Повышение эффективности токарной обработки сложнопрофильных деталей на станках с ЧПУ путем назначения функционально изменяемого режима резания
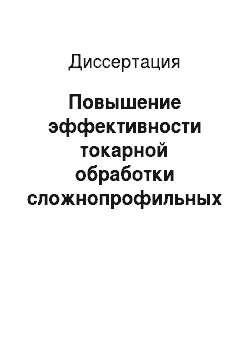
В настоящее время, как в нашей стране, так и за рубежом опубликовано большое количество работ по проблеме аналитического определения параметров качества поверхностей изготовляемой детали при осуществлении различных видов механической обработки. Среди этих работ следует особо отметить широко известные монографии Балакшина Б. С., Колева К. С., Корсакова К. В., Соколовского А. П., Маталина А. А… Читать ещё >
Содержание
- ПЕРЕЧЕНЬ УСЛОВНЫХ ОБОЗНАЧЕНИЙ
- 1. АНАЛИЗ ВОПРОСОВ, СВЯЗАННЫХ С УПРАВЛЕНИЕМ ГЕОМЕТРИЧЕСКИМИ ПАРАМЕТРАМИ И ФИЗИКО-МЕХАНИЧЕСКИМИ СВОЙСТВАМИ ПОВЕРХНОСТНОГО СЛОЯ ДЕТАЛЕЙ МАШИН
- 1. 1. Влияние параметров, характеризующих качество обработки поверхностей, на эксплуатационные свойства деталей машин
- 1. 2. Влияние режима резания, на показатели характеризующие шероховатость, размерную точность и точность профиля обработанной поверхности
- 1. 3. Состояние вопроса назначения режима обработки деталей резанием, обеспечивающих требуемые показатели качества обработанной поверхности
- 1. 4. Задачи исследования и научная новизна работы
- Выводы по главе 1
- 2. МАТЕМАТИЧЕСКОЕ МОДЕЛИРОВАНИЕ ПРОЦЕССА ТОЧЕНИЯ С УЧЕТОМ ДИНАМИЧЕСКИ ИЗМЕНЯЮЩИХСЯ ПАРАМЕТРОВ ОБРАБОТКИ
- 2. 1. Технологические факторы, влияющие на выходные характеристики токарной обработки заготовок сложной конфигурации с переменным припуском
- 2. 2. Технологические факторы, влияющие на выходные характеристики токарной обработки заготовок независимо от их конфигурации
- 2. 3. Принципы моделирования процесса точения с учетом изменяющихся условий обработки
- Выводы по главе 2
- 3. АНАЛИТИЧЕСКОЕ ОПРЕДЕЛЕНИЕ ОСНОВНЫХ ХАРАКТЕРИСТИК ПРОЦЕССА ТОКАРНОЙ ОБРАБОТКИ МАТЕРИАЛОВ
- 3. 1. Методология аналитического определения выходных характеристик процесса лезвийной обработки материалов
- 3. 2. Аналитическое определение жесткости технологической системы при осуществлении процесса точения
- 3. 2. 1. Определение статистической жесткости технологической системы при осуществлении процесса точения
- 3. 2. 2. Определение коэффициента динамичности технологической системы в анализируемых условиях токарной обработки
- 3. 3. Определение параметров сечения среза, угла схода стружки и действительных углов режущего инструмента при несвободном резании материалов
- 3. 3. 1. Определение параметров сечения среза и угла схода стружки при несвободном резании материалов
- 3. 3. 2. Определение действительных значений переднего и заднего углов режущего инструмента при несвободном резании материалов
- 3. 4. Расчет критериальных комплексов Е, Д Г", И, Да, Nu, ББс, Б0(сотс) и определение оптимальной по размерной стойкости инструмента скорости резания VQ
- 3. 4. 1. Определение критерия Нуссельта
- 3. 4. 2. Определение критерия подобия Б
- 3. 5. Аналитическое определение температурно-силовых характеристик процесса токарной обработки материалов
- 3. 5. 1. Определение составляющих силы резания Р^о), Pz (o)
- 3. 5. 2. Определение температуры резания <ЭР
- 3. 6. Аналитическое определение параметров износа и периода стойкости режущего инструмента
- 3. 6. 1. Относительный линейный износ режущего инструмента h0Jl
- 3. 6. 2. Расчет критического износа режущего инструмента h3(Kp)
- 3. 6. 3. Определение критического периода стойкости режущего инструмента
- 3. 6. 4. Определение коэффициента пропорциональности К между характеристиками износа h3 и hr
- 3. 7. Аналитическое определение размерной точности и шероховатости обработанной поверхности
- 3. 7. 1. Математическая модель суммарной погрешности токарной обработки деталей
- 3. 7. 2. Аналитическое определение параметров шероховатости поверхностного слоя, формируемого при токарной обработке
- 4. 1. Расчетная проверка сходимости и надежности разработанной методики
- 4. 2. Экспериментальная проверка разработанной методики
- 4. 3. Апробация и использование разработанной
Повышение эффективности токарной обработки сложнопрофильных деталей на станках с ЧПУ путем назначения функционально изменяемого режима резания (реферат, курсовая, диплом, контрольная)
В настоящее время до 75% предприятий отечественного машиностроения выпускают продукцию, которая по своему характеру является серийной и мелкосерийной [1−4]. Ежегодно на каждом из таких предприятий выполняются десятки и сотни заказов на новые изделия, при этом номенклатура деталей, входящих в отдельные новые изделия, достигает 150 тысяч наименований и более.
