Разработка микродугового оксидирования рабочих поверхностей форм из высокопрочных алюминиевых сплавов
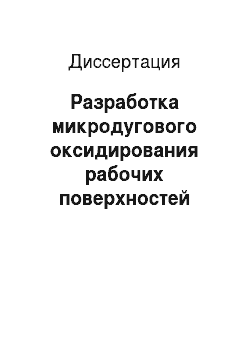
Одним из главных вопросов технологии машиностроения является учение о детали и технологических процессах ее изготовления с заданными размерами и взаимным положением поверхностей, а также требуемыми свойствами поверхностного слоя. Поэтому в настоящее время, опираясь на разработки новых технологических процессов, на первый план при проектировании и изготовлении деталей ДЛА и элементов… Читать ещё >
Содержание
- 1. ОБОСНОВАНИЕ И ТЕХНОЛОГИЧЕСКИЕ ВОЗМОЖНОСТИ МЕТОДОВ ЗАЩИТЫ РАБОЧИХ ПОВЕРХНОСТЕЙ ФОРМ ИЗ АЛЮМИНИЕВЫХ СПЛАВОВ В ПРОИЗВОДСТВЕ ДЛА И ЛА
- 1. 1. Анализ и оценка перспектив использования алюминиевых сплавов для изготовления форм
- 1. 2. Обоснование и выбор метода МДО для повышения стойкости и ресурса рабочих поверхностей форм
- 2. АНАЛИЗ И МОДЕЛИРОВАНИЕ ПРОЦЕССОВ В ЛИТЕЙНОЙ ФОРМЕ
- 2. 1. Анализ динамики изменения давления и температуры пластмассы в полости формы
- 2. 2. Напряжения и деформации основных элементов форм в литейном цикле
- 2. 3. Конечно-элементный анализ модельного образца
- 2. 4. Анализ причин разрушения литейных форм
- 3. ИССЛЕДОВАНИЕ ВОЗМОЖНОСТЕЙ МЕТОДА МДО ДЛЯ УПРОЧНЕНИЯ ПОВЕРХНОСТЕЙ ВЫСОКОПРОЧНЫХ АЛЮМИНИЕВЫХ СПЛАВОВ И ОПРЕДЕЛЕНИЕ ОПТИМАЛЬНОГО РЕЖИМА
- 3. 1. Состав экспериментальной установки и средства измерения
- 3. 2. Обрабатываемость методом МДО высокопрочных авиационных алюминиевых сплавов и обоснованный выбор сплава
- 3. 2. 1. Анализ химического состава и механических характеристик алюминиевых сплавов А1разе М-1, (±-С-7 и А1цтес
- 3. 2. 2. Влияние химического состава алюминиевых сплавов на их
- 3. 2. 3. Исследование возможности микродугового оксидирования сплавов А1разе М-1, (±-С-7 и А1ишес
- 3. 2. 4. Обоснование выбора алюминиевого сплава А1ишес
- 3. 3. Определение оптимального режима процесса МДО для сплава А
- 4. 1. Методики определения физико-химических свойств покрытий
- 4. 2. Результаты исследования и анализа физических и химических свойств покрытий
- 4. 3. Оборудование, методики и результаты исследования эксплуатационных свойств покрытий
- 4. 3. 1. Исследование образцов с МДО покрытиями на циклическое сжатие
- 4. 3. 2. Методика исследований и результаты испытаний МДО покрытий в условиях усталостного нагружения
- 4. 3. 3. Износостойкость покрытий, полученных методом МДО
- 4. 3. 4. Разработка оборудования и результаты термоциклических испытаний
- 4. 3. 5. Методика и контроль защитных свойств покрытий
- 5. 1. Разработка и изготовление опытно-промышленной установки МДО
- 5. 2. Разработка технологического процесса МДО алюминиевой вставки инжекционной формы и результаты ее испытаний
Разработка микродугового оксидирования рабочих поверхностей форм из высокопрочных алюминиевых сплавов (реферат, курсовая, диплом, контрольная)
Дальнейшее повышение эффективности работы деталей агрегатов двигателей летательных аппаратов (ДЛА) и летательных аппаратов (ЛА), а также технологической оснастки, используемой при их изготовлении, связано, как правило, с повышением температуры и усилением агрессивности рабочей среды, рабочего процесса. Кроме того, необходимо обеспечить требуемую износостойкость и эрозионную стойкость деталей ДЛА и технологической" оснастки, подвергающихся механическому, абразивному и эрозионному износу в процессе эксплуатации.
