Разработка технологического процесса изготовления осесимметричных деталей с фланцем с применением комбинированного трёхстороннего выдавливания
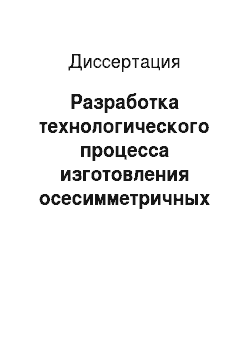
В третьей главе проведены исследования формообразования заготовки типа втулка с фланцем экспериментальным методом координатных сеток и методом конечных элементов (С>Рогт-20) при комбинированном выдавливании. На основе результатов. эксперимента и моделирования получены рекомендации по выбору размеров исходной заготовки и формообразования при комбинированном выдавливании в сужающийся канал… Читать ещё >
Содержание
- ГЛАВА 1. СОСТОЯНИЕ ВОПРОСА
- 1. 1. Исследование процессов прямого, обратного, радиального и комбинированного выдавливания
- 1. 2. Особенности теоретического анализа комбинированного выдавливания
- 1. 3. Исследование напряженно-деформированного состояния металла при холодной объемной штамповке
- 1. 4. Понятие твердости и методы её определения. Влияние деформации на изменение значения твёрдости
- 1. 5. Цель и задачи работы
- ГЛАВА 2. ИССЛЕДОВАНИЕ КИНЕМАТИКИ ТЕЧЕНИЯ МЕТАЛЛА ДЕТАЛЕЙ ТИПА ВТУЛКА С ФЛАНЦЕМ ПРИ КОМБИНИРОВАННОМ ТРЁХСТОРОННЕМ ВЫДАВЛИВАНИИ
- 2. 1. Исходные данные для конечно-элементного моделирования
- 2. 2. Моделирование и исследование комбинированного трёхстороннего выдавливания при различной геометрии рабочего инструмента
- 2. 3. Исследование и прогнозирование возникновения дефекта металла (утяжина) при комбинированном трёхстороннем выдавливании детали типа втулка с фланцем
- 2. 4. Результаты и
- выводы
- ГЛАВА 3. ЭКСПЕРИМЕНТАЛЬНОЕ ИССЛЕДОВАНИЕ КИНЕМАТИКИ ТЕЧЕНИЯ МЕТАЛЛА ДЕТАЛЕЙ ТИПА ВТУЛКА С ФЛАНЦЕМ ПРИ КОМБИНИРОВАННОМ ВЫДАВЛИВАНИИ
- 3. 1. Исследование кинематики течения металла методом координатной сетки
- 3. 2. Обработка результатов испытания образцов
- 3. 3. Сравнение данных, полученных экспериментальным путём, с результатами компьютерного моделирования в системе С>Рогт-2В
- 3. 4. Исследование энергосиловых показателей при комбинированном трёхстороннем выдавливании деталей типа втулка с фланцем в сужающийся канал
- 3. 5. Результаты и
- выводы
- ГЛАВА 4. ИССЛЕДОВАНИЕ ВЛИЯНИЯ ДЕФОРМАЦИИ И
- СХЕМЫ НАПРЯЖЕННОГО СОСТОЯНИЯ НА
- ТВЁРДОСТЬ СТАЛИ
- 4. 1. Исследование зависимости твёрдости от величины деформации и схемы напряженного состояния. Методика проведения испытаний
- 4. 2. Обработка результатов экспериментов
- 4. 3. Результаты и
- выводы
ГЛАВА 5. ПРАКТИЧЕСКОЕ ВНЕДРЕНИЕ ПОЛУЧЕННЫХ РЕЗУЛЬТАТОВ НА ПРИМЕРЕ ТЕХНОЛОГИЧЕСКОГО ПРОЦЕССА ХОЛОДНОЙ ОБЪЕМНОЙ ШТАМПОВКИ ДЕТАЛИ «КОРПУС ШАРОВОГО ПАЛЬЦА», С ПРИМЕНЕНИЕМ КОМБИНИРОВАННОГО ТРЕХСТОРОННЕГО ПРОЦЕССА ВЫДАВЛИВАНИЯ
5.1 Назначение детали
5.2 Разработка и исследование технологического процесса штамповки детали «Корпус шарового пальца», входящей в сборочный узел шаровой опоры передней подвески легкового автомобиля
5.3 Компьютерное моделирование технологического процесса холодной объемной штамповки детали «Корпус. шарового пальца»
5.4 Производственная оснастка для изготовления детали «Корпус шарового пальца»
5.5 Результаты опытной штамповки детали «Корпус шарового пальца»
5.6 Выбор оборудования
5.7 Результаты и
выводы
Разработка технологического процесса изготовления осесимметричных деталей с фланцем с применением комбинированного трёхстороннего выдавливания (реферат, курсовая, диплом, контрольная)
С бурным развитием современной науки и техники всё больше внимания уделяется разработке новых технологий, и последующему их внедрению с целью повышения уровня производства. Благодаря разработке новых технологических процессов появляется возможность получать изделия высокого качества с заданными эксплуатационными свойствами и с наименьшими затратами на их производство.