Следует также отметить, что конкурентоспособность любого предприятия, независимо от формы собственности и размеров, зависит в первую очередь от качества его продукции и соответствия ее цены с предлагаемым качеством.
В этих условиях успех производителя зависит от скорости его адекватной реакции на запрос потребителя. Производителю необходимо сократить время подготовки к выпуску намеченной продукции, одновременно обеспечив ее высокое качество и низкую себестоимость технологического процесса.
Постоянно возрастающая номенклатура выпускаемых изделий с одновременным усложнением их конструкции и технологии изготовления вызывают необходимость использования для механической обработки этих изделий станков с ЧПУ, т. к. в условиях серийного и мелкосерийного машиностроительного производства именно станки с ЧПУ позволяют быстро перейти на выпуск новой продукции или её модернизацию при одновременном повышении производительности труда и снижении себестоимости производственного процесса.
Так как в отечественном машиностроении наиболее распространенным видом механообработки является процесс точения, то, учитывая вышеизложенные обстоятельства и тенденции, можно констатировать, что проблема научно обоснованного выбора наиболее рациональных технологических условий осуществления токарной обработки деталей машин и механизмов на станках с ЧПУ, обеспечивающих повышение точности и качества поверхностного слоя этих деталей при одновременном повышении технико-экономических показателей производства, является важной и актуальной, представляющей не только научный, но и значительный практический интерес. Российскими и зарубежными учеными достигнуты значительные успехи в данной области, однако некоторые аспекты теории и практики назначения рациональных технологических условий токарной обработки деталей требует дальнейшего рассмотрения.
В частности, это относится к обработке сложнопрофильных поверхностей, являющейся частным случаем нестационарных процессов резания. Интерес к указанной проблеме со стороны инженерно-технических работников предприятий неслучаен, так как, судя по результатам теоретико-экспериментальных исследований, проведенных в последние годы, здесь заложен мощный, но недостаточно используемый резерв дальнейшего повышения рентабельности машиностроительного производства.
Исследования и практический опыт авторитетных ученых свидетельствуют об изменении параметров процесса резания непосредственно во время механической обработки [8−10]. Причинами нестабильности процесса резания являются нарастающий во времени износ резца, изменение действительных геометрических параметров инструмента, диаметра обработки, жесткости системы резания вдоль обрабатываемой поверхности и др. Таким образом, постоянные режимные условия не могут являться оптимальными на протяжении всей обработки анализируемой поверхности при нестационарных процессах резания.
В настоящее время задача повышения технико-экономической эффективности нестационарных процессов резания решается одним из перечисленных ниже способов:
— назначением переменных режимных условий обработки с использованием эмпирических методик и методик, учитывающих только один переменный параметр;
— путем использования узкоспециализированных станков {например, сферотокарных) или приспособлений {например, поворотный суппорт);
— использованием систем адаптивного управления процессом резания. К сожалению, все упомянутые способы не лишены существенных недостатков.
При использовании эмпирических методик назначением переменных режимных условий обработки отсутствует комплексный учет переменных параметров {как правило, учитывается только один). Кроме того, использование зависимостей упрощенного вида, может приводить к снижению достоверности расчета режимов резания.
Специализированные станки и приспособления обеспечивают постоянство некоторых параметров. Например, жесткости детали {люнет), угла между осью резца и касательной к обрабатываемой поверхности {сферо-токарные станки и поворотный суппорт) и т. д. Однако они не обеспечивается постоянства прочих переменных параметров, применительно к обработке сложнопрофильных поверхностей часто являются узкоспециализированными и требуют дополнительных капиталовложений.
В настоящее время создано большое количество системы адаптивного управления {САУ), существенно отличающихся друг от друга [5−16]. Динамическое изменение режимных условий обработки в САУ происходит на основе постоянного мониторинга процесса резания, что позволяет учитывать даже те факторы, которые является неизвестными на этапе технической подготовки производства (Г/777). Это является существенным плюсом по сравнению с методиками назначении режимов резания на стадии ТПП, основываясь исключительно на информации полученной до начала обработки.