Одной из наиболее распространенных причин выхода деталей и сборочных единиц ДЛА и ЛА из строя является не поломка, а износ и повреждение рабочих поверхностей. Применяя покрытия с заданными свойствами можно решить вопросы повышения износостойкости, коррозионной и эрозионной стойкости элементов конструкций ДЛА ЛА и технологической оснастки для их производства.
Одним из главных вопросов технологии машиностроения является учение о детали и технологических процессах ее изготовления с заданными размерами и взаимным положением поверхностей, а также требуемыми свойствами поверхностного слоя. Поэтому в настоящее время, опираясь на разработки новых технологических процессов, на первый план при проектировании и изготовлении деталей ДЛА и элементов технологической оснастки выдвигаются вопросы формирования и исследования поверхностного слоя с использованием новых способов их формирования. В большинстве случаев, именно поверхностный слой деталей ДЛА и элементов технологической оснастки определяет эффективность протекания рабочих процессов в двигателях и энергоустановках и технологических процессов в технологических реакторах и камерах, в литьевых формах, в прессформах и др. Все больше деталей проектируется с переменными свойствами по сечению, когда требуемыми оптимальными свойствами для протекания рабочего или технологического процесса обладает только поверхностный слой.
В технологии производства ДЛА, ЛА и технологической оснастки все технологические процессы обеспечения заданных физико-химических и эксплуатационных свойств поверхностных слоев деталей можно разделить на две большие группы:
— формирование заданных свойств непосредственно в поверхностном слое (закалка, диффузное насыщение поверхностного слоя, ионная имплантация и пр.);
— нанесение покрытий, защитных пленок с заданными свойствами.
Перспективным методом нанесения керамико-подобных покрытий с заданными свойствами на авиационные металлы «вентильной» группы (А1, 14, ЫЬ и др.) является метод микродугового оксидирования (МДО), позволяющий одновременно в одном технологическом процессе получить заданные свойства, как в поверхностном слое детали (образца), так и в сформированном покрытии.
В производстве ДЛА, ЛА и технологической оснастки их производства покрытия находят самое широкое применение. Традиционно используемыми методами нанесения коррозионно-и износостойких покрытий являются гальванический и химический методы. Так для деталей из высокопрочных сталей широко применяется гальваническое кадмирование и цинкование.
Для повышения коррозионно-и износостойкости алюминиевых сплавов (корпуса, фланцы, клапаны, крыльчатки, пуансоны и матрицы форм для литья и прессования) традиционно используется химическое оксидирование и электрохимическое оксидирование (анодирование). Однако в процессе развития и исследования анодирования было обнаружено, что окисная пленка на аноде может образовываться при довольно широком варьировании напряжений на ванне, в том числе и напряжений, превышающих напряжения искрового режима, переходящего в дуговой или микродуговой. Так возник перспективный способ, получивший название микродугового оксидирования (МДО).
Этот метод позволяет получить на поверхности, в частности, деталей из алюминиевых сплавов композиционный упрочненный слой, характеризующийся повышенными механическими и износостойкими характеристиками. Если ресурс рабочих поверхностей деталей агрегатов ДЛА и технологической оснастки можно увеличить за счет использования покрытий МДО, то использование алюминиевых сплавов позволит значительно снизить трудоемкость изготовления этих деталей и уменьшить их стоимость. Хорошие результаты от применения МДО можно ожидать при изготовлении форм для литья термопластов и прессования реактопластов, для прессования резинотехнических изделий, для изготовления литьевых моделей в производстве ДЛА.
Пока же, несмотря на перспективность, широкого практического применения в технологии изготовления форм процесс МДО не нашел. Это объясняется несколькими основными причинами.
Во-первых, недостаточно изучены и систематизированы процессы, протекающие при микродуговом оксидировании высокопрочных, деформируемых алюминиевых сплавов, являющихся перспективными для изготовления технологических форм.
Во-вторых, не разработаны оптимальные технологии МДО обработки деталей форм, изготавливаемых из новых деформируемых алюминиевых сплавов, и не проведены исследования свойств МДО покрытий для этих сплавов, которые могли бы доказать эффективность новых технологических процессов МДО обработки.