Холодная объемная штамповка является одним из прогрессивных ресурсосберегающих методов получения изделий высокого качества. Холодной объемной штамповкой (ХОШ) получают. болыиое количество изделий весом от нескольких грамм до нескольких килограмм с точностью до 2−3 класса, чистотой поверхности до 7−10 класса шероховатости. ХОШ получают ответственные детали с высокими и стабильными механическими свойствами, что объясняется отсутствием рекристаллизации в металле и упрочнением (в отличие от горячей объёмной штамповки). Так как заготовки не нагреваются, на поверхности штампованных деталей не происходит образования окалины, обезуглероживания, обесцинкования и т. п., что улучшает качество поковок в целом и сокращает припуски на дальнейшую обработку, тем самым, увеличивая коэффициент использования металла (по сравнению с литьём и горячей штамповкой на 30% и более, по сравнению с обработкой резанием — в 2−3 раза). В ряде случаев поковки не требуют дополнительной обработки, являясь готовыми деталями (коэффициент использования металла составляет 1). Благодаря ХОШ на штампуемых деталях отсутствуют надрезы, появляется направленность волокон вдоль конфигурации штампованной заготовки, улучшается микрогеометрия. Помимо экономии металла существенно снижается трудоёмкость и себестоимость детаI лей, высокий уровень автоматизации и механизации самих процессов. Применение многопозиционных штамповочных автоматов, а также установка на прессы многопозиционных штампов-автоматов, обеспечивает повышение производительности в 5−10 раз и более по сравнению с современными автоматами с ЧПУ для обработки резанием подобных деталей. В отличие от горячей объёмной штамповки, холодная, объёмная штамповка придаёт металлам мелкозернистую структуру.
Помимо выше перечисленных преимуществ, имеется и ряд недостатков при использовании процессов ХОШ. Самый главный недостаток — это высокое сопротивление пластической деформации и пониженная пластичность большинства металлов при комнатной температуре. Данный недостаток возникает из-за деформационного упрочнения металлов.
Главной проблемой теоретического и экспериментального анализа операций ХОШ является определение технологической силы деформирования, в зависимости от вида напряжённо-деформированного состояния значения деформации, геометрии инструмента, условий на контакте заготовки с инструментом, а также изучение напряжённого состояния. Эти вопросы рассмотрены в работах Ю. А. Алюшина, А. Э. Артеса, А. Л. Воронцова, O.A. Ганаго, В. А. Головина, Г. Я. Гуна, A.M. Дмитриева, В. В. Евстифеева, В. А. Евстратова, А. З: Журавлёва, Г. И. Кириллова, С. М. Колесникова, Ф. А. Коммеля, A.A. Коставы, Д. П. Кузнецова, А. Д. Матвеева, А. Н. Митькина, Г. А. Навроцкого, Р. И. Непершина, А. Г. Овчинникова, В.А. ОгородниковаЛ.Д. Оленина, И. П. Ренне, Ю.С. Сафа-рова, Е. И. Семёнова, Г. А. Смирнова-Аляева, Л. Г. Степанского, А. Д. Томленова, Е. П. Унксова, В. Е. Фаворского, Ю. Ф. Филимонова, Ю. К. Филиппова, А.И. Хы-бемяги, В. Я. Шехтера, Л. А. Шофмана, а также Б. Авицура, У. Джонсона, Э. Томсена, Г. Д. Фельдмана, Р. Хилла, Ч. Янга и др.
Комбинированное выдавливание является перспективным процессом холодной объёмной штамповки. Комбинированное выдавливание может быть успешно применено для изготовления изделий типа втулка с фланцем с различным профилем, как внутренней, так и наружной поверхностей.
Цель работы.
Повышение качества осесимметричных деталей типа втулка с фланцем, получаемых холодным выдавливанием с учетом влияния деформации на изменение значения твёрдости.