В то же время, несмотря на определенные преимущества систем адаптивного управления процессом резания, существует и ряд недостатков, значительно ограничивающих возможность их широкого практического использования в сфере машиностроительного производства. Основной недостаток заключается в высокой стоимости данных систем, сопоставимой со стоимостью металлорежущего оборудования, на котором устанавливаются указанные системы. Кроме того, как указывалось выше, созданы и продолжают создаваться новые САУ существенно отличающиеся друг от друга, что свидетельствует об их узкой специализации.
Другими недостатками адаптивных систем управления являются сложность их технического обслуживания, а также длительный процесс отладки и настройки этих систем, приводящий к увеличению времени технологической подготовки производства новой и модернизируемой продукции. Установка контрольно-измерительной аппаратуры на станке приводит к снижению жесткости технологической системы и к увеличению уровня вибраций.
Еще одним недостатком САУ является отсутствие возможности использования сложного математического аппарата и современных аналитических зависимостей из-за ограничения времени отклика, что снижает достоверность расчетов.
Использование САУ является экономическим обоснованным только в случае если априорной информации об управляемом процессе токарной обработкой (то есть информации имеющейся на стадии ТПП) недостаточно для обеспечения заданных характеристик качества обработанной поверхности.
В связи с этим наиболее перспективным способом решения указанной проблемы является научно обоснованное назначение переменных режимных условий резания на стадии ТПП при комплексном учете всех переменных параметров процесса точения. Такой подход позволит совместить высокое качество обработки, достигаемого при применении САУ, с низкой себестоимостью и быстротой технологической подготовки производства. Кроме того, поскольку режимы резания, расход инструмента и результаты обработки известны на стадии ТПП, это позволяет точнее планировать осуществление производственного процесса, что также приводит к повышению экономической эффективности производства.
Указанный способ решения проблемы возможен только при наличии соответствующих аналитических методик {теоретического или теоретико-экспериментального характера), позволяющих определять выходные характеристики механической обработки материалов расчетным путем без проведения каких-либо дополнительных {как правило, дорогостоящих, длительных и трудоемких) экспериментальных исследований. Создание такого рода методики, основанной на аналитической модели процесса резания, является сложнейшей научно-прикладной задачей, ввиду значительной сложности самой технологической системы и протекающих в ней процессов.
В настоящее время, как в нашей стране, так и за рубежом опубликовано большое количество работ по проблеме аналитического определения параметров качества поверхностей изготовляемой детали при осуществлении различных видов механической обработки. Среди этих работ следует особо отметить широко известные монографии Балакшина Б. С., Колева К. С., Корсакова К. В., Соколовского А. П., Маталина А. А., Базрова Б. М., Безъязычного В. Ф., Суслова А. Г. и др. [17−30]. Благодаря достижениям в области теории и практики обработки материалов резанием, задача создания и применения на практике надежной и точной аналитической модели процесса резания становится не только возможной, но и достаточно актуальной [30−34].
Учитывая вышеизложенное сформулирована цель диссертационной работы: повышение технико-экономической эффективности токарной обработки сложнопрофильных поверхностей деталей на станках с ЧПУ при условии обеспечения заданной размерной точности, точности формы профиля продольного сечения и шероховатости обработанных поверхностей путем научно обоснованного назначения на стадии технологической подготовки производства функционально изменяемого режима резания (V, s, t).
Отличительными особенностями данной исследовательской работы являются: во-первых, управление выходными параметрами обработки без применения САУ, в том числе при обработке деталей имеющих сложный профиль обрабатываемой поверхности и переменную величину припускаво-вторых, возможность поддержания постоянных выходных характеристик процесса механической обработки, а также получение перечисленных характеристик, изменяющихся по заданному закону.
В работе [9] рассматривается назначение режимных условий обработки на стадии ТПП при помощи использования вариационного исчисления. Однако такой подход связан с рядом сложностей. В первую очередь следует отметить отсутствие возможности использования ограничений в виде неравенств, на что указывает даже автор данной работы. Во-вторых, затруднено использование кусочно-заданных аналитических зависимостей. В-третьих, отсутствует возможность использования зависимостей заданных не в виде функций (например, изменение отдельных параметров могут быть заданы в виде некоторой модели).
В связи с этим выбор режимных условий резания производится в ходе поэтапного моделирования процесса точения. С этой целью обрабатываемый участок разбивается на ряд зон {их количество выбирается исходя из требования достижения высокой точности выполняемого прогноза). Моделирование токарной обработки позволяет точнее учесть особенности нестационарных процессов резания (в том числе и износа режущего инструмента) при нестационарном процессе резания и также является отличительной особенностью данной диссертационной работы.
ВЫВОДЫ ПО РАБОТЕ.