В-третьих, не создано специализированное автоматизированное и надежное оборудование для реализации МДО процесса. Причем решение последней проблемы тесно связано с решением первых двух.
В связи с этим актуальность темы настоящей работы определяется разработкой методик комплексного, всестороннего исследования покрытий, формируемых МДО на новых высокопрочных алюминиевых сплавах для рабочих поверхностей форм. Другими важными аспектами актуальности является необходимость разработки технологий обработки МДО новых высокопрочных алюминиевых сплавов и создание промышленно-экспериментальной автоматизированной установки МДО.
Цель настоящего исследования: разработка и исследование метода МДО получения покрытий на новых высокопрочных деформируемых сплавах, которые используются при изготовлении формдля повышения износостойкости наиболее напряженных элементов форм.
В соответствии с этим для реализации поставленной цели в работе решаются следующие задачи:
1.) анализ и оценка перспектив использования форм из алюминиевых сплавов и, в частности, для литья пластмасс под давлением;
2.) анализ возможностей метода МДО для повышения стойкости и ресурса рабочих поверхностей литьевых форм;
3.) обоснование и выбор конкретной марки нового высокопрочного деформируемого алюминиевого сплава и оптимальных режимов его упрочнения методом МДО;
4.) исследование геометрических и физико-химических параметров и свойств оптимальных покрытий, полученных МДО на выбранном алюминиевом сплаве;
5.) исследование эксплуатационных характеристик покрытий, полученных МДО: термостойкость, циклическое сжатие, изгиб, износостойкость;
6.) разработка и изготовление автоматизированной опытно-промышленной установки МДО;
7.) разработка и реализация опытного технологического процесса МДО применительно к высокопрочным алюминиевым сплавам форм, используемых в переработке пластмасс и резин.
УСЛОВНЫЕ ОБОЗНАЧЕНИЯ И СОКРАЩЕНИЯ.
1К — катодный импульс тока, А.
1а — анодный импульс тока, А.
НУ200, Ни — микротвердость, кг/ мм2.
I — интенсивность изнашивания, мм/м.
Р — давление в полости формы, МПа (кг/см2).
Т — температура, °С.
Ь — времена процессов, мин (час).
V — объем усадки пластмассы, см3/г.
С, — жесткость узлов запирания формы, кг/см.
СууЪ Си — жесткость половин формы, кг/см.
Ь — длина деформируемых элементов, см.
Ек — усилие запирания, кг.
Рр — усилие от давления внутри формы, кг.
А1 — деформация линейных элементов формы, см.
Ар — проецируемая площадь детали, см2 у.
8К — контактная поверхность формы, см.
Гь Тг, f — суммарная деформация элементов формы, см.
N — количество циклов испытаний (работы), шт иа — анодное напряжение, В ик — катодное напряжение, В.
Ье, Ь — толщина покрытия, мкм.
Е — модуль упругости, кг/см.
Ств — предел прочности, кг/см2.
СТод — предел текучести, кг/см.
8 — относительное удлинение, %.
Ат — прирост массы образца, г.
Сяагяюз, Скон — концентрация составляющих раствора, г/л.
— плотность тока, А/дм2 иВг — напряжение пробоя, В.
Чьаве" 42 — количество электричества через покрытие, К.
ОСНОВНЫЕ ВЫВОДЫ.
На основании проведенного исследования можно сделать следующие выводы:
1. На основании анализа перспектив использования форм из алюминиевых сплавов для переработки пластмасс и резин в производстве ДЛА и технологической оснастки показана техническая и экономическая целесообразность применения для защиты рабочих поверхностей форм из высокопрочных алюминиевых сплавов технологического процесса микродугового оксидирования.
2. С привлечением методов Mold Flow Analisis и Final Element Analisis проведено исследование теплового, силового и напряженно-деформированного состояния рабочих поверхностей форм для литья пластмасс под давлением, изучены причины их разрушения, что позволило выделить наиболее ответственные поверхности, подвергаемые МДО, и сформулировать технические требования к МДО покрытиям.
3. Исследования физико-механических характеристик новых высокопрочных, деформируемых алюминиевых сплавов М-1, QC-7 и А1−89, их МДО обрабатываемости и анализ полученных МДО покрытий показали преимущество сплава Alumec-89 для изготовления форм.