Для решения этой задачи необходимо определить кинематику течения металла в условиях холодной деформации, а так же её зависимость от изменения геометрии рабочего инструмента, напряжённо-деформированного состояния и др. Для создания нового технологического процесса производства деталей холодной объёмной штамповкой требуется более подробное изучение поведения материалов в процессе их формообразования.
Актуальность научной задачи.
Для повышения качества изделий и технологических возможностей ХОШ необходимо развитие технологий заготовительного производства за счет изучения и освоения процессов комбинированного выдавливания, а также исследования влияния деформации на изменение механических свойств.
Научная новизна:
— получены зависимости управления процессом комбинированного выдавливания за счёт изменения геометрии рабочего инструмента;
— получена зависимость, устанавливающая влияние угла матрицы на процесс деформирования, конечную форму и размеры готовой детали, а также на силу деформирования при комбинированном процессе трёхстороннего выдавливания в сужающийся, канал- ?
— разработана методика прогнозирования дефекта металла (утяжина) и даны рекомендации по предотвращению появления данного-дефекта при комбинированном трёхстороннем выдавливании деталей типа втулка с фланцем;
— экспериментально доказано, что для ведения расчётов в качестве меры деформации максимальный сдвиг предпочтительнее, чем интенсивность деформации.
— определена экспериментально зависимость значения твёрдости стали 10 от величины деформации и схемы напряженно-деформированного состояния.
Практическая значимость:
— определены герметрические соотношения инструмента, обеспечивающие рациональные технологические режимы операции комбинированного трёхстороннего выдавливания в сужающийся канал;
— определены погрешности по геометрии и энергосиловым показателям получаемой заготовки методом комбинированного выдавливания, сравнивая данные, полученные экспериментальным методом координатной сетки, с конечно-элементным моделированием в программе С? Рогт-2В;
— определены зависимости значений твёрдости стали 10 от величины деформации и схемы напряженно-деформированного состояния, выраженного в показателе Лодэ-Надаи, благодаря чему появилась возможность прогнозировать значение твёрдости деталей, получаемых холодной объёмной штамповкой;
— получена количественная оценка размера дефекта металла (утяжина) при комбинированном трехстороннем выдавливании деталей типа втулка с фланцем;
— разработан технологический процесс комбинированного выдавливания деталей типа втулка с фланцем на примере детали «Корпус шарового пальца» из стали 10 с учетом изменения значения твёрдости. Спроектированы и изготовлены: экспериментальная оснастка, производственные штампы. Технологический процесс и производственные штампы приняты к внедрению в производство на ООО «ЛМЗ-Универсал» (Пермский край, г. Лысьва) — методика расчета технологии принята к внедрению в учебный процесс.
Личный вклад соискателя заключается в следующем:
— обоснование цели работы, разработка основных идей и методик исследований, постановка и решение задач диссертационной работы;
— исследован процесс комбинированного выдавливания, установлены зависимости влияния геометрии рабочего инструмента на процесс комбинированного выдавливания, разработана технология производства осесимметричных деталей типа втулка с фланцем;
— разработана конструкторская документация на экспериментальную и промышленную штамповую оснастку для выдавливания деталей с фланцем;
— проведено моделирование процессов выдавливания осесимметричных деталей типа втулка с фланцем методом конечных элементов в программе (^Рогт-20 при различной геометрии рабочего инструмента;
— по результатам экспериментальных исследований установлена зависимость значений твёрдости стали 10 от величины деформации и схемы напряженно-деформированного состояния.
Апробация работы. Результаты исследований доложены на научно-технической конференции «Состояние, проблемы и перспективы разработки корабельных информационно-управляющих комплексов (эффективность, надежность, экономика)», г. Москва, 2007; на научно-технической конференции «Состояние, проблемы и перспективы создания корабельных информационно-управляющих комплексов», г. Москва, 2008; на международном научном симпозиуме «Автотракторостроение — 2009», г. Москва, 2009.
В первой главе приводится обзор литературных источников, связанных с изучаемыми вопросами: формообразование тела при холодной деформацииисследование процессов прямого, обратного, радиального и комбинированного трехстороннего выдавливаниясуществующие подходы к моделированию процессов холодного выдавливанияклассификация типовых деталей с фланцем и существующих математических моделей процессов выдавливания деталей с фланцем.
Из обзора литературы, следует, что отсутствует анализ процесса комбинированного трёхстороннего выдавливания заготовки типа втулка с фланцем в сужающийся канал, не изучено влияние геометрии инструмента на конечные размеры детали и силу деформирования. А так же до сих пор не достаточно изучена зависимость величины твёрдости от величины деформации и схемы напряженного состояния для многих марок сталей.