1. На основе анализа физико-механических и теплофизических явлений, сопровождающих процесс лезвийной обработки материалов, модернизирована методология определения основных технико-технологических и технико-экономических выходных характеристик токарной обработки сложнопрофильных и конусообразных поверхностей, в том числе:
— разработаны аналитические зависимости для расчета толщины Ъ j и ширины а/ среза, а также угла схода стружки г] с учетом угла наклона обрабатываемой поверхности к оси детали у/{рис. 3.8) и износа режущего инструмента;
— разработана методика моделирования износа резца при изменении угла у/, позволяющая учитывать неравномерность износа различных участков режущих кромок при расчете параметров сечения среза и угла схода стружки;
— учтено влияние угла у/ и неравномерность износа различных участков режущих кромок на различные выходных характеристики, за счет использования при их расчете критериев подобия Е, Д, И, Да (зависящих от параметров сечения среза), и угла схода стружки.
Данная модернизация позволила повысить точность расчета выходных характеристик токарной обработки сложнопрофильных и конусообразных поверхностей за счет учета вышеописанных факторов.
2. Используя вышеуказанную модернизированную методологию определения основных выходных характеристик, разработано математическое обеспечение, позволяющее осуществить оптимизационный выбор изменяющихся по длине обработки режимных условий резания (V, s, t) с целью повышения технико-экономической эффективности процесса точения (снижения себестоимость, повышения производительности технологической операции или увеличения размерной стойкости режущего инструмента) с учетом:
— обеспечения заданных (фиксированных или изменяющихся по заданному закону вдоль обрабатываемой поверхности) значений шероховатости, размерной точности и точности формы профиля продольного сечения обработанной поверхностидиаметра обработки и угла щ вдоль обрабатываемой поверхности (при точении сложнопрофильных и конусообразных поверхностей) — нарастающего износа режущего инструментапеременной вдоль обрабатываемой поверхности жесткости системы резанияпеременной величины припуска оставленного на токарную обработкутемпературного удлинения используемого резца и расширения обрабатываемой заготовки.
3. На основе проведенных научных исследований разработана САПР ТП «VERWALTUNG», позволяющая определить наиболее эффективные (с точки зрения технико-экономических показателей обработки), функционально изменяемые режимные условия (V, sx, sy) точения деталей на станках с ЧПУ. САПР ТП также подготавливает подпрограмму обработки анализируемой поверхности для УЧПУ станка (в программу заложено 8 типов УЧПУ).
4. Применение САПР ТП «VERWALTUNG» на ОАО «Автодизель» (ЯМЗ), позволило снизить себестоимость отдельных токарных операций на 15−20% и повысить их производительность до 20−25% за счет интенсификации режимов резания.
В результате использования функционально изменяемых режимных условий в ряде случаев удалось повысить размерную точность и снизить шероховатость обработанных поверхностей, вследствие чего устранена необходимость дополнительной технологической обработки этих поверхностей, что привело к снижению себестоимости изготовления деталей в целом.
Результаты экспериментальной проверки и производственных испытаний подтвердили работоспособность САПР ТП «VERWALTUNG» и достоверность ее математического обеспечения, что позволяет рекомендовать данную САПР ТП для широкого практического использования на стадии технологической подготовки производства.
Список литературы
- Система автоматизированного проектирования. В 9-ти книгах. Кн.6. Автоматизация конструкторского и технологического проектирования: Учебное пособие для вузов/ Н. М. Капустин, Г. Н. Васильев- Под ред. И. П. Норенкова. -М.: Высшая школа, 1986. 191 с.
- Автоматизированная система проектирования технологических процессов механосборочного производства/ Под ред. Н. М. Капустина. М.: Машиностроение, 1979. — 247 с.
- Капустин Н.М. Разработка технологических процессов обработки ЭВМ. М.: Машиностроение, 1976. — 278 с.
- Горанский Г. К., Бендерова Э. И. Технологическое проектирование в комплексных автоматизированных системах подготовки производства. М.: Машиностроение, 1981. — 455 с.
- Грачев Л.Н., Гиндин Д. Е. Автоматизированные участки для точной размерной обработки деталей. М.: Машиностроение, 1981. — 240 с.
- Соломенцев Ю.М., Сосонькин В. Л. Управление гибкими производственными системами. М.: Машиностроение, 1988. — 352 с.
- Адаптивное управление технологическими процессами/ Ю. М. Соломенцев, В. Г. Митрофанов, С. П. Протопопов и др. М.: Машиностроение, 1980. — 536 с.
- Старков В.К. Обработка резанием. Управление стабильностью и качеством в автоматизированном производстве. — М.: Машиностроение, 1989. 296 с.
- Тверской М.М. Автоматическое управление режимами обработки деталей на станках. М.: Машиностроение, 1982. — 208 с.