4. С использованием факторного эксперимента и планирования на симплексе получены зависимости выбранных параметров оптимизации от режимов процесса МДО (плотности тока, времени оксидирования, температуры электролита и состава электролита). Получены регрессионные математические модели для скорости роста, количества электричества, микротвердости и пробивного напряжения МДО покрытия на сплаве А1−89, с учетом анализа реализованного симплекс-центроидного плана эксперимента определен оптимальный состав электролита. Определены оптимальные значения режимов получения МДО покрытия на сплаве А1−89.
5. Разработанные методики определения механических и физико-химических свойств оксидных покрытий позволили получить на выбранном сплаве А1−89 следующие наилучшие характеристики МДО покрытий:
— толщина суммарная (базового слоя) — до 200 мкм;
— твердость — до 75 HRT микротвердость — HVo, i = 1370 кг/см2.
— адгезия — до 630 кг/см2.
— пробойное напряжение — до 1000 В.
6. Созданное оборудование и методики исследования эксплуатационных свойств МДО покрытий позволили определить, что: при циклическом сжатии с частотой ~10 Гц и давлением до 1500 кг/см2 и выше используемый образец с покрытием выдержал 105 циклов без каких-либо следов деформации и разрушения;
— хотя при циклическом нагружении на изгиб с амплитудой равной 150 МПа период общей долговечности у образцов с покрытием в два раза меньше, чем у исходных образцов, однако отслаивания МДО покрытия от основного материала в процессе усталостного нагружения не наблюдается;
— МДО покрытие выдержало в течение 105 циклов изменение температуры образца от 215 °C до 80 °C;
— износостойкость образцов с МДО покрытием в 6 раз выше, чем у основного алюминиевого сплава и в 2 раза выше, чем у инструментальной стали Р20, традиционно используемой в американской промышленностикоррозионная стойкость (химическая коррозия в кислоте НС1) составила 102 минуты.
7. На основании проведенных исследований разработан типовой технологический процесс получения МДО покрытий и внедрены на предприятиях США Visteon Automotive Ford Motor Company, США и Venture Industries Corporation, США:
— опытно-промышленная установка МДО мощностью 10 кВт, обеспечивающая микродуговое оксидирование образцов и деталей площадью до 4 дм в ручном, диалоговом и автоматическом режимах при управлении от PC;
— МДО покрытие на вставке промышленной инжекционной формы для литья пластмасс под давлением и проведены их испытания в реальном литейном цикле на термопластавтомате «Toshiba» с общим числом циклов 105.
Список литературы
- Plastics: Components, Processes and Technology, SAE, SP-1410, 1999. 131 p.
- Раковский B.C., Райтбарг JI.X., Роттенберг Н. Д., Геллис М. Я. Авиационные материалы и их обработка., М., Машиностроение, 1979. 34 с.
- Шпак Т.С. Неметаллические материалы в авиастроении. Пластмассы, Куйбышев, КуАИ, 1969. 98 с.
- Лепетов В. А. Резиновые технические изделия, Л., Химия, 1976. 440 с.
- Резниченко В.И., Хомич В. И. Применение композиционных материалов, М., ЦРДЗ, НВЦ Источник, 1992. 238 с.
- Буланов И.М., Воробей В. В. Технология ракетных и аэрокосмических конструкций из композиционных материалов, М., МГТУ им. Н. Э. Баумана, 1998. 516 с.
- Plastics: Components Processes and Technology, SAE, SP-1340, 1998. 232 p.
- New Plastics Application for the Automotive Industry, SAE, SP-1253, 1997. 178 p.
- Injection Molding of Plastic Components. A Guide to Efficiency, Fault Diagnosis and Cure Book Company Limited, UK, 1968. 167 p.
- Menges. Mohren. How to Make Injection Molds. Hauser Publishers, Munich Vienna New York, USA, 1986. 385 p.
- Технологическая оснастка для переработки термопластов. Отраслевой каталог, М. ЦНИИТЭстроймаш, 1983. 384 с.
- Drink Н. Increasing Rationalization Reserves by Methodical Analysis of Weaknesses. .Text of Lecture 7th Plastics Engineering Colloquium 20th and 21st March, 1974. 47 p.