В заключение обзора сформулированы неисследованные или требующие уточнения проблемы, на основании которых поставлены цель и задачи настоящей работы.
Во второй главе проведено моделирование комбинированного процесса трёхстороннего выдавливания методом конечных элементов в программе (2Рогт-2 В при различной геометрии рабочего инструмента для деталей типа втулка с фланцем. Изучена кинематика течения металла и предложена оптимальная геометрия рабочего инструмента, при которой идёт максимальное заполнение полости штампа металлом. Получена возможность управлять процессом комбинированного трёхстороннего выдавливания при изготовлении деталей типа втулка с фланцем за счёт изменения геометрии рабочего инструмента.
Кривая упрочнения стали 10 для проведения моделирования взята из работы [5], так как строилась совместно с автором и все последующие эксперименты, связанные с данным материалом, проводились из той же партии проката. Виртуальные размеры исходной заготовки и инструмента для моделирования соответствовали размерам образца, рассчитанного для технологического процесса и штампа для комбинированного выдавливания.
Исследован процесс зарождения такого дефекта, как утяжина металла, разработана методика прогнозирования и выработаны рекомендации по предотвращению появления данного дефекта при комбинированном трёхстороннем выдавливании деталей типа втулка с фланцем. Получена количественная оценка размеров данного дефекта металла.
В третьей главе проведены исследования формообразования заготовки типа втулка с фланцем экспериментальным методом координатных сеток и методом конечных элементов (С>Рогт-20) при комбинированном выдавливании. На основе результатов. эксперимента и моделирования получены рекомендации по выбору размеров исходной заготовки и формообразования при комбинированном выдавливании в сужающийся канал. Приводятся сравнительные данные энергосиловых, кинематических и геометрических характеристикпри формообразовании изделий втулочного типа с фланцем, полученных в системе конечно-элементного моделирования <�ЗРогт-2Б?и экспериментальным методом.
Кривая упрочнения сплава АД1 для эксперимента и моделирования взята из работы [68], так как использовался материал из той же партии проката.
В четвертой главе приводятся результаты исследований влияния величины деформации и схемы напряженного состояния на значение твёрдости стали 10.
Для производства многих деталей, согласно техническим требованиям чертежа, необходимо получить заложенную конструктором твёрдость. С учётом специфики работы многих деталей, которые выдерживают периодические ударные нагрузки (узловые соединения подвески автомобиля и т. п.), нужно уметь прогнозировать значение твёрдости получаемой детали холодной объёмной штамповкой. Анализ литературы показал, что нет данных по изменению величины твёрдости стали 10 от различной величины деформации при различных схемах нагружения.
Поэтому была поставлена задача определить зависимость твердости от величины деформации и от схемы напряженного состояния для прогнозирования свойств деталей, получаемых холодной объемной штамповкой.
В пятой главе представлен технологический процесс и спроектированные производственные штампы для изготовления детали «Корпус шарового пальца», входящей в сборочный узел шаровой опоры передней подвески легкового-автомобиля. Тем самым показана возможность использования результатов’моделирования и экспериментальных исследований формообразования^ прш решении практической задачи. Результаты эксперимента и компьютерного моделирования формообразования детали типа «Корпус шарового пальца» позволили разработать, совершенно новую технологию^ изготовления целого класса деталей, получаемых методом комбинированного выдавливания холодной объём-" нойг штамповкой. Это позволило повысить качество получаемых изделий и обеспечило надежность самого процесса. При помощи комбинированного процесса трёхстороннего выдавливания-удалось получить высокую точность детали при минимальном числе переходов и сниженных энергозатратах.
Работа выполнена на кафедре и в лаборатории «Кузовостроение и обработка давлением» МГТУ МАМИ и на предприятии ОАО «Концерн «Морин-формсистема — Агат».
ОБЩИЕ ВЫВОДЫ.
1. На основании исследования кинематики течения металла в верхней и нижней. трубчатой части корпусаа так же диаметра фланца, получена возможность прогнозирования конечной геометрии штампованной заготовки корпуса.
2.Даны рекомендации по предотвращению дефекта металла (утяжина) при комбинированном выдавливании осесимметричных деталей типа втулка с фланцем в диапазоне углов матриц от 0° до 60°. При углах матриц от 45° до 60°, а так же при их комбинации между собой, вероятность возникновенияданного дефекта сводится к нулю.