- Подураев В.Н. Автоматически регулируемые и комбинированные процессы резания. М.: Машиностроение, 1977. — 304 с.
- Аршанский М.М., Щербаков В. П. Вибродиагностика и управление точностью обработки на металлорежущих станках. — М.: Машиностроение, 1988. 136 с.
- Невельсон М.С. Автоматическое управление точностью обработки на металлорежущих станках. — JL: Машиностроение, 1982. — 184 с.
- Невельсон М.С. Автоматическое управление точностью металлообработки. — JL: Машиностроение, 1973. 176 с.
- Солод В.И. и др. Унифицированные системы автоматического управления резанием. — М.: Машиностроение, 1975. — 162 с.
- Палк К.И. Системы управления механической обработкой на станках. Л.: Машиностроение, Ленигр. отд-ние, 1984. — 215с.
- Макаров В.Н. Исследование систем автоматического управления режимами резания и нарезания резьбы на токарных станках с ЧПУ мод. АТПр-2М12У в цеховых условиях. / Отчет о НИР. Рыбинск, 1976.-73 с.
- Балакшин B.C. Основы технологии машиностроения. — М.: Машиностроение, 1969. 72 с.
- Корсаков B.C. Точность механической обработки. М.: Машгиз, 1961.-379 с.
- Соколовский А.П. Расчеты точности обработки на металлорежущих станках. М.: Машгиз, 1952. — 288 с.
- Соколовский А.П. Научные основы технологии машиностроения. — М.: Машгиз, 1955. 515 с.
- Маталин А.А. Технология механической обработки. Л.: Машиностроение, 1977. — 462 с.
- Колев К.С. Точность обработки и режимы резания. М.: Машиностроение, 1968.- 131 с.
- Колев К.С. Технология машиностроения. — М.: Высшая школа, 1977.-256 с.
- Медведев Д.Д. Точность обработки в мелкосерийном производстве. М.: Машиностроение, 1973. — 119 с.
- Базров Б.М. Технологические основы проектирования самоподналаживающихся станков. М.: Машиностроение, 1978.
- ЕЯйтимизация технологических условий механической обработки деталей авиационных двигателей/ В. Ф. Безъязычный, Т. Д. Кожина и др.-М.: МАИ, 1993.- 184 с.
- Безъязычный В.Ф., Чистяков Ю. П. Расчетное определение технологической погрешности обработки лезвийным инструментом// Расчет режимов на основе общих закономерностей процесса резания: Сб. науч. тр. /ЯПИ, Ярославль, 1982. — Вып. 10. — С.51−63.
- Козлов В.А. Структурно-параметрическая оптимизация процесса точения: Монография. Рыбинск: РГАТА, 2000. — 671 с.
- Суслов А. Г. Совершенствование существующих и разработка новых методов обработки для повышения качества поверхностного слоя. Инженерный журнал № 10, 2001. С. 22−24.
- Киселев Э.В. Автоматизированное управление процессом токарной обработки на основе энергетического критерия резания с целью обеспечения качества поверхностного слоя и точности изготовления деталей авиационных двигателей. Диссертация. — Рыбинск, 1997.
- Технологические способы и средства повышения точности обработки нежестких деталей. / Тараненко В. А., Митрофанов В. Г., Косое М. Г. М., ВНИИТЭМР, 1987 — 64 с.
- Гороленко А.О. Инженерия криволинейных поверхностей трения. -Справочник. Инженерный журнал № Ю, 2001. С. 25−26.
- Пудов А.В. Оптимизация режимов резания при обработке на станках с ЧПУ с целью повышения точности размеров и формы деталей в процессе точения: диссертация. / Науч. Руковод. В.Ф. Безъязычный- науч. консультант В. А. Козлов. Рыбинск, 2000. — 265 с.
- Демкин Н.Б., Рыжов Э. В. Качество поверхности и контакт деталей машин. М.: Машиностроение, 1981. — 244 с.
- Маталин А.А. Качество поверхности и эксплуатационные свойства деталей машин. М.: Машгиз, 1956. — 252 с.
- Теория резания. Физические и тепловые процессы в технологических системах: Учебник для вузов / П. И. Ящерицин, M.JI. Яременко, Е. Э. Фельдштейн. Мн.: Вышэйшая школа, 1990. — 512 с.
- Ящерицын П.И., Мартынов А. Н. Чистовая обработка деталей в машиностроении. Мн., 1983.
- Форрест П. Усталость металлов. М.: Машиностроение, 1968. — 353с.
- Сулима А.Н., Евстигнеев М. И. Качество поверхностного слоя и усталостная прочность деталей из жаропрочных и титановых сплавов. М.: Машиностроение, 1974. — 255 с.