- Стамубргский E.A., Бейль А. И., Карливан В. П., Беспалов Ю. А. Износ оборудования при переработке пластмасс М., Химия, 1985. 208 с.
- Handbook of Plastic Materials and Technology. Edited by Irvin I. Rubin, Robinson Plastic Corporation, A Wiley-Interscience Publication John Wiley&Sons, Inc., New York, 1990. P. 1393−1399.
- Marten H. Cast Non-ferrous Metal Molds. Applied Non-Ferrous Metal-Applied Casting (G), VDI Bildungswerk BW 2197, 1979. p. 75.
- Automotive Components Division Tooling: Calendar Jear Spending. Report № 71−96 Ford Motor Company, USA, 1996. 15 p.
- Технология самолетостроения. Под ред. проф. А. Л. Абибова, М., Машиностроение, 1970. 600 с.
- Шрейдер А.В. Оксидирование алюминия и его сплавов. М., Метллургиздат, 1960. 220 с.
- Aluminum. Properties and Physical Metallurgy. Edited by John E.Hatch. American Society for Metals, 1984. 422 p.
- Грилихес С.Я. Оксидные и фосфатные покрытия металлов J1., Машиностроение, 1978. 104 с.
- Беленький М.А., Иванов А. Ф. Электроосаждение металлических покрытий. Справочник, Металлургия, М., 1985. 288 с.
- The Anodizing of Aluminum. Report from the Material Business File Database N D613GB. Innovator’s Direct, FL, USA, 1996. 250 p.
- Аверьянов E.E. Справочник по анодированию, M., Машиностроение, 1988. 224 с.
- Черненко В.И., Снежко JI.A., Папанова И.И, Литовченко К. И. Теория и технология анодных процессов при высоких напряжениях, Киев, Наукова Думка, 1995. 198 с.
- Ямпольсский A.M., Ильин В. А. Краткий справочник гальванотехника, Л., Машиностроение, 1981. 272 с.
- Henley V.F. Anodic Oxidation of Aliminium and its Alloys. Peregamon Press Ltd., USA, 1992. 152 p.
- Colombini C. The use of Pulse Rectifiers in Anodising and Plating Metal Finishing, № 5, 1992. p. 31−36.
- Томашов Н.Д., Тюкина M.H., Заливалов Ф. П. Толстослойное анодирование алюминия и его сплавов, М., Машиностроение, 1968. 156 с.
- O’Hanlon J.F. Plasma Anodization of Metals and Semiconductors. J. Vac. Sci. And Technol., v. 7, № 2, 1970. p. 330−338.
- Аверьянов E.E. Плазменное анодирование в радиоэлектронике, М., Радио и связь, 1983. 80 с.
- Alwitt R.S., Vijh A.V. Sparking voltages observed on anodization of some valve metals// J. Electorchem Soc, v 116, № 5, 1969. p. 388−390.
- Vijh A.K. Sparkling voltages and side reactions during anodization of valve metals in terms of electron tunneling. Corrosion Sci. v. 11, № 6, 1971. p. 411−417.
- Малиненко В.П. ОдынецЛ.Л., Чекмасова C.C., Ханина Е. Я. Электропроводность систем металл-окисел-электролит. Электрохимия т. 7, № 12, 1971. с. 1946−1848.
- Баковец В.В., Поляков О. В., Долговесова И. П. Плазменно-электролитическая анодная обработка металлов. Новосибирск, Наука, Сибирское Отделение РАН, 1991. 168 с.
- Марков Г. А., Маркова Г. В. Авторское свидетельство № 526 960. Бюллетень изобретений и открытий, 32, 1976. с. 163.
- Николаев А.В., Марков Г. В., Пещевицкий Б. Н. Новое явление в электролизе. Известия СО АН СССР, Серия химических наук, вып. 5, № 12, 1977. с. 32−33.
- Федоров В.А., Великосельская Н. Д. Физико-механические характеристики упрочненного поверхностного слоя на сплавах алюминия, полученного при микродуговом оксидировании. Физика и химия обработки материалов. № 4, 1990. с. 57−62.
- Федоров В.А., Великосельская Н. Д. Влияние микродугового оксидирования на износостойкость алюминиевых сплавов. Трение и износ, том 10, № 3, 1989 г. с.521−524.