3. Сравнительный анализ энергосиловых показателей комбинированного выдавливания, полученный при помощи программы конечно-элементного-моделирования: (~)Еогт-2В-и метода координатной сетки показал расхождение в результатах от 4% до 7,4%.
4. Исследование энергосиловых показателей прикомбинированном трёхстороннем выдавливании деталей типа втулка с фланцем показало, что самым оптимальным углом с точки зрения силы деформирования, является? угол 30°, так как при да! шом значении углов матриц сила деформирования минимальна на всем протяжении процесса выдавливания.
5. Экспериментально доказано, что максимальный сдвиг в качестве меры деформации предпочтительнее, чем интенсивность деформации. Погрешность в построении, графиков зависимости твёрдости от величины деформации составляет не более 0,8%. вместо 3%. '.
6. Построенная поверхность зависимости твёрдости от величины деформации и схемы* напряженного состояниядаёт возможность прогнозировать значение твёрдости деталей, получаемых холодной объёмной штамповкой!
7. Определены значения твёрдости при различных испытаниях образцов, которые подтверждают, что при деформации от е=0,4 до 0,5 сталь 10 соответствует по твёрдости стали 35 в исходном состоянии. Это обосновывает замену марки стали для штамповки детали «Корпус шарового пальца» из более технологичной стали 10.
8. На основании результатов проведённых исследований разработан технологический процесс производства детали «Корпус шарового пальца». Спроектированы и изготовлены промышленные штампы для производства деталей в условиях серийного производства. Изготовлена опытная партия деталей «Корпус шарового пальца». Технологический процесс принят к внедрению на ООО «ЛМЗ-Универсал» (Пермский край, г. Лысьва). По предварительным подсчётам экономический эффект при внедрении данного процесса по сравнению с горячей объёмной штамповкой составит около 800 тыс. рублей на программу 600 000 штук деталей в год. Результаты работы приняты к внедрению в учебный процесс. 131:. .
Список литературы
- Зг. Сторожевом®--, Попов Е. А. Теория? обработки, металлов давлением. М.: Машиностроение- 1977. 423с.
- Тун Г. Я-, Полухин П. И., Полухин В. П., Прудковский- Б. А. Пластическоеформоизменение металлов: М1 Металлургия-, 1968- 416 с:
- Игнатеико В-А. Совершенствование технологии- комбинированного? выдавливания¦ полых деталей- с фланцем, с учётом изменения механических свойств./ Дисс. канд. техн- наук. М.: МГТУ «МАМИ» — 2009!.- 175 с.
- Чудаков П.Д., Коробкин В. Д. Обратное осесимметричное выдавливание упрочняющегося материала. // Прогрессивные технологические процессы обработки давлением. М: Машиностроение, 1971, с!, 8−14. .
- У иксов Е.П., Сафаров Ю. С. Экспериментальные исследования контактных напряжений при прессовании в плоском контейнере. В сб. Повышение прочнос ти и долговечности машин. М.: ЦНИИТМАШ, 1969- 110, С- .22−45. ¦."'.''.'
- Яшаев С.Ш. Основьв дифференцированного выдавливания. // Кузнечно-штамповочноепроизводство: 1979^№ 9- с. 4−6:
- Можейко Ю.П., Розенталь Н. К. / Расчет гидравлического устройства для выдавливания металлических деталей: // Прогрессивные технологические процессы обработки давлением. М.: Машиностроение, 1978, С. 9−14.
- Дмитриев А.М., Воронцов А.Л'., Аппроксимация кривых упрочнения: металлов: // Кузнечно-штамповочное производство. Обработка материалов давлением: № 6* 2002, с. 16−21.132 •
- Дмитриев А. М., Воронцов А. Л. Выдавливание полых изделий с раздачей заготовки в движущейся матрице // Вестн. машиностр. 2004. — № 10.-С. 55−61.
- Гуменюк Ю.И., Кузнецов Д. П. Общая и специальная терминология ОМД на примере, классификации основных видов процесса, выдавливания?// Заготовительные производства в машиностроении. — 2005. № 2. — С. 26−35.
- Алиев И.С. Технологические процессы, холодного поперечного выдавливания //Кузнечно-штамповочное производство.— 1988. № 6. — С. 1−4.
- Способ изготовления изделий со ступенчатой? боковой поверхностью: A.c. 1 030 081 СССР, МКИ В 21 J 5/12./В:Г. Шибаков (СССР). -№ 3 256 982/25−27-:Заявлено 0б103−81- Открытия, Изобретения: 1983- № 2−7.