- Резников Н.И., Жарков И. Г., Зайцев В. М. и др. Производительная обработка нержавеющих и жаропрочных материалов / Под ред. Резникова Н. И. — М.: Гос. н.-техн. Изд-во машиностроительной литры, 1960.-200 с.
- Суслов А.Г. Технологическое обеспечение параметров состояния поверхностного слоя деталей. М. Машиностроение, 1987. — 208 с.
- Кравченко Б.А., Пакшев Д. Д., Колесников Б. Н. и др. Повышение выносливости и надежности деталей машин и механизмов. Куйбышев: Куйбышевское кн. изд-во, 1966 — 222 с.
- Севастьянов В.Я. Наклеп и остаточные напряжения при резании металлов. Автореферат кандидатской диссертации. М.: МАТИ,
- М&йаров А. Д. Оптимизация процессов резания. М.: Машиностроение, 1976. — 278с.: ил.
- Семенченко И.В., Нипер Я. Г. Повышение надежности лопаток газотурбинных двигателей технологическими методами. М.: Маши' ностроение, 1977. — 160 с.
- Армарего И.Дж.А., Браун Р. Х. Обработка металлов резанием.: Пер сIi англ. / Пер. Пастунов В. А. М.: Машиностроение, 1977. -325 с.
- Исаев А.И. Процесс образования поверхностного слоя при обработке металлов резанием. — М.: Машгиз, 1950. 324 с.
- Кривченко Б.А., Скиба Е. А. Теоретический расчет остаточных на-^ пряжений при механической обработке. // Остаточные напряжения (— резерв прочности в машиностроении.: Тез. докл. Всесоюз. науч.техн. конф. Ростов Н/Д: РИСХМ, 1991. — С. 144−146.
- Лившиц Б.Г., Крапошин B.C., Линецкий Я. Л. Физические свойства металлов и сплавов. М.: Металлургия, 1980. — 320 с.
- Даниелян A.M. Теплота и износ инструментов в процессе резания. -М.: Машгиз, 1954. 276 с.
- Корчак С.Н., Кошин А. А., Ракович А. Г. и др. Системы автоматизированного проектирования технологических процессов, приспособлений и режущих инструментов: Учебник для вузов/. — М.: Машиностроение, 1988. — 352 с.
- Рыжов Э.В., Аверченков В. И. Оптимизация технологических процессов механической обработки/. Киев, Наук.дум., 1989. — 192 с.
- Суслов А.Г., Дальский A.M. Научные основы технологии машиностроения. М.: Машиностроение, 2002. — 684 с.
- Аверченков В.И., Каштальян И. А., Пархутик А. П. САПР технологических процессов, приспособлений и режущих инструментов: Уч. пособие для вузов/.- Мн.: Высш.шк., 1993. 288 с.
- Горанский Г. К. Автоматизированные системы технологической подготовки производства: структура, функционирование и перспективы развития в СССР и за рубежом: Обзорная информация/. -Минск, БелНИИНТМ, 1989. Вып.1. — 56 с.
- Горанский Г. К. Методика выбора металлорежущих станков, инструментов и режимов резания в автоматизированных системах технологического проектирования: Обзорная информация/. Минск, БелНИИНТМ, 1990. — Вып.6. — 64 с.
- Аверченков В.И. Оптимизация технологических процессов в САПР ТП: Учебно-методическое пособие/ БИТМ. Брянск, 1987. — 108 с.
- Павлов В.В. Математическое обеспечение САПР в производстве летательных аппаратов. — М.: МФТИ, 1981. 64 с.
- Великанов К.М., Новожилов В. И. Экономические режимы резания металлов. Д.: Машиностроение, 1972. — 119 с.
- Горанский Г. К., Владимиров Е. В., Ламбин Л. Н. Автоматизация технического нормирования на металлорежущих станках с помощью ЭВМ. М.: Машиностроение, 1970. — 222 с.
- Игумнов Б.Н. Расчет оптимальных режимов обработки для станков и автоматических линий. М.: Машиностроение, 1974. — 200 с.
- Автоматизированное проектирование оптимальных наладок металлорежущих станков/ A.M. Гильман, Г. В. Гостев, Ю. Б. Егоров и др. -М.: Машиностроение, 1984. 168 с.
- Оптимизация режимов резания на металлорежущих станках/ A.M. Гильман, JI.A. Брахман, Д. И. Батищев и др. М.: Машиностроение, 1972.- 188 с.
- Соломенцев Ю.М., Басин A.M. Оптимизация технологических процессов механической обработки и сборки в условиях серийного производства: Обзор/. М.: НИИМАШ, 1977. — 73 с.
- Аветисян Д.А., Башмаков И. А., Геминтерн В. И. Системы автоматизированного проектирования: Типовые элементы, методы и процессы. — М.: Издательство стандартов, 1985. 180 с.