- Кан А.Г., Максутов Р. А., Федоров В. А. Поверхностное упрочнение деталей из легких сплавов на основе процесса микродугового оксидирования. Известия вузов. Нефть и газ т. 31, № 2, 1989. с. 28−40.
- Timoshenko A.V., Opara В.К., Kovalev A.F. Microarc oxidation of D16T alloy with alternating current in ab alkali electrolyte. Zashita Metallov, v. 27, № 3, May-Jun 1991. p. 417−424.
- Wirtz G. P, Brown S.D., KrivenW.M., Ceramic Coatings by Anodic Spark Deposition. Materials & Manufacturing Processes. 6(1), 1991. p. 87−115.
- Марков Г. А., Терлеева О. П., Шуленко E.JI. Электрохимическое окисление алюминия при катодной поляризации. Изв. СО АН СССР Серю Химические науки, Т 7, 1983. с. 31−34.
- Марков Г. А., Шулейко Е. К., Жуков М. Ф., Пещевицкий Б.П, Способ анодирования металлов и их сплавов. Бюллетень изобретений, № 7, 1982. с. 4.
- Федоров В.А., Белозеров В. В., Великосельская Н.Д, Булычев С. П. Состав и структура упрочненного поверхностного слоя на сплавах алюминия, получаемого при микродуговом оксидировании. Физика и химия обработки материалов, № 4, 1988. с. 92−97.
- Elbe W., Stitz S" Wubken G. Injection Molding of Plastomers II (G), Practice at IKV, 1978.
- Калинчев Э.Л., Калинчева Е. И., Саковцева М. Б. Оборудование для литья пластмасс под давлением. Расчет и конструирование, М., Машиностроение, 1985.
- Gilmore G.D., Spenser R.S. Photographic Study of the Polymer Cycle in Injection Molding Plastics, April 1951. p. 117.
- Видгоф Н.Б. Основы конструирования литьевых форм для термопластов М. Машиностроение, 1979. 264 с.
- Application of Mold Filling and Cooling Analysis, Society of Manufacturing Engineers, Oak Brook, Illinois, USA, 1994. 178 p.
- Бернхардт Э. Переработка термопластических материалов М., Госхимиздат, 1962. 748 с.
- Мак-Келви Д. М. Переработка полимеров М., Химия, 1975. 442 с.
- Doring Е., Schurmann Е. Thermal and Mechanical Design of Injection Molds (G), Internal Report of IK V Aachen, 1979.
- Lakzkovich H. Molds for Plastics Processing Made by Sand-Casting (G), VDI-Verlag GmbH, Dusseldorf, 1976. p. 15.
- Горюнов И.И. Пресс-формы для литья под давлением. Справочное пособие. JI, Машиностроение, 1973. 256 с. ' ' •
- Стамбургский Е.А., Бейль А. И., Каливан В. П., Беспалов Ю. А. Износ оборудования при переработке пластмасс. М., Химия, 1985. 208 с.
- ANSYS Structural Non Linearities User’s, Guide for Revision 5.1 ANSYS Corp., v. II, 1995. p. 13−1-13−69.
- Mark’s Standard Hand Book for Mechanical Engineers, 10-th Edition McGraw — Hill, 1997. 923 p.
- Mechanical Engineering Design, 5-th Edition McGraw — Hill, 1989. p. 243−246.
- Weakley Sh, ZaluzecM. Surface Hardening of Aluminium Moulds Using Micro-Arc Oxidation, Technical Report, Manufacturing and Materials Research Laboratory, Ford Motor Company, 1996. 19 p.
- Солнцев C.C. Защитные технологические покрытия и тугоплавкие эмали. М., Машиностроение, 1984. 256 с.
- Демиденко JI.M. Высокоогнеупорные композиционные покрытия. М., Металлургия, 1979.216 с.
- Кинджерн В.Д. Измерения при высоких температурах. Пер. с англ. М., Металлургиздат, 1963. 466 с.
- Buessem W.R., Bush Е. J. Amer. Ceram. Soc. V. 38, № 1, 1955. p. 27−32.
- Designing plastic injection molds. Society of Manufacturing Engineers (SME), USA, 1994. 260 p.
- Kuzze P., Krysmann W" Marx G., Wiss Z. Techn. Hochsch. (Karl-Marx-Stadt), v. 24, № 6, 1982. p. 665−670.
- Лахтин Ю.М., Леонтьева В. П. Материаловедение. JI., Машиностроение, 1980. 494 с.