- Способ получения изделий: A.c. 638 412 СССР, МКИ В 21 J 5/08: / Ю. А- Бочаров, A.B. Сафонов- A.F. Овчинников- (СССР): № 2 008 609/25−27- Заявлено'19.03:74- Открытия.Изобретения. 1978- № 47!
- Штамп для- изготовления? деталей: с фланцами: — A.c. 26 Г153 СССР, МКИЩШ J> 13/02,/ Е. И: Семенов- С: И!.Рожков.(СССР)^- № 1 278 167/25−27-: Заявлено 28.10.68-:Открытия. Изобретения. 1970, № 4.
- Способ формовки кольцевого утолщения? ная цилиндрической- детали: A.c. 396 159 СССР, МКИ В-21 J 5/08. / Е. И. Мошнин, Н. И- Ромашко, П. П. Костин (СССР). № 1 481 388/25- Заявлено 30.09.70- Открытия: Изобретения. 1973, № 36.
- Алиев И.С. Технологические возможности^ новых способов- комбинированного выдавливания // Кузнечно-штамповочное производство.-1990.-№ 2.-С. 7−10.
- Коган Р.Т. Штамповка с противодавлением.//Конструирование и технология машиностроения. — Сер. В'. 1965. — № 2. — С. 1−7.
- Теоретические основы ковки и горячей объемной штамповки / Е. М. Макушок, A.C. Матусевич, B.IT. Северденко, В. М. Сегал. Мн.: Наука и техника, 1968. — 408 с.
- Определение удельного усилия на пуансонах при оформлении цилиндрической шестерни методом двухстороннего деформирования/И.Л. Акаро, A.C. Григоренко и др: // Технология и машины обработки металлов давлением. Омск: ОМПИ, 1971. — С. 72−85.
- Чудаков- П. Д. Нестационарное пластическое течение упрочняющегося^материала // Исследование в области пластичности и ОМД. Тула: ТЛИ- 1974. — С. 34−41.
- Кузнецов' Д.П., Савушкин Е. Т. Напряженно-деформированное состояние заготовки1 при холодном поперечном выдавливании/ТКузнечно-штамповочное производство. 1974. — № 3. -С. 5 — 8.
- Оленин Л.Д. К выбору оптимальной' заготовки под точную объемную штамповку // Повышение точности и качества при штамповке. -М.: МДНТП, 1975. С. 72−79:
- Овчинников А-.Г., Кузнецов F. B'. Определение поля напряжений и удельных усилий при радиальном выдавливании // Известия вузов. Машиностроение. 1977. — № 12. — С. 114−119.
- Дрель О.Ф., Поляков И. С. Боковое выдавливание поковок звездочек с зубьями// Кузнечно-штамповочное производство. 1979.- № 12. — С. 6−8.
- Калпин Ю.Г., Филиппов Ю. К., Беззубов' H.H. Оценка деформационной способности металлов в процессах холодной объемной штамповки// Технология, оборудование- организация- и экономика машиностроительного производства. 1988. — Вып. 10: — С. 1−16.
- Калпин Ю.Г., Филиппов. Ю.К., Беззубов H.H. Критерий1 пластичности при холодной деформации металлов. // Деп., М: Черметинформация, Л989, per. № 4498'. 20с.
- Абдуллаев Ф.С. Разработка^ и исследование технологического процесса, 'штамповки осесимметричных поковок в закрытых штампах выдавливанием в кольцевую-полость: Автореферат дисс.канд. техн. наук. -М.:МВТУ им. Баумана, 1979. 16 с.
- Колмогоров B.JI. Механика обработки металлов давлением. М: Металлургия- 1986. — 688 с.
- Исследование изменения механических свойств стали при холодной объемной штамповке./ Бовтало Я. Н., Игнатенко В. Н. и др.
- Состояние, проблемы и перспективы создания корабельных информационно-управляющих комплексов. — сборник докладов научно-технической конференции. М.: ОАО «Концерн «Моринформсистема — Агат», 2008, С. 260 — 262.
- Зыонг За Мань. Разработка технологических процессов радиального выдавливания с контурной осадкой для стержневых деталей с широким утолщением: Дисс.канд. техн. наук. -М.: МАМИ, 1993. 253 с.
- Биба Н.В., Стебунов С. А. Применение программы QFORM 2D/3D для разработки малоотходной технологии штамповки // Пластическая деформация металлов. Днепропетровск. 16−19 сентября-2002. С. 221−226.
- Оленин Л.Д. Исследование процесса холодного комбинированного выдавливания. Дисс.канд. техн. наук. -М.:МАМИ, 1967. 167с.
- Оленин Л'.Д. Анализ комбинированного выдавливания через три канала в • режиме управления течением // Кузнечно-штамповочное производство. 1997. — № 7. — С. 5−6.
- Алиев- И. С. Исследование процесса холодного поперечного выдавливания: Автореферат дисс.канд. техн. наук. Л.: ЛПИ, 1977. — 22 с.
- Рагулин A.B. Разработка технологии комбинированного процесса прямого и обратного выдавливания в коническом инструменте: дисс. канд. техн. наук. М.: МАМИ, 2006. — 20 с.
- Джонсон В., Кудо X. Механика процессов выдавливания металла. -М.: Металлургия, 1966. 317 с.
- Технологические процессы изготовления поковок с фланцами на прессах для штамповки в разъемных матрицах/В.Т. Кондратенко, М.В.
- Блинов и др.//Кузнечно-штамповочное производство. — 1985. № 4. — С. 1114.
- Алиев И.С., Солодун Е. М., Крюгер К. Анализ деформированного состояния при комбинированном выдавливании деталей с фланцем // Металлургия и горнорудная промышленность. Днепропетровск. 2002. — № 89. — С. 495−499:
- Определение усилия прессования при истечении металла в поперечном направлении / Н. М. Золотухин, Г. Г. Ахадов, С. М. Годжаев, В. П. Святославский // Кузнечно-штамповочное производство. 1973. — № 11. — С. 810.
- Третьяков A.B., Зюзин В. И. Механические свойства металлов и сплавов при обработке давлением// 2-е изд. М., «Металлургия» 1973, — С. 202−206.
- Применение холодной объемной штамповки в заготовительном производстве/ Игнатенко В. Н.// Обработка металлов давлением. сборник научных трудов. — Краматорск. ДГМА. 2008. — 376 с.
- Соловцов С.С. Производство точных заготовок отрезкой и вырубкой // КШП ОМД. — 2005. — № 9. — С. 22−24.
- Шибаков В-Г., Гончаров? С.Н., Шибаков Р. В. Интенсивное пластическое деформирование выдавливанием // КШП-ОМД. 2004. — № 3. — С. 3133.. '
- Анализ силового режима процессов осадки и поперечного выдавливания/ Трошин В- 1 Усманов Д. В-,. Даниленко С. В.// Обработка металлов давлением. сборник научных трудов. — Краматорск. ДГМА. 2008 С. 77.
- АнурьевВ.И. Справочник конструктора-машиностроителя в 3-х т., Т.1 8-е изд., перераб. и доп. Под ред. И. Н. Жестковой. — М.: Машиностроение, 2001. — 920 е.: ил.
- Вербицкая А.Г., Кирносов В. И. Определение механических свойств материалов. Учебн. пос. 1984. 192 с.
- Степанский Л.Г. Расчеты процессов* обработки металлов давлением. М.: Машиностроение, 1979. -216с.
- Сторожев М.В., Попов Е. А. Теория обработки металлов давлением. М.: Машиностроение. 1977. 423 с.
- Гневашев Д.А. Совершенствование технологии холодного выдавливания при высоких значениях деформации: дисс. канд. техн. наук. -М.: МАМИ, 2005. 69 с.
- Губкин С.И. Диаграмма схем механических состояний.// Известия АН СССР. Отделение технических наук. 1950, № 8, с. 1165−1182.
- Теоретический анализ процесса комбинированного радиально-обратного выдавливания/Алиев И. С., Грудкина Н. С.// Обработка металлов давлением. — сборник научных трудов. Краматорск. ДГМА. 2008 С. 55.
- Теория ковки и штамповки / Е. П. Унксов, У. Джонсон, В.Л. Колмогоров' и др. / Под ред. Е. П. Унксова, А. Г. Овчинникова. М.: Машиностроение, 1999. — 598 с.
- Теория обработки металлов давлением* / И. Я. Тарновский, A.A. Поздеев, O.A. Ганаго и др. М.: Металлургия, 1963. — 672 с.
- Евстратов В.А. Теория обработки металлов давлением. Харьков: Вища шк. Изд-во при Харьк. ун-те, 1981. — 248 с.
- Шофман Л.А. Теория и расчеты процессов холодной штамповки. -М.: Машиностроение, 1964 .- 375 с.
- Физический энциклопедический словарь/ Гл.ред. A.M. Прохоров. М.: Сов. энциклопедия. 1983. 928 с.
- Формоизменение при радиально-прямом выдавливании на оправке/ Алиев И. С., Алиева Л. И., Жбанков Я. Г. // Обработка металлов давлением. -сборник научных трудов. Краматорск. ДГМА. 2008 С. 171.
- Хван Д.В. Повышение эффективности в обработке металлов давлением. — Воронеж: Изд-во Воронежского ун-та, 1995. 224 с.
- Холодная объемная штамповка. Справочник / Под ред. Г. А. Навроцкого. М.: Машиностроение. 1973. 496.
- Чиченев Н.А., Кудрин А. Б., Полухин П. И., Методы исследования процессов обработки металлов давлением: учебн. пос. М.: «Металлургия», 1977. С. 273.
- Дмитриев A.M., Воронцов А. Л. Технология ковки и объемной штамповки. Часть 1. Объемная штамповка выдавливанием: Учебник для вузов. М.: Машиностроение-1, 2005. 500 с.
- Испытания металлов. Сборник статей под ред. К.Нитцше., Перевод с немецкого Е. В. Лайнер., М.: Металлургия, 1967. 450 с.
- Дель Г. Д. Определение напряжений в пластической области по распределению твердости.- М.: Машиностроение, 1971.- 199 с.
- Бриджмен П. Исследование больших пластических девормаций и разрыва. М., Изд. иностр. лит., 1955.
- Савицкий Ф.С., Вандышев Б. А., Якутович М. В. Распределение наклёпа вокруг конического отпечатка. «Заводская лаборатория», 1948, № 12.
- Смирнов-Аляев Г. А., Розенберг В. М. Технологические задачитеории пластичности. Лениздат, 1951.
- Kudo Н., Avitzur В., Yoshiki Т. Cold forging of hollow cylindrical components having an intermediate flange Ubet analysis and experiment // CIRP Annalen. — 1980. -№ 1. — P. 129−133.
- Shall reduziert die Umformcrafte // Technica. 2000. — № 18. — P. 20−25.
- Vickers G.W., Plumtree A. Simulation of the Heading Process // Transactions of the ASME. 1975. — № 2. — P. 120−135.
- Simulation, of the heading process/G.W. Vickers, A. Plumtree, R. Sowerby, T.L. Duncan//Trans. ASME/ 1975- -H. 97. — № 2. — P. 126 — 135.
- Bungardt K., Mielders O., Spyra W. Stahl und Eisen, 1957, Bd 77, № 26, S. 1878.
- Schepers A., Licht F.R. Stahl und Eisen, 1958, Bd 78, № 4, S. 227.
- Fast J. D. Phillips. Teclin. Rundsch., 1950, № 10, S.308.
- Jontschew R. Mit einem Gegendruck-Werkzeug Kegelformige B outeile formen // Maschinenmark. 2000. — № 37. — P. 36−38.94: Weingraber. Technische Hurtemessung./ Carl Hanser Verlag- 1952.
- Holm R. Soc. for metals, 1950, S. 309.
- Bucklein R. VDI-Zeitschrift, 1960, Bd 102,№ 4, S. 128. ¦
- Kirsch A. VDI-Berichte, 1957, Bd 11, S. 59.
- Hengemuhle W. Im Handbuch der Werkstoffprufung, Bd 11, 1955, S. 386−437. ,
- Hanke E. Prufung metallischer Werkstoffe,. Berlin, VEB Verlag Technik, 1954, S. 174.
- Balendra R., Qin Y. Research dedicated to the development of advanced metal-forming technologies//L Mater. Process. TechnoE 2004. — № 2. -P. 144−152.
- BergsmanE. B., Travail le J. VDI-Berichte, 1957, Bd 11, S. 51.
- Rossow E. VDI-Berichte, 1957, Bd 11, S. 75.
- Tschirf L. VDI-Berichte, 1957, Bd 11, S. 85.
- Potyka K. VDI-Berichte, 1957, Bd 11, S. 140.105-, Bernhardt E. O: Die Mikroharteprufiing. Anwendungsbeispiele aus der: Technologie der Kraftverformung. Zeit, des VDL, Bd. 84, 1940, № 39.
- Martens A., ITeym E. Handbuch der Materialkunde fur den Maschinenbau, Bd I- Berlin, Springer-Verlag, 1912.
- Hertz H. Gesammelte Werke, Bd 1, Leipzig, 1895.
- Meyer E. VDI-Forschungsheft, Nr 65/66- 1909. .