- Аллик Р.А., Бородянский В. И., Бурин А. Г. и др. САПР изделий и технологических процессов в машиностроении. Л.: Машиностроение, 1986. — 319 с.
- Локтев В.Г. Автоматизированный расчет режимов резания и норм времени. М.: Машиностроение, 1990. — 80с.
- Шпур Г., Ф.-Л. Краузе. Автоматизированное проектирование в машиностроении. / Пер. с нем. Г. Д. Волковой и др.- под ред. Ю.М. Со-ломенцева, В. П. Диденко. М.: Машиностроение, 1988. — 648с.
- Якобе Г. Ю., Якоб Э., Кохан Д. Оптимизация резания. Параметризация способов обработки резанием с использованием технологической оптимизации: Пер. с нем./. -М.: Машиностроение, 1981. 279с.
- Оптимизация технологических процессов механической обработки. / Рыжов Э. В., Аверченков В.И.- Отв. ред. Гавриш А.П.- АН УССР. Инт сверхтвердых материалов. — Киев: Нукова думка, 1989. — 192 с.
- Розенберг Ю.А., Пономарев В. П. Резание металлов и технологическая точность деталей в машиностроении. Курган: КМИ, 1968. -4.1.-293 с.
- Колев К.С., Горчаков Л. Ь. Точность обработки и режимы резания. -М.: Машиностроение, 1976. — 144 с.
- Колев К.С. Вопросы точности при резании металлов. Машгиз, 1961.- 134 с.
- Маталин А.А. Точность обработки и проектирование технологических процессов. М.: Машиностроение, 1970. — 320 с.
- Левант Х.В. Чистота обработанной поверхности при точении в зависимости от режимов резания, геометрии и износа инструмента. — М.: Машиностроение, 1948. 229 с.
- Исаев А.И. Влияние износа резца на процесс образования поверхностного слоя // Чистовая обработка конструкционных материалов: Сб.науч.тр./ЦНИИТМАШ. -М.: Машгиз, 1952.-Кн. 15.-С. 15−19.
- Шустер Л.Ш. Исследование шероховатости обработанной поверхности в связи с износом резца // Станки и инструмент. — 1966. № 2.-С. 34−35.
- Алейниченко Г. Ф. О соотношении радиуса округления режущей кромки инструмента и толщины срезаемого слоя // Резание и инструмент: Респ. сб. научн. тр. Харьков: Техника, 1976-Вып. 16. — С. 94−102.
- Медведев Д. Д. Автоматизированное управление процессом обработки резанием. М.: Машиностроение, 1980. — 143 с.
- Макаров А.Д. Износ и стойкость инструментов. М.: Машиностроение, 1966. — 264 с.
- Макаров А.Д., Мухин B.C., Шустер Л. Ш. Износ инструмента, качество и долговечность деталей из авиационных материалов. Уфа: УАИ, 1974.-372 с.
- Грановский Г. И., Грановский В. Г. Резание металлов. М.: Высшая школа, 1985.-304 с.
- Реклейтис Г., Рейвидран А., Рэксдел К. Оптимизация в технике: в 2-х кн. Кн. 1 пер. с англ. — М.: Мир, 1986. 350 с.
- Химмельблау Д.М. Прикладное нелинейное программирование -М.: Мир, 1975.
- Paviani D., Himmelblau D.M., Operation Res., 17 (1969)
- Nelder J.A., Mead R., Computer J., 7, 308 (1964)
- Козлов В.А. Унификация математического обеспечения систем автоматизированного проектирования токарной обработки: Вестник Верхневолжского отделения АН РФ/ РГАТА. Рыбинск. — Вып. 4. -2001.-С. 82−88.
- Козлов В.А. Температурно-силовые характеристики процесса резания и их теоретико-экспериментальное определение: Учебное пособие / РГАТА. Рыбинск, 1997. — 4.1, 2. — 449 с.
- Козлов В.А. Прогнозирование точности обработки и характеристик качества поверхностного слоя при точении материалов/ РГАТА. -Рыбинск, 1998.- 110 с. Деп. в ВИНИТИ 16.10.98, N 3018-В98.23.
- Козлов В.А. Аналитическое определение критического износа режущих инструментов/РГАТА. Рыбинск, 1998. — 40 с. Деп. в ВИНИТИ 12.5.98, N 1434-В98.
- Козлов В.А. Аналитическое определение параметров сечения среза и угла схода стружки при лезвийной обработке материалов: Учебное пособие/ РГАТА. Рыбинск, 1990. — 209 с.
- Козлов В.А., Смирнова Г. В. Влияние вибраций в технологической системе СПИД на высотные характеристики поверхностного слоя, формируемого при токарной обработке материалов/ РАТИ. Рыбинск, 1990. — 86 с. — Деп. в ВНИИТЭМР N 203 — мш 90.