- Адлер Ю.П., Марков Е. В., Грановский Ю. В. Планирование эксперимента при поиске оптимальных условий. М., Наука, 1976. 279 с.
- Монтгомери Д.К. Планирование эксперимента и анализ данных. Л., Судостроение, 1980.
- Новик Ф.С. Планирование эксперимента на симплекс при изучении металлических систем, М., Металлургия, 1985.
- Non-conductive coatings on njn magnetic basic metals. Measurement of coating thickness. Eddy current method. ISO 2360, 1982.
- Покрытия металлические и неметаллические неорганические. Методы контроля. ГОСТ 9.302−88.
- Metallic and related coatings. Vickers and Knoop microhardness tests. ISO 4516, 1980.
- Измерение твердости материалов. ГОСТ 22 975–78.
- Методы определения электрической прочности при переменном (частота 50 Гц) и постоянном напряжении. ГОСТ 6433.3−71.
- Statgraphics Plus, Experimental Design, Manugistics, Inc, 1995. 210 p.
- Метод испытания на сжатие. ГОСТ 25.503−80.
- Метод испытания на контактную усталость. ГОСТ 25.501−78.
- Методы испытаний на усталость. ГОСТ 25.502−79.
- Методы испытаний на малоцикловую усталость при термотехническом нагружении. ГОСТ 25.505−85.
- Методы определения предела текучести и предела прочность при сжатии для твердых сплавов спеченных. ГОСТ 27 034–86.
- Металлы. Метод испытания на ползучесть. ГОСТ 3248–81.
- Металлы. Метод испытания на длительную прочность. ГОСТ 10 145–81.
- Методы испытаний на релаксацию напряжений. ГОСТ 26 007–83.
- Машины для испытания материалов на ползучесть, длительную прочность и релаксацию. ГОСТ 28 845–90.169
- Standart Test Methods of Compession Testing of Metallic Materials at Room Temperature E9−24T ASTM Standard, USA.
- Орлов A.B., Черменский O.H., Нестеров B.M. Испытание конструкционных материалов на контактную усталость. М., Машиностроение, 1980, 110 с.
- Plastic Tools Engineering was responsible for modeling part geometry and also cooling lines into a format which is useful for moldflow simulation.1. Approach:
- Этот отчет запрошен Е. Пруссом для определения следующего:
- Определение уменьшения времени охлаждения при использовании алюминия в качестве материала формы по сравнению со сталью.
- А также определения разницы во времени охлаждения при увеличении толщины детали.
- Отдел проектирования инструмента для пластмасс несет ответственность замоделирование геометрии детали, а также каналы охлаждения, в формате, который полезен для использования в «молдфлоу» моделировании.1. Приближения:
- Constant polymer specific heat Cp = 2.0520E+03 J/kg-C
- Constant polymer thermal conductivity K = 3.2000E-01 W/m-C
- Cross-WLF polymer viscosity ETAo
- ETA =----------------------1 + (ETAo*GAMMA/TAUS)A (1-n) A1*(T-TS)where ETAo = D1*EXP (-----)
- A2+(T-TS) TS = D2 + D3*p A2 = A2T + D3*p n = 1.7000E-01 TAUS = 7.4227E+05 Pa D1 = 7.7400E+11 Pa-s D2 = 4.1715E+02 K D3 = 0.0000E+00 K/Pa A1 = 2.7416E+011. A2T = 5.1600E+01 K
- Transition temperature Ttrans = 1.3300E+02Cprocess conditions.
- Post-fill time = 5.0000E+00 s
- F/P switch over by % volume = 9.9000E+01%
- Timer for hold pressure = 5.0000E+00 s1. Ram speed profile (rel):stroke % speed
- Pack/hold pressure profile (rel): % time % fill pres0.0000E+00 8.0000E+011.0000E+02 6.0000E+01
- Ambient temperature = 2.4850E+01 C1. let melt temperature = 3.2819E+02C1. Coolant manifold control:1. Pres drop CID1 1.5000Е+01 С 1.0000Е+01 lit/min О. ООООЕ+ОО МРа 12 1.5000Е+01 С 1.0000Е+01 lit/min О. ООООЕ+ОО МРа 1
- Average coolant temperature1.5000Е+01 С1. Results & Conclusions: