров, М. X. Ахметзянов. М.: Наука, 1973.-576 с.
- Андреев, Г. С. Исследование напряжений в рабочей части резца на поляриза-ционно-оптической установке с применением киносъемок / Г. С. Андреев // Вестник машиностроения. 1958. — № 5. — С.54 -57.
- Армарего, И. Д. Обработка металлов резанием Текст. / И. Д. Армарего, Р. X. Браун. М.: Машиностроение, 1977. — 325 с.
- Артамонов, Е. В. Сборный инструмент / Е. В. Артамонов, Ю. И. Некрасов, Н. И. Смолин // Машиностроитель.- М., 1984.- № 5.- С.32
- Артамонов, Е. В. Напряженно-деформированное состояние и прочность режущих элементов инструментов: монография Текст. / Е. В. Артамонов, И. А. Ефимович, Н. И. Смолин, М: X. Утешев. М.: Недра, 2001.- 199 с.
- Артамонов, Е. В. Прочность и работоспособность сменных твердосплавных пластин сборных режущих инструментов Текст. / Е. В. Артамонов. -Тюмень: ТюмГНГУ, 2003. 192 с.
- А. с. 778 940 СССР, МКИ 023 В 27/16. Сборный резец / Е. В. Артамонов, Н. И. Смолин, Ю. И. Некрасов (СССР). № 2 692 663/25−08- Заявл. 06.12.78- Опубл. 15.11.80, Бюл. № 42.
- А. с. 901 844 СССР, МКИ 001 К 7/02. Устройство для измерения температуры / Ю. И. Некрасов, Е. В. Артамонов, И. А. Ефимович, В. С. Воронов (СССР). -№ 2 884 590/18−10- Заявл. 19.02.80- Опубл. 30.01.82, Бюл. № 4.
- А. с. 948 546 СССР, МКИ 023 В 27/16: Сборный резец / Е. В. Артамонов, Ю. И. Некрасов, Н. И. Смолин (СССР). № 3 250 286/25−08- Заявл. 25.02.81- Опубл. 07.08.82, Бюл. № 29.
- А. с. 1 089 539 СССР, МКИ в 02 В 27/17. Сканирующее утройство / Ю. И.
- Некрасов, В- В. Долгушин, И. А. Еремеев (СССР). № 358 891/18−10- Заявл. 08:02.83- Опубл. 30.04.84, Бюл. № 16:
- А. с. 1 143 526 СССР, МКИ В23С 5/06. Режущий инструмент / И: А. Ефимович, Е. В. Артамонов, Ю. И. Некрасов (СССР). № 3 629 284/25−08- Заявл. 05.08.83- Опубл. 07.03.85, Бюл. № 9.
- А. С. 1 157 601 СССР, — МКИ, НО 1 КЗ* 5/00. Устройство для- электрической связи между неподвижным и вращающимся объектами / Ю. И: Некрасов, Е. В. Артамонов, И. А. Ефимович (СССР). № 3 573 114/24−07- Заявл. 04.04.83- Опубл. 23.05.85, Бюл. № 19.
- А. с. 1 173 179 СССР, МКИ 001 В 11/16. Способ исследования деформации материалов в процессе снятия стружки резанием / Е. В. Артамонов, Ю. И. Некрасов, И. А. Ефимович (СССР). № 3 588 086/25−08- Заявл. 08.02.83- Опубл. 15.08.85, Бюл. № зо.
- Афанасьев, Н. Н. Статистическая теория усталостной прочности Текст. / Н. Н. Афанасьев. Киев: изд-во АН УССР, 1953. — 128 с.
- Базров, Б. М. Адаптивное управление станками Текст. / Б: М1 Базров. М.: -М.: Знание, 1975.- 57 с.
- Базров, Б. М. Технологические основы проектирования самопод-настраивающихся станков Текст. / Б. М. Базров. М.: Машиностроение, 1977.-217 с.
- Банков, В. Д. Решение траекторных задач в микропроцессорных системах ЧПУ Текст. / В. Д. Байков, С. Н. Вашкевич- под ред. В. Б. Смолова. JL: Машиностроение, 1986. — 106 с.
- Бакуль, В. Н. Алмазная обработка и прочность твердых сплавов Текст. / В. Н. Бакуль, М. Г. Лошак, Ф. П. Смагленко // Синтетические алмазы ключ к техническому прогрессу: сб. ст.- Ч. 1. — Киев.: Наукова думка, 1977. — С. 114 -118.
- Безлепкин, В. В. Эксплуатация технологических машин Текст.: учебное пособие / В. В. Безлепкин. М.: Станкин, 1996. — 241 с.
- Безъязычный, В. Ф. Оптимизация технологических условий механическойобработки деталей авиационных двигателей Текст. / В. Ф. Безъязычный, Т. Д., А. В. Константинов. М.: МАИ, 1993. — 184 с.
- Беляев, М. С. Надежность и долговечность машин Текст. / М. С. Беляев. -Техника, 1973, — 120 с.
- Бетанели, А. И. К общению метода расчета прочности режущей части инструмента / А. И. Бетанели // Вестник машиностроения: 1965.- № 2. — С. 16−18.
- Бетанели, А. И. Прочность и надежность режущего инструмента Текст. / А, И. Бетанели. Тбилиси: Сабчота Сакартвело, 1973. — 302 с.
- Бобров, В. Ф. Определение напряжений в режущей части металлорежущих инструментов Текст. / В. Ф. Бобров // Высокопроизводительное резание в машиностроении: сб. ст. М., 1966. — С. 233−228.
- Бобров, В. Ф. Основы теории резания металлов Текст. / В. Ф. Бобров. М.: Машиностроение, 1975. — 344 с.
- Бойцов, Б. В. Прогнозирование долговечности напряженных конст- рукций Текст. / Б. В4. Бойцов. М.: Машиностроение, 1985. — 231 с.
- Болотин, В. В. Прогнозирование ресурса машин и конструкций Текст. / В.
- B. Болотин. М.: Машиностроение, 1984. — 311'с.
- Вальков, В. Н. Контроль в ГАП Текст. / В. Н. Вальков. Л.: Машиностроение, 1986. — 232 с.
- Васильев, Д. Т. Силы на режущих поверхностях инструмента / Д. Т. Васильев // Станки и инструмент. 1954. — № 4. — С. 31−33.
- Васильев, Д. Т. Системы автоматического регулирования и управления Текст. / Д. Т. Васильев, В. Г. Чуич. М.: Высшая школа, 1967. — 417 с.
- Васин, С. А. Резание материалов. Термомеханический подход к системе взаимосвязей при резании Текст.: учебник для техн. вузов / С. А. Васин, А.
- C. Верещака, В. С. Кушнер. М.: Изд-во МГТУ им. Н. Э. Баумана, 2001. -448 с.
- Вейбулл, В. Усталостные-испытания и анализ их результатов Текст. / В. Вейбулл- под ред. С. В. Серенсена- пер. с англ. Т. А. Бекш и Е. С. Муслина.- М.: Машиностроение, 1964. 257 с.
- Великанов, К: М. Экономичные режимы резания металлов Текст. / К. М. Великанов, В. И. Новожилов. М.: Машиностроение, 1972. — 120 с.
- Вентцель, Е. С. Теория вероятностей Текст. / Е. С. Вентцель. М.: Наука, 1969.-263 с.
- Верещака, А. С., Исследование теплового состояния режущих инструментов с помощью многокомпозиционных термоиндикаторов / А. С. Верещака, М. В. Провоторов, В. В. Кузин // Вестник машиностроения. 1986. — № 1. -С. 45 — 49.
- Верещака, А. С. Режущие инструменты с износостойкими покрытиями Текст. / А. С. Верещака, И. П. Третьяков. М.: Машиностроение, 1986. -192 с.
- Верещака, А. С. Работоспособность режущего инструмента с износостойкими покрытиями Текст. / А. С. Верещака. М.: Машиностроение, 1993. -198 с.
- Вестфаль, А. Н. Расчет термических напряжений в режущем клине инструмента / А. Н. Вестфаль // Надежность режущего инструмента сб. ст. / Киев, 1975, — С. 78−82.
- Виноградов, А. А. Связь напряжений сдвига при резании с механическими характеристиками обрабатываемого металла / А. А. Виноградов // Сверхтвердые материалы. 1981. — № 2. — С. 47−51.
- Виноградов, А. А. Определение оптимальной скорости резания по коэффициенту усадки стружки / А. А. Виноградов // Станки и инструмент. 1991. — № 7. — С. 32−33.
- Виноградов, А. А. Физические основы процесса сверления труднообрабатываемых металлов твердосплавными сверлами Текст. / А. А. Виноградов.- Киев. Наукова думка, 1992. — 186 с.
- Владимиров, В. И. Физическая природа разрушения металлов Текст. / В. И. Владимиров. М.: Металлургия, 1984. — 280 с.
- Волков, С. Д. Статистическая теория прочности Текст. / С. Д. Волков. -Свердловск: Машгиз, 1960. 176 с.
- Вычислительные методы в механике разрушения Текст. / пер. с англ.- подред. С. Атлури. М.: Мир, 1990. — 392с.
- Гнеденко, Б. В. Курс теории вероятностей Текст. / Б. В. Гнеденко. М.: Наука, 1969. — 400 с.
- Гордеева, Т. Д. Анализ изломов при оценке надежности материалов Текст. / Т. Н. Гордеева, И. П. Жегина. М.: Машиностроение, 1978. -200 с.
- ГОСТ 25.101 83. Расчеты и испытания на прочность. Методы схематизации случайных процессов нагружения элементов машин и конструкций и статистического представления результатов / М., 1983. — 205 с.
- ГОСТ 25.507 85. Расчеты и испытания на прочность в машиностроении. Методы испытаний на усталость при эксплуатационных режимах нагружения /-М., 1985.-321 с.
- Грановский, Г. И. О стойкости инструмента как исходном параметре для расчета режимов резания / Г. И. Грановский // Вестник машиностроения. -1965. № 8. — С. 59- 64.
- Гречишников, В. А. Системы проектирования режущих инструментов Текст. / В. А. Гречишников. М.: ВНИИТЭМР, 1987. — № 2. — 52 с.
- Грищенко, Ю. Ф. О надежности металлорежущего инструмента Текст. / Ю. Ф. Грищенко // Труды МИНХ и ГП им. Губкина. Выпуск 81. — М., 1968. — С. 138−141.
- Громадка, Ц. Т., Лей Ч. Комплексный метод граничных элементов в инженерных задачах Текст. / Ц. Т. Громодка, Ч. Лей.- пер. с англ. М.: Мир, 1990. — 303 с.
- Грубый, С. В. Физическое моделирование процесса изнашивания твердосплавных резцов / С. В. Грубый // Справочник. Инженерный журнал. -2002.-№ 2.-С. 37−43.67