- Корсаков B.C. Исследование деформаций деталей машин в процессе их обработки / МВТУ. Москва, 1950. — 160 с.
- Зорев Н.Н., Грановский Г. И., Ларин М. Н. и др. Развитие науки о резании металлов — М.: Машиностроение, 1967. — 416 с.
- Силин С.С. Расчет оптимальных режимов на основе изучения процессов резания методами теории подобия//Технология машиностроения: Сб. научн. тр./ ЯПИ. Ярославль, 1968. — Вып. 1. — С. 43−64.
- Силин С.С. Метод подобия при резании материалов. М.: Машиностроение, 1979. — 152 с.
- Силин С.С. Установление критериальных зависимостей при резании металлов на основе изучения тепловых явлений//Тепловые явления и обрабатываемость резанием авиационных материалов: Сб. науч. тр./ МАТИ. М.: Машиностроение, 1966. — Вып. 64. — С. 102−138.
- Клушин М.И. Алгоритмы расчета сил и скоростей резания// Сборник научн. тр./ ПТНИ ВВСНХ. Горький, 1963. — Вьга.2. — С. 117−132.
- Накаяма К. Исследование методов управления процессами стружкообразования при обработке резанием // Кикай гидзюцу. -1972. № 4, т.21. — С. 69−74.
- Губкин С.И. Теория обработки металлов давлением. — М.: Машгиз, 1951.-415 с.
- Головин А.Ф. Прокатка металлов. М.: Металлургиздат, 1933. -4.1.-307 с.
- Еремин А.Н. Физическая сущность явлений при резании сталей. — М.: Машгиз, 1951. 326 с.
- Трусов В.В., Козлов В. А. Взаимосвязь между значениями износа режущего инструмента по задней поверхности и в радиальном направлении/ РАТИ.- Рыбинск, 1986.- 32 е.- Деп. в ВНИИТЭМР (№ 5мш -86).
- Филоненко С.Н. Резание металлов.- Киев, Техника, 1975 — 237 с.
- Доброрез А.П. Выбор радиуса при вершине резца при тонком точении // Станки и инструмент. 1962. — № 12. — С. 27−31.
- Грановский Г. И., Грудов П. П., Кривоухов В. А. Резание металлов. -М.: Машгиз, 1954. 368 с.
- Ящерицин П.И., Еременко M.J1. Фельдштейн Е. Э. Теория резания. Физические и тепловые процессы в технологических системах: Учебник для вузов. Мн.: Высш.шк., 1990. — 512 с.
- Козлов В.В., Мартюшина Н. Ф. Применение метода факторного планирования экспериментов для решения теоретических задач механической обработки материалов/ РАТИ. Рыбинск, 1985. — 21 с. — Деп. в ВНИИТЭМР 12.10.85, N 20 — мш 85.
- Смазочно-охлаждающие технологические средства для обработки металлов резанием: Справочник/ Под общей ред. С. Г. Энтелиса, Э. М. Берлинера. 2-е изд., перераб. и доп./.- М.: Машиностроение, 1995.-495 с.
- Чулок А.И., Лобанцева B.C. Термический анализ эффективности действия СОЖ. М.: ВНИИТЭМР, 1988. — 40 с.
- Малиновский Г. Т. Масляные СОЖ для обработки материалов резанием.- М.: Химия, 1988. 192 с.
- Гжиров Р.И., Серебреницкий П. П. Программирование обработки на станках с ЧПУ: Справочник. — Д.: Машиностроение, 1990. — 588 с.
- Силин С.С., Козлов В. А. Аналитическое определение температурного удлинения режущих инструментов. Депонированная рукопись. ВНИИТЭМР № 360мш-88. 86 с.
- Михайлов-Михеев П. Б. Справочник по металлическим материалам турбино- и моторостроения. М.: Машгиз, 1961. — 838 с.
- Справочник по машиностроительным материалам / Под ред. Г. И. По година-Алексеева, т.1 М.: Машгиз, 1959. — 908 с.
- Прогрессивные режущие инструменты и режимы резания металлов: Справочник. В. И. Баранчиков, А. В. Жаринов, Н. Д. Юдина и др.- Под общей редакцией В. И. Баранникова. М.: Машиностроение. 1990.-400 с.
- Козлов В.А. Аналитическое определение температурного удлинения режущих инструментов/ РАТИ. Рыбинск, 1988. — 48 с. — Деп. в ВНИИТЭМР, N. 360мш-88.
- Силин С.С., Козлов В. А. Аналитическое определение теплофизических и физико-механических характеристик процесса лезвийной обработки материалов// Вестник машиностроения. 1993. -№ 5−6. — С. 32−